Tektronix 7T11 User manual

Ibktronix-
COMMITTED TO EXCELLENCE
PLEASE CHECK FOR CHANGE INFORMATION
AT THE REAR OF THIS MANUAL.
7T11
SAMPLING
SWEEP UNIT
INSTRUCTION MANUAL
Tektronix, Inc.
P.O. Box 500
Beaverton, Oregon 97077 Serial Number
070-0986-00
Product Group 42
First Printing MAY 1970
Revised MAR 1985

Copyright ©1970 Tektronix, Inc. All rights reserved.
Contents of this publication may not be reproduced in any
form \without the written permission of Tektronix, Inc.
Products of Tektronix, Inc. and its subsidiaries are covered
by U.S. and foreign patents and/or pending patents.
TEKTRONIX, TEK, SCOPE-MOBILE, and 1^ are
registered trademarks of Tektronix, Inc. TELEQUIPMENT
is aregistered trademark of Tektronix U.K. Limited.
Printed in U.S.A. Specification and price change privileges
are reserved.
INSTRUMENT SERIAL NUMBERS
Each instrument has aserial number on apartel insert, tag,
or stamped on the chassis. The first number or letter
designates the country of manufacture. The last five digits
of the serial number are assigned sequentially and are
unique to each instrument. Those manufactured in the
United States have six unique digits. The country of
manufacture is identified as follows:
BOOOOOO Tektronix, Inc., Beaverton, Oregon, USA
100000 Tektronix Guernsey, Ltd., Channel Islands
200000 Tektronix United Kingdom, Ltd., London
300000 Sony/Tektronix, Japan
700000 Tektronix Holland, NV, Heerenveen,
The Netherlands

TABLE OF CONTENTS
Page
SECTION 1SPECIFICATION
General Information 1-1
Instrument Features 1-1
Electrical Characteristics 1-1
Mechanical Characteristics 1-4
SECTION 2OPERATING INSTRUCTIONS
General Information 2-1
Installing the 7T1 12-1
TIME/DIV Readout 2-2
Controls and Connectors 2-3
First-Time Operation 2-4
Setup Information 2-5
Adjusting SWEEP CAL 2-5
Observing aFastrise Pulse 2-6
Triggering Considerations 2-7
Trigger Rate 2-8
SWEEP RANGE Control 2-8
TIME/DIV Settings 2-9
TIME POSITION Control 2-9
SCAN Control 2-10
TRIG LEVEL and STABILITY Controls 2-10
Trigger Pushbutton Switches 2-11
PULSE OUT Connector 2-11
Use of Real Time Mode 2-1
1
Using the 7M1 1Delay Line 2-1
1
SECTIONS CIRCUIT DESCRIPTION
THEORY OF OPERATION
Real-Time Sampling Theory 3-1
General 3-1
Staircase Ramp 3-2
Lead Time 3-3
Samples/Division 3-3
Summary 3-3
Additional Real-Time Circuits 3-4
Controls Affecting Timing and Delay 3-5
Important Waveforms 3-6
Sequential Sampling Theory 3-9
Additional Circuits Required 3-9
Constructing The Display 3-1
1
Waveform Relationships 3-11
Factors Affecting Dot Density 3-13
Blanking Circuits 3-14
Unavoidable Delay 3-15

7T11
SECTION 4
ii
TABLE OF CONTENTS (cont)
Random Sampling Theory
Introduction
Random Block Diagram
Random Operation
Waveform Relationships
CIRCUIT ANALYSIS
Relationship to Vertical Unit
Triggering Circuits
Internal Triggering
External Triggering
Trigger Slope Amplifier
Trigger (X10) Amplifier
Schmitt Trigger
HF SYNC
Arming and Output Tunnel Diodes
Output Tunnel Diode Circuits
Real and Equivalent-Time Logic
Start Multivibrator
TTH Circuit
Horizontal Amplifier
Real-Time Multivibrator
Horizontal Memory
Output Amplifiers
Hold-off Multivibrator (HOMV)
Slewing Ramp
Strobe Drivers
Slow Ramp Generator
Slow Ramp Inverter and Time Position Amp
Dot Position Memory
Ratemeter
Ratemeter Start Correction Circuits
Timing Switches
Readout Logic
MAINTENANCE
Preventive Maintenance
Troubleshooting
Transistor and 1C Pin Arrangement
7T11 Troubleshooting Procedure
Soldering Techniques
Component Replacement
Circuit Boards
Pin Sockets and Connectors
Tunnel Diode CR28
Switch Replacement
Instrument Repackaging
Circuit Board Connections and Component
Locations
3-16
3-16
3-16
3-18
3-18
3-20
3-22
3-22
3-23
3-24
3-24
3-24
3-26
3-26
3-28
3-29
3-29
3-30
3-33
3-34
3-35
3-35
3-35
3-39
3-41
3-41
3-43
3-44
3-45
3-47
3-47
3-48
4-1
4-1
4-3
4-5
4-7
4-7
4-8
4-8
4-8
4-9
4-11
4-12 to 4-18

7T11
TABLE OF CONTENTS (cont)
SECTION 5PERFORMANCE CHECK/CALIBRATION
Introduction 5-1
Test Equipment Required 5-1
Short Form Procedure 5-2
Calibration and Pe'-formance Check 5-4
Adjust +10 Volts 5-7
Check Manual Scan and Adjust Sweep
Cal and Position 5-7
Timing Accuracy 5-7
Time Position Range 5-9
Adjust Timing 5-9
Adjust Random Timing 5-11
Adjust Trig Level 5-12
Adjust Stability 5-12
Adjust External Trigger Zero 5-13
Adjust HF Sync 5-13
Adjust Output Bias 5-14
Check Triggering 5-15
Check Display Jitter 5-16
Check Pulse Out into 50 5-19
Check Trigger Kickout 5-19
Trigger Holdoff 5-20
Strobe Kickback into Trigger 5-20
Minimum Trigger Rate in Random 5-21
Repetition Scan Rate 5-21
Sweep Out Range 5-21
External Input 5-21
SECTION 6ELECTRICAL PARTS LIST
Abbreviations and Symbols
Parts Ordering Information
Index of Electrical Parts List
Electrical Parts List
SECTION 7DIAGRAMS AND MECHANICAL PARTS ILLUSTRATIONS
Diagrams
Mechanical Parts Illustrations
Accessories
Repackaging Instructions
SECTION 8MECHANICAL PARTS LIST
Mechanical Parts List Information
Index of Mechanical Parts Illustrations
Mechanical Parts List
CHANGE INFORMATION
Abbreviations and symbols used in this manual are based on or
taken directly from IEEE Standard 260 "Standard Symbols for
Units", MIL-STD-12B and other standards of the electronics
industry. Change information, if any, is located at the rear of this
manual.
®iii

7T11

SECTION 1
SPECIFICA TION
7T11
Change information, if any, affecting this section will be found at the rear of the manual.
General Information
The 7T1 1Sampling unit is designed for use in Tektronix
7000-series oscilloscopes. Several plug-in combinations,
including a7T1 1, are shown in Fig. 1-2. A7S1 1must be in
the compartment to the left of, and adjacent to, the com-
partment in which the 7T11 is operated. Therefore, two
7T1 1's are not used in the same mainframe.
In Fig. 1-2A the 7T11 is shown in the "A" Horizontal
compartment of the oscilloscope. The Vertical Mode and
Horizontal Mode pushbuttons, providing useful presenta-
tions, are designated for plug-in configurations A, B, and C.
For the configuration of Fig. 1-2A, four combinations are
shown. Plug-in arrangements other than those shown in Fig.
1-2 are possible.
An alternate to the configuration shown in Fig. 1-2B is
with the "LEFT" or "B" or both of these mainframe com-
partments empty. The 7M11 may be used in any available
mainframe compartment or operated out of the mainframe.
For further information, see the Operating Instructions
section of this manual under the heading of General
Operating Information.
Instrument Features
The 7T11 features awide range of sweep rates using
real-time and equivalent-time sampling. Concentric switches
select the sweep range and time position range in different
combinations for the time/div desired. On equivalent time
ranges, either sequential or random sampling is available.
Use of random sampling permits display of the leading edge
of fast-rise input signals without the use of asignal delay
line (such as the 7M1 1) or apretrigger pulse from the signal
source.
Internal triggering, or any of three modes of external
triggering can be selected by using the front panel
pushbuttons. ASchmitt trigger circuit is used except
when HF SYNC is selected. With EXT 50 Cl input
selected, the Schmitt circuit provides jitter free triggering
from input trigger signals from DC to 1GHz. The display is
free of trigger jitter or double triggering, even at low trigger
repetition rates or when using asquare wave as the input
trigger signal. Arecovery time control is not needed.
Selecting EXT HF SYNC permits using frequencies of 1
GHz to approximately 12 GHz as the trigger input source.
With HF SYNC selected, the signal connected to the TRIG
INPUT connector is routed to abuilt-in synchronizer, thus
permitting Xband signals to be viewed.
Excellent sweep linearity is provided when using the
7T11. The timing circuitry in the 7T11 uses atime
measurement rather than atime programming process for
horizontal sample positioning on all equivalent-time sweep
ranges. During both random and Sequential operation the
horizontal position of the dot on the screen is determined
by measuring the time interval between strobe and trigger.
This method results in improved timing linearity and a
reduction in display jitter. The accuracy of sweep timing
and linearity make it unnecessary, during equivalent time
sampling, to exclude the sweep start from accuracy specifi-
cations.
Characteristics
The following characteristics apply over an ambient tem-
perature range of 0°C to -t50°C at altitudes up to 15,000
feet and after afive-minute warmup, providing the instru-
ment was calibrated at atemperature between -t20°C and
-H30°C. During non-operation, do not subject the 7T11 to
altitudes above 50,000 feet or to temperatures below
-55°C.
ELECTRICAL CHARACTERISTICS
Characteristic Performance Requirement
SWEEP RATES
TIME/DIV Calibrated from 5ms/div to 10
ps/div, selectable in a1, 2, 5se-
quence, using SWEEP RANGE and
TIME/DIV controls.
1-1

Specification—7T 1
1
ELECTRICAL CHARACTERISTICS (cont)
Characteristic Performance Requirement
SWEEP RATES (cont)
Equivalent Time 5Ms/div to 10 ps/div using the 50
JUS to 50 ns Time Position Ranges.
Accuracy Within 3%.
Real Time 5ms/div to .1 jus/div using the 50
ms to .5 ms Time Position Ranges.
ELECTRICAL CHARACTERISTICS (cont)
Characteristic Performance Requirement
SWEEP RATES (cont)
Accuracy
On 50 ms
TIME POS
RNG
Within 3%, beginning 250 /is after
undelayed sweep start.
On 5ms
TIME POS
RNG
Within 3%, beginning 25 /is after
undelayed sweep start.
Fig. 1-2. Several plug-in configurations using the 7T11 and a7000-series oscilloscope.
1-2

Specification—7T1
1
ELECTRICAL CHARACTERISTICS (cont)
Characteristic Performance Requirement
SWEEP RATES (cont)
On 0.5 ms
TIME POS
RNG
Within 3%, beginning 2.5, /ts after
undelayed sweep start, or after 500
ns from start of displayed portion
of sweep. Does not include 100 ns/
div and 200 ns/div positions.
VARIABLE
(TIME/DIV)
Range
Extends fastest sweep rate to at
least 4ps/div. Permits increasing
the speed of all sweep rates to at
least 2.5 times the calibrated speed.
TRIGGERING
Input Resistance
EXT 50 Q. 50 within 10%.
EXT 1Mn 1Mfi within 5%.
EXT HE SYNC 1Mf2 within 5%.
*Sinewave
Triggering
Internal
Sensitivity
Range
XI Trig
Amp 125 mV to 1VP-P at vertical in-
put (5 kHz to 500 MHz).
XIOTrig
Amp 12.5 mV to 1VP-P at vertical in-
put (5 kHz to 50 MHz).
*NOTE
Trigger circuits will operate to DC
with pulse triggering, except for HP
SYNC.
External
50 OInput
Sensitivity
Range
XI Trig
Amp’
12.5 mV to 2V(P-P), DC to 1GHz.
XIOTrig
Amp 1.25 mV to 2V(P-P), 1kHz to 50
MHz.
Safe
Overload
2V(DC +peak AC).
ELECTRICAL CHARACTERISTICS (cont)
Characteristic Performance Requirement
TRIGGERING (cont)
1M12 Input
Sensitivity
Range
XI Trig
Amp 12.5 mV to 2V(P-P), DC to 100
MHz.
XI 0Trig
Amp 1.25 mV to 2V(P-P), 1kHz to 50
MHz.
Safe
Overload
100 VDC or 100 V(P-P) to 1kHz;
derated 6dB/octave above 1kHz to
5V(P-P).
HP SYNC
Input
Sensitivity
Range
10 mV to 500 mV (peak-peak) at 1
GHz; 200 mV to 500 mV (peak-
peak) at 12.4 GHz.
Safe
Overload
2V(peak-peak).
Display Jitter
50 and 1Mf2
Triggering
Sequential Mode 10 ps or less at fastest SWEEP
RANGE position (fully CCW); 0.4
divisions or less at remaining six
positions of SWEEP RANGE;
measurements made under opti-
mum trigger conditions.
Random Mode 30 ps or less at fastest SWEEP
RANGE position (fully CCW); one
division or less at remaining six
positions of SWEEP RANGE;
measurements made under opti-
mum trigger conditions.
HP SYNC
Random or
Sequential
Mode
20 ps or less with a12.4 GHz, 200
mV (peak-peak) signal; measured
under optimum trigger conditions.
REV. B, SEPT. 1977 1-3

Specification—7T 1
1
ELECTRICAL CHARACTERISTICS (cont)
Characteristic Performance Requirement
TRIGGERING (cont)
PULSE OUT (into
50nj
Amplitude Positive-going pulse of at least 400
mV.
Risetime 2.5 ns or less.
Trigger Kickout ±2 mV or less into 50 H(except
HF SYNC).
Minimum Trigger
Rate in RANDOM
Mode
100 Hz.
SLOW RAMP GENERATOR
Scan Rate
REPETITIVE
SCAN Continuously variable from less
than 2sweeps/sec to at least 40
sweeps/sec.
HORIZONTAL DEFLECTION SYSTEM
Deflection Factor
SWEEP CAL Permits adjustment of deflection
factor for all 7000-series main-
frames.
ELECTRICAL CHARACTERISTICS (cont)
Characteristic Performance Requirement
HORIZONTAL DEFLECTION SYSTEM (cont)
EXTERNAL INPUT
Input Resistance 100 kl2 within 10%.
Deflection Factor Continuously variable from 10 Vto
1V/div.
Maximum Input
Voltage
100 V(DC -t- peak AC).
SWEEP OUT -tS Vto -5 V
MECHANICAL CHARACTERISTICS
Dimensions
Height «^5 inches.
Width s»2% inches.
Length (including
front panel knobs
and rear connector)
^^4V2 inches.
Construction Aluminum alloy chassis with epoxy
laminated circuit boards. Front
panel is anodized aluminum.
Accessories An illustrated list of the accessories
supplied with the 7T11 is at the
end of the Mechanical Parts List
pullout pages.
1-4 @1

SECTION 2
OPERATING INSTRUCTIONS
7T11
Change information, if any, affecting this section will be found at the rear of the manual.
General Information
This section covers installation, first time operation,
function of front panel controls and connectors, and
general operation of the 7T1 1Sampling Sweep Unit.
The 7T11 is intended for use in the Tektronix 7000-
series oscilloscopes. Use of the 7T11 with a7S11 Sampling
Unit and any of avariety of S-series Sampling Heads
provides asampling system adaptable to awide range of
applications.
Real-time sampling is provided at the three slowest
sweep rate settings of the 7T11 Sweep Range switch.
Sampling is in equivalent-time for the remaining four posi-
tions of the Sweep Range switch. On these four ranges
either sequential or random equivalent-time sampling may
be selected.
WttV»VtV*V»V»V«VAV ••• ••4
Fig. 2-1. Connector J641 (fixed shoe), providing interconnection
between 7T 11 and 7S11 for strobe and trigger signals.
The 7T11 sweep may be synchronized using an internal
or external triggering source. External signals from DC up
to approximately 12 GHz can be used as the trigger source.
Atrigger amplifier providing X10 amplification is available.
NOTE
Internal trigger signals are not routed through the
trigger source switches on the oscilloscope due to the
frequencies involved and noise considerations. Selec-
tion of the trigger source is made on the front panel
of the plug-ins.
Triggering signals travel between plug-in units along 50
El coaxial or strip lines. These signals travel between plug-in
units using contacts on connector strips fastened to the
sides of the plug-ins. Aconnector strip is shown in the
photograph of Fig. 2-1. Since the strobe pulses also travel
between a7T1 1and a7S1 1plug-in through contacts on the
connector strips, these units must be located in adjacent
oscilloscope compartments.
Installing the Type 7T1 1in the Oscilloscope
The 7T11 is designed to drive the horizontal deflection
plates of the oscilloscope CRT, and therefore is installed in
the right-hand compartment of the oscilloscope. When only
one Type 7T11 and one 7S11 are used in a7000-series
oscilloscope providing two vertical and two horizontal com-
partments, the 7T11 is inserted in the left-hand horizontal
compartment and the 7S1 1in the right-hand vertical com-
partment. This provides an interconnecting path between
the 7T1 1and the 7S1 1for strobe and trigger signals.
To insert the 7T11 into the oscilloscope compartment,
align the grooves along the top and bottom of the plug-in
with the upper and lower slide rails in the oscilloscope com-
partment. The unit slides straight in and self-locks itself in
place. The plug-in is removed by pulling straight out on the
plastic button labeled 7T11.
Mating the 7T1 1to the Oscilloscope
The 7T11 horizontal gain must be matched to the hori-
zontal deflection factor of the CRT in the oscilloscope.
Horizontal gain is set using the Sweep Cal control (screw-
driver adjustment) located on the 7T11 front panel. A
d) 2-1

Operating lnstructions-7T1
1
method of adjusting the Sweep Cal is discussed in the First
Time Operation Procedure later in this section. This adjust-
ment must be reset each time the 7T11 is transferred be-
tween oscilloscopes, and when aconsiderable change in
ambient temperature occurs.
TIME/DIV Readout
The 7T11 TIME/DIV setting selected is displayed near
the top of the CRT except when the 7T11 is used in a
oscilloscope without readout circuitry. The horizontal posi-
tion of the readout on the CRT corresponds to the horizon-
tal position of the oscilloscope compartment in use.
The TIME/DIV selected at the 7T11 front panel is dis-
played on the CRT using the digits 1, 2, or 5followed by
one or two zeros if required. The TIME/DIV readout does
not use decimal points. The displayed digits are followed by
the units-of-measure readout. With the 7T11 the units-of-
measure displayed will be ms/div, jUs/div, ns/div or ps/div. If
the VARIABLE (CAL IN) switch is in the out position the
symbol used to indicate less than «), is displayed pre-
ceding the TIME/DIV readout as awarning that the display
is uncalibrated. The intensity of the readout is independ-
ently adjustable by afront panel control on the oscillo-
scope, which also permits the readout to be switched off.
FINE
TIME POSITION
SWEEP CAE
TRIG
INPUTSWEEP
TRIG LEVEL
RANDOM
m
SEQUENTIAL ETRIG AMP
11H'xi
smoN <!•
POSITION <
E®;:. ^
VARIABLE (CAL IN)
TIME/DIV
time sweep range
P""
R
Fig. 2-2. 7T11 front panel.
®I
2-2

Operating Instructions—7T1
1
FRONT PANEL CONTROLS AND
CONNECTORS
All controls required for operation of the 7T11 are
located on the front panel of the unit (see Fig. 2-2).
Controls, pushbuttons, and connectors associated with trig-
gering are located along the right side of the front panel and
are included in an area outlined in green. The SCAN con-
trol, pushbuttons, and an external input connector are in a
grey outlined area at the lower left of the panel. The
remainder of the front panel contains Sweep circuit con-
trols, switches, and adjustments.
Abrief description of the function or operation of the
front panel controls follows. More detailed information is
given under General Operating Information.
SWEEP Controls and Connectors
TIME POSITION and Two concentric controls providing
FINE controls coarse or fine control of the time
relationship between triggering and
the start of the CRT display. The
TIME POSITION control permits
continuously variable adjustment of
delay in starting the display, up to
the amount indicated in the TIME
POS RNG window. The FINE con-
trol has only about 1% of the effect
of the TIME POSITION control,
and is particularly useful at TIME/
DIV settings of high magnification.
RANDOM Selects Random Sampling mode of
Pushbutton operation. Does not function in the
three slowest (real-time) Sweep
Ranges. Permits the display of the
input signal prior to the triggering
point without use of adelay line or
pretrigger.
SEQUENTIAL
Pushbutton
SWEEP RANGE
Switch
Selects Sequential Sampling mode
of operation. Does not function in
the three slowest (real-time) Sweep
Ranges. Permits equivalent-time
operation at lower trigger repe-
tition rates than does the Random
mode.
Selects the range of operation of
the TIME/DIV switch and indicates
the corresponding time position
range (TIME POS RNG). Permits a
choice of any of nine TIME/DIV
settings at each of the seven posi-
tions of the SWEEP RANGE
SWITCH. The SWEEP RANGE con-
TIME/DIV
Switch
VARIABLE (CAL
IN) Control
TIME POS RNG
SWEEP CAL
Control
POSITION
Control
SWEEP OUT
Jack
SCAN Controls
Variable SCAN
Control
REP Pushbutton
@
trol is concentric with the TIME/
DIV and VAR (CAL IN) controls.
Selects calibrated time/division set-
tings from 10 ps/div to 5ms/div, in
27 steps, in a1, 2, 5sequence.
When in the out position, rotating
the VARIABLE control permits
changing time per division from the
calibrated value selected by the
TIME/DIV switch. Push knob in
and release to activate; the knob
moves outward from the TIME/
DIV control when activated.
Time-positioning ranges from 50 ns
to 50 ms in seven decades are avail-
able. Time-positioning range avail-
able and indicated in the TIME POS
RNG window is determined by the
setting of the SWEEP RANGE
switch. The indicated range is
always ten times the slowest time/
div of the Sweep Range selected.
Afront panel screwdriver adjust-
ment that adjusts horizontal gain to
match the oscilloscope deflection
factor. Adjusted when switching
7T11 from one oscilloscope to
another.
Afront panel screwdriver adjust-
ment to position the display hori-
zontally on the CRT of the oscillo-
scope.
Pin jack providing an output volt-
age proportional to the display.
With an output resistance of 10 kST
an output of one volt for each divi-
sion of display is provided.
Provides an internal voltage for
adjusting the scan rate in the REP
mode, or for manually scanning the
display in the MAN mode. Also
used to set the horizontal gain using
the SWEEP CAL control. Serves as
avariable attenuator in the
EXTERNAL INPUT mode.
Provides repetitive scanning of the
display. Scan rate is adjusted using
the variable SCAN control. It does
2-3

Operating Instructions—7T1
1
REP Pushbutton
(cont)
MAN Pushbutton
EXT INPUT
Pushbutton
External Input
Jack
Triggering Controls
SLOPE (+), (-)
Pushbuttons
TRIG LEVEL
Control
STABILITY
Control
TRIG AMP
Pushbuttons
INT Pushbutton
EXT 50 a
Pushbutton
EXT 1MQ,
Pushbutton
EXT HE SYNC
Pushbutton
not function in the three slowest
(real-time) Sweep Ranges.
Provides manual operation of the
scan function using the variable
SCAN control. Does not function
in the three slowest (real-time)
Sweep Ranges.
Allows scanning the display using
an external signal. In this mode of
operation, the variable SCAN con-
trol serves asavariable attenuator.
Apin jack (input resistance of 100
kL2) providing an input facility for
externally scanning the display.
With the SCAN control fully CW a
one volt input is needed for each
division of display.
Selects the positive-going (-t) or
negative-going (—)slope of the trig-
gering signal.
Determines the amplitude level on
the triggering waveform where trig-
gering is to occur. Also serves as a
fine synchronizing adjustment in
the HE SYNC mode. The TRIG
LEVEL control is concentric with
the STABILITY control.
Adjusts the width of the trigger
hysteresis. Also serves as acoarse
sync adjustment in the HE SYNC
mode.
Select XI or X10 amplification of
the trigger signal.
Selects internal triggering for opera-
tion with sampling heads that pro-
vide atrigger pickoff.
Selects external, DC-coupled, low-
impedance trigger operation at the
common trigger input connector.
Selects external, DC-coupled, high-
impedance trigger operation at the
common trigger input connector.
Selects external, AC-coupled (1 MJ2
to ground) HE SYNC operation. In
this mode of trigger operation, the
STABILITY and TRIG LEVEL
controls are used to obtain astable
display with trigger signals above
approximately 1GHz.
EXT TRIG INPUT A3mm connector located near the
Connector lower right portion of the front
panel and used for introducing an
external triggering signal to the
7T11.
PULSE OUT ABSM connector providing a posi-
Connector tive pulse corresponding to the
firing of the trigger circuit.
FIRST-TIME OPERATION
General
When shipped from the factory, the 7T11 Sampling
Sweep Unit has been calibrated to meet the specifications
listed in Section 1and is ready to be used with aTektronix
7000-series oscilloscope.
The following steps demonstrate the basic operation of
the controls of the 7T1 1. It is recommended that this pro-
cedure be followed completely for familiarization with the
instrument. Operation of the oscilloscope and vertical plug-
in unit (Sampling Unit) is described in the instruction
manuals for these units. The equipment set-up used during
the following procedure is shown in Pig. 2-3.
Fig. 2-3. Equipment setup used during first time operation.
@
2-4

Operating Instructions—7T1
1
Setup Information 7T11 (cont)
1.
Insert a7S11 Sampling Unit with aType S-2
Sampling Head in the left vertical compartment of the 7504
oscilloscope.
NOTE
Any Tektronix 7000-series osciiioscope may be sub-
stituted for the 7504. Oniy the piug-ins iisted in steps
2and 3are actuaiiy needed to perform this First-
Time Operation but the use of Piug-ins iisted in steps
1and 4is iiiustrated iater in this section under the
heading of Generai Operating information.
2.
Insert a7S11 Sampling Unit with aType S-1
Sampling Head in the right vertical compartment of the
oscilloscope.
3.
Insert a7T11 Sampling Sweep Unit in the "A" hori-
zontal plug-in compartment.
REP pushbutton
STABILITY control
TRIG LEVEL control
SLOPE pushbutton
TRIG AMP pushbutton
EXT 50 ^2 triggering
pushbutton
Pushed in
Fully CCW
Midposition
(-I-) pushed in
X10 pushed in
Pushed in
Type 284
Square Wave Amplitude
Period
Mode
Lead Time
1.0 Vposition
1ps
Square Wave or Sine
Wave Output
75 ns
NOTE
Type 284 instruments having seriai numbers prior to
SN B030236 require instaiiation of Fieid Modifica-
tion Kit, Tektronix Part No. 040-0487-01 in order to
obtain a75 ns trigger iead time.
4.
Insert a7M11 50 El Delay Line in the Bhorizontal
compartment. This plug-in may be used on the bench along-
side of the oscilloscope instead of in the plug-in compart-
ment since the only connections required are to the 7M11
front panel.
Turn on power and allow the equipment to warmup for
5minutes. Connect a50 coaxial' cable having a5ns
signal delay and GR874 connectors between the Type 284
Square Wave or Sine Wave Output connector and the input
connector of the Type S-1 Sampling Head.
5. Set the controls as follows:
7504
Right
A
Midposition
High
Fully CCW
7S11
Pushed in
Midposition
200
Pushed in
7T11
TIME POSITION controls
SEQUENTIAL pushbutton
TIME POS RNG
TIME/DIV
VARIABLE (CAL IN)
control
SCAN control
Fully clockwise
Pushed in
5 MS
.5 Ms/Div
(500 ns readout)
Pushed in
Midposition
Vertical Mode
Horizontal Mode
Readout
Control Ilium
Intensity
+UP pushbutton
DC Offset control
mVolt/Div switch
Normal pushbutton
Connect the Trigger Output connector of the Type 284
to the 7T11 TRIG INPUT connector through a50
coaxial cable with a2ns signal delay and BNC connectors.
A3mm male to BNC adapter (Tektronix Part No.
015-1018-00), included as astandard accessory with the
7T11, must be connected to the 3mm TRIG INPUT con-
nector on the 7T1 1
.
Adjust the Focus, Intensity, and DC Offset controls for
adisplay similar to that shown in Fig. 2-4. Rotate the
SCAN control slowly from one extreme to the other and
note that clockwise rotation increases the scan rate and
reduces the dot density. Return the SCAN control to its
midposition. Push in and release the VARIABLE (CAL IN)
control and note that the less-than symbol (<) is displayed
on the CRT just to the left of the 500 ns readout. Rotate
the VARIABLE control from its fully CCW position and
note that clockwise rotation results in an increasing magni-
fication of the display or areduction in actual time per
division. Return the VARIABLE control to its fully CCW
position and push it into the CAL position.
Adjusting SWEEP CAL
Push the MAN SCAN pushbutton in and observe that
the pushbutton lights. Turn the SCAN control fully
REV. B.SEPT. 1977 2-5

Operating Instructions—7T1
1
Fig. 2-4. Sequential equivalent-time sampling display of 1jus, 1 V
square-wave output of the Type 284.
during Sequential equivalent-time sampling. These methods
provide ameans of getting the trace started before the verti-
cal signal reaches the CRT vertical deflection plates. These
methods are as follows;
(a) The path of the vertical signal that must travel from
the signal source to the Sampling Head input can be
lengthened while the distance traveled by the triggering
signal is kept as short as possible. This method, using a
7IVI11 50 Delay Line, is discussed later in this section
under the heading of General Operating Information.
(b) The method used during First-Time Operation is to
use asignal source, such as the Type 284, that provides a
signal for triggering slightly before it delivers an output
pulse to the Sampling Head input. Apretrigger Lead Time
of either 5ns or 75 ns can be selected at the Type 284
front panel.
counterclockwise. Aspot should be observed at the left
edge of the graticule. Rotate the SCAN control to its fully
CW position. The spot should have moved exactly ten divi-
sions to the right of its previous position. Use asmall screw-
driver to adjust the SWEEP CAL on the 7T11 front panel
for ten divisions of movement when the SCAN control is
turned from one extreme to the other. This adjustment
should be made whenever the plug-in is switched to a
different oscilloscope. This adjustment should be checked
occasionally even if the plug-in remains with the same
oscilloscope.
The POSITION control on the 7T11 front panel is
adjusted with ascrewdriver so the spot appears at the left
graticule edge with the SCAN control fully CCW. Return
the SCAN to repetitive by pushing the REP pushbutton and
set the SCAN control it its approximate midposition.
Observing aFast-Rise Pulse
One method of observing the leading edge of afast-rise
pulse is to use aslow enough sweep so that the pulse fol-
lowing the one producing triggering is displayed. Either
Internal or External triggering can be used. By using the
TIME POSITION control to move the displayed pulse near
to the left graticule edge and turning the TIME/DIV switch
clockwise to asetting providing high magnification, satis-
factory results can be obtained if the input signal has the
proper characteristics. The input signal repetition rate must
be constant; otherwise jitter or ameaningless display will
result. Also, if the interval between pulses is excessively
long compared to the time interval of interest, asuitable
combination of TIME POS RNG and TIME/DIV will be
unattainable.
Two other methods of seeing before the triggering point,
without the limitations of the method above, are available
Change the settings on the following controls:
Type 284
Mode switch PULSE OUTPUT
7S11
mV/Div 50mV/Div
TIME POS RNG
TIME/DIV
7T11
50 ns
5ns
Disconnect the coaxial cable from the Type 284 Square
Wave or Sine Wave Output connector and reconnect it to
the Type 284 Pulse Output connector. Check that the read-
out displayed on the CRT is 5ns, and that the Type 284
Lead Time switch is set to the 75 ns position. Vertically
center the display using the 7S1 1DC Offset control.
With the TIME POSITION controls fully CW the leading
edge of the output pulse of the Type 284 should be visible
as shown in the typical display of Fig. 2-5A. Fig. 2-5A
shows that although the Type 284 is supplying atrigger 75
ns before the Pulse Output signal, the signal is displayed
only 7or 8ns after the trace starts. If the 3ns difference in
travel time through the coaxial cables delivering the vertical
input and trigger input signals is considered, the actual
effective trigger lead time is approximately 78 ns. In Fig.
2-5A the lead time is only 7 or 8ns more than the mini-
mum required to display the input signal leading edge. The
location of the pulse in Fig. 2-5A is typical. Factors that
will affect the horizontal position, of the pulse leading edge
with respect to the start of the sweep are: slight differences
in the Lead Time provided by different Type 284's, differ-
2-6

Operating Instructions—7T1
1
(A) Typical display with TIME POSITION fully CW and 75
ns of pretrigger.
(B) Effect on display of Fig. 2-5A of CCW movement of
TIME POSITION control.
(C) Same set-up as Fig. 2-5B except for addition of 5ns
length of coax to vertical signal path.
Fig. 2-5. Observing the leading edge of afastrise pulse using the
SEQUENTIAL equivalent-time mode.
ences in the delay within different 7T11's, and the setting
of the TRIG LEVEL control.
Rotate the TIME POSITION and FINE controls slowly
CCW and notice that they increase delay and thereby cause
the displayed pulse to move to the left. Using the TIME
POSITION controls, set the pulse leading edge one division
from the left edge of the graticule as shown in Fig. 2-5B.
Disconnect the coaxial cable from the input of the Type
S-1 Sampling Head and insert an additional 5ns length of
coaxial cable between the cable just disconnected and the
Sampling Head input. The additional 5ns of delay inserted
in the path of the input signal will cause the pulse to move
one division (5 ns) to the right as shown in Fig. 2-5C. This
provides ameans of providing additional lead time and also
ameans of determining the delay caused by alength of
cable.
Turn the TIME/DIV switch to the .2 ns/Div position
(200 ps readout on CRT) and use the TIME POSITION
control to horizontally position the pulse leading edge to
graticule center. Note that the FINE control has more
effect in moving the display as the TIME/DIV control is set
to its more clockwise positions.
Specified risetime of the Type S-1 «350 ps) is too slow
to accurately measure the Type 284 output pulse risetime
«70 ps). If this risetime measurement is desired, use a
Type S-4 Sampling Head which has arisetime of less than
25 ps. Consult the instruction manual for this sampling
head for more information on measuring fast-rise signals.
Turn the oscilloscope Intensity control fully counter-
clockwise and push in the HF SYNC pushbutton. The HF
SYNC pushbutton will light and the X10 TRIG AMP and
(+) SLOPE lights will go out. When using HF SYNC, the
triggering slope and the TRIG AMP controls have no effect.
Rotate the SWEEP RANGE control fully CW to where
the TIME POS RNG window shows 50 ms. Real-Time
sampling is provided at this setting of the SWEEP RANGE
control as well as at the next two faster SWEEP RANGE
settings. The SEQ or RANDOM pushbuttons will not light
on these three Real-Time ranges. The SCAN controls are
also inoperative on Real-Time ranges and these pushbuttons
will not light.
GENERAL OPERATING INFORMATION
Triggering Considerations
When using Sequential equivalent-time sampling to
observe afast risetime pulse, apretrigger or external delay
2-7

Operating Instructions—7T1
1
line is normally required. Use of a7M11 Delay Line is
discussed later in this section.
Internal triggering or any one of three modes of External
triggering can be selected by using four pushbuttons on the
7T1 1front panel. Triggering signals are not routed through
the pushbuttons. The front panel pushbuttons control reed
relays located in the 50 Qpath provided for triggering
signals. (Triggering controls on the oscilloscope mainframe
have no controlling effect.) This triggering system reduces
pickup of unwanted noise and loss of high frequency com-
ponents of the trigger signals.
Internal triggering of the 7T1 1from the signal applied to
either vertical channel is available. Pushing in the INT push-
button on the 7T1 1will cause this button to light. The INT
pushbutton lights on the 7S11 that is supplying the trig-
gering signal.
Triggering Rate
Triggering rate is limited by holdoff. The minimum trig-
ger holdoff time at each of the seven available time posi-
tioning ranges (indicated in the TIME POS RNG window) is
shown in Table 2-1. The TIME POS RNG is determined by
the setting of the SWEEP RANGE control.
TABLE 2-1
Minimum Trigger Holdoff
Indication in
TIME POS RNG
window
Minimum Trigger
Holdoff Time
RT
EI
AM
LE
50 ms at least 2ms
5ms at least 2ms
500 MS at least 2ms
-I
>
50 MS at least 220 ms
5MS at least 25 ms
500 ns at least 25 ms
50 ns at least 25 ms
The maximum rate at which triggers can be recognized is
the reciprocal of the minimum trigger holdoff time shown
in Table 2-1. In Real-Time operation, delay introduced
using the TIME POSITION controls and the duration of the
time window (ten times the TIME/DIV setting) must be
added to the minimum values shown in Table 2-1. The
Sweep Range providing the greatest time-positioning range
and the slowest real-time sweep can therefore cause the
greatest variation from the minimum holdoff time shown in
Table 2-1.
In Random mode the triggering point, Tq, is displayed
close to the center line of the CRT with the Time Position
control fully CW and the Time/Div switch fully CCW. The
lowest allowable triggering rate for the 7T11 in Random
mode is 100 Hz; this applies to all equivalent-time Sweep
Ranges. The lowest usable triggering rate for any particular
Time/Div setting depends on the minimum dot density that
the operator is willing to use. In Random mode, the
sampling event referenced to aparticular trigger is timed
from the preceding trigger. If the trigger rate is high and
uniform, then the sampling event prediction is more
accurate and the samples occur where they are programmed
to occur. As the rate goes down, the ability to predict when
the next trigger will occur diminishes, and the samples
begin to happen in amore random fashion. When the trig-
ger rate slows (or the period jitter increases) sufficiently,
the predictability is reduced to the point where the
sampling distribution fails over the whole screen. In this
case, best dot density is obtained by selecting MAN SCAN
and placing the center of the dot distribution at mid-screen.
SWEEP RANGE Control
Sweep rate of the display is controlled by three con-
centric knobs. The outer, larger knob (SWEEP RANGE
control) controls the sweep range over which the TIME/
DIV knob may be switched. The window on the left of the
TIME/DIV knob displays the TIME POS RNG (time posi-
tioning range); this number is always 10 times the slowest
available TIME/DIV of aparticular SWEEP RANGE setting.
The selected TIME/DIV is displayed on the CRT by the
oscilloscope if the oscilloscope is provided with readout
capability. The VARIABLE control can provide aminimum
of 2.5 to 1magnification at any TIME/DIV setting. At the
three slowest SWEEP RANGE settings, sampling is in Real-
Time while the remaining four positions provide equivalent-
time (random or sequential) sampling.
The TIME/DIV settings available at each position of the
SWEEP RANGE control are shown in Table 2-2. Turning
the SWEEP RANGE control fully CW selects the slowest
setting of the SWEEP RANGE control. Thus the fully CW
position has been designated as SWEEP RANGE position 1
in Table 2-2. Reading horizontally to the right from the
fully CW (designated as position 1in Table 2-2) SWEEP
RANGE position shows, under the TIME POS RNG
column, avalue of 50 ms. Continuing to the right shows
that nine TIME/DIV settings, from 5ms/div at XI magnifi-
cation to 10 /is/div at X500 magnification, are available. As
the SWEEP RANGE control is rotated CCW increasingly
faster Sweep Ranges are selected.
It should be noted that the nine TIME/DIV settings
available at each of the seven positions of the SWEEP
2-8

Operating Instructions—7T1
1
TABLE 2-2
Sweep Range |
Position
TIME POS RNG
T
CCW TIME/DIV CW
and Magnification
XI X2.5 X5 X10 X25 X50 X100 X250 X500
RT
E1
AM
L E
Fully CW 150 ms 5ms 2ms 1ms .5 ms .2 ms .1 ms 50 ys 20 ys 10 ys
25ms .5 ms .2 ms .1 ms 50 ys 20 ys 10 ys 5ys 2ys 1ys
3.5 ms 50 ys 20 ys 10 ys 5ys 2ys 1ys .5 ys .2 ys .1 ys
VM
iE
450 ys 5ys 2ys 1ys .5 ys .2 ys .1 ys 50 ns 20 ns 10 ns
55ys .5 ys .2 ys .1 ys 50 ns 20 ns 10 ns 5ns 2ns 1ns
6.5 ys 50 ns 20 ns 10 ns 5ns 2ns 1ns .5 ns .2 ns .1 ns
Fully CCW 750 ns 5ns 2ns 1ns .5 ns .2 ns .1 ns 50 ps 20 ps 10 ps
RANGE control provide atotal of 63 combinations. Only
27 different TIME/D IV settings are available, however,
since most TIME/DIV settings are available at two or three
settings of the SWEEP RANGE control. For example,
TIME/DIV settings of 50 ps, 20 ps and 10 ps are shown in
Table 2-2 to be available at all three Real-Time positions of
the SWEEP RANGE control. If aTIME/DIV setting of 20
As/div is required, any of the three Real-Time Sweep
Ranges can be used; however, more time-positioning range
(TIME POS RNG) is provided at the slower SWEEP
RANGE settings.
TIME/DIV Settings
Atotal of 27 different sweep rates are available ranging
from 5ms/div to 10 ps/div in a5, 2, 1sequence (see Table
2-2). On the slowest SWEEP RANGE position atotal of
nine TIME/DIV settings (5 ms/div to 10 /is/div) are avail-
able. Each of the six other positions of the SWEEP RANGE
also offer achoice of nine TIME/DIV settings.
The nine TIME/DIV control settings determine the
amount of display magnification. See Fig. 2-6. On all Sweep
Ranges the display magnification changes from XI to X500
in a1, 2.5, 5sequence as the selected TIME/DIV setting is
changed from the slowest available rate to the fastest.
TIME POSITION Control
The TIME POSITION control permits delaying the dis-
play or time window start by an amount up to the value
indicated in the TIME POS RNG window. Delay introduced
by this control is removed by turning the control fully
clockwise. The FINE control serves the same purpose but
has only about 1% as much effect as the TIME POSITION
control.
Fig. 2-6. Magnification depends upon the position, within the con-
trol window, of the selected TIME/DIV setting.
Fig. 2-7A and 2-7B show that the duration of the display
or time window is ten times the selected TIME/DIV setting.
At the SWEEP RANGE setting specified in Fig. 2-7 the
TIME POS RNG (time positioning range) is 50 /us. During
SEQUENTIAL operation and with the TIME POSITION
control fully CW (clockwise) the start of the display or time
window occurs just after trigger recognition (time Tq).
During RANDOM equivalent-time sampling alead-time
of approximately 1/2 TPR (time-positioning range) is pro-
vided. Trigger recognition (Tq) will therefore occur at
about 25 IIS with the SWEEP RANGE setting represented in
Fig. 2-7. During Random sampling the 50 jus of time-

Operating Instructions—7T1
1
Display Window
TIME POSITION
fully CW
Display Window
TIME POSITION
fully CCW
‘l
1
50 iis time
1
1
1
range >1
1
Tcpn ^
Tq random
\J---_
1
1
1
010 20 30 '40 50 6*0 '7*0 *8*0 90
lA) TIME/DIV set at 5ms position (XI magnification) time (ms)
Display Window TIME
POSITION fully CW Display Window TIME
POSITION fully CCW
f^
450 MS time
r^
1
1
1
1
1
range
.1
Tq random 1
•
TqSEO —
^
C10 20 30 40 50 60 70 80 90 100
(B) TIME/DIV set at 1ns position (X5 magnification) time (ms) ^
Fig. 2-7. Effect of TIME POSITION control (SWEEP RANGE at 5/is/div to 10 ns/div position).
positioning range shown in Fig. 2-7B permits seeing from
25 jus before Tq to 35 ns after Tq.
The TIME POSITION control also works during Real-
Time operation. The smaller the delay from Tq the brighter
the display.
SCAN Control
During Real-Time operation the SCAN control and push-
buttons are inoperative and the pushbutton lights go out.
The SCAN control serves three functions, selected by
the pushbuttons. Pushing in the REP pushbutton results in
afree-running sweep, the scan rate increasing with CW
rotation of the SCAN control. Selecting MAN gives asingle
point of time on the screen, or centers the distribution of
samples around apoint on the screen. This control also
provides ameans of setting the SWEEP CAL adjustment for
10 centimeters of scan using abuilt-in zener diode as a
voltage reference. EXT input allows the 7T11 to be driven
from other sweep sources, with the SCAN control acting as
an attenuator. Single Sweep operation has not been pro-
vided, but is possible by EXT INPUT drive from aReal-
Time Sweep plug-in.
As mentioned above, turning the SCAN control clock-
wise increases the scan rate. At faster scan rates the hori-
zontal spacing between dots is increased. Fewer samples per
scan are taken, resulting in adecrease in dot density.
Counterclockwise rotation of the SCAN control has the
opposite effect; scan rate decreases and dot density is
increased.
TRIG LEVEL and STABILITY Controls
These controls provide control of the Schmitt trigger
circuit as in aconventional oscilloscope. Rotation clockwise
from acentral position picks up triggering on amore and
more positive portion of the wave; counterclockwise from
midrange picks up triggering from more and more negative
2-10
Other manuals for 7T11
1
Table of contents
Other Tektronix Time Base manuals
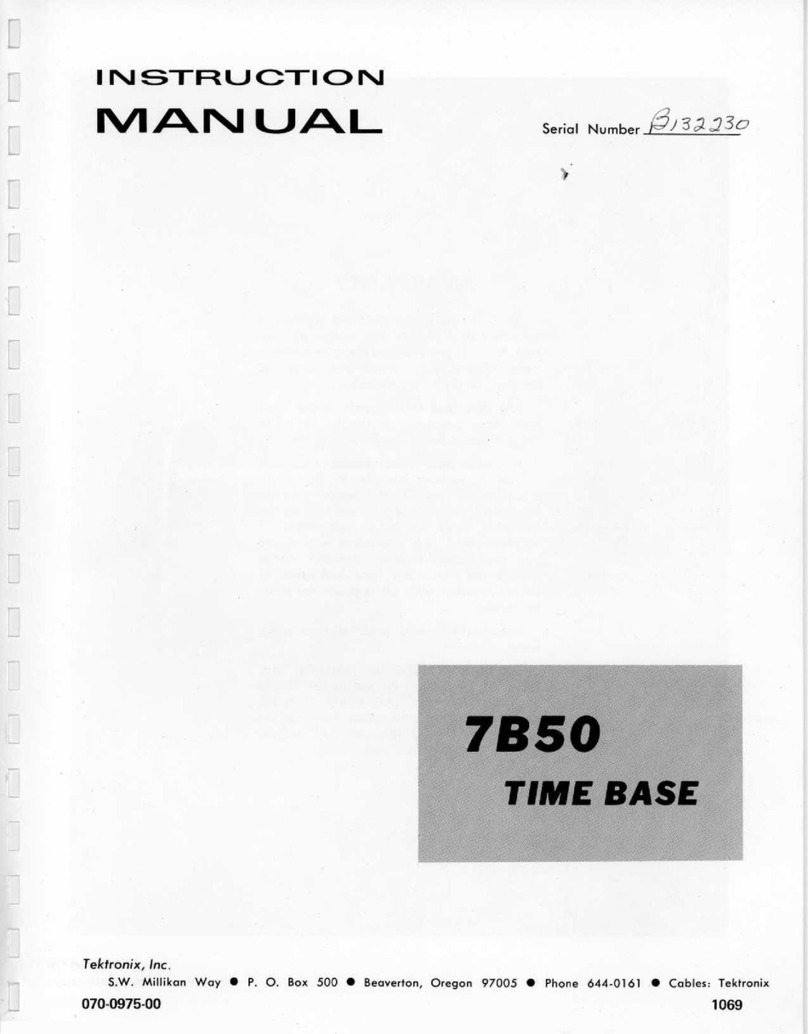
Tektronix
Tektronix 7B50 User manual

Tektronix
Tektronix 7B15 User manual
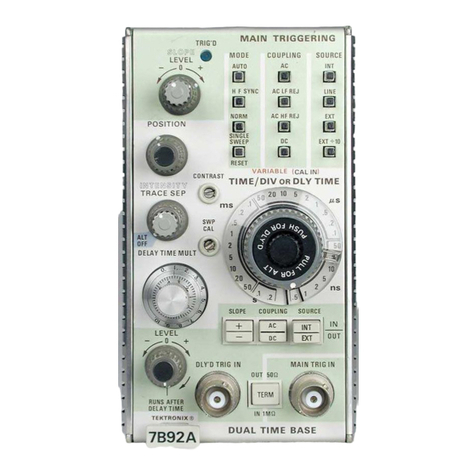
Tektronix
Tektronix 7B92A User manual
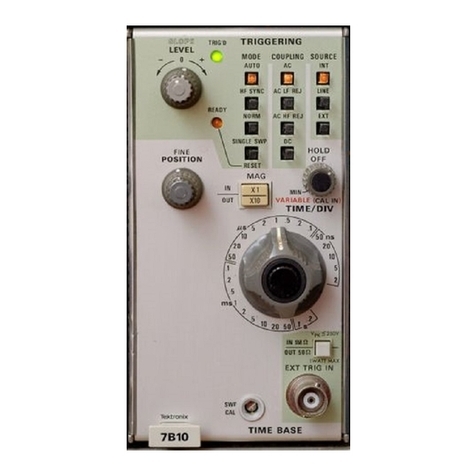
Tektronix
Tektronix 71310 User manual

Tektronix
Tektronix 7B80 User manual
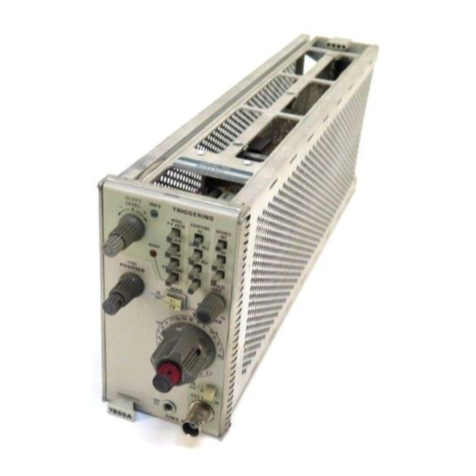
Tektronix
Tektronix 7B50A User manual
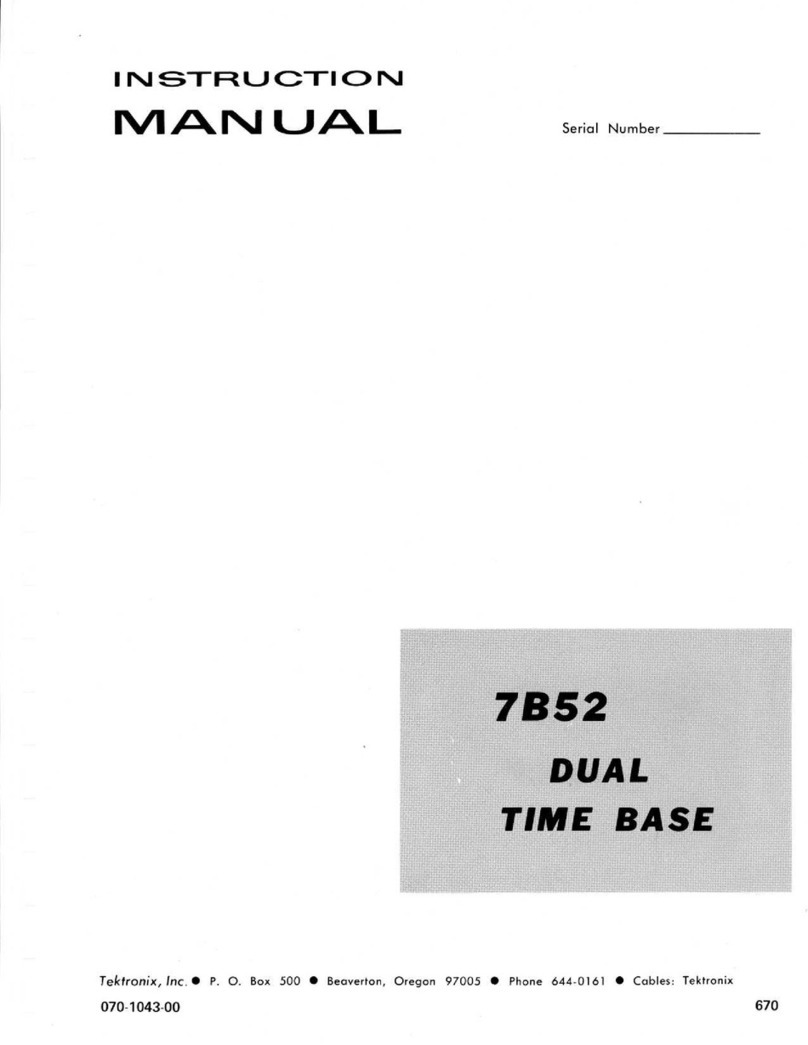
Tektronix
Tektronix 7B52 User manual
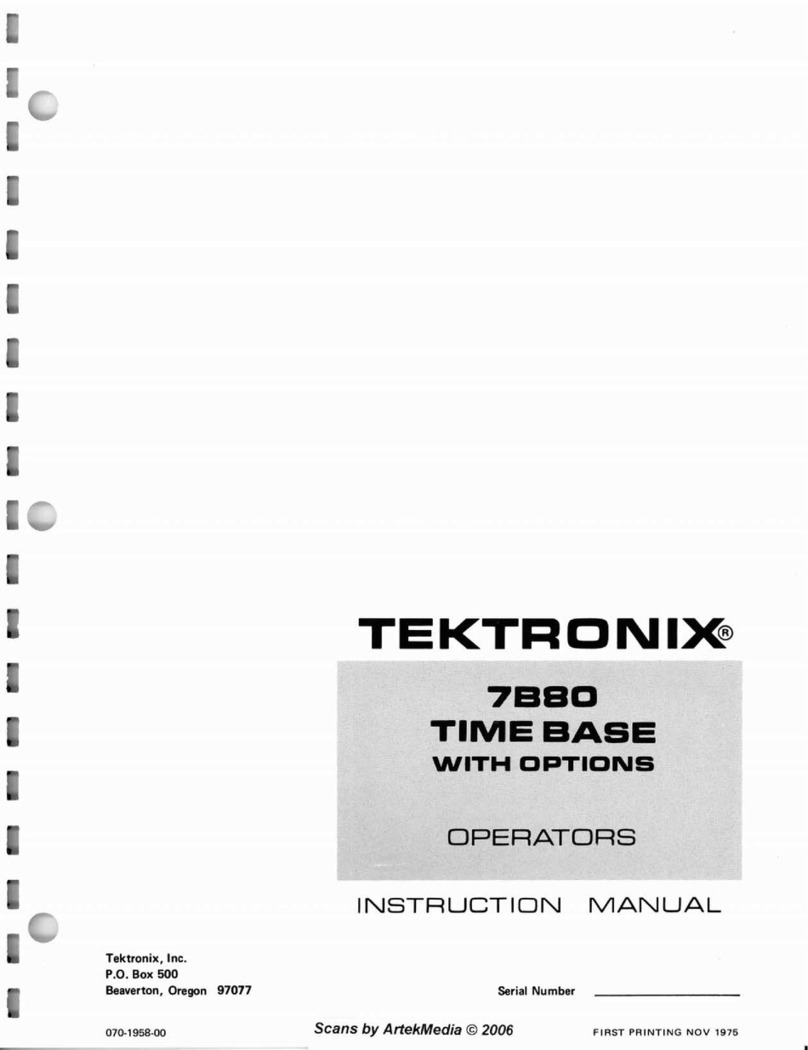
Tektronix
Tektronix 7B80 User manual
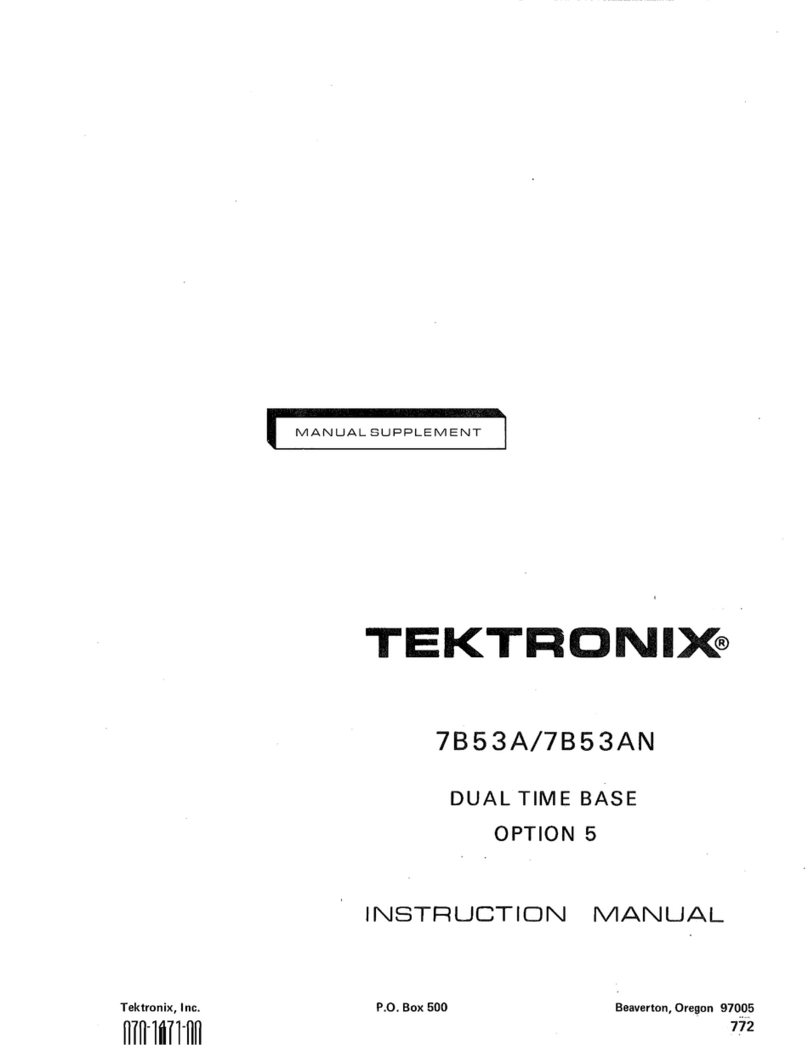
Tektronix
Tektronix 7B53A User manual
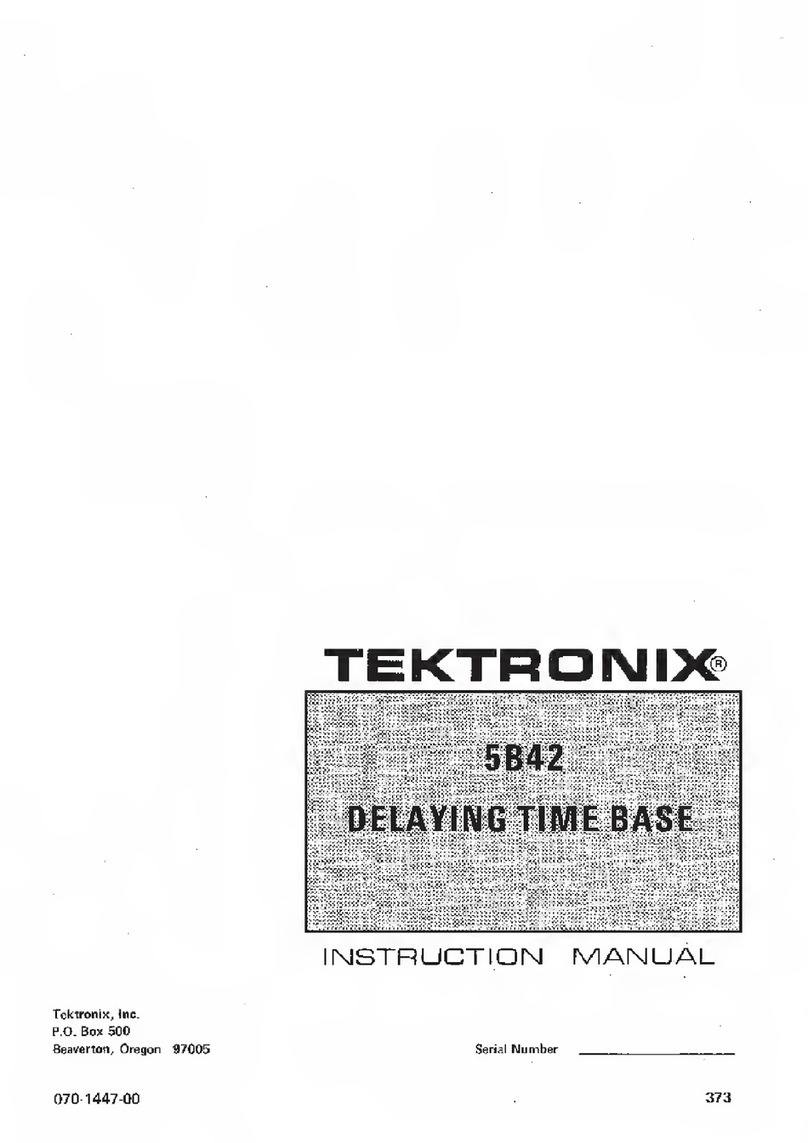
Tektronix
Tektronix 5B42 User manual