VENMA COMFORT Series Installation and operation manual

T
Operating & Maintenance Manual
COMFORT Series pellet
burners
P E L L E T B U R N E R S

2
P E L L E T B U R N E R S
1. Product overview
The Comfort series is state-of-the-art and most advanced biomass fuel combustion
units from VENMA. These burners feature a fly and bottom ash removal system.
Firing-u , combustion, quenching and cleaning is contained to the burner and
rocessed automatically for o eration without any need for manual interaction. The burner
is fired u by su lying a re-charge of fuel and ignition by an integrated igniter which heats
the re-charged fuel to its ignition oint. The combustion and quenching rocesses are
managed by an electronic control unit (ref. the control unit user manual). The burner is
cleaned of solid combustion residues by an ash rake. The burner is cleaned eriodically
which hel s with secondary combustion to use 100% of the charged fuel and im rove the
costs of heating and reduce its environmental foot rint. Cleaning of the burner also hel s
extend the service life of the combustion chamber.
The burners are com atible with central heating boilers fired with solid fuels and
certain gas or fuel-oil boilers which feature a combustion chamber and an ash tra .
The VENMA burner is a very green heating solution which can be fuelled with
renewable materials, including ellets, fruit stones or oats.
The burner is managed by the included control unit which rovides ste less
adjustment of the fuel and air mixing ratio to control the heat out ut to the heat demand.
The control unit can su ort u to 4 circulation um s and 3 mixing valves. The control unit
also su orts u to 6 tem erature sensors (to acce t out uts from a s ace heating cycle
tem erature sensor, a DHW tem erature sensor, a valve o eration sensor, a return
tem erature sensor, and thermal buffer sensors). The control unit features multi le
convenience and management features, including a PID flue gas sensor, a room tem erature
controller, or an oxygen sensor to make o eration of the burner easy and with much
comfort.
The burner features multi le fire rotection features which, in the event of a failure
or overheating, isolate the fuel su ly to revent ro agation of flames and a fire outside of
the combustion chamber. No electrical ower blackout can harm the burner, since the fuel
charge resent at any time in the burner’s combustion chamber is relatively small.
The fuel to be charged to the burner must be ke t in a solid, sealed container
(a bunker) and handled to the burner via a screw (auger) fuel feeder from VENMA with
ro erly selected length and ower out ut.
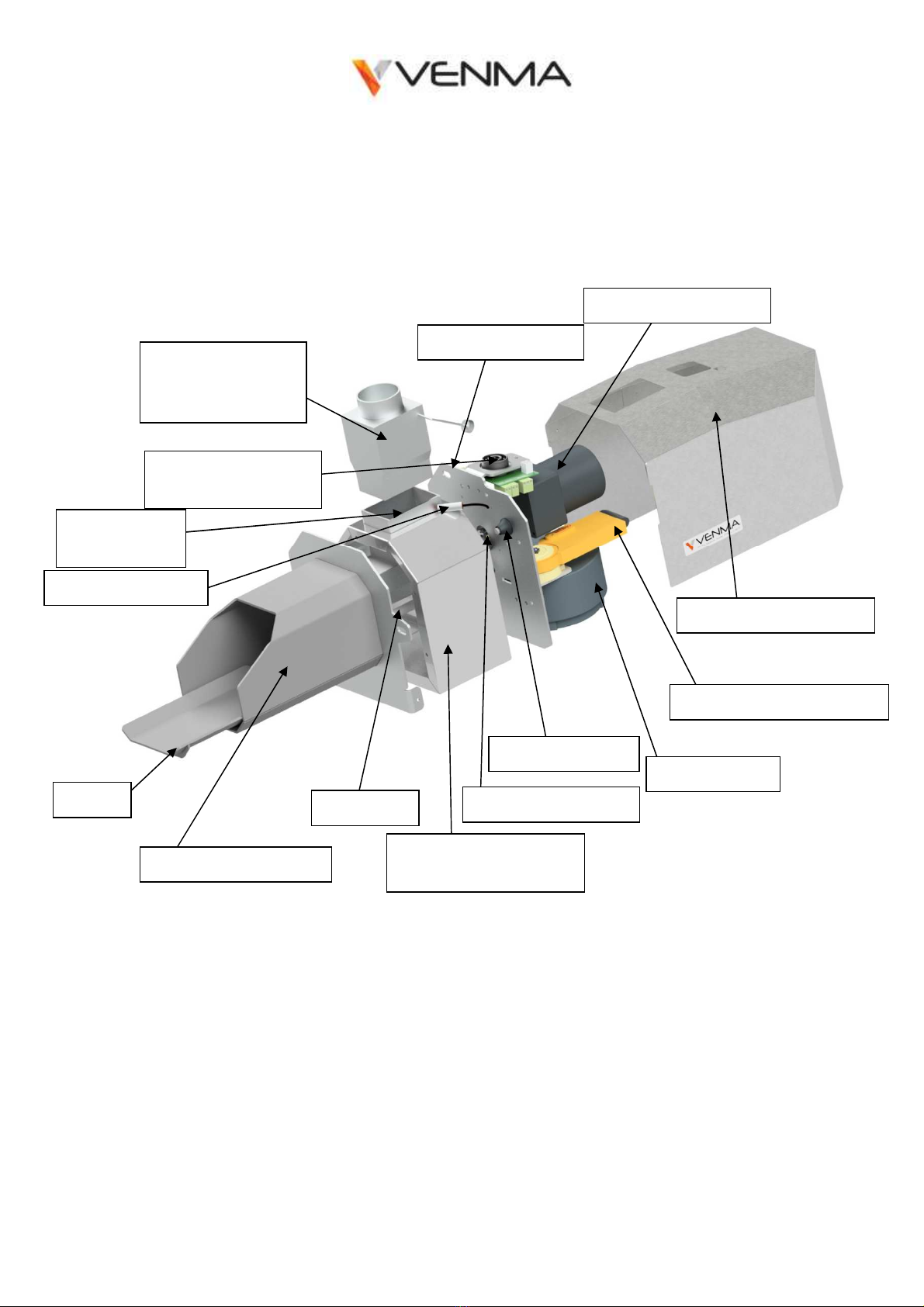
3
P E L L E T B U R N E R S
2. Burner design
The VENMA burner com rises steel com onents and electrical arts. The combustion
chamber and the grate of the burner are made of heat-resistant stainless steel. The steel
material has been tested for resistance at tem eratures above 1,000°C. The fuel feeder duct
is made from galvanized black steel for corrosion rotection throughout the o erating life.
The design revents overheating of the burner electrical com onents for maximum service
life and reliability.
. Operating principle
The burner starts o erating by firing u , followed by sustained combustion of fuel.
The o eration ends by quenching the fire and cleaning of the burner.
The external screw fuel feeder handles the fuel from the bunker to the burner.
The first firing-u of a brand-new burner must be started manually; each next firing
u rocess will be managed automatically by the control unit following the user-defined
settings.
Before each firing-u , the burner is blown through to clean the combustion chamber of any
residues left from rior quenching. Next, a fuel re-charge is fed, meanwhile the igniter
Grate
Combustion chamber
Outer casing
Positive- ressure
chamber
Flame sensor
Air fan
Ash
removal system
Internal fuel feeder
Power in ut
rece tacle
Base late
Fuel feeder sensor
Fuel charging
duct
Inner screw
Igniter
Fuel charging
ho er with a fire
dam er

4
P E L L E T B U R N E R S
heats u to a rox. 1,000°C, heating u the stream of air forced in by the fan until the re-
charged fuel ignites.
Next a flame sensor (which is a hoto-sensitive device) detects the illumination growing
from the flame inside the combustion chamber and de-energizes the igniter; the control unit
enters the Flame Stabilization stage to heat u the burner for maintained combustion.
Further o erating modes de end on the algorithm and may include: (Ref. the control unit
user manual for detailed information about the o erating modes.)
- Heat modulation (between the minimum out ut and the maximum out ut)
- PID control
- Automatic o eration
The burner is cleaned of ash during combustion or after quenching; the sequence for
ash removal can be selected on the control unit (ref. the control unit user manual).
The burner is quenched automatically; it can also be done manually with the control unit
(ref. the control unit user manual). This o erating mode rovides secondary combustion to
consume the remaining fuel in the combustion chamber.
4. Product delivery contents
The roduct includes:
Part designation: Indicative figure:
VENMA ellet burners
VEMNA control unit with a com lete
wiring and sensor ackage
Standard 2 m long galvanized steel fuel
feeder (a longer o tion is available on
request)
Flex tube, 1 m long
Installation flange (o tional)*
* Standard feature for 100 kW or higher-rated burners
Fuel charging ho er with a fire dam er
Ceramic gasket
VENMA O erating & Maintenance

5
P E L L E T B U R N E R S
Manual
VENMA Control Unit O erating &
Maintenance Manual
5. Installation and commissioning
The burner shall be installed by a licensed and qualified rofessional. VENMA
shall not be liable for any defective installation of the burner.
The VENMA burner is intended for integration with central heating
boilers, as well as most ty es of gas or fuel-oil boilers. The installation location of the
VENMA burner may vary with the boiler configuration; however, it is usually recommended
to install it on the fuel charging door. When measuring the size of installation o enings to be
made, mind that the VENMA burner will require eriodic ins ection. The installation
o enings must be located so as to kee the boiler’s original fuel charging and other doors
o erable.
The VENMA burner has been designed for relatively easy installation: the combustion
chamber and installation o enings are factory-made.
If you want to retrofit a regular boiler with the VENMA burner, the combustion
chamber and installation o enings must be sized carefully. The table further in this Manual
shows the combustion chamber dimensions and the s acing and size of the installation
o enings. The VENMA burner heat out ut must be com atible with the boiler’s heat rating.
1. Measure and make the o ening for the burner’s combustion chamber.
2. Measure and make the installation o enings for the burner bolts.
3. Install the burner on the fuel charging door of the boiler by securing both com onents with the bolts.
4. Set u the ellet fuel bunker.
5. Measure and adjust the ellet fuel feeder length; the angle between the floor and the fuel feeder duct
must not be higher than 45°. (Ref. Fig. 2)
6. Sus end the fuel feeder on a chain sling. (Ref. Fig. 2)
7. Connect the burner to the fuel feeder with the s iral flex i e. Note that the flex i e run cannot be
too long and its bending radius must be long enough to ermit a gravity-assisted flow of the ellet fuel
without clogging or bridging.
8. The control unit’s actuator module can be installed anywhere; however, choose an installation
location not directly ex osed to the heat from the boiler or CH i ing and with easy access for
o eration of the control unit.
9. Install the control unit dis lay and the wiring for um s, valves and other system com onents.
10. Install the sensors from the ackage in res ective locations.
11. Connect the ower cable and the grate cable to the burner.
12. Fill the bunker with fuel.
13. With the bunker full, ower on the control unit and wait for the initialization screen to be dis layed.
14. Prime the fuel feeder (the galvanized steel duct which houses the screw) with the ellet fuel. The fuel
feeder is rimed in full when the ellet fuel starts flowing down the flex i e (ref. the control unit user
manual).
15. If the flex i e is full of fuel, select Manual O eration and Internal Fuel Feeder. Wait for the ellet fuel
to flow into the combustion chamber; next, remove the ellet from the combustion chamber or move
it to the ash tra . DO NOT SELECT “FIRING UP” IF YOU ARE NOT SURE THAT THE COMBUSTION
CHAMBER AND THE FLEX PIPE ARE EMPTY.
EXPLOSION HAZARD!
16. With the foregoing ste s com leted, you may o erate your VENMA burner; ref. the control unit user
manual for the configuration settings.
CAUTION

6
P E L L E T B U R N E R S
VENMA Comfort 16-35 burners
Mode : Power
range:
Max. current input:
(Firing-up / Combustion)
Weight: A
[mm]
B
[mm]
C
[mm]
D
[mm]
E
[mm]
F
[mm]
G
[mm]
H
[mm]
Comfort 16 4-16 kW 300/70 W 11 kg 185 244 485 110 110 131 109 100
Comfort 25 5-26 kW 300/70 W 13 kg 215 274 515 125 125 150 113 96
Comfort 35 6-35 kW 300/70 W 15 kg 240 299 540 138 138 163 109 100
VENMA Comfort 46-300 burners
Model:
Power
range:
Max. current
in ut: (Firing-
u /
Combustion)
Weight:
A*
[m
m]
B
[m
m]
C
[m
m]
D
[m
m]
E
[m
m]
F
[m
m]
G
[m
m]
H
[m
m]
I
[m
m]
J
[m
m]
K
[m
m]
L
[m
m]
X
[m
m]
Y
[m
m]
S
[m
m]
S1
[m
m]
Comfort
46
10
-
46
kW
450/150 W
24 kg
198
301
377
665
286
385
178
178
274
274
236
236
137
137
223
325
Comfort
58
12
-
58
kW
450/150 W
30 kg
238
341
417
705
286
358
178
178
274
274
236
236
137
137
223
325
Comfort
70
15
-
70
kW
450/150 W
36 kg
228
342
443
765
312
411
198
198
300
300
265
265
150
150
255
365
Comfort
85
20
-
85
kW
450/150 W
40 kg
277
395
493
815
312
411
198
198
300
300
265
265
150
150
255
365
Comfort
100
25
-
100
kW
510/210 W
64 kg
277
441
600
997
383
467
250
260
360
370
314
314
184
186
326
435
Comfort
125
35
-
125
kW
510/210 W
70 kg
327
495
650
1047
383
467
250
260
360
370
314
314
184
186
326
435
Comfort
150-300
Consult a reseller
* O tional feature on the Comfort 46-85 burners; standard feature on Comfort 100 and
higher-rated burners.

7
P E L L E T B U R N E R S
FIG. 2
6. Fuel specifications
The fuel for the burner shall conform to the following s ecifications:
Form Granulated
Diameter 6-8 mm
Length 3-40 mm
Dust fraction ≤1%
Fuel density ≥620 kg/m
3
Moisture content <8%
Calorific value 16-20 MJ/kg
Ash ≤0.7%

8
P E L L E T B U R N E R S
7. Screw fuel feeder
The screw fuel feeder connects the fuel bunker with the burner. The screw fuel
feeder com rises a galvanized steel or stainless-steel duct 60 mm in diameter. The duct
houses a steel screw (auger) driven by an 230V AC motor over a gear. The motor is wired
with a ower cable to the res ective ower out ut rece tacle of the burner control unit. The
burner is fed automatically with fuel and automatically managed. If the fuel feeder duct fails
e.g. by overheating with a flame flashback, the fuel feeder sto s o eration which quenches
the burner. This revents flames from ro agating to the outside and a risk of fire in the
boiler room.
8. Operating the burner
The burner shall be installed and o erated according to this Manual and the
Warranty Certificate. VENMA shall not be liable for any damage resulting from im ro er use
of the burner.
The burner shall be cleaned and maintained according to the sound judgement of the
user. The obligatory annual ins ection of the burner shall be scheduled with the authorized
technical service at least two weeks in advance.
The heating equi ment safety regulations require a minimum clearance of 0.8 m
around the installed burner. Provide a sufficient clearance for service access to the burner.
The boiler room shall be a dry and well-ventilated indoor location. No flammables shall be
resent near the burner

9
P E L L E T B U R N E R S
9. Inspection of the burner
To ensure trouble-free o eration of the burner for many years, ro er maintenance
must be erformed. It is highly recommended to order an authorized technical service for an
annual ins ection of the burner after each heating season. However, if it is undesirable or
im ossible to have authorized technical service erform the annual ins ections, the user
must erform them anyway.
CAUTION! Power off the contro unit and disconnect the power supp y wiring from
the burner!
The burner internal com onents are shown below with the casing removed.
•Re lacing the igniter: remove bolt #1 (with a 4 mm hex key) and remove the igniter
assembly with the tube shield; remove the rubber gland and release the small bolt
(with a 3 mm hex key) from the tube shield until the igniter can be freely removed.
Install the new igniter and reassemble in the reverse order of disassembly.
Bolt #1
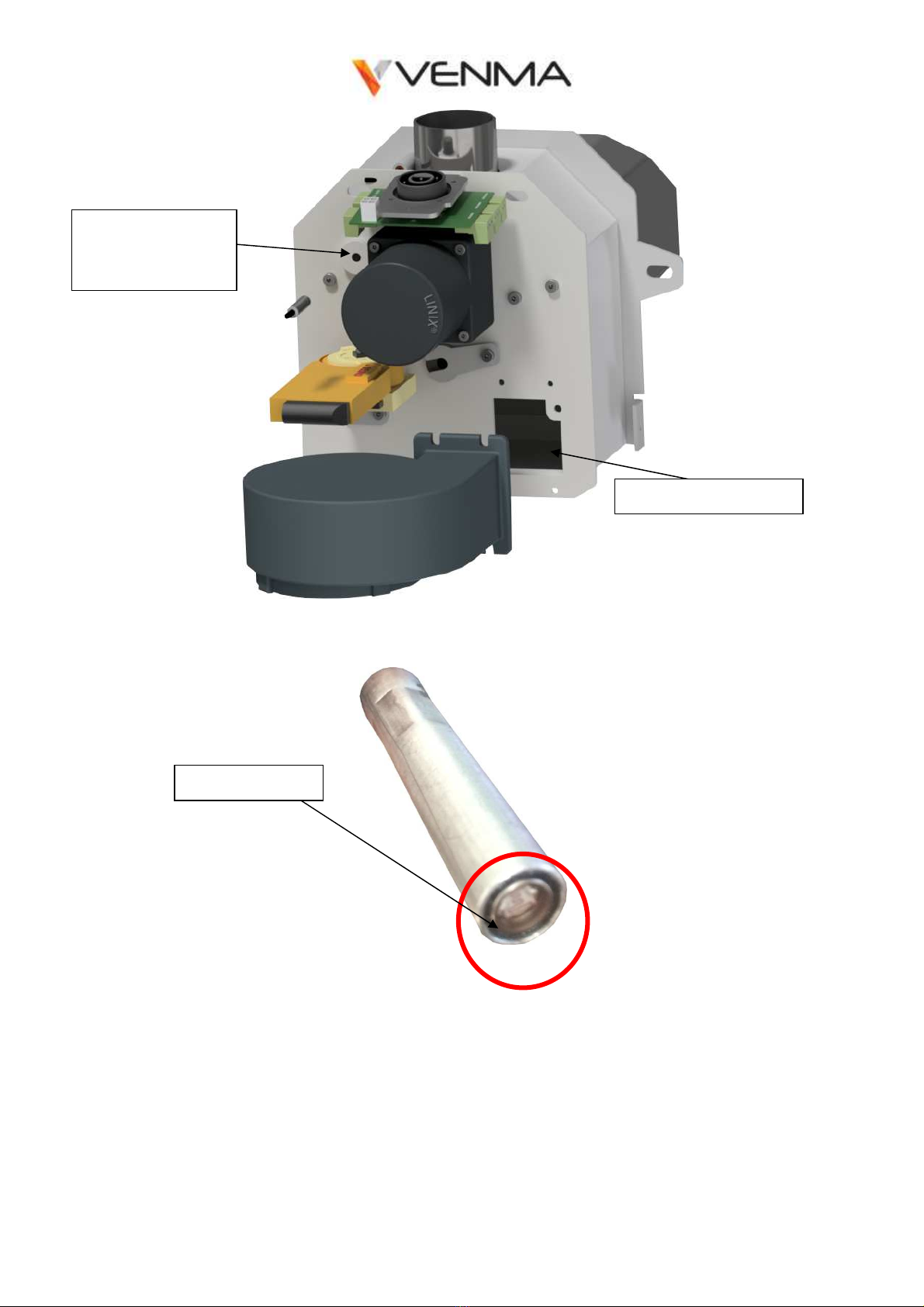
10
P E L L E T B U R N E R S
•Cleaning the flame sensor ( hoto-sensitive device): remove the flame sensor
carefully by ulling it out towards you and clean with a dry cloth. Reinstall the flame
sensor in the rubber gland.
•Cleaning the ositive- ressure chamber: remove the air fan and use its ort to access
and thoroughly clean all dust and ash.
Clean here
Flame sensor
( hoto-sensitive
devide)
Air fan ort
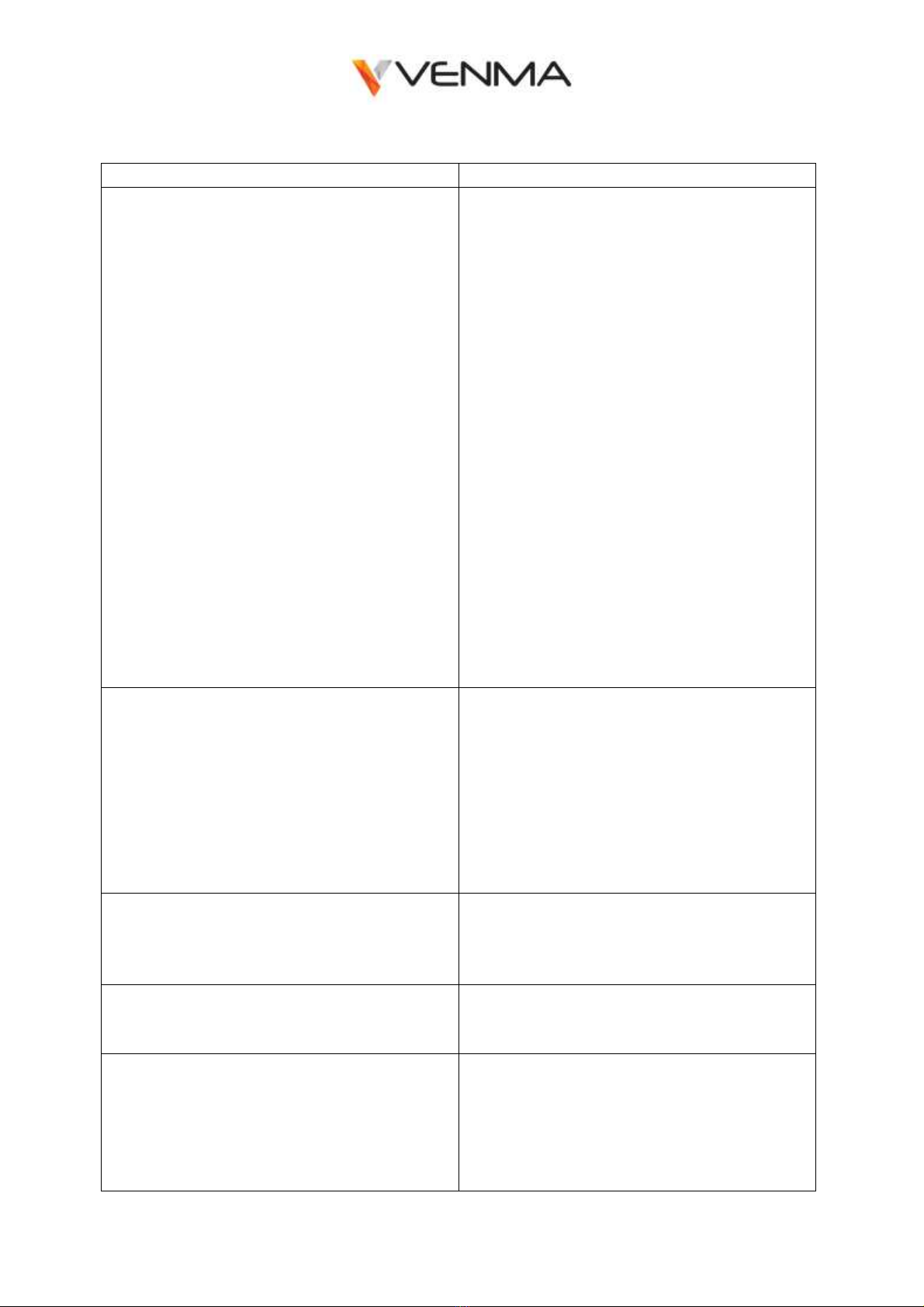
11
P E L L E T B U R N E R S
10. FAQ (Frequently Asked Questions)
Error A arm / Notification Potentia cause
The burner failed to ignite; the dis lay reads
Firing Up Fai ed.
- No fuel left in the bunker; restock and
rime the fuel feeder duct in manual control
mode;
- Run a functional test of the igniter in
manual control mode. If the igniter has
failed, contact the authorized technical
service.
- Check the burner grate for clogging with
ash. Clean the grate manually if required;
reduce the ash removal interval in the
service menu of the dis lay.
- Switch to manual control mode and run a
functional test of the external fuel feeder. If
the fuel feeder runs but it still fails to charge
a sufficient dose of fuel, clean the charging
ho er of the fuel bunker and the fuel
feeder duct.
- Check that the igniter’s ti (heat out ut
a erture) is clearly visible. Poor ellet fuel
grades may obstruct the igniter.
- Clean the flame sensor (do this carefully
with a dry cloth).
The control unit’s dis lay reads Feeder
Overtemperature
- Check that the flue gas duct and the
chimney connection for clogging.
- Carefully ins ect the boiler chambers, the
heat exchanger and the smoke breeching for
de osits of ash and soot which may obstruct
correct draught.
– Check the burner grate for excessive
de osits of ash. Remove the ash manually if
required; reduce the ash removal interval.
The air fan and the external fuel feeder are
ino erative.
Most likely the bi-metallic thermal cut-out
was tri ed. Wait a roximately 60
minutes. If the error ersists, contact the
authorized technical service.
The burner failed to fire u des ite DHW
demand or a room tem erature controller.
- Weekly Schedule Control is active;
- Burner Quenched Manually by User.
The CH circulation um fails to start when
it reaches the start tem erature.
- The control unit o erates in the Summer
Mode. Change the Running Mode to Parallel
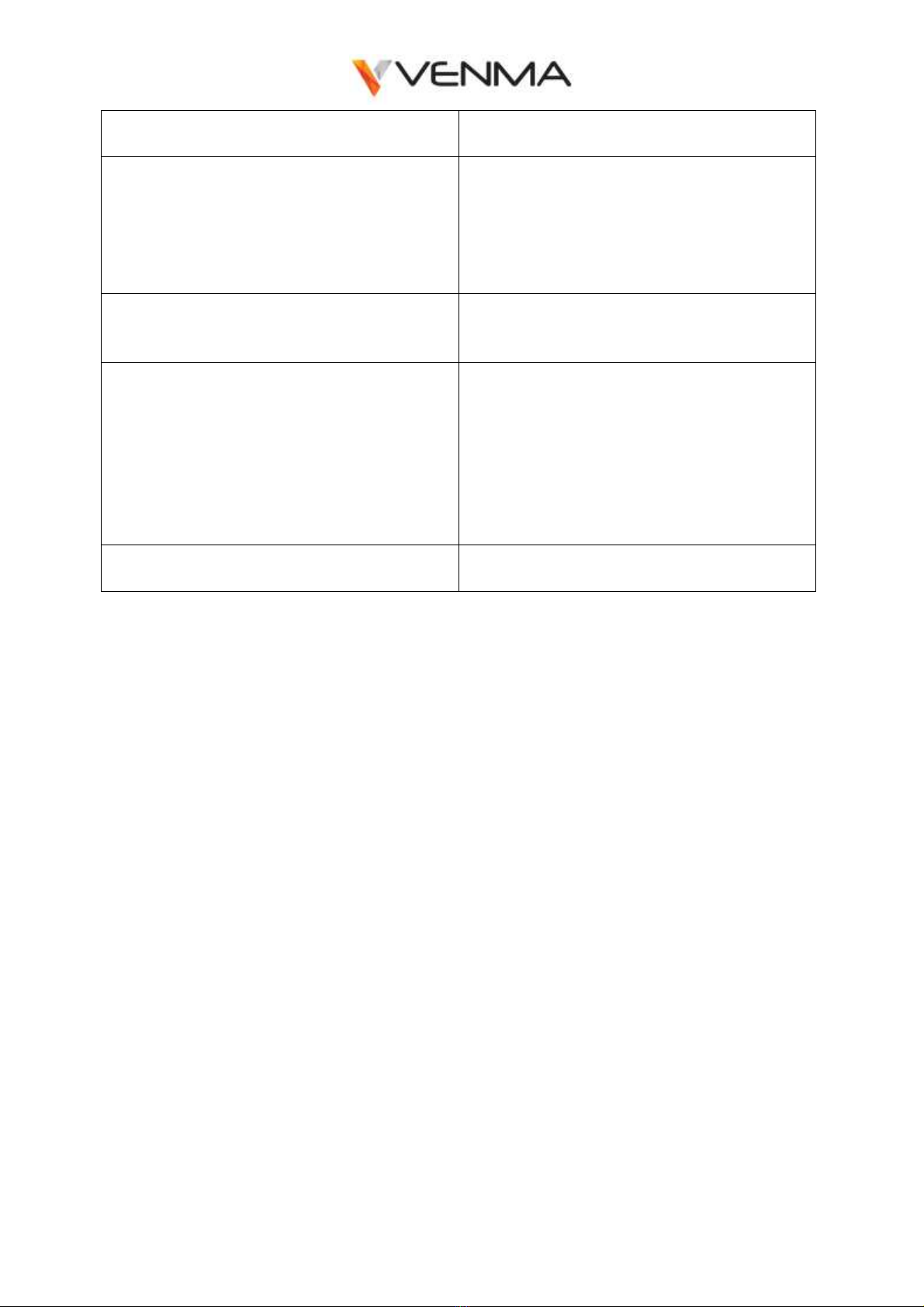
12
P E L L E T B U R N E R S
Pum s or S ace Heating.
- The CH Pum Room o tion is enabled.
The DHW um fails to start when it reaches
the start tem erature.
- The control unit o erates in the Summer
Mode. Change the Running Mode to Parallel
Pum s or Boiler in Priority.
- The actual DHW tem erature is above the
DHW tem erature.
- The DHW Schedule is enabled.
The control unit fails run. Re lace the ower fuse in the actuator
module (locate the white ower terminal
box to which all wiring is connected).
The burner smokes heavily and leaves soot
inside the boiler.
Insufficient oxygen or too much fuel in the
mix:
- Reduce the fuel dosage or increase the
oxygen;
- - Check the grating slots and the
combustion chamber anel vents for
obstructions. If there is obstruction, unclog
with e.g. a chisel less than 4 mm in diameter.
The combustion rocess leaves much slag. The fuel grade is oor:
- Use a fuel grade o timum for the burner.

13
P E L L E T B U R N E R S
11. Installation Report
Buyer’s data:
Location: Postal code: City:
Street address: Phone: E-mail:
Reseller’s data:
Location: Postal code: City:
Street address: Phone: E-mail:
Burner installer’s data:
Location: Postal code: City:
Street address: Phone: E-mail:
Burner s ecifications:
Standard o eration: Automatic o eration: PID o eration:
Min. heat out ut:
Fuel feeder running
time:..........
Fuel feeder sto time:..........
Combustion air
su ly:...................
Max. heat out ut:
Fuel feeder running
time:..........
Fuel feeder sto time:..........
Combustion air
su ly:...................
Fuel s ecific
weight:..........................
Calorific value:..............
Max. air fan:...................
Min. air fan:.....................
Max. fuel feeder
ratio:....................
Min. fuel feeder
ratio:....................
Max. air fan
ratio:....................
Min. air fan
ratio:....................
.....................................................
Installer’s legible signature:
.....................................................
Buyer’s legible signature:

14
P E L L E T B U R N E R S
12. Warranty
Certificate
Periodic, warranty and ost-warranty burner ins ection
Date: Service engineer’s stamp and egib e
signature:
Inspection type and Report
no.:
NOTICE!!!
Each inspection on site sha have the Inspection Report fi ed out and signed by the service
engineer.

15
P E L L E T B U R N E R S
1 . Warranty Terms & Conditions
1. VENMA grants this Warranty for the roduct with a warranty eriod of 12-36 months
and the warranty eriod shall not exceed 36 months ast the roduct’s roduction date
( rovided that the roduct asses an eriodic ins ection after every 12 months of
o eration).
2. All workmanshi defects found in the roduct will be removed at VENMA’s cost in 21
business days from filing the warranty claim.
3. The sco e, method and terms of warranty re air are solely at VENMA’s discretion.
4. The Warranty shall remain valid if the Warranty Certificate signed and retained with the
roof of original urchase of the roduct.
5. Each defect of the roduct shall be claimed immediately u on discovery.
6. The Warranty does not include mechanical failure of the roduct.
7. The Warranty does not include the installation, commissioning, control unit
configuration rogramming, cleaning or maintenance.
8. Excluded from this Warranty are:
•incorrect configuration settings of the burner;
•damage caused during trans ort or handling;
•installation and/or o eration of the roduct in de arture from the O erating &
Maintenance Manual;
•unauthorized alteration or modification of the burner or control unit;
•insufficient flue duct draught;
•unauthorized re air of the roduct;
•damage caused by defective electrical ower wiring on site;
•feeding incom atible fuel ty es (e.g. elletized MDF).
9. The Warranty holder shall be charged with the costs of technical service claimed for
defects excluded from this Warranty.
10. The igniter of this roduct is covered by a 12-month warranty only.
11. File your warranty claim with the Claim form on VENMA’s official website, e-mail, ost,
or fax.

16
P E L L E T B U R N E R S
14. Contents
1.
Product overview ................................................................................................................ 2
2.
Burner design ...................................................................................................................... 3
3.
O erating rinci le ............................................................................................................. 3
4.
Product delivery contents ................................................................................................... 4
5.
Installation and commissioning .......................................................................................... 5
6.
Fuel s ecifications ............................................................................................................... 7
7.
Screw fuel feeder ................................................................................................................ 8
8.
O erating the burner .......................................................................................................... 8
9.
Ins ection of the burner ..................................................................................................... 9
10.
FAQ (Frequently Asked Questions) ............................................................................... 11
11.
Installation Re ort ......................................................................................................... 13
12.
Warranty Certificate ...................................................................................................... 14
13.
Warranty Terms & Conditions ....................................................................................... 15
14.
Contents ........................................................................................................................ 16
VENMA Nata ia Mączka
Pustków 385b
39-205 Pustków, Poland
NIP (Tax ID): 872-232-44-95
Office:
(Mo.-Fri. 7:00-15:00)
E-mai : biuro@venma.eu
Phone: +48 14 658 42 00
Service:
(Mo.-Fri. 7:00-15:00)
E-mai : [email protected]
Phone: +48 14 658 42 02
www.venma.eu
This manual suits for next models
11
Table of contents