Vemco W41 Series Assembly instructions

Edition 12.2014 Ident.-no. 83627 01
Installation, operating and
maintenance instructions
Transnorm motors with squirrel-cage rotor
Low-voltage (up to 1.000 V)
High-voltage (up to 11.000 V)
Size 315 … 450
Translation
W41./W42./ A41./A42.
W52.
Motors that comply with the Regulation 2005/32/EC
and the order No. 640/2009 receive the marking
IEx before the type designation, whereas x= 2,3
(acc. to EN 60034-30)
(Example IE3-W42R 355 M 2)

Installation, Operating and Maintenance Instructions (Translation) English
.
VEM motors GmbH-2013
2
The reproduction, transmission or use of this document
or its contents is not permitted without express written
authority. Offenders will be liable for damages. All
rights, including rights created by patent grant or regis-
tration of a utility model, are reserved.
© VEM motors GmbH 2013 All rights reserved
This manual is subject to changes.

Installation, Operating and Maintenance Instructions (Translation) English
.
VEM motors GmbH-2013
3
Content
1.
General
1.1
Qualified personnel
1.2
Intended use
1.3
Check after delivery
1.4
Disclaimer
1.5
Used units
2.
General description
2.1
Motor design
2.2
Bearing
2.3
Cooling system
2.4
Monitoring devices
2.5
Identification of motor
3.
Efficiency
4.
Degree of Protection
5.
Type of Construction
6.
Transport, Storage and Packing
7.
Installation and Fitting
7.1
General remarks
7.2
Removal of the Transport Safety Device
7.3
Deconservation
7.4
Completion of motor
7.5
Mounting the coupling
7.6
Steel foundations
7.7
Concrete foundations
7.7.1
Concrete foundation with foundation blocks
7.7.2
Concrete foundation with base plate or base frame / with stone bolts
7.7.3
Concrete foundation with base plate or base frame / with anchor bolts
7.7.4
Concrete foundation with base plate or base frame / with T-head bolts
8.
Fastening, exact alignment
9.
Insulation Check
10.
Motor connection
10.1
Electric connection for low-voltage (up to 1,000 V)
10.2
Electric connection for high-voltage (2.2 kV up to 11 kV)
10.3
Direction of rotation
11.
Commissioning
12.
Maintenance
12.1
Initial inspection
12.2
Main inspection
12.3
Bearings and Lubrication
12.4
Condensate drain
12.5
Cleaning
13.
Long term storage (more than 12 months)
14.
Additional devices (optional)
14.1
Thermal motor protection
14.2
Anti-condensation heating
14.3
Forced ventilation unit
15.
Electromagnetic Compatibility
16.
Trouble Shooting
17.
Disposal
18.
Warranty, Repair, Spare Parts
19.
Terminal board connections / connection diagrams
20.
Design of terminal box
20.1
Design of terminal box for low-voltage applications
20.2
Design of terminal box for high-voltage applications
21.
Overview of spare parts
22.
Trouble shooting
22.1
Electrical Faults
22.2
Mechanical Faults
23.
EC declaration of conformity for low voltage motors and generators
24.
Declaration of incorporation of partly completed machinery

Installation, Operating and Maintenance Instructions (Translation) English
.
VEM motors GmbH-2013
4
1. General
To prevent damage to motors and the driven equipment the procedures laid down in the Operating and Mainte-
nance Instructions must be followed. Especially to avoid risk of injury, the separately enclosed Safety Regulations
must be adhered to strictly.
Since for reasons of clarity the Operating and Maintenance Instructions cannot contain specific information with
regard to all conceivable special applications and areas with special requirements, the user himself has to make
appropriate protection arrangements during the installation process.
1.1 Qualified personnel
Electric motors have dangerous life parts and rotating parts and can also be hot on the surface. It is not
permitted to stand on the motor. All work in connection with transport, storage, installation, connection,
commissioning and maintenance must be done by responsible qualified staff (in accordance with EN
50110-1 / DIN VDE 0105 / IEC 60364). Improper use can result in severe injuries and material damage.
1.2 Intended use
The motors are only approved for the intended use given by the manufacturer in his catalogue and the correspond-
ing technical documentation. This includes consideration of all corresponding product documents. Changes or re-
construction of the motor are not allowed. Other or additional use is not intended. Changes or modifications of the
motor are not permitted. External products and components that shall be used together with the motor must be
approved or recommended by the manufacturer.
The motors comply with the harmonized standard series IEC/EN 60034 / DIN VDE 0530. The use in explosive at-
mosphere is prohibited, if they are not expressly designed for this application.
Delivery of motors complying with special regulations (i.e. classification societies, regulations for explosion protec-
tion) is possible. For these applications special additional manuals are available like for example for roller table
motors and motors in explosion protected design. As scope of delivery the details on the corresponding order con-
firmation are binding.
High-voltage motors are designed for use in industrial plants according to the directive for machine safety
2006/42/EC. The commissioning is prohibited until the final product complies with the directive (please ob-
serve especially the local security and installation regulations i.e. EN 60204).
1.3 Check after delivery
Please check if there was any damage on the motor during transport. Transport damages must be reported imme-
diately to the forwarding agent and the manufacturer.
1.4 Disclaimer
Observance of this manual and the conditions and methods used for installation, operation, use and maintenance
of the electric motor cannot be monitored by the manufacturer. An improper installation can result in property dam-
age and thus result in personal injuries. We therefore do not accept responsibility and liability for losses, damages
or costs resulting from improper installation, improper or wrong use and maintenance or connected with this in any
kind.
We strive to improve our products continuously. Consequently technical data and illustrations remain subject to
change without prior notice. Specifications may only be considered binding after written confirmation by the suppli-
er.
A claim of warranty is excluded in case the operation conditions of the motor were changed, the design of the mo-
tor was modified or repair work was done without prior written agreement from the production site of VEM that has
manufactured the motor.
1.5 Used units
The units used in the manual are based on the SI system (metric system).

Installation, Operating and Maintenance Instructions (Translation) English
.
VEM motors GmbH-2013
5
2. General description
2.1 Motor design
Three-phase asynchronous motors with squirrel-cage rotor in series W41./W42./A41./A42./W52. Are surface-
cooled motors (rip cooling) that are manufactured in shaft sizes 315, 355, 400 and 450 mm. The motors are manu-
factured in basic design with cooling type IC 411 and type of protection IP 55. Other types of cooling, i.e. IC 416
(forced ventilation), IC 410 (non-ventilated) and IC 31W (cooling with water jacket) or types of protection (i.e. IP 54,
IP 56 or IP65) are possible on request as special design. The horizontal types of construction IM 1001 (IM B3), IM
2001 (IM B35) and the vertical type of construction IM 3011 (IM V1) are standard design. Other types available on
request.
Please refer to the name plate and to the data sheets of the electronic catalogue for all information on your motor.
The motors consist of the following main components:
•Stator housing with laminated core and winding
•End shield with bearing
•Rotor with pressure casted winding
•Fan with fan cover
•Terminal box
The stator housing with feet is produced in grey cast iron. The end shields and terminal boxes for low-voltage mo-
tors are also made in grey cast iron. For high-voltage motors a welded steel construction is used for the terminal
box. The cover of the fan on N-end is made of steel sheets or glass fibre reinforced plastics. The terminal box is
placed on top as standard. For terminal boxes from shaft size 355 upwards an assembly of the terminal box at the
sides is not possible.
The terminal boxes KK 200, 400 A and B can be rotated through 90°. The terminal boxes KK 630A and 1000A can
be rotated through 180° and can be placed on top/straight, on top/diagonally to the right and on top/diagonally to
the left. A later modification to another location is not possible for these types of terminal boxes. Marked earthing
points can be found in the terminal box and on the stator housing.
2.2 Bearing
The motors are designed for horizontal types of construction and in basic design „light duty bearing“ with grooved
ball bearings on D- and N-side. The basic design “heavy duty bearing” has a cylinder roller bearing on D-side. Oth-
er types of constructions can have a different type of bearing design. All bearings are dust-tight and from shaft size
315MX upwards they have lubrication device and grease feed regulator. (Information about bearings see chapter
12.3)
2.3 Cooling system
The motors are surface cooled (cooling type IC 411 complying with IEC 60034). The heat exchange is done from
stator core to the ripped housing and from shaft size 355MX there is also an additional internal cooling cycle, which
transfers part of the generated thermal losses to hollow rips designed as cooling channels. The motors all have an
outer and inner fan. For cooling type forced ventilation (IC 416) the outer fan is not used. The air for surface cooling
is sucked in through the additional fan installed within the cover.
2.4 Monitoring devices
Monitoring devices (thermal winding protection, speed monitoring, vibration monitoring, etc.) can be installed on
customer request. For protection of stator windings against thermal overload PTC thermistors according to DIN
44081 can be installed (from shaft size 400 2 sets are standard; for high speed motors there are 6 PT100 in an
additional terminal box). In addition it is possible to install PT100 sensors for monitoring of the winding temperature
and/or bearing temperature. The related triggering units can be supplied on request.
2.5 Identification of motor
Each motor is marked with an identification number. It is listed on the name plate of the motor. This identification
number must be indicated in each correspondence concerning the motor as it is a unique information necessary for
identification of the individual motor.
As standard the motor name plate is printed in German/English as standard. Other languages are available related
to the order and to the motor type. On the name plate the following details of the motor are listed: type designation,
motor number and the most important rated values like output, rated voltage and frequency, rated current, type of
construction, power factor, speed and thermal class. The information can differ according to the individual types.
For motors with lubrication device the amount of grease for each lubrication and the lubrication periods are also
listed on the name plate or on an additional plate. The name plates are fixed on the housing by grooved drive
studs. They can be made in aluminium or stainless steel.

Installation, Operating and Maintenance Instructions (Translation) English
.
VEM motors GmbH-2013
6
Figure 1 Example for name plate and mains operation
Item no.
Information on name plate/designation
1
Efficiency class (IE1/IE2/IE3…)
2
Efficiency
3
Standard and individual approval stamp
4
Motor number, current type
3~Mot.no.
5
Type designation
6
Rated output
kW
7
Rated power factor
8
Connection type
9
Rated voltage
V
10
Rated current
A
11
Rated speed
r.p.m.
12
Rated frequency
Hz
13
Thermal class
Th.cl.
14
Type of protection
IP
15
Mass of product
kg
16
Additional information
17
Additional information, coolant temperature 1 /
coolant temperature 2*)
°C *)
18
Type of construction
19
Month/year of construction
20
Type of grease
21
Bearing DE
22
Amount of grease DE
g
23
Bearing NE
24
Amount of grease NE
g
25
Lubrication interval
h
*) when coolant temperature is 40°C, no indication on the name plate

Installation, Operating and Maintenance Instructions (Translation) English
.
VEM motors GmbH-2013
7
Figure 2 Example for name plate and inverter operation
Item no.
Information on name plate/designation
1
Thermal class
2
Type of protection
3
Mass of product
kg
4
Mot.-Nr. current type
3~Mot.no.
5
Type
V
-
Hz
6
Units of measurement
cos
A
r.p.m.
kW
7
Rated voltage
8
Connection type
9
Mains frequency
10
Rated power factor
11
Rated current
12
Efficiency class
13
Efficiency
14
Rated speed
15
Rated output
16
Inverter information part 1
17
Inverter information part 2
18
Inverter information part 3
19
Inverter information part 4
20
Additional information
21
Type of construction
22
Standard
23
Month/year of construction
24
Additional information, coolant temperature 1
/ coolant temperature 2*)
°C *)
Standard and individual approval stamp
25
Type of grease
26
Bearing DE
27
Amount of grease DE
g
28
Bearing NE
29
Amount of grease NE
g
30
Lubrication interval
h
*) when coolant temperature is 40°C, no indication on the name plate

Installation, Operating and Maintenance Instructions (Translation) English
.
VEM motors GmbH-2013
8
3. Efficiency
The efficiency is determined according to the specifications of EN 60034-2-1. For motors < 1kW the direct meas-
urement method is used. The measurement uncertainty of this method is rated „low“. For motors ≥ 1kW the individ-
ual loss method is used. The additional losses of this method are determined from the residual losses. The meas-
urement uncertainty of this method is also rated as “low”. Efficiency and Efficiency class complying with EN 60034-
30 are listed on the name plate of energy saving motors.
4. Degree of Protection
The degree of protection of the motors is indicated on their rating plate. The degree of protection of additional de-
vices fitted to the motor can be different than the degree of protection of the motor. This needs to be taken into
consideration during the installation of the motors. If motors are installed in the open, they should be protected
against direct effects of the climate (freezing of the fan due to direct fall of rain, snow and formation of ice).
5. Type of Construction
The type of construction of the motors is indicated on the rating plate. The motors can be used in different types of
construction only with permission of the manufacturer and if necessary after modification carried out in accordance
with the manufacturer’s instructions. Especially with types of construction with vertical shaft the user has to ensure
that foreign particles cannot fall into the fan cowl.
6. Transport, Storage and Packing
If possible the motors should only be stored in closed and dry rooms. Outdoor storage under cover is permitted for
a short time only and requires adequate protection against all harmful effects of the climate. The motors also have
to be protected against mechanical damage. Never transport or store the motors resting on their fan cowls. The eye
bolts/attachment eyes of the motors together with appropriate lifting tackle must be used for transport. The eye
bolts/attachment eyes are intended for the lifting of the motors only. No other additional load must be lifted together
with the motor. If eye bolts/attachment eyes are removed after installation, the tapped holes must be blanked off
permanently according to the Protection Standard. For longer periods of storage a low vibration environment shall
be provided so that bearing damages due to downtime can be avoided. After a storage period of more than 12
months the condition of the grease must be checked before putting the motor into operation.
When handling parts of the motor ropes for lifting must not be slung around bearings on the
shaft. If transport is not possible in another way the bearings must be protected accordingly.
7. Installation and Fitting
7.1 General remarks
Since during normal operation of electric motors, temperatures in excess of 100 °C can occur on their
surface, any contact with them must be prevented if the motors are installed in accessible areas. Because
of this temperature sensitive parts must never be fitted to them or have contact with them.
The permissible coolant temperature (room temperature at place of installation) according to IEC/EN 60034-1 is
max. 40°C/min. –20°C without labelling and the permissible altitude of site is up to 1000 m above sea level (other
than the given values have to be specified on the name plate of the motor and must be certified separately if nec-
essary).
Please make sure that the cooling air can enter and leave the air in/outlet without hindrance and without getting
sucked in again. Inlet and outlet openings have to be protected against pollution and dirt particles. The direct intake
of discharged air from neighbouring aggregates must be prevented by suitable measures. The minimum distance of
air inlet of the fan cover against any obstacles (dimension BI) has to be observed under all circumstances.
Figure 3: Minimum distance for air inlet
Size
Bl [mm]
315
55
355
60
400
100
450
100

Installation, Operating and Maintenance Instructions (Translation) English
.
VEM motors GmbH-2013
9
It must be prohibited that foreign particles and liquids can fall into the fan of motors with vertical shaft orientation.
This shall be done as follows:
Shaft end directed downwards:
The protection cover of the fan is equipped with a protective roof (supplied condition).
Shaft end directed upwards:
For type of constructions with shaft end upwards the operator has to ensure that no foreign substances can fall
inside from above. For shaft ends directed upwards it must be prohibited that water or other liquids can penetrate
into the motor next to the shaft.
When setting up surface-cooled motors it must be observed that the bore for condensate drain is located at the
lowest point. If the bores are closed as standard, they must be closed again after the condensate is drained. When
the bores are open direct contact with water jets or water splashes must be avoided. A careful set-up of the motors
on completely level fundament is absolutely necessary to avoid tension during fastening. When machines must be
coupled exact alignment is necessary. It is recommended to use elastic couplings.
The key in the shaft end is secured by the shaft protective sleeve for transport and storage only. Because
of the danger that the key may be thrown aside, a start-up or a trial run with the key protected by the shaft
sleeve only is strictly forbidden.
Transmission components (such as couplings, pinions or belt pulleys) should be drawn onto the shaft by means of
pull-on devices or by heating-up the part to be drawn onto the shaft. For the purpose of drawing the transmission
components onto the shaft, the shaft ends are provided with tapped centring holes according to DIN 332 Part 2.
Transmission components must never be driven onto the shaft using hammer blows because the shaft, the bear-
ings and other components of the motor could be damaged.
All components that are to be fitted to the shaft end must be balanced dynamically according to the balancing sys-
tem of the motor (full or half key). The rotors of the motor are balanced with half key; this is indicated by letter H
after the serial number on the rating plate. Motors with letter F after the serial number are balanced with full key. If
possible the motors are to be installed in such a way that they are free from vibrations. With precision balanced
motors special instructions are to be followed. When the installation is completed the user must ensure protection
of movable parts and safety of operation.
Direct coupling to the driven machine requires a particularly accurate alignment. The shafts of both machines must
be in alignment. The shaft height is to be adjusted to that of the driven machine using appropriate shims.
Belt drives put a lot of stress on the motor because of relatively high radial forces. When dimensioning belt drives,
apart from the instructions and calculation programmes issued by the manufacturers of the belts, it must be en-
sured that the radial force permissible at the shaft end of the motor as stated in our data is never exceeded by the
pull and pre-tensioning of the belt. When pre-tensioning the belt during installation the instructions of the belt manu-
facturers must be strictly adhered to.
Relatively large radial forces or masses can be taken up at the end of the motor shaft by the use of cylindrical roller
bearings (“heavy bearing arrangement” VL). The minimum radial force at the shaft end must be a quarter of the
permissible radial force. The permissible shaft end load is to be taken into account. The information can be taken
from the tables and diagrams in the design selection data.
If the radial force falls below the minimum value, damage to the bearings can be caused within a few hours. Test
runs in no-load state only permissible for a short period.
7.2 Removal of the Transport Safety Device
On motors with transport safety device (roller bearing), the hexagon head screw provided for the fastening of the
transport safety device is to be loosened and taken off together with the transport safety device. Subsequently the
bearing cover bolt packed in a bag inside the terminal box is to be screwed into the bearing cover. If it is necessary
for the motor type the bag will also contain a lock washer that is to be placed onto the bearing end shield bolt be-
fore screwing it into the bearing cover.
After removal of the transport safety device micro movements of the rotor must be prevented by suitable
measures (risk of downtime damages).
7.3 Deconservation
The motor is conserve by the manufacturer. The conservation of machine parts must only be removed when the
installation starts at the installation site. The deconservation is done by using commercial solvents (i.e. benzine or
cleaning solvents).

Installation, Operating and Maintenance Instructions (Translation) English
.
VEM motors GmbH-2013
10
Caution!
When using chemical solvents observe the warning notices and instructions for use in the applicable ma-
terial safety data sheet. Chemicals must be suitable for the components, especially for plastic parts.
7.4 Completion of motor
In some exceptional cases the transport of the motor is done with all accessories (i.e. fan cover, fan motors or en-
coders) separately. These parts must be attached to the motor by using the supplied securing components accord-
ing to the dimensional drawing.
7.5 Mounting the coupling
Caution!
For motors with two floating bearings only couplings with limited axial clearance must be used.
Attention!
The coupling must be balanced with balancing class G2.5 according to ISO 1940.
The following steps are necessary, if nothing else is described by the manufacturer of the coupling:
The mounting temperature of the coupling must be detected.
(belongs to the scope of work for coupling design)
The dimensions and shape of shaft end and coupling bore must be checked.
All contact surfaces must be deconserved (see chapter 7.3)
The coupling half must be warmed evenly until mounting temperature is reached (i.e. by induction heating,
in a furnace or with a ring burner.
The coupling half must be mounted quick and centrically on the shaft end. During this assembly no ham-
mering must be used so that the bearings will not be damaged.
7.6 Steel foundations
The design of a steel foundation is determined by the application of the motor. In many cases they are foundation
slabs or steel floors in buildings or vehicles. Foundation slabs must be erected on load-bearing concrete.
When the motor is starting or running down the natural frequency is passed in case of foundations with deep fre-
quency tuning. This can result in unsteady running for a short period of time.
Procedure:
The motor is placed on the prepared raw foundation.
The exact alignment can be done immediately if the threaded holes for the foot bores are already available
in the steel foundation (1) (see chapter 8). In all other cases further steps are necessary.
The motor must be aligned roughly. During this process a uniform gap (for exact dimension refer to the
coupling manufacturer or plant project) between the coupling and the work machine must be kept. The di-
mension of the gap must be measured right and left. The difference should not be bigger than 0.5 mm. The
motor must stand 3-4 mm lower than the work machine so that it is possible to do exact alignments with
shims.
The foot bores have to be marked on the steel foundation (1).
The motor is removed.
In the marked places core holes must be drilled in the steel foundation suitable for the hexagonal head
screws (12). The holes must then be threaded. Chips from threading must be removed.
1
Steel foundation
9
Shims for exact alignment
10
Foot of machine
11
Washer, reinforced
12
Hexagonal head screw ISO 4017

Installation, Operating and Maintenance Instructions (Translation) English
.
VEM motors GmbH-2013
11
After the motor has again been placed on the steel foundation the exact alignment can start immediately
(see chapter 8).
7.7 Concrete foundations
The used concrete must have a minimum quality complying with strength class C20/25 according to EN 206-1 or
C20/25 according to DIN 1045-2. Before starting the work the raw foundations must be compared with the infor-
mation on the dimensional drawing.
The term „anchor bolt“ is used in the following for anchor screws, stone bolts and T-head bolts.
In the following figures the anchor bolts are used shortened. The length depends on the constructional details.
Tightening torques
The tightening torques are only valid for anchor bolts in concrete foundations. For tightening torques for motor
screws refer to chapter 11.
Threads lubricated
with MoS2 compound
(=0,11)
Threads slightly oiled
(=0,14)
Dimension
Assembly
Test
Assembly
Test
[Nm]
[Nm]
[Nm]
[Nm]
M24
148
126
182
155
M30
296
252
366
311
M36
509
433
631
536
M42
826
702
1025
871
7.7.1 Concrete foundation with foundation blocks
1
Raw foundation
2
Cast concrete
3
Sprue
4
Foundation block
9
Shims for exact alignment
10
Foot of machine
11
Washer, reinforced
12
Hexagonal head screw ISO 4017
Procedure:
The foundation blocks (4) are screwed on centred to the through bores of the machine feet (10) without the
shims (9). To ensure exact centring the hexagonal head screws (12) can be covered with pieces of card-
board.
The motor is placed on the prepared raw foundation (1) were the holes for the foundation blocks (4) are al-
ready available.
The motor must be aligned roughly. During this process a uniform gap (for exact dimension refer to the
coupling manufacturer or plant project) between the coupling and the work machine must be kept. The di-
mension of the gap must be measured right and left. The difference should not be bigger than 0.5 mm. The
motor must stand 3-4 mm lower than the work machine so that it is possible to do exact alignments with
shims.
With a water level the horizontal alignment in longitudinal and transversal direction is checked. For the lon-
gitudinal check the water level is placed on the cylindrical shaft end or the clutch hub; for the transversal
check it is placed on the housing. If necessary the above listed steps must be repeated.
The bores of the foundation blocks must be wetted and if necessary excess water must be removed.

Installation, Operating and Maintenance Instructions (Translation) English
.
VEM motors GmbH-2013
12
The bores of the foundation blocks must be filled with concrete (2). Take care that the concrete is not high-
er than approx. 10 mm below the upper edge of the concrete block (4).
Depending on the type of concrete the hardening of the cast concrete can take up to one week. During
hardening the motor should remain placed on the foundation.
The hexagonal head screws (12) in the motor feet must be loosened. If strips of cardboard were used, they
must be removed. Then the exact alignment can be done (see chapter 8).
7.7.2 Concrete foundation with base plate or base frame / with stone bolts
1
Raw foundation
2
Cast concrete
3
Sprue
4
Flattened steel bar for rough alignment
5
Base plate / base frame
6
Anchor bolt sleeve
7
Anchor bolt: stone bolt DIN 529
8
Hexagonal nut ISO 4032
9
Shims for exact alignment
10
Foot of machine
11
Washer, reinforced
12
Hexagonal head screw ISO 4017
In the following the construction with base plates is described. The construction with base frame is done in the
same way.
Procedure:
The base plates (5) must be screwed centred to the through bores of the motor feet (10) without shims (9).
To ensure exact centring the hexagonal head screws (12) can be covered with pieces of cardboard.
The stone bolts (7) must be placed from below in the anchor bolt sleeves (6) and then fastened at the up-
per end with a hexagonal nut (8). The thread should jut out for approx. 20 mm.
The motor is placed on the prepared raw foundation (1). Below the base plate there should be 40 to 60 mm
space for flattened steel bars for rough alignment (4).
By placing flattened steel bars (4) between raw foundation (1) and base plate (5) the motor is roughly
aligned. The flattened steel bars (4) should be placed within a distance of approx. 500 mm and immediately
left and right of the anchor bolt sleeves (6) so that the stone bolts (7) will not distort the base plate when
tightened. The motor must stand 3-4 mm lower than the work machine so that it is possible to do exact
alignments with shims later. During the rough alignment a uniform gap (for exact dimension refer to the
coupling manufacturer or plant project) between the coupling and the work machine must be kept. The di-
mension of the gap must be measured right and left, on top and from below. The biggest difference should
not be bigger than 0.5 mm.
With the hexagonal head screws (8) the stone bolts (7) are fastened.
With a water level the horizontal alignment in longitudinal and transversal direction is checked. If necessary
the above listed steps must be repeated.
The block-outs in the raw foundation must be wetted and if necessary excess water must be removed.
The block-outs are filled with cast concrete (2). Take care that the concrete is not higher than approx. 10
mm below the upper edge of the base plate (5).
Depending on the type of concrete the hardening of the cast concrete can take up to one week. During
hardening the motor should remain placed on the foundation.

Installation, Operating and Maintenance Instructions (Translation) English
.
VEM motors GmbH-2013
13
When the cast concrete is completely hardened, the hexagonal nuts (8) of the stone bolts (7) must be
tightened crosswise.
The hexagonal head screws (12) in the motor feet (10) must be loosened. If strips of cardboard were used,
they must be removed. Then the exact alignment can be done (see chapter 8).
7.7.3 Concrete foundation with base plate or base frame / with anchor bolts
1
Raw foundation
2
Cast concrete
3
Sprue
4
Flattened steel bar for rough alignment
5
Base plate / base frame
6
Anchor bolt sleeve
7
Anchor bolt: stone bolt DIN 529
8
Hexagonal nut ISO 4032
9
Shims for exact alignment
10
Foot of machine
11
Washer, reinforced
12
Hexagonal head screw ISO 4017
13
Anchor plate
14
Special foundation nut
In the following the construction with base plates is described. The construction with base frame is done in the
same way.
Procedure:
The base plates (5) must be screwed centred to the through bores of the motor feet (10) without shims (9).
To ensure exact centring the hexagonal head screws (12) can be covered with pieces of cardboard.
The stone bolts (7) must be placed from below in the anchor bolt sleeves (6) and then fastened at the up-
per end with a hexagonal nut (8). The thread should jut out for approx. 20 mm.
The motor is placed on the prepared raw foundation (1). Below the base plate there should be 40 to 60 mm
space for flattened steel bars for rough alignment (4).
The anchor plates (13) and special foundation nuts (14) are fastened temporarily so that a height alignment
is possible. If necessary repeat the adjusting of the hexagonal nut (8) and special foundation nut (14).
By placing flattened steel bars (4) between raw foundation (1) and base plate (5) the motor is roughly
aligned. The flattened steel bars (4) should be placed within a distance of approx. 500 mm and immediately
left and right of the anchor bolt sleeves (6) so that the stone bolts (7) will not distort the base plate when
tightened. The motor must stand 3-4 mm lower than the work machine so that it is possible to do exact
alignments with shims later. During the rough alignment a uniform gap (for exact dimension refer to the
coupling manufacturer or plant project) between the coupling and the work machine must be kept. The di-
mension of the gap must be measured right and left, on top and from below. The biggest difference should
not be bigger than 0.5 mm.
With the hexagonal head screws (8) the stone bolts (7) are fastened crosswise. Take care that no distor-
tions result in the machine feet.
With a water level the horizontal alignment in longitudinal and transversal direction is checked. If necessary
the above listed steps must be repeated.
The block-outs in the raw foundation must be wetted and if necessary excess water must be removed.
The block-outs are filled with cast concrete (2). Take care that the concrete is not higher than approx. 10
mm below the upper edge of the base plate (5).
Depending on the type of concrete the hardening of the cast concrete can take up to one week. During
hardening the motor should remain placed on the foundation.

Installation, Operating and Maintenance Instructions (Translation) English
.
VEM motors GmbH-2013
14
When the cast concrete is completely hardened, the hexagonal nuts (8) of the stone bolts (7) must be
tightened crosswise.
The hexagonal head screws (12) in the motor feet (10) must be loosened. If strips of cardboard were used,
they must be removed. Then the exact alignment can be done (see chapter 8).
7.7.4 Concrete foundation with base plate or base frame / with T-head bolts
1
Raw foundation
2
Cast concrete
3
Sprue
4
Flattened steel bar for rough alignment
5
Base plate / base frame
6
Anchor bolt sleeve
7
Anchor bolt: T-head bolt DIN 261
8
Hexagonal nut ISO 4032
9
Shims for exact alignment
10
Foot of machine
11
Washer, reinforced
12
Hexagonal head screw ISO 4017
13
Anchor plate DIN 24539
14
Anchor plate DIN 24539 tube
In the following the construction with base plates is described. The construction with base frame is done in the
same way.
Procedure:
The anchor plates (13) and the corresponding tubes (14) are embedded in concrete according to the
planned position of the anchor bolts in the raw foundation (1). During this process the tubes must not be
filled with concrete.
The base plates (5) must be screwed centred to the through bores of the motor feet (10) without shims (9).
To ensure exact centring the hexagonal head screws (12) can be covered with pieces of cardboard.
The T-head bolts (7) must be placed from below in the anchor bolt sleeves (6) of the base plate (5) and
then fastened at the upper end with a hexagonal nut (8). The thread should jut out for approx. 20 mm.
The motor is placed on the prepared raw foundation (1). Below the base plate there should be 40 to 60 mm
space for flattened steel bars for rough alignment (4).
The T-head bolts (7) are inserted in the anchor plates (13). There is only one possibility to insert the T-
head bolts in the anchor plates. They are then fastened by rotating them around 90° in clockwise direction.
To be able to do a rough alignment take care to have enough clearance for the anchor bolts.
By placing flattened steel bars (4) between raw foundation (1) and base plate (5) the motor is roughly
aligned. The flattened steel bars (4) should be placed within a distance of approx. 500 mm and immediately
left and right of the anchor bolt sleeves (6) so that the T-head bolts (7) will not distort the base plate (5)
when tightened. The motor must stand 3-4 mm lower than the work machine so that it is possible to do ex-
act alignments with shims later. During the rough alignment a uniform gap (for exact dimension refer to the
coupling manufacturer or plant project) between the coupling and the work machine must be kept. The di-
mension of the gap must be measured right and left, on top and from below. The biggest difference should
not be bigger than 0.5 mm.
With the hexagonal head screws (8) the T-head bolts (7) are fastened crosswise. Take care that no distor-
tions result in the machine feet (10).
With a water level the horizontal alignment in longitudinal and transversal direction is checked. If necessary
the above listed steps must be repeated.
The block-outs in the raw foundation must be wetted and if necessary excess water must be removed.

Installation, Operating and Maintenance Instructions (Translation) English
.
VEM motors GmbH-2013
15
The block-outs are filled with cast concrete (2). Take care that the concrete is not higher than approx. 10
mm below the upper edge of the base plate (5). The tubes (14) must not be embedded in concrete so that
it is possible to change the T-head bolts (7) later.
Depending on the type of concrete the hardening of the cast concrete can take up to one week. During
hardening the motor should remain placed on the foundation.
When the cast concrete is completely hardened, the hexagonal nuts (8) of the T-head bolts (7) must be
tightened crosswise.
The hexagonal head screws (12) in the motor feet (10) must be loosened. If strips of cardboard were used,
they must be removed. Then the exact alignment can be done (see chapter 8).
8. Fastening, exact alignment
Caution!
A good alignment is prerequisite for a quiet, vibration-free operation of the motor. This is valid for rigid and
flexible coupling. If the alignment is not correct, coupling defects or bearing damage can occur.
The length of engagement of the hexagonal head screws in the foot bores must be at least as long as the diameter
of the screws.
The term „anchor bolt“ is used in the following for anchor screws, stone bolts and T-head bolts.
Tightening torques
See chapter 11
Necessary measurement devices
Gauge with stand
Laser alignment device
Sensor gauge
Water level
Preliminary preparations
Before exact alignment the following preparations must be done:
The cast concrete must be hardened completely.
Check the tight fit of the anchor bolt in the base plate or the base frame. Tightening torques see chapter
7.6.
The openings of the anchor sleeves must be closed by using the supplied covers.
All transport devices must be removed. See chapter 7.2.
Work flow
The exact alignment of the motor is done by measurement between the coupling halves of the motor and the work
machine.
For alignment shims are placed under the motor feet. The thinnest shims must not be thicker than 0.3 mm. The
shims must be combined in a way that the height compensation is realised with the smallest possible amount of
shims. The shims must be fitting for the size of the feet. It must be possible that the whole foot rests on the shim.
Motors with grey-cast feet have 0.2 mm relief cuts in the contact surfaces. These relief cuts are used for realising
defined clamping. Therefore the rest of motor feet on the foundation must only be checked for all surfaces outside
of the relief cuts during assembly.
1
Foot of the motor
2
Check of shims

Installation, Operating and Maintenance Instructions (Translation) English
.
VEM motors GmbH-2013
16
Procedure (Figures see chapter 7):
The motor feet (10) must be loosely fitted to the foundation by using hexagonal head screws (12) and
washers (11). Take care that there is enough clearance under the hexagonal head so that a height align-
ment of the motor is possible.
A height alignment is done with shims (9) on all motor feet (10) until the coupling half of the motor is level
with the coupling half of the work machine.
Check with the sensor gauge on the shims, if the feet of the motor are evenly loaded. If necessary correct
the shims.
Check with the water level if the motor is horizontally level at right angle to the longitudinal axis. If neces-
sary the above listed steps must be repeated.
The motor must be moved axially so that the gap between the coupling halves complies with the dimension
given by the coupling manufacturer or the plant specification.
Check with a gauge if the axial runout of the coupling halves on the shafts is kept. The shafts must be ro-
tated during this test. The values for axial runout must not exceed x given in the table below. Alternatively
the manufacturer must be contacted.
With the laser alignment device the following tolerances are checked. If the manufacturer of the work ma-
chine has defined dimensions about an increase in height for the work machine, this specification must be
observed during alignment as well.
The exact alignment is done by adding or removing shims and by moving the motor until the tolerances are
kept. Afterwards fasten the hexagonal head screws (12) for the motor feet (10) crosswise.
Recheck the correct alignment. This check must be repeated again after the rotor is rotated around 180°.
The measured values must be recorded.
Bolting of the motor
1
Taper pins EN 28736
2
Washer, reinforced
3
Hexagonal head screw ISO 4017
The bolting of the motor is recommended to assist the alignment process during a possible reinstallation of this
motor.
Speed [r.p.m.]
x [mm]
< 1,400
0.03
1,400 … 2,900
0.02
2,900
0.01

Installation, Operating and Maintenance Instructions (Translation) English
.
VEM motors GmbH-2013
17
Procedure:
Near the screw holes of the motor feet diagonal bores are made; the diameter depends on the size of the
machine and is 12 to 25 mm. These bores must be extended diagonally into the steel parts of the founda-
tion with the same diameter.
These bores must be opened by using a taper reamer (taper 1:50) until it is possible to insert the taper pin
flush from above.
On the taper pin (1) the hexagonal head screw (3) must be screwed on together with the washer (2) for ap-
prox. 5 mm. Then the taper pin (1) is driven in carefully by using a hammer so that it is sunk in some mm.
The hexagonal head screw (3) is screwed on tight by hand.
When the motor is disassembled the taper pin can be removed by fastening the hexagonal head screw.
9. Insulation Check
When the motor is first commissioned and especially after extended storage, the insulation resistance of
the winding is to be measured to earth and between phases. During and immediately after the measure-
ments dangerous voltages are present at the terminals. Therefore never touch the terminals and follow
the operating instructions of the insulation resistance meter closely!
Caution!Secure motor against accidental starting! Ground the windings at least 10 s to avoid electrostatic charging
before and after insulation measurement!
To assess the insulation resistance the following table is used. Please observe that always the insulation value Ris
of the cold motor (that is at ambient temperature of approx. 25°C) is assessed, as values from warm motors are not
unambiguously reproducible. For a new motor from production or after rewinding of the stator the minimum value of
the insulation at ambient temperature must comply with the values of point 1 in the table.
During transport and storage under unfavourable conditions this value can be reduced without damage to the insu-
lation. Even motors standing still for some time under extreme climate conditions and with no anti-condensation
heating (condensation on the winding) can be taken into operation if the insulation resistance of the cold motor is
not below the values from point 2 of the table. If the insulation value is below that value the windings must be dried
or in some special cases even cleaned and then dried. It must be checked if the insulation value was restored after
a short time of operation. Under normal storage conditions and operational breaks the insulation resistance must
not fall below the values from point 2 when the motor is still cold.
Voltage
Rated voltage < 1.5 kV
Rated voltage > 1.5 kV
Test voltage
> 100 V up to max. 500 V
1000 V
Test duration
1 min
1. Winding new or after rewinding, dry,
25 °C
Ris > 50 MΩ
Ris > 100 MΩ
2. Winding after longer operational
time, drying condition unknown, 25 °C
Ris > 1 MΩ
Ris > 5 MΩ / kV
Table: Insulation resistance
If the minimum values are lower, the winding must be dried properly until the insulation resistance corresponds to
the required value.
10. Motor connection
10.1 Electric connection for low-voltage (up to 1,000 V)
The connection has to be done by qualified personnel according to the valid security regulations.
Outside of Germany the required national standards must be applied.
Name plate designations have to be observed under all circumstances!
The electric installation should be organised in detail before realisation. Connection diagrams delivered with the
motor must be read carefully before starting installation work. It is important that the supply voltage and the fre-
quency comply with the data on the name plate of the motor. In addition the mains voltage and the frequency must
be within the limits of the tolerances specified within the corresponding standard. Please observe the data on the
name plate and the connection diagram under all circumstances.
CAUTION! Ground the motor with the provided connection terminals for the grounding in the terminal box and
on the foot.
The terminal box must be free of pollution, humidity and foreign particles. The terminal box itself, the cable glands
and unused cable entries must be closed protected against dust and water. Take extra care when connecting the

Installation, Operating and Maintenance Instructions (Translation) English
.
VEM motors GmbH-2013
18
supply cables in the terminal box of the motor. The nuts of the connection screws have to be fastened without
force. Before connecting the power line, the existing motor connections must eventually be retightened. The termi-
nals for connecting additional devices and monitoring units are situated in the terminal box (in the additional termi-
nal box only when ordered accordingly).
CAUTION ! The distances between live parts and against ground must not go below the following values:
Rated voltage UN
[V]
400
500
725
1,000
Minimum distance
[mm]
6
8
12
14
Terminal box overview
Terminal box type
Terminal board
Rated current
Connecting
thread
Tightening torque
[A]
[Nm]
KK 400 B
KM 12
400
M12
20 4
KK 400 B
KM 16
630
M16
30 4
KK 630 A
KLP 630-16
630
M16
30 4
KK 630 A
KLP 630-20
630
M20
30 4
KK 1000 A
KLSO 1000
1000
current bar
-
The arrangement of cable lugs, nuts and counter nuts must be done according to the drawings from chapter 20
(Design of terminal boxes).
10.2 Electric connection for high-voltage (2.2 kV up to 11 kV)
The terminals for connecting addition devices and monitoring units are situated in the additional terminal box.
CAUTION ! The distances between live parts and against ground must not go below the following values:
Rated voltage UN
[kV]
3
3.3
6
6.6
10
11
Minimum distance
[mm]
36
40
60
70
100
110
The arrangement of cable lugs, nuts and counter nuts must be done according to the drawings from chapter 20
(Design of terminal boxes).
Terminal box
Rated current
Type of
protec-
tion
Terminal
Cable lug
Max.
terminal
cross sec-
tion
[A]
[mm2]
6 kV
250
IP 55
DIN46264-6-M16-Ms or
DIN46264-6-M12-Ms *)
DIN46234
150
10 kV ± 10%
315 (400)
IP 55
DIN46264-6-M16-Ms
DIN46234,
DIN46235
240
*) Bolt M12 only permitted for short-circuit power at the terminals of 200 MVA (DIN V 42962)
10.3 Direction of rotation
The marking of the terminals is done according to DIN EN 60034-8 / IEC 60034-8. In standard design motors are
suitable for both directions of rotation. When the phases L1, L2, L3 are connected correct at the terminals U-V-W
the motors rotate in clockwise direction; that means seen from the drive end the direction of rotation is in clockwise
direction.
For motors only suitable for one direction of rotation the direction is marked by an arrow on the motor, on
the fan or on the name plate. When these motors shall be operated in the other direction please contact
the manufacturer first!
For direct starting and pole-changing motors with separate winding the direction of rotation can be reversed by
changing two of the line conductors on the terminal board. For motors with star/delta-starting and pole-changing
motors with Dahlander winding two line conductors must be changed at the supply to the motor switch.
A motor with only one shaft end or two shaft ends with different diameters the direction of rotation is that one seen
from the front end of the only shaft end or the bigger shaft end.

Installation, Operating and Maintenance Instructions (Translation) English
.
VEM motors GmbH-2013
19
11. Commissioning
Please follow the Safety Regulations closely. All work is to be carried out only when there is no voltage on the mo-
tor. The installation must be carried out according to the valid regulations by qualified skilled personnel. Initially the
mains conditions (voltage and frequency) must be compared with the data on the rating plate of the motor. The
dimensions of the connecting cables must be adjusted in line with the rated currents of the motor.
The connection points of the motor are marked in accordance with EN 60034-8 (VDE 0530 Part 8). In Section 19 of
these instructions the most common circuit diagrams for three phase motors in basic design are provided, accord-
ing to which the connection will be implemented. For all other versions, the special circuit diagrams are glued to the
inside of the terminal box cover or placed in the terminal box. An additional terminal box can be provided for the
connection of auxiliary and protection devices (e.g. anti-condensation heaters); the same regulations apply as for
the main terminal box.
Always start the motors with an over-current protection device that is set in accordance with the relevant nominal
values of the motor (1.05 Inom). Otherwise warranty claims with respect to damaged windings become void. Before
the motor is connected for the first time it is recommended to check the insulation resistances between winding and
earth and between phases (see Section 9). After prolonged storage it is absolutely essential that the insulation
resistance is measured. Before coupling the motor to the driven machine, check the direction of rotation of the mo-
tor to prevent possible damage being caused to the driven machine. If the power lines are connected with the
phase sequence L1, L2, L3 to U, V, W, the direction of rotation is clockwise (view to shaft end on drive side DS). If
two terminals are changed, the direction of rotation is counter clockwise (i.e. L1, L2, L3 to V, U, W). For machines
with only one direction of rotation the required sense of rotation is marked by an arrow on the machine. For the
permissible tightening torques for the terminal board bolts refer to the table below:
Tightening torques for bolts (terminal box, end shield, bearing cover)
Thread Ø
M8
M10
M12
M16
M20
M24
Attachment eyes
-
-
-
150
250
400
End shield
25
45
75
170
275
-
Bearing cover
15
20
20
-
-
-
Terminal box
7,5
12,5
-
20
-
-
Before closing the terminal box make absolutely sure that:
- the connection has been made in accordance with the wiring diagram
- all terminal box connections are tightened
- all minimum values of air paths are maintained (see ch. 7)
-the interior of the terminal box is clean and free from foreign particles
-unused cable entries are blanked off and the threaded plugs with seals are tightened
-the seal in the terminal box cover is clean and tightly glued and all sealing surfaces
are in the correct state to ensure that the relevant degree of protection is maintained.
Before starting up the motor check that all safety regulations are strictly adhered to, that the machine is correctly
installed and aligned, that all fixing parts and earthing connections are tightened, that the auxiliary and additional
devices are functionally and correctly connected and if a second shaft end is fitted that the key is secured against
being thrown aside.
If possible the motor is to be connected without load. If the motor is running smoothly and without any abnormal
noises, the load of the driven machine is to be applied onto the motor. When the motor is started up it is recom-
mended to monitor the current consumption if the motor is loaded with its driven machine so that any possible over-
loads and asymmetries occurring in the mains can be recognised immediately.
For mountings like encoders, brakes and others please observe the corresponding operating and maintenance
instructions of the manufacturer.
12. Maintenance
You are once again referred to the Safety Regulations, in particular to isolation, to securing against reconnection,
to checking whether all components connected to a voltage source are in dead state. If it is necessary to discon-
nect the motor from the mains for maintenance work particular care must be taken to ensure that any possibly ex-
isting auxiliary circuits (e.g. anti-condensation heaters, forced ventilators, brakes) are also disconnected from the
mains.
If the motor is to be dismantled during maintenance work, the sealing compound on the centring shoulders is to be
removed. When re-assembling the motor these need to be re-sealed using a suitable motor sealing compound.
Existing copper sealing washers must always be refitted.
Careful and regular maintenance, inspections and revisions are necessary to detect and clear faults in time, before
consequential damages will happen. As individual operating conditions cannot be defined for all applications the

Installation, Operating and Maintenance Instructions (Translation) English
.
VEM motors GmbH-2013
20
listed terms represent a general advice for undisturbed operation. Individual local conditions (degree of pollution,
load, etc.) must be taken into account when adjusting these terms.
What to do?
Time period
Terms
First inspection
After about 500 operating hours
½ year at the latest
Control of air circulation
and surface of motor
Depending on local environmental pollu-
tion
Lubrication (as option)
See name plate or lubrication sign
Main inspection
After about 10,000 operating hours
Once a year
Remove condensate water
Depending on the local environmental
conditions
12.1 Initial inspection
According to the requirements an initial inspection of the motor must be organised after approximately 500 hours of
operation, but not later than half a year after start of operation.
The following examinations will be done at standstill of the motor:
a) Check of the foundations. There must be no cracks or other damages like depressions.
The following examinations will be done when the motor is running:
a) Check of the electric characteristics.
b) Check of the bearing temperatures. It is examined if the permissible bearing temperatures will be exceeded
during operation of the motor (for standard grease and max. 120°C)
c) Check of the running noises. When the motor is running, it is checked if the quiet running has changed for
the worse.
If the examination results in differences from the values specified in the maintenance manual or if there are other
faults or damages detected, than these must be corrected immediately.
12.2 Main inspection
According to the requirements a main inspection of the motor must be organised annually after approximately
10,000 hours of operation.
The following examinations will be done at standstill of the motor:
a) Check of the foundations. There must be no cracks or other damages like depressions.
b) Check of the motor alignment. The motor alignment must be within the given tolerances.
c) Check of the fastening bolts. All bolts used for fixing mechanical and electrical connections must be tight
(see also the table for tightening torques for bolts in chapter 11. Commissioning).
b) Check of the cables and the insulation material. The examination must check if the cables and used insula-
tion materials are in good conditions. They must not be discoloured or even burnt and they must not be
broken, cracked or faulty in any other way.
c) Check of the insulation resistance. The insulation resistance of the winding must be measured. The re-
quirements in the maintenance manual (chapter 9) must be kept.
d) According to the grease quality and bearing type of the motor it can be necessary to change the grease af-
ter 10,000 working hours (see chapter 12.3 Bearings and Lubrication). Apart from that the necessary lubri-
cation periods for friction bearings must be observed, because they differ from the inspection periods.
The following examinations will be done when the motor is running:
a) Check of the electric characteristics.
b) Check of the bearing temperatures. It is examined if the permissible bearing temperatures will be exceeded
during operation of the motor.
c) Check of the running noises. When the motor is running, it is checked if the quiet running has changed for
the worse.
If the examination results in differences from the values specified in the maintenance manual or if there are other
faults or damages detected, than these must be corrected immediately.
12.3 Bearings and Lubrication
The anti-friction bearings of the motors in standard design are filled with anti-friction bearing grease in the factory
(or with sealed bearings by the bearing manufacturer) according to DIN 51825 in compliance with the table below:
This manual suits for next models
85
Table of contents
Other Vemco Engine manuals
Popular Engine manuals by other brands

Sumitomo
Sumitomo Cyclo Drive 6000 operating manual
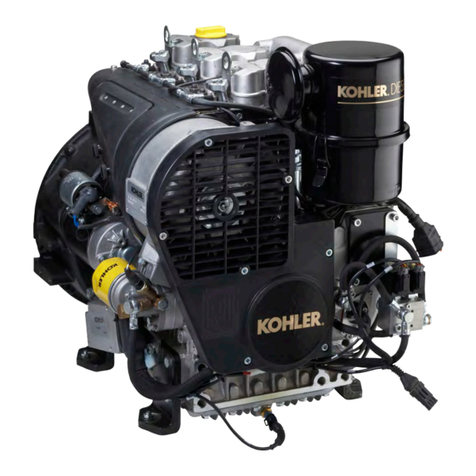
Kohler
Kohler KD625-3 Workshop manual

Wyco
Wyco EZ Vibe EH035 Operation, maintenance and parts manual

Ametek
Ametek dunkermotoren GR Series Translation of the original assembly instruction
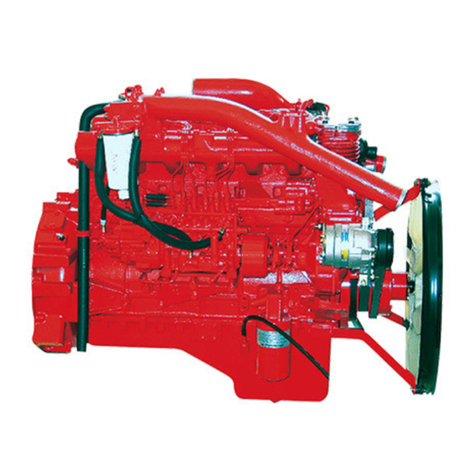
Doosan
Doosan DE08TS Disassembly/Assembly
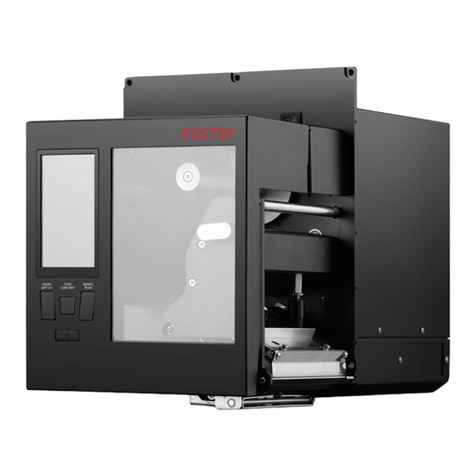
Postek
Postek MX Series user manual