Techna-Tool BK MIKRO 50-LIN.B User manual

OI:BK MIKRO LIN.B
Rev. 1.01 dated 24.1.2006 -I-
BK MIKRO 50/100-LIN.B
Tool monitoring system for linear scanning
Scanners with maximum stroke of 50 mm or 100 mm
Operating Instructions
Issue 1.01
Released: Jan, 2001
553 Industrial Dr. Hartland, WI 53029 262-367-8665 fax 262-367-0208
web-site www.techna-tool.com email techtool@techna-tool.com

OI: BK MIKRO LIN.B
-II -Rev. 1.01 dated 24.1.2006
General Notice
Safety guidelines
These operating instructions contain notices, which you should observe to ensure your own
personal safety, as well as to protect the product and connected equipment. These notices are
highlighted in the manual by a warning triangle and are marked as follows according to the level of
danger:
Immediate danger
to life and limb of personnel and others.
Non-compliance may cause death or
serious (crippling) injury.
Hazardous situation
to life and limb of personnel and others.
Non-compliance may cause death or
serious injury.
Potentially hazardous situation
Non-compliance may cause slight injury;
possible damage to property.
Notes on correct handling
Non-compliance may cause damage to the product
and/or damage to parts/items in the vicinity.
Environmental protection
Non-compliance may have an impact on the environment.
Intended use
Danger
!
!
Warning
!
Caution
i

OI:BK MIKRO LIN.B General Notice
Rev. 1.01 dated 24.1.2006 -III -
BK MIKRO is a control system suitable for tool as well as for object
and free space monitoring applications. It may only be used for the applications
described in the technical documents, and only in connection with devices or
components from other manufacturers which have been approved or
recommended by us.
This product can only function correctly and safely if it is transported, stored,
set up, and installed correctly, and operated and maintained as recommended.
!
Warning

General Notice OI: BK MIKRO LIN.B
-IV -Rev. 1.01 dated 24.1.2006
Qualification of personnel
Only qualified personnel may carry out the following activities on the control system:
installation, commissioning, operation, and maintenance.
Qualified persons in accordance with the safety guidelines are defined as persons who are
authorized to commission, to ground, and to tag circuits, equipment, and systems in accordance
with established safety practices and standards.
Disclaimer of liability
We have checked the contents of this document for agreement with the hardware and software
described. Since deviations cannot be precluded entirely, we cannot guarantee full agreement.
However, the data in this manual are reviewed regularly and any necessary corrections included in
subsequent editions. Suggestions for improvement are welcomed.
EEC directive EMC 89/336/EEC
The following applies to control system BK MIKRO:
Products which carry the CE symbol meet the requirements of the EEC directive
89/336/EEC on electromagnetic compatibility.
The EEC declarations of conformity and the related documentation will be maintained at the
following address for inspection by the responsible officials in accordance with article 10(1) of the
above stated EEC directive:
Leukhardt Systemelektronik GmbH
Rudolf-Diesel-Straße 17
D-78532 Tuttlingen
Areas of use
Control systems of the BK MIKRO series meet the applicable, harmonized, European standards for
the respective area of applications.
Fitting conditions
The fitting conditions and safety notes in the operating instructions must be adhered to when
commissioning and operating the devices.
Copyright
These operating instructions are intended for the operator and the operator’s personnel only. This
document and its contents may not be disclosed to third parties, either in full or in part, by
reproduction, transmission or any other means without express written authority.
Non-compliance may lead to prosecution under criminal law.

OI:BK MIKRO LIN.B Contents
Rev. 1.01 dated 24.1.2006 Page 1
Contents
1Characteristics.....................................................................................................................3
2System Components............................................................................................................4
2.1 Control unit...........................................................................................................................4
2.1.1 Technical data ......................................................................................................................6
Mechanical dimensions..........................................................................................................7
2.1.2 Connection terminals.............................................................................................................7
Power supply.........................................................................................................................7
Control inputs........................................................................................................................8
Selection inputs....................................................................................................................8
Relay outputs........................................................................................................................9
2.1.3 Light-emitting diodes..............................................................................................................9
2.1.4 Rotary switches...................................................................................................................10
2.1.5 Toggle switches ..................................................................................................................10
"Scanning intensity" switch...................................................................................................11
"Output relay" switch............................................................................................................11
"Scanner" switch.................................................................................................................11
"Tolerance range" switch(es)................................................................................................11
"O.K. indication" switch........................................................................................................11
2.1.6 Notes on technical safety.....................................................................................................12
2.2 Scanner..............................................................................................................................13
2.2.1 Technical data ....................................................................................................................13
Mechanical dimensions........................................................................................................14
TK50-LIN.B = "50 mm max. stroke" .................................................................................14
TK100-LIN.B = "100 mm max. stroke"...............................................................................14
2.2.2 Accessories........................................................................................................................15
2.2.3 Scanning Wand...................................................................................................................15
Stop position.......................................................................................................................15
Initial position......................................................................................................................15
Scanning range...................................................................................................................15
Exchange the scanning tip...................................................................................................15
2.3 Connection cable ................................................................................................................16
3Mode of Operation.............................................................................................................17
3.1 Scanning process................................................................................................................17
3.2 Reference procedure when system is switched on..................................................................17
3.3 Output of results .................................................................................................................18
3.4 Return travel monitoring.......................................................................................................18
4Monitoring Functions........................................................................................................19
4.1 Teach mode = Monitoring with learn function..........................................................................19
4.1.1 "Teach-in", the learn cycle....................................................................................................19
4.1.2 "Start", the real scanning process.........................................................................................20
4.1.3 Multi Learn..........................................................................................................................20
4.2 Switch mode = Monitoring with setting the scanning range.......................................................21
4.2.1 Control operation "Object monitoring"....................................................................................21
4.2.2 Control operation "Free space monitoring" .............................................................................21
4.2.3 Setting the position..............................................................................................................22
4.2.4 Example for range settings...................................................................................................22
5Cycle Times.......................................................................................................................23
Scanning times...................................................................................................................23

Table of Figures OI: BK MIKRO LIN.B
Page 2Rev. 1.01 dated 24.1.2006
6Status Indication................................................................................................................24
6.1 Yellow LED.........................................................................................................................24
6.2 Red LED / Green LED.........................................................................................................24
6.3 Error messages –Flashing red and green LED......................................................................24
7Installation Notes...............................................................................................................25
7.1 Control voltage connection ...................................................................................................25
7.2 Mounting brackets..............................................................................................................26
7.3 Interference prevention ........................................................................................................28
Appendix A
Techna-Tool & Manufacturing Part Numbers....................................................................................28
Table of Figures
Fig. 2-1: Control unit –Front view with plug-in connections ................................................................4
Fig. 2-2: Control unit –"Multi" and "Single" ......................................................................................5
Fig. 2-3: Control unit –Dimensions .................................................................................................7
Fig. 2-4: Control unit –Light-emitting diodes ....................................................................................9
Fig. 2-5: Control unit –Rotary switches..........................................................................................10
Fig. 2-6: Control unit –Toggle switches.........................................................................................10
Fig. 2-7: Range of tolerance.........................................................................................................11
Fig. 2-8: Scanner TK50-LIN.B.......................................................................................................14
Fig. 2-9: Scanner TK100-LIN.B.....................................................................................................14
Fig. 2-10: Scanners –Accessories.................................................................................................15
Fig. 2-11: Stop position of the wand ................................................................................................15
Fig. 2-12: Connection cable –Pin configuration ...............................................................................16
Fig. 4-1: "Teach-in", the learn cycle...............................................................................................19
Fig. 4-2: "Start" cycle using "Teach mode" ....................................................................................20
Fig. 4-3: "Start" cycle using "Switch mode"....................................................................................21
Fig. 4-4: Range setting using rotary switches .................................................................................22
Fig. 7-1: Control voltage connection..............................................................................................25
Fig. 7-2: Mounting bracket [ø 32 mm] ...........................................................................................26
Fig. 7-3: Mounting bracket [ø 20 mm] ...........................................................................................27
© Copyright Techna-Tool Inc..
Subject to change without notice.

OI:BK MIKRO LIN.B
Rev. 1.01 dated 24.1.2006 Page 3
1Characteristics
BK MIKRO LIN.B is a tool monitoring system
customized for longitudinal scanning applications.
The complete BK MIKRO LIN.B system comprises
•a control unit,
•a sensor (scanner),
•a connection cable.
BK MIKRO LIN.B is based on existing design concepts for tool, object and free space monitoring.
These system monitors geometries, which require longitudinal scanning, especially in cases where
rotary scanning is inappropriate or impossible, for example cavities, bore holes, limited space
arrangements or critical coolant pressure.
The two control units "Multi" and "Single" have different features of monitoring:
•Tool monitoring
Monitoring of the scanning position whose precise location has been previously entered by
"Teach-in", e.g. to carry out a tool check before each working cycle (tool monitoring), especially
for "Multi": 8 scanning positions can be coded.
•Object monitoring, free space monitoring
Monitoring a scanning range freely selectable via two adjusting switches, e.g. to check cavities
with varying depth (object monitoring), or to check bore holes (free space monitoring), only for
"Multi".
Two types of scanners are available for each control unit.
TK50-LIN.B : Scanner with maximum stroke of 50 mm.
TK100-LIN.B : Scanner with maximum stroke of 100 mm.
Principle of operation
The wand of the scanner scans tools, objects or critical process spaces free of potential,
in line with machine cycles.
A control unit equipped with a micro-computer triggers the movement of the wand upon an external
signal and passes the scanning result on to the machine control via relay contacts.
The galvanically isolated inputs and outputs guarantee a high degree of operational safety and
protection against interferences.
Further features
•Variants for the tip of the wand (also project-specific)
•Two steps for scanning intensity
•Output relay contacts selectable as N.C. or N.O.
•Various ranges of tolerance for "O.K." message
•Indication of the scanning result by two LEDs for "O.K." and "K.O." at the control unit
•Detection of cable breaks

BA: LS-IC/BK MIKRO LIN.B
Page 4Rev. 1.01 dated 24.1.2006
2System Components
2.1 Control unit
The control unit is available in three models preconfigured for different supply voltages.
The relevant version will be marked on the rating plate: 24 VDC, 120 VAC, 230 VAC.
On its front panel, the control unit is fitted with plug-in screw terminals to connect all machine
inputs and outputs, supply voltage, and the scanner.
•The screw terminals have been arranged on two plug-in terminal blocks. These blocks
are keyed so that they cannot be accidentally plugged into the wrong socket.
•When in operation, plastic caps cover the screws in the front. Wires to be connected are routed
from the top or bottom of the unit.
The scanner will be connected via a 6-wire cable to the scanner socket of the control unit.
Fig. 2-1:Control unit –Front view with plug-in connections
Note:
These plugs may only be inserted or removed
when the power supply has been disconnected.
!
Caution
Scanner o.k.
L1 N
AC IN
+–
24 V DC
Com Start S1 S2 S3Teach
25%
0%
50%
75%
P1 BK MIKRO
LIN
k.o.
25%
0%
50%
P2
1
2
Homeok: Obj. 50
100
Terminal block with connected wires
removed from housing
Key-bitKey-bit
Scanner socket
Screws of the terminal block
coverd by plastic cap
Connected wires

OI:BK MIKRO LIN.B
Rev. 1.01 dated 24.1.2006 Page 5
"Multi" "Single"
Designation: BK MIKRO LIN.B Multi Designation: BK MIKRO LIN.B Single
Fig. 2-2:Control unit –"Multi" and "Single"
Please note: New BK Linear Controllers are the same for Multi and Single
Important: When applying power to S1, S2, and S3 the 24 volts must be delayed(50 ms)until the controller is
fully powered up and done performing its internal operations.
Features(due to the different control units) "Multi" "Single"
Number of toggle switches 64
2 steps for scanning intensity xX
Relay as N.C. or N.O. contact xX
Scanner TK50-LIN.B or TK100-LIN.B xX
Ranges of tolerance for "O.K." (referred to the learned position) 42
"O.K." message at "Object" x–
Rotary switches P1, P2 x–
Selection inputs S1, S2, S3 x–
Monitoringof a learned position: Teach mode xX
Tool monitoring / Object monitoring P1=0, P2=0 Standard
Number of learned positions, which can be stored. 81
Monitoring of a preset range: Switch mode P1 ≥0, P2 >0 –
Object monitoring: "O.K.", if an object is detected. S1=0 –
Free space monitoring: "O.K.", if no object is detected. S1=1 –
10050
Scanner
o.k.
L1 N
AC IN
+–
24 V DC
Com Start Lern
BK MIKRO LINEAR
k.o.
Control inputs
Power supply and
Control voltage
24 VDC
These terminals must not be connected !
"O.K."
relay
"K.O."
relay
Power
supply
230 VAC
or
120 VAC
Scanner connection
These terminals must not
be connected !
Scanner o.k.
L1 N
AC IN
+–
24 V DC
Com Start S1 S2 S3Teach
25%
0%
50%
75%
P1 BK MIKRO
LIN
k.o.
25%
0%
50%
P2
1
2
Homeok: Obj. 50100
Scanner connection
Control inputs
Power supply and
Control voltage
24 VDC Selection inputs
These terminals must not be connected !
"O.K."
relay
"K.O."
relay
Power
supply
230 VAC
or
120 VAC

BA: LS-IC/BK MIKRO LIN.B
Page 6Rev. 1.01 dated 24.1.2006
2.1.1 Technical data
Housing Insulating material housing, protection class II, built-in unit
Protection type IP 20
Dimensions (W x H x D) 45 mm x 75 mm x 107.5 mm
Case mountings Sectional rail, 35 mm, to DIN EN 50022
Power supply voltage
(depending on model) 24 VDC ±20% PELV1) Imax = 0.25 A
120 VAC Imax = 0.05 A
230 VAC Imax = 0.025 A
Power consumption 6 VA max.
Control voltage (int./ext.) 24 VDC ±20% PELV1)
Inputs Galvanically isolated
–Input current 5 mA approx.
–Pulse duration 6 ms min.
Switched outputs 2 x 250 VAC / 30 VDC, 2 A max.
Making/breaking capacity 500 VA / 60 W (max.)
10 mA min. at 10 V
Operational life of relay 5 x 107switching cycles
ConnectionsPlug-in screw terminals for connecting
–power supply
–control inputs
–selection inputs (only for "Multi")
–relay outputs
Scanner socket to DIN 45322, 6 pin
Climatological conditions Classification 3K3 under EN 50178
Ambient temperature 0 ºC to +50 ºC
Storage temperature –25 ºC to +80 ºC
Note:
The control unit of BK MIKRO LIN.B is a built-in unit!
1) PELV = Protected Extra Low Voltage
The voltage applied must meet the requirements for an extra low function
potential with safe disconnection (PELV).
!
Warning

OI:BK MIKRO LIN.B
Rev. 1.01 dated 24.1.2006 Page 7
Mechanical dimensions
Fig. 2-3:Control unit –Dimensions
2.1.2 Connection terminals
Power supply
"24 VDC" model:
+Supply voltage input 24 VDC
–Reference potential of 24 VDC supply voltage
"120 VAC" and "230 VAC" models 2):
L1 Supply voltage input,
depending on model: 120 VAC or 230 VAC
NSupply voltage input,
depending on model: 120 VAC or 230 VAC
+Control voltage for "Start", "Teach" and S1,
S2, S3 controlling inputs: 24
VDC unregulated output current 0.1 A max.
If an ext. control voltage is applied, this terminal is not connected.
–When using the internal control voltage, this terminal must be
connected to the "Com" control inputs terminal.
If an ext. control voltage is applied, this terminal is not connected.
See section "Control voltage connection" in chapter "Installation Notes".
Note:
2) Alternatively, "120 VAC" and "230 VAC" models may also be supplied with 24
VDC.
In this case, "L1" and "N" terminals must not be connected.
"+24 VDC" and "–24 VDC" terminals are to be connected as described above
for "24 VDC" model.
i
107.5
110
75
78
45
General tolerances
ISO 2768 – mK
+–
24 V DC
L1 N
AC IN
+–
24 V DC

BA: LS-IC/BK MIKRO LIN.B
Page 8Rev. 1.01 dated 24.1.2006
Control inputs
Com Reference potential for control inputs and selection inputs
"Multi"
Start
An input level of +24 VDC relative to "Com" terminal will trigger a "Start"
cycle (the real scanning process).
"Single"
Teach An input level of +24 VDC relative to "Com" terminal will trigger a learn
cycle (the "Teach-in").
Note: This terminal is marked "Lern" at the "Single" unit.
In the following it will be designated also "Teach".
Selection inputs
Only for "Multi”!
S1
S2
S3
The input signal (static) of +24 VDC relative to "Com" terminal must be
stable during 50 ms min. before "Teach" or "Start".
•using "Teach mode"
S1, S2, S3 for function "Multi Learn":
3 selection inputs = 8 coded scanning positions
A maximum of eight positions can be binary coded via
the three selection inputs.
•using "Switch mode"
S1 for dividing "Monitoring function":
S1=0 : Object monitoring
S1=1 : Free space monitoring
Inputs which are not used, remain open.
Default: S1=0, S2=0, S3=0
S1 S2 S3
Teach
Com Start Teach
Com Start Lern

OI:BK MIKRO LIN.B
Rev. 1.01 dated 24.1.2006 Page 9
Relay outputs
K.O. These two terminals are used to indicate a fault message (K.O.).
O.K. These two terminals are used to indicate a no fault message,
i.e. a good cycle (O.K.).
The terminals have been designed as dry relay contacts. By switch selection, they may be
configured as either normally open or normally closed.
The contacts have been designed for 250 VAC and, by additional internal circuits, protected
against inductive switch-off peaks of up to 19 W (2 ms).
Note:
Relay as normally closed contact: active =open
inactive =closed
Relay as normally open contact: active =closed
inactive =open
When there is no power to the unit, the contacts always will be open.
Even when using relay as normally closed, they are open
(like the active status) when the power supply is not connected.
2.1.3 Light-emitting diodes
Three light-emitting diodes (LEDs) on the front panel provide information about the current status of
the BK MIKRO LIN.B monitoring system (see chapter "Status Indication"):
Fig. 2-4:Control unit –Light-emitting diodes
yellow Power supply / Status
Indication of supply voltage and status
red "K.O." relay
Indication of fault message
green "O.K." relay
Indication of no fault message
red/green Error messages
Indication of illegal switch settings
i
k.o.
o.k.
k.o.
o.k.
k.o. o.k.
o.k.
L1 N
AC IN
k.o.
LED
yellow LED
red LED
green

BA: LS-IC/BK MIKRO LIN.B
Page 10 Rev. 1.01 dated 24.1.2006
2.1.4 Rotary switches
Only for "Multi”!
The two rotary switches P1 and P2 are used to set the start position and the end position of the
range, which is controlled by object monitoring or free space monitoring.
The position settings are possible in steps of 6.25%.
The figure shows the setup on delivery.
Fig. 2-5:Control unit –Rotary switches
Rotary switches Meaning
P1=0, P2=0 Scanning with learn function
P1 ≥0
P2 >P1
P2 ≤93.75
Scanning with setting the scanning range:
P1= start position
P2= end position
–No tolerances selectable
–Selection input S1 for:
Object monitoring S1=0
Free space monitoring S1=1
Illegal switch settings
•P1=P2≠0Error
•P1 ≠0 and P2=0 Error
will cause flashing red and green LED.
2.1.5 Toggle switches
Using the toggle switches, the following functions may be set.
"Multi" "Single"
Fig. 2-6:Control unit–Toggle switches
Note:
The figure above shows the switch settings on delivery !
i
!
Caution
25%
0%
50%
75%
P1
25%
0%
50%
P2
ok: Obj.
100
1
2
Home
50
Intensity low
Relay N.O.
"O.K." at stop pos.
Scanner TK50-LIN.B
Tolerance small
Intensity high
Relay N.C.
"O.K." at object
Scanner TK100-LIN.B
Tolerance great
50 100
Scanner TK100-LIN.B
Tolerance great
Intensity high
Relay N.C.
Scanner TK50-LIN.B
Tolerance small Intensity low
Relay N.O.

OI:BK MIKRO LIN.B
Rev. 1.01 dated 24.1.2006 Page11
"Scanning intensity" switch
Speed and force of scanner's wand in its scanning range.
For "Teach-in" and "Start" cycle, in case of a good message, the impact force amounts to:
approx. 5 N
approx. 9 N
"Output relay" switch
Mode of operation for the two output relays (see section "Relay outputs").
Relay N.O. (normally open contact)
Relay N.C. (normally closed contact)
"Scanner" switch
Selection of the scanner.
50 Scanner with max. stroke of 50 mm
100 Scanner with max. stroke of 100 mm
"Tolerance range" switch(es)
Range of tolerance for "O.K." message referred to the position learned by "Teach-in".
Fig. 2-7:Range of tolerance
"Multi" "Single" Tolerance [mm]
––– 0.32 (±0.16)
1(±0.5)
––– 2(±1)
10 (±5)
"O.K. indication" switch
Only for "Multi" !
"O.K." message can be output at different times.
Obj. after detecting the object
Homeafter reaching the stop position
Range of tolerance
Object
"learned" position
1
2
1
2
1
2
1
2

BA: LS-IC/BK MIKRO LIN.B
Page 12 Rev. 1.01 dated 24.1.2006
2.1.6 Notes on technical safety
according to DIN VDE 160
according to EMC directive 89/336/EEC
for the models with power supply 24 VDC and 120 VAC
The control unit comprises the following circuits, all isolated from each other:
K.O. output (2 terminals) safely isolated from all other circuits
O.K. output (2 terminals) safely isolated from all other circuits
AC power supply (L1, N) safely isolated from all other circuits
DC power supply
(+24 V,–24 V) safely isolated from K.O. output, O.K. output,
and AC power supply
Control inputs
(Com, Start, Teach) safely isolated from K.O. output, O.K. output,
and AC power supply
Selection inputs
(S1, S2, S3) safely isolated from K.O. output, O.K. output,
and AC power supply
Scanner connections safely isolated from K.O. output, O.K. output,
and AC power supply
Inputs
–control inputs
(Com, Start, Teach)
–selection inputs
(S1, S2, S3)
–Pulse inputs from scanner
opto-decoupled,
no safely isolation from each other

OI:BK MIKRO LIN.B
Rev. 1.01 dated 24.1.2006 Page13
2.2 Scanner
The scanner housing is cylindrical and smooth, thus permitting easy installation (e.g. by using a
mounting bracket). The scanner is designed for easy access for servicing and changing the wand's
tip. Aligning the scanner is easy and requires no additional instruments or aids.
After a supply voltage has been applied, the scanner travels from the momentary position to the
internal backstop, moves into its stop position and will be held there by applying a low voltage.
Using the scanners with a different control unit than BK MIKRO LIN.Bmay damage the scanner
and control unit.
Note:
•Due to its small diameter, a wand is easily overlooked.
•Your wand is a wearing part! Each contact with a rotating object will cause
corresponding wear on the wand. This may even lead to the metal wand
breaking.
Due to the injury hazard this causes, users should exercise particular caution
within any BK MIKRO moving area.
2.2.1 Technical data
General
Housing anodized aluminum
Protection type IP 64
Scanning tip exchangeable, thread M3x6
Connection to control unit small circular connector M12x1, 6 pin
Ambient temperature 0 ºC to +80 ºC
Storage temperature –25 ºC to +85 ºC
Scanning cycles > 5 million at minimum scanning intensity
TK50-LIN.B
Control unit –BKM LIN.B Multi "Scanner" switch set to "50"
–BKM LIN.B Single "Scanner" switch set to "50"
Scanning range 50 mm max. stroke
Wand length 67 mm approx.
TK100-LIN.B
Control unit –BKM LIN.B Multi "Scanner" switch set to "100"
–BKM LIN.B Single "Scanner" switch set to "100"
Scanning range 100 mm max. stroke
Wand length 117 mm approx.
!
Warning

BA: LS-IC/BK MIKRO LIN.B
Page 14 Rev. 1.01 dated 24.1.2006
Mechanical dimensions
TK50-LIN.B = "50 mm max. stroke"
Requirement for correct monitoring: "Scanner" switch at control unit set to "50" !
Fig. 2-8:ScannerTK50-LIN.B
TK100-LIN.B = "100 mm max. stroke"
Requirement for correct monitoring: "Scanner" switch at control unit set to "100" !
Fig. 2-9:Scanner TK100-LIN.B
27.5
154
73 ø 32 49
ø 4
83.5
max. 145 ø 2041
1750
General tolerances
ISO 2768 – mK
max.stroke
Stop position
Housing
Connection cable
(angled connector)
Scanning wand
(tip exchangeable, M3x6)
Connector
(straight)
Connection cable
(connector at the control unit end)
ø 4
254
123 ø 32 99
17
83.5
max. 111
ø 20
100
General tolerances
ISO 2768 – mK
27.5
41
Connector
(angled)
Connectioncable
(connector at the control unit end)
Scanning wand
(tip exchangeable, M3x6)
Housing
Connection cable
(straight connector)
max. stroke Stop position

OI:BK MIKRO LIN.B
Rev. 1.01 dated 24.1.2006 Page15
2.2.2 Accessories
BK MIKRO LIN.B, all scanners !
Fig.2-10:Scanners –Accessories
2.2.3 Scanning Wand
Stop position
Stop position =
Zero position of the wand
Stop position ≠
Internal backstop !
Fig.2-11:Stop position of the wand
Note:
Do not push the wand back to its internal backstop (the real limit position)
by hand.
This damages the gear !
Initial position
The tip of the wand is to be positioned at random between the object to be monitored and the
internal backstop of the wand.
After supply voltage has been applied, and at the end of "Teach-in" or "Start" the wand will move
into its stop position in any case.
Scanning range
Any scanning range between stop position and maximum stroke can be used.
Exchange the scanning tip
The tip can easily be removed from the wand (thread M3x6) and exchanged by a project-specific
variant.
i
Internal backstopStop position
approx. 1.5 mm
Wand holder
Adapter (with point of fracture
in case of damage),
M3
M3 565
ø 4
M3
Scanning tip extension,
M3
M3
0.7 x ø2.0
ø 7
M2.5
125 56.5
ø 4
M3
21
ø 1.3
ø 7
M2.5 M2.5
M3
Scanner tip, plastic
Scanner tip, brass
ø 4.5
ø 6
12
57
M3
10
ø 4
ø 5
M3

BA: LS-IC/BK MIKRO LIN.B
Page 16 Rev. 1.01 dated 24.1.2006
2.3 Connection cable
Control unit and scanner are connected by a 6-wire PUR-cable:
•Small circular connector to DIN 45322 at the control unit end.
•Molded plug at the scanner end.
•Length 5 m, can be extended to a maximum length of approximately 25 m
with extension cables.
Pin configuration (at the control unit end)
Small circular connector to DIN 45322, 6 pin
1wh
white
2br brown
3gn
green
4ye yellow
5gr gray
6pi pink
Fig.2-12:Connection cable –Pin configuration
Note:
•To increase the operational life of this cable, it should not be subject to more
than a minimum amount of movement during operating cycles.
•If this plug needs to be removed during fitting, please ensure that this pin
configuration is followed on reassembly.
gr
ye
gn
br
wh
pi
3
1
2
6
5
4
i
This manual suits for next models
3
Table of contents
Other Techna-Tool Measuring Instrument manuals
Popular Measuring Instrument manuals by other brands
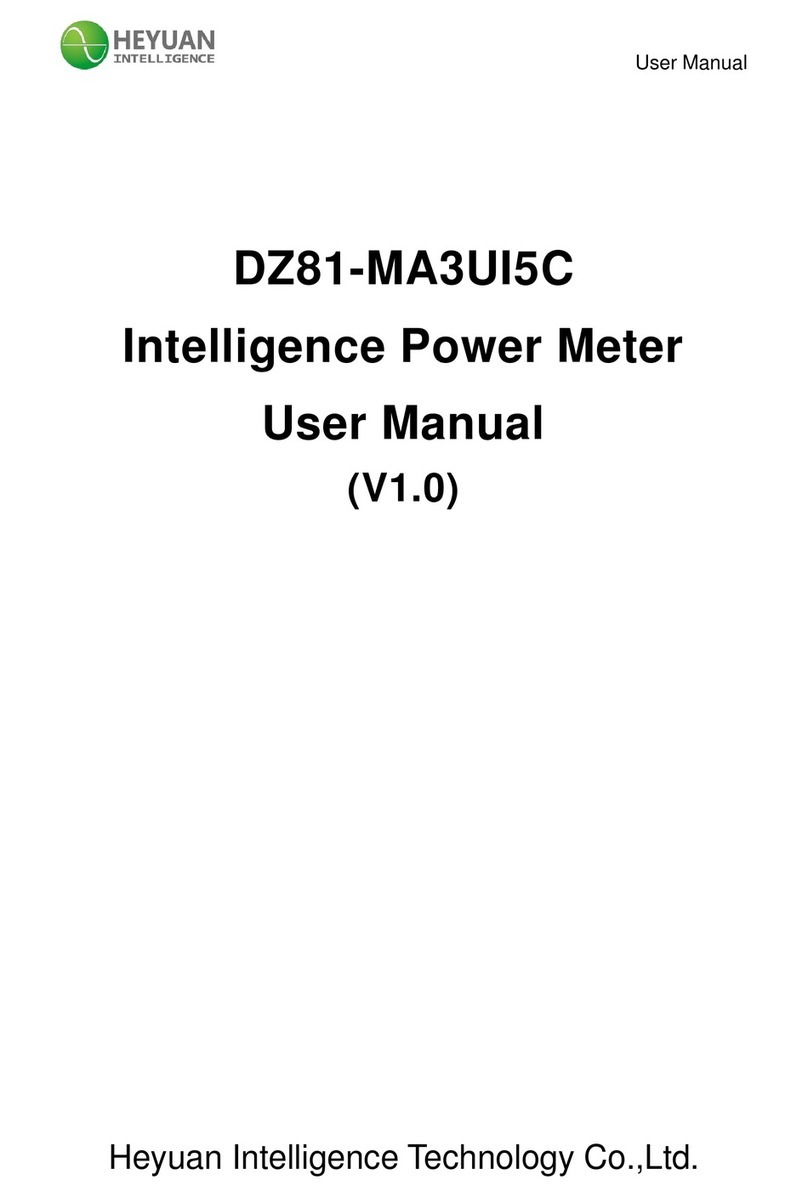
Heyuan Intelligence
Heyuan Intelligence DZ81-MA3UI5C user manual
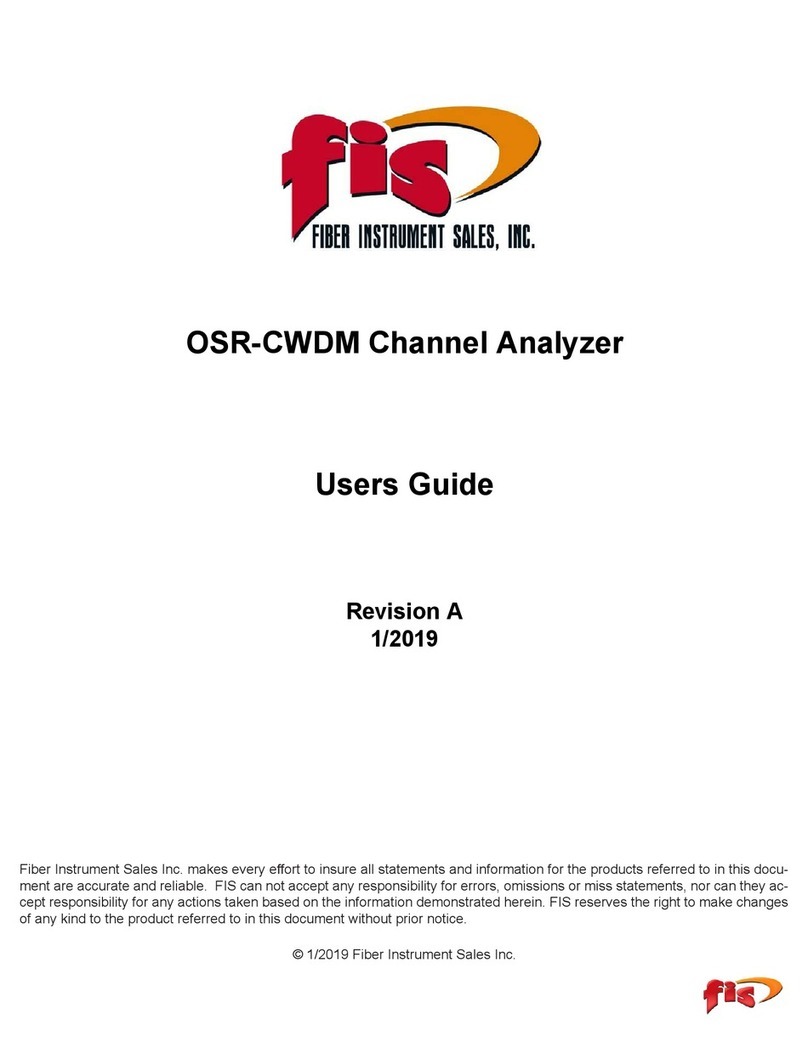
FIS
FIS OSR-CWDM user guide
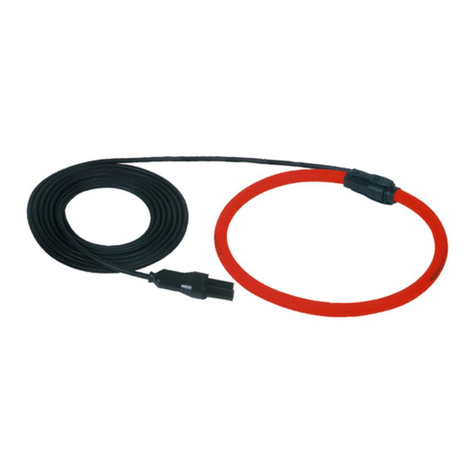
AEMC
AEMC 193-24-BK user manual
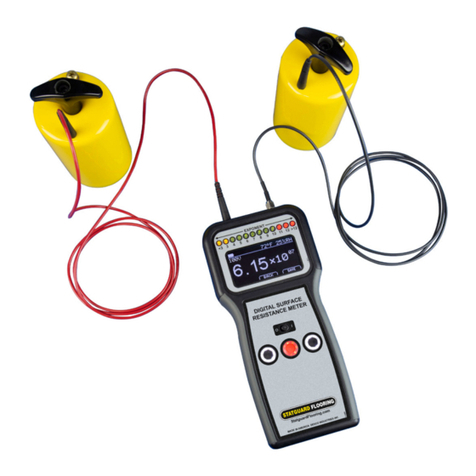
Desco
Desco Statguard Flooring D19290 Installation, operation and maintenance
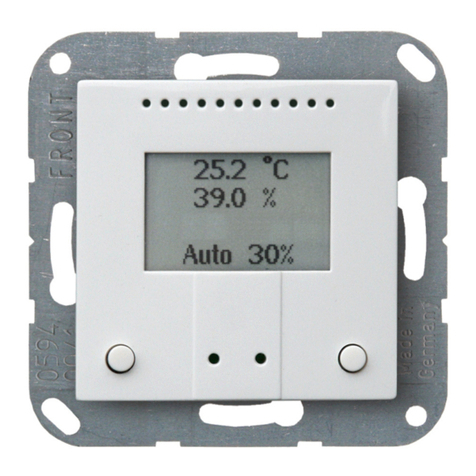
elsner elektronik
elsner elektronik TH PF Series Technical specifications and installation instructions

IFM
IFM SD6020 operating instructions