ST STEVAL-IHT001V1 User manual

August 2006 Rev 1 1/32
UM0277
User manual
Getting started with the
Cold Thermostat Kit based on AC switches and ST7LITE MCU
Introduction
The STEVAL-IHT001V1 Thermostat Kit (figure below) is designed to control a refrigerator or
a freezer. This thermostat kit enables the control of a single-phase induction motor, a light
bulb and a defrost resistor (or a fan) working on 230 VRMS 50/60 Hz mains voltage.
The board can operate in an ambient temperature range of 0 to 40 °C. The exact maximum
temperature depends on the power of the loads (Section 3.1: Load power).
The kit includes a Graphic User Interface (GUI) for sending commands to the ST7LITE39F2
Microcontroller or to access MCU information via the Serial Communication Interface (SCI).
This enables users to easily change MCU software parameters and acquire measurements
during appliance testing.
This document provides all the information needed to make the board work (how to connect
it, how it works). For specific information about modifying MCU parameters, please refer to
the “Help” section of the GUI software.
STEVAL-IHT001V1 Thermostat Kit
The main goals of this tool are:
●Evaluate full ST solution (microcontroller + AC switch) for cold thermostat applications
●Measure and save the appliance main parameters during operation (load status,
compressor operation duty cycle and running period, evaporator temperature)
●Check and analyze efficiency gains by reducing the Hysteresis threshold or adapting
the defrost resistor management
●Check the board immunity against fast transient voltages (without GUI connection).
www.st.com

Contents UM0277
2/32
Contents
1 Kit introduction . . . . . . . . . . . . . . . . . . . . . . . . . . . . . . . . . . . . . . . . . . . . . 4
1.1 Package contents . . . . . . . . . . . . . . . . . . . . . . . . . . . . . . . . . . . . . . . . . . . . 4
1.2 Board presentation . . . . . . . . . . . . . . . . . . . . . . . . . . . . . . . . . . . . . . . . . . . 5
2 Functional description . . . . . . . . . . . . . . . . . . . . . . . . . . . . . . . . . . . . . . . 6
2.1 Performances . . . . . . . . . . . . . . . . . . . . . . . . . . . . . . . . . . . . . . . . . . . . . . . 6
2.2 Ensured functions . . . . . . . . . . . . . . . . . . . . . . . . . . . . . . . . . . . . . . . . . . . . 6
2.2.1 Temperature control . . . . . . . . . . . . . . . . . . . . . . . . . . . . . . . . . . . . . . . . . 6
2.2.2 Compressor control . . . . . . . . . . . . . . . . . . . . . . . . . . . . . . . . . . . . . . . . . 7
2.2.3 Light bulb and buzzer operation control . . . . . . . . . . . . . . . . . . . . . . . . . . 7
2.2.4 Defrost resistor (or fan) control . . . . . . . . . . . . . . . . . . . . . . . . . . . . . . . . 7
2.3 Hardware features . . . . . . . . . . . . . . . . . . . . . . . . . . . . . . . . . . . . . . . . . . . 8
2.3.1 ACS and ACST devices . . . . . . . . . . . . . . . . . . . . . . . . . . . . . . . . . . . . . . 8
2.3.2 ST7LITE39F2 microcontroller . . . . . . . . . . . . . . . . . . . . . . . . . . . . . . . . . 9
2.3.3 Capacitive power supply . . . . . . . . . . . . . . . . . . . . . . . . . . . . . . . . . . . . . 9
2.4 Graphic user interface (GUI) . . . . . . . . . . . . . . . . . . . . . . . . . . . . . . . . . . 10
3 Getting started . . . . . . . . . . . . . . . . . . . . . . . . . . . . . . . . . . . . . . . . . . . . . 11
3.1 Load power . . . . . . . . . . . . . . . . . . . . . . . . . . . . . . . . . . . . . . . . . . . . . . . . 11
3.2 Measure points . . . . . . . . . . . . . . . . . . . . . . . . . . . . . . . . . . . . . . . . . . . . . 11
3.3 Pulse control . . . . . . . . . . . . . . . . . . . . . . . . . . . . . . . . . . . . . . . . . . . . . . . 12
3.4 Getting started . . . . . . . . . . . . . . . . . . . . . . . . . . . . . . . . . . . . . . . . . . . . . 13
3.4.1 Using the GUI software . . . . . . . . . . . . . . . . . . . . . . . . . . . . . . . . . . . . . 14
3.5 GUI windows description . . . . . . . . . . . . . . . . . . . . . . . . . . . . . . . . . . . . . 16
3.5.1 Temperature control . . . . . . . . . . . . . . . . . . . . . . . . . . . . . . . . . . . . . . . . 16
3.5.2 Timing control . . . . . . . . . . . . . . . . . . . . . . . . . . . . . . . . . . . . . . . . . . . . 17
3.5.3 Force debug . . . . . . . . . . . . . . . . . . . . . . . . . . . . . . . . . . . . . . . . . . . . . . 18
3.5.4 Parameter measurements . . . . . . . . . . . . . . . . . . . . . . . . . . . . . . . . . . . 19
4 Conclusion . . . . . . . . . . . . . . . . . . . . . . . . . . . . . . . . . . . . . . . . . . . . . . . . 20
Appendix A Thermal sensor linearization . . . . . . . . . . . . . . . . . . . . . . . . . . . . . . 21
Appendix B Wiring connections . . . . . . . . . . . . . . . . . . . . . . . . . . . . . . . . . . . . . . 23
Appendix C STEVAL-IHT001V1 thermostat kit. . . . . . . . . . . . . . . . . . . . . . . . . . . 24

UM0277 Contents
3/32
Appendix D Bill of materials . . . . . . . . . . . . . . . . . . . . . . . . . . . . . . . . . . . . . . . . . 25
Appendix E Procedure to apply IEC 61000-4-4 bursts test. . . . . . . . . . . . . . . . . 28
Appendix F PC interface parameters description . . . . . . . . . . . . . . . . . . . . . . . . 29
Appendix G Capacitor value according to country . . . . . . . . . . . . . . . . . . . . . . . 30
Revision history . . . . . . . . . . . . . . . . . . . . . . . . . . . . . . . . . . . . . . . . . . . . . . . . . . . . 31

Kit introduction UM0277
4/32
1 Kit introduction
1.1 Package contents
This package (Figure 1) includes the following items:
●A thermostat board (ref.: STEVAL-IHT001V1)
●A M2020 5k NTC thermistor from EPCOS (ref.: M2020/5k/A17)
●A CD-ROM, including products presentations and data-sheets, user manual,
Application Notes and the GUI software.
●“Getting Started” User Manual (this document)
●The insulated PC interface board (ref.: MC/UNI/0001.01 PC-INTERFACE ver.1.1)
●A 230VAC/9VDC insulated power supply for the SCI interface board
●One RS-232 Interface cable
●One SCI Interface cable
Figure 1. Package contents
RS232 Interface
cable
230VAC/9VDC
insulated power
supply
M2020 5k NTC
thermostat board SCI Interface
cable
PC insulated
interface board
RS232 Interface
cable
230VAC/9VDC
insulated power
supply
M2020 5k NTC
thermostat board SCI Interface
cable
PC insulated
interface board

UM0277 Kit introduction
5/32
1.2 Board presentation
Figure 2 shows the STEVAL-IHT001V1 board and the main components used on this board.
Figure 2. Power board (top view)
This board mainly embeds (refer to Appendix C for the complete schematic):
●A capacitor power supply. The average output current of the capacitor power supply is
approximately 25 mA with he embedded 1µF C3 capacitor (for a 230V-50Hz Line RMS
voltage)
●A ST7LITE39F2 MCU
●AC Switches: one ACS102-6TA, one ACS110-7SB2 and one ACST6-7ST to control
respectively a light bulb, a defrost resistor or fan, and a compressor
●ON/OFF LED. This LED switches ON when the board is powered
●Temperature order visualization. Three LEDs indicate the temperature order using
three different settings: low, medium and high
●BP1 Push Button, to change the temperature order setting
●Transducer (or buzzer) to warn the user if the door is opened for an extended time
●SCI connector, for communication between the board and a computer (using the GUI
software)
●An In-Dart connector, to load the firmware in the MCU
Warning: To avoid electrical shock through the computer, if the In-Dart
connector is used to connect a computer, the STEVAL-
IHT001V1 board must be plugged into an insulated mains
plug.
Temperature order
visualization
BP1 Push But ton
(temperature selection)
J1 connector (AC mai ns)
ON/OFF
Led
SCI connector Transducer
ACS / ACST
Power
suppl y
capacitor
ST7Lit e
MCU
Temperature order
visualization
BP1 Push But ton
(temperature selection)
J1 connector (AC mai ns)
ON/OFF
Led
SCI connector Transducer
ACS / ACST
Power
suppl y
capacitor
ST7Lit e
MCU
J1 connector (AC mai ns)
ON/OFF
Led
SCI connector Transducer
ACS / ACST
Power
suppl y
capacitor
ST7Lit e
MCU

Functional description UM0277
6/32
2 Functional description
2.1 Performances
This board meets the following requirements:
●Medium-end appliances: this thermostat board can control the loads traditionally used
in medium-end cold appliances (compressor, light, defrost resistor).
●Electromagnetic Compatibility: the board is able to withstand bursts of more than 2.3kV
during IEC61000-4-4 standard tests without any operational problems (and up to 4.5kV
without any damage). Surge tests have also been performed (IEC61000-4-5 standard):
2 kV bursts can be applied without any damage for the semiconductors.
●Safety standards have also been taken into account. A 2-mm creepage is ensured
between all high voltage parts and low voltage parts (to achieve the functional
insulation level). The (NTC) thermistor is a class II sensor, and can be put on non-
earthed accessible and conductive parts.
2.2 Ensured functions
2.2.1 Temperature control
The thermal sensor used is an NTC thermal resistor (thermistor) from EPCOS (M2020 5 k
2%). It should be placed on the evaporator of the fridge or the freezer. The controlled
evaporator temperature range should be between -20 and 5 °C. The range can be modified
by changing the value of the resistor placed in series with the NTC (refer to Appendix A).
The NTC resistance value decreases, following an exponential variation, when the
temperature increases. Then, to get back the temperature data, the MCU could use a
numerical table. In the STEVAL-IHT001V1 board, a simple resistor has been added in
series with the NTC in order to linearize its thermal response (refer to Appendix A). Two
advantages come from this choice:
●Memory area savings
●Easy way to measure the temperature.
Temperature regulation is achieved by Hysteresis control (see Figure 3).
Figure 3. Hysteresis law

UM0277 Functional description
7/32
The linear temperature information is then simply compared to the temperature order.
TEMP1 is the upper limit of the Hysteresis cycle. It is equal to the temperature order plus a
threshold value (Temperature Hysteresis divided by 2). TEMP2 is equal to the same
temperature order minus this threshold. The compressor is switched on if the detected
temperature is above TEMP1, and switched off when this temperature becomes lower than
TEMP2.
The temperature order can be set to low, medium or high levels using the GUI software or
using push button PB1 on the board. Moreover, the Hysteresis value can only be changed
using the GUI software. For more information, see Section 3.5.1: Temperature control.
2.2.2 Compressor control
An ACST6-7ST AC switch (refer to mark Q1 in Appendix C) is used to turn on and off the
compressor according to the evaporator temperature detected by the NTC thermistor. Note
that such compressor motors usually present an auxiliary winding that only works during the
first seconds of operation in order to apply a higher torque at start-up. A PTC thermal
resistor is used to switch off this winding after start-up. In the STEVAL-IHT001V1 thermostat
kit, this PTC is not replaced by a TRIAC as proposed on our previous THERM01EVAL kit
(refer to AN1354).
2.2.3 Light bulb and buzzer operation control
A light bulb is driven by the ACS102-6TA AC switch (refer to mark Q3 in Appendix C). This
device is ON or OFF when the “Door” switch (J12) is opened or closed respectively. Instead
of using the switch placed on the board (J12), one can connect an external switch using the
“Door” connector (J13).
Note that if the fridge door or the “Door switch” is in “open” position more than one minute,
the buzzer will ring and the LEDs will flash. The buzzer can be stopped by pressing the
“temp selection” button or using the GUI software (refer to the Help menu of the GUI). When
the door is open, the temperature order can only be changed using the GUI software.
Note that a resistor (R1) has been added in series with ACS102-6TA AC switch (Q3).
Indeed, at the end of the lamp lifetime, the filament breaks and the overall filament can be
short-circuited by the flashover resulting in a load current that is no longer limited. This
current can exceed the i².t capability of the ACS and destroy it (refer to AN1172). To avoid
destroying the ACS102 switch at each lamp flashover, a power resistor is added in series
with the light. This resistor (refer to the Appendix C) is rated in order to limit the ACS current
to its ITSM value (10 A for a 10 ms half sinus conduction). In this case, a 33Ω1/2 W resistor
is sufficient.
2.2.4 Defrost resistor (or fan) control
The defrost resistor is driven by the ACS110-7SB2 AC switch (refer to mark Q2 in Appendix
C). This device is ON following the “Defrost activation delay” parameter time defined using
the GUI software. This time is compared to the sum of Q1 TRIAC ON times. When this sum
is higher than the “Defrost activation delay”, Q2 TRIAC is switched ON (Figure 4).
But the software (MCU) waits for the next compressor conduction cycle before turning on
the Defrost. Then, the Defrost is switched on when the evaporator temperature is the higher
value. This helps reduce power consumption and improve appliance efficiency. Switch Q2
remains on during the “Defrost duration” parameter defined on the GUI software.

Functional description UM0277
8/32
Figure 4. Defrost activation principle
Note: The ACS110-7SB2 switch can drive a fan instead of a defrost resistor in order to move the
air around the coils inside the refrigerator. This fan helps to increase the cooling efficiency,
and also speeds up the defrost process.
2.3 Hardware features
2.3.1 ACS and ACST devices
The STEVAL-IHT001V1 board embeds one ACS102-6TA, one ACS110-7SB2 and one
ACST6-7ST switches. The datasheet of these devices can be found in our web site (go to
www.st.com/thyristors). Ta b le 1 sums up the main differences between ACS and ACST
switches and traditional TRIACs.
Sum of Compressor ON times > DEFROST
ACTIVATION DELAY
ÖDefrost enabled
TEMP1
TEMP2
DEFROST
Compressor
Evaporator temperature evolution
∆t
t
t
t
TEMP1
TEMP2
DEFROST
Compressor
Evaporator temperature evolution
∆t
t
t
t
Evaporator temperature > TEMP1
ÖDefrost turn-on
Aft er DEFROST DURATI ON (∆t)
ÖDefrost turn-off
ÖCompressor turn-on
Table 1. Differences between ACS/ACST and TRIACs
Device 1A TRIAC ACS102 1A TRIAC ACS110 6A TRIAC ACST6
Igt (mA) 5 5 10 10 10 10
Overvoltage Protection No Yes No Yes No Yes
(dV/dt) 20 V/µs 300 V/µs 50 V/µs 500 V/µs 100 V/µs 200 V/µs
(dI/dt) at turn-on 10 A/µs 20 A/µs 20 A/µs 50 A/µs 20 A/µs 100 A/µs

UM0277 Functional description
9/32
2.3.2 ST7LITE39F2 microcontroller
The MCU used in the thermostat kit is the ST7LITE39F2. It belongs to the ST7LITE39F2
MCU family. It embeds a large number of features at the minimum cost. The peripheral
hardware requirements are then reduced to the minimum:
●No crystal oscillator or external resonator is used. Indeed, the internal RC-oscillator of
the ST7LITE39F2 is used to generate the clock.
●No external RESET circuit is used, due to the internal circuit of the ST7LITE39F2.
In case of MCU firmware change, four options have to be set:
●Software watchdog activation
●RC oscillator selection
●PLL disabled
●Low Voltage Detection selection
2.3.3 Capacitive power supply
To reduce the board price as much as possible, a capacitive power supply is used on the
board. The maximum average current sunk by the board is about 30mA for 4ms gate current
pulse widths (see Ta ble 2 ). In this case, a 1µF C3 capacitor value should be used in order
for the board to work correctly under typical application conditions (nominal capacitor value,
230V RMS line voltage).
For higher or lower currents, the C3 capacitor can be changed. Tabl e 3 lists the maximum
allowed average current versus the different C3 capacitor values for typical application
conditions (nominal capacitor value, 230 VRMS line voltage) and worst application case
(nominal C3 capacitor value -10%, 198 VRMS line voltage), for a 50Hz mains frequency.
For more information about the design of the capacitive power supply please refer to
Application Note AN1476.
Table 2. Maximum average current sunk by the board
Devices Average current
consumption Comments
MCU 2.5mA Maximum supply current in Run Mode.
fCPU = 1MHz and VDD = 5.5V
LEDs 2.7mA
LEDs switch ON/OFF alternatively on each AC mains
polarity in order to reduce the current consumption.
VF= 1.6V @ IF= 4mA, VDD_Max = 5.5V and
R9= R10 = R11 = 750Ohms±1%
Gate average
current necessary
to control AC
switches
21mA
Switches Q1 (Compressor) and Q2 (Defrost) cannot be
switched ON at the same time. The gate average current is
only defined according to the Q2 (Defrost) and Q3 (Light
Bulb) gate current.
VDD_Max = 5.5V, RDSON_MCU = 25Ω, R4= 130Ω±5%,
R5= 390Ω±5% and 4ms gate currents pulses widths
Others (Push
Button, NTC
supply, Buzzer)
4.3mA
VDD_Max = 5.5V, RNTC@0°C = 16Ω, R14 = 10kΩ±5% and
R15 = 200Ω±5%
(IBuzzer supply current = 4mA)
Total 30.5mA

Functional description UM0277
10/32
In order to reduce the surge current, a R6 resistor is used in series with the C3 capacitor.
The power dissipation of this resistor is limited to ½ Watt. In this case, with a 30 mA output
DC average current, a 47Ωresistor value can be used on the board for typical application
conditions (100/230 VRMS line voltage and 50/60 Hz mains frequency).
Appendix G defines, in typical application conditions (nominal capacitor value, nominal RMS
line voltage), the C3 capacitor value for a 30mA output DC current versus different AC mains
and frequency values used in different countries. Moreover, the typical and minimal (nominal
capacitor value -10%, minimum RMS line voltage) output DC current capabilities are given
for information.
One particularity of the STEVAL-ITH001V1 board power supply is to be a “negative” one.
Indeed, the VDD terminal is connected to Neutral. This means that the GND voltage is 5V
below Neutral. Such a connection is mandatory for driving ACS devices. Indeed, ACSs can
only be triggered by a negative current (i.e. sourced from the gate).
2.4 Graphic user interface (GUI)
A Graphic User Interface (GUI) is provided to set ST7LITE39F2 Microcontroller parameters
and to access MCU information through the Serial Communication Interface (SCI). The GUI
provides the following features (refer to the “Help” menu of the GUI software for more
information):
●Sliding buttons to change MCU parameters:
– temperature hysteresis
– evaporator temperature order
– gate current pulse widths and delays
– time before defrost activation and defrost duration
– ZVS delay (synchronization of MCU commands with the mains voltage)
●Virtual graduated potentiometer to set the evaporator temperature between low,
medium or high levels
●Virtual switch to force the loads to ON or OFF states (Light, Defrost, Compressor) for
easier board validation
●Measurement and storage of several parameters during operation (duty cycle and
running period of the compressor, evaporator temperature evolution, mains frequency
and loads status)
Table 3. Maximum output DC average currents
C3
capacitor
Max. output DC current for typical
application conditions
Max. output DC current for worst
application case
220nF 7.1mA 5.5mA
330nF 10.7mA 8.3mA
470nF 15.2mA 11.8mA
680nF 22.1mA 17.1mA
1µF 32.5mA 25.2mA
1.5µF 48.8mA 37.8mA

UM0277 Getting started
11/32
3 Getting started
3.1 Load power
Initially, there is no heat sink mounted on the TO220-AB of the ACST6-7ST device. In this
case, Figure 2.1 of their datasheet shows that the maximum permanent allowed current is
1.5 A RMS, for an ambient temperature lower than 40 °C. If the ACST6-7ST must sink a
higher current, or works at a higher temperature, a heat sink can be added. Also refer to
AN1354 for more information on single-phase compressor control.
The ACS102-6TA, in a TO-92 package, can withstand a 0.2 A RMS permanent current up to
an ambient temperature of 90 °C. The ACS102-6TA can drive the common light bulbs found
in Fridge or Freezer without any problem. Indeed, a 25 W bulb will always sink a current
lower than 150 mA. The ACS110-7SB2, in DIL-8 package, can withstand a 1 A RMS
permanent current up to an ambient temperature of 90 °C. In this case, the ACS102-6TA
can drive a maximum 200W defrost resistor. Moreover, this AC switch can drive a fan (with a
RMS current lower than 1 A) instead of a defrost resistor without any additional snubber.
3.2 Measure points
Figure 5 shows the GND map and where the test points are placed on the board. Ta b l e 4
defines the measurement points.
Figure 5. Measurement points (top layer view)

Getting started UM0277
12/32
3.3 Pulse control
All loads are controlled in full cycle mode by a pulsed gate current. The MCU senses both
the mains rising and falling edges to synchronize the gate pulse with the mains supply. Their
delays and widths can be adjusted using the GUI from 0 to 4 ms in order to ensure a correct
control of loads (especially in case of different phase shift for the compressor than the
default value: 0.5 to 1.5 ms). Figure 6 shows the different times useful to understand when
the gate current pulses are applied for the three AC switches (Q1, Q2 and Q3):
●T1 is the mains voltage / compressor current phase shift. It helps to apply the gate
current pulse just when the Q1 current reaches zero, in order to control the compressor
in full cycle mode. Rq: a higher delay could be applied to test the compressor in phase
angle mode.
●T3 is the gate current pulse width for switch Q1 (compressor)
●T2 is the gate current pulse width for switches Q2 and Q3 (light bulb and defrost
resistor)
Figure 6. Timing definition for gate current pulses
Note: The gate currents are negative (i.e. they are sunk from the gates).
Table 4. Measurement points
Footprint Name Description
LLine
NNeutral
VDD +5V power supply (also connected to ACS/ACST cathodes)
GND GND power supply
ZVS Zero Voltage Signal at MCU Input
NTC- NTC value at MCU Input
RUN Gate control of the ACST6 (compressor) at MCU Output
LIGHT Gate control of the ACS102 (light bulb) at MCU Output
DEFROST Gate control of the ACS110 (Defrost) at MCU Output
Gate current (Light bulb / Defrost or Fan)
AC Mains
Gate current (Compressor)
T2
T1 T3
T2
t (s)
t (s)
t (s)
T3
T1
T2
II
COMPRESSOR
Gate current (Light bulb / Defrost or Fan)
AC Mains
Gate current (Compressor)
T2
T1 T3
T2
t (s)
t (s)
t (s)
T3
T1
T2
Gate current (Light bulb / Defrost or Fan)
AC Mains
Gate current (Compressor)
T2
T1 T3
T2
t (s)
t (s)
t (s)
T3
T1
T2
II
COMPRESSOR
Gate current (Light bulb / Defrost or Fan)
AC Mains
Gate current (Compressor)
T2
T1 T3
T2
t (s)
t (s)
t (s)
T3
T1
T2

UM0277 Getting started
13/32
3.4 Getting started
Warning: The Kit is not electrically isolated from the AC input. The MCU
is directly linked to the mains voltage. No insulation is
ensured between the accessible parts and the high voltage.
The STEVAL-IHT001V1 Kit must be used with care and only
by persons qualified for working with electricity at mains
voltage levels. All measurement equipment must be isolated
from the mains before powering the board.
When using an oscilloscope with the Kit, it is safer to isolate
it from the AC line. This prevents a shock from occurring as a
result of touching any SINGLE point in the circuit, but does
NOT prevent shocks when touching TWO or MORE points in
the circuit.
To operate the STEVA-LIHT001V1 board correctly, use the following procedure:
●Connect the NTC thermistor to the “NTC” connector on the thermostat board.
●Connect the DOOR switch (if you use an external door switch) to the “Door” connector
on the thermostat board
●Push the board “Door” switch to the “Close” position in order to allow “temperature
selection” push-button operation
●Connect the loads on the thermostat board:
– Compressor to “MOTOR” connector
– Defrost resistor to “DEFROST” connector
– Light bulb to “LIGHT” connector
●In case of control with a computer (using the GUI), please go to Section 2.3.3:
Capacitive power supply).
●Apply the mains wire to the “MAINS” connector. Plug this wire to the mains voltage.
●After a few seconds:
– The “ON/OFF” green LED must light ON
– The “medium” red LED must light ON
– The compressor switches ON if the sensed temperature is above the temperature
order (should be the case if the NTC thermistor is at ambient temperature).
– The Light Bulb is switched ON if the DOOR switch is on “open” position.
●Troubleshooting:
– If no LED is ON: replace the fuse.
– If LEDs seem OK, unplug the board from the mains. Discharge the VDD supply
with a short-circuit between VDD and GND. Plug back the board to the mains.
Note: The temperature order can be changed using the BP1 push button on the thermostat board.
Each time the BP1 push button is pressed, the red LEDs light on alternatively.
Note: If the “Door” Switch is in “Open” position or if the fridge door is opened, the temperature
order cannot be changed from the thermostat board (only by using the GUI software).

Getting started UM0277
14/32
3.4.1 Using the GUI software
In order to use the GUI of our STEVAL-IHT001V1 kit, a recent version of Windows®, such
as Windows 98, Windows 2000 or Windows XP must be installed on your computer. The
version of the Windows OS installed on your PC may be checked by clicking on the
“System” icon on the Control Panel.
To install the PC software (GUI) tool:
●Put the companion CDROM into the PC.
●Browse the CDROM directory to locate the GUI setup executable.
●Double-click on the GUI setup executable file.
●Follow the instructions as they appear on the screen.
Figure 7 explains how to connect the different STEVAL-IHT001V1 kit boards and the
computer.
Figure 7. STEVAL-IHT001V1 thermostat kit connections
An insulated interface is required in order to control the different parameters of the fridge
(Figure 8). The SCI insulated interface board is used in order to insulate the PC from the
STEVAL-IHT001V1 Kit Board and converts the RS-232 levels (about +10 and -10V) to TTL
voltage (0 and +5V) used by MCU, and vice versa, without requiring anything else than a
+9V power supply.
Computer
GUI
RS232 Interface
cable
Male DB9 Female DB9
PC interface board
STEVAL-I HT001V1
temperat ure
t
Power supply connector
230V – 9V
SCI Interface
cable
SCI
SCI

UM0277 Getting started
15/32
Figure 8. Interface board
Perform the following start-up procedure for the GUI:
1. Connect the insulated PC interface board to the PC via the RS232 Interface cable and
to the thermostat board via the SCI Interface wire.
2. Connect the 230V/9V insulated power supply to the SCI interface board. First check
that the 230V/9V insulated power supply is correctly set: the Volt switch to the “9V”
position and the Polarity switch to the “Positive” position (Figure 9).
3. In case of a problem, ensure that the “selected Serial Communication Port number”
(COM1 or COM2) in the options dialog box is correct.
4. In order to enable communication between the GUI software and the thermostat board,
it is necessary to push the “connected” button (“Connected” LED switch ON).
Note: Refer to the “Help” menu of the GUI software for more information.

Getting started UM0277
16/32
Figure 9. 230V/9V insulated power supply configuration
3.5 GUI windows description
3.5.1 Temperature control
Use the “Thermostat Order” switch position on the GUI (Figure 10) or the “Temp Selector”
push button on the board to select the correct temperature order. Note:
●If “Thermostat order” or “LED temperature” = High, then the Evaporator Temperature
Order is “Evaporator Temperature Order 1".
●If “Thermostat order” or “LED temperature” = Medium, then the Evaporator
Temperature Order is “Evaporator Temperature Order 2".
●If “Thermostat order” or “LED temperature” = Low, then the Evaporator Temperature
Order is “Evaporator Temperature Order 3".
The value of the three temperature orders must be set according to the appliance and the
desired cabinet temperature for each operation point (Low, Medium or High).

UM0277 Getting started
17/32
Figure 10. Temperature control tab
3.5.2 Timing control
The Timing Control tab (Figure 11) controls the gate current width for the TRIACs, the delay
to switch ON the TRIACs Q1 (for compressor), the ZVS delay, the delay to activate defrost
and the defrost duration. Note that the initial parameters are given in Appendix F. These
parameters are sent and received by clicking on “Set” or “Get” buttons, respectively.
Figure 11. Timing control tab
The ZVS delay is the delay between the AC mains zero voltage and the detection of this
zero voltage by MCU in order to synchronize the MCU orders with the AC mains voltage.
The MCU uses Zero Voltage Crossing (ZVC) events to synchronize the TRIACs' gate
current pulses. The LINE voltage is connected to the input pin through two resistors (R7 and
R8). An interruption will then occur at each ZVC event. As soon as the ZVC is detected, the
AUTO-RELOAD Timer is started and a routine is launched to define the PORT A
configuration. The required time introduces then a delay from the ZVS. The maximum delay

Getting started UM0277
18/32
measured to switch ON the TRIACs which controls the Light Bulb and the Defrost resistor is
approximately 130µs for the AC mains negative cycle (230 VRMS 50 Hz line). The maximum
delay measured to switch ON the compressor is approximately 170µs for the AC mains
negative cycle (see Figure 12).
Figure 12. Gate current pulses
3.5.3 Force debug
The Force Debug tab is used to force the AC loads state regardless of the control state
defined by the MCU for easier board validation (Figure 13). In order to control these AC
Loads, it is necessary to click the “Debug Mode” button. In this case, the green lights of the
AC Loads buttons are ON, if the associated loads are also ON, otherwise:
●Clicking the “Compressor” button will turn on Q1, and then the compressor is running.
●Clicking the “Bulb” button will turn on Q2, and then the light bulb is lit.
●Clicking the “Defrost” button will turn on Q3, and then the defrost resistor is heating.
Note: 1 The Defrost and Compressor cannot be switched ON at the same time. Setting Defrost
resets Compressor, and vice-versa.
2 In order to return to “Normal” mode, click the “Debug Mode” button. In this case, all the
green lights turn off.

UM0277 Getting started
19/32
Figure 13. Force debug tab
3.5.4 Parameter measurements
The GUI can detect and display all the various parameters of the MCU, such as the
temperature order, the evaporator temperature, the AC load states, the compressor cycle
information (running period and duty cycle) and the Mains frequency. For more information,
refer to the “Help” menu of the GUI software.
To enable data acquisition, press the “Acquisition” button. If the acquisition is successful
(MCU firmware parameters and measurements obtained), the “ACQUISITION” LED turns
green. If the “ACQUISITION” LED remains OFF, the acquisition function is disabled. If red, a
samples acquisition error occurred.

Conclusion UM0277
20/32
4 Conclusion
This document will help cold-appliance designers to use our STEVAL-IHT001V1 thermostat
kit to:
●Check the immunity of this ST solution
●Easily check the efficiency gains by hysteresis threshold reduction
●Define the better management of the defrost cycles to improve the overall efficiency
●Adapt the software and hardware for other dedicated designs (different compressors,
potentiometer control, added loads, etc.)
Table of contents
Popular Thermostat manuals by other brands
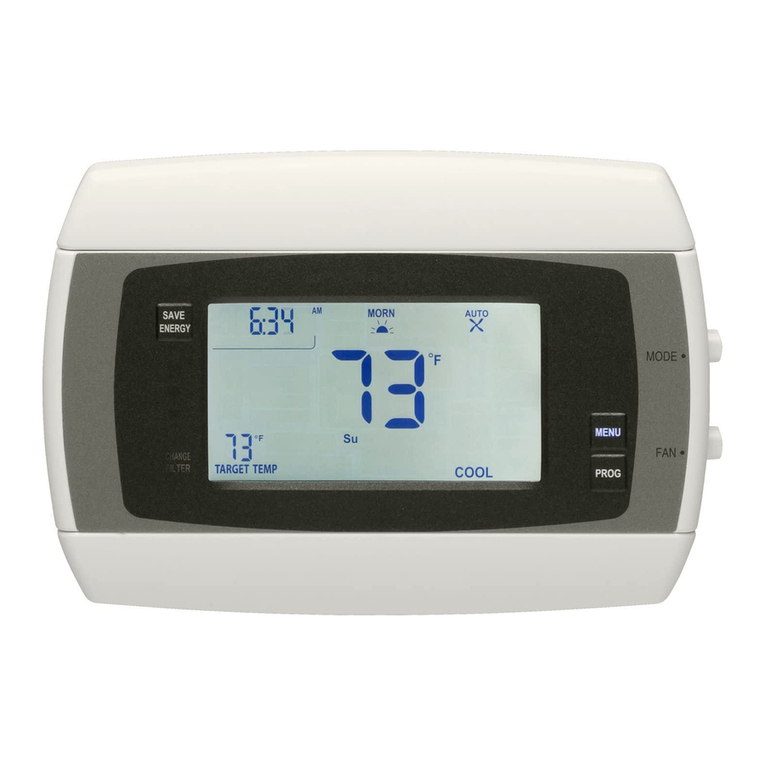
Radio Thermostat
Radio Thermostat CT30 install guide
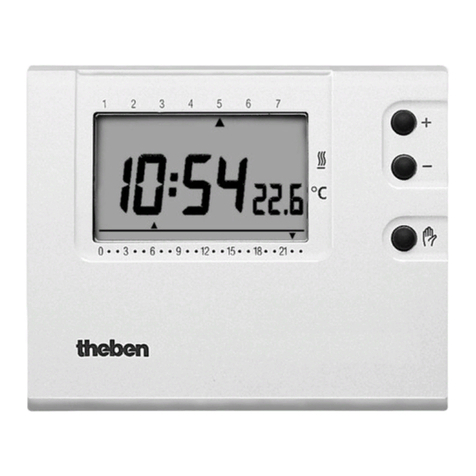
Theben
Theben RAMSES 797 B operating instructions
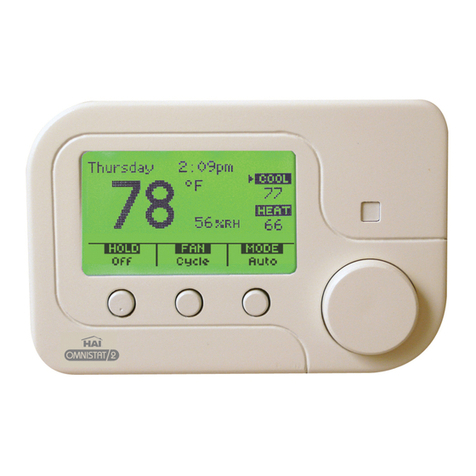
HAI
HAI RC-2000 installation instructions
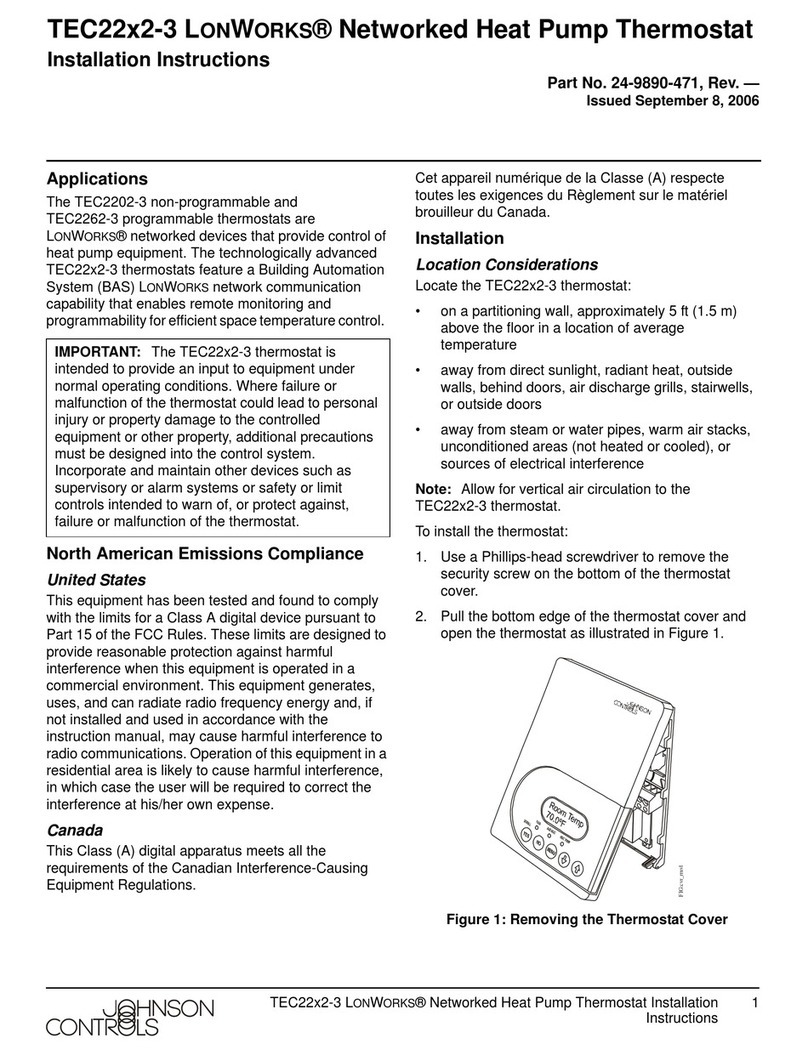
Johnson Controls
Johnson Controls TEC22 2-3 LonWorks Series installation instructions
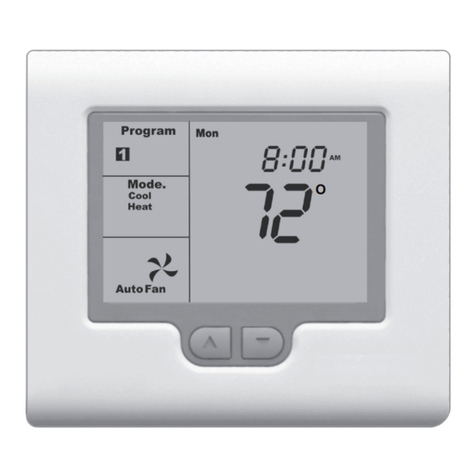
Specified Controls
Specified Controls SC-T32-P installation manual
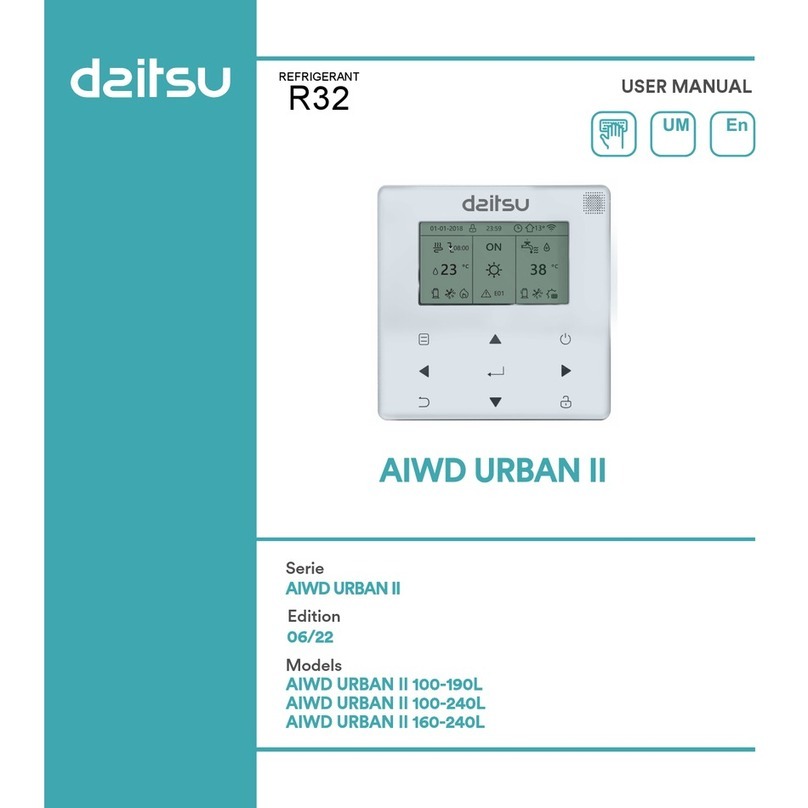
Daitsu
Daitsu AIWD URBAN II Series user manual

White Rodgers
White Rodgers 1F78 installation instructions
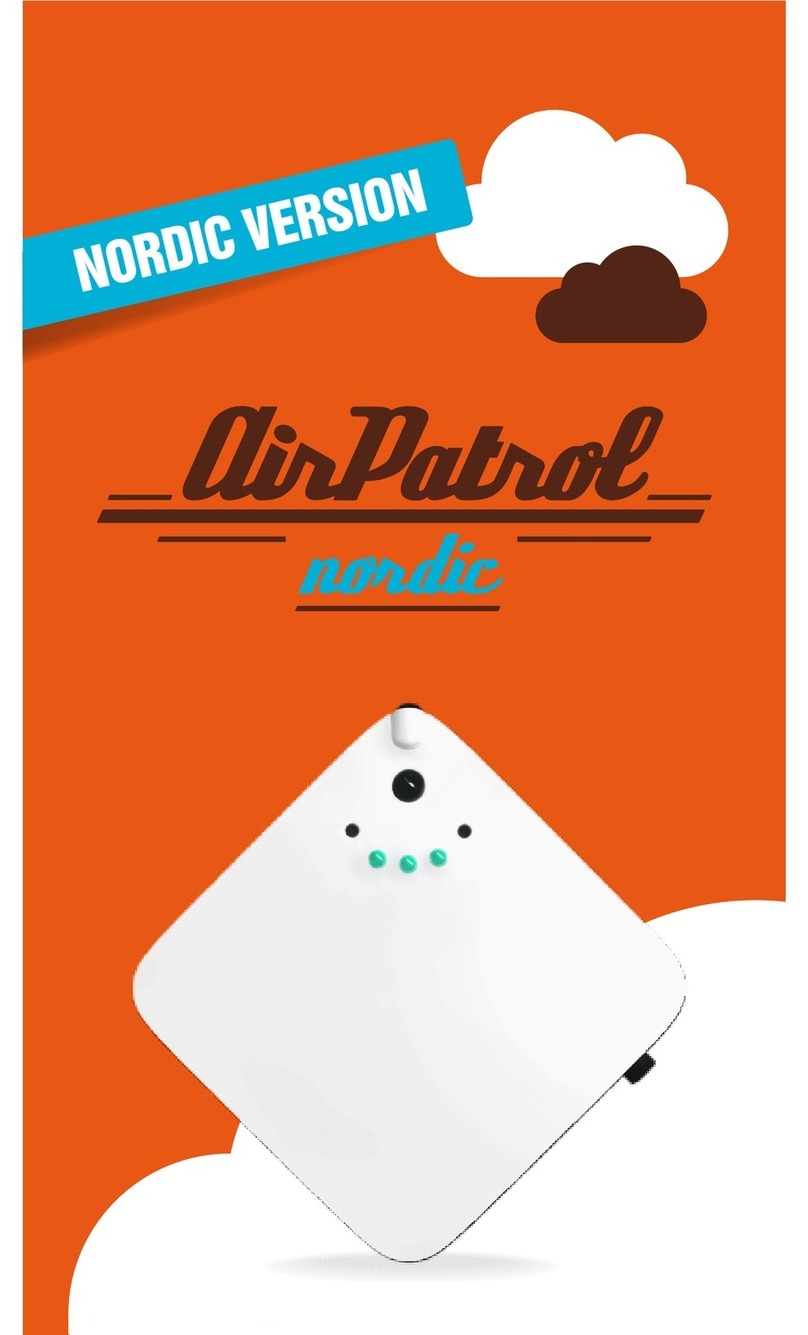
AirPatrol Lite
AirPatrol Lite Nordic quick start guide

Carrier
Carrier Infinity Control Home installation instructions
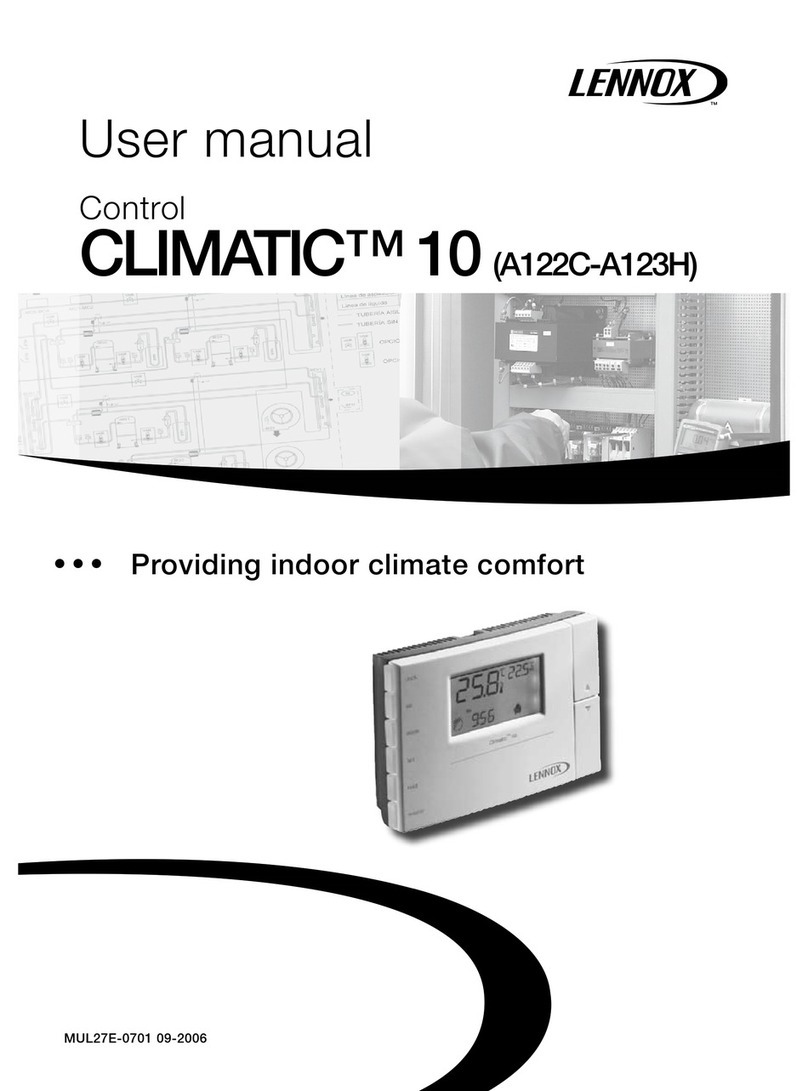
Lennox
Lennox CLIMATIC 10 A122C-A123H user manual

meitav-tec
meitav-tec ETN24 Owner's manual & technnician settings

Alpha
Alpha CONNECT installation guide