SuperFlow CycleDyn-AC User manual

ii
Please keep this manual for future reference.
This manual is intended to assist operating personnel in becoming familiar with the product and as guidance
in ordering necessary parts inclusive of SuperFlow's warranty requirements. Maximum operating eciency
and life of any SuperFlow Product will be attained through complete understanding of the instructions and
recommendations contained within this manual.
Services performed beyond preventive
maintenance by personnel other than SuperFlow
Service Technicians on any SuperFlow products
during the warranty period may void the warranty.
!WARNING
When available, please include the model
number and serial number of the product in any
correspondence.
IMPORTANT
Copyright 2019 by SuperFlow, a division of Power Test, Inc. All rights reserved. No part of this publication may
be reproduced, transcribed, or translated by any means without the prior written permission of SuperFlow,
N60 W22700 Silver Spring Drive, Sussex, WI 53089 USA.
No part of the software or rmware provided with this product may be upgraded, modied, or changed by any
means without the prior written permission of SuperFlow.
Power Test, PowerNet, SuperFlow, WinDyn, ProFilter, SF902, XConsole, XDyno, XCart, NSCR, CycleDyn,
AutoDyn, FlowCom, SuperBench, ProExport, SF-110/120/260/450/600/750, SF-1020, SF1200, ProBench,
SuperBench, TD-1200, TDAC,AIDCO, Axiline, TCRS, Hicklin, Racer’s Pack, and SuperShifter are trademarks
of Power Test, Inc. Other trademarks and trade names may be used in this document that refer to the entities
claiming the marks and names or their products. Power Test, Inc. does not hold any proprietary interest in
trademarks or trade names other than its own.
Trademark Notices

Introduction
Welcome
Thank you purchasing the SuperFlowAC Motoring Chassis Dynamometer Option. This is a quality
product designed and manufactured to give years of dependable service. If you have any questions
or comments, please call the SuperFlow Technologies Customer Service Department in Sussex,
Wisconsin at 1-262-252-4301.
Product Features
Features of the AC Motoring Chassis Dynamometer include:
•Feature
•Feature
•Feature
•Feature
•Feature
About This Manual
This operator manual provides user information regarding basic component functions and
operational procedures. It is your responsibility to become completely familiar with the information in
this manual. Any person instructed to carry out installation, maintenance, or repair of the equipment
must read and understand this manual and in particular the technical safety instructions.
SuperFlow Technologies Group is not responsible for any personal or property damage resulting
from negligent actions by the user of this product.
How to Use This Manual
This manual is provided as a reference to explain the setup and operation of the AC Motoring Chassis
Dynamometer and contains the following information:
• Safety
General safety and operating safety, including warnings regarding non-observance of safety
instructions.
• Overview
Describes features and lists specifications.
• Packaging and Handling
Describes how the unit was packagedand what parts to expect
• Installation
Describes installation and how to prepare for operation.

•Operation
Describes the basic operation principles and procedures.
• Maintenance, Calibration & Troubleshooting
Covers general, daily, and periodical maintenance; calibration; and basic troubleshooting
procedures.
• Parts Lists
Replacement parts list.
• Drawings
Includes general drawings.
Manual Conventions
The following conventions indicate items of interest or concern:
WARNING: Failure to take or avoid a specific action could result in physical harm to the user or
the hardware.
CAUTION: Failure to take or avoid a specified action could result in loss of data or equipment.
IMPORTANT: Essential operating information.
NOTE: Helpful information that may provide insight to the user/operator.
TIP: Additional information that may provide convenient workarounds or solutions.
Cross-references refer the reader to additional information in the chapter, manual, or other sources
(including Web sites).

SuperFlow Acceptance Certificate
Agreement made _________ __, ____ between SuperFlow Technologies Group and
________________________________________________________ (hereinafter called receiver) located
at:
Receiver acknowledges and agrees that SuperFlow has supplied, installed and conducted training to
its satisfaction on the SuperFlow equipment listed below:
If any of the above components were never ordered and therefore never received, then indicate Never
Ordered in place of that component’s serial number.
Remarks: ___________________________________________________________
By: ________________________________________________________________
Contract Components
Component Description Component Serial No.
Date
Company Name
Company Location (address)


• Safety Warnings
–Dangers Due to Non-observance of Safety
Instructions
• Room Requirements
• General Safety Procedures
• Noise Levels
• Carbon Monoxide Warnings
SAFETY


Safety Warnings
SuperFlow Technologies Group 1-3
1.1 Safety Warnings
WARNING: To ensure safe operation, this equipment must only be operated according to
the instructions in the SuperFlow Dynamometer Operator’s Manual. It is also essential that
this equipment is installed, maintained, and operated according to local safety
requirements.
Any person instructed to carry out installation, maintenance or repair of the equipment must read
and understand the SuperFlow Operator’s Manual and in particular the technical safety
instructions. Any users of this equipment must operate only the controls of the equipment. Only
qualified personnel should remove exterior panels and service equipment.
1.1.1 Dangers Due to Non-observance of Safety
Instructions
• Hearing damage due to high noise level
• Electrical shock
• Exposure to rotating parts
1.2 Room Requirements
Follow all local construction codes when building a test cell.
• Install a Carbon Monoxide (CO) detector in the test cell.
• Provide fire extinguishers that are rated for gasoline and oils.
• Provide adequate lighting in the test cell and at the operators console.
• Provide a switch outside the test cell to turn off the ventilation fans and water pumps.
• Provide a means outside the test cell to shut off the fuel supply.
1.3 General Safety Procedures
CAUTION: Electronic controls contain static-sensitive parts. Observe the following precautions to
prevent damage to these parts.
•Discharge body static before handling the control (with power to the control turned off, contact a
grounded surface and maintain contact while handling the control).
•Avoid all plastic, vinyl, and Styrofoam (except antistatic versions) around Printed Circuit Boards
(PCBs).
•Do not touch the components or conductors on a PCB with your hands or with conductive
devices.
CAUTION: To prevent damage to a control system that uses an alternator or battery-charging
device, make sure the charging device is turned off before disconnecting the battery from the
system.

Safety
1-4 CycleDyn AC Motoring Chassis Dynamometer
Always follow basic safety precautions when using this product to reduce risk of injury or
damage to equipment.
• Only authorized personnel trained in the operation of the dynamometer should have access
to the equipment.
• Read and understand all instructions in the operator’s manual.
• Use only the proper electrical sources as prescribed in the installation guide. Ensure circuit
breakers are easily accessible and have the proper rating.
• Observe all warnings and instructions marked on the product.
• Provide fire extinguishers that are rated for electrical and oils.
• Provide adequate lighting in the test cell and at the operators console.
• Always wear proper protective clothing and eye/ear protection.
• Refer all service questions to qualified personnel.
• Do not remove any safety guards while the machine is in operation and be sure the safety
guards are correctly mounted before operating the device.
• Disconnect the external power switch before opening any panel on the device.
• Replace the power cable if it is damaged.
• Keep the air inlet grids free of dust or dirt.
• Keep loose material away from the inlet and exhaust ducts.
• Do not store flammable materials in the vicinity of the equipment.
• Keep all personnel, flammable items, and sensitive objects away from any rotating object
that can throw debris radially outward
1.4 Noise Levels
SuperFlow Technologies Group always recommends ear protection when operating the ________.
Warning Signs of Hazardous Noise1
• You must raise your voice to be heard.
• You cannot hear someone two feet away from you.
• Speech around you sounds muffled or dull after leaving a noise area.
• You have pain or ringing on your ears (tinnitus) after exposure to noise.
Hazardous Noise
Both the amount of noise and the duration of exposure determine the amount of damage to
hearing. Noise levels are measured in decibels (dB). The higher the decibel level, the louder the
noise.
For sound levels of 85 decibels (dB) or above, use hearing protection. Please follow all safety
standards when operating this or any equipment.
1. Information in this section was adapted from “Noise and Hearing Loss,” American Speech-Language-Hearing
Association, 1997–2007, http://www.asha.org/public/hearing/disorders/noise.htm, February 2007.

Carbon Monoxide Warnings
SuperFlow Technologies Group 1-5
1.5 Carbon Monoxide Warnings
When operating fuel-generated equipment in enclosed areas, take the following precautions to
protect you and your employees against carbon monoxide exposure.
What is carbon monoxide?1
Carbon monoxide (CO) is a poisonous, colorless, odorless, and tasteless gas. Although it has no
detectable odor, CO is often mixed with other gases that do have an odor; therefore, you can
inhale carbon monoxide right along with gases you can smell and not even know that CO is
present.
CO is a common industrial hazard resulting from the incomplete burning of natural gas and any
other material containing carbon such as gasoline, kerosene, oil, propane, coal, or wood. One of
the most common sources of exposure in the workplace is the internal combustion engine.
How does CO harm you?
Carbon monoxide is harmful when breathed because it displaces oxygen in the blood and
deprives the heart, brain, and other vital organs of oxygen. Large amounts of CO can overtake you
in minutes without warning—causing you to lose consciousness and suffocate.
Besides tightness across the chest, initial symptoms of CO poisoning may include headache,
fatigue, dizziness, drowsiness, or nausea. Sudden chest pain may occur in people with angina.
During prolonged or high exposures, symptoms may worsen and include vomiting, confusion,
and collapse in addition to loss of consciousness and muscle weakness. Symptoms vary widely
from person to person. CO poisoning may occur sooner in those most susceptible: young children,
elderly people, people with lung or heart disease, people at high altitudes, or those who already
have elevated CO blood levels such as smokers. CO poisoning poses a special risk to fetuses.
Acute poisoning may result in permanent damage to the parts of your body.
How can employers help prevent CO poisoning?
To reduce the chances of CO poisoning in your workplace:
• Install an effective ventilation system that will remove CO from work areas.
• Maintain equipment and appliances that can produce CO to ensure they are in good
working order, promote their safe operation, and reduce CO formation.
• Consider switching from gasoline-powered equipment to equipment powered by
electricity, batteries, or compressed air if it can be used safely.
• Prohibit the use of gasoline-powered engines or tools in poorly ventilated areas.
• Provide personal CO monitors with audible alarms if potential exposure to CO exists.
• Test air regularly in areas where CO may be present, including confined spaces.
• Install CO monitors with audible alarms.
1. Information in this section was adapted from the “OSHA Fact Sheet,” U.S. Department of Labor, Occupational Safety
and Health Administration, 2002, http://www.osha.gov/OshDoc/data_General_Facts/carbonmonoxide-factsheet.pdf,
February 2007.

Safety
1-6 CycleDyn AC Motoring Chassis Dynamometer
• Use a full-face piece, pressure-demand, Self-Contained Breathing Apparatus (SCBA)
certified by the National Institute for Occupational Safety and Health (NIOSH) or a
combination full-face piece, pressure demand supplied-air respirator with auxiliary self-
contained air supply in areas with high CO concentrations (those immediately dangerous to
life and health atmospheres).
• Use respirators with appropriate canisters for short periods under certain circumstances
where CO levels are not exceedingly high.
• Educate workers about the sources and conditions that may result in CO poisoning as well
as the symptoms and control of CO exposure.
• In addition, if your employees are working in confined spaces where the presence of CO is
suspected, you must ensure that workers test for oxygen sufficiency before entering.
What can employees do to help prevent CO poisoning?
To reduce the chances of CO poisoning in the workplace, employees should:
• Report any situation to your employer that might cause CO to accumulate.
• Be alert to ventilation problems—especially in enclosed areas where gases of burning fuels
may be released.
• Report promptly complaints of dizziness, drowsiness, or nausea.
• Avoid overexertion if you suspect CO poisoning, and leave the contaminated area.
• Tell your doctor that you may have been exposed to CO if you get sick.
• Avoid the use of gas-powered engines, such as those in powered washers as well as heaters
and forklifts, while working in enclosed spaces.
What are the OSHA standards for CO exposure?
The OSHA PEL is 50 parts per million (ppm). OSHA standards prohibit worker exposure to more
than 50 parts of the gas per million parts of air averaged during an 8-hour time period.
For more information on carbon monoxide, visit the OSHA Web site at http://www.osha.gov.


Introduction
SuperFlow Technologies Group 2-3
2.1 Introduction
Figure 2-1. CycleDyn AC Motoring Dynamometer with EC Absorber Option
A dynamometer, or “dyno” for short, is a device used to measure the torque and horsepower
output of an engine. On a chassis dynamometer, torque is produced by applying a force or load on
the vehicle tires as they rotate. Horsepower is calculated by simultaneously measuring the torque
along with the rotational speed of the dynamometer.
The SuperFlow CycleDyn is a motorcycle chassis dynamometer designed to test motorcycles, go-
karts, ATVs (quads), and similar vehicles within a safe, controlled environment. Testing on a
dynamometer reduces road testing liability, improves measurement accuracy, and enhances
productivity. Typical applications include:
• Research and Development (R&D)
• Performance testing and tuning
• Diagnostics
• Durability and quality control
• Fuel consumption and emissions testing
•Education
• Vehicle certification
CAUTION: This equipment generates, uses, and can radiate radio frequency energy. If not
installed according to the CycleDyn Operator Manual, this equipment may cause interference to
radio communications. The equipment was designed to provide reasonable protection against
such interference when operated in a commercial environment. Operating this equipment in a
residential area is likely to cause interference, and the user will be required to correct the
interference at the user’s own expense.

2-4 AC Motoring Chassis Dynamometer
A dynamometer can also be used to determine the
power required to “drive” an engine or vehicle. In
thatcase,a motoring ordrivingdynamometer isused.
A dynamometer that is designed to only be driven by
the machine under test (MUT) is called an absorption
or passive dynamometer. These are typically water
brake or eddy current systems. A dynamometer that
can either drive or absorb is called a universal or
active dynamometer. Universal dynamometers can
not only absorb the power of the MUT but can also
drive the MUT for measuring friction, drive train
losses and other factors.
Figure 2-2. AC Motor Module
The SuperFlow motoring dynamometer uses an AC electric motor with a specialized type of
adjustable-speed drive. This setup classifies the system as a “universal” dynamometer where it
can operate:
• As a generator that is driven by the MUT and applies a load as commanded by the system
controller. In this mode the dyno functions as a typical water brake or eddy current system.
However, the power “absorbed” by the AC motor must be transferred to a resistive load
(load bank) or other outlet. In some systems, regenerative control units can transfer power
from the unit under test to the electric utility where owner of the dynamometer can receive
payment (or credit) from the utility for the returned power.
• As a motor that spins the dynamometer roll in controlled conditions, and therefore can
“drive” the MUT at a desired speed or torque setpoint.
A motoring dynamometer provides the features of a brake dynamometer system, but can also can
measure the frictional losses in an engine and allow testing of very small power small outputs. On
chassis dynamometers it can duplicate speeds and loads that are experienced when operating a
vehicle traveling downhill or on/off throttle operations. Many tests can even be run without the
test vehicle’s engine running.
In addition to being used to determine the torque or power characteristics of a machine under test,
motoring dynamometers are employed in a number of other roles. In standard emissions testing
cycles such as those defined by the US Environmental Protection Agency (US EPA),
dynamometers are used to provide simulated road loading of either the engine (using an engine
dynamometer) or the full power train (using a chassis dynamometer). The hardware and software
system can then “motor” the test vehicle to perform emissions drive cycles and inertia
simulations, evaluate frictional losses, map Engine Control Units (ECUs) and numerous other
engineering-grade test procedures. Using the AC Motoring option, you can test brakes,
drivetrains, and other chassis components.
In fact, beyond simple power and torque measurements, motoring dynamometers can be used as
part of a test bed for a variety of engine development activities such as the calibration of engine
management controllers or detailed investigations into combustion behavior.

Specifications
SuperFlow Technologies Group 2-5
2.2 Specifications
NOTE: These specifications are for a standard 75hp model and may vary based on the actual motor
used. Refer to the documentation provided with the individual units for precise information.
• Dynamometer Power Rating
– Inertia only: 500 hp [370 kW]
– AC Motor: contingent on power rating of AC Motor
– Continuous with Eddy Current option: 300 hp @ 80 mph [220 kW @ 130 Kph]
• Inertia Simulation
– 50 – 1,250 lbs [22.7 – 568.2 kg]
• Load Bank Breaking Power
– 58,000 Watts continuous
• Torque Measurement
– In-line rotary torque transducer
• Power Requirements (motor drive)
– 480 VAC, 200 Amps, 3Ph, 50 or 60 hz
• Dimensions (standard model only)
– AC Motor module: 35 L x 23 W x 21 H inches [89 x 58 x 54 cm]
– AC Motor Drive: 17 W x 17 D x 36 H inches [43 x 43 x 110 cm]
– AC Load Bank: 30 W x 18 D x 40 H [76 x 46 x 102 cm]
• Weights
– AC Motor Module: 1200 lbs [545 kg]
– AC Motor Drive: 170 lbs [77 kg]
– AC Load Bank: 250 lbs [114 kg]
• Shipping weights and dimensions
– AC Motor module: 1400 lbs / 60 x 35 x 28 inches [635 kg / 152 x 89 x 71 cm]
– AC Drive Unit: 175 lbs / 39 x 17 x 24 inches [80 kg / 99 x 43 x 61 cm]
– AC Load Bank: 250 lbs / 36 x 22 x 46 inches [115 kg / 92 x 56 x 117 cm]

2-6 AC Motoring Chassis Dynamometer
2.3 Packaging and Handling
The components of a CycleDyn dynamometer are shipped on wooden pallets or in crates. It is
shrinkwrapped and covered by a fitted cardboard box secured by plastic or metal straps.
CAUTION: The dynamometer modules may have UNEVEN weight distributions.
2.3.1 Lifting and Handling Instructions
If possible, leave the dynamometer and auxiliary modules on the shipping pallets until ready for
installation.
Place hooks on a lifting chain or strap into theopenings at each end of
the AC Motor module. Lift the module carefully and place it into
position. You can make the final adjustment of the module position by
hand.
Once off the pallet, use a forklift or pallet jack to move the frames or
modules. Make sure the forks are completely across the frame and
extend out the opposite side. Always use blocks under the frame
edges when removing the forklift or pallet jack.
Use an overhead hoist to lower the dynamometer frame and modules to their final position on the
floor. Never push the frame off the forklift, pallet jack, or blocks.
WARNING: Failure to use the lift points indicated or improperly using a hoist or forklift
may result in damage or severe personal injury.
TIP: An alternative method for moving the dynamometer and modules is to use a heavy-duty strap
under the frame and lift them with a forklift or hoist. When the dynamometer is in position, slide
the strap out from under the frame.
2.3.2 Packaging
Use the list below as a general checklist when the system arrives. The list describes a standard
75HP AC Motor option. Individual systems may vary; this list is for a standard system and does
not include options. Check the order acknowledgement for the exact listing for the particular
system.
AC Motor module
4-foot calibration arm
Calibration support arm with turnbuckle link
Motor Drive Unit
Regenerative Load Bank
Shaft coupler with in-line torque transducer
Six each ½-13 x 1-½ bolts to connect the AC Motor module to the main dynamometer frame
Cable, Sensor Box to AC Motor Drive (1200A-0270)
Cable, Sensor Box to AC Motor Drive (1200A-0271)

Installation
SuperFlow Technologies Group 2-7
2.4 Installation
IMPORTANT: This section covers only the installation of an AC Motor module on a dynamometer.
Refer the regular system operator’s manual for details on the installation of the dynamometer itself
and the Eddy Current option if applicable. Read the unpacking and inspection instructions in it’s
entirety before installing the dynamometer or any accessories.
The installation involves both mechanical connections and electrical connections.
• The AC Motor module attaches to the roll shaft on the dynamometer chassis but can also be
coupled to an eddy current module to provide even greater testing capability.
• The motor drive unit connects to the AC motor, the resistive load bank (if applicable), and
to the data acquisition system (sensor box).
Consider where the dynamometer will be located. The floor must be level and able to support the
weight of the dynamometer, all add-on options, and the vehicle under test including the operator.
Allow access space on all sides of the dynamometer.
Inspect allcrates and boxes for external damage.Be sure to check underneath the crate forpossible
forklift damage. Report any damage to the shipping company and SuperFlow Customer Service.
Unpack the equipment and take inventory of all the provided parts. Contact SuperFlow Customer
Service if there are any questions.
2.4.1 Mechanical Connections
Detailed information for this section is pending.
Figure 2-3. AC Motor Coupling - Overview

2-8 AC Motoring Chassis Dynamometer
1. Attach the AC Motor cube to the side of the main CycleDyn chassis ensuring the cube is level.
2. Insert the shaft keys and slide the couplers on the shafts.
3. Place the keys and couplers on the in-line torque/speed transducer
4. Mount the transducer assembly on the bracket in the AC Motor cube. Be certain to mount the
nylon cushions on both sides of the bracket.
5. Bolt the couplers together.
6. Verify the coupler and transducer run-out is less than 0.020". Adjust if necessary.
Table of contents
Other SuperFlow Measuring Instrument manuals
Popular Measuring Instrument manuals by other brands

CMT ORANGE TOOLS
CMT ORANGE TOOLS DAG-001 quick guide

Chauvin Arnoux
Chauvin Arnoux PAC 21 user manual
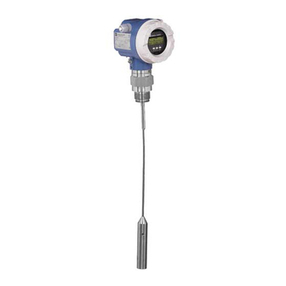
Endress+Hauser
Endress+Hauser Levelflex M FMP40 Description of Device Functions

Desco
Desco 19665 Installation, operation and maintenance
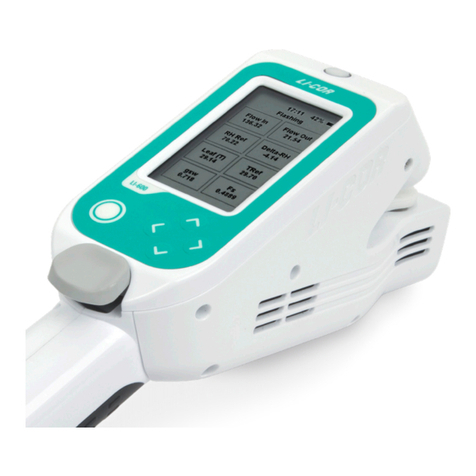
LI-COR
LI-COR LI-600 instruction manual
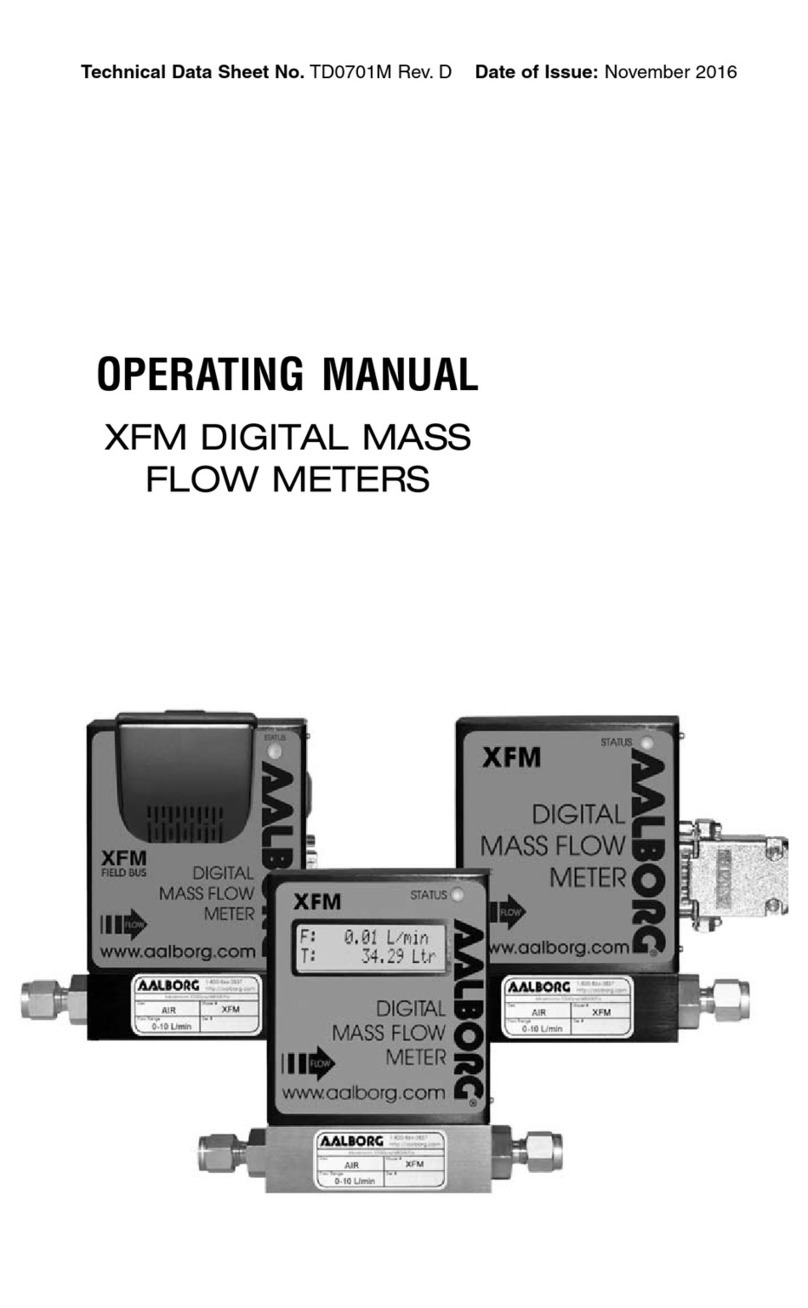
Aalborg
Aalborg XFM Series operating manual
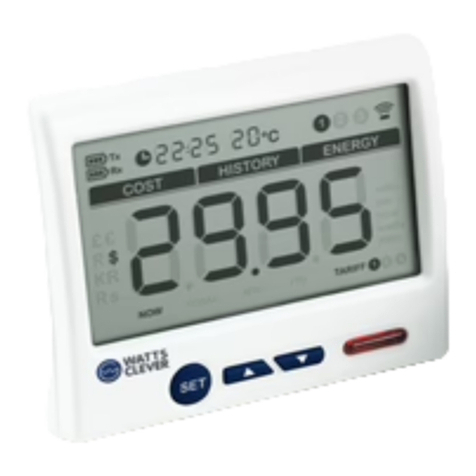
Watts Clever
Watts Clever EW4008 instruction manual
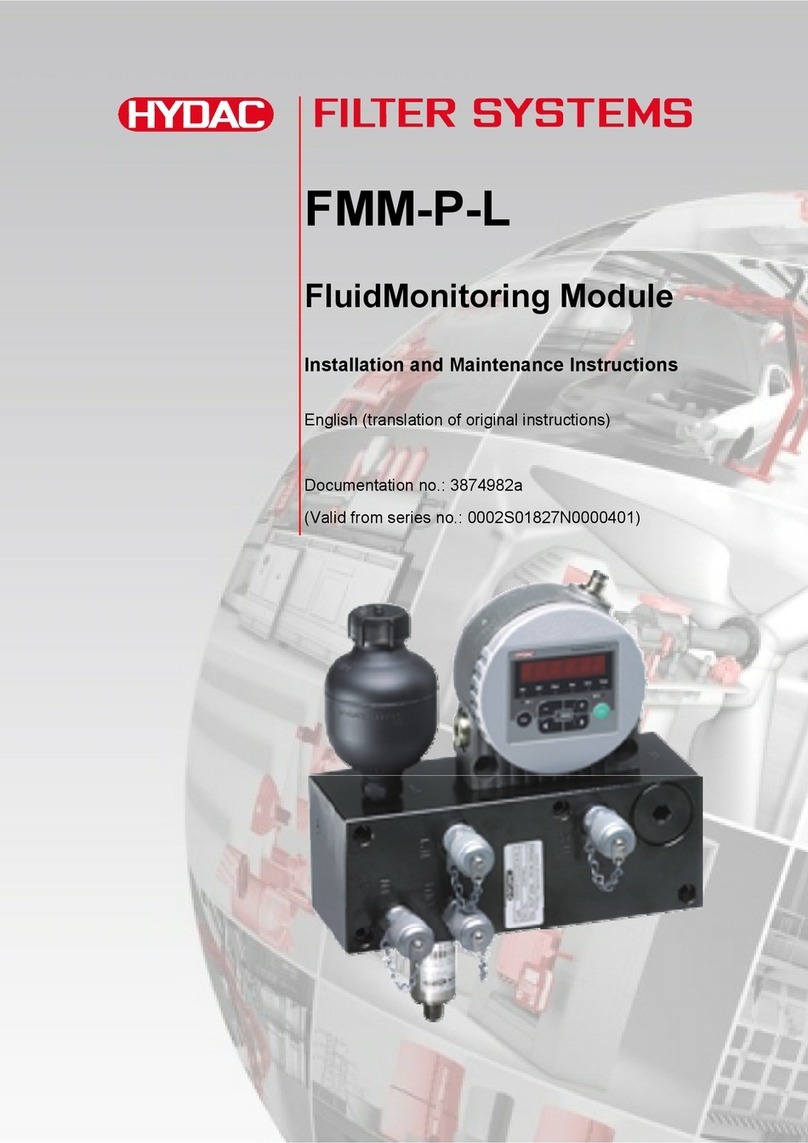
HYDAC FILTER SYSTEMS
HYDAC FILTER SYSTEMS FMM-P-L Installation and maintenance instruction
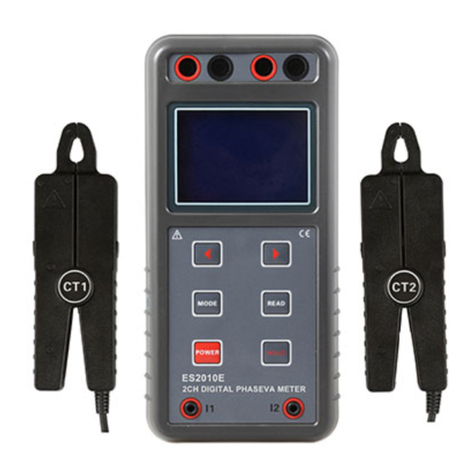
Electronic Technologies
Electronic Technologies ES2010E user manual
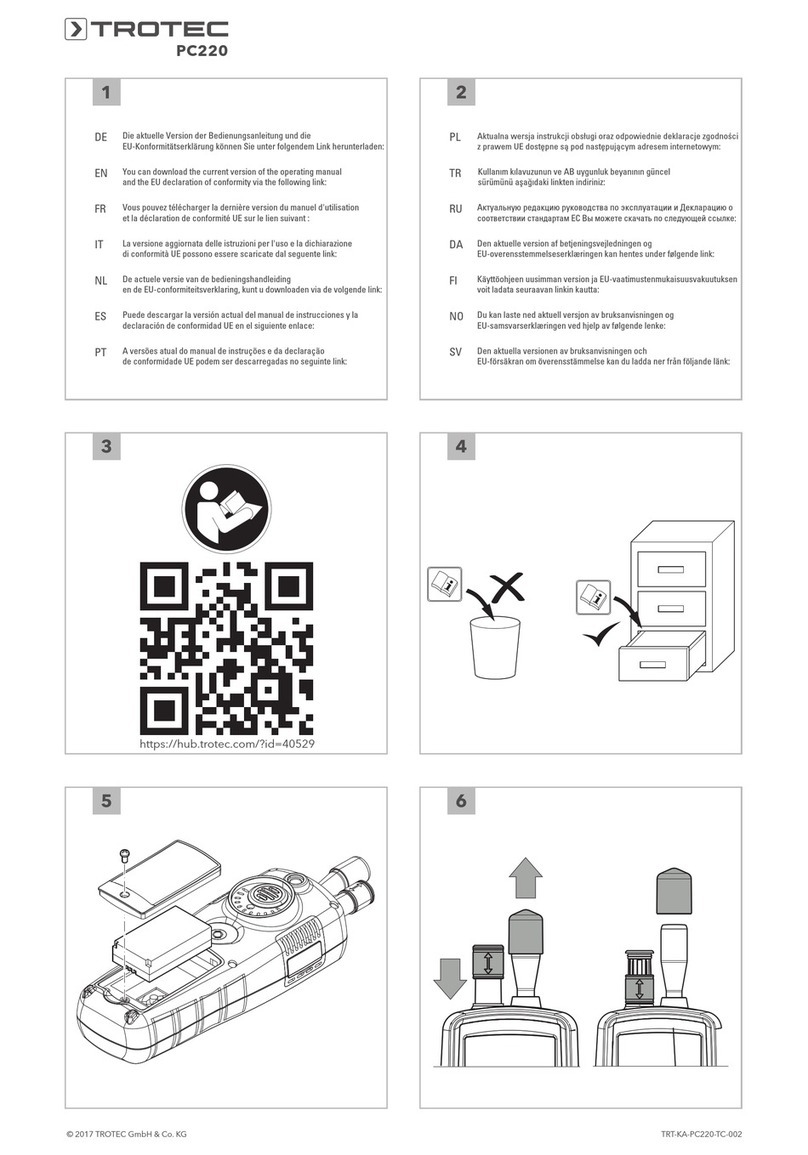
Trotec
Trotec PC220 quick start guide
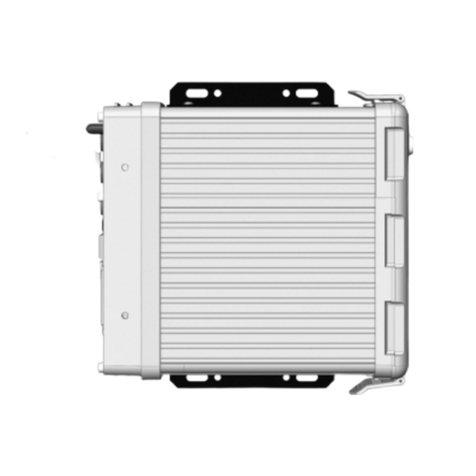
Gatekeeper
Gatekeeper G4-508HD4a User manual & installation guide

Anritsu
Anritsu MS2665C Service manual