SUMTOR HSC86A User manual

HSC86A
Digital hybrid servo driver
user's Guide
Address: No. 118-1, Liangdong Road, Liangxi District, Wuxi City
Phone: 0510-82729456
Fax: 0510-82729457
E-mail:sales@sumtor.com
Http://www.sumtor.com
All copyrights must not be reproduced
【Please read this manual carefully before use to avoid damaging the drive】

HSC86AInstruction manual of hybrid servo driver
1
table of Contents
一、Product Brief .........................................2
1. Overview ...............................................2
2. Features ...............................................2
3. Application field ......................................3
二、Electrical, mechanical and environmental indicators ...3
1. Electrical indicators ..................................3
2. Use environment and parameters .........................4
3. Mechanical structure size chart ........................4
4. Thermal considerations .................................4
三、Driver interface and wiring introduction ..............5
1. Interface description ..................................5
2. Control signal interface circuit .......................8
3. Control signal timing diagram ..........................9
4. Control signal mode setting ...........................10
5. Wiring requirements ...................................10
四、DIP switch setting ...................................11
五、Protective function ..................................13
六、common problem .......................................13
1.Common problems and solutions in the application .......13
2.Frequently asked questions about drives ................14
Our company product warranty terms .......错误!未定义书签。

HSC86AInstruction manual of hybrid servo driver
2
一、Product Brief
1.Overview
HSC86A is a new type of low-voltage hybrid servo product developed by our company based
on many years of experience in low-voltage servo systems. This product uses the latest
DSP digital processing chip and advanced variable current and variable frequency control
algorithm technology to provide a high level for equipment manufacturers. Cost-effective
hybrid servo drive solution. HSC86A has a compact structure, small size, saves space,
and reduces electromagnetic interference between lines; it adopts better vibration
technology and low heat generation technology, which effectively solves the problems
of heat, vibration and noise of motors and drivers. Environmental protection.
2.Features
●Working voltage: AC and DC universal, AC input voltage 24 ~80VAC, recommended
working voltage 60VAC
●Maximum continuous output current 8.0A (advanced stepping servo overload capability)
●Accepts differential and single-ended pulse / direction commands, and has three
control modes of position / speed / torque
●Adopt FOC magnetic field positioning control technology and space vector pulse width
modulation (SVPWM) closed-loop control technology
●Adopt advanced variable current technology and frequency conversion technology,
effectively reduce the heat of motor and driver
●The number of pulses per revolution can be set by debugging software or code extraction
(subdivision)
●With over-voltage, under-voltage, over-current and over-tolerance protection
functions
●Single / double pulse mode, optional pulse effective edge
●The maximum pulse frequency of the control command is 500KHz (the factory default
is 200KHz)
●Pulse, direction and enable signal input interface level is compatible with 4.5-28V

HSC86AInstruction manual of hybrid servo driver
3
●With serial port RS232 debugging function, but need to use the company's special
serial debugging cable
●Performance: stable speed, small overshoot, small tracking error, low heating of
motor and driver
3.Application field
Suitable for all kinds of small and medium-sized automation equipment and instruments,
such as: laser machines, inkjet machines, small and medium-sized engraving machines,
electronic processing equipment, automatic grasping equipment, special CNC machine
tools, packaging equipment and robots. It is especially effective in devices where users
expect low noise and high speed.
二、Electrical, mechanical and environmental indicators
1.Electrical indicators
parameter
HSC86A
Minimum
value
Typical
value
Maximum
unit
Continuous output current
0.5
-
13
A
Power supply voltage (AC / DC)
24
60
80
VAC
Logic input current
6
10
16
mA
Logic input voltage
4.5
5
28
Vdc
Pulse frequency
0
200
500
kHz
Pulse high width
1.5
-
-
uS
Position error control accuracy
-
±1
-
Pulse
Speed control accuracy
-
±2
-
rpm
Maximum acceleration (no load)
-
100
-
rpm /ms
Overvoltage protection voltage
90
VAC
Insulation resistance
100
-
-
MΩ

HSC86AInstruction manual of hybrid servo driver
4
Note: If the power input is DC, the input range is 24 ~ 110Vdc!!!
2.Use environment and parameters
cooling method
Natural cooling or forced air cooling
Use
environment
occasion
It cannot be placed beside other heat-generating equipment. Avoid dust, oil
mist, corrosive gas, excessive humidity and strong vibration. Combustible
gas and conductive dust are prohibited
temperature
-5℃~+45℃
humidity
40~90%RH
vibration
10~55Hz/0.15mm
Storage temperature
-20℃~+65℃
Use altitude
≤1000m
weight
约0.6KG
3.Mechanical structure size chart
The structure of HSC86A driver can match any type of two-phase hybrid motors of
Figure 1 Mechanical installation dimension drawing (unit: mm)
139
6
14.5
52
2-Φ4.5
97
151

HSC86AInstruction manual of hybrid servo driver
5
60 and 86 bases. The company mainly recommends hybrid servo motors of 3.0NM, 4.5NM,
8.5NM and 12NM, and can also match the hybrid servo motors of other manufacturers. The
number of encoder lines can be 250 to 5000 lines, but you need to contact our company
to provide motor parameters and match related programs according to different motors.
If the customer has higher requirements for low-speed vibration or high-speed
performance, it is recommended to contact our company. Our company will write an
algorithm for matching the motor according to the motor parameters, and the motor will
show perfect performance.
4. Thermal considerations
The reliable working environment temperature of the driver is usually within -5 ℃~
45 ℃, when the driver is working, the temperature is within 65 ℃, and when the motor
is working, the temperature is within 70 ℃. If necessary, install a fan near the driver
to force heat dissipation to ensure that the driver works reliably Work within the
temperature range.
三、Driver interface and wiring introduction
1.Interface description
1.1Control port
Use green 6 + 4Pin 3.81mm spaced terminals
Pin number
signal
Features
Explanation
1
PUL+
Pulse positive input
Compatible with 4.5V ~ 28V level signals
2
PUL-
Pulse negative input
3
DIR+
Positive direction input
4
DIR-
Direction negative input
5
ENA+
Enable positive input

HSC86AInstruction manual of hybrid servo driver
6
6
ENA-
Enable negative input
7
ALM+
Alarm signal positive output
Open collector OC output, maximum
pull-up level 24V, maximum output
current 100mA
8
ALM-
Alarm signal negative output
9
PEND+
In-position signal positive
output
Open collector OC output, maximum
pull-up level 24V, maximum output
current 100mA
10
PEND-
In-position signal negative
output
1.2Motor and power input ports
Use green 6Pin 5.0mm spaced screw terminals
Terminal number
symbol
Name
Explanation
1
A+
A-phase motor winding +
2
A-
A-phase motor winding-
3
B+
B-phase motor winding +
4
B-
B-phase motor winding-
5
AC
AC input
24V~ 80Vac
6
AC
AC input
24V~ 80Vac
1.3Encoder port
Use green 6Pin 3.81mm interval with screw terminals (note the positive and negative poles
of the power supply, do not reverse the positive and negative poles !!!)
Pin number
signal
Function Description
1
EB+
Encoder signal B + input
2
EB-
Encoder signal B-input
3
EA+
Encoder signal A+ input
4
EA-
Encoder signal A-input
5
VCC
Driver + 5V output, power supply for encoder
6
EGND
Driver GND output, power supply for encoder

HSC86AInstruction manual of hybrid servo driver
7
1.4Serial RS232 / RS485 communication interface
It can be connected to the PC through a serial port adapter device (serial adapter
device is optional) and a dedicated serial cable (prohibited live plugging and
unplugging). The function and parameter settings of the driver can be set through the
PC software, such as the subdivision and current value and effective edge required by
the customer, and the resonance point can be eliminated and adjusted.
Terminal
number
Symbol
Name
Explanation
1
+5V
5V positive terminal
External STU only
2
TXD
RS232 transmitter
3
RXD
RS232 receiver
4
GND
5V power ground
0V
Note: The HSC86A serial cable must be a special cable of our company, depending on
the user's condition, please confirm before use to avoid damage.
1.5LED status indicator
The green LED is the power indicator. When the drive is powered on, the LED is always
on; when the drive is turned off, the LED is off. The red LED is a fault indicator. When
a fault occurs, the indicator flashes in cycles of 5 seconds; when the fault is cleared
by the user, the red LED is often off. The red LED flashes at a frequency of 2 Hz, with
the LED on for 200 ms and off for 300 ms. The number of red LED flashes within 5 seconds
represents different fault information, the specific relationship is shown in the
following table:
Serial
number
Number of
flashes
Red indicator flashing
waveform
Fault description
1
1
Overcurrent fault (I peak ≥25A)
2
2
Overvoltage fault (Vac≥90V)

HSC86AInstruction manual of hybrid servo driver
8
3
5
Tracking error out of tolerance fault
When the drive fails, the drive will stop and prompt the corresponding fault code.
The fault can only be cleared when the user needs to power off and re-power on. When
the drive fails, the drive will save the latest fault in the drive's EEPROM in the form
of a queue, and the drive will save up to 10 latest historical faults. The user can read
the corresponding fault code through the PC and the text display.
2.Control signal interface circuit
HSC86A driver signal input interface can be differential signal input, common anode signal
single-ended input and common cathode signal single-ended input, built-in high-speed photoelectric
isolation coupler; output is triode open collector OC output, interface connection method is as follows:-
Figure 2 Input signal differential connection
Figure 3 Input signal single-ended common anode connection

HSC86AInstruction manual of hybrid servo driver
9
Figure 4 Input signal single-ended common cathode connection
Note: The voltage range of the signal input interface in the figure is 4.5 ~ 28Vdc. No
matter whether it is single-ended connection or differential connection, no series
current limiting resistor is required. For the external pull-up voltage of the output
interface, the maximum is 28Vdc, and the maximum output current is 100mA. According to
the external pull-up voltage, select the appropriate pull-up resistor. If the external
pull-up voltage is 24Vdc, the pull-up resistor is 2K. If The external pull-up voltage
is 12Vdc, and the pull-up resistor is 1K. If it is a drive relay or motor holding brake
coil, please consult our application engineers.
3.Control signal timing diagram
In order to avoid some misoperations and deviations, PUL-, DIR- and ENA- should meet
certain requirements, as shown in the following figure:

HSC86AInstruction manual of hybrid servo driver
10
Comment:
1) t1: ENA (enable signal) should be at least 5μs in advance DIR, determined to be high.
Under normal circumstances, it is recommended to hang in the air;
2) t2: DIR determines the state of high or low at least 1μs in advance of the falling edge of
PUL;
3) t3: pulse width is at least 1.5μs;
4) t4: Low level width is not less than 1.5μs.
4.Control signal mode setting
Pulse trigger edge selection: PC pulse software sets the pulse rising edge or falling edge trigger is
valid.
Single and double pulse selection: Single pulse or double pulse is set by PC software.
Direction selection: Set the initial running direction of the motor through the PC software.
5.Wiring requirements
1) In order to prevent the driver from being disturbed, it is recommended to use shielded cable for the
control signal, and the shielding layer is short-circuited with the ground wire. Except for special
t2
t4
t1
t3
t2
PUL
DIR
EN
A
>1us
>1us
>5us
高电平高于 3.5V
高电平高于 3.5V
低电平低于 0.5V
低电平低于 0.5V
Figure 5 Control signal timing
diagram

HSC86AInstruction manual of hybrid servo driver
11
requirements, the shielded wire of the control signal cable is grounded at one end: the upper end of the
shielded wire is grounded and the shielded wire End of the drive is floating. The same machine is only
allowed to be grounded at the same point. If it is not a real ground wire, the interference may be serious.
At this time, the shielding layer is not connected. If the conditions permit, thermal grounding
technology is most effective for shielding.
2) The pulse and direction signal lines and the motor line are not allowed to be bundled side by side,
preferably separated by at least 10cm or more, otherwise the motor noise will easily interfere with the
pulse direction signal and cause motor positioning inaccuracy, system instability and other faults.
3) If one power supply is used for multiple drives, parallel connection should be adopted at the power
supply, and it is not allowed to go to one first and then to another chain connection.
4) It is strictly forbidden to plug and unplug the driver terminal with electricity. When the live motor
stops, a large current still flows through the coil. Pulling and plugging the terminal will cause a huge
instantaneous induced electromotive force to burn the driver.
5) It is strictly forbidden to insert the wire head into the terminal after tin, otherwise the terminal may
be damaged due to overheating of the contact resistance.
6) The wiring head should not be exposed outside the terminal to prevent accidental short circuit and
damage to the driver.
四、DIP switch setting
HSC86A digital integrated low-voltage servo driver adopts 8-bit dial switch to
set the subdivision accuracy (electronic gear ratio), the initial direction of
motor rotation, self-test and function mode selection. The detailed description
is as follows:
SW1
SW2
SW3
SW4
SW5
SW6
SW7
SW8
Direction and function mode settings
Subdivision accuracy (electronic gear ratio)
Motor selection

HSC86AInstruction manual of hybrid servo driver
12
Pulse/rev
S1
S2
S3
S4
Default
On
On
On
On
800
Off
On
On
On
1600
On
Off
On
On
3200
Off
Off
On
On
6400
On
On
Off
On
12800
Off
On
Off
On
25600
On
Off
Off
On
51200
Off
Off
Off
On
1000
On
On
On
Off
2000
Off
On
On
Off
4000
On
Off
On
Off
5000
Off
Off
On
Off
8000
On
On
Off
Off
10000
Off
On
Off
Off
20000
On
Off
Off
Off
40000
Off
Off
Off
Off
Subdivision accuracy (electronic gear ratio): When S1, S2, S3, S4 are all on, the driver
microstep subdivision adopts the internal default microstep subdivision number of the driver. The
electronic gear ratio can also be set through the debugging software. SW5 sets the motor direction,
when it is ON, the motor rotates clockwise (CW), when it is OFF, the motor rotates
counterclockwise (CCW); SW6 function mode selection, when it is OFF, the drive is space vector
control mode (FOC) , When it is on, the driver moves in point mode (PM), which has better
start-stop effect.
Motor
SW7
SW8
说明
60-30
ON
ON
Adapt to our 60
series 3NM closed
loop motor
86-45
OFF
ON
Adapt to our 86
series 4.5NM closed
loop motor
86-85
ON
OFF
Adapt to our 86
series 8.5NM closed
loop motor

HSC86AInstruction manual of hybrid servo driver
13
86-120
OFF
OFF
Adapt to our 86
series 12NM closed
loop motor
五、Protective function
1)Overvoltage protection
When the input voltage of HSC86A is higher than 90VAC, the driver will stop working.
At this time, the fault must be eliminated and reset after power on again.
2)Undervoltage protection
When the input voltage of HSC86A is lower than 15VAC, the driver will stop working. At
this time, the fault must be eliminated and reset after power on again.
3)Overcurrent protection
When overcurrent occurs in HSC86A, the driver will stop working. At this time, the fault
must be eliminated and reset after power on again.
4)Tracking error
When the tracking error exceeds the tolerance of HSC86A, the driver stops working. At
this time, the fault must be eliminated and reset after power on again.
六、common problem
1.Common problems and solutions in the application

HSC86AInstruction manual of hybrid servo driver
14
phenomenon
Possible problem
solution
The motor does
not rotate
Power light is off
Check the power supply circuit, normal
power supply
Powerful motor
shaft
The pulse signal is weak, the signal current
is increased to 7-16mA
Subdivision is too
small
Select the right segment
Drive is protected
Power cycle
Enable signal is
low
This signal is pulled high or not connected
Does not respond to
control signals
Not powered
Motor wire is
broken
Check and connect
The voltage is too
high or too low
Check the power supply
Damaged motor or
driver
Replace the motor or drive
Inaccurate
location
Signal is disturbed
Eliminate interference
Shielding ground is
not connected or
not connected
Reliable ground
Motor wire is
broken
Check and connect
Segmentation error
Set subdivision
Stall when the
motor accelerates
The acceleration
time is too short
Increased acceleration time
Motor torque is too
small
Choose high torque motor
Low voltage
Appropriately increase the voltage
2.Frequently asked questions about drives
1)What are the advantages of subdividing servo drives?
●Since the step angle of each step is reduced, the step uniformity is improved, so the control
accuracy can be improved.
●It can greatly reduce the vibration of the motor. Low-frequency oscillation is an inherent
characteristic of the stepper motor. Subdivision is the best way to eliminate it.

HSC86AInstruction manual of hybrid servo driver
15
●It can effectively reduce torque ripple and increase output torque.
●These advantages are generally recognized by users and bring them benefits, so it is
recommended that you choose a subdivision driver.
2)Why does my motor only run in one direction?
●It is possible that the direction signal is too weak, or the polarity of the wiring is wrong, or the signal
voltage is too high, and the direction current limiting resistor is burned out.
●The pulse mode does not match, the signal is pulse / direction, the drive must be set to this mode.
Our company product warranty terms
1 One year warranty
Our company provides a one-year warranty for defects in raw materials and
workmanship of its products from the date of shipment. During the warranty period,
our company provides free repair services for defective products.
2 Not covered by warranty
●Inappropriate wiring, such as reverse connection of positive and negative
power supply and live plugging
●Unauthorized changes to internal devices
●Use beyond electrical and environmental requirements
●Environmental heat dissipation is poor
3 Repair process
Please contact the relevant agent or the company's salesperson
4 Warranty restrictions
●The warranty scope of our company's products is limited to the product's
devices and processes (ie consistency).

HSC86AInstruction manual of hybrid servo driver
16
●Our company does not guarantee that its products can be adapted to the
customer's specific use, because the suitability is also related to the
technical index requirements, use conditions and environment of the use.
Other manuals for HSC86A
1
Table of contents
Other SUMTOR Servo Drive manuals
Popular Servo Drive manuals by other brands

Oriental motor
Oriental motor CSD2120-T Connection and Operation
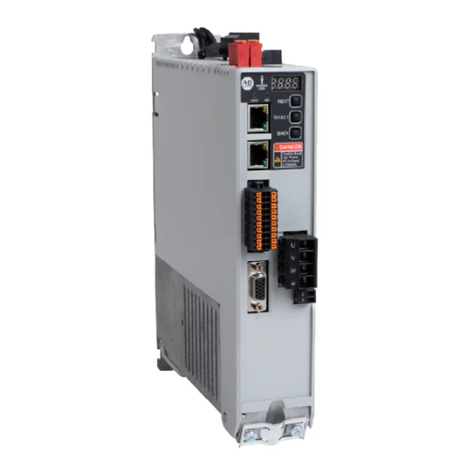
Rockwell Automation
Rockwell Automation Allen-Bradley Kinetix 5300 installation instructions
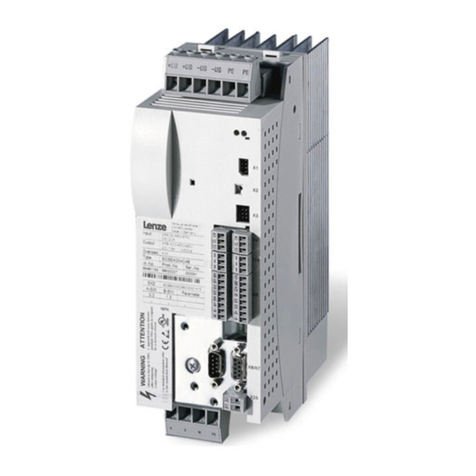
Lenze
Lenze ECSCS Series Mounting instructions
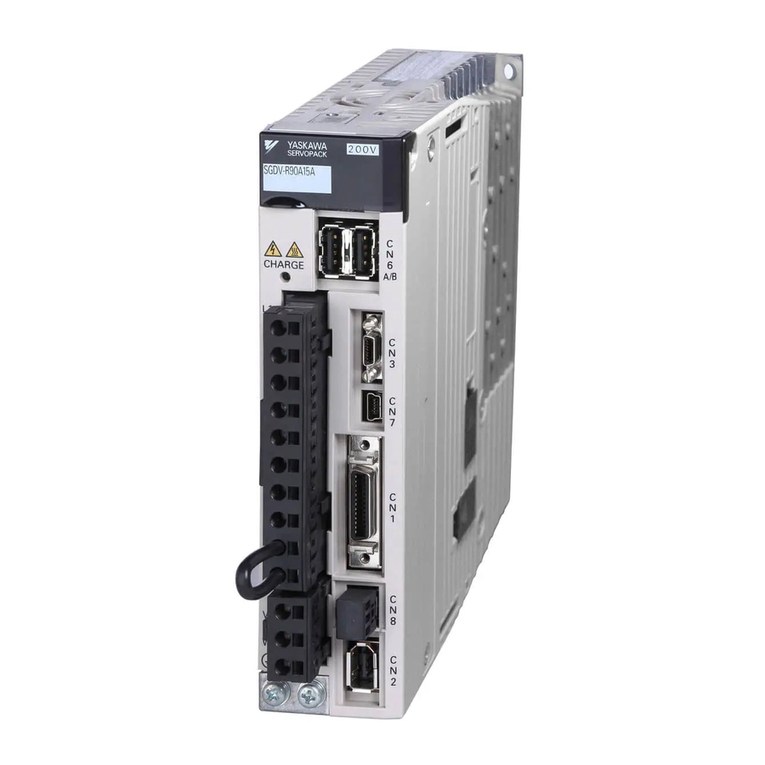
YASKAWA
YASKAWA SGDV SERVOPACK user manual
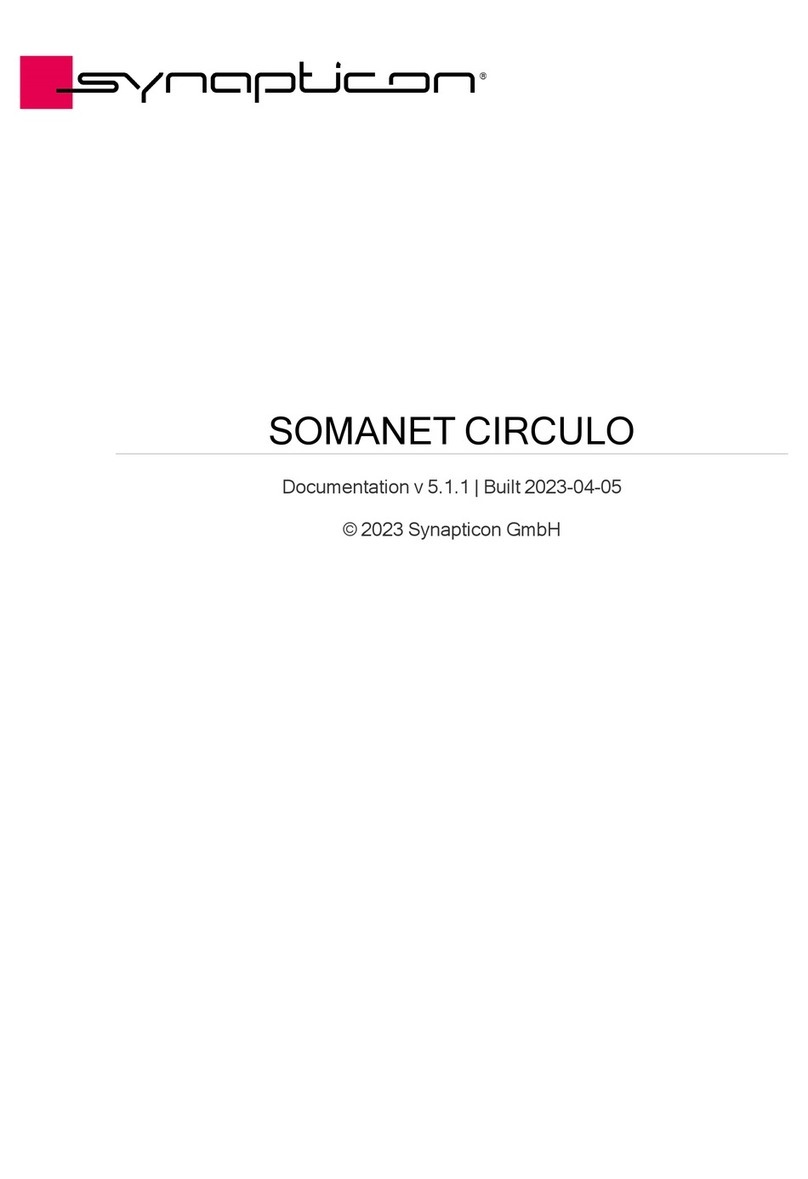
SYNAPTICON
SYNAPTICON SOMANET Circulo 7 manual
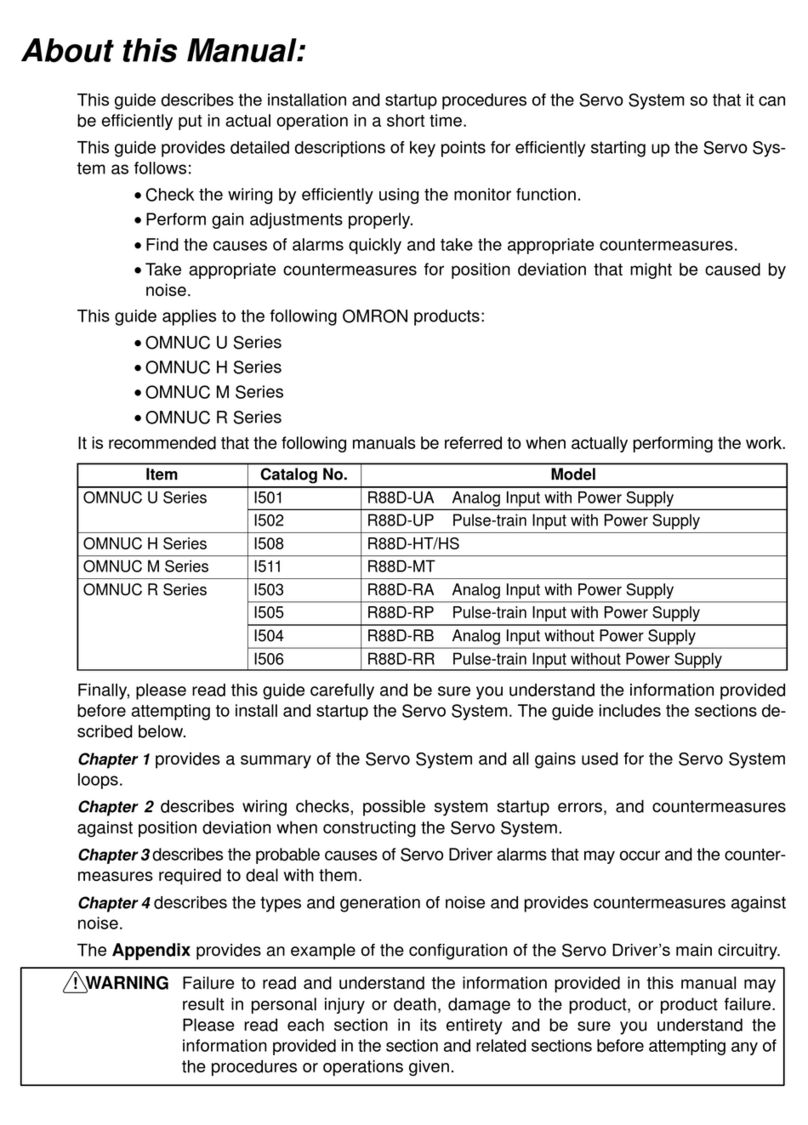
Omron
Omron R88D-UA manual