TUG M3 Guide

Property of American Airlines
Maintenance

Chapter 2-Contents Aug, 1997 p. 2
Maintenance
SECTION PAGE
E. MAIN POWER ("IGNITION") SWITCH REMOVAL .......................................................................2
F. MAIN POWER ("IGNITION") SWITCH INSTALLATION ...............................................................2
G. MASTER CYLINDER REMOVAL ..................................................................................................3
H. MASTER CYLINDER INSTALLATION...........................................................................................3
I. STEER VALVE REMOVAL.............................................................................................................3
J. STEER VALVE INSTALLATION..................................................................................................... 4
K. TIRES AND WHEELS ...................................................................................................................4
M. ACCELERATOR PEDAL INSTALLATION: ....................................................................................6
N. HYDRAULIC STEERING PUMP REMOVAL .................................................................................6
O. HYDRAULIC STEERING PUMP INSTALLATION .........................................................................7
P. BRAKE BOOSTER PUMP REMOVAL ..........................................................................................8
Q. BRAKE BOOSTER PUMP INSTALLATION...................................................................................8
R. REPLACE DRIVE MOTOR BRUSHES .........................................................................................9
S. DRIVE MOTOR(S) REMOVAL ....................................................................................................10
T. DRIVE MOTOR(S) INSTALLATION............................................................................................. 11
U. CONTACTOR TIPS REMOVAL/REPLACEMENT ....................................................................... 11
V. BATTERY REMOVAL/REPLACEMENT:......................................................................................13
W. SERVICE BRAKES REMOVAL/INSTALLATION .........................................................................13
X. PLANETARY REDUCTION HUBS REMOVAL ............................................................................14
Y. PLANETARY REDUCTION HUBS INSTALLATION ....................................................................14
IV. ADJUSTMENTS......................................................................................................................................1
A. PARK BRAKE ................................................................................................................................1
B. SERVICE BRAKE ADJUSTMENT.................................................................................................1
Property of American Airlines

Chapter 2-Contents Aug, 1997 p. 3
SECTION PAGE
C. VERTICAL HEADLIGHT ADJUSTMENT.......................................................................................1
D. FRONT SPRING PRELOAD ADJUSTMENT ................................................................................2
E. BLEED REAR BOOSTED BRAKES (CONT) ................................................................................4
V. INSTRUCTIONS FOR JACKING AND POSITIONING VEHICLE .........................................................1
A. SAFETY PREREQUISITES...........................................................................................................1
B. PROCEDURE ................................................................................................................................1
Property of American Airlines

Chapter 2-Contents Aug, 1997 p. 4
(This Page Intentionally Left Blank)
Property of American Airlines

Chapter 2: Maintenance Sept. 1995 Section 2-1 p. 1
I. SERVICING
A complete preventive maintenance checklist is included in Chapter 5 of this manual (Appendices).
See section 5-1.
A. GENERAL PREPARATIONS FOR USE:
1. Battery
Assuming a minimum 80% charge, the duration of usable charge of the M3 battery will
vary from several hours to perhaps a day or more, depending on many factors. Variables
that affect length of usable charge include the percentage of initial day's charge, intensity
of use, size and condition of battery, weight of towed loads as well as environmental
factors such as ambient temperature. The battery should be fully charged before the unit
is put into service on a daily basis. For a complete discussion on battery charging cycles
and electrolyte maintenance, see chapter 1-5.
(a) Check the battery fluid level. Top up with distilled or approved drinking water, as
necessary.
(b) Connect the battery cables, if disconnected, positive first.
2. Brake System
(a) Check master cylinder fluid level.
Should the brake system require fluid, the master cylinder is located behind the
console panel to the right of the steering wheel. Master cylinder reservoir should be
topped off with a high quality brake fluid, DOT 3 or better.
The second brake fluid reservoir is located in the right service compartment above
the hydraulic pump (See Figure 1). The brake booster pump that provides braking
power to the rear wheels.
If low, check for leaks in brake lines.
Figure 1
Property of American Airlines

Chapter 2: Maintenance Sept. 1995 Section 2-1 p. 2
I. SERVICING
A. GENERAL PREPARATIONS FOR USE:
2. Brake System (cont)
(b) Service brakes should be tested for pedal firmness and braking effectiveness.
(c) Check park brake. With the main switch in the off position, the park brake should
hold the unit in place on a 10% grade.
IMPORTANT: Drive train has no "park" position and must rely on park brake to
prevent vehicle from rolling. Always make sure park brake is properly
adjusted before putting vehicle into service.
Adjust park brake cable tension by rotating cap
handle on park brake lever.
3. Check Tire Inflation.
4. Check hydraulic fluid level.
(Refer to lubrication section, ch. 2-1B)
Figure 1: Brake System Layout
Property of American Airlines

Chapter 2: Maintenance Sept. 1995 Section 2-1 p. 3
B. PREVENTIVE MAINTENANCE SCHEDULE (SEE ALSO: PREVENTATIVE MAINTENANCE
CHART IN APPENDICES CHAPTER)
THE TRACTOR SHOULD BE MAINTAINED IN ACCORDANCE WITH THE FOLLOWING
SCHEDULES:
1. Daily; Check:
(a) That all controls are in good working order. Report a faulty TUG control and do not
use until repaired.
(b) Battery charge level.
(c) Hydraulic fluid level.
(d) Battery electrolyte level
(e) The pressure of the pneumatic tires:
Drive Wheels 60 psi
Steer Wheels 40 psi
WARNING: Do not change pneumatic tire for cushion tire or vice versa
without first consulting TUG Manufacturing Corporation. Tires of a different
type or make, tread or material can reduce the load capacity or affect safety.
(f) The tire treads for damage. Remove any stone, etc.
(g) The operation of the headlights and if aimed correctly.
(h) The operation of backup, tail, stop and turn signal lights (if so equipped).
(i) The operation of the cab marker lights, the heater, the wiper and cab light, if
equipped.
(j) The horn.
2. Weekly or 50 Hour Check:
(a) Lug Nut tightness: The wheel lug nuts are tightened to 125 ft. - lbs.
WARNING: Lug nuts must be retightened to 125 ft. - lbs. after any change of a
wheel and anytime the lug nuts have been loosened for any reason, and at the
intervals specified in this Preventive Maintenance Section.
(b) The level of the brake fluid in the master cylinder & brake booster. If low, top up as
necessary.
Property of American Airlines

Chapter 2: Maintenance Sept. 1995 Section 2-1 p. 4
Figure 3
CHECK
I. SERVICING
B. PREVENTIVE MAINTENANCE SCHEDULE (CONT)
3. Monthly or 200 Hour Check:
(a) The Parking Brake
With the parking brake handle in ‘lock’ position, the tractor should not move on an 10
or less percent grade. If the tractor does not move, no adjustment is necessary, but
if the tractor rolls, then adjustment is advised. Follow the recommended adjustment
instructions in this Section.
(b) Power steering fluid.
(c) Planetary Reduction Hub fluid level.
(d) The adjusting slides beneath the operator’s seat.
(e) The service brake pedal pivot.
(f) The parking brake linkage.
(g) The throttle linkage.
(h) The steering axle & king pins adjustment.
(i) The sliding pins on the
rear brake calipers.
(j) All grease fittings.
(k) Console and battery
cover latches and
hinges.
(l) Cab door handles (if
equipped).
4. Two (2) Months or 400 Hours;
Check:
Inspect Front wheel bearings;
clean and repack.
5. Yearly or 2400 Hours
(a) Drain, flush and refill the hydraulic brake system, and bleed the brake system.
Property of American Airlines

Chapter 2: Maintenance Sept. 1995 Section 2-1 p. 5
(b) Drain, flush and refill the hydraulic
steering system.
(c) Drain & refill planetary drive hubs.
(See Figure 3 and Chapter 5 Supplement)
6. Lubricant Chart
(a) Schematic
ITEM # COMPONENT/SYSTEM
1 STEER CYLINDER ENDS
2 KING PINS (TOP)
3 TIE ROD ENDS
4 KING PINS (BOTTOM)
5 WHEEL BEARINGS
6 PLANETARY REDUCTION HUBS
7 HYDRAULIC PUMP
8 BRAKE BOOSTER PUMP
(b) Alphabetical Table
Component/System Lubricant Type or Specification
Adjusting Slides, Seat, Operator’s Multipurpose lithium-based grease
Axle Hubs, Front Multipurpose lithium-based grease
Brake Calipers. Rear Silicon Base Grease
Cab Door Handles Multipurpose lithium-based grease
Hydraulic Brake System Brake Fluid, DOT 3, Extra Heavy Duty
Power Steering Fluid Transmission Fluid; Dexron Type II
Steering King Pins Multipurpose lithium-based grease
Figure 4
Property of American Airlines

Chapter 2: Maintenance Sept. 1995 Section 2-1 p. 6
B. PREVENTIVE MAINTENANCE SCHEDULE
6. Lubricant Tables (cont.)
(c) Lubricant to Component/System Table:
Hydraulic Fluid, DOT 3, Extra Heavy Duty: Hydraulic Brake System
Multipurpose Lithium based Grease: Adjusting Slides, Seat, Operator’s
Axle Hubs, Front
Brake Pedal Pivot
Cab Door Handles
Drive Shaft Joints
Hood Latch and Hinges
Parking Brake Linkage
Steer King Pins
Rear Brake Calipers
(d) Lubricant to (Commercially Available) Product Table
Hydraulic Fluid, DOT 3, Extra Heavy Duty
-Lockheed Super 105 Hydraulic Fluid
Multipurpose Lithium-based Grease
-Texaco Marfak Multipurpose 2
Silicon Base Grease
-Ford Part No. D7AZ-19A-331-A
Planetary Reduction Hub Fluid
-Amzoil Lubricant
Property of American Airlines

Chapter 2: Maintenance Mar, 1996 Section 2-2 p. 1
II. Troubleshooting
The M3 is an electric vehicle and depends on sound electrical connections for all its power.
Subesquently, a higher emphasis should be placed on checking for and maintaining clean, corrosion-
free electrical connections. Many of the troubleshooting procedures listed in the following pages
indicate possible connection or contact problems that might prevent the proper flow of electricity from
one point to the next. IN ANY TROUBLESHOOTING PROCEDURE, ALWAYS LOOK FOR APPRO-
PRIATE ELECTRICAL CONNECTIONS BEFORE ATTEMPTING TO REMOVE, REPLACE OR
TROUBLESHOOT COMPONENTS.
WARNING! WHEN TESTING AN ELECTRIC VEHICLE, JACK THE DRIVE WHEELS OFF THE
GROUND AND SECURE IN THIS POSITION WITH JACK STANDS OF ADEQUATE CAPACITY.
DANGER - AVOID DEATH - WHEN TESTING THE CONTROLLER, DO NOT TOUCH HIGH VOLT-
AGE CONNECTIONS EXCEPT WITH PROPER TEST EQUIPMENT. WHEN WORKING INSIDE
THE CONTROL PANEL, USE THE FOLLOWING PROCEDURE TO DISCHARGE THE CAPACI-
TORS INSIDE THE CONTROLLER.
1. TURN THE IGNITION KEY ON.
2. DISCONNECT THE BATTERY.
3. WAIT 10 SECONDS, THEN TURN THE KEY OFF.
DIAGNOSTICS:
The SC2000 controller in your M3 Tow Tractor contains a powerful fault diagnostic system that must be
used in conjunction with a portable electronic diagnostics computer. This device, referred to in the
following pages as a "handset" has a modular connector that connects directly to the controller. The
handset is sold separately, but need not be purchased with each M3 tractor. Rather, one handset will
probably be sufficient for your needs in diagnosing and servicing your entire Tug Model M3 Tow Tractor
fleet.
If the tractor will not drive, and resetting the shifter, handbrake e-stops and recycling the keyswitch fails
to clear the problem, the handset or controller fault code should be used first to diagnose the problem.
The controller will flash out "fault codes" when an error is detected. The diagnostic light is located on
the end of the controller closest to the front of the vehicle. The telephone-type plugs for plugging the
handset in are also located there. (See Figure 1.)
Property of American Airlines

Chapter 2: Maintenance Mar, 1996 Section 2-2 p. 2
Diagnostic LED
Handset Plugs
Property of American Airlines

Chapter 2: Maintenance Mar, 1996 Section 2-2 p. 3
II. TROUBLESHOOTING (CONT)
A. CAN CONTROLLER
A sophisticated yet easy to use hand held adjustment unit, called the Can Controller is used to
make adjustments to the controller and select configurations. The CAN Controller is also used as
a diagnostic tool displaying the status of all voltages, currents and temperatures within the
controller together with the condition of all the controllers switch and analogue inputs.
The diagram below describes how the CAN Controller is used. The left and right arrows move
between screens on the same level. The up and down arrows move between levels and the (+)
and (-) buttons increment or decrement the parameters by the amount indicated in the STEP
column.
Property of American Airlines

Chapter 2: Maintenance Mar, 1996 Section 2-2 p. 4
II. TROUBLESHOOTING (CONT)
B. TRACTION PERSONALITIES (CONTROLLER ADJUSTMENTS)
Cal. Parameter Adjusted Min Settings Max. SettingsMax Settings Step Size Factory Settings
Ref. (All Units) (500A units) (650A units) (all units) (all units)
1.1.1 Current Limit Min. Setting 500A 650A 10 Amps 500A
1.1.2 Acceration Delay Max. Setting 5.0S 5.0S 0.1 Secs 2.4 Secs
1.1.3 Deceleration Delay Max. Setting .05S .05S 0.1 Secs 0.1 Secs
1.1.4 Creep Speed (all units) 25% 25% 1.00% %
1.1.5 Maximum speed (500A units) 100% 100% 1.0~ 100o
1.1.6 Cutback Speed 1 (650 A units) 100% 100% 1.00% 25%
1.1.7 Acceleration Delay1 50A 5.0S 5.0S 0.1 Secs 4.0 Secs
1.1.8
Cutback Speed 2/Inch Speed
0.1S 100/25% 100/25% 1.00% 40%
1.1.9 Acceleration Delay 2 0.1S 5.0S 5.0S 0.1Secs 5.0 Secs
1.1.10 Direction Brake Current 0% 500A 650A 10 Amps 50 Amps
1.1.11 Footbrake Current p% 500A 650A 10 Amps 70 Amps
1.1.12 Neutral Brake Current 0% 500A 650A 10 Amps 40 Amps
1.1.13 Bypass Over Current 0.1S 750A 970A 10 Amps 600 Amps
1.1.14 Field weak Pull In p% 500A 650A 10 Amps ---
1.1.15 Field Weak Drop Out 0.1S 500A 650A 10Amps ---
1.1.16 Power Steer Delay 50A 50S 50S 1.0 Secs 10 Secs
1.1.17 Seat Switch Delay 10A(0 disables) 5.0S 5.0S 0.1 Secs 1.5 Secs
1.1.18 Regen Speed Factor 10A(0 disables) 255% 255% 1.0~o 150
1.1.19 Brake Constant Factor 10A(0 disables) 25.5x 25.5x .01x 0.9
1.1.20 Accelerator Zero Level 50A 5.5V 5.5V 0.1 Volts 3.4 V
1.1.21 Accelerator Full Level 50A 5.5V 5.5V 0.1 Volts 0.1V
1.1.22 Footbrake Pot Zero Level OS 5.5V 5.5V 0.1 Volts 5.0V
1.1.23 Footbrake Pot Full Level OS 5.5V 5.5V 0.1 Volts 2.0V
1.1.24 Economy Pot Zero Level 0% 5.5V 5.5V 0.1 Volts ---
1.1.25 Economy Pot Full Level Ox 5.5V 5.5V 0.1 Volts ---
1.1.26 Contactor Chopping Select OV On off
Current Limit -Maximum allowable motor current.
Acceleration Delay -Time taken to ramp up from 0 to 100% on.
Deceleration delay -Time taken to ramp down from 100% to 0% on.
Creep Speed -Minimum applied % on when drive first selected.
Maximum Speed -Maximum allowable % on.
Cutback Speed 1 & 2 -Maximum allowable % on when cutback switches active, or inching.
Accel. Delay 1 & 2 -Independently adjustable accel. delays during speed cutbacks.
Dir. Brake Current -Maximum braking current during direction switch change.
Footbrake Current -Maximum braking current in neutral when F. Srake switch active
Neut. Brake Current -Maximum braking current in neutral
Bypass Over Current -Maximum allowable current in Bypass before contactor opens.
F.W. Pull In Current -F.Weak contactor allowed to pull in at currents ~ pulll in level
F.W Drop out Curr. -F. Weak contactor will drop out at current ~ drop out level
Power Steer Delay -Delay after power steer trigger removed until contactor opens
Seat Switch Delay -Delay after seat switch opens until pulsing is inhibited.
Regen Speed -Regen attempted at lower speeds (Low Nos.) or higher speeds (High Nos.) used to prevent
delays for unsuccesful regen attempts at low speeds
Brake Factor -Multiplication factor used to scale regen currents into end plug currents. E.g. Regen neut
brake=100A, factor=0.8, plug current at end of cycle=80A.
Zero Levels (3 off) -Used to select minimum voltage input level for function.
Full Levels (3 off) -Used to select maximum voltage input level for function.
Property of American Airlines

Chapter 2: Maintenance Mar, 1996 Section 2-2 p. 5
C. TRACTION FAULT MESSAGES
Message No. of Flashes Description Check
OK (on) Traction Operational N/A
“Sequence Fault” (2) Direction or FSl sw at power up Dir and FS1 in neutral, Wiring
“2 Dir Fault” (2) Two directions selected together Only one direction selected, Wiring
“SRO Fault” (2) Dir sw selected >2secs after FSl Dir first then FS1, FS1 wiring
“Seat Fault” (2) Drive selected and no seat sw Ciose seat sw, wiring
“Inch Fault” (2) Inch sw at power up, or both Both in neutral, or only one switch
selected
“Mosfet s/c” (3) Bypass cont. S/C or Mosfet S/C Bypass welded, Wiring, Mosfets s/c
“Forward o/c” (4) Forward contactor didn’t close Coil wiring, Cont. Wiring Tips,
Motor o/c
“Reverse o/c” (4) Reverse contactor didn’t close Coil wiring, Cont. Wiring & Tips,
Motor o/c
“Regen o/c” (4) Regen contactor didn’t close Coil wiring, Cont. Wiring Tips,
Motor o/c
“Contactor s/c” (4) Fwd or Rev cont. short circuit Welded tips & Contactor wiring
“Forward s/c” (4) Forward contactor didn’t open Welded tips & Contactor wiring
“Reverse s/c” (4) Reverse contactor didn’t open Welded tips 8 Contactor wiring
“Regen s/c” (4) Regen contactor didn’t open Welded tips Contactor wiring
“Capacitor Fault” (5) Main caps not charging at power Power wiring or Charge resistor o/c
Up
“Accel Fault” (6) Accel. pedal at power up or wire Pedal not pressed, Wire off, Wiring
off
“Battery Low” (7) Battery <Low Battery personality Correct Batt. Voltage, Discharged
battery
“Thermal Cutback” (8) Traction heatsink above 75' C
Heatsinking, Mounting, Surface’s
“Coil s/c” (9) A contactor coil s/c or Pin connected directly to B+ve, coil
misconnected s/c
“CRC error” (1) Personality or other config error Reconfigure and check all personali-
ties
“Failed” (off) Controller unable to autofailsafe Wiring
Property of American Airlines

Chapter 2: Maintenance Mar, 1996 Section 2-2 p. 6
II. TROUBLESHOOTING (CONT)
D. STATUS
Status indicators provide information on the voltages and currents of various components both
within the controller and throughout the tractor. The normal status readings available are as
follows:
Key on - Not Driving
Battery Voltage: 0 - 127 volts. 80-86 volts
Traction Motor Voltage Left: 0 - 127 volts. 0 volts
Traction Motor Voltage Right: 0 - 127 volts. 0 volts
Traction Motor Current Left: 0 - 1200 Amps. 0 amps
Traction Motor Current Right: 0 - 1200 Amps. 0 amps
Traction Controller Temp Left: 30°C - 225°C
Traction Controller Temp Right: 90°C - 225°C
Traction MOFSET Voltage Left: 0 - 127 Volts. 11 - 12 volts
Traction MOFSET Voltage Right: 0 - 127 Volts. 11 - 12 volts
Capacitor Voltage: 0 - 127 Volts: 80 - 86 volts
Key Switch Hours: 0 - 65279.9 hours
Traction Pulsing Hours: 0 - 65279.9 hours
E. TEST
The test section allows the technician to troubleshoot the tractor by observing the inputs that the
controller is receiving. The following test modes are available:
Accelerator %
Accelerator voltage
Footbrake %
Footbrake voltage
Economy % (not used)
Forward switch
Reverse switch
FS1
Seat
Handbrake
Speed cutback 1
Speed cutback 2
Power steer trigger
Inch forward
Inch reverse
Software version
Property of American Airlines

Chapter 2: Maintenance Mar, 1996 Section 2-2 p. 7
F. SC2000 FAULT FINDING FLOW CHARTS
1. Two Flash Fault (2FF) - Procedure Fault
CAN Calibrator
Display Message CONDITION CHECK
Direction or FS1 1. Direction & FS1 are in
Sequence Selected at Key Neutral at Key Switch On
Fault? Switch on. 2. Wiring is Correct
1. Only One direction
2 DIR FWD and REV selected.
Fault? Selected together 2. Wiring
SRO Dir. selected <2 secs 1. Direction first, then FS1.
Fault? after FS1. 2. FS1 Wiring
Seat Drive selected and no 1. Select seat switch
Fault? seat switch. before drive.
2. Wiring
Inch Inch switch selected 1. Both inch switches
Fault? at power up or both are in neutral.
selected. 2. Wiring
YES
NO
YES
NO
YES
NO
YES
NO
YES
Property of American Airlines

Chapter 2: Maintenance Mar, 1996 Section 2-2 p. 8
F. SC2000 FAULT FINDING FLOW CHARTS
2. Three Flash Fault (3FF) - Bypass Contactor Welded
CAN Calibrator
Display Message CONDITION CHECK
1. Bypass contactor 1. Direction & FS1 are in
MOFSET Short circuit. Neutral at Key Switch On
S/C? 2. Mofsets short 2. Power and control
circuit wiring for shorts.
3. Mofset short circuit.
Replace controller.
YES
Property of American Airlines

Chapter 2: Maintenance Mar, 1996 Section 2-2 p. 9
YES
NO
YES
NO
YES
NO
3. Four Flash Fault (4FF) - Contactor Fault or Motor Open Circuit (O/C)
- Contactor Fault or Motor Short Circuit (S/C)
CAN Calibrator
Display Message CONDITION CHECK
1. Contactor coil wiring.
Forward Forward contactor 2. Contactor power cable
O/C? did not close. wiring.
3. Contactor tips.
4. Open Circuit Motor.
5. Replace Controller.
Reverse Reverse contactor
O/C? did not close.
Regen Regen contactor
O/C? did not close.
Property of American Airlines

Chapter 2: Maintenance Mar, 1996 Section 2-2 p. 10
YES
NO
YES
NO
YES
NO
II. TROUBLESHOOTING (CONT)
F. SC2000 FAULT FINDING FLOW CHARTS
3. Four Flash Fault (4FF) - Contactor Fault or Motor Short Circuit (cont)
CAN Calibrator
Display Message CONDITION CHECK
1. Welded contactor tips.
Contactor Forward or Reverse 2. Contactor power cable
S/C? contactor short circuit. wiring.
3. Motor for armature to
field short circuit.
4. Short to frame and
battery leakage.
5. Replace Controller.
Forward Forward contactor
S/C? did not open.
Reverse contactor
Reverse did not open.
S/C?
Regen contactor
Regen did not open.
S/C?
YES
Property of American Airlines
Other manuals for M3
1
Table of contents
Other TUG Tractor manuals
Popular Tractor manuals by other brands
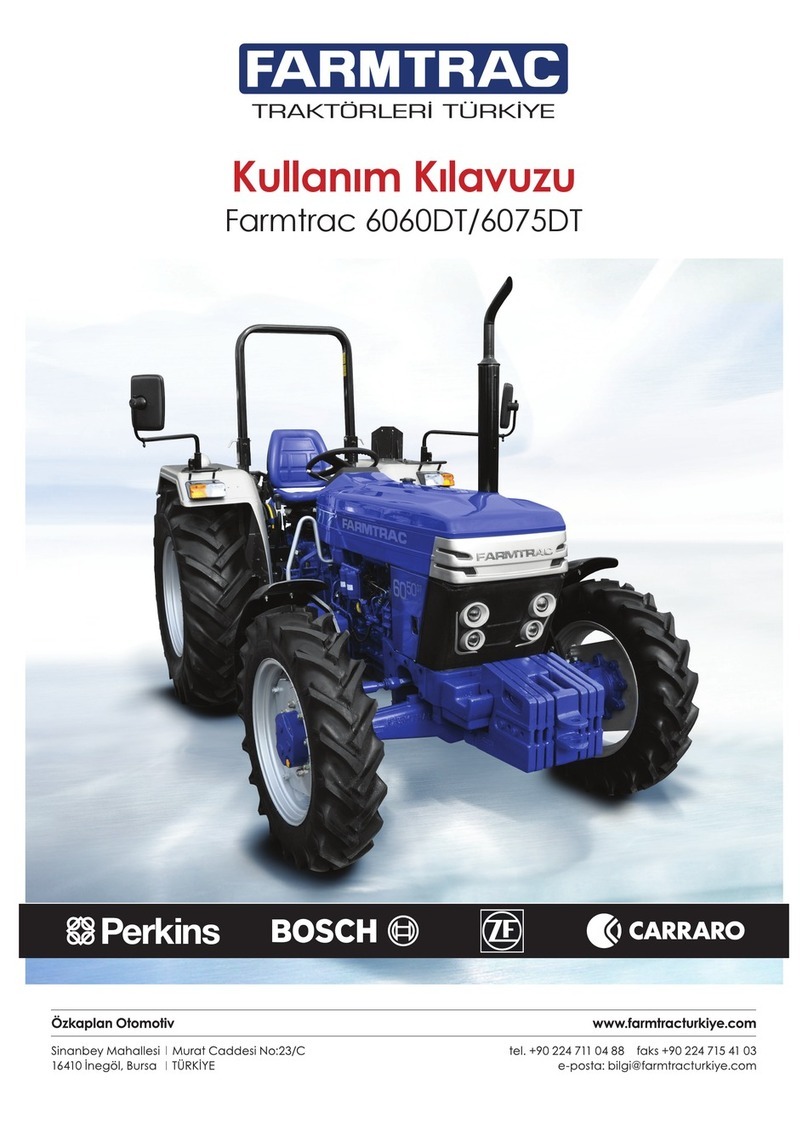
Farmtrac
Farmtrac 6060DT Operator's manual
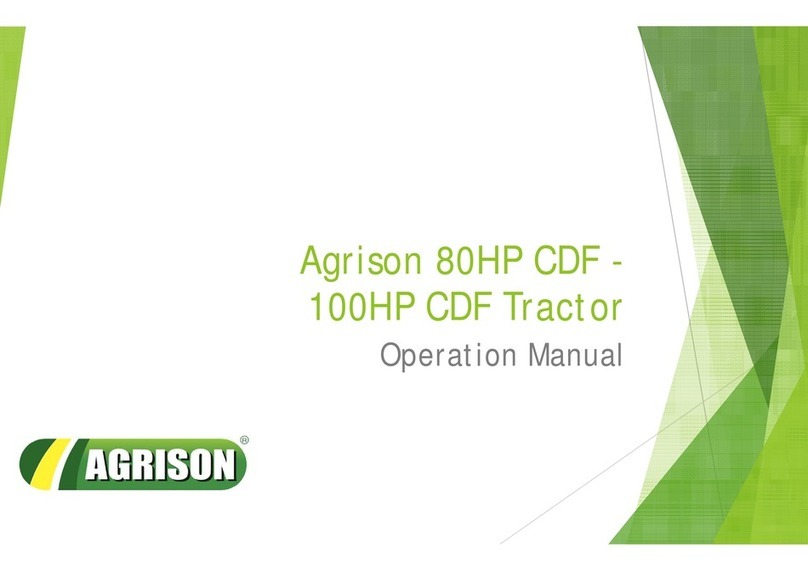
Agrison
Agrison 80HP CDF Operation manual
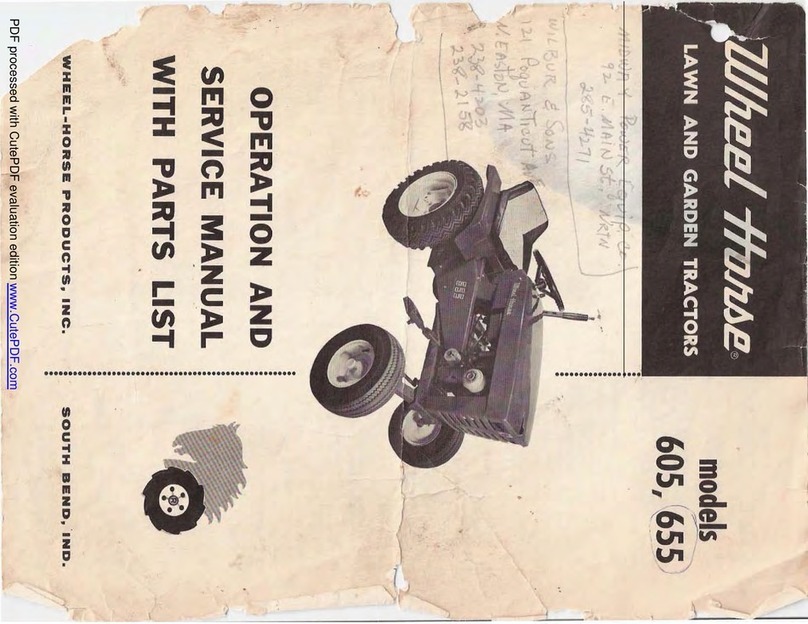
Wheel Horse
Wheel Horse 605 Operation and Service Manual with Parts List
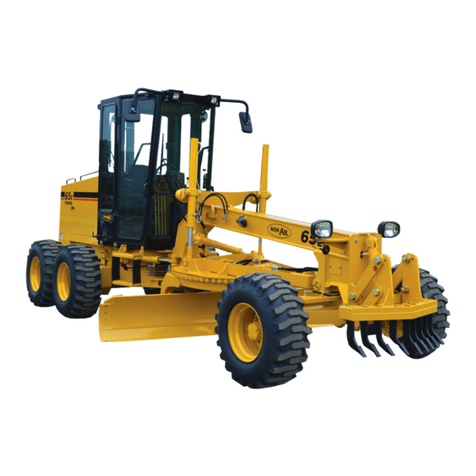
NorAM
NorAM 65E Turbo Motor Grader Service manual
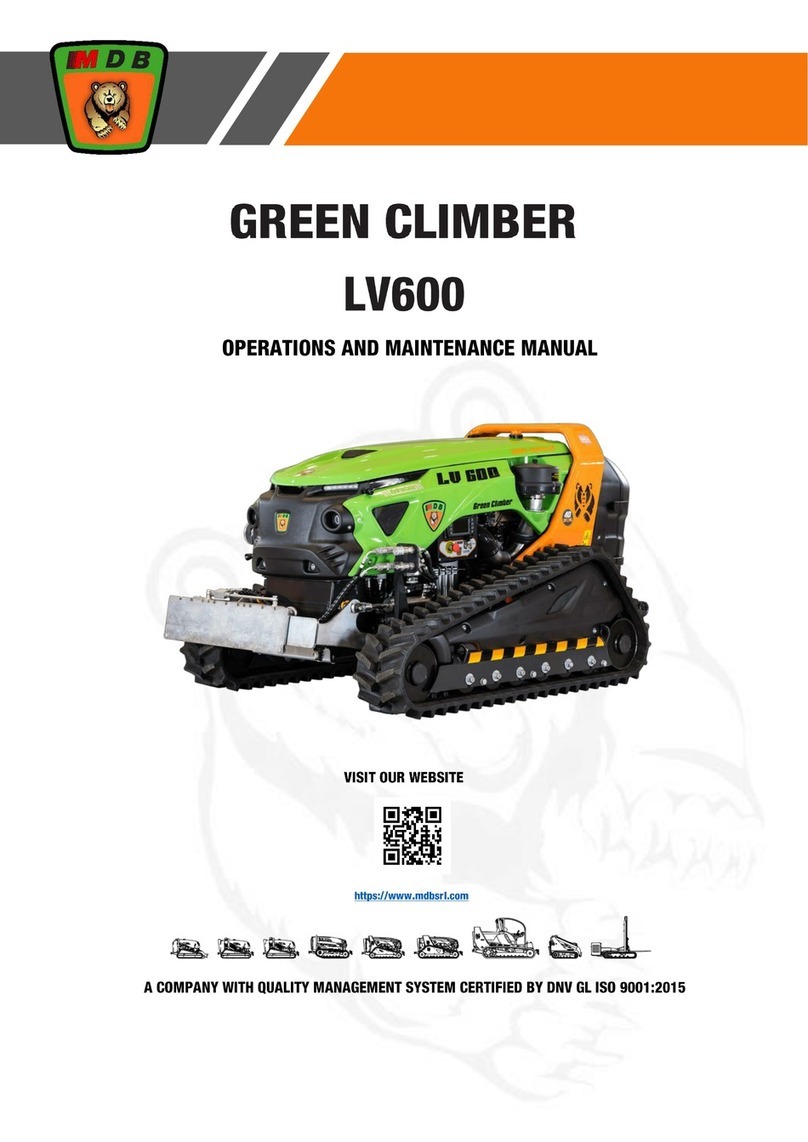
MDB
MDB GREEN CLIMBER LV600 Operation and maintenance manual
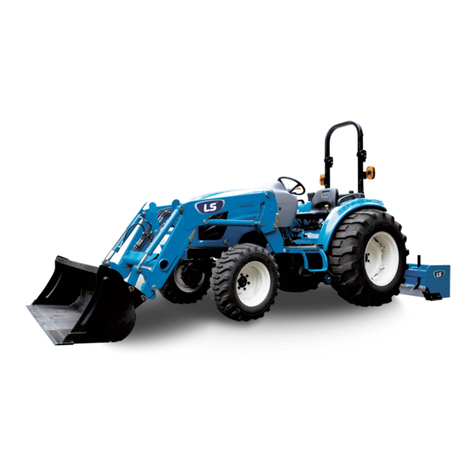
LS tractor
LS tractor MT345E Operator's manual