SNT ACLE 101 Installation and operating instructions

INSTALLATION, OPERATION AND MAINTENANCEnance
NO/02/210002
LINEAR ACTUATORS
ACLE 101 - ACLE 002 - ACLE 103
ENGLISH Ed 01-2021

2
WARNING
Read this manual before installing, operating or maintaining this actuator. Failure to
follow safety precautions and instructions could cause actuator failure and result in
serious injury, death or property damage.
This manual provides important information on how to work with the actuator safely
and efficiently. The manual is part of the device, must always be kept in the device’s
direct proximity and should be available for personnel to read at any time. Failure to
comply with the installation, use and maintenance instructions indicated in this
manual will result in immediate termination of the warranty conditions of the
actuator and completely relieve SNT from any liability for damage caused to persons
and / or property.
SNTdoes not assume direct or indirect responsibility for an improper use of the
actuator, not respecting the performances of the actuator declared in the catalogs.
The manufacturer will not be liable for damage to the actuator or the equipment into
which the actuator has been installed resulting from:
• disregarding this manual
• unintended use
• employment of untrained personnel
• unauthorized conversions
• technical modifications
• manipulation or removal of the screws on the device
• use of unapproved spare parts
The aforementioned conditions are therefore not contemplated and entail the
immediate termination of the guarantee and the immediate decay of any
responsibility on the part of SNT.
SNT reserves the right to make changes to the actuators and this manual without
giving any notice.

3
LINEAR ACTUATORS ACLE 101-002-103
Installation, operation and maintenance manual
Contents
1 MODELS COVERED BY THIS DOCUMENT....................................................................................................4
2 IDENTIFICATION OF THE MANUFACTURER AND THE PRODUCT................................................................4
2.1
2.2
Description of the product .................................................................................................................4
Identification of the product ..............................................................................................................5
3 TRANSPORT AND HANDLING ......................................................................................................................6
4 USE RESTRICTION .........................................................................................................................................6
4.1 Intended use.......................................................................................................................................6
4.1.1 Use restrictions...........................................................................................................................7
4.1.2 Standard operating conditions...................................................................................................7
4.1.3 Thermal limit ..............................................................................................................................7
4.2 Personnel requirements / Qualifications ...........................................................................................8
5 STORAGE.....................................................................................................................................................8
6 INSTALLATION ............................................................................................................................................8
6.1 Safety warnings ..................................................................................................................................8
6.2 Stroke end limit switches FC2...........................................................................................................10
6.3 Stroke end limit switches FC2X ........................................................................................................11
6.4 Encoder GI21 –GI24.........................................................................................................................12
6.5 Electric DC motor wiring...................................................................................................................13
6.6 Linear actuator installation ..............................................................................................................14
6.7 Installation of rod end fitting elements............................................................................................15
7 COMMISSIONING AND USE......................................................................................................................16
8 LUBRICATION............................................................................................................................................17
9 MAINTENANCE .........................................................................................................................................17
10 WIRING SCHEMES.....................................................................................................................................18

4
1MODELS COVERED BY THIS DOCUMENT
The present manual is referred to following products:
Acme screw linear actuators: ACLE101 - ACLE002 - ACLE103
2IDENTIFICATION OF THE PRODUCT
2.1Description of the product
For all the technical characteristics of the product (performance, features, dimensions) refer to the
technical catalog.
Main actuator components:
Figure 2.1 –Main actuator components
1) Push rod
2) External profile
3) Gearbox housing
4) Front housing
5) Rod end
6) Rear hinge
7) Stroke end limit switches cover
8) DC electric motor
6
1
4
2
3
5
7
8

5
2.2Identification of the product
Every linear actuator is provided with a product label, which allows the product identification and
gives technical information about the product.
On the actuator label following data are printed:
CODE: article code;
•Product Description (the mining of symbols and their sequence are indicated on the
catalogue);
•Production batch number (gives the full traceability of products);

6
3TRANSPORT AND HANDLING
It is recommended to pay attention and care during the handling and transport of linear actuators
not to damage mechanical parts and / or accessories and to prevent risks for the personnel in charge
of this activity.
The packaging must be lifted and moved with care and in a safe way.
For lifting and transporting the linear actuator, the push rod must be in retracted position.
Lift the actuator from the housing and outer tube, supporting the motor during transport.
DO NOT lift the actuator only from the push rod and / or the motor.
In case of doubt, consult SNT to get the appropriate information and prevent any kind of damage!
4USE RESTRICTION
The information contained in this chapter provides important prescriptions for operating safely during all
phases of the product's life.
Not knowing or not complying with these provisions can generate dangerous situations that could cause
damage to equipment and risks for the safety of persons.
4.1 Intended use
Actuators are used to perform very different functions within machines. It is the responsibility of the machine
builder to design the application in compliance with the laws in force in the specific sector and in the field of
safety, in compliance with the requirements provided in the product catalog and in this manual.
ACTUATORS ARE ELECTRIC AXIS, WHATEVER DRIVER OR CONTROL WILL BE USED: THE SELECTION OF
THE PRODUCT AS STROKE, SPEED, TYPE OF LIMIT SWITCHES, MOTOR AND BRAKE, MUST BE DONE
ACCORDING TO THE BEHAVIOR EXPECTED, IN FUNCTION OF THE TYPE OF CONTROL CHOOSEN AND
THE STATIC AND DYNAMIC BEHAVIOR OF THE SYSTEM IN WHICH THE ACTUATOR IS PLACED!
The actuators have been designed and built to operate mobile parts of various types, shapes and
construction, in the ways and within the limits set out in the descriptions and tables of the technical data in
the catalog and in this user manual.
The actuators are designed to work with a purely axial applied load.
They must be subjected to the loading and speed conditions specified in the catalog.
Modification of parts of the actuator or replacement of components with different and non-original parts
is not permitted. The replacement of components with original spare parts is carried out only by SNT.
Any different use is to be considered improper and therefore potentially dangerous for the safety of
the operators, as well as such as to void the contractual guarantee.
In the event of particular processing requirements, we recommend consulting our sales department. Every
modification must be authorized by SNT with written documents.
ANY OTHER USE OUTSIDE THAT THAT JUST DESCRIBED IS NOT PERMITTED BY SNT.

7
4.1.1 Use restrictions
Actuators can not be used for unforeseen applications.
Any utilization of this device beyond its intended purpose may lead to potentially hazardous situations.
Therefore:
•Strictly adhere to all safety precautions and instructions in this operating manual.
•Do not allow this device to be subjected to weather conditions, strong UV rays, corrosive or explosive
air media as well as other aggressive media (*).
•Do not modify, retool or change the structural design or individual components of the actuator.
•Never use the device outside of the technical application and operational limits.
(*) –THE USE OF THE ACTUATOR IN ABOVE CONDITIONS MUST BE PREVIOUSLY DECLARED AND
AGREED WITH SNT, SINCE A SPECIAL EQUIPMENT OF THE PRODUCT MUST BE PROVIDED.
4.1.2 Standard operating conditions
The actuator must be used in an environment whose conditions comply with the provisions of SNT. The
works necessary for obtaining and maintaining that conditions are in charge of the owner and, where
applicable, are in charge of the end user.
The actuator must be installed and used indoor only, in dry area with environmental conditions as specified
below:
Temperature range +0°C ÷ +40°C
Relative atmospheric humidity 5% ÷ 85%
No build up of condensation
Linear actuator must be installed and used in a room with a constant illumination of 500lux at least,
complaining the norm UNI EN 1837:2009, or complaining specific norms related to specific application fields.
THE USE OF THE ACTUATOR IN DIFFERENT CONDITIONS THAN JUST DESCRIBED MUST BE PREVIOUSLY
DECLARED AND AGREED WITH SERVOMECH, SINCE A SPECIAL EQUIPMENT OF THE PRODUCT MUST
BE PROVIDED.
4.1.3 Thermal limit
The actuator duty cycle permissible Fu [%] is the maximum working time expressed in percentage that the
actuator can perform during the reference time period of 10 minutes, under rated load stated in the
catalogue at ambient temperature 25°C, without risk of internal parts overheating.
𝑭𝒖[%]=𝑀𝑎𝑥 𝑤𝑜𝑟𝑘𝑖𝑛𝑔 𝑡𝑖𝑚𝑒 𝑜𝑣𝑒𝑟 10 𝑚𝑖𝑛
10 𝑚𝑖𝑛 ×100
Actuator
Fu [%]
ACLE 101
15
ACLE 002
15
ACLE 103
15
For the proper operation do never exceed the permissible duty cycle limit.

8
4.2 Personnel requirements / Qualifications
This manual must be made available to the personnel in charge of installation, start up and use of the
actuator. It is the responsibility of the machine builder:
use personnel with the necessary qualifications for the installation and commissioning of the
actuator;
periodically check the qualification of the assigned personnel;
check that the personnel in charge are aware of the contents of this manual.
5STORAGE
Do not store outside.
Storage should be dry and dust-free.
Keep away from any aggressive media.
Protect from UV radiation.
Avoid mechanical vibrations.
Storage temperature: 0 to +50 °C.
Relative atmospheric humidity: max. 95% (no build up of condensation).
6INSTALLATION
The operations described in the paragraphs of this chapter provide both electrical and mechanical
connections of the actuator, as well as the execution of test motions at reduced speed and motor torque or
with small displacement steps.
6.1 Safety warnings
MOTORS CANNOT BE CONNECTED DIRECTLY TO THE ELETRICITY GRID. A PROPER CIRCUITS AND
DEVICES FOR MOVEMENT MANAGEMENT ON BOTH DIRECTIONS IS REQUIRED. STROKE END LIMIT
SWITCHES (MICROSWITCHES OR SENSORS) MUST BE CONTROLLED TO BE SURE THE LINEAR
MOVEMENT OF THE ACTUATOR (DUE TO THE OPERATION OF THE MOTOR OR TO THE INERTIA OF
THE MOVING PARTS) STOPS BEFORE TO REACH THE MECHANICAL STROKE END LIMITS. IN CASE THIS
HAPPENS, THE ACTUATOR CAN BE LOCKED AND THE INTERNAL COMPONENTS CAN BE DAMAGED.
WHEN THE MOTORS MUST BE POWERED BY A CONVERTER (ELECTRIC DRIVE), THIS MUST BE CHOSEN
BY QUALIFIED PERSONNEL.
IN CASE THERE ARE INVOLVED ELECTRONIC DRIVE AND CONTROL DEVICES ON THE ACTUATOR
MOVING CONTROL, REFER TO MANUALS FOR ALL THE NECESSARY INFORMATION AND CORRECT
INSTALLATION AND MAINTENANCE OF THE PRODUCT.
BEFORE TO PROCEED TO THE ELECTRIC CONNECTION, MAKE SURE THE SUPPLY VOLTAGE IS TURNED
OFF.
BEFORE TO TURN-ON THE MOTOR, MAKE SURE THE ELECTRIC CONNECTIONS ARE TIGHTENED AND
STABLE.
CHECK POWER SUPPLY CABLES NOT TO BE DAMAGED DURING THE COMMISSIONING. POWER
SUPPLY CABLES MUST BE OUT OF HEAT SOURCES AND MOVING ORGANS.
DURING FUNCTIONING ARE PRODUCED MAGNETIC, ELECTRIC AND ELECTROMAGNETIC FIELDS. THIS
MAY BE DANGEROUS FOR PEOPLE THAT USE CARDIAC STIMULATOR (PACEMAKER), IF NOT
SUFFICIENT DISTANCE.
DO NOT DISCONNECT ANY CONNECTION DURING OPERATION OR IN PRESENCE OF SUPPLY VOLTAGE.
BEFORE TO TURN-ON THE MOTOR, MAKE SURE THE MECHANICAL CONNECTIONS OF THE ACTUATOR
REMAIN TIGHTENED AND STABLE, ALSO DURING THE OPERATION.

9
DURING THE COMMISSIONING, UNEXPECTED MOVEMENT OF THE MOTOR MAY BE CAUSED BY:
WIRING ERRORS
MOUNTING ERRORS
DAMAGES ON POWER SUPPLY CABLES
HARDWARE OR SOFTWARE ERRORS
DRIVER PARAMETERS ERRORS
OPERATION IN CONDITIONS OUTSIDE THE SPECIFICATIONS PROVIDED BY THE
CATALOG AND THIS MANUAL
MAKE SURE THE SAFETY PROTECTION OF THE MACHINE (MECHANICAL AND ELECTRICAL) ARE
ACTIVE.
DURING OPERATION, TEMPERATURE OF THE EXTERNAL SURFACE OF MOTORS CAN REACH HIGH
TEMPERATURES. HOT SURFACES ON ACTUATOR CAN CAUSE BURNS AND SHOULD NOT BE TOUCHED.
DO NOT FASTEN OR PLACE NEAR THE MOTOR THERMO SENSITIVE COMPONENTS: DAMAGES MAY
OCCUR.

10
6.2 Stroke end limit switches FC2
Each of the two micro-switches is fitted in a slot with a cam for switches commutation. A screw allows to lock
the assembly in the desired position, adjusting in this way the switching position. The nut with suitable shape
makes the cams rotate, so to activate the switches. This cam-operated device provides a stable and self-
keeping commutation of the switches.
Figure 6.1 –Stroke end limit switches FC2
RETRACTED ACTUATOR (Lc) position is adjusted and controlled by FC 1 switch.
EXTENDED ACTUATOR (La) position is adjusted and controlled by FC 2 switch.
Following pictures show the switching sequence of the switch.
Figure 6.2 –FC2 functioning
To setup the stop positions:
Loosen the screws (1) of the limit switches cover.
Remove the cover (2): pull out side A first (push rod
side), then side B (gearbox side).
Loosen the switch fixing screw (see Fig. 6.1).
Move the plastic support on the required position.
Screw fasten the fixing screw again and close the
cover.
1
2
A
B
Figure 6.3 –FC2 limit switches setup

11
Limit switches FC2 –TECHNICAL FEATURES
Contact
Standard: NC
On request: NO, CS
Supply voltage
250 V AC
30 V DC
Max current (resistive load)
12 A
5 A
Max current (inductive load)
6 A
3 A
Output
Multicore PVC cable - length 0.3 m
For FC2 limit switches wiring instructions: see Section 10.
DO NOT TRAVEL OVER THE STROKE LIMIT SWITCHES POSITIONS, AVOIDING TO REACH MECHANICAL
STOP AND PREVENTING DAMAGE TO THE INTERNAL COMPONENTS OF THE ACTUATOR.
6.3 Stroke end limit switches FC2X
Technical features, setup instructions and functioning of FC2X limit switches is the same as FC2 switches (see
Section 6.2).
The two electric cam-operated switches are internally wired between power supply and electric motor, in
order to switch off the power supply directly, without relays.
With FC2X limit switches wiring it is NOT possible to read signal coming from the switches. For this
reason it is recommended to provide a timing control on motor power supply and/or a current limit
on the power supply circuit.
Wiring of limit switches and electric motor is shown on following schemes:
Figure 6.4 –Stroke end limit switches FC2X
For wiring instructions: see Section 10.

12
6.4 Encoder GI21 –GI24
Encoder GI21-GI24 –TECHNICAL FEATURES
Transducer type
Hall effect probe, incremental, bidirectional
Resolution
1 pulse/rev (GI21) - 4 pulses/rev (GI24)
Output
PUSH-PULL
2 channels (A/B)
Supply voltage
5 ÷ 24 V DC
Max commutable current
50 mA
Cable length
0.3 m
Electrical protection
Polarity inversion
Supply voltage peaks
Wiring scheme:
Figure 6.5 –Encoder GI21/GI24
Following table shows n° of pulses for 100 mm of stroke, for each actuator size and ratio:
N° of pulses for 100 mm of stroke
Encoder resolution
1 ppr (GI21)
4 ppr (GI24)
ACLE101
RL1
967
3867
RL2
483
1933
RN1
383
1533
RN2
192
767
ACLE002
RL1
1550
6200
RL2
775
3100
RN1
492
1968
RN2
246
984
ACLE103
RL1
1725
6900
RL2
862
3450
RN1
650
2600
RN2
325
1300
For GI21 - GI24 encoder wiring instructions: see Section 10.

13
6.5 Electric DC motor wiring
Connect the motor to the power unit of the plant or to the driver according to the following wiring diagrams:
Figure 6.6 –Electric wiring diagrams to power supply of DC motor
Figure 6.7 –DC motor wiring
Check if the push rod shifting direction is compatible to the indications on the control unit, by powering the
electric motor on VERY BRIEFLY.
Figure 6.8 –Push rod shifting directions
If the push rod shifting directions are not compatible: invert contacts of the two motor supply cables.
For stroke limit switches and/or encoder wiring instruction: see Section 10.
K1, K2 = contactor
M = motor
RED +Vdc
BLACK -Vdc
RED -Vdc
BLACK +Vdc

14
6.6 Linear actuator installation
ALL MECHANICAL AND ELECTRICAL PROTECTION MUST BE INSTALLED AND ACTIVATED TO PREVENT
DAMAGE TO PERSONS OR PROPERTY.
•Check that all plant fixing elements are well machined and cleaned, and that they fit the dimensions of
the actuators fixing elements they have to be fixed to.
•If the length of the actuator have to be changed (push rod more retracted or extended) during
installation, power the motor with limited speed and torque values, in order to avoid possible damages
in case of a mechanical stop is reached.
•In case of actuators without anti-rotation device (AR), it is possible to manually screw/unscrew the push
rod to change the length of the actuator.
DO NOT SET THE LENGTH OF THE ACTUATOR OVER ITS EXTREME VALUES:
“Lc” = RETRACTED ACTUATOR
“La” = EXTENDED ACTUATOR
Figure 6.9 –“Lc” and “La” dimensions
Dimensions “Lc” and “La” are indicated in the technical catalogue of the product.
Stroke
Lc
La = Lc + stroke

15
•Fit the actuator to the plant in order to have ONLY axial load applied to the actuator.
•Check the correct alignment between front and rear pins: they must be PARALLEL.
•Check the correct alignment between the actuator and the moving parts.
a)
b)
Figure 6.10 –Load on actuator: a) correct; b) not correct
RIGHT WORKING OF THE ACTUATOR AND PLANT CANNOT BE GUARANTED IF SIDE OR NOT AXIAL
LOAD ARE APPLIED TO THE ACTUATOR.
6.7 Installation of rod end fitting elements
To install a mounting element on the rod end threaded bore (BA), use a wrench flat on the rod end
to counterhold the locking torque.
In case of actuator equipped with AR (anti-rotation) device: DO NOT TRANSFER ANY TORQUE TO
THE PISTON ROD.
WARNING: in case of torque transfer into the actuator with AR device, the internal mechanical
components can be damaged.
Fix the threaded element with Loctite 270.
To unmount the element, heat the threaded area to unlock it.
Unscrew the fitting element counterholding the torque with a wrench flat on the rod end.
Figure 6.11 –Installation of rod end fitting element
F
F
F

16
7COMMISSIONING AND USE
Linear actuators are supplied lubricated and ready to be used. Before to start commissioning and
activation, the following checks must be carried out:
Shifting direction check
Check if the push rod shifting direction is compatible to the indications on the control unit, by
powering the electric motor on VERY BRIEFLY. If not, see Section 6.5.
For actuators without anti-rotation device (AR): TO ALLOW THE TRANSLATION OF THE ROD END, THE
PUSH ROD ROTATION MUST BE REACTED BY USING EXTERNAL GUIDES.
Check of extreme working positions
Check if the extreme dimensions of the actuator “Lc” and “La” (see Fig. 6.9) are compatible with
extreme positions of the plant component that has to be moved.
Measure the initial length of the actuator, then run the actuator GRADUALLY from the control unit,
in order to reach the plant to its more distant extreme position.
Check continuously the current actuator length during the motion.
Repeat the same procedure for the other extreme position.
TO AVOID DAMAGES, DO NOT TRAVEL OVER THE EXTREME STROKE VALUES Lc and La!
DO NOT REACH STROKE END MECHANICAL STOP!
Commissioning
At this stage it is possible to start commissioning:
Carry out one complete working cycle, without load, adjusting the previously set limit switch
positions if necessary (see Sections 6.2).
Carry out some complete working cycles, increasing gradually the load, until full load is reached.
DURING COMMISSIONING, DO NEVER EXCEED THE MAX ALLOWED DUTY CYCLE FOR THE LINEAR
ACTUATOR INDICATED IN SECTION 4.1.4. ANY ABUSE OF SUCH DUTY CYCLE CAN CAUSE
OVERHEATING AND UNINTENTIONAL PREMATURE DAMAGING!

17
8LUBRICATION
Linear actuators ACLE101-002-103 series are supplied lubricated, with lubricants indicated in the table
below.
ACTUATOR
GEARBOX
LINEAR DRIVE
ACLE101
Grease (NLGI 2 DIN 51818):
ENI Grease SM 2
Also suitable:
SHELL Gadus S2 V220D 2 (NLGI 2)
MOBIL Mobilgrease XHP 222 Special (NLGI 2)
FUCHS Renolit FLM 2 (NLGI 2)
Grease (NLGI 2 DIN 51818):
ENI Grease SM 2
Also suitable:
SHELL Gadus S2 V220D 2 (NLGI 2)
MOBIL Mobilgrease XHP 222 Special (NLGI 2)
FUCHS Renolit FLM 2 (NLGI 2)
ACLE002
ACLE103
Table 8.1 –Lubricants
DO NOT USE LUBRICANTS DIFFERENT FROM THOSE ABOVE MENTIONED.
DO NOT MIX INCOMPATIBLE GREASES.
IF DIFFERENT LUBRICANT SHOULD BE USED, PLEASE CONTACT SERVOMECH BEFORE PROCEED.
IN CASE OF CUSTOM PRODUCT EXECUTION, THE LUBRICANTS COULD BE DIFFERENT FROM THE
STANDARD ABOVE.
9MAINTENANCE
Linear actuators ACLE101-002-103 series are long-life lubricated and do not require any further
relubrication. Maintenance tasks to be carried out monthlyare described below:
Visual inspections of actuator conditions.
Cleaning of dirty parts of the actuator.
Check of electric power supply and signal cables.
In case of lubricant leakage or malfunctions, contact SNT.

18
10 WIRING SCHEMES
For actuator electrical wiring instructions, please refer to following wiring schemes.
In case of special wirings, please refer to the wiring instructions supplied with the product.
ACLE101 - 002
ACTUATOR EQUIPMENT
SCHEME CODE
Motor DC
CA.31.01.70U
Motor DC + microswitches FC2 (NC)
CA.31.01.02U
Motor DC + microswitches FC2 (NO)
CA.31.01.18U
Motor DC + microswitches FC2 (CS)
CA.31.01.05U
Motor DC + microswitches FC2(NC) + GI2x
CA.31.01.33nU
Motor DC + microswitches FC2(NO) + GI2x
CA.31.01.74U
Motor DC + microswitches FC3 (NC)
CA.31.01.03U
Motor DC + microswitches FC2X
CA.31.01.01U
Motor DC + microswitches FC2X + NO
CA.31.01.63U
Motor DC + microswitches FC2X+FC3 (NC)
CA.31.01.04U
Motor DC + microswitches FC2X+FC3 (NO)
CA.31.01.20U
Motor DC + microswitches FC2X + GI2x
CA.31.01.34U
Motor DC + pulses generator GI2x
CA.31.01.30U
Table 10.1 –Wiring schemes of ACLE101 - ACLE002
ACLE103
ACTUATOR EQUIPMENT
SCHEME CODE
Motor DC
CA.31.01.70U
Motor DC + microswitches FC2 (NC)
CA.31.03.02U
Motor DC + microswitches FC2 (NO)
CA.31.03.18U
Motor DC + microswitches FC2 (CS)
CA.31.03.05U
Motor DC + microswitches FC2(NC) + GI2x
CA.31.03.60U
Motor DC + microswitches FC3 (NC)
CA.31.03.03U
Motor DC + microswitches FC2X
CA.31.03.01U
Motor DC + microswitches FC2X + NO
CA.31.01.63U
Motor DC + microswitches FC2X+FC3 (NC)
CA.31.03.04U
Motor DC + microswitches FC2X+FC3 (NO)
CA.31.03.20U
Motor DC + microswitches FC2X + GI2x
CA.31.03.72U
Table 10.2 –Wiring schemes of ACLE103

-
+
ALE101 Wiring diagram for DC motor + switches FC2X
CA.31.02.01U
RETRACTING
EXTENDING
LH
LEFT
RIGHT
RH
BROWN
BLUE

ACLE101 - Wiring diagram for DC motor + switches FC2 (NC)
CA.31.01.02U
EXTENDING
RETRACTING
-
+
NC RETRACTED POSITION
NC EXTENDED POSITION
LH
LEFT
RH
RIGHT
STROKE
STROKE
EXTENDED POSITION
RETRACTED POSITION
RETRACTED POSITION
EXTENDED POSITION
0,75mm2 RED
0,75mm2 BLACK
0,22mm2. REDD
0,22 mm2 WHITE
0,22mm2 YELLOW
0,22mm2 GREEN
This manual suits for next models
2
Table of contents
Other SNT Controllers manuals
Popular Controllers manuals by other brands
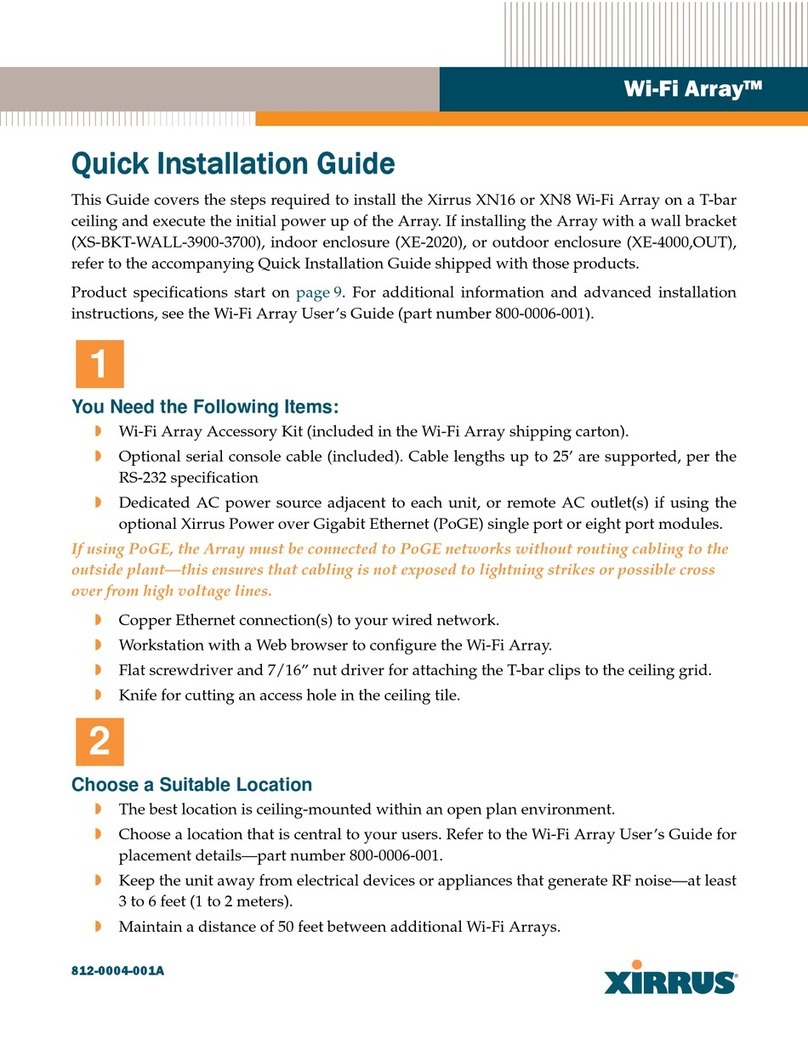
Xirrus
Xirrus Wi-Fi Array XN16 Quick installation guide
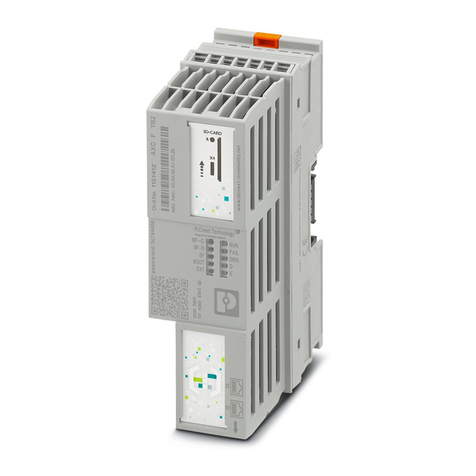
Phoenix Contact
Phoenix Contact AXC F 1152 user manual

Contemporary Research
Contemporary Research ICC-ZS2 product manual
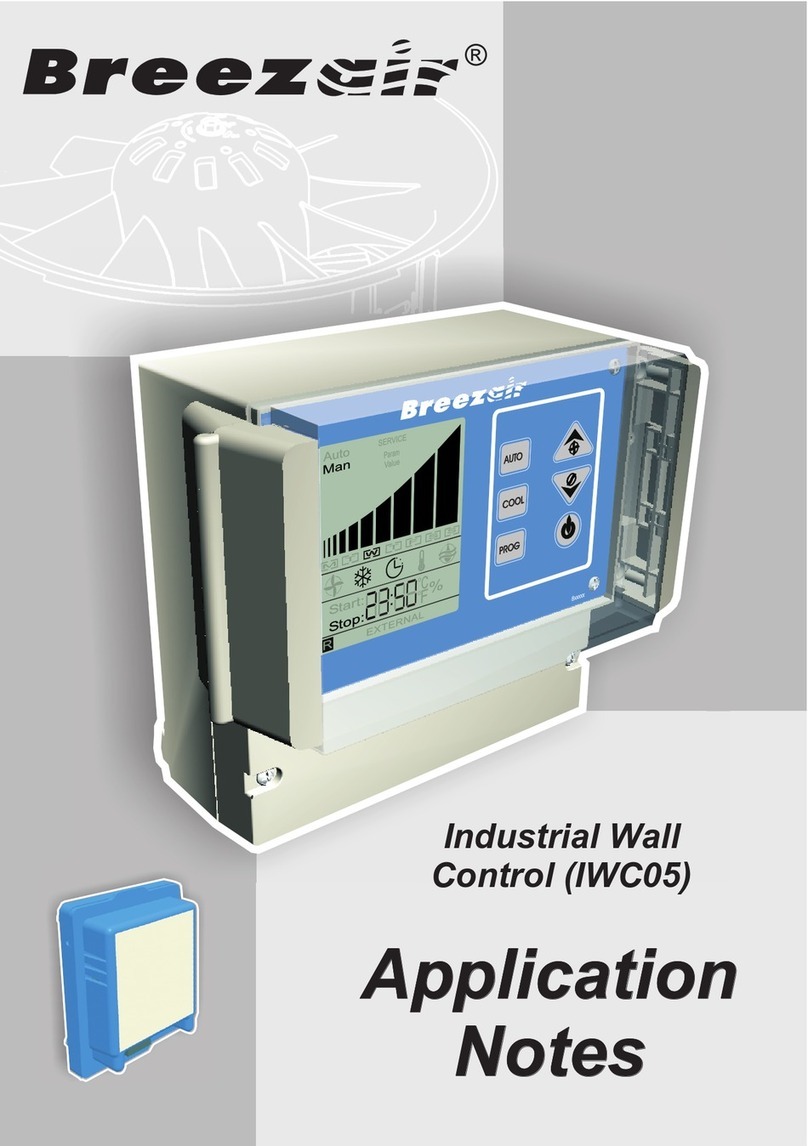
Breezair
Breezair IWC05 quick start guide
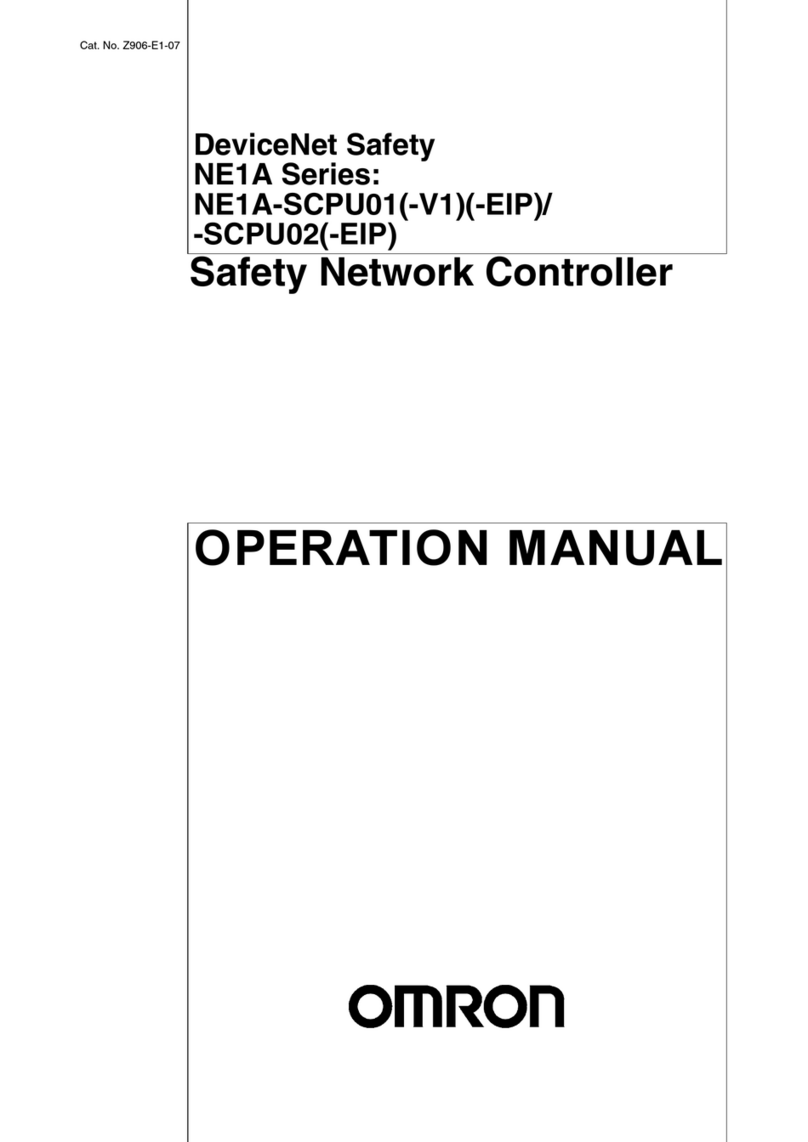
Omron
Omron NE1A-SCPU01 - 07-2009 Operation manual
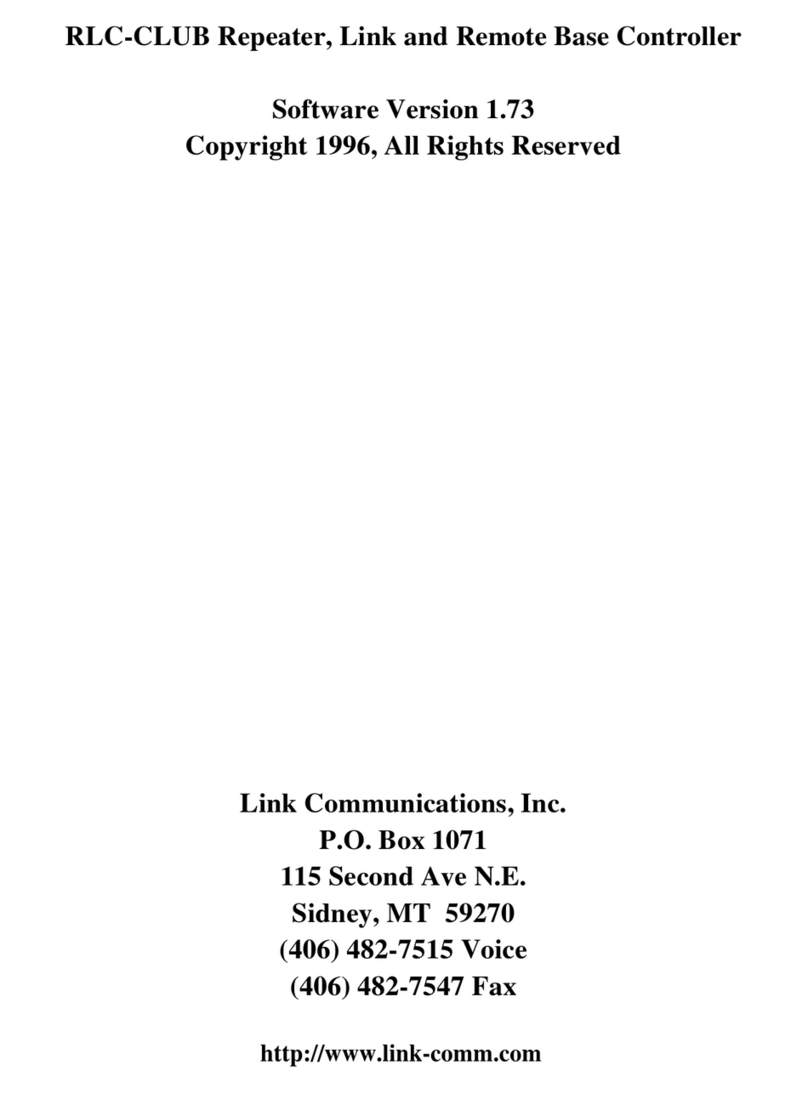
Link Communications
Link Communications RLC-CLUB user manual