Technische Alternative FRISTAR3 User manual

ta.co.at
FRISTAR3
FRESH WATER STATION
Operating manual
EnglishManual Version 1.02.4


3
Table of contents
Safety instructions . . . . . . . . . . . . . . . . . . . . . . . . . . . . . . . . . . . . . . . . . . . . . . . . . . . . . . . . . . . . 4
Disposal . . . . . . . . . . . . . . . . . . . . . . . . . . . . . . . . . . . . . . . . . . . . . . . . . . . . . . . . . . . . . . . . . . . . . . . . . . . . . .4
Mode of operation . . . . . . . . . . . . . . . . . . . . . . . . . . . . . . . . . . . . . . . . . . . . . . . . . . . . . . . . . . . . . 5
Hydraulic circuit diagram . . . . . . . . . . . . . . . . . . . . . . . . . . . . . . . . . . . . . . . . . . . . . . . . . . . . . . . . . . . . . . . . .5
Components . . . . . . . . . . . . . . . . . . . . . . . . . . . . . . . . . . . . . . . . . . . . . . . . . . . . . . . . . . . . . . . . . 6
Installation . . . . . . . . . . . . . . . . . . . . . . . . . . . . . . . . . . . . . . . . . . . . . . . . . . . . . . . . . . . . . . . . . . 7
Preparation . . . . . . . . . . . . . . . . . . . . . . . . . . . . . . . . . . . . . . . . . . . . . . . . . . . . . . . . . . . . . . . . . . . . . . . . . . . .7
Special accessories: VMS pre-mixing set . . . . . . . . . . . . . . . . . . . . . . . . . . . . . . . . . . . . . . . . . . . . . . . . . . . .7
Dimensions . . . . . . . . . . . . . . . . . . . . . . . . . . . . . . . . . . . . . . . . . . . . . . . . . . . . . . . . . . . . . . . . . . . . . . . . . . . .8
Interchanging connections . . . . . . . . . . . . . . . . . . . . . . . . . . . . . . . . . . . . . . . . . . . . . . . . . . . . . . . . . . . . . . . .9
Installation . . . . . . . . . . . . . . . . . . . . . . . . . . . . . . . . . . . . . . . . . . . . . . . . . . . . . . . . . . . . . . . . . . . . . . . . . . .10
Commissioning . . . . . . . . . . . . . . . . . . . . . . . . . . . . . . . . . . . . . . . . . . . . . . . . . . . . . . . . . . . . . . 10
Connection of a circulation line . . . . . . . . . . . . . . . . . . . . . . . . . . . . . . . . . . . . . . . . . . . . . . . . . . 11
Activating the DHW circulation pump using the FRISTAR3 controller . . . . . . . . . . . . . . . . . . . . . . . . . . . . . .11
Hydraulic circuit diagram with circulation line . . . . . . . . . . . . . . . . . . . . . . . . . . . . . . . . . . . . . . . . . . . . .11
Circulation pump (optional) . . . . . . . . . . . . . . . . . . . . . . . . . . . . . . . . . . . . . . . . . . . . . . . . . . . . . . . . . . .11
Activating the DHW circulation pump using a different switching device . . . . . . . . . . . . . . . . . . . . . . . . . . .11
Cascade switching . . . . . . . . . . . . . . . . . . . . . . . . . . . . . . . . . . . . . . . . . . . . . . . . . . . . . . . . . . . . 12
Hydraulic circuit diagram of a cascade with four FRISTAR3 fresh water stations . . . . . . . . . . . . . . . . . .12
Control with UVR67 . . . . . . . . . . . . . . . . . . . . . . . . . . . . . . . . . . . . . . . . . . . . . . . . . . . . . . . . . . . . . . . . . .13
Control of cascade switching with freely programmable controllers . . . . . . . . . . . . . . . . . . . . . . . . . . . .14
Cascade switching with circulation line . . . . . . . . . . . . . . . . . . . . . . . . . . . . . . . . . . . . . . . . . . . . . . . . . . . . .14
Schematic diagram for activating the DHW circulation pump with the FRISTAR3 controller . . . . . . .14
Schematic diagram for activating the DHW circulation pump with a different switching device . . . .15
Data transfer with DL bus . . . . . . . . . . . . . . . . . . . . . . . . . . . . . . . . . . . . . . . . . . . . . . . . . . . . . . . 16
Status (Index 13) . . . . . . . . . . . . . . . . . . . . . . . . . . . . . . . . . . . . . . . . . . . . . . . . . . . . . . . . . . . . . . . . . . . . . .17
For x2 devices . . . . . . . . . . . . . . . . . . . . . . . . . . . . . . . . . . . . . . . . . . . . . . . . . . . . . . . . . . . . . . . . . . . . . .17
For UVR67 . . . . . . . . . . . . . . . . . . . . . . . . . . . . . . . . . . . . . . . . . . . . . . . . . . . . . . . . . . . . . . . . . . . . . . . . .18
Electrical connection . . . . . . . . . . . . . . . . . . . . . . . . . . . . . . . . . . . . . . . . . . . . . . . . . . . . . . . . . . 19
Safety instructions . . . . . . . . . . . . . . . . . . . . . . . . . . . . . . . . . . . . . . . . . . . . . . . . . . . . . . . . . . . . . . . . . . . . .19
Operation of the controller and LED indicators . . . . . . . . . . . . . . . . . . . . . . . . . . . . . . . . . . . . . . . 20
Manual-automatic changeover switch . . . . . . . . . . . . . . . . . . . . . . . . . . . . . . . . . . . . . . . . . . . . . . . . . . .20
Status LED indicator . . . . . . . . . . . . . . . . . . . . . . . . . . . . . . . . . . . . . . . . . . . . . . . . . . . . . . . . . . . . . . . . .20
Pump LED indicator . . . . . . . . . . . . . . . . . . . . . . . . . . . . . . . . . . . . . . . . . . . . . . . . . . . . . . . . . . . . . . . . . .20
Technical data . . . . . . . . . . . . . . . . . . . . . . . . . . . . . . . . . . . . . . . . . . . . . . . . . . . . . . . . . . . . . . . 21
Pressure loss characteristic curve plate heat exchanger . . . . . . . . . . . . . . . . . . . . . . . . . . . . . . . . . . . . . . . .22
Pump curve . . . . . . . . . . . . . . . . . . . . . . . . . . . . . . . . . . . . . . . . . . . . . . . . . . . . . . . . . . . . . . . . . . . . . . . . . .22
Information on the Eco-design Directive 2009/125/EC . . . . . . . . . . . . . . . . . . . . . . . . . . . . . . . . . . . . . . . . .23
Plate heat exchanger corrosion resistance . . . . . . . . . . . . . . . . . . . . . . . . . . . . . . . . . . . . . . . . . . . . . . . . . .23
Tips on troubleshooting . . . . . . . . . . . . . . . . . . . . . . . . . . . . . . . . . . . . . . . . . . . . . . . . . . . . . . . . 24

4
Safety instructions
Intended use
The freshwater station may only be installed in heating systems between the buffer tank and the
drinking water circuit. The technical limit values specified in this manual must be considered.
Incorrect use will result in the negation of any liability claims.
Electrical connection
Any electrical connections must be made by qualified electricians. Connection cables must be rout-
ed in the recesses provided in the insulated base in such a way that direct contact with the pump
casing and the pipes is prevented.
Before switching on, check whether the supply voltage matches that stated on the power rating
plates of the pump and the controller. All connections must correspond to the local regulations. Be-
fore opening the controller, all poles of the power supply must be isolated.
If you are connecting the FRISTAR3 to an electrical system via a residual current device (RCD), use
an RCD of type A which will detect pulsating direct currents and bears the following marking:
Checking using a high voltage insulation tester may cause damage to the pump and the control elec-
tronics.
Safety standards during installation, commissioning and maintenance
Installation, commissioning and maintenance may only be carried out by qualified persons who are
familiar with these operating instructions.
Before you start work on the system, ensure that the system is switched off and all components are
cooled down. When replacing the pump, turn the 4 ball valves into the closed position.
In multi-occupancy dwellings, legionella protection must be observed in accordance with the local
regulations.
Disposal
• Devices no longer in use or beyond a state of repair must be disposed of in an en-
vironmentally responsible manner by an authorised collection point. They mus nev-
er be treated as ordinary household waste.
• We can undertake the environmentally responsible disposal of devices sold by the
Technischen Alternative company upon request.
• Packaging material must be disposed of in an environmentally responsible man-
ner.
• Incorrect disposal may result in considerable damage to the environment, as
many of the materials used require professional handling.
These instructions are intended exclusively for authorised professionals. To avoid
accidents and damage due to incorrect operation, carefully read through these op-
erating instructions before you start working with the freshwater station. If you
carry out any alterations to the construction of the freshwater station or the safety
devices, you may invalidate your right to make guarantee claims. Always observe
the local regulations.
WARNING! Dependent on the pump and system operating conditions, the surface temper-
atures can be very high. Direct contact with the pump or pipes can result in burns!

5
Mode of operation
Through use of the instantaneous heating concept, drinking water is heated both hygienically and
with low energy consumption in the FRISTAR freshwater station.
If water is drawn from the mains, the primary circuit pump transports tank water from a buffer tank
through the plate heat exchanger.
On the secondary side of the heat exchanger the drinking water flowing through is heated to the set
temperature. The cooled tank water is returned to bottom layer of the buffer tank.
The speed control of the primary circuit pump takes place in the FRISTAR3 controller based on the
readings from the volume flow sensor in the hot water line (flow rate VWW and temperature TWW)
and the temperature sensors in the cold water line (TKW) and the primary flow (TPri). The pump is
controlled with PWM signals. Optimal matching of the control behaviour with the pump, valve and
heat exchanger ensures perfect stabilisation of the outlet temperature.
The controller has an integral heat meter, which enables the values to be read via the data link.
Hydraulic circuit diagram
Pre-mixer (recommended)
Temperature
Primary flow
Flow rate sensor and DHW
temperature
Cold water temperature
Safety valve max. 6 bar
Primary pump

6
Components
Controller
Plate heat ex-
changer
Ball valve
Ball valve
Ball valve
Primary
sensor
Volume flow
sensor + DHW
temperature
Ball valve
Ventilation primary circuit
Cold water
sensor
Power cable
Flow primary
circuit
Return pri-
mary circuit
Hot water Sec-
ondary circuit
Cold water Sec-
ondary circuit
Valve
Pump
(Orientation of the
plug-in strip varies)

7
Installation
Preparation
• A safety valve (max. 6 bar) must be installed in the cold water supply corresponding to stand-
ards DIN 1988 and 4753, part 1 and TRD 721.
• If the cold water pressure > 6 bar, fit a diaphragm pressure reducer max. 6 bar.
• The installation of flushing equipment before and after the plate heat exchanger in the primary
and secondary circuits is recommended for descaling or cleaning as necessary.
Special accessories: VMS pre-mixing set
If the tank is operated at a temperature higher than 70 °C a pre-mixer that restricts the temperature
to less than 70 °C must be used in the primary circuit.
In order to prevent damage from calcification, the maximum pre-mixing temperature must be 70 °C
with a water hardness of up to 10 °dH, 65 °C with up to 15 °dH and 60 °C at most with a hardness
above 15 °dH.
The VMS pre-mixing set is suitable for both FRISTAR models (left pump, right pump).
Figure: Connection for FRISTAR with right pump
Technical data
Maximum temperature of pri-
mary circuit
95°C, short term: 100°C
Setting range 45°C - 65°C
Flow coefficient of mixing valve 4,5m3/h
Connections for FRISTAR ¾“

8
Dimensions
Housing dimensions (thermal insulation cover)
W x H x D = 366 x 573 x 160 mm

9
Interchanging connections
For optimum matching of the pipelines to the freshwater station it is possible to interchange the con-
nections (right/left). This does not change venting of the primary circuit, however.
Procedure:
1. Demounting of pipe elements 1 - 4 including pump from the heat exchanger
2. Removal of the pump and installation in the correct position.
3. Remount pump connection plug 5 on the other side. The flow direction of the pump is upwards.
On WILO pumps, the connection plug is above the pump, and on Grundfos pumps it is below.
4. Mounting of pipe elements 1 - 4 and the pump on the heat exchanger (see figures above) on the
other side, correct positional setup of the volume flow sensor
5. Commissioning according to the "Commissioning" chapter
Important: The primary and secondary connections must be exchanged together!
11
22
3
4
5
3
4
Pump connection-plug
Version
„Pump right“
Version
„Pump left“

10
Installation
• Mounting position: Only vertical
• Installation with the heat exchanger at the top/above the controller (acc. to diagrams) is recom-
mended.
• Pull off the cowling in a forwards direction.
• If necessary: Interchange the right/left connections (see chapter "Interchanging connections").
• Mark the fastening points, insert rawl plugs, fasten the station to the wall.
• Fitting and connection of the pipe connections (3/4" outside thread connector). Plan for as short
as possible pipes in the primary circuit (tank -> freshwater station).
• Check all the freshwater module's connections for leaks and ensure that they are securely fit-
ted.
• Electrical connection
The freshwater station is pre-wired ready for installation, connection to the electricity mains
takes place on site:
• using a plug in a wall socket or
• using a double pole isolator with a permanent connection.
Commissioning
• Before filling the system, thoroughly flush both the primary and secondary side systems.
•Slowly fill the house system with drinking water via the secondary side ball valves.
• Vent the house system at the draw-off valves.
• Slowly fill the system with hot water via the ball valves in the primary flow.
• Vent the primary circuit using the venting opening of the plate heat exchanger.
• Set the pump to continuous operation and check pump running. Audible background noise dur-
ing operation of the circulating pump indicates air in the system.
Warning! Only start the pump when it is filled.
• Check all connections, including in the freshwater station, for correct seating and leaktightness.
If necessary, retighten to the necessary torque.
• When using a circulation pump: Set the differential temperature at the potentiometer inside the
controller (Caution! Switch off the 230 V power supply before opening the controller!)
• Place the cowling on the bottom part
• Set the pump in automatic mode and select the setpoint temperature.

11
Connection of a circulation line
Activating the DHW circulation pump using the FRISTAR3 controller
Hydraulic circuit diagram with circulation line
Circulation pump (optional)
If an external DHW circulation pump is connected directly to the FRISTAR3 controller, it will operate
in pulse mode. While water is being drawn off (once or continually), the DHW circulation pump runs
until the temperature at sensor TZirku reaches the set temperature (potentiometer on the front of the
controller) plus the set difference (potentiometer inside the controller) (no maximum runtime). Once
the temperature is reached, pump operation can only start again after a 10 minute pause.
If a DHW circulation pump is not used, the potentiometer must be set to 0 (= factory setting), as oth-
erwise the primary pump would run on after every draw-off.
To connect the circulation line, a tee is installed in the secondary circuit cold water pipe.
The sensor TZirku is optional. If it is not connected, the temperature of the sensor TKW is used. A
PT1000 sensor is used for the TZirku sensor.
Activating the DHW circulation pump using a different
switching device
It must be ensured that the flow rate in the DHW circulation line is greater than the flow sensor min-
imum flow rate (2 l/min or 120 l/h).
When the DHW circulation pump is switched on, the VKW sensor measures the flow rate and the pri-
mary pump is enabled.
Primary pump
Circulation pump

12
Cascade switching
The FRISTAR3 is designed for a maximum water draw-off of 30 l/min. For a greater draw-off of do-
mestic hot water, multiple freshwater stations can be used in a cascade.
The first module is fed directly, all others stations are added with stop valves, if necessary. These
valves must open or close in at least 30 seconds. The UDV universal 3-way valve from Technische
Alternative is excellent for this purpose.
Valves are added via overriding controller with a volume flow sensor that measures the total volume
flow. With up to 3 modules, the FTS5-85DL sensor is adequate; with 4-5 modules, the FTS9-150DL
sensor must be used.
The sensors in the FRISTAR stations should not be subjected to more than 30 litres per minute. The
final station, however, should be flushed several times a day to prevent stagnant water from forming.
This is ensured if the overriding controller increases the station number in stages of about 8-10 l/
min. In the following "step-by-step" instructions, the first stage with 9 l/min was selected because
sensor FTS9-150DL is activated properly starting at 9 l/min only.
A UVR67 controller can be used for switching the modules. Cascade control can of course also be
integrated into the programs of freely programmable controllers.
Hydraulic circuit diagram of a cascade with four FRISTAR3 fresh
water stations
Figure with fresh water stations version, version "Pump on the right"
The initial designations for stop valves A1 – A3 refer to controller UVR67.

13
Control with UVR67
Step-by-step instructions
The 3 outputs A1, A2 and A3 for the shut-off valves are switched on if the corresponding flow rate
thresholds min1 (540 l/h), min2 (960 l/h) and min3 (1440 l/h) are exceeded.
Level/menu Technician menu password 32, expert menu PW 64
1Expert
Ext. sensors
Adoption of the flow rate at sensor FTS9-150DL as
EXT input 1. When using an FTS5-85DL, the DL bus
index is specified as 7.
2Expert
Sensor menu
S1
Adoption of EXT input 1 at sensor S1.
3Expert
Sensor menu
S3
Adoption of EXT input 1 at sensor S3.
4Expert
Sensor menu
S4
Adoption of EXT input 1 at sensor S4.
5
Expert
System protection
Excess temp. lim-
iter 1
Deactivation of collector excess temperature shut-
down activated at the factory.
6Expert
Program settings Selection of program 496.
7Technician
Parameters
The values Max1, Max2 and Max3 must be set to
"No". This eliminates their influence on the control
process.
8Technician
Parameters
The parameter Min1 maintains its start threshold at
54.0 °C (≙ 540 l/h = 9 l/min). The stop threshold is
49.0 °C. These thresholds are used to switch output
A1.
9Technician
Parameters
Start value 96.0 °C (≙ 960 l/h = 16 l/min) for the value
Min2. The stop threshold is 91.0 °C. These thresholds
are used to switch output A2.
10 Technician
Parameters
Start value 144.0 °C (≙ 1440 l/h = 24 l/min) for the
value Min3. The stop threshold is 139.0 °C. These
thresholds are used to switch output A3.
11 Technician
Parameters
The values Diff1, Diff2 and Diff3 must be set to "No".
This eliminates their influence on the control process

14
Control of cascade switching with freely programmable controllers
The outputs for the stop valves are switched on by comparison functions, with one comparison func-
tion for each valve. The relevant switch-on and switch-off thresholds should be chosen in the same
way as for the UVR67.
Cascade switching with circulation line
Schematic diagram for activating the DHW circulation pump with the FRI-
STAR3 controller
Figure with fresh water stations version, version "Pump on the right"
The circulation pump is connected only to the always ready FRISTAR3.
Circulation pump

15
Schematic diagram for activating the DHW circulation pump with a different
switching device
If the DHW circulation pump is switched via a different controller, the DHW circulation return must
be connected to the cold water supply line.
However, it must be ensured that the flow rate in the DHW circulation line is greater than the mini-
mum flow rate of the flow sensor in the FRISTAR3 (2 l/min or 120 l/h).
UVR67
If the DHW circulation pump is also to be switched on and off according to temperature, the maxi-
mum possible number of FRISTAR3 modules is three. This is done using the program 480 for switch-
ing modules 2 and 3 on and off via outputs A1 and A2. The DHW circulation pump can be switched
at output A3 via the differential S5 – S4 (S5 is unused, S4 measures the DHW circulation temperature
and switches off when the max3 value is reached).
Freely programmable controllers
The circulation pump can be controlled with the "circulation" function.

16
Data transfer with DL bus
The FRISTAR3 controller can be connected to the DL bus. The DL bus allows the sensor values, the
set value and the heat meter values to be adopted via DL inputs on the TA controllers. This also
makes logging of the values possible
With the programmable controllers (e.g. UVR16x2), a set value can be issued via a DL output which
will overwrite the setting on the FRISTAR3 controller.
The FRISTAR3 controller returns the corresponding value when requested by the control system. The
request is made up of the DL address of the FRISTAR3 controller and the index of the reading.
The address is set with DIP switches on the PCB of the FRISTAR3 controller, which are labelled 1, 2
and 4. These are located on the outer edge of the PCB. If the DIP switches are not in the ON position,
address 1 is assigned to the FRISTAR3 controller (factory setting). Provided no other sensors are
connected to the DL bus, no change of address is required.
The new address is derived from address 1 (= factory setting) plus the sum of all values of the DIP
switches that are set to ON.
Example: desired address 6 = 1 (from factory settings) + 1 + 4
= DIP switches 1 and 4 must be set to ON
The index of the respective values is fixed:
Index: Measurement:
1 Actual DHW temperature Tww [°C]
2 Cold water temperature TKW [°C]
3 Flow rate [l/h]
4 Primary temperature TPri [°C]
5 Circulation temperature [°C]
6 Set temperature [°C]
7 Pump output [%]
8 Valve position [%]
9 Current output [kW]
10 Total energy [kWh]
11 Total energy [MWh]
12 Water meter [m3]
13 Status (see "Status" on page 17)
DIP switches

17
Status (Index 13)
A status code is assigned to each status. The sum of all active status codes is output under
index 13 ("Status").
Example: A status of 3 would mean that the circulation pump is running (1) and the Zirkomat is
enabled (2).
For x2 devices
The measured values are parameterised in the menu "DL bus" as DL inputs.
Example: Reading the actual DHW temperature (amend DL address!)
A set value can also be specified through a DL output.
Example: Specification of the set temperature via the function "Time switch"
1 Circulation pump running
2 Zirkomat, enable
16 Sensor T.DHW circ: short circuit
32 Sensor T.DHW circ: open circuit
64 Sensor T.DHW: short circuit
128 Sensor T.DHW: open circuit
256 Sensor T.cold water: short circuit
512 Sensor T.cold water: open circuit
1024 Sensor T.primary: short circuit
2048 Sensor T.primary: open circuit
4096 Pump fault
8192 Valve fault

18
For UVR67
In the expert level under "Ext. sensors", DL bus is specified as the source for
one of the inputs and the DL address of the FRISTAR3 controller is specified.
The required index according to the table on the previous page should be en-
tered underneath.

19
Electrical connection
Terminal S1: Cold water temperature sensor TKW
Terminal S2: Primary temperature sensor TPri
Terminal S3: Circulation temperature sensor TZirku
The polarity of the DL bus connections (DL and "Earth") is not interchangeable and must be observed.
Safety instructions
If you are connecting the FRISTAR3 to an electrical system via a residual current device (RCD), use
an RCD of type A which will detect pulsating direct currents and bears the following marking:
Checking using a high voltage insulation tester may cause damage to the pump and the control elec-
tronics.
Primary pump
Optional: Circulation pump
Fuse 3.15A
fast-acting
Temperature differential set-
ting for circulation pump
Valve terminal
PWMIN | PWMOUT | GND | +12V
DL address for
DIP switches
Volume flow sensor
connection
0°C 25°C

20
Operation of the controller and LED indicators
Operation of the controller has been kept as simple as possible, so that it can also be operated by
inexperienced users.
The temperature can only be selected on the FRISTAR3 controller if no set value has been issued by
a freely programmable controller (e.g. UVR16x2) via the DL bus.
Manual-automatic changeover switch
Status LED indicator
This LED indicates the functional status of the sensors.
Pump LED indicator
AUS (off) The pump is permanently off and the valve is closed.
AUTO Pump and valve operate as specified by the controller.
EIN (on) The pump runs permanently at full speed and the valve is fully open, regardless of
the control temperature.
green All sensors are working properly
red
Sensor for actual DHW temperature T WW (inside the flow rate sensor) defective
flashing red Primary pump defective
Flashing red/orange Valve defective
orange Sensor for inlet temperature TKW (in volume flow sensor) defective
flashing orange Sensor for primary temperature TPri defective
off Pump is switched off. If the "Pump" LED indicator is not lit up even though hot wa-
ter is being drawn off, either the volume flow sensor or the controller is defective.
green Primary pump is active
flashing green DHW circulation pump are active
Status LED
Pump LED
Manual/automatic switch
Temperature
selection
Table of contents
Other Technische Alternative Water System manuals
Popular Water System manuals by other brands

Thermo Scientific
Thermo Scientific PC200 manual
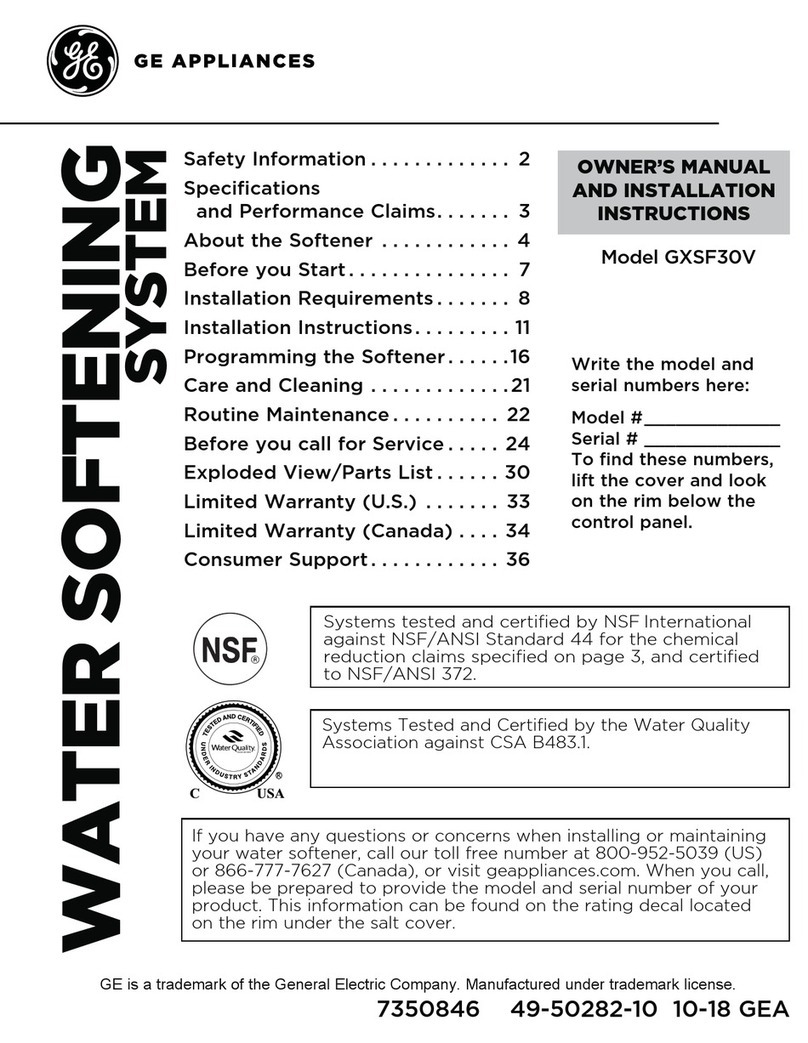
GE
GE GXSG30V Owner's manual and installation instructions
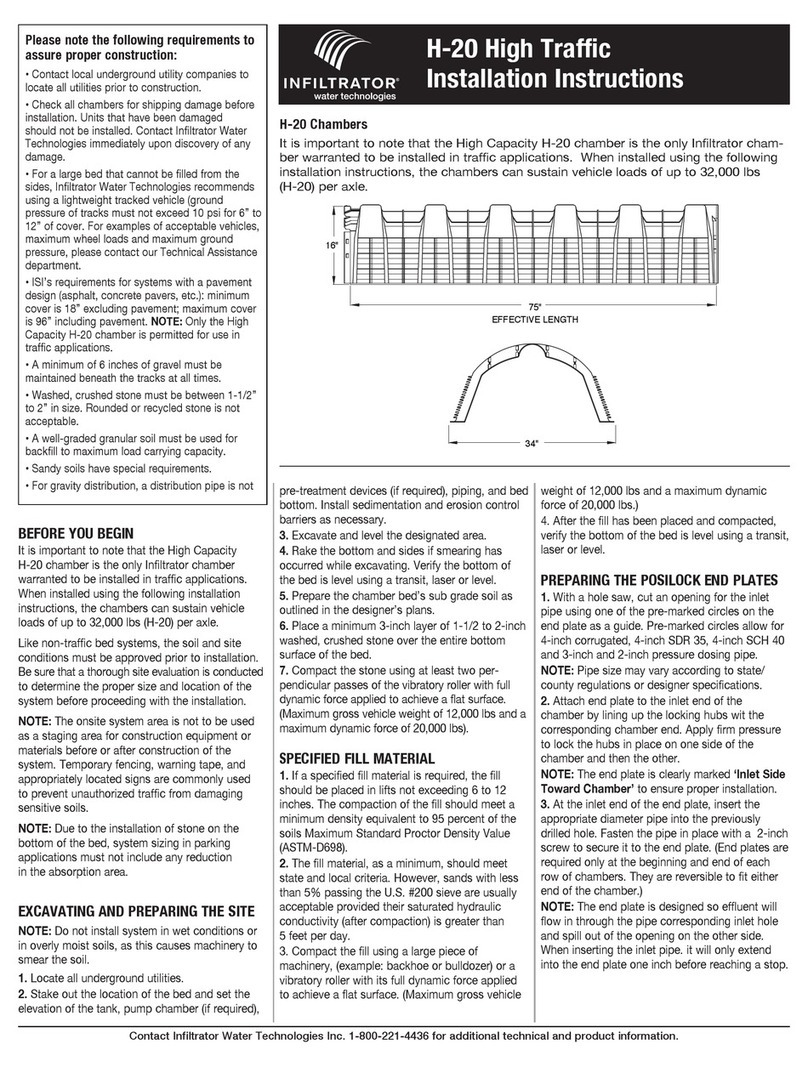
Infiltrator
Infiltrator H-20 installation instructions
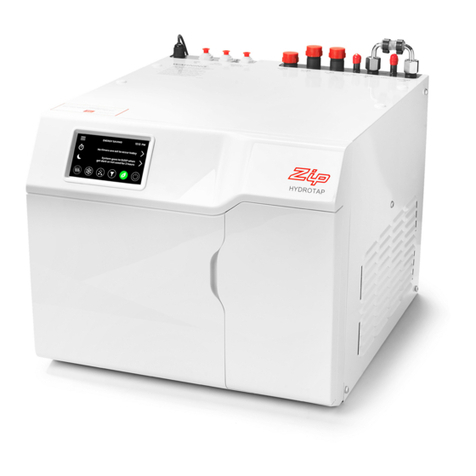
Zip
Zip HydroTap G5 Touch-Free Wave installation instructions
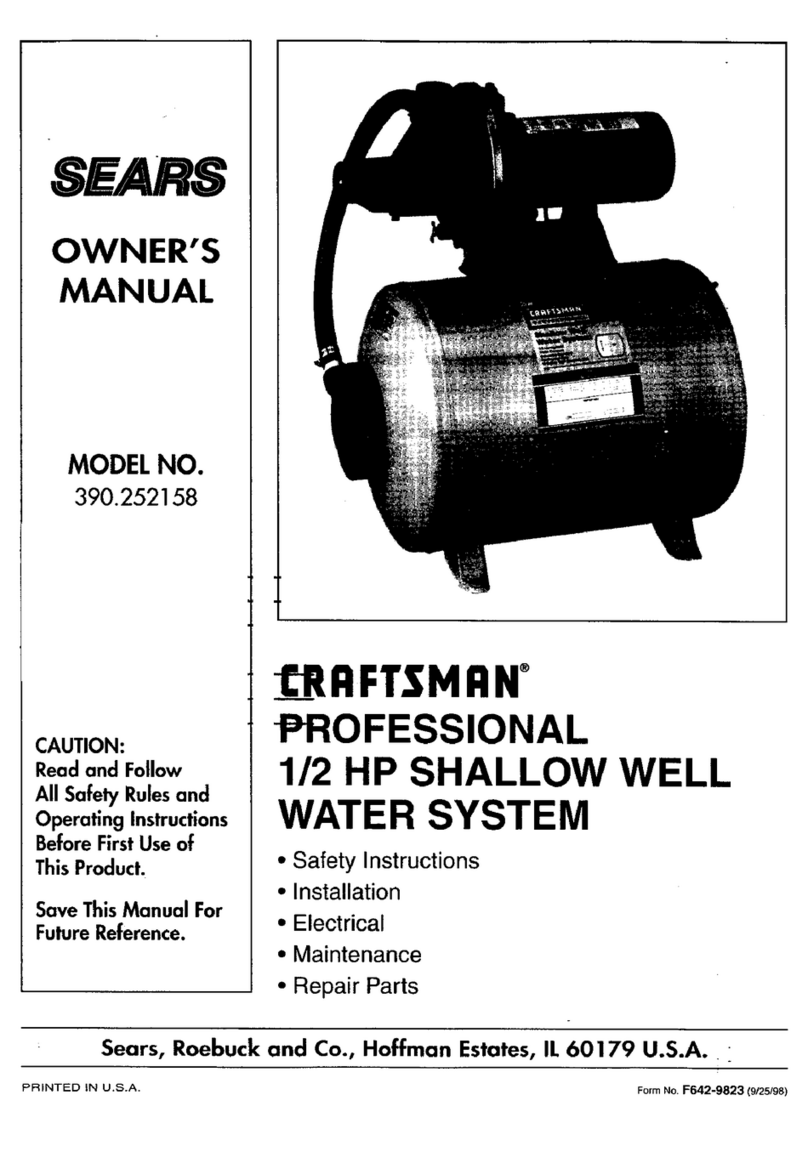
Craftsman
Craftsman 390.252158 owner's manual
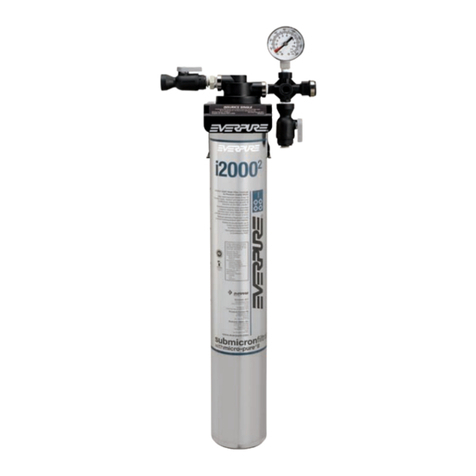
Everpure
Everpure Insurice Single-i20002 Specification sheet

Franklin Electric
Franklin Electric SubDrive300 installation manual

Ecosolar
Ecosolar Solar Hot Water System installation guide

Everpure
Everpure Helia Water Appliance EV9318-50 Specification sheet
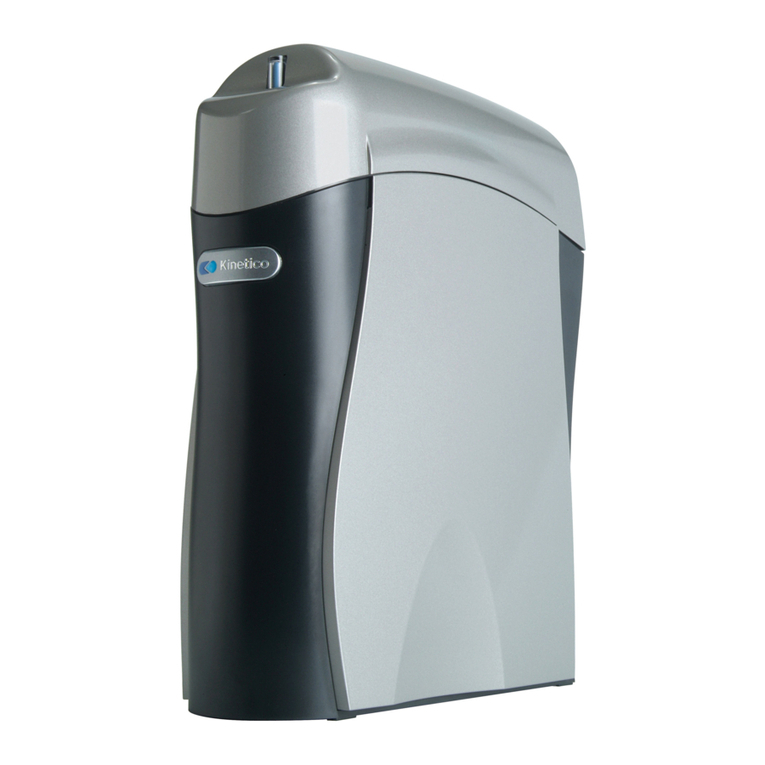
Kinetico
Kinetico K5 owner's manual

Hague
Hague WaterMax H3500 Owner's manual and installation guide

NEXT pool
NEXT pool STERILOR Duo Installation & user guide