Vallox 280 L User manual

• 1.09.357E
• 22.01.07
© VALLOX
Supply air
Extract air
290 dm3/s 100 Pa
240 dm3/s 100 Pa
520 W 3.2 A
520 W 3.2 A
Heat recovery
Heat recovery bypass
Electric preheating radiator
Electric post-heating radiator
Water post-heating radiator
Filters
– control via control panel
(DIGIT SED)
–CO
2and %RH control
– remote monitoring control
(LON converter)
– remote monitoring control
(voltage / current signal)
– silencer
– electric preheating radiator
– electric post-heating radiator
– water post-heating radiator
–CO
2sensor
– %RH sensor
– pressure difference switch
– LON converter
– extract air filter F5
Ventilation adjustment options
Input power 230 V, 50 Hz, 400 V, 15.0 A
(+ preheating unit 11 A)
Class of protection IP 34
Weight
Options
Direct current fans Extract air
Supply air
2 HR cells, = 70%
Summer / winter automation
2.5 kW, 11 A
2.5 kW, 11 A
ca. 5 kW
G3 and F7
G3
206 kg
DIGIT SED
ELECTRONIC CONTROLLER
WITH LCD DISPLAY
© VALLOX • We reserve the right to make changes without prior notification.
TECHNICAL SPECIFICATION
VALLOX 280 L
VALLOX 280 R
Models:
• For dwelling- and room-specific ventilation
• Good heat recovery efficiency
• Supply and extract air ventilation with heat
recovery
• Electronic control panel with LCD display
• Week clock control as a standard feature
• Humidity control (option)
• Carbon dioxide control (option)
• Maintenance reminder
• Fireplace / booster switch function
• Good filtering
• Summer / winter automation
• Fixed air flow measuring outlets
Code 3487

Electrical connections
Pipe connections
VALLOX 280
DIMENSIONS AND MAIN PARTS
2
2
© VALLOX • We reserve the right to make changes without prior notification.
A
B
Outdoor air
to the unit
Supply air
to the dwelling
Extract air from
the dwelling
Exhaust air outside
C
D
Duct outlets
Inner diameter of collar ø250 mm
VALLOX 280 L
C
D
A
B
Exhaust air
outside
Extract air
from the dwelling
Supply air
to the dwelling
Outdoor air
to the unit
VALLOX 280 R
VALLOX 280 L VALLOX 280 R
VALLOX 280 L VALLOX 280 R
1370
1100
187
665
220
220
222 282 222 187
Silencer
Mounted on top of the unit
Options
Main parts
Supply air fan
Extract air fan
Heat recovery cells
Heat recovery bypass
Suppy air filter F7
Extract air filter G3
Outdoor air filter G3
Condensing water tank
Condensing water outlet
Electrical connection lead-ins
Control panel
Measurement outlets
2370
665
220 220
1100
187
222 282 222 187
1000
1370
Ø 250 4 PCS
10 9 8 7 6 5 4 3 2 1
A
BC
D
7
1
13
5
4
14
82
3
11
16
17 9
15
19
6
10
VALLOX 280 model L in the picture
18
12 1
2
3
4
5
6
7
8
9
10
11
12
13
14
15
16
17
18
19
Post-heating radiator
• Electric or water
Preheating radiator
• Electric
Pressure difference switch
Carbon dioxide sensor
Humidity sensor
LON converter
Extract air filter F5
Water going
to the radiator
Water coming
from the radiator
7
6
Feed cable
- distribution panel
Connection cable
- control panel
- CO2sensor
- LON controller
Connection cable
- humidity sensor
- remote monitoring
control
1
2
3
Water going
to the radiator
Water coming
from the radiator
5
4
Feed cable
- distribution panel
Connection cable
- control panel
- CO2sensor
- LON controller
Connection cable
- humidity sensor
- remote monitoring
8
9
10

Measuring points after the outlet collar.
Fan curves indicate the total pressure
available for duct losses.
VALLOX 280, supply G3 + F7,
extract G3
Supply
air
Extract
air
HR
HR
VALLOX 280 L
SUPPLY / EXTRACT AIR VOLUMES - VALLOX 280
SUPPLY G3 + F7, EXTRACT G3
Air volumes
© VALLOX • We reserve the right to make changes without prior notification.
VALLOX 280
PERFORMANCE / VALLOX 280
3
Sound values / VALLOX 280, supply G3 + F7, extract G3
Sound power level from the ventilation unit
to supply air ducts by octave band Lw, dB
Medium
frequency
of the octave
band, Hz
ADJUSTMENT POSITION / AIR FLOW
Sound power level from the ventilation unit to
extract air ducts by octave band Lw, dB
ADJUSTMENT POSITION / AIR FLOW
63
125
250
500
1000
2000
4000
8000
LW, dB
LWA, dB(A)
Hz
ADJUSTMENT POSITION / AIR FLOWS (supply / extract)
A-weighted sound pressure level dB (A) coming from
the unit through the envelope to the rooms where the
unit has been installed
LpA, dB(A)
2
128 l/s 4
164 l/s 6
202 l/s 8
238 l/s 2
171 l/s 4
210 l/s 6
242 l/s 8
261 l/s
2
119/171 l/s 4
149/209 l/s 6
177/239 l/s 8
208/260 l/s
45 50 53 55
84
73
70
54
49
48
38
28
84
64
86
76
74
57
51
51
42
31
87
68
75
73
60
47
43
40
30
19
77
59
82
77
65
51
47
45
35
25
83
63
84
81
69
55
50
49
39
29
86
67
85
86
72
57
51
52
41
32
89
71
78
63
60
46
43
39
29
17
78
56 61
82
69
66
50
47
43
34
24
82
LpA = A-weighted sound pressure level (10 m2sound absorption)
1
2
3
4
5
6
7
8
Fan speeds
150
180
250
320
405
510
620
830
Fan input
power
W
130
150
170
190
210
230
250
290
Air
flow
(l/s)
S
E
P
esU
,kW/(m
3
/s), 2.0
Volume flow rate
q
v
(
d
m
3
/s)
20
40 60 80 100 120 140 160 180 200 220 240 260 280 300 320
Pressure loss in ducts. Total pressure
p
tot
Pa

Measuring points after the outlet collar.
Fan curves indicate the total pressure
available for duct losses.
VALLOX 280 L SILENCER
VALLOX 280 + silencer,
supply G3 + F7, extract G3
Sound power level from the ventilation unit
to supply air ducts by octave band Lw, dB
ADJUSTMENT POSITION / AIR FLOW
Sound power level from the ventilation unit
to extract air ducts by octave band Lw, dB
ADJUSTMENT POSITION / AIR FLOW
ADJUSTMENT POSITION / AIR FLOWS (supply / extract)
A-weighted sound pressure level dB (A) coming from
the unit through the envelope to the rooms where the
unit has been installed
Supply
air
Extract
air
HR
HR
VALLOX 280
PERFORMANCE / VALLOX 280 + SILENCER
2
4
© VALLOX • We reserve the right to make changes without prior notification.
Sound values / VALLOX 280 + silencer, supply G3 + F7, extract G3
Medium
frequency
of the octave
band, Hz
63
125
250
500
1000
2000
4000
8000
LW, dB
LWA, dB(A)
Hz
LpA, dB(A)
2
99 l/s 4
123 l/s 6
159 l/s 8
199 l/s 2
136 l/s 4
158 l/s 6
186 l/s 8
218 l/s
2
122/151 l/s 4
153/186 l/s 6
183/215 l/s 8
218/239 l/s
Volume flow rate
Pressure loss in ducts. Total pressure
Air volumes
SUPPLY G3 + F7, EXTRACT G3
Supply / extract air volumes - VALLOX 280 + silencer
42 47 50 53
68
51
39
24
68
43
75
61
50
36
23
75
51
78
65
55
42
31
22
78
55
68
62
42
28
13
69
48
70
66
46
32
21
72
51
75
71
50
36
27
9
77
56
78
73
53
41
32
25
19
79
58
72
57
45
30
11
72
48
LpA = A-weighted sound pressure level (10 m2sound absorption)
1
2
3
4
5
6
7
8
110
140
180
240
320
400
480
680
90
110
130
150
170
190
210
250
S
E
q
v
(
d
m
3
/s)
20
100
150
200
250
50
300
350
P
esU
,kW/(m
3
/s), 2.5
E8
E7
E6
S8
E5
S7
S6
E4
S5
E3
S4
E2
E1
S3
S2
S1
40 60 80 100 120 140 160 180 200 220 240 260 280 300 320
p
tot
Pa
PesU,kW/(m3/s), 2.0
Air
flow
(l/s)
Fan speeds Fan
input power
W
RECOMMENDED
OPERATING RANGE

© VALLOX • We reserve the right to make changes without prior notification.
VALLOX 280
CONTROL PANEL
5
The control panel is wired straight from the electrical connection box. The control panel
can also be connected in series with a CO2sensor or another control panel. (See
External electrical connections on page 8).
Control panel addresses
If two or more control panels are connected to the system, the addresses of the control
panels need to be changed.
E.g. 3 control panels.
• Connect the first control panel to the unit and change its address to 3.
• Connect the second control panel to the unit and change its address to 2.
• Connect the third control panel and make sure that its address is 1.
If control panels have the same address, they go to bus fault state. In this case, remove one of the control panels
and change the address of the other panel. The above mentioned situation can arise in connection with the later
installation of an additional control panel.
1 2 3 4
5 6 7 8
Keyboard
21 C
Main display
Scrolling up
With this button, you can scroll
the displays upward.
Scrolling down
With this button, you can scroll
the displays downward.
Increase button
With this button, you can increase
values.
Decrease button
With this button, you can decrease
values.
Start button
With this button, you switch the unit on and off.
When the indicator is lit, the unit is on.
Carbon dioxide adjustment
With this button, you set carbon dioxide adjustment on and off.
When the indicator is lit, the adjustment is on.
Humidity adjustment
With this button, you set humidity adjustment on and off.
When the indicator is lit, the adjustment is on.
Post-heating
With this button, you set post-heating on and off.
When the indicator is lit, post-heating is on.
The summer function is active when the indicator is not lit.
1
2
3
4
5
6
7
8
Fan speed
Supply air temperature
Post-heating is on
Filter guard alert
Maintenance reminder alert
Fireplace / booster switch on
Week clock control
Main display
Fan speed may be changed in this display with the + and - buttons.
Control panel
Mounting, removing and wiring of control panel
Paneelin osoite
1
Panel address
1
1
Control
VALLOX 280 can be controlled with the control panel coming with the unit (3 at most) and with
optional CO2(5 at most) and %RH sensors (2 at most). Fan speeds of the unit can be controlled
via remote monitoring with a voltage or current signal. In case of disturbances, a potential-free
relay point signal is issued.
With an optional VALLOX LON converter, the whole operation of the unit can be controlled via
remote monitoring.
Week clock control
The week clock in the control panel of the unit can be used to programme the desired fan power
option (1…8) for each hour in the day.
Connecting two or more
units (slave unit)
Connect slave units as specified in the
adjoining connection instructions. Slave
units do not operate independently, but
follow the instructions received from the
host unit. Neither control panel nor
sensors must be connected to a slave
unit. NOTE! + wire must not be connected to a SLAVE UNIT. SLAVE UNIT must not have a 6K8 resistor in place.
SLAVE UNIT TERMINAL BLOCKHOST UNIT TERMINAL BLOCK SLAVE UNIT TERMINAL BLOCK SLAVE UNIT TERMINAL BLOCK

S +
VALLOX 280
SENSORS
2
6
© VALLOX • We reserve the right to make changes without prior notification.
The sensor is wired straight from the electrical connection box of the unit.
The CO2sensor is connected directly from the connection box of the unit, or in series with
another CO2sensor or control panel (see External electrical connections on page 8).
Surface mounting Wiring
Cable:
2 x 0,5 mm2
Electronics board of
%RH sensor
HUMIDITY SENSORS
• When mounting two or more humidity
sensors, connect them to the terminal
block of the connection box by connec-
ting the first humidity sensor to %RH1,
in place of the resistor 6K8 in the termi-
nal block (remove the resistor in this ca-
se), and the second humidity sensor to
%RH2. See the electrical diagram.
CARBON DIOXIDE SENSORS
• Carbon dioxide sensors are connected
individually.
• When the first carbon dioxide sensor has
been connected to the system, the unit is
switched on. After this, the unit gives the
sensor an address. Follow the same steps
for other carbon dioxide sensors.
Surface mounting Wiring
Cable:
NOMAK 2 x 2 x 0.5 mm2+ 0.5 mm2
Base plate of the CO2sensor Electronics card of the CO2sensor (model may vary)
NOTE!
Faulty coupling of the (+) wire destroys
the carbon dioxide sensor!
1 = orange 1 = +
2 = white 1 = –
3 = orange 2 = A
4 = white 2 = B
5 = metal = signal ground
ca. 21 VDC
}
1 2 3 4 5
14
125
+ – A B M
38
76
Base plate
of sensor
14
125
38
76
Mounting and wiring of humidity sensor
Mounting and wiring of carbon dioxide sensor
Surface mounting
of control panel
A control panel is
mounted on the wall
or on a 1-part
instrument box.
Wiring
Width 90 mm
Height 110 mm
Depth 23 mm
Electronics board of control panel
1 = orange 1 = +
2 = white 1 = –
3 = orange 2 = A
4 = white 2 = B
5 = metal = signal ground
ca. 21 VDC
}
Cable:
NOMAK 2 x 2 x 0.5 mm2+ 0.5 mm2
NOTE!
Faulty coupling of the (+) wire
destroys the control panel!
1 2 3 4 5
+ – A B M

© VALLOX • We reserve the right to make changes without prior notification.
VALLOX 280
INTERNAL ELECTRICAL CONNECTION
7
USE OF JUMPER IN VOLTAGE SIGNAL
CONTROL (FACTORY SETTING)
USE OF JUMPER
IN CURRENT SIGNAL CONTROL
FAN CONTROL WITH VOLTAGE
OR CURRENT SIGNAL
TE 1 (EXTRACT AIR)
TE 3 (OUTDOOR AIR)
TE 2 (SUPPLY AIR)
TE4 (EXHAUST AIR), HR CELL
SF = SUPPLY AIR FAN 520 W DC
EF = EXTRACT AIR FAN 520 W DC
H1= INTERFERENCE SUPPRESSOR, MOTHERBOARD
H2= INTERFERENCE SUPPRESSOR, MOTHERBOARD
FG = DAMPER MOTOR 24 VAC
TE = TEMPERATURE SENSORS
R1 = AUXILIARY RESISTOR 6.8 KOHM
TR = TRANSFORMER 230 V 4 A / 24 V 25 VA
F = MOTHERBOARD FUSE
S = MAINTENANCE SWITCH (DOOR SWITCH)
LP1 = ELECTRIC HEATER 2500 W (PREHEATING, OPTION)
LP2 = ELECTRIC HEATING UNIT 2500 W (POST-HEATING, OPTION)
SV = WATER HEATING UNIT ACTUATOR (POST-HEATING UNIT, OPTION)
TZ1 = OVERHEAT PROTECTION +60 ˚C
TZ2 = OVERHEATING PROTECTOR +95 ˚C (NEEDS TO BE ACKNOWLEDGED)
PDS1 = SUPPLY AIR FILTER PRESSURE DIFFERENCE SWITCH (OPTION)
PDS2 = EXTRACT AIR FILTER PRESSURE DIFFERENCE SWITCH (OPTION)
230 V
0 V
0 V
16 V
H1
U3 N4
L2
S
PWM
L3L4 N PWM
L5 NCL GND 12
SV
U1
R
TZ2
TZ1
LP1
FG
~
TZ2
Y
SF
R
Y
Bl
EF
TZ1
LP2
L
-
+
A
B
M
%RH-2/S
%RH-2/+
%RH-1/S
%RH-1/+
N
PDS 2
PDS 1
5104938271 6
S
SS
104 938271
-+AB
SSD
C
P
SS
D
C
T
LN NC
G
N
D
F
Bl
L
H2
N4
L2 U1
L1
N
TR
FAULT
FAULT
VAK GND
VAK S
PDS +
PDS S
BOOSTER SWITCH
R1
NN
MOTHERBOARD

VALLOX 280
EXTERNAL ELECTRICAL CONNECTIONS
2
8
© VALLOX • We reserve the right to make changes without prior notification.
FAN CONTROL:
Voltage signal: 0...10 VDC
(Factory setting)
Current signal: 0...20 mA
For moving the jumper in the motherboard,
see the internal electrical connection diagram.
REMOTE MONITORING
(Additional control option)
FAULT SIGNAL
(1 A, 24 VDC)
NOTE! When bus system based fan control
is used in the VALLOX 280 unit, looping
between VAK S and VAK GND is disconnected.
LON CONVERTER
OPTION
LonWorks-FT10
CO2
SENSOR
ONE OR MORE
OPTION
NOTE!
Faulty coupling of the + wire
DESTROYS THE SENSOR.
CONTROL PANEL 1
ONE OR MORE
1 INCLUDED AS STANDARD
NOTE!
Faulty coupling of the + wire
DESTROYS THE CONTROL PANEL.
THE RESISTOR IS REMOVED WHEN
THE FIRST HUMIDITY SENSOR IS
CONNECTED TO THE UNIT
ORANGE 1 = +
WHITE 1 = –
ORANGE 2 = A
WHITE 2 = B
METAL = M
HUMIDITY SENSOR
1
OPTION
HUMIDITY SENSOR
2
OPTION
CONNECTED TO REPLACE RESISTOR R
(CONNECTOR %RH-1/+ AND %RH1/S)
NOTE! When VALLOX 280 is used with a PREHEATING UNIT and a WATER-
CIRCULATING POST-HEATING UNIT, L and L1 in the terminal block are
looped. There is then NO NEED for a separate supply for preheating.
S GND
VALLOX 280
NOMAK 2x2x0.5+0.5
3x2,5S (4x2,5S)
2x0.5
2x0.5
-
AB+
NOMAK 2x2x0.5+0.5
AMB
-
+
4 X 0.5
R= 6K8
S+S+
AM
B
-
+
20
19
18
13
17
15
16
14
12
7
9
10
11
8
6
1
3
5
4
2
DISTRIBUTION PANEL
230 V/400 V
16 A
PE
N
BOOSTER SWITCH / FIREPLACE SWITCH
(Additional control option)
2x0.5
NOMAK 2x2x0.5+0.5
NOTE! When VALLOX 280 is used with a PREHEATING UNIT and an
ELECTRIC POST-HEATING UNIT, a separate 16 A supply is needed for
PREHEATING.
16 A
%RH-2/S
%RH-2/+
%RH-1/S
%RH-1/+
FAULT
FAULT
BOOSTER SWITCH
VAK GND
VAK S
PDS +
PDS S
L
-
+
A
B
M
N
L1

© VALLOX • We reserve the right to make changes without prior notification.
VALLOX 280
FILTERING, HEAT RECOVERY, HEATING
9
Filtering
Efficient filtering of outdoor air (G3 + F7) prevents harmful particles
from entering the ductwork and rooms via the unit. Good filtering
of extract air (G3) diminishes the contamination of the unit and
ensures efficient heat recovery and extract air fan operation.
Clogging of the supply / extract air filters can be monitored by
equipping the unit with a pressure difference switch.
Heat recovery and heating
With efficient heat recovery, most of the heat of contaminated
extract air can be transmitted to outdoor air coming inside. The
efficiency of the heat recovery cells is circa 70%. If outdoor air
does not get sufficiently warm in the heat recovery cells, it can
be heated with a water or electric post-heating unit (optional).
The unit features an automatic heat recovery bypass function,
which eliminates needless heating of outdoor air during summer.
The unit also has an automatic defrost function for the water post-
heating unit.
Defrost
The automatic defrosting of the heat recovery cells intermittently
stops the supply air fans when the temperature of exhaust air
goes under the set threshold value. In order to minimise momentary
stoppages of the supply air fans the fan can also be equipped
with an electric preheating unit.
Electric preheating unit (option)
• Power 2.5 kW, 11 A.
Electric post-heating unit (option)
• Power 2.5 kW, 11 A.
Water post-heating unit VKL (option)
Power of water radiator
VKL WATER RADIATOR PRESSURE LOSS IN WATER
CIRCULATION
Defined for 100-% water.
Total pressure loss kPa
Radiator + valve (KVS 1.0)
Radiator
Water flow
Total power of the radiator kW
Temperature of water coming to the radiator (tv) 70 ˚C
Temperature of air coming to the radiator (ti) 15 ˚C
Water flow dm3/s
Air flow
dm3/s
Cooling of water in the radiator ˚C
Total power of the radiator kW
Temperature of water coming to the radiator (tv) 55 ˚C
Temperature of air coming to the radiator (ti) 15 ˚C
Water flow dm3/s
Air flow
dm3/s
Cooling of water in the radiator ˚C

VALLOX 280
CONTROL DIAGRAM, electric post-heating unit
2
10
© VALLOX • We reserve the right to make changes without prior notification.
LON
CONVERTER
S
SILENCER UNIT
2
1
H%RH
BOOSTER SWITCH / FIREPLACE SWITCH
CARBON DIOXIDE SENSOR (5 AT MOST)
CONTROL PANEL (3 AT MOST)
CONTROL PANEL (2 AT MOST)
1
CO2%RH
TE1
16A
230 V
DISTRIBUTION PANEL
VALLOX 280
INTERNAL ELECTRICAL AND CONTROL CONNECTIONS
TE2
F 5
TZ1
F 7
Pressure
difference switch
LP2
PDS1
M
EF
TE4
HR2
G 3
TE3
FG
M
SF
TZ1 TZ2
LP1
TZ2
G 3
PDS2
1
2x16 A, if resistance power exceeds 2.5 kW,
a separate supply is needed for preheating
REMOTE MONITORING CONTROL CENTRE OF THE PROPERTY
ALARM
OPERATION MODE
CONTROL
MEASUREMENT
ADJUSTMENT
Electric
preheating unit
HR1
VENTILATION ZONE
Electric post-
heating unit
Pressure
difference
switch

Control of operation
Power supply to the unit can be controlled with a contactor in the distribution panel if nee-
ded, e.g. with a timer programme. After starting, the unit first operates at basic fan speed.
After that power is adjusted based either on the measurement data received from air quality
sensors and/or on manual control at the control panel.
Fan speed adjustment
Manual control
Fan speed of the ventilation unit is controlled in 8 steps at control panel H.
Week clock control
Fan speed of the ventilation unit is controlled in 8 steps using the week clock in control panel
H. The week clock can be used to programme the desired fan power option for each hour in
the day.
Carbon dioxide and humidity control
The fan power of the ventilation unit is controlled in multiple steps depending on loads, and
based on the measurement results of the air quality sensors (CO2and %RH sensors) located
in the ventilation zone. The aim is to keep carbon dioxide and/or humidity content below
the threshold set at control panel H. It is also possible to select an automatic search for the
humidity content setpoint at the control panel. One or more modes of control may be used
simultaneously. The dominant mode is the one demanding boosting. Fan speed varies de-
pending on load status between the basic and maximum fan speeds. The basic and maxi-
mum fan speeds can be set at the desired level at control panel H.
Control through voltage or current signal
The fan power of the ventilation unit is controlled in 8 steps with a voltage signal of 0…10
VDC, or with a current signal of 0…20 mA. However, fan power cannot be raised above the
set maximum fan speed.
Voltage or current signal control is used to control basic fan speed. Because of this, it is
possible to raise fan speed with the manual, CO2and %RH controls when needed, but not to
lower it.
Supply air temperature
Supply air temperature can be controlled with either constant temperature control or casca-
de control.
Supply air constant temperature control
The control unit directs the operation of post-heating unit LP2 on the basis of the measuring
data given by by supply air temperature sensor TE2, aiming at keeping supply air tempe-
rature at the temperature value set at control panel H(+10…+30 ˚C).
Supply air cascade control
The control unit directs the operation of post-heating unit LP2 on the basis of the measure-
ment data given by extract air temperature sensor TE1, aiming at keeping extract air tem-
perature at the temperature value set on control panel H(+10…+30 ˚C).
Heat recovery bypass
Heat recovery is enabled whenever post-heating has been switched on. Automatic heat reco-
very bypass is active whenever post-heating has been switched off and outdoor temperature
exceeds the setpoint (to be set between 0…+25 ˚C). In this case, the control unit directs the
operation of damper motor FG on the basis of measuring results given by outdoor sensor
TE3 and extract air temperature sensor TE1. The aim is to get as cool supply air to the
ventilation zone as possible. However, heat recovery is always active when outdoor air tem-
perature is below the setpoint.
Heat recovery defrosting
Active when outdoor temperature is less than 0 ˚C. The control centre of the unit controls the
operation of preheating unit LP1 on the basis of the measurement data of exhaust air
temperature sensor TE4, preventing freezing alerts and the stopping of supply air fan SF. If
the power of preheating unit LP1 is not sufficient, the control centre keeps stopping supply
air fan SF on the basis of the measurement data of exhaust air temperature sensor TE4, thus
preventing the HR cell from freezing. As soon as the risk passes, the fan restarts automatical-
ly. The threshold temperature (–6...+15 ˚C) and the difference area (1...10 ˚C) for defrosting
can be set at control panel H. When the SF fan stops, power supply from preheating unit LP1
is stopped and post-heating radiator LP2 continues to heat.
Overheating protection of heating unit
Overheating protection thermostats TZ1 and TZ2 monitor the surface temperature of hea-
ting units LP1 and LP2. If surface temperature exceeds the threshold, overheat protection is
triggered and power supply to the heating unit is stopped. Overheat protector TZ1 is reset
automatically and TZ2 manually.
Alarms
Pressure difference switches PDS1 and PDS2 monitor the pressure difference between the
supply and extract air sides. If the pressure difference rises too high, an alarm will be issued.
This is indicated by a symbol ( ) in the main display of the control panel. If the unit is not
equipped with pressure difference switches, the symbol ( ) appearing in the main display of
the control panel reminds of the need of servicing the unit. The reminder interval can be set
between 1...15 months. The factory setting is 4 months. This function is always active.
The fault signal relay in the unit gives potential-free alarm indications on the following fault
conditions:
• alarm of high carbon dioxide content (> 5000 ppm ) switches the relay at 1-second inter-
vals. The fans stop. This is acknowledged by switching off the unit.
• in other fault situations, such as a sensor fault and a filter guard alarm ( ), the points of
the relay close.
Booster or fireplace switch function
The booster or fireplace switch function of the unit is controlled either at control panel H
and/or separate switch S, which can be connected to the connection box of the unit. The mode
of switch operation is selected at control panel H.
The booster switch function raises fan speed to the set maximum speed for 45 minutes. The
fireplace switch stops the extract air fan for 15 minutes and produces overpressure in the
ventilation zone.
LON remote monitoring control can be implemented with a VALLOX LON converter.
VALLOX 280
DESCRIPTION OF OPERATION, electric post-heating unit
11 © VALLOX • We reserve the right to make changes without prior notification.
PARTS LIST VALLOX 280, electric post-heating unit
Code Name Technical data Standard /
(factory settings in parentheses) Option
Voltage and current signal values (selection in the motherboard)
Voltage values for each fan speed:
0 0.20...1.25 VDC
1 1.75...2.25 VDC
2 2.75...3.25 VDC
3 3.75...4.25 VDC
4 4.75...5.25 VDC
5 5.75...6.25 VDC
6 6.75...7.25 VDC
7 7.75...8.25 VDC
8 8.75...10.00 VDC
Current values for each fan speed:
0 0.5...2.5 mA
1 3.5...4.5 mA
2 5.5...6.5 mA
3 7.5...8.5 mA
4 9.5...10.5 mA
5 11.5...12.5 mA
6 13.5...14.5 mA
7 15.5...16.5 mA
8 17.5...20.0 mA
CO2 Carbon dioxide sensor, 5 at most Adjustment range 500...2000 ppm (900) Option
Carbon dioxide control Adjustment interval 1...15 min. (10)
FG Damper motor HR bypass automation, 24 V, 2 W, 8 Nm Standard
H Control panel, 3 at most Setting, operation, display, 1 included standard
S Booster / fireplace Either booster or fireplace switch Standard in
switch function operation (booster switch) control panel
LON LON converter Remote monitoring control Option
LP1 Preheating unit Electric radiator 2.5 kW Option
LP2 Post-heating unit Electric radiator 2.5 kW Option
HR1, HR2 Heat recovery cell 2-step, = 70% Standard
PDS1 Pressure difference switch Adjustment range 0...500 Pa Option
Pressure guard of the supply air filter
PDS2 Pressure difference switch Adjustment range 0...500 Pa Option
Pressure guard of the extract air filter
EF Extract air fan qv = 290 dm3/s (100 Pa) Standard
%RH Humidity sensor, 2 at most Automatic / adjustment range 1...99% Option
Humidity control Adjustment interval 1...15 min. (10)
G3, F7 Filter Supply air G3+F7, extract air G3 Standard
F5 Filter Extract air F5 Option
TE4 Temperature sensor Exhaust air temperature Standard
HR cell antifreezing, Adjustment range -6...+15 ˚C (3)
preheating control Adjustment range -6...+15 ˚C (5)
TE2 Temperature sensor Supply air temperature Standard
TE3 Temperature sensor Outdoor air temperature Standard
TE1 Temperature sensor Extract air temperature Standard
SF Supply air fan qv = 245 dm3/s (100 Pa) Standard
TZ1 Overheating protection Automatic (+ 60 ˚C), Self-resetting Included in
of heating unit LP1/LP2
TZ2 Overheating protection Manually reset (+95 ˚C) Included in
of heating unit LP1/LP2

VALLOX 280
CONTROL DIAGRAM, water-circulating post-heating unit
2
12
© VALLOX • We reserve the right to make changes without prior notification.
Pressure
difference switch
INTERNAL ELECTRICAL AND CONTROL CONNECTIONS
Pressure
difference switch
Electric preheating unit
SILENCER UNIT
REMOTE MONITORING CONTROL CENTRE OF THE PROPERTY
ALARM
OPERATION MODE
CONTROL
MEASUREMENT
ADJUSTMENT
BOOSTER SWITCH / FIREPLACE SWITCH
CARBON DIOXIDE SENSOR (5 AT MOST)
CONTROL PANEL (3 AT MOST)
CONTROL PANEL (2 AT MOST)
VENTILATION ZONE
S2
1
H%RH
1
CO2%RH
1
LON
CONVERTER
TE1
16A
230 V
DISTRIBUTION PANEL
VALLOX 280
TE2
F 5
F 7
PDS1
M
EF
TE4
HR2
G 3
TE3
FG
MSF
TZ1 TZ2
LP1
G 3
PDS2
SV
LP2
Ljp
Ljm
HR1

Control of operation
Power supply to the unit can be controlled with a contactor in the distribution panel if nee-
ded, e.g. with a timer programme. After starting, the unit first operates at basic fan speed.
After that power is adjusted based either on the measurement data from air quality sensors
and/or on manual control at the control panel.
Fan speed adjustment
Manual control
Fan speed of the ventilation unit is controlled in 8 steps at control panel H.
Week clock control
Fan speed of the ventilation unit is controlled in 8 steps using the week clock in control panel
H. The week clock can be used to programme the desired fan power option for each hour in
the day.
Carbon dioxide and humidity control
The fan power of the ventilation unit is controlled in multiple steps depending on loads, and
based on the measurement results of the air quality sensors (CO2and %RH sensors) located
in the ventilation zone. The aim is to keep carbon dioxide and/or humidity content below
the threshold set at control panel H. It is also possible to select an automatic search for the
humidity content setpoint at the control panel. One or more modes of control may be used
simultaneously. The dominant mode is the one demanding boosting. Fan speed varies de-
pending on load between the basic and maximum fan speeds. The basic and maximum fan
speeds can be set at the desired level at control panel H.
Control through voltage or current signal
The fan power of the ventilation unit is controlled in 8 steps with a voltage signal of
0…10 VDC, or with a current signal of 0…20 mA. However, fan power cannot be raised
above the set maximum fan speed. Voltage or current signal control is used to control basic
fan speed. Because of this, it is possible to raise fan speed with the manual, CO2and %RH
controls when needed, but not to lower it.
© VALLOX • We reserve the right to make changes without prior notification.
VALLOX 280
DESCRIPTION OF OPERATION, water-circulating post-heating unit
13
Supply air temperature
Supply air temperature can be controlled with either constant temperature control or casca-
de control.
Supply air constant temperature control
The control unit directs the operation of control valve SV in post-heating unit LP2 on the
basis of the measuring data given by supply air temperature sensor TE2, aiming at keeping
supply air temperature at the temperature value set at control panel H(+10…+30 ˚C).
Supply air cascade control
The control unit directs the operation of control valve SV in post-heating unit LP2 on the
basis of the measurement data given by extract air temperature sensor TE1, aiming at
keeping extract air temperature at the temperature value set on control panel H
(+10…+30 ˚C).
Heat recovery bypass
Heat recovery is enabled whenever post-heating has been switched on. Automatic heat re-
covery bypass is active whenever post-heating has been switched off and outdoor tempera-
ture is more than the set threshold value (to be set between +0…+25 ˚C). In this case, the
control unit directs the operation of damper motor FG on the basis of measuring results
given by outdoor sensor TE3 and extract air temperature sensor TE1. The aim is to get as
cool supply air to the ventilation zone as possible. However, heat recovery is always active
when outdoor air temperature is below the setpoint.
Heat recovery defrosting
Active when outdoor temperature is less than 0 ˚C. The control centre of the unit controls the
operation of preheating unit LP1 on the basis of the measurement data of exhaust air
temperature sensor TE4, preventing freezing alerts and the stopping of supply air fan SF.
If the power of preheating unit LP1 is not sufficient, the control centre keeps stopping
supply air fan SF on the basis of the measurement data of exhaust air temperature sensor
TE4, thus preventing the HR cell from freezing. As soon as the risk passes, the fan restarts
automatically. The threshold temperature (–6...+15 ˚C) and the difference area (1...10 ˚C)
for defrosting can be set at control panel H. When fan SF stops, power supply from prehea-
ting unit LP1 is stopped and post-heating radiator LP2 continues to heat.
Water radiator freezing protection
The control centre of the unit stops fans SF and EF on the basis of the measurement data of
outdoor temperature sensor TE3 (outdoor air < 0 ˚C) and supply air temperature sensor TE2
(supply air + 7 ˚C), thus preventing water heating unit LP2 from freezing. A freezing alert
appears in the display of the control panel. The fans restart automatically as soon as the risk
of freezing passes (supply air > +10 ˚C).
Preheating unit overheat protection
Overheating protection thermostats TZ1 and TZ2 monitor the surface temperature of hea-
ting units LP1 and LP2. If surface temperature exceeds the threshold, overheat protection is
triggered and power supply to the heating unit is stopped. Overheat protector TZ1 is reset
automatically and TZ2 manually.
Alarms
Pressure difference switches PDS1 and PDS2 monitor the pressure difference between the
supply and extract air sides. If the pressure difference rises too high, an alarm will be issued.
This is indicated by a symbol ( ) in the main display of the control panel. If the unit is not
equipped with pressure difference switches, the symbol ( ) appearing in the main display of
the control panel reminds of the need of servicing the unit. The reminder interval can be set
between 1...15 months. The factory setting is 4 months. This function is always active.
The fault signal relay in the unit gives potential-free alarm indications on the following fault
conditions:
• When the defrost function of the water-circulating radiator is on, the points of the relay
close and open at a 10-second interval.
• Alarm of high carbon dioxide content (> 5000 ppm ) switches the relay at 1-second inter-
vals. The fans stop. This is acknowledged by switching off the unit.
• In other fault situations, such as a sensor fault and a filter guard alarm ( ), the points of
the relay close.
Booster or fireplace switch function
The booster or fireplace switch function of the unit is controlled either at control panel H
and/or separate switch S, which can be connected to the connection box of the unit. The mode
of switch operation is selected at control panel H.
The booster switch function raises fan speed to the set maximum speed for 45 minutes. The
fireplace switch stops the extract air fan for 15 minutes and produces overpressure in the
ventilation zone. LON remote monitoring control can be implemented with a VALLOX LON
converter.
PARTS LIST VALLOX 280, water-circulating post-heating unit
Code Name Technical data Standard /
(factory settings in parentheses) Option
CO2 Carbon dioxide sensor, 5 at most Adjustment range 500...2000 ppm (900) Option
Carbon dioxide control Adjustment range 1...15 min (10)
FG Damper motor HR bypass automation, 24 V, 2 W, 8 Nm Standard
H Control panel, 3 at most Setting, operation, display, 1 included Standard
S Booster / fireplace Either booster or fireplace switch Standard in
switch function operation (booster switch) control panel
LON LON converter Remote monitoring control Option
LP1 Preheating unit Electric radiator 2.5 kW Option
LP2 Post-heating unit Water radiator 5.0 kW, 70/50 ˚C Option
HR1, HR2 Heat recovery cell 2-step, = 70% Standard
PDS1 Pressure difference switch Adjustment range 0...500 Pa Option
Pressure guard of the supply air filter
PDS2 Pressure difference switch Adjustment range 0...500 Pa Option
Pressure guard of the extract air filter
EF Extract air fan qv = 290 dm3/s (100 Pa) Standard
%RH Humidity sensor, 2 at most Automatic / adjustment range 1...99% Option
Humidity control Adjustment interval 1...15 min. (10)
G3, F7 Filter Supply air G3 + F7, extract air G3 Standard
F5 Filter Extract air F5 Option
TE4 Temperature sensor Exhaust air temperature Standard
HR cell antifreezing, Adjustment range -6...+15 ˚C (3)
preheating control Adjustment range -6...+15 ˚C (5)
TE2 Temperature sensor Supply air temperature Standard
TE3 Temperature sensor Outdoor air temperature Standard
TE1 Temperature sensor Extract air temperature Standard
SF Supply air fan qv = 245 dm3/s (100 Pa) Standard
TZ1 Overheating protection Automatic (+ 60 ˚C), self-resetting Included in
of heating unit LP1/LP2
TZ2 Overheating protection Manually reset (+95 ˚C) Included in
of heating unit LP1/LP2
Voltage and current signal values (selection in the motherboard)
Voltage values for each fan speed:
0 0.20...1.25 VDC
1 1.75...2.25 VDC
2 2.75...3.25 VDC
3 3.75...4.25 VDC
4 4.75...5.25 VDC
5 5.75...6.25 VDC
6 6.75...7.25 VDC
7 7.75...8.25 VDC
8 8.75...10.00 VDC
Current values for each fan speed:
0 0.5...2.5 mA
1 3.5...4.5 mA
2 5.5...6.5 mA
3 7.5...8.5 mA
4 9.5...10.5 mA
5 11.5...12.5 mA
6 13.5...14.5 mA
7 15.5...16.5 mA
8 17.5...20.0 mA

VALLOX 280
INSTALLATION
2
14
© VALLOX • We reserve the right to make changes without prior notification.
Location
• The unit is mounted indoors, in a place where temperature does not fall below
+10 ºC.
• The unit is to be mounted in a place where the sound pressure level coming through
the envelope is not acoustically disturbing (storerooms, corridors, technical rooms,
and in some cases rooms where people spend time, such as classrooms).
• The unit is equipped with an adjustable base. If the unit is mounted on the wall,
attention needs to be paid to the weight of the unit (206 kg) and to vibration
isolation.
• The unit is splash protected (IP 34) and can thus also be mounted in a damp room.
Electrical connections
• The unit is permanently connected to the mains supply. The electrical connection box
of the unit is located inside the unit, in connection with the exhaust air duct.
• Cables connected to the unit are led through the lead-in seals next to the extract air
duct outlet.
• The cables are connected to the unit by taking off the upper door and the cover of
the electrical connection box located in the exhaust air duct. Follow the connection
instructions. The external and internal connection diagrams are shown in these
instructions and inside the cover of the electrical connection box.
Duct connections
• The unit is equipped with four ø 250 external connection outlets. Necessary
connecting pieces (e.g. inner or bent connectors) can be attached to external
connection outlets.
NOTE! LENGTH OF THE CONNECTING HEAD OF THE CONNECTING PIECE NO MORE THAN 50 MM.
Fix the ducts steadily and tightly to the relevant outlets. (NOTE! Unit models L/R).
Implement duct insulation if needed as defined in the ventilation plan.
Air flow measurement outlets
• The fixed air flow measurement outlets are located behind the VALLOX nameplate
(12) at the upper edge the unit. You can easily remove the nameplate by sliding it
upward and pulling it toward yourself.
• Via the measurement outlets, the total pressure of the supply and extract air ductwork
can be measured with a differential pressure instrument. Pressure readings and air
volume tables (p. 3 or 4) show volume flow rates at various adjustment positions.
• The red measurement hose is on the pressure side and the black hose on the suction
side of the fan.
Condensing water connections
• Water condensing from extract air going through the unit can be removed from the
bottom tank in two ways.
• When the humidity content of extract air is high, as for example in washrooms, the
condensing water is led from the screw-type coupling in the bottom tank to the floor
drain via the condensing water outlet (water seal) delivered with the unit.
• When the humidity content of extract air is low, as in office rooms, the condensing
water can be led from the screw-type coupling in the bottom tank to the condensing
water tank delivered with the unit. It is pushed below the bottom tank to the guide
posts in the base. In this case, no separate condensing water outlet is used. NOTE!
When a condensing water tank is used, it has to be inspected sufficiently often.
• The screw-type coupling is located almost in the middle of the unit. This is why the
unit has to be mounted level with the horizontal.
Pipe connections
• If the unit is equipped with a water-circulating post-heating unit, it is connected to the
warm water circuit with 15/13 copper tubes.
NOTE! WATER-CIRCULATING HEATING RADIATOR INCLUDES A CONTROL VALVE.
Pressure difference switches
If the unit is equipped with pressure difference switches controlling the pressure difference
in the supply and/or extract air filters, they have to be set at correct values according
to the adjustment position chosen. For further instructions, see the instructions for use and
maintenance of VALLOX 280.
483
332
332
483
DOOR
CONDENSING WATER
OUTLET, MODEL L
CONDENSING WATER
OUTLET, MODEL R
VALLOX 280 L
OUTDOOR AIR
SUPPLY AIR
EXTRACT AIR
EXHAUST AIR
VALLOX 280 R
EXHAUST AIR
EXTRACT AIR
SUPPLY AIR
OUTDOOR AIR
A
B
C
D
A
B
C
D
Lead-in seals for electrical connections
Condensing water outlet
Condensing water tank
Base
Measurement outlets
Condensing water outlets
A
10
B
CD
8
20
12
9
10
9
8
20
12

© VALLOX • We reserve the right to make changes without prior notification.
VALLOX 280
INSTALLATION
15
Silencer
General
• The silencing unit is meant as a duct silencer mounted
upon the VALLOX 280 unit. The unit has an opening
cover, thanks to which the unit can be cleaned wit-
hout detaching the ducts.
• The unit also incorporates detachable lamellar silen-
cer plates in supply and extract air ducts.
• 4 external joints with a diameter of ø 250 mm are
used as duct joints, allowing the leading of ductwork
directly from the unit with curved sections, for instan-
ce.
• The top of the unit has lead-in seals for the lead-in
pipes of cables and also for the supply and return
water pipes of a water-circulating heater if such a
heater is used.
• The weight of the silencer unit is 105 kg with door,
and 82 kg without door.
Installation
NOTE! BEFORE INSTALLATION CHECK THE MODEL OF
VALLOX 280 (L or R).
• Detach the door of the silencer unit. (See the adjoi-
ning figure.)
• Pierce the lead-in seals on VALLOX 280. (See figure
item D.)
• Pierce the lead-in seals at the bottom of the exhaust
air duct of the silencer unit (no insulation inside).
NOTE! VALLOX 280 model L or R. (See the figure.)
• If VALLOX 280 is equipped with a water-circulating
heater, also detach the lamellar silencer plate in the
supply air duct of the heater.
NOTE! VALLOX 280 model L or R. (See the figure.)
• Lift the unit on top of VALLOX 280.
• Mount the lead-in pipes (included in the delivery) for
cables in place by pushing them first through the
lead-in seals located at the top of the silencer unit
and then through the lead-in seals in the VALLOX 280
unit.
• Thread necessary cables through lead-in pipes to the
connection box located within VALLOX 280.
• If you use a water-circulating heater, mount the supp-
ly and return water pipes for it (not included in the
delivery) through the lead-in seals located at the top
of the silencer unit and VALLOX 280, and connect
them to the supply and return water outlets, using
e.g. a straight connector. (See items A and B in the
figure.)
• Mount the lamellar silencer section in place.
• Carefully fix the door of the silencer unit in place.
• Fix the ducts steadily and tightly to the relevant out-
lets. Implement duct insulation if needed as defined
in the ventilation plan.
VALLOX 280 L
(Note model)
Supply and return water pipe
ø15/13 2 pcs
Silencer unit
(Note! VALLOX model)
Lead-in seal for supply
and return water pipe 2 pcs
Supply and return water pipe
ø15/13 2 pcs
Duct connection ø250 4 pcs
Straight connector
MS 15 2 pcs Cable lead-in pipe 3 pcs
Supply and return
water outlet 2 pcs Lead-in seal for cable
lead-in pipe 3 pcs
Lamellar silencer section
Cable lead-in pipe 3 pcs

1.09.357E/22.01.07/PDF
© VALLOX • We reserve the right to make changes without prior notification.
Vallox Oy FI-32200 Loimaa Finland Telephone +358 2 7636 300 Fax +358 2 7631 539
www.vallox.com
This manual suits for next models
1
Table of contents
Other Vallox Control Panel manuals
Popular Control Panel manuals by other brands
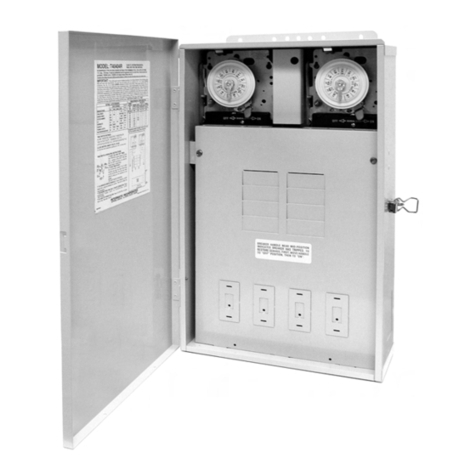
Intermatic
Intermatic INTT40404R Installation, operation & service manual
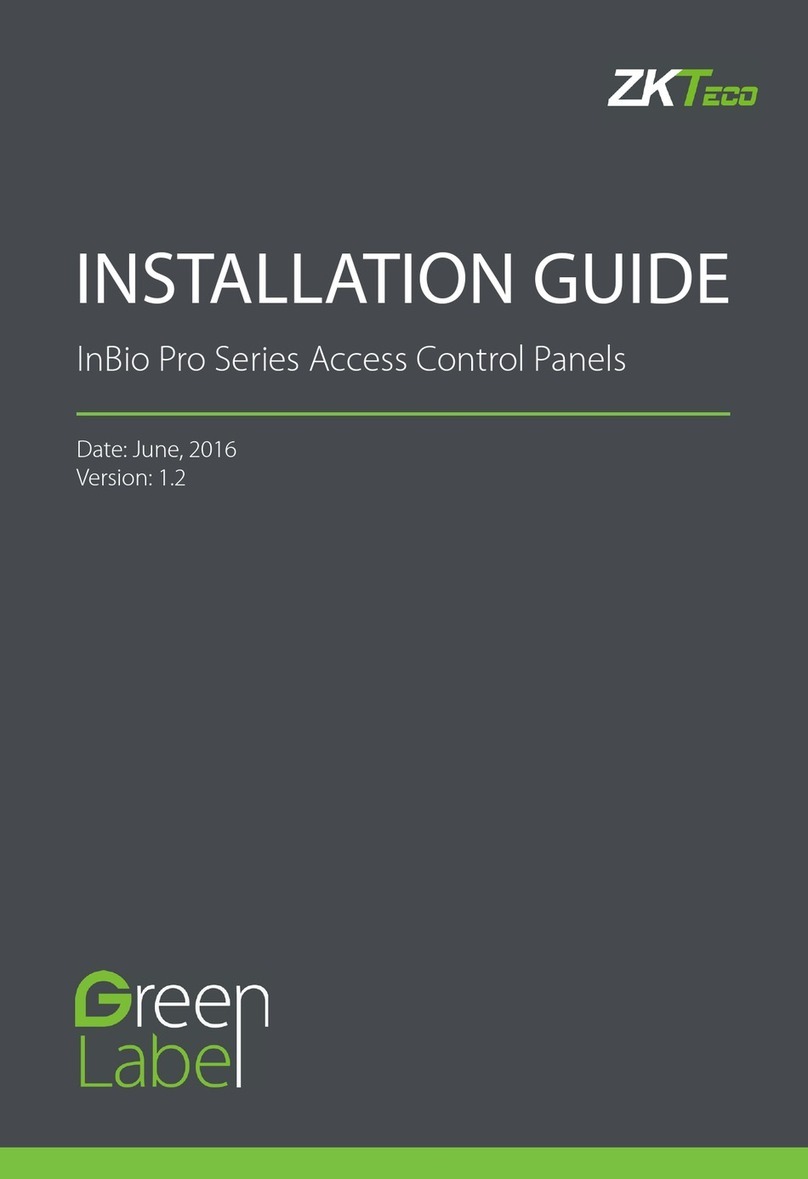
ZKTeco
ZKTeco InBio Pro Series installation guide

Riello
Riello RIELLOtech PRIME Installation, operation and maintenance manual
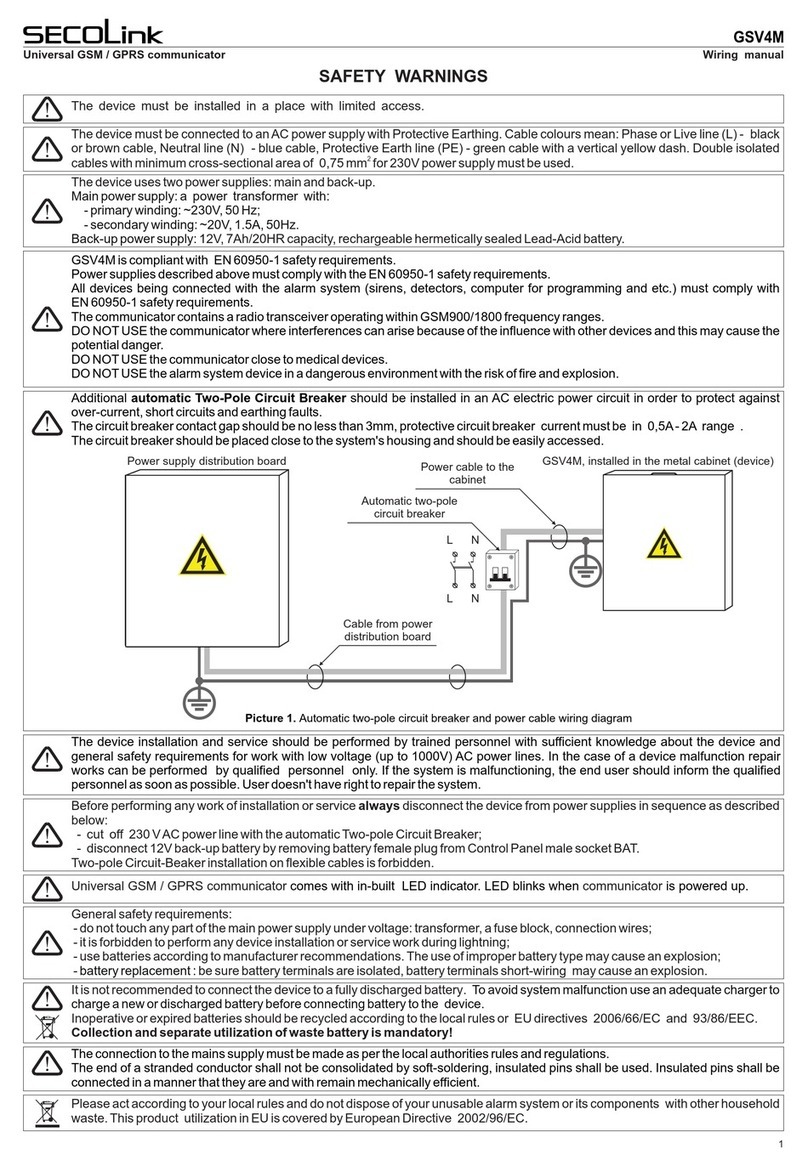
SECOLink
SECOLink GSV4M Wiring Manual
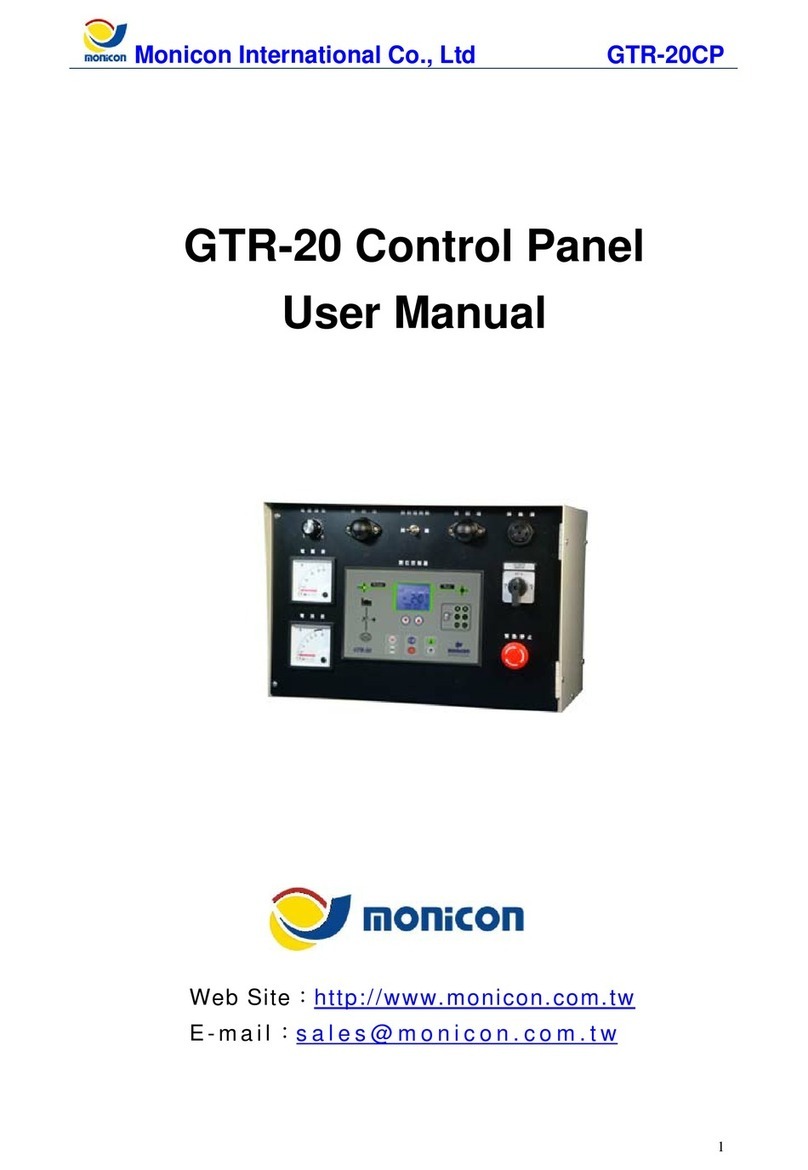
Monicon
Monicon GTR-20 user manual
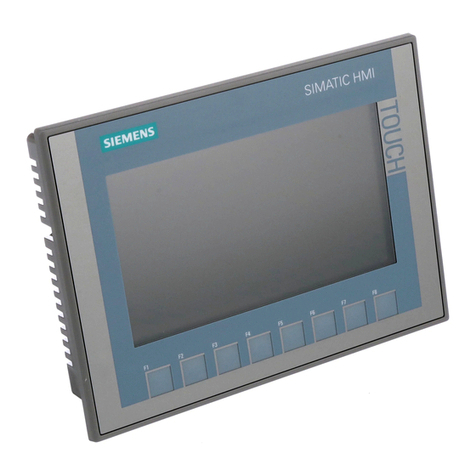
Siemens
Siemens SIMATIC HMI series Getting started