View Benchmark 450 User manual

VIEW Engineering, Inc.
Benchmark™ 450
Installation Manual


VIEW Engineering, Inc.
Benchmark™ 450
Installation Manual
Copyright © 2008 VIEW Engineering, Inc., a Quality Vision International
company.
All rights reserved. Printed in the U.S.A.

Part No. 799034, Revision A, 10/08
Information in this document is subject to change without notice and
does not represent a commitment on the part of VIEW Engineering, Inc.
Benchmark, VIEW, and the Benchmark and VIEW logos are trademarks
of VIEW Engineering, Inc. All other trademarks mentioned in this
manual are property of their respective owners.
Benchmark equipment is made in the U.S.A.

Installation Manual 799034, Revision A, 10/08 Pagei
Table of Contents
Important System Labels iii
1 About This Manual 1
1.1 What This Chapter Contains 1
1.2 Who Should Read This Manual 1
1.3 Required Knowledge 1
1.4 What’s In this Manual? 2
1.5 Where to Get Help 2
2 System Overview 3
2.1 What This Chapter Contains 3
2.2 What Is the Benchmark 450 System? 3
2.3 System Components 4
2.4 How the System Operates 5
3 Safety Information 7
3.1 What This Chapter Contains 7
3.2 Emergency Stops 7
3.3 System Status LEDs 8
3.4 System Power 9
3.5 System Lockout 10
3.6 Safety Guidelines 11
4 Installation 13
4.1 What This Chapter Contains 13
4.2 Choosing an Installation Site 14
4.3 Benchmark 450 System Layout 15
4.4 Unpacking the Machine 16
4.5 Removing the X, Y, and Z Restraints 19
4.6 Connecting the System 22
4.7 Installing the Stage Glass 24
4.8 Leveling the Stage Glass 25

Installation Manual 799034, Revision A, 10/08 Pageiii
Important System Labels
Label: Location: Definition:
Around the remote E-
Stop
Around the E-Stop on
the front of the machine
(Yellow ring
around red
switch)
Emergency stop
Left and right sides of
the Front Cover Pinch hazard
Rear panel of the
electronics enclosure,
lower-left corner
Dangerous
voltagepresent;
disconnect
power before
servicing to
avoid electrical
shock
Right side of the
electronics enclosure,
above the power cord
receptacle
Fuse label
Lower-left corner of
Main System ID label System meets
the
requirements of
the European
Union (EU)

Page iv 799034, Revision A, 10/08 Benchmark450
Front surface of the
base, upper-right corner System model
and serial
number
Rear panel of the
electronics enclosure,
lower-left corner
Main system ID
Right side of the laser
(if equipped) International
laser symbol
Right side of the laser
(if equipped) Indicates that
the laser meets
Class 2
requirements of
the IEC-825
European
standard
Right side of the laser
(if equipped) Indicates that
the laser meets
Class II
requirements of
the CFR 21
standard
Right side of the laser
(if equipped) Identifies the
laser emitting
aperture
Label: Location: Definition:

Installation Manual 799034, Revision A, 10/08 Page1
Chapter
About This Manual
1.1 What This Chapter Contains
This chapter covers the following:
• Who should read this manual
• What knowledge you must possess in order to use this manual
• What this manual contains
• Where to get help
1.2 Who Should Read This Manual
Read this manual if you will perform any of the following tasks on the Benchmark
450 system:
• Unpacking
• Installation
• Power up
• Shut down
• Operation
For information about using the metrology software, refer to the VMS Fast Start
Guide (P/N 790438) or VMS Reference Guide (P/N 790411).
1.3 Required Knowledge
To use this manual, you should be familiar with:
• Fundamental computing concepts
• Non-contact measurement concepts
1
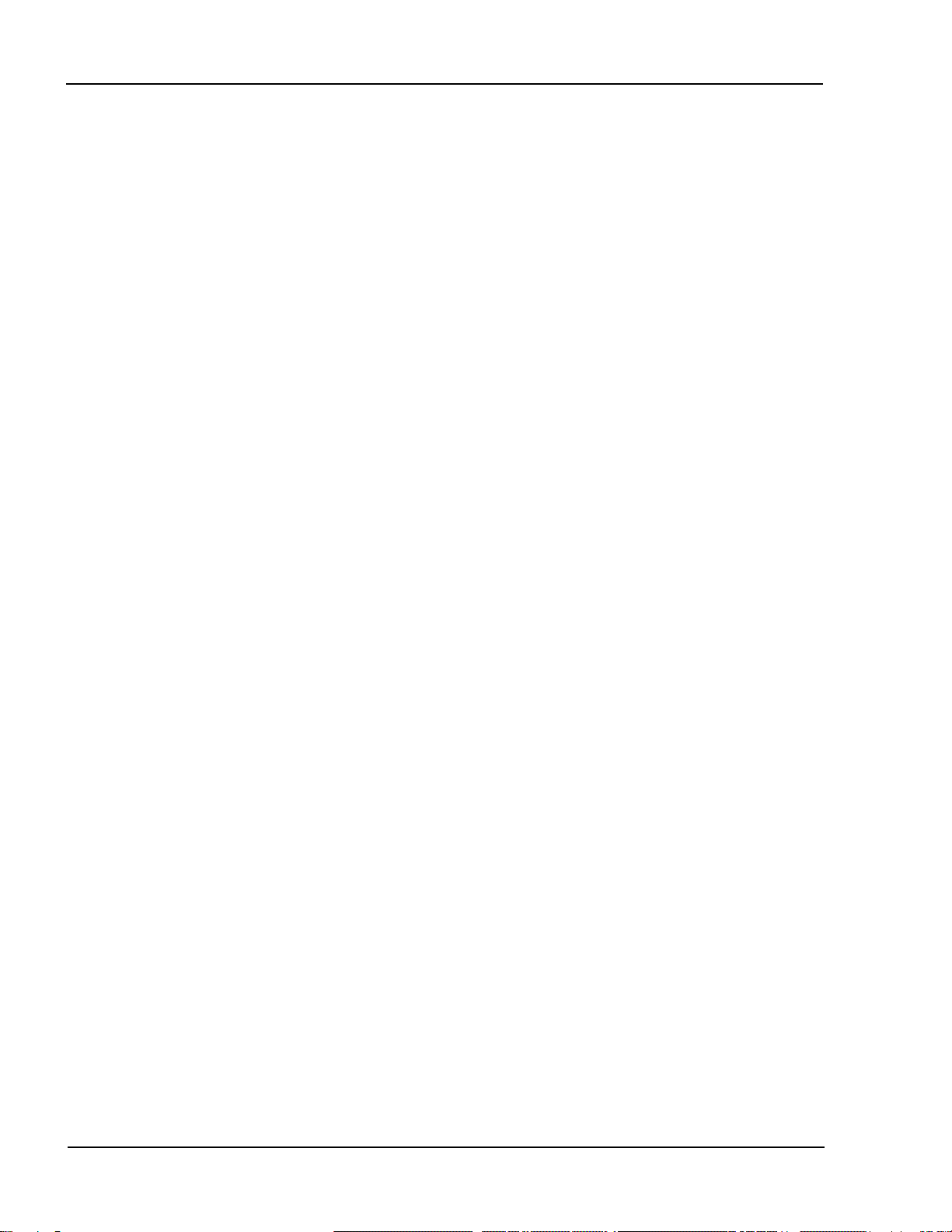
Chapter 1 About This Manual
Page 2 799034, Revision A, 10/08 Benchmark450
1.4 What’s In this Manual?
This manual will help you unpack, install, set up, and power up the Benchmark
450 video metrology system. Important safety information is also included.
1.5 Where to Get Help
If you need help, contact the Customer Support HelpDesk, at:
Be ready to provide the following information when contacting us:
• Model and serial number of your system
• Nature of the problem
• Steps you have taken
• Your phone and fax numbers
• Case number if you are calling about an issue that has already been reported
VIEW Engineering, Inc.
1650 N. Voyager Avenue
Simi Valley, CA 93063, USA
Phone: 805-578-5000
Toll free: 877-SOS-VIEW
(877-767-8439)
Fax: 805-578-5092
E-mail: [email protected]
Website: www.vieweng.com

Installation Manual 799034, Revision A, 10/08 Page3
Chapter
System Overview
2.1 What This Chapter Contains
This chapter covers the following:
• What Is the Benchmark 450 System?
• System Components
• How the System Operates
2.2 What Is the Benchmark 450 System?
The Benchmark 450 is a high-accuracy, non-contact, dimensional measurement
system. In Quality Assurance applications, Benchmark 450 moves dimensional
inspection out of the lab and onto the production floor. Benchmark 450 is fully
automatic and can run part inspection programs, collect data, print results, and
send the results to a Statistical Process Control (SPC) program without any manual
intervention.
Based on the Windows® XP operating system, the Benchmark 450 system comes
with the VMS metrology software, which provides an easy-to-use graphical user
interface and a full range of dimensional measurement tools.
The Benchmark 450 system has precision dual magnification optics, co-axial and
backlight illumination, and patented autofocus circuitry for high-accuracy Z-axis
measurements over a variety of surface textures, finishes, and colors. The patented
LED Programmable Ring Light (PRL) is optional.
Note: See the VIEW Benchmark 450 Technical Data Sheet (part number 799003)
for more technical information.
2

Chapter 2 System Overview
Page 4 799034, Revision A, 10/08 Benchmark450
2.3 System Components
Figure 2-1 Benchmark 450 System Components
Caution: Do not store items inside the base of the machine, which could result in
X motion problems if the items interfere with the IGUS track inside the base.
System
Computer
Flat Panel
Display
Joystick
Worktable (stage
glass & stage)
Front
Cover
E-Stop
Remote E-
Stop
Base

System Overview Chapter 2
Installation Manual 799034, Revision A, 10/08 Page5
2.4 How the System Operates
Based on the Windows XP operating system, the Benchmark 450 system comes
installed with its own proprietary application software, image processing
hardware, an easy-to-use graphical user interface, and a full range of dimensional
measurement tools. The following describes a typical processing operation.
Figure 2-2 Benchmark 450 Operation
Select and load a part inspection program from within the metrology software.
Place the part(s) to be measured on a mechanical fixture located on the measuring stage.
Start the part inspection program. The measurement stage locates the first feature to be
measured under the CCD camera and optics, controlled by the metrology software.
The X, Y, and Z position of the stage is read from the corresponding axis measuring scales.
The image is analyzed by the image processing subsystem, and the results of the
measurement are sent to a printer or file.
The system runs automatically until all the features called out by the part program are
measured and the program stops.
Data collected during the program run can be sent directly to the printer, sent to a
Statistical Process Control (SPC) program for further analysis, or put onto a computer
network for use by a remote application program such as Microsoft Excel.
Unload the part(s) and load a new part for inspection. Frequently, a multiple-part inspection
fixture is built so many parts can be inspected without having to stop and reload after each one.

Chapter 2 System Overview
Page 6 799034, Revision A, 10/08 Benchmark450
This page has been left intentionally blank.

Installation Manual 799034, Revision A, 10/08 Page7
Chapter
Safety Information
3.1 What This Chapter Contains
This chapter covers the following:
• Emergency Stops
• System Status LEDs
• System Power
• System Lockout
• Safety Guidelines
Also, be sure to review the information about Important System Labels on page iii.
3.2 Emergency Stops
Activate the emergency off (EMO) circuit by pressing the remote E-Stop on the
workstation (see Figure 3-1) or the E-Stop on the front of the machine.
Figure 3-1 Remote E-Stop
The EMO circuit is responsible for disabling system motion in case of an
emergency. The EMO circuit places the system in a safe (shutdown) condition,
which cuts power to the motors.
3

Chapter 3 Safety Information
Page 8 799034, Revision A, 10/08 Benchmark450
3.3 System Status LEDs
The system status LEDs are located on the right-hand side of the Z-axis cover.
• The top LED is (yellow) is the Stop LED
• The middle LED (green) is the Power On
LED
• The bottom LED (blue) is the Laser
Indicator LED (only present is if system is
equipped with a laser).
The following table includes information
regarding the status of the Stop LED and
provides instructions for recovering from
different Stop conditions.
StopLED
Status Description Cause How to Recover
Off System is in
normal
operation
——
On Recoverable
stop Occurs during the
normal power-up
sequence until the
Stop/Start button onthe
joystick is pressed
When prompted, press
theStop/Start buttonon
the joystick.
Occurs when the X, Y,
or Z transport
encounters an end-of-
travel limit
Move the transport off of
the limit, and then press
theStop/Start buttonon
the joystick
Occurs when servo
parameter settings are
incorrect
Check LED DS7 on the
DSP Multi Axis PCBA
for the source of the E-
Stop.
Occurs when the
remote E-Stop is
pressed
Reset the remote E-Stop
switch by twisting the
knob in the direction of
the arrows, and then
press the Stop/Start
button on the joystick.
SystemStatus
LEDs

Safety Information Chapter 3
Installation Manual 799034, Revision A, 10/08 Page9
3.4 System Power
The system comes with an IEC power strip (P/N 037545) and three identical
power cords (P/N 019978) that connect the monitor, system computer, and
machine to the power strip. An external power cord connects the power strip to the
external power source (outlet). External power cord characteristics vary depending
on the country of installation, as outlined in the table below.
The main power fuse is located in the fuse holder that is part of the machine power
cord receptacle assembly. A fuse label indicating the type of fuse installed in the
fuse cartridge is located near the fuse holder.
• Systems configured for 100/120 volt operation have one 10 Amp, 250 Volt,
Slo Blo fuse
• Systems configured for 200/240 volt operation have two 6.3 Amp, 250 Volt,
Slo Blo fuses
Warning: Always use the IEC power strip and the external power cords provided
with the system. Use of an inappropriate power connection could lead to
equipment damage and/or electrical shock.
Country Power Part
Number Type AWG
(US) Wire Cross
Section (CE)
United
States 120 VAC, 50/60 Hz 019938 3-Conductor 18 0.82 mm2
Japan 100 VAC, 50 Hz 019938 3-Conductor 18 0.82 mm2
United
Kingdom 240 VAC, 50 HZ 019971 3-Conductor 18 1.00 mm2
Italy 220 VAC, 50 HZ 019972 3-Conductor 18 1.00 mm2
Denmark 220 VAC, 50 HZ 019974 3-Conductor 18 1.00 mm2
Switzerland 220 VAC, 50 HZ 019975 3-Conductor 18 1.00 mm2
Other
European
Countries
220 VAC, 50 HZ 019973 3-Conductor 18 1.00 mm2

Chapter 3 Safety Information
Page 10 799034, Revision A, 10/08 Benchmark450
3.5 System Lockout
Before servicing the system, you must unplug the power cord and lock out the
system. This will protect you and others from unintended machine operation,
which could result in personal injury. No one should attempt to defeat a lockout
while the machine is being serviced.
Most companies have a safety department and written procedures for locking out
the system. These procedures typically have the following features as a minimum:
• Each operator, supervisor, and maintenance person who may be required to
work on the machine shall have a key operable lock.
• If more than one key exists for the lock, the owner of the lock shall have
possession of all of the keys.
• Each lock shall be labeled with the owner’s name, or the owner shall be
supplied with an identity tag that may be attached to the lock when it is
applied to the machine.
To lock out the system:
1. Close all programs and shut down Windows.
2. Power down the monitor.
3. Press the remote E-Stop.
4. Unplug the main power cord from the power source and lock the plug into an
appropriate energy isolating device.
5. Perform the required service and/or maintenance.
To resume normal operation:
1. After determining it is safe, have each person remove his or her own lock.
2. When all locks are removed, reconnect the power cord to the main power
source.
3. Reset the remote E-Stop by twisting the knob in the direction of the arrows.
4. Power up the system and resume normal operation.
Note: Each person performing maintenance or making adjustments to the system
should have their own lock attached to the energy isolating device. There are
commercially available multi-lock devices to allow this.

Safety Information Chapter 3
Installation Manual 799034, Revision A, 10/08 Page11
3.6 Safety Guidelines
For your personal safety, observe the following safety precautions and guidelines.
They are provided for your protection and to help prevent damage to the system.
General Precautions:
• The system is intended to be used by personnel who recognize the hazards
associated with electrical shock and computer-controlled mechanical motion.
• The system is intended to be used for metrology applications only; other use
may void your warranty.
• To prevent the accidental pinching of your hands, do not approach or touch
the machine during operation.
• To avoid personal injury, never attempt to manually move the Z-axis slide
with power applied to the machine.
• To avoid personal injury, always mount the part(s) you are measuring or
inspecting in a fixture that is secured to the worktable.
• Always power down and lock out the system before servicing it.
Power and Grounding:
• Ensure that the source of power connected to the system does not apply more
than the rated voltage (specified by VIEW Engineering, Inc.) between the
supply conductors or between either supply conductor and ground.
• The system is grounded through the power cord. To avoid electrical shock,
connect the power cord to a properly wired receptacle with an earth ground
connection.
• Connect the system to a dedicated circuit.
Power Cord:
• Only use the power cord and connector specified for the system.
• Do not operate the system if the power cord is damaged.
• Position the power cord so it will not be a trip hazard, or come in contact with
a hot surface.

Chapter 3 Safety Information
Page 12 799034, Revision A, 10/08 Benchmark450
Miscellaneous:
• To avoid a fire hazard, only use fuses that meet all type, voltage, and current
requirements specified by VIEW Engineering, Inc.
• Do not operate the system without all covers and panels installed properly.
• Keep water and other liquids away from the system to reduce the risk of
spillage and electrical shock.
• Do not use any accessory attachments other than those provided or approved
by VIEW Engineering, Inc. Improper accessories can cause fire, electrical
shock, and/or personal injury.
• Do not drop anything on the stage glass.
Unsafe Operating Environments:
• Do not operate the system in hospitals, clinics, or laboratories where sensitive
patient monitoring equipment may be affected.
• Do not operate the system in a radioactive environment because the
electronics in the machine are not radiation-hardened.
• Do not operate the system in environments where flammable gases and
vapors or explosive dust are present. These could be ignited by the heat or
sparks that may be generated by the system.
Other manuals for Benchmark 450
1
Table of contents
Other View Measuring Instrument manuals