VICI ITC2 User manual

Valco Instruments Co. Inc.
6/20
Instrumentation
Temperature Controller
Instruction Manual
Model ITC2
Valco Instruments Co. Inc.
800 · 367· 8424 sales
713 · 688· 9345 tech
713 · 688· 8106 fax
VICI AG International
Schenkon, Switzerland
Int + 41 · 41 · 925· 6200 phone
Int + 41 · 41 · 925· 6201 fax
North America, South America, and Australia/Oceania contact: Europe, Asia, and Africa contact::

General Safety Requirements
Do not open the controller enclosure. There are no user-serviceable parts
inside, and you may cause a dangerous failure.
Do not replace the power entry module fuses with anything but 5 x 20 mm
250V 5A FAST BLOW fuses.
Do not make physical or electrical contact with the heater assembly
controlled by the ITC2 before disconnecting the ITC2 from its power source
and allowing adequate time for the heater to cool. The time required will
vary, depending on the heater mass.
Make sure that the heater voltage rating matches the power input voltage
rating of the power into which the ITC2 is connected
To prevent temperature runaways on new installations, after power up,
watch to see that the measured temperature begins to show a positive
movement upward. (This may take slightly longer for a large heated
mass.) If there is no increase, shut down everything and check the system
for correct thermocouple polarity.

Table of Contents
Description ................................................................................................................................................... 1
Setup and Operation ................................................................................................................................ 2
Connections ........................................................................................................................................ 2
Adjusting the Temperature Setpoint ......................................................................................... 2
Verifying Thermocouple Polarity
Running Autotune ...............................................................................................................................
Initiating the Autotune Sequence: Fast Mode ........................................................... 2
Initiating the Autotune Sequence: Full Mode ............................................................ 3
When to Repeat Autotune............................................................................................................. 3
Specifications............................................................................................................................................... 4
Troubleshooting......................................................................................................................................... 4
Appendix A: Operation Terms and Principles................................................................................... 5
Warranty ....................................................................................................................................................... 6

This page intentionally left blank for printing purposes

1
Description
The ITC2 is designed to control an isothermal zone,such as a Valco heated valve enclosure
(HVE), to a high degree of accuracy and stability through the use of a type K thermocou-
ple. The thermocouple was chosen because of its low mass, simplicity, and quick response
to temperature changes. It also employs a solid state zero crossing high current relay to
keep electromagnetic noise and heat generation to an absolute minimum.
Temperature sensing is provided through a 15-bit analog-to-digital converter. The
controller utilizes a PID* algorithm for configuring the best scheme according to the
mass, power applied, and heat loss.
*For more on PID, refer to “Appendix A: Operation Terms and Principles” on page 5.
For proper functioning, the input voltage will determine the output
power. That is, if you are supplying 120VAC at the input, you must
use a 120VAC heater rated at 600 watts maximum; 240VAC at the
input requires a 240VAC heater rated at 1100 watts maximum
Figure 1: ITC2 front panel
DISPLAY
Figure 2: ITC2 rear panel
TYPE K
THERMOCOUPLE
INPUT
2 POLE
FUSE HOLDER
POWER ON/OFF
SWITCH
MAIN POWER
INPUT
(POWER OUTPUT
(FOR HEATER
(1100W @ 240 VAC,
(600W @ 110 VAC)
PROGRAMMING
KEYS

2
Setup and Operation
Connections
1. Connect the thermocouple and heater power cord to the ITC2 rear panel.
NOTE: Take care to verify the polarity of the thermocouple input, as described below.
2. Plug the power cord into the ITC2 and into a properly grounded outlet
3. Turn the power switch to“On”.
On initial power up, the controller will go through a boot sequence in which the ther-
mocouple is checked for proper connection. If the red temperature display shows“
nnnn
”,
the thermocouple is not connected properly. Turn the power off and fix the connection
before proceeding.
When a proper connection is detected, the controller starts controlling at the setpoint
indicated in the green LED readout. The ITC2 leaves the factory with a setpoint of 20.0,
so there will probably be no power applied to the heater until the setpoint is increased.
Adjusting the Temperature Setpoint
Use the up and down arrows on the controller (Figure 3) to select the desired
temperature setpoint.
Verifying Thermocouple Polarity
To verify the correct polarity of the thermocouple input, increase the set point and verify
that the temperature increases. If the temperature in the readout is decreasing, the
thermocouple is not polarized correctly. Correct before proceeding.
Running Autotune
As mentioned previously, the controller utilizes a PID algorithm for configuring the best
scheme according to the mass, power applied, and heat loss. We recommend using the
autotune feature to establish these values. To learn more, refer to “Appendix A: Operation
Terms and Principles” on page 6. All other functions of the controller have been factory set
for optimum performance; it is recommended that these settings remain unchanged.
Autotune has two modes: Fast, for the shortest execution time, and Full, for maximum
temperature stability.
Initiating the Autotune Sequence: Fast Mode
1. Press hold the P key for five seconds. “
Atun
”will appear in the upper red LED and “
oFF
”
will appear in the lower green LED
2. Momentarily press the down arrow. When “
FASt
”appears in the lower green LED, press
the P key again to select the fast mode.
3. Press the P key eight times. At this point, the TUNE LED illuminates, the setpoint and
actual temperatures are displayed, and the fast autotune sequence begins.
4. Use the up and down arrows on the controller (Figure 3) to adust the temperature
setpoint to the desired reading. This can be done before the autotune sequence is
completed.

3
Initiating the Autotune Sequence: Full Mode
1. Press hold the P key for five seconds. “
Atun
”will appear in the upper red LED and “
oFF
”
will appear in the lower green LED
2. Momentarily press the down arrow. When “
FASt
”appears in the lower green LED, press
the down arrow again to show“
FULL
”. Press the P key again to select the full mode.
3. Press the P key eight times. At this point, the TUNE LED illuminates and the setpoint
and actual temperatures are displayed.
4. Use the up and down arrows on the controller (Figure 3) to adust the temperature
setpoint to the desired reading.
The ITC2 will now execute a full autotune. This can take from 10 to 60 minutes,
depending on the zone conditions.
During a full autotune, the controller will overshoot the set point
several times, by as much as 40°C. If there are any components in
the heated zone that might be damaged by this, set the temperature
40°C lower than the nal setpoint. When the TUNE LED goes out,
indicating that the autotune procedure is completed, set the
temperature as desired
5. Allow an additional 15 minutes for further temperature stabilization of the heated
zone.
When to Repeat Autotune
Autotune should be repeated any time there are physical changes to the heated zone or
if there is a large change in the set point temperature.
Figure 3: ITC2 controls and display
ACTUAL
TEMPERATURE
TEMPERATURE
SETPOINT
AUTOTUNE
INDICATOR
OUTPUT
INDICATOR
PROGRAMMING
KEYS
UP AND DOWN ARROWS

4
Specifications
Power supply 100 to 240 VAC (±10%), 50/60Hz
Maximum consumption 5 amps
Environmental conditions
Operation temperature 0 - 50°C
Relative humidity 80% @ 30°C*
Input
Input type Type K thermocouple
Internal resolution 32767 (15 bits)
Resolution of display 0.1 Celsius
Control Range -20 to 400 Celsius
Rate of reading up to 5 / second
Accuracy ± 0.25% of span ± 1 degree
Output 5 amps max, 100-240 VAC
*For temperatures above 30 Celsius, reduce 3% for each degree.
Troubleshooting
Symptom Cause
Red temperature display shows “nnnn”Faulty thermocouple connection
No LEDs are lit Fuse is blown

5
Appendix A: Operation Terms and Principles
P (band)
Pb
“P” (band) is the proportion term – the primary term for controlling the error, or deviation
from the temperature set point. This setting directly scales the error, so with a small “P”
the controller will make small attempts to minimize the error, and with a large“P” the
controller will make larger attempts. If “P”is too small the error may never be minimized,
and the unit may not be able to respond to changes affecting the zone. If “P” is too large,
unstable oscillations can occur, resulting in a severe overshoot of the desired temperature.
I(rate)
Ir
“I”(rate) is the integral term that allows the controller to handle errors that accumulate
over time. This works well for handling steady state errors. If ” I”is too high there can be
instability in response to short term changes.
D(time)
dt
“D” (time) is the derivative term, concerned with how the system is responding between
intervals. This helps dampen the system, improving stability.
The autotune feature has 3 options: OFF, FAST, and FULL. If the OFF option is selected the
P, I, and D values may be set manually. Consult the factory for more information.

6
Warranty
This Limited Warranty gives the Buyer specific legal rights, and a Buyer may also have
other rights that vary from state to state. For a period of 365 calendar days from the date
of shipment,Valco Instruments Company, Inc. (hereinafter Seller) warrants the goods to
be free from defect in material and workmanship to the original purchaser. During the
warranty period, Seller agrees to repair or replace defective and/or nonconforming goods
or parts without charge for material or labor OR at seller’s option demand return of the
goods and tender repayment of the price. Buyer’s exclusive remedy is repair or replace-
ment of defective and nonconforming goods OR at Seller’s option repayment of the
price. SELLER EXCLUDES AND DISCLAIMS ANY LIABILITY FOR LOST PROFITS, PERSONAL
INJURY, INTERRUPTION OF SERVICE, OR FOR CONSEQUENTIAL INCIDENTAL OR SPECIAL
DAMAGES ARISING OUT OF, RESULTING FROM, OR RELATING IN ANY MANNER TO THESE
GOODS.The Limited Warranty does not cover defects, damage or nonconformity resulting
from abuse, misuse, neglect, lack of reasonable care, modification or the attachment of
improper devices to the goods.This Limited Warranty does not cover expendable items.
This warranty is VOID when repairs are performed by a nonauthorized service center or
representative. If you have any problem locating an authorized service center or represen-
tative, please call or write Customer Repairs, (713) 688-9345, Valco Instruments Company,
Inc., P.O. Box 55603, Houston,Texas 77255. At Seller’s option, repairs or replacements will
be made on site or at the factory. If repairs or replacements are to be made at the fac-
tory, Buyer shall return the goods prepaid and bear all the risks of loss until delivered to
the factory. If Seller returns the goods, they will be delivered prepaid and Seller will bear
all risks of loss until delivery to Buyer. Buyer and Seller agree that this Limited Warranty
shall be governed by and construed in accordance with the laws of the State of Texas.THE
WARRANTIES CONTAINED IN THIS AGREEMENT ARE IN LIEU OF ALL OTHER WARRANTIES
EXPRESSED OR IMPLIED, INCLUDING THE WARRANTIES OF MERCHANTABILITY AND FIT-
NESS FOR A PARTICULAR PURPOSE.This Limited Warranty supersedes all prior proposals
or representations oral or written and constitutes the entire understanding regarding the
warranties made by the Seller to Buyer.This Limited Warranty may not be expanded or
modified except in writing signed by the parties hereto.
Table of contents
Popular Temperature Controllers manuals by other brands

United Electric Controls
United Electric Controls 100 Series Installation and maintenance instructions
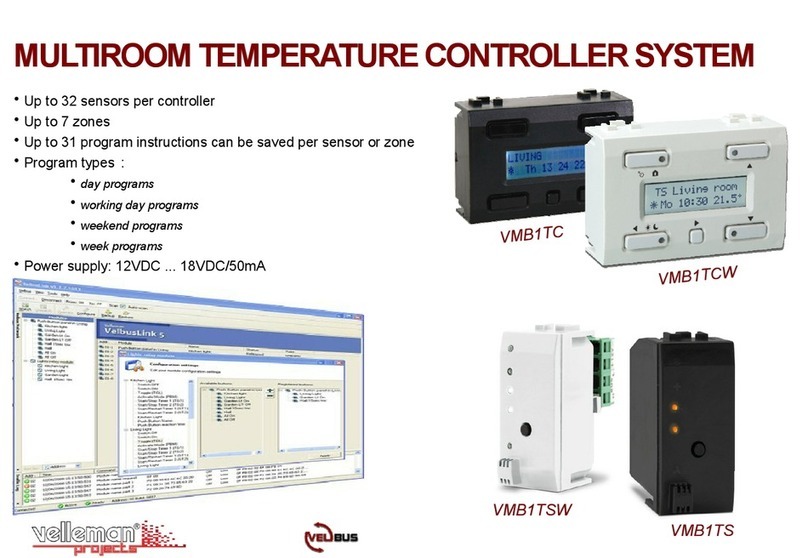
Velleman
Velleman VELBUS VMB1TSW manual

Danfoss
Danfoss 103E7 Installation & user's instructions
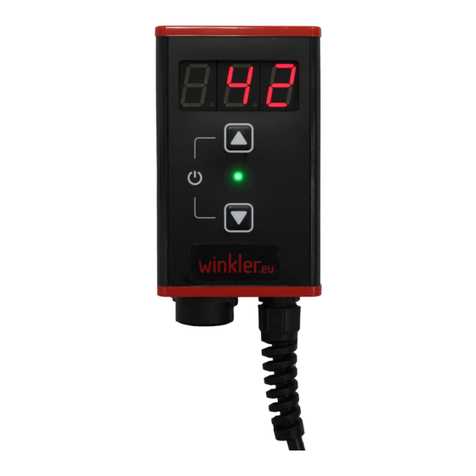
winkler
winkler L-400 Series Operation manual
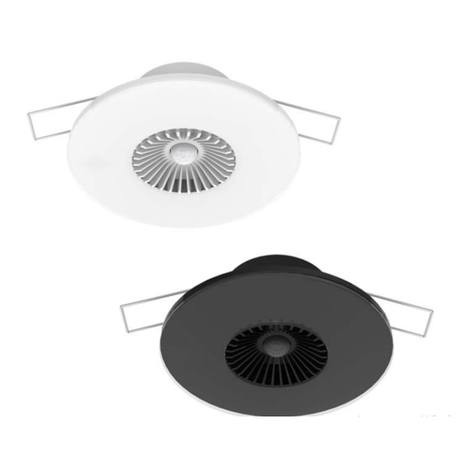
KNX
KNX 70662 Installation and adjustment
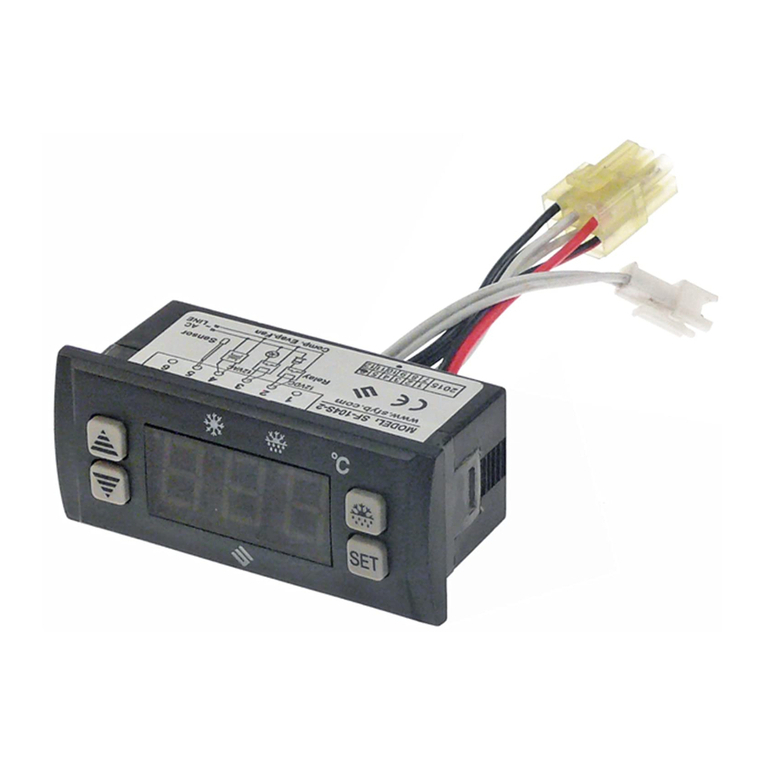
Shangfang
Shangfang SF-104S-2 quick guide
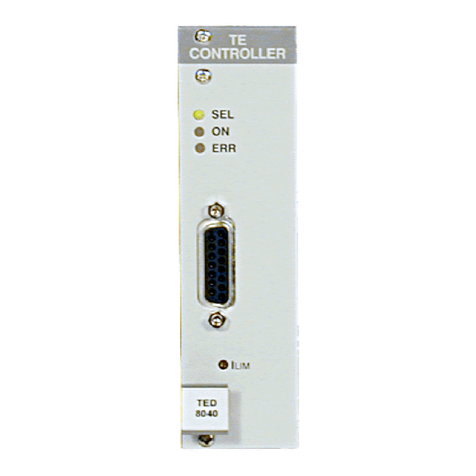
THORLABS
THORLABS TED8 Series Operation manual
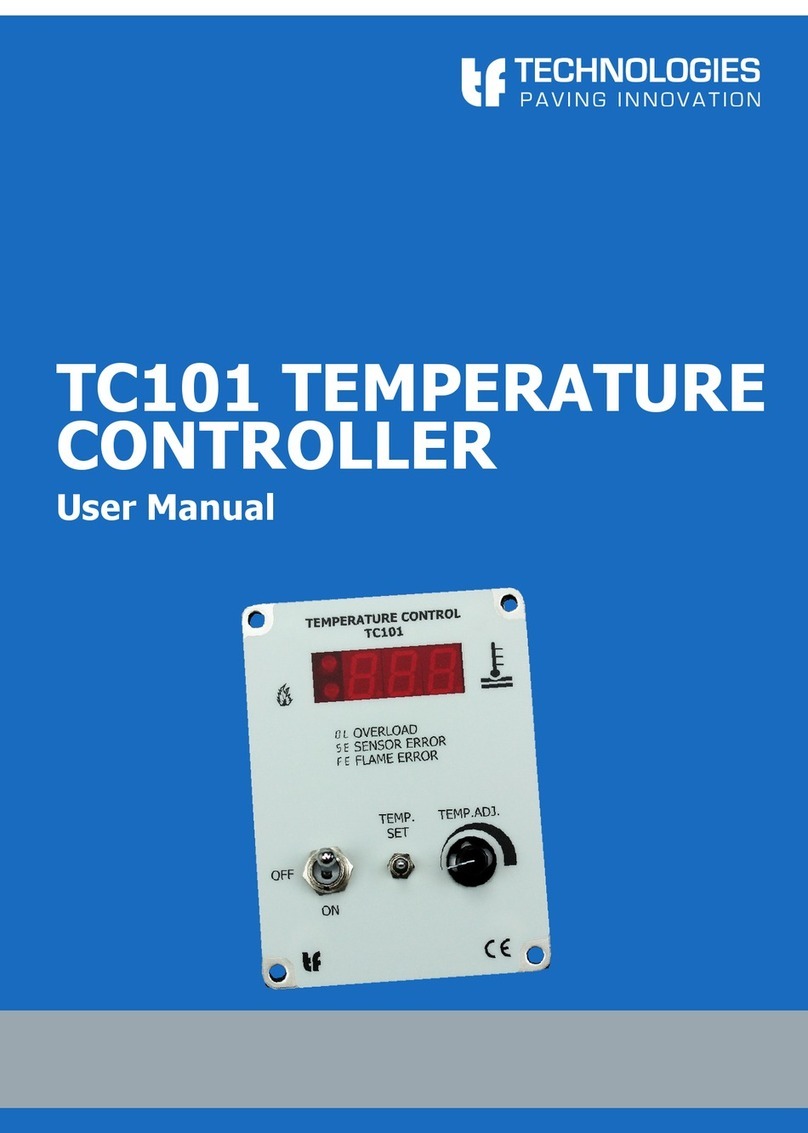
Technologies Paving Innovation
Technologies Paving Innovation TC101 user manual
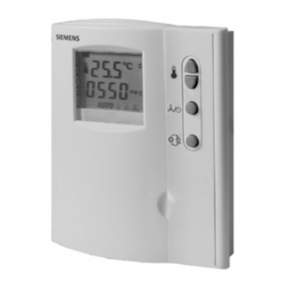
Siemens
Siemens RDF210 manual

Stanford Research Systems
Stanford Research Systems PTC10 user manual
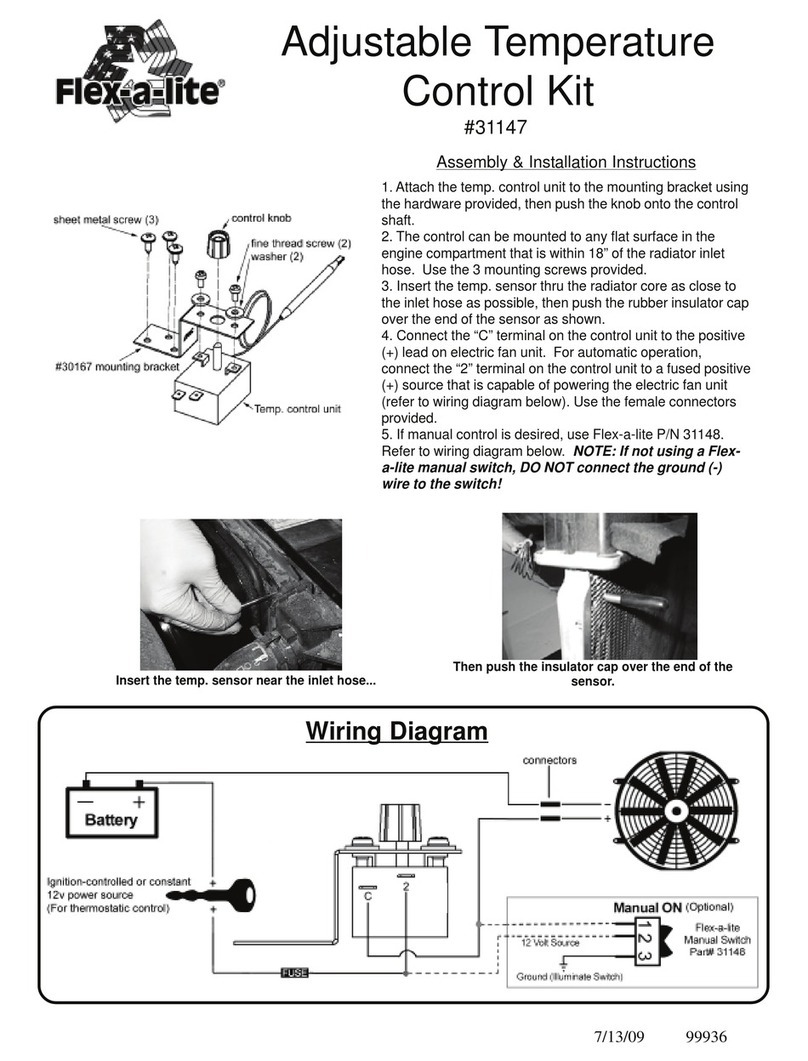
Flex-a-Lite
Flex-a-Lite 31147 installation instructions
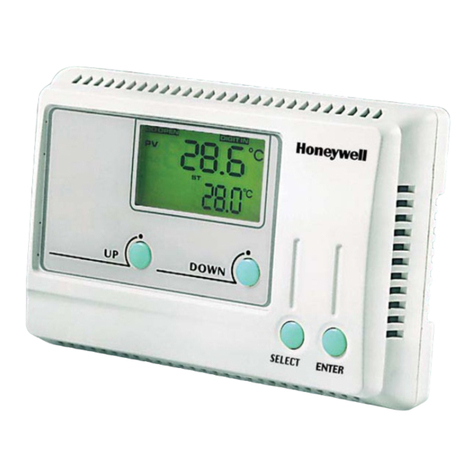
Honeywell
Honeywell Smartronic70 T9275A1002 user manual