TRI tool BOILERMASTER User manual

Operation
Manual
92-0629 Rev. 160129
Model BOILERMASTER

ABOUT TRI TOOL INC.
Tri Tool’s extensive experience in the design, development and manufacture of portable
machine tools and welding equipment has resulted in machinery that is designed to meet
the highest standards of quality, safety, and performance. Our products are backed by a
company totally committed to service, integrity, and customer satisfaction.
Tri Tool Services has developed a solid reputation as a trusted provider of dependable and
cost-effective on-site service solutions including turnkey project management, machining
services, and mechanized and manual code welding services using experienced and well-
trained machinists and welders.
In addition to developing industry leading machining and welding equipment, Tri Tool’s
engineering team provides custom equipment design and manufacturing solutions to suit
the most rigorous requirements of our customers’ special applications.
Please contact us for more information on any of our products or services. Company
representatives are available for demonstrations of most of our products at your facility.
Printed in the USA

92-0629 Rev. 160129
Model BOILERMASTER
TABLE OF CONTENTS
1. ABOUT THE MANUAL 3
2. SAFETY 3
3. GENERAL DESCRIPTION 7
4. SPECIFICATIONS 8
5. MAINTENANCE 12
6. SETUP 15
7. OPERATION 19
8. CUTTING SPEEDS AND FEEDS 21
9. JAW BLOCKS AND RAMP SETS 22
10. TOOL BITS 26
11. TROUBLESHOOTING 29
12. ACCESSORIES 31
13. ILLUSTRATED PARTS BREAKDOWN 32

TRI TOOL INC. Warranty
All products manufactured by Tri Tool Inc., except for tool bits and for other consumable
items, are warranted to the original purchaser to be free from defects in materials and
workmanship under normal use for a period of one year from the date of purchase.
The purchaser shall bear all shipping, packing and insurance costs and all other costs to
and from a designated repair service center. The product will be returned to the purchaser
freight prepaid and billed to the purchaser.
The warranty will not apply to those products that have been misused, abused, or altered
without the express permission in writing by Tri Tool Inc.
Neither this warranty nor any other warranty, expressed or implied, including implied
warranties of mechanical ability, tness for a particular use, or merchantability, shall
extend beyond the warranty period. No responsibility is assumed for any incidental or
consequential damages.
Some states do not allow limitations on how long an implied warranty lasts and some states
do not allow the exclusion or limitations incidental or consequential damages, so the above
limitation of exclusion does not apply to all purchasers. This warranty gives the purchaser
specic legal rights. Other rights vary from state to state.
Tool Bit Resharpening Policy
Tri Tool Inc. can not resharpen badly gouged, chipped, or broken tool bits. Check the tool
bits before you send them and package them well. Within two working days of receipt, the
tool bits are evaluated and the customer is contacted for authorization.
The customer will receive a price and a scheduled return shipment date. The price structure
is available from your Tri Tool Inc. sales representative.
Tool bits that are not suitable for resharpening are returned with the tool bits that were
resharpened, unless Tri Tool Inc. is instructed otherwise.
The customer is responsible for shipping charges to and from Tri Tool Inc.
This policy only covers tool bits manufactured by Tri Tool Inc.

3
Model BOILERMASTER
92-0629 Rev. 160129
1. ABOUT THE MANUAL
1.1 COPYRIGHT
Copyright 2016. Proprietary property of Tri Tool Inc. No reproduction, use, or
duplication of the information shown hereon is permitted without the express
written consent of Tri Tool Inc.
1.2 DISCLAIMER
The instructions and descriptions in this manual were accurate when the manual
was written. However, the information in the manual is subject to change without
notice. Check for updated information before you start any job. The Tri Tool Inc.
web site has the most current information.
Do not operate or work on this equipment unless you have read and understood
the instructions in this Manual. Failure to follow the instructions or follow the
safety instructions could result in serious injury or death. This manual describes
conditions and hazards that are common and anticipated during equipment
operation. No manual can address all conditions which may occur.
2. SAFETY
2.1 SAFETY SYMBOLS
The manual may contain one or more safety symbols. These symbols and the
associated text warn you of potentially hazardous conditions. Examples of the
safety symbols and the associated text follow:
CAUTION
CAUTION: Indicates a hazardous situation which, if not avoided,
could result in minor or moderate injury, or cause property damage.
DANGER
DANGER: Indicates a hazardous situation which, if not avoided, will
result in death or serious injury.
WARNING
WARNING: Indicates a hazardous situation which, if not avoided,
could result in death or serious injury.

4
TRI TOOL INC.
92-0629 Rev. 160129
2.2 PERSONAL PROTECTIVE EQUIPMENT
• Use standard safety equipment such as: hard hats, safety shoes, safety
harnesses, protective clothes, and other safety devices when appropriate.
• Wear safety glasses.
• Do not wear loose clothing or jewelry.
• Wear nonskid footwear.
• Secure long hair.
2.3 PERSONNEL
• Only personnel who are trained or are being trained may operate the
equipment.
• Keep the operation manual available where the equipment is used.
• The operator must read the operation manual before using the equipment.
• The equipment must be operated in accordance with the manual information.
• The operator must follow the safety precautions in this manual and good
engineering practices to reduce the risk of injury.
• Before using the equipment, the operator must ensure that all safety
messages on the equipment are legible.
2.4 WORK AREA
• Keep the work area clean.
• Keep the area well lit.
• Keep items such as; electrical cords, cables, rags, rigging straps, away from
rotating equipment.
• Do not use power-cutting tools in the presence of ammable liquids and
gases.
• Do not let visitors or untrained personnel near tools that are in use.
• Ensure all observers wear eye protection.
• Keep proper footing at all times.
DANGER
DANGER: Do not wear gloves when you use operate the equipment.
If you are using the index trip mechanism, a glove may be caught or
pulled into the pinch point created by the equipment head. This will
result in serious personal injury.

5
Model BOILERMASTER
92-0629 Rev. 160129
2.5 AREA EQUIPMENT
• Secure the pipe with clamps, vises, chains or straps.
• Ensure that both sides of the pipe at the cut site is fully supported so that the
pipe will not move after the cut is completed. Long lengths of pipe may be
under load and the separation of the pipe can release pressure. This pressure
can cause both sides of the pipe to move.
2.6 TOOL CARE
• Keep tools in good operating condition. Sharp tool bits perform better and are
safer than dull tool bits.
• Do not use damaged tools. Always check your tools for damage especially if a
tool has malfunctioned, been dropped or hit, check it for damage.
• Before you start operating the equipment, do no-load tests and feed function
checks.

6
TRI TOOL INC.
92-0629 Rev. 160129
2.7 TOOL USE
• Use the right tool and tool bit for the job. Contact Tri Tool to help with your
application.
• Keep the tool bits fully engaged in the tool bit holders. Loose bits are sharp
and can cause cuts or punctures.
• Disconnect power supply during setup and maintenance. Use all ‘Stop’ or
Shut off’ features available when changing or adjusting tool bits, maintaining
the tool, or when the tool is not in use.
• Remove adjusting keys and wrenches before applying power to the
equipment. Check the tool before turning it on to make sure that all keys and
wrenches have been removed.
• Do not force tools. Tools and tool bits function better and safer when used at
the recommended speeds.
• Do not reach into rotating equipment.
• Do not reach into the rotating head stock to remove chips, to make
adjustments, or to check the surface nish.
• Handle chips with care. Chips have very sharp edges and are hot. Do not try
to pull chips apart with bare hands.
• Store tools properly. Disconnect tools from the power source, remove the tool
bits, and store in a safe place.

7
Model BOILERMASTER
92-0629 Rev. 160129
3. GENERAL DESCRIPTION
The BOILERMASTER™ is a Pipe Beveler designed for facing, beveling and/or
counterboring the ends of the pipe or tubing in preparation for welding.
These machining operations may be performed either simultaneously or
separately.
Pipe weld end preparations that meet all existing conventional codes including
the more stringent nuclear codes may be machined.
The various interchangeable Jaw Blocks and Ramps will secure the
BOILERMASTER to pipe and tubing having an inside diameter ranging from
1.25” (31.8 mm) through 4.33” (110.0 mm).
The expanding mandrel provides fast, accurate self-centering and alignment to
the pipe or tubing to be machined.
There are two different head kits available. They are the 2.63” DIA head kit and
the 4.00” DIA head kit.
The BOILERMASTER accepts the reaction torque generated by the machining
operations through the mandrel. No additional restraining devices are required.

8
TRI TOOL INC.
92-0629 Rev. 160129
4. SPECIFICATIONS
4.1 BOILERMASTER WITH AN AIR MOTOR
Figure: 1. Model BOILERMASTER
Air Flow (Speed)
Control Valve
Mandrel
Cutting Head
Feed
Handle
On/Off Lever with
Deadman Switch
Draw Nut
Handle
2.63"
(66.8 mm)
16.41"
(416.8 mm)
8.72"
(221.5 mm)
19.88"
(505.0 mm)
Weight 8.5 lbs. (3.9 kg)
Power Requirements 67 cfm at 90 psi
(32 L/s at 621 kPa)

9
Model BOILERMASTER
92-0629 Rev. 160129
PIPE CUTTING CAPACITIES
Basic Pipe Sizes All schedules of 1 1/4” through 4” pipe. Some schedules
may require optional equipment.
Basic Tube Sizes Up to .531” (13.5 mm) wall tubing with a maximum OD of
4.50” (114.3 mm)
and minimum ID of 1.25” (31.7 mm) may be beveled with
standard
procedures.
Wall Thickness Capacity Wall thickness of all standard pipe schedules (.531” [13.5
mm] maximum) in
the range listed.
Contact Tri Tool Inc. for procedures for heavier wall pipe.
Counterboring Operation The machine will counterbore pipe and tubing with an ID
range of 1.50” (38.1
mm) to 4.33” (110.2 mm).
MATERIAL CUTTING CAPACITIES
Mild steels, chrome steels (Rc 35 maximum), stainless steel, copper-nickel and
aluminum without limitations except size and wall thickness as specied.
Inconel and some other high temperature alloys may require special procedures as a
function of wall thickness and type of end preparation.
Contact the Tri Tool Inc. engineering department for details.
CUTTING HEAD SPEEDS
Maximum Cutting Head Speed 162 rpm
Cutting Head Speed at Maximum H.P. 82 rpm
Functional Speed Range 20 to 100 rpm
RPM at 300 surface inches per minute (762 surface centimeters per minute)
4.50” (114.3 mm) 21 rpm
1.25” (31.8 mm) 76 rpm

10
TRI TOOL INC.
92-0629 Rev. 160129
DRIVE SYSTEM
Final Drive Gear driven
Pneumatic Motor
Free Speed 325 rpm
Maximum H.P. Speed 162 rpm
SPEED CONTROL
Deadman type, on/off valve and twist type airow control valve
MOUNTING
Manually actuated draw rod expands the mandrel ramps and the jaw blocks
FEED
Manual feed wrench is in line at the back of the machine
Feed rate is .100” (2.5 mm) per revolution of the feed wrench
4.2 BOILERMASTER WITH AN ELECTRIC MOTOR
Weight 18 lbs. (8.1 kg)
Power Requirements 115 VAC, 28 to 60 Hz 5.25 amp
PIPE CUTTING CAPACITIES
Basic Pipe Sizes
1" Pipe
Schedule 40 (Small Mandrel required to mount in 1” schedule 80 and above.
1 1/4” through 2 1/2” Pipe
Up to Schedule 80
3” through 4” Pipe
Up to Schedule 40
* Some Schedules may require optional equipment
Basic Tube Sizes
Up to .250” (6.4 mm) wall tubing with a maximum OD of 4.50” (114.3 mm) and a
minimum ID of 1.25” (31.7 mm) may be beveled with standard mandrel.

11
Model BOILERMASTER
92-0629 Rev. 160129
Wall Thickness Capacity (Limitations)
Wall thickness of schedules listed, .276” (7 mm) maximum, in the range listed can
be machined without limitations.
Wall thicknesses greater than .276” (7 mm) require special procedures and are
subject to Duty Cycle limitations to prevent motor damage. Contact Tri Tool Inc. for
heavier wall procedures.
Counterboring Operations
The tool will counterbore pipe and tubing with an ID of 1.50” (38.1 mm) to
4.33” (110.2 mm).
DUTY CYCLE
The BOILERMASTER™ with an electric motor duty cycle on high cutting load
applications (see above), is limited to 50% ‘On’ time with a maximum of ve minutes
continuous ‘On’ time.
MATERIAL CUTTING CAPABILITIES
Mild steels, chrome steels (Rc 35 maximum), stainless steel, copper-nickel and
aluminum without limitations except size and wall thickness as specied.
Inconel and some other high temperature alloys may require special procedures as a
function of wall thickness and type of end preparation.
Contact the TRI TOOL INC. engineering department for details.
DRIVE SYSTEM
Final Drive Gear Driven
Electric Motor - 2 speed Ranges & 6:1 Gear Reduction
Free Speed
Low Range 168 rpm
High Range 316 rpm
Max. HP Speed
Low Range 112 rpm
High Range 210 rpm

12
TRI TOOL INC.
92-0629 Rev. 160129
5. MAINTENANCE
5.1 BOILERMASTER
• Clean all components, refer to Fig 2.
• Coat all components with a light lm of oil before use. Use a clean, non-
detergent oil, preferably SAE 10 (90SSU) or lighter.
• If the BOILERMASTER is operated in the vertical position (Cutting Head
up), turn it upside down and remove the chips and all debris after each cut.
The tool life may be severely shortened, if chips and/or other debris are not
removed.
• Make sure that the gear box has grease. Add more if necessary.
• Use a lithium based grease for gears and bearings.
• The Air Supply for the BOILERMASTER with an air motor required adequate
lter, regulator and lubricator (FRL).
• The maximum line pressure is 90 PSI (621 kPa).
CAUTION
CAUTION: If the Motor is damaged by contaminated air or lack of
lubrication, the Motor warranty is void.

13
Model BOILERMASTER
92-0629 Rev. 160129
Figure: 2. Model BOILERMASTER Sites to Clean
5.2 AIR MOTOR MAINTENANCE
CAUTION
CAUTION: Disassembly of a power unit voids warranty, except
when performed by a Tri Tool Inc. designated person. A letter of
designation is required
AIR SUPPLY
• Make sure that the air supply ows through a lter/regulator/lubricator (FRL).
• Maintain the FRL according to the manufacturer's manual. The frequency
depends on the quality of the air supply.
• Keep the water trap drained.
• Keep the lter cleaned.
• Keep the lubricator oil reservoir lled so that a drop of oil every 2 to 5 seconds
is owing.

14
TRI TOOL INC.
92-0629 Rev. 160129
AIR MOTOR LUBRICATION
If the BOILERMASTER will not be used for 24 hours or more after being run
on 'wet air', squirt oil directly into the air motor inlet and run the motor for 2 to 3
seconds. This will prevent rusting and freezing of the rotor vanes.
5.3 LUBRICATION RECOMMENDATIONS
The air motor requires a Class 2 lubricant, viscosity of 100 to 200 SSU at 100° F
(38° C) minimum aniline point of 200° F (93° C).
• TRI TOOL Inc. – Air Tool Lubricant (P/N 68-0022)
• AMOCO – American Industrial Oil No. 32
• Atlantic Richeld – Duro Oil S-150
• Chevron – A. W. Machine Oil 32
• Exxon – Nuto H32
• Shell – Tellus Oil 32
The bearings in the air motor are sealed and do not require any lubrication.
The drive gears require a lithium-based grease.

15
Model BOILERMASTER
92-0629 Rev. 160129
6. SETUP
DANGER
DANGER: Do not override the deadman switch on the power unit.
Locking down, obstructing, or in any way defeating the deadman
switch may result in serious injury.
6.1 PREPARE THE BOILERMASTER
1. Select the jaw blocks for the pipe size to be machined. Refer to Section 9.
2. Gently slide the mandrel assembly into the BOILERMASTER until it comes to
a stop against the torque acceptance key. Refer to Fig. 3.
3. Rotate the mandrel assembly as required to engage the torque acceptance
key of the BOILERMASTER with the slot in the mandrel shaft.
CAUTION
CAUTION: Do not allow the machine to impact the lead threads of
the feed nut with the lead threads of the mandrel.
Make sure that the mandrel is properly installed to avoid damage to
the machine.
4. Rotate the feed handle clockwise to engage the feed nut with the thread on
the mandrel shaft until the mandrel shaft is ush with the end of the feed nut.
Figure: 3. Parts of the Model BOILERMASTER
Tool bit
Mandrel
Assembly
Feed HandleDraw Nut
Handle
Proper Mandrel
Installation

16
TRI TOOL INC.
92-0629 Rev. 160129
5. The BOILERMASTER with the mandrel assembly installed may be mounted
into the pipe or tube as one unit. Refer to Fig. 4.
CAUTION
CAUTION: Install the mandrel beyond the nal end preparation. This
will help to avoid cutting the ramps or jaw blocks.
6. Tighten the draw nut to force the jaw blocks out to the inside diameter of the
pipe or tube.
Figure: 4. BOILERMASTER with Mandrel Assembly in Pipe

17
Model BOILERMASTER
92-0629 Rev. 160129
6.2 INSTALL TOOL BIT
WARNING
WARNING: Check that the BOILERMASTER is disconnected from
the power source before you install a tool bit.
1. Make sure there is a clearance of 1/8” (3 mm) minimum between the tool bit
and the pipe face. Refer to Fig. 5.
Figure: 5. Tool Bit Installation
2. Select the tool bit(s) required to machine the pipe. Refer to Section 10,
Tool Bits. The use of dull or improperly designed tool bits or tool bits not
manufactured by Tri Tool Inc. may result in poor performance and may
constitute abuse of the machine. This action voids the Tri Tool Inc. factory
warranty.
3. When performing any multiple machining operation such as facing and
beveling, make sure the facing tool bit is installed as shown Fig 6.

18
TRI TOOL INC.
92-0629 Rev. 160129
Figure: 6. Cutting Head
4. Insert the tool bit(s) into the slot(s) in the cutting head.
5. Make sure the cutting edge of the tool bit(s) must be located on the radial
centerline.
6. Make sure that the tool bit(s) are not installed backwards.
7. Make sure that there is a clearance between the tool bit(s) and the mandrel.
8. Tighten the wedge screws or set screws to secure the tool bit in the slot.
9. Adjust the bevel tool bit radially to control the land width.
Other manuals for BOILERMASTER
1
Table of contents
Other TRI tool Power Tools manuals
Popular Power Tools manuals by other brands

Rockler
Rockler 36407 quick start guide
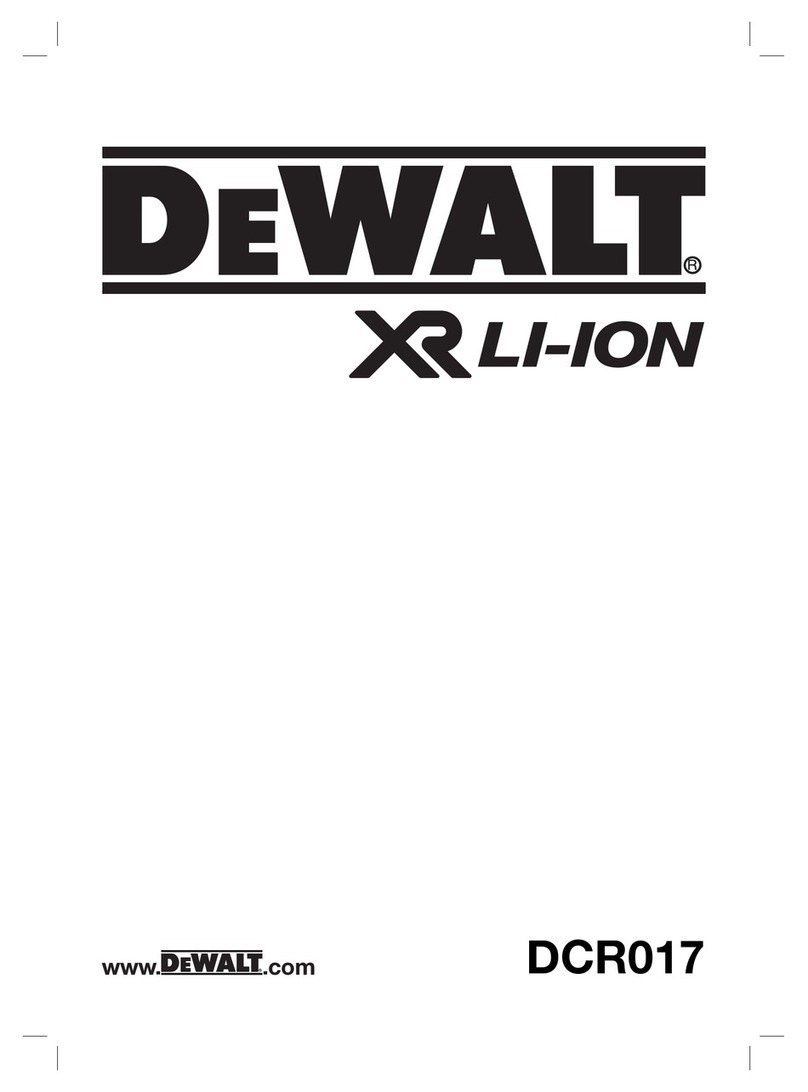
DeWalt
DeWalt DCR017 Original instruction
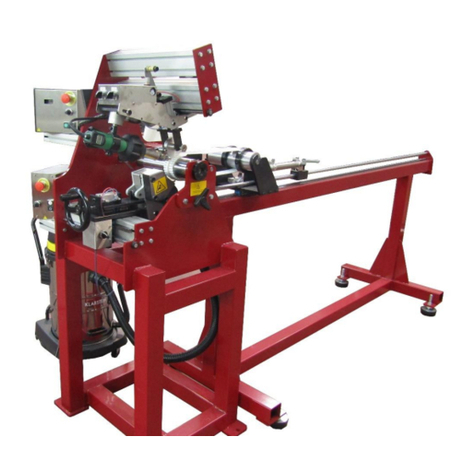
ermengineering
ermengineering LRSE-180 Use and maintenance manual
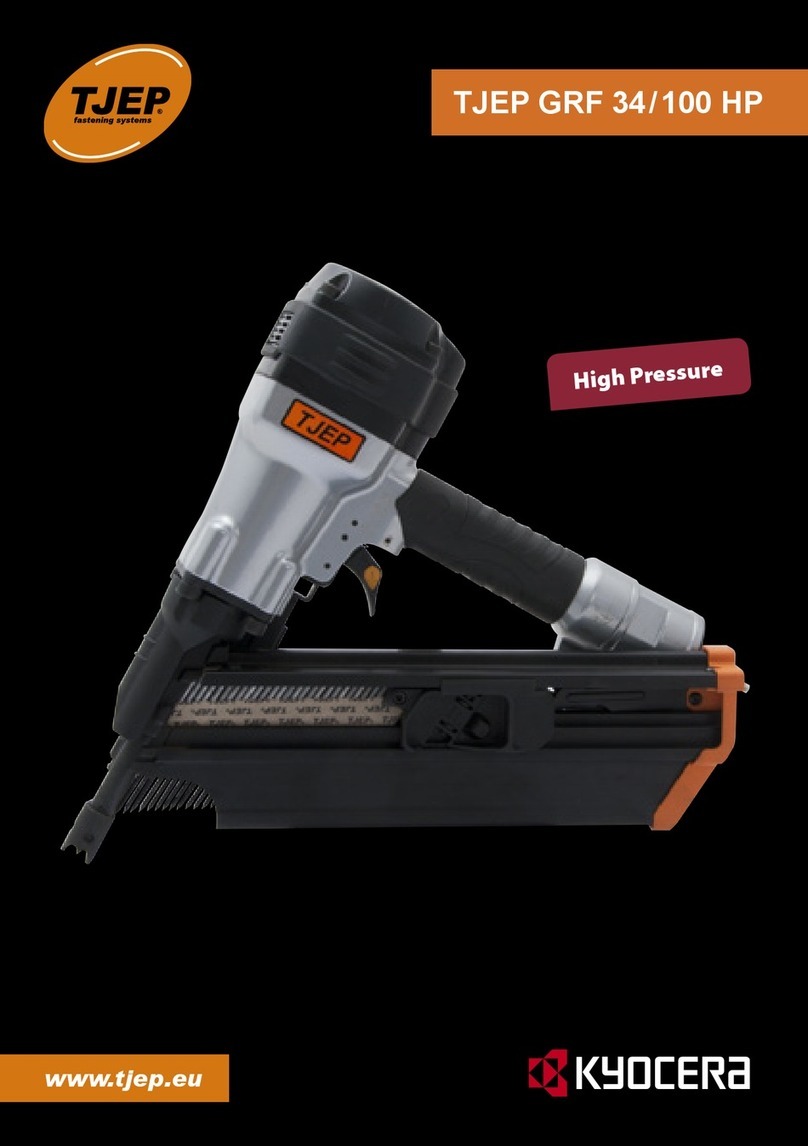
Kyocera
Kyocera TJEP GRF 34/100 HP quick start guide

Bosch
Bosch GBL 800 E Professional Original instructions
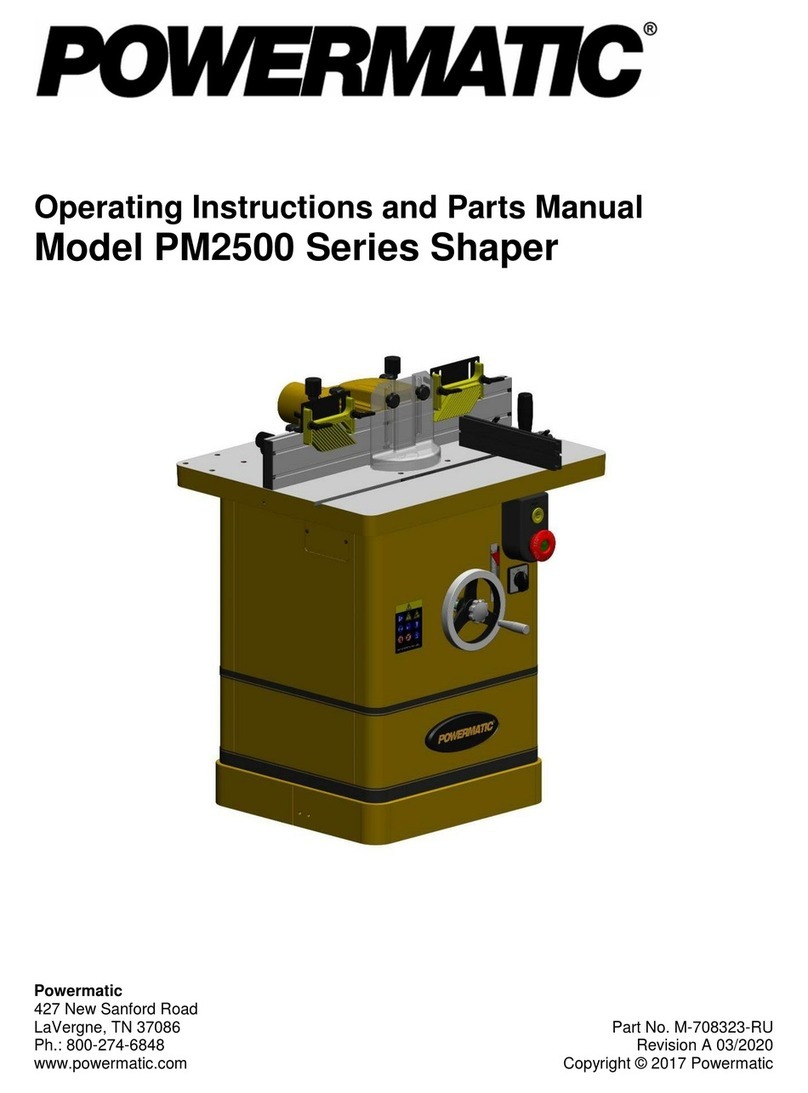
Powermatic
Powermatic PM2500 Series Operating instructions and parts manual