Stihl FS 460 C Manual

STIH)
Technical Information
TI_40_2010_13_01_02.fm englisch / English
New clearing saw STIHL FS 460 C – Series 4147
Contents
1. Overview
2. STIHL M-Tronic
3. Technical description
4. Specifications
5. Cutting attachments
6. Accessories
7. Service accessories
8. Spare parts
9. Servicing
FS 460 C FS 460 C K
40.2010

Page 2 Technical Information 40.2010
TI_40_2010_13_01_02.fm
The new clearing saw STIHL FS 460 C is the
newest member of the clearing saw line and, in
future, will be the follow-up model to the
STIHL FS 450.
The STIHL FS 460 C stands out because of the
following strengths:
– STIHL M-Tronic – optimal engine performance
at all times, see b2
– Modern, low-emission 2-MIX engine
– High torque over a wide range of engine speeds
– Easy starting – fewer steps to start
– ErgoStart standard
– Functional, modern shape – outstanding
handling and ergonomics
– Very reliable and rugged
The new clearing saws are ideally suited for
professional users in landscaping and forestry.
Depending on the version, the scope of application
extends from mowing and thinning to mowing tough
grass, clearing scrub and thorny hedges, shredding
and sawing. The clearing saw STIHL FS 460 C with
a short drive tube is designed especially for use in
forests.
1. Overview
The new clearing saw STIHL FS 460 C is available
in various versions with varying features.
1.1 Versions with mowing handlebars
– Versions with varying drive tube lengths,
see b4.4
– Drive tube diameter: 28 mm
– New, maintenance-free gearbox
– Gearhead angle 35°, see b3.6.1, b4.5
– New deflectors and limit stops,
see b3.7.1, b5.1
– New, 4-point anti-vibration system - very low
vibration levels, see b3.8
– Can be used with the new PolyCut 41-3 mowing
head
– New universal harness ADVANCE included,
see b3.9.1
1.2 Version with sawing handlebars for use
in forests
– Version with short drive tube, see b4.4
– Drive tube diameter: 28 mm
– New, maintenance-free gearbox
– Gearhead angle 25°, see b3.6.2
– New limit stops, see b3.7.2, b5.2
– New, 4-point anti-vibration system – very low
vibration levels, see b3.8
– Only for sawing
– New forestry harness ADVANCE included,
see b3.9.2

Technical Information 40.2010 Page 3
TI_40_2010_13_01_02.fm
2. STIHL M-Tronic
The FS 460 C is the first STIHL clearing saw to be
equipped with the innovative M-Tronic fully
electronic engine management system. It regulates
the ignition timing and electronically adjusts the fuel
flow, taking external conditions into account.
Electronic cold / warm start detection permits a
position "Start }" on the choke lever for starting the
engine and ensures easy starting with fewer pulls of
the starter rope. The very good acceleration is
realized using the electronic controller. By means of
the engine temperature and speed, the control unit
continually checks the operating state of the
clearing saw and adjusts the fuel flow so that
optimal engine power is always available. The
electronic memory (memory function) remembers
the settings from the last time the machine was
used. Thus if the machine is restarted under the
same general conditions, the full power of the
engine is available immediately.
According to the system of product names for
convenience features (C-versions), machines with
M-Tronic are denoted with an "M".
2.1 Functional description
2.2 Components
Control unit (1)
Control center for the optimum adjustment of fuel
flow, the exact ignition timing and the memory
function.
Second pair of poles (2)
Supplies power to the control unit and solenoid
valve
Wiring harness (3)
Connects control unit, solenoid valve, micro switch
(integrated in switch gear) and diagnostic jack
Solenoid valve (4)
Electronically switched solenoid valve adjusts the
overall fuel flow in milliseconds – this permits
adjustment from 0 % to 100 % fuel
Micro switch (5)
Reports the position of the choke shutter – start
detection;
the micro switch (5) is integrated in the switch gear
Diagnostic jack (6)
Preparation for a software-based diagnostic unit
6
5
4
1
2
5903TI001 KN
3

Page 4 Technical Information 40.2010
TI_40_2010_13_01_02.fm
2.2.1 Starting
Set the choke lever to }(Start) – choke shutter is
closed. Simultaneously, the micro switch on the
switching device is closed. During starting and if the
engine is running, the control unit is powered via the
second pair of poles.
The following processes occur within the space of
milliseconds.
The microprocessor detects that the micro switch
has been actuated and thus the choke shutter is
closed and computes the necessary amount of fuel
and the ignition timing for the start.
During starting, the fuel-air mixture in the carburetor
is highly concentrated ("enriched") – a large quantity
of fuel flows through the solenoid valve. After initial
combustion, the quantity of fuel is reduced. The
engine does not stall out because the fuel-air
mixture is too rich; it keeps running and can be
accelerated immediately. After the throttle trigger is
actuated, the choke shutter and micro switch open
and the choke lever jumps to the operating
position F. The control unit receives the information
"choke shutter open" and the microprocessor
adjusts the amount of fuel.
2.2.2 Idle
The target idle speed is controlled by adjusting the
ignition timing and the fuel flow.
The engine speed can be influenced instantly by
adjusting the ignition timing. Changing the fuel flow
only influences the engine speed after 5 to
10 revolutions of the crankshaft.
For this reason, to establish steady idling, the
ignition timing is adjusted first and then the fuel flow.
The fuel flow control is designed so that the target
idle speed is attained with the target ignition timing.
2.2.3 Acceleration
If the control unit detects that the engine is being
accelerated, the ignition timing is set earlier and the
fuel flow is increased – the fuel-air mixture is
enriched. Optimal, spontaneous acceleration.
2.2.4 Full throttle
A regulating cycle only starts if the clearing saw is
operated for approximately 2 seconds under
constant conditions.
The solenoid valve closes for approx. 0.1 seconds –
the current fuel-air mixture is made leaner.
The speed change due to the brief leaning of the mix
is so slight as to be imperceptible to the user.
The resulting engine speed pattern is analyzed by
the microprocessor.
The following results are possible:
Engine speed increases
.The mix was too rich before the solenoid valve
closed – the fuel flow is reduced for next phase
of operation
Engine speed decreases
.The mix was too lean before the solenoid valve
closed – the fuel flow is increased for the next
phase of operation
Engine speed does not change
.The current carburetor setting is optimal – the
current setting will be maintained
2.2.5 Cut-off speed
The cut-off speed is kept constant by controling the
fuel-air mixture and the ignition timing.

Technical Information 40.2010 Page 5
TI_40_2010_13_01_02.fm
2.2.6 Advantages
Easy starting
With M-Tronic there is only one start position on the
choke lever because the system detects cold or
warm starts and electronically computes the exact
fuel flow. Starting with a few pulls of the starter rope
and immediate full throttle.
Permanent optimum engine performance
By means of the engine temperature and speed, the
control unit continually checks the operating state of
the clearing saw and adjusts the fuel flow for
constant optimum engine performance.
Very good acceleration
The FS 460 C accelerates spontaneously and
quickly by virtue of electronic ignition timing control
and fuel flow adjustment.
No manual carburetor adjustments
M-Tronic electronically adjusts the fuel-air mixture in
the carburetor: for all operating states such as start,
idle, part throttle and full throttle as well as taking
into account the external conditions, e. g., use at
varying altitudes, changing temperatures or fuel
quality (caloric value – energy content of the fuel,
alcohol content, knock resistance).
Memory function (electronic memory)
M-Tronic remembers, for an unlimited period of
time, the settings from the last time the clearing saw
was used and retrieves them the next time the
clearing saw is started. Thus full engine power is
available immediately each time the machine is
started under the same external conditions.
3. Technical description
3.1 Attaching the bicycle handle with
rotating handlebar support
The clamps are already attached to the handlebar at
the factory.
.Attaching the control handle
To assemble the rotating handlebar support, the
clamps must be fitted with a spring and fastened to
the handlebar support on the machine.
.Remove spring (1) from the set of parts included
with the machine
.Fit spring (1) in the lower clamp (2)
.Carry out further assembly in accordance with
Instruction Manual
1
2
317TI003 KN

Page 6 Technical Information 40.2010
TI_40_2010_13_01_02.fm
3.2 Operating elements
1Throttle trigger lockout
2Throttle trigger
3Stop switch – with the positions for Run and
Stop. To switch off the engine, the stop switch
(STOP) must be pressed.
3.3 Stop switch function
When the stop switch is not actuated, it is in the
position Run: The ignition is switched on – the
engine is ready for starting and can be started. If the
stop switch is actuated, the ignition is switched off.
Once the engine comes to a standstill, the ignition is
automatically switched on again.
3.4 Choke lever
To start the engine, the choke lever (1) must be
pressed in at the edge (arrows) and rotated to the
position }. Once the engine has been started and
the throttle trigger lockout and throttle trigger have
been pressed, the choke lever automatically returns
to the position Run F. It is not necessary to move the
choke lever to Run Fby hand.
After a cold start, let the engine warm up with a few
load cycles.
1
2
3
317TI005 KN
1
5903TI002 KN

Technical Information 40.2010 Page 7
TI_40_2010_13_01_02.fm
3.5 Summer and winter operation
3.5.1 At temperatures below +10 °C
Pre-heat carburetor
Moving a shutter causes heated air to be drawn in
from around the cylinder and mixed with cold air in
order to prevent carburetor icing.
An arrow on the shroud (1) shows the position of the
shutter (2) for summer or winter operation.
Key to symbols
Symbol "Sun" = summer operation
Symbol "Snowflake" = winter operation
.Unscrew and remove screw (3) on shutter
.Remove shutter (2) from the shroud
.Rotate shutter (2) from summer position to
winter position and reinsert
.Screw the screw (3) through the shutter into the
shroud
3.5.2 At temperatures between +10 °C and
+20 °C
Within this temperature range, the machine can
normally be operated with the shutter (2) in summer
position. Change the position of the shutter as
necessary.
2
317TI008 KN
1
2
3
317TI009 KN

Page 8 Technical Information 40.2010
TI_40_2010_13_01_02.fm
3.5.3 At temperatures above +20 °C
.Always return the shutter (2) to summer position
.Do not use the machine in winter operation at
temperatures above +20 °C, otherwise there is
a risk of engine damage due to overheating
3.5.4 At temperatures below -10 °C
Under extreme winter conditions with the following
conditions
– Temperatures below -10 °C
– Powdered or drifting snow
use of the "cover plate kit", which is available as a
special accessory, is recommended.
3.5.5 Cover plate kit
The "cover plate kit" contains the following parts for
covering the machine:
4Cover plate for partially covering the slits in the
starter housing
5Filter insert made of cloth and plastic for the air
filter
– O-ring for the filler cap
– Information sheet describing conversion of the
machine
After installation of the cover plate kit:
.Set shutter (2) to winter operation
.if the chain saw is extremely cold (frost
formation) – after starting, bring the engine up to
operating temperature at increased idle speed
(cutting attachment rotates!)
3.5.6 At temperatures above -10 °C
.Reconvert the machine and replace the parts
from the "cover plate kit" with the parts for
summer operation
The O-ring installed on the filler cap with the "cover
plate kit" can remain on the machine.
Depending on the ambient temperature:
.Set shutter to summer or winter operation
2
317TI010 KN
2
4
5
317TI011 KN

Technical Information 40.2010 Page 9
TI_40_2010_13_01_02.fm
3.6 Gearbox
3.6.1 Versions with standard drive tube and
long drive tube, see b4.4
A new, maintenance-free gearbox with a gearhead
angle of 35° is used for the series FS 460 C in the
version with a standard drive tube and long drive
tube.
Gearhead angle 35°
3.6.2 Version with short drive tube, see b4.4
A new, maintenance-free gearbox with a gearhead
angle of 25° is used for the series FS 460 C in the
version with a short drive tube and sawing
handlebars.
Gearhead angle 25°
3.7 New deflectors and limit stops
3.7.1 Versions with standard drive tube and
long drive tube, see b4.4
The optimal deflector is available for each
application:
1Deflector for mowing heads,
Diameter of cutting circle: 480 mm
2Deflector for grass cutting blades and brush
knives
3Deflector for shredder blade
4Limit stop 200 mm for circular saw blades
5Limit stop 225 mm for circular saw blades
All new deflectors and limit stops are fastened with
3 screws secured against loss.
For details about the approved deflectors and limit
stops, see b5.1.
317TI012 KN
317TI013 KN
317TI014 KN
5
4
3
2
1

Page 10 Technical Information 40.2010
TI_40_2010_13_01_02.fm
3.7.2 Version with short drive tube, see b4.4
1Limit stop 200 mm for circular saw blades
2Limit stop 225 mm for circular saw blades
The new limit stops are fastened with 3 screws
secured against loss.
For details about the approved deflectors and limit
stops, see b5.2.
3.8 4-point anti-vibration system
Four anti-vibration elements for damping vibrations
are installed between the engine and the drive tube,
In addition to rubber buffers and annular buffers as
anti-vibration elements in the area of the engine,
steel springs are used as anti-vibration elements in
the area of the handlebars. The 4-point anti-
vibration system ensures a very low vibration level,
optimal control and reduced operating effort.
3.9 New full harnesses
3.9.1 Universal harness ADVANCE
– Functional, modern shape – outstanding
handling and ergonomics
– Very low weight: 0.74 kg
– Available in two sizes
The new universal harness ADVANCE includes an
exhaustive information sheet about putting on the
harness properly and the ways in which it can be
adjusted.
1
2
317TI015 KN
317TI017 KN
317TI018 KN

Technical Information 40.2010 Page 11
TI_40_2010_13_01_02.fm
3.9.2 Forestry harness ADVANCE
– Functional, modern shape – outstanding
handling and ergonomics when sawing
– Central chest clasp
– Closed hip belt
– Freely suspended leg panel – high freedom of
movement
– Low weight: 0.97 kg
– Available in two sizes
The new forestry harness ADVANCE includes an
exhaustive information sheet about putting on the
harness properly and the ways in which it can be
adjusted.
4. Specifications
4.1 Engine
4.2 Fuel system
The STIHL one-cylinder, two-stroke engine uses
mixture lubrication and requires a mixture of
gasoline and engine oil.
4.2.1 Fuel
4.2.2 Fuel tank
317TI019 KN
STIHL single cylinder two-stroke engine
Displacement: 45.6 cm3
Bore: 44 mm
Stroke: 30 mm
Engine power to ISO 8893: 2.2 kW
Speed at max. output: 9500 rpm
Max. torque: 2.7 Nm
Idle speed: 2700 rpm
Clutch engages at: 4200 rpm
Cut-off speed: 12300 rpm
Starter
Starter rope: 3.0 mm x 1010 mm
Pull-out reserve: 1 to 2 turns
Mixing fuel: See Instruction Manual
Capacity: 750 cm3(0.75 l)

Page 12 Technical Information 40.2010
TI_40_2010_13_01_02.fm
4.2.3 Carburetor
4.3 Ignition system
4.4 Handle version, drive tube, antivibration
system
1) Version with standard drive tube
2) Version with long drive tube
3) Version with short drive tube
4.5 Gearbox
1) Version with standard drive tube, see b4.4
2) Version with long drive tube, see b4.4
3) Version with short drive tube, see b4.4
4) maintenance-free
4.6 Weight / dimensions
1) Version with standard drive tube, see b4.4
2) Version with long drive tube, see b4.4
3) Version with short drive tube, see b4.4
4.7 Sound and vibration levels
See Instruction Manual; for further details
concerning compliance with the Physical Agents
Directive Vibration 2002/44/EC, see
www.stihl.com/vib/
All-position diaphragm carburetor with integral fuel
pump
No manual carburetor
adjustment required see b2.2.6
Service work on carburetor see b9.9
Ignition module with integrated electronic speed
limiter
Spark plug (suppressed): NGK CMR6H
Electrode gap: 0.5 mm
Handle version: Mowing
handlebars 1) 2)
Sawing
handlebars 3)
Drive tube diameter: 28 mm
Drive tube length: 1360 mm 3)
1475 mm 1)
1535 mm 2)
Antivibration system: 4-point
Drive shaft: Hollow shaft, multi-
splined
Transmission ratio: 1:1.45 1) 2)
1:1.27 3)
Gearhead angle: 35° 1) 2)
25° 3)
Max. output shaft speed
(tool):
8450 rpm 1) 2)
9690 rpm 3)
Lubricant: STIHL gear lubricant
for brushcutters
Fill quantity: 9.8 g
Top-up quantity: -- 4)
dry, without cutting attachment
and deflector:
8.4 kg 3)
8.5 kg 1)
8.6 kg 2)
Total length without cutting
attachment:
1675 mm 3)
1790 mm 1)
1850 mm 2)

Technical Information 40.2010 Page 13
TI_40_2010_13_01_02.fm
5. Cutting attachments
Observe the permissible combinations of cutting
attachments, deflectors, limit stops and harnesses,
which vary depending on the version. Observe the
additional information in the Instruction Manual
5.1 Versions with standard drive tube and
long drive tube, see b4.4
5.1.1 Mowing heads and deflector
Full harness must be used.
5.1.2 Grass cutting blades, brush knives and
deflector
Full harness must be used.
5.1.3 Shredder blade and deflector
Full harness must be used.
Designation Part number
1Mowing head
STIHL SuperCut 40-2 4003 710 2140
2 Mowing head
STIHL AutoCut 40-2 4003 710 2125
3Mowing head
STIHL AutoCut 40-4 4005 710 2100
4 Mowing head
STIHL TrimCut 41-2 4003 710 2104
5 Mowing head
STIHL PolyCut 41-3 4003 710 2113
6Deflector only for mowing
heads 4147 710 8100
4
1
5
6
3
2
5903TI003 KN
Designation Part number
7 Grass cutting blade 230-4 4000 713 3801
8Grass cutting blade 255-8 4000 713 3802
9Grass cutting blade 250-40
Spezial 4000 713 3806
10 Brush knife 305-2 Spezial 4000 713 4103
11 Brush knife 300-3 4119 713 4100
12 Deflector for grass cutting
blades and brush knives 4147 710 8101
Designation Part number
13 Shredder blade 270-2 4000 713 3903
14 Deflector for shredder
blade 4147 710 8102
9
11
10
78
12
5903TI004 KN
13
14
5903TI005 KN

Page 14 Technical Information 40.2010
TI_40_2010_13_01_02.fm
5.1.4 Circular saw blades and limit stop
Full harness must be used.
5.2 Version with short drive tube, see b4.4
5.2.1 Circular saw blades and limit stop
Full harness must be used.
Designation Part number
15 Circular saw blade 200-44,
scratcher tooth 4000 713 4200
16 Circular saw blade 200-22,
chisel tooth 4119 713 4200
17 Limit stop 200 4147 710 8200
18 Circular saw blade 225-48,
scratcher tooth 4000 713 4205
19 Circular saw blade 225-24,
chisel tooth
4110 713 4204
4000 713 4207
20 Circular saw blade 225-36,
carbide tipped 4000 713 4211
21 Limit stop 225 4147 710 8201
15 16 17
18
19
20
21
5903TI006 KN
Designation Part number
1Circular saw blade 200-44,
scratcher tooth 4000 713 4200
2Circular saw blade 200-22,
chisel tooth 4119 713 4200
3Limit stop 200 4147 710 8210
4Circular saw blade 225-48,
scratcher tooth 4000 713 4205
5Circular saw blade 225-24,
chisel tooth
4110 713 4204
4000 713 4207
6Circular saw blade 225-36,
carbide tipped 4000 713 4211
7Limit stop 225 4147 710 8211
123
4
5
6
7
317TI027 KN

Technical Information 40.2010 Page 15
TI_40_2010_13_01_02.fm
6. Accessories
Designation Part number Use
STIHL gear lubricant for brushcutters Lubrication between rope rotor and starter post
– Tube 80 g 0781 120 1117
– Tube 225 g 0781 120 1118
STIHL special lubricant 0781 417 1315 Coating the rewind spring in the starter
Cover plate kit 4147 007 1001 Under extreme winter conditions
Full harnesses:
– Universal harness ADVANCE 4147 710 9002
– Universal harness ADVANCE XXL 4147 710 9004
– Forestry harness ADVANCE 4147 710 9003
– Forestry harness ADVANCE XXL 4147 710 9009
Chest strap 0000 790 7700 for universal harness ADVANCE
Tool backpack 4147 881 5700

Page 16 Technical Information 40.2010
TI_40_2010_13_01_02.fm
7. Service accessories
7.1 New special tools
7.2 Existing special tools
The existing special tools are listed in the Service
Manual for STIHL FS 240 C, FS 260 C, FS 360 C,
FS 410 C, FS 460 C.
Designation Part number Use
1Setting gauge 0000 890 6400 Setting the air gap between ignition module and
flywheel
2Press sleeve 4147 893 2400 Press in oil seal
3Flange 5910 850 4201 Leak testing
4Puller 5910 890 4408 Removing the drive pinion of the gearbox
5Sleeve 5910 893 1709 Mounting the hookless snap ring
6Ring 5910 893 7005 Place on the clutch housing to protect the guide
sleeves
7Puller 5910 890 4503 Removing the flywheel and the starter-side half of the
crankcase
23
1
4
5
6
7
317TI028 KN

Technical Information 40.2010 Page 17
TI_40_2010_13_01_02.fm
7.3 Aids
8. Spare parts
The spare parts lists will be available in time for the
market launch and are already contained on the
03/2010 edition of the STIHL Service
Communication System DVD.
9. Servicing
The specific national safety regulations and the
safety instructions in the instruction manual must be
observed if the machine has to be started up during
servicing.
9.1 Troubleshooting plan
The flow charts that follow deal with specific parts
diagnosis and troubleshooting for the M-Tronic
engine management system.
The flow charts help you to take the correct step at
the correct time.
Designation Part number Use
Set of gaskets 4147 007 1600 Engine
Set of carburetor parts 4147 007 1700 Carburetor
Grease (225 g tube) 0781 120 1111 Lubricating oil seals, sliding and bearing
points
Press fluid OH 723 0781 957 9000
STIHL gear lubricant for brushcutters Lubricating the gearbox and lubrication
between the rope rotor and starter post
– Tube 80 g 0781 120 1117
– Tube 225 g 0781 120 1118
STIHL multi-purpose grease Lubricating the drive shaft
– Tube 80 g 0781 120 1109
– Tube 225 g 0781 120 1110
Tube of sealant Dirko HT red 0783 830 2000 Sealing the crankcase
Standard solvent-based degreasant not
containing any chlorinated or
halogenated hydrocarbons
Cleaning mating surfaces and
carburetor, cleaning the crankshaft stub
and the cone in the flywheel

Page 18 Technical Information 40.2010
TI_40_2010_13_01_02.fm
9.1.1 Engine does not start
Is it possible to start the
engine?
no
Move choke lever to position }Troubleshooting completed
Check ignition system
according to "Flow chart
ignition system troubleshooting“,
see Service Manual
Check ignition
(spark plug, spark plug boot, ignition
spark)
Ignition spark
present?
Mechanically check start detection
(b9.6.1)
Clean switch gear
replace if necessary
Electrically check start detection
(b9.6.2)
yes
Mechanically
OK?
Are target values
attained?
Look for a fault in the fuel path,
check engine for leaks
Replace switch gear if necessary
no
yes
no
no
Engine does not start
Is it possible to start
the engine?
yes yes
no
Check solenoid valve (b9.5) Are target values
attained?
Replace switch gear and/or
carburetor
yes
yes
no

Technical Information 40.2010 Page 19
TI_40_2010_13_01_02.fm
9.1.2 Engine does not start in position }
Is it possible to start
the engine?
Troubleshooting completed
Mechanically check start detection
(b9.6.1)
Clean switch gear
replace if necessary
Electrically check start detection
(b9.6.2)
yes
Mechanically
OK?
Are target values
attained?
Look for a fault in the fuel path
(inlet needle, lever, spring,
membrane),
check engine for leaks
Replace switch gear if necessary
yes
no
no
Engine does not start in position
}–
engine floods. The flooded engine can
be started in position F
yes
no

Page 20 Technical Information 40.2010
TI_40_2010_13_01_02.fm
9.1.3 Engine speed drops under load –
low power
Look for a fault in the fuel path,
check engine for leaks
Check air filter, replace if necessary
Troubleshooting completed
Cut-off speed =
12300 rpm?
yes no
Engine speed drops under load – low
power
Remove cutting attachment, all
mounting hardware and thrust plate.
Let the machine run three to four
times for approx. 30 s in the cut-off
range
This manual suits for next models
1
Table of contents
Other Stihl Saw manuals
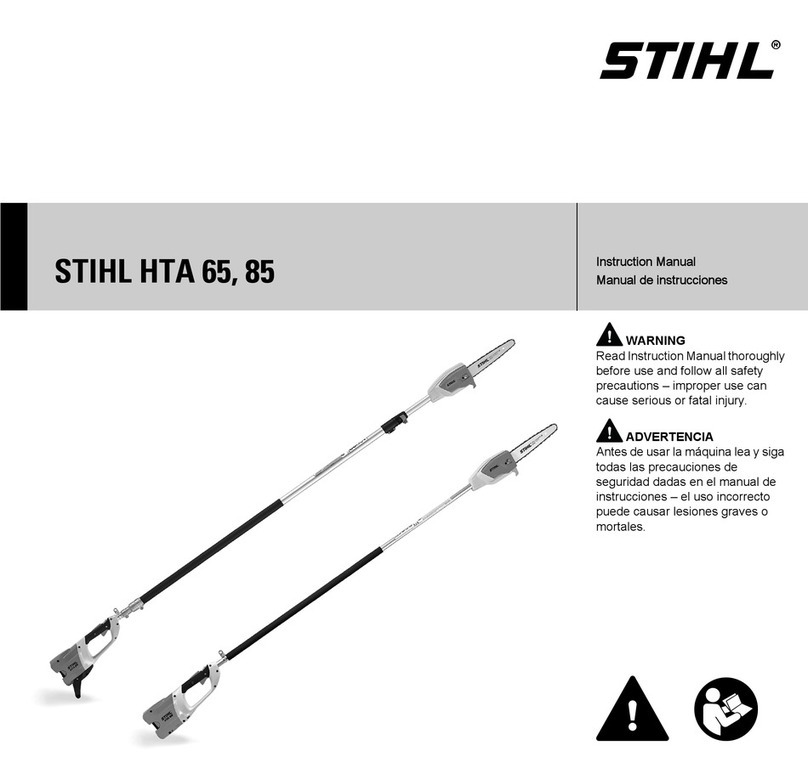
Stihl
Stihl HTA 65 User manual
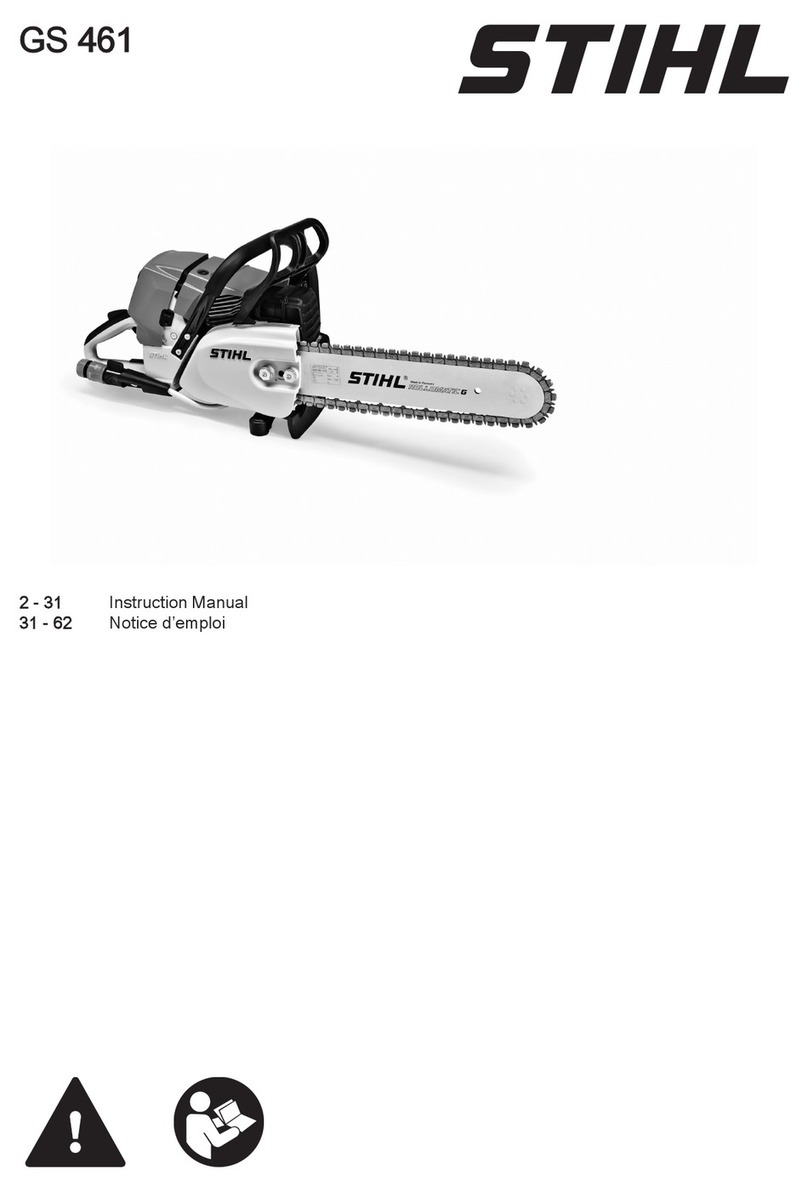
Stihl
Stihl GS 461 User manual
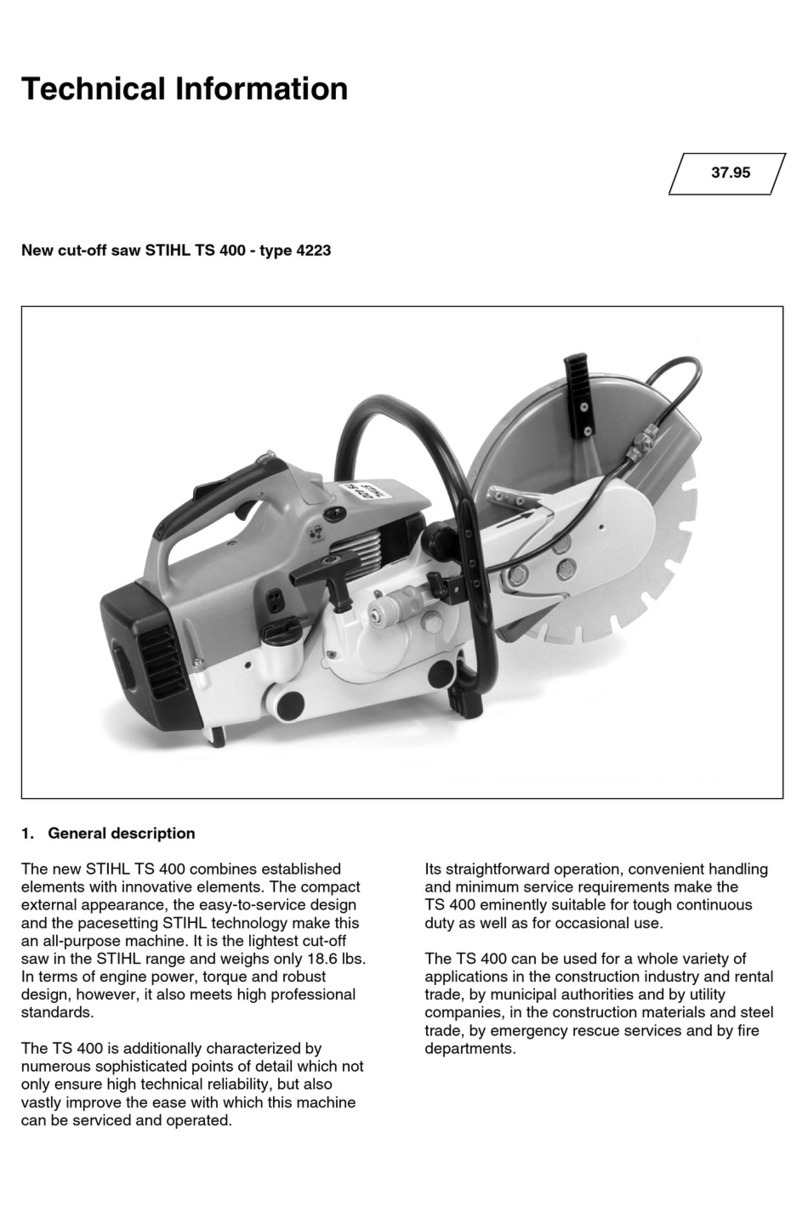
Stihl
Stihl TS 400 Cutquick Manual

Stihl
Stihl Cutquik TS 410 User manual
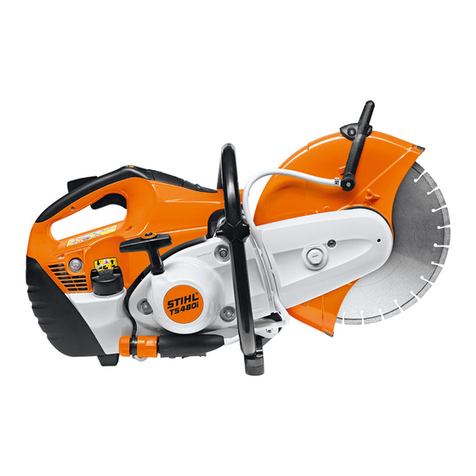
Stihl
Stihl TS 480i User manual
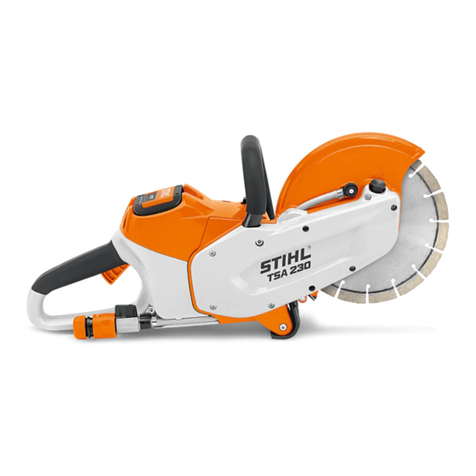
Stihl
Stihl TSA 230 User manual
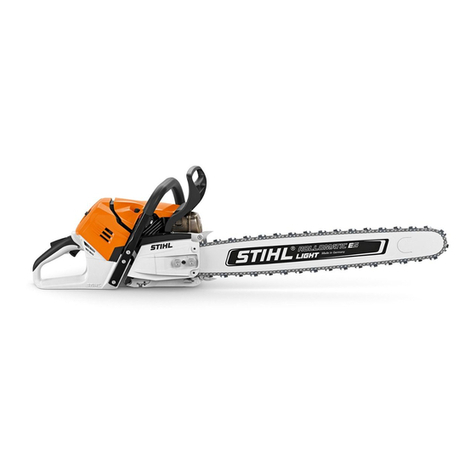
Stihl
Stihl MS 500i User manual
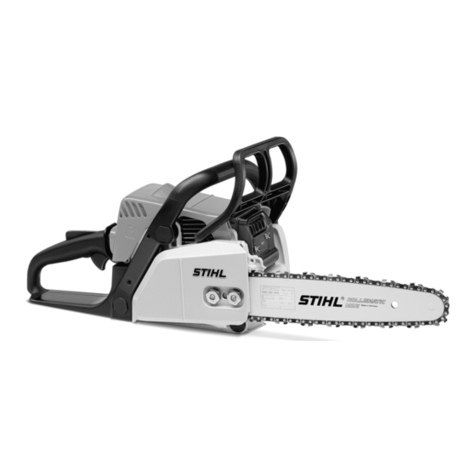
Stihl
Stihl MS 180 User manual
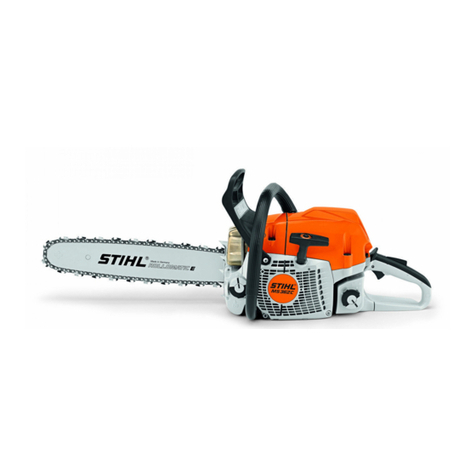
Stihl
Stihl MS 362 User manual
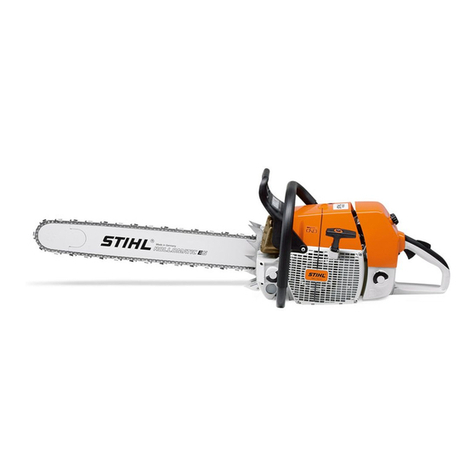
Stihl
Stihl MS 880 User manual
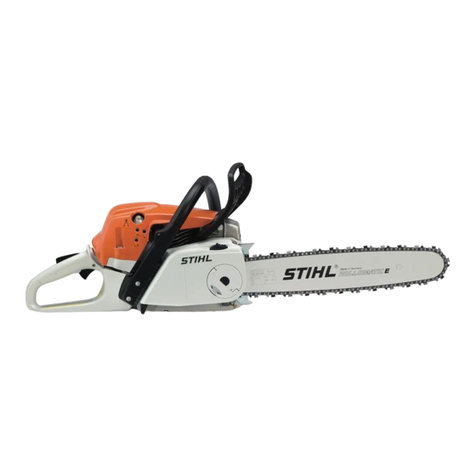
Stihl
Stihl MS 291 C-Q User manual
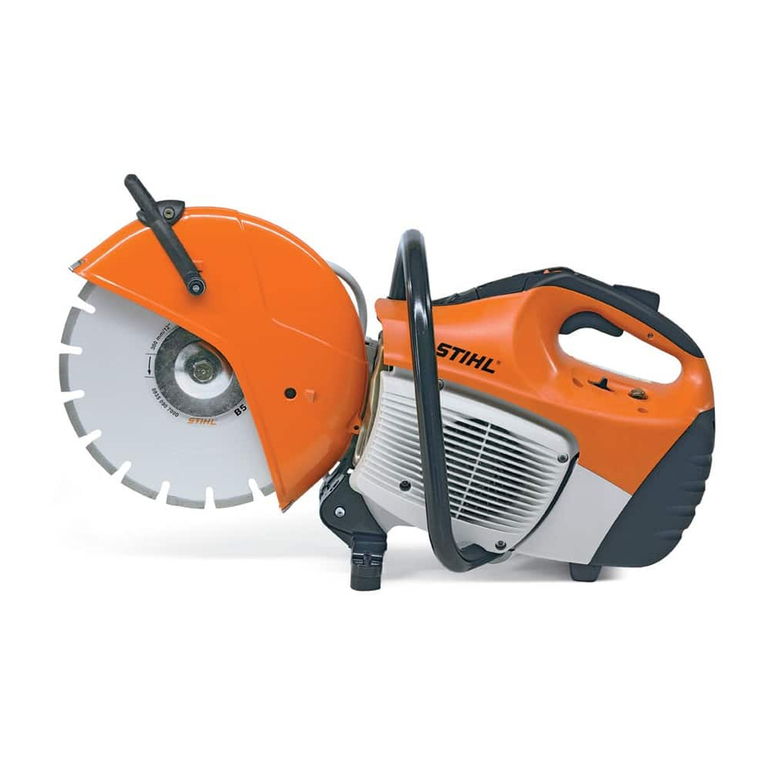
Stihl
Stihl TS 410 User manual
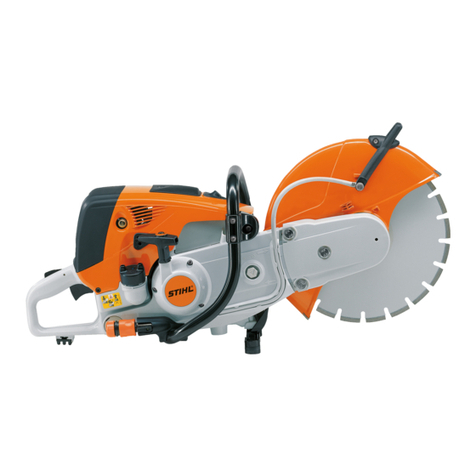
Stihl
Stihl TS 700 User manual
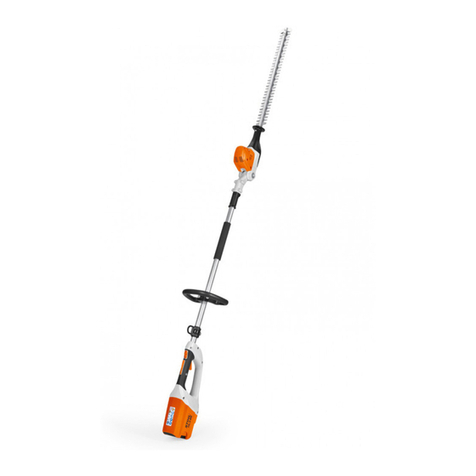
Stihl
Stihl HLA 65 User manual
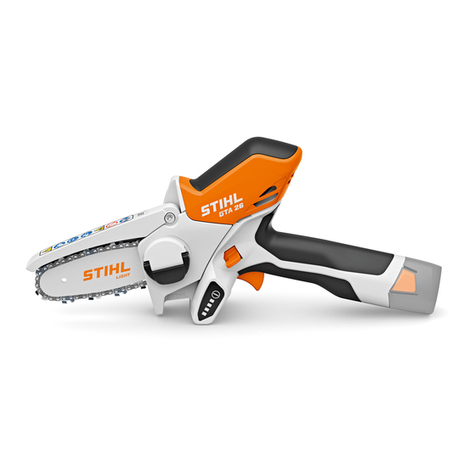
Stihl
Stihl GTA 26 User manual
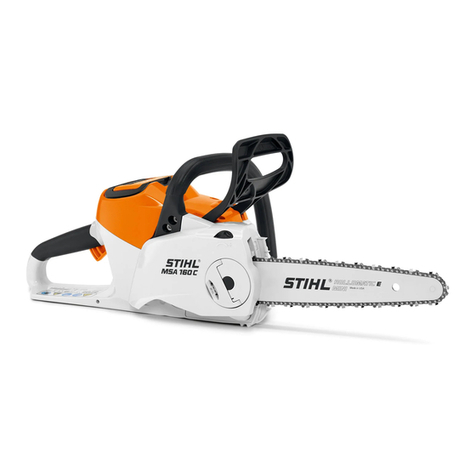
Stihl
Stihl MSA 160.0 C User manual
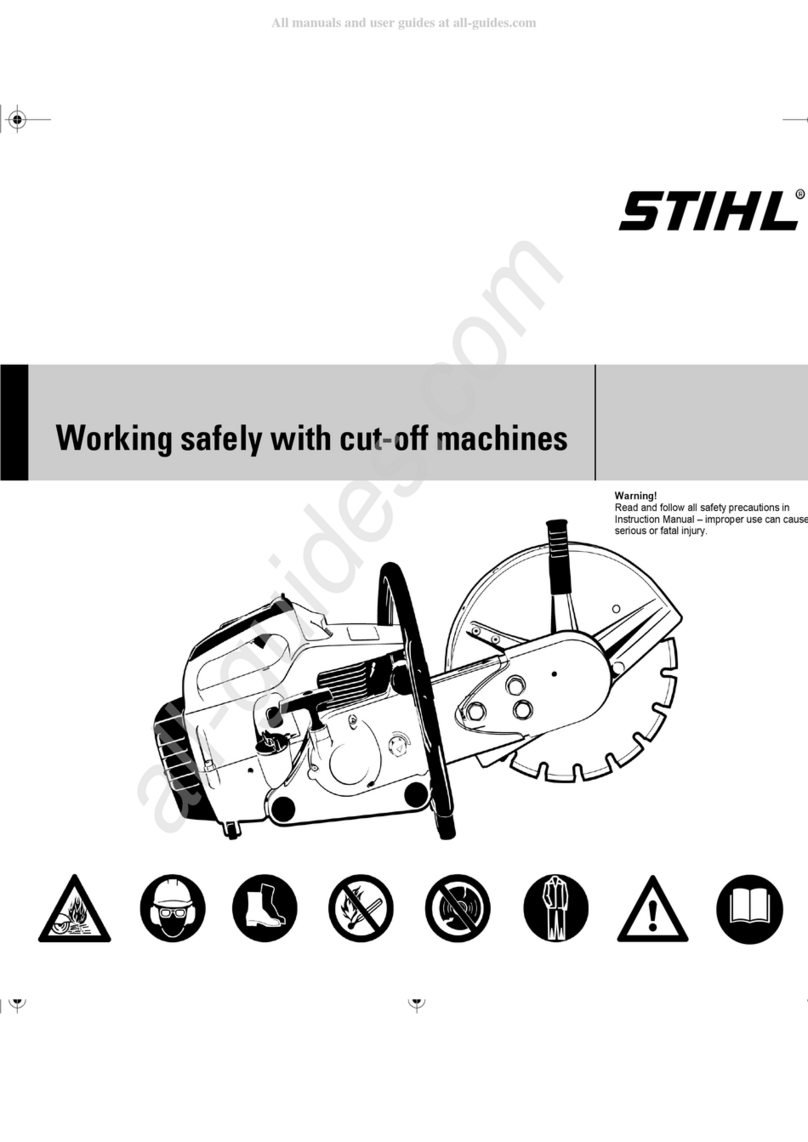
Stihl
Stihl Cutquik TS-420 User manual
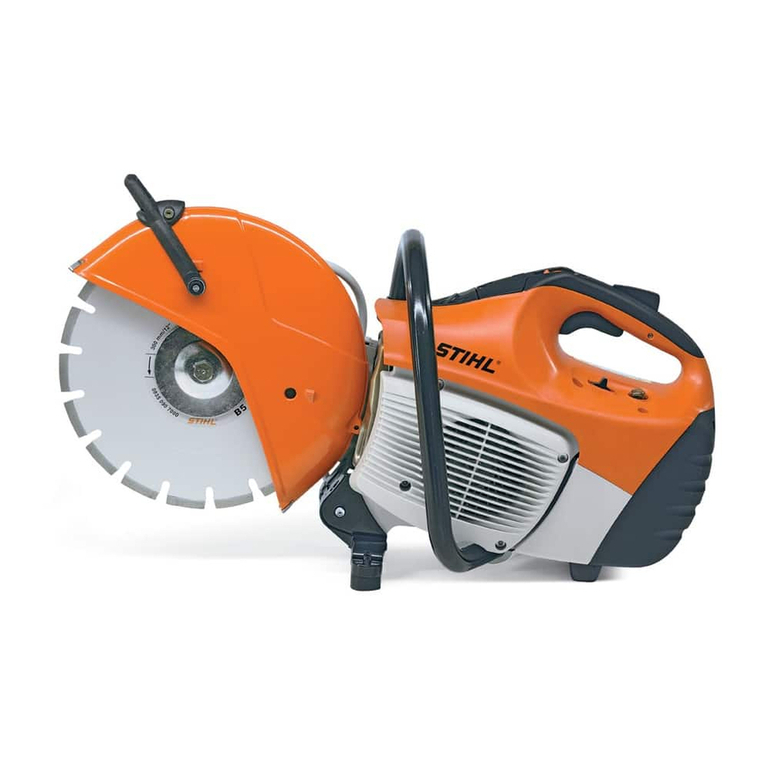
Stihl
Stihl TS 410 User manual

Stihl
Stihl TS 510 Cutquik User manual
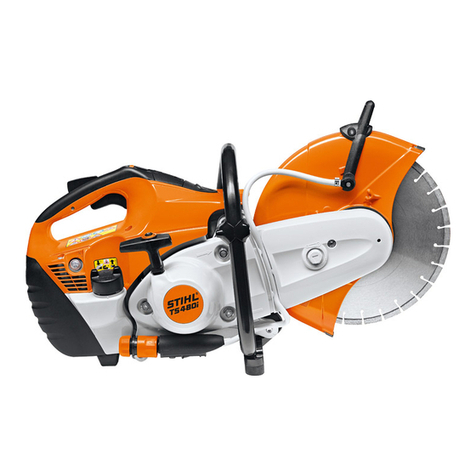
Stihl
Stihl TS 480i User manual