Sun Microsystems ALIGNMENT EELR124A User manual

INSTALLATION
d OPERATION
INSTALLATION
d OPERATION
SUN®an
d
OPERATION
MANUAL
an
d
OPERATION
MANUAL
READ THIS INSTRUCTION MANUAL THOROUGHLY BEFORE
INSTALLING OPERATING SERVICING OR MAINTAINING THE
INSTALLING
,
OPERATING
,
SERVICING
OR
MAINTAINING
THE
LIFT. SAVE THIS MANUAL.
KODIAK QUAD RACK
MODEL: ALIGNMENT EELR124A /
EELR124APKG
SERVICE WHE18406
18000 LB
JUL 2010 REV.- 6-1787
SUN is a trademark of
Snap-on Tools
Corporation
1-800-268-7959

2 of 42
THE FOLLOWING APPLIES TO ALL LIFTS
IMPORTANT SAFETY INSTRUCTIONS
When using this lift, basic safety precautions should always be followed, including
the following:
1. Read all instructions in this manual and on the lift thoroughly before
installing, operating, servicing or maintaining the lift.
2. Inspect lift daily. Do not operate if it malfunctions or problems have been
encountered.
3. Never attempt to overload the lift. The manufacturer’s rated capacity is
shown on the identification label on the power side column. Do not
override the operating controls or the warranty will be void.
4. Only trained and authorized personnel should operate the lift. Do not allow
customers or bystanders to operate the lift or be in the lift area.
5. Caution! Never work under the lift unless the mechanical safety locks
are engaged.
6. Always keep the lift area free of obstruction and debris. Grease and oil
spills should always be cleaned up immediately.
7. Never raise vehicle with passengers inside.
8. Before lowering check area for any obstructions
9. To protect against the risk of fire, do not operate lift in the vicinity of open
containers of flammable liquids.
10. Adequate ventilation should be provided when working on internal
combustion engines.
11. Do not remove hydraulic fittings while under pressure.
12. Do not raise or lower the lift with the vehicle on the Jacking Beam.
SAVE THESE INSTRUCTIONS

3 of 42
TABLE OF CONTENTS PAGE
1.0 GENERAL SPECIFICATION......................................................................4
2.0 TOOLS REQUIRED FOR INSTALLATION.................................................5
3.0 CONTENTS................................................................................................6
4.0 INSTALLATION INSTRUCTIONS..............................................................7
4.1 Chalk Line Layout....................................................................9
4.2 Front And Rear Crossmember Assemblies............................10
4.3 Power Pack Installation..........................................................14
4.4 Hydraulic Installation..............................................................14
4.5 Electrical Connections ...........................................................15
4.6 Cable Installation...................................................................15
4.7 Air Installations ......................................................................16
4.8 Anchor Installation.................................................................17
4.9 Deck Leveling Procedure.......................................................18
4.10 Final Check Of Assembled Lift.............................................20
4.11 Operation Test With Vehicle ................................................21
5.0 SAFETY AND OPERATING INSTRUCTIONS.........................................22
6.0 SAFETY AWARENESS............................................................................23
7.0 RECOMMENDED MAINTENANCE..........................................................24
8.0 PARTS LIST.............................................................................................25
8.1 Lift Assembly .........................................................................25
8.2 Parts List – Lift Assembly ......................................................26
8.3 Tower Assembly....................................................................27
8.4 Parts List – Power Tower Assembly......................................28
8.5 Deck Assembly (Left Side).....................................................29
8.6 Parts List – Deck Assembly (Left Side)..................................30
8.7 Crossmember Assembly........................................................31
8.8 Parts List – Crossmember Assembly.....................................32
8.9 Cylinder Assembly.................................................................33
8.10 Parts List – Cylinder Assembly ............................................34
8.11 Hydraulic And Air Kit............................................................35
8.12 Parts List – Hydraulic And Air Kit .........................................36
8.13 Cable Routing......................................................................37
8.14 Parts List – Cable Routing ...................................................38
8.15 Power Pack Assembly .........................................................39
8.16 Parts List – Power Pack.......................................................40
9.0 AVAILABLE ACCESSORIES ...................................................................42

4 of 42
1.0 GENERAL SPECIFICATION
Maximum Capacity: 18,000 lb. 8,165 kg
Overall Length: 304-7/8” 7468mm
Overall Width: 152-1/8” 3864mm
Down Position Height: 9-1/2” 241mm
Maximum Lifting Height: 72” 1829mm
Maximum Wheel Base: 210” 5334mm
Power Rating: 208-230 Volts, 1Ph., 20 Amp, 60Hz.
Air Requirements: 90 – 120 psi Shop Air
Shipping Weight: 5,465 lb. 2,484 kg

5 of 42
CHECK CONTENTS OF ACCESSORY BOX WITH THE PACKING LIST
ENCLOSED
ATTENTION! This lift is intended for indoor installation only. It is
prohibited to install this product outdoors. Operating environment
temperature range should be 41 – 104 °F (5 – 40 °C). Failure to
adhere will result in decertification, loss of warranty, and possible
damage to the equipment.
2.0 TOOLS REQUIRED FOR INSTALLATION
ROTARY HAMMER DRILL
3/4” CONCRETE DRILL BIT
4’ LEVEL
HAMMER (for anchor installation)
PRY BAR (for shim installation)
CHALK LINE (lift location)
TAPE MEASURE
ELECTRICAL TAPE
STEP LADDER (adjusting cables and/or safety ladder in posts)
SIDE CUTTERS (for cutting shipping straps)
4 WORK STANDS (set up)
STANDARD SOCKETS AND WRENCHES
ALLAN KEY SET
SCREWDRIVER SET
FLOOR JACK OR ENGINE HOIST

6 of 42
3.0 CONTENTS
The lift is packaged to protect it from any damage that may occur during shipping.
The two deck assemblies and crossmembers are packaged together with the
accessory boxes strapped to them.
Main Structural Components:
1 - Left Side Deck Assembly (complete with hydraulic cylinder, sheaves
and cables)
1 - Right Side Deck Assembly
1 - Front Crossmember Assembly (with air cylinder release locks and
sheaves)
1 - Rear Crossmember Assembly (with air cylinder release locks and
sheaves)
Accessory Box Components
Box 1 Contents:
1 - Power Post (with safety ladder)
3 - Post (with safety ladder)
Box 2 Contents:
1 - Hardware Kit (with separate packaging list)
2 - Ramp pin
2 - Front Wheel Stop
4 - Sheave Cover
2 - Approach Ramp
1 - Coupler, ¼”NPT
2 - Recoil Hose
1 - Power Unit 220v/1Ph/3hp
10ft - 1/4” DIA. Polytube
10ft - 3/8” DIA. Polytube
1 - Hose Guard
1 - Hydraulic Hose Assembly (16ft. lg.)
2 - Cable Tie
1 - Air Valve & Filter Assembly
1 - Flow Control
1 - Installation & Operation Manual
1 - Lift it Right Manual “ALI”
1 - Lift it Right Safety Tips
1 - “ALI” Standards
1 - “ALI” Quick Reference Guide
8 - Glide Bearing

7 of 42
4.0 INSTALLATION INSTRUCTIONS
PLEASE TAKE THE TIME TO READ THESE INSTRUCTIONS COMPLETELY.
A QUICK CHECK OF THE CONTENTS OF THE ACCESSORY BOX WOULD
ALSO DECREASE THE INSTALLATION TIME.
•Gather the tools and materials required for the installation.
•Select the location best suited for your lift.
NOTE: In determining lift area check for the following:
- Ease of driving a vehicle on and off the lift.
- Overhead obstructions, low ceiling height, overhead doors, overhead
heaters etc.
- Floor obstructions, uneven floor in lift area, floor drains, work benches,
electrical wiring in floor, etc.
- Concrete grade: Lifts should only be installed on level concrete floors with
a minimum thickness of five (5) inches. Concrete must have a minimum
strength of 4,000 psi., and should be aged 30 days prior to the installation
of the lift.
Recommended clearance around the lift is three (3) feet. Ensure clearance
conforms to local building and fire codes.
Recommended overhead clearance is a minimum twelve (12) foot ceiling
providing 6 feet for the maximum lift height and 6 feet for the supported vehicle.
For vehicles taller than 6 feet it is recommended that the user provides additional
overhead clearance or a shut off mechanism to stop the lift from raising the
vehicle too high.
An outline matching the dimensions shown in Figure 1 will need to be marked
on the floor. Refer to Figure 1 for outline dimensions. Refer to General Lift
Specifications for overall lift dimensions.

8 of 42
TYPICAL BAY LAYOUT

9 of 42
4.1 CHALK LINE LAYOUT
Figure 1. Chalk line layout
•Refer to Figure 1. Make a chalk line parallel to the doorway at least 322-7/8” in
from the doorway. This will be the location for the front face of the tower baseplate.
Call this line "A".
•Determine the center of the doorway and bay. Make a centerline to intersect with line
"A".
•Make a chalk line parallel to line “A”, 263-3/8” back toward the door. Call this line “B”.
•Make two chalk lines spaced 76-1/8” to the left and right side of the centerline
intersecting line “A” and line ”B”. Call these lines, line “C”. These will be the lines that
the outside edge of the tower baseplate runs along.

10 of 42
4.2 FRONT AND REAR CROSSMEMBER ASSEMBLIES
IMPORTANT
NOTE: To determine the front, rear, left side and right side of the decks check the
following:
•The left side deck has the hydraulic cylinder mounted to its underside and
includes the cables. The work steps, attached to the turn plate pocket cutouts,
are located at the front of the lift and should point outward when installed.
NOTE: To determine the front and rear, of the crossmembers check the
following:
•The rear crossmember has three ears for attaching the approach ramps.
There are 2 locating tabs on each side of the crossmembers for positioning the
decks between the crossmembers (see Figure 2).
Figure 2. Front and rear crossmembers
Front Right
Rear Right
Rear Left Front Left
Locating Tabs

11 of 42
•Remove the left and right deck assemblies from their packaging and place
them on axle stands as follows (see Figure 1):
- Place the left deck assembly so that the inside edge lies along chalk line “B”
- Place the right deck assembly so that the inside edge lies along chalk line “C”
- Position both decks so that the front edge lies along chalk line “A”
•Using a floor jack or engine hoist, move the front crossmember into position in
front of the lift and the rear crossmember into position at the rear of the lift.
Refer to Figure 2 to identify the front and rear crossmembers.
NOTE: THE PULLEYS (SHEAVES) IN THE DECK ASSEMBLY DO NOT NEED
TO BE REMOVED FOR ASSEMBLY.
•Check the part numbers of the cables (located on each stud) to determine
routing.
2-1360 FRONT LEFT
2-1361 FRONT RIGHT
2-1362 REAR LEFT
2-1363 REAR RIGHT
NOTE: Refer to Figure 4 and the Parts Manual, Cable Routing Diagram
for a detailed layout of cable routing.
•Remove the pulleys (sheaves) from the crossmembers along with the spacers
and nylon thrust washers. Place these to the side of the crossmembers.
•Run each cable through the crossmembers and out past the safety lock (see
Figure 3).
•Raise the front crossmember up to the level of the decks and attach it using
the ½”DIA x 4½”LG Hex Bolts, ½” Washers, ½” Lockwashers and ½” Hex Nuts
found in the polybag labeled “D” (Decks).
NOTE: THE CABLES RUNNING INSIDE THE CROSSMEMBERS MUST PASS
BETWEEN THE ½”DIA x 4½”LG HEX BOLTS USED TO FASTEN THE
CROSSMEMBERS TO THE DECK ASSEMBLIES.
•Repeat the previous step for the rear crossmember.
•Position the decks between the locating tabs on the crossmembers using the
½”-13UNC x 1”LG Set Screws found in the polybag labeled “D” (Decks). The
set screws go in the outer locating tabs and should be tightened until the
inside of the edge of the deck assemblies are flush with the inside edge of the
locating tabs on the crossmembers.
•At this point the decks should be completely fastened to the crossmembers
and the threaded portion of each cable should be routed through the
crossmembers, past the lock safety. The crossmember pulleys should be

12 of 42
removed and lying at each corner of the lift. Before proceeding, check that the
layout matches that shown in Figure 1, that the lift is square and that there is a
40” gap between the decks along their entire length.
Figure 3. Cable routing diagram
NOTE: THE 40” DIMENSION SHOWN IN THE TYPICAL BAY LAYOUT (PAGE
4) IS CRITICAL AS IT IS NECESSARY TO ALLOW THE JACKING BEAMS
TO ROLL FREELY.
•Remove the slider block weldments from both crossmembers by removing the
3/8”-16UNC x 1”LG Hex HD Bolts and 3/8” Lockwashers attaching them to the
crossmember.
•Determine which tower is the power post (the tower with the mounting plate for
the powerpack) and position it in the front left corner. Position the remaining
three towers at the other corners of the lift.
•Slide each tower around the crossmember so that the holes for attaching the
slider blocks are roughly halfway inside the channel.

13 of 42
•Place the Glide Bearings (located in the accessory box) on the slider block
weldments and bolt the slider block weldments back onto the crossmember
using the 3/8”-16UNC x 1”LG Hex HD Bolts and 3/8” Lockwashers removed
previously.
•Replace all of the crossmember pulleys, being sure to lock the sheave pins
with the 3/8”-16UNC x 1”LG Hex HD Bolt. Be sure to replace pulleys and
spacers in the same arrangement as they were removed (see Figure 3 and the
Parts Manual, Front Crossmember Assembly).
•Pull the towers backwards (away from the decks) so that the slider blocks are
flush with the tower roll form.
NOTE: THE CYLINDER ROD MUST BE FULLY EXTENDED IN ORDER TO
ATTACH THE THREADED ENDS OF THE CABLES TO THE TOP PLATE OF
THE TOWERS. TO EXTEND THE CYLINDER ROD, THE POWERPACK AND
HYDRAULIC KIT MUST BE INSTALLED AND THE ELECTRICAL
CONNECTIONS MADE (SEE FOLLOWING SECTIONS).
•The non-threaded ends of the cables are pre-installed on the cable flange.
Ensure that the cable flange in installed with the counterbores facing towards
the hydraulic cylinder as shown in Figure 4
•Ensure that the two retaining nuts are positioned as shown in Figure 4. The
nuts should be locked against each other using two wrenches.
Figure 4. Cable Installation at Flange

14 of 42
4.3 POWER PACK INSTALLATION
NOTE: WHEN WORKING WITH HYDRAULIC LINES AND VALVES, IT IS
IMPORTANT TO KEEP ALL COMPONENTS CLEAN AND FREE OF DIRT.
Figure 5. Power pack details
•Install the power pack to the mounting bracket on the front face of the left front
post using the 5/16"-18UNC × 1"LG. hex head bolts and 5/16" washers,
lockwashers and hex head bolts, found in polybag “C” (Powerpack). Refer to
the Parts Manual, Power Post Tower Assembly Diagram.
4.4 HYDRAULIC INSTALLATION
•Refer to Parts Manual, Hydraulic and Air Kit Diagram
•Locate the supply lines: 1/4" and 3/8" polytube (10ft.), 3/8" flexible hydraulic
line (16ft.), and install the hose guard to cover all three lines. All four items are
found in the accessory box
TIP: TAPE ONE END OF THE HYDRAULIC HOSE TO THE TWO POLYTUBES
AND FEED THEM THROUGH HOSE GUARD. NOW REMOVE THE
TAPE.
•Feed the hose guard through the opening on the front left crossmember
assembly.
Connection for hydraulic
fitting assembly
Do not remove blue plastic
cap. No pressure at this point.
Lowering Lever Instruction Label
Breather Screw
Filler Cap
Up control Button

15 of 42
•Connect the end of the flexible hydraulic hose (3/8" JIC, F SWIVEL) to the
fitting at the cylinder. DO NOT OVER TIGHTEN.
•Connect the other end of the flexible hydraulic hose (3/8" JIC, F SWIVEL) to
the flow control on the powerpack.
4.5 ELECTRICAL CONNECTIONS
CAUTION: ALL ELECTRICAL CONNECTIONS SHOULD BE MADE BY A
QUALIFIED ELECTRICIAN.
Refer to Figure 6, Electrical Diagram for electrical connections.
Electrical Breaker Size Recommendation: 20Amps
Figure 6. Electrical diagram for 230V/1 ph
4.6 CABLE INSTALLATION
•Remove the hydraulic cap from the fitting at the base of the hydraulic cylinder.
•Depress the lowering lever on the powerpack, while using an air chuck to blow
air into the breather hole at the base of the cylinder to extend the rod.
•Extend the rod until it reaches its full stroke.
•Fill the reservoir on the powerpack with ISO 32 (10 Hydraulic Weight)
hydraulic fluid.
•Install the threaded stud end of the cables to the tower top plates using the
7/8” Flat Washer, and two (2) 7/8”-14UNF Hex Nuts with Cable Spacers as
required (see Figure 3). The Hex Nuts, Washers and Cable Spacers are
located in polybag “A” (cables).

16 of 42
4.7 AIR INSTALLATIONS
NOTE: FOR ALL AIR INSTALLATIONS REFER TO THE HYDRAULIC AND
AIR KITS DIAGRAM IN THE PARTS MANUAL.
•Install the air valve and filter assembly (found in the accessory box) to the
mounting bracket on the power post. To do this pull off the pushbutton and
unscrew the plastic nut. Slide the assembly into the mounting bracket and re-
fasten the plastic nut so that the assembly is attached to the top hole. Replace
the pushbutton by pressing it firmly back onto the air valve and filter assembly.
NOTE: MOST OF THE 1/4" AND 3/8" POLYTUBE CONNECTIONS HAVE
BEEN MADE IN THE FRONT AND REAR CROSSMEMBER ASSEMBLIES.
THE 1/4” AND 3/8” POLYTUBES THAT RUN THE LENGTH OF THE DECK
ARE ALSO INSTALLED. THE 1/4" POLYTUBE IS USED FOR THE AIR
CYLINDER LOCKS, THE 3/8" POLYTUBE IS USED FOR THE AIR OUTLETS
TO THE JACKING BEAMS.
•Connect all of the 1/4" polytubes, coming out of the front left and rear left
crossmember assemblies and the front and rear of the left side deck, to the ¼”
pushlock cross and tee ftittings – As shown in Views “D” and “E” of the
Hydraulic and Air Kit Diagram (Page 35).
•Connect the 1/4" polytube from the hose guard (i.e. supply line) to the ¼”
pushlock cross at the front of the left side deck assembly. Connect the
opposite end to the Air Valve and Filter assembly on the front left tower.
•Connect the 3/8” polytube from the hoseguard to the 3/8” fitting at the front of
the left deck assembly (jacking beam air bracket). Connect the opposite end
to the Air Valve and Filter assembly on the front left tower.
NOTE: FOR THOSE UNITS EQUIPPED WITH JACKING BEAMS, THIS IS THE
APPROPRIATE TIME TO INSTALL THEM. CONSULT THE JACKING BEAM
INSTRUCTION MANUALS FOUND IN EACH JACKING BEAM BOX.
•Hook up an air supply to the inlet of the water trap on the Air Valve and Filter
Assembly located on the front left post.
•Check for air leaks.
•Check the operation of the air cylinder locks by pressing the pushbutton on the
Air Valve and Filter Assembly on the front left post. This should cause the
safety shoes to be pulled into the crossmembers, releasing the lift from the
safety racks.
•The pneumatics are now completely installed. Press the "UP" button on the
power pack and continue until the lift is fully supported by the cables.
NOTE: MAKE CERTAIN THAT THE MECHANICAL SAFETY LOCKS AND
CABLE ROLLERS ARE WORKING PROPERLY.

17 of 42
4.8 ANCHOR INSTALLATION
•Check all layout dimensions in the General Specifications (pg. 4) and Figure 1
before continuing with anchor installation.
1. Refer to Figure 7 while reading through these instructions.
Figure 7. Anchor installation
2. Ensure that the lift is fully supported by the cables and is at a level just
above the work stands.
3. Prior to installing anchors, assemble the nut and washer onto anchors. A
minimum of six threads must be visible below the surface of the nut.
4. Using a 3/4” concrete drill bit and rotary hammer drill, drill through the
concrete floor in the anchor holes positioned on the base of each post. (In
case longer anchors are required, supplied anchors can be hammered
through concrete).
5. Using a hammer, drive each anchor into floor leaving space for shimming.
6. Use a 4’ level, to level the posts. Refer to Figure 9.
7. Shim as required and hammer anchors till they make contact with
Baseplate. Do not tighten anchors.
8. Check the distance from the top of the anchor to the floor. If this dimension
exceeds 2¼” due to floor slope, DO NOT use the supplied anchors.
Longer anchor must be used (see #2 above).
9. Tighten all anchor bolts to a torque of 150 ft. lbs. Recheck and adjust the
level of post(s) and cable(s) if necessary.

18 of 42
Figure 8. Floor slope
4 FT
LEVEL
Figure 9. Post leveling
NOTE: THE 3/4” ×5 ½” LG. WEDGE ANCHOR BOLTS SUPPLIED MUST
HAVE A MINIMUM EMBEDMENT OF 3¼” INTO CONCRETE FLOOR.
NOTE: IN CASES WHERE THE FLOOR IS EXTREMELY OUT OF LEVEL, THE
MECHANICAL SAFETIES MAY NOT ENGAGE ON THE SAME LOCK.
4.9 DECK LEVELING PROCEDURE
•Raise the lift so that it is fully supported by the cables and is not resting on the
safety ladders.
•Using a 4’ level, check the level of the decks front to rear and side to side as
shown in Figure 10.
•Lower the lift onto the nearest safety
•Adjust the cable lengths by tightening or loosening the two (2) 7/8”-14UNF hex
nuts attached to each cable at the tower top plate to raise or lower each
corner.
•Repeat the preceding steps until the lift is completely level when supported by
the cables.
•Raise the lift so that the deck is supported by the cables and is not resting on
the safety ladders.
•Loosen the 3/8"-16 UNC × 1" LG. hex bolts at the bottom and top of each
safety ladder (on the back side of the tower) and pull the safety ladders up
until they come into full contact with each safety shoe on the crossmember
assemblies.

19 of 42
•When flush with the safety shoe, tighten the two (2) 5/8"-11 UNC hex nuts at
the top of each safety ladder and the 3/8"-16 UNC × 1"LG hex bolts at the
bottom and top of each safety ladder (on the back side of the tower).
•Raise the lift and check that the ladders engage evenly.
Figure 10. Deck leveling
•Raise the lift to its full height and check for full operating height of 72". This
measurement is taken from the top of the decks to the floor.
•Install the approach ramps using the ramp pins, 1/8” x 2”LG cotter pins, 1/2”
washers, and approach ramps provided. The ramps and ramp pins are
located in the accessory box, the cotter pins and washers are found in polybag
“E” (Misc.). Ensure the proper operation of the ramps.
•Install the front wheel stops using the 1/2"-13 UNC × 1"LG hex bolts and 1/2"
lockwashers found in polybag “E” (Misc.).
•Install the (4) sheave covers over the sheaves in the crossmember assembly.
These are found in the accessory box.
•Cycle the lift several times to check proper operation of the cables, safety lock,
air locks, etc.
STOP IMMEDIATELY IF THE LIFT IS NOT OPERATING PROPERLY.
•Make any necessary adjustments and check again for proper operation.

20 of 42
4.10 FINAL CHECK OF ASSEMBLED LIFT
1. Final dimension check after anchoring. ____
2. Check for air and hydraulic leaks. ____
3. Ensure cables are properly routed and free from obstructions. ____
4. Ensure all safety lock mechanism are working correctly. ____
5. Re-check level of post and decks. ____
6. Makes sure ramps are secured correctly with cotter pins ____
and washers.
7. Check all fasteners, tighten if necessary. ____
8. Check direction of flow control (arrow pointed toward power unit). ____
9. If jack beams are supplied, ensure keeper bracket are installed. ____
10. Check jam nuts on cables and safety ladders are tightened. ____
11. Ensure cable flange clamp is installed correctly and tighten. ____
12. Ensure cylinder shaft Jam Nuts are installed as per instructions. ____
13. Ensure wheelstops are installed. ____
14. Ensure wheel chocks are provided. ____
15. Operate lift to full stroke then lower to ground while checking ____
for proper functionality.
16. Ensure Customer Care Kit is complete and given to operator. ____
a. Operation Manual ____
b. ANSI / ALI Lift It Right Manual ____
c. ANSI / ALI Safety Tip Card ____
d. ANSI / ALI ALIS Safety Requirements for Installation ____
and Service of Automotive Lifts
e. ANSI / ALI Quick Reference Guide ____
17. Train end user on operation of the lift. ____
This manual suits for next models
1
Table of contents
Popular Lifting System manuals by other brands

Genie
Genie GS-3384 Operator's manual

piER plEASURE
piER plEASURE HYDRAULIC BOAT LIFT Owner's manual & assembly guide
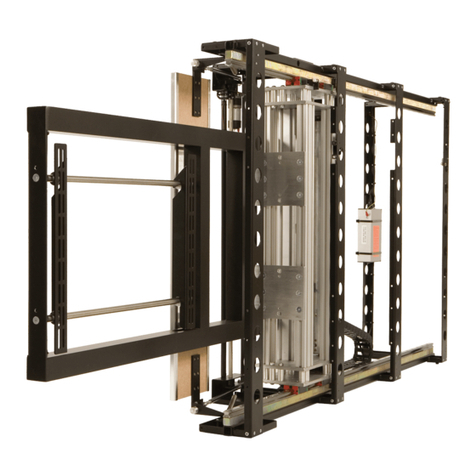
Future Automation
Future Automation HL installation instructions
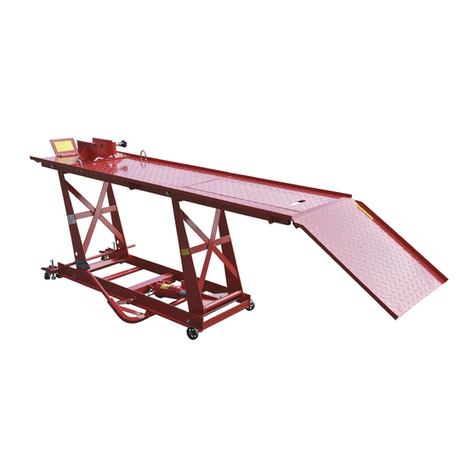
RAWLINK
RAWLINK 79587 instruction manual
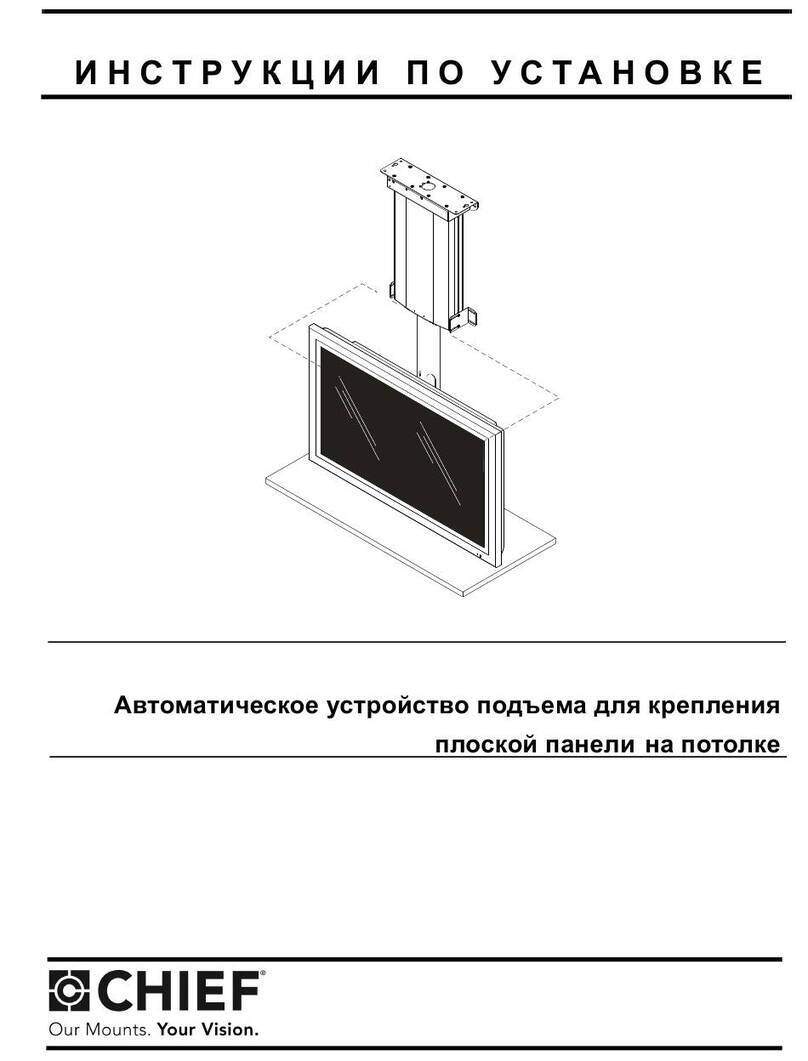
CHIEF
CHIEF CM2C40U installation instructions
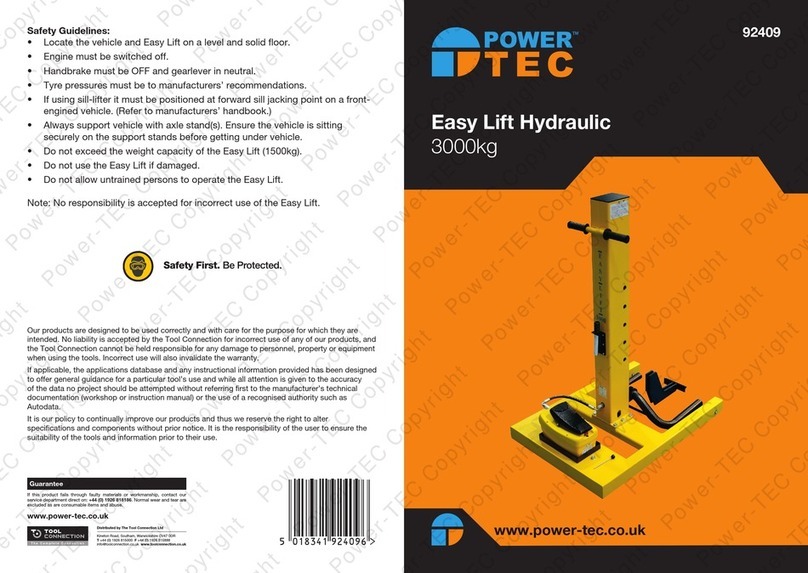
Power Tec
Power Tec Easy Lift 92409 quick start guide
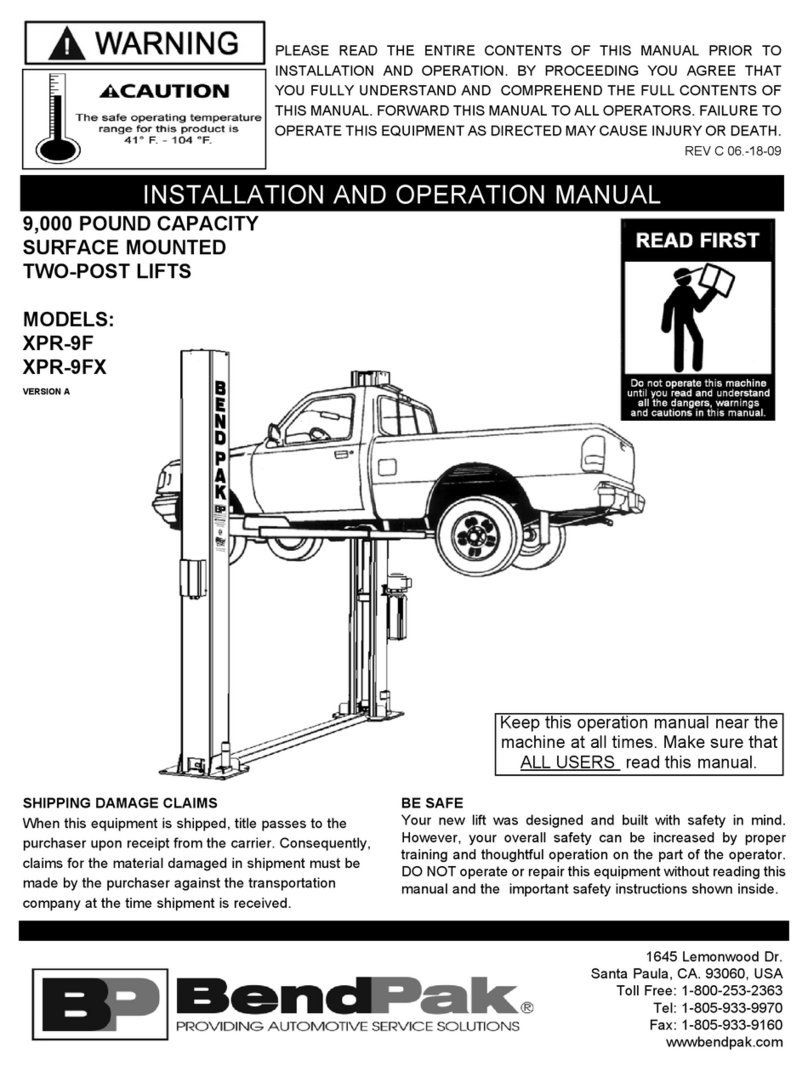
Bend-Pak
Bend-Pak XPR-9F manual
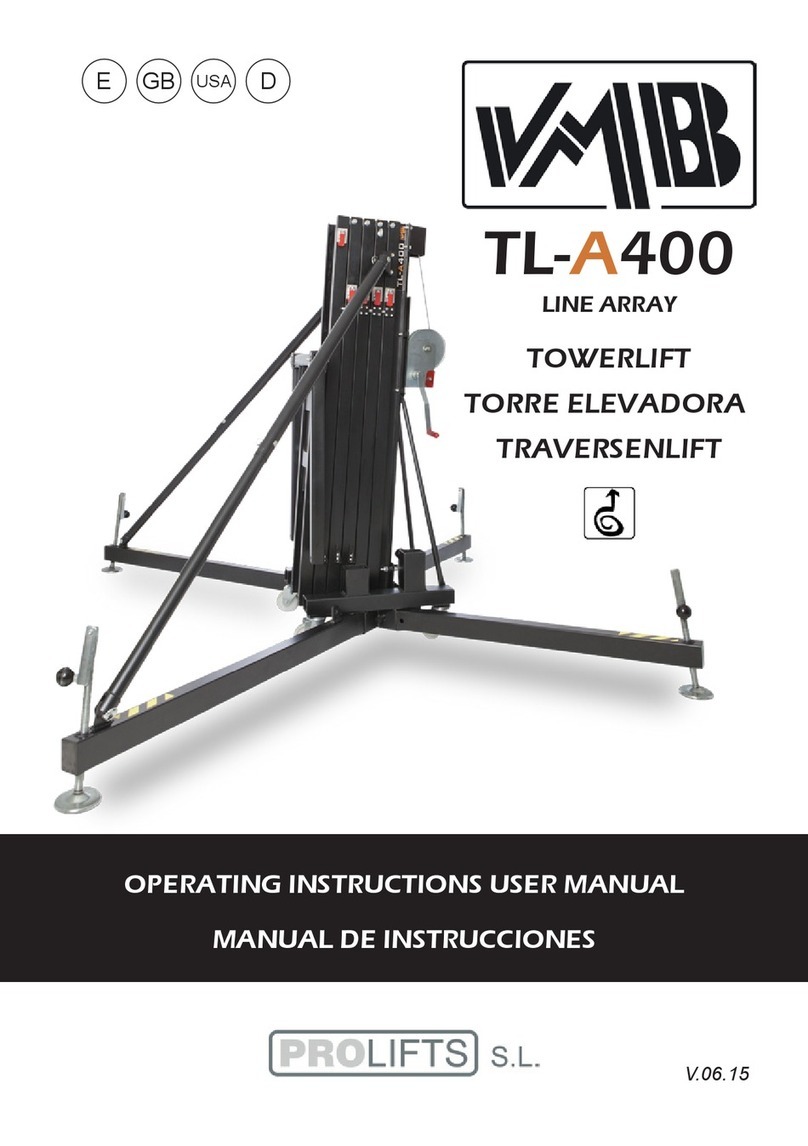
PRO LIFTS
PRO LIFTS VMB TL-A400 Operating instructions & user manual

Bend-Pak
Bend-Pak HD-9 Installation and operation manual
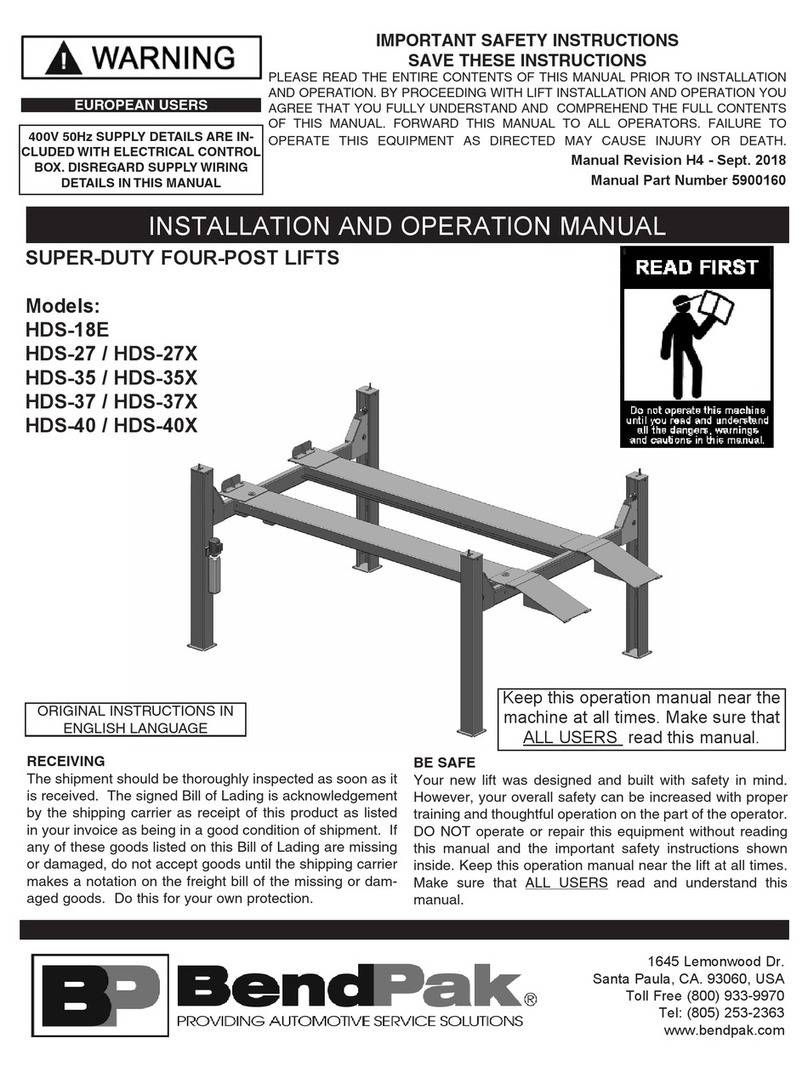
Bend-Pak
Bend-Pak HDS-37 Installation and operation manual
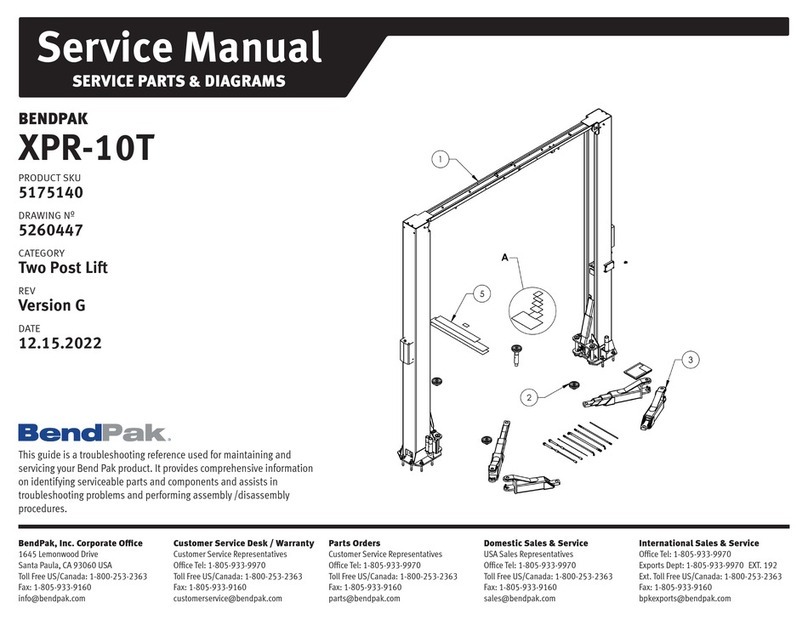
Bend-Pak
Bend-Pak XPR-10T Service manual
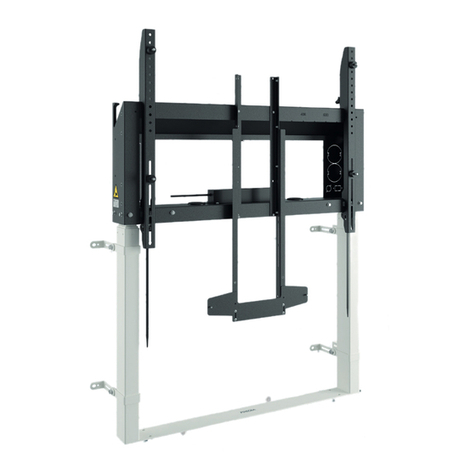
SmartMetals
SmartMetals Predia Wall lift product manual