VHF E4 User manual

E4
ORIGINAL OPERATING
INSTRUCTIONS
Originalbetriebsanleitung
Instrucciones de uso originales
Mode d'emploi d'origine
Istruzioni d'uso originali
dentalportal.info
https://stomshop.pro/

https://stomshop.pro/

Contents
1 Welcome 5
1.1 Target group 5
1.2 Used symbols 5
1.3 Signal words 5
1.4 Copyright 5
2 General safety instructions 6
2.1 Intended use 6
2.2 User skills 6
2.3 Incorrect operation of the machine 6
2.4 Personal injury 6
2.4.1 Electric shock 6
2.4.2 Fire hazard 7
2.4.3 Housing 7
2.4.4 Working chamber 7
2.4.5 Air extraction system 7
2.4.6 Operating noise 7
2.4.7 Maintenance and troubleshooting 7
2.4.8 Spare parts, extra equipment and accessories 7
2.5 Material damage 7
2.5.1 Spindle 7
2.5.2 DENTALCAM & DENTALCNC software 8
2.5.3 Power 8
2.5.4 Wet machining 8
2.5.5 Air extraction system 8
2.5.6 Working chamber 8
2.5.7 Working chamber door 8
3 Transportation and storage 9
3.1 Transporting the machine in the carton 9
3.2 Preparing transportation or storage 9
3.3 Repackaging 9
3.4 Putting the machine back into operation after storage 9
4.1 Unpacking and positioning of the machine 10
4.1.1 Choosing the installation site 10
4.1.2 Unpacking the machine 10
5 Getting to know your machine 14
5.1 Front side of the machine 14
5.2 Rear side of the machine 14
5.3 Connection panel 15
5.4 Start button 15
5.5 Working chamber door 15
5.6 Lever for emergency release of the working chamber
door 15
5.7 Working chamber 15
5.8 Cooling liquid tank and dry tank 16
5.9 Axes 17
5.10 Location of the identification plate and serial number 17
5.11 Technical data 18
6 Installation 19
6.1 Checking the scope of delivery 20
6.2 Connecting the machine 22
6.2.1 Machine installation scheme 22
6.2.2 Connecting the CAM computer 22
6.2.3 Installing the air extraction system 22
6.2.4 Establishing the electric connection 24
6.3 Commissioning 26
6.3.1 Starting the machine 26
6.3.2 Setting up a software connection to the machine 26
6.3.3 Warming the spindle 28
6.3.4 Drill tool magazine inserts 28
6.3.5 Filling the cooling liquid 28
7 Operating the machine 29
7.1 Starting the machine 30
7.1.1 Starting the machine 30
7.1.2 Starting the machine with a tool in the collet chuck 30
7.2 Switching between wet and dry machining 31
7.2.1 Switching from wet to dry machining 31
7.2.2 Switching from dry to wet machining 31
7.3 Filling the cooling liquid 33
7.4 Mounting & removing blanks 34
7.4.1 Suitable blanks 34
7.4.2 Overview of the blank holder 34
7.4.3 Moving the axes to the default position 34
7.4.4 Mounting & removing blocks 34
7.5 Inserting and exchanging tools 36
7.5.1 Automatic or manual tool change 36
7.5.2 Inserting tools into the tool magazine 36
7.5.3 Removing tools from the tool magazine 38
7.5.4 Adding backup tools 38
7.6 Starting, interrupting, canceling jobs 39
7.6.1 Starting jobs 39
7.6.2 Interrupt and continue machining 39
7.6.3 Aborting machining 39
7.7 Switching off the machine 41
7.7.1 Switching off the machine 41
8 Maintenance 42
8.1 Basic maintenance 42
8.2 Preventive maintenance 42
8.3 Maintenance section 42
8.4 Servicing 42
Original Operating Instructions: E4
Version: 4/4/2023
EN 3
https://stomshop.pro/

8.5 Warranty 42
8.6 Maintenance table 43
8.6.1 Once per week 43
8.6.2 Every 4 weeks 43
8.6.3 Every 2 years 43
8.6.4 When necessary 43
8.7 Spare parts and wear parts 44
8.7.1 Definition of wear parts 44
8.7.2 Spare part list 44
8.8 Cleaning the machine 46
8.8.1 Performing the weekly cleaning 46
8.9 Cleaning or replacing the collet chuck of the spindle 53
8.9.1 Removing the collet chuck 53
8.9.2 Cleaning the collet chuck 54
8.9.3 Greasing the collet chuck 54
8.9.4 Inserting the collet chuck 54
8.10 Cleaning the nozzle plate 56
8.11 Exchanging the cooling liquid and cleaning the cool-
ing liquid tank 57
8.12 Cleaning the cooling liquid system 61
8.13 Exchange tool magazine inserts and associated hold-
ers 62
8.14 Exchanging the blank holder 68
8.15 Exchanging the measuring key 69
8.16 Exchanging the gasket of the working chamber door 71
8.17 Exchanging the tank cover 72
8.18 Disassembling and assembling the machine housing 73
8.18.1 The components of the machine housing 73
8.18.2 Removing and installing back panel and top
cover 73
8.18.3 Removing and installing the service cover 74
8.18.4 Removing and installing side panels 75
8.19 Exchanging the main fuse 77
8.20 Calibrating the axes 78
8.21 Updating the software and firmware 79
8.21.1 Updating DENTALCAM & DENTALCNC 79
8.21.2 Updating the firmware of the machine 79
9 Troubleshooting 80
9.1 Links to troubleshooting guides 80
9.2 Machine-specific notes 80
9.2.1 Loud machining noise 80
9.2.2 How to proceed in the event of a machine mal-
function 80
9.2.3 How to proceed in the event of a tool breakage 80
9.2.4 How to proceed in the event of a power failure 80
9.3 Emergency opening of the working chamber door 82
9.4 Loosening a fixed tool magazine 83
9.5 Removing broken tools from the collet chuck 85
10 Disposal 86
10.1 Disposing of the cooling liquid and machining
residues 86
10.1.1 General 86
10.1.2 Disposing of the cooling liquid 86
10.1.3 Solid machining residues 86
10.2 Disposing of the machine 86
10.3 Dismantling, transport and packaging 86
Index 87
Original Operating Instructions:E4
Version: 4/4/2023
Contents
EN 4
https://stomshop.pro/

1 WELCOME
Thank you for purchasing this E4dental machine.
These operating instructions were prepared to help
you understand all functions of your new dental
machine.
You may find updates to this document at:
dentalportal.info/E4
1.1 Target group
These instructions are intended and released for the
following groups of people:
nEnd users
nAuthorized resellers
nAuthorized service technicians
1.2 Used symbols
Calls to action
Single or general calls to action
1. Numbered action step
Result
Other symbols
Cross reference
nList (first level)
List (second level)
1. Numbered image labels
Correct or Do this
Incorrect or Do not let this happen or Don’t do
this
1.3 Signal w ords
The following signal words may be used:
DANGER
DANGER indicates a hazardous situation which will
result in death or serious injury.
WARNING
WARNING indicates a hazardous situation which can
result in death or serious injury.
CAUTION
CAUTION indicates a hazardous situation which can
result in minor injury.
NOTICE
NOTICE indicates a situation which can lead to physical
damage of the product or in the surrounding areas.
1.4 Copyright
Distribution or duplication of all content is only
allowed by written consent of vhf camfacture AG. This
includes reproduction by presentation and broad-
casting.
This document is published by:
vhf camfacture AG
Lettenstraße 10
72119 Ammerbuch, Germany
dentalportal.info
Welcome EN 5
Original Operating Instructions: E4
Version: 4/4/2023
https://stomshop.pro/

2 GENERAL SAFETY
INSTRUCTIONS
2.1 Intended use
The machine and the manufacturing software are
designed for the commercial machining of dental-tech-
nical objects. The processed objects require additional
work before their use on patients.
The machine is designed for wet and dry machining.
Machine only blanks and objects whose types you
can select in each case in the manufacturing soft-
ware. Although you can also machine any other
objects and blanks, neither the manufacturing soft-
ware nor the machine are designed for these other
blanks and objects.
Under certain circumstances, the use of this
machine may be subject to legal requirements.
Observe applicable local and national regulations
as well as the requirements of other authorized
organizations or agencies (e.g., professional asso-
ciations, health authorities) that have jurisdiction.
Obtain authorization from the appropriate organ-
ization (e.g., professional associations, health
authorities) as needed. For all materials machined
with this machine, observe the material’s instruc-
tions for use with respect to the intended use and
all related software and machining procedure
requirements.
Do not manufacture implants or parts of objects
that are designed to have contact with implants.
These parts include parts of two-part abutments
which contain the connection geometry for the
implant. Do not manipulate the connection
geometry of prefabricated abutments and always
check finished objects for correct connection
geometries (i.e. connection geometries of finished
jobs were not damaged).
2.2 User skills
Action Necessary qualification
Using DENTALCAM Persons trained in dentistry
Use of machine/ DENTALCNC
for manufacturing dental
objects
Instructed persons
Activity must be supervised
by a persons trained in
dentistry
Use machine / DENTALCNC
for cleaning and maintenance
Instructed persons
Action Necessary qualification
All other activities described
in the operating instructions
Instructed persons
Service work/ preventive
maintenance*
vhf-authorized service tech-
nicians
*Further information on maintenance:Maintenance –
on page42
2.3 Incorrect operation of the
machine
Before installation, putting into operation and main-
tenance of the machine, read all the documents
provided for the machine.
If it is unclear how to operate the machine in any
way, do not use the machine and contact customer
service.
Ensure that every user has access to the operating
instructions.
Instruct every user on safe and proper machine
handling.
2.4 Personal injury
2.4.1 Electric shock
Electric shock by touching live parts
Remove the housing of the machine only for neces-
sary repairs. Keep the following order:
1. Switch off the machine at the main power switch.
2. Disconnect the machine from all lines.
3. Remove the housing.
4. Carry out the necessary repair.
5. Install the housing.
6. Connect the machine to all lines.
7. Switch on the machine at the main power switch.
Only have qualified electricians work on any elec-
tric equipment.
Ensure that an operational Residual Current
Device/ Ground Fault Circuit Interrupter is
installed on the electric circuit of the machine.
Run electric cables so that they cannot be
damaged by sharp edges.
Check the power cable for damage before every
startup.
In the following cases, disconnect the machine
from the electrical source immediately and prevent
it from being restarted:
Original Operating Instructions:E4
Version: 4/4/2023
General safety instructions
EN 6
https://stomshop.pro/

nWhen machine connections or electric cables are
damaged
nWhen liquid is leaking
nBefore you check or run electric cables
Do not touch the machine and especially the
cables with wet or damp hands.
Do not place any liquid containers on the machine.
Never put any machines or devices which are
powered by electricity under the machine.
Electric shock when disconnecting the power cable
with the main power switch in “ON” position.
Follow the following sequence:
1. Switch off the machine at the main power switch.
2. Disconnect the power cable.
2.4.2 Fire hazard
Unattended operation
Only allow unattended operation of the machine
to occur if the following conditions are met:
nThe working chamber of the machine is com-
pletely clean.
nUnauthorized users cannot access the machine.
nThe room in which the machine is located has an
automatic fire detection system.
2.4.3 Housing
Danger of entrapment by moving housing parts
nWorking chamber door
nCooling liquid tank
nDry tank
If you move these housing parts, use only the desig-
nated grip points.
Make sure that your hands are not trapped during
movement.
2.4.4 Working chamber
Danger of crushing due to moving machine parts in
the working chamber
Only use the machine when the working chamber
door is completely closed and undamaged during
machining.
Do not circumvent or deactivate safety devices of
the machine.
Check the machine regularly for damage, espe-
cially the safety devices.
Danger of cutting and burning
Always wear gloves when performing manual work
on the machine or with blanks / tools.
Only touch tools on the shaft.
Do not touch the spindle body after machining.
2.4.5 Air extraction system
Respiratory diseases when processing harmful
materials
Always use a suitable air extraction system during
dry machining.
Use a suction unit with fine dust filter class M.
Avoid materials which damage your health.
2.4.6 Operating noise
Hearing loss and tinnitus due to regular loud
working noises
If loud working noises cannot be prevented, use an
ear protector during machining.
2.4.7 Maintenance and troubleshooting
Risk of injuries from machine malfunctions due to
inadequate or incorrect maintenance/
troubleshooting
Perform the maintenance tasks according to the
maintenance table.
Never perform any troubleshooting while the
machine is operating.
2.4.8 Spare parts, extra equipment and
accessories
Risk of injuries due to unsuitable spare parts / extra
equipment / accessories
Use only original spare parts, original extra equip-
ment and original accessories for the machine.
2.5 Material damage
2.5.1 Spindle
Damage caused by the warm-up phase being
omitted
When initially starting a machine or if it has not been
used for at least 2 weeks, you must warm the spindle
before use.
Use the warm-up process in DENTALCNC.
The DENTALCAM & DENTALCNC user Information
provides instructions on how to do this.
Damage due to poor maintenance
Clean and exchange the collet chuck according to
the maintenance table.
General safety instructions EN 7
Original Operating Instructions: E4
Version: 4/4/2023
https://stomshop.pro/

Damage caused by unsuitable tools
Recommendation: Only use original tools from vhf.
Use tools only within the maximum tool life shown
in DENTALCNC.
See the requirements in the chapter Technical data.
Impact damage
When working in the working chamber, do not
apply manual pressure against the spindle.
2.5.2 DENTALCAM & DENTALCNC softw are
Machine damage due to incompatibility,
malfunctions and/or incorrect operation of the
software
Always use the latest version of the program that
your machine supports according to vhf.
Ensure that your CAM computer meets all system
requirements.
Before installing or operating the machine, read
the documentation for the applications.
2.5.3 Pow er
Damage to the control electronics due to strong
mains voltage fluctuations and voltage peaks
Connect the machine to a dedicated current circuit
or ensure that no devices are connected that can
cause heavy voltage fluctuation when switched on.
If heavy voltage fluctuations cannot be avoided,
install a surge protector that protects the machine
from heavy voltage fluctuations.
2.5.4 Wet machining
Damage to machine, tools and blanks due to wet
machining without or with unsuitable cooling liquid
Always fill with sufficient cooling liquid that meets
the requirements in the corresponding chapter.
Change the cooling liquid as described in the cor-
responding chapter and in the maintenance table.
If you use a cleaning agent to clean the tank,
ensure that no residues of it remain in the tank.
2.5.5 Air extraction system
Machine damage during dry machining without an
air extraction system
Always use a suitable external air extraction system
during dry machining.
2.5.6 Working chamber
Damage to tools and blanks as well as defective
machining results due to job cancelations
Ensure that all operating parameters are within the
permissible range during the entire machining
process.
Ensure that your network is working without disrup-
tions. WiFi connections are not as reliable as wired
networks.
Machine damage caused by broken tool and blank
parts
Carefully check all blanks and tools for damage.
2.5.7 Working chamber door
Damage caused by improper handling
Only open a locked working chamber door via
emergency release.
Original Operating Instructions:E4
Version: 4/4/2023
General safety instructions
EN 8
https://stomshop.pro/

3 TRANSPORTATION AND
STORAGE
WARNING Injuries caused by unsafe
transportation
If you transport the machine unsafely, the machine
may slip and cause injuries.
Parts that are not properly mounted can fall and injure
you and/or be damaged.
Always transport unpacked machines individually
and do not stack them.
Ensure that only trained personnel transport the
machine to and from the installation site.
Always transport the machine in an upright pos-
ition.
Transport and position the machine with as many
people as required for the weight of the machine in
accordance with local and/ or national laws and
regulations.
Grip unpacked machines only by the left and right
handles at the bottom of the machine. Do not tilt
the machine when carrying it.
NOTICE Machine damage due to improper
transport and/or storage
Ensure that all conditions set forth in the chapter
are met during the entire transport and/or storage
period Technical data.
3.1 Transporting the machine in the
carton
Grasp the carton by the recessed handles.
Always set the package down during transport so
that the arrows on the transport position sticker are
pointing upward.
3.2 Preparing transportation or stor-
age
1. Remove all blanks from the working chamber.
2. If the machine was used for wet machining:
a. Rinse the cooling liquid system.
b. Empty and clean the cooling liquid tank.
Ensure that the tank is completely dry.
3. Clean the working chamber. Ensure that the work-
ing chamber is completely dry.
4. Install the transport lock. For this, follow the cor-
responding steps on the supplement.
5. Ensure that the machine housing is closed as far as
possible. While doing so, do not close the working
chamber door.
6. Switch off the machine at the main power switch.
7. Disassemble the machine components by following
the installation instructions in reverse order.
8. In case of overseas transport, take proper measures
against corrosion.
3.3 Repackaging
To repack the machine after preparing its trans-
portation or storage, the following steps are necessary:
1. If possible, use the original packaging. If the
original packaging is not available, use a packaging
of similar size and quality.
Original packaging is available from customer
service.
2. Pack the machine and its accessories securely. Fol-
low the instructions on the supplement.
3. Protect the packaging against slipping. If machines
are properly packed and protected against slip-
ping, they may be stacked.
3.4 Putting the machine back into
operation after storage
Follow the instructions for initial start-up.
Commissioning – on page26
Transportation and storage EN 9
Original Operating Instructions: E4
Version: 4/4/2023
https://stomshop.pro/

4.1 Unpacking and positioning of
the machine
4.1.1 Choosing the installation site
The installation site must meet the limit values and
requirements in chapter Technical data.
Technical data (page 18)
4.1.2 Unpacking the machine
1. Place the transport carton on a surface that can
carry the weight.
nThe arrows on the transport position sticker
must be pointing upward.
nYou need a free space of at least 60 x 80 x 80
cm / 24 x 32 x 32 in (W/D/H) at the front of
the carton.
2. Cut the carton seal and open the carton.
FIG. 1
FIG. 2
NOTICE! Housing damage by pulling on the
housing
3. The machine stands on a separate insert. Grasp the
insert by the handle and pull the machine out of
the carton.
4. Cut the fastener of the blue transport protection
cover on the front of the machine.
5. Pull the transport protection cover backwards over
the machine and press it down on all sides until the
top of the bottom cushion is exposed.
FIG. 3
FIG. 4
6. Remove the accessory pad from the machine.
7. Remove the upper padding from the machine.
8. Remove the support pad under the working
chamber door.
9. Open the working chamber door.
FIG. 5
Original Operating Instructions:E4
Version: 4/4/2023
Unpacking and positioning of the machine
EN 10
https://stomshop.pro/

FIG. 6
FIG. 7
10. Reach into the left and right recessed grips in the
lower padding.
Slide your hands under the machine until you have
a firm grip on the underside of the machine.
FIG. 8
11. Lift the machine out of the padding.
a. Place the machine on a surface that can carry
the machine weight.
FIG. 9
FIG. 10
b. NOTICE! Ensure that the following safety
distances are always maintained.
Top view
FIG. 11 BLUE AREA: WORKSPACE
Side view
Unpacking and positioning of the machine EN 11
Original Operating Instructions: E4
Version: 4/4/2023
https://stomshop.pro/

FIG. 12
12. Pull the protective housing cover upwards off the
machine.
13. Remove the transport lock from the working
chamber:
a. Push the plastic dowel downwards out of the
transport lock.
b. Pull the lower part of the transport lock out of
the machine.
c. Tilt the upper part down and remove it.
FIG. 13
FIG. 14
FIG. 15
14. Close the working chamber door.
Commissioning is only possible with the working
chamber door closed.
FIG. 16
Original Operating Instructions:E4
Version: 4/4/2023
Unpacking and positioning of the machine
EN 12
https://stomshop.pro/

The working chamber door is locked. You cannot
open it again until after installation.
In case of emergencies: Emergency opening of the
working chamber door – on page82
15. Keep all parts of the transport lock and the packing
set for possible service returns.
FIG. 17
Unpacking and positioning of the machine EN 13
Original Operating Instructions: E4
Version: 4/4/2023
https://stomshop.pro/

5 GETTING TO KNOW
YOUR MACHINE
5.1 Front side of the machine
1. Service cover for access to the machine interior
2. Start button
Start button (
page 15)
3. Working chamber door
Working chamber door – on the facing page
4. View window to the working chamber
5. Recessed grip for opening the working chamber door
6. Cooling liquid tank or dry tank
Cooling liquid tank and dry tank (
page 16)
5.2 Rear side of the machine
1. Connection panel
Connection panel (
page 15)
2. Air extraction interface (6 pins, IEC 61076-2-106)
Installing the air extraction system (
page 22)
3. Hose connection for the air extraction system
Installing the air extraction system (
page 22)
4. Openings for the ventilation of the working chamber
Original Operating Instructions:E4
Version: 4/4/2023
Getting to know your machine
EN 14
https://stomshop.pro/

5.3 Connection panel
1. Main power switch
Commissioning (
page 26)
2. Power connection including glass fuse T6,3A L250V
Establishing the electric connection (
page 24)
Exchanging the main fuse (
page 77)
3. Network port (Ethernet RJ-45)
Connecting the CAM computer (
page 22)
4. 1 x USB port 2.0 Type B (for future extensions)
5. 2 x USB port 2.0 Type A (for future extensions)
5.4 Start button
FIG. 18
The Start button is used to start and interrupt a job.
To press the Start button, place a finger on it.
Do not press.
Starting jobs (page 39)
Interrupt and continue machining (page 39)
5.5 Working chamber door
The working chamber door locks the working chamber
and protects the user from injuries during operation.
You can open and close the working chamber door
manually.
You cannot open the door when the machine is
switched off or while the axes are moving.
5.6 Lever for emergency release of
the w orking chamber door
The lever for the emergency release is located on the
right underside of the machine.
Emergency opening of the working chamber door –
on page82
5.7 Working chamber
You can insert blanks and tools into the working
chamber. This is where the blanks are processed.
1. Spindle with collet chuck for picking up tools
Inserting and exchanging tools (
page 36)
Cleaning or replacing the collet chuck of the spindle
(
page 53)
2. Measuring key
Getting to know your machine EN 15
Original Operating Instructions: E4
Version: 4/4/2023
https://stomshop.pro/

page 46
3. Insert for the AirTool
Inserting and exchanging tools (
page 36)
4. Tool magazine insert
Inserting and exchanging tools (
page 36)
5. Tool magazine
Exchange tool magazine inserts and associated holders
(
page 62)
Loosening a fixed tool magazine (
page 83)
6. Blank holder
Mounting & removing blanks (
page 34)
7. Drain cover for wet machining
Switching between wet and dry machining – on
page31
Colors of the working chamber lighting
Color Status Working cham-
ber door
Green The machine is ready for
operation.
unlocked
White The machine is ready for
operation.
unlocked
Blue The machine is operating. locked
Red A machine malfunction has
occured.
locked
5.8 Cooling liquid tank and dry
tank
Your E4 uses the following interchangeable tanks:
nCooling liquid tank for wet machining
nDry tank for dry machining (extra equipment)
Extra equipment can be obtained from your customer
service provider.
Depending on the machining mode, the required tank
must be located in the compartment below the
working chamber.
Without a dry tank in place, a connected air extraction
system does not generate the required vacuum in the
working chamber.
FIG. 19
1. Compartment for the cooling liquid tank / dry tank
2. Dry tank
Switching from wet to dry machining (
page 31)
3. Cooling liquid tank
Von Trocken- auf Nassbearbeitung wechseln
Filling the cooling liquid (
page 33)
Exchanging the cooling liquid and cleaning the
cooling liquid tank (
page 57)
FIG. 20
Original Operating Instructions:E4
Version: 4/4/2023
Getting to know your machine
EN 16
https://stomshop.pro/

5.9 Axes
This machine has 4 axes: 3 linear axes and 1 rotational
axis.
nLinear axes X, Y, Z
The spindle moves along these axes.
nRotational axis A
The blank holder rotates about this axis.
FIG. 21
5.10 Location of the identification
plate and serial number
The identification plate of the machine contains identi-
fying information such as the serial number. You can
find the identification plate and machine serial number
at the following location:
FIG. 22 SERIAL NUMBER ON THE IDENTIFICATION PLATE (MARKED ORANGE)
Getting to know your machine EN 17
Original Operating Instructions: E4
Version: 4/4/2023
https://stomshop.pro/

5.11 Technical data
Dimensions (W/D/H)
Unit Value
Footprint (approx.) mm
in
260 x 260
10,2 x 10,2
Housing fully closed
(approx.)
mm
in
360x 370x 490
14,2x 14,6x 19,3
Minimum required space for
operation (approx.)
mm
in
560x 620x 530
15 x 25 x 21
Base system
Unit Value
Weight (approx.) kg
lbs
29
64
Axes
– Rotational axis A
4
+190° bis -10°
Overvoltage category
(IEC60664-1)
II
External air extraction system
Unit Value
Minimum extraction capacity l/min
cfm
2.500 (at 220 hPa)
88,3 (at 3.2 psi)
Suction unit Designed for the commercial
use in the dental sector
Equipped with a filter of the
filter class M
Ambient conditions
Unit Value
Relative air moisture 80%, non-condensing
Ambient temperature for stor-
age/transport
°C
°F
-20 – 60
-4 – 140
Ambient temperature for
operation
°C
°F
10 – 35
50 – 95
Location type Indoor
Maximum height above
mean sea level
m
ft
2000
6561
Ambient air (IEC60664-1) Dust free, pollution degree 2
Spindle
Unit Value
Model SFE 300E (synchronous)
Maximum rotational speed rpm 60.000
Nominal power under
continuous operation (S1)
W 300
Nominal power under unin-
terrupted periodic operation
(S6)
W 400
Peak power (Pmax) W 816
Diameter collet chuck mm 3
Tool changer
Unit Value
Maximum tools in magazine 7
Maximum tool length mm 40
Standard blank holder
Unit Value
Maximum block dimensions
(L/D/H)
mm 45x 20x 20
Cooling liquid system
Unit Value
Cooling liquid Drinking water
Maximum tank capacity l
qt
1,45
1,5
Sound emission
Operating condition Unit Value
Processing dB(A) 74,55
All other operating condi-
tions
dB(A) <70
Measuring conditions Value
Machined material Composite (VITA CAD temp block)
Condition of the tools worn
Measured value Sound pressure level (distance:1m)
Measurement according to ISO 3746, survey method 3
Connections
Unit Value
Power connection
(and maximum power
consumption in watts)
VAC
Hz
W
100 – 240
50/60
500
Glass fuseT6,3A L250V
Network port
– Speed
RJ-45
10BASE/100BASE-
TX/1000BASE-T (Auto-
sensing)
USB port 2x 2.0 A
1x 2.0 B
Original Operating Instructions:E4
Version: 4/4/2023
Getting to know your machine
EN 18
https://stomshop.pro/

6.1 Checking the scope of delivery
Unpack the machine and ensure that you have
received the following items:
1234
5678
9 10 11 12
13 14 15 16
17 18 19 20
21 22 23 24
25 26
1. 1x Machine E4
2. 1x Cooling liquid tank
3. 1x Drain insert
4. 1x Ethernet network cable
5. 1x Power cable
6. 1x Torque screwdriver 1.5Nm
7. 1x TX10 bit for mounting blanks
8. 1x TX20 bit for the tool magazine
9. 2x Angle screwdriver
n1x TX10
n1x TX25
10. 1x 10mm wrench
11. 1x Spindle service set
12. 1x Calibration set:
n1x Micrometer
n5x Calibration blank
n1 x AirTool P250-F1-40-T
13. 1x Cleaning brush for the blank holder
14. 1x Microfiber cloth
15. 1 x Drill bit for tool positions (2.8 mm)
16. 1x 5.5mm wrench to remove a broken tool
17. 1x Interdental brushfor cleaning the nozzle plate
18. 3x Bags of Tec Powder for cleaning the cooling liquid
system (50 g per bag)
19. 1x M4 cylinder screw for loosening a stuck tool magazine
20. 1x Cleaning brush for cleaning the cooling liquid tank
21. 2x Insert for the AirTool
22. 2x Tool magazine insert
23. 2 x Grub screw (M5 x 10) for the blank holder
24. 1 x Cover cap for the tool magazine
25. 1 x Foam filter for the cooling liquid tank
26. 4 x Fastening element for the side panel
Not depicted:
nTransport lock
2x Foam insert
1 x Plastic dowel
Original Operating Instructions:E4
Version: 4/4/2023
Installation
EN 20
https://stomshop.pro/
Table of contents
Popular Power Tools manuals by other brands
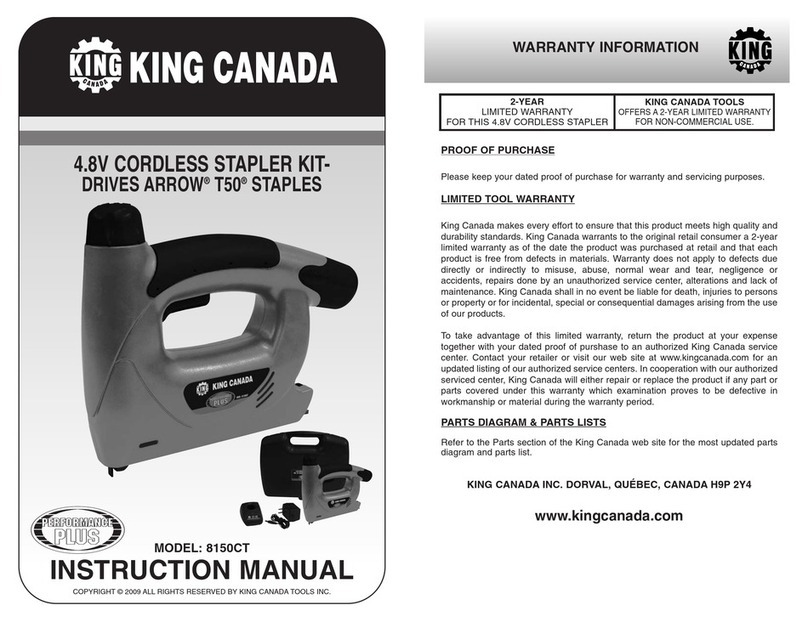
King Canada
King Canada 8150CT instruction manual
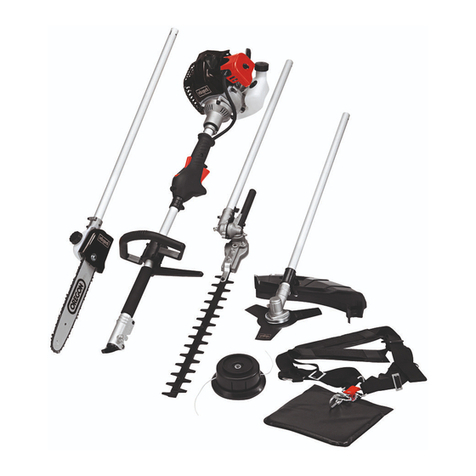
Scheppach
Scheppach ZGONIC Yellow Garden Line NEW GENERATION... instruction manual

RED ROOSTER
RED ROOSTER RRI-BA90S4 manual
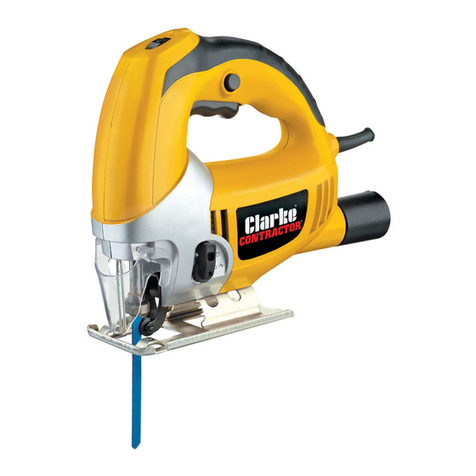
Clarke
Clarke Contractor CON750 Operation & maintenance instructions
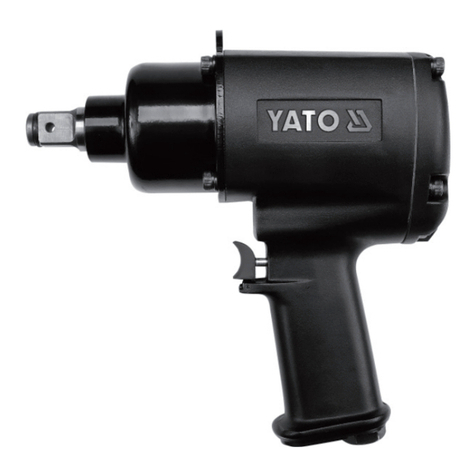
YATO
YATO YT-09564 Original instructions
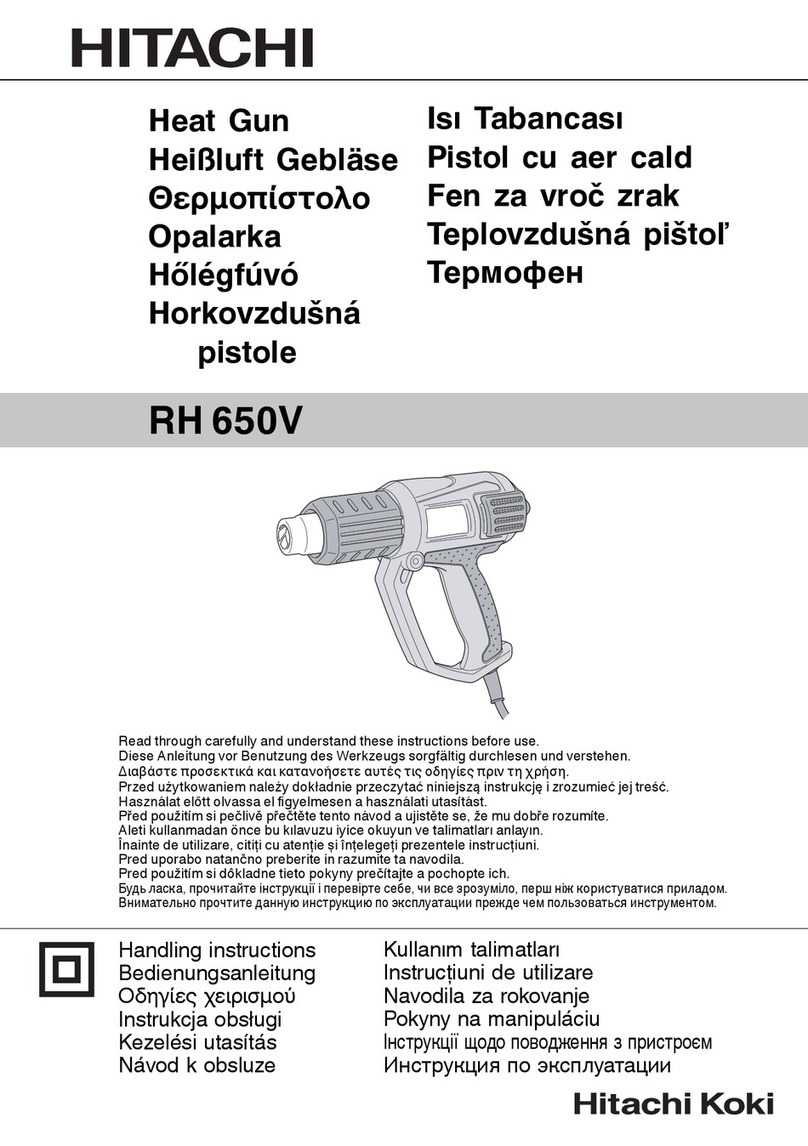
Hitachi
Hitachi RH 650V Handling instructions