TDW D2000 Manual

TDW Pub. No. 00-3795-0283
March 2002
TDW D
TDW DTDW D
TDW D-
--
-2000
20002000
2000 Closure
ClosureClosure
Closure
Installation, Operation and Maintenance Instructions
16 – 30 Inch

© Copyright 2002
All rights reserved
T. D. Williamson, Inc.
NOTICE
Any operation involving work on pipe containing liquids or
gases under pressure is potentially hazardous. It is
necessary, therefore, that correct procedures be followed in
the use of this equipment to maintain a safe working
environment.
No person should use this equipment who is not fully
trained in the procedures stated in this manual, and who is
not fully aware of the potential hazards connected with
work on pipe containing liquids or gases under pressure.
The purchaser of this equipment is responsible for the
manner in which this equipment is used and maintained and
for the training and competence of the operators.
Should any difficulty arise at any time in the use of this
equipment, please contact TDW immediately.
For Parts and Service:
P. O. Box 3409
Tulsa, OK 74101- 3409 USA
In the U.S. toll free 1-888-TDWmSon (839-6766)
Phone (918) 447-5100
Fax (918) 446-6327
Visit TDW's Web site at www.tdwilliamson.com
T. D. Williamson, Inc. is ISO 9001 and 9002 Certified
™ Trademark of T. D. Williamson, Inc. in the United States
and foreign countries.
® Registered trademark of T. D. Williamson, Inc., in the
United States and foreign countries.

i
Table of Contents
Section I: Introduction ............................................................................................................... 1
1.0 Purpose ............................................................................................................................................ 1
2.0 Discussion........................................................................................................................................ 1
3.0 Safety............................................................................................................................................... 1
Section II: Installation and Operation...................................................................................... 3
1.0 Installation....................................................................................................................................... 3
2.0 Operation......................................................................................................................................... 5
3.0 Removal and Installation of Closure Door ..................................................................................... 9
Section III: Maintenance.......................................................................................................... 11
1.0 Maintenance .................................................................................................................................. 11
Section IV: Parts List 1 D-2000 Closure, 16"–30"................................................................. 13

ii

1
TDW Pub No. 00-3795-0283
Revised March 2002
D-2000 Closure, 16"–30"
Instructions for Installation, Operation, and Maintenance
Section I: Introduction
1.0 Purpose
This manual provides instructions for the
installation, operation, and maintenance of the
TDW®D-2000 Clamp Ring Closure, 16"–30". This
closure is also available in other sizes.
2.0 Discussion
The TDW clamp ring closure is a quick-opening
closure easily operated by one person. It is
equipped with a pressure warning lock, in
accordance with UG-35 of ASME Sect. VIII, Div.
1, to alert the operator to the existence of internal
pressure prior to opening the closure.
The closure is designed primarily for horizontal
installation, meaning that the door swings open on
the horizontal axis. However, the closure can be
installed on a vertical installation. In the latter case,
a counterbalance, not addressed in this instruction,
can be provided to facilitate opening. Figure 1
shows the clamp ring closure, installed horizontally.
Figure 1. TDW® D-2000 Clamp Ring Closure
3.0 Safety
3.1 General
TDW clamp ring closures are designed for fast,
easy, and safe operation. A closure may not
operate effectively if it has been subjected to
misuse or external damage or has been operated or
maintained contrary to TDW's printed instructions.
It is mandatory that correct procedures be followed
in the care and use of TDW closures to maintain
their safety features, efficiency, and ease of
operation.
The following reminders are useful in ensuring that
your TDW clamp ring closures operate properly:
1. Clean the O-rings and O-ring sealing
surfaces and coat them with a thin film of
grease before the closure is closed.
2. Inspect the O-ring for cuts, scratches,
deterioration, twisting, or swelling.
Replace O-rings if there is any sign of
abnormality.
3. Clean the interior surfaces of the clamp
ring, and apply a thin film of lubricant
before the closure is closed. This is
particularly important in corrosive
environments.
4. Lubricate all hinge points at regular
intervals.
5. Make sure that the door, clamp ring, and
pressure warning lock are fully closed and
secured before attempting to pressurize the
vessel.
• Never allow pressure to be applied to
any TDW closure that may be
inoperative.

2
• Never try to open a TDW closure
while the vessel is under pressure.
• Never force the clamp ring operating
mechanism if the clamp ring does not
operate freely.
Although it may be necessary to force the door
open or closed, the clamp ring should always
operate freely. Do not force the clamp ring
operating mechanism or use a "cheater" pipe on the
handle of a lever-operated clamp ring. Damage to
components may result. Damaged components
could prevent the clamp ring from closing fully.
If excessive force has been used on the clamp ring
operating mechanism, the component attachment
welds should be visually inspected for damage
and/or examined by any common NDT method.
The closure door face must always be parallel to
and concentric with the face of the barrel collar. If
a TDW closure does not operate freely and easily
following routine maintenance and adjustment, and
the door face is not parallel to and concentric with
the barrel collar face, contact the TDW factory for
assistance and repair, as necessary.
Do not allow anyone to operate a TDW closure
who is not fully trained in the procedures contained
in the printed operating instructions, and who is
not fully aware of the potential hazards created by
liquids or gases under pressure.
Should any questions or difficulties arise at any
time in the use of TDW clamp ring closures, please
contact TDW immediately.
3.2 WARNINGS and CAUTIONS
The purpose of WARNINGS and CAUTIONS in
this manual is to call the operator's attention to
the possible danger of injury to personnel and
equipment. All warnings and cautions deserve
careful attention and understanding.
A. WARNING: Indicates a potentially
hazardous situation that, if not avoided, could
result in death or serious injury and damage
to equipment.
B. CAUTION: Indicates a potentially hazardous
situation that, if not avoided, could result in
minor to moderate injury and damage to
equipment. A CAUTION may also be used to
warn operators about unsafe practices.

3
Section II: Installation and Operation
1.0 Installation
1.1 General
A. To maintain the closure in proper working
order, those making the shop or field
installation must carefully follow the welding
instructions and preventive maintenance
instructions.
B. It is important to keep the following points in
mind during installation:
• Level the closure during the installation
process;
• Properly align the barrel collar;
• Position the door hinge in the vertical
position (horizontal on a vertical
installation) to permit easy opening and
closing of the door.
C. A bleeder valve and a pressure gauge must be
installed on the vessel the closure is welded
to. An operator must be able to bleed the
vessel and determine when there is zero (0)
psig within the vessel.
1.2 Welding Procedures
A. The same welding procedures are to be used
whether post-weld heat treatment is required
or not.
1. Remove closure door O-ring and pressure
warning lock O-ring before welding. (See
Figures 2 and 3.)
2. If post-weld heat treatment is required, it is
recommended that it be accomplished by
localized stress relieving. If that is not
possible, the closure door must be
removed prior to heat treatment. (See
Section II, subsection 3.1, beginning on
page 9, for removal instructions.)
Figure 2. Remove O-Ring on Closure Door
Figure 3. O-Ring on Pressure Warning Lock

4
B. Standard Barrel Collar—Materials:
• ASTM A694 F46
• Carbon maximum: 0.26%
• Manganese maximum: 1.40%
• Minimum tensile strength: 60,000 psi
• Minimum yield strength: 46,000 psi
1. TDW refers the welder to the applicable
codes such as ASME, API, ANSI, etc.
These codes require that the welder and
the weld procedure be previously
qualified.
2. These codes recommend the proper
preheat and post-weld heat treatment
procedures. The welder should refer to
these codes and follow the recommended
welding procedures for the materials being
welded.
NOTE:Standard barrel collar material and
properties shown above. Other materials
provided on request. Refer to material test
reports supplied with each closure to determine
weld procedure for actual materials being
welded.
NOTE:Any practical welding process (manual,
submerged arc, etc.) can be used. Applying as
low a heat range as possible is recommended,
to help prevent the barrel collar sealing surface
from warping.
C. The procedures for welding are as follows:
1. Position the barrel collar to align properly
with the vessel. Make sure the door hinge
is vertical (horizontal for a vertical
installation).
CAUTION: When welding to a vessel of high-
yield strength steel (over 71,000 psi),
preheating may be required to avoid
cracking. Refer to proper ASME, API, or
ANSI codes.
2. Tack weld approximately every four
inches around circumference and check
again for proper alignment.
CAUTION: When welding on the barrel collar, a
low welding heat range and the following
proper sequence of welds will help
prevent possible warping of the barrel
collar sealing surface.
3. Weld stringer bead and immediately start
the hot pass with two or more men on
opposite sides to equalize stress. Figure 4
shows the recommended welding
sequence.
Figure 4. Recommended Welding Pass Sequence
4. When the welding process is completed,
replace the O-rings on the closure door and
the pressure warning lock.
D. If post-weld heat treatment is required, a
localized heat treatment procedure should be
followed.
1. Coat the O-ring groove with a heat
resistant material (such as "TURCO PRE-
TREAT," or "WATER NO SCALE") for
protection during post-weld heat treatment.
2. Precautions such as interior braces should
be used during treatment so that the barrel
collar does not warp or droop.
3. After post-weld heat treatment, clean the
barrel collar and reinstall the O-ring. Open
and close the door to check for proper
actuation and alignment.
4. If a localized heat treatment procedure is
not possible, the door and clamp ring pivot
nut must be removed prior to heat
treatment. (See Subsection 3.1, beginning
on page 9for removal instructions.)
CAUTION: When cleaning the barrel collar, be
very careful not to damage the O-ring
sealing surfaces.
E. Before placing the closure in service, all
surfaces should be clean, with the O-ring and
O-ring sealing surfaces covered with a thin

5
film of grease. The closure door face should
be parallel with and concentric to the face of
the barrel collar. If these two faces become
misaligned, use the eight setscrews located in
the hinge's mounting bracket hubs to bring
the faces into correct alignment. Each hub has
four setscrews. See Figure 5, below.
Figure 5. Aligning Door and Barrel Collar
Face Using Setscrews
2.0 Operation
2.1 General
A. As shown in Figures 5 and 6, a warning plate
is attached to the front of the closure. This
warning concerns personal safety precautions
and must be observed to prevent injury to
personnel. Always keep this plate legible.
Figure 6. Warning Plate
B. The closure contains a pressure warning lock
to alert the operator to pressure in the vessel
before the closure is opened. The lock is
mounted on top of the barrel collar, as shown
in Figure 7. The pressure warning lock is
integral to the clamp ring and must be
removed before the clamp ring can be spread.
Figure 7. Pressure Warning Lock
C. Always clean the O-rings and O-ring surfaces
and coat them with a thin film of grease each
time the closure is open. Inspect for cuts,
scratches, or deterioration. Replace if there is
any sign of damage. See Figure 8.

6
Figure 8. Inspect and Lubricate O-Ring
WARNING: Replace damaged O-rings im-
mediately.
A damaged O-ring will cause
leakage of gases or fluids that
can lead to serious injury and
property damage.
D. Always clean the interior surfaces of the
clamp ring and apply a thin film of lubricant.
When opening, check lubrication of all hinge
points on the clamp ring assembly. These
include the following:
• One clamp ring pivot pin (Figure 9);
• Three clamp ring link pins (Figures 9 and
10); these pins should be lubricated at all
points along the pin, not just the front
(Figure 11).
The door-hinge bearings are oil impregnated,
sintered bronze and do not require lubrication but
should be checked at regular intervals for excessive
wear.
Figure 9. Grease the Clamp Ring Pivot Pin
Figure 10. Clamp Ring Hinge Points

7
Figure 11. Rear View of Three Clamp Ring Pins
2.2 Opening Procedures
WARNING: Do not open closure while vessel
is under pressure.
Bleed all pressure from vessel
before opening pressure warning
lock. Pressure gauge on vessel
must read zero (0) psig. If
product vents or sprays from
pressure warning lock, vessel is
still pressurized. When all
internal pressure is relieved,
open pressure warning lock and
open closure.
When opening pressure warning
lock, clamp ring, and door,
always stand on the side of the
closure that is opposite the door
hinge. Do not stand in front of
closure or on door hinge side of
closure (or above it in a vertical
installation) while opening.
Spraying line fluids or sudden
door opening may result in
personal injury or property
damage.
A. Isolate the vessel from line pressure, bleed
pressure to 0 psig, and drain.
B. Open the pressure warning lock by turning
the screw counterclockwise. See Figure 12.
Figure 12. Open Pressure Warning Lock
C. Once the pressure warning lock is completely
unthreaded, remove the screw and open the
clamp ring by lifting the clamp ring handle
(Figure 13). This will spread the two clamp
ring pieces so the closure door can be opened
(Figure 14).
Figure 13. Lift Clamp Ring Handle
to Spread Clamp Ring

8
Figure 14. With Clamp Ring Spread
Door Can Be Opened
NOTE:The pressure warning lock is not designed
or intended to be used as a pressure bleed-
down valve and should never be used as such.
2.3 Closing Procedures
A. Inspect, clean, and lubricate the O-ring,
O-ring grooves and sealing surfaces, and the
pressure warning lock. Replace the O-ring if
it is damaged.
WARNING: Replace damaged O-rings
immediately.
A damaged O-ring will cause
leakage of gases or fluids that
can lead to serious injury and
property damage.
B. Push the door firmly shut. Before the clamp
ring can be closed, the door must be
completely closed, showing no gap between
the door face and the hub face.
C. Close the clamp ring by pulling the clamp
ring handle over the top of the closure. Lower
it fully so that the pressure warning lock
screw can be inserted through the aligned
holes in the bars and threaded into its
bushing. The clamp ring does not use any
wedging action during closing since the
clamping surfaces are parallel to the door and
the hub faces. Do not force the clamp ring
handle if the clamp ring will not close freely.
Verify that the door is adjusted properly and
check for debris.
NOTE:As the clamp ring is closed, the bars
attached to the back of the clamp ring move
closer together (Figure 15). When the clamp
ring is fully closed, the holes in the bars are in
alignment. If the holes do not overlap, you will
not be able to thread the pressure warning lock
screw into the bushing. If the clamp ring
appears to be closed and the holes still do not
line up, re-open the clamp ring and check for
damage and debris.
Figure 15. Holes in Bars Don't Overlap When Clamp
Ring Handle Is Not in Closed Position
D. Install the pressure warning lock screw. Make
sure it is not cross-threaded into the bushing.
Tighten hand tight, and then add about one-
eighth of a turn with a small wrench. Do not
over tighten.
Figure 16. Pressure Warning Lock in Place
WARNING: Never attempt to pressurize
vessel until you have made sure
that door, clamp ring, and
pressure warning lock are fully
closed and secured.
A line spraying fluids or a door
opening suddenly can result in
personal injury or property
damage or both.
E. The vessel can now be pressurized to line
pressure and placed on-stream.

9
3.0 Removal and Installation of
Closure Door
3.1 Removal
A. Unthread the pressure warning lock and the
O-ring.
B. Open the closure door and remove the O-ring
carefully to prevent damage.
C. Close the door and push the clamp ring
handle all the way down to lock the door in
place.
D. Attach a hoist to the lifting eye.
CAUTION: All major components of the D-2000
closure are extremely heavy. Make sure
the hoist used has an adequate lifting
capability to avoid possible injury to
personnel.
E. Remove the eight door hinge cap plugs.
F. Remove the eight door hinge setscrews.
G. Remove the two split clamp collars.
H. Remove the upper bearing assembly.
I. Lift up on the clamp ring handle and spread
the clamp ring.
J. Open the door clear of the clamp ring
assembly.
K. Lift the door until the lower hinge pin clears
the lower hinge bracket. Pull the lower hinge
pin away from the bracket and remove the
lower bearing assembly.
L. Lower the door until the upper hinge pin is
clear of the upper hinge bracket.
M. Set the door aside.
O. If disassembly is for post-weld heat
treatment, other than a localized procedure,
restrain the clamp ring by temporarily
replacing the nylon insert clamp ring pivot
nut with something that will not melt.
Caution: Clamp ring could slip off pin during
handling if not adequately restrained.
Note: The clamp ring is not designed for removal
in the field. If removal of the clamp ring is
required, contact TDW for assistance.
3.2 Installation
A. To reinstall the closure door, follow the
reverse of the removal instructions.
B. Adjust the hinge setscrews to align door with
the barrel collar.


11
Section III: Maintenance
1.0 Maintenance
1.1 General
Maintenance is required on TDW closures. Most is
preventive maintenance and can be performed each
time the closure is opened.
1.2 O-Ring/O-Ring Surfaces
There are two O-rings on the D-2000, 16"–30"
closure. One is on the pressure warning lock screw,
and another is on the barrel collar, making a seal
when the door is closed. Always clean and coat
these with a thin film of grease each time the
closure is open. Inspect for cuts and scratches or
deterioration. Replace O-rings if there is any sign
of damage.
Figure 17. Lube O-Ring on Pressure
Warning Lock Screw
Figure 18. Additional Lube Points
1.3 Clamp Ring
Always clean the interior surfaces of the clamp
ring and apply a thin film of lubricant. At regular
intervals:
A. Lubricate all hinge points on clamp ring
assembly. The door hinge bearings are oil
impregnated, sintered bronze and do not
require lubrication but should be checked at
regular intervals for excessive wear.
B. Keep all exterior surfaces painted to prevent
rust.
1.4 Pressure Warning Lock
A. Make sure threads are clean and free of nicks.
B. Inspect the O-ring and bushing.

12
C. Keep the assembly free of paint.
D. Lube inside the bushing periodically.
Figure 19. Lube Bushing for Pressure Warning Lock

13
Section IV: Parts List 1
D-2000 Closure, 16"–30"
Item Qty. Description
1 1 barrel collar
2 1 door
3 1 clamp ring
4 1 clamp ring handle
5 1 door hinge arm
6 1 clamp pivot plate
8 2 shaft collar
9 2 flat plain washer
10 2 handle link
11 3 grease fitting
12 2 bearing assembly
13 2 Clevis pin
14 2 spacer
15 1 O-ring
16 1 nameplate
17 1 pressure warning plate
18 1 pressure warning plate
19 2 clamp ring locking lug
20 1 Spirol™ pin
21 2 flat washer
22 2 cotter pin
23 8 setscrew
24 8 cap plug
25 2 flat bar
27 1 handle
28 2 rubber seal
29 2 drive screw
31 1 chain assembly
34 1 clamp ring pivot pin
36 1 flat washer
37 1 Esna™ nut
38 1 pressure warning lock screw
39 1 warning pad
40 1 Buna-N O-ring
41 1 bushing
42 12 drive screw
43 1 instructions (not shown)
44 1 caplug
NOTE:Item numbers correspond with TDW Assembly Drawing 19-3716-0600-SUF and the numbering on
page 14.

14
Figure 20. D-2000 Clamp Ring Closure, 16"–30"

Product Warranty
1. Products manufactured by T. D. Williamson, Inc., are warranted free from defects in material and
workmanship for a period of three (3) years from the date of shipment from the factory.
Elastomer products are warranted for one (1) year under proper storage to be free from
defects in material and workmanship. The foregoing warranty does not apply to any items
not manufactured by T.D. Williamson, including but not limited, to, electronic devices,
switch components, pumps, O-rings, purchase cylinders, etc. These third party parts will
revert back to suppliers warranty. TDW assumes no liability under this or any other
warranty for components not manufactured by TDW. This Warranty applies only to
products shipped after June 30, 2000.
2. If TDW accepts any claim made under this Warranty, TDW’s liability, if any, shall be limited to,
at TDW’s sole option, repair or replacement of the failed part or product, or a refund of the
purchase price, less an allowance for services rendered for the product prior to the Warranty claim.
TDW disclaims any and all responsibility for special, consequential or incidental damages
arising out of or related to the sale, use, or inability to use any products covered by this
Warranty.
3. Buyer agrees not to return goods for any reason except with the prior written consent of TDW,
which consent, if given, shall specify the terms, conditions and charges upon which any returns
may be made. Materials returned to TDW for Warranty work must have a Return Material
Authorization (RMA) number, and such number must be noted on the package at the time of
shipment. Claims under this Warranty must be made in writing within ten (10) days of any failure
and sent by registered mail to: P. O. Box 3409, Tulsa, Oklahoma 74101. Any failed products or
parts must be held for inspection by TDW or, at TDW’s option, returned to TDW’s factory.
Customer shall prepay shipping charges, and shall pay all duties and taxes, as applicable, for
products or parts returned to TDW for warranty service.
4. This Warranty shall not apply to any product or component which has been repaired or altered by
anyone other than TDW, or has become damaged due to misuse, negligence or casualty, or has
been operated or maintained contrary to TDW’s printed instructions and warnings.
5. The sole purpose of the exclusive remedy contained in the limited Warranty shall be to provide
repair or replacement of failed products, or to refund the purchase price of the failed product as
explained above in paragraph 2. This exclusive remedy shall not be deemed to have failed of its
essential purpose so long as TDW agrees to repair or replace the failed product or to refund the
purchase price as explained above.
6. All rights, duties, and obligations arising under this limited Warranty shall be governed by the laws
of the State of Oklahoma, U.S.A., regardless of conflict of laws provisions. In the event Buyer
initiates litigation under this Warranty, Buyer hereby agrees that jurisdiction for such litigation
shall be brought only in the District Court for the County of Tulsa, Oklahoma.
7. TDW reserves the right to make any changes in or improvements on its products without incurring
any liability or obligation to update or change previously sold product and/or the accessories
thereto.
8. This warranty is in lieu of all other warranties express or implied, including the warranties
of merchantability and fitness for particular purpose, which are expressly disclaimed. TDW
neither assumes nor authorizes any other person to modify these terms and conditions,
warrant specific applications, or assume for TDW any other liability in connection with the
sale of any TDW product other than as provided in this warranty.
Rev. 06-30-00

T.D. Williamson, Inc. is ISO 9001 certified.
TDW Pub. 00-3795-0283 March 2002 Copyright 2002
Printed in USA All rights reserved
Visit TDW's home page on the World Wide Web at www.tdwilliamson.com T. D. Williamson, Inc.
Other manuals for D2000
1
Table of contents
Popular Enclosure manuals by other brands

Palazzoli
Palazzoli ALUPRES-EX Series Instructions for safety, use and maintenance
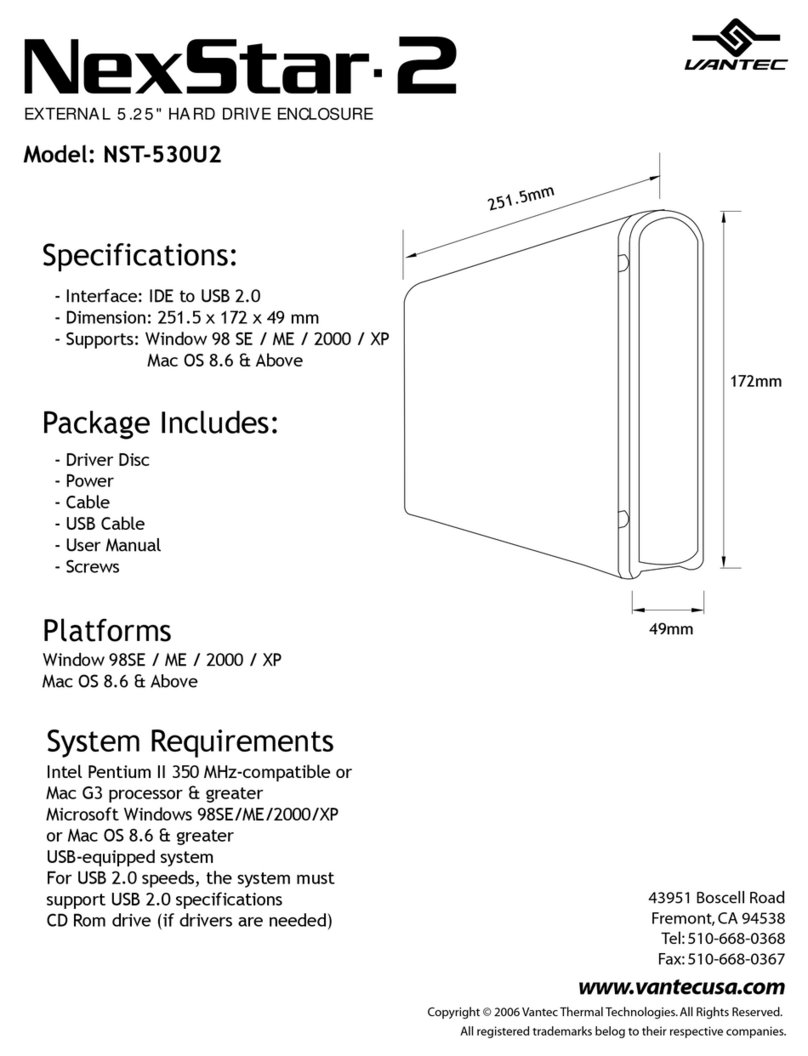
Vantec
Vantec NEXSTAR.2 NST-530U2 Specifications
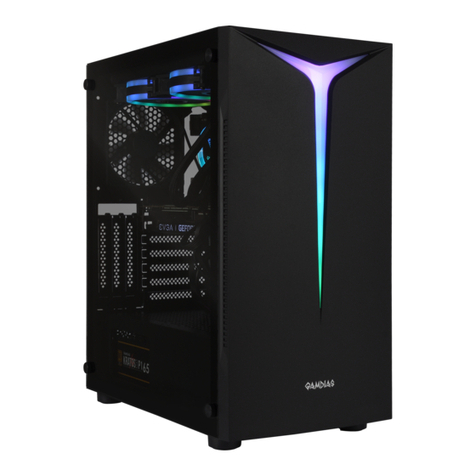
GAMDIAS
GAMDIAS ARGUS E2 ELITE Quick installation guide
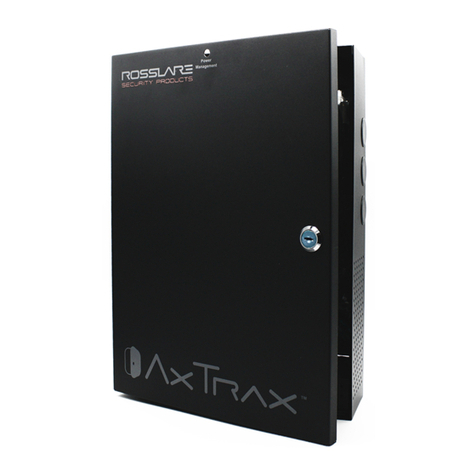
Rosslare
Rosslare ME-1015 installation manual
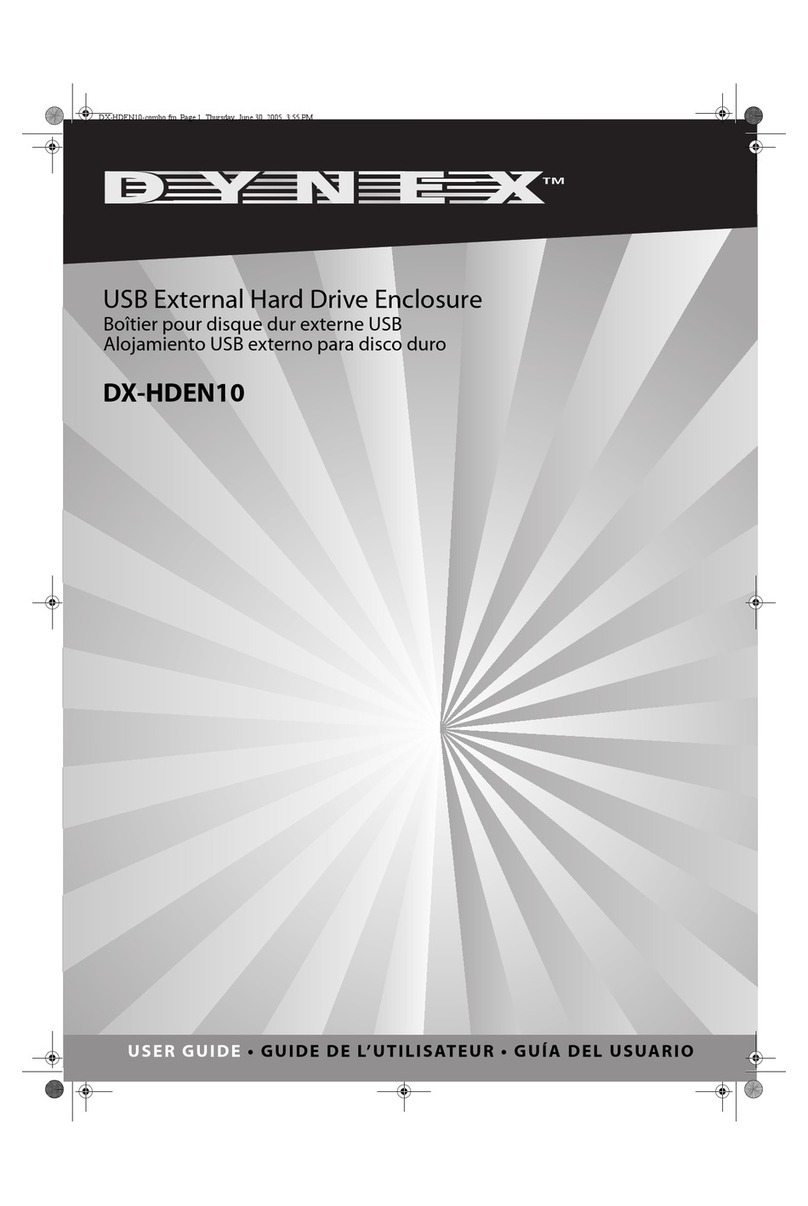
Dynex
Dynex DX-HDEN10 user guide

Metra Electronics
Metra Electronics Saddle Tramp BC-DSPX-HD1 installation instructions