Time Electronics 5012 User manual

5012
Programmable
Switch
Technical Manual
Time Electronics Ltd
Unit 11 Botany Industrial Estate
Tonbridge, Kent, TN9 1RH
Tel: 01732 355993 Fax: 01732 770312
Web Site: www.TimeElectronics.co.uk
V2 26/06/03

Page 2
Contents
Page
1. Introducing the 5012 3
Installing the 5012 3
Switch connections 6
2. Specifications 8
3. Operation 10
Introduction 10
Front Panel Operation 10
Remote control via the IEEE-488 Interface Bus 10
Commands 14
Data Format Commands 16
Readback of switch settings 17
Programming example 17
4. Technical Description 18
Introduction 18
Digital Board 18
The Relay Board 19
The LED Board 19
5. Fault Diagnosis 20
Introduction 20
Fault check list 20
Fuse replacement 20
Replacement of the digital/relay or LED Boards 21
6. Spare Parts 23
Introduction 23
7. Guarantee and Servicing 24
Guarantee Period 24
Service after guarantee period 24
Returning instruments 24
All Time Electronics' instruments are subject to continuous development
and improvement and in consequence may incorporate minor detail
changes from the information contained herein.

Page 3
The 5012 is a microprocessor controlled, 24 channel switch which may be oper-
ated either manually or by the IEEE - 488 interface bus.
The 5012 offers a wide variety of switching solutions. Applications include A.T.E.,
production, process control and environmental monitoring.
Special relays with multi-layered contacts have been used to give the performance
needed for applications such as thermocouple measurement to current switching.
Local operation is easily performed by entering the required channel on the key-
board. The LED’s directly indicate the selected channels.
Features available in the local mode prove invaluable during system design and
for troubleshooting. The step left and right keys will move all selected channels left
or right one channel. An ‘All Off’ key will immediately turn off all selected channels
and the self test function will select each channel in turn without external bus con-
trol.
Operation over the IEEE - 488 bus is also very simple. To operate a channel just
send the number to the 5012. Again the LED’s will indicate the selected channels.
Another feature of the 5012 is the timing feature. If timing is critical in your applica-
tion, delays may be specified before a channel is turned on or off
The 5012 is constructed in a standard size 19” 2 units high metal case, suitable for
rack mounting.
Installing the 5012
This section contains information about the power requirements, fuses and instal-
lation of the instrument into a 19” rack mount frame.
Grounding Requirements
The instrument is supplied with a three conductor A.C. power lead. This lead must
be connected to a three conductor power supply that has its ground conductor
connected to an electrical earth (safety ground). The power socket and cable both
comply to IEC safety standards.
FOR CONTINUED PROTECTION AGAINST ELECTRICAL
SHOCK, ALWAYS ENSURE THAT THE INSTRUMENT IS
PROPERLY EARTHED.
Section 1 - Introducing the 5012
!

Page 4
Power Requirements
You can operate the 5012 from a single phase source rated at 100V A.C., 220V
A.C., or 240V A.C. 50/60Hz.
Line voltage may vary by up to 10% but must not exceed 250V A.C.
The power lead must be wired in accordance with the diagram below.
Be sure that the voltage setting on the instrument is correct before connecting to a
power source and that the correct fuse has been installed.
Setting the line voltage
To alter the line voltage setting, firstly remove the power lead from the instrument.
Remove the fuse holder/voltage setting cartridge from the power connector then
locate and remove the fuse holder.
Rotate until the correct voltage setting is displayed in the window.
Install the correct fuse and replace the cartridge. (800mA for 220/240V A.C. or
1.6A for 110V A.C.)
Bench Use
The instrument may be used free standing by using the tilt feet on the base.
Removal of the transit screws is not necessary.
19” Rack Mounting
Refer to Figure 1.1, removing the feet and transit screws and Figure 1.2, rear fix-
ing detail. To mount the instrument in a 19” rack you must first have the 19” rack
mount kit. (Part No 9728).
First remove the two tilt feet and two standard feet from the base of the instru-
ment.
Then remove the carrying handle.
Fix the two mounting ‘ears’ on each side of the instrument using the two fixing
holes and the 2BA screws.

Page 5
Remove the two large transit screws located on the base of the instrument.
Locate the rear support fixings as in Figure 1.2 on the rack and fix using the
screws provided.
Mount the instrument in the rack, locating the two ‘ears’ in the rear support fixings.
Fix the front panel of the unit to the frame using the screws provided.
Figure 1.1
Figure 1.2

Page 6
IEEE-488 Connection
This instrument implements the requirements of the IEEE - 488/1978 standard.
The connection is made by a standard 24 pin IEEE connector mounted on the rear
panel. The IEEE address is selected by a DIP switch again on the rear of the in-
strument as shown in Figure 1.3.
Refer to Section 3 for IEEE operations.
Switch Connections
Connections to the 5012 are made via four 37 way Cannon ‘D’ connectors.
Each connector is wired identically and has the contacts of 6 channels.
Each channel has two poles with change over contacts as shown in Figure 1.4.
When the channel is selected the relay contacts change over.
Figure 1.4
Figure 1.3

Page 7
The switch connections are identical for each connector and are detailed in Table 1.1
and figure 1.5.
Wiring details of the 37 way ‘D’ connector is shown in Figure 1.5. To wire channels 7-24,
follow the diagram replacing the appropriate channel numbers, i.e. For channels 7, 13
and 19, wire as channel 1 and for channels 8, 14 and 20, wire as channel 2, etc.
Pin 1 has been provided as a ground connection.
Pin Number Channels Pole Connection
1
2
3
4
5
6
7
8
9
10
11
12
13
14
15
16
17
18
19
20
21
22
23
24
25
26
27
28
29
30
31
32
33
34
35
36
37
N/A
1,7,13,19
1,7,13,19
1,7,13,19
2,8,14,20
2,8,14,20
2,8,14,20
3,9,15,21
3,9,15,21
3,9,15,21
4,10,16,22
4,10,16,22
4,10,16,22
5,11,17,23
5,11,17,23
5,11,17,23
6,12,18,24
6,12,18,24
6,12,18,24
1,7,13,19
1,7,13,19
1,7,13,19
2,8,14,20
2,8,14,20
2,8,14,20
3,9,15,21
3,9,15,21
3,9,15,21
4,10,16,22
4,10,16,22
4,10,16,22
5,11,17,23
5,11,17,23
5,11,17,23
6,12,18,24
6,12,18,24
6,12,18,24
N/A
1
2
2
1
2
2
1
2
2
1
2
2
1
2
2
1
2
2
1
1
2
1
1
2
1
1
2
1
1
2
1
1
2
1
1
2
CHASSIS
COM
N.O.
N.C.
COM
N.O.
N.C.
COM
N.O.
N.C.
COM
N.O.
N.C.
COM
N.O.
N.C.
COM
N.O.
N.C.
N.O.
N.C.
COM
N.O.
N.C.
COM
N.O.
N.C.
COM
N.O.
N.C.
COM
N.O.
N.C.
COM
N.O.
N.C.
COM
Figure 1.5
Table 1.1

Page 8
Section 2 - Specifications
Interface
Interface Type: IEEE-488/GPIB/HPIB
Device Address: Rear panel switch 0-31
Bus Connection: Standard 24 pin IEEE-4888 connector
Bus Isolation: All switches are isolated from the bus up to
350V.
Switch Specification
Type: 24 way double pole changeover, break before
make.
Contact Res: <40mΩper switch
Contacts: Gold Layer
Operation Time: 20 milli seconds
Operating Life: Up to 200 million operations
Connections: Four 37 way ‘D’ connectors
Rating: 1 Amp @ 30VDC (100VAC)
Thermal EMF’S: Less than 5uV per switch
General Specification
Power Supply: 110V, 220V or 240V A.C. 50/60 Hz
Dimensions: 482 x 381 x 89mm
Programming
Each switch is addressed by its physical position number as shown on the front
panel (1-24). Either a single switch or several may be selected by one command
string. The commands to each switch are separated by a semicolon (;) and the de-
lay option specified by ‘/X/Y’ where ‘X’ is the turn on delay and ‘Y’ is the turn off de-
lay, both in 1/10ths of a second. The complete command string is terminated by ei-
ther a carriage return (CR) or line feed (LF).

Page 9
Program Modes
Decimal:
Switches to be turned on are specified by decimal commands. All other switches
are turned off.
Memory +:
Switches to be turned on are specified by a positive decimal command. All other
switches remain unchanged.
Memory-:
Switches to be turned off specified as a negative decimal command. All other
switches remain unchanged.
Delay Option:
Delays the decimal, memory + or - commands by a specified amount (0.1s -
25s). On and Off delays are specified separately.
Hexadecimal:
Turn on switches by a hexadecimal string. All others turn off.
G.E.T.:
Sets the 5012 to execute commands after the Group Execute Trigger command
has been received.
Goto Local:
Sets the 5012 into local mode for operation via the front panel.
Transmit Local:
Instructs the 5012 to send back all its settings.

Page 10
Section 3 - Operation
Introduction
The 5012 may be operated in either local or remote modes which is invaluable dur-
ing system design or troubleshooting.
The LED’s on the front panel indicate which channel has been selected. The data
LED will indicate when a command has been received by the IEEE interface or if a
key has been pressed in local mode. A bleep will also be heard when a key has
been pressed.
The 5012 is put into remote mode whenever a valid command is received by the
IEEE Bus. To return control to the front panel, press the Local key.
Front Panel Operation
By using the keypad, any channel may be turned on or off with just a few key
presses.
For example - To turn switches 1 and 22 on, press ‘1’ and ‘ADD+’ for switch 1
then ‘22’ and ‘ADD+’ for switch 22. The LED’s will show that these channels have
been selected.
To turn switch 1 off, leaving 22 on, press ‘1’ and ‘SUB-’. Alternatively to turn all
switches off press the ‘ALL OFF’ key.
If a mistake is made during numeric entry press the cancel key.
If the channel keyed in is invalid, the unit will give a long beep.
The step keys may be used to repeatedly step all the channels selected up or
down one place.
Pressing the ‘Self Test’ Key will initiate the self test sequence. This will step
through each channel, energising the relay and also indicating the channel se-
lected on the front panel.
The Local key will return control back to the front panel when under remote control.
The Reset key will reset the relays, IEEE interface and processor.
Remote Control Via The IEEE - 488 Interface Bus
Computer control of the 5012 via the IEEE interface is both simple and efficient.
A host of features becomes available under remote control.
Single letter or number commands will select or deselect channels, read back
which channels have been selected or set delays between relays operating.
The IEEE - 488 Interface Bus
The IEEE - 488 interface, sometimes called GPIB (General Purpose Interface Bus)
or the HPIB (Hewlett Packard Interface Bus) allows remote control of the instru-
ment by a suitable computer or controller.

Page 11
The 5012 is compatible with the IEEE - 488 (1978) interface bus.
The IEEE - 488 standard defines a complete interface system for the interconnec-
tion of instruments and computers using a bit parallel, byte serial bi-directional
bus. Protocols, connections and cables are also defined, enabling computer con-
trolled systems to be quickly realized.
The main limitations of the IEEE are:-
1) A maximum of 15 devices on the bus.
2) The maximum bus length should not be greater than 20m or number of de-
vices x 2, which ever is the shorter.
Data Transfer and Device Addressing
Before a controller can send data it has to identify the recipient. Each device on
the IEEE is given an address to which it will respond when called by the control-
ler, in this way data can be transferred between selected devices in an orderly
manner.
The rate at which data is transferred is controlled by hand shake signals, the
speed being governed by the slowest device active on the bus.
Set baud rates are therefore unnecessary with this system.
IEEE Cables
The IEEE - 488 cable contains 24 wires terminated at both ends with identical
plug/sockets which allow for daisy-chaining of additional cables to extend the bus.
Cables used on IEEE systems are available in various lengths to suit different
layouts.
IEC Bus Connections
Users wishing to connect the 5012 to a European standard bus (IEC-625), must
be aware of the differences in connector pin assignments from the IEEE bus and
provide a suitable interface.
Table 3.1 (overleaf) compares the pin designations for each standard.

Page 12
PIN NUMBER
1
2
3
4
5
6
7
8
9
10
11
12
13
14
15
16
17
18
19
20
21
22
23
24
IEEE-488
STANDARD
FUNCTION
DIO1
DIO 2
DIO 3
DIO 4
EOI
DAV
NRFD
NDAC
IFC
SRQ
ATN
SHIELD
DIO 5
DIO 6
DIO 7
DIO 8
REN
GND 6
GND 7
GND 8
GND 9
GND 10
GND 11
LOGIC GND
IEC-625
FUNCTION
DIO 1
DIO 2
DIO 3
DIO 4
REN
EOI
DAV
NRFD
NDAC
IFC
SRQ
ATN
SHIELD
DIO 5
DIO 6
DIO 7
DIO 8
GND 5
GND 6
GND 7
GND 8
GND 9
GND 10
GND 11
Table 3.1
IEEE Connector
The pin connections and dimensions of the IEEE connector are illustrated in
Figure 3.1 and in Table 3.1. Figure 3.2 illustrates the connections.
Figure 3.2
Figure 3.1

Page 13
IEEE Address Section
Before operating the DMM over the IEEE bus, set the address on the rear of the
unit to the required address and operating mode.
Address 31 is used to select self test mode.
The first five switches set the IEEE address and the last three switches are used
to select the instruments operation mode. The last three switches are normally set
off but may be used as follows:
Switch 6 - Disable IEEE talk (transmit) mode.
Switch 7 - Disable IEEE listen (receive) mode.
Switch 8 - Dual Primary Addressing mode. In this mode, the unit will respond to
two primary addresses differing only in the least significant bit. For example, if the
unit address selection switches are set for an address of 8, the unit will also re-
spond to address 9.
NOTE: The instrument only reads the address switch upon power up. Therefore if
the IEEE address is changed it will be necessary to switch the unit off and on
again.
The 5012 may be made to display its IEEE address from the front panel by enter-
ing ‘99’ on the keypad. This will display the DIP switch positions on LED’s 1 to 8.
Local/Remote Operation
The 5012 is switched into remote operation when a valid command is received on
the IEEE bus. The unit will remain in remote control until the LOCAL key is
pressed from the front panel, the local command has been received by the IEEE
or until the unit is switched off.
Interface Clear Command - IFC
This command initiates a complete reset of the unit, which is then unable to re-
spond to any further IEEE commands for 1 second.
IEEE Command Format
IEEE commands are comprised of characters from the ASCII set. A series of com-
mands can be used to simulate the manual operation of the unit.
The commands must be in one of the following formats:
1) A single upper case character (A to Z).
2) An upper case character followed by a number.

Page 14
Commands may be sent individually or built into a string separated with a slash
character (/).
A command string may take the form of -
Terminator Character
IOCTL #2, "1; 3; 4" + CHR$ (13)
Controller Specific Command 5012 Command String
The controller specific command is an instruction to the IEEE controller to read or
write the following string to the device on the bus. This command may vary con-
siderably between controllers and the example shown is a typical QuickBasic lan-
guage by Microsoft command. Refer to your IEEE controller for specific com-
mands.
The 5012 command string consists of commands from the 5012 Instruction set.
These commands will instruct the 5012 to select a channel or other function.
Terminating Character
All command strings must end with a terminator character for the string to exe-
cute. This may be either a line feed or carriage return character as set by the O1,
O12, O2 or O21 command.
IEEE Command Execution
Before and IEEE command can be executed the following conditions must be
met.
1) The IEEE address and the talk/listen switches set correctly on the rear panel
switch.
2) The command must be a valid command (invalid commands are ignored).
3) The command must be followed by a valid terminator character.
Commands
There are two formats for sending programming instructions to the unit.
Decimal Programming
The unit is programmed by sending the switch numbers which are to be operated.
In the simplest form, the numbers are sent separately by semicolons and the new
settings will over write the old settings.
i.e.- 100 IOCTL #2, "1;4;8;21"+CHR$ (13)
This will set switches 1, 4, 8 and 21 on and all the rest off.

Page 15
The switches can be operated without affecting the current settings by adding a
‘+’ or ‘-’ sign before sending the switch settings. If for example switches 1, 4, 8,
and 21 are currently on the command string:
100 IOCTL #2, " - 1; + 6; + 22 " + CHR$ (13)
will turn switch 1 off and 6 and 22 on, leaving all the other switches the un-
changed. Therefore after this command, switches 4, 6, 8, and 22 are all on.
If the timing of the operations is critical, delays can be specified in the command
string. The delay may be specified in multiples of 100ms.
For example, if switches 1, 2, 3, 24 are currently switched on:
100 IOCTL #2, " - 1; +23 / 10 / 20"
This command will turn switch 1 off in 1 seconds time from the command being
received and turn switch 23 on in 2 seconds time.
The slash ‘/’ figure indicates a delay and the delay value follows respectively. A
maximum delay of 25 seconds may be set. If an on delay only is to be set, an off
delay of zero must still be specified.
100 IOCTL #2, " - 1; - 2 / 25"
Which will turn switch 1 and 2 off in 2.5 seconds.
100 IOCTL #2, " - 1; + 7 / 0 / 2"
Which will turn off switch 1 now and turn 7 on in 0.2 seconds.
Hexadecimal Programming
By sending a string of six characters any pattern of relays can be set.
The Characters 0-9 and A-F (i.e. Hexadecimal) are used to set the relay combina-
tions in blocks of 4 relays.
In Table 3.2 W, X, Y and Z make up the block of four relays. W is the highest re-
lay and Z the lowest.
For example, if the first hexadecimal character was to be sent it would apply to the
first block of four, relays 24-21, W being relay 24 and Z being relay 21.
CHARACTER 1st 2nd 3rd 4th 5th 6th
RELAYS 24-21 20-17 16-13 12-9 8-5 4-1

Page 16
CHARACTER RELAYS OPERATED
SENT
W X Y Z
0 0 0 0 0
1 0 0 0 1
2 0 0 1 0
3 0 0 1 1
4 0 1 0 0
5 0 1 0 1
6 0 1 1 0
7 0 1 1 1
8 1 0 0 0
9 1 0 0 1
A 1 0 1 0
B 1 0 1 1
C 1 1 0 0
D 1 1 0 1
E 1 1 1 0
F 1 1 1 1
For example the following line would operate relays 1, 2 and 24.
100 IOCTL #2, "800003" + CHR$ (13)
If a terminator character is not received, the unit will ignore all subsequent com-
mands until the termination character has been transmitted.
If an illegal character is received it will be ignored.
Data Format Commands
There are a number of commands to change the format of data the unit receives
and transmits.
Table 3.2
CHARACTERS SENT EFFECT
l1 Change to Hexadecimal input mode
l2 Change to decimal mode (Default)
G1 Execute commands after G.E.T., <CR> or <LF>
G2 Execute commands after <CR> or <LF> only
L Enter Local mode
T Transmit the relay settings
O1 Terminate transmit and receive strings with <CR>
O2 Terminate transmit and receive strings with <LF>
O12 Terminate transmit and receive strings with <CR><LF>
O21 Terminate transmit and receive strings with <LF><CR>
Table 3.3

Page 17
Group Execute Trigger
In this mode of operation, the entered data is stored until a Group Execute Trig-
ger (G.E.T.) command is received. In this way, several instruments on the bus
can be made to respond simultaneously.
To select Group Execute Trigger mode send G1 to the unit. To return to immedi-
ate mode, send data G2 to the instrument.
Readback of Switch Settings
The settings of the switches may be read back from the unit via the IEEE bus.
The settings are in hexadecimal format and are terminated with the character de-
fined by the ‘O’ command.
To read back the switch settings, the ‘T’ command is sent.
Programming Example
The following simple demonstration program has been written in Microsoft’ Quick-
Basic.
The following program will allow the operator to send a number to the 5012 which
can switch a relay on or off. Delays can also be specified and the switch settings
may be read back.
100 REM *** 5012 IEEE CONTROL DEMO PROGRAM
200 OPEN "IEEECTRL" FOR RANDOM AS #1 'Open Control File
210 OPEN "IEEEDATA" FOR RANDOM AS #2 'Open Data File
220 T$ = CHR$ (13) + CHR$ (10) 'Set the terminator character
230 CLS
240 INPUT "Enter IEEE Address of 5012 ";IE$ 'Select IEEE address
250 IOCTL #1, IE$ 'Send IEEE address
300 INPUT "ENTER COMMAND
(X TO EXIT, R TO READ SWITCH SETTINGS ";C$
310 IF C$ = "x" THEN END
320 IF C$ = "R" THEN GOSUB 400 : GOTO 300
330 IOCTL #2, C$ + T$ 'Send command to IEEE
340 GOTO 300 'Transmit switch settings
410 FOR DLY = 1 TO 1000 : NEXT DLY Delay
420 R$ = IOCTL$ (2) 'Readback from IEEE
430 PRINT R$ 'Display Readings
440 RETURN

Page 18
Section 4 - Technical Description
Introduction
This section is a brief introduction to the technical description of the 5012.
The 5012 consists of four boards with plug in modules. -
The Digital Board
The Relay Boards. (2 off)
The LED Display Board
Digital Board
This board can be examined in three sections.
PSU Section
The transformer has three primary tappings on one winding and three secondary
windings, of which one is centre tapped. One side of the 110V and 9V windings are
taken to a common reference point and then to mains earth and the chassis of the
instrument. The 22V-0V-22V winding has its centre tap taken to earth via a neon
and capacitor. This will ensure that the 0V line does not drift above approximately
90V but still remains isolated from the other supplies.
The power supply section supplies five outputs. It has two unregulated supplies ;
+10V and an unregulated +5V supply which may be pulsed up to 12V for latching
relays. A regulated +5V supply is derived for the TTL circuits.
A regulated +15V/0V/-15V output is also supplied from the separate 22V-0V-22V
winding. These supplies are not used in the 5012.
Both the +5V and +15V/-15V supplies have zener protection in case of over volt-
age.
Processor Section
The heart of the unit is the 6802 processor with its support I.C.’s. The main ROM is
a 128k device, the 27128.
The board has 64k of RAM, (the 6264) for processor operation.
32 lines of I/O provided by two 68A21 Peripheral Interface Adaptors connected to
the uP bus. These lines are used to select the relay channels.
A stall circuit will reset the board if the processor hangs and stops the PIA giving a
low frequency pulse from its CA2 output.
Additional address decoding is used to select the IEEE chip, RAM, ROM, etc.
The membrane keyboard is read by an encoder, I.C.19, a 74LS923 addressed by
IC8.
An additional PIA is used to provide the processor with information of installed op-
tions.

Page 19
The IEEE Interface
The IEEE interface section is built around the Motorola 68488 General Purpose
Interface Adapter (GPIA). The I/O lines of the 68488 are driven through MC3448
drivers. IEEE address selection is by an 8 digit switch whose condition is gated to
the uP bus via a 74LS244 tristate buffer, I.C. 17.
The Relay Board
Both relay boards are identical in respect of their operation. However a connector
is relocated between boards to obtain two banks of twelve relays.
The relays are turned on or off by the PIA lines from the digital board via a
ULN2803 buffer I.C.
The LED Board
The LED’s are driven directly by the PIA lines via current limiting resistor networks.
Also the local LED is driven by a spare PIA line.

Page 20
Section 5 - Fault Diagnosis
Operations involve removal of the top cover. Before proceeding,
ensure that the mains supply and any inputs have been discon-
nected. Failure to do so may expose live terminals and present
an electric shock hazard.
Introduction
This section gives details of some possible problems and how to correct them.
Spare parts are available from Time Electronics and are listed in Section 6.
If the fault is not listed or if parts required are not listed, please enquire quoting in-
strument type and serial number.
Fault Check List
If the unit is completely dead with no front panel lights, check the following:
1) Mains supply.
2) Mains fuse blown in plug.
3) Mains fuses blown in appliance inlet.
4) Internal fuses have blown. (See fuse replacement).
The unit responds to manual controls but not to IEEE operation.
1) Defective IEEE cable.
2) Incorrect IEEE cable.
3) Incorrect terminator characters.
4) Incorrect IEEE commands.
The unit powers up but operates incorrectly.
1) Run the self test.
The 5012 occasionally resets to power on state.
1) Excessive mains interference is causing the uP to stop. The watchdog circuit
is causing the reset. Add additional mains filtering.
Fuse Replacement
The 5012 has three types of fuse fitted. The mains fuse must be of the 20mm,
HBC, Sand filled and ceramic body type.
The internal D.C. supplies have two 1A, 20mm anti-surge for the +15V and –15V
rails and two 2A, 20mm semi-delay (type T) fuses for the 5V and 5/12V rail.
Replacement of the mains fuse.
The main fuse is located in the mains inlet socket. To replace this fuse, first re-
move the power lead from the instrument.
Remove the fuse holder / voltage setting cartridge from the power connector, then
locate and remove the fuse holder.
Install the correct fuse and replace the cartridge. (800mA for 220V/240V A.C. or
1.6A for 110V A.C.)
!
Table of contents
Popular Switch manuals by other brands

Cisco
Cisco HyperSwitch A100 user guide
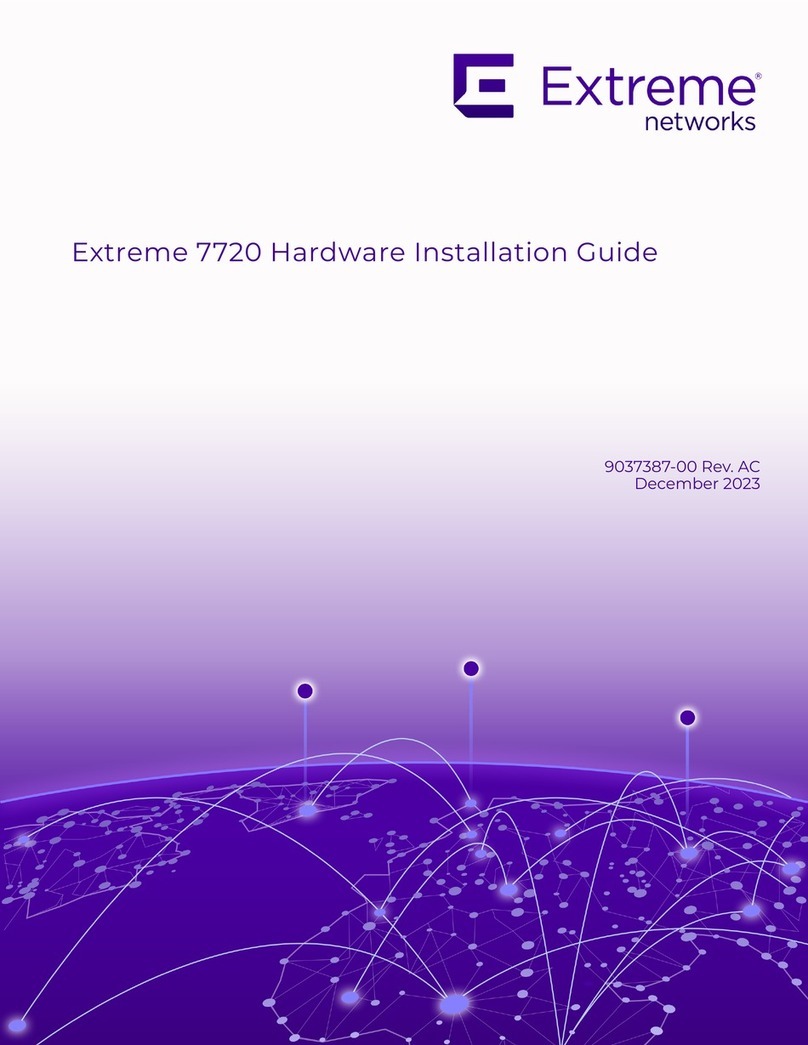
Extreme Networks
Extreme Networks 7720 installation guide
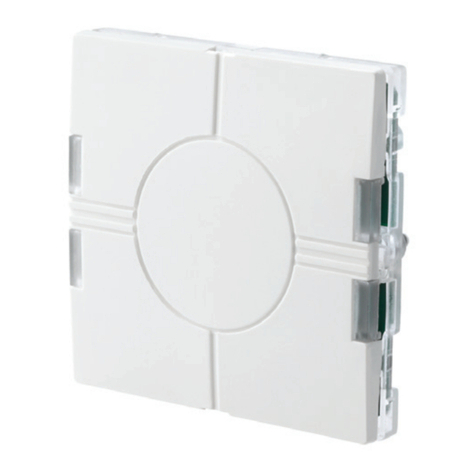
CARLO GAVAZZI
CARLO GAVAZZI SHE5XWLS4BF instruction manual
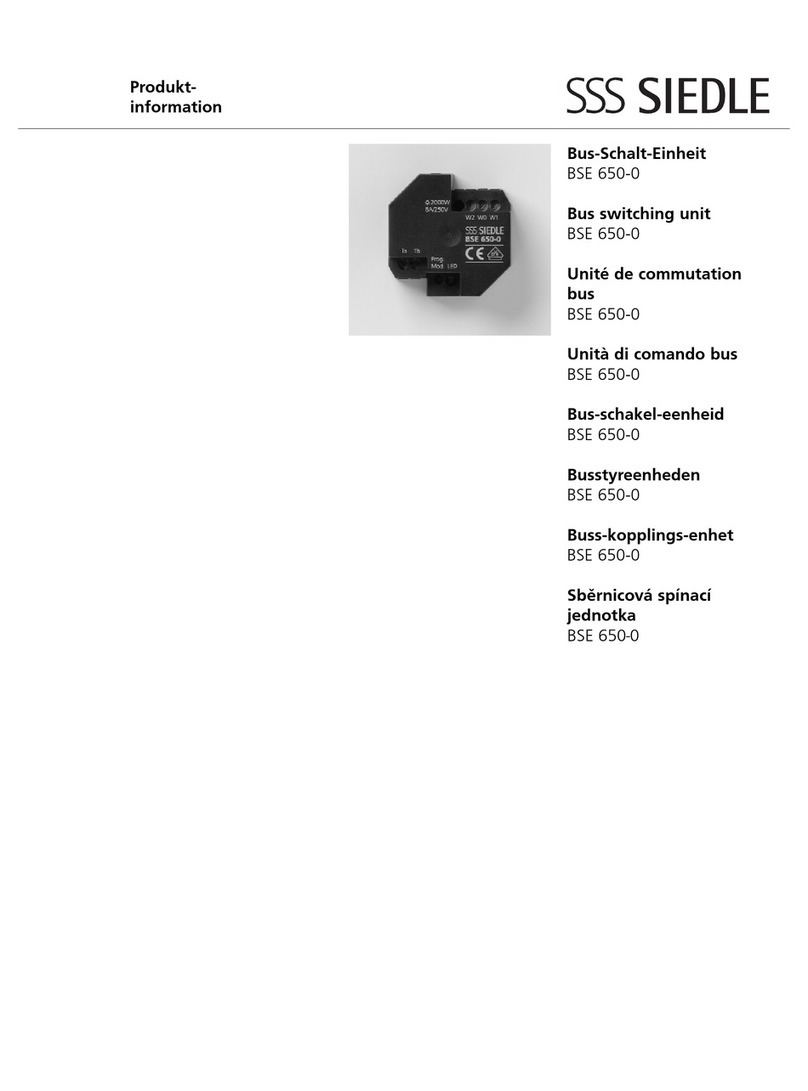
SSS Siedle
SSS Siedle SIEDLE BSE 650-0 Product information
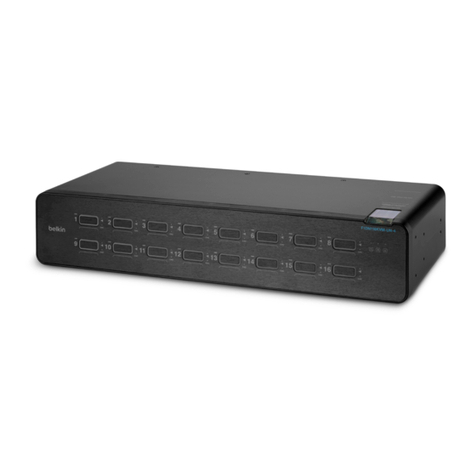
Belkin
Belkin F1DN116KVM-UN-4 Quick installation guide
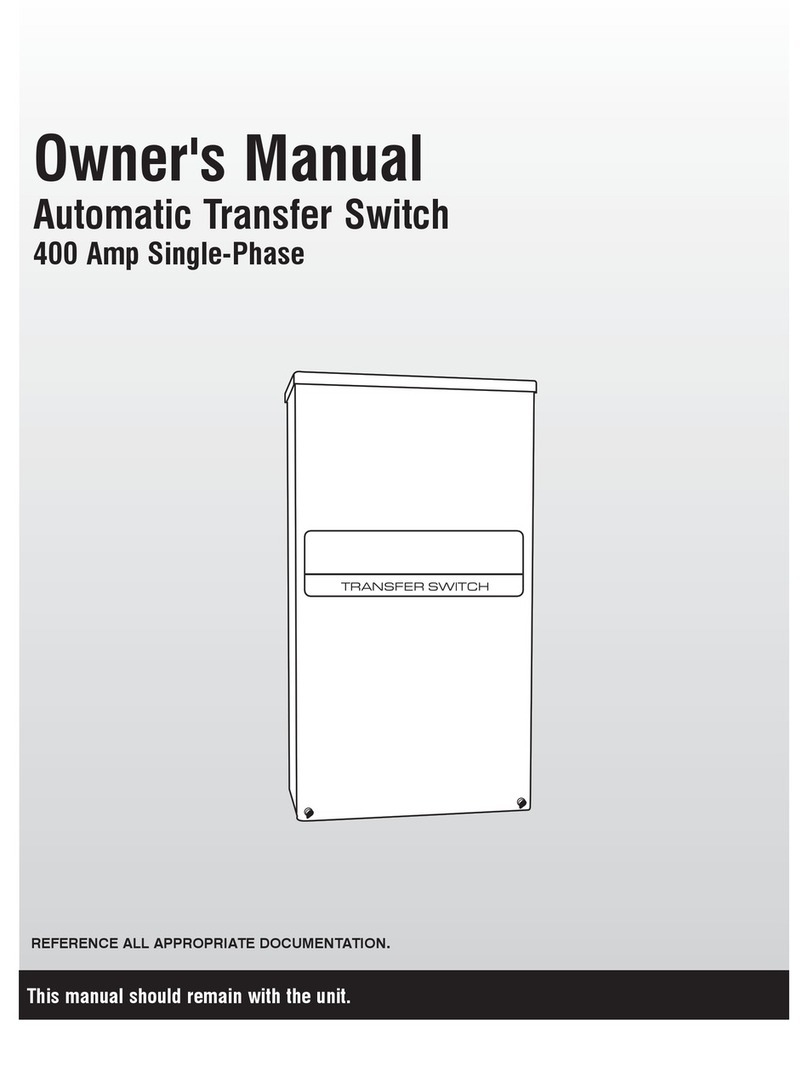
Generac Power Systems
Generac Power Systems Automatic Transfer Switch owner's manual