Elmo SimpliQ Line User manual

-~
ARTISAN
®
~I
TECHNOLOGY
GROUP
Your definitive source
for
quality
pre-owned
equipment.
Artisan Technology
Group
Full-service,
independent
repair
center
with
experienced
engineers
and
technicians
on staff.
We
buy
your
excess,
underutilized,
and
idle
equipment
along
with
credit
for
buybacks
and
trade-ins
.
Custom
engineering
so
your
equipment
works
exactly as
you
specify.
•
Critical
and
expedited
services
•
Leasing
/
Rentals/
Demos
• In
stock/
Ready-to-ship
•
!TAR-certified
secure
asset
solutions
Expert
team
ITrust
guarantee
I
100%
satisfaction
All
tr
ademarks,
br
a
nd
names, a
nd
br
a
nd
s a
pp
earing here
in
are
th
e property of
th
e
ir
r
es
pecti
ve
ow
ner
s.
Visit our website - Click HERE

Notice
This guide is delivered subject to the following conditions and restrictions:
•This guide contains proprietary information belonging to Elmo Motion Control Ltd. Such
information is supplied solely for the purpose of assisting users of the DC Trombone
servo drive in its installation.
•The text and graphics included in this manual are for the purpose of illustration and
reference only. The specifications on which they are based are subject to change without
notice.
•Information in this document is subject to change without notice.
Elmo Motion Control and the Elmo Motion Control logo are
registered trademarks of Elmo Motion Control Ltd.
Document no. MAN-DCTROIG (Ver. 1.602)
Copyright 2017
Elmo Motion Control Ltd.
All rights reserved.
Catalog Number

Revision History
Version Date Details
Ver. 1.0 Initial release
Ver. 1.1 Updated with new template
Ver. 1.2 Changes and updates to the following sections:
2.1, 2.2.6, 2.2.7, 2.3, 3.0, 3.11, 3.3.1, 3.4, 3.5, 3.5.2, 3.6, 3.7,
3.8, 3.9, 3.10, 4.1, 4.1.7, 4.3, 4.4.1, 4.6, 4.7
Ver. 1.3 Sections 4.3, 4.4.1: Auxiliary supply range: 18 to 30 V
Ver. 1.4 September 2012 Change the overvoltage in 800 V mode, Pin layout, UL
recognition, and further optional versions added
“Metronome” was replaced by the “Composer” software.
Ver. 1.401 February 2013 Added a caution and recommendation on the type of
cleaning solution to use for the Elmo unit.
Ver. 1.500 May 2013 Addition of heat-sink option to lower side of the drive.
Ver. 1.600 June 2014 Manual updated
Ver. 1.601 July 2014 General format updates
Ver. 1602 Oct 2014 Updated the Warranty Information section 1.5 and updated
the part number label in section 3.2

Elmo Worldwide
Head Office
Elmo Motion Control Ltd.
60 Amal St., P.O. Box 3078, Petach Tikva 4951360
Israel
Tel: +972 (3) 929-2300 • Fax: +972 (3) 929-2322 • info-il@elmomc.com
North America
Elmo Motion Control Inc.
42 Technology Way,Nashua, NH 03060
USA
Tel: +1 (603) 821-9979 • Fax: +1 (603) 821-9943 • info-us@elmomc.com
Europe
Elmo Motion Control GmbH
Hermann-Schwer-Strasse 3, 78048 VS-Villingen
Germany
Tel: +49 (0) 7721-944 7120 •Fax: +49 (0) 7721-944 7130 • info-de@elmomc.com
China
Elmo Motion Control Technology (Shanghai) Co. Ltd.
Room 1414, Huawen Plaza, No. 999 Zhongshan West Road, Shanghai (200051)
China
Asia Pacific
Elmo Motion Control APAC Ltd.
B-601 Pangyo Innovalley, 621 Sampyeong-dong, Bundang-gu, Seongnam-si, Gyeonggi-do,
South Korea (463-400)
Tel: +82-31-698-2010 • Fax: +82-31-801-8078 • info-asia@elmomc.com

DC Trombone Installation Guide
MAN-DCTROIG (Ver. 1.602)5
Table of Contents
Chapter 1: Safety Information.......................................................................................... 8
1.1. Warnings......................................................................................................................... 9
1.2. Cautions.......................................................................................................................... 9
1.3. Directives and Standards.............................................................................................. 10
1.4. CE Marking Conformance............................................................................................. 10
1.5. Warranty Information .................................................................................................. 10
Chapter 2: Product Description ...................................................................................... 11
2.1. Drive Description ..........................................................................................................11
2.2. Product Features ..........................................................................................................12
2.2.1. Current Control.............................................................................................. 12
2.2.2. Velocity Control .............................................................................................12
2.2.3. Position Control .............................................................................................12
2.2.4. Advanced Position Control ............................................................................13
2.2.5. Communication Options................................................................................13
2.2.6. Feedback Options ..........................................................................................13
2.2.7. Fault Protection .............................................................................................14
2.2.8. Built-in Protection..........................................................................................14
2.3. System Architecture .....................................................................................................14
2.4. How to Use this Guide..................................................................................................15
Chapter 3: Installation ................................................................................................... 16
3.1. Before You Begin ..........................................................................................................16
3.1.1. Site Requirements .........................................................................................16
3.1.2. Hardware Requirements ...............................................................................17
3.2. Unpacking the Drive Components................................................................................ 19
3.3. Connectors....................................................................................................................20
3.3.1. Connector Types............................................................................................20
3.4. Mounting the DC Trombone ........................................................................................21
3.5. Connections.................................................................................................................. 23
3.5.1. Wiring the DC Trombone...............................................................................23
3.5.2. Connection Diagrams.....................................................................................24
3.6. Connecting the Power Cables....................................................................................... 27
3.6.1. For S type drives ............................................................................................ 27
3.6.2. For Non-S 400 VDC Type Drives..................................................................... 28
3.6.3. Connecting the Motor Cable .........................................................................29
3.6.4. Connecting the DC Power..............................................................................29
3.6.5. Direct-to-Mains Power Source (Non-Isolated Rectifier)................................30
3.6.5.1. Three-Phase Direct-to-Mains Connection Topology ....................30
3.6.5.2. Single-Phase Direct-to-Mains Connection Topology ....................31
3.6.5.3. Multiple Connections Topology.................................................... 32

DC Trombone Installation Guide Table of Contents
MAN-DCTROIG (Ver. 1.602) 6
3.6.6. Battery Power Supply ....................................................................................33
3.6.7. Connecting the Control and Backup Supply (24 V)........................................33
3.7. Feedback and Control Cable Assemblies...................................................................... 35
3.7.1. Main Feedback Cable (FEEDBACK A) .............................................................35
3.7.2. Main and Auxiliary Feedback Combinations .................................................44
3.7.3. FEEDBACK B (Auxiliary Feedback).................................................................. 48
3.7.3.1. Emulated Encoder Outputs Option on FEEDBACK B (YA[4]=4) ....48
3.7.3.2. Differential Auxiliary Encoder Input Option on FEEDBACK B
(YA[4]=2) ....................................................................................... 51
3.7.3.3. Differential Pulse-and-Direction Input Option on FEEDBACK B
(YA[4]=0) ....................................................................................... 53
3.8. I/O Cables .....................................................................................................................55
3.8.1. General I/O Port (P1) ..................................................................................... 55
3.8.1.1. Digital Output (as Source Configuration) & Input (as Sink
Configuration)...............................................................................56
3.8.1.2. Digital Output (as Sink Configuration) & Input (as Source
Configuration)...............................................................................58
3.8.2. General I/O Port (P2) ..................................................................................... 60
3.9. Communication Cables................................................................................................. 62
3.9.1.1. RS-232 Communication ................................................................62
3.9.1.2. CAN Communication.....................................................................63
3.10. Powering Up .................................................................................................................65
3.11. Initializing the System................................................................................................... 65
Chapter 4: Technical Specifications ................................................................................ 66
4.1. Features........................................................................................................................66
4.1.1. Motion Control Modes ..................................................................................66
4.1.2. Advanced Positioning Control Modes ...........................................................66
4.1.3. Advanced Filters and Gain Scheduling........................................................... 66
4.1.4. Fully Programmable.......................................................................................66
4.1.5. Feedback Options ..........................................................................................66
4.1.6. Input/Output ................................................................................................. 67
4.1.7. Built-In Protection .........................................................................................68
4.1.8. Accessories ....................................................................................................68
4.1.9. Status Indication ............................................................................................68
4.1.10. Automatic Procedures ................................................................................... 68
4.2. Dimensions ...................................................................................................................69
4.3. Power Ratings for the 400 V Type ................................................................................70
4.4. Power Ratings for the 800 V Type ................................................................................71
4.4.1. Auxiliary Supply (only for S Type Drive).........................................................72
4.5. Environmental Conditions............................................................................................ 72
4.6. Control Specifications...................................................................................................73
4.6.1. Current Loop.................................................................................................. 73
4.6.2. Velocity Loop .................................................................................................74
4.6.3. Position Loop .................................................................................................74

DC Trombone Installation Guide Table of Contents
MAN-DCTROIG (Ver. 1.602) 7
4.7. Feedbacks .....................................................................................................................75
4.7.1. Feedback Supply Voltage...............................................................................75
4.7.2. Main Feedback Options................................................................................. 75
4.7.2.1. Incremental Encoder Input ........................................................... 75
4.7.2.2. Digital Halls ...................................................................................76
4.7.2.3. Absolute Encoder.......................................................................... 76
4.7.2.4. Interpolated Analog Encoder (Sine/Cosine) .................................76
4.7.2.5. Resolver ........................................................................................77
4.7.2.6. Tachometer*.................................................................................77
4.7.2.7. Potentiometer ..............................................................................78
4.7.3. Main Encoder Buffered Output .....................................................................78
4.7.4. Auxiliary Feedback Port (output mode YA[4]= 4).......................................... 79
4.7.5. Auxiliary Feedback Port (input mode YA[4]= 2, 0).........................................80
4.8. I/Os ............................................................................................................................... 81
4.8.1. Digital Input Interfaces ..................................................................................81
4.8.2. Digital Output Interface.................................................................................82
4.8.3. Analog Input .................................................................................................. 83
4.9. Communications...........................................................................................................83
4.10. Pulse Width Modulation (PWM) .................................................................................. 83
4.11. Compliance with Standards.......................................................................................... 84

DC Trombone Installation Guide
MAN-DCTROIG (Ver. 1.602)
www.elmomc.com
8
Chapter 1:
Safety Information
In order to operate the DC Trombone servo drive safely, it is imperative that you implement
the safety procedures included in this installation guide. This information is provided to protect
you and to keep your work area safe when operating the DC Trombone and accompanying
equipment.
Please read this chapter carefully, before you begin the installation process.
Before you start, make sure that all system components are connected to earth ground.
Electrical safety is provided through a low-resistance earth connection.
Only qualified personnel may install, adjust, maintain and repair the servo drive. A qualified
person has the knowledge and authorization to perform tasks such as transporting, assembling,
installing, commissioning and operating motors.
The DC Trombone servo drive contains electrostatic-sensitive components that can be
damaged if handled incorrectly. To prevent any electrostatic damage, avoid contact with highly
insulating materials, such as plastic film and synthetic fabrics. Place the product on a
conductive surface and ground yourself in order to discharge any possible static electricity
build-up.
To avoid any potential hazards that may cause severe personal injury or damage to the product
during operation, keep all covers and cabinet doors shut.
The following safety symbols are used in this manual:
Warning:
This information is needed to avoid a safety hazard, which might cause bodily
injury.
Caution:
This information is necessary for preventing damage to the product or to other
equipment.

DC Trombone Installation Guide Safety Information
MAN-DCTROIG (Ver. 1.602)
www.elmomc.com
9
1.1. Warnings
•To avoid electric arcing and hazards to personnel and electrical contacts, never
connect/disconnect the servo drive while the power source is on.
•Disconnect the DC Trombone from all voltage sources before it is opened for servicing.
•The DC Trombone servo drive contains grounding conduits for electric current protection.
Any disruption to these conduits may cause the instrument to become hot (live) and
dangerous.
•After shutting off the power and removing the power source from your equipment, wait at
least 1 minute before touching or disconnecting parts of the equipment that are normally
loaded with electrical charges (such as capacitors or contacts). It is recommended to
measure the electrical contact points with a meter before touching the equipment.
1.2. Cautions
•The DC Trombone servo drive contains hot surfaces and electrically-charged components
during operation.
•The maximum DC power supply connected to the instrument must comply with the
parameters outlined in this guide.
•When connecting to DC Trombone to an approved isolated 24 VDC auxiliary power supply,
connect it through a line that is separated from hazardous live voltages using reinforced or
double insulation in accordance with approved safety standards.
•Before switching on the DC Trombone, verify that all safety precautions have been
observed and that the installation procedures in this manual have been followed.
•Do not clean any of the DC Trombone drive's soldering with solvent cleaning fluids of pH
greater than 7 (8 to 14). The solvent corrodes the plastic cover causing cracks and eventual
damage to the drive's PCBs.
Elmo recommends using the cleaning fluid Vigon-EFM which is pH Neutral (7).
For further technical information on this recommended cleaning fluid, select the link:
http://www.zestron.com/fileadmin/zestron.com-usa/daten/electronics/Product_TI1s/TI1-
VIGON_EFM-US.pdf

DC Trombone Installation Guide Safety Information
MAN-DCTROIG (Ver. 1.602)
www.elmomc.com
10
1.3. Directives and Standards
The DC Trombone conforms to the following industry safety standards:
Safety Standard Item
Approved IEC/EN 61800-5-1, Safety Adjustable speed electrical power drive systems
Recognized UL 508C Power Conversion Equipment
In compliance with UL 840 Insulation Coordination Including Clearances and
Creepage Distances for Electrical Equipment
In compliance with UL 60950-1
(formerly UL 1950)
Safety of Information Technology Equipment
Including Electrical Business Equipment
In compliance with EN 60204-1 Low Voltage Directive 73/23/EEC
The DC Trombone servo drive has been developed, produced, tested and documented in
accordance with the relevant standards. Elmo Motion Control is not responsible for any
deviation from the configuration and installation described in this documentation.
Furthermore, Elmo is not responsible for the performance of new measurements or ensuring
that regulatory requirements are met.
1.4. CE Marking Conformance
The DC Trombone servo drive is intended for incorporation in a machine or end product. The
actual end product must comply with all safety aspects of the relevant requirements of the
European Safety of Machinery Directive 98/37/EC as amended, and with those of the most
recent versions of standards EN 60204-1 and EN 292-2 at the least.
According to Annex III of Article 13 of Council Directive 93/68/EEC, amending Council Directive
73/23/EEC concerning electrical equipment designed for use within certain voltage limits, the
DC Trombone meets the provisions outlined in Council Directive 73/23/EEC. The party
responsible for ensuring that the equipment meets the limits required by EMC regulations is
the manufacturer of the end product.
1.5. Warranty Information
The products covered in this manual are warranted to be free of defects in material and
workmanship and conform to the specifications stated either within this document or in the
product catalog description. All Elmo drives are warranted for a period of 12 months from the
date of shipment. No other warranties, expressed or implied — and including a warranty of
merchantability and fitness for a particular purpose — extend beyond this warranty.

DC Trombone Installation Guide
MAN-DCTROIG (Ver. 1.602)
www.elmomc.com
11
Chapter 2:
Product Description
This installation guide describes the DC Trombone servo drive and the steps for its wiring,
installation and power-up. Following these guidelines ensures optimal performance of the drive
and the system to which it is connected.
2.1. Drive Description
The DC Trombone series of digital servo drives are highly resilient and designed to deliver the
highest density of power and intelligence. The DC Trombone delivers up to 10 kW of
continuous power or 16 kW of peak power in a compact package.
The digital drives are based on Elmo’s advanced SimplIQ motion control technology. They
operate from a DC power source in current, velocity, position and advanced position modes, in
conjunction with a permanent-magnet synchronous brushless motor, DC brush motor, linear
motor or voice coil. They are designed for use with any type of sinusoidal and trapezoidal
commutation, with vector control. The DC Trombone can operate as a stand-alone device or as
part of a multi-axis system in a distributed configuration on a real-time network.
The drives are easily set up and tuned using Elmo’s Composer software tools. This Windows-
based application enables users to quickly and simply configure the servo drive for optimal use
with their motor. The DC Trombone, as part of the SimplIQ product line, is fully programmable
with Elmo’s Composer motion control language.
Power to the drives is provided by a DC power source (not included with the DC Trombone). Elmo
recommends using the Elmo Tambourine Power Supply, which is ideally suited to the Trombone,
DC Trombone, and Solo Trombone.
Since the power stage is fully isolated from the control stage, the DC rectifier can be fed directly
from the mains, without the need for a bulky and expensive transformer.
If backup functionality is required to store control parameters in the event of a mains power
outage, then an S-model DC Trombone should be used, with an external 24 VDC isolated supply
connected to it.
Note: The backup functionality can operate from an isolated voltage source within the range
of 18 to 30 VDC.
Whenever backup functionality is not required, DC Trombone models that do not have the S
option in the catalog number (only for 400 V model) can be used. In these models, a smart
control-supply algorithm enables the DC Trombone to operate with only the main power
supply VP+ and VN-, with no need for a 24 VDC auxiliary power supply for the logic.
The DC Trombone is available in two versions:
•The Standard DC Trombone is a basic servo drive, which operates in current, velocity and
position modes including Follower and PT & PVT. It operates simultaneously via RS-232 and
CAN DS 301, DS 305, DS 402 communications and features a third-generation programming
environment. (The catalog number begins DC-TRO but is not followed by an A.)

DC Trombone Installation Guide Product Description
MAN-DCTROIG (Ver. 1.602)
www.elmomc.com
12
•The Advanced DC Trombone includes all the motion capabilities and communication
options included in the Standard model, as well as advanced positioning capabilities:
ECAM, Dual Loop and increased program size. (The catalog number starts DC-TROA.)
Both versions operate with RS-232 and CAN communication.
2.2. Product Features
2.2.1. Current Control
•Fully digital
•Sinusoidal commutation with vector control or trapezoidal commutation with encoder
and/or digital Hall sensors
•12-bit current loop resolution
•Automatic gain scheduling, to compensate for variations in the DC bus power supply
2.2.2. Velocity Control
•Fully digital
•Programmable PI and FFW (feed forward) control filters
•Sample rate two times current loop sample time
•“On-the-fly” gain scheduling
•Automatic, manual and advanced manual tuning and determination of optimal gain and
phase margins
2.2.3. Position Control
•Programmable PIP control filter
•Programmable notch and low-pass filters
•Position follower mode for monitoring the motion of the slave axis relative to a master axis,
via an auxiliary encoder input
•Pulse-and-direction inputs
•Sample time: four times that of the current loop
•Fast event capturing inputs
•PT and PVT motion modes
•Fast output compare (OC)

DC Trombone Installation Guide Product Description
MAN-DCTROIG (Ver. 1.602)
www.elmomc.com
13
2.2.4. Advanced Position Control
This relates to the Advanced model only.
•Position-based and time-based ECAM mode that supports a non-linear follower mode, in
which the motor tracks the master motion using an ECAM table stored in flash memory
•Dual (position/velocity) loop
2.2.5. Communication Options
Depending on the application, DC Trombone users can select from two communication options:
•RS-232 serial communication
•CAN for fast communication in a multi-axis distributed environment
2.2.6. Feedback Options
•Incremental Encoder – up to 20 Megacounts (5 Megapulses) per second
•Digital Halls – up to 2 kHz
•Incremental Encoder with Digital Halls for commutation – up to 20 Megacounts per second
for encoder
•Interpolated Analog Sine/Cosine Encoder – up to 250 kHz (analog signal)
Internal Interpolation - up to x4096
Automatic correction of amplitude mismatch, phase mismatch, signals offset
Auxiliary emulated, unbuffered, single-ended, encoder output
•Resolver
Programmable 10 to 15 bit resolution
Up to 512 revolutions per second (RPS)
Auxiliary emulated, unbuffered, single-ended, encoder output
•Tachometer, Potentiometer
•Absolute Encoder
Heidenhain 2.1
Heidenhain 2.2
Panasonic
Stegmann
Note: Elmo drives provide supply voltage for all the feedback options.

DC Trombone Installation Guide Product Description
MAN-DCTROIG (Ver. 1.602)
www.elmomc.com
14
2.2.7. Fault Protection
The DC Trombone includes built-in protection against possible fault conditions, including:
•Software error handling
•Status reporting for a large number of possible fault conditions
•Protection against conditions such as excessive temperature, under/over voltage, loss of
commutation signal, short circuits between the motor power outputs and between each
output and power input/return
•Recovery from loss of commutation signals and from communication errors
2.2.8. Built-in Protection
•Additional heat-sink options, for demanding applications:
External Heat Sink with fins (P/N with suffix 2)
External Heat Sink with fins and fan (P/N with suffix 1)
2.3. System Architecture
Motor
PWM
Controller
Communication
RS 232 and CANopen
Isolated Power Stage
Protection
I/Os
Resolver
Tachometer
Analog
Encoder
or
Main
DC Power
Supply
Potentiometer
or
or
or
Auxilliary
Encoder
24V Logic
Supply
(Optional)
Isolation
Boundary
Isolation
Boundary
Current
Feedback
Incremental
Encoder
Absolute
or
Main Feedback
Buffered
Output
Figure 1: DC Trombone System Block Diagram

DC Trombone Installation Guide Product Description
MAN-DCTROIG (Ver. 1.602)
www.elmomc.com
15
2.4. How to Use this Guide
In order to install and operate the DC Trombone servo drive, you will use this manual in
conjunction with a set of Elmo documentation. Installation is your first step; after carefully
reading the safety instructions in the first chapter, the following chapters provide you with
installation instructions as follows:
•Chapter 3 - Installation, provides step-by-step instructions for unpacking, mounting,
connecting and powering up the DC Trombone
•Chapter 4 - Technical Specifications,lists all the drive ratings and specifications
Upon completing the instructions in this guide, the DC Trombone servo drive should be
successfully mounted and installed. From this stage, you need to consult higher level Elmo
documentation in order to set up and fine-tune the system for optimal operation:
•The SimplIQ Software Manual, which describes the comprehensive software used with the
DC Trombone
•The SimplIQ Command Reference Manual, which describes, in detail, each software
command used to manipulate the DC Trombone motion controller
•The Composer Software Manual, which includes explanations of all the software tools that
are part of Elmo’s Composer software environment

DC Trombone Installation Guide
MAN-DCTROIG (Ver. 1.602)
www.elmomc.com
16
Chapter 3:
Installation
3.1. Before You Begin
3.1.1. Site Requirements
You can guarantee the safe operation of the DC Trombone by ensuring that it is installed in an
appropriate environment.
Feature Value
Ambient operating temperature 0 °C to 40 °C (32 °F to 104 °F)
Maximum Operating Altitude 2,000 m (6562 feet)
Maximum non-condensing humidity 90%
Operating area atmosphere No flammable gases or vapors permitted in area
Models for extended environmental conditions are available.
Caution:
The DC Trombone dissipates its heat by convection. The maximum ambient
operating temperature of 40 °C (104 °F) must not be exceeded.

DC Trombone Installation Guide Installation
MAN-DCTROIG (Ver. 1.602)
www.elmomc.com
17
3.1.2. Hardware Requirements
The components that you will need to install your DC Trombone are:
Component Connector Described
in Section
Diagram
Main Power Cable PE VN-VP+ 3.6.4
Motor Cable M3 M2 M1 PE 3.6.3
Backup Supply Cable
(needed for S type drive)
VL+ VL- 3.6.7
Main Feedback Cable MAIN FEEDBACK
(FEEDBACK A)
3.7.1
Auxiliary Feedback Cable
(if needed)
AUX. FEEDBACK
(FEEDBACK B)
3.7.3.2

DC Trombone Installation Guide Installation
MAN-DCTROIG (Ver. 1.602)
www.elmomc.com
18
Component Connector Described
in Section
Diagram
Digital I/O Cable
(if needed)
GENERAL I/O
P1
3.8.1
Digital Inputs and
Analog Inputs Cable
(if needed)
GENERAL I/O
P2
3.8.1.2
RS232 Communication
Cable
RS232 3.9.1.1
CAN Communication
cable(s) (if needed)
CAN (in)
CAN (out)
3.9.1.2
PC for drive setup and
tuning
Motor data sheet or
manual

DC Trombone Installation Guide Installation
MAN-DCTROIG (Ver. 1.602)
www.elmomc.com
19
3.2. Unpacking the Drive Components
Before you begin working with the DC Trombone system, verify that you have all of its
components, as follows:
•The DC Trombone servo drive
•The Composer software and software manual
The DC Trombone is shipped in a cardboard box with Styrofoam protection.
To unpack the DC Trombone:
1. Carefully remove the servo drive from the box and the Styrofoam.
2. Check the drive to ensure that there is no visible damage to the instrument. If any damage
has occurred, report it immediately to the carrier that delivered your drive.
3. To ensure that the DC Trombone you have unpacked is the appropriate type for your
requirements, locate the part number sticker on the side of the DC Trombone. It looks like
this:
The P/N number at the top gives the type designation as follows:
4. Verify that the DC Trombone type is the one that you ordered, and ensure that the voltage
meets your specific requirements.
Table of contents
Other Elmo Servo Drive manuals

Elmo
Elmo Gold Series User manual
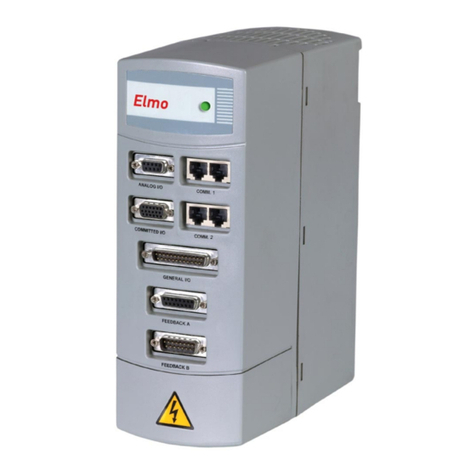
Elmo
Elmo TUB Series User manual

Elmo
Elmo Gold Drum HV User manual
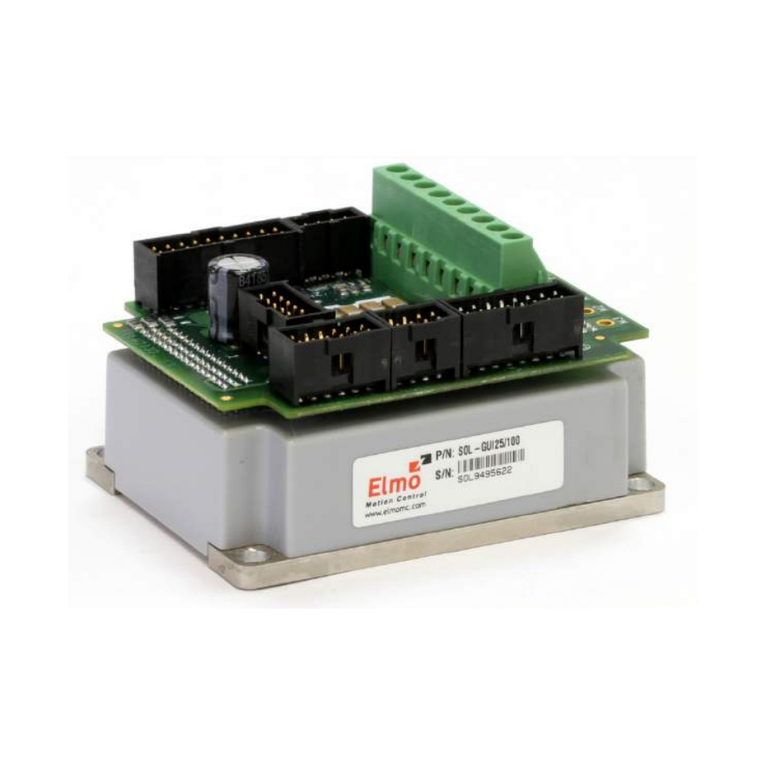
Elmo
Elmo SimplIQ Series User manual
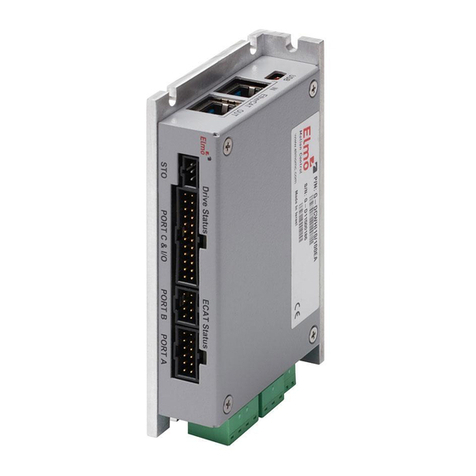
Elmo
Elmo Gold DC Whistle Series User manual
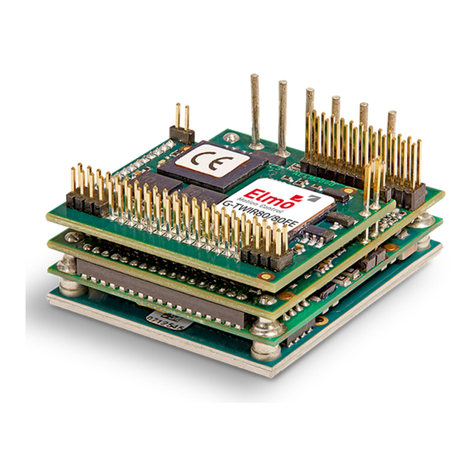
Elmo
Elmo 30/60 User manual
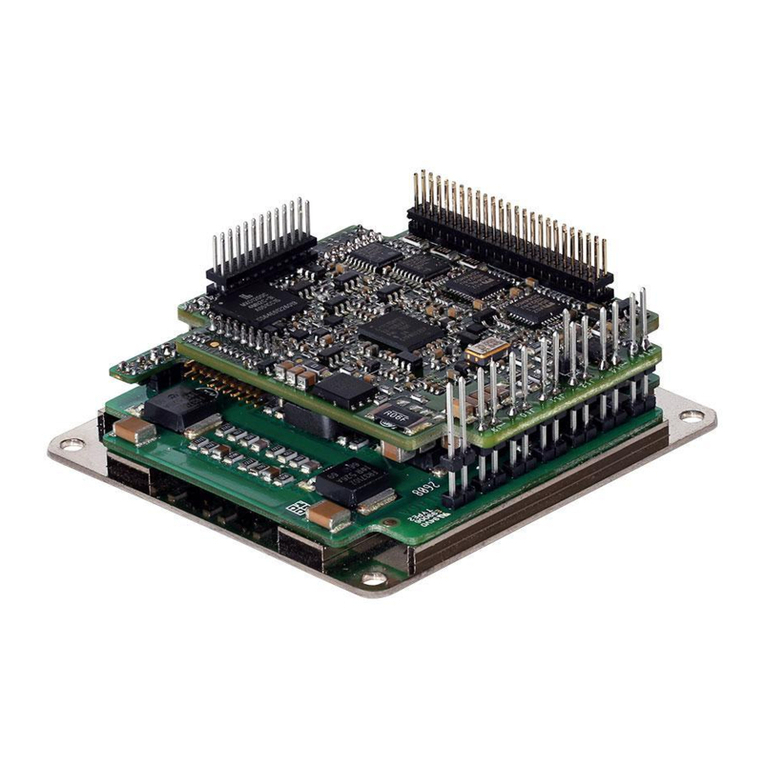
Elmo
Elmo Gold Bell User manual

Elmo
Elmo Gold DC Bell User manual
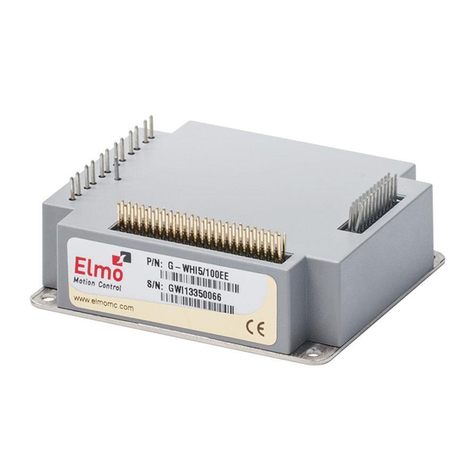
Elmo
Elmo Gold Whistle Series User manual
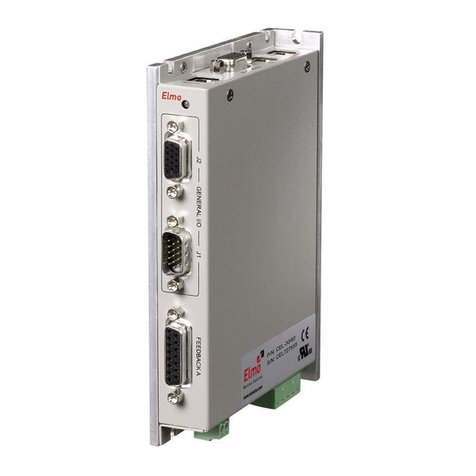
Elmo
Elmo Cello User manual