Timpdon Electronics GPRX7 User manual

Timpdon Electronics Tel: 0161 980 7804 Issue 1 — February 2018
www.timpdon. o.uk Page 12 of 12
User Notes
Timpdon Electronics Tel: 0161 980 7804 Issue 1 — February 2018
www.timpdon. o.uk Page 1 of 12
GigaRad Radio Points System
Point Controller
Model GPRX7
Timpdon
Electronics
This advanced 2.4 GHz GigaRad Radio
Receiver/Controller is designed to be used
with a GigaRad GPTX10 transmitter only, as
art of a com lete GigaRad Radio Points
System.
It is designed for the radio control of a single
oint using a standard RC servo as the oint
motor, and has two additional switched
out uts for the automatic control of interlinked
colour light or sema hore signals.
The controller may be user rogrammed,
in-situ for:
•
Allocation to any one of twelve oint
numbers, each individually controllable
from the GPTX10.
•
Point set and reset servo ositions.
The servo rotation rate is re- rogrammed to
give realistic slow s eed oint o eration.
It com lies fully with all UK legislation for
licence free o eration.
Specification
Frequency 2.4 GHz Radio Control Model Band
RF Sensitivity -94 dBm
Modulation Gaussian Frequency Shift Keying
Range U to 100 metres with a GigaRad GPTX10
transmitter, in a normal model railway or
garden environment
Size 47 mm [over ins] x 35 mm x 11 mm
Power Su ly 4.8 V to 6V d.c. battery su ly

Timpdon Electronics Tel: 0161 980 7804 Issue 1 — February 2018
www.timpdon. o.uk Page 2 of 12
Introduction
The GPRX7 com rises a 2.4 GHz Gigarad radio receiver and oint
controller within a single ackage.
The receiver will o erate only with any GigaRad GPTX10 Point
Control transmitter and, during setu , is bound to a s ecific
transmitter, such that it will res ond only to transmissions from that
transmitter. It may be re-bound by the user to another transmitter at
any time.
The out ut from the GPRX7 is a standard servo control PWM signal,
with two user rogrammable stable ositions [Set and Reset] and a
controlled rotation rate between these two ositions.
The activation of the servo out ut can be user rogrammed to res ond
to the activation of any one of the twelve available oint number
channels on the transmitter.
In addition, the GPRX7 has two additional switched auxiliary out uts for
the automatic control of interlinked colour light or sema hore signals.
Principles of Operation
The GPRX7 is designed to use any standard RC servo as a oint motor,
with movement of the oint blades controlled directly by the servo arm,
rotating over a small angle between two fixed ositions, Set and Reset.
Point setting is controlled by any one of the twelve transmitter
channels, selected by a rotary switch, and a single air of Set and
Reset switches.
Both the Set and Reset ositions of the servo are user rogrammable
from the transmitter, o erating in a s ecial calibration mode.
Point Servo
Me hani al Linkage
Stress Relief
[See Text]
Timpdon Electronics Tel: 0161 980 7804 Issue 1 — February 2018
www.timpdon. o.uk Page 11 of 12
User Notes

Timpdon Electronics Tel: 0161 980 7804 Issue 1 — February 2018
www.timpdon. o.uk Page 10 of 12
Auxiliar Outputs
Continued
Semaphore Signals
The Red and black wires su ly +5V ower to the SCS1, and the
Blue or Green wire is the trigger in ut.
Timpdon Electronics Tel: 0161 980 7804 Issue 1 — February 2018
www.timpdon. o.uk Page 3 of 12
The maximum rogrammable rotation angle of the servo is constrained
to a roximately 25°, centred around the nominal servo centre osition,
corres onding to a PWM ulse width of 1.5 ms. This will give a linear
oint blade movement of a roximately 5 mm, when connected by a 12
mm servo arm, adequate for most track. If greater travel is required, a
longer servo arm may be used.
The rotation rate of the servo arm during o eration is automatically
controlled by the GPRX7 to give a realistic rototy ical rotation eriod
of a roximately 1.7 seconds for the maximum 25° rotation, and ro-
rata for smaller angles.
To minimise the load on the servo motor when the oint is locked in
either end osition, you are strongly recommended to fit a stress relief
omega loop or Z bend in the connecting linkage between the servo
and the oint mechanism. You are also recommended to remove any
built-in sna action oint locking mechanism.
Binding and Point Number Allocation
Before use, the GPRX7 must be bound to the transmitter with which it
is to be used, and allocated to a s ecific point number in the range 1
to 12. Once bound, this rocess need not be re eated unless you wish
to use a different transmitter, or change the allocated oint number.
All binding and point number allocation rocedures are undertaken
from the transmitter, and no access to the receiver is required. Refer to
the user manual of your GigaRad GPRX10 transmitter for binding and
oint number allocation instructions.
This manual is available for download from the Tim don Electronics
website.
Wiring and Connections
4.8 to 6 V d. .
Power Supply
GPRX7
GigaRad
Point
Controller
LED
Bla k
Red
Bla k
Red
Yellow
Power
Point
Servo
Yellow [or White] lead this end
Bla k [or Brown] lead this end
Point Servo
Set
Output
Reset
Output
Bla k
Blue
Bla k
Red
Red
Green
To Set Signal
To Reset Signal
See below for details of
connections to auxiliary
signal out uts.

Timpdon Electronics Tel: 0161 980 7804 Issue 1 — February 2018
www.timpdon. o.uk Page 4 of 12
Notes on Wiring and Connections
1 Connect the servo via its 3 wire lug directly to the GPRX7 Point
Servo connector. Ensure that you observe the correct olarity.
2 Connect a d.c. su ly to the GPRX7 Power connector. Ensure
that you observe the correct olarity. The su ly voltage must be
between 4.8 V and 6 V nominal, to match the o erating voltage
limits of standard servos.
The oint system will only draw significant current while the servo
is in motion, so 4 x AA rimary or rechargeable batteries are
erfectly adequate, and should give reasonable battery life.
You are recommended to switch off or disconnect the battery
su ly when your layout is not in use, to avoid draining the
batteries unnecessarily.
3 Before use, the GPRX7 must be bound to your transmitter, as
described above, allocated to a s ecific point number and
rogrammed for servo rotation angles. The calibration
rocedure is described below.
Servo Mounting and Calibration
For o timum erformance and ease of calibration you are strongly
recommended to follow the guidelines given here for servo mounting
and set u .
Operating linkage at 90
degrees to straight tra k
Servo arm parallel
to straight tra k
Point Blades in
Mid Position
Timpdon Electronics Tel: 0161 980 7804 Issue 1 — February 2018
www.timpdon. o.uk Page 9 of 12
Auxiliar Outputs
Each auxiliary out ut is an active low voltage source, switching between
+5V [ igh] and 0V [Low], with a maximum current rating of 20 mA er
out ut.
Each auxiliary out ut can therefore drive LEDs directly for colour light
signalling or, when used to trigger an external Timpdon Electronics
ServoSwitch, Model SCS1, will o erate a servo controlled sema hore
signal arm.
Auxiliar Output Wiring Diagrams
Colour Light Signals
Green Clear signal only on each Auxiliary Output
Green Clear signal and Red Danger signal on
Each Auxiliary Output
Each LED requires a current limiting resistor in series. A value of
470 ohm will give a LED current of about 5 mA, for both Red and
Green LEDs, adequate for most a lications.

Timpdon Electronics Tel: 0161 980 7804 Issue 1 — February 2018
www.timpdon. o.uk Page 8 of 12
Operation Timing Diagram
Timpdon Electronics Tel: 0161 980 7804 Issue 1 — February 2018
www.timpdon. o.uk Page 5 of 12
1 Mount the servo so that the oint o erating linkage will be
a roximately at 90° to the straight track when in use. At this
stage, do not connect the o erating linkage to the servo.
2 Connect the servo to the GPRX7. Power u and bind the GPRX7
to the transmitter.
The factory default settings for the GPRX7, as shi ed, are:
•
Reset Servo PWM = 1.50 ms [central]
•
Set Servo PWM = 1.55 ms [rotation angle =
a rox. 10°]
3 Set the GPTX10 transmitter for normal operation. Select the
appropriate point number, and ress and release the
transmitter Reset switch.
The servo will take u the factory default osition, corres onding
to a servo PWM ulse width of 1.50 ms — i.e. central.
Fit the servo arm to the servo so that it is parallel to the
straight track.
4 Now ress and release the transmitter Set switch, and check that
the servo arm rotates a roximately 10°. Do not worry if the
servo rotation direction is o osite to that required. This will be
corrected during calibration.
5 Return the servo to its Reset osition using the transmitter
Reset switch. Fit the o erating linkage between the oint and the
servo, and adjust its length so that the oint blades are roughly
midway between the set and reset osition, with the servo arm
ositioned as described in Ste 3.
6 This com letes the mechanical set u rocedure. You may now
roceed to calibrate the GPRX7 for final Set and Reset ositions
for the oint. All servo calibration is erformed from the
transmitter. Refer to the GPTX10 user manual for detailed
instructions.
7 You may wish to ex eriment with calibration before fitting the
oint o erating linkage described in Ste 5, in order to familiarise
yourself with the rocedure, without risking damaging the servo
by accidental mis-setting.

Timpdon Electronics Tel: 0161 980 7804 Issue 1 — February 2018
www.timpdon. o.uk Page 6 of 12
Indicator LED
At all times, the GPRX7 indicator LED shows the current o erational
status of the unit.
LED Indication Interpretation
LED Off No ower to GPRX7.
Fast Flash No valid radio ulses detected at ower
[ 5 er second ] u .
Transmitter not on, or not bound.
Very Fast Flash Bind rocedure successful.
[ 15 er second] Normal o eration.
The LED flashes once each time a valid
data acket is received from the
transmitter, normally once every 65 ms.
Slow Flash Loss of valid radio ulses following
[ 1 er second ] normal o eration.
On Power Up
On ower u of the GPRX7, the oint will remain at its current osition
until the first valid data acket has been received from the transmitter.
It will then assume the osition s ecified by the transmitter. As the
transmitter automatically remembers the last valid transmitted setting
before ower off, this will normally result in the oint remaining at its
initial ower u setting.
On loss of Radio Communication
If radio communication is lost, for any reason, during normal o eration,
the oint will remain in its last valid controlled state, until radio
communication is restored or until ower is removed from the GPRX7
and re-a lied.
Timpdon Electronics Tel: 0161 980 7804 Issue 1 — February 2018
www.timpdon. o.uk Page 7 of 12
Auxiliar Output Operation
Once calibrated, the GPRX7 will change the state of the controlled oint
in accordance with the transmitted Set and Reset instructions for that
oint.
In addition, however, it will change the state of the Set and Reset
auxiliary outputs to corres ond to the point setting, to ermit
automatic o eration of signals associated with the oint.
Both of these out uts are active low - that is to say they generate a
voltage of +5V [ igh] when inactive, and a voltage of 0V [Low] when
active. This ermits each auxiliary out ut to drive either a LED, for a
colour light signal, or an external Timpdon Electronics ServoSwitch,
model SCS1, to control a further servo for a semaphore signal. Wiring
diagrams for each ty e of signal are given below.
To ermit realistic automatic control of both signals and oints, the
order of o eration, for both Point Set and Point Reset is:
Point Set
•
The Reset auxiliary output is immediately switched to igh =
Danger.
•
After a 1 second delay, the point starts to move to the Set
osition.
•
Once the point has reached the Set osition, the Set auxiliary
output is switched to Low = Clear, after a further 1 second
delay.
Point Reset
•
The Set auxiliary output is immediately switched to igh =
Danger.
•
After a 1 second delay, the point starts to move to the Reset
Position.
•
Once the point has reached the Reset osition, the Reset
auxiliary output is switched to Low = Clear, after a further
1 second delay.
The timing diagram for both directions of o eration is shown below.
Note that once a Set or Reset command has been issued by the transmitter, the
com lete sequence described above will be erformed. If a further transmission,
for the opposite setting, is made before com letion, the initial sequence will first
be com leted and then, after a delay of 1 second, the o osite sequence will be
initiated.
Table of contents
Other Timpdon Electronics Controllers manuals
Popular Controllers manuals by other brands
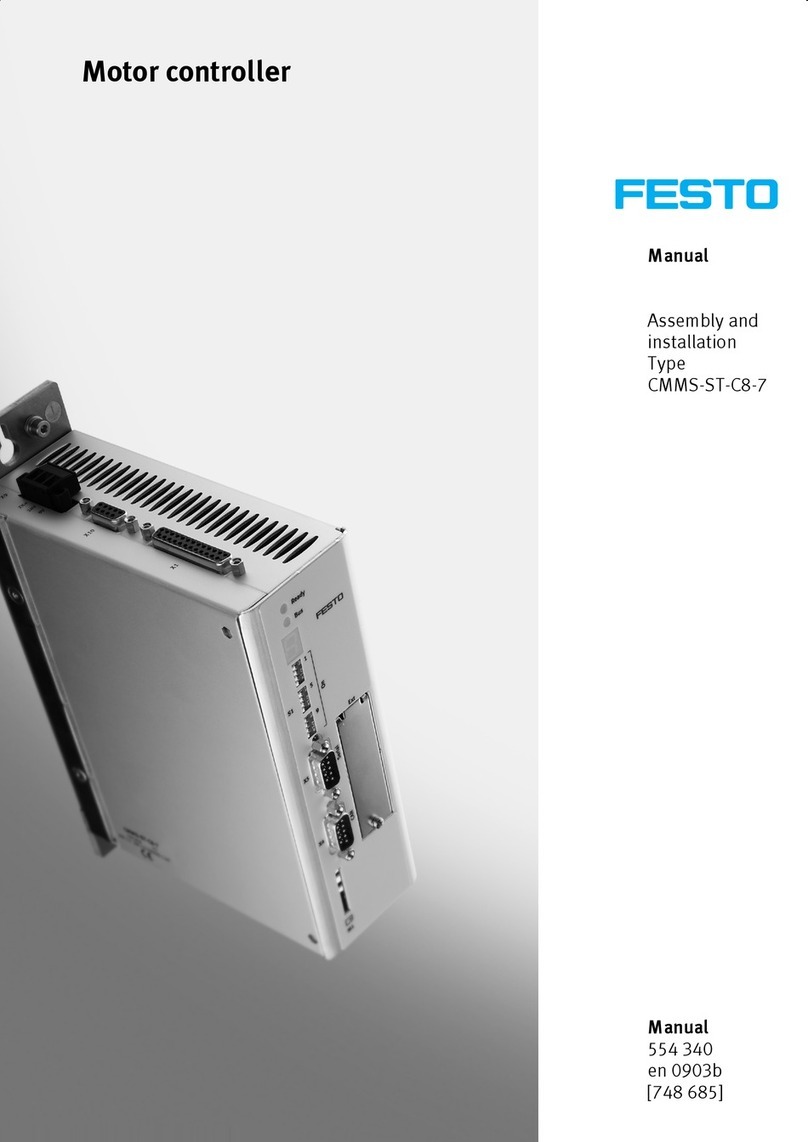
Festo
Festo CMMS-ST-C8-7 Assembly and installation
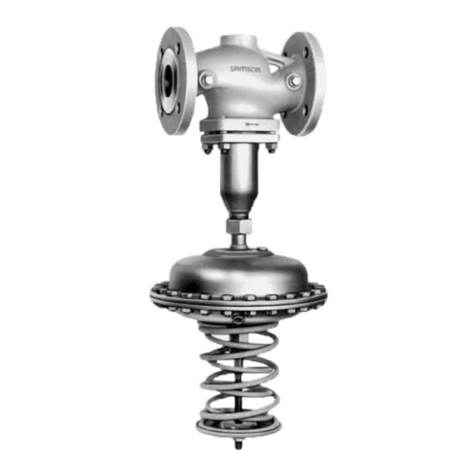
Samson
Samson 42-24 Mounting and operating instructions
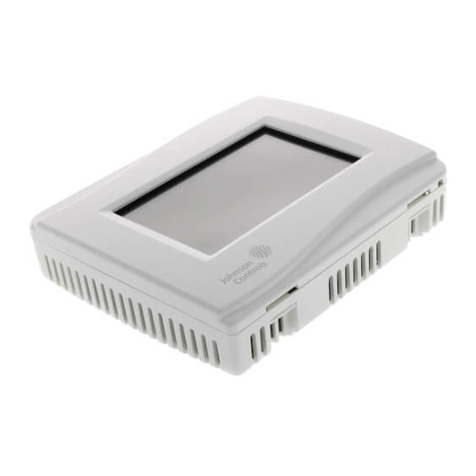
Johnson Controls
Johnson Controls TEC3310 installation instructions
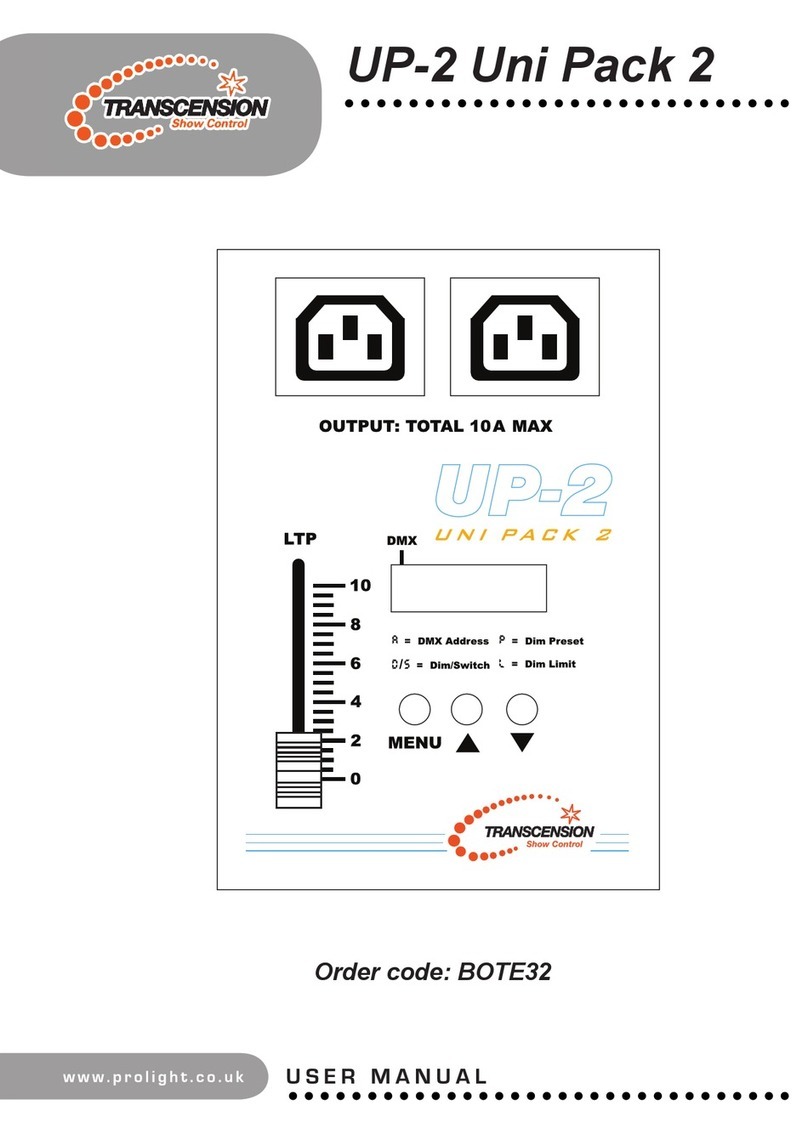
Transcension
Transcension UP-2 Uni Pack 2 user manual
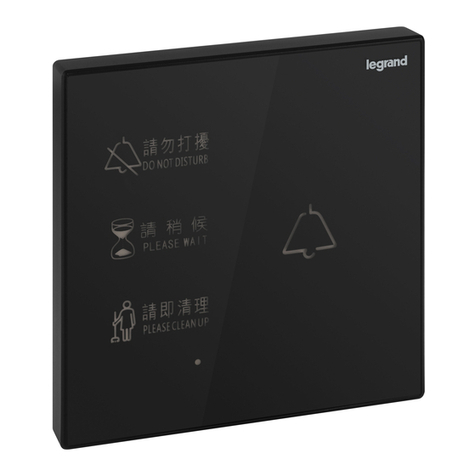
LEGRAND
LEGRAND Galion K8/H251-HK quick start guide
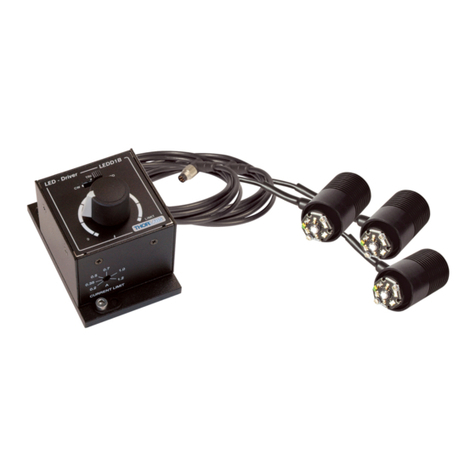
THORLABS
THORLABS T-Cube LEDD1B Operation manual