WEG WECM User manual

www.weg.net
WECM / Emerald eZA Manual | 1
WECM / Emerald eZA
Three-Phase Motors
Installation, Operation and
Maintenance Manual
Motors | Automation | Energy | Transmission & Distribution | Coatings

www.weg.net
2 | WECM / Emerald eZA Manual
Read carefully this manual before installing and configuring the equipment
The objective of this manual is to provide important information, which must be considered during the shipment, storage,
installation, operation and maintenance of WEG motors. Therefore, we advise to make a careful and detailed study of the
instructions contained herein before performing any procedures on the motor. The noncompliance with the instructions
informed in this manual and others mentioned on the website www.weg.net voids the product warranty and may cause
serious personal injuries and material damages. For further information or explanations, check our FAQ at www.weg.net/
br/faq.
The instructions presented in this document are valid for: WECM / Emerald eZA products.

www.weg.net
WECM / Emerald eZA Manual | 3
1. GENERAL INFORMATION
WECM / Emerald eZA product is an Electronically Commutated Motor composed by a permanent magnet motor and a
drive with features customized for commercial ventilation solutions.
This Manual contains only the required information that allows qualified and trained personnel to carry out their services.
The product images are shown for illustrative purpose only.
1.1. WARNINGS IN THIS MANUAL
ATTENTION!
The information mentioned in this warning is important for the proper understanding and good operation of the
product.
ATTENTION!
The procedures recommended in this warning have the purpose of avoiding material damage.
DANGER!
The procedures recommended in this warning have the purpose of protecting the user against death, serious
injuries and considerable material damage.
2. SAFETY MEASURES
Only trained personnel, with proper qualifications, and familiar with this kind of equipment and associated machinery shall
plan and implement the installation, starting, operation and maintenance of this equipment. The personnel shall follow all
the safety instructions described in this manual and/ or defined by the local regulations.
DANGER!
Always disconnect the main power supply before touching any electrical device associated with the product.
Several components may remain charged with high voltage and/or in movement and may cause injuries to
people, even after the AC power supply has been disconnected or turned off. Wait at least 10 minutes to guarantee the
fully discharge of capacitors. Always connect the equipment to the ground protection (PE)
ATTENTION!
Contains permanent magnets. For pacemaker users, it is recommended to avoid close or prolonged contact with
this product, as it may interfere with the proper operation of the device.
++
ATTENTION!
Any service on the internal parts of the motor must be performed by qualified personnel only, since, due to the
attraction between metallic parts caused by the magnets, risk of accident is present both in the assembly and
disassembly of the motor.
3. SHIPMENT, STORAGE AND HANDLING
Check the conditions of the motor immediately upon receipt. Where any damage is noticed, this must be reported in writing
to the transportation company, and immediately communicated to the insurance company and to WEG. In this case, no
installation job can be started before the detected problem has been solved.
Check if the nameplate data matches the invoice data and the environmental conditions in which the motor will be installed.
If the motor is not immediately installed, it must be stored in a clean and dry room protected against dust, vibrations, gases
and corrosive agents, and with temperature between -25 ºC and 60 ºC and relative humidity not exceeding 60%.
If the motors are stored for more than two years, it is recommended to change the bearings, or to remove, wash, inspect
and relubricate them before the motor is started.
DANGER!
g Always handle the motor carefully in order to prevent personal injuries and impacts that could damage the
bearings.
When available, do not lift and/or carry the product holding by the input cables.
When available, use only the eyebolts to lift the motor. However, these eyebolts are designed for the motor weight
only. Thus, never use these eyebolts to lift the motor with additional loads coupled to it. For multimounting motors (with
removable feet/ base), the eyebolts must be positioned according to the motor mounting position so that the lifting angle
is vertically aligned (lifting at 0°).
Additional information regarding the maximum allowable angle-of-inclination is indicated in the general manual
available on the website www.weg.net.

www.weg.net
4 | WECM / Emerald eZA Manual
4. IDENTIFICATION LABELS
There is one nameplate with general product information on the WECM / Emerald eZA product that is affixed to the side of
the motor frame and one label with basic electronic information that is affixed to the drive (back cover).
Figure 1 - Drive label
Figure 2 - Europe market motor nameplate
5. INSTALLATION
DANGER!
g Make sure the AC power supply is disconnected and protected against accidental energization before starting
the installation;
Check the motor direction of rotation, turning it without load before it is coupled to the load;
To prevent accidents, ensure that the grounding connection has been performed according to the applicable
standards and that the shaft key has been securely fastened before the motor is started;
When available, do not lift and/or carry the product holding by the input cables.
Motors must be only installed in places compatible with their mounting features and in applications and environments for
which they are intended.
Those motors with feet must be installed on bases duly planned in order to prevent vibrations and assure perfect alignment.
The motor shaft must be properly aligned with the shaft of the driven machine. Incorrect alignment, as well as improper
belt tension, will certainly damage the bearings, resulting in excessive vibrations and even causing the shaft to rupture. The
admissible shaft radial and axial loads for standard bearings are specified on the Table 1 and Table 2. Use flexible coupling
whenever possible.

www.weg.net
WECM / Emerald eZA Manual | 5
Allowed loads for WECM (IEC 80) motors, according maximum speed:
Direction Mounting position Type
1500 rpm 1800 rpm 3000 rpm
Force (kN) Force (kN) Force (kN)
Axial 1)
Horizontal Pushing 0.90 0.86 0.74
Pulling 0.50 0.46 0.34
Vertical shaft down Pushing 0.96 0,91 0.77
Pulling 0.47 0.44 0.33
Vertical shaft up Pushing 0.87 0.84 0.73
Pulling 0.56 0.51 0.37
Radial 2) All L0.66 0.61 0.49
L/2 0.74 0.69 0.56
Table 1 - Maximum permissible thrust - Fr in (kN) 20000 hours
Allowed loads for WECM (IEC 100) motors, according maximum speed:
Direction Mounting position Type
1500 rpm 1800 rpm 3000 rpm
Force (kN) Force (kN) Force (kN)
Axial 1)
Horizontal
Pushing 1.31 1.25 1.10
Pulling 0.71 0.65 0.50
Vertical shaft down
Pushing 1.46 1.37 1.18
Pulling 0.62 0.58 0.45
Vertical shaft up
Pushing 1.22 1.18 1.05
Pulling 0.86 0.76 0.58
Radial 2) All
L0.96 0.88 0.74
L/2 1.07 1.0 0.85
Table 2 - Maximum permissible thrust - Fr in (kN) 20000 hours
Notes:
1) Axial maximum load (radial zero).
2) Radial maximum load (axial zero).
1 - All belt loads are considered to act in vertically downward direction.
2 - Overhung loads include belt tension and weight of sheave.
3 - Overhung load limits do not include any effect of unbalanced magnetic pull.
Only remove the corrosion protection grease from the shaft end and flange immediately before the motor installation.
Unless specified otherwise in the purchase order, WEG motors are dynamically balanced with “half key” and without load
(uncoupled).
The driving elements, such as pulleys, couplings, etc., must be balanced with “half key” before they are mounted on the
shaft of the motors.
ATTENTION!
g The air used for cooling the motor must be at ambient temperature, limited to the temperature indicated on
the motor nameplate;
Take the required measures in order to ensure the degree of protection indicated on the motor nameplate:
Unused cable inlet holes in the terminal boxes must be properly closed with blanking plugs;
The cable entries used must be fitted with components, such as, cable glands and conduits;
Components supplied loose (for example, terminal boxes mounted separately) must be properly closed and sealed;
Fixing elements mounted in the threaded through holes in the motor enclosure (for example, the flange) must be
properly sealed.
For flying leads motors, do not push the overlength of leads into the motor in order to prevent that they touch the
rotor.

www.weg.net
6 | WECM / Emerald eZA Manual
Drain hole: WECM / Emerald product can be supplied with drains. Figure 3, Figure 4 and Figure 5 give details about the
mounting configuration.
Figure 3 - Drain position Figure 4 - Drain closed Figure 5 - Drain open
ATTENTION!
g The motor must always be positioned so the drain hole is at the lowest position;
g Motors supplied with rubber drain plugs leave the factory in the closed position and must be opened
periodically to allow the exit of condensed water. For environments with high water condensation levels and motor with
degree of protection IP55, the drain plugs can be mounted in open position;
For motors with degree of protection IP56, IP65 or IP66, the drain plugs must remain at closed position, being
opened only during the motor maintenance procedures.
Slinger: WECM / Emerald product in vertical shaft up mounting should be fitted with water slinger ring to prevent water
ingress inside the motor. Consult WEG about this option.
ATTENTION!
Motors installed outdoors or in the vertical position require the use of additional shelter to protect them from
water.
Allowed inertias for WECM frames IEC80 and IEC100, according output power and speed:
Frame Power (kW) 1500 rpm (kgm²) 1800 rpm (kgm²) 3000 rpm (kgm²)
IEC80
0.12 0.16 0.16 0.05
0.18 0.16 0.16 0.05
0.25 0.16 0.16 0.05
0.37 0.27 0.16 0.05
0.55 0.40 0.27 0.11
0.75 0.40 0.40 0.11
1.10 0.62 0.40 0.11
1.50 0.62 0.62 0.11
IEC100
1.50 0.98 0.98 0.27
2.20 1.20 1.20 0.47
3.00 1.63 1.55 0.47
3.70 1.63 1.63 0.62
4.00 1.63 1.63 0.62
Table 3 - Table of inertias allowed for three phase line

www.weg.net
WECM / Emerald eZA Manual | 7
5.1. POWER CONNECTIONS
DANGER!
Connect the motor properly to the power supply by means of safe and permanent contacts, always considering
the data informed on the nameplate, such as rated voltage, wiring diagram, drive inputs, among others.
For power cables, switching and protection devices dimensioning, consider the rated motor current, the service factor, and
the cable length, among others. For motors without terminal block, insulate the motor terminal cables by using insulating
materials that are compatible with the insulation class informed on the nameplate. The minimum insulation distance between
the non-insulated live parts themselves and between live parts and the grounding must meet the applicable standards and
regulations for each country.
Make the power connections following nameplate indication.
Three-phase:
Power input: L1, L2 and L3 terminals
Protective earth: PE - green screw
If used, connect the optional external harmonic filter (passive PFC) in series to the line conductor.
WEG declares that the WECM / Emerald eZA motor line is intended to be used as a part of an end-product and thus is
not an independently used machine. All cables of this product need to be internally installed into the enclosure of the final
product.
DANGER!
Always connect the equipment to the ground protection (PE).
ATTENTION!
The power supply that feeds the inverter shall have a solid grounded neutral.
5.2. CONTROL CONNECTIONS
Make the control connections following nameplate indication.
Three-phase:
DC voltage: VDC and GND terminals
DC current: ADC and GND terminals
Frequency duty-cycle / PWM: PWM and GND terminals
Speed feedback (reference): REF and GND terminals
10 VDC source: 10 V and GND terminals
24 VDC source: 24 V and GND terminals
RS485 communication: 485+, 485- and GND terminals
Alarm relay: NO, NC and COM terminals
5.3. EMC REQUIREMENTS FOR CONFORMING INSTALLATIONS
The standard Three-phase WECM / Emerald eZA mounting solution (drive attached to the motor) comply with EN IEC
61800-3 / FCC requirements.
For optional decentralized mounting, the product class may change and the product may require the use of external
filters. Consult WEG for the solution that better comply with your installation requirements.
WECM / Emerald eZA product may require the use of an external filter to comply with harmonic current emissions
requirements (EN61000-3-2). Consult WEG about optional external filters.
Power Conducted Radiated
2,2 kW – 4 kW C3 C3
Table 4 - EMC Class - IEC100
To meet the EMC levels in the Table 4, it is necessary to strictly comply with the installation configuration requirements
below mentioned:
The maximum permissible cable lenght of the power supply must be within a maximum distance of 3 meters.
Grounding must be carried out on the drive cover in an isolated manner.
Measurements must be carried out under load, providing the air velocity over the motor as specified in the design.
NOTE!
The end user takes personal responsibility for the EMC compliance of the whole installation.

www.weg.net
8 | WECM / Emerald eZA Manual
6. OPERATION INSTRUCTIONS
DANGER!
During operation, do not touch the non-insulated energized parts and never touch or stay too close to rotating
parts.
The rated performance values and the operating conditions are specified on the motor nameplate. The voltage and
frequency variations of the power supply should never exceed the limits established in the applicable standards.
Occasional different behavior during the normal operation (actuation of thermal protections, noise level, vibration level,
temperature and current increase) must always be assessed by qualified personnel. In case of doubt, turn off the motor
immediately and contact the nearest WEG service center.
6.1. SELECTING THE ROTATION DIRECTION
Remove the lid from the back side of the drive cover;
Use the DIP switch identified as CW / CCW to select the rotation direction between counter-clockwise (CCW) or
clockwise (CW), looking from the motor drive end (shaft);
Reinstall the lid to the back side of the drive cover after the adjust;
NOTE!
If the rotation direction is changed while the product is running, the motor will decelerate, reverse the direction
and accelerate to the same speed that was running before.
6.2.
ATTENTION!
After remove and reinstall, make sure that the lid from the back side of the drive cover is securely closed to
guarantee the protection degree.
HOW TO ADJUST SPEED
The product speed can be changed by local adjust (buttons) or remote adjust (control inputs);
To select between local or remote speed adjust:
Remove the lid from the back side of the drive cover;
Use the DIP switch identified as L / R to select between local (L) or remote (R);
Reinstall the lid to the back side of the drive cover after the adjust.
ATTENTION!
After remove and reinstall, make sure that the lid from the back side of the drive cover is securely closed to
guarantee the protection degree.
Local speed adjusts:
Remove the lid from the back side of the drive cover;
Use the two tact buttons located in the opening on the back cover to change speed;
Keep pressing the button to decelerate or accelerate the motor according identified on the nameplate;
The motor will turn off when the speed reaches a value lower than the minimum speed of the range;
The product will not go to speeds higher than the value adjusted to be the maximum speed (see 6.4
Reinstall the lid to the back side of the drive cover after the adjust.
NOTE!
g The standard maximum speed value is preset at WEG to be the highest value of the speed range but, can be
changed by the user (see item 6.4).
The product has speed memory when operating in local speed adjustment. The last speed adjusted will be kept in
memory when the input power supply is removed. The motor will accelerate to the memorized speed when the input
power supply is reconnected.
The local controls inside the opening on the back cover of the product are totally insulated. There is no risk of shock
when touch any internal part of this opening, even when the solution is running.
ATTENTION!
After remove and reinstall, make sure that the lid from the back side of the drive cover is securely closed to
guarantee the protection degree.

www.weg.net
WECM / Emerald eZA Manual | 9
Remote speed adjusts:
The speed can be adjusted by:
DC voltage: 2 to 10 VDC [tolerance: + 10%].
DC current: 4 to 20 mA DC [tolerance: + 10%].
Frequency duty-cycle / PWM: 10 to 95%
Voltage: 10 to 24 Vpk [tolerance: -5% / + 10%].
Frequency: 80 Hz [tolerance: -2,5% / + 2,5%].
When available, using the RS485 serial communication (see item6.7).
The speed can be adjusted using the external speed controller (see item 6.5).
The product will turn off if imposed signals lower than 2 V DC, 4 mA DC or 10%.
10 VDC
20 mA DC
95%
2 VDC
4 mA DC
10%
zero VDC ª
zero mA DC
zero %
min
speed
max
speed b
c
INPUT SIGNAL
SPEED [rpm]
Figure 6 - Control input reference
Table 5 -
Signal type Condition Resulting speed value
DC voltageaLower than 2 VDC Zero (motor is off)
From 2 to 10 VDC ((Maxb-Minc)/8)×(ISd-2)+Min
DC current
Lower than 4 mA DC Zero (motor is off)
From 4 to 20 mA DC ((Maxb-Minc)/16)×(ISd-4)+Min
Frequency
Lower than 10% Zero (motor is off)
From 10 to 95% ((Maxb-Minc)/85)×(ISd-10)+Min
Control input reference
Notes:
a. The DC voltage signal can be applied by an external power supply or using the built-in 10VDC source and an additional
potentiometer (5 kΩ to 10 kΩ).
b. Maximum speed adjusted (see item 6.4).
c. Minimum speed adjusted (see item 6.4).
d. Input signal (V DC, mA DC, %) supplied to the respective remote input.
ATTENTION!
g The built-in power supplies have an output limit of:
g Three-Phase: 10 mA for the 10 VDC and 350 mA for the 24 VDC.
The product can be permanently damaged if imposed signals out of the specification.
Make sure that all unused conductors in control cable are insulated to avoid product malfunction or damage.

www.weg.net
10 | WECM / Emerald eZA Manual
6.3. PRODUCT STANDARD FEATURES AND CONTROL REFERENCE
The product has characteristics of reference signals and these can be found in the Table 6 and Figure 7:
Signal Detail Signal reference
DC Source 10 VDC Voltage: 10 VDC, Current: 10 mA max
24 VDC Voltage: 24 VDC, Current: 350 mA max
Speed reference Speed = zero Frequency [Hz]: zero (4,8 V)
Speed > zero Frequency [Hz]: speed (rpm) x 0,6015
Serial communication RS485 See item 6.7
Alarm relay
Normally Open Voltage: 250 VAC, 220 VDC – max
Current: 2 A max
Normally Closed
Table 6 - Product standard features and control reference
Figure 7 - Product standard features and control reference
6.4. HOW TO ADJUST THE MAXIMUM AND MINIMUM SPEED VALUE
6.4.1. MAXIMUM SPEED
The maximum speed value for the remote speed adjust signals can be changed:
Using the optional WEG EC Motor Speed Controller (see item 6.5 ).
Using the product local tact buttons (only up to the maximum speed set by WEG EC Motor Speed Controller).
Select local speed reference in the DIP switch (see item 6.2).
Using the tact buttons, adjust the speed to the value desired to be the maximum.
Select remote speed reference in the DIP switch.
When available, using the RS485 serial communication (see item 6.7);
NOTE!
g The standard factory preset value for the maximum speed is the rated speed informed in the product nameplate;
g The maximum speed must be equal or lower than the rated speed.
Consult WEG about different factory maximum speed values.
6.4.2. MINIMUM SPEED
The standard factory preset value for the minimum speed is 200 rpm for the rated 1500 rpm and 1800 rpm product
and 500 rpm for the rated 3000 rpm product.
Consult WEG about different factory minimum speed values.

www.weg.net
WECM / Emerald eZA Manual | 11
6.5. WEG EC MOTOR SPEED CONTROLLER (OPTIONAL)
The running speed and the maximum speed adjust can be done using the external WEG EC Motor Speed Controller.
WEG EC MOTOR SPEED CONTROLLER
Operation mode:
Running speed adjust
1 2 3 4
CTR GND BACK +10 V
PWM
[10-95%]
COM -
Common
REF - Speed
reference
10V - 10 VDC
source
Figure 8 - The diagram of controller Figure 9 - WEG EC Motor speed controller
Fed the EC motor following the instructions of the item 5.2;
Running speed adjust
Remove the lid from the back side of the drive cover;
Connect the control signals (item 5.2) to the external speed controller according to Figure 8;
Rotate CTR in clockwise direction (CW) to increase the running speed;
Rotate CTR in counter-clockwise direction (CCW) to reduce the running speed;
During the adjust, the running speed can be verified in the display;
Reinstall the lid to the back side of drive cover after the connections are done;
Maximum speed adjust
Remove the lid from the back side of the drive cover;
Connect the external controller to the EC motor using the cable supplied with the external controller and the connector
inside the EC motor back opening;
Rotate MAX in clockwise direction (CW) to increase the maximum speed;
Rotate MAX in counter-clockwise direction (CCW) to reduce the maximum speed;
During the adjust, the maximum speed can be verified in the display;
Push the button “Enter” to set the maximum speed;
Disconnect the cable from the EC motor back opening connector;
Reinstall the lid to the back side of drive cover after the adjust;
If the maximum speed set is lower than the running speed, the motor will decelerate until reaching the new maximum
speed set.
If the maximum speed set is lower than the running speed, the motor will decelerate until reaching the new maximum
speed set.
ATTENTION!
After remove and reinstall, make sure that the lid from the back side of the drive cover is securely closed to
guarantee the protection degree.

www.weg.net
12 | WECM / Emerald eZA Manual
6.6. FIRE MODE FUNCTION (OPTIONAL)
DANGER!
Notice that the WECM / Emerald eZA is just one of the components of the ventilation system, and it is configurable
for different functions, including the “Fire Mode” function;
Thus, the full operation of the “Fire Mode” function depends on the accuracy of the project and on the joint performance
of the components of the system;
Ventilation systems that work on life safety applications must be approved by the Fire Department and/or another
competent public authority;
The non-interruption of the operation of the WECM / Emerald eZA, when configured for operation in the “Fire Mode”
function, is critical and must be taken into account in the preparation of safety plans in the environments in which they
are installed, since damages may occur to the WECM / Emerald eZA itself and to other components of the ventilation
system, to the environment in which it is installed and to people with risk of death;
The operation in the “Fire Mode” function may, under certain circumstances, result in fire, since the protection devices
will be disabled;
Only personnel from engineering and safety must consider the configuration of the equipment for the “Fire Mode”
function;
WEG strongly recommends to follow the cares and procedures above before using the WECM / Emerald eZA in the
“Fire Mode” function, and it will not be liable to the final user or third parties for any losses or damages direct or indirectly
incurred due to the programming and operation of the WECM / Emerald eZA in “Fire Mode” regime, considering the
critical and special use of this function.
NOTE!
When the user activates the "Fire Mode" function, he/she acknowledges that the protection functions of the
WECM / Emerald eZA are disabled, which may result in damages to the WECM / Emerald eZA itself, to the
components connected to it, to the environment in which it is installed and to people present in such environment;
therefore, the user takes full responsibility for the risks arising from such operating condition. Operation with the “Fire
Mode” function programmed voids the warranty of the product. The operation in this condition is internally registered by
the WECM / Emerald eZA and must be validated by a duly qualified professional of engineering and occupational safety,
since such procedure significantly increases the operating risk.
The “Fire Mode” function is intended to make the WECM / Emerald eZA continue work under adverse conditions, inhibiting
most faults generated by the electronic in order to protect itself or protect the motor.
The “Fire Mode” is selected by applying 10VDC to the frequency input. The built-in 10 VDC source can be used. When
selected, the motor will speed up to the maximum speed set and will disable all motor software protections.
The only possible way to turn off the “Fire Mode” operation function is to de-energize the complete solution and energize
it back again.
6.7. SERIAL COMMUNICATION
6.7.1. Hardware preparation:
USB to 485 Converter
Setting:
Step 1: Install the driver of USB to 485 Converter on PC.
Step 2: Connect converter with ECM Motor:
Connect A pin of USB to 485 Converter with 485+ signal of ECM Motor.
Connect B pin of USB to 485 Converter with 485- signal of ECM Motor.
Connect GND of USB to 485 Converter with GND signal of ECM Motor.

www.weg.net
WECM / Emerald eZA Manual | 13
6.7.2 . Software preparation:
Modbus RTU communication tool (provided by EMC Group).
Modbus RTU MulticomV3.0 Parameter Setting:
1. Communication parameter setting:
Step 1: Connect USB to 485 Converter with PC USB port.
Step 2: Select interface: Serial.
Step 3: Communication common port configure (refer to Figure 10).
Step 4: After the above operations are completed, please select “connect” (refer to Figure 11).
Port Name:
Figure 10 - Modbus parameter setting Figure 11 - Modbus connecting
After completing the above preparations, please turn on the power of the ECM Motor.
Confirm the ECM Motor Modbus slaver address: The default address is 0x55(85).
2. Operation instruction:
Step 1: Input the default address 85 in the Node box.
Step 2: Select “Read/Write register”, input register the initial address and quantity, and click read. Check whether the
read function can be executed successfully. If communicating successes, it shows like Figure 10. If communicating fails, it
shows like Figure 11, and it is required to get the right address of this ECM Motor (Refer to Step 3).
Figure 12 - Modbus communication succeed Figure 13 - Modbus communication fail

www.weg.net
14 | WECM / Emerald eZA Manual
Step 3: Obtain the current Modbus address, please refer Figure 14. Input the broadcast address 0, Select “Other
function”, read device ID (01-Basic Objects) or directly send “00 2B 0E 01 00 4D B7”. When the ECM Motor received the
request, the LED1 on the PCBA will flash address count.
Figure 14 - Modbus communication fail
3. Set Modbus address (The master can only set slaver address one by one):
Step 1: Establish the Modbus RTU communication, the default address is 85 for the first-time connection.
Step 2: Input the new address (for example 10) in register 7 (the register address is 00 07), and click write ( Figure 15).
Step 3: After write-in the new address, the old one is disable. Input the new address in Node, and check communication
(Figure 16).
Figure 15 - Write address Figure 16 - Check communication
Note: If the MODBUS address is not the default address and communication can be established with the original address,
the new address can be set in the same way as above.
4. Set Modbus address (The master can only set slaver address one by one now):
After setting the new address successfully, please refer to Modbus command and address section below for more Read
/ Write details.
5. Default serial configuration:
If the Modbus serial configuration of Inverter has never been changed, then the default setting will be always available.
Baud rate: 19200 bits/s
Start bit: 1 bit
Data bits: 8 bits
Parity: Even
Stop: 1 bit

www.weg.net
WECM / Emerald eZA Manual | 15
6. Reset Modbus control and serial configuration to factory default:
Remove the lid from the back side of the drive cover.
Press and hold local tact buttons SW1 and SW2 both for 5 Sec.
After 5 Sec, LED #2 starts fast blinking at 5 Hz to confirm even handled.
Factory default reset value are as follow:
Modbus control enable: 0
MODBUS address: 0x55(85)
Baud rate: 19200 bits/s
Start bit: 1 bit
Data bits: 8 bits
Parity: Even
Stop: 1 bit
Reinstall the lid to the back side of drive cover.
7. Modbus serial configuration selection
In order to make the Modbus control available for different serial configuration. The serial parameters of inverter can be
changed by Modbus command.
The register 0x0008 is used to set the baud rate, writing the corresponding baud rate in the register 0x0008 according to
Table 7.
The register 0x0009 is used to set the other parameters of serial (Parity and Stop bit), writing the corresponding value in the
register 0x0009 according to Table 8.
Baud rate (bits/s) Correspond Value of Register 0x0008
2400 2400
4800 4800
9600 9600
19200 19200
38400 38400
57600 57600
Table 7 - Baud Rate setting
Parity /Stop bit Correspond Value of Register 0x0009
No parity, 1 stop bit 0x0000
Even parity, 1 stop bit 0x0001
Odd parity, 1 stop bit 0x0002
No parity, 2 stop bits 0x0003
Even parity, 2 stop bits 0x0004
Odd parity, 2 stop bits 0x0005
Table 8 - Parity and Stop bit setting

www.weg.net
16 | WECM / Emerald eZA Manual
8. Setting serial configuration
Step 1: Firstly establish Modbus communication between slave inverter and master:
Step 2: Writing Register 0x0008 and 0x0009 according to Table 7 and Table 8, other values are invalid;
Step 3: Writing “0x0001” into Register 0x000A to enable new serial configuration as Step 2;
Step 4: After Step 3, Master with original configuration will losses communication with slaver, then master needs to
change to new serial configuration, rebuild the communication with slaver.
Using function code 16 to execute the serial configuration.
For example, use function code 16 to set serial configuration as below:
Baud rate: 38400 bits/s (0x9600)
Start bit: 1 bit
Data bits: 8 bits
Parity: odd
Stop: 1 bit
Modbus address is 0x55, function code is 0x10(16), initial register address is 0x0008, register quantity is 0x0003, bytes
quantity is 0x06 (3 x 2), baud rate is 0x9600(38400), ‘Parity and Stop’ parameter is 0x0002, and enable the parameters
setting 0x000A with 0x0001, CRC16 is 0xD488.
The master send format:
T-> (13:33:31:103) 55 10 00 08 00 03 06 96 00 00 02 00 01 D4 88 10
The slaver responses format:
R<-(13:33:31:114) 55 10 00 08 00 03 0C 1E
When slaver responses, it means setting successfully.
9. Modbus command and address
01 Request Frame
Slaver Address
(1 byte)
0x01
(function code)
Register Address
(2 bytes)
0x0001
(2 bytes)
CRC
(2 bytes)
01 Answer
Slaver Address
(1 byte)
0x01
(function code)
Register Number
(1 byte)
Data
(1 byte)
CRC
(2 bytes)
03 Read Frame
Slaver Address
(1 byte)
0x03
(function code)
Register Start Address
(2 bytes)
Register Numbers N
(2 bytes)
CRC
(2 bytes)
03 Answer
Slaver Address
(1 byte)
0x01
(function code)
Register Numbers
N*2
(1 byte)
Request Data1
(2 bytes)
……
(datas)
Request Data N
(2 bytes)
CRC
(2 bytes)
06 Write Frame
Slaver Address
(1 byte)
0x06
(function code)
Register Address
(2 bytes)
Write content
(2 bytes)
CRC
(2 bytes)
06 Answer
Slaver Address
(1 byte)
0x06
(function code)
Register Address
(2 bytes)
Write content
(2 bytes)
CRC
(2 bytes)
16 Write Frame
Slaver Address
(1 byte)
0x10
(function code)
Register start
Address
(2 bytes)
Registers number
N
(2 bytes)
Registers byte
number N*2
(1 byte)
Write content 1
(2 bytes)
Write content N
(2 bytes)
CRC
(2 bytes)
16 Answer
Slaver Address
(1 byte)
0x10
(function code)
Register start Address
(2 bytes)
Register number N
(2 bytes)
CRC
(2 bytes)
Figure 17 - Modbus command and address

www.weg.net
WECM / Emerald eZA Manual | 17
10. Address table
R(01) – Single Register reading
R(03) – Multiple Register reading
Read / Write Function Address and Notes
R(01) Local/Remote Mode Read Register address:0x0000
0: Local;
1: Remote.
R(01) Relay State Read Register address: 0x0001
0: open
1: close
R(01) Read Fire mode flag Read Register address: 0x0002
0: out fire mode;
1: in fire mode
R(01) Read AC lose flag Read Register address: 0x0003
0: False
1: True
R(01) Read direction Read Register address: 0x0004
0: CW
1: CCW
R(01) Read Run/Stop Read Register address: 0x0005
0: Stop;
1: Run.
R(03) Read motor number Read Register address: 0x0000
R(03) Read firmware version of motor driver MCU Read Register address: 0x0001
R(03) Read software version of Mid-controller Read Register address: 0x0002
R(03) FCT Max Speed Read Register address: 0x0003
R(03) Current Max Speed Read Register address: 0x0004
R(03) Read motor Target speed Read Register address: 0x0005
R(03) Read motor actual speed Read Register address: 0x0006
R(03) Read DC bus voltage Read Register address: 0x0007
R(03) Read output current (motor) Read Register address: 0x0008
R(03) Read output voltage (motor) Read Register address: 0x0009
R(03) Read frequency (motor) Read Register address: 0x000A
R(03) Read IPM Temperature Read Register address: 0x000B
R(03) Read Error code Read Register address: 0x000C
Refer to Fault error code
R(03) Read multi register 0x01 + 0x03 + start address +
register number N + CRC
W(06) Modbus control enable Write Register address: 0x0000
0: disable
1: enable
W(06) Run/Stop Write Register address: 0x0001
0: Stop
1: Run
W(06) Write Max speed Write Register address: 0x0002
W(06) Write Target speed Write Register address: 0x0003

www.weg.net
18 | WECM / Emerald eZA Manual
Read / Write Function Address and Notes
W(06) WWrite Target direction Write Register address: 0x0004
0: CW
1: CCW
W(06) Turn on/off Fire mode Write Register address: 0x0005
0: Out fire mode
1: In fire mode
W(06) Write Local/remote Write Register address: 0x0006
0: Local
1: Remote
W(06) Write Modbus address Write Register address: 0x0007
W(06) Write Serial Configure: Baud Rate Write Register address: 0x0008
Refer to Table 6.3
W(06) Write Serial Configure: Parity & Stop Write Register address: 0x0009
Refer to Table 6.4
W(06) Write New Serial Configure Enable Write Register address: 0x000A
0: None action;
1: Enable configure
W(16) Write Multi register Write Register address:0000
Table 9 - Register table.
11. Fault error code
Error Code Fault Description
0x0001 DCBUS LOW
0x0002 DCBUS HIGH
0x0003 OVER CURRENT (HARDWARE PROTECTION)
0x0004 TEMPERATURE CRITICALLY HIGH
0x0005 LOCKED ROTOR
0x0006 COMMUNICATION TIMEOUT
0x0007 OVER LOAD
0x0008 OVER SPEED
7. PRODUCT PROTECTIONS AND FAULT DIAGNOSIS
WECM / Emerald eZA products have the following electronic protections:
Input under voltage protection.
Input over voltage protection.
Input over load protection.
Locked rotor protection.
Over temperature protection.
Output overcurrent / short-circuit protection.
WECM / Emerald eZA products have LED’s in the opening on the back side to indicate the solution status and to help in
the fault diagnosis:
Input Power supply Motor status LED #1 LED #2
Off Stopped Off Off
On Stopped Off Blinking (1 Hz)
On Running On Blinking (1 Hz)
On Fault Blinking according fault
(check Table 9) Blinking (1 Hz)

www.weg.net
WECM / Emerald eZA Manual | 19
DANGER!
g The LED in OFF condition doesn`t mean that there is no power supply to the drive;
g Make sure that the input power supply is disconnected before do any maintenance in the product.
If the Fire Mode function is active, the failures will be detected, but ignored by WECM / Emerald eZA, i.e., will not
block the IGBTs. If the motor was spinning, will continue spinning. For more information see item 6.5
The LED #1 will blink in case of any fault. Table 10 indicates the blinking behavior according the fault type:
Table 10 -
Blinking periods Fault ON time (s) Off time (s) Wait / interval time (off) (s)
2Under voltage 0,1 0,1 -
3Over current (shor-circuit)
0,25 0,25 2
6 Over voltage
7Over load
8Over speed
9Communication timeout
10 Over Temperature
11 Locked rotor
The blinking behavior according to fault type
Communication timeout fault: failure in the drive to motor communication;
Watchdog timeout fault: failure in the drive processor / software.
7.1. INFORMATION FOR CONTACTING TECHNICAL SUPPORT
For technical support and servicing, it is important to have the following information in hands:
Motor model, Batch number, and manufacturing date available in the motor nameplate (refer to item 4).
Installed software version available in the drive label (refer to item 4).
8. MAINTENANCE
DANGER!
g Before any service is performed, ensure that motor is it at standstill, disconnected from the power supply and
protected against accidental energization. Even when the motor is stopped, dangerous voltages may be present
in space heater terminals;
For motors with permanent magnet rotor (WECM and Emerald eZA), the motor assembly and disassembly require
the use of proper devices due to the attracting or repelling forces that occur between metallic parts. This work must only
be performed by a WEG Authorized service center specifically trained for such an operation. People with pacemakers
cannot handle these motors. The permanent magnets can also cause disturbances or damages to other electric
equipment and components during maintenance.
ATTENTION!
g Motor disassembly during the warranty period must be performed by a WEG authorized service center only;
g Regularly inspect the operation of the motor, according to its application, and ensure a free air flow. Inspect
the seals, the fastening bolts, the bearings, the vibration and noise levels, the drain operation, etc. The lubrication interval
is specified on the motor nameplate.

www.weg.net
20 | WECM / Emerald eZA Manual
9. ENVIRONMENTAL INFORMATION
For information regarding disposal at end of life cycle refer to the manual “Disposal and Environmental Information” available
in the website www.weg.net or contact WEG.
10. ADDITIONAL INFORMATION
For further information about shipment, storage, handling, installation, operation and maintenance of electric motors,
access the website www.weg.net.
For special applications and operating conditions refer to the manual 50033244 available in the website or contact WEG.
When contacting WEG, please, have the full description of the motor at hand, as well as the Motor model, Batch Number
and manufacturing date, indicated on the motor nameplate.
10.1. WARRANTY TERM
WEG Equipamentos Elétricos S/A, Motors Unit (“WEG”), offers warranty against defects in workmanship and materials for
its products for a period of 18 months from the invoice date issued by the factory or distributor/dealer, limited to 24 months
from the date of manufacture.
The paragraphs above contain the legal warranty periods.
If a warranty period is defined in a different way in the commercial/technical proposal of a particular sale, that will supersede
the time limits set out above.
The warranty periods above are independent of the product installation date and the startup.
If any defect or abnormal occurrence is detected during machine operation, the customer must immediately notify WEG in
writing about the occurred defect and make the product available for WEG or its Authorized Service Center for the period
required to identify the cause of the defect, check the warranty coverage, and perform the proper repairs.
In order for the warranty to be valid, the customer must be sure to follow the requirements of WEG’s technical documents,
especially those set out in the product Installation, Operation and Maintenance Manual, as well as the applicable standards
and regulations in force in each country.
Defects arising from the inappropriate or negligent use, operation, and/or installation of the equipment, non-execution
of regular preventive maintenance, as well as defects resulting from external factors or equipment and components not
supplied by WEG, will not be covered by the warranty.
The warranty will not apply if the customer at its own discretion makes repairs and/or modifications to the equipment
without prior written consent from WEG.
The warranty will not cover equipment, components, parts and materials whose lifetime is usually shorter than the warranty
period. It will not cover defects and/or problems resulting from force majeure or other causes not imputable to WEG, such
as, but not limited to: incorrect or incomplete specifications or data supplied by the customer; transportation, storage,
handling, installation, operation and maintenance not complying with the provided instructions; accidents; defects in the
construction works; use in applications and/or environments for which the machine was not designed; equipment and/or
components not included in the scope of WEG supply. The warranty does not include disassembly services at the buyer’s
premises, product transportation costs and travel, lodging and meal expenses for the technical staff of the Service Centers,
when requested by the customer.
The services under warranty will be provided exclusively at WEG authorized Service Centers or at one of its manufacturing
plants.
Under no circumstances will the warranty services extend the equipment warranty period.
WEG’s Civil Liability is limited to the supplied product; WEG will not be liable for indirect or consequential damages, such
as losses of profit and revenue losses and alike which may arise from the contract signed between the parties.
Table of contents
Other WEG Engine manuals
Popular Engine manuals by other brands
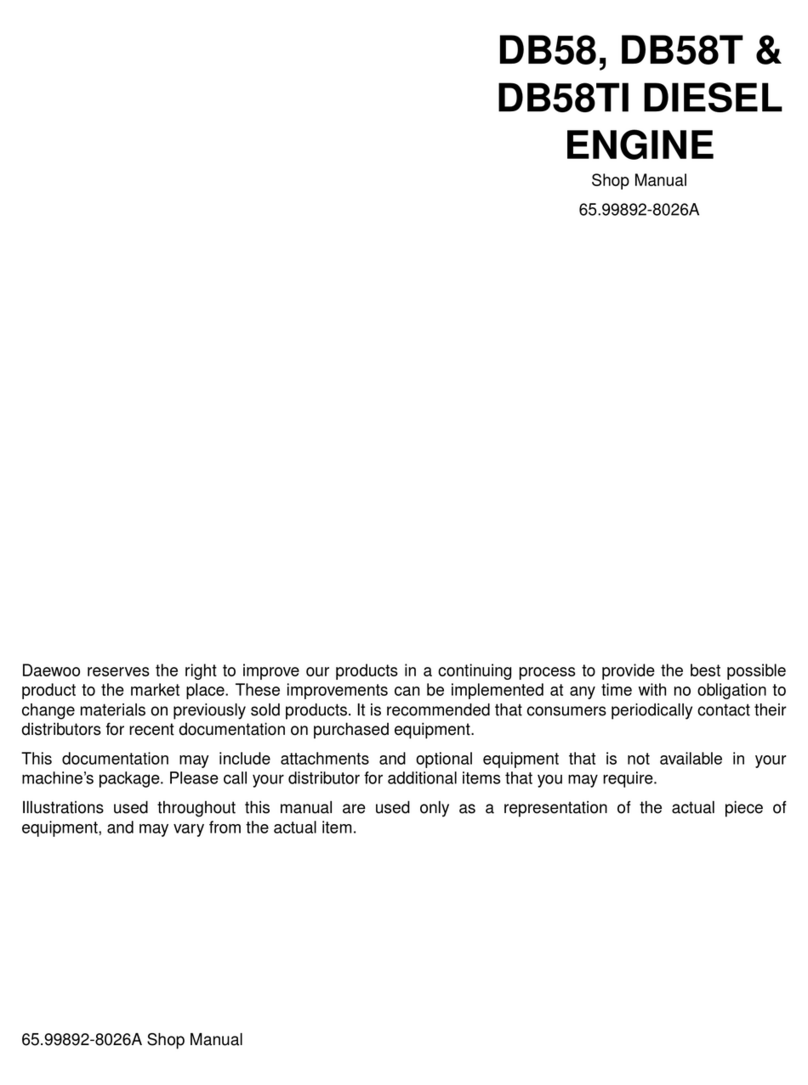
Daewoo
Daewoo DB58 Shop Manual

Detroit Diesel
Detroit Diesel MBE4000 Application and installation guide
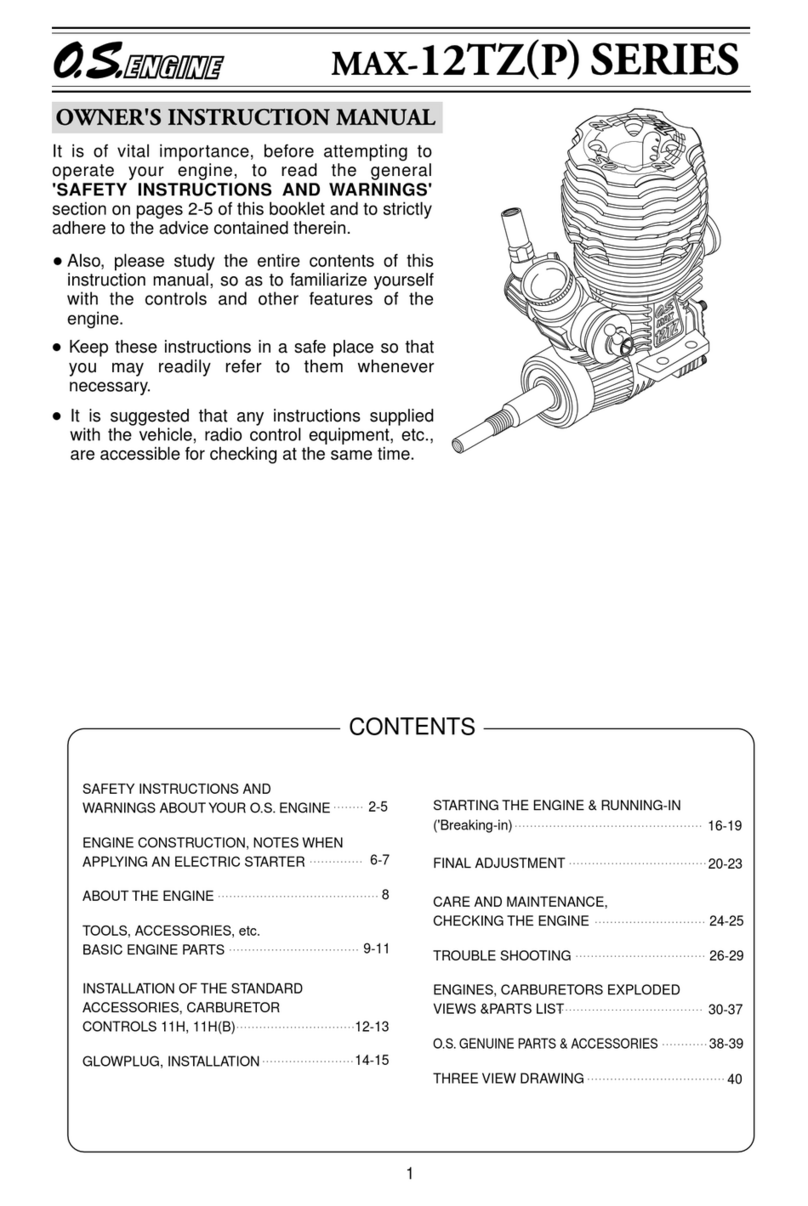
O.S. engine
O.S. engine max-12TZ series Owner's instruction manual

Singer
Singer BAK Electric Motor Instructions for using and adjusting
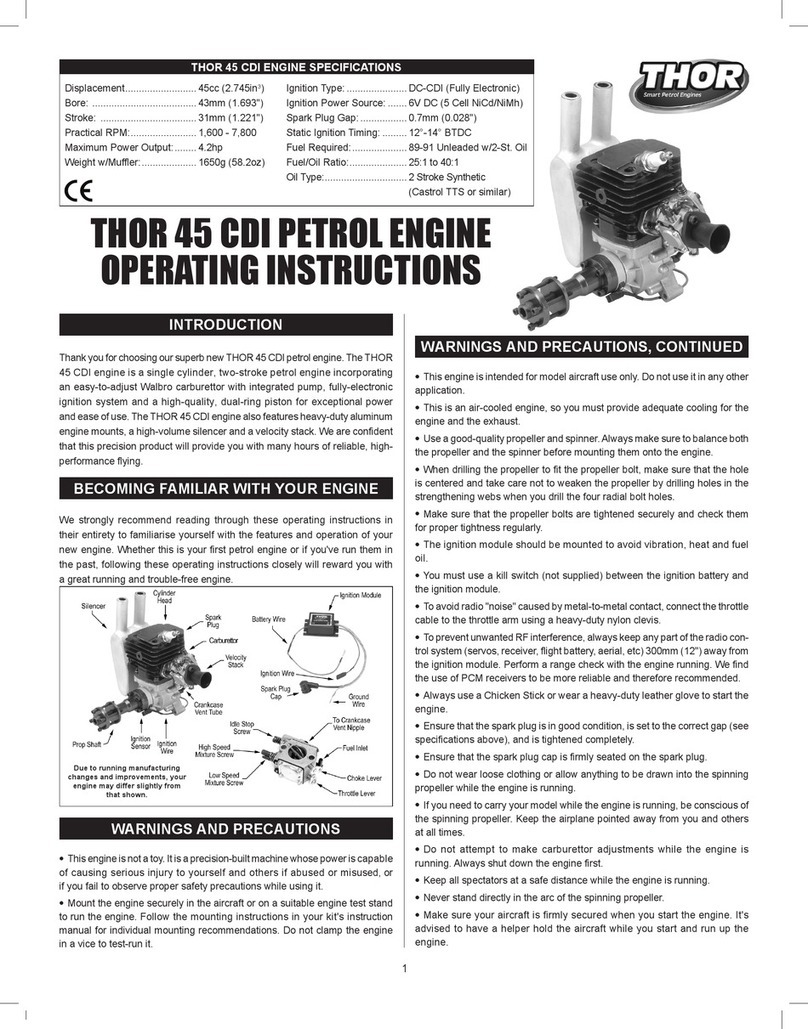
THOR
THOR THOR 45 CDI operating instructions
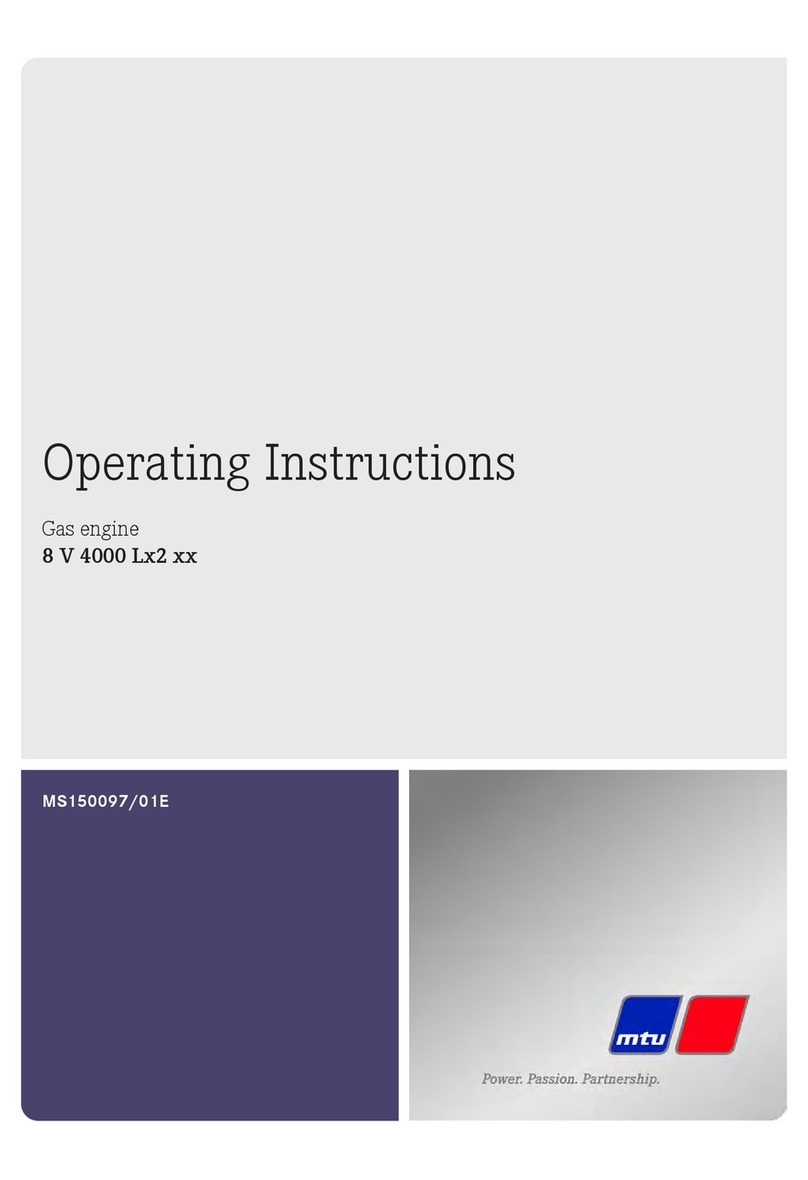
MTU
MTU 8V4000L62FB operating instructions