Virtec Instruments pFLOW E5 Series User manual

Update
Record
Revision 3.0.1
Date 05 .2020
Instruction Manual - Model: E5
Ultrasonic Energy Meter

E5 Series Ultrasonic Energy Meter
Revision: 3.0.1 Page 2 of 60
Notice:
This instruction manual is appropriate for E5 series ultrasonic Energy Meter.
This ultrasonic Energy Meter adopts ARM.FPGA chip and low-voltage wide-pulse sending technology.
This instruction manual contains important information. Please read carefully before the operation of the Energy
Meter,avoiding damaging Energy Meter and improper use.
This instruction manual will introduce how to use the Energy Meter step-by-step, including product component,
installation, wiring, quick setup etc. to make it easier to operate.
Understanding more about the menu settings can fulfill your higher requirements with the Energy Meters’
powerful function option and output function.
Warning
May cause injury.
Attention
May damage the flow meter.
Some of the instructions may be different to the Energy Meters you purchased, depending on configuration
requirements, otherwise, there is no indication about the product design and upgrade requirement in the
instructions, please refer to the version number, as well as the appendix.

E5 Series Ultrasonic Energy Meter
Revision: 3.0.1 Page 3 of 60
Product Components
Inspection should be made before installing the Energy Meter. Check to see if the spare parts are in accordance
with the packing list. Make sure that there is no damage to the enclosure due to a loose screw or loose wire, or
other damage that may have occurred during transportation. Any questions, please contact your representative as
soon as possible.
Transmitter
Transducers Temperature Sensor
Accessories Documents
1. Instruction Manual
2. Packing List
3. Position drawing
Pipe Straps Coupling compound
Install accessory SD Card Reader

E5 Series Ultrasonic Energy Meter
Revision: 3.0.1 Page 4 of 60
Content
1 Transmitter Installation and Connection .................................................................................7
1.1 Inspection prior to Transmitter Installation........................................................................................................ 7
1.2 Wire Connecting ................................................................................................................................................ 8
1.2.1 Power supply option .................................................................................................................................. 8
1.2.2 Transmitter Wiring .................................................................................................................................... 8
1.2.3 Lengthened Cable Method......................................................................................................................... 8
1.3 Powering on ..................................................................................................................................................... 10
1.4 Keypad Functions ............................................................................................................................................ 10
1.5 Keypad Operation ............................................................................................................................................ 10
1.6 Energy Meter Window Descriptions................................................................................................................ 11
2 Pipe Parameter Entry Shortcuts .............................................................................................12
2.1 Dual function keys menu description............................................................................................................... 12
2.2 Examples.......................................................................................................................................................... 13
3 Measurement Site Selection .....................................................................................................15
4 Transducer Installation ............................................................................................................16
4.1 Installing the transducers ................................................................................................................................. 16
4.1.1 Transducer Spacing ................................................................................................................................. 16
4.1.2 Transducer Mounting Methods................................................................................................................ 16
4.1.3 V Method................................................................................................................................................. 16
4.1.4 Z Method ................................................................................................................................................. 17
4.1.5 N Method (not commonly used).............................................................................................................. 17
4.2 Transducer Mounting Inspection ..................................................................................................................... 17
4.2.1 Signal Strength ........................................................................................................................................ 17
4.2.2 Signal Quality (Q value) .......................................................................................................................... 18
4.2.3 Total Time and Delta Time...................................................................................................................... 18
4.2.4 Transit Time Ratio................................................................................................................................... 18
4.2.5 Warnings.................................................................................................................................................. 18
5 Temperature Sensor Installation.............................................................................................19
5.1 Selection of measuring point............................................................................................................................ 19
5.2 Installation of temperature sensor .................................................................................................................... 19
6 Operating Instructions .............................................................................................................20
6.1 System Normal Identification .......................................................................................................................... 20
6.2 Zero Set Calibration ......................................................................................................................................... 20
6.3 Scale Factor...................................................................................................................................................... 20
6.4 System Lock..................................................................................................................................................... 20
6.5 Frequency Output............................................................................................................................................. 21
6.6 4~20mA Current Loop Output Verification (Optional) ................................................................................... 21
6.7 Recover the Factory Default ............................................................................................................................ 21

E5 Series Ultrasonic Energy Meter
Revision: 3.0.1 Page 5 of 60
6.8 4~20mA Analog Output Calibration................................................................................................................ 22
6.9 ESN.................................................................................................................................................................. 22
7 Windows Display Explanations ...............................................................................................23
7.1 Windows Display Codes.................................................................................................................................. 23
7.2 Display Explanation......................................................................................................................................... 24
8 Error Diagnoses.........................................................................................................................38
8.1 Table1. Error codes and solutions.................................................................................................................... 38
8.2 Frequently Asked Questions and Answers....................................................................................................... 39
9 Product Overview .....................................................................................................................40
9.1 Introduction...................................................................................................................................................... 40
9.2 Features of E5 .................................................................................................................................................. 40
9.3 Operating principle .......................................................................................................................................... 40
9.4 Specifications................................................................................................................................................... 41
10 Appendix1-Serial Interface Network Use and Communications Protocol ..........................42
10.1 Overview.......................................................................................................................................................... 42
10.2 Direct connection via RS-485 to the host device ............................................................................................. 42
10.3 Communication protocol and the use............................................................................................................... 42
10.3.1 FUJI Protocol........................................................................................................................................... 43
10.3.2 MODBUS Communication Protocol ....................................................................................................... 44
11 Appendix2-W211 Insertion Transducer .................................................................................48
11.1 Overview.......................................................................................................................................................... 48
11.2 Measurement Point Selection........................................................................................................................... 48
11.3 Determining Transducer Spacing & Transducer Installation........................................................................... 48
11.4 Transducer Mounting Methods........................................................................................................................ 50
11.4.1 Z Mounting Method................................................................................................................................. 50
11.4.2 Pipe Parameter Entry Shortcuts ............................................................................................................... 50
12 Appendix3-RTD Module and PT1000 Wiring (Module optional)........................................52
12.1 RTD Energy Meter Function ........................................................................................................................... 52
12.2 Wiring(PT1000)............................................................................................................................................... 52
12.3 Energy Measurement Methods ........................................................................................................................ 52
12.4 Temperature Calibration Methods ................................................................................................................... 52
12.5 Installation of RTD Module ............................................................................................................................. 54
13 Appendix 5-WiFi Operation Instructions...............................................................................55
13.1 A Brief Introduction on Functions ................................................................................................................... 55
13.2 Energy Meter Distribution Network Mode ...................................................................................................... 55
13.2.1 Automatic Access .................................................................................................................................... 55
13.2.2 Manual Access......................................................................................................................................... 55
13.3 Energy Meter Distribution Network ................................................................................................................ 56
13.3.1 Download WeChat ............................................................................................................................... 56

E5 Series Ultrasonic Energy Meter
Revision: 3.0.1 Page 6 of 60
13.3.2 Search Gentos’ public cloud number ....................................................................................................... 56
13.3.3 Click on following button........................................................................................................................ 57
13.3.4 Click on air-condition system.................................................................................................................. 57
13.3.5 Configuration of equipment for Internet access....................................................................................... 58
13.3.6 Visit SMART METERS.......................................................................................................................... 58
14 Appendix 6-Operation Instructions of SD Card ....................................................................59
14.1 Technical Specifications .................................................................................................................................. 59
14.2 Online Insert and Removal of SD Card ........................................................................................................... 60
14.3 Offline Data Reading: ...................................................................................................................................... 60
Update Information:
__________________________________________________________________________________________
__________________________________________________________________________________________
__________________________________________________________________________________________

E5 Series Ultrasonic Energy Meter
Revision: 3.0.1 Page 7 of 60
1 Transmitter Installation and Connection
1.1 Inspection prior to Transmitter Installation
You will find a "Position Drawing" in the packing.
Please use it as a template in the place that you are
going to install the Energy Meter. Then drill 4
installing holes at the screws position shown on the
drawing with the 5.0mm drill.
Take out the enclosed screws and plastic bushings.
Insert the plastic bushings into the installing holes. Put
the Energy Meter to the position and screw it in.
Attention
When installing please ensure the front cover is secure and will not fall open.
135 mm
5.32lnch
Position drawing
1. Place this template on the wall and drill 4
holes of 5mm diameter & 40mm deep.
2. Insert a plastic bushing into each of the 4
holes.
3. Screw 4 pcs PA 4 ×30mm self tapping
screws through the transmitter enclosure
base and attach it to the wall.
4. Tighten the screws to secure to the
enclosure on the wall.
MODEL DCT1188
Digital Correlation Transit -TimeFlowmeter
135mm
5.32lnch
·

E5 Series Ultrasonic Energy Meter
Revision: 3.0.1 Page 8 of 60
1.2 Wire Connecting
1.2.1 Power supply option
Customers should pay special attention to specify the desired power supply when wiring.
Factory standard power supply is 10~36VDC/1A max.
To ensure the transmitter can work normally, please pay attention to the followings when wiring:
Ensure that power connections are made in accordance with the specifications shown on the transmitter.
1.2.2 Transmitter Wiring
Once the electronics enclosure has been installed, the Energy Meter wiring can be connected.
Open the case, you will find the transmitter interfaces labels, from up to down, from left to right as follows:
Connect to the RTD module,Power supply, Relay output, OCT Output, Upstream transducer, Downstream
transducer, 4-20mA, RS485 interface.
Refer to the below diagram for specific connection:
1.2.3 Lengthened Cable Method
Standard cable length of sensor is 9 meters; it can be lengthened to be 300 meters according to the actual need for
fluid measurement.
Red Bushing
Flow
DC+ DC- GE
DC 10 - 36V
E UP+ UP- E DN+ DN-
TRANSDUCER
I+ I-
4-20mA
Blue Bushing
Being tested pipe
Black
Red
Shield
Pipe Straps
Upstream Transducer Downstream Transducer
OCT+ OCT-
OCT OUT
RL+ RL-
RELAY
Shield
Red
Black
10~36VDC
Tx Rx GND
RS232(RS485)
A B
4mA 20mA 4mA 20mA
A1 B1 C1 A2 B2 C2
Red
White
Black
White
Red
Black
temperature sensors

E5 Series Ultrasonic Energy Meter
Revision: 3.0.1 Page 9 of 60
1.2.3.1 Sketch of lengthened Cable
1.2.3.2 Junction Box Requirements
The Energy Meter use sealed waterproof junction box, installing 6×2 press-connections, the recommended
minimum specifications of the junction box is 115×90×55mm.
1.2.3.3 Cable Specifications
Name: Shielded Twisted Pair
Administer Standard: JB8734.5-1998
Diameter: 5 mm
Twist Line Space: 50 mm
Multi Core Line: 0.4 mm2/radix
Wire Guage: AWG 20#
Core Line Color: Red and Black
Shield Floor: 128 Intwine
Warning
Wire with power off. The flow meter must be reliable grounding before installation.

E5 Series Ultrasonic Energy Meter
Revision: 3.0.1 Page 10 of 60
1.3 Powering on
As soon as the Energy Meter is switched on, the self-diagnosis program will start to run. If any error is detected,
an error code will display on the screen (Refer - Error Diagnoses). After that self-diagnosis, the system will run
automatically according to the last input parameters.
If the installation is accomplished when system is switched on, gain adjustment can be monitored in Window M01.
After S1, S2, S3, S4 are displayed on the upper left corner of the screen, the system will activate the normal
measurement condition automatically. It is indicated by code "*R" on the upper left corner of the screen.
If it is the first time to use or install on a new site, the customer need to input the new installation site parameters.
The system will default to the last window settings and automatically display them at next power on.
1.4 Keypad Functions
This keypad is dual function keypad:
1. When separately pressed, is shortcut function,
referring to "2. Quickly set menu instructions ";
2. Press and Number key, is Menu key,
referring to"6.Menu Window Description".
Follow these guidelines when using the Energy Meter
keypad (Refer to Keypad Figure):
~ And To input numbers.
Backspace or delete characters to the left.
And Return to the last menu or to open
the next menu. Acts as "+" and "-" functions when
entering numbers.
Select a menu. Press this key first, input two
menu numbers and then enter the selected menu. For
example, to input a pipe outside diameter, press
keys, where "11" is the window ID to
display the parameter for pipe outside diameter.
1.5 Keypad Operation
The flow meter adopts the window software design to consolidate or subdivide all of the parameters entered, the
instrument setup and measurement result displays into more than 100 independent windows. The operator can
input parameters, modify settings or display measurement results by "visiting" a specific window. These windows
are arranged by 2-digit serial numbers (including "+" sign) from 00~99, then to +0, +1, etc. Each window serial
number, or so-called window ID code, has a defined meaning. For example, Window M11 indicates the parameter
input for pipe outside diameter, while Window M25 indicates the mounting spacing between the transducers, etc.
(Refer –Windows Display Explanations).
The keypad shortcut to visit a specific window is to press the key at any time, then input the 2-digit window
ID code. For example, to input or check the pipe outside diameter, just press the keys for window
ID code 11.
Another method to visit a particular window is to press and keys to scroll the screen. For example, if
the current window ID code is M02, press key to enter Window M01, press the button again to enter
Window M00; then, press the key to back Window M01, and press the key again to enter Window
M02.
Windows are separated into three types: (1) Data Type, such as M11, M12; (2) Option Type, such as M14; (3)
Pure Display Type, such as M01, M00.
You can check the corresponding parameters by visiting the Data Type Windows. If you want to modify the
parameters, input the digits and press or press first, input the digits then press again to confirm.
Menu
0 9
<
^
^
Menu
Menu
1 1
Menu
Menu 1 1
^
^
^ ^
^^
Enter Enter Enter

E5 Series Ultrasonic Energy Meter
Revision: 3.0.1 Page 11 of 60
Example1: To enter a pipe outside diameter of 219.234, the
procedure is as follows:
Press keys to enter Window M11 (the
numerical value displayed currently is a previous value). Now
press key. The symbol ">" and the flashing cursor are
displayed at the left end of the second line on the Screen. Then
input the parameters; or do not press the key, directly enter
.
You can check the selected option by visiting Option Type
Windows. If you want to modify it, you must press first,
the symbol ">" and the flashing cursor are displayed at the left
of the Screen. Operator can use the and to scroll
the screen and get the required value then press to
confirm; or enter the corresponding value option directly and
press to confirm.
For example, if the pipe material is "Stainless Steel", Press
to enter Window M14, press to modify
the options. Select the "1. Stainless Steel" option by pressing
and , then press to confirm the selection; It is
possible to press key to change the selection and wait
until "1.Stainless Steel" is displayed on the second line of the
screen, then press to confirm.
Attention
Generally, press key first if operator wants to enter "modify" status. If the "modify" is still not
possible even after pressing the key, it means that system is locked by a password. To
"Unlock" it, select "Unlock" in Window M47 and enter the original password.
1.6 Energy Meter Window Descriptions
These windows are assigned as follows:
01~08 Flow Totalizer Display: to display flow rate, positive total, negative total, net total, velocity, date &
time, present operation and flow results today, etc.
10~29 Initial Parameter Setup: to enter pipe outside diameter, pipe wall thickness, fluid type, transducer type,
transducer mounting method and spacing, etc.
30~38 Flow Units Options: to select the flow unit such as cubic meter, liter or other units, can turn totalizers
on/off and reset totalizers, etc.
40~49 Setup options: Scaling factor, system lock (Window M47), etc.
55~89 Input and output setup: date and time, ESN, communication baud rate setting, etc.
90~98 Diagnoses: Signal strength and signal quality (Window M90), TOM/TOS*100 (Window M91), flow
sound velocity (Window M92), total time and delta time (Window M93), Reynolds number and factor
(Window M94), etc.
+0~+5 Appendix: power on/off time, total working hours, on/off times and a single-accuracy function calculator.
Attention
The other windows for hardware adjustment are reserved by the manufacturer.
Menu 1 1
Enter
Enter
219 2 34 5 Enter
Enter
^
^
Enter
Enter
Menu 14 Enter
^
^
Enter
1
Enter
Enter
Enter

E5 Series Ultrasonic Energy Meter
Revision: 3.0.1 Page 12 of 60
2 Pipe Parameter Entry Shortcuts
2.1 Dual function keys menu description
Press key
Display Net Flow Today /Flow Max /Flow Min/The
Average/Current Rate in turn.
Press key
Display Day Totalizer Flow /Monthly Totalizer Flow
/ Yearly Totalizer Flow in turn.
Press key
Display Totalizer Start and Stop in turn.
Press key
Display instantaneous cool capacity and cool capacity
totalizer.
Press key
Display instantaneous heat capacity and heat capacity
totalizer.
Press key
Display the temp in, out and temperature difference .
Press key
Display Flow Rate and Velocity.
Press key
Display Flow Sound Velocity.
Press key
Display Signal Strength and Signal Quality.

E5 Series Ultrasonic Energy Meter
Revision: 3.0.1 Page 13 of 60
Press key
Press Ent to start Manual Totalizer, then press Ent to
end Manual Totalizer, press Ent to input Standard
Totalizer to get the final K factor. Complete the
calibration with pressing Ent to store.
Press key
Input Code 1234 to complete Reset Zero.
Press key
Display System Error Codes.
2.2 Examples
For example, measuring the diameter of 219mm and pipe wall thickness of 6mm, measuring medium is water,
Pipe Material is carbon steel, No Liner, can be operated as follows:
Step1. Pipe outside diameter:
Press keys to enter Window
M11, and enter the pipe outside diameter, and
then press the key to confirm.
Step2. Pipe wall thickness
Press the key to enter Window
M12, and enter the pipe wall thickness, and
press the key to confirm.
Step3. Pipe Material
Press the keys to enter Window
M14, press the key, press the or
key to select Pipe Material, and press the
key to confirm.
Step4. Transducer type
(The transmitter is available for various
transducer types.)
Press the key to enter Window
M23,press the key,move the or
key to select transducer type,and press the
key to confirm.
Menu 1 1
Enter
Menu 12
Enter
Menu 14
Enter ^
^
Enter
Menu 2 3
Enter ^
^
Enter

E5 Series Ultrasonic Energy Meter
Revision: 3.0.1 Page 14 of 60
Step5. Transducer mounting methods
Press the key to enter Window
M24, press the key, press the or
key to select transducer-mounting
method, and press the key to confirm.
Step6. Adjust Transducer spacing
Press the key to enter Window
M25, accurately install the transducer according
to the displayed transducer mounting spacing
and the selected mounting method (Refer to
Installing the Transducers in this chapter).
Step7. Display measurement result
Press the keys to enter Window
M01 to display measurement result. (Base on
the actual measurement)
Menu 2 4
Enter ^
^
Enter
Menu 2 5
Menu 0 1

E5 Series Ultrasonic Energy Meter
Revision: 3.0.1 Page 15 of 60
3 Measurement Site Selection
When selecting a measurement site, it is important to select an area where the fluid flow profile is fully developed
to guarantee a highly accurate measurement. Use the following guidelines to select a proper installation site:
Choose a section of pipe that is always full of liquid, such as a vertical pipe with flow in the upward direction or a
full horizontal pipe.
Ensure enough straight pipe length at least equal to the figure shown below for the upstream and downstream
transducers installation.
Ensure that the pipe surface temperature at the measuring point is within the transducer temperature limits.
Consider the inside condition of the pipe carefully. If possible, select a section of pipe where the inside is free of
excessive corrosion or scaling.
L 10D
L 5D
10D min
L 50D
L 10D
L 30D
5D min
L 5D
L 10D L 5D
L 50D
P
L 30D L 10D
Straight length of Upstream
piping
Name Straight length of Downstream
piping
Pump
Value
Diffuser
Tee
90obend
Reducer
Detector
Flow controlled downstreamFlow controlled upstream
Check Value
Check Value

E5 Series Ultrasonic Energy Meter
Revision: 3.0.1 Page 16 of 60
4 Transducer Installation
4.1 Installing the transducers
Before installing the transducers, clean the pipe surface where the transducers are to be mounted. Remove any rust,
scale or loose paint and make a smooth surface. Choose a section of sound conducting pipe for installing the
transducers. Apply a wide band of sonic coupling compound down the center of the face of each transducer as
well as on the pipe surface, ensure there are no air bubbles between the transducers and the pipe wall, and then
attach the transducers to the pipe with the straps provided and tighten them securely.
Note:
The two transducers should be mounted at the pipe’s centerline on horizontal pipes.
Make sure that the transducer mounting direction is parallel with the flow.
During the installation, there should be no air bubbles or particles between the transducer and the pipe wall. On
horizontal pipes, the transducers should be mounted in the 3 o’clock and 9 o’clock positions of the pipe section in
order to avoid any air bubbles inside the top portion of the pipe. (Refer to Transducer Mounting). If the
transducers cannot be mounted horizontally symmetrically due to limitation of the local installation conditions, it
may be necessary to mount the transducers at a location where there is a guaranteed full pipe condition (the pipe is
always full of liquid).
4.1.1 Transducer Spacing
After entering the required parameters, the spacing between the ENDS of the two transducers is considered as the
standard transducer spacing (Refer to Top View on transducer mounting methods). Check the data displayed in
Window M25 and space the transducers accordingly.
4.1.2 Transducer Mounting Methods
Three transducer mounting methods are available. They are respectively: V method, Z method and N method. The
V method is primarily used on small diameter pipes (DN100~300mm, 4 ~12 ). The Z method is used in
applications where the V method cannot work due to poor signal or no signal detected. In addition, the Z method
generally works better on larger diameter pipes (over DN300mm, 12 ) or cast iron pipes.
The N method is an uncommonly used method. It is used on smaller diameter pipes (below DN50mm, 2 ).
4.1.3 V Method
The V method is considered as the standard method. It usually gives a more accurate reading and is used on pipe
diameters ranging from 25mm to 400mm (1 ~16 ) approximately. Also, it is convenient to use, but still
requires proper installation of the transducers, contact on the pipe at the pipe’s centerline and equal spacing on
either side of the centerline.
Downstream Transducer
Upstream Transducer
Transducer Space
Flow
Side View Top ViewSection
Pipe Strap
Transducer

E5 Series Ultrasonic Energy Meter
Revision: 3.0.1 Page 17 of 60
4.1.4 Z Method
The signal transmitted in a Z method installation has less attenuation than a signal transmitted with the V method
when the pipes are too large, there are some suspended solid in the fluid, or the scaling and liner are too thick .
This is because the Z method utilizes a directly transmitted (rather than reflected) signal which transverses the
liquid only once.
The Z method is able to measure on pipe diameters ranging from 100mm to 800mm (4 ~32 ) approximately.
Therefore, we recommend the Z method for pipe diameters over 300mm (12 ).
4.1.5 N Method (not commonly used)
With the N method, the sound waves traverse the fluid three times and bounce twice off the pipe walls. It is
suitable for small pipe diameter measurement.
The measurement accuracy can be improved by extending the transit distance with the N method (uncommonly
used).
4.2 Transducer Mounting Inspection
Check to see if the transducer is installed properly and if there is an accurate and strong enough ultrasonic signal
to ensure proper operation and high reliability of the transducer. It can be confirmed by checking the detected
signal strength, total transit time, delta time as well as transit time ratio.
The "mounting" condition directly influences the flow value accuracy and system long-time running reliability. In
most instances, only apply a wide band of sonic coupling compound lengthwise on the face of the transducer and
stick it to the outside pipe wall to get good measurement results. However, the following inspections still need to
be carried out in order to ensure the high reliability of the measurement and long-term operation of the instrument.
4.2.1 Signal Strength
Signal strength (displayed in Window M90) indicates a detected strength of the signal both from upstream and
downstream directions. The relevant signal strength is indicated by numbers from 00.0~99.9. 00.0 represents no
signal detected while 99.9 represents maximum signal strength.
Normally, the stronger the signal strength detected, the longer the operation of the instrument reliably, as well as
the more stable the measurement value obtained.
Adjust the transducer to the best position and check to ensure that enough sonic coupling compound is applied
adequately during installation in order to obtain the maximum signal strength.
Downstream Transducer
Upstream Transducer
Transducer Spacing
Flow
Side View Top ViewSection
Pipe Strap
Transducer
Downstream Transducer
Upstream Transducer
Transducer Spacing
Flow
Side View Top ViewSection
Pipe Strap
Transducer

E5 Series Ultrasonic Energy Meter
Revision: 3.0.1 Page 18 of 60
System normally requires signal strength over 60.0, which is detected from both upstream and downstream
directions. If the signal strength detected is too low, the transducer installation position and the transducer
mounting spacing should be re-adjusted and the pipe should be re-inspected. If necessary, change the mounting
method to be Z method.
4.2.2 Signal Quality (Q value)
Q value is short for Signal Quality (displayed in Window M90). It indicates the level of the signal detected. Q
value is indicated by numbers from 00~99. 00 represents the minimum signal detected while 99 represent the
maximum.
Normally, the transducer position should be adjusted repeatedly and coupling compound application should be
checked frequently until the signal quality detected is as strong as possible.
4.2.3 Total Time and Delta Time
"Total Time and Delta Time", which displays in Window M93, indicates the condition of the installation. The
measurement calculations in the Energy Meter are based upon these two parameters. Therefore, when "Delta
Time" fluctuates widely, the flow and velocities fluctuate accordingly, this means that the signal quality detected
is too poor. It may be the resulted of poor pipe-installation conditions, inadequate transducer installation or
incorrect parameter input.
Generally, "Delta Time" fluctuation should be less than ±20%. Only when the pipe diameter is too small or
velocity is too low can the fluctuation be wider.
4.2.4 Transit Time Ratio
Transit Time Ratio indicates if the transducer mounting spacing is accurate. The normal transit time ratio should
be 100+/-3 if the installation is proper. Check it in Window M91.
4.2.5 Warnings
(1) Pipe parameters entered must be accurate; otherwise the Energy Meter will not work properly.
(2) During the installation, apply enough coupling compounds in order to stick the transducers onto the
pipe wall. While checking the signal strength and Q value, move the transducers slowly around the
mounting site until the strongest signal and maximum Q value can be obtained. Make sure that the
larger the pipe diameter, the more the transducers should be moved.
(3) Check to be sure the mounting spacing is accordance with the display in Window M25 and the
transducer is mounted at the pipe’s centerline on the same diameter.
(4) Pay special attention to those pipes that formed by steel rolls (pipe with seams), since such pipe is
always irregular. If the signal strength is always displayed as 0.00, that means there is no signal
detected. Thus, it is necessary to check that the parameters (including all the pipe parameters) have
been entered accurately. Check to be sure the transducer mounting method has been selected properly,
the pipe is not worn-out, and the liner is not too thick. Make sure there is indeed fluid in the pipe or
the transducer is not too close to a valve or elbow, and there are not too many air bubbles in the fluid,
etc. With the exception of these reasons, if there is still no signal detected, the measurement site has
to be changed.
Attention
If the transit time ratio is over 100±3, it is necessary to check:
(1) If the parameters (pipe outside diameter, wall thickness, pipe material, liner, etc.) have
been entered correctly,
(2) If the transducer mounting spacing is accordance with the display in Window M25,
(3) If the transducer is mounted at the pipe’s centerline on the same diameter,
If the scale is too thick or the pipe mounting is distorted in shape, etc.

E5 Series Ultrasonic Energy Meter
Revision: 3.0.1 Page 19 of 60
(5) Make sure that the Energy Meter is able to run properly with high reliability. The stronger the signal
strength displayed, the higher the Q value reached. The longer the Energy Meter runs accurately, the
higher the reliability of the flow rates displayed. If there is interference from ambient electromagnetic
waves or the signal detected is too poor, the flow value displayed is not reliable; consequently, the
capability for reliable operation is reduced.
(6) After the installation is complete, power on the instrument and check the result accordingly.
5 Temperature Sensor Installation
Standard configuration PT1000 temperature sensor.
Before the temperature sensor transducer is installed, it is necessary to select the appropriate measuring point
to ensure the accuracy of measurement.
5.1 Selection of measuring point
The installation position of the temperature sensor shall be selected according to the following principles:
1. The installation position of the temperature sensor shall be selected at the place with sensitive and
representative medium temperature change, not near the resistance parts such as valves, welds and the
dead angle of medium flow rate.
2. Installed in a place convenient for operation and maintenance.
3. The temperature of the measured fluid does not exceed the rated working temperature, and the
working temperature range of the temperature sensor is 0-100 .
4. The installation of the temperature sensor shall not affect the installation of the ultrasonic sensor
because it will become a resistance part for the fluid in the pipelineafter the temperature sensor is
installed , which will cause turbulence of the fluid flow). It shall be installed downstream of the
ultrasonic sensor.
5.2 Installation of temperature sensor
Before installing the clamp on temperature sensor, the area to be installed on the surface of the pipeline shall
be cleaned and the rust and paint shall be removed, and then the clamp on temperature sensor shall be tightly
bound on the pipe wall. Note that the water inlet temperature sensor is installed on the water inlet pipe wall, and
the water outlet temperature sensor is installed on the water outlet pipe wall.
temperature sensor

E5 Series Ultrasonic Energy Meter
Revision: 3.0.1 Page 20 of 60
6 Operating Instructions
6.1 System Normal Identification
Press the keys. If the letter "*R" displays on the screen, it indicates system normal.
If the letter "G" is displayed, it indicates that system is adjusting the signal gain prior to the measurement. Also, it
means system normal. Only when the adjustment takes too long without stopping, can system be identified as
abnormal.
Letter "I" indicates no signal is being detected. Check the transducer wiring connections are correct, the
transducers are installed firmly, etc.
6.2 Zero Set Calibration
Once zero flow occurs, a zero point may indicate on each measuring instrument, but the displayed measuring
value is not equal to "0", this value indicates "Zero". To any measuring instrument, the smaller the "Zero" is, the
better the quality is. Conversely, if the Zero is too big, that indicates the quality of the instrument is poor.
If the zero set point is not at true zero flow, a measurement difference may occur. The smaller the physical
measurement capacity is, the larger the measurement difference from the zero point will exist. Only when zero
point reduced to a definite degree, as compared with the physical measurement capacity, can the measuring
difference from zero point be ignored.
For an ultrasonic Energy Meter, the measurement difference from zero point cannot be ignored at low flow. It is
necessary to perform a static zero set calibration to improve low flow measurement accuracy.
Press Window M42 to set the Zero, press first, and then wait the readings displayed at the lower right
corner reducing to be "0". If this is carried out with flow, the flow will be displayed as "0", M43 can help to
restore settings.
6.3 Scale Factor
Scale factor refers to the ratio between "actual value" and "reading value". For example, when the measurement
and is 2.00, and it is indicated as 1.98 on the instrument, the scale factor reading is 2/1.98. This means that the
best scale factor constant is 1.
However, it is difficult to keep the scale factor as "1" on the instrument especially in batch productions. The
difference is called "consistency".
During operation, there still exists possible difference in pipe parameters, etc. The "scale factor" may be necessary
when used on different pipes. Thus, scale factor calibration is specially designed for calibrating the differences
that result from application on different pipes. The scale factor entered must be one that results from actual
calibration. The scale factor can be input in Window M45.
6.4 System Lock
System lock is readable but not modifiable to prevent operation error due to unauthorized tampering by
unauthorized personnel.
Press the keys, if displays "Unlock" on the screen, then press the key, enter 6 numerically
long password, and then press the key to confirm.
Unlock it by using the selected password only. Press , if "lock" is displayed on the screen, then
press the key and enter the correct password, then press to confirm.
Keep the password in mind or recorded in a safe place, otherwise the instrument cannot be used.
Menu 0 8
Enter
Menu 4 7 Enter
Enter
Menu 4 7
Enter Enter
Table of contents
Popular Measuring Instrument manuals by other brands

Honeywell
Honeywell AutoSet 1500 user manual
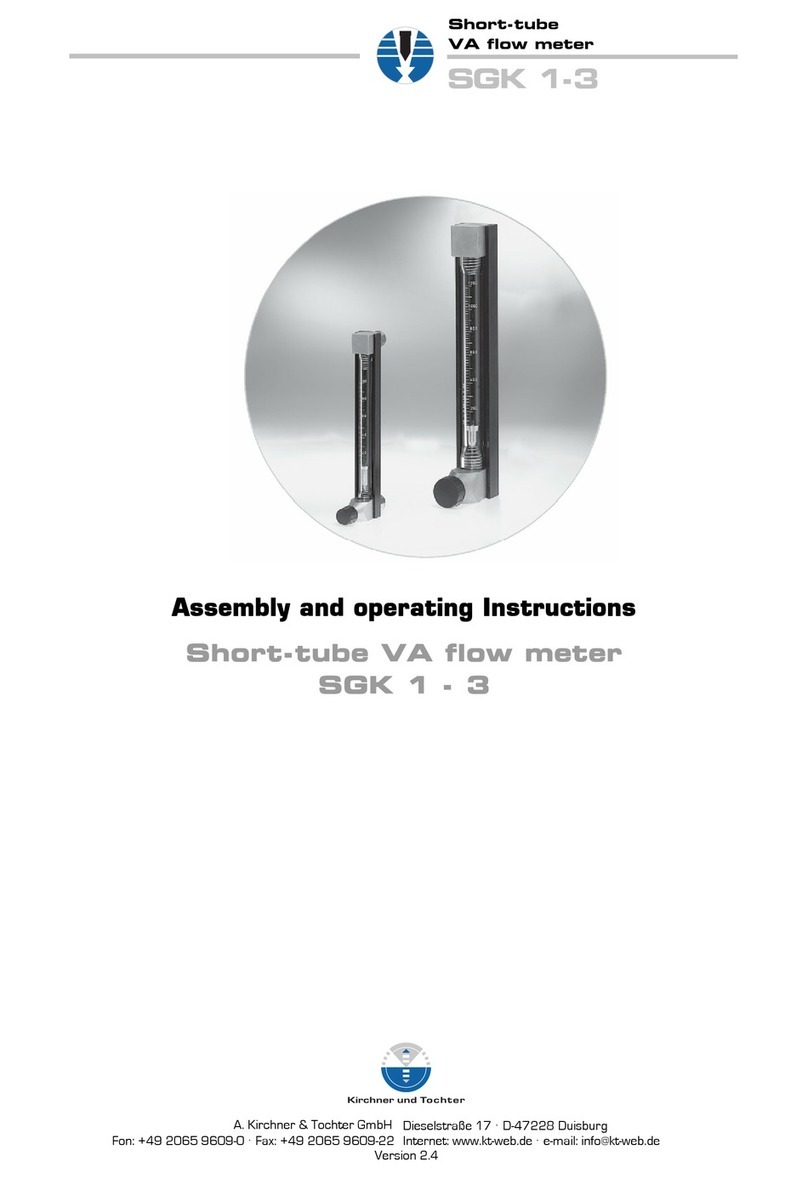
Kirchner und Tochter
Kirchner und Tochter SGK 1-3 Assembly and operating instructions

UTC Fire and Security
UTC Fire and Security Chubb FSM-ES Installation, operation and maintenance manual
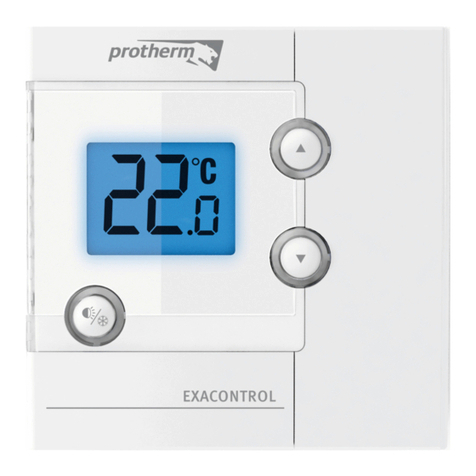
Protherm
Protherm Exacontrol operating instructions
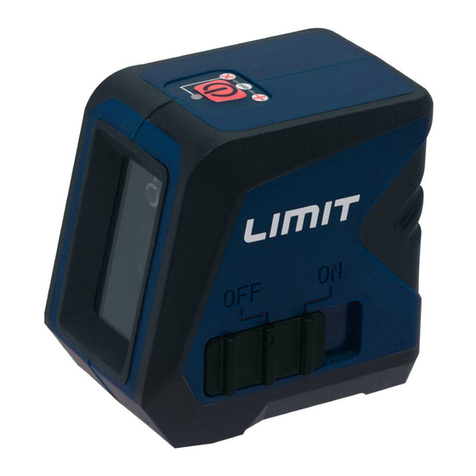
LIMIT
LIMIT 1000-R operating manual

Oven
Oven SAU-M6 Passport and user manual