THORLABS LK220 User manual

LK220
Thermoelectric
Liquid Chiller
User Guide


Liquid Chiller
Table of Contents
Chapter 1Safety..............................................................................................................................1
Chapter 2Overview.........................................................................................................................2
Chapter 3Getting Started...............................................................................................................3
3.1.Shipping List.............................................................................................................. 3
3.2.Front & Back Panels ................................................................................................. 4
Chapter 4Operation........................................................................................................................5
4.1.Starting the Device.................................................................................................... 5
4.2.Front Panel Operation............................................................................................... 7
4.2.1.Quick Operation ............................................................................................................. 7
4.2.2.SetTemp ......................................................................................................................... 7
4.2.3.Menu .............................................................................................................................. 8
4.2.4.Status Display ................................................................................................................ 9
4.3.I/O................................................................................................................................ 9
4.4.LED Indicator ........................................................................................................... 10
4.5.Connecting an External Sensor ............................................................................. 10
4.6.Software Operation ................................................................................................. 11
4.7.Dust Filter................................................................................................................. 11
Chapter 5Command Line Operation..........................................................................................12
5.1.Description of Commands...................................................................................... 14
Chapter 6Maintenance.................................................................................................................19
6.1.Fuse Replacement................................................................................................... 19
6.2.Draining The Reservoir........................................................................................... 19
Chapter 7Specifications..............................................................................................................20
Chapter 8Mechanical Drawings..................................................................................................22
Chapter 9Certification and Compliance....................................................................................23
Chapter 10Regulatory....................................................................................................................25
Chapter 11Thorlabs Worldwide Contacts...................................................................................26

Liquid Chiller
Rev A, December 6, 2019 Page 1
Chapter 1 Safety
The device comes with a switching power supply compatible with voltages from 100 to 240 VAC. There is no
need to change the fuse when selecting your regional voltage. If the user needs to change the fuse located
below the AC plug on the back of the unit, see section 6.1.
SHOCK WARNING
High voltage inside. To avoid electrical shock, before powering unit, make sure that the
protective conductor of the 3-conductor power cord is correctly connected to the protective
earth contact of the socket outlet. Improper grounding can cause electric shock resulting in
severe injury or even death. Do not operate without cover installed.
WARNING
This unit must not be operated in explosive environments.
WARNING
Always power off the unit before opening the housing.
CAUTION
Never disassemble the chiller as irreparable damage may occur.
CAUTION
Do not operate the chiller in ambient temperatures of 40 ºC or higher.
CAUTION
Do not operate the chiller within 2 ºC of the coolant’s freezing point.
CAUTION
Do not store the chiller over 60 °C.
CAUTION
Do not use alcohol (methanol, ethanol or isopropanol) based coolants.
CAUTION
Do not ship the chiller with coolant inside the unit as freezing temperatures may be encountered
which would damage the unit. Always pump all coolant out of the chiller prior to shipping.

Liquid Chiller
Page 2 CTN014239-D02
Chapter 2 Overview
The LK220 is an air-cooled, recirculating liquid chiller based on thermoelectric elements (TECs) that provides
up to 1.2 bar of pumping capability. The bi-polar operation of the TECs allows the LK220 to be used for cooling
or heating applications. This liquid chiller has a maximum heat pump capability of 200 W when set to the ambient
temperature and a temperature control stability of ±0.1 °C. The temperature can be set between -5 °C and
45 °C using the front panel controls or the software GUI when the unit is connected to a PC via the included
USB cable.
For easy hose installation or removal, the LK220 features valved quick-connections. Two valved quick-
connection fittings and 5 meters of hose with 4 mm inner diameter are included in the package.
The LK220 is designed to be used with the CDTX Coolflow DTX Refrigerant Antifreeze, which is available on
the Thorlabs website. This liquid chiller is compatible with most ethylene glycol-based antifreeze or coolant.
Water can also be used as an alternative coolant, however, the cooling performance is reduced. Please note
that a funnel and a siphon pump are included to help transfer coolant into the chiller.
To measure the outlet coolant temperature, the LK220 is equipped with an internal thermistor sensor. The
LK220 also features an external sensor port for more precise temperature control, which is compatible with
Thorlabs' TSP-TH temperature probe (not included) or other third party thermistors.

Liquid Chiller
Rev A, December 6, 2019 Page 3
Chapter 3 Getting Started
3.1. Shipping List
The package contains the following items:
1 Chiller
1 Power Cord
1 USB Cable
5 Meters of 4.3 mm (0.17”) Inner Diameter Hose
1 Siphon Pump
1 Funnel
2 CPC® Valved Quick-connection Fittings for 4.3 mm (0.17”) Inner Diameter Hose
1 Flash Drive Containing the Operation Software and Manual

Liquid Chiller
Page 4 CTN014239-D02
3.2. Front & Back Panels
Figure 1 Front and Back Panels of LK220
F1. Secondary Power Switch
F2. SMA Port for Analog IN: 0 V to 5 V
F3. 2.5 mm Stereo Jack for External Thermistor
F4. LCD Screen
F5. Knob for Adjustment and Confirmination / LED Indicator
F6. SMA Port for Trigger IN: 5 V CMOS
F7. BNC Port for Interlock: 0 V to 5 V
F8. BNC Port for Monitor: 0 V to 5 V
F9. USB Port
F10. Airflow Inlet
B1. AC Power Inlet / Fuse Drawer / Main Power Switch
B2. Airflow Output
B3. 1/4" Hose Valved Coupling Insert for Coolant Supply
B4. 1/4" Hose Valved Coupling Insert for Coolant Return
F2
F1
F6
F7
F5 B1
F4
F8
F3
F10
F9
B2
B3
B4

Liquid Chiller
Rev A, December 6, 2019 Page 5
Chapter 4 Operation
4.1. Starting the Device
Connect the hose to the female quick-connection fittings provided in the package. Then, connect the hose to
the coolant in/out port on the back panel of the chiller. Connect the other side of the hoses to the thermal load.
Figure 2 Ferruleless Compression Fitting for Easy Connection with Tubing
Figure 3 Connecting Hoses to the LK220

Liquid Chiller
Page 6 CTN014239-D02
Open the hatch on top of the chiller and remove the plastic cap. Fill the reservoir with coolant, using the included
funnel for help if necessary. If moving coolant from a large container, we strongly recommend using the included
siphon pump. Please note that this device is safe to operate even if small spills occur or the reservoir overflows.
Figure 4 Removing the Plastic Cap (Top) and Filling the Reservoir (Bottom)
Toggle the rocker switch (B1 in Figure 1) on the back panel to “I” to power on the device. Press the secondary
power switch (F1 in Figure 1) on the front panel to enable the system.
Leave the reservoir open and set the target temperature to room temperature (see section 4.2 for details). Start
running the chiller. The pump will start, filling the tubes and heat load with coolant, and the air remaining inside
will be released to the atmosphere at the open reservoir. If the coolant level is low, an alarm will start. Fill the
reservoir with more coolant and press the knob to reset the warning.
Figure 5 Set Target to Room Temperature and Run LK220
Once the hoses, heat load, and the reservoir are filled, put the cap back on the reservoir, close the hatch, and
start regular operation.

Liquid Chiller
Rev A, December 6, 2019 Page 7
4.2. Front Panel Operation
Turn the knob to move the cursor on the screen, and press to confirm/select. The device status is displayed on
the title bar (see Section 4.2.4).
4.2.1. Quick Operation
Set the target temperature by selecting Target and turning the knob clockwise or counterclockwise to increase
or decrease the temperature, respectively. Press the knob to confirm the temperature value. Select the
Run/Stop option to enable the device.
Figure 6 Quick Operation to Run LK220 by Panel Control
4.2.2. SetTemp
Select the SetTemp button to enter the set temperature screen; the target temperature and temperature window
can be set here. The temperature control window defines the allowed temperature shift of the device. Please
note that a warning message appears when the difference between the actual and target temperature if larger
than the temperature window. However, the chiller will continue to run.
Figure 7 SetTemp Menu Accessed with Panel Control

Liquid Chiller
Page 8 CTN014239-D02
4.2.3. Menu
Select Menu to enter the menu screen.
Figure 8 Select Menu to Enter Menu Screens
On the first page of the menu screen, users are able to monitor and control the control mode, the temperature
sensor, pump drive, fan drive, and back light.
Ctrl MOD: There are four different control modes supported by the devices:
LOCAL: The device responds to knob and software GUI operation.
LOCAL-ANG: The target temperature is set by the Analog IN port, and the RUN/STOP of the chiller is
controlled by the knob and GUI.
TRIG: The target temperature is set by the knob and GUI, and the RUN/STOP of the chiller is controlled
by the Trigger IN port.
TRIG-ANG: The target temperature is set by the Analog IN port, and the RUN/STOP of the chiller is
controlled by the Trigger IN port.
Ctrl SEN (Control Sensor):
INT: The internal sensor measuring the output coolant temperature is selected to provide the actual
temperature reading;
EXT: The external TSP-TH sensor connected on the front panel is selected to provide the actual
temperature reading. If this control sensor is selected while no sensor is connected, a error message
will appear and a alarm will be set off. The LK220 chiller will be disabled until a TSP-TH is connected
or the control sensor is switched back to INT.
Pump DRV (Pump Driving):
This sets the pumping power, which defaults to 60%. 30 - 60% pumping power usually provides the
best cooling performance.
Fan DRV (Set the Duty Cycle of the Fan)
This sets the duty cycle of the main fan, which defaults to AUTO.
Figure 9 Second and Third Pages of the Menu Screen

Liquid Chiller
Rev A, December 6, 2019 Page 9
On the second and third page of the menu screen, users are able to monitor the operation state of the chiller.
Inlet T1: Temperature of Inlet Coolant
Cold T2: Temperature of the Cold Plate Inside the Chiller
HSink T3: Temperature of the Heat Sink Inside the Chiller
Outlet T4: Temperature of the Outlet Coolant when the Sensor Type is Set to Internal; Temperature of
the External Sensor when the Sensor Type is Set to External
AMB T5: Temperature of the Ambient Environment
TEC Current: TEC Driving Current
TEC Driver: TEC Driving Duty Cycle
PUMP Driver: Pumping Driving Duty Cycle
FAN Driver: Fan Driving Duty Cycle
Flow Rate: Current Coolant Flow Rate
4.2.4. Status Display
The device status is displayed on the title bar:
Standby Local: When the Unit is in Standby and Local Operation Mode
Standby Analog: When the Unit is in Standby and Local-ANG Operation Mode
Standby TRIG: When the Unit is in Standby and TRIG Operation Mode
Standby TRIG-ANG: When the Unit is in Standby and TRIG-ANG Operation Mode
Cooling: When the Unit is Running and the Actual Temperature is Higher than the Target but within the
Temperature Window
Heating: When the Unit is Running, the Actual Temperature is Lower than the Target but within the
Temperature Window
Low ActTemp: When the Unit is Running, the Actual Temperature is Lower than the Target and Outside
the Temperature Window
High ActTemp: When the Unit is Running, the Actual Temperature is Higher than the Target and Outside
the Temperature Window
4.3. I/O
There are six I/O ports on the front panel of LK220.
Analog In: SMA Port, provides control of the target temperature from a external signal, 0 V to +5 V DC
Input Corresponds to -5 °C to 45 °C Target temperature;
Analog Out: BNC Port, provides a monitor signal of the actual temperature, 0 V to +5 V DC Output
Corresponds to -5 °C to 45 °C Actual Temperature
Trigger In: SMA Port, High Level (+ 5 V) Input to enable the temperature control function of the Chiller;
Low Level (0 V) Input to Disable the Chiller (default)
Interlock: BNC Port, High Level (+5 V) Output when Chiller Errors Occur; Low Level (0 V) Output when
there are no Chiller Errors

Liquid Chiller
Page 10 CTN014239-D02
USB: For Connecting to a PC for Software or Command Line Operation
TSP-TH: For use with the TSP-TH Sensor as the External Sensor
4.4. LED Indicator
The LED indicator (F5 in Figure 1) has four possible colors to indicate the current status of the device:
1. Blue: The temperature has reached the target and stabilized while the device is controlled in Local or
Local-Ana mode.
2. Green: The temperature has reached the target and stabilized while the device is controlled in TRIG or
TRIG-Ana mode.
3. Yellow: indicates warning conditions under which the device is still fully operation. When an error
occurs, it may be due to one of the following reasons:
a) The device is working properly but the temperature has not reached the target.
a) Low Flow: the Flow Measured by the Flow Meter is <0.1 Litre per Minute (LPM)
4. Red: There are errors in the device and operation has stopped. When an error occurs, it may be due to
one of the following reasons:
b) High Temperature Error: Any of the Internal Temperature Sensors are > 65 °C (TBD)
c) Low Temperature Error: Any of the Internal Temperature Sensors are < -10 °C
d) Low Level Error: Coolant Level is <25% of the Maximum Coolant Capacity
e) No Flow Error: the Flow Measured by the Flow Meter is <0.1 Litre per Minute (LPM) for more than
30 seconds
f) Pump Failure Error: Pump Open Circuit and Short Circuit
g) TEC Failure Error: TEC Open Circuit and Short Circuit
h) Fan Failure Error: Fan Open Circuit and Short Circuit.
i) EXT Sensor Error: the Sensor is Set to External but no Temperature Sensor is Connected
j) Connection Error: the Control Mode is Set to Remote but no Trig or Analog Cable is Connected
4.5. Connecting an External Sensor
On the front panel of the LK220, there is a 2.5 mm Stereo Jack (F2 in Figure 1). It is designed to accept a
Thorlabs TSP-TH thermistor temperature probe as an external sensor. Other 10 kΩ thermistors (R0 = 10 kΩ @
T0 = 25 °C) soldered with a 2.5 mm Stereo Jack can also be used.
Connect the TSP-TH and toggle the “Ctrl SEN” in 1st Menu screen to “EXT”. Then, the LK220 will use the
external thermistor as the temperature monitor for its temperature control feedback loop instead of the internal
thermistor inside the return coolant hose.
When “Ctrl SEN” is set to “EXT”, the LK220 chiller is configured by default according to the parameters of TSP-
TH. No additional settings need to be adjusted. To get accurate temperature readings while using other
thermistors, the Beta value must be set in the LK220 software GUI.

Liquid Chiller
Rev A, December 6, 2019 Page 11
4.6. Software Operation
Connect the device to a computer with the included USB cable. The device can be controlled by the LK220
software, included with the device. The most up-to-date software GUI is also available on www.thorlabs.com.
Within the software, users can carry out all the operations of the panel control mode, and the PID parameters
can also be adjusted. Using the software GUI, users can also set temperature sequences and save all data
from the device monitor.
4.7. Dust Filter
The chiller is equipped with a dust filter behind the front panel. Users can remove the dust filter to achieve the
full cooling power of the chiller, which is 200 W when the actual temperature is kept the same as the ambient
temperature. With the filter installed, there is a 30 W to 50 W loss of cooling power. Please note that long term
operation of the chiller without a filter is only recommended for a standard photonics lab environment or a
cleanroom.
Unscrew the 4 cap screws with a 2 mm (5/64ʺ) ball driver or hex key to remove the front panel. Peel off the dust
filter from the back of the front panel, and then put the panel back on.
The dust filter can be cleaned using a vacuum cleaner or by flushing under tap water.
Figure 10 Unscrewing the Front Panel (Left) and Removing the Dust Filter (Right)

Liquid Chiller
Page 12 CTN014239-D02
Chapter 5 Command Line Operation
The LK220 can be controlled by a command-line language through the USB port. Users can either use a terminal
emulator or write their own program to control the unit. The command language is described below. Prior to
running the command-line interface, the included drivers should be installed, the unit should be powered on,
and a USB cable should be connected between the liquid chiller and the host PC.
The terminal emulator should be configured as follows:
• Baud Rate: 115.2 kbps
• Data Bits: 8
• Parity: None
• Stop Bits: 1
• Flow Control: None
If the connection parameters are correct, you will see the following after pressing the Enter key (without any
leading commands):
CMD_NOT_DEFINED
>
The above error indicates that an empty command (which is equivalent to an incorrect command) has been
sent.
The basic structure of the interface is a keyword followed by either an equals sign (=) or a question mark (?).
The = or ? character determines if the string is a command or a query. All strings, commands, and queries must
be terminated by a carriage return (CR) or by pressing the Enter key on the computer.
The command structure is as follows:
Keyword=argument(CR)
Here, “keyword” defines the function and “argument” as a numerical value followed by a carriage return (CR).
Note that some commands might have more than one argument, separated by a space character.
The query structure is as follows:
Keyword?(CR)
Where “keyword” defines the function and the question mark (?) indicates a query. The string is terminated with
a carriage return (CR).
There are a few exceptions to this, which are noted below. Also noted below are unique shortcut keys. The
following table lists the commands and queries available with this device. The prompt symbol (>) appears on
power up and after a command is accepted by the controller, indicating it is ready to receive the next command.
If the command is incorrect, the chiller returns CMD_NOT_DEFINED;
If the command parameter is incorrect, the chiller returns PARAMETER_ERR;
The table on the next two pages lists all the available commands for the operation of LK220.

Liquid Chiller
Rev A, December 6, 2019 Page 13
Command Syntax Description
Get Commands COMMAND? List the available commands
Get ID IDN? Return the device hardware and firmware versions
Get Device State ST? Return device state
Disable/Enable
the Chiller EN=0,1 0=Disable chiller,1=Enable chiller
Get Target
Temperature TSET? Get the target temperature (range: -5.0 - 45.0 °C)
Set Target
Temperature TSET=n Set the target temperature(n = -50 - 450, representing -5.0 - 45.0 °C)
Get Actual
Temperature TACT? Get the actual temperature (range: -10.00 - 60.00 °C, resolution = 0.01°C)
Set Temperature
Window WINDOW=n Set temperature window (n = 1 - 50, representing ±0.1 - ±5 °C)
Get Temperature
Window WINDOW? Get temperature window ((range 0.1 - 5, representing ±0.1 - ±5 °C)
Set Control Mode MOD=n Set control mode (n = 0 Local; 1 Local-Analog; 2 Trig; 3 Trig-Analog)
Get Control Mode MOD? Return the control mode (n = 0 Local; 1 Local-Analog; 2 Trig; 3 Trig-
Analog)
Set Control
Sensor Mode SENS=n Set control sensor (0 = internal sensor; 1 = external sensor)
Get Control
Sensor Mode SENS? Return control sensor state (0 = internal sensor; 1 = external sensor)
Set the EXT
Sensor Type EXT=n Set the external sensor type, n = 1 TSP01; 2 other TSP, reserved for
future use; 8 other 10k ohm thermistor
Get the EXT
Sensor Type EXT? Get the external sensor type, n = 1 TSP01; 2 other TSP, reserved for
future use; 8 other 10k ohm thermistor
Set EXT Sensor
Constant BETA=n Set the β value of the thermistor of external sensor when the external
sensor type is set to 8 (other 10k ohm thermistor), n from 0 to 9999
Get EXT Sensor
Constant BETA? Return the β value of the thermistor of external sensor when the external
sensor type is set to 8 (other 10k ohm thermistor), n from 0 to 9999
Set Pump Driver PUMP=n Set driving power of the coolant pump in LK220 (n = 10 - 100,
representing 10 - 100%)
Get Pump Driver PUMP? Return the driving power of the coolant pump in LK220 (range 10 - 100%)
Set Fan Mode FAN=n Set the duty cycle of the main cooling fan (n = 0 Auto; 1 0%, 2 25%, 3
50%, 4 75%, 5 100%)
Get Fan Mode FAN? Get the duty cycle of the main cooling fan (n = 0 Auto; 1 0%, 2 25%, 3
50%, 4 75%, 5 100%)
Get Tec Current TEC? Return “n”, n from 0 to 10.0, representing 0 - 10.0A
Get Liquid Flow
Rate FLOW? Return the coolant flow rate: “n”, n from 0 to 5.0, representing 0 - 5.0 LPM
Set Knob State KNOB=n Set the knob state, n=0 Unlock; n=1 Locked. When set to locked, LK220
will not respond to any movement on the knob on the front panel.
Get Knob State KNOB? Get the knob state (0=Unlock 1=Locked)
Set P Parameter KP=n Set the gain value of the P share in the temperature PID control loop (n =
0 - 999, representing gain value of 0 ~ 9.99).
Get P Parameter KP? Return the gain value of the P share in the temperature PID control loop
(range: 0 - 9.99)
Set I Parameter TI=n Set the gain value of the I share in the temperature PID control loop (n = 0
- 999, representing gain value of 0 - 9.99).
Get I Parameter TI? Return the gain value of the I share in the temperature PID control loop
(range: 0 - 9.99).
Set D Parameter TD=n Set the gain value of the D share in the temperature PID control loop (n =
0 - 999, representing gain value of 0 - 9.99)
Get D Parameter TD? Return the gain value of the D share in the temperature PID control loop
(range: 0 - 9.99)
Set Period
Parameter PERIOD=n Set the integrating period of the PID servo loop (n = 500 - 5000,
representing 500 - 5000ms).

Liquid Chiller
Page 14 CTN014239-D02
Command Syntax Description
Get Period
Parameter PERIOD? Return the integrating period of the PID servo loop “n” (n = 500 ~ 5000,
representing 500 ~ 5000ms).
Get Error
Message ERR? Return the error message value
Get Warning
Message WARN? Return the warning message value
Get Monitor
Message MONITOR? Return all monitor status
Load Factory
Parameter LOADFACT! Restore the device factory parameters
5.1. Description of Commands
COMMAND? – Get Device Commands
Return: All of the command list in the Table1.
IDN? – Get device Information
Queries the device part number, hardware and firmware versions.
Return:
THORLABS LK220 HV x.xx FV x.xx.
Where HV is the hardware version; and FV is the firmware version.
ST?–GetDeviceInformation
Return:an 8-bit byte was defined as in below table:
Device state define 8bit
bit0=1 Standby
bit1=1 Heating
bit2=1 Cooling
bit3=1 Warning
bit4=1 Error
bit5=1 Reserved
bit6=1 Reserved
bit7=1 Reserved
EN=n – Disable/Enable the Chiller
n=0, Disable chiller;
n=1, Enable chiller.
TSET? – Get Target Temperature
Get the target temperature (range: -5.0 - 45.0 °C).
E.g. returned “10.0” means target temperature = 10.0 °C.

Liquid Chiller
Rev A, December 6, 2019 Page 15
TSET=n – Set Target Temperature
Set the target temperature (n = -50 - 450, representing -5.0 -45.0 °C).
E.g. "TSET=100" means to set target temperature to 10.0 °C.
TACT? – Get Actual Temperature
Get the actual temperature (range: -10.00 - 60.00 °C, resolution = 0.01 °C).
E.g. returned “20.00” means actual temperature = 20.00 °C.
WINDOW=n – Set Temperature Window
Set temperature window (n = 1 - 50), representing ±0.1 to ±5 °C. When the difference between the
actual temperature and the target temperature is outside the set temperature window, a warning will
occur.
E.g. "WINDOW=5" means to set temperature window to ±0.5 °C
WINDOW? – Get Temperature Window
Get temperature window (range 0.1 - 5, representing ±0.1 - ±5 °C).
E.g. returned "0.5" means the temperature window is ±0.5 °C.
MOD=n – Set Control Mode
Set control mode (n = 0 Local; 1 Local-Analog; 2 Trig; 3 Trig-Analog).
MOD? – Get Control Mode
Return control mode “n” (n = 0 Local; 1 Local-Analog; 2 Trig; 3 Trig-Analog).
SENS=n – Set Control Sensor
Set which sensor will be providing the actual temperature reading, n = 0 Internal Sensor; 1 External
Sensor.
SENS? – Get Control Sensor
Get the state on which sensor has be selected to provide the actual temperature reading, n = 0 internal
sensor; 1 external sensor.
Return “n”, n = 0 internal sensor; 1 external sensor.
EXT=n – Set the EXT Sensor Type
Set the external sensor type, n = 1 TSP01; 2 other TSP, reserved for future use; 8 other 10k ohm
thermistor.
EXT? – Get the EXT Sensor Type
Return the external sensor type “n”. n = 1 TSP01; 2 other TSP; 8 other 10k ohm thermistor.
BETA=n – Set EXT Sensor Constant
Set the β value of the thermistor of external sensor when the external sensor type is set to 8 (other 10k
ohm thermistor), n from 0 to 9999.
E.g. "BETA=3488" means to set the β value to 3488.

Liquid Chiller
Page 16 CTN014239-D02
BETA? – Get EXT Sensor Constant
Return the β value of the thermistor of external sensor when the external sensor type is set to 8 (other
10k ohm thermistor), n from 0 to 9999.
PUMP=n – Set Pump Driver
Set driving power of the coolant pump in LK220 (n = 10 - 100, representing 10 - 100%).
E.g. "PUMP=60" means to set the driving power of the pump to 60% of its maximum.
PUMP? – Get PUMP Driver
Return the driving power of the coolant pump in LK220 (range 10 - 100%).
FAN=n – Set Fan Mode
Set the duty cycle of the main cooling fan (n = 0 Auto; n = 1 0%, n = 2 25%, n = 3 50%, n = 4 75%, n =
5 100%).
E.g. "FAN=5" means to set duty cycle of the cooling fan to 100%.
FAN? – Get the FAN Driver
Return the duty cycle of the main cooling fan (n = 0 Auto; 1 0%, 2 25%, 3 50%, 4 75%, 5 100%)
TEC? – Get the TEC Current
Return the TEC current “n”, n from 0 to 10.0, representing 0 - 10.0 A.
FLOW? – Get Liquid Flow Rate
Return the coolant flow rate: “n”, n from 0 to 5.0, representing 0 - 5.0 LPM (Liter per Minute).
KNOB=n – Set Knob State
Set the knob state, n=0 Unlock; n=1 Locked. When set to locked, LK220 will not respond to any
movement on the knob on the front panel.
KNOB? – Get Knob State
Return the knob state “n”, n=0 Unlock; n=1 Locked.
KP=n – Set P Parameter
Set the gain value of the P share in the temperature PID control loop (n = 0 - 999, representing gain
value of 0 - 9.99).
E.g. “KP=100” means to set the gain value of the P share to 1.00.
KP? – Get P Parameter
Return the gain value of the P share in the temperature PID control loop (range: 0 - 9.99).
E.g. “1.00” means the gain value of the P share is 1.00.

Liquid Chiller
Rev A, December 6, 2019 Page 17
TI=n – Set I Parameter
Set the gain value of the I share in the temperature PID control loop (n = 0 - 999, representing gain
value of 0 - 9.99).
E.g. “TI=200” means to set the gain value of the I share to 2.00.
TI? – Get I Parameter
Return the gain value of the I share in the temperature PID control loop (range: 0 - 9.99).
E.g. “2.00” means the gain value of the I share is 2.00.
TD=n – Set D Parameter
Set the gain value of the D share in the temperature PID control loop (n = 0 - 999, representing gain
value of 0 - 9.99).
E.g. “TD=200” means to set the gain value of the D share to 2.00
TD? – Get D Parameter
Return the gain value of the D share in the temperature PID control loop (range: 0 - 9.99).
E.g. “1.00” means the gain value of the D share is 1.00.
PERIOD=n – Set Period Parameter
Set the integrating period of the PID servo loop (n = 500 - 5000, representing 500 – 5000 ms).
E.g. “PERIOD=2000”, means to set the integrating period of the PID servo loop to 2000 ms.
PERIOD? – Get PID Period Time Value
Return the integrating period of the PID servo loop “n” (n = 500 - 5000, representing 500 – 5000 ms).
E.g. “2000”, means the integrating period of the PID servo loop is 2000 ms.
ERR? – Get Error Message
Return: an 8-bit byte was defined in below table:
bit0=1 Coolant Level Low
bit1=1 Device Over Temperature
bit2=1 Device Low Temperature
bit3=1 TEC Error
bit4=1 Eternal Sensor Error
bit5=1 Internal Sensor Error
bit6=1 No flow
bit7=1 Reserved
Error is defined as fatal error occurs to the device. The device will be disabled and an alarm will be set
off when an error occurs.
WARN? – Get Warning Message
Return: an 8-bit byte was defined In below table:
Table of contents
Popular Chiller manuals by other brands

Haier
Haier CA0100MANB Installation, operation and technical manual
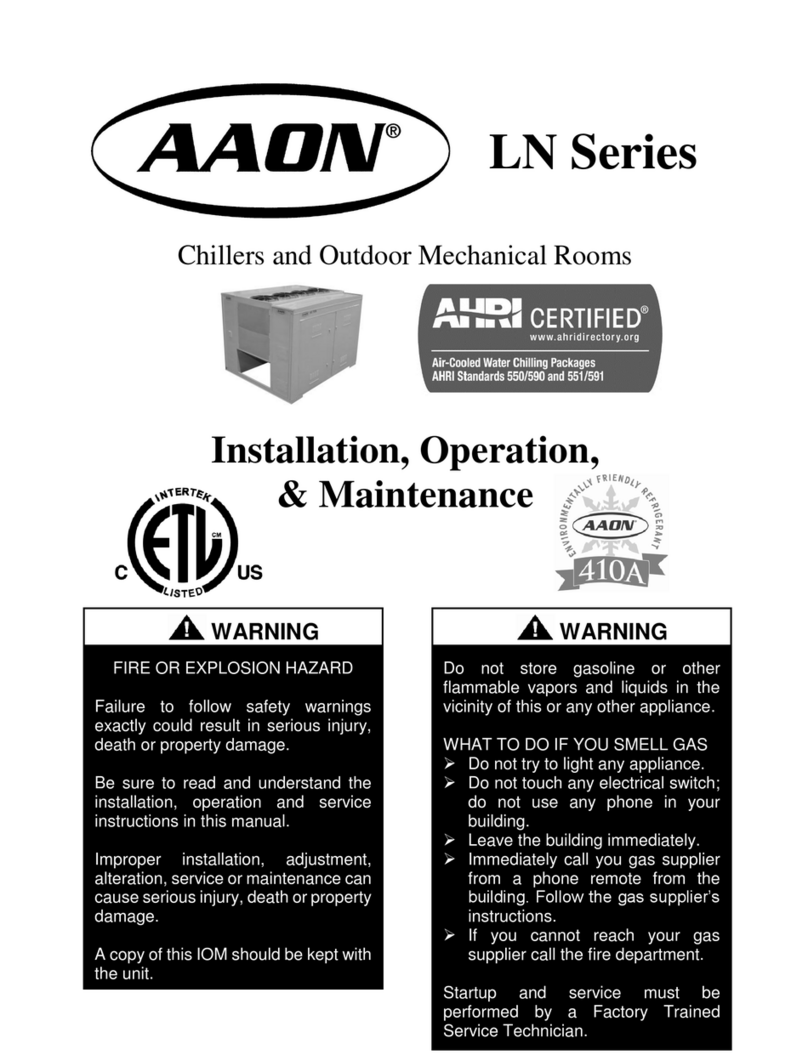
AAON
AAON LN Series Installation operation & maintenance

Polar Electro
Polar Electro U-Serie instruction manual
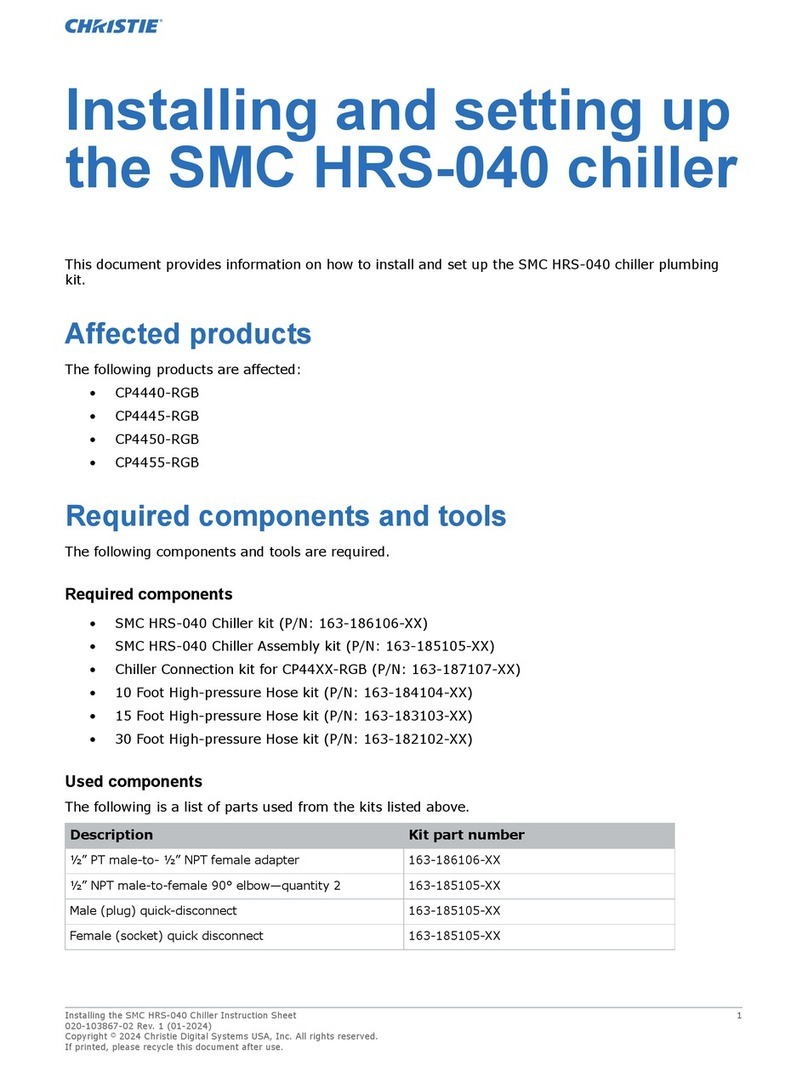
Christie
Christie SMC HRS-040 Installing and setting up
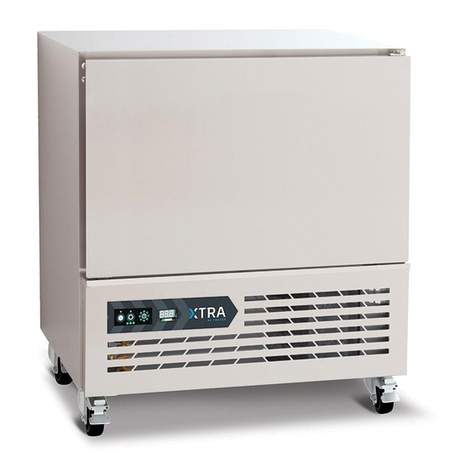
xtra
xtra XR10 Original service manual

Elkay
Elkay ERS1-1E/2E Installation, care & use manual
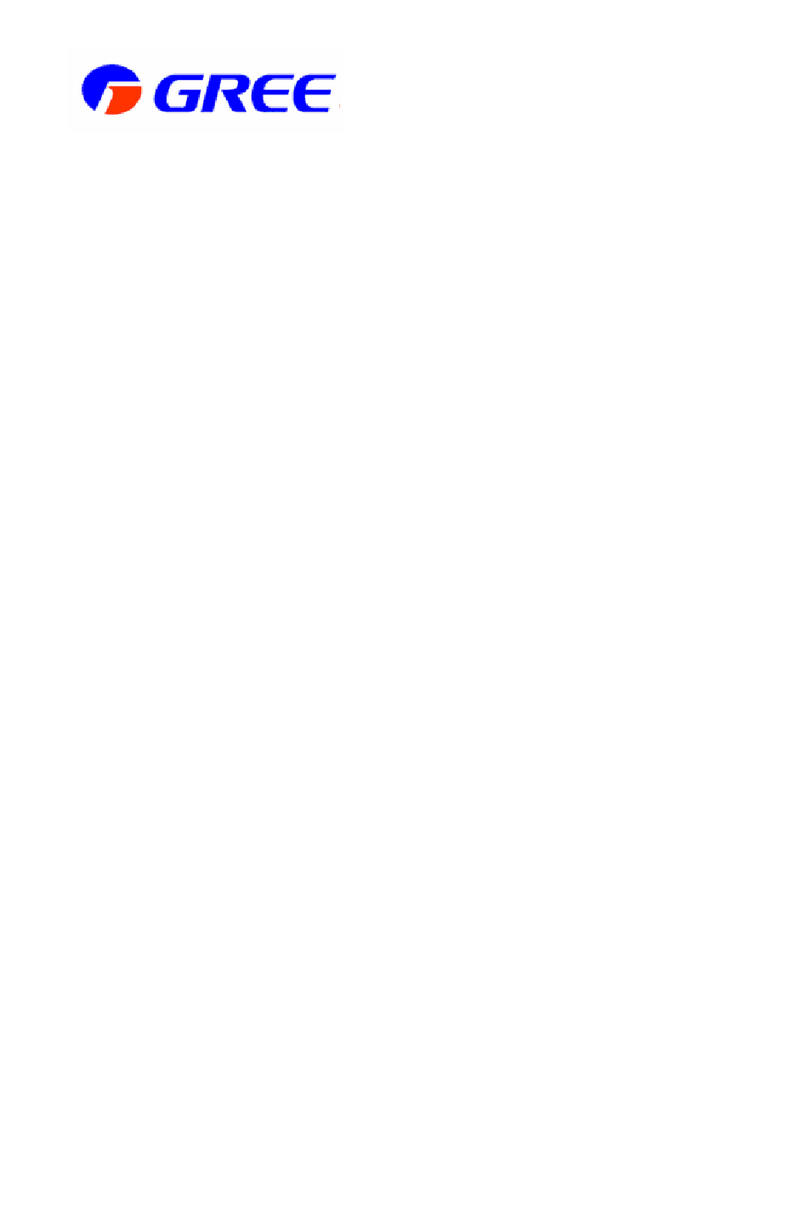
Gree
Gree LSQWF65M/N-M Service manual
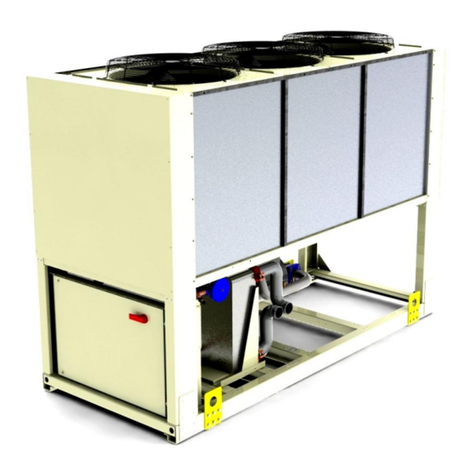
Daikin
Daikin EWAD E-SS Series Installation, operation and maintenance manual
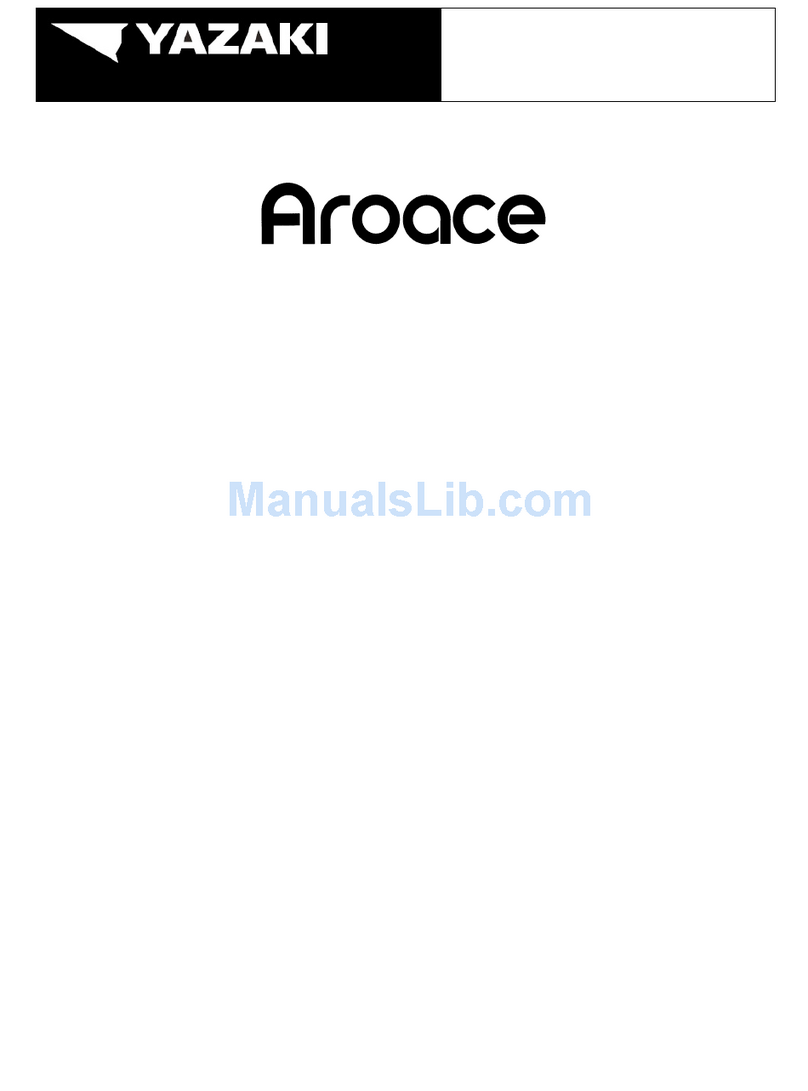
Yazaki
Yazaki Aroace WFC-SC10 installation instructions

Carrier
Carrier Flotronic 30GB user manual
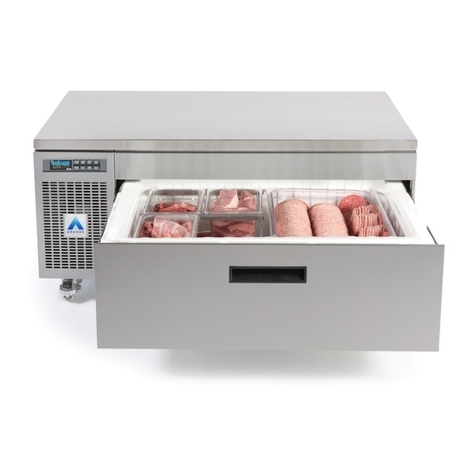
Adance
Adance ADE-2022-C Maintenance manual
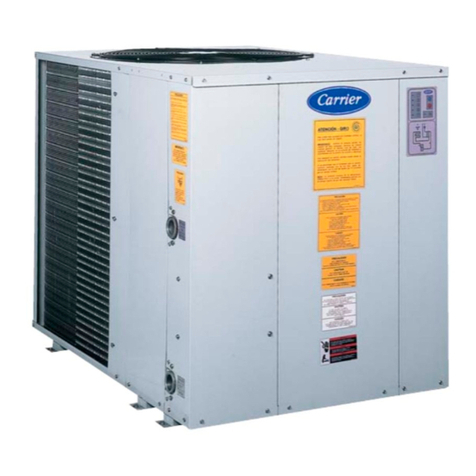
Carrier
Carrier 30AJ Installation, operation and maintenance manual