TDK InvenSense RoboKit1 Operating and maintenance manual

AN-000350
InvenSense, Inc. reserves the right to change
specifications and information herein without
notice unless the product is in mass production
and the application note has been designated by
InvenSense in writing as subject to a specified
Product / Process Change Notification Method
regulation.
InvenSense, a TDK Group Company
1745 Technology Drive, San Jose, CA 95110 U.S.A
+1(408) 988–7339
invensense.tdk.com
Document Number: AN-000350
Revision: 1.0
Release Date: 01/24/2022
RoboKit1 Hardware
Reference Guide

AN-000350
Document Number: AN-000350 Page 2 of 13
Revision: 1.0
TABLE OF CONTENTS
1RoboKit1 Module................................................................................................................................................... 3
Introduction................................................................................................................................................. 3
Connections ................................................................................................................................................. 4
Instructions to load the RoboKit Firmware Image....................................................................................... 4
Powering on................................................................................................................................................. 5
Header Pin configurtion............................................................................................................................... 6
LEDs ............................................................................................................................................................. 6
Chirp connections ........................................................................................................................................ 7
Industrial IMU (IIM-46230) connection ....................................................................................................... 8
Motor controller connections...................................................................................................................... 9
Switching data output between USB1 and header Pins ............................................................................10
2References ........................................................................................................................................................... 12
3Revision History ................................................................................................................................................... 13
Figure 1. RoboKit1 Top View .........................................................................................................................................3
Figure 2. RoboKit1 Bottom View ...................................................................................................................................4
Figure 3. RoboKit1 USB Ports.........................................................................................................................................4
Figure 4. Loading Firmware ...........................................................................................................................................5
Figure 5. Powering On ................................................................................................................................................... 5
Figure 6. LEDs ................................................................................................................................................................7
Figure 7. Chirp Connectors ............................................................................................................................................8
Figure 8. RoboKit with Chirp connected........................................................................................................................8
Figure 9. IIM Socket on RoboKit1 and IIM 46230 ..........................................................................................................9
Figure 10: Switches and Jumpers for Motor Controllers...............................................................................................9
Figure 11. Motor Control Header Pins Connections....................................................................................................10
Figure 12. Switch for Protocol interface over USB or Header Pins..............................................................................10
Figure 13. RoboKit and ESP32 Connections.................................................................................................................11
Table 1. Header Pins ...................................................................................................................................................... 6
Table 2. LED GPIO Pins...................................................................................................................................................7

AN-000350
Document Number: AN-000350 Page 3 of 13
Revision: 1.0
1ROBOKIT1 MODULE
INTRODUCTION
This document provides details of the RoboKit1 board, the location of various sensors on the board, power
supplies, communication interface, a description of the header pins, LED connections, and a description of how to
connect the Chirp CH101 and CH201 modules and Industrial IMU (IIM-46230). Figure 1 shows the top view and
Figure 2 shows the bottom view of a RoboKit1 board. The RoboKit1 has a Pressure sensor, IMU, Temperature
sensor, Magnetometer, Microphone, Motor controller, and Battery connector. It also provides connectors to
connect nine ultrasonic Time of Flight sensors (Chirp CH101/CH201) and a socket to connect industrial grade IMU
as well.

AN-000350
Document Number: AN-000350 Page 4 of 13
Revision: 1.0
CONNECTIONS
As shown in Figure 3, USB1 is used for power supply and for serial interface with the board. USB2 is used as port
for debug messages, and USB 3 is used to load the firmware image.
INSTRUCTIONS TO LOAD THE ROBOKIT FIRMWARE IMAGE
Connect a micro-USB cable to USB1 for power supply (note that when USB is connected to the USB1 Power port,
the LEDs D1 and D2 at the top right corner should be turned on), and connect a micro-USB cable to USB 3 EDBG
port for loading the image, turn ON the four switches “SW5” (move them towards the blue push button) and run
following command.
edbg-b61-WINDOWS-175e58c.exe -b -t same70 -pv -f rkbin-1.0.20211025.088a.bin
Where rkbin-1.0.20211025.088a.bin is RoboKit firmware

AN-000350
Document Number: AN-000350 Page 5 of 13
Revision: 1.0
After loading the image if USB 3 EDBG port connection needs to be removed turn OFF all the four switches of
“SW5” (move them away from the blue push button).
POWERING ON
As described in the Figure 5 below, power to the board can be supplied either through USB1 or by connecting a
11.1 Volt battery with XT30 connector. When the power is supplied through USB1 the board will not be able to
drive the motors. However, when the power is supplied through the battery connector it will be able to drive the
motors. The RoboKit1 has an on/off switch to turn the power on or off and a reset button to reset the board.

Document Number: AN-000350 Page 6 of 13
Revision: 1.0
HEADER PIN CONFIGURTION
The Robokit board has a 40 pins header J30, the functionality of the pins is as described in the Table 1.
DESCRIPTION SIGNAL NAME PIN PIN SIGNAL NAME DESCRIPTION
SPI 0 Chip Select 0
PA31_SPI0_CS0
1
2
5V_RASP
5V Power Supply
SPI 0 Chip Select 1
PD0_SPI0_CS1
3
4
5V_RASP
5V Power Supply
Not Used
PC23_SPI0_CS1
5
6
VDD_3V3
3.3V Power Supply
SPI 0 Chip Select 2
PC29_SPI0_CS2
7
8
VDD_3V3
3.3V Power Supply
SPI 0 Chip Select 3
PC30_SPI0_CS3
9
10
VDD_1V8P
1.8V Power Supply
SPI 0 Chip Select 4
PC31_SPI0_CS4
11
12
VDD_1V8P
1.8V Power Supply
USART 0 CTS
PD19_USART0_CTS_3V3
13
14
PD18_USART0_RTS_3V3
PD10_GPIO
15
16
PD11_GPIO
PD12_GPIO
17
18
PD13_GPIO
PC27_SPI1_MOSI
19
20
PD22_SPI0_CLK
PC26_SPI1_MISO
21
22
PD17_GPIO
PC24_SPI1_CLK
23
24
PD23_GPIO
PC25_SPI1_CS0
25
26
PD24_GPIO
PD20_SPI0_MISO
27
28
PD29_GPIO
PD30_GPIO
29
30
PD31_GPIO
PE3_GPIO
31
32
GND
PD21_SPI0_MOSI
33
34
PE4_GPIO
PD25_UART2_RX_ROBO
35
36
PD16_USART0_TX_3V3
PD26_UART2_TX_ROBO
37
38
PD15_USART0_RX_3V3
GND
39
40
GND
GND
Table 1. Header Pins
LEDS
The RoboKit1 board has four general purpose LEDs as shown in the Figure 6 and as described in the Table 2.

Document Number: AN-000350 Page 7 of 13
Revision: 1.0
Figure 6. LEDs
MCU PIN
MCU SIGNAL
FUNCTION
LED NAME
64
PA11
LED1
D7
68
PA12
LED2
D8
42
PA13
LED3
D9
51
PA14
LED4
D10
Table 2. LED GPIO Pins
CHIRP CONNECTIONS
There are nine connectors to connect the Chirp modules. CH101 or CH201 can be connected to any or all nine of
the connectors. Six connectors are on the top and three connectors are at the bottom of the board. The connector
numbering is described in the Figure 7. Figure 7 shows how to connect the Chirp module to the RoboKit1 using a
flex cable.

Document Number: AN-000350 Page 8 of 13
Revision: 1.0
Figure 7. Chirp Connectors
Figure 8. RoboKit with Chirp connected
INDUSTRIAL IMU (IIM-46230) CONNECTION
Industrial IMU (IIM-4230) is an add-on module. It is connected to the RoboKit1 board through the connector J32
and is mounted at the space allocated on the board as shown in the Figure 9.

Document Number: AN-000350 Page 9 of 13
Revision: 1.0
Figure 9. IIM Socket on RoboKit1 and IIM 46230
MOTOR CONTROLLER CONNECTIONS
For the RoboKit1 board to drive the motors, 11.1 Volts of power must be supplied through the XT30 connector, the
pins 2 and 3 of jumpers J17 and J27 should be connected, SW10 should be in ON position, and SW11 in OFF
position. Figure 10 describes the locations of J17, J27 SW10, and SW11. The connectors J13 and J24 are used to
load the Motor controller firmware image to the Master (U17) and Slave (U19) Motor controllers respectively.
Figure 11 describes the master and slave motor controller pins connections to the Motors.
Figure 10: Switches and Jumpers for Motor Controllers

Document Number: AN-000350 Page 10 of 13
Revision: 1.0
Figure 11. Motor Control Header Pins Connections
SWITCHING DATA OUTPUT BETWEEN USB1 AND HEADER PINS
For the USART0 interface over the USB1, the Switch SW16 on the back side of the board should ON. For the
USART0 Tx and Rx over the J30 header pins 36 and 38 respectively as shown in Figure 13, the Switch SW16 should
be OFF. Figure 12 shows the location of the switch on the RoboKit1 board.
Figure 12. Switch for Protocol interface over USB or Header Pins

Document Number: AN-000350 Page 11 of 13
Revision: 1.0
Figure 13. RoboKit and ESP32 Connections

Document Number: AN-000350 Page 12 of 13
Revision: 1.0
2REFERENCES
https://invensense.tdk.com/robokit/
https://invensense.tdk.com/products/motion-tracking/6-axis/icm-42688-p/
https://invensense.tdk.com/products/1-axis/icp-101xx/icp-10111/
https://invensense.tdk.com/products/ics-43434/
https://invensense.tdk.com/products/ch101/
https://invensense.tdk.com/products/ch201/
https://www.akm.com/global/en/products/electronic-compass/lineup-electronic-compass/ak09918c/
https://www.micronas.tdk.com/en/products/embedded-motor-controllers/hvc-4223f4420f

Document Number: AN-000350 Page 13 of 13
Revision: 1.0
3REVISION HISTORY
REVISION DATE REVISION DESCRIPTION
01/24/2022 1.0 Initial Draft
This information furnished by InvenSense or its affiliates (“TDK InvenSense”) is believed to be accurate and reliable. However, no responsibility
is assumed by TDK InvenSense for its use, or for any infringements of patents or other rights of third parties that may result from its use.
Specifications are subject to change without notice. TDK InvenSense reserves the right to make changes to this product, including its circuits
and software, in order to improve its design and/or performance, without prior notice. TDK InvenSense makes no warranties, neither expressed
nor implied, regarding the information and specifications contained in this document. TDK InvenSense assumes no responsibility for any claims
or damages arising from information contained in this document, or from the use of products and services detailed therein. This includes, but is
not limited to, claims or damages based on the infringement of patents, copyrights, mask work and/or other intellectual property rights.
Certain intellectual property owned by InvenSense and described in this document is patent protected. No license is granted by implication or
otherwise under any patent or patent rights of InvenSense. This publication supersedes and replaces all information previously supplied.
Trademarks that are registered trademarks are the property of their respective companies. TDK InvenSense sensors should not be used or sold
in the development, storage, production or utilization of any conventional or mass-destructive weapons or for any other weapons or life
threatening applications, as well as in any other life critical applications such as medical equipment, transportation, aerospace and nuclear
instruments, undersea equipment, power plant equipment, disaster prevention and crime prevention equipment.
©2022 InvenSense. All rights reserved. InvenSense, MotionTracking, MotionProcessing, MotionProcessor, MotionFusion, MotionApps, DMP,
AAR, and the InvenSense logo are trademarks of InvenSense, Inc. The TDK logo is a trademark of TDK Corporation. Other company and product
names may be trademarks of the respective companies with which they are associated.
©2022 InvenSense. All rights reserved.
Table of contents
Other TDK Network Hardware manuals
Popular Network Hardware manuals by other brands

Cabletron Systems
Cabletron Systems SWPIM-BRI installation guide
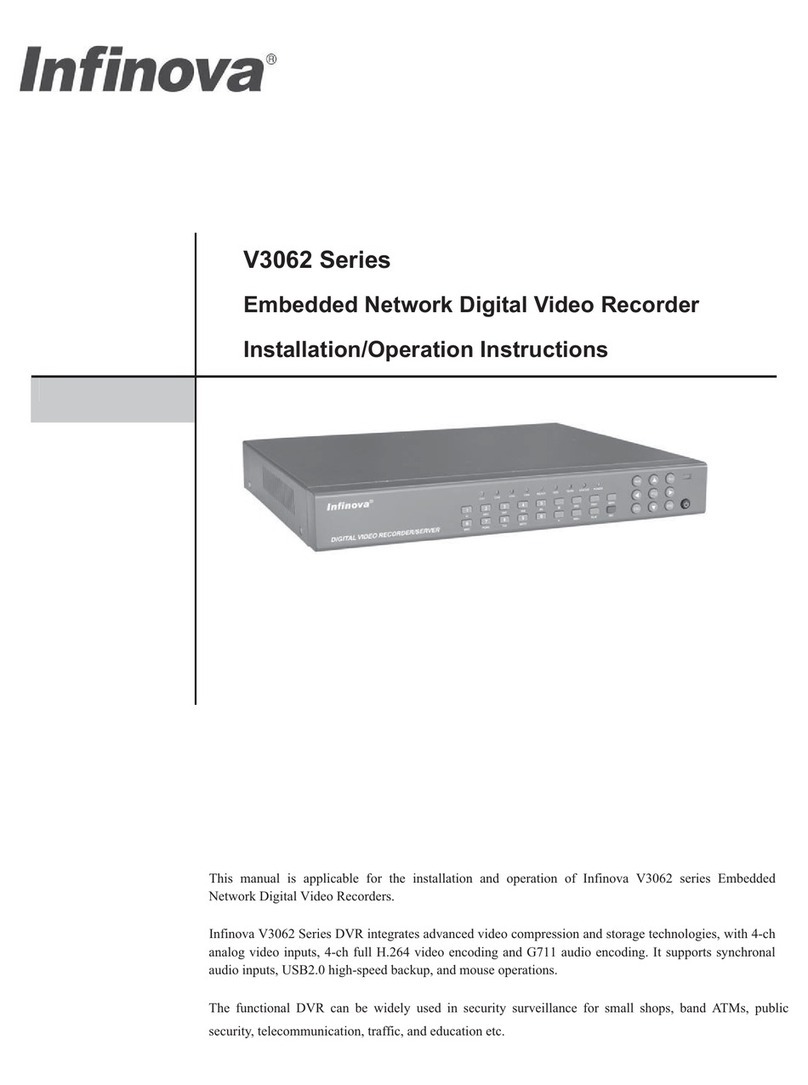
Infinova
Infinova V3062 Series Installation & operation instructions
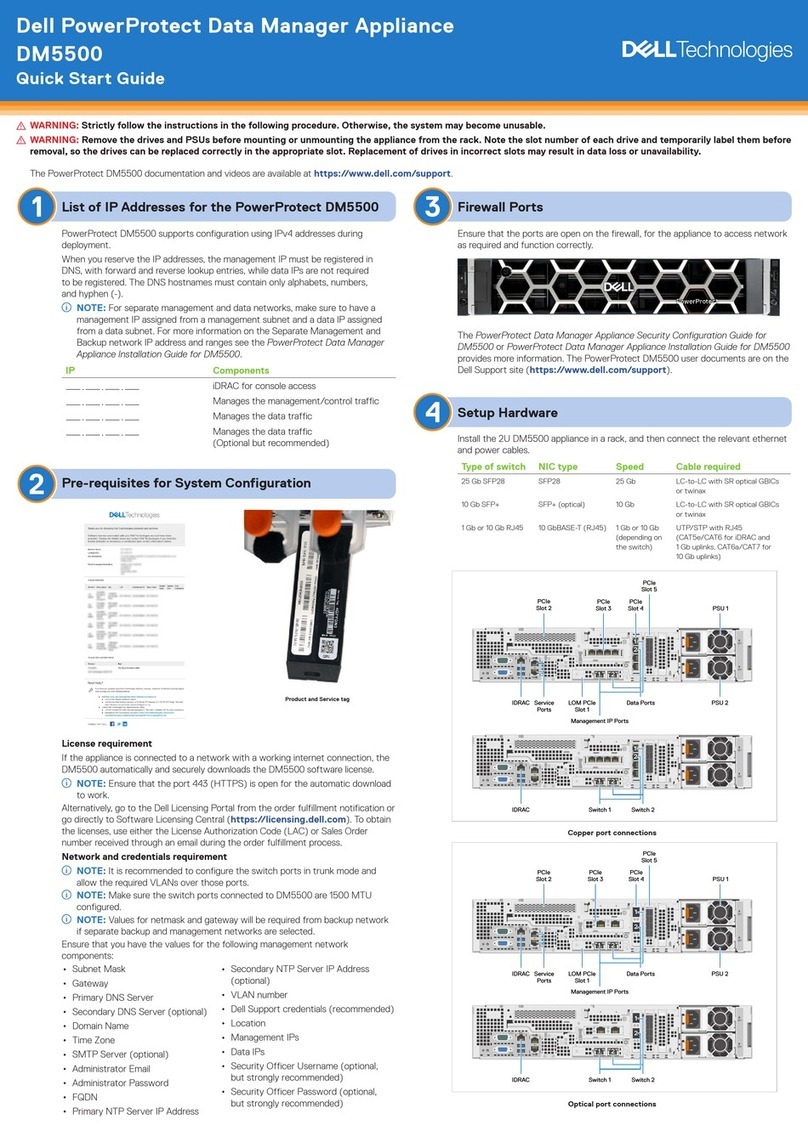
Dell
Dell PowerProtect DM5500 quick start guide

ZyXEL Communications
ZyXEL Communications WAP6405 quick start guide
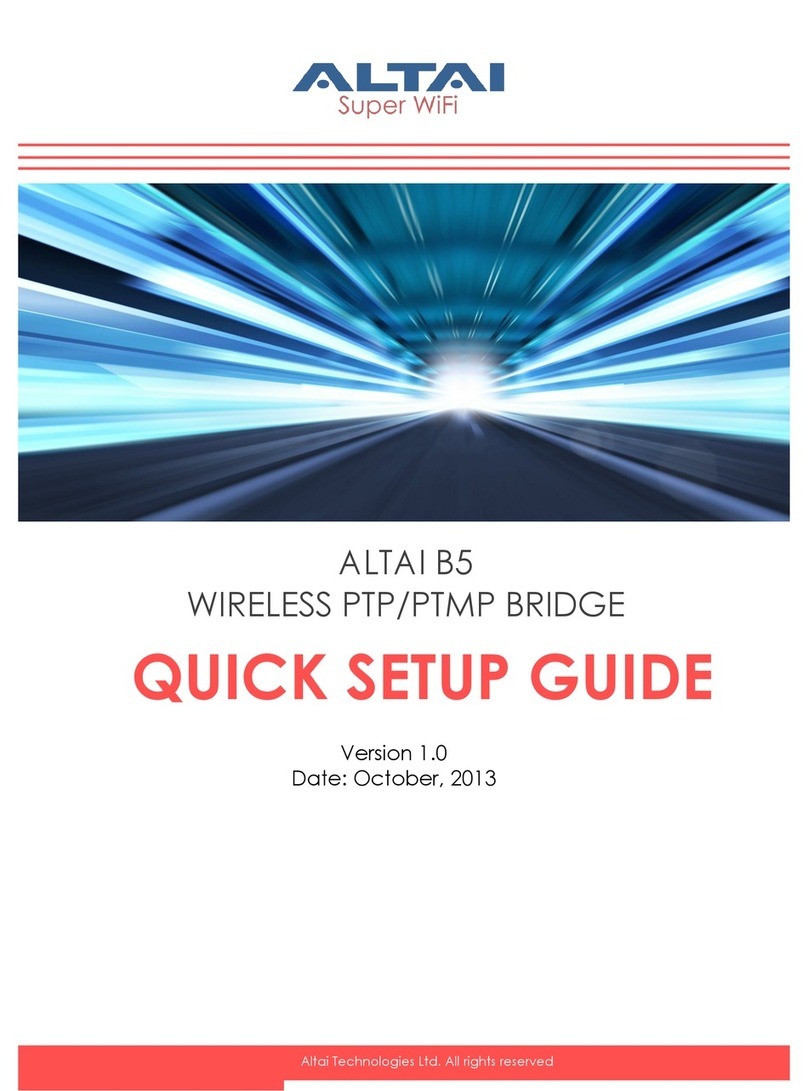
ALTAI
ALTAI B5 Quick setup guide
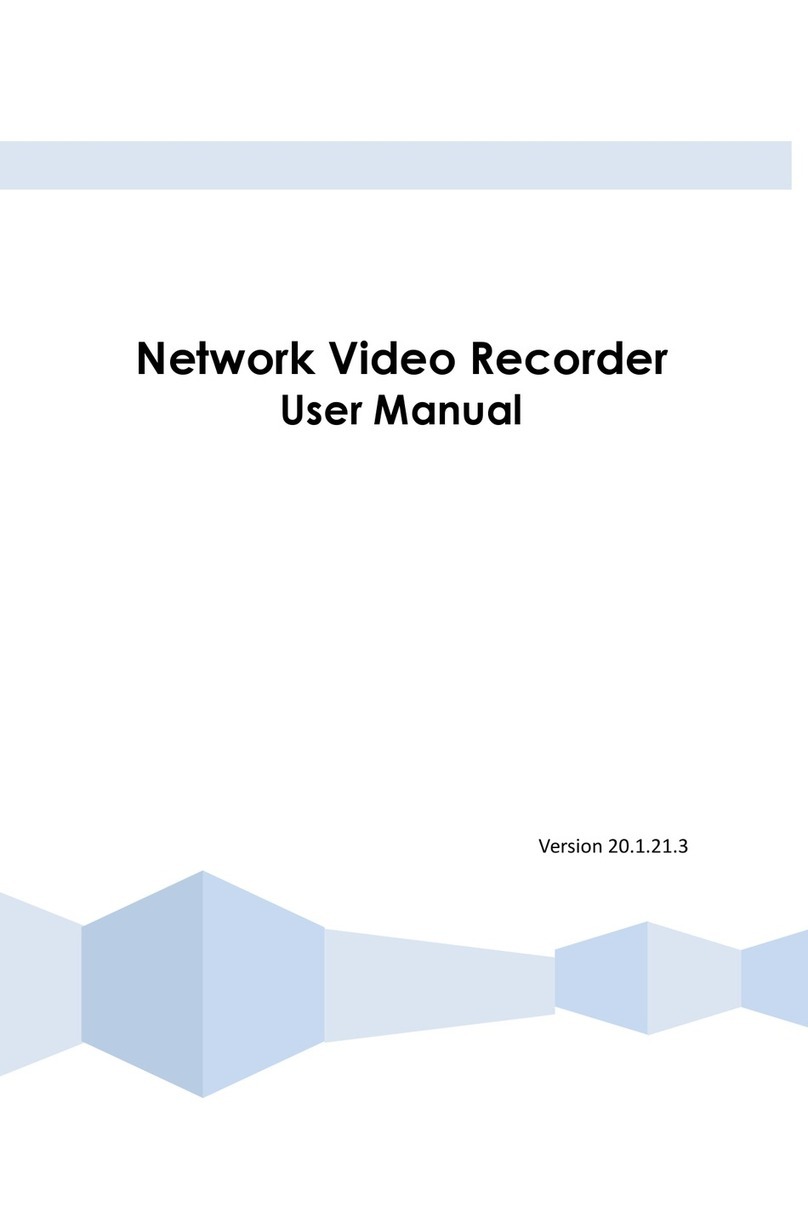
HeroSpeed
HeroSpeed NVR user manual
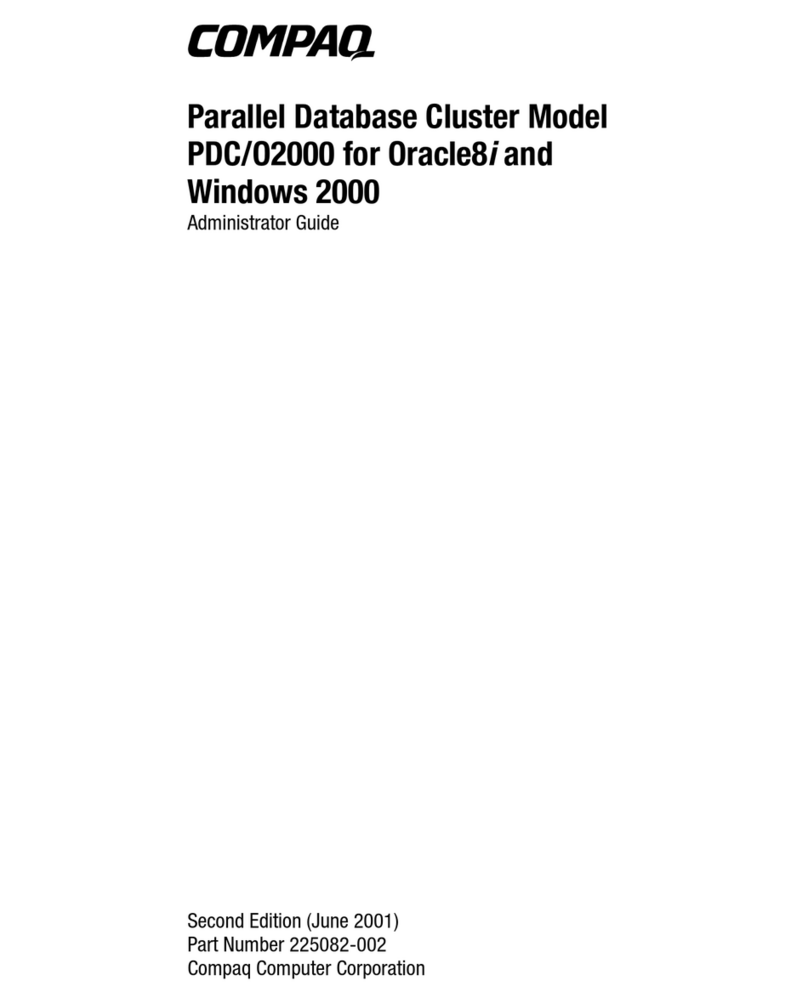
Compaq
Compaq 112726-001 - ProLiant - 6500 Administrator's guide
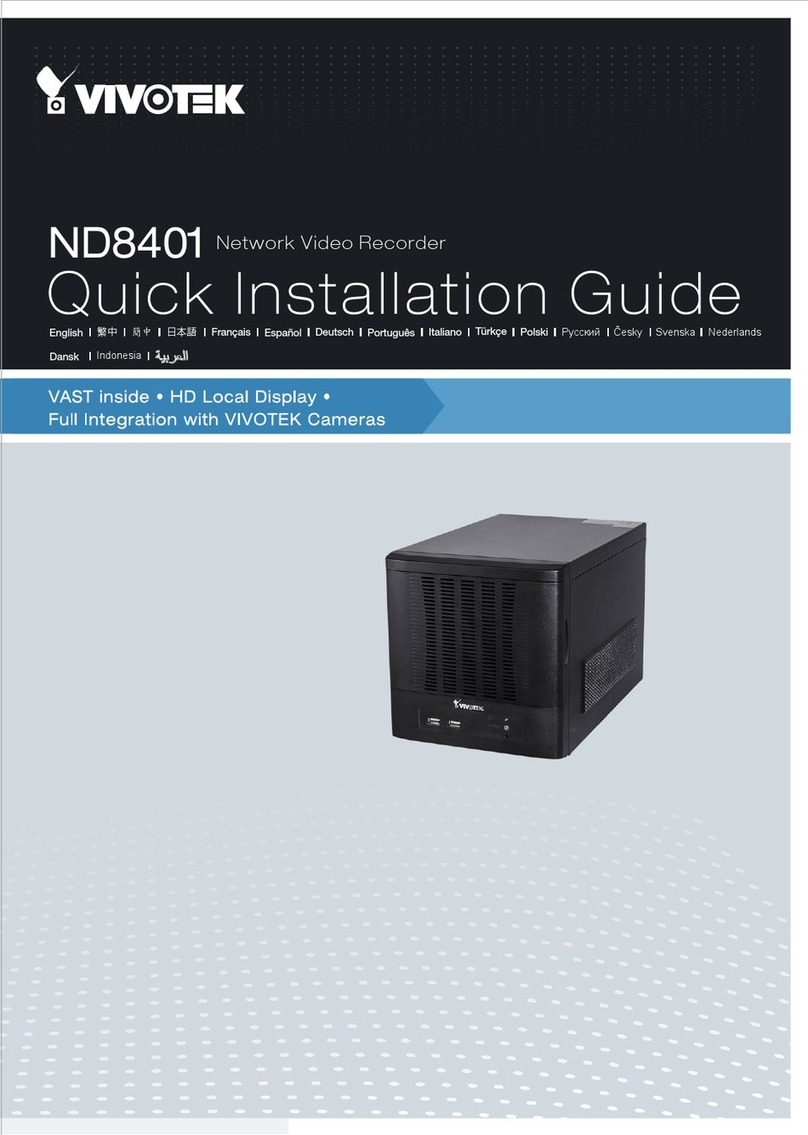
Vivotek
Vivotek ND8401 Quick installation guide
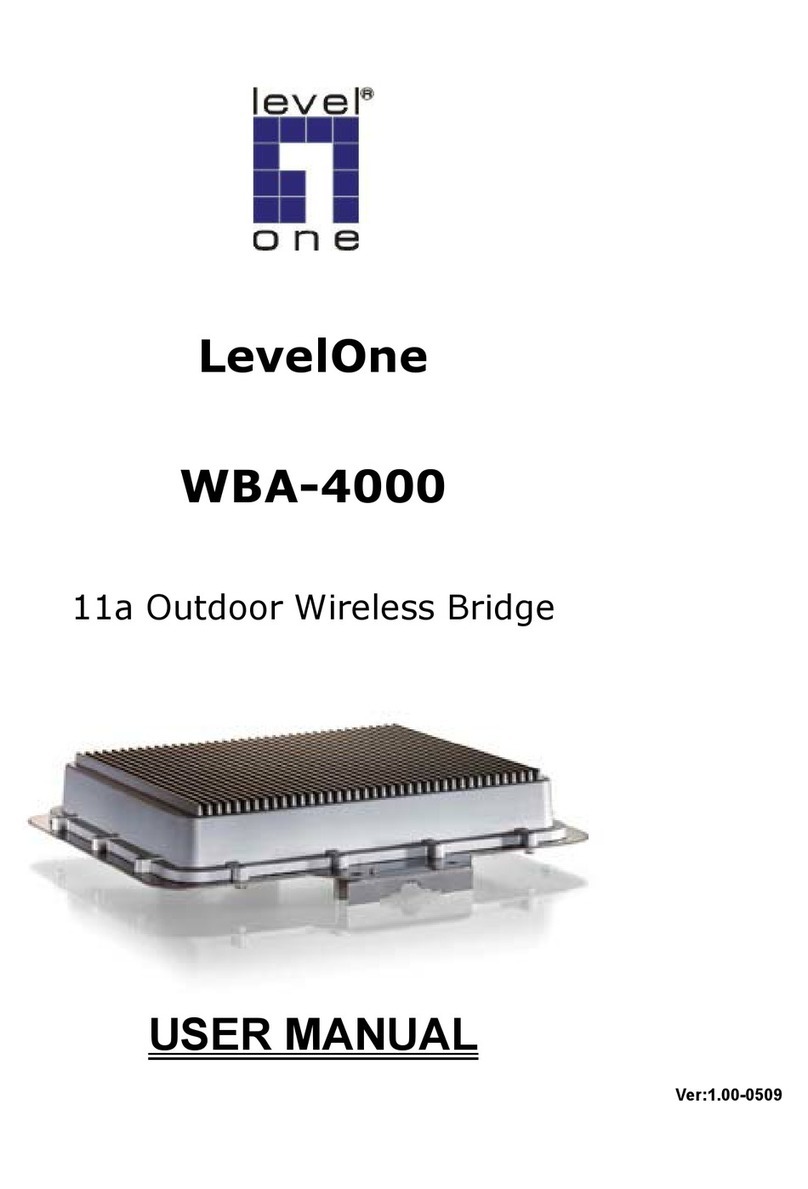
LevelOne
LevelOne WBA-4000 user manual
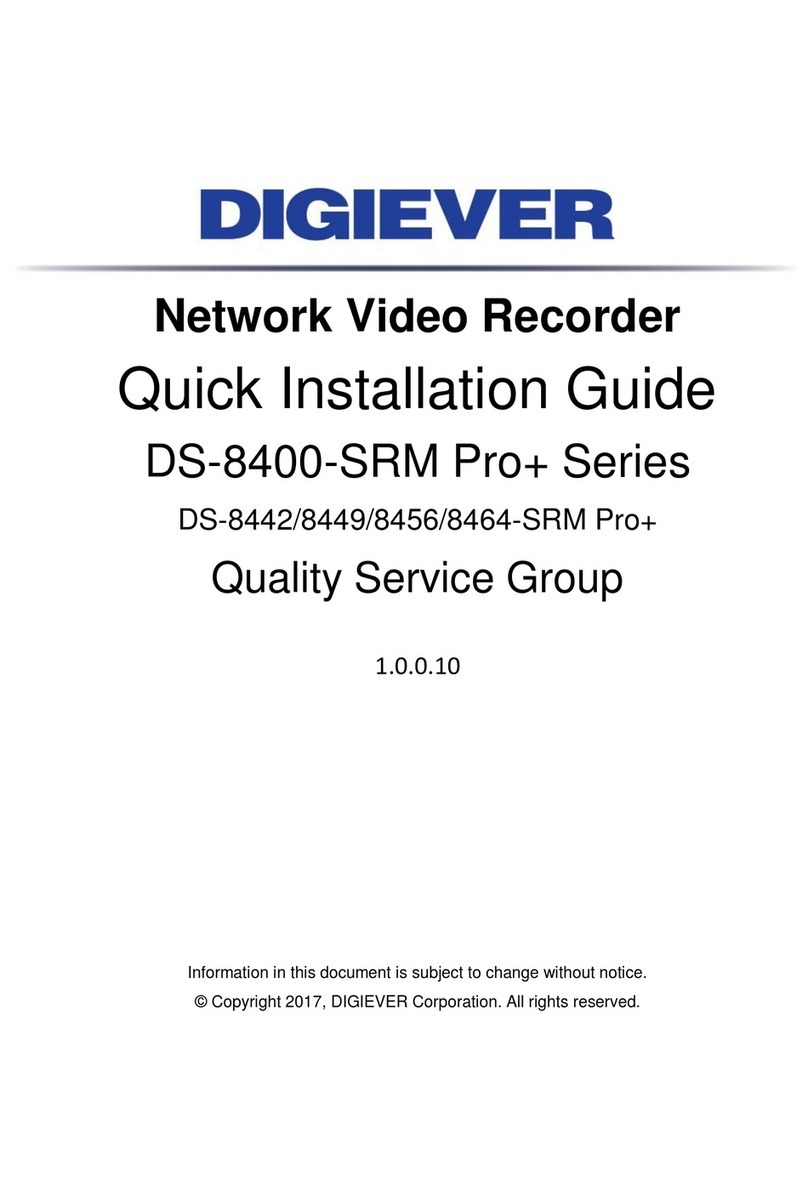
Digiever
Digiever DS-8400-SRM Pro+ Series Quick installation guide
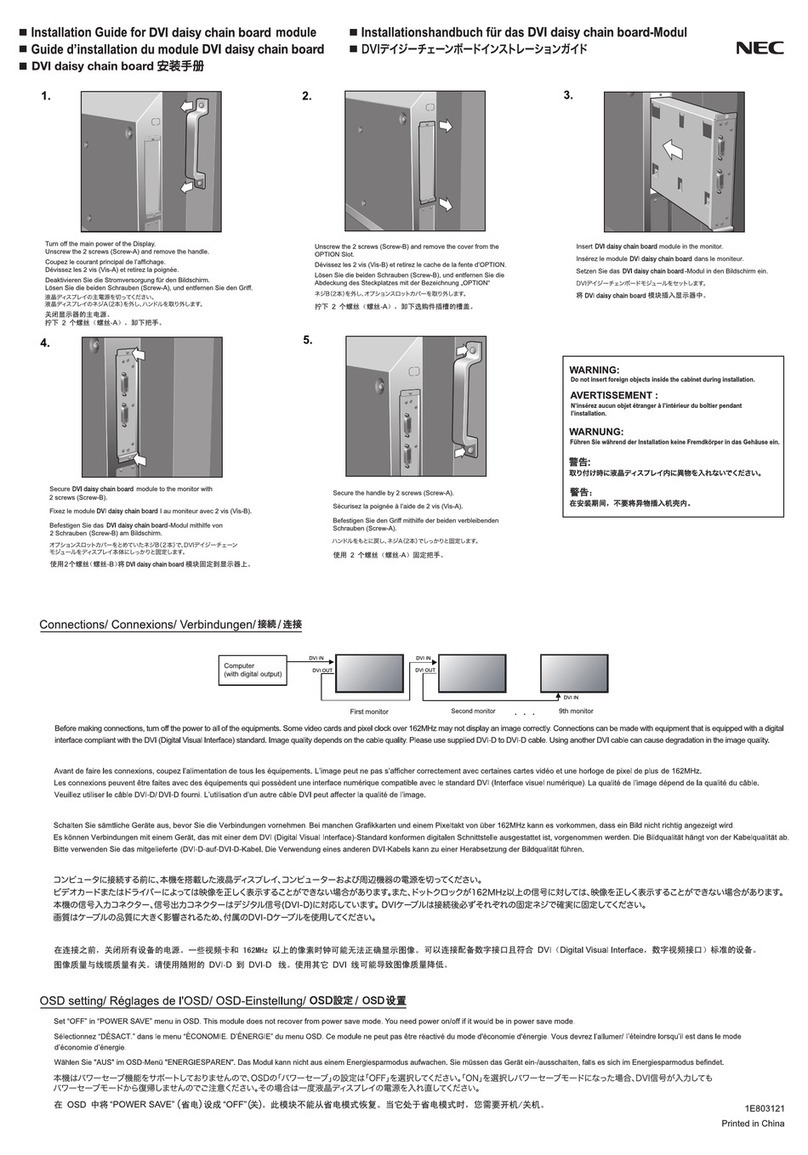
NEC
NEC P401-TMX4D user manual
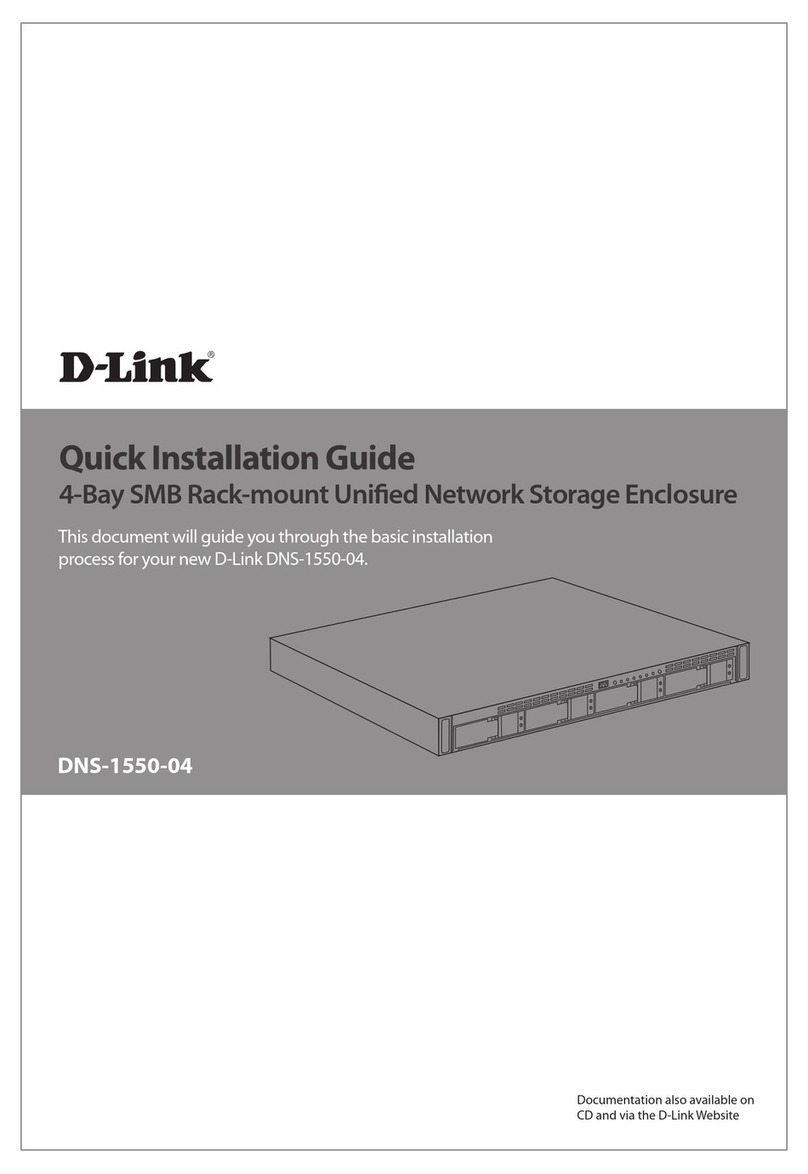
D-Link
D-Link ShareCenter Pro DNS-1550-04 Quick installation guide