Unitec DS-205.4 User manual

issue 1111-V6
MANUAL
Digital Servo Controller
DS-205.4, DS403.4
for
EC Servo Motors
AC Induction Motors
DC-Servo Motors

1
DS 205.3 ; DS403.4
Contents
Contents
Part 1 Hardware-Manual
Contents Page
1Basis-Information
Safety instractions 3,4
General 5
Application 6
Contruction 74
Technical data 8,9,10
2Mechanical Installation
Important instructions 11
Dimension DS 400 12
Dimension Frontpanel 13
Dimension Accessories 14
Assembly 15
3Electrical Installation
Important instructions 16
Block diagram 17,18
Connection diagram 19,20
EMC 21
Connectors 22
Mains connecting 23 -- 26
Power supply 26
Motor connection 27
Regen resistor 28
Control signals 29 -- 32
RS232 33
CAN-BUS 34
Resolver 35
Encoder 36
SIN-COS 37
BL 38
X8 Encoder OUT-IN 39,40
LED-Display 41
Error list 42
Warning list 43
Options 44
4Guarantee 45
Part2 Software -Manual NDrive
Part3 Commissioning- Manual
Part4 CAN-BUS Reference
Document created with COREL VENTURA 8
TM
and Adobe Acrobat 5.0
TM

2
DS 205.3 ; DS403.4
Blank page

3
DS 205.3 ; DS403.4
Electronic devices are never fail-safe.
This manual must be carefully read and understood by the professional prior to installation
or start-up.
Consult the manufacturer or the dealer if anything is unclear.
Faulty installation can lead to destruction of the devices.
The DS xx series devices are electrical resources (EB) for power electronics regulating
electric currents.
They are designed to control EC synchronous motors (brushless dc motors, BLDC) in
industrial applications.
IP20 protection standard for cabinet-mounting.
Only connect to earthed mains or an earthed three-phase network.
Regulations and guidelines:
Mount and connect the devices and their appropriate components in compliance with
technical regulations locally applicable and required by law:
- EG-guidelines 2004/108/EG, 2006/95/EG, 2006/42/EG
- EN60204-1, EN292, EN 50178, EN60439-1, EN61800-3, ECE-R100
ISO 6469, ISO 26262, ISO 16750, ISO 20653, ISO 12100
- IEC/UL IEC 61508, IEC364, IEC 664, UL508C, UL840
- VDE-regulations VDE 100, VDE 110, VDE 160 und
- TÜV-regulations
- Trade association regulations, VGB4
Do not operate unless the control cabinet is closed or secured.
Control and power connections can be live even though the drive
is inoperative.
The DC-BUS discharge time is more than 4 minutes.
Measure the voltage prior to dismounting!
Safety instractions
Caution: High voltage DC 900V=.
Electric shock hazard!
Danger to personnel!
DC-BUS discharge - time >4min

4
DS 205.3 ; DS403.4
The user must ensure:
- that when the unit fails
- when an operator error occurs,
- when the controlling and control units fail, etc..
the drive homes to a safe operating state.
Apart from that machines and installations must be provided
with monitoring and safety systems independent from the unit.
Danger to man and property must be impossible to incur!
Assembly work
- only if all power is cut
- only by qualified professionals
Installation work
- only if all power is cut
- only by qualified electrical professionals
- Comply with safety regulations
Setting and programming work
- only by qualified professionally specialised in electronic drives and software
- observe programming notes
- Comply with safety regulations
CE:
When it is mounted in machines and installations the proper operation of the unit is not
permitted until the machine or installation has been approved according to the regulations
of the EC machine directive 2006/42/EG, and the EMC directive 2004/108/EG .
Die EC directive 2004/108/EG plus the EMC standards EN61000-2 and EN61000-4
are complied with in the EMC Notes chapter specified installation and test conditions.
A manufacturer’s certificate is available.
The manufacturer of the machine or the installation is responsible for the observance of the
threshold values prescribed in the EMC regulations..
QS:
Based on their serial number and test data the units are archived by the manufacturer for 5
years.
The test certificates are available on request.
Safety symbols
Attention danger Attention
High voltage Warning
Important
Safety instractions

5
DS 205.3 ; DS403.4
A feature of the digital three-phase servo amplifier DS xxx and the brushless d.c. motor
(synchro servomotor, EC motor) drive unit is that it is maintenance-free and has high
control dynamics.
The drive exhibits the known good control characteristics of d.c. drives without the
disadvantages of carbon brush service times and the commutation limit.
The moment of inertia of the rotor is considerably smaller and the maximum power is higher
than for d.c. motors of an identical construction. This results in acceleration values that are
higher up to a factor of 5.
Compared to asynchronous motors with frequency converters the stability, the control
range and the efficiency of the drive are considerably improved.
Since the temperature increase of the motor is only in the stator, the EC motors are always
designed to protection degree IP 65.
The brushless d.c. motor is electrically designed as a synchronous motor with a permanent
magnet rotor and a three-phase stator.
The physical properties correspond to those of the d.c. Motor, i.e. the current is proportional
to the torque and the voltage is proportional to the speed. The speed is controlled stably up
to the maximum current (max. torque). When an overload occurs the speed drops and the
current remains constant.
Rectangular speed/torque characteristic.
The current, the speed and the position are measured exactly. The rotary field frequency is
not a controlled variable, it sets itself automatically.
The motor voltages and currents are sinusoidal. Maximum motor efficiency by
compensating current control.
DS 400 can be used as a torque amplifier, a speed amplifier or a single axis position
amplifier.
The position and speed actual values are generated from the sensor unit (resolver or
incremental encoder). The encoder pulses are emitted from the amplifier for a superposed
SPC/CNC control.
The current, speed and position control loops are easily programmable digital PID
controllers. Programming is at a PC or a programming box.
Communication with superposed controls through BUS systems (standard CAN-BUS,
RS232) or through an analog interface.
Caution:
For DC-BUS fed DC, AC or bl servo amplifiers in the braking mode it is necessary to take
into account the power reverse feed in the DC-BUS. (lifting drives, unwinders, great
flywheel masses)
External regenerative circuit discharge resistor.
Information:
Other products
Classic Thyristor-Drive 200W up to 800kW
BAMO, BAMOBIL, BAMOCAR Battery-Motor-Controller up to 100kW
General

6
DS 205.3 ; DS403.4
Application in:
All types of machines and installations up to a drive power of 1kW.
Especially as
4Q- servo drives in feed axes, for highly dynamic acceleration and braking applications,
for large control ranges,
for high efficiency,
for small motor dimensions,
for an even and smooth travel.
For speed and torque regulation or combined speed and torque regulation with or without a
superimposed position controller.
Constant drives for hoisting equipment, spindle drives, pumps, transverse and longitudinal
slitting drives, multi-motor parallel drives. Synchro –servo drives are compacter than other
electrical drives.
For use in:
Insertion machines, testing machines, sheet-metal working machines, machine tools,
machines for the plastics industry, automatic assembly machines, knitting and sewing
machines, textile machines, grinding machines,
wood and stone working machines, metal working machines, XY tables, machines for the
food industry, robot and handling systems, rack feeders, extruders, calenders and
also in many other machines and installations
The motors are:
designed for protection standard IP 65,
compact, for harsh environments,
for a high dynamic overload, maintenance-free
Note:
Braking operation for EC - drives
For example.: Un-reeling machines, hoists, flyweights. The braking energy is dissipated in
the regenerative circuit or fed back to the mains via an external inverter.
Caution: The internal regenerative resistors have only a small continuous rating.
Calculate the retarding power and use external regenerative circuit discharge
resistors if necessary or for design safety. Calculation of regenerative power. See
page 24.
Application

7
DS 205.3 ; DS403.4
Construction, characteristics:
Cabinet-mounted device in an all-steel housing.
In compliance with VDE/DIN and EU guidelines. (IP20, VGB4).
Standard fully-digital regulation electronics.
Power electronics from 5A ;3A (S1 - operation).
Power input voltage 30V~ to 480V~.
Independent 24V - chopper power supply unit for auxiliary voltages.
DC decoupling between:
the housing to all electrical parts
auxiliary voltage connection to power unit and control electronics,
power unit and control electronics
Control electronics and logic inputs.
The clearance in air and leakage distances comply with VDE.
Used are:
Generously dimensioned, fully insulated FET or IGBT - power semiconductors.
Only commercially available, industrial standard components,
SMD - placed,
LED displays
Characteristics:
* Direct to 230 V~(DS 205xx), up to 480 V~(DS403xx) mains connection
* Independent 24V= auxiliary voltage connection.
* Digital RS232, CAN-BUS (additional option) interfaces.
* Analog inputs, programmable differential inputs,
* Digital programmable inputs/outputs. Opto-decoupled,
* Enable and limit switch logic,
* Ready for operation signal BTB, relay contact.
* Position, speed and torque regulation,
* Incremental resolver or encoder (optionally a sinus transmitter),
* Encoder output,
* Static and dynamic current limit.
* Standard, fully digital control unit,
* Intrinsically safe, short-circuit proof power unit,
* DC-BUS choke (EMC choke),
* Integrated regenerative discharge circuit,
* DC power bus.
* Processor-independent safety switch-off when either the amplifier or the motor have
* over voltage, under voltage, a short circuit, a line-to-earth fault or excess
temperature.
Feature

Basic - Information
8
Power supply voltage DS205.4 1x oder 3x 30V~ bis 1x230V~ +10% 50/60 Hz
Power supply voltage DS403.4 1x oder 3x 30V~ bis 1x480V~ +10% 50/60 Hz
Auxiliary supply 24V= ±10% / 2A Ripple voltage <10%, self-resttable fuse
Data Dim. DS-405.4 DS-403.4
Rated supply voltage V~ 1xoder 3x 230 1xoder 3x 400(480)
Rated output voltage V~eff 3x200 3x380 (420)
DC-link voltage V= 320 560 ( 670)
Rated installed load S1 kVA 1,2 1.2
Rated output load S1. kW 1 1
Continue current rms A
eff
5 3
Peak current A
Io
10 6
Dissipation max. W 51 80
Clock frequency kHz 8 8
Level regen circuit V= 400 ±10 780 ±10
Level Over voltage V= 440 ±10 820 ±10
Regen resistor extern minimum W80 100
External fusing
integral A
A
2
s10
150 10
150
Weight kg 1.2 1.2
Dimension HxWxD mm 140x70x190 140x70x190
Size 1 1
Input / Output V A Function Connector
Analog Input ±10 0.005 Differential input X1
Digital input ON
OFF 10-30
<6 0.010
0Opto X1
Digital output +24 0.03 Opto X1
Resolver input Differential input X7
Encoder input >3.6V Opto X7
Encoder output >4.7 Opto X8
CAN-interface Opto X9
RS232-interface 9600 Baud X10
Technical Data

Basic - Information
9
Ambient conditions
Enclosure protection IP20, VGB4
Norms EN60204,
Ambient temperature 0 bis +45
o
C
Maximum ambient temperature +45
o
C to +60
o
C with power derating 2%/
o
C
Storage temperature -30
o
C to +80
o
C
Humidity in operation Klasse F rel. humidity <85% ,no condensation !
Site altitude £1000m a.m.s.l. 100%, >1000m with power derating 2%/100m
Ventilation Built-in fan
Mounting position Vertical, Horizontal with power derating 20%
Program Type Software-Version Extension
Firmware > FW-V350 x
x
x
x
Technical Data

Basic - Information
10

11
DS 205.3 ; DS403.4
Important notes:
Mounting surface blank metal, not varnished (surface EMC contact)
Check device for mechanical damage. Mount only perfect devices.
Cut all power prior to assembly.
Insert shortening plug and attach warning signs at installations
already electrically connected.
Assembly permitted only by competent professionals.
Vertical mounting position.
Note power reduction if mounted horizontally.
Ensure adäquatem ventilation clearance. (at least 100mm).
Use dimension diagram or drill template to trace fastening holes of
device.
Do not mark off from device.
Drill mounting holes (M4) in mounting base.
Screw in screws up to 4mm.
Insert device and tighten screws.
Mount filter and choke near to device.
Surface-contact line shields to mounting surface.
Keep unshielded cable ends as short as possible.
Brake resistors can become very hot. (200°C).
Mount resistors so that neither injuries (burns) nor damage caused by their heat can occur.
Use vibration-proof bolted joints.
Ensure adequate control cabinet ventilation. Use air conditioners for excessive room
temperatures (>30°C).
Caution: Operation with devices covered in dew is not permissible!
Mechanische Installation

12
DS 205.3 ; DS403.4
Dimensions
Size 1
DS-205.4 to DS-403.4
Depth without connectors 190mm
with connectors max. 250mm
Screw for hex key M4x10 DIN 912

13
DS 205.3 ; DS403.4
Dimensions accessories
EMC-Filter
Motor choke
Dimensions
Type Spannung Strom Masse Gew.
V~ A~ HxBxTmm kg
F250V-B90-16 1x250 1x16 45x90x40 0,4
F400V-B51 1x400 1x5 35x51x40 0,3
Filter for stricter EMC - requirements.
DC-BUS filters and input capacitors are incorporated
in the device.
Mount filter close to device.
Type Strom Indukt. Masse Ge
w.
A mH HxBxTmm kg
MDD 1.6a-5 5 1.9 95x54x108 1.3
MDD 1.6b-10 10 1 95x58x108 1.4
Motor choke cable core to screen capacitiance >5nF.
Cable length 25m approx.

14
DS 205.3 ; DS403.4
Assembly
Assembty notice:
Recommended DIN 912 M4x12 fixing bolt with
lock washer.
Place M4 tap holes at a vertical distance of
312mm.
Drilling template in appendix.
Fix M4x12 screws.
Distance to rear wall of control cabinet approx.
4mm.
Position device with the top edge (1).
Slide it upwards to stop (2).
Press its bottom up to rear wall of control
cabinet (3)
and lower it (4).
Tighten screws.
For good EMC values we recommend blank metal, unvarnished mounting bases. Good
surface contact is achieved by the blank metal rear wall of the device. Lay signal lines and
power cables in separate cable channels, cross them at right angles.
(Spacial separation of interference coupling).

15
DS 205.3 ; DS403.4

16
Electrical Installation
Important notes
With reference to allocation of connections to the plug and terminal numbers the connection
notes are binding.!
All other notes on this subject are not binding.
The input and output lines can be changed and supplemented
to comply with electrical regulations and guidelines.
The regulations to be observed are:
Connection and operation notes, local regulations,
EU regulations such as the 2006/42/EG machine directive,
VDE, TÜV and trade association regulations
Cut all power prior to the electrical installation.
Make sure enabling is safe.
Insert shortening plugs,
attach warning signs
Installation is permissible only by electro technically competent
professionals.
Compare connected loads with information on rating plate.
Ensure adequate fuse protection for the feed, the auxiliary voltage and the external
regenerative resistors.
Lay power cables and control lines spacially separated. Perform shield connections and
earthing work in compliance with EMC guidelines. Use the right lead cross sections.
Caution: Operation without a “ PE - connection “ is forbidden!
Rating plate (example),
serial number
Electrical Installation
726 Drehstrom-Servoverstärker
DS 412-RS
Leistungsanschluss 3(1) x 30V~ bis 480V~
Nennstrom 12A eff IP20
Hilfsspannung 24V=
Fax+49(0)7195/928329 www.unitek-online.de
044444

17
Electrical Installation
Block diagram
AD
&
CAN
CAN-V+
CAN-GND
CANH
CANL
HPRES
FAULT
Ballast
Uesp
IIST2A
IIST1A
PWM 6x
RFE
GND
VCC
-15
+15
GND24
+24
4x
3x
FRG
RUN/FRG
LMT1/END1
LMT2/END2
DIN1
DIN2
GNDE
DOUT1
DOUT2
+24
AIN1+
AIN1-
AIN2+
AIN2-
OUT-AN
RFE
2x
RS232
CAN
Feedback
INC-OUT
X1
4
3
7
5
6
11
12
10
13
14
8
9
15
16
20
X10
X9
X7
X8 TMS 1-3
X4
27/28
29/30
3/4
7/8
5/6
9/10
11
12
17
16
19
20
21
22
23
24
25
26
9pol
9pol-D
-D
15pol-D
9pol-D
GND24
+24
AGND
DOUT3
+24
BTB/RDY
19
17
21
1
2
18

18
Electrical Installation
Block diagram
3x PWM-Low
KURZ
TEMP
EKURZ
3x PWM-High
6x
PWM 6x
HPRES
FAULT
Ballast
M3
M2
M1
PE
UBMA
IIST2A
IIST1A
PWM-B
+24
GND
VCC
-15
+15
GND24
GNDE
+5E
+15E
X1
Bex
+UB 2
3
3
2
1
X4
4
L2
L1
8
digi 205-403
BAL-
intern
1
6
5
L3
(N)
X3
X3
Regen-
resistor

19
Electrical Installation
Connection diagram
X7
X10
X9
X8
X1-1
X1-2
1
2
3
4
5
6
7
8
9
10
11
12
13
14
15
16
17
18
BTB
GND24
+24
END1
END2
FRG
GNDE
AIN2+
AIN2-
DOUT3
RFE
DIN1
DIN2
DOUT1
DOUT2
AIN1+
AIN1-
INC-OUT
CAN-BUS
RS232
CAN-
MASTER
GND System-
GND
L1
N
PE
+24V
GND24
PC COMx
DS 205.x
31
26 28
31
31
32
31
26
31
31
27
32
32
32
41
36
28
37..
40
35
19
20
21
+24
AOUT
GND
Master
connector
Line
protection
Mains
filter
Auxiliary voltage
Mains voltage maximum 3x230V+10%
24V=
Safety
circuit
Control
Protective earth PE connection
EMC earth connections
Connector with shielded cable
Drive enable
Analog
setpoint 1
Logic GND
Logic
input
Digital
output
Analog
output
System
GND
Enable
Analog
input 1
Digital-GND
Digital
input
Digital
output
Analog
input 2
Analog
output 3
Limit
switch
Auxiliary
voltage
Ready
Detail
Page
Limit
switch
Encoder output
Counter
input
Rotation
enable
+24V
Digital
output 3
Analog
setpoint 2
Digital
output
RFE
input
Encoder input
Feedback
Feedback
Logic
input
4
5
6
L1
L2
L3
X3
EC
MOTOR
3
RS IN
8
1
2
3
PE
M3
M2
M1
2
3BAL
+UB
X4
1
ext. regen
resistor
bridge for int. regen
resistor
K1
Fx
This manual suits for next models
1
Table of contents
Popular Controllers manuals by other brands
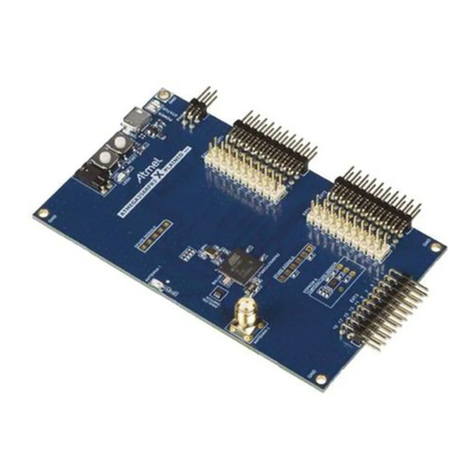
Atmel
Atmel ATMEGA256RFR2 Xplained Pro manual
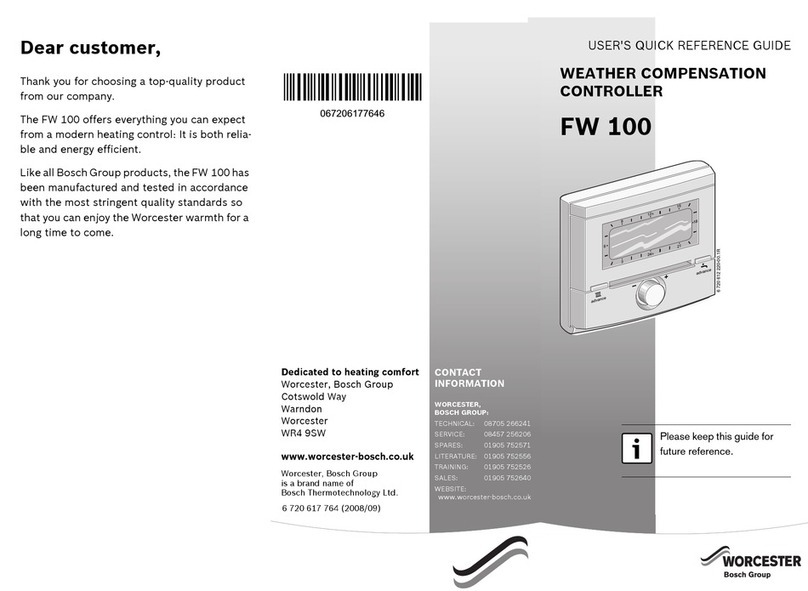
Worcester
Worcester FW 100 User quick reference guide

AP
AP UM200 Specification & installation instructions
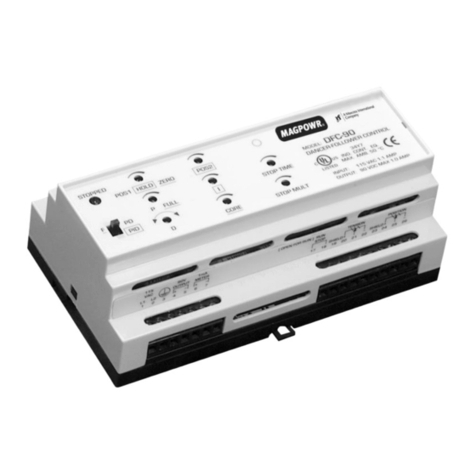
Maxcess
Maxcess MAGPOWR DFC-90 instruction manual
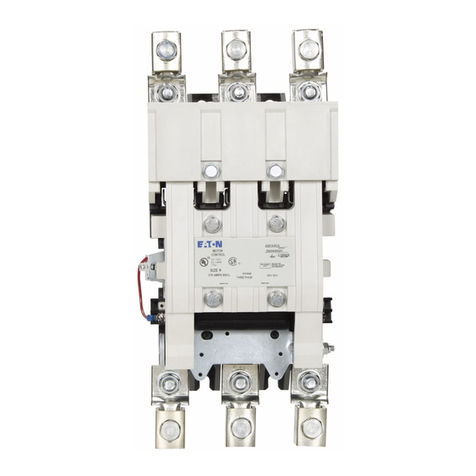
Eaton
Eaton A201 Instruction leaflet

Mercoid
Mercoid D Series Specifications-installation and operating instructions