Trakka Corp Trakkabeam A800 User manual

COMPONENT MAINTENANCE MANUAL
Publication No. 051019-1 Rev H
DOCUMENT UNCONTROLLED WHEN PRINTED Page 1
33-46-00
AS9100 Certified
23-Mar-2015
Rev B
Trakkabeam® A800 Searchlight
System
Component Maintenance Manual
1. Description and Operation
A. Description
(1) The Trakkabeam®A800 airborne high intensity searchlight represents the latest in design and
development for this type of system. The searchlight can be mounted to the helicopter external
structure at any suitable position required by the operator but with reference to the Installation
Manual.
(2) The searchlight system consists of the following major assemblies:
(a) Gimbal/Lamp assembly (PN 200003-XXXXXXX).
(b) Power Conditioning Interface Unit MKII (PCIU) (PN 011012-XXXXXXX).
(c) Control Interface Unit MKII (CIU) (PN 091016-XXXXXXX).
(d) Trakka Control Panel (TCP) (PN 021019-XXXXXXX)
(e) Grip Hand Controller (PN 021012-XXXXXXX).
NOTE: Assemblies that are provided with different options are identified with part
numbers consisting of ‘base number-XXXXXXX’. Part numbers will be shown
in this way throughout the manual where they apply.
(3) Gimbal Assembly.
(a) A two axis gimbal providing both azimuth and elevation tracking is controlled by using either
one or two grip hand controllers which can be integrated with a camera system using RS422
or RS232 slaving. The main assembly utilises a worm gear and brushed DC motors together
with a simple position encoder to control each axis. All control electronics are located in the
PCIU MKII.
(b) Searchlight movement is software controlled for both elevation and azimuth to prevent
operation in unsafe regions on the aircraft. In the event of system failure, mechanical hard
stops provide a safety backup to stop movement of the searchlight.
(c) The lamp assembly consists of an 800W lamp and up to six optional filters (including IR) with
zoom capability. The light source is a short arc xenon type operating off a 12-24VDC
regulated (power controlled) supply located in the PCIU MKII.
(d) The unique Trakkabeam®quartz optical elements focus a high energy light beam with energy
spreading evenly from the centre to the outside edge to ensure the best possible search
capability while an integrated optical filter system provides a maximum of six different
coloured light beams, including infra-red. The filter elements are easily selected during flight
via the grip hand controller.
(e) When first turned on, the A800 system performs diagnostic and alignment checks in both
azimuth and elevation to find the travel envelope and when finished, will return to a pre-
defined position.
(f) The basic system layout for the A800 is shown in Figure 1 and Figure 2. These illustrate the
primary system components as well as the optional secondary grip hand controller which may
be built into the cyclic, collective, or other suitable control point inside the aircraft.
Rev H
10 Dec 2015
AIRBUS HELICOPTERS: CMM L334M6304E01 ISSUE: B PAGE 19 OF 165
The document reference is online, please check the correspondence between the online documentation and the printed version.

COMPONENT MAINTENANCE MANUAL
Publication No. 051019-1 Rev H
Page 2 DOCUMENT UNCONTROLLED WHEN PRINTED
33-46-00
AS9100 Certified
23-Mar-2015
Rev B
(4) PCIU MKII.
(a) The PCIU MKII is the central power and control hub for the entire system.
(b) The aircraft supply (28VDC) is converted and distributed to each item in the system. Lamp
power is regulated and supplied to the lamp via the 6 pin power cable. The PCIU MKII
performs all gimbal position control, filter selection, light zoom and lamp on/off control via the
26 pin control cable.
(c) The PCIU MKII also provides an interface to the grip hand controller, CIU MKII and a third
port for interfacing to third party equipment such as cameras for the purpose of slaving or
moving map outputs.
(5) CIU MKII.
(a) The CIU MKII provides grip hand controller functionality via an interface to customer supplied
switches that are joystick mounted in pilot collectives.
(b) The CIU MKII is configured for one collective, discrete inputs and provides voltage free relay
outputs to annunciate system status.
(6) TCP.
(a) The TCP provides an interface (RS-232) to the PCIU MKII (or CIU MKII if required) and also
contains discrete inputs to allow remote mounting of switches that provide the same
functionality as the front panel. There are also discrete outputs used to indicate system status
and discrete inputs to control the brightness levels of illuminated components Figure 5 shows
the TCP integrated into a searchlight system and interfaced to the grip hand controller.
(b) The panel text of the TCP uses LED backlighting and brightness is varied by the aircraft
dimming control. Panel text backlighting, annunciators and display are NVG compatible.
(7) Grip Hand Controller.
NOTE: This manual describes the basic configuration of the Trakka Searchlight. For
installation, refer to the OEM Aircraft Maintenance Manual (particularly for the
Master Power Switch).
(a) The grip hand controller provides a user interface between the A800 system and operator via
displays to indicate filter position and current system status including all switches and a
joystick to control system operation.
(b) The grip hand controller is used in conjunction with the CIU MKII and in this application is
connected into the CIU MKII although it may be connected directly to the PCIU MKII as it
contains a master power switch which is rendered inoperative when the unit is connected to
the CIU MKII. The grip hand controller may also be connected to the TCP.
Rev H
10 Dec 2015
AIRBUS HELICOPTERS: CMM L334M6304E01 ISSUE: B PAGE 20 OF 165
The document reference is online, please check the correspondence between the online documentation and the printed version.

COMPONENT MAINTENANCE MANUAL
Publication No. 051019-1 Rev H
DOCUMENT UNCONTROLLED WHEN PRINTED Page 3
33-46-00
AS9100 Certified
23-Mar-2015
Rev B
Figure 1 - Typical A800 System
Figure 2 - A800 Basic Wiring System
A418a
Pilot
Collective
CIU MKII
Grip Hand
Controller
Searchlight
Annunciator Outputs Discrete Inputs
PCIU MKII
Power Cable
Control Cable
6 Pin
Connector
26 Pin
Connector
Dovetail Mounting
Block
LPM
CBM
GCM
+28
Vdc
Coiled Cable
LAMP
Deploy Stow
Unit Status
Lamp ON
LASER
Slave Dim
Master
Power
Filter
Gimbal Assembly and
Lamp Core
Power Conditioning
Interface Unit MKII
(PCIU)
Grip Hand
Controller
Camera
(Sending position
information to allow
the Trakka system to
slave to it)
Control Interface Unit
MKII
(CIU)
Advisories
Not part of the Trakka system
Supplied and installed by Customer
A/C 28VDC Power
Discrete Inputs
Pilot Collective
AIRBUS HELICOPTERS: CMM L334M6304E01 ISSUE: B PAGE 21 OF 165
The document reference is online, please check the correspondence between the online documentation and the printed version.

COMPONENT MAINTENANCE MANUAL
Publication No. 051019-1 Rev H
Page 4 DOCUMENT UNCONTROLLED WHEN PRINTED
33-46-00
AS9100 Certified
23-Mar-2015
Rev B
Figure 3 - Connectors
Table 1 - Connectors
Item
Description
1 CIU MKII/Grip hand controller Interface
(PCIU MKII J1)
2 Slave Port (PCIU MKII J2)
3 Interface to LPM (PCIU MKII J4)
4 Searchlight Control Cable Connector
(PCIU MKII J3)
5 Main Power Input (PCIU MKII J7)
6 Interface to GCM (PCIU MKII J5)
7 Searchlight Power Cable Connector
(PCIU MKII J6)
8 50 Amp Circuit Breaker (Main)
9 Bonding Stud Connection
10 PCIU MKII To Gimbal Lamp Power Circuit
breakers (total quantity 6, 3 front & 3 rear)
11 Grip hand controller Input Connector
(CIU MKII J3)
12 PC (Configuration and maintenance port)
(CIU MKII J2)
13 Interface to PCIU MKII (CIU MKII J1)
14 Collective Interface (CIU MKII J4)
15 Discrete Inputs (CIU MKII J5)
16 Annunciators Interface (CIU MKII J6)
41 23
5
6
7
8
9
10
PCIU A419
CIU
A422
1514 16
12
11 13
AIRBUS HELICOPTERS: CMM L334M6304E01 ISSUE: B PAGE 22 OF 165
The document reference is online, please check the correspondence between the online documentation and the printed version.

COMPONENT MAINTENANCE MANUAL
Publication No. 051019-1 Rev H
DOCUMENT UNCONTROLLED WHEN PRINTED Page 5
33-46-00
AS9100 Certified
23-Mar-2015
Rev B
Figure 4 - Typical A800 System with CIU and TCP
Figure 5 - A800 Basic Wiring System with CIU and TCP
A538
Gimbal Assembly
Optional 2nd Grip
Hand Controller PCIU MKII
CIU MKII
Grip Hand
Controller
TCP
Not part of the Trakka System
Camera
Sending position
information to allow the
Trakka system to slave
to it.
Pilot Collective
to Discrete Inputs
Pilot Collective Advisories
Customer Supplied
A/C 28V DC Power
Control
Power
A418c
Gimbal
Grip Hand
Controller
Line of
Fuselage
Pilot
Collectives
Trakka
Control
Panel
Power
Slave
PCIU MKII
J2
J3 J1
Auxiliary
Power Cable
Control Cable
Bulkhead Power
Cable
Bulkhead Control Cable
6 Pin
Connector
26 Pin
Connector
Lamp Assembly
Pilot Collective
CIU
MKII
Discrete Inputs
Annunciator
Outputs
TRAKKA
LASER
IR
ON
OFF
STOW SLAVE
Rev H
10 Dec 2015
AIRBUS HELICOPTERS: CMM L334M6304E01 ISSUE: B PAGE 23 OF 165
The document reference is online, please check the correspondence between the online documentation and the printed version.

COMPONENT MAINTENANCE MANUAL
Publication No. 051019-1 Rev H
Page 6 DOCUMENT UNCONTROLLED WHEN PRINTED
33-46-00
AS9100 Certified
23-Mar-2015
Rev B
Figure 6 - Typical A800 System with PCIU, TCP and Grip Hand Controller
Figure 7 - A800 Basic Wiring System with PCIU, TCP and Grip Hand Controller
A538a
Gimbal Assembly
Optional 2nd Grip
Hand Controller PCIU MKII
TCP
Grip Hand
Controller
Not part of the Trakka System
Camera
Sending position
information to allow the
Trakka system to slave
to it.
Pilot Collective
to Discrete Inputs
Pilot Collective Advisories
Customer Supplied
A/C 28V DC Power
Control
Power
A418d
Gimbal
Grip Hand
Controller
Line of
Fuselage
Pilot
Collectives
Trakka
Control
Panel
Power
Slave
PCIU MKII
J2
J3 J1
Auxiliary
Power Cable
Control Cable
Bulkhead Power
Cable
Bulkhead Control Cable
6 Pin
Connector
26 Pin
Connector
Lamp Assembly
TRAKKA
LASER
IR
ON
OFF
STOW SLAVE
Rev H
10 Dec 2015
AIRBUS HELICOPTERS: CMM L334M6304E01 ISSUE: B PAGE 24 OF 165
The document reference is online, please check the correspondence between the online documentation and the printed version.

COMPONENT MAINTENANCE MANUAL
Publication No. 051019-1 Rev H
DOCUMENT UNCONTROLLED WHEN PRINTED Page 7
33-46-00
AS9100 Certified
23-Mar-2015
Rev B
B. System Performance and Operation
(1) Prior to performing any maintenance on the A800 system, support personnel should familiarize
themselves with the system operation and safety procedures described in the Installation and
Operation Manual (Part No. 051002-2).
C. Performance Data
Table 2 - Performance Data
Description Specification
Voltage input 22−32 Vdc
Current input ≤42 amps at 28 Vdc
Power output (full) 800 ± 20 Watts
Power output (dim) 70% to 75% of full power
Peak luminance @ 1km 15.8 lux
Effective Beam angle (focus range) (Nominal) 13.9° to 13.3°
Azimuth rotation (nominal) ± 184° (non-continuous) 2
Elevation rotation (nominal) +37° to -99° 2
Rate of rotation (Azimuth and Elevation) 0°–60°/sec (variable)
Maximum velocity 140 knots (operational) / 200 Knots Vne (structural)
Maximum altitude 7,620m (25,000ft)
Operating Ambient Temperature range
(Searchlight) -30°C to +50°C (-49°F to 122°F) 3
Operating Ambient Temperature range (PCIU
MKII, CIU MKII and Grip Hand Controller) -45°C to +70°C (-49°F to +158°F)
Operational humidity range 95% non-condensing
Time to overhaul 10,000 flying hours
Mean Time Between Failures (MTBF) lamp 1,000 operating hours
Note 1: The beam characteristics are shown below in Figure 8.
Note 2: These are soft stop angles and are the actual operating angles.
Note 3: With the lamp operating, ambient temperatures of >50° C and <70° C will not
damage the unit. However, the lamp may turn off due to internal over temperature.
Figure 8 - Beam Angles
G030a
D
Distance
Zoom narrow effective beam angle: D=3,9°
Zoom wide effective beam angle: D=13,3°
AIRBUS HELICOPTERS: CMM L334M6304E01 ISSUE: B PAGE 25 OF 165
The document reference is online, please check the correspondence between the online documentation and the printed version.

COMPONENT MAINTENANCE MANUAL
Publication No. 051019-1 Rev H
Page 8 DOCUMENT UNCONTROLLED WHEN PRINTED
33-46-00
AS9100 Certified
23-Mar-2015
Rev B
(1) Beam diameter calculated
Table 3 - Beam Diameter and Distance
Distance (metres) Narrow Beam
Diameter (metres)
Wide Beam
Diameter (metres)
50 4 12
100 7 24
250 18 60
500 36 120
1,000 73 239
D. Mechanical Configuration
CAUTION: ENSURE THE SEARCHLIGHT DOES NOT POINT AT THE AIRCRAFT DURING
OPERATION. DAMAGE TO THE AIRCRAFT OR AIRCRAFT COMPONENTS
MAY RESULT, E.G. BURSTING OF THE FLOAT TUBES.
(1) Following maintenance, the system must be realigned to avoid exposure of any part of the aircraft
to the light beam. Figure 9 provides details of the overall dimensions of the searchlight and its
range of movement.
(2) When installed, operate the searchlight through its range of movement and note the points of the
aircraft at which the light beam points. Ensure that the azimuth and elevation hard stops are set to
prevent travel to those aircraft points.
NOTE: The searchlight should not be returned to service until the limit switches are
properly set.
Figure 9 – Gimbal Movement Envelope
483 mm
593 mm
90°
(Ref)
Pointing Forward Pointing Rearward
487 mm
±180°
478 mm
Envelope Height in mm at 0° elevation
(Ref)
Pointing Downward
A154c
487 mm
441 mm
423 mm
(Ref)
AIRBUS HELICOPTERS: CMM L334M6304E01 ISSUE: B PAGE 26 OF 165
The document reference is online, please check the correspondence between the online documentation and the printed version.

COMPONENT MAINTENANCE MANUAL
Publication No. 051019-1 Rev H
DOCUMENT UNCONTROLLED WHEN PRINTED Page 9
33-46-00
AS9100 Certified
23-Mar-2015
Rev B
2. Operation
A. Description
WARNING: TRAKKABEAM®SEARCHLIGHTS PRODUCE A HIGH INTENSITY BEAM AND
OPERATE WITH HIGH INTERNAL VOLTAGE LEVELS. MAINTENANCE AND
REPAIRS SHOULD ONLY BE CARRIED OUT BY TRAKKA TRAINED AND
QUALIFIED PERSONNEL.
(1) The A800 searchlight electrical system consists of:
(a) Gimbal/Lamp assembly (PN 200003-XXXXXXX).
(b) PCIU MKII (PN 011012-XXXXXXX).
(c) CIU MKII (PN 091016-XXXXXXX).
(d) TCP (PN 021019-XXXXXXX).
(e) Grip Hand Controller (PN 021012-XXXXXXX).
(f) Electrical cables.
(2) Figure 2 illustrates the basic wiring of the system including the heavy load carrying cables supplied
by the manufacturer.
(3) Trakka Corp recommends that cables or wires installed or repaired during the course of repair or
maintenance be crimped only by properly trained personnel.
NOTE: A poor crimp connection may lead to improper operation or failure of the
searchlight system.
CAUTION: HIGH POWER CABLES CONNECTED TO THIS SEARCHLIGHT SYSTEM MAY
CAUSE ELECTROMAGNETIC INTERFERENCE (EMI) OR RADIO FREQUENCY
INTERFERENCE (RFI) WITH AIRCRAFT INSTRUMENTS OR SYSTEMS. USE
CARE WHEN INSTALLING ALONGSIDE SENSITIVE WIRING LOOMS.
(4) If the searchlight is slaved to another aircraft system, such as a thermal imaging system, video
camera, moving map, etc. a separate document may be required to show additional wiring and
mechanical interfaces. Optional configurations are not within the scope of the basic system wiring
diagram; refer to Third Party equipment documents.
(5) The following rectification and maintenance of the A800 electrical system should only be carried
out by Trakka Trained Personnel:
(a) Removal/Reinstallation of:
i. Lamp housing assembly.
ii. Lamp.
iii. Lamp cooling fan.
iv. Ignitor.
(b) Cleaning of the lenses and front protection window.
(6) The control of the system varies according to the type of controller and/or optional equipment
required; some of which must be supplied by the Operator.
NOTE: A controller must always be connected to CIU MKII/Grip Hand Controller Interface
(J1) for the system to operate.
AIRBUS HELICOPTERS: CMM L334M6304E01 ISSUE: B PAGE 27 OF 165
The document reference is online, please check the correspondence between the online documentation and the printed version.

COMPONENT MAINTENANCE MANUAL
Publication No. 051019-1 Rev H
Page 10 DOCUMENT UNCONTROLLED WHEN PRINTED
33-46-00
AS9100 Certified
23-Mar-2015
Rev B
Figure 10 - Typical Trakka A800 System Interconnection (CIU to PCIU MKII)
G014
AIRBUS HELICOPTERS: CMM L334M6304E01 ISSUE: B PAGE 28 OF 165
The document reference is online, please check the correspondence between the online documentation and the printed version.

COMPONENT MAINTENANCE MANUAL
Publication No. 051019-1 Rev H
DOCUMENT UNCONTROLLED WHEN PRINTED Page 11
33-46-00
AS9100 Certified
23-Mar-2015
Rev B
Figure 11 - Typical Trakka A800 System Interconnection (TCP to PCIU MKII)
1
2
3
4
5
6
7
8
9
10
11
12
13
14
15
16
17
18
19
20
21
22
23
24
25
26
27
28
29
30
31
32
33
34
35
36
37
1
2
3
4
5
6
7
8
9
1 0
11
1 2
1 3
1 4
1 5
1 6
1 7
1 8
1 9
2 0
2 1
2 2
2 3
2 4
2 5
2 6
2 7
2 8
2 9
3 0
3 1
3 2
3 3
3 4
3 5
3 6
3 7
Trakka
Control
Panel
Searchlight
and Gimbal
Assembly
PCIU MKII
Laser
Pointer
(optional)
Optional Camera
for Slaving
To Grip Hand
Control ler
Customer Su pplied Conn ector
(Pin Numbers for Refere nce Only)
D38 999/ 20M C3 5BA
AIRBUS HELICOPTERS: CMM L334M6304E01 ISSUE: B PAGE 29 OF 165
The document reference is online, please check the correspondence between the online documentation and the printed version.

COMPONENT MAINTENANCE MANUAL
Publication No. 051019-1 Rev H
Page 12 DOCUMENT UNCONTROLLED WHEN PRINTED
33-46-00
AS9100 Certified
23-Mar-2015
Rev B
Table 4 - PCIU MKII Connector Pin Descriptions
J1
J2
J3
A RxD1 (RS-232)
1 RxD (RS-232)
A Filter switch
B
TxD1 (RS-232)
2
TxD (RS-232)
B
Lamp Temp. Sensor
C
Serial port common 1
3
RxD+ (RS-422)
C
IR Filter Switch
D
+12/15Vdc (out) 1
4
RxD- (RS-422)
D
Sensor/Switch GND
E
GND 1
5
TxD+ (RS-422)
E
Fan +
F
RxD2 (RS-232)
6
TxD- (RS-422)
F
Fan -
G
TxD2 (RS-232)
7
Analogue slaving
G
Zoom motor +
H
Serial port common 2
8
Analogue input – Az
H
Zoom motor -
J
+12/15Vdc (out) 2
9
Analogue input – El
J
Filter motor +
K
GND 2
10
Analogue GND
K
Filter motor -
L Reserved
11 Reserved
L Elevation motor +
M
Reserved
12
Reserved
M
Elevation motor -
N
Reserved
13
Signal Ground
N
Azimuth motor +
P
Reserved
P
Azimuth motor -
R
Reserved
J6
R
Az. Micro-switch Right
S
Master/Observer
A
Lamp Power +
S
Az. Micro-switch Left
T
Power On Switch
B
Lamp Power +
T
El. Micro-switch Down
U Arm Switch
C
Lamp Power +
U El. Micro-switch Up
V
NVG Mode Input
D
Lamp Power -
V
Az. encoder signal
W
Laser On Input
E
Lamp Power -
W
Azimuth encoder +
X Lamp On Ann.
F Lamp Power -
X Azimuth encoder -
Y
IR Mode Ann.
Y
Elevation encoder +
Z
Weight On Wheels
J7
Z
Elevation encoder -
a
Switch/Ann. Common
A
+28V nominal
a
El. encoder signal
b
Laser On Ann.
B
0V
b
Laser pointer +ve
c
+28Vdc
C
Not used
c
Laser pointer GND.
D
Not used
AIRBUS HELICOPTERS: CMM L334M6304E01 ISSUE: B PAGE 30 OF 165
The document reference is online, please check the correspondence between the online documentation and the printed version.

COMPONENT MAINTENANCE MANUAL
Publication No. 051019-1 Rev H
DOCUMENT UNCONTROLLED WHEN PRINTED Page 13
33-46-00
AS9100 Certified
23-Mar-2015
Rev B
Figure 12 - Typical CIU MKII Interconnection Diagram
+28 Vdc
+28 Vdc
Gnd
GND
DIM Light (rising edge)
G016a
AIRBUS HELICOPTERS: CMM L334M6304E01 ISSUE: B PAGE 31 OF 165
The document reference is online, please check the correspondence between the online documentation and the printed version.

COMPONENT MAINTENANCE MANUAL
Publication No. 051019-1 Rev H
Page 14 DOCUMENT UNCONTROLLED WHEN PRINTED
33-46-00
AS9100 Certified
23-Mar-2015
Rev B
Figure 13 - Typical CIU MKII Interconnection Diagram (Controller Connection)
GRIP HAND
CONTROLLER
CIU MKII
PCIU MKII
G015
AIRBUS HELICOPTERS: CMM L334M6304E01 ISSUE: B PAGE 32 OF 165
The document reference is online, please check the correspondence between the online documentation and the printed version.

COMPONENT MAINTENANCE MANUAL
Publication No. 051019-1 Rev H
DOCUMENT UNCONTROLLED WHEN PRINTED Page 15
33-46-00
AS9100 Certified
23-Mar-2015
Rev B
Figure 14 - TCP to CIU MKII Interconnection Diagram
Rev H
10 Dec 2015
AIRBUS HELICOPTERS: CMM L334M6304E01 ISSUE: B PAGE 33 OF 165
The document reference is online, please check the correspondence between the online documentation and the printed version.

COMPONENT MAINTENANCE MANUAL
Publication No. 051019-1 Rev H
Page 16 DOCUMENT UNCONTROLLED WHEN PRINTED
33-46-00
AS9100 Certified
23-Mar-2015
Rev B
Figure 15 - TCP to Collective and Grip Hand Controller (with Laser Switch)
Rev H
10 Dec 2015
AIRBUS HELICOPTERS: CMM L334M6304E01 ISSUE: B PAGE 34 OF 165
The document reference is online, please check the correspondence between the online documentation and the printed version.

COMPONENT MAINTENANCE MANUAL
Publication No. 051019-1 Rev H
DOCUMENT UNCONTROLLED WHEN PRINTED Page 17
33-46-00
AS9100 Certified
23-Mar-2015
Rev B
B. Control Interface Unit MKII (CIU) Interconnection
Figure 16 - CIU MKII Interface Connectors
Table 5 - Pin Numbers and Functions
Designator
Type
Description
J1
D38999/20WC35SA
Interface to PCIU MKII
J2
D38999/20WB35S
PC (Configuration and maintenance port)
J3
D38999/20WB35SA
Grip hand controller port
J4 D38999/20WC35SN
Collective 1 interface cable
Pin
Description
1
Filter increment input (rising edge)
2
Filter decrement switch input (rising edge)
3
ZOOM wide (level)
4
ZOOM Narrow (level)
5
Lamp On/Off (rising edge)
6
Deploy (rising edge)
7
Stow (rising edge)
8
Camera slave on/off (rising edge)
9
System on/off (level)
10
Disable Handgrip (level)
11 Output 28V (500 mA current limited) for switch
inputs.
12
Up
13
Down
14
Left
15
Right
16
Reserved
17
Arm Switch (level)
18
Dim Light
19
GND
20 Input to the Grip/Hand Controller “Master
Power” switch
21 Input to the Grip/Hand Controller “Master
Power” switch
22
Weight On Wheels (level)
J5
J4
J6
J1
J3
J2
A442
AIRBUS HELICOPTERS: CMM L334M6304E01 ISSUE: B PAGE 35 OF 165
The document reference is online, please check the correspondence between the online documentation and the printed version.

COMPONENT MAINTENANCE MANUAL
Publication No. 051019-1 Rev H
Page 18 DOCUMENT UNCONTROLLED WHEN PRINTED
33-46-00
AS9100 Certified
23-Mar-2015
Rev B
J5 D38999/20WC35SN
Discrete Inputs
Pin
Description
1
Laser ON (level)
2
Laser OFF (level)
3
ZOOM wide (level)
4
ZOOM Narrow (level)
5
Lamp On/Off (rising edge)
6
Deploy (rising edge)
7
Hold in Stow (level)
8
Camera slave on/off (level)
9
System on/off (level)
10
Disable Handgrip (level)
11 Output 28V (500 mA current limited) for switch
inputs.
12
Up
13
Down
14
Left
15
Right
16
DIM Light
17
Arm Switch (level)
18
Reserved
19
Visible On (level)
20
Visible Off (level)
21
IR On (level)
22
IR Off (level)
J6 D38999/20WB35SN
Annunciator interface (Relays)
Contact details: Normally open 500 mA @ 24 Vdc
Pin
Description
1
System Power ON
2
3
Stowed
4
5
Fault
6
7
Lamp ON
8
9
Laser ON
10
11
IR Mode
12
13
Reserved for future use
AIRBUS HELICOPTERS: CMM L334M6304E01 ISSUE: B PAGE 36 OF 165
The document reference is online, please check the correspondence between the online documentation and the printed version.

COMPONENT MAINTENANCE MANUAL
Publication No. 051019-1 Rev H
DOCUMENT UNCONTROLLED WHEN PRINTED Page 19
33-46-00
AS9100 Certified
23-Mar-2015
Rev B
C. Power Conditioning Interface Unit MKII (PCIU) Description
Figure 17 - PCIU MKII
Mounting Frame Required
No Mounting Frame Required
A407a
AIRBUS HELICOPTERS: CMM L334M6304E01 ISSUE: B PAGE 37 OF 165
The document reference is online, please check the correspondence between the online documentation and the printed version.

COMPONENT MAINTENANCE MANUAL
Publication No. 051019-1 Rev H
Page 20 DOCUMENT UNCONTROLLED WHEN PRINTED
33-46-00
AS9100 Certified
23-Mar-2015
Rev B
Table 6 - PCIU MKII
Item Description
1 Lamp Power Module (LPM)
2 Circuit Breaker Module (CBM)
3 Gimbal Control Module (GCM)
4 Mounting Frame
5 Searchlight Power Cable Connector (PCIU MKII
J6)
6 50 Amp Circuit Breaker (Main)
7 Bonding Stud Connection
8 CIU MKII/Grip hand controller Interface (PCIU
MKII J1)
9 Slave Port (PCIU MKII J2)
10 Interface to LPM (PCIU MKII J4)
11 Searchlight Control Cable Connector (PCIU
MKII J3)
12 PCIU MKII To Gimbal Lamp Power Circuit
breakers (total quantity 6, 3 front & 3 rear)
13 Main Power Input (PCIU MKII J7)
14 Interface to GCM (PCIU MKII J5)
(1) The PCIU MKII (Figure 17) is shipped for mounting with a mounting frame assembly or mounting
lugs and must be installed in the aircraft in accordance with the approved installation data.
(2) The basic electrical cable system consists of the:
(a) Power input cable connected to port J7 on the PCIU MKII,
(b) Searchlight power cable connected between port J6 on the PCIU MKII and the 6 pin
connector on the searchlight gimbal dovetail assembly,
(c) Searchlight control cable between port J3 on the PCIU MKII and the 26 pin connector on the
searchlight gimbal dovetail assembly,
(d) CIU MKII & grip hand controller cables between port J1 on the PCIU MKII and port J1 on the
CIU MKII.
(e) SLAVE cable between port J2 on the PCIU MKII and a camera – if fitted.
(3) The two searchlight cables and the grip hand controller cable may need to pass through a
bulkhead. In this case, additional cabling is required. Refer to the approved installation data.
(4) In addition to these basic cables, additional cables will be required to utilise the CIU MKII for
operation of the pilot control and discrete inputs – refer to the approved installation data.
(5) Refer to the approved installation data paying attention to the routing and correct securing of all
cabling.
(6) The basic wiring diagram and cable data for the system are shown in Figure 10, Figure 12 and
Figure 13.
(7) If the searchlight is slaved to another aircraft system such as a thermal imaging system, video
camera, moving map, etc., or additional grip hand controllers are to be connected, a separate
document may be required to show additional wiring and mechanical interfaces. Optional
configurations are not within the scope of the basic system wiring diagram. Please contact your
Trakka Corp representative for further information.
AIRBUS HELICOPTERS: CMM L334M6304E01 ISSUE: B PAGE 38 OF 165
The document reference is online, please check the correspondence between the online documentation and the printed version.
Popular Floodlight manuals by other brands
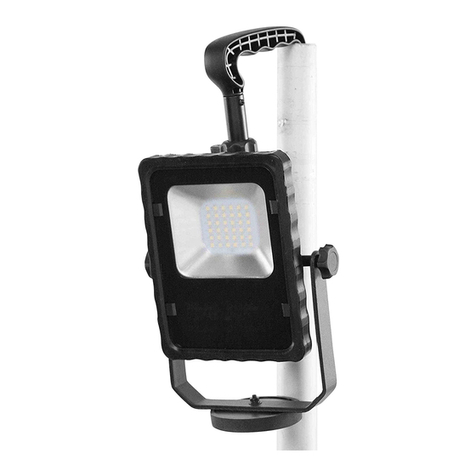
Larson Electronics
Larson Electronics RL-16-LED-M instructions
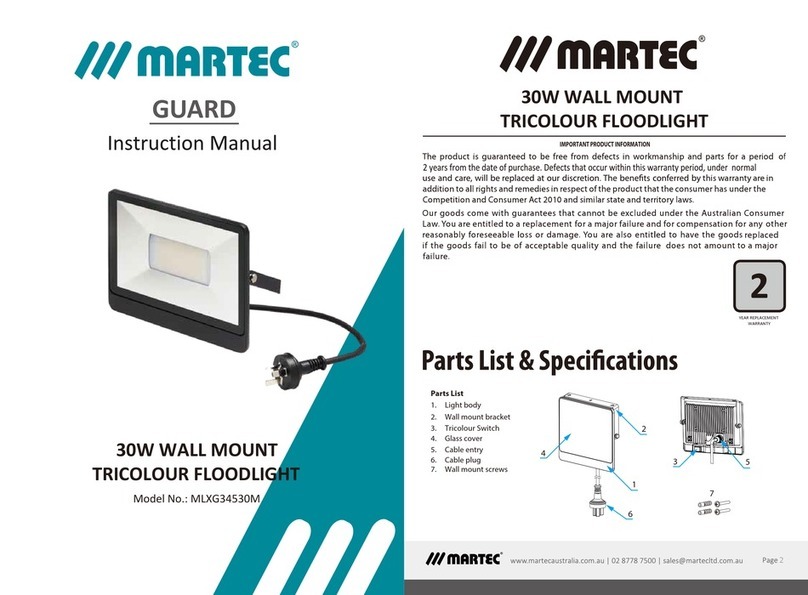
Martec
Martec MLXG34530M instruction manual
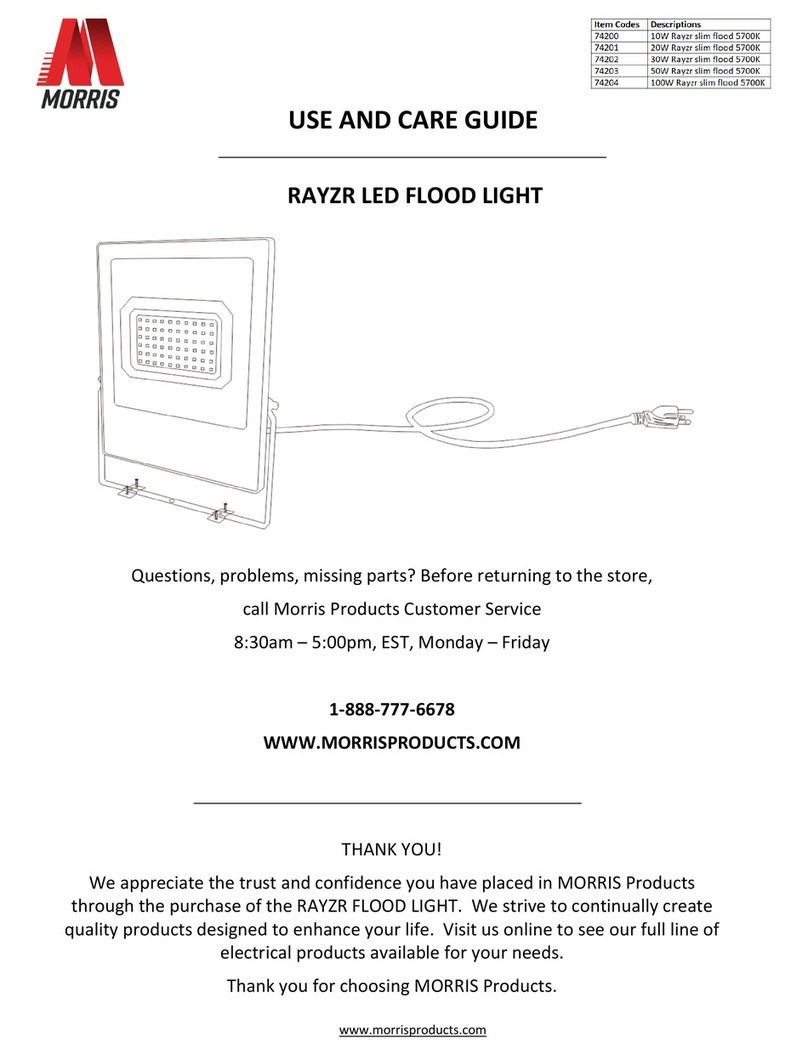
Morris
Morris 74200 Use and care guide
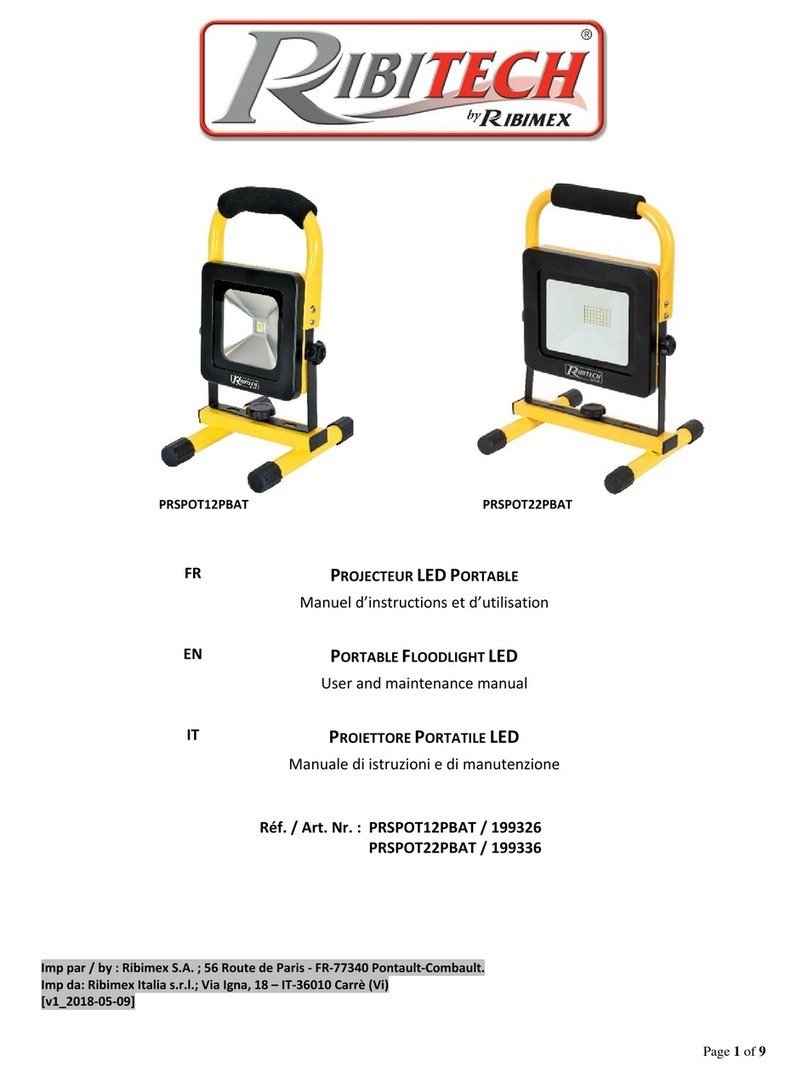
Ribimex
Ribimex Ribitech PRSPOT22PBAT User and maintenance manual
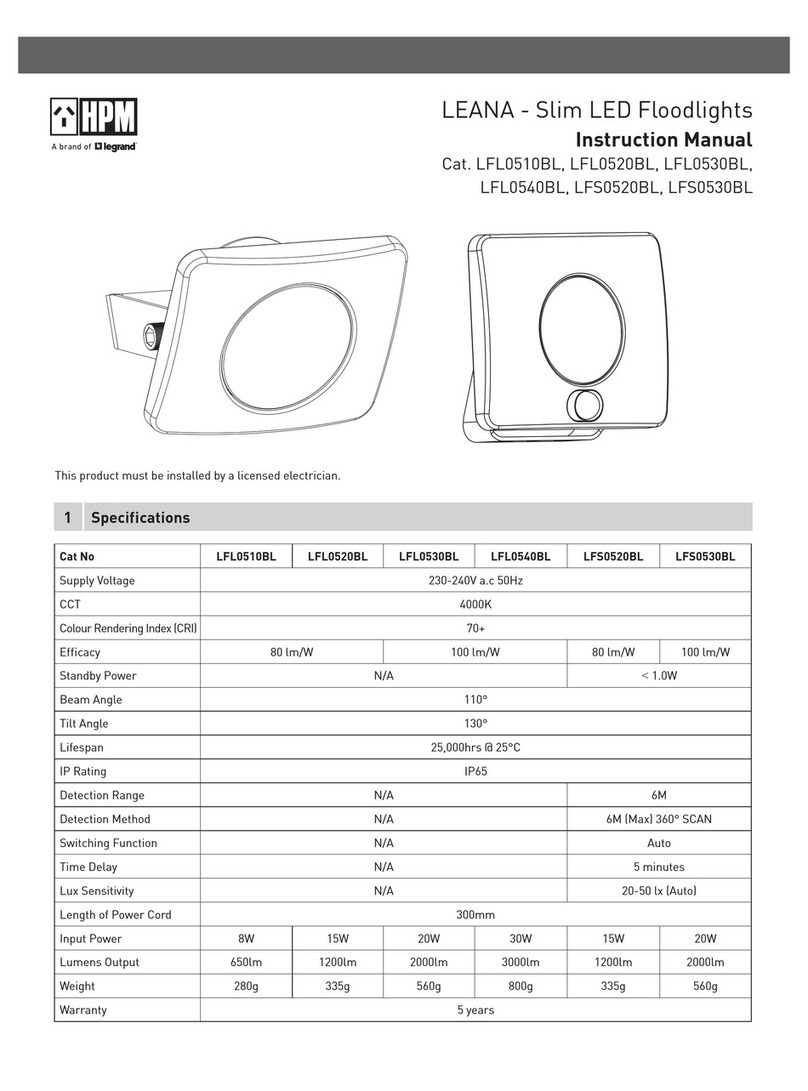
HPM
HPM LEANA LFL0510BL instruction manual

brennenstuhl
brennenstuhl ProfessionalLINE R 17000 user manual