Technical 3000 Series User manual

FORM 119-ING. 04/11 We reserve to modify our production without previous communication
.
1/8
S.r.l.
Via Toscana, 9
20060 Vignate (MI) - Italy
Tel. +39-2-95.36.12.40
Fax +39-2-95.60.273
www.technical.it
S
SA
AF
FE
ET
TY
Y
V
VA
AL
LV
VE
ES
S
S
SE
ER
RI
IE
E
3
30
00
00
00
0
T
TY
YP
PE
E
3
32
20
0
U
US
SE
E
A
AN
ND
D
M
MA
AI
IN
NT
TE
EN
NA
AN
NC
CE
E
M
MA
AN
NU
UA
AL
L

FORM 119-ING. 04/11 We reserve to modify our production without previous communication
.
2/8
SAFETY VALVE FOR GASES,
VAPOURS AND LIQUIDS
Characteristics
Homologation ASME / PED:
overpressure 10%;
blowdown 5 - 10%;
spring range ± 5% of set pressure ;
gases and vapours discharge coefficient
K = 0,94 PED
K = 0,951 ASME
liquids discharge coefficient
K = 0,6 PED
K = 0,720 ASME
connections: ANSI, UNI, DIN, AFNOR etc
Accessories
Test gag;
soft seat;
balancing bellows
lifting lever;
heating jacket
CARATTERISTICHE E LIMITI DI PRESSIONE
ORIFIZIO
MAX. CONTROPRESSIONE
ø AreaTipo
mm cm² Sq. in
Alzata
mm
Max. pressione
di scatto
bar
Senza soffietto
bar
Con soffietto
bar
D
10
0.785
0.121
2.5
413
19 ÷ 41
10
E
13.3
1.389
0.215
3.1
413
19 ÷ 41
10
F
16.6
2.164
0.335
4.2
344
19 ÷ 51
15 ÷ 34
G
21.2
3.53
0.547
6.2
255
19 ÷ 51
15 ÷ 32
H
26.5
5.515
0.854
9.8
189
15 ÷ 28
19 ÷ 51
H1
30
7.068
1.095
10
189
15 ÷ 28
19 ÷ 51
J
34
9.079
1.407
11
186
19 ÷ 41
15
K
40.6
12.94
2.006
13
153
19 ÷ 41
10 ÷ 13
K1
45
15.9
2.465
14
153
19 ÷ 41
10 ÷ 13
L
50.6
20.1
3.116
16
103
19
7 ÷ 11
M
56.8
25.33
3.927
19
75
19
5 ÷ 11
N
62.4
30.58
4.74
20
68
19
5 ÷ 11
P
75.7
45
6.976
24
68
19
5 ÷ 10
Q
99.6
77.91
12.07
30
41
8
4 ÷ 8
R
119.8
112.7
17.47
36
20
4 ÷ 7
4 ÷ 7
T
152.8
183.3
28.42
46
20
2 ÷ 7
2 ÷ 7

FORM 119-ING. 04/11 We reserve to modify our production without previous communication
.
3/8
30000 SERIES SAFETY VALVES
Safety valves 30000 Series, designed and manufactured by Technical s.r.l. in accordance with API 526, are full
nozzle and total lift type. They posses a high discharge coefficient (k=0.94), certified by I.S.P.E.S.L. and (K=0.951)
certified da ASME/NATIONAL BOARD on the basis of experimental tests performed by authorized laboratories; are
suitable for gaseous and liquid fluids.
The body and the bonnet are made from casting. The bonnet contains the spiral spring that, depending on the use
and type of fluid, can be assembled with closed cap or with open bonnet (vapour).
The seat is plane and “ metal on metal” type; it is possible to add valves with a soft sealing ring (FPM rubber). Upon
request, the valve is also available with accessories such as the packed or open lifting lever, test gag, balancing-
isolation bellows and heating jacket.
1. INSTALLING
Before installing the valve on the plant make sure that:
the line fluid is indicated on the construction declaration or is compatible with the construction materials;
the inlet piping in the valve are clean, impurities less, slag less etc. and eventually remove them.
the inlet and discharge piping are dimensioned in such a way that they generate the minimum possible loss of
pressure.
The mounting of the valve on the plant has to be carried out tightening the lock nuts in a crossed and uniform way.
Once the valve has been installed on the plant make sure that:
the discharge is not positioned in such a way to result dangerous for people or for instruments;
the discharge is properly conveyed .
1.1 SETTING UP
Before shipment all the safety valves are hydrostatically tested and set at the setting pressure required by the Client.
Therefore regulation in loco should not be necessary.
The maximum setting error is less than 3% for pressure up to 21 bar, with a minimum of 0,2 bar; it is less than 0,7
bar up to 70 bar; it is less than 1% for pressure over 70 bar.
In case it should be necessary to modify the set pressure or the re-closure pressure of the valve (blowdown) , it
should be necessary proceed as follows:
1.1.1 setting regulation ( referring to drawing )
In order to carry out setting regulation of the valve it is necessary:
remove the cap (11) and unloosen the lock nut (16);
turn the adjusting screw (10) clockwise in case the set pressure should be increased;
turn the adjusting screw (10) counter clockwise in case the pressure should be decreased.
The adjustment range of the spring setting is ± 5% of the set pressure indicated on the label of the valve.
Once the valve setting is regulated tighten the lock out (16) and re-screw the bonnet cap (11).
1.1.2 blowdown ring regulation (table 1)
In order to carry out the regulation of the blowdown ring execute the following operations:
loosen the screw (8);
raise the blowdown ring (5) by turning it counter-clockwise until touch the disc holder (3);
withdraw the blowdown ring (5) by turning it clockwise, as indicated in table 1;
tighten the screw (8) making sure it does not block the blowdown ring (5) but only that it prevents the blowdown
ring rotation.
If is required a more precise blowdown regulation, should be necessary carry out it with the valve installed on the
plant at full flow, taking into consideration that:
reducing the number of withdrawing notches it is favoured the opening and it is delayed the re-closure;
increasing the number of withdrawing notches it is delayed the full opening and it is favoured the re-closure.
2. DISASSEMBLING
In order to execute disassembling carry out progressively the following operations:
CAUTION : before disassembling the valve make sure that the plant on which it
is mounted is not “under pressure” and that no pressure inside
the valve itself has remained.
before disassembling the bonnet of the valve body make sure that the spring (13)
is totally released using the adjusting screw (10).

FORM 119-ING. 04/11 We reserve to modify our production without previous communication
.
4/8
TABELLA 1
REGOLAZIONE ANELLO BLOWDOWN
PRESSIONE
TARATURA
NUMERO TACCHE DI ARRETRAMENTO DALLA POSIZIONE DI CONTATTO
bar
ORIFIZIO
D E F - G H J K L M N P Q R T
0.5 - 7
8 - 15
16 - 25
26 - 40
41 - 60
61 - 90
91 - 125
126 - 190
191 - 280
281 - 360
1 - 2
4 - 5
5 - 6
6 - 9
9 - 12
12 - 15
15 - 18
18 - 21
21 - 24
24 - 27
1 - 2
5 - 6
6 - 7
7 - 10
10 - 13
13 - 17
17 - 20
20 - 23
23 - 26
26 - 29
2 - 3
4 - 8
8 - 10
10 - 13
13 - 16
16 - 19
19 - 22
22 - 25
25 - 28
28 - 31
2 - 3
4 - 8
9 - 11
10 - 13
14 - 17
17 - 20
20 - 25
25 - 28
2 - 3
4 - 9
9 - 11
11 - 14
14 - 18
18 - 22
22 - 26
26 - 30
2 - 5
5 - 8
8 - 12
12 - 16
16 - 20
20 - 25
25 - 30
3 - 6
6 - 9
9 - 12
12 - 16
16 - 22
22 - 28
28 - 32
3 - 6
6 - 12
12 - 15
15 - 18
18 - 25
25 - 32
3 - 9
9 - 13
13 - 18
18 - 25
25 - 32
32 - 40
3 - 10
10 - 15
15 - 22
22 - 28
28 - 35
35 - 45
3 - 10
10 - 18
18 - 22
22 - 32
32 - 40
4 - 12
12 - 22
22 - 32
4 - 22
22 - 30
30 - 45

FORM 119-ING. 04/11 We reserve to modify our production without previous communication
.
5/8
2.1 VALVE WITHOUT ACCESSORIES
remove the valve from the plant;
remove the cap (11) and unloosen the lock nut (16) and the adjusting screw (10);
remove the screws (15), the bonnet (14) and remove all the internal parts.
2.2 VALVE WITH PACKED LEVER
2.2.1 - Type “A”
unloosen the screw (37) and remove the lever (26);
remove the nut (25) and remove the packing rings (29) and camshaft (28);
remove the lever cap (42) from the valve turning it counter clockwise;
unloosen the lock nut (27) and remove it together with the disc (33);
unloosen the lock nut (16) and the adjusting screw (10);
remove the screws (15), the bonnet (14) and remove all the internal parts.
2.2.2 - Type “B”
remove the nuts/screws (43) if any;
turn the camshaft (28) counter clockwise, putting the fork (30) at the end of stroke, and remove the lever cap (42)
from the valve
unloosen the screw (37) and remove the lever (26);
remove the nut (25) and remove the packing rings (29), the spacer, the camshaft (28) and the fork (30);
unloosen the lock nut (27) and remove it together with the disc (33);
unloosen the lock nut (16) and the adjusting screw (10);
remove the screws (15), the bonnet (14) and remove all the internal parts.
2.3 VALVE WITH OPEN LEVER
2.3.1 - Type “C”
remove the self-locking nuts with the screw (39) and remove the lever (26);
remove the nuts/screws (43)
remove the lever cap (42);
unloosen the lock nut (27) and remove it together with the disc (33);
unloosen the lock nut (16) and the adjusting screw (10);
remove the screws (15), the bonnet (14) and remove all the internal parts.
2.3.2 - Type “D”
remove the self-locking nuts with the screws (39) and remove the lever (26) and the fork (30);
remove the nuts/screws (43)
remove the lever cap (42);
unloosen the lock nut (27) and remove it together with the disc (33);
unloosen the lock nut (16) and the adjusting screw (10);
remove the screws (15), the bonnet (14) and remove all the internal parts.
3. ASSEMBLING
3.1 VALVE WITHOUT ACCESSORIES
For assembling carry out the same operations of point 2.1) but in reverse order, tightening first the nozzle (1) into
the valve body (7). Before pushing the spring (13), make sure that the blowdown ring (5) is free and does not touch
the disc holder (3).
3.3VALVE WITH PACKING LEVER
3.2.1 - Type “A”
For assembling carry out the same operations of point 2.2.1) but in reverse order, tightening first of all the nozzle (1)
into the valve body (7). Before pushing the spring (13), make sure that the blowdown ring (5) is free and does not
touch the disc holder (3).
Once assembled the valve and tightened the lock nut (16) it is necessary to put the disc (33) and the lock nut (27) at
the end of the thread and tightening one against the other.
After assembling make sure that the lever can turn easily with no efforts and without interferences.
3.2.2 - Type “B”
For assembling carry out the same operations of point 2.2.2) but in reverse order, tightening first of all the nozzle (1)
into the valve body (7). Before pushing the spring (13), make sure that the blowdown ring (5) is free and does not
touch the disc holder (3).
Once assembled the valve and tightened the lock nut (16) it is necessary to put the disc (33) and the lock nut (27) at
the end of the thread and tightening one against the other.
After assembling make sure that the lever can turn easily with no efforts and without interferences.

FORM 119-ING. 04/11 We reserve to modify our production without previous communication
.
6/8
3.3VALVE WITH OPEN LEVER
3.3.1 - Type “B”
For assembling carry out the same operations of point 2.3.1) but in reverse order, tightening first of all the nozzle (1)
into the valve body (7). Before pushing the spring (13), make sure that the blowdown ring (5) is free and does not
touch the disc holder (3).
Once assembled the valve and tightened the lock nut (16) it is necessary to put the disc (33) and the lock nut (27) at
the end of the thread and tightening one against the other.
After assembling make sure that the lever can turn easily with no efforts and without interferences
3.3.2 - Type “D”
For assembling carry out the same operations of point 2.3.2) but in reverse order, tightening first of all the nozzle (1)
into the valve body (7). Before pushing the spring (13), make sure that the blowdown ring (5) is free and does not
touch the disc holder (3).
Once assembled the valve and tightened the lock nut (16) it is necessary to put the disc (33) and the lock nut (27) at
the end of the thread and tightening one against the other.
After assembling make sure that the lever can turn easily with no efforts and without interferences
4. MAINTENANCE
The safety valves requires an ordinary but careful maintenance (SEE MAINTENANCE PLAN ) and in case it should
be necessary , follow the operation stated in point 2) for disassembling and in point 3) for assembling.
In case of seat damaging it is necessary to carry out a new lapping: this operation has to be executed by skilled
workers.
In case of inconveniences should occur to the valve, verify if in DAMAGE TABLE are contained some useful
instructions for solving the problem.
If the damage is different from what stated in the table, contact our Service Department.
WARNING
The safety valves should not be subjected to bumps or such stresses that could compromise the
working.
High loads on the spring can damage the valve.
The safety valves must be used only exclusively for the use stated in the construction declaration.
The safety valve must be revised within two years from installation for dangerous fluid (Group 1) and
within three years for other fluids (Group 2) independently from the number of interventions executed by
the valve.
ACCESSORIES
SOFT SEAT JACKET BELLOWS

FORM 119-ING. 04/11 We reserve to modify our production without previous communication
.
7/8
ORDINARY MAINTENANCE PLAN
Check of seat and disc tightness on the plant
Every valve opening
or
every 6-month working.
Check of outwards valve tightness in case of back pressure on the
plant.
Every 30 days.
Check of the painting condition on the plant.
Every 6 months.
Ordinary maintenance of the valve installed on the plant, including the
tightness check and the surface check of the movable components.
Every 12-month working.
General maintenance of the valve removed from the plant including the
disassembling, the seat and the disc check, the incidental seat and
disc lapping, gaskets substitution, painting restoration and test on the
test bench.
Every opening with seats damaging
or
every 24-month working (Group 1)
every 36-month working (Group 2)
DAMAGE TABLE
INCONVENIENT POSSIBLE DAMAGE ACTION TO BE CARRIED OUT
Fluid leakage in-line Seat wear and tear Nozzle substitution or revision
Disc wear and tear Disc substitution or revision
Seat and disc damaging Nozzle and disc revision
Impurities presence between seat and disc Nozzle and disc cleaning and revision
Valve-use with fluid different from the one stated in the
purchase order Nozzle and disc revision
Valve gaskets damaging Gaskets substitution
Valve body-bonnet damaging Valve revision or substitution
External back pressure fluid
leakage.
Cap or blowdown screw loosen Check and setting-up of the cap and of the
blowdown screw.
Opening at pressure value
different form setting valve
Back pressure variable Check of dimensioning and of the discharge piping
working conditions and possible valve substitution
with another type.
Spring release Spring substitution and check compatibility of the
material with the fluid.
Setting screw withdraw Resetting the valve and tighten very well the lock
nut
Valve intervention with quick
opening and re-closures
repeated in the time
Strong pressure loss in the inlet piping Check the inlet piping length
Not correct setting-up of the blowdown ring Withdraw the blowdown ring until obtain a proper
working, basing the first regulation one table 1; for
liquid fluids withdraw the blowdown ring
completely.
Pulsating flow rate to be discharged Check plant regulation.
Over dimensioned valve Substitute the valve with one correctly
dimensioned.

FORM 119-ING. 04/11 We reserve to modify our production without previous communication
.
8/8
MATERIAL TABLE SAFETY VALVE 30000 SERIES
TEMPERATURE LIMITS °C - 29° ÷ 232° - 29° ÷ 232° - 101° ÷ 232° - 29° ÷ 538° - 196° ÷ 350°
ITEM PARTS 16 (1) 1L (2) L3 (3) W0 (4) 50 (8) (9) 60 (5) (6) (7)
1 NOZZLE AISI 316L AISI 316L AISI 316L AISI 316L AISI 316L AISI 316L
2 DISC 17-4PH AISI 316L AISI 316L AISI 316L 17-4PH 17-4PH
2 BALL AISI 420 AISI 420 AISI 420 AISI 420 AISI 316 AISI 316
3 DISC HOLDER 17-4PH 17-4PH 17-4PH AISI 316L 17-4PH 17-4PH
4 STEM GUIDE AISI 316L AISI 316L AISI 316L AISI 316L AISI 316L AISI 316L
5 BLOWDOWN RING AISI 316L AISI 316L AISI 316L AISI 316L AISI 316L AISI 316L
6 RING AISI 316 AISI 316 AISI 316 AISI 316 AISI 316 AISI 316
7 BODY A 216WCB A 216WCB A 352LC3 A 217WC6 A 351CF8M A 351CF3M
8 BLOWDOWN SCREW AISI 303 AISI 303 AISI 303 AISI 303 AISI 303 AISI 316L
9 SPRING GUIDE CARBON STEEL / ST. STEEL
10 ADJUSTING SCREW AISI 431 AISI 431 AISI 431 AISI 431 AISI 431 AISI 431
11 CAP CARB.STEEL CARB.STEEL CARB.STEEL CARB.STEEL AISI 316L AISI 316L
12 STEM AISI 316L AISI 316L AISI 316L AISI 316L AISI 316L AISI 316L
13 SPRING CARBON STEEL / ST. STEEL / TUNGSTEN
14 BONNET A 216WCB A 216WCB A 352LC3 A 217WC6 A 351CF8M A 351CF3M
15 SCREW / AISI 304 AISI 304 AISI 304 AISI 304 AISI 304 AISI 316
16 LOCK NUT AISI 303 AISI 303 AISI 303 AISI 303 AISI 303 AISI 303
17 GASKET ALUMINIUM ALUMINIUM ALUMINIUM AISI 316 AISI 316 AISI 316
18 GASKET ARAM. FIBER ARAM. FIBER ARAM. FIBER ARAM. FIBER ARAM. FIBER ARAM. FIBER
19 GASKET ALUMINIUM ALUMINIUM ALUMINIUM AISI 316 AISI 316 AISI 316
20 GASKET ARAM. FIBER ARAM. FIBER ARAM. FIBER ARAM. FIBER ARAM. FIBER ARAM. FIBER
21 GASKET FPM RUBBER FPM RUBBER FPM RUBBER FPM RUBBER FPM RUBBER FPM RUBBER
22 SCREW AISI 304 AISI 304 AISI 304 AISI 304 AISI 304 AISI 304
23 PLUG AISI 304 AISI 304 AISI 304 AISI 304 AISI 304 AISI 304
24 PIN AISI 304 AISI 304 AISI 304 AISI 304 AISI 304 AISI 304
25 RING NUT AISI 431 AISI 431 AISI 431 AISI 431 AISI 431 AISI 431
26 LEVER CARB.ST./ ST.ST CARB.ST./ ST.ST CARB.ST./ ST.ST CARB.ST./ ST.ST ST. STEEL ST. STEEL
27 LOCK NUT LEVER AISI 303 AISI 303 AISI 303 AISI 303 AISI 303 AISI 303
28 CAMSHAFT 17-4PH 17-4PH 17-4PH 17-4PH 17-4PH 17-4PH
29 PACKING RING TEFLON TEFLON TEFLON TEFLON TEFLON TEFLON
30 FORK AISI 316L AISI 316L AISI 316L AISI 316L AISI 316L AISI 316L
33 SPACER AISI 431 AISI 431 AISI 431 AISI 431 AISI 431 AISI 431
35 BELLOWS AISI 316L AISI 316L AISI 316L AISI 316L AISI 316L AISI 316L
36 SPACER AISI 316L AISI 316L AISI 316L AISI 316L AISI 316L AISI 316L
37 LEVER SCREW AISI 304 AISI 304 AISI 304 AISI 304 AISI 304 AISI 304
38 TEST GAG AISI 304 AISI 304 AISI 304 AISI 304 AISI 304 AISI 304
39 SCREW ST. STEEL ST. STEEL ST. STEEL ST. STEEL ST. STEEL ST. STEEL
42 LEVER CAP CARB.STEEL CARB.STEEL CARB.STEEL CARB.STEEL AISI 316L AISI 316L
43 NUT / SCREW ST. STEEL ST. STEEL ST. STEEL ST. STEEL ST. STEEL ST. STEEL
45 GASKET / FPM RUBBER FPM RUBBER FPM RUBBER / FPM RUBBER
46 SOFT SEAT SCREW / AISI 316L AISI 316L AISI 316L / AISI 316L
47 SOFT SEAT DISC / AISI 316L AISI 316L AISI 316L / AISI 316L
1. Available with stellited nozzle - code H6
2. Available with stellited nozzle & disc - code K6
3. Available with stellited nozzle & disc - code L6
4. Available with stellited nozzle & disc - code W1
5. Available with stellited nozzle - code 6H
6. Available with trim in AISI 316L - code 6L
7. Available with stellited nozzle & disc - code 6K
8. Available with stellited nozzle & disc - code 5H
9. Available with stellited nozzle - code 5K
Table of contents
Other Technical Control Unit manuals
Popular Control Unit manuals by other brands
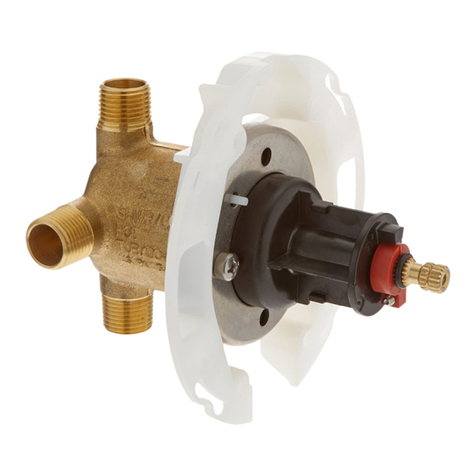
Kohler
Kohler K-305 Homeowner's guide

Mid-Continent Instrument
Mid-Continent Instrument MD41-1510 Installation manual and operating instructions
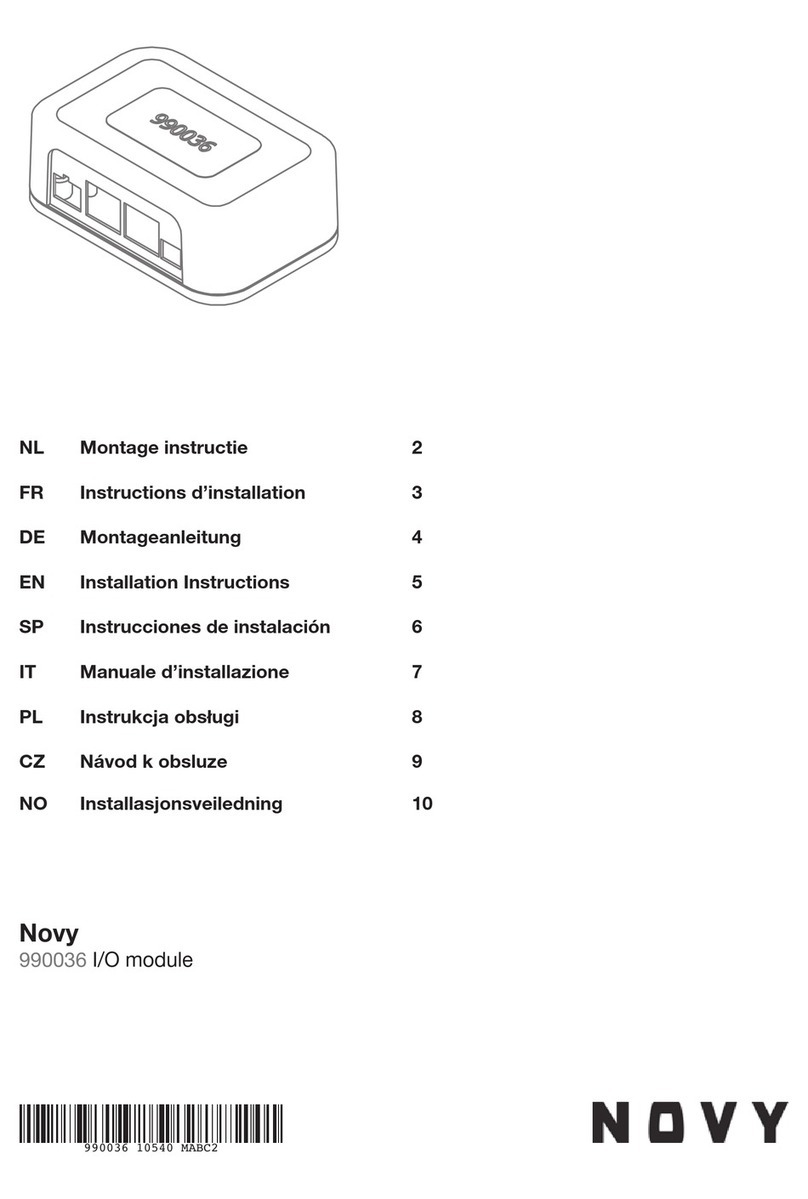
Novy
Novy 990036 installation instructions
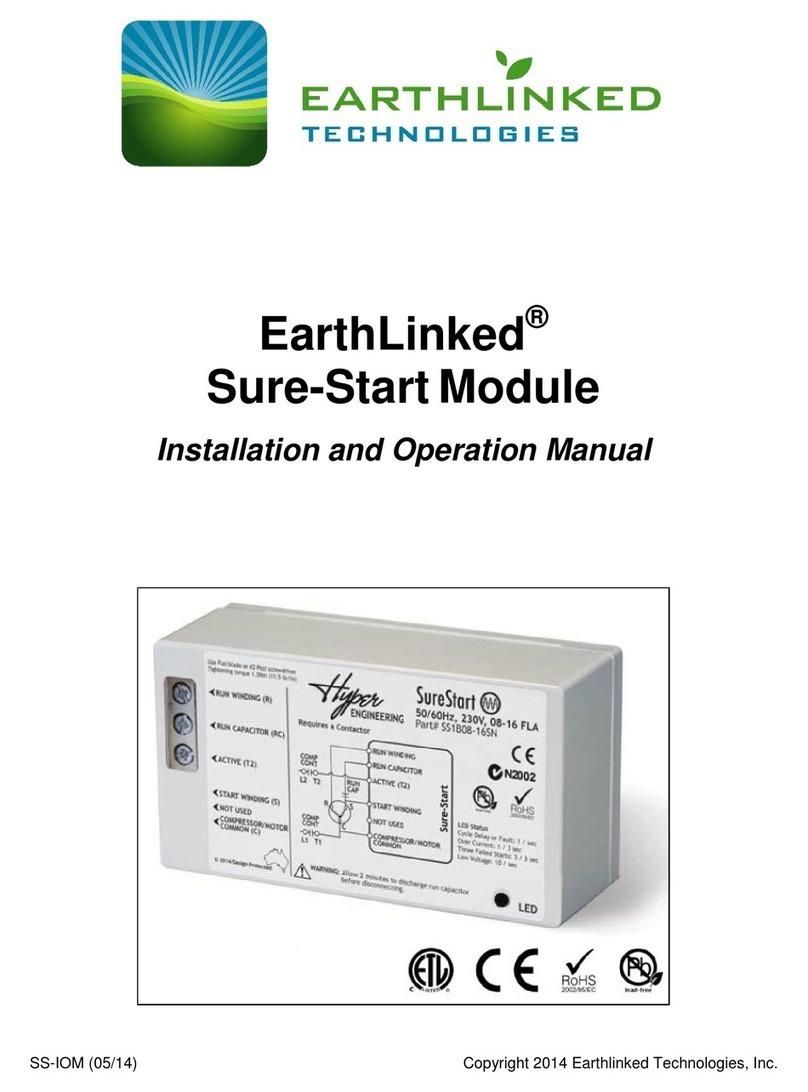
Hyper
Hyper EarthLinked Sure-Start Operation manual
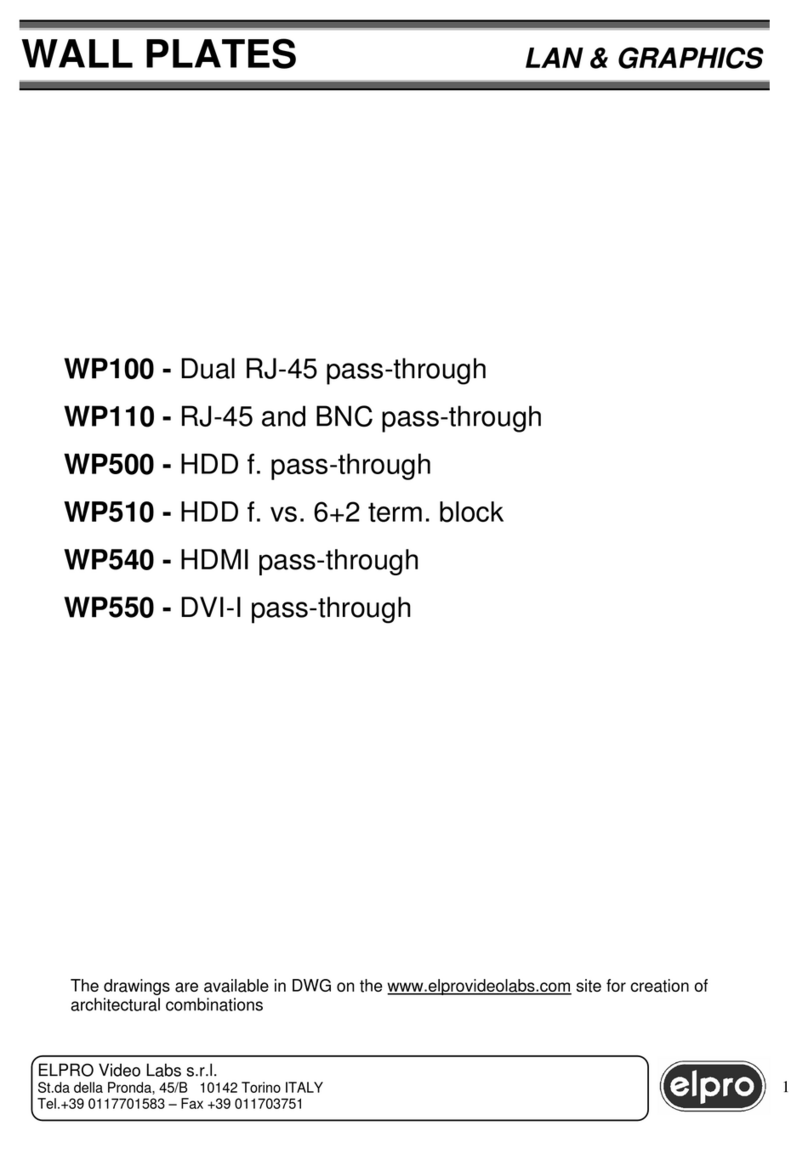
ELPRO
ELPRO WP100 manual

Comelit
Comelit Ultra Simplebus2 Technical manual