Standa 8SMC5-USB User manual

Download user manual in pdf
For quick simple questions you can contact us via Telegram.
The official technical support channel @SMC5TechSupport ( https://t.me/SMC5TechSupport).
Available online Mon-Fri 8:00-16:00 UTC.
8SMC5-USB User Manual
1. About
1. General information
2. Benefits
3. Table of specifications
4. Specifications
2. Safety instructions
3. Overview and getting started
1. One axis configuration
2. Example of a motor connection
3. Manual profile setting
4. Calculation of the nominal current
5. Possible problems and solutions
4. Technical specification
1. Appearance and connectors
1. Controller board
2. One axis system
3. Two axis system
2. Kinematics and rotation modes
1. Predefined speed rotation mode
2. Rotation for predefined point
3. Predefined displacement mode
4. Acceleration mode
5. Backlash compensation
6. Rotation reversal
7. Recommendations for accurate rotation
8. PID-algorithm for DC engine control
9. Stop motion modes
10. PID-algorithm for BLDC engine control
3. Main features
1. Supported motor types
2. Motor limiters
3. Limit switches
4. Automatic Home position calibration
5. Operation with encoders
6. Revolution sensor
7. Steps loss detection
8. Power control
9. Critical parameters
10. Saving the parameters in the controller flash memory
11. User defined position units
4. Safe operation
5. Additional features
1. Operating modes indication
2. Operations with magnetic brake
3. Joystick control
4. Left-Right buttons control
5. TTL synchronization
6. Design of multi-axis system
7. General purpose digital input-output
8. General purpose analog input
9. External driver control interface
10. Serial port
11. Saving the position in controller's FRAM memory
12. The Standa stages detection
6. Secondary features
1. Zero position adjustment
2. User-defined position adjustment
3. Controller status
4. USB connection autorecovery
5. XILab application User's guide
1. About XILab
2. Main windows of the XILab application
1. XILab Start window
2. XILab Main window in single-axis control mode
3. XILab Main window in multi-axis control mode
4. Application Settings
5. Charts
6. Scripts
Page 1 / 345
Page 1 / 345

7. XiLab Log
3. Controller Settings
1. Settings of kinematics (Stepper motor)
2. Motion range and limit switches
3. Critical board ratings
4. Power consumption settings
5. Home position settings
6. Synchronization settings
7. Brake settings
8. Position control
9. Settings of external control devices
10. UART settings
11. General purpose input-output settings
12. Motor type settings
13. Settings of kinematics (DC motor)
14. Settings of PID control loops
15. About controller
16. Settings of kinematics (BLDC motor)
4. XILab application settings
1. XILab general settings
2. General motor settings
3. Attenuator settings
4. Cyclical motion settings
5. Log settings
6. Charts general settings
7. Charts customization
8. User units settings
9. About the application
5. Positioner specifications
1. Positioner name
2. Positioner general characteristics
3. Motor characteristics
4. Encoder specifications
5. Hall sensor characteristics
6. Reducing gear specifications
7. Accessories specifications
6. Correct shutdown
7. Working over network
8. XILab installation
1. Installation on Windows
1. Installation on Windows XP
2. Installation on Windows 7
3. Installation on Windows 8
2. Installation on Linux
3. Installation on MacOS
6. Programming
1. Programming guide
1. Working with controller in Labview
2. Working with controller in Matlab
2. Communication protocol specification
3. 8SMC1-USBhF software compatibility
4. Libximc library timeouts
5. XILab scripts
7. Files
1. Configuration files
1. Translation Stages
1. 8MT160 - Motorized Delay Line
2. 8MT295 - Long-Travel Motorized Linear Stages
3. 8MT195 - Long-Travel Motorized Linear Stages
4. 8MT167 - Motorized Translation Stage
5. 8MT173 - Motorized Translation Stages
6. 8MT173DC - Motorized Translation Stages
7. 8MT50 - Motorized Translation Stages
8. 8MT30 - Narrow Motorized Translation Stages
9. 8MT175 - Motorized Translation Stages
10. 8MT177 - Motorized Translation Stage
11. 8MT184 - Motorized Translation Stage
12. 8MT193 - Motorized Translation Stage
13. 8MT200 - Motorized Translation Stages
14. 8MTF - Motorized XY Scanning Stage
15. 8MTF2 - Motorized Fiber Coupling Stage
16. 8MTFV - Motorized Translation Stage
17. 8MT60 - Motorized Translation Stage
2. Rotation Stages
1. 8MR151 - Motorized Rotation Stages
2. 8MR170 - Motorized Rotation Stages
Page 2 / 345
Page 2 / 345

3. 8MR174 - Motorized Rotation Stage
4. 8MR190 - Motorized Rotation Stage
5. 8MR191 - Motorized Rotation Stage
6. 8MRB250 - Large Motorized Rotation Stage
7. 8MRU - Universal Motorized Rotation Stages
8. 8MPR16-1 - Motorized Polarizer Rotator
9. 8MRH240 - Large High Capacity Rotary Stage
3. Vertical Translation Stages
1. 8MVT100 - Vertical Translation Stage
2. 8MVT120 - Vertical Translation Stage
3. 8MVT188 - Vertical Translation Stage
4. 8MVT40 - Vertical Translation Stage
5. 8MVT70 - Vertical Translation Stage
4. Screws and actuators
1. 8MS00 - Motorized Screws
2. 8CMA06 - Motorized Actuator
3. 8CMA20 - Compact Motorized Actuator
4. 8CMA28 - Motorized Linear Actuator
5. 8CMA16DC - Motorized Linear Actuator
5. Motorized Goniometers
1. 8MG00 - Motorized Goniometers
2. 8MG99 - Motorized Goniometer
6. Mirror Mounts
1. 8MTOM2 - Motorized Two Axis Translation Optical Mount
2. 8MUP21 - Motorized Optical Mount
3. 8MBM24 - Motorized Mirror Mounts
4. 8MMA60 - Motorized Mirror Mounts
5. 8MBM57 - Large Aperture Motorized Mirror Mount
6. 8MKVDOM - Motorized Vertical drive optical mount
7. Motorized Attenuators
1. 10MCWA168 - Motorised Closed Variable Wheel Attenuator
2. 10MWA168 - Motorized Variable Wheel Attenuator
8. Motorized Iris Diaphragms
1. 8MID98 - Motorized Iris Diaphragm
2. Software
8. Related products
1. Ethernet adapter
1. Overview
2. Administration
Page 3 / 345
Page 3 / 345

1.1. General information
Controller board.
We offer an inexpensive and ultra-compact servo-drive with USB interface for stepper motors with external power supply.
Forget about cumbersome and expensive servo-drives! All you need is a stepper motor, a controller, a USB cable and any stabilized
external power supply. That is all! Forget about active coolers as well. Controller's board is about the same size as a notepad or a
cellphone, therefore, you may just put it down on the worktable without any assembly procedures. The controller works with any type
of compact stepper motors with the rated winding current of up to 3A. Controller works with stepper motors with no feedback as well
as with ones equipped with encoders in feedback loop, including linear encoders on the stages. The motor connector on the controller
board is the same as one used by Standa company and it fits to all the Standa stages. USB connector provides easy communication
and work with computer. Several controllers can be connected to one computer either via USB ports or through a special backplane
supplied with multiaxis systems. The controller is fully compatible with the majority of operating systems, e.g., Windows, Mac OS X,
Linux, etc.
XILab main window.
All the necessary software including all configuration files are supplied with the controller. It allows you to start working with it the
controller right out of the box, according to "plug-and-play" principle. We continuously develop additional configuration files for newly
supported motors. Therefore, all you need is to download the file for your stage from Configuration files chapter, open it with XILab
software and hit Apply. Your controller is now fully configured! Just issue movement commands and controller will do whatever you
want.
Page 5 / 345
Page 5 / 345

1.2. Benefits
Main benefits
Compact and powerful! The controller's dimensions are 47x25x125 mm including all connectors. The device is adapted to all
stepper motors with rated winding current of up to 3A.
Compatible with 8SMC1-USBh After updating the MicroSMC driver, all the software for 8SMC1-USBh will be working with
8SMC5-USB.
Compatible with all the Standa stages! Have you got a Standa stage? Just plug and play, we have already done the rest for
you!
It does remember all! Do not worry about saving the current position on the computer: the controller does it itself using its
own nonvolatile memory that works even after a sudden power cut.
It works with peripherals! It supports a quadrature encoder, magnetic brake, a joystick, limit switches, a zero position sensor
– all included, just plug and work!
Built-in zero calibration! Using the limit switches, the revolution sensor, the external signal or their combination, the zero
calibration is performed by a single command!
It works with all computers! All the supplied software is compatible with Windows 8, Windows 7, Windows Vista, Windows XP
SP3, Linux, Mac OS X , including 64-bit versions.
All benefits
Really powerful! It is adapted to all the stepper motors with rated winding current of up to 3A.
Compatible with 8SMC1-USBh After updating the MicroSMC driver, all the software for 8SMC1-USBh will be working with
8SMC5-USB.
Compatible with all the Standa stages! Have you got a Standa stage? Just plug and play, we have already done the rest for
you!
It knows its own set! A built-in feature for downloading the configuration file right from the stage memory is available! The
stage's support of such memory is required.
Choose your interface! Both USB and serial port are built-in and ready to use.
Really fast! Up to 35,000 steps per second for any microstep mode!
Precise! The microstep modes from full step to 1/256 of the step on all the speeds.
It does remember all! Do not worry about saving the current position on the computer: the controller does it itself using its
own nonvolatile memory that works even after a sudden power cut.
It works with peripherals! It supports a quadrature encoder, magnetic brake, a joystick, limit switches, a zero position sensor
– all included, just plug and work! Additional stabilized output for peripherals (5V, 100mA) is available.
Built-in zero calibration! Using the limit switches, the revolution sensor, the external signal or their combination, the zero
calibration is performed by a single command!
Stand-alone! Would you like to work in the stand-alone mode? Just go ahead! An external joystick, a keypad or their
combination is supported.
Energy conserving! Programmable current reduction in the motor windings in the hold mode with 1% accuracy.
Silent! Smooth movement at lower speeds and no extra noise at higher speeds.
Protected! An ESD protection on all pins of external connectors and additional short circuit protection for the motor windings.
Attentive! It controls the temperature of the processor and the power driver as well as both currents and voltages for the power
supply and USB.
Modern! The firmware in the nonvolatile memory of the controller can be updated via USB interface.
Controlling and controllable! The built-in synch input and output allow to start the rotation to desired position by the
incoming external signal and/or to transmit the outgoing signal after the desired position is reached. The analog common input
and the digital common input/output are built in as well.
Comprehensible! The status LED displays the power supply and the controller's state. For convenience of use both signals
doubled at the external LEDs as well as the state of the limit switches.
Multiaxis machine! The multiaxis systems are designed by using standard USB hubs, either external or mounted at a special
backplane. There may be up to 32 axis in the system.
It works with all computers! All the supplied software is compatible with Windows 8, Windows 7, Windows Vista, Windows XP
SP3, Linux, Mac OS X , including 64-bit versions.
Examples for all programming languages! Controllers are supplied with cross-platform library and examples which allow
rapid development using C++, C#, .NET, Delphi, Visual Basic, gcc, Xcode, Matlab, Java and LabVIEW.
Full-featured interface! The XILab user interface is supplied with the controller. It allows to easily control all the functions and
features of the device without any programming.
Unique scripting language! A scripting language is integrated into XILab software. It allows easy setting the sequence of
actions, including cycles and branches, without compilation or learning any programming language.
New! Stepper motor close-loop control algorithm are ready! Motion is smoother and faster than ever with innovation
encoder based close-loop on all 8SMC5-USB motor controllers. It combines advantages of BLDC motor control with cheapness of
conventional stepper motors. No hidden catch, no stall or hitch, just free move!
Page 6 / 345
Page 6 / 345

1.3. Table of specifications
Power supply external 12V - 48V DC
Current
consumption up to 5A (depending on the voltage) from external power supply
Current in the
motor winding up to 3A
Protection types current overload protection, voltage overload protection, short circuit protection, motor hotplug/unplug protection
Motion modes move left/right, move to point, shift on delta, continuous speed, acceleration and deceleration ramps, backlash
compensation mode, automatic home position calibration mode
Step modes full-step, 1/2, 1/4, 1/8, 1/16, 1/32, 1/64, 1/128, 1/256
Rotation speed up to 35 000 full steps per second
Speed profile trapezoidal
Position counter 40 bit
Feedback Single-ended and differential quadrature encoder (optional)
Limit switches 2
Feedback
bandwidth 200 kHz for single-ended and 5MHz for differential encoder
Note: The controller's working voltage range is 12V to 48V DC. The voltage limits are 12V and 50V DC. If the voltage
exceeds 50V, the controller is guaranteed to fail. If the voltage falls below 12V, the controller turns off.
Page 7 / 345
Page 7 / 345

1.4. Specifications
Motor requirements
Motor type: bipolar stepper motor, DC motor.
Rated winding current: minimum 100mA.
Rated winding voltage: minimum 2V DC.
Electric specifications of the controller
Power supply modes: external.
Current in each motor winding: up to 3A.
Maximum encoder pulse frequency: 200 kHz for single-ended and 5MHz for differential encoder.
Stabilized 5V DC output (the power supply for encoder and other peripherals): 100mA maximum output current, 5% or better
output voltage stability.
ESD-protection on all pins of the output connectors (e.g., D-Sub 15 pin, mini-USB or power jack).
Winding-to-ground short circuit protection.
Winding-to-winding short circuit protection.
Motor hot-swapping protection.
Wrong power polarity protection (no more than 1s).
Voltage overload protection (no more than 1s).
USB-supplied current limitation.
External power supply current limitation.
Motor rotation speed limitation.
Programmable full winding current with 10mA precision.
Programmable winding current decrease with 1% precision for the hold mode.
Rotation control features
Microstep modes: full-step, 1/2, 1/4, 1/8, 1/16, 1/32, 1/64, 1/128, 1/256.
Noiseless at low speeds.
Minimum speed is 1/256 of the full step per second.
Maximum speed is up to 35 000 full steps per second for all microstep modes.
Minimum shift is 1/256 of the step.
Maximum shift is 2,147,483,647 full steps for all microstep modes.
Smooth start/stop mode.
40-bit position counter (32 bits for full step and 8 bits for microstep).
Motion modes: left/right move, move to point, shift on delta, continuous speed, acceleration and deceleration ramps, backlash
compensation mode, automatic home position calibration mode.
Additional firmware features
Automatic HOME calibration at firmware level.
The nonvolatile memory used for saving/downloading the controller settings.
Software update via USB interface.
Automatic position saving according to step counter and encoder with power-off protection.
Additional features available via motor connector
Processing the signals from one or two limit switches; software configurable.
The Standa stages recognition and automatic downloading of the configuration file right from the stage if the last one supports
this feature.
The "step loss" detection and position recovery using either a revolution sensor or a quadrature encoder (if the stage supports
this feature).
The position detection using a quadrature encoder. The x4 mode.
The stepper motor control using master quadrature encoder mode, providing the maximum speed without any step loss. Starting
with firmware 4.1.
Additional features available via backplane connector
USB connector on backplane that duplicates USB input on controller board.
A serial RS-232 port. TX and RX lines are available. Specifications: 9600 - 921600 baud speed, TTL 3.3V. The Ethernet,
Bluetooth, WiFi, ZigBee and other configurations based on the serial port are available by request.
Synchronization input: once the pulse is received via this pin, the controller starts rotating the motor to predetermined position
or by predetermined shift value. The triggering mode, the polarity and duration of the pulse are adjustable by user.
Specifications: TTL 3.3V.
Synchronization output: emit pulse to this pin if rotation is started or finished, or predetermined user-defined shift value is
reached. The triggering mode, the polarity and duration of the pulse are adjustable by user. Specifications: TTL 3.3V.
Left or right buttons. Once the button is pressed, the rotation in corresponding direction starts and the speed increases gradually
according to acceleration and other settings. Specifications: TTL 3.3V.
Joystick pin allowing operation with various joysticks with the voltage range no more than 0–3V.
Magnetic brake control pin providing control to magnetic brake mounted on the motor shaft. Specifications: TTL 3.3V, 5mA.
Common analog input pin allowing operation with signals within 0–3V range. Reading frequency is 1kHz. The configuration is
programmable.
Common digital input/output pin. 1kHz update frequency, software configurable. Specifications: TTL 3.3V, 5mA.
Page 8 / 345
Page 8 / 345

Limit switches indication pins designed for LED direct connection. Specifications: TTL 3.3V, 2mA.
Digital "Power" and "Status" pins duplicate the status LED and designed for direct connection of LEDs. Specifications: TTL 3.3V,
2mA.
External driver control interface allowing to control any type of external driver using three signals: enable, direction, clock.
Multiaxis systems development. The multiaxis systems are created from standard USB hubs, either external or mounted at a
special backplane. On the PC a multiaxis system is represented as a set of virtual serial ports, according to the number of
connected axes.
Programming the controller
All the software supplied with controller is compatible with Windows 8, Windows 7, Windows Vista, Windows XP SP3, Linux, Mac
OS X, including 64-bit versions.
Controllers are supplied with cross-platform library and examples which allow rapid development using C++, C#, .NET, Delphi,
Visual Basic, gcc, Xcode, Matlab, Java and LabVIEW.
The XILab user interface is supplied with the controller. It allows to easily control all the functions and features of the device
without any programming.
A scripting language, an EcmaScript language dialect, is integrated into XILab software. It allows easy setting the sequence of
actions, including cycles and branches, without compilation or learning any programming language.
Page 9 / 345
Page 9 / 345

2. Safety instructions
Power supply and grounding requirements. Connection to controller
General requirements for a controller board, systems in box ( single and double axes) are listed below.
IMPORTANT. Either the power supply unit should be plugged to grounded 220V AC socket (a three-wire connection
scheme). Make sure that the minus electrode of your power supply unit is grounded. If the power supply unit with
minus electrode disconnected from the grounding circuit is used, ground the controller board via special grounding
terminal (look at the picture below). Non-compliance with these rules may lead to the decrease in controller stability
and noise resistance.
Top view of the controller board. A grounding terminal marked with the red square
Typical connection diagram for a controller (board, systems in box):
Controller
8SMC5-USB
PC Power
supply
Motor
USB 220 V
Controller grounded via minus electrode of power cable connection diagram
Controller
8SMC5-USB
PC Power
supply
Motor
USB 220 V
Controller connection diagram with grounding via special terminal
Page 10 / 345
Page 10 / 345

Warning. Power supply unit should be able to supply sufficient current to rotate the motor. As an absolute minimum
it should be able to supply where is the minimum working current of
power supply unit, is the operating current in the winding, is power supply unit stabilized voltage, and
is rated operating voltage of the motor. It is recommended to use a power supply unit with operating current
equal to . The voltage should be greater than . The higher the voltage, the
faster rotation speed could be reached.
One can use power consumption of power supply unit to calculate minimum requirements instead. An absolute
minimum of power is . For example, for motor with
operating winding current of 1A and operating voltage of 5V (with 5W rated power consumption), the operating
voltage of power supply unit may be chosen at 20V with the output power of at least 10W (the maximum operating
current of power supply unit is at least 0.5A).
Controller board
IMPORTANT. It is strictly forbidden to touch the controller board without any antistatic equipment. We recommend
you to use antistatic wrist strap.
IMPORTANT. It is strictly forbidden to connect positive wire of power supply to the controller board when
ground wire is not connected. It is strictly forbidden to connect or disconnect power cable when the
power supply is on, the controller is connected to the PC and the power supply and the PC are grounded.
This may damage the PC! This is a common requirement for any electronic device with separate power source,
which is connected to the PC via USB.
Warning. Before connecting the controller board to the motor or to the PC via USB interface, it is recommended to
connect controller to power supply with proper grounding or to use separate grounding for controller with the specially
marked ground terminal (look above).
One and two axes system in box
IMPORTANT. You should not exceed maximum allowed voltage of 48V. If voltage goes over allowed value at
more than 2 volts, it can immediately and irreversibly damage the controller.
Page 11 / 345
Page 11 / 345

3. Overview and getting started
This guide describes the operation of controller for multi-axis and one-axis systems, basic parameters configuration and getting started
with XILab software for Windows 7.
One axis configuration - a brief description of the beginning of work with the controller + 8SMC5-USB for one axis +. It is also
considered quick XiLab setup and lists all necessary equipment.
Example of a motor connection - connection of stepper motor Nanotec ST5918L3008-B with encoder CUI INC AMT112S-V to
8SMC5-USB controller. It is described how to make your own cable, guided by the specification on the engine and explanation of
the specification is given.
Manual profile setting - setting of working profile for XiLab. Overview of the main features.
Calculation of the nominal current - setting of amplitude of nominal current for stepper motors.
Possible problems and solutions - description and solution of the most common problems when working with 8SMC5-USB
controller.
Page 12 / 345
Page 12 / 345

3.1. One axis configuration
Introduction
System requirements
Software installation and startup procedures
Getting started with XILab software
Functional test
Control from user applications
3.1. One axis configuration
Controller board.
Introduction
This manual describes the controller installation procedures and getting started with XILab software for Windows 7. The detailed
controller specifications are described in Specifications chapter. For developing your own applications, please read the Programming
guide 8SMC5 chapter and download the programming software package from the software chapter.
System requirements
Note. There are only brief requirements in this chapter. For detailed information please read the Specifications
chapter.
For successful installation you will need:
PC with USB port
A standard PC with USB port.
Make sure that your PC has all of the current Windows updates installed. It will help you to maintain software compatibility. If
necessary, please download the latest updates from www.microsoft.com/updates.
Software
All necessary software to work with the controller can be downloaded from software page.
USB A - mini-B cable
USB-A to mini-USB-B cable.
For detailed information about the USB cable please read the data connector chapter.
8SMC5-USB controller
Page 13 / 345
Page 13 / 345

The motor controller board.
The controller appearance may differ from the one shown on the above figure depending on its configuration and version. For
detailed information about versions please read the Appearance and connectors 8SMC5 chapter.
Positioner or motor
The stepper motor-based positioner.
The stepper motor-based positioner used in the operations is shown at the figure. The detailed motor requirements are described
in Specifications chapter. If you use your own cables for connecting the positioner to the controller, please refer to positioner
connection scheme and the controller's output connector scheme . For positioners with limited movement range, two limit
switches must be used: SW1 and SW2. These pins are used to determine the movement limits.
Power supply
Stabilized power supply unit.
Notes.
Please use the 12–36V DC stabilized power supply. Too high voltage may damage the controller. For more
information please read the Safety instructions 8SMC5 chapter. The power supply unit must provide the current
enough for sustainable rotation of the motor.
Please pay attention on the manual supplied with your controller. The more strict power voltage limitation is
possible depending on the controller model. Please check the connection of external power supply unit to the
controller carefully.
If controller is supplied inside the metal case, the case must be grounded. If controller is supplied without any
body, the grounding circuit of power supply unit is used. For more information please read the Safety
instructions 8SMC5 chapter.
If the board is operated without the casing, make sure it lays on the insulating surface and there are no
extraneous particles on the board or around it.
Software installation and startup procedures
Make sure that all controllers are disconnected from your PC.
The software installation manual is here. The installer file name is "xilab-<version_name>.exe". It automatically detects whether it is
running on 32-bit or 64-bit version of Windows and installs the appropriate version of XiLab. Launch the installation program, the
installation window will appear. (The software versions may slightly differ from each other).
Page 14 / 345
Page 14 / 345

XILab main installation window.
Press “Next>” button and follow the instructions on screen. All the necessary software including all drivers, packages and programs will
be installed automatically. After installation is finished, the XiLab software starts by default and the following window will open:
XILab "No devices found" dialogue window.
Don't press any buttons.
Connect the positioner to the controller. Connect the stabilized power supply unit to the controller. Ground the controller or power
supply unit. Connect the controller to your PC using the USB-A to mini-USB-B cable.
The LED indicator at the controller board will start flashing. The New Hardware Wizard starts working after the first connection of the
controller to PC. Please wait until Windows detects a new device and installs all necessary drivers for it.
If the automatic driver installation has failed, please select ”No, not this time” in the window being opened and press “Next>” button.
Select “Install from a list or specific location (Advanced)” in the next window and press “Next>” again. Browse the software disk
supplied with controller and find the *.inf file there or in the XiLab-install-path\driver\ folder and wait until installation is completed.
Go back to XILab "No devices found" dialog window and press "Retry" button.
If this window was closed, please go to “Start” menu, select Programs->XILab Х.Х.Х->XILab and launch it. The dialog window will
open again.
Getting started with XILab software
XILab is a user-friendly graphic interface designed for control, diagnostics and adjustment of motors. It can also be used for easy
installation and save/restore of parameters for any type of motors. This chapter describes the startup procedures with XILab software.
For complete information please refer to XILab application User's guide chapter.
Page 15 / 345
Page 15 / 345

XILab main window.
Open “Settings...”, then press “Restore from file...” and select the configuration file for your positioner from the opened C:\Program
Files\XILab\profiles\ folder. The values applicable for your positioner will automatically fill all the fields of “Settings...” menu. If the
necessary file isn't found, please refer to the Configuration files chapter. If there is still no solution, please leave your request at our
customer service website.
Page 16 / 345
Page 16 / 345

XILab, the Settings menu window.
Warning. For the controller to work with stepper motors it is required to properly set up:
working current,
displacement limits and limit switches ,
critical parameters,
limiters,
power supply mode.
If you decide to configure your controller by yourself, please check these parameters carefully!
Congratulations, your controller is ready for operation!
Functional test
Check if the controller is configured properly by pressing left or right button in the central row of XILab main window control buttons.
The positioner has to start moving. Use the central "soft stop" button to stop the rotation. Please pay attention to the power supply
parameters of the controller in the Power section. The power voltage, working current and temperature of the controller can be set
there.
If Xilab main window is shaded red when the movement was supposed to start, that means that protection was activated and controller
entered the Alarm state. This may be caused by incorrect settings, wrong connection of the positioner or controller malfunction. For
detailed information please read the Critical parameters chapter.
Page 17 / 345
Page 17 / 345

Control from user applications
Xilab software is a convenient way to control stages connected to 8SMC5-USB controller. However, if you need to control the 8SMC5-
USB from your own application, you may do so by using libximc library. Programming guide 8SMC5 has several examples in C, C#,
Delphi, Java, VB.net, Matlab, LabView programming languages. If all you need is to automate a small number of control steps, then
instead of a standalone program you may find it easier to use Xilab scripting language.
Page 18 / 345
Page 18 / 345

3.2. Example of a motor connection
General case
Positioner standard connection diagrams
Example
Preparation
Connecting the motor and encoder to the
controller
3.2. Example of a motor connection
General case
To connect a motor to the controller please refer to positioner connector, and
use the scheme of positioner connection:
Positioner standard connection diagrams
General diagram of positioner and encoder connection using Dsub connector.
Note. If A and B encoder channels work in open drain mode, some extra pull-up of encoder outputs to 5V power
voltage using the resistors may be required at high rotation speeds in order to provide the maximum signal
transmission speed (see Operation with encoders ).
Note. Only firmwares 4.1.0 and older support BLDC.
Example
Consider the connection of the two-phase stepper motor Nanotec ST5918L3008-B with encoder CUI INC AMT112S-V to controller
8SMC5-USB.
Preparation
To get started, we need:
Motor;
Encoder;
Pinout of D-SUB connector for 8SMC5-USB;
Motor datasheet ;
Encoder datasheet ;
Soldering equipment: soldering-iron, wires, flux, solder, nippers, heat shrink tubes of different sizes;
Screws M2.5x6 for fixing the encoder;
D-SUB cover + connector (male) and wires for cable manufacturing;
Page 19 / 345
Page 19 / 345

Connecting the motor and encoder to the controller
Before you begin, assemble the encoder in accordance with the appropriate instructions.
The motor without encoder. Note 2 holes M2.5 to which is usually attached an encoder
Motor with attached encoder
Let us look in the specification of the engine and find the wiring diagram (for Nanotec ST5918L3008-B it is at the bottom right in
the specification):
Motor contacts
Connection type
There exist serial and parallel winding connection and each type allows to obtain various characteristics for the motor. We
will connect the windings in series (red frame on the picture). To do this, wires having two colors BLK/WHT and GRN/WHT,
as well as RED/WHT and BLU/WHT must be connected to each other in pairs. Next, you need to put in accordance A, not A,
B, not B pins of controller to contacts of motor windings ST5918L3008-B: black, green, red, blue. One winding is a
connection of A and not A or B and not B. After the connection between a two-color wire, you will get that one winding of
the motor is black - green connection, other is red - blue. Therefore, matching contacts will be the follows: black - A, green
- not A, red - B, blue - not B. It can be seen in the picture above Connection type.
Page 20 / 345
Page 20 / 345
Table of contents
Other Standa Controllers manuals
Popular Controllers manuals by other brands
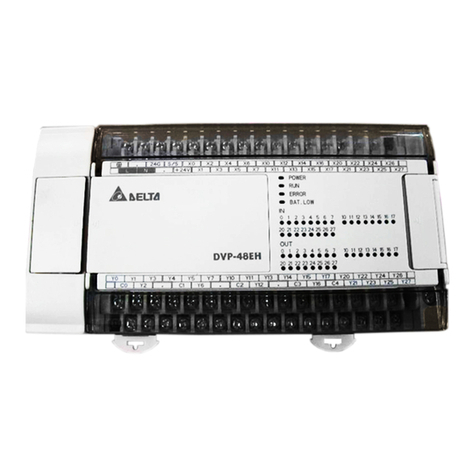
Delta Electronics
Delta Electronics Programmable Logic Controller DVP-PLC instruction sheet
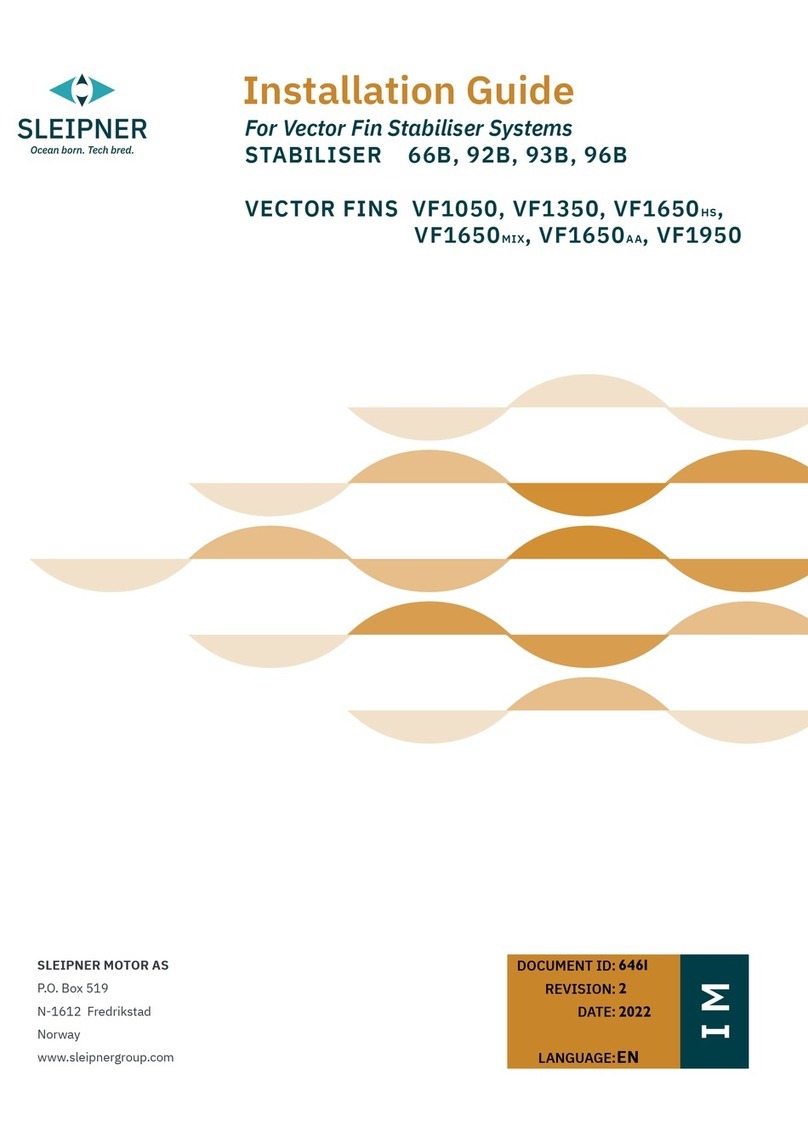
Sleipner
Sleipner STABILISER 66B installation guide
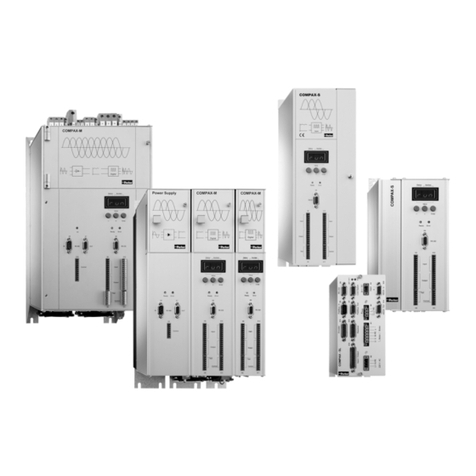
Parker
Parker COMPAX-M /-S (L) user guide

Hyster
Hyster P2.0 Service & repair manual
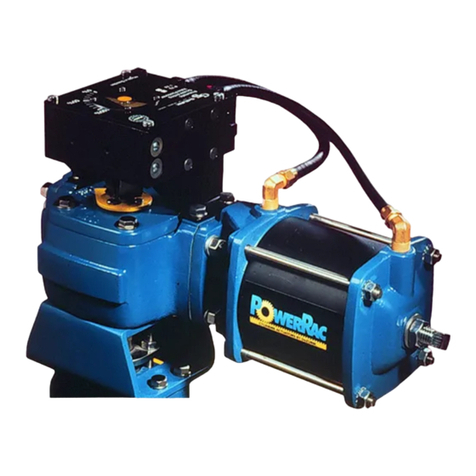
DeZurik
DeZurik POWERRAC R1 instruction manual
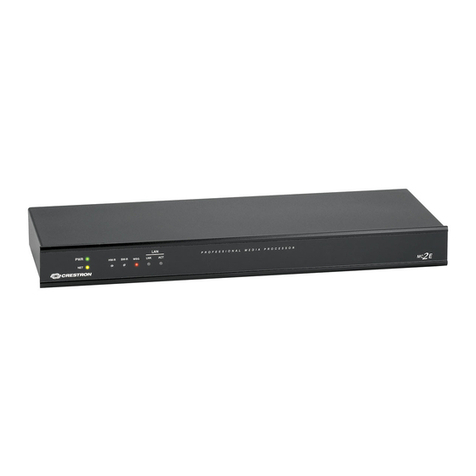
Crestron
Crestron MC2E Operation guide
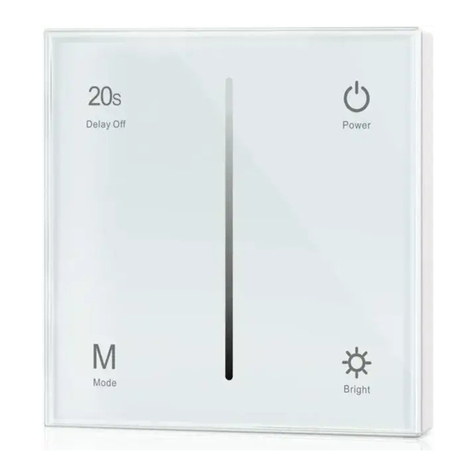
Lampo
Lampo WALLDIMTOUCH quick start guide
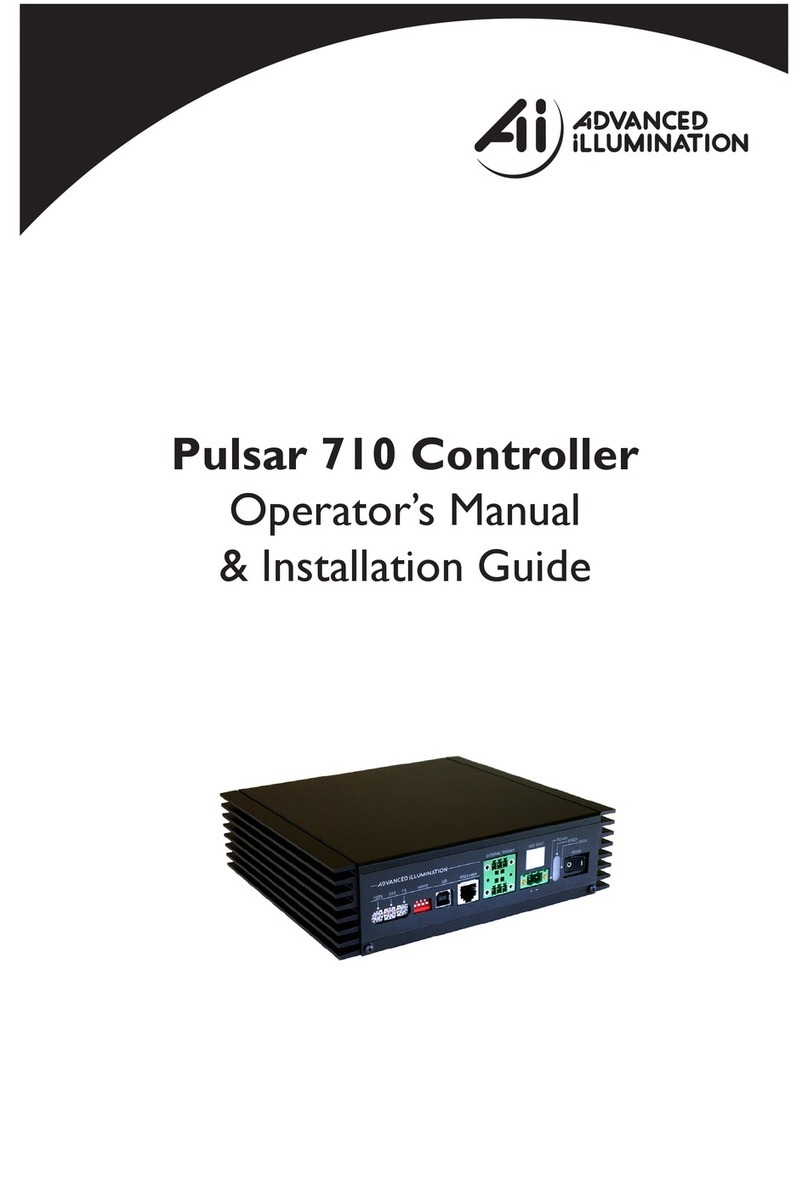
Advanced lluminated
Advanced lluminated Pulsar 710 Operator's manual & installation guide
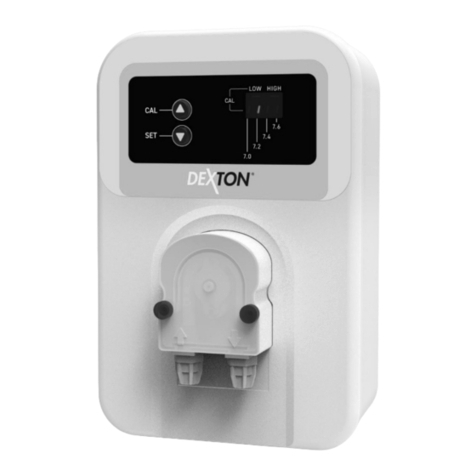
Dexton
Dexton C-11-213031 Instructions for use
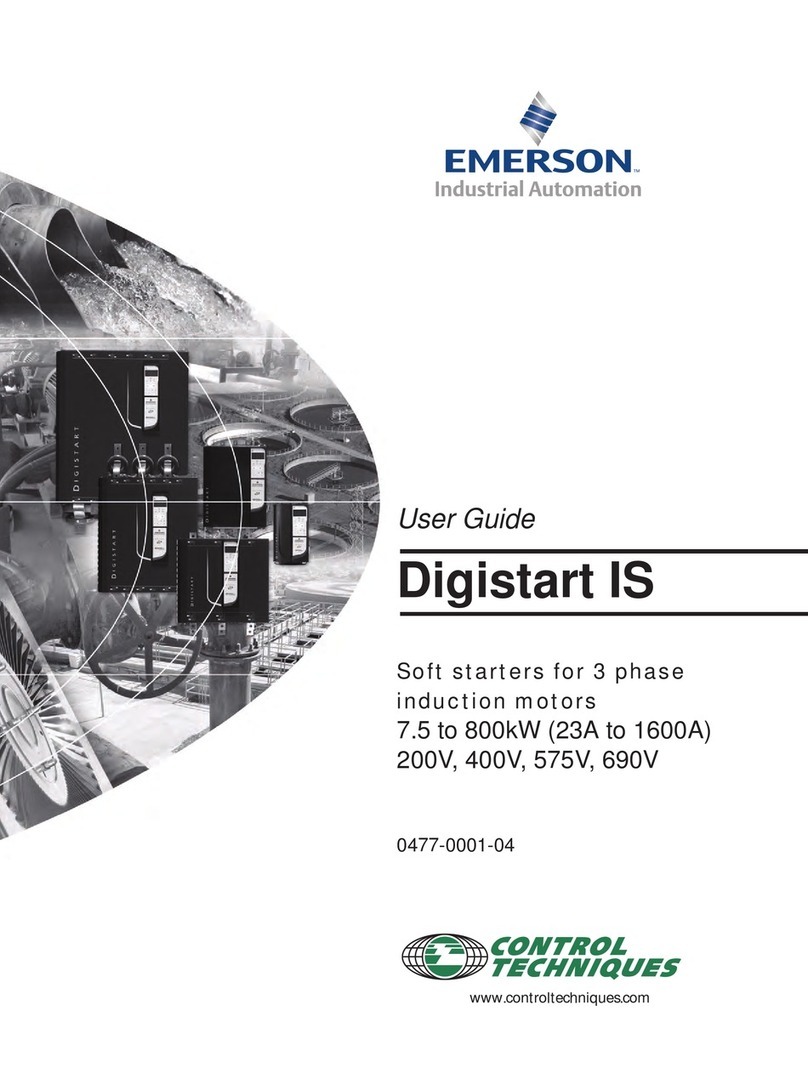
Emerson
Emerson Digistart IS1x0043B series user guide
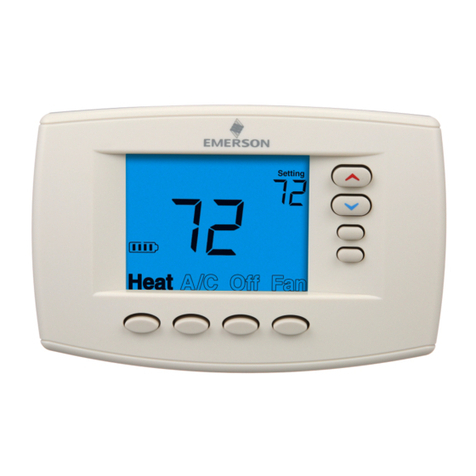
White Rodgers
White Rodgers 1F98EZ-1621 installation instructions

miicare
miicare miicube Guide