Warner TCS-200-1 User manual

TCS-200-1 and TCS-200-1H
Tension Controls
Service & Installation Instructions
P-2003-2-WE
819-0420
An Altra Industrial Motion Company

2Warner Electric • 800-825-9050 P-2003-2 • 819-0420
Contents
Introduction ............................2
Theory of Operation ......................3
Technical Specifications ..................3
Installation
Control Mounting .....................4
External Sensor Mounting...............5
System Wiring ..........................5
System Start-Up and Adjustment ..........11
Voltage Tables .........................19
System Troubleshooting .................20
Component Parts List
Coupling, MCS-605-1 284-8000-003
Roll Pin (Drive) for Sensor Coupling 679-8001-067
TCS-200-1 Tension Control 6910-448-086
TCS-200-1H Tension Control 6910-448-087
Ultrasonic Sensor 4-40in 7600-448-001
List of Illustrations and Figures
Figure 1 Dimensional Data, Mounting ....... 6
Figure 2 Power Connections .............. 7
Figure 3 Brake Connections .............. 8
Figure 4 Remote Torque and Roll
Follower Connections............. 9
Figure 5 Remote Switch, Analog Input and
Analog Input Isolation Connections . 10
Tables 1,2,3 Voltage/Current Tables .......... 19
Templates TCS-200-1H Template........... 21
TCS-200-1 Template ............ 21
Introduction
The Warner Electric Tension Control system is
comprised of a tension brake, control module, and
optional external sensor input.
This manual has been designed to cover installation,
start-up, adjustment, and maintenance of your
tension control system and covers the control system
only. Further information on brake sizing and selection
can be found in catalogs P-1234 or P-771.
Power Source
The TCS-200-1 series Tension Controls operates
from a power source of 115 or 230 VAC, 50/60 Hz
input. Primary voltage is determined by the
customer’s input voltage source. The control is
factory set to accept 115 VAC input. Refer to the
wiring section for 230 VAC input connections.
Control
The TCS-200-1 series controls are selectable
voltage or current controlled power supply designed
to power up to a 16 magnet Electro Disc tension
brake system, Electromagnetic Particle Brakes,
TB series brakes or Advanced Technology tension
brakes. This control can be operated manually from
the front panel or remotely via an analog voltage
input, a current input, a remote pot, or a roll follower.
External inputs are also provided for remote brake
“off”, “run”, and “stop” functions, as well as front
panel control of these functions.
The analog voltage and current inputs are
electrically isolated from the main power circuitry of
the control when 15-35 VDC supply is provided to
maintain full isolation. If isolation is not needed, an on
board 15 VDC supply is jumpered to act as a default.
Sensors
When the TCS-200-1 series controls are operated
in a remote torque adjust mode, a 1,000 ohm
potentiometer is required. This should be a linear type
potentiometer with a rating of .5 watts, 10 percent
tolerance, and a .5 percent linearity.
For roll follower input applications, a 1,000 ohm
potentiometer with a rating of .5 watts, 10 percent
tolerance, and .5 percent linearity is required for best
performance.
Brakes
All 24 VDC tension brakes that Warner Electric offers,
to a maximum of 4.25 amps, can be used with the
TCS-200-1 tension control. For all 24 VDC tension
brakes that require greater current capability from the
control (not to exceed 5.8 amps), use a TCS-200-
1H. The brake converts electrical current supplied by
the control into torque, which retards material flow,
maintaining the desired web tension.

Warner Electric • 800-825-9050 P-2003-2 • 819-0420 3
Theory of Operation
When in operation, the control is powered by a
standard 115/230 VAC line. The control has a
transformer that converts that voltage to a level
suitable for any 24 VDC brake system. The signal is
rectified to DC and pulse width modulated (PWM) to
the desired brake current via the TENSION ADJUST
knob.
The front panel TENSION ADJUST feeds a small
voltage to a comparator, which compares this signal
to a triangular wave. This is where the PWM pulse is
generated. This pulse is then inverted and used to
drive a power circuit. The main brakes and a sense
brake are then energized by the power circuit at
regular intervals. From the sense brake, a growth and
decay signal is converted to a voltage that can be
added to the signal by setting a jumper on the inside
of the cover. This signal, when selected, is used to
maintain constant current to the brake. The signal
must not be selected when no sense brake is
connected.
The control has several options that allow for
external/remote tension adjust in addition to the
tension adjust pot on the front of the panel. Two such
options are the remote pot or a roll follower. Another
is the option for an analog input of voltage or current
from a PLC or ultrasonic sensor. A special feature of
the analog inputs is that they are optically isolated
from the rest of the control circuitry if an external
power source is used to power the isolated circuits.
The isolation is needed when using a PLC or an
external power supply for the ultrasonic sensor. An
internal power source is also available and jumpered
in as default if isolation is not necessary. The tension
adjust pot on the front of the panel becomes a span
adjust when any of the external control options are
connected.
The control also has the capability to duplicate the
front panel selector switch at a remote location.
Brake “off” mode overrides the tension adjustment
and provides for resetting the short circuit indicator.
In the “run” mode, output operation is normal and is
controlled by any of the front panel or remote tension
adjust features discussed above. The brake “stop”
mode provides for full output current to the brake.
The two indicators on the front of the panel are
green for “power on” and red to indicate a short
circuit. When a short occurs in the brake, the control
disables the power circuits to prevent damage. Turn
the switch to “off” to reset the short circuit indicator.
Because this is a basic tension control, no anti-residual
circuits, zero adjust circuits, or other complex control
circuits (found in other Warner Electric tension control
systems) are included in the TCS-200-1 series controls.
Technical Specifications
TCS200-1 and TCS200-1H
Input Power
115/230 VAC 50/60 Hz
Output TCS-200-1
Adjustable 0-24 VDC. Maximum of 4.25 amps
continuous. Can be used with any 24 VDC
tension brake with or without the need for a
sense coil.
Output TCS-200-1H
Adjustable 0-24 VDC. Maximum of 5.8 amps
continuous. Can be used with any 24 VDC
tension brake with or without the need for a
sense coil.
Ambient Temperature
-20° to 125° F (-29° to 51° C)
Fuse
2.5 Amp, 250 VAC, Slow-Blow
Protection
Internal short-circuit protection on driver output
stage
Sensor Inputs
• Remote Torque Adjust 1,000Ω
• Roll Follower 1,000Ω
• Analog voltage input, 0-10 VDC (Optically isolated
when 15-35 VDC supplied from external source)
• Analog current input, 4-20mA (Optically isolated
when 15-35 VDC supplied from external source)

4Warner Electric • 800-825-9050 P-2003-2 • 819-0420
Auxiliary Inputs
• Brake Stop – Applies full voltage to the
connected brakes. Active high input.
• Brake Run – Voltage to the brake is controlled by
any of the sensor inputs and/or the front panel
tension adjust. Active high input.
• Brake Off – Removes output current to the brake.
Puts the brake at zero current level. Active high
input.
Note 1: The remote input signal for these functions
requires a minimum contact rating of 20 VDC at .01
amps and a maximum of state leakage current less
than 100 micro-amps.
Note 2: The remote switch input overrides the front
panel switch.
Front Panel
• Tension Adjust – Provides current adjust to the
brake from 0 to 100%. In the remote and
analog input mode, provides for maximum output
level set to the brake.
• Brake Mode Switch –
Modes: “stop”-brake full on
“run” -normal operation
“off” -brake off
Indicators (Front Panel)
• Green LED indicates AC power has been applied
to the control.
• Red LED indicates there is a short on the output.
Turn the front panel switch “off” to reset the short
circuit.
General
The control chassis must be considered NEMA 1
and should be kept clear of areas where foreign
material, dust, grease, or oil might affect control
operation.
Potentiometers (supplied by the customer)
• Remote Torque Adjust
1,000 ohms, 10% tolerance, .5% linearity,
.5 watts, linear taper
• Roll Follower – 1,000 ohms, 10% tolerance, .5%
linearity, .5 watts, linear taper
o 1. If you are using a PLC or an
external power supply with this control, you must
enable the isolation of the control.
o2. The TCS-200-1 cannot operate a single brake
or brakes that require more than 4.25 amps
continuous.
o3. The TCS-200-1H cannot operate a single
brake or brakes that require more than 5.8 amps
continuous.
This Installation and Operation Manual has been
arranged for the systematic installation and start-up
of your tension control system. To achieve the best
possible results, we recommend checking off each
completed step in the space provided before
proceeding to the next step.
Sample
oAttach the TCS-200 control chassis to the
mounting surface and secure with mounting
hardware.
Check box after completing each step.
Control Mounting
o1. Determine a suitable location for the control to
be mounted. Consideration should be given to
whether the front panel adjustments will require
access by the operator.
o2. Using the dimensional data supplied in Figure
1a and Figure 1b, drill four mounting holes using
a #16 drill if #8 through-bolts are used. For #8
capscrew mounting, use a #29 drill and tap holes
for #8 screws. Templates for hole drilling are
found on page 21.
o3. Attach the TCS-200-1 or TCS-200-1H control
chassis to the mounting surface and secure with
mounting hardware.
Note: The control chassis has been designed to
accommodate two half-inch conduits for wiring when
the control is mounted to the machine frame.

Warner Electric • 800-825-9050 P-2003-2 • 819-0420 5
o4. Attach conduit or seal tight connectors.
The control is now ready to be wired. Refer to the
wiring section of this manual for proper system wiring.
Brake Installation
Refer to the brake manual that is appropriate for the
brake selected for its installation procedures.
External Sensor Mounting (Optional)
Options for four types of external sensor inputs are
available. These consist of either an external torque
adjust, roll follower input that provides a signal
directly proportional to the diameter of the roll to be
processed, analog voltage, or analog current input.
Determine which type of external sensor will be
used and proceed to the appropriate section of this
manual.
Remote Torque Adjust Potentiometer (Optional)
o1. Select an appropriate mounting location for the
external torque-adjust potentiometer.
Note: In determining this mounting location, take
into consideration the routing of the wires necessary
to connect the control, access for the operator,
and space required by the physical size of the
potentiometer.
o2. Drill a mounting hole based on the bushing
diameter of the potentiometer selected.
o3. Mount and secure the potentiometer.
This completes the mounting for an external remote
torque adjust potentiometer. Refer to the wiring
section of this manual for proper control wiring.
Roll Follower Adjust Potentiometer (Optional)
o1. Mount the roll follower potentiometer and
determine the amount of angular rotation at the
potentiometer shaft.
Note: If angular rotation is not adequate, insufficient
output from the control is possible. In this case, a
timing belt drive between the roll follower pivot-point
and the sensor potentiometer may be necessary to
obtain adequate angular rotation.
o2. Secure the roll follower potentiometer. This
completes the mounting for a roll follower
potentiometer. Refer to the wiring section of this
manual for proper control wiring.
Analog Input (Optional)
o1. Select an appropriate mounting location for the
PLC or ultrasonic sensor.
o 2. Mount and secure the PLC or ultrasonic
sensor according to the specifications for those
products.
This completes the mounting. Refer to the wiring
section of this manual for proper control wiring.
System Wiring
System Wiring Precautions
The following wiring precautions will help you
properly wire and install a trouble free system.
o1. Use a proper gauge wire for all wiring.
o2. Insure that wires are cut and stripped so that
no excess bare wire is exposed.
o3. Segregate AC input power from control
switching and external sensor wiring (if used).
o4. Do not run AC power lines with DC power,
input sensor wiring, or switching wiring. Noise
transients can be easily transferred, causing
erratic control operation.
o5. Use shielded cable when possible for
connecting the TCS-200-1 to external switches,
the sensor potentiometer, PLC’s, and ultrasonic
sensor.
o6. Under no circumstances should auxiliary
accessories be operated from the TCS-200-1
control.

6Warner Electric • 800-825-9050 P-2003-2 • 819-0420
WA RNER ELECTRIC®
TCS-200-1H
POWER SHORT
TENSION
ADJUSTMENT BRAKE MODE
.875 DIA. 2 PLCS.
FOR 1/2 CONDUIT
3.75
1.25
3.00
C
L
4.00
1.00 6.82
6.00
.875 DIA. 2 PLCS.
2.87
1.25
3.00
6.00
7.50
WA RNER ELECTRIC®
TCS-200-1
POWER SHORT
TENSION
ADJUSTMENT BRAKE MODE
.31 Dia.
5.75
WA RNER ELECTRIC®
TCS-200-1H
POWER SHORT
TENSION
ADJUSTMENT BRAKE MODE
.875 DIA. 2 PLCS.
FOR 1/2 CONDUIT
3.75
1.25
3.00
C
L
4.00
1.00 6.82
6.00
.875 DIA. 2 PLCS.
2.87
1.25
3.00
6.00
7.50
WA RNER ELECTRIC®
TCS-200-1
POWER SHORT
TENSION
ADJUSTMENT BRAKE MODE
.31 Dia.
5.75
TCS-200-1H with Heat Sink
Figure 1a
CS-200-1
Figure 1b

Warner Electric • 800-825-9050 P-2003-2 • 819-0420 7
o7. Do not attempt to incorporate
external switching schemes between two or
more brakes and the TCS-200-1 output. This will
damage the control and void the warranty.
o 8. Do not attempt to wire two or more controls in
parallel.
TCS-200-1 Series Controls Wiring
Refer to Figure 2 for actual wiring connections.
o1. Unlatch the front cover of the TCS-200-1.
Power
Determine if 115 VAC or 230 VAC will be used to
power the control and proceed to that section of this
manual.
Insure power is off and disconnects
open on the control panel before connecting the AC
input. Failure to do so can result in damage to
equipment and injury or even death to personnel.
115 VAC
Refer to Figure 2a for 115 VAC power input
connections.
o1. Connect the 115 VAC power to terminals 4
& 8 of terminal block TB2 located in the base of
the TCS-200-1 enclosure. Secure the terminal
screws.
o 2. Connect an earth ground wire between
terminal 9 of terminal block TB2 and an
unpainted metal surface of the control panel to
ensure a good ground connection. Secure the
terminal screw. Make sure the control panel itself
is properly grounded.
230 VAC Input
Refer to Figure 2b for 230 VAC power input
connection.
o1. Remove the factory installed jumpers from
terminals 4 & 5 and 6 & 7 of terminal block TB2
located in the base of the TCS-200-1 enclosure.
o2. Connect one of the jumpers to terminals 5
and 6 of terminal block TB2 and discard the
spare jumper.
o 3. Connect the 230 VAC power to terminals 4
& 8 of terminal block TB2. Secure the terminal
screws.
o 4. Connect an earth ground wire between
terminal 9 of terminal block TB2 and an
unpainted metal surface of the control panel to
ensure a good ground connection. Secure the
terminal screw. Make sure the panel itself is
properly grounded.
1
2
3
4
5
JP1
SEE FIG. 3
FOR THIS
JUMPER
LOCATION
REMOVE
THIS JUMPER
JP1-4 AND 5
FOR ANALOG
INPUT
TB1 1 2 3 4 5 6 7 8 9 10 11
STOP
STOP
SIGNAL
COMMON
OFF
RUN
+15V
OFF
SIGNAL
TB1 1 2 3 4 5 6 7 8 9 10 11
ISO
COMMON
4-20mA
4-20mA
INPUT
-+
TB1 1 2 3 4 5 6 7 8 9 10 11
ISO
COMMON
15-35V
15-35VDC
ISOLATION
SUPPLY
-+
TB1 1 2 3 4 5 6 7 8 9 10 11
ISO
COMMON
0-10VDC
0-10VDC
INPUT
-+
PI:1000Ω, 1/2 WATT,
10% TOLERANCE,
0.5% LINEARITY,
LINEAR TAPER
TB1 1 2 3 4 5 6 7 8 9 10 11
PI
REMOTE
POT
WIPER
COMMON
PI:1000Ω, 1/2 WATT,
10% TOLERANCE,
0.5% LINEARITY,
LINEAR TAPER
TB1 1 2 3 4 5 6 7 8 9 10 11
PI
ROLL
FOLLOWER
WIPER
COMMON
PLACE JUMPER
HERE FOR
2 WIRE TENSION
BRAKES 1
2
3
4
5
JP1
1
2
3
4
5
6
7
8
9
TB2
BRAKE
BRAKE
SENSE
BRAKE
RETURN
DO NOT WIRE
ANY MAGNETS
ON TB2, 1.
!CAUTION
#1 RED
1
2
3
4
5
6
7
8
9
TB2
RED
BLK
2 THRU 16
BRAKE
MAGNETS
BRAKE
SENSE
BRAKE
RETURN
DO NOT WIRE MORE
THAN ONE MAGNET
BETWEEN TERMINALS
TB2, 1 AND TB2, 3.
!
1
2
3
4
5
JP1
CAUTION
NEUTRAL
1
2
3
4
5
6
7
8
9
115 VAC
HOT
TB2
NEUTRAL
1
2
3
4
5
6
7
8
9
230 VAC
HOT
TB2
FACTORY
INSTALLED
JUMPERS
INSTALL
JUMPER
SEE FIG. 5
FOR JUMPER
REMOVAL.
INSTALL THIS
JUMPER FOR
APPLICATIONS
NOT USING
ANALOG INPUTS.
SEE FIG. 5
FOR JUMPER
REMOVAL.
INSTALL THIS
JUMPER FOR
APPLICATIONS
NOT USING
ANALOG INPUTS.
PLACE JUMPER
HERE FOR
ELECTRO DISC
BRAKES
1
2
3
4
5
JP1
SEE FIG. 3
FOR THIS
JUMPER
LOCATION
REMOVE
THIS JUMPER
JP1-4 AND 5
FOR ANALOG
INPUT
GNDGND
CW CW
a. 115 AC Power Wiring b: 230 VAC Power Wiring
Figure 2
Note: Do not apply power to the system at this point.
Brake
Determine the type of brake to be used with this
control and proceed to that section of this manual.
Insure connections are tightly secured.
Intermittent connection will cause the control to shut
down and output current to the brake will be
removed.
Electro Disc Tension Brake
Refer to Figure 3a for the Electro Disc Tension Brake
wiring connections.
o1. Connect the red wire from one brake
magnet to terminal 1 of terminal block TB2 of the
TCS-200-1. This becomes the sense magnet.

8Warner Electric • 800-825-9050 P-2003-2 • 819-0420
o2. In a system with more than one magnet,
connect the remaining red wires from magnets 2
through 16 to terminal 2 of terminal block TB2 of
the TCS-200-1.
o 3. Connect all black magnet wires to terminal 3
of terminal block TB2 of the TCS-200-1.
Note: Magnets of the Electro Disc tension brake
must be properly connected, otherwise the control
system will not function properly.
All Other 2 Wire Tension Brakes
To connect all other 2-wire tension brakes [Warner
Electric’s Magnetic Particle Brakes, Precision
Torque Magnetic Particle Brakes, TB series brakes,
or Advanced Technology (AT) tension brakes],
refer to Figure 3b for 2-wire tension brakes wiring
connections.
o1. Connect one wire from the brake magnet to
terminal 2 of terminal block TB2 of the TCS-200-
1. Secure the terminal screw.
o 2. Connect the second wire from the brake
magnet to terminal 3 of terminal block TB2 of the
TCS-200-1. Secure the terminal screw.
o 3. Locate the five position jumper in the inside
cover of the TCS-200-1. Move the 2-position
black selector jumper from positions 1 & 2 to 2
& 3. This allows the control to operate without a
brake sense magnet.
Remote Torque Adjust Input (Optional)
Refer to Figure 4a for remote torque adjust input
connections.
o 1. Wire a three conductor shielded cable to the
remote sensor potentiometer previously installed.
Note: Using a shielded cable with wire colors
red, black, and green is recommended to simplify
potentiometer and terminal connections:
a. Black wire to low resistance end terminal of
potentiometer.
b. Red wire to high resistance end terminal of
potentiometer.
c. Green wire to wiper terminal of potentiometer.
Do not connect the shield lead of
the cable at the potentiometer end. Cut the
shield lead off at this end.
o 2. Route the cable from the sensor potentiometer
to the control, keeping the cable segregated from
high voltage AC power lines and other wiring that
may cause noise transients.
o 3. Connect the black wire from the low resistance
end of the remote potentiometer to terminal 11
of terminal block TB1 in the TCS-200-1. Snug
terminal only.
o 4. Connect the green wire from the wiper of the
remote potentiometer to terminal 9 of terminal
block TB1 in the TCS-200-1. Secure the terminal
screw.
1
2
3
4
5
JP1
SEE FIG. 3
FOR THIS
JUMPER
LOCATION
REMOVE
THIS JUMPER
JP1-4 AND 5
FOR ANALOG
INPUT
TB1 1 2 3 4 5 6 7 8 9 10 11
STOP
STOP
SIGNAL
COMMON
OFF
RUN
+15V
OFF
SIGNAL
TB1 1 2 3 4 5 6 7 8 9 10 11
ISO
COMMON
4-20mA
4-20mA
INPUT
-+
TB1 1 2 3 4 5 6 7 8 9 10 11
ISO
COMMON
15-35V
15-35VDC
ISOLATION
SUPPLY
-+
TB1 1 2 3 4 5 6 7 8 9 10 11
ISO
COMMON
0-10VDC
0-10VDC
INPUT
-+
PI:1000Ω, 1/2 WATT,
10% TOLERANCE,
0.5% LINEARITY,
LINEAR TAPER
TB1 1 2 3 4 5 6 7 8 9 10 11
PI
REMOTE
POT
WIPER
COMMON
PI:1000Ω, 1/2 WATT,
10% TOLERANCE,
0.5% LINEARITY,
LINEAR TAPER
TB1 1 2 3 4 5 6 7 8 9 10 11
PI
ROLL
FOLLOWER
WIPER
COMMON
PLACE JUMPER
HERE FOR
2 WIRE TENSION
BRAKES 1
2
3
4
5
JP1
1
2
3
4
5
6
7
8
9
TB2
BRAKE
BRAKE
SENSE
BRAKE
RETURN
DO NOT WIRE
ANY MAGNETS
ON TB2, 1.
!CAUTION
#1 RED
1
2
3
4
5
6
7
8
9
TB2
RED
BLK
2 THRU 16
BRAKE
MAGNETS
BRAKE
SENSE
BRAKE
RETURN
DO NOT WIRE MORE
THAN ONE MAGNET
BETWEEN TERMINALS
TB2, 1 AND TB2, 3.
!
1
2
3
4
5
JP1
CAUTION
NEUTRAL
1
2
3
4
5
6
7
8
9
115 VAC
HOT
TB2
NEUTRAL
1
2
3
4
5
6
7
8
9
230 VAC
HOT
TB2
FACTORY
INSTALLED
JUMPERS
INSTALL
JUMPER
SEE FIG. 5
FOR JUMPER
REMOVAL.
INSTALL THIS
JUMPER FOR
APPLICATIONS
NOT USING
ANALOG INPUTS.
SEE FIG. 5
FOR JUMPER
REMOVAL.
INSTALL THIS
JUMPER FOR
APPLICATIONS
NOT USING
ANALOG INPUTS.
PLACE JUMPER
HERE FOR
ELECTRO DISC
BRAKES
1
2
3
4
5
JP1
SEE FIG. 3
FOR THIS
JUMPER
LOCATION
REMOVE
THIS JUMPER
JP1-4 AND 5
FOR ANALOG
INPUT
GNDGND
CW CW
Electro disc tension braking system
Figure 3a.
1
2
3
4
5
JP1
SEE FIG. 3
FOR THIS
JUMPER
LOCATION
REMOVE
THIS JUMPER
JP1-4 AND 5
FOR ANALOG
INPUT
TB1 1 2 3 4 5 6 7 8 9 10 11
STOP
STOP
SIGNAL
COMMON
OFF
RUN
+15V
OFF
SIGNAL
TB1 1 2 3 4 5 6 7 8 9 10 11
ISO
COMMON
4-20mA
4-20mA
INPUT
-+
TB1 1 2 3 4 5 6 7 8 9 10 11
ISO
COMMON
15-35V
15-35VDC
ISOLATION
SUPPLY
-+
TB1 1 2 3 4 5 6 7 8 9 10 11
ISO
COMMON
0-10VDC
0-10VDC
INPUT
-+
PI:1000Ω, 1/2 WATT,
10% TOLERANCE,
0.5% LINEARITY,
LINEAR TAPER
TB1 1 2 3 4 5 6 7 8 9 10 11
PI
REMOTE
POT
WIPER
COMMON
PI:1000Ω, 1/2 WATT,
10% TOLERANCE,
0.5% LINEARITY,
LINEAR TAPER
TB1 1 2 3 4 5 6 7 8 9 10 11
PI
ROLL
FOLLOWER
WIPER
COMMON
PLACE JUMPER
HERE FOR
2 WIRE TENSION
BRAKES 1
2
3
4
5
JP1
1
2
3
4
5
6
7
8
9
TB2
BRAKE
BRAKE
SENSE
BRAKE
RETURN
DO NOT WIRE
ANY MAGNETS
ON TB2, 1.
!CAUTION
#1 RED
1
2
3
4
5
6
7
8
9
TB2
RED
BLK
2 THRU 16
BRAKE
MAGNETS
BRAKE
SENSE
BRAKE
RETURN
DO NOT WIRE MORE
THAN ONE MAGNET
BETWEEN TERMINALS
TB2, 1 AND TB2, 3.
!
1
2
3
4
5
JP1
CAUTION
NEUTRAL
1
2
3
4
5
6
7
8
9
115 VAC
HOT
TB2
NEUTRAL
1
2
3
4
5
6
7
8
9
230 VAC
HOT
TB2
FACTORY
INSTALLED
JUMPERS
INSTALL
JUMPER
SEE FIG. 5
FOR JUMPER
REMOVAL.
INSTALL THIS
JUMPER FOR
APPLICATIONS
NOT USING
ANALOG INPUTS.
SEE FIG. 5
FOR JUMPER
REMOVAL.
INSTALL THIS
JUMPER FOR
APPLICATIONS
NOT USING
ANALOG INPUTS.
PLACE JUMPER
HERE FOR
ELECTRO DISC
BRAKES
1
2
3
4
5
JP1
SEE FIG. 3
FOR THIS
JUMPER
LOCATION
REMOVE
THIS JUMPER
JP1-4 AND 5
FOR ANALOG
INPUT
GNDGND
CW CW
All other 2 wire tension brake wiring
Figure 3b.

Warner Electric • 800-825-9050 P-2003-2 • 819-0420 9
o 5. Connect the red wire from the high resistance
end of the remote potentiometer to terminal 7 of
terminal block TB1 of the TCS-200-1. Secure the
terminal screw.
o 6. Connect the shield lead from the cable to
terminal 11 of terminal block TB1 of the
TCS-200-1. Secure the terminal screw.
Roll Follower Adjust Input (Optional)
Refer to Figure 4b for roll follower adjust input
connections.
o 1. Wire a three conductor shielded cable to the
roll follower potentiometer previously installed.
Note: Using a shielded cable with wire colors
red, black, and green is recommended to simplify
potentiometer and terminal connections:
a. Black wire to low resistance end terminal of
potentiometer.
b. Red wire to high resistance end terminal of
potentiometer.
c. Green wire to wiper terminal of potentiometer.
o 2. Route the cable from the sensor potentiometer
to the control, keeping the cable segregated from
high voltage AC Power lines and other wiring that
may cause noise transients.
o 3. Connect the black wire from the low resistance
end of the roll follower potentiometer to terminal
11 of terminal block TB1 of the TCS-200-1. Do
not tighten the terminal screw. Snug down only.
o 4. Connect the green wire from the wiper of
the roll follower potentiometer to terminal 9 of
terminal block TB1 of the TCS-200-1. Secure
the terminal screw.
o 5. Connect the red wire from the high resistance
end of the roll follower potentiometer to terminal
8 of terminal block TB1 of the TCS200-1. Secure
the terminal screw.
o 6. Connect the shield lead from the cable to
terminal 11 of terminal block TB1 on the
TCS-200-1. Secure the terminal screw.
Remote Mode Selector Switch (Optional)
Refer to Figure 5a for the remote mode selector
switch connections.
o 1. Install selector switch at a convenient location.
o 2. Wire a three conductor shielded cable to the
external mode selector switch.
Note: It is recommended that a shielded cable with
wire colors of red, black, and green be used as this
will simplify switch and terminal connections.
a. Black wire to common contacts of both switch
poles.
b. Red wire to normally open contact for “on” or
“stop” pole.
c. Green wire to normally open contact for “off”
pole.
1
2
3
4
5
JP1
SEE FIG. 3
FOR THIS
JUMPER
LOCATION
REMOVE
THIS JUMPER
JP1-4 AND 5
FOR ANALOG
INPUT
TB1 1 2 3 4 5 6 7 8 9 10 11
STOP
STOP
SIGNAL
COMMON
OFF
RUN
+15V
OFF
SIGNAL
TB1 1 2 3 4 5 6 7 8 9 10 11
ISO
COMMON
4-20mA
4-20mA
INPUT
-+
TB1 1 2 3 4 5 6 7 8 9 10 11
ISO
COMMON
15-35V
15-35VDC
ISOLATION
SUPPLY
-+
TB1 1 2 3 4 5 6 7 8 9 10 11
ISO
COMMON
0-10VDC
0-10VDC
INPUT
-+
PI:1000Ω, 1/2 WATT,
10% TOLERANCE,
0.5% LINEARITY,
LINEAR TAPER
TB1 1 2 3 4 5 6 7 8 9 10 11
PI
REMOTE
POT
WIPER
COMMON
PI:1000Ω, 1/2 WATT,
10% TOLERANCE,
0.5% LINEARITY,
LINEAR TAPER
TB1 1 2 3 4 5 6 7 8 9 10 11
PI
ROLL
FOLLOWER
WIPER
COMMON
PLACE JUMPER
HERE FOR
2 WIRE TENSION
BRAKES 1
2
3
4
5
JP1
1
2
3
4
5
6
7
8
9
TB2
BRAKE
BRAKE
SENSE
BRAKE
RETURN
DO NOT WIRE
ANY MAGNETS
ON TB2, 1.
!CAUTION
#1 RED
1
2
3
4
5
6
7
8
9
TB2
RED
BLK
2 THRU 16
BRAKE
MAGNETS
BRAKE
SENSE
BRAKE
RETURN
DO NOT WIRE MORE
THAN ONE MAGNET
BETWEEN TERMINALS
TB2, 1 AND TB2, 3.
!
1
2
3
4
5
JP1
CAUTION
NEUTRAL
1
2
3
4
5
6
7
8
9
115 VAC
HOT
TB2
NEUTRAL
1
2
3
4
5
6
7
8
9
230 VAC
HOT
TB2
FACTORY
INSTALLED
JUMPERS
INSTALL
JUMPER
SEE FIG. 5
FOR JUMPER
REMOVAL.
INSTALL THIS
JUMPER FOR
APPLICATIONS
NOT USING
ANALOG INPUTS.
SEE FIG. 5
FOR JUMPER
REMOVAL.
INSTALL THIS
JUMPER FOR
APPLICATIONS
NOT USING
ANALOG INPUTS.
PLACE JUMPER
HERE FOR
ELECTRO DISC
BRAKES
1
2
3
4
5
JP1
SEE FIG. 3
FOR THIS
JUMPER
LOCATION
REMOVE
THIS JUMPER
JP1-4 AND 5
FOR ANALOG
INPUT
GNDGND
CW
CW
1
2
3
4
5
JP1
SEE FIG. 3
FOR THIS
JUMPER
LOCATION
REMOVE
THIS JUMPER
JP1-4 AND 5
FOR ANALOG
INPUT
TB1 1 2 3 4 5 6 7 8 9 10 11
STOP
STOP
SIGNAL
COMMON
OFF
RUN
+15V
OFF
SIGNAL
TB1 1 2 3 4 5 6 7 8 9 10 11
ISO
COMMON
4-20mA
4-20mA
INPUT
-+
TB1 1 2 3 4 5 6 7 8 9 10 11
ISO
COMMON
15-35V
15-35VDC
ISOLATION
SUPPLY
-+
TB1 1 2 3 4 5 6 7 8 9 10 11
ISO
COMMON
0-10VDC
0-10VDC
INPUT
-+
PI:1000Ω, 1/2 WATT,
10% TOLERANCE,
0.5% LINEARITY,
LINEAR TAPER
TB1 1 2 3 4 5 6 7 8 9 10 11
PI
REMOTE
POT
WIPER
COMMON
PI:1000Ω, 1/2 WATT,
10% TOLERANCE,
0.5% LINEARITY,
LINEAR TAPER
TB1 1 2 3 4 5 6 7 8 9 10 11
PI
ROLL
FOLLOWER
WIPER
COMMON
PLACE JUMPER
HERE FOR
2 WIRE TENSION
BRAKES 1
2
3
4
5
JP1
1
2
3
4
5
6
7
8
9
TB2
BRAKE
BRAKE
SENSE
BRAKE
RETURN
DO NOT WIRE
ANY MAGNETS
ON TB2, 1.
!CAUTION
#1 RED
1
2
3
4
5
6
7
8
9
TB2
RED
BLK
2 THRU 16
BRAKE
MAGNETS
BRAKE
SENSE
BRAKE
RETURN
DO NOT WIRE MORE
THAN ONE MAGNET
BETWEEN TERMINALS
TB2, 1 AND TB2, 3.
!
1
2
3
4
5
JP1
CAUTION
NEUTRAL
1
2
3
4
5
6
7
8
9
115 VAC
HOT
TB2
NEUTRAL
1
2
3
4
5
6
7
8
9
230 VAC
HOT
TB2
FACTORY
INSTALLED
JUMPERS
INSTALL
JUMPER
SEE FIG. 5
FOR JUMPER
REMOVAL.
INSTALL THIS
JUMPER FOR
APPLICATIONS
NOT USING
ANALOG INPUTS.
SEE FIG. 5
FOR JUMPER
REMOVAL.
INSTALL THIS
JUMPER FOR
APPLICATIONS
NOT USING
ANALOG INPUTS.
PLACE JUMPER
HERE FOR
ELECTRO DISC
BRAKES
1
2
3
4
5
JP1
SEE FIG. 3
FOR THIS
JUMPER
LOCATION
REMOVE
THIS JUMPER
JP1-4 AND 5
FOR ANALOG
INPUT
GNDGND
CW
CW
Remote torque adjust input
Figure 4a
Roll follower adjust input
Figure 4b

10 Warner Electric • 800-825-9050 P-2003-2 • 819-0420
Do not connect the shield lead of
the cable at the switch contacts. Cut the
shield lead off at this end.
o 3. Route the remote mode switch cable to the
control, keeping the cable segregated from high
voltage AC power lines and other control wiring
that may cause noise transients.
o 4. Connect the black wire from the switch
common contacts of the remote mode switch to
terminal 10 of terminal block TB1 of the
TCS-200-1. Tighten the screw.
o 5. Connect the red wire from the normally open
contact for the “on” or “stop” position of the
remote mode switch to terminal 5 of terminal
block TB1 of the TCS-200-1. Tighten the screw.
o 6. Connect the green wire from the normally
open contact for the “off” position of the remote
mode switch to terminal 6 of terminal block TB1
of the TCS-200-1. Tighten the screw.
o 7. Connect the shield wire from the cable to
terminal 11 of terminal block TB1 of the
TCS-200-1. Securely tighten the screw.
The TCS-200 Tension Control has now been wired
for operation. Before applying power to the system,
double check the wiring and installation for proper
connection. After this check has been completed,
proceed to the start-up and adjustment section of
this manual.
Analog Input (Optional)
Two options for the analog input signal are available.
These include 0-10 VDC or 4-20 mA signal.
Determine which signal will be supplied and refer
to the proper section of this manual below. Also,
determine if this input needs to be isolated from the
control ground. For example, if a PLC is used, this
input must be isolated. Then refer to the Isolation
section of this manual.
Note: A shielded cable is recommended for the 0-10
VDC or 4-20 mA input to insure a good signal.
0-10 VDC
Refer to Figure 5b for the 0-10 VDC analog input
connections.
1
2
3
4
5
JP1
SEE FIG. 3
FOR THIS
JUMPER
LOCATION
REMOVE
THIS JUMPER
JP1-4 AND 5
FOR ANALOG
INPUT
TB1 1 2 3 4 5 6 7 8 9 10 11
STOP
STOP
SIGNAL
COMMON
OFF
RUN
+15V
OFF
SIGNAL
TB1 1 2 3 4 5 6 7 8 9 10 11
ISO
COMMON
4-20mA
4-20mA
INPUT
-+
TB1 1 2 3 4 5 6 7 8 9 10 11
ISO
COMMON
15-35V
15-35VDC
ISOLATION
SUPPLY
-+
TB1 1 2 3 4 5 6 7 8 9 10 11
ISO
COMMON
0-10VDC
0-10VDC
INPUT
-+
PI:1000Ω, 1/2 WATT,
10% TOLERANCE,
0.5% LINEARITY,
LINEAR TAPER
TB1 1 2 3 4 5 6 7 8 9 10 11
PI
REMOTE
POT
WIPER
COMMON
PI:1000Ω, 1/2 WATT,
10% TOLERANCE,
0.5% LINEARITY,
LINEAR TAPER
TB1 1 2 3 4 5 6 7 8 9 10 11
PI
ROLL
FOLLOWER
WIPER
COMMON
PLACE JUMPER
HERE FOR
2 WIRE TENSION
BRAKES 1
2
3
4
5
JP1
1
2
3
4
5
6
7
8
9
TB2
BRAKE
BRAKE
SENSE
BRAKE
RETURN
DO NOT WIRE
ANY MAGNETS
ON TB2, 1.
!CAUTION
#1 RED
1
2
3
4
5
6
7
8
9
TB2
RED
BLK
2 THRU 16
BRAKE
MAGNETS
BRAKE
SENSE
BRAKE
RETURN
DO NOT WIRE MORE
THAN ONE MAGNET
BETWEEN TERMINALS
TB2, 1 AND TB2, 3.
!
1
2
3
4
5
JP1
CAUTION
NEUTRAL
1
2
3
4
5
6
7
8
9
115 VAC
HOT
TB2
NEUTRAL
1
2
3
4
5
6
7
8
9
230 VAC
HOT
TB2
FACTORY
INSTALLED
JUMPERS
INSTALL
JUMPER
SEE FIG. 5
FOR JUMPER
REMOVAL.
INSTALL THIS
JUMPER FOR
APPLICATIONS
NOT USING
ANALOG INPUTS.
SEE FIG. 5
FOR JUMPER
REMOVAL.
INSTALL THIS
JUMPER FOR
APPLICATIONS
NOT USING
ANALOG INPUTS.
PLACE JUMPER
HERE FOR
ELECTRO DISC
BRAKES
1
2
3
4
5
JP1
SEE FIG. 3
FOR THIS
JUMPER
LOCATION
REMOVE
THIS JUMPER
JP1-4 AND 5
FOR ANALOG
INPUT
GNDGND
CW CW
1
2
3
4
5
JP1
SEE FIG. 3
FOR THIS
JUMPER
LOCATION
REMOVE
THIS JUMPER
JP1-4 AND 5
FOR ANALOG
INPUT
TB1 1 2 3 4 5 6 7 8 9 10 11
STOP
STOP
SIGNAL
COMMON
OFF
RUN
+15V
OFF
SIGNAL
TB1 1 2 3 4 5 6 7 8 9 10 11
ISO
COMMON
4-20mA
4-20mA
INPUT
-+
TB1 1 2 3 4 5 6 7 8 9 10 11
ISO
COMMON
15-35V
15-35VDC
ISOLATION
SUPPLY
-+
TB1 1 2 3 4 5 6 7 8 9 10 11
ISO
COMMON
0-10VDC
0-10VDC
INPUT
-+
PI:1000Ω, 1/2 WATT,
10% TOLERANCE,
0.5% LINEARITY,
LINEAR TAPER
TB1 1 2 3 4 5 6 7 8 9 10 11
PI
REMOTE
POT
WIPER
COMMON
PI:1000Ω, 1/2 WATT,
10% TOLERANCE,
0.5% LINEARITY,
LINEAR TAPER
TB1 1 2 3 4 5 6 7 8 9 10 11
PI
ROLL
FOLLOWER
WIPER
COMMON
PLACE JUMPER
HERE FOR
2 WIRE TENSION
BRAKES 1
2
3
4
5
JP1
1
2
3
4
5
6
7
8
9
TB2
BRAKE
BRAKE
SENSE
BRAKE
RETURN
DO NOT WIRE
ANY MAGNETS
ON TB2, 1.
!CAUTION
#1 RED
1
2
3
4
5
6
7
8
9
TB2
RED
BLK
2 THRU 16
BRAKE
MAGNETS
BRAKE
SENSE
BRAKE
RETURN
DO NOT WIRE MORE
THAN ONE MAGNET
BETWEEN TERMINALS
TB2, 1 AND TB2, 3.
!
1
2
3
4
5
JP1
CAUTION
NEUTRAL
1
2
3
4
5
6
7
8
9
115 VAC
HOT
TB2
NEUTRAL
1
2
3
4
5
6
7
8
9
230 VAC
HOT
TB2
FACTORY
INSTALLED
JUMPERS
INSTALL
JUMPER
SEE FIG. 5
FOR JUMPER
REMOVAL.
INSTALL THIS
JUMPER FOR
APPLICATIONS
NOT USING
ANALOG INPUTS.
SEE FIG. 5
FOR JUMPER
REMOVAL.
INSTALL THIS
JUMPER FOR
APPLICATIONS
NOT USING
ANALOG INPUTS.
PLACE JUMPER
HERE FOR
ELECTRO DISC
BRAKES
1
2
3
4
5
JP1
SEE FIG. 3
FOR THIS
JUMPER
LOCATION
REMOVE
THIS JUMPER
JP1-4 AND 5
FOR ANALOG
INPUT
GNDGND
CW CW
a. Remote mode selector switch b. 0-10v analog input
c. 4-20m A analog input
Figure 5
d. Isolation power supply

Warner Electric • 800-825-9050 P-2003-2 • 819-0420 11
o 1. Connect the positive lead of the 0-10 VDC
input to terminal 3 of terminal block TB1.
Securely tighten the screw.
o 2. Connect the negative lead of the 0-10 VDC
input to terminal 2 of terminal block TB1. Snug
terminal only.
o 3. Connect the shield wire to terminal 2 of
terminal block TB1. Securely tighten the screw.
o 4. Locate the five-position jumper mounted on
the board on the inside cover of the TCS-200-1.
Remove the two position black selector from
positions 4 & 5 of jumper JP1 and discard.
4-20 mA
Refer to Figure 5c for the 4-20 mA Analog input
connections.
o 1. Connect the positive lead of the 4-20 mA input
to terminal 4 of terminal block TB1. Securely
tighten the screw.
o 2. Connect the negative lead of the 4-20 mA
input to terminal 2 of terminal block TB1. Snug
terminal only.
o 3. Connect the shield wire to terminal 2 of
terminal block TB1. Securely tighten the screw.
o 4. Locate the five-position jumper mounted on
the board on the inside front cover of the
TCS-200-1. Remove the two position black
selector from positions 4 & 5 of jumper JP1 and
discard.
Isolation Power Supply
Refer to Figure 5d for analog input isolation power
supply connections.
Note: To isolate the analog input from the TCS-200-1
control ground, a separate 15-35 VDC voltage supply
is needed.
o 1. Connect the positive side of the 15-35 VDC
external voltage supply to terminal 1 of terminal
block TB1. Securely tighten the screw.
o 2. Connect the negative side of the 15-35 VDC
external voltage supply to terminal 2 of terminal
block TB1. Securely tighten the screw.
System Start-Up and Adjustment
Manual Tension Adjust (Front Panel)
o 1. Apply power to the control system.
o 2. Check that the green LED marked “power” is
illuminated.
o 3. Using an AC voltmeter, measure the AC input
voltage at terminals 4 and 8 of terminal block
TB2. This voltage should be 115 or 230 VAC,
depending on the voltage chosen.
o 4. Remove power from the control system and
wait approximately 30 seconds before proceeding
to the next step.
Electro Disc Tension Brake
Note: If you are not using electro disc tension brakes,
proceed to step 5 under all other 2 wire tension
brakes section.
o 5. Remove the sense magnet lead from terminal
1 of terminal block TB2 and insert a DC current
meter between the lead of the sense magnet
and terminal 1 of terminal block TB2. Note: Use
a DC current meter that reads 0 to 500 mA with
the Positive (+) lead connected to terminal 1 and
negative (-) lead connected to the wire.
o 6. Reapply power to the control system.
o 7. Place the mode selector switch in the brake
“off” position. The meter should read zero current
and the brake should free wheel.
o 8. Place the mode selector switch in the brake
“on” or “stop” position. The meter should read
345 to 375 mA and the brake should be locked.

12 Warner Electric • 800-825-9050 P-2003-2 • 819-0420
o 9. Place the mode selector switch in the “run”
position and set the tension adjust potentiometer
to zero (or fully counterclockwise). The meter
should read zero current output to the brake.
o 10. Slowly rotate the tension adjust
potentiometer from fully counterclockwise to fully
clockwise, noting that the output current
increases from zero to 345-375 mA at maximum
output.
o 11. This concludes checkout of the control
system. Remove power and allow approximately
30 seconds before proceeding to the next step.
o 12. Remove the meter and reattach the sense
magnet lead to terminal 1 of terminal block TB2
and secure the lead. Proceed to step 13.
All other 2 wire tension brakes
o 5. Attach a DC voltmeter to terminals 2 and 3 of
terminal block TB2.
Note: A DC voltmeter with the capability of reading 0
to 24 VDC should be used. Positive (+) to terminal 2
and negative (-) to terminal 3.
o 6. Reapply power to the control system.
o 7. Place mode selector switch in the brake “off”
position. The meter should read zero voltage and
the brake armature should be free-wheeling.
o 8. Place mode selector switch in the brake “stop”
position. The meter should read approximately 24
VDC and the brake should be locked up tight.
o 9. Place mode selector switch in the brake “run”
position and set the tension adjust potentiometer
to zero or full counterclockwise position. The
meter should read zero output voltage to the
brake.
o 10. Slowly rotate the tension adjust potentiometer
from fully counterclockwise to full clockwise,
noting the output voltage increases from zero to
approximately 24 VDC at maximum output.
o 11. This concludes check-out of the control
system. Remove power and allow approximately
30 seconds before proceeding to the next step.
o 12. Remove the meter from terminals 2 and 3 of
terminal block TB2 and secure.
o 13. Reapply power to the control system.
o 14. Adjust the tension potentiometer for the
desired brake level required for operation.
Note: If start-up and adjustment procedures
do not produce the desired results, consult the
troubleshooting section of this manual.
o 15. If a remote mode selector switch is used,
repeat steps 5 through 13 using the remote
mode selector switch.
o 16. Close the cover to the control chassis using
the cover screw supplied with the control.
Remote Tension Adjust
o 1. Apply power to the control system.
o 2. Check that the green LED marked “power” is
illuminated.
o 3. Using an AC voltmeter, measure the voltage
at terminals 4 and 8 of terminal block TB2. This
should be approximately 115 VAC or 230 VAC,
depending on the input voltage chosen.
o 4. Remove power from the control system
and wait approximately 30 seconds before
proceeding to the next step.
Electro Disc Tension Brake
Note: If you are not using electro disc tension brakes,
proceed to step 5 under all other 2 wire tension brake
section.

Warner Electric • 800-825-9050 P-2003-2 • 819-0420 13
o 5. Remove the sense magnet lead from terminal
1 of terminal block TB2 and insert a DC current
meter in series with the lead of the sense magnet
and terminal 1 of terminal block TB2.
Note: Use a DC current meter that reads 0 to 500
mA with the Positive (+) lead connected to terminal 1
and negative (-) lead connected to the wire.
o 6. Reapply power to the control system.
o 7. Place the mode selector switch in the brake
“off” position. The meter should read zero output
current and the brake should free wheel.
o 8. Place the mode selector switch in the brake
“on” or “stop” position. The meter should read
345 to 375 mA and the brake should be locked.
o 9. Place the mode selector switch in the “run”
position and set the tension adjust potentiometer
to zero (or fully counterclockwise). The meter
should read zero current output to the brake.
o 10. Slowly rotate the remote tension adjust
potentiometer from fully counterclockwise to
full clockwise, noting that the output current
increases from zero to 345-375 mA at maximum
output. Leave this potentiometer at its maximum
setting.
o 11. Slowly rotate the front panel tension adjust
potentiometer from its fully clockwise, or
maximum setting, to its fully counterclockwise, or
minimum setting. Monitor the meter, observing
that the current goes from 345 - 375 mA to zero
at the minimum setting.
o 12. This concludes the control system checks.
Remove power and allow approximately 30
seconds before proceeding to the next step.
o 13. Remove the meter and reattach the sense
magnet lead to terminal 1 of terminal block TB2
and secure it.
Proceed to step 14 in next section.
All Other Two Wire Tension Brakes
o 5. Attach a DC voltmeter to terminals 2 and 3 of
terminal block TB2.
Note: Use A DC voltmeter that reads from 0 to 24
VDC. Connect the positive (+) lead to terminal 2 and
negative (-) lead to terminal 3.
o 6. Reapply power to the control system.
o 7. Place the mode selector switch in the brake
“off” position. The meter should read zero
voltage and the brake should free wheel.
o 8. Place the mode selector switch in the
brake “stop” position. The meter should read
approximately 24 VDC and the brake should be
locked.
o 9. Place the mode selector switch in the brake
“run” position and set the remote tension adjust
potentiometer to the zero, or fully counter-
clockwise, position. The meter should read zero
voltage output to the brake.
o 10. Slowly rotate the remote tension adjust
potentiometer from fully counterclockwise to
full clockwise, noting that the output voltage
increases from zero to approximately 24 VDC at
its maximum. Leave the potentiometer at its full
clockwise, or maximum, position.
o 11. Slowly rotate the front panel tension adjust
potentiometer from its fully clockwise, or
maximum setting, to its fully counterclockwise, or
minimum setting. Monitor the meter, observing
that the voltage goes from 24 VDC to zero at the
minimum setting.
o 12. This concludes the control system checks.
Remove power and allow approximately 30
seconds before proceeding to the next step.
o 13. Remove the meter from terminals 2 and 3 of
terminal block TB2 and secure the leads to the
terminals.
o 14. Reapply power to the control system.

14 Warner Electric • 800-825-9050 P-2003-2 • 819-0420
o 15. Adjust the front panel tension adjust
potentiometer to the maximum output level
required for the application. Now set the remote
tension adjust potentiometer between maximum
and zero.
Note: If start-up and adjustment procedures
do not produce the desired results, consult the
troubleshooting section of this manual.
o 16. If a remote mode selector switch is used,
repeat steps 5 through 13 using the remote
mode selector switch.
o 17. Close the control front cover and latch it by
tightening the screw that is provided.
Roll Follower Tension Adjust
o 1. Apply power to the control system.
o 2. Check that the green LED marked “power” is
illuminated.
o 3. Using an AC voltmeter, measure the AC input
voltage at terminals 4 and 8 of terminal block
TB2. This voltage should be approximately 115
or 230 VAC, depending on the voltage chosen.
o 4. Remove power from the control system
and wait approximately 30 seconds before
proceeding to the next step.
Electro Disc Tension Brake
Note: If you are not using electro disc tension brakes,
proceed to step 5 under all other 2 wire tension brake
section.
o 5. Remove the sense magnet lead from terminal
1 of terminal block TB2 and insert a DC current
meter in series with the lead of the sense magnet
and terminal 1 of terminal block TB2.
Note: Use a DC current meter that reads 0 to 500
mA with the positive (+) lead connected to terminal 1
and the negative (-) lead connected to the wire.
o 6. Reapply power to the control system.
o 7. Set the mode selector switch to the brake “off”
position. The meter should read zero current and
the brake should free wheel.
o 8. Place the mode selector switch in the brake
“stop” position. The meter should read 345 to
375 mA and the brake should be locked.
o 9. Place the mode selector switch in the
brake “run” position and set the tension adjust
potentiometer to its maximum (fully clockwise)
setting.
Note: Refer to Table 1 for various inputs and outputs
when using the roll follower system
o 10. Connect a second DC voltmeter between
terminals 9 and 11 of terminal block TB1.
Note: Use a DC voltmeter capable of measuring zero
to 10 volts DC.
o 11. With the roll follower potentiometer disconnected
from the roll follower arm, position the follower
arm to its true zero position, which should be the
centerline of the unwind spindle.
o 12. Adjust the roll follower potentiometer to a
zero voltage reading on the voltmeter which is
connected per step 10, page 14.
o 13. Connect the roll follower potentiometer to
the roll follower arm. After coupling the follower
arm to the potentiometer, recheck the voltage
between terminals 9 and 11 of terminal block
TB1 to insure the voltage is still zero VDC.
o 14. Place a full roll of material on the unwind
stand.
o 15. Set the roll follower arm on the unwind roll.
o 16. Check the voltage between terminals 9 and
11 of terminal block TB1 and refer to Table 1. If
the voltage reading is less than 0.8 VDC, refer to
Table 1 for the nominal output current available.

Warner Electric • 800-825-9050 P-2003-2 • 819-0420 15
Note: If maximum starting torque available is less
than the actual starting torque required, the amount
of angular travel of the roll follower potentiometer
must be increased.
If the voltage reading is greater than 1.3 VDC,
decrease the front panel tension adjust until a 2.5
VDC reading is obtained.
o 17. Set the front panel tension adjust for the
desired starting torque required for the
application.
o 18. Start the machine and draw the web through.
o 19. Monitor the voltage at terminals 9 and 11 of
terminal block TB1, as well as the brake current
on terminal 1 of terminal block TB2. As the roll
diameter decreases, the sensor voltage and the
brake current will decrease, keeping the tension
relatively constant.
o 20. After an initial run has been completed,
remove power from the system and wait
approximately 30 seconds before proceeding to
the next step.
o 21. Disconnect the meter from the sense magnet
lead to terminal block TB2. Tighten the lead
screws.
Proceed to step 23 in next section.
All Other Two Wire Tension Brakes
o 5. Connect a DC voltmeter between terminals 2
and 3 of terminal block TB2.
Note: Use a DC voltmeter that reads from 0 to 24
VDC. Connect the positive (+) lead to terminal 2 and
the negative (-) lead to terminal 3.
o 6. Reapply power to the control system.
o 7. Place the mode selector switch in the brake
“off” position. The meter should read zero
voltage and the brake should be free wheel.
o 8. Place the mode selector switch in the
brake “stop” position. The meter should read
approximately 24 VDC and the brake should be
locked.
o 9. Place the mode selector switch in the brake
“run” position and set the tension adjust
potentiometer to its maximum (fully clockwise)
setting.
Note: Refer to Table 1 for various inputs and outputs
when using the roll follower system.
o 10. Connect a second DC voltmeter between
terminals 9 and 11 of terminal block TB1.
Note: Use a DC voltmeter that measures zero to 10
VDC and connect the positive (+) lead to terminal 9
and the negative (-) lead to terminal 11.
o 11. With the roll follower potentiometer disconnected
from the roll follower arm, position the follower
arm to true zero, which should be the centerline
of the unwind spindle.
o 12. Adjust the roll follower potentiometer to zero
voltage on the voltmeter connected between
terminals 9 and 11 of terminal block TB1.
o 13. Connect the roll follower potentiometer to
the roll follower arm. After coupling the follower
arm to the potentiometer, recheck the voltage
between terminals 9 and 11 of terminal block
TB1 to insure that the voltage is still zero VDC.
o 14. Place a full roll of material on the unwind
stand.
o 15. Set the roll follower arm on the unwind roll.
o 16. Check the voltage between terminals 9 and
11 of terminal block TB1 and refer to Table 1. If
the voltage reading is less than 0.8 VDC, refer to
Table 1 for the nominal output voltage available.
Note: If maximum starting torque available is less
than the actual starting torque required, the amount
of angular travel of the roll follower potentiometer
must be increased. If the voltage reading is greater
than 1.3 VDC, decrease the front panel tension adjust
until a 1.3 VDC reading is obtained.

16 Warner Electric • 800-825-9050 P-2003-2 • 819-0420
o 17. Set the front panel tension adjust for the
starting torque required for the application.
o 18. Start the machine and draw the web through.
o 19. Monitor the voltage at terminals 9 and 11 of
terminal block TB1, as well as the brake voltage
at terminals 2 and 3 of terminal block TB2. As
the roll diameter decreases, the sensor and the
brake voltage will decrease, keeping the tension
relatively constant.
o 20. After an initial run has been completed,
remove power from the system and wait
approximately 30 seconds before proceeding to
the next step.
Note: If start-up and adjustment procedures do
not provide the desired results, consult the trouble
shooting section of this manual.
o 21. Remove the meter from terminals 2 and 3
of terminal block TB2 and tighten the terminal
screws.
o 22. Disconnect the second voltmeter used from
terminals 9 and 11 of terminal block TB1.
o 23. Reapply power to the control system.
o 24. If the remote mode selector switch is used,
repeat steps 5 through 21 using the remote
mode selector switch.
Note: If start-up and adjustment procedures do
not provide the desire results, consult the trouble-
shooting section of this manual.
o 25. Close the cover of the TCS-200-1 and latch it
by tightening the screw that is provided.
Analog Input
o 1. Apply power to the control system.
o 2. Check that the green LED marked “power” is
illuminated.
o 3. Using an AC voltmeter, measure the AC input
voltage at terminals 4 and 8 of terminal block
TB2. This voltage should be approximately 115
or 230 VAC, depending on the voltage chosen.
o 4. Remove power from the control system
and wait approximately 30 seconds before
proceeding to the next step.
Electro Disc Tension Brake
If you are not using electro disc tension brakes,
proceed to step 5 under “All other 2 wire tension
brake” section.
o 5. Remove the sense magnet lead from terminal
1 of terminal block TB2 and connect a DC
current meter that reads from 0 to 500 milliamps
between the lead of the sense magnet and
terminal 1 of terminal block TB2. Connect the
positive (+) lead to terminal 1.
o 6. Reapply the power to the control system.
o 7. Place the mode selector switch in the brake
“off” position. The meter should read zero current
and the brake should free wheel.
o 8. Place the mode selector switch in the brake
“run” position. The meter should read 345 to 375
mA and the brake should be locked.
o 9. Place the mode selector switch in the
brake “run” position and set the tension adjust
potentiometer to its maximum (fully clockwise)
setting.
Note: Refer to Table 2 and Table 3 for various inputs
and outputs when using the analog input system.
o 10. If using a 0-10 VDC input, connect a second
DC voltmeter capable of reading from zero to 10
VDC between terminals 3 and 2 of terminal block
TB1. Connect the positive (+) lead to terminal 3
and the negative (-) lead to terminal 2.

Warner Electric • 800-825-9050 P-2003-2 • 819-0420 17
If using a 4-20 mA input, remove the wire from
terminal 4 of terminal block TB1 and connect a
second DC current meter capable of reading zero
to 20 mA between this terminal and the positive
4-20 mA signal wire. Connect the positive (+) lead
to terminal 4 and the negative (-) lead to the wire.
o 11. Adjust the analog input to obtain a zero
voltage reading on the voltmeter connected
between terminals 3 and 2, or a 4 mA reading
on the current meter connected on terminal 4 of
terminal block TB1.
o 12. Place a full roll of material on the unwind
stand.
o 13. Set the front panel tension adjust for the
starting torque required for the application.
o 14. Start the machine and draw the web through.
o 15. Monitor the voltage at terminals 3 and 2 or
the current at terminal 4 of terminal block TB1, as
well as the brake current on terminal 1 of terminal
block TB2.
a. If using a sensor: As the roll diameter
decreases, the sensor voltage or current will
decrease which will cause the brake torque to
decrease, keeping the tension proportional to the
roll size.
b. If using a PLC: As the roll diameter decreases,
the analog signal from the PLC must decrease to
keep the tension proportional to the roll size.
o 16. After an initial run has been completed,
remove power from the system and wait
approximately 30 seconds before proceeding to
the next step.
o 17. Remove the meter from between the sense
magnet lead to terminal 1 of terminal block TB2
and tighten the terminal screw.
Proceed to step 19.
All Other Two Wire Tension Brakes
o 5. Attach a DC voltmeter capable of reading
zero to 24 VDC between terminals 2 and 3 of
terminal block TB2. Connect the positive (+) lead
to terminal 2 and the negative (-) lead to terminal 3.
o 6. Reapply power to the control system.
o 7. Place the mode selector switch in the brake
“off” position. The meter should read zero voltage
and the brake should free wheel.
o 8. Place the mode selector switch in the
brake “stop” position. The meter should read
approximately 24 VDC and the brake should be
locked.
o 9. Place the mode selector switch in the
brake “run” position and set the tension adjust
potentiometer to its maximum (fully clockwise)
setting.
Note: Refer to Table 2 and Table 3 for various inputs
and outputs when using the analog input system.
If using a 4-20 mA input, remove the wire from
terminal 4 of terminal block TB1 and connect a
second DC current meter capable of reading zero
to 20 mA between this terminal and the positive
4-20 mA signal wire. Connect the positive (+) lead to
terminal 4 and the negative (-) lead to the wire.
o 11. Adjust the analog input to obtain a zero
voltage reading on the voltmeter connected
between terminals 3 and 2, or a 4 mA reading
on the current meter connected on terminal 4 of
terminal block TB1.
o 12. Place a full roll of material on the unwind
stand.
o 13. Set the front panel tension adjust for the
starting torque required for the application.
o 14. Start the machine and draw the web through.

18 Warner Electric • 800-825-9050 P-2003-2 • 819-0420
o 15. Monitor the voltage at terminals 3 and 2 or
the current at terminal 4 of terminal block TB1, as
well as the brake current on terminal 1 of
terminal block TB2.
a. If using a sensor: As the roll diameter
decreases, the sensor voltage or current will
decrease which will cause the brake torque to
decrease, keeping the tension proportional to the
roll size.
b. If using a PLC: As the roll diameter
decreases, the analog signal from the PLC must
decrease to keep the tension proportional to the
roll size.
o 16. After an initial run has been completed,
remove power from the system and wait
approximately 30 seconds before proceeding to
the next step.
o 17. Remove the meter from between the sense
magnet lead to terminal 1 of terminal block TB2
and tighten the terminal screw.
o 18. Disconnect the second voltmeter from
terminals 2 and 3 of terminal block TB1.
o 19. Reapply power to the control system.
o 20. If the remote mode selector switch is used,
repeat steps 5 through 17, using the remote
mode selector switch.
Note: If start-up and adjustment procedures do
not provide the desired results, consult the
troubleshooting section of this manual.
o 21. Close the cover of the TCS-200-1 and latch
by tightening the screw that is provided.

Warner Electric • 800-825-9050 P-2003-2 • 819-0420 19
Table 1
Ω
Resistance Degrees
Input
Voltage
from Roll
Follower
Brakes
2-Wire Mode
MTB Brakes
3-Wire Mode
Output
Voltage
Current
Output
0 0 0 0 0
27.8 10 .062V 1.354 20mA
55.6 20 .150V 2.903 40mA
83.4 30 .256V 4.41 60mA
111.11 40 .368V 6.05 84mA
138.9 50 .464V 7.53 103mA
166.7 60 .578V 8.92 125mA
194.4 70 .681V 10.46 145mA
222.2 80 .795V 11.95 167mA
250 90 .888V 13.62 184mA
277.8 100 .998V 14.97 203mA
305.6 110 1.103V 16.47 222mA
333.3 120 1.200V 17.90 240mA
361.11 130 1.324V 19.44 255mA
Voltage Tables
Table 2
Analog Input
Voltage
Brakes
2-Wire Mode
MTB Brakes
3-Wire Mode
Voltage
On Brake
Current On
Brake Sense
0 0 0
1 3.7 50mA
2 6.9 90mA
3 9.9 140mA
4 13.5 180mA
5 16.1 220mA
6 19.3 260mA
7 22.5 290mA
8 25.5 330mA
9 27.2 350mA
10 27.2 350mA
Table 3
Current
Input
Brakes
2-Wire Mode
MTB Brakes
3-Wire Mode
Voltage
On Brake
Current On
Brake Sense
4mA 0 0
6mA 4.3 60mA
8mA 7.5 110m
10mA 10.7 160mA
12mA 14.2 200mA
14mA 17.4 240mA
16mA 20.7 280mA
18mA 23.8 320mA
20mA 27.1 350mA

20 Warner Electric • 800-825-9050 P-2003-2 • 819-0420
Troubleshooting
General: The chart below will be helpful when isolating exact problems that may occur in the control system. When
the system has been running for some time, the chart will also prove helpful when checking for worn, broken or
frayed wires; bent or broken control system parts; blown fuses; loose terminal connections and defective wire
connections.
Symptom A: Green LED indicator does not illuminate with power on
Probable Cause Solution
No power is applied to the control Check that AC power is on.
Fuse Blown Check fuse and replace if blown.
Symptom B: Red LED illuminates short circuit
Shorted magnet coil Check magnet coil resistance for approximately 66-68 ohms
cold for MTB’s. Coil resistance for 2-wire brakes, TB’s,
ATT’s and Magnetic Particle units will vary. Check resistance
specifications in Tension Catalog P-771 or appropriate
service manual.
Brake connections improperly wired Check wiring and rewire if necessary.
Transient Noise Check for source of noise and suppress.
Segregate wiring.
Used shielded cable.
Note: After checking control. Reset control by turning the switch to “off” and then to “run”.
Symptom C: Brake is not engaging
Mode switch in brake “off” position Set mode selector to “run” position.
Tension set at zero Increase tension adjust.
Remote mode switch in brake off position Set remote mode switch to “run” position.
Remote sensors incorrectly wired Check wiring and rewire if necessary.
No signal on analog inputs Check wiring and signal from PLC or ultrasonic sensor.
No power to control Refer to Symptom A.
Symptom D: Brake is not releasing
Mode switch in brake “on” or “stop” position Set mode selector switch to “run” position.
Tension adjust set at maximum Reduce level and see if brake rotates.
Remote mode switch in brake “on” or “stop” Set remote mode selector to “run”.
position
Remote sensor incorrectly wired Check wiring and rewire if necessary.
Mechanical binding Check brake for freewheeling when control power is off.
Correct if mechanical problems still exist.
Symptom E: Brake does not have adequate torque capacity
Brake is incorrectly sized Verify brake sizing by repeating the selection procedure in
Tension Catalog P-771.
Brake is incorrectly wired Recheck wiring and magnet connections and rewire if
necessary.
Local or remote tension adjust Recheck set-up procedures for the incorrectly set mode of
operation in which the control is used. Readjust if necessary.
This manual suits for next models
1
Table of contents
Other Warner Controllers manuals
Popular Controllers manuals by other brands
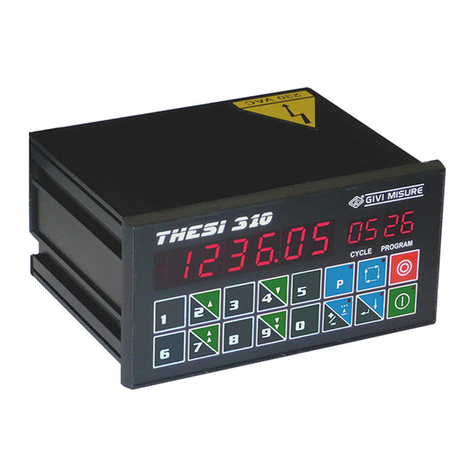
Givi Misure
Givi Misure THESI 310 user manual
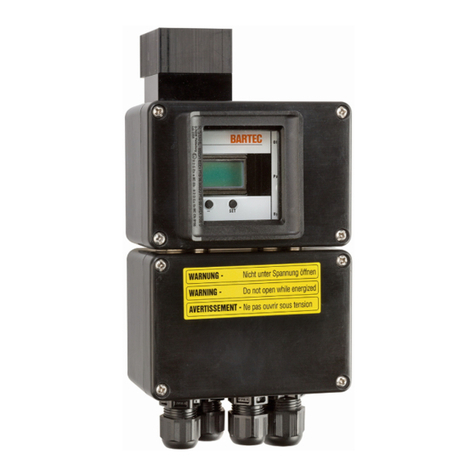
Bartec
Bartec SILAS A7-3741-1110 Series operating instructions
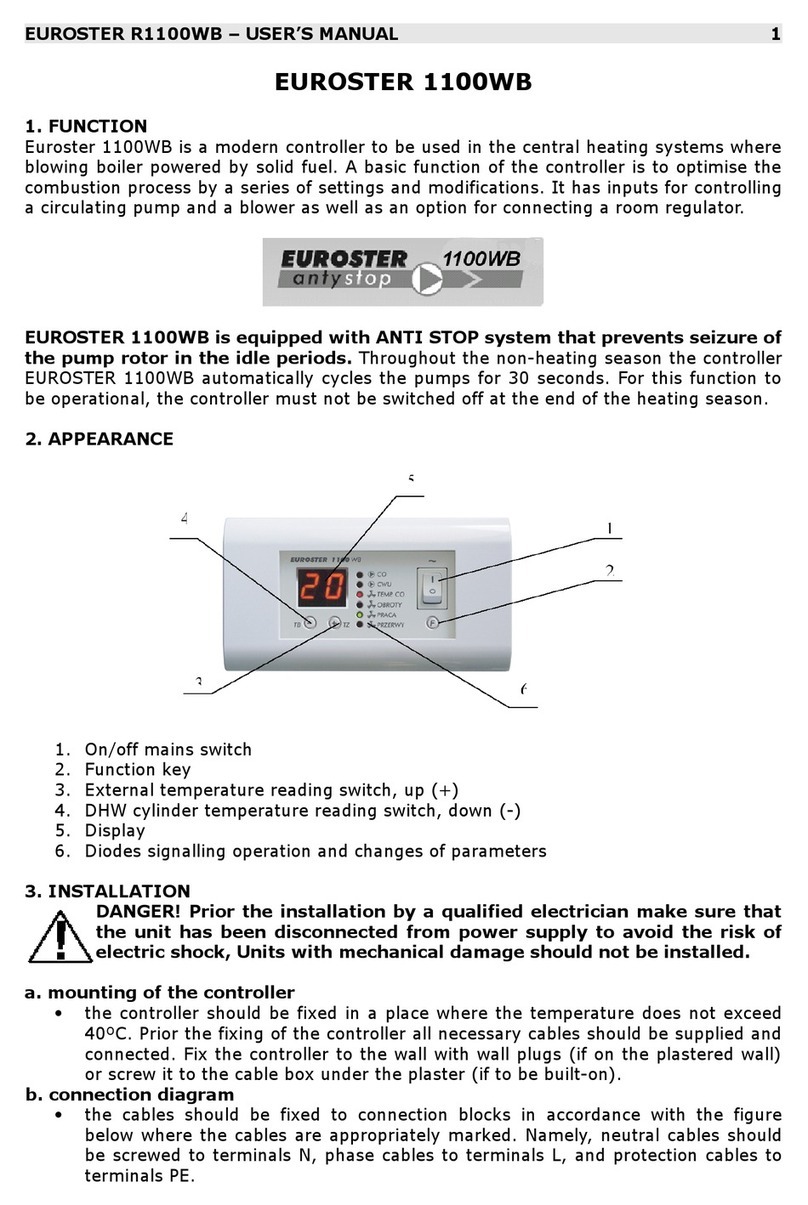
EUROSTER
EUROSTER R1100WB user manual

ELECTROMEN
ELECTROMEN EM-176A quick start guide
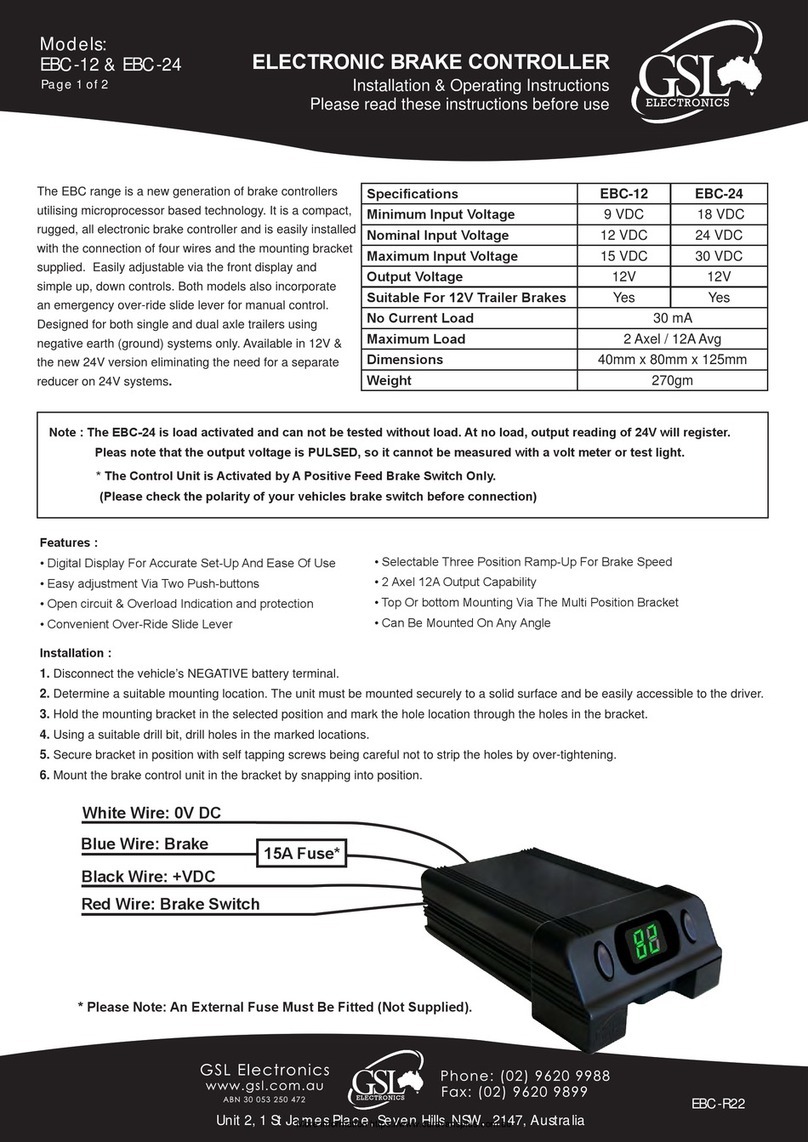
GSL electronics
GSL electronics EBC-12 Installation & operating instructions
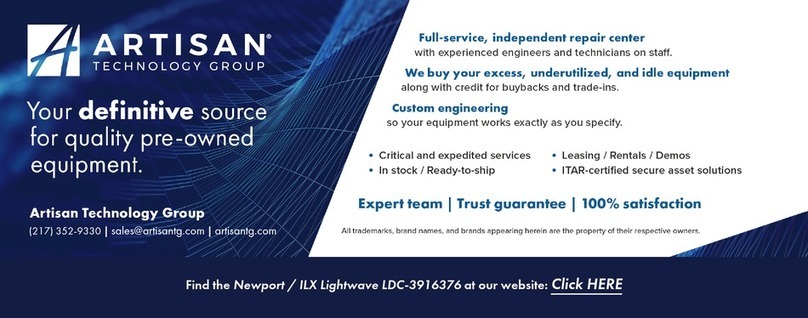
ILX Lightwave
ILX Lightwave LDC-3916371 user guide