THORLABS SH1 User manual

SH1 and SH1/M
Ø1" Beam Shutter
User Guide

Ø1" Beam Shutter
Table of Contents
Chapter 1Warning Symbol Definitions ........................................... 1
Chapter 2Safety ................................................................................. 2
Chapter 3Introduction....................................................................... 3
3.1.ProductDescription.......................................................3
3.2.ShutterOverview...........................................................4
3.2.1.Timing Performance .................................................................... 5
3.2.2.Typical Performance .................................................................... 5
Chapter 4Specifications ................................................................... 6
4.1.GeneralSpecifications...................................................6
4.2.InterfaceConnector.......................................................6
Chapter 5Drawing ............................................................................. 8
5.1.SH1................................................................................8
5.2.SH1/M...........................................................................9
Chapter 6Regulatory ....................................................................... 10
6.1.WasteTreatmentisYourOwnResponsibility...............10
6.2.EcologicalBackground.................................................10
Chapter 7Thorlabs Worldwide Contacts....................................... 11

Ø1" Beam Shutter Chapter 1: Warning Symbol Definitions
Rev E, March 16, 2020 Page 1
Chapter 1 Warning Symbol Definitions
Below is a list of warning symbols you may encounter in this manual or on your
device.
Symbol Description
Direct Current
Alternating Current
Both Direct and Alternating Current
Earth Ground Terminal
Protective Conductor Terminal
Frame or Chassis Terminal
Equipotentiality
On (Supply)
Off (Supply)
In Position of a Bi-Stable Push Control
Out Position of a Bi-Stable Push Control
Caution: Risk of Electric Shock
Caution: Hot Surface
Caution: Risk of Danger
Warning: Laser Radiation
Caution: Spinning Blades May Cause Harm

Ø1" Beam Shutter Chapter 2: Safety
Page 2 21340-D02
Chapter 2 Safety
WARNING
Extremely high powered lasers will create a safety hazard and cause damage to
this product. The shutter for this product was tested with high power laser
sources at wavelengths of 532 nm and 1064 nm. The point at which damage to
the shutter surface occurred is given in the chart below. If the damage to the
shutter surface occurs and bare aluminum is present, then unwanted and
dangerous reflections can occur. Be aware not to exceed the given limits when
focusing the beam; damage to the unit may occur at a lower power level than
given in the table below when using focusing optics.
Wavelength Damage
Threshold Spot Dia. Exposure Incidence Angle
532 nm 1500 W/cm2 730 μm 10 sec/site 0°
1064 nm 20 000 W/cm2 950 μm 10 sec/site 0°
WARNING
Safety Eyewear is recommended whenever working with laser beams. While
working with laser beams in conjunction with this shutter, dangerous situations
can occur if the shutter is open while the laser beam is on. It is recommended
that the shutter remain close while making adjustments to a laser set up and the
proper eyewear should always be worn while operating lasers.
WARNING
This product operates at a sound level near or slightly above 70 dB. During
operation at 25 Hz the sound level was measured to be 71 dB at a distance of 1
meter.
ATTENTION
Caution is given when there is a possibility of damage to the product. This
product was not assessed to ISO 61508 which is a Safety Equipment Standard.
!
!
!
!
!
!

Ø1" Beam Shutter Chapter 3: Introduction
Rev E, March 16, 2020 Page 3
Chapter 3 Introduction
3.1. Product Description
The SH1 is a rotary, electro-mechanical actuator to provide millisecond shutter
operation. In general operation, the shutter remains in a closed position and then
opens with a pulse control signal. As long as the control voltage to the shutter
remains high, the shutter will stay open; however, if the voltage suddenly
decreases, the shutter will close, providing inherent “fail-safe” operation. An optical
sensor, which detects the shutter blade's position within the housing, confirms the
state of the shutter position, making it ideal in applications where a laser safety
lockout is required. The rate at which the device is opened can be controlled. The
unit has a 1.0" aperture opening and is compatible with Thorlabs’ SM1 mounting
system.
The input aperture of the SH1 is threaded with Thorlabs' SM1 (1.035"-40) thread
to interface easily with all of our SM1 lens tubes. The SH1 comes with 8-32 tapped
holes for mounting to our imperial Ø1/2" posts. The SH1/M comes with M4 tapped
holes for mounting to our metric Ø1/2" posts. All shutters come with a 10' cable to
connect the shutter directly to the SC10 Controller (sold separately).
The SH1 can also be used with a third party controller.

Ø1" Beam Shutter Chapter 3: Introduction
Page 4 21340-D02
3.2. Shutter Overview
The SH1 shutter contains a rotary solenoid presenting a large inductive load to the
controlling device. As this inductor is charged, the resulting movement of the
actuator takes a finite amount of time (opening of the shutter). Conversely when
the voltage is removed from the shutter it takes a finite time for the inductor to
discharge and for the mechanics to release the actuator (closing the shutter). The
shutter timing varies and is dependent on the duration and magnitude of the driving
pulse and the magnitude of the sustaining hold voltage.
The SC10 provides a 10 millisecond 24 Volt driving voltage to actuate the shutter
and a holding voltage of 10 Volts. The timing for the SH1 is characterized in Figure
1 when operated with the SC10 controller.
Figure 1 SH1 Timing Diagram when driven with Thorlabs’ SC10 Shutter Controller

Ø1" Beam Shutter Chapter 3: Introduction
Rev E, March 16, 2020 Page 5
3.2.1. Timing Performance
Event Time (Typical)
TI 10 ms
TO 10 ms
TD/R 20 ms
TC 10 ms
MSOP 40 ms
MOP (SC10) 40 ms
TI, Transfer Initialize: Time from the application of an energizing voltage
to the initial movement of the shutter.
TO, Transfer Open: Time for the shutter to open from 20% exposed to
the 80% exposed.
TD/R, Transfer Dwell/Release: Time from the removal of the holding
voltage or pulse to the point where the shutter begins to close.
TC, Transfer Close: Time for shutter to close from an 80% exposure to
20% exposure.
MSOP, Minimum Shutter Open Time: Minimum shutter open time using
the MOP from the SC10 controller.
MOP, Minimum Open Pulse: Minimum pulse width of SC10 controller.
Note: The shutter SH1 is not meant for operation in critical timing
applications. Performance may vary from unit to unit.
3.2.2. Typical Performance
The SH1 is capable of operating at a sustained maximum rate of 12.5 Hz with a
minimum on time of 40 ms. As programmed exposure times (open times) increase
to beyond 60 ms the dominant characteristics of magnetic distortion, TI and TD/R
as shown in Figure 1, become constants. The net effect of this anomaly is that the
delay from the control pulse (or trigger) to the shutter opening is 10 ms, and the
duty cycle distortion incurred is ±10 ms. As an example: If the SC10 is programmed
for 200 ms open and 200 ms close time, the result would be a 210 ms exposure
and a 190 ms closure on the SH1.

Ø1" Beam Shutter Chapter 4: Specifications
Page 6 21340-D02
Chapter 4 Specifications
4.1. General Specifications
The following specifications are given for those not using a SC10 controller.
General Specifications
Solenoid Coil Resistance 31.84 Ohms
Max Solenoid (Pulse) Voltage 75 V
Max Solenoid Power (@ 20 °C)
Steady State 9 Watts
50% Of Duty Cycle 18 Watts
25% Of Duty Cycle 36 Watts
5% Of Duty Cycle 180 Watts
Max Solenoid Time On (@ 20 °C)
Steady State Continuous
50% Of Duty Cycle 100 s
25% Of Duty Cycle 36 s
5% Of Duty Cycle 2.8 s
4.2. Interface Connector
The interface connector on the SH1 is a 6-pin HRS female connector
(HR10A-7R-6SB(73)). The pin descriptions are as follows:
Pin Description
1 Monitor Opto Anode
2 Solenoid
3 Solenoid
4 Monitor Opto Cathode
5 Monitor Opto Emitter
6 Monitor Opto Collector
Figure 2 SH1 Controller
61

Ø1" Beam Shutter Chapter 4: Specifications
Rev E, March 16, 2020 Page 7
A schematic snippet to show the pin assignments: Typically pins 4 and 5 (cathode
and emitter) are tied to circuit ground. The anode is the anode connection of an IR
LED. This is tied to a voltage source (Vsupply) thru a current set resistor. Current
could be set to 10 mA (0.01 A), then the forward voltage for the LED is around
1.2 V. So to set the LED current the resistor value would be (Vsupply-
1.2 V)/0.01 A. The LED should be on always when the shutter is in operation.
The Collector pin is the output signal and needs a pullup resistor to an
appropriate logic supply, typically 3.3 V or 5 V. Do not use more than 5 V.

Ø1" Beam Shutter Chapter 5: Drawing
Page 8 21340-D02
Chapter 5 Drawing
5.1. SH1
1" Clear Aperture
1.035-40 (SM1) Thread Thru
4 x 4-40 Thread
8-32 Thread
8-32 Thread HR10-7R-6S
Female Receptacle
8-32 Thread
8-32 Thread
4.70"
(119.4 mm)
1.75"
(44.5 mm)
0.90"
(22.9 mm)
4.39"
(111.5 mm)
1.44"
(36.6 mm)
1.38"
(34.9 mm) 0.85"
(21.6 mm)
0.26"
(6.6 mm)
3.80"
(96.5 mm)
3.21"
(81.5 mm)
4 x 4-40 Thread
0.90"
(22.9 mm)
1.44"
(36.6 mm)
1.75"
(44.5 mm)
0.89"
(22.7 mm)
1.15"
(29.2 mm)
0.85"
(21.6 mm)
1.79"
(45.6 mm)
0.85"
(21.6 mm)
0.90"
(22.9 mm)
0.26"
(6.6 mm)
4.39"
(111.5 mm)
3.21"
(81.5 mm)

Ø1" Beam Shutter Chapter 5: Drawing
Rev E, March 16, 2020 Page 9
5.2. SH1/M
4 x 4-40 Thread 4 x 4-40 Thread
M4 Thread
M4 Thread
HR10-7R-6S
Female Receptacle
M4 Thread
1.38"
(34.9 mm)
M4 Thread
0.85"
(21.6 mm)
1.44"
(36.6 mm)
0.26"
(6.6 mm)
4.39"
(111.5 mm)
3.80"
(96.5 mm)
1" Clear Aperture
1.035-40 (SM1) Thread Thru
3.21"
(81.5 mm)
0.85"
(21.6 mm)
1.79"
(45.6 mm)
0.85"
(21.6 mm)
0.90"
(22.9 mm)
0.90"
(22.9 mm)
1.75"
(44.5 mm)
4.70"
(119.4 mm) 0.90"
(22.9 mm)
1.75"
(44.5 mm)
1.15"
(29.2 mm)
0.89"
(22.7 mm)
3.21"
(81.5 mm)
4.39"
(111.5 mm)
0.26"
(6.6 mm)
1.44"
(36.6 mm)

Ø1" Beam Shutter Chapter 6: Regulatory
Page 10 21340-D02
Chapter 6 Regulatory
As required by the WEEE (Waste Electrical and Electronic Equipment Directive)
of the European Community and the corresponding national laws, Thorlabs offers
all end users in the EC the possibility to return “end of life” units without incurring
disposal charges.
This offer is valid for Thorlabs electrical and electronic equipment:
Sold after August 13, 2005
Marked correspondingly with the crossed out
“wheelie bin” logo (see right)
Sold to a company or institute within the EC
Currently owned by a company or institute
within the EC
Still complete, not disassembled and not
contaminated
As the WEEE directive applies to self contained
operational electrical and electronic products, this end of
life take back service does not refer to other Thorlabs products, such as:
Pure OEM products, that means assemblies to be built into a unit by the
user (e.g. OEM laser driver cards)
Components
Mechanics and optics
Left over parts of units disassembled by the user (PCB’s, housings etc.).
If you wish to return a Thorlabs unit for waste recovery, please contact Thorlabs or
your nearest dealer for further information.
6.1. Waste Treatment is Your Own Responsibility
If you do not return an “end of life” unit to Thorlabs, you must hand it to a company
specialized in waste recovery. Do not dispose of the unit in a litter bin or at a public
waste disposal site.
6.2. Ecological Background
It is well known that WEEE pollutes the environment by releasing toxic products
during decomposition. The aim of the European RoHS directive is to reduce the
content of toxic substances in electronic products in the future.
The intent of the WEEE directive is to enforce the recycling of WEEE. A controlled
recycling of end of life products will thereby avoid negative impacts on the
environment.
Wheelie Bin Logo

Ø1" Beam Shutter Chapter 7: Thorlabs Worldwide Contacts
Rev E, March 16, 2020 Page 11
Chapter 7 Thorlabs Worldwide Contacts
For technical support or sales inquiries, please visit us at
www.thorlabs.com/contact for our most up-to-date contact information.
USA, Canada, and South America
Thorlabs, Inc.
UK and Ireland
Thorlabs Ltd.
Europe
Thorlabs GmbH
Scandinavia
Thorlabs Sweden AB
scandinavia@thorlabs.com
France
Thorlabs SAS
Brazil
Thorlabs Vendas de Fotônicos Ltda.
Japan
Thorlabs Japan, Inc.
China
Thorlabs China

www.thorlabs.com
This manual suits for next models
1
Table of contents
Popular Remote Control manuals by other brands

Peweta
Peweta DCF77 installation manual
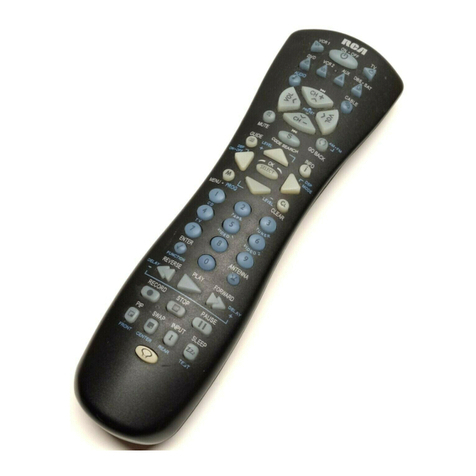
RCA
RCA D770 - D 770 Universal Remote Control Code List

Russound
Russound USRC installation manual
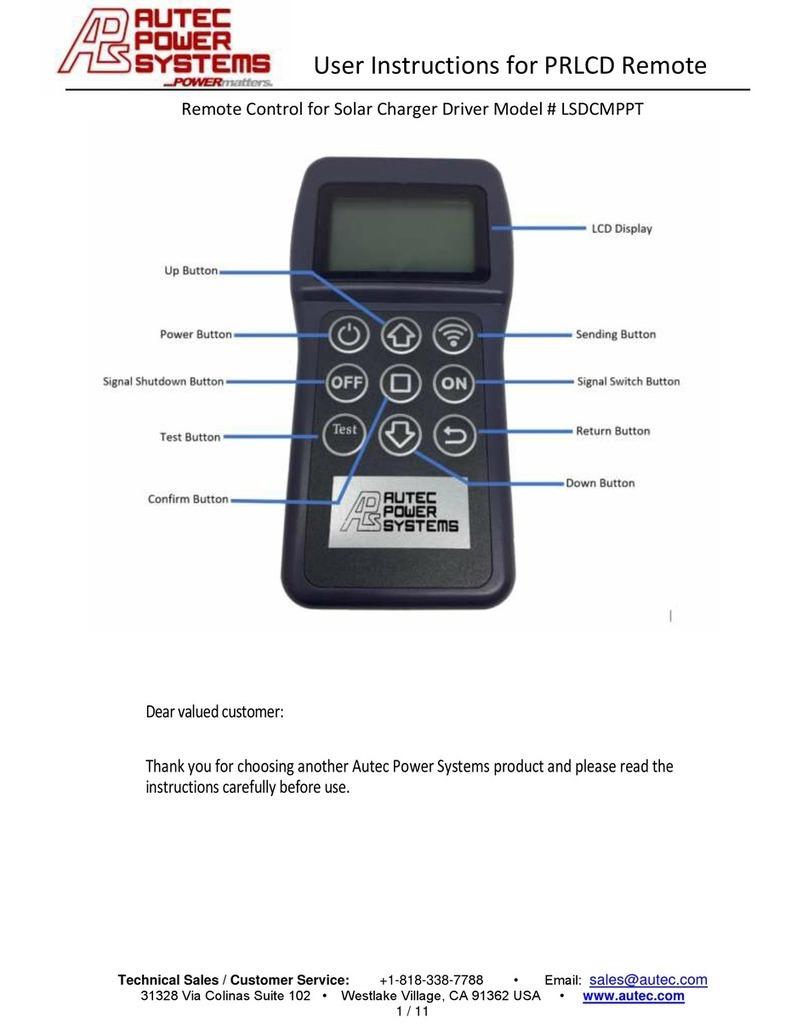
AUTEC
AUTEC LSDCMPPT User instructions
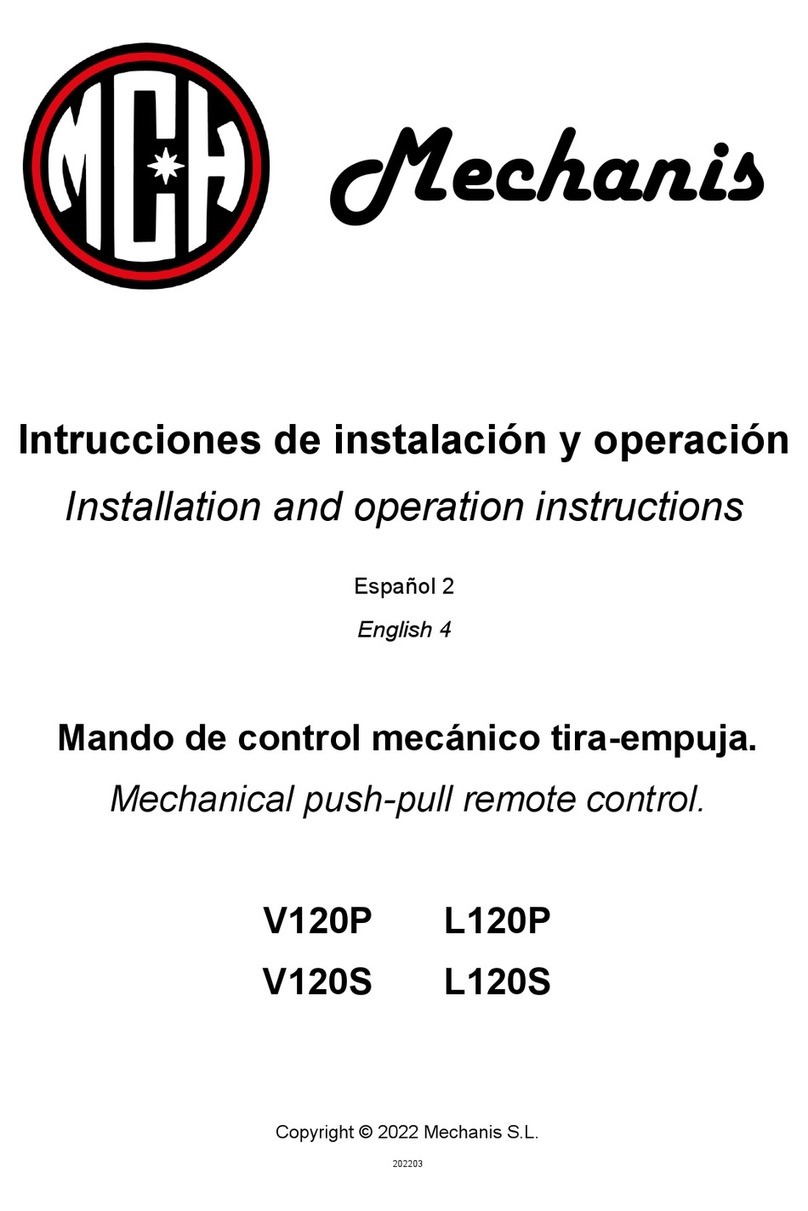
MECHANIS
MECHANIS V120P Installation & operation instructions

Horizon Hobby
Horizon Hobby Spektrum FIRMA Smart Marine ESC Series instruction manual