Space Pak WCSP JV Series Instruction manual

SECTION 1: INTRODUCTION
SpacePak System Design.......................................
Code Compliance....................................................
Air Distribution Requirements..................................
Air Distribution Components....................................
Warranty Information...............................................
Shipment of Unit......................................................
SECTION 2: SYSTEM INSTA ATION
Step 1: Locating The Unit........................................
Step 2: Cutting Return Air Opening........................
Step 3: Attaching Supply Air Plenum Adaptor.............
Step 4: Setting The Unit..........................................
Step 5: Connecting Water Lines..............................
Step 6: Installing The Condensate Trap & Line.......
2
2
2
3
5
5
8
9
9
10
11
Step 7: Wiring The Unit.......................................
Step 8: Installing Air Distribution Components....
SECTION 3: START UP & OPERATION
Sequence Of Operation.......................................
Prior To Start-Up..................................................
System Start-Up & Adjustments..........................
Operating Setpoints.............................................
Factors Affecting the Balance of the System.......
SECTION 4: MAINTENANCE
Biannual Maintenance Checklist..........................
If System Fails To Operate..................................
Service/Troubleshooting Form.............................
Parts List..............................................................
Warranty...............................................................
11, 12
13
18
18
18
19
22
23
23
24
25, 26
27
IN UNIT D STAT S: 260 NORTH LM ST. W STFI LD, MA 01085 800-465-8558 / FAX (413) 564-5815
IN CANADA: 7555 TRANM R DRIV , MISSISSAUGA, ONTARIO, L5S 1L4 (905) 670-5888 / FAX (905) 670-5782
Central Hydronic Coil Series
2 to 5 Tons
Fan Coil Unit/Air Supply
Components
MODE
WCSP-JV SYSTEM
INSTA ATION,
OPERATION
& MAINTENANCE
MANUA
WCSPV2-0118
45W30-WG0706-01
Back Cover

2
SPACEPAK SYSTEM DESIGN
The SpacePak WCSP-J V unit is a hydronic fan coil unit
which utilizes chilled or heated water from a chiller or
boiler to provide the conditioned air through the specially
designed prefabricated preinsulated flexible duct system.
The system and its basic components operate the same
as in any conventional air-to-air cooling system.
The SpacePak system is covered by the following U.S.
Patents: 3,507,354; 3,575,234; 3,596,936; 3,605,797;
3,685,329; 4,045,977; 4,698,982; 926,673 and Canadian
Patents: 891,292; 923,935; 923,936.
CODE COMP IANCE
Fan coil unit installation must conform to the require-
ments of the local authority having jurisdiction or, in
the absence of such requirements, to the National Board
of Fire Underwriters regulations. Fan coil unit meets
TL listing requirements.
All electrical wiring must be in accordance with
the National lectrical Code ANSI/NFPA No. 70-latest
edition and any additional state or local code require-
ments. If an external electrical source is utilized, the fan
coil unit, when installed, must be electrically grounded.
NOTICE: It is a requirement of the International
Mechanical Code (307.2.3 ) to install a secondary drain
or an auxiliary drain pan where damage to any building
components will occur as a result of overflow from the
equipment drain pan or stoppage in the condensate
drain piping from a cooling or an evaporator coil.
AIR DISTRIBUTION SYSTEM
COMPONENT REQUIREMENTS
Air distribution components installation must conform
to the requirements of local authority having jurisdiction
or, in the absence of such requirements, to the National
Fire Protection Association 90A or 90B.
Do not begin the installation of the system without a
system layout and material take-off. If a layout plan is
not already available and room terminator requirements
determined, then refer to the SpacePak Application
Manual, SP9, to complete this information. A description
of air distribution system components is shown in Figure
1.1.
Section 1: INTRODUCTION
The following terms are used throughout this
manual to bring attention to the presence of potential
hazards or to important information concerning the
product:
Indicates an imminently hazardous
situation which, if not avoided, will result in death,
serious injury or substantial property damage.
Indicates an imminently hazardous
situation which, if not avoided, could result in
death, serious injury or substantial property damage.
Indicates an imminently hazardous
situation which, if not avoided, may result in
minor injury or property damage.
NOTICE: Used to notify of special instructions on
installation, operation or maintenance which are
important to equipment but not related to personal
injury hazards.

3
RETURN AIR BOX (SPC-1D, AC-RBF-3, SPC-3D):
ach includes filter grill with metal frame, permanent
filter, and 2 clamp bands. SPC-1D is for WCSP-2430JV.
AC-RBF-3 is for WCSP-3642JV and SPC-3D is for
WCSP-4860JV.
RETURN AIR DUCT (SPC-4,5, & 6): Flexible, 10' long
with round shape. SPC-4 (15" dia.) for WCSP-2430JV.
SPC-5 (19" dia.) for WCSP-3642JV and SPC-6 (24" dia.)
is for WCSP-4860JV .
P ENUM ADAPTOR: 9" round OR 10" X 10" square
metal component to attach plenum duct to fan coil unit.
Plenum Adaptor - 9" Round-AC-PAJ
Plenum Adaptor - 10" x 10" Square-AC-PAJSQ
P ENUM DUCT & COMPONENTS: May be SmartPak
System Duct, 9" round sheet metal or 10" X 10" (O.D.)
square, fiberboard duct types as specified by the
installing contractor. Above layout is shown as an
illustrative assembly reference only.
R6 SUPP Y TUBING (AC-ST6-100): Flexible, R6
insulated, 2" I.D. and 3-1/4" O.D. ach section is 100' long.
R8 SUPP Y TUBING (AC-ST8-75): Flexible, R8 insulated,
2" I.D. and 5-3/8" O.D. ach section is 75' long.
INSTA ATION KITS: Contains a specified amount
of sound attenuating tubes, kwik-connects, terminator
plates (incl. spring clips & screws), winter supply air
shut-offs and a balancing orifice set to complete
installation of room outlets. Supplied in (2) [AC-ILKT-2]
and (5) [AC-ILKT-5] outlet boxed quantities.
P ENUM TAKE-OFF KIT: Contains a specific amount
of plenum take-offs, gaskets and fasteners to complete
installation of room outlets. Take-offs available for round
sheet metal or square fiberboard duct as specified by
installing contractor. Supplied in (2) [AC-TKMR-2] and
(5) [AC-TKMR-5] outlet boxed quantities for round sheet
metal and (2) [AC-TKFS-2] and (5) [AC-TKFS-5] outlet
boxed quantities for square fiberboard.
KWIKCONNECTWA E BOW(AC-KCWE): To
allow for wall terminations in 2" X 4" stud spaces.
SECONDARYDRAINPAN: Specifically sized for
SpacePak horizontal fan coil units. Constructed of
durable polyethylene. Fan coil unit sets directly on top
and can be installed with threaded rod.
P IERS (SPC-72): To assure full setting of all clips
(fasteners) in plenum take-off (not shown).
P ENUM HO E CUTTER (SPC-71-10): To cut 2" hole
in fiber board for plenum take-off installation (not shown).
FIGURE 1.1: AIR DISTRIBUTION SYSTEM COMPONENTS

4
Plenum Duct
The plenum duct can be run in practically any location
accessible for the attachment of the supply tubing (see
suggested layouts in Figure 1.2). The plenum is normally
located in the attic or basement, and it is usually more
economical to run the plenum where it will appreciably
shorten the lengths of two or more supply runs.
In some two-story split level homes, it may be advanta-
geous to go from one level to another with the plenum
duct. Whenever necessary, either between floors or
along the ceiling, the small size of the plenum makes it
easy to box in.
The fan coil unit is designed to operate with a total
external static pressure of 1.5" of water column (minimum
1.2 - maximum 1.5). xcessive static pressure is an
indication of too few outlets and may cause the coil to
freeze and some or all outlets to be noisy.
For systems with a bullhead tee installed as on Unit No.
1 (Figure 1.3), the best results are obtained if not more
than 60% of the total number of system outlets are
attached to any one branch of the tee. For systems with
a branch tee installed as on Unit No. 2 (Figure1.3), not
more than 30% of the total number of system outlets
should be attached to the perpendicular branch of the tee.
The larger system capacities (WCSP-3642/4860) are
effected more by higher system static pressure than
the smaller systems. Installation of the plenum tee clos-
er than the minimum indicated in Fig. 1.3 will reduce per-
formance of the system. No supply runs should be
installed between unit outlet and this tee. Static readings
on system should be taken before tee.
FIGURE 1.2: P ENUM/TUBING AYOUT EXAMP ES
(FOR GUIDANCE ON Y)
UNIT NO. 1
UNIT NO. 2
FAN COIL UNIT
FAN COIL UNIT
NO MORE THAN
60% OF CAPACITY
ON ONE SIDE
30% MAX. OF CAPACITY
MINIMUM 18"
MINIMUM 18"
FIGURE 1.3: USE OF TEES

5
AA
AA
ROOM
TERMINATOR
FIGURE 1.4: TERMINATOR IN SOFFIT AREA
AA
AA
AAA
AAA
AAA
AAAAA
AAAAA
AAAA
SUPPLY
TUBING
ROOM
TERMINATOR
FIGURE 1.5: TERMINATOR IN C OSET TOP AREA
SECTION 2: SYSTEM INSTALLATION
NOTICE: Before proceeding with the installation, we
recommend reading through this section of the
manual for an overall understanding of the air
conditioning fan coil unit and air distribution system
component installation procedures.
STEP 1: OCATING THE UNIT
The fan coil unit may be installed in an unconditioned
space (as long as it is protected from the weather) such
as an attic, garage or crawlspace, or a conditioned space
such as a basement, closet or utility room (see dimen-
sions in Figures 2.2 and 2.3).
The fan coil unit is shipped set-up for horizontal supply
air discharge. This can be easily field converted to verti-
cal discharge, as detailed on pg. 9 and Figures 2.9A and
2.9B pg. 10.
When selecting a location, consider the locations (as
shown in Figures 2.4, 2.5 and 2.6) of the return air box;
routing of the plenum duct, supply tubing, refrigerant
lines, condensate drain line; and all recommended clear-
ances (see Figures 2.2).
Supply Tubing
In the case of two-story or split-level applications, supply
tubing may run from one story to another. It is small
enough to go in stud spaces, but this is often difficult
in older homes because of hidden obstructions in stud
spaces. It is more common to run the supply tubing
from the attic down through second story closets to
the first story terminators.
Supply tubing runs in the corners of the second story
rooms can be boxed in and are hardly noticeable since
overall diameter is only 3-1/4" (Model Number AC-ST6-
100).
Room Terminators
Terminators should be located only in the ceiling or floor
for vertical discharge. Horizontal discharge is accept-
able, but is sometimes more difficult to install. Two
excellent spots for horizontal discharge are in the soffit
area above kitchen cabinets (see Figure 1.4) and in the
top portion of closets (see Figure 1.5).
Terminators should always be out of normal traffic
patterns to prevent discharge air from blowing directly
on occupants. And they should not be located directly
above shelves or large pieces of furniture. Outside wall
or corner locations are recommended if the room has
more than one outside wall. Locating terminators away
from interior doors prevents short cycling of air to the
return air box. SHIPMENT OF UNIT
ach fan coil unit is shipped in a single carton. Packed with
the unit, there are vibration isolation pads, a condensate
trap assembly and a factory installed primary float switch.

6
Model
System
capacity
(Nom. Tons)
Water
In
Water
Out
Cond.
Drain
(NPT)
Return
Inlet
(Dia.)
Connections
C
WCSP-2430JV
WCSP-3642JV
WCSP-4860JV
2 - 2-1/2
3 - 3-1/2
4- 5
Electrical
Characteristics
230/1/60
230/1/60
230/1/60
7/8"
7/8"
7/8"
7/8"
7/8"
7/8"
115V/230V
3/4"
3/4"
3/4"
15"
19"
24"
Model
System
capacity
(Nom. Tons)
Std.
CFM @
1.5" W.C.
Motor
HP
F. L .
Amps
No. of
Rows
Deep
Blower
per Ton
(GPM)
Ship.Flow Rate
Wt.
(lbs)
WCSP-2430JV
WCSP-3642JV
WCSP-4860JV
2 - 2-1/2
3 - 3-1/2
4- 5
440, 550 3/4
3/4
3/4
5.6/2.8
7.6/4
10.6/5.4
6
6
6
2.4 120
144
171
660, 850
880, 1150
2.4
2.4
Coil
Wheel Dia.
and
Width
10" x 6"
10" x 6"
10" x 6"
Bottom To p
FIGURE 2.1: MODE WCSP-JV SPECIFICATIONS
FIGURE 2.2: UNIT DIMENSIONS AND C EARANCES (Inches)
A
10 9
16
268
B
C
Ø7/8 O.D.
(WATER OUT)
Ø7/8 O.D.
(WATER IN)
MIN. CLEARANCE MIN. CLEARANCE
16 1
8
409
79
16
192
41
4
108
34
864
11
16
17
3
76
2
51
LOW VOLTAGE
230VAC
411
16
118
25
8
67
11 1
4
285
11
4
31
25
16
58
21
2
64
3/4 NPT DRAIN CONNECTION
81
4
209
87
8
226
D
83
16
208
SUPPLY AIR OPENING
RETURN AIR OPENING
SPL-WG0996_A
GENERAL ASSEMBLY - DIMENSIONS & CLEARANCES
ALL DIMENSIONS IN INCHES [mm]
12
[305]
38
[965]
MODEL
AB
CD
WCSP-2430 (V)
24-3/8 [619] 18-1/4 [464]
12-3/16 [310]
6-1/16 [154]
WCSP-3642 (V)
33-3/8 [848] 25-1/2 [648]
16-11/16 [424]
15-1/4 [387]
WCSP-4860 (V)
43-3/8 [1102]
38-7/8 [987]
21-11/16 [551]
21-7/8 [556]

7

8
STEP 2: CUTTING RETURN AIR OPENING
Select exact location for return air box. Avoid installing
box in dining room, living room, kitchen, etc., unless
return air duct can be installed with at least two 90°
bends (accomplished by splicing two return air ducts
together.)
For attic installations to raise fan coil unit up through
opening, cut return air opening 14-1/2" wide by the "A"
dimension (Figure 2.7) of appropriate unit size. These
openings will accomodate the return air box with suffi-
cient frame lip to cover the opening (see Figure 2.7).
Refer to the "Installation Tip" supplied with the return
air box.
If ceiling joists are on 16" centers, the 14-1/2" width of the
return air box should fit between successive joists.
Where joists run in the opposite direction, or to properly
center the return, it may be necessary to cut joists and
install headers.
For all wall return applications, cut the return air opening
to accomodate the return air box (measure box itself).
Remember, location of opening must allow for a 90° bend
in the return air duct.
Check the opening for proper fit of the return air box. Do
not install the return air box until the installation of the
entire SpacePak system is completed, if you want to fit
materials up through this hole.
FIGURE 2.3: TYPICA C OSET/UTI ITY ROOM INSTA ATION
FIGURE 2.4: TYPICA C OSET INSTA ATION

9
STEP 3: ATTACHING SUPP Y AIR
P ENUM ADAPTOR
Refer to Figure 2.6 and duct installation instructions
supplied with fan coil unit.
14-5/16"
FIGURE 2.7: RETURN AIR BOX FRAME DIMENSIONS
Measure return air box dimension
"A" to determine length of opening.
Height = 14-5/16"
DWG0045
#8 X 3/4
MOUNTING SCREWS
(10 SUPPLIED)
10 INCH SQUARE SUPPLY AIR
PLENUM ADAPTOR ASSEMBLY KIT
PART NO. AC-PAJSQ
SPL-WG0986_B
ESP-2436 (V) SHOWN
FIGURE 2.6: P ENUM ADAPTOR ASSEMB Y
STEP 4: SETTING THE UNIT
Construct a platform for the fan coil unit, as shown in
Figure 2.10. The platform can be constructed of 2 x 4
(minimum), 2 x 6, 2 x 8 and 2 x 10 lumber, as necessary
to achieve sufficient height so that proper condensate
drain line pitch of 1/4" per foot can be maintained. Figure
2.11 shows the approximate normal allowable run of con-
densate piping as a function of the framing lumber used
for platform construction. The platform covering should
be 1/2" plywood minimum.
Attach vibration isolation pads (supplied inside fan coil
unit) to platform covering as shown in Fig. 2.10.
Secure the platform to the joist or floor, depending on
location selected for the fan coil unit. Make sure platform
is level.
For locations where the fan coil unit will be suspended,
suspend platform from overhead by 1/4" threaded rods.
NOTICE: eave room on sides for servicing.
For installations with a return air box and return air
duct, set fan coil unit on the platform with the elliptical
opening facing in the direction of the return air opening.
The supply air plenum adaptor should overhang the
platform. DO NOT let the adaptor support the weight of
the unit.
Do not secure the unit to the platform, as the weight of the
unit will hold it in position.

10
JV
JV
JV
FIGURE 2.7: MOUNTING P ATFORMS FOR VERTICA INSTA ATIONS
FIGURE 2.11: CONDENSATE PIPING RUNS
LUMBER SIZE
MAXIMUM
HORIZONTAL
2 x 4
8'
2 x 6
16'
2 x 8
24'
2 x 10
32'
STEP 5: CONNECTING WATER
INES
Connect water lines from outdoor chiller unit to the fan
coil unit in accordance with the chiller manufacturer’s
recommendations.

11
ITEM
1
2
3
4
5
6
MALE ADAPTER, 3/4''
DESCRIPTION
ELBOW 45
°
, 3/4''
1/2'' PLUG
3/4'' X 1/2'' BUSHING
TEE, 3/4''
P-TRAP, 3/4''
3/4'' P-TRAP ASS'Y KIT
WG0127B
NOTE: PIPE SECTIONS ARE FIELD SUPPLIED.
1
2
3
5
4
6
SEE NOTE
SECOND 3/4" MALE ADAPTER SUPPLIED FOR OVERFLOW CONNECTION
*
*
NOTICE: It is a requirement of the International
Mechanical Code (307.2.3) to install a secondary drain
or an auxiliary drain pan where damage to any building
components will occur as a result of overflow from the
equipment drain pan or stoppage in the condensate
drain piping from a cooling or an evaporator coil.
Follow local code requirements
Refer to Fig. 2.2 for primary and secondary condensate
drain locations. Components for the PVC condensate
trap are provided in a separate bag with fan coil unit (see
Fig. 2.12) and should be cemented together with PVC
pipe cement.
Do not use substitute trap. Do not cut
off or alter trap components.
Thread male adapter (see Fig. 2.12) into unit’s primary
condensate drain connection. Assemble and cement
remaining components together. Then cement assembly
to male adapter. The 45° elbow provides an offset from
beneath unit suction line for access to clean-out plug.
Run a condensate line from the trap to a suitable drain
that’s in accordance with local codes. Make sure the line
is pitched 1/4" per foot.
STEP 6: INSTA ING THE CONDENSATE TRAP & INE
STEP 7: WIRING THE UNIT
Turn off electrical power supply before
servicing. Contact with live electric components can
cause shock or death.
All electrical and control wiring must be installed in
accordance with the codes listed in Section 1 of this
manual. Wiring diagram is provided in Figure 2.13. A
separate 208-230/60/1 power supply is recommended
for the unit. Use standard 15-amp fuse and 16-gauge
wire from power supply to unit.
Connect power supply to Terminals L1 and L2 on the high
voltage terminal block. Connect a ground wire to the
equipment ground terminal located next to the high volt-
age terminal block.
The low voltage transformer in the unit has a 208 volt tap
in the primary winding (color coded R D). If unit is to be
operated with 208 volt electrical service, remove the 230
volt ORANG lead from the L2 terminal and connect the
208 volt R D lead to the L2 terminal. Be sure to insulate
the end of the unused ORANG lead.
Locate the room thermostat on a wall near the return air
box, between 40" to 48" from the floor. Connect the low-
voltage thermostat wiring from the room thermostat to
the control board in the unit.
Connect low voltage from air handler to condensing unit
as shown in figure 2.13.
Set DIP switches according to application. See page 13,
SpacePak JV Series Control DIP switch settings.
NOTICE: The secondary drain connection requires
field supplied components to complete installation.
Follow local code requirements.
NOTICE: Never connect condensate line to a closed
drain system.
FIGURE 2.12: CONDENSATE TRAP ASSEMB Y

12
FIGURE 2.13: MODE WCSP-JV WIRING SCHEMATIC

13
STEP 8: INSTA ING AIR DISTRIBUTION COMPONENTS
All plenum duct and supply tubing runs as well as room
terminator locations must be in accordance with air
distribution system requirements listed in Section 1 of
this manual. Where taping of joints is required, UL181
approved tape is required.
Plenum Duct Installation
All tees, elbows and branch runs must be a minimum of 18"
from the fan coil unit or any other tee, elbow or branch run.
Keep all tees and elbows to a minimum to keep system
pressure drop on larger layouts to a minimum.
NOTICE: Refer to duct installation instructions
supplied with fan coil unit or follow manufacturers
instructions supplied with other duct system types.
CWC
HWC
HP
OB
PWC
FC
Cooling Water Coil Present
Cooling Water Coil Settings
Switch 1
No Cooling Water Coil Present
Heat Pump Present
Heat Pump Settings
Switch 3
No Heat Pump Present
ON
Potable Water Circulation Settings
Switch 5
OFF
Heating Water Coil Present
Heating Water Coil Settings
Switch 2
No Heating Water Coil Present
Energized in Cooling Mode
Changeover Valve Settings
Switch 4
Energized in Heating Mode
ON
Fan Circulation Settings
Switch 6
OFF
SpacePak V Series Control Dip Switch Settings
Fan On Delay for
Water Coil Heat Demands
Adjustable from
0 - 2 Minutes
SpacePak V Series
Control Variable
Time Delay Settings
02
Fan Off Delay for ALL
Heating and Cooling Cycles
Adjustable from
0 - 2 Minutes
02
1 2 3 4 5 6
SpacePak JV Series Control Indicator EDs
Power Indicator
The Power indicator will blink to indicate that the control
is operational.
Fan Prove Indicator
The Fan Prove indicator will illuminate when there is
power to the fan and the optional damper is in the open
position.
Note: The Fan Prove Terminal will also energize with
24VAC when the above conditions are met.
Fault Indicator
Fault Flash Codes:
Float Switch 1 Flash
Anti-Frost Switch 2 Flashes
Fan Prove Fault 3 Flashes
Note: All Flash Codes are latched until power is cycled,
even if the fault is cleared. The Float Switch requires
power to be cycled to resume operation.

14
In marking location for room terminator (see Figure
2.20), the center of the terminator should be 5" from
the wall or, when installed in the corner of a room 5" from
both walls.
After marking location, drill a 1/8" diameter hole for
outlet. Verify there is at least a 2" clearance all around
the 1/8" hole to receive tubing and connector. Adjust
direction of hole as needed, to gain this 2" clearance.
After all clearances have been checked, take a 4"
diameter rotary-type hole saw and cut a hole, using the
1/8" diameter hole as a pilot.
Assemble spring clips to terminator plate with screws
provided in installation kit. Tighten clips until they are
close to the thickness of the material they are being
mounted to.
Assemble the room terminator to the sound attenuating
tubing by simply fitting the two pieces together and
twisting until tight (see Figure 2.21). If the terminator is
to be used in a floor location, then field fabricate a small
screen (1-1/2" square; 1/4 x 1/4 20-gauge galvanized
wire screen) and place screen over opening on the back
of the terminator prior to twisting on the kwik-connect
(on the sound attenuating tube).
NOTICE: Do not shorten sound attenuating tube
length. The result would be unacceptable noise.
Push the free end of the sound attenuating tube through
the 4" hole until the two toggle springs on the room
terminator snap into place.
ININSINSULAINSULATINSULATIINSULATIOINSULATIONINSULATIONINSULATION 3/8INSULATION 3/8INSULATION 3/8 NINSULATION 3/8 NOINSULATION 3/8 NOMINALINSULATION 3/8 NOMINAL
SHEETSHEETSHEET ROCKSHEET ROCK
SOUNDSOUNDSOUND ATTENUATORSOUND ATTENUATOR
33.3.5003.500 00.0.6250.625
3/163/163/16 GA3/16 GAP3/16 GAP
FOR
3/16 GAP
FOR
3/16 GAP
FOR APP
3/16 GAP
FOR APPL
3/16 GAP
FOR APPLICATIONS
3/16 GAP
FOR APPLICATIONS
3/16 GAP
FOR APPLICATIONS W
3/16 GAP
FOR APPLICATIONS WITH
3/16 GAP
FOR APPLICATIONS WITH
3/16 GAP
FOR APPLICATIONS WITH
THICKER
3/16 GAP
FOR APPLICATIONS WITH
THICKER
3/16 GAP
FOR APPLICATIONS WITH
THICKER WAL
3/16 GAP
FOR APPLICATIONS WITH
THICKER WALL
3/16 GAP
FOR APPLICATIONS WITH
THICKER WALLBOARD
3/16 GAP
FOR APPLICATIONS WITH
THICKER WALLBOARD,
3/16 GAP
FOR APPLICATIONS WITH
THICKER WALLBOARD,
3/16 GAP
FOR APPLICATIONS WITH
THICKER WALLBOARD,
RE
3/16 GAP
FOR APPLICATIONS WITH
THICKER WALLBOARD,
REM
3/16 GAP
FOR APPLICATIONS WITH
THICKER WALLBOARD,
REMOVE MATERIAL FROM
3/16 GAP
FOR APPLICATIONS WITH
THICKER WALLBOARD,
REMOVE MATERIAL FROM
3/16 GAP
FOR APPLICATIONS WITH
THICKER WALLBOARD,
REMOVE MATERIAL FROM
THIS A
3/16 GAP
FOR APPLICATIONS WITH
THICKER WALLBOARD,
REMOVE MATERIAL FROM
THIS AR
3/16 GAP
FOR APPLICATIONS WITH
THICKER WALLBOARD,
REMOVE MATERIAL FROM
THIS AREA TO ALL
3/16 GAP
FOR APPLICATIONS WITH
THICKER WALLBOARD,
REMOVE MATERIAL FROM
THIS AREA TO ALLO
3/16 GAP
FOR APPLICATIONS WITH
THICKER WALLBOARD,
REMOVE MATERIAL FROM
THIS AREA TO ALLOW FOR
3/16 GAP
FOR APPLICATIONS WITH
THICKER WALLBOARD,
REMOVE MATERIAL FROM
THIS AREA TO ALLOW FOR
PROPER 3/16 GAP
FOR APPLICATIONS WITH
THICKER WALLBOARD,
REMOVE MATERIAL FROM
THIS AREA TO ALLOW FOR
PROPER 3/16 GAP
FOR APPLICATIONS WITH
THICKER WALLBOARD,
REMOVE MATERIAL FROM
THIS AREA TO ALLOW FOR
PROPER F3/16 GAP
FOR APPLICATIONS WITH
THICKER WALLBOARD,
REMOVE MATERIAL FROM
THIS AREA TO ALLOW FOR
PROPER FI3/16 GAP
FOR APPLICATIONS WITH
THICKER WALLBOARD,
REMOVE MATERIAL FROM
THIS AREA TO ALLOW FOR
PROPER FIT. 3/16 GAP
FOR APPLICATIONS WITH
THICKER WALLBOARD,
REMOVE MATERIAL FROM
THIS AREA TO ALLOW FOR
PROPER FIT.
SPL-0050-A
FIGURE 2.19: INSTA ATION WITH KWIK
CONNECT WA E BOW
SOUND
AT T E N UAT I N G
TUBE
THIS RADIUS
TOO SHORT
STUD SPAC E
TERMINATOR
DRY WALL
OR PLASTER
FIGURE 2.18: INCORRECT TUBING INSTA ATION
Room Terminator & Sound Attenuating
Tubing Installation
Room terminators and pre-assembled sound attenuating
tubes are provided in the installation kits.
NOTICE: Do not install terminators in a wall in which
a sharp bend in the sound attenuating tube is
required (see Figure 2.18). The result would be
unacceptable noise.
OPTION: Using a SpacePak Kwik Connect Wall
Elbow (Model Number: AC-KCWE) addresses this
condition (see Figure 2.19).
4" DIA.
5"
5"
FIGURE 2.20: TERMINATOR MEASUREMENTS

15
Supply Tubing Installation
Kwik-connects and balancing orifices are provided in the
Installation Kits. Plenum take-offs, gaskets and fasten-
ers are supplied in the separate plenum take-off kits.
Avoid sharp bends in the supply tubing (as well as the
sound attenuating tube). The minimum radius bend is 4"
(see Figure 2.22); however, wherever possible, hold to a
larger radius.
At the plenum, all supply tubing connections must be
a minimum of 18" from any plenum tee, plenum elbow
or the fan coil unit.
Individual supply tubing runs must be a minimum of
6-feet, even if the distance between the sound attenuat-
ing tubing and plenum is less than 6 feet.
Supply tubing comes in 100-foot sections (R8 tubing
comes in 50-foot sections and R6 tubing comes in 75-foot
sections) and may be cut to length with a knife or fine
tooth hacksaw.
For each supply tubing run, estimate and cut the length
of tubing that will be needed between the plenum and
sound attenuating tube. At the open end of the supply
tubing a kwik-connect will be installed (see Figure 2.22).
First, push back the cover and the insulation exposing
approximately 4" of the inner core. Fold in any tails or
frays that may be present after cutting the supply tubing.
Second, hand compress the corrugations until they are
densely compacted 1-1/2" to 2" from the open end of the
supply tube. Third, thread kwik-connect into the inner
core until snug. Fourth, pull the insulation and cover for-
ward and tuck it into the deep groove on the back side of
the kwik-connect. Fifth, wrap the connection securely
with UL181 approved tape..
When finished, simply twist together (see Figure 2.24)
the kwik-connect on the sound attenuating tube, and
wrap the connection securely with tape.
After attaching the supply tubing to the sound attenuating
tube, bring the open end of the tubing to the plenum.
To cut a hole in the plenum, refer to duct installation
instructions supplied with fan coil unit. Sheet metal duct
requires a 2-1/16" hole.
Remove the hole cut-out from the plenum. Make sure
there is no “flap” left inside plenum that could block hole
during operation.
4" MINIMUM RADIUS
FIGURE 2.22: MINIMUM TUBING BEND
TUBINGROUTING
FIGURE 2.21: POSITIONING ROOM TERMINATOR
FIGURE 2.23: KWIK-CONNECT INSTA ATION
FIGURE 2.24: CONNECTING TUBING
Center the two spring clips on a line parallel to the
direction of the tubing routing from the room terminator
(see Figure 2.21). This is important since the weight
of the tubing will have a tendency to cause a part of the
terminator to pull away from the ceiling if the clips and
tubing do not run parallel.
Then tighten the screws (attached to the terminator) until
the terminator is snug against the ceiling or floor. Do
not overtighten. For installations with floors or ceilings
which are thicker than normal, longer toggle screws
or special mounting plates may be required.

16
PLENUM
GASKET
Place the plenum take-off gasket on the back side of the
plenum take-off and insert the assembly into the hole in
the plenum (see FIgure 2.25).
NOTICE: Gasket must be installed to seal plenum
take-off to prevent air leakage.
Orient the plenum take-off to match the curvature of the
plenum duct. Hand insert the four plenum take off
fasteners one at a time such that each clip reaches the
interior of the duct. Using the SpacePak pliers, snap the
fasteners into place until they lock in place (see Figure
2.26).
FIGURE 2.28: ORIFICE INSTA ATION
FIGURE 2.25: TAKE-OFF INSTA ATION
PLENUM
FASTENER
GASKET
PLENUM TAKE-OFF
GASKET
PLENUM TAKE-OFF
PLENUM
FASTENER
1. HAND INSERT FASTENER INTO PLENUM TAKE-OFF 2. WITH PLIERS, SNAP FASTENER INTO PLACE UNTIL IT LOCKS IN PLACE
FIGURE 2.26: P ENUM TAKE-OFF FASTENER INSTA ATION
NOTICE: All four fasteners must be installed to
assure air tight fitting between plenum take-off and
plenum.
In accordance with your calculations as to requirements
for balancing orifices, mount the orifice in the outlet of
the plenum take-off (see Figure 2.28), prior to attaching
the supply tubing.
Next, install a kwik-connect in the open end of the supply
tubing, using the same procedures as before, and twist
together kwik-connects on supply tubing and plenum
take-off. Wrap connection securely with tape.

17
Return Air Box & Duct Installation
Remove the return air grill from the return air box and
remove the air filter from the return air grill.
Insert the return box from below for ceiling installation
(or from the front for wall installations) and fasten with
four screws through holes provided on the long side of
the box. (see Figure 2.24).
Remove the grill and the filter from the grill frame. Insert
the frame into the box and mount in place with the
screws provided through a hole at each corner of the
frame. Finally, place the air filter into the frame and
replace the grill. Turn the latches a quarter turn to lock
the grille in place. Slide a clamp band (provided with
return air box) over one end of the return air duct. Place
that end over the elliptical flange on the fan coil unit (see
Figure 2.25). Move the clamp over the flange and tight-
en so the clamp holds the return air duct securely to the
flange.
Follow the same procedures to attach the return air duct
to the return air box (see Figure 2.25).
FIGURE 2.25: TYPICA C OSET/UTI ITY ROOM
INSTA ATION
ROOM
TERMINATOR
WINTER
SUPPLY
SHUT-OFF
FIGURE 2.27: WINTER SUPP Y SHUT-OFF
FIGURE 2.24:RETURN AIR BOX INSTA ATION
Direct Mount Filter Box
& Ductless Returns
Center filter box over the eliptical flange of fan coil unit
(see Figure 2.26). Mark the (4) hole locations on fan coil
unit and drill holes using 5/32" bit. Mount filter box to unit
using screws provided and insert air filter.
Winter Supply Shut-Off Installation
Simply insert winter supply shut-offs into the room
terminator openings (see Figure 2.27). Wrap the return
air filter in a plastic bag and reinstall it to block the return
air opening. Winter supply shut-offs prevent moisture
from collecting in ductwork during winter months. Be
sure to remove the plastic bag and all winter supply
shut-offs before operating the system
FIGURE 2.26: FI TER BOX INSTA ATION
AIR OUT
AIRIN

18
SECTION 3: START-UP & OPERATION
SEQUENCE OF OPERATION
When power is turned on and thermostat fan switch is
set to ON and the cooling indicator is set to OFF, the
indoor fan motor is energized in approximately 2 min-
utes. The outdoor unit is off.
When power is turned on and thermostat fan switch is
set to ON or AUTO and the cooling indicator to COOL
the indoor and outdoor units will start.
AUTO position on the thermostat will stop and start your
system when the temperature setting is satisfied. The
ON position on the thermostat will stop the outdoor unit
only when the temperature setting is satisfied and the
indoor unit will continue to run, recirculating indoor air.
The fan coil unit is equipped with a protective device
called an anti-frost control which will automatically stop
the outdoor unit (while the indoor unit continues to run) if
ice accumulates on the indoor unit evaporator coil
causing abnormal operating conditions. When the
accumulated ice has melted, the anti-frost control will
restart the outdoor unit.
The fan coil unit is equipped with primary float switch, and the
system will automatically shut down if the drain pan is full of water
(condensate) and not draining. The system requires service.
PRIOR TO START-UP
1. Check all electrical connections for tightness.
2. Check air filter has been installed in return air box or
filter box.
3. Remove all winter supply shut-offs and store them in a
safe place.
SYSTEM START-UP & ADJUSTMENTS
1. Place thermostat fan switch in ON position and cooling
indicator in OFF position. In about 2 minutes, indoor
unit blower will start.
2. Check blower operation for excess noise or vibration.
3. Check entire distribution system for leakage and apply
additional tape where necessary.
4. Measure/adjust blower voltage/speeds
a. Remove the control box cover located on the side
of the unit.
b. With the unit powered and operating from a
conventional thermostat, ensure there is no conditioning
call (Thermostat is satisfied) and switch the fan
control to “Manual” or “On” to create a G call.
NOTE: IF NO AIRF OW DURING W OR Y CA ,
POTENTIOMETER MAY BE IN “OFF” POSITION.
TURN CW TO ACHIEVE AIRF OW
c. Place the ground/neutral probe in the lower right hole
marked “COM” and the volt probe in the hole marked
“Flo0” (for fan only, G call) and measure DC volts between
0 and 5V. Adjust the potentiometer adjacent to the “Flo0”
to achieve the desired volt reading. Repeat for remaining
adjustments marked Flo1 through Flo4 as indicated on
the label inside the cover. (Refer to Figure 3)
d. To determine unit airflow, in CFM, measure the voltage
corresponding to the current conditioning call, and
measure the external static pressure in the plenum, at
least 18” from the unit or nearest transition point. Locate
the static pressure on the left side of the charts (Figure
3.2/3.3/3.4) and read across until you reach the curve
corresponding to the measured voltage. From the point
where this crosses, drop a line straight down to read the
airflow at the bottom of the chart. For system settings of
1.2" inch static pressure, refer to tables in Figures 3.21,
3.31 and 3.41.
e. To adjust airflow, locate the nearest system curve, and
follow parallel to this curve while adjusting the signal
voltage to achieve the desired airflow. If the static pressure
falls above or below the desired operating range for the
given airflow, then the air delivery system must be
adjusted. To lower static pressure, provide additional
outlets to the system, to raise the static pressure, install
restrictor orifices as described in the Installation and
Operations Manual.
f. Replace the speed control cover.
Flo0
Fan Only
Flo1
Cooling
Flo2
Heating
Flo3
Stage 2
Cooling
Flo4
Stage 2
Heating
FIGURE 3: SPEED CONTRO PANE
4
3
2
1
0

19
FIGURE 3.2
FIGURE 3.21
OPERATINGSETPOINTS
00.0.00.0
0
0.0
0.
0.0
0.5
0.0
0.5
1
0.0
0.5
1.
0.0
0.5
1.0
0.0
0.5
1.0
1
0.0
0.5
1.0
1.
0.0
0.5
1.0
1.5
0.0
0.5
1.0
1.5
2
0.0
0.5
1.0
1.5
2.
0.0
0.5
1.0
1.5
2.0
0.0
0.5
1.0
1.5
2.0
2
0.0
0.5
1.0
1.5
2.0
2.
0.0
0.5
1.0
1.5
2.0
2.5
0.0
0.5
1.0
1.5
2.0
2.5
2
0.0
0.5
1.0
1.5
2.0
2.5
20
0.0
0.5
1.0
1.5
2.0
2.5
200
0.0
0.5
1.0
1.5
2.0
2.5
200 2
0.0
0.5
1.0
1.5
2.0
2.5
200 25
0.0
0.5
1.0
1.5
2.0
2.5
200 250
0.0
0.5
1.0
1.5
2.0
2.5
200 250 3
0.0
0.5
1.0
1.5
2.0
2.5
200 250 30
0.0
0.5
1.0
1.5
2.0
2.5
200 250 300
0.0
0.5
1.0
1.5
2.0
2.5
200 250 300 3
0.0
0.5
1.0
1.5
2.0
2.5
200 250 300 35
0.0
0.5
1.0
1.5
2.0
2.5
200 250 300 350
0.0
0.5
1.0
1.5
2.0
2.5
200 250 300 350 4
0.0
0.5
1.0
1.5
2.0
2.5
200 250 300 350 40
0.0
0.5
1.0
1.5
2.0
2.5
200 250 300 350 400
0.0
0.5
1.0
1.5
2.0
2.5
200 250 300 350 400 4
0.0
0.5
1.0
1.5
2.0
2.5
200 250 300 350 400 45
0.0
0.5
1.0
1.5
2.0
2.5
200 250 300 350 400 450
0.0
0.5
1.0
1.5
2.0
2.5
200 250 300 350 400 450 5
0.0
0.5
1.0
1.5
2.0
2.5
200 250 300 350 400 450 50
0.0
0.5
1.0
1.5
2.0
2.5
200 250 300 350 400 450 500
0.0
0.5
1.0
1.5
2.0
2.5
200 250 300 350 400 450 500 5
0.0
0.5
1.0
1.5
2.0
2.5
200 250 300 350 400 450 500 55
0.0
0.5
1.0
1.5
2.0
2.5
200 250 300 350 400 450 500 550
0.0
0.5
1.0
1.5
2.0
2.5
200 250 300 350 400 450 500 550 6
0.0
0.5
1.0
1.5
2.0
2.5
200 250 300 350 400 450 500 550 60
0.0
0.5
1.0
1.5
2.0
2.5
200 250 300 350 400 450 500 550 600
0.0
0.5
1.0
1.5
2.0
2.5
200 250 300 350 400 450 500 550 600 6
0.0
0.5
1.0
1.5
2.0
2.5
200 250 300 350 400 450 500 550 600 65
0.0
0.5
1.0
1.5
2.0
2.5
200 250 300 350 400 450 500 550 600 650
0.0
0.5
1.0
1.5
2.0
2.5
200 250 300 350 400 450 500 550 600 650 7
0.0
0.5
1.0
1.5
2.0
2.5
200 250 300 350 400 450 500 550 600 650 70
0.0
0.5
1.0
1.5
2.0
2.5
200 250 300 350 400 450 500 550 600 650 700
0.0
0.5
1.0
1.5
2.0
2.5
200 250 300 350 400 450 500 550 600 650 700 7
0.0
0.5
1.0
1.5
2.0
2.5
200 250 300 350 400 450 500 550 600 650 700 75
0.0
0.5
1.0
1.5
2.0
2.5
200 250 300 350 400 450 500 550 600 650 700 750
0.0
0.5
1.0
1.5
2.0
2.5
200 250 300 350 400 450 500 550 600 650 700 750 8
0.0
0.5
1.0
1.5
2.0
2.5
200 250 300 350 400 450 500 550 600 650 700 750 80
0.0
0.5
1.0
1.5
2.0
2.5
200 250 300 350 400 450 500 550 600 650 700 750 800
0.0
0.5
1.0
1.5
2.0
2.5
200 250 300 350 400 450 500 550 600 650 700 750 800 8
0.0
0.5
1.0
1.5
2.0
2.5
200 250 300 350 400 450 500 550 600 650 700 750 800 85
0.0
0.5
1.0
1.5
2.0
2.5
200 250 300 350 400 450 500 550 600 650 700 750 800 850
0.0
0.5
1.0
1.5
2.0
2.5
200 250 300 350 400 450 500 550 600 650 700 750 800 850 9
0.0
0.5
1.0
1.5
2.0
2.5
200 250 300 350 400 450 500 550 600 650 700 750 800 850 90
0.0
0.5
1.0
1.5
2.0
2.5
200 250 300 350 400 450 500 550 600 650 700 750 800 850 900
0.0
0.5
1.0
1.5
2.0
2.5
200 250 300 350 400 450 500 550 600 650 700 750 800 850 900
S
0.0
0.5
1.0
1.5
2.0
2.5
200 250 300 350 400 450 500 550 600 650 700 750 800 850 900
St
0.0
0.5
1.0
1.5
2.0
2.5
200 250 300 350 400 450 500 550 600 650 700 750 800 850 900
Sta
0.0
0.5
1.0
1.5
2.0
2.5
200 250 300 350 400 450 500 550 600 650 700 750 800 850 900
Stat
0.0
0.5
1.0
1.5
2.0
2.5
200 250 300 350 400 450 500 550 600 650 700 750 800 850 900
Stati
0.0
0.5
1.0
1.5
2.0
2.5
200 250 300 350 400 450 500 550 600 650 700 750 800 850 900
Static
0.0
0.5
1.0
1.5
2.0
2.5
200 250 300 350 400 450 500 550 600 650 700 750 800 850 900
Static
0.0
0.5
1.0
1.5
2.0
2.5
200 250 300 350 400 450 500 550 600 650 700 750 800 850 900
StaticP
0.0
0.5
1.0
1.5
2.0
2.5
200 250 300 350 400 450 500 550 600 650 700 750 800 850 900
StaticP
0.0
0.5
1.0
1.5
2.0
2.5
200 250 300 350 400 450 500 550 600 650 700 750 800 850 900
StaticPi
0.0
0.5
1.0
1.5
2.0
2.5
200 250 300 350 400 450 500 550 600 650 700 750 800 850 900
StaticPin
0.0
0.5
1.0
1.5
2.0
2.5
200 250 300 350 400 450 500 550 600 650 700 750 800 850 900
StaticPin
0.0
0.5
1.0
1.5
2.0
2.5
200 250 300 350 400 450 500 550 600 650 700 750 800 850 900
StaticPinW
0.0
0.5
1.0
1.5
2.0
2.5
200 250 300 350 400 450 500 550 600 650 700 750 800 850 900
StaticPinWC
0.0
0.5
1.0
1.5
2.0
2.5
200 250 300 350 400 450 500 550 600 650 700 750 800 850 900
StaticPinWC
A
0.0
0.5
1.0
1.5
2.0
2.5
200 250 300 350 400 450 500 550 600 650 700 750 800 850 900
StaticPinWC
Ai
0.0
0.5
1.0
1.5
2.0
2.5
200 250 300 350 400 450 500 550 600 650 700 750 800 850 900
StaticPinWC
Air
0.0
0.5
1.0
1.5
2.0
2.5
200 250 300 350 400 450 500 550 600 650 700 750 800 850 900
StaticPinWC
Airf
0.0
0.5
1.0
1.5
2.0
2.5
200 250 300 350 400 450 500 550 600 650 700 750 800 850 900
StaticPinWC
Airfl
0.0
0.5
1.0
1.5
2.0
2.5
200 250 300 350 400 450 500 550 600 650 700 750 800 850 900
StaticPinWC
Airflo
0.0
0.5
1.0
1.5
2.0
2.5
200 250 300 350 400 450 500 550 600 650 700 750 800 850 900
StaticPinWC
Airflow
0.0
0.5
1.0
1.5
2.0
2.5
200 250 300 350 400 450 500 550 600 650 700 750 800 850 900
StaticPinWC
Airflow
0.0
0.5
1.0
1.5
2.0
2.5
200 250 300 350 400 450 500 550 600 650 700 750 800 850 900
StaticPinWC
Airflow C
0.0
0.5
1.0
1.5
2.0
2.5
200 250 300 350 400 450 500 550 600 650 700 750 800 850 900
StaticPinWC
Airflow CF
0.0
0.5
1.0
1.5
2.0
2.5
200 250 300 350 400 450 500 550 600 650 700 750 800 850 900
StaticPinWC
Airflow CFM
0.0
0.5
1.0
1.5
2.0
2.5
200 250 300 350 400 450 500 550 600 650 700 750 800 850 900
StaticPinWC
Airflow CFM
SpacePak XXX-2430JV
5.0VDC
4.0VDC
3.0VDC
2.5VDC
2.0VDC
1.7VDC
1.5VDC
1.3VDC
1.0VDC
System Curves
Nominal operating
point, 550 CFM at 1.2"
5.0V 4.5V 4.0V 3.5V 3.0V 2.5V 2.0V 1.5V 1.0V
2.2 530 390 250
2.0 766 652 550 351
1.8 828 740 598 530
1.6 870 717 690 500 250
1.5 819 762 575 385
1.4 825 680 475
1.2 750 600 260
1.0 845 700 475
0.8 780 540 270
0.6 865 630 400
Static P
"WC
CFM's @ Speed Control Setting (VDC) -2430JV

20
FIGURE 3.3
FIGURE 3.31
00.0.00.0
0
0.0
0.
0.0
0.5
0.0
0.5
1
0.0
0.5
1.
0.0
0.5
1.0
0.0
0.5
1.0
1
0.0
0.5
1.0
1.
0.0
0.5
1.0
1.5
0.0
0.5
1.0
1.5
2
0.0
0.5
1.0
1.5
2.
0.0
0.5
1.0
1.5
2.0
0.0
0.5
1.0
1.5
2.0
2
0.0
0.5
1.0
1.5
2.0
2.
0.0
0.5
1.0
1.5
2.0
2.5
0.0
0.5
1.0
1.5
2.0
2.5
2
0.0
0.5
1.0
1.5
2.0
2.5
20
0.0
0.5
1.0
1.5
2.0
2.5
200
0.0
0.5
1.0
1.5
2.0
2.5
200 3
0.0
0.5
1.0
1.5
2.0
2.5
200 30
0.0
0.5
1.0
1.5
2.0
2.5
200 300
0.0
0.5
1.0
1.5
2.0
2.5
200 300 4
0.0
0.5
1.0
1.5
2.0
2.5
200 300 40
0.0
0.5
1.0
1.5
2.0
2.5
200 300 400
0.0
0.5
1.0
1.5
2.0
2.5
200 300 400 5
0.0
0.5
1.0
1.5
2.0
2.5
200 300 400 50
0.0
0.5
1.0
1.5
2.0
2.5
200 300 400 500
0.0
0.5
1.0
1.5
2.0
2.5
200 300 400 500 6
0.0
0.5
1.0
1.5
2.0
2.5
200 300 400 500 60
0.0
0.5
1.0
1.5
2.0
2.5
200 300 400 500 600
0.0
0.5
1.0
1.5
2.0
2.5
200 300 400 500 600 7
0.0
0.5
1.0
1.5
2.0
2.5
200 300 400 500 600 70
0.0
0.5
1.0
1.5
2.0
2.5
200 300 400 500 600 700
0.0
0.5
1.0
1.5
2.0
2.5
200 300 400 500 600 700 8
0.0
0.5
1.0
1.5
2.0
2.5
200 300 400 500 600 700 80
0.0
0.5
1.0
1.5
2.0
2.5
200 300 400 500 600 700 800
0.0
0.5
1.0
1.5
2.0
2.5
200 300 400 500 600 700 800 9
0.0
0.5
1.0
1.5
2.0
2.5
200 300 400 500 600 700 800 90
0.0
0.5
1.0
1.5
2.0
2.5
200 300 400 500 600 700 800 900
0.0
0.5
1.0
1.5
2.0
2.5
200 300 400 500 600 700 800 900 1
0.0
0.5
1.0
1.5
2.0
2.5
200 300 400 500 600 700 800 900 10
0.0
0.5
1.0
1.5
2.0
2.5
200 300 400 500 600 700 800 900 100
0.0
0.5
1.0
1.5
2.0
2.5
200 300 400 500 600 700 800 900 1000
0.0
0.5
1.0
1.5
2.0
2.5
200 300 400 500 600 700 800 900 1000 1
0.0
0.5
1.0
1.5
2.0
2.5
200 300 400 500 600 700 800 900 1000 11
0.0
0.5
1.0
1.5
2.0
2.5
200 300 400 500 600 700 800 900 1000 110
0.0
0.5
1.0
1.5
2.0
2.5
200 300 400 500 600 700 800 900 1000 1100
0.0
0.5
1.0
1.5
2.0
2.5
200 300 400 500 600 700 800 900 1000 1100 1
0.0
0.5
1.0
1.5
2.0
2.5
200 300 400 500 600 700 800 900 1000 1100 12
0.0
0.5
1.0
1.5
2.0
2.5
200 300 400 500 600 700 800 900 1000 1100 120
0.0
0.5
1.0
1.5
2.0
2.5
200 300 400 500 600 700 800 900 1000 1100 1200
0.0
0.5
1.0
1.5
2.0
2.5
200 300 400 500 600 700 800 900 1000 1100 1200 1
0.0
0.5
1.0
1.5
2.0
2.5
200 300 400 500 600 700 800 900 1000 1100 1200 13
0.0
0.5
1.0
1.5
2.0
2.5
200 300 400 500 600 700 800 900 1000 1100 1200 130
0.0
0.5
1.0
1.5
2.0
2.5
200 300 400 500 600 700 800 900 1000 1100 1200 1300
0.0
0.5
1.0
1.5
2.0
2.5
200 300 400 500 600 700 800 900 1000 1100 1200 1300
S
0.0
0.5
1.0
1.5
2.0
2.5
200 300 400 500 600 700 800 900 1000 1100 1200 1300
St
0.0
0.5
1.0
1.5
2.0
2.5
200 300 400 500 600 700 800 900 1000 1100 1200 1300
Sta
0.0
0.5
1.0
1.5
2.0
2.5
200 300 400 500 600 700 800 900 1000 1100 1200 1300
Stat
0.0
0.5
1.0
1.5
2.0
2.5
200 300 400 500 600 700 800 900 1000 1100 1200 1300
Stati
0.0
0.5
1.0
1.5
2.0
2.5
200 300 400 500 600 700 800 900 1000 1100 1200 1300
Static
0.0
0.5
1.0
1.5
2.0
2.5
200 300 400 500 600 700 800 900 1000 1100 1200 1300
Static
0.0
0.5
1.0
1.5
2.0
2.5
200 300 400 500 600 700 800 900 1000 1100 1200 1300
StaticP
0.0
0.5
1.0
1.5
2.0
2.5
200 300 400 500 600 700 800 900 1000 1100 1200 1300
StaticP
0.0
0.5
1.0
1.5
2.0
2.5
200 300 400 500 600 700 800 900 1000 1100 1200 1300
StaticPi
0.0
0.5
1.0
1.5
2.0
2.5
200 300 400 500 600 700 800 900 1000 1100 1200 1300
StaticPin
0.0
0.5
1.0
1.5
2.0
2.5
200 300 400 500 600 700 800 900 1000 1100 1200 1300
StaticPin
0.0
0.5
1.0
1.5
2.0
2.5
200 300 400 500 600 700 800 900 1000 1100 1200 1300
StaticPinW
0.0
0.5
1.0
1.5
2.0
2.5
200 300 400 500 600 700 800 900 1000 1100 1200 1300
StaticPinWC
0.0
0.5
1.0
1.5
2.0
2.5
200 300 400 500 600 700 800 900 1000 1100 1200 1300
StaticPinWC
A
0.0
0.5
1.0
1.5
2.0
2.5
200 300 400 500 600 700 800 900 1000 1100 1200 1300
StaticPinWC
Ai
0.0
0.5
1.0
1.5
2.0
2.5
200 300 400 500 600 700 800 900 1000 1100 1200 1300
StaticPinWC
Air
0.0
0.5
1.0
1.5
2.0
2.5
200 300 400 500 600 700 800 900 1000 1100 1200 1300
StaticPinWC
Airf
0.0
0.5
1.0
1.5
2.0
2.5
200 300 400 500 600 700 800 900 1000 1100 1200 1300
StaticPinWC
Airfl
0.0
0.5
1.0
1.5
2.0
2.5
200 300 400 500 600 700 800 900 1000 1100 1200 1300
StaticPinWC
Airflo
0.0
0.5
1.0
1.5
2.0
2.5
200 300 400 500 600 700 800 900 1000 1100 1200 1300
StaticPinWC
Airflow
0.0
0.5
1.0
1.5
2.0
2.5
200 300 400 500 600 700 800 900 1000 1100 1200 1300
StaticPinWC
Airflow
0.0
0.5
1.0
1.5
2.0
2.5
200 300 400 500 600 700 800 900 1000 1100 1200 1300
StaticPinWC
Airflow C
0.0
0.5
1.0
1.5
2.0
2.5
200 300 400 500 600 700 800 900 1000 1100 1200 1300
StaticPinWC
Airflow CF
0.0
0.5
1.0
1.5
2.0
2.5
200 300 400 500 600 700 800 900 1000 1100 1200 1300
StaticPinWC
Airflow CFM
0.0
0.5
1.0
1.5
2.0
2.5
200 300 400 500 600 700 800 900 1000 1100 1200 1300
StaticPinWC
Airflow CFM
SpacePak XXX-3642JV
5.0VDC
4.0VDC
3.0VDC
2.5VDC
2.0VDC
1.7VDC
1.5VDC
1.3VDC
1.0VDC
System Curves
NNoNomNomiNominNominaNominalNominalNominal oNominal opNominal opeNominal operNominal operaNominal operatNominal operatiNominal operatinNominal operatingNominal operatingNominal operating pNominal operating poNominal operating poiNominal operating poinNominal operating pointNominal operating point,Nominal operating point,Nominal operating point, 8Nominal operating point, 85Nominal operating point, 850Nominal operating point, 850Nominal operating point, 850
C
Nominal operating point, 850
C F
Nominal operating point, 850
CFM
Nominal operating point, 850
CFM
Nominal operating point, 850
CFM a
Nominal operating point, 850
CFM at
Nominal operating point, 850
CFM at
Nominal operating point, 850
CFM at 1
Nominal operating point, 850
CFM at 1.
Nominal operating point, 850
CFM at 1.2
Nominal operating point, 850
CFM at 1.2"
Nominal operating point, 850
CFM at 1.2"
Nominal operating point, 850
CFM at 1.2" E
Nominal operating point, 850
CFM at 1.2" ES
Nominal operating point, 850
CFM at 1.2" ESP
Nominal operating point, 850
CFM at 1.2" ESP
Nominal operating point, 850
CFM at 1.2" ESP 2
Nominal operating point, 850
CFM at 1.2" ESP 2.
Nominal operating point, 850
CFM at 1.2" ESP 2.7
Nominal operating point, 850
CFM at 1.2" ESP 2.7V
Nominal operating point, 850
CFM at 1.2" ESP 2.7VD
Nominal operating point, 850
CFM at 1.2" ESP 2.7VDC
Nominal operating point, 850
CFM at 1.2" ESP 2.7VDC
Nominal operating point, 850
CFM at 1.2" ESP 2.7VDC
5.0V 4.5V 4.0V 3.5V 3.0V 2.5V 2.0V 1.5V 1.0V
2.2 650 460
2.0 860 735 610
1.8 1020 910 800 670 550
1.6 1135 1045 955 800 730 505
1.5 1190 1115 1040 908 800 595 400
1.4 1195 1075 1008 860 665 480
1.2 1200 1073 975 780 625 310
1.0 1180 1070 875 720 470
0.8 1160 960 810 580 330
0.6 1035 875 675 460
CFM's @ Speed Control Setting (VDC) -3642JV
Static P
"WC
This manual suits for next models
3
Table of contents
Other Space Pak Fan manuals
Popular Fan manuals by other brands

Linea 2000
Linea 2000 DOMO DO8142 Instruction booklet

Brandson Equipment
Brandson Equipment 303055 user manual
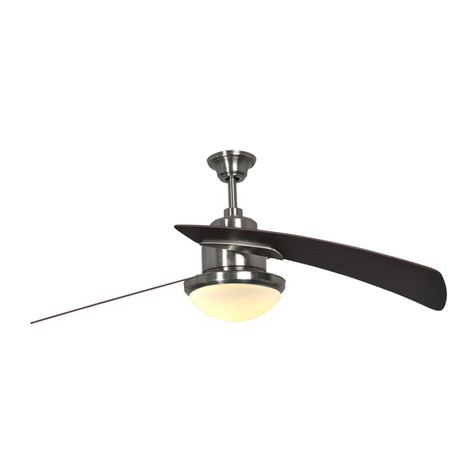
Harbor Breeze
Harbor Breeze Santa Ana LP8294LBN manual
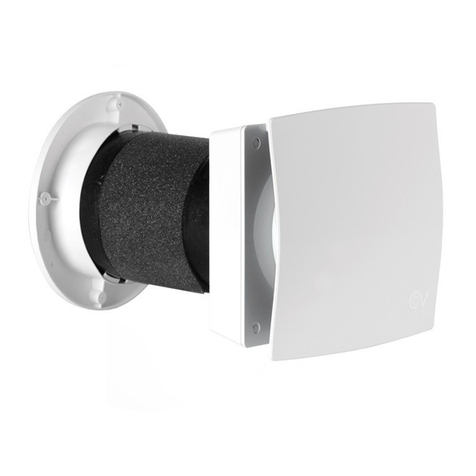
Vortice
Vortice VORT HRW 20 MONO Instruction booklet
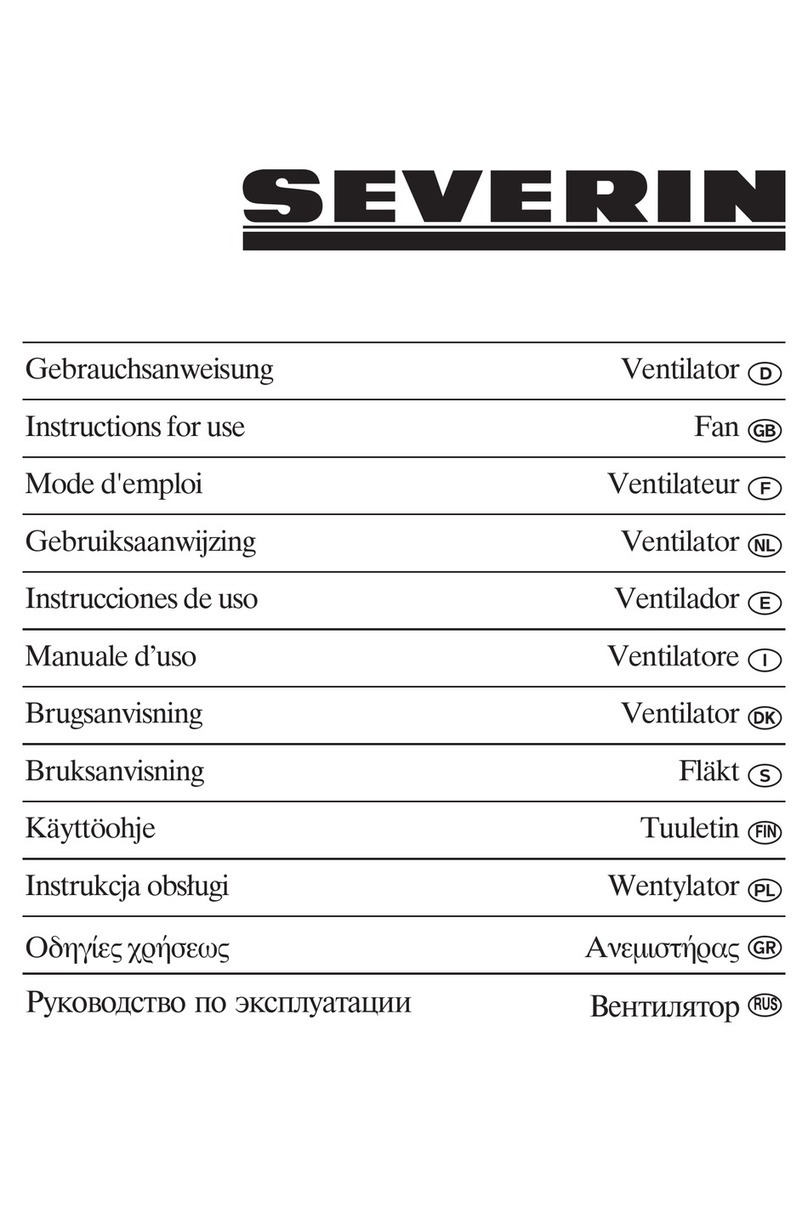
SEVERIN
SEVERIN VL 8630 - Instructions for use
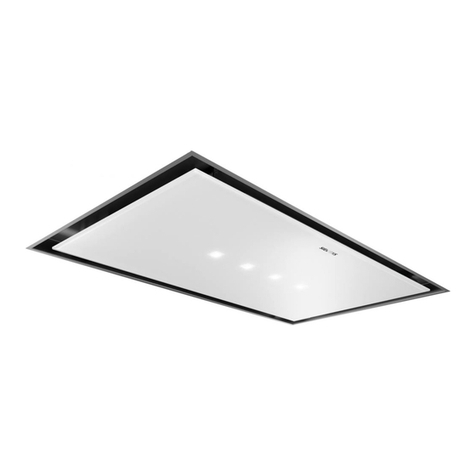
Siemens
Siemens LR96CBS20 User manual and assembly instructions