UHVD MASC User manual

MASC Revision: 1.1 Author: N.Carapiet
QUICK START GUIDE
Product: MASC Multi Axis Stepper Controller
Product Description
Stepper Motor Controller

MASC QUICK START GUIDE
Page 2of 19
TABLE OF CONTENTS
Table of Contents
IMPORTANT SAFETY INFORMATION!.........................................................................................4
POSITION CONTROL SYSTEMS ARE INHERENTLY HAZARDOUS. EVEN A SMALL MOTOR, IF
COUPLED TO A LEADSCREW, GEARBOX, OR ANY OTHER FORM OF MECHANISM THAT
PROVIDES A MECHANICAL ADVANTAGE, CAN GENERATE CONSIDERABLE FORCE AND
COULD CAUSE SERIOUS INJURY. INCORRECT OPERATION CAN ALSO LEAD TO DAMAGE
TO THE MOTOR OR ASSOCIATED MACHINERY. IT IS ESSENTIAL THAT THE PURPOSE OF
THE VARIOUS FAULT DETECTION FEATURES BUILT INTO THE MASC’S ST5-Q CONTROLLER
BE FULLY UNDERSTOOD AND USED CORRECTLY. .......................................................................4
AS SUCH, INSTALLATION MUST BE CARRIED OUT ONLY BY COMPETENT PERSONS WHO ARE
FAMILIAR WITH ELECTRONIC CONTROL SYSTEMS.......................................................................4
OVERVIEW......................................................................................................................................4
LAYOUT - FRONT...................................................................................................................4
LAYOUT –REAR ....................................................................................................................5
GETTING STARTED.......................................................................................................................5
UNPACKING ...........................................................................................................................5
CONNECTIONS TO MASC.....................................................................................................6
3.2.1 Power Connection.................................................................................................................7
3.2.2 D Type Connectors...............................................................................................................7
3.2.3 M12 Connectors....................................................................................................................8
3.2.4 Single Axis Systems .............................................................................................................8
3.2.5 Multi Axis Systems................................................................................................................9
CONNECTIONS TO DEVICES ...............................................................................................9
3.3.1 M12 Connectors....................................................................................................................9
3.3.2 UTO Connectors.................................................................................................................10
3.3.3 LEMO Connectors ..............................................................................................................11
3.3.4 Encoder Connections..........................................................................................................11
CONNECTION TO PC...........................................................................................................12
CONNECTION TO JOG BOX................................................................................................13
CHECKS................................................................................................................................13
OPERATION..................................................................................................................................14
JOG BOX...............................................................................................................................14
4.1.1 Jog Mode ............................................................................................................................15
4.1.2 SEQUENCE MODE............................................................................................................16
4.1.3 Limits and Datum Mode......................................................................................................18
4.1.4 Status Mode........................................................................................................................19
JOG EMULATOR ..................................................................................................................19

MASC QUICK START GUIDE
Page 4of 19
IMPORTANT SAFETY INFORMATION!
This document is intended as a user guide to operation as determined by the design.
Position control systems are inherently hazardous. Even a small motor, if coupled to a leadscrew,
gearbox, or any other form of mechanism that provides a mechanical advantage, can generate
considerable force and could cause serious injury. Incorrect operation can also lead to damage to
the motor or associated machinery. It is essential that the purpose of the various fault detection
features built into the MASC’s ST5-Q controller be fully understood and used correctly.
As such, Installation must be carried out only by competent persons who are familiar with electronic
control systems
OVERVIEW
The MASC is a single axis stepper motor controller in a compact rack mountable enclosure. It is a
versatile, high-performance microstepping packaged unit suitable for light industrial and scientific uses
where precision and system-level integration are required. Monitoring and control can be achieved over
a RS-485 serial connection that can be easily configured in multi-drop for the coordinated use of several
drivers over the same connection. RS232 is also an option for single axis applications.
The MASC controller consists of a ST5-Q programmable microstepping drive and an integrated 24V
DC universal input power supply built into a 21HP 3U subrack unit for mounting into industry standard
19” racks. This allows for up to four MASC units to be fitted in one standard 84HP wide rack.The MASC
is supplied for plug and play operation with UHV Design stepper motorised products. The MASC will be
factory preset when purchased with a stepper motorised device.
LAYOUT - FRONT
On/Off Switch
Axis Identification
Sticker (if more than
one axis configured).
Status LED’s

MASC QUICK START GUIDE
Page 5of 19
LAYOUT –REAR
GETTING STARTED
UNPACKING
Included in each package:
MASC (stepper motor controller) x 1
MASC-TP (RS485/232 terminator plug) x 1
MASC-JC-03 (PC/Jog Box connection lean) x 1
Mains Power
Input
Mains Fuse
RS-485/RS232
in (from PC or
Jog Box)
RS-485/RS232
out (terminator
or next MASC)
Stepper
Motor Socket
Limit & Home
Switch Socket
Encoder
Socket
Brake Socket

MASC QUICK START GUIDE
Page 6of 19
MASC-USB (USB to serial RS-485 converter) x 1
UK Mains power Lead x 1
US Mains power lead x 1
EU Mains power lead x 1
Additional cables and jog box for connection to UHV Design stepper motorised products are
provided with the control packages and should be configured when purchasing the device. Cables
may be packaged within the MASC packaging.
CONNECTIONS TO MASC
A dedicated series of cables that allow connection between the MASC and any UHV Design stepper
motorised devices are available and should be configured when purchaing the MASC and device
together.
Note: It is important not to switch on the MASC until all connections are securely made. Unplugging
cables, in particular the motor cables, whilst the MASC is switched on can cause damage to the
MASC or motor.

MASC QUICK START GUIDE
Page 7of 19
Note: all connectors going into the back of the MASC are straight. Connectors going to motors
and switches are generally right angled.
3.2.1 Power Connection
1. Choose appropriate power lead for region e.g. UK, US
2. Push plug into IEC socket on rear of MASC.
3.2.2 D Type Connectors
1. Push connector into socket
2. Rotate locking screws clockwise until finger tight
Note: it is easier to plug in the 25 way D connector for switches (if used) after plugging in the
motor and encoder connectors.
Locking Screws

MASC QUICK START GUIDE
Page 8of 19
3.2.3 M12 Connectors
1. Push connector into socket. Note: socket will not engage unless key features are aligned
correctly.
2. Turn knurled nut clockwise until finger tight to fully engage connector pins.
3.2.4 Single Axis Systems
When only one MASC is used:
1. Connect to a PC/laptop using MASC-JC-03 into the RS-485 In port
2. Plug the RS-485 termination plug, MASC-TP, into the RS-485 out port. Failure to use the
MASC-TP can cause communication error.
Alignment key and slot
Knurled Nut
RS-485 Out Port
MASC-TP
RS-485 In Port
MASC-JC-03

MASC QUICK START GUIDE
Page 9of 19
3.2.5 Multi Axis Systems
When more than one MASC is configured to work as a multi axis system (all controlled by one PC or
MASC-JB) then the MASC’s are daisy chained together. Use the MASC-LC to link MASC’s together.
1. Plug First MASC (Axis 1) into PC/laptop as described in section 3.4
2. Plug the MASC-LC into the out port of the first axis MASC’s RS-485 out port and into the next
MASC’s RS-485 In port.
3. Repeat step 2 for as many MASC’s that have been configured
4. Plug the MASC-TP. Into the last MASC’s RS-485 out port. Failure to use the MASC-TP can
cause communication error.
CONNECTIONS TO DEVICES
3.3.1 M12 Connectors
Connecting stepper motors and encoders with M12 motor connections. The procedure is the same for
male and female connectors.
1. Push connector into socket. Note: socket will not engage unless key features are aligned
correctly.
2. Turn knurled nut clockwise until finger tight to fully engage connector pins.
Alignment key and slot
MASC-TP
MASC-LC
MASC-JC-
03 (to PC)

MASC QUICK START GUIDE
Page 10 of 19
3.3.2 UTO Connectors
Older stepper motorised products use UTO style connectors on the motors. There is an adaptor cable
supplied with every motor cable to convert from the standard M12 connector to a UTO (part number
WD-C-006). To attach M12 cables together, see section 3.2.3
1. Push connector into socket. Note: socket will not engage unless key features are aligned
correctly on both the plug and locking ring
2. Twist the knurled locking ring clockwise until it clicks. (approximately 30°)
Knurled Nut
Knurled
Locking Ring
Plug alignment key
and slot
Locking ring
locating key

MASC QUICK START GUIDE
Page 11 of 19
3.3.3 LEMO Connectors
All limit switch connectors are made with a 6 pin right angled LEMO connector.
1. Push the connector into the socket until it clicks into place. Ensure the alignment key is
aligned with the alignment slots
3.3.4 Encoder Connections
Motors with M12 connectors and integral encoder (specified with order) have a built in 500 line
incremental rotary encoder. The connector is sited next to the motor connector. To connect the
cable, see section 3.3.1. Encoders have 8 pin connectors.
Motors with UTO connectors and integral encoder (specified with order) have a built in 500 line
incremental rotary encoder wired to a 9 way D socket.
1. Push the plug into the connector socket
2. Screw in the locking screws using a suitable, flat bladed screwdriver. Turn screws clockwise
until finger tight
`
Plug alignment key
and slot
Encoder Connector
Motor Connector
Locking screws

MASC QUICK START GUIDE
Page 12 of 19
Devices with LM10 Incremental linear encoders including; LSM’s, Y-shifts, XY stages and TTX stages
have a 9 pin D connector on a flying lead.
1. Using coupling nuts provided with cable, screw nut onto locking screw until finger tight
2. Push connectors together.
3. Screw in the locking screws from the encoder cable connector until finger tight.
CONNECTION TO PC
If no remote jog box has been purchased, then the device will need to be connected to a PC or
laptop in order to perform basic functions.
1. Plug all cables into the MASC and device as described above.
2. If the PC/laptop has a dedicated serial port that supports RS-485 or RS-232, then the
MASC-JC-03 can be plugged directly into the port. 9 way connectors are connected as
described in section 3.2.2
3. If no serial port is available then an RS-485 to USB cable is supplied with each system (MASC-
USB). Connect the 9 way D connectors of the MASC-JC-03 and MASC-USB together as
described in section 3.3.4
4. Plug USB connector into appropriate port.
Coupling nuts
Locking Screws
Locking Screws

MASC QUICK START GUIDE
Page 13 of 19
CONNECTION TO JOG BOX
If the remote jog has been purchased, then it will need to be plugged into the MASC, using the
MASC-JC-03 cable.
1. Ensure the MASC-JB is turned off.
2. Plug the MASC-JC-03 into the MASC-JB
3. Screw in the locking screws until finger tight
CHECKS
1. Check that all connections have their relevant locking mechanisms in place to prevent cables
from accidentally coming loose.
Note: Unplugging cables, in particular the motor cables, whislt the MASC is switched on can
cause damage to the MASC or device.
Locking Screws

MASC QUICK START GUIDE
Page 14 of 19
OPERATION
Once all connections and checks have been made, the unit can be switched on using the on/off
switch on the front of the MASC. The built in red light of the switch should illuminate and the upper
status LED should be either solid green or flashing green. If not, then a fault may be present. Please
refer to the troubleshooting section of this guide or contact your supplier.
The MASC should now be ready for use.
JOG BOX
Switch on the MASC-JB. Using the on/off switch. The touchscreen display will illuminate
On/Off Switch
Status LED
Touchscreen
Display
Power Switch
Direction
Buttons

MASC QUICK START GUIDE
Page 15 of 19
The following should be displayed on the touchscreen display. The MASC-JB has been factory pre-set
to operate each MASC and therefore its relevant device. No setup should be required. If in doubt,
contact UHV Design or refer to the MASC-JB specific manual.
From this screen, the current axis number is displayed on the axis indicator.
4.1.1 Jog Mode
1. To move the device, press either the green or blue direction buttons. The device should then
move in either direction until it hits an end of travel limit switch The direction indicator
needle will move depending on which direction button is pressed. Note: rotary drives that
have no limit switches will continuously rotate until the button is released.
2. To alter the speed, slide the speed select slider up or down until the desired speed is
achieved. The MASC-JB has factory pre-set maximum and minimum values, specific to the
device being used. If these need to be altered, please refer to the MASC-JB manual or
contact UHV Design. Note: the speed change will not take effect whilst the direction
buttons are being held down. The direction button must be released and then pressed to
confirm the speed change.
3. To select a different axis (if more than one axis is connected) press the axis select button
until the relevant number is displayed.
Axis Indicator
Axis Select
Button
Speed indicator
Direction
Indicator
indicator
Mode Select
Button
Speed Select
Slider

MASC QUICK START GUIDE
Page 16 of 19
4.1.2 SEQUENCE MODE
The jog box can save up to four positions, on four of the configured axes. These positions can be
saved from the position mode screen and then returned to when needed.
Note: these positions are absolute from the set zero position, if you change the zero position, or
switch off the controller then the saved positions will change accordingly. It is strongly
recommended to zero each axis first and then save the positions. See section Error! Reference s
ource not found. for details.
4.1.2.1 Saving a Position
1. Using the jog mode, move the device to the desired position. Note: the speed on the slider
will be saved as the speed at which the device moves when saving the position
2. Press the Select Axis button to navigate to the Position Mode Screen
3. Press and hold the desired axis button until the screen changes.
4. Select the sequence number that you wish to save using the select button. The press the set
button to save that position.
Press and hold
Select Button
Set Button

MASC QUICK START GUIDE
Page 17 of 19
5. Repeat as required.
4.1.2.2 Activating a Saved Position
1. Navigate to the position mode screen.
2. Press the desired Select Axis button once.
3. Select the sequence number that you wish to activate by pressing the Select button until the
desired sequence is shown.
4. Press the Activate Button
Press Once
Select Button
Activate Button

MASC QUICK START GUIDE
Page 18 of 19
4.1.3 Limits and Datum Mode
1. The MASC-JB has built in home and limit seek functions pre-programmed into it. To access
these functions, press the mode select button once.
2. The following screen will appear. Press the function you wish to perform by pressing on the
desired label. Note: the red dot indicates which function is selected.
3. Press the SEEK button to perform the operation. The speed at which these functions is
performed is defined by the speed selection slider in the jog mode screen. If you wish to
stop the move before it is complete, press the mode select button.
4. If desired, once the move is complete, the position can be set to 0 by pressing the SET ZERO
button. Alternatively the Pos. display shows the current position and updates every few
seconds. These numbers may be written down for later use in automated programs.
Mode Select
Button
Press CCW label to
select CCW seek
function
SEEK Button
In this example, the
red dot indicates that
CW seek is selected
SET ZERO
Button
Press HOME label
to select home
seek function
Mode Select
Button
Position
display

MASC QUICK START GUIDE
Page 19 of 19
UHV DESIGN LTD
JUDGES HOUSE
LEWES ROAD
LAUGHTON
UNITED KINGDOM
BN8 6BN
TEL: +44 (0)1323 811188
www.uhvdesign.com
4.1.4 Status Mode
Occasionally there may be error which men that the direction buttons or SEEK functions do not
work. Pressing the Mode Select Button will display the status screen where a range of values are
displayed. If the alarm status is red, a fault may have been detected. Pressing the mode select
button will clear the error and display the jog mode screen unless there is an external fault with the
MASC itself. In this case refer to the MASC specific manual or contact UHV Design.
JOG EMULATOR
If the MASC is being run from a PC/laptop then the Jog Emulator Application can be used to perform
all functions as described in section, with the exception of saving positions. 4.1
Q PROGRAMMER
If more advanced functionality is required, writing automated programs for example, then a PC or
laptop will be required to communicate with the MASC. Plug the MASC into a PC as described in
section 3.4. Note: The MASC-JB cannot be used at the same time as connection to a PC.
The software is free to download from www.applied-motion.com/products/software
The Applied Motion Products Q Programmer software gives the ability to write complex sequences
and programs that can be stored and called up at specific times. For further information please see
the Applied Motion Products manuals, available from www.applied-motion.com/support.
Alarm status
Table of contents
Popular Controllers manuals by other brands
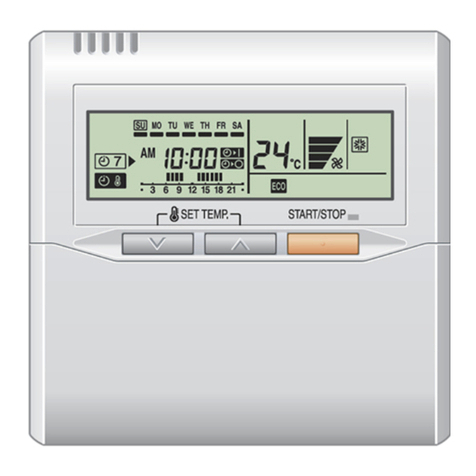
AirStage
AirStage UTY-RNKY installation manual
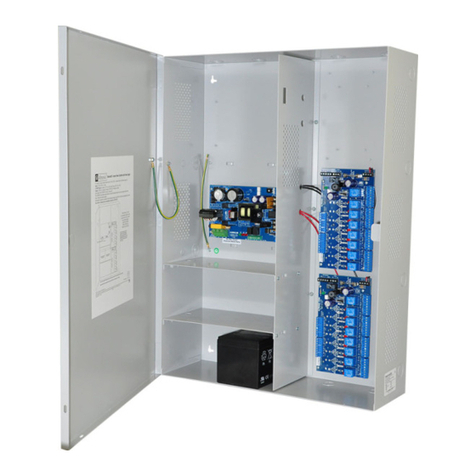
maximal
maximal Maximal3D installation guide
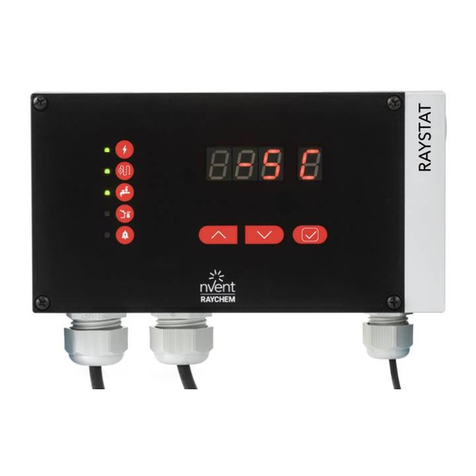
nvent
nvent RAYCHEM Raystat V5 manual
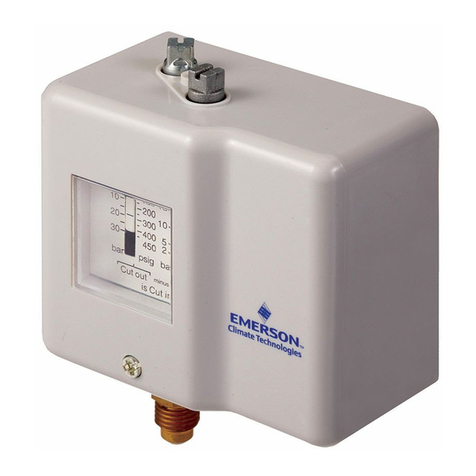
Emerson
Emerson Alco Controls PS1 Series operating instructions
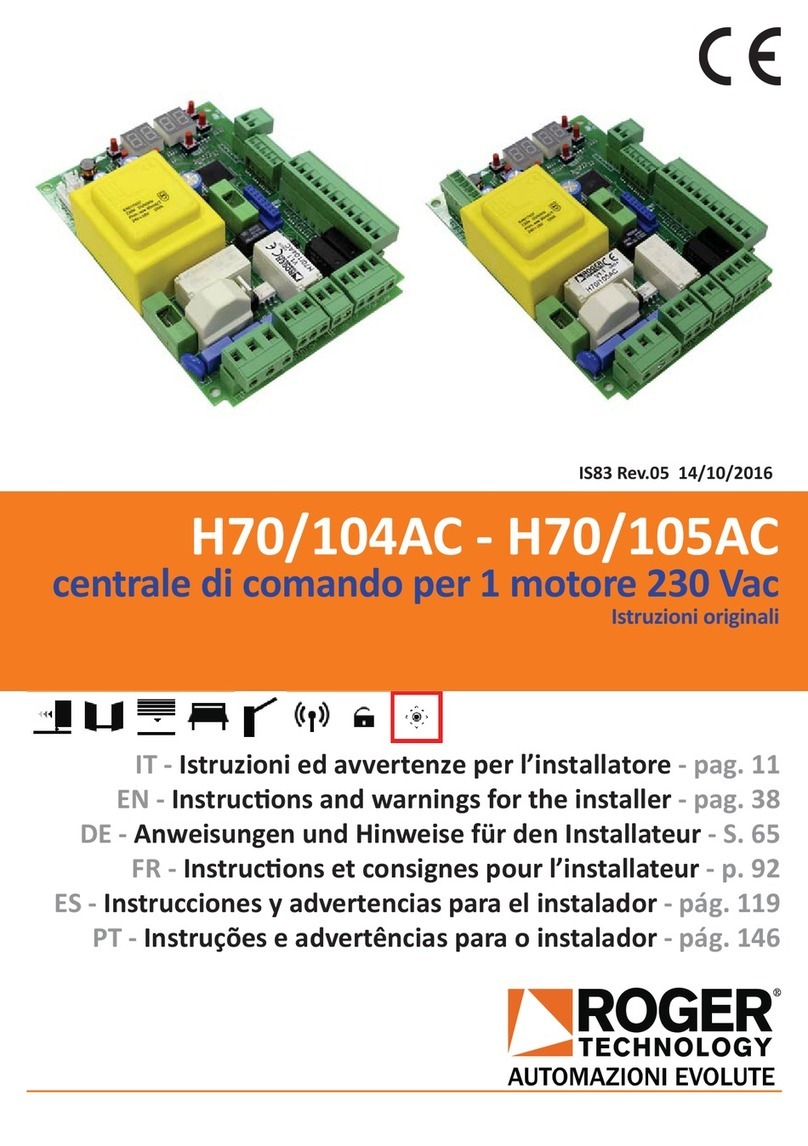
Roger Technology
Roger Technology H70/105AC Instruction and warnings for the installer
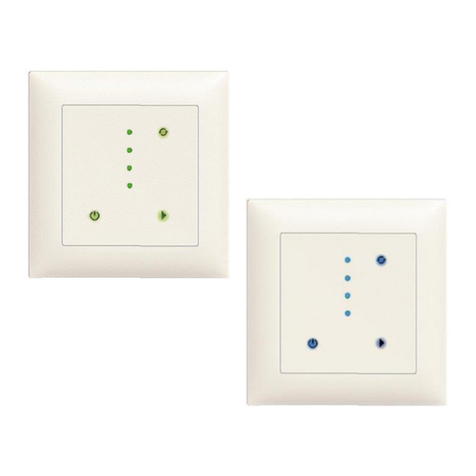
Vector
Vector MZ3-V11 quick start guide
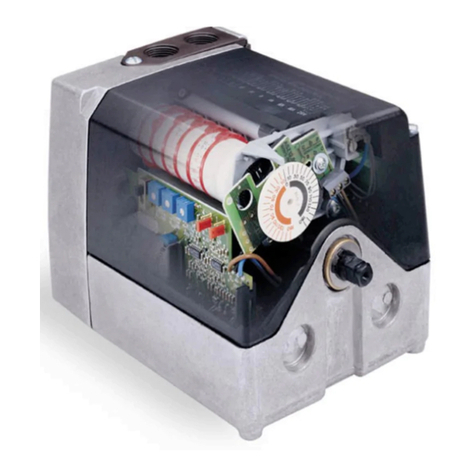
Siemens
Siemens SQM50.261R1Z3 Technical instructions
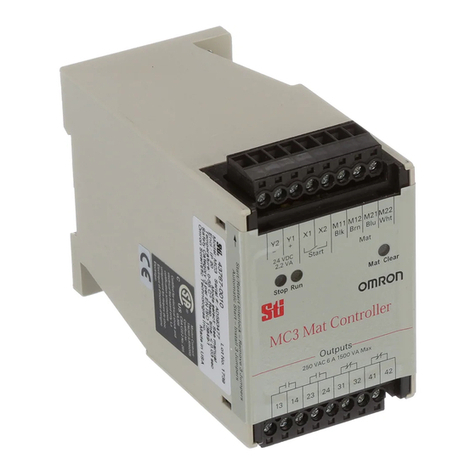
Omron
Omron MC3 Series Installation and operating manual
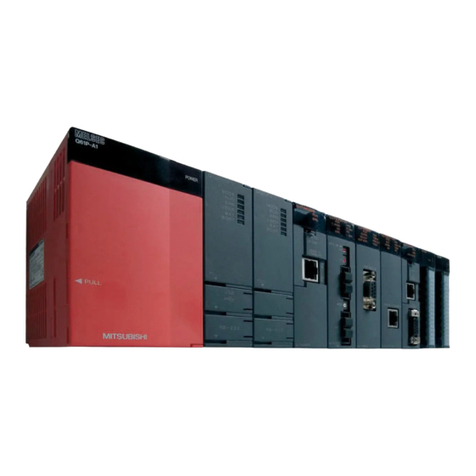
Mitsubishi
Mitsubishi MELSEC QCPU Programming manual
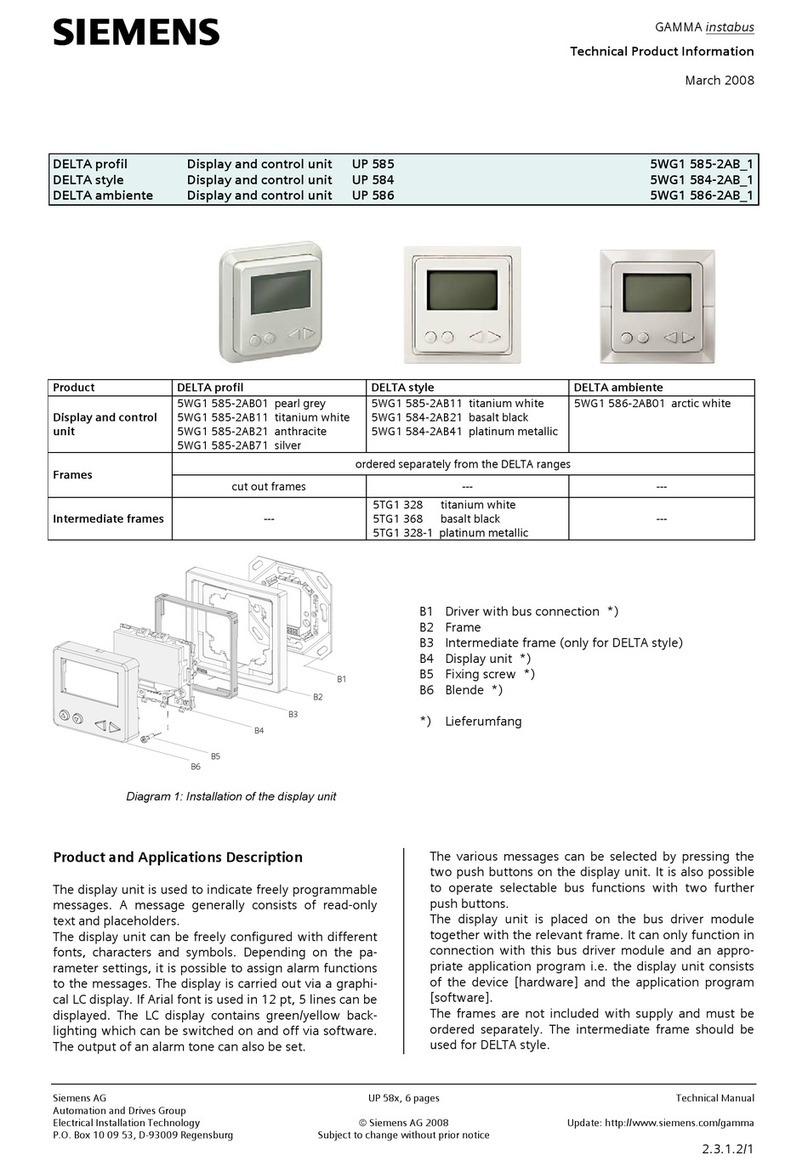
Siemens
Siemens Delta Series Technical product information
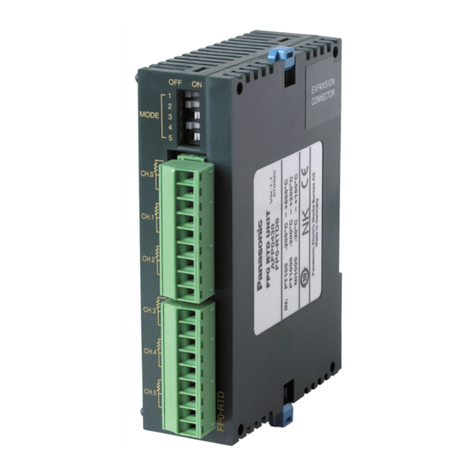
Panasonic
Panasonic FP Series Technical manual

Siemens
Siemens Desigo TRA QMX3.P36F manual