WEG W22Xdb C 315 User manual

W22Xdb –Flameproof Motors
Motors | Automation | Energy | Transmission & Distribution | Coatings
Rib-cooled
Tube-cooled
Installation, Operation and Maintenance
Manual


Dear Customer,
Thank you for acquiring a WEG motor. This is a product developed with levels of quality and efficiency that
ensure an excellent performance.
Since electric motors play an important role in comfort and wellbeing, they need to be identified and treated
as driving machines, whose features include certain handling procedures such as storage, installation, and
maintenance.
All efforts were employed in order to ensure that all of the information provided in this manual is accurate
regarding the configurations and applications of the motor.
Therefore, careful reading of this manual before proceeding with the motor installation, operation or
maintenance is highly recommended in order to ensure safe and continuous motor operation, ensuring its
safety and that of its installations. In case of any remaining doubts, please contact WEG.
Maintain this manual close to the motor at all times so it can be consulted whenever necessary.
W22Xdb - Rib-cooled
W22XdbT –Tube-cooled
www.weg.net/w22xdb
www.weg.net/w22xdb-tube
This manual is also applicable for BFGC4 line motors.
ATTENTION
Following the procedures provided in this manual is mandatory to maintain a valid
product warranty;
Motor installation, operation, and maintenance procedures must be performed only by
qualified personnel.
---- IMPORTANT ----
READ CAREFULLY THE INSTRUCTIONS INCLUDED IN THIS MANUAL IN ORDER TO
ENSURE A SAFE AND CONTINUOUS OPERATION OF THE EQUIPMENT
WEGeuro –Indústria Eléctrica, S.A.
Rua Engº Frederico Ulrich, Sector V
4470-605 MAIA - PORTUGAL
Phone: +351 229 477 700 | Fax: +351 229 477 792
www.weg.net
13564560 v05 - 11/2019 - EN


Flameproof motors | 5
www.weg.net
Table of Contents
1. GENERAL INFORMATION .................................................................................................................... 9
INTRODUCTION............................................................................................................................9
SAFETY INFORMATION...............................................................................................................9
2. GENERAL INSTRUCTIONS................................................................................................................. 11
MOTOR APPLICATION...............................................................................................................11
2.1.1. SAFETY WARNINGS IN THE MANUAL....................................................................................... 11
TRANSPORTATION....................................................................................................................11
RECEIVING INSPECTION ..........................................................................................................12
3. STORAGE............................................................................................................................................. 12
INDOOR STORAGE ....................................................................................................................12
OUTDOOR STORAGE ................................................................................................................12
VERTICAL MOTORS STORAGE................................................................................................13
OTHER CARES DURING STORAGE .........................................................................................13
INSULATION RESISTANCE........................................................................................................13
POLARIZATION INDEX...............................................................................................................14
PROLONGED STORAGE............................................................................................................14
3.7.1. INTRODUCTION........................................................................................................................... 14
3.7.2. GENERALITIES ............................................................................................................................ 14
3.7.3. STORAGE PLACE........................................................................................................................ 15
3.7.3.1 INDOOR STORAGE ........................................................................................................15
3.7.3.2 OUTDOOR STORAGE ....................................................................................................15
3.7.4. SPARE PARTS ............................................................................................................................. 15
3.7.5. SPACE HEATERS ........................................................................................................................ 15
3.7.6. INSULATION RESISTANCE......................................................................................................... 16
3.7.7. EXPOSED MACHINED SURFACES ............................................................................................ 16
3.7.8. FLAMEPROOF JOINTS................................................................................................................ 16
3.7.9. BEARINGS.................................................................................................................................... 16
3.7.9.1 ANTIFRICTION BEARINGS LUBRICATED BY GREASE ...............................................16
3.7.9.2 SLEEVE BEARINGS........................................................................................................16
3.7.10. CONNECTION BOX.................................................................................................................... 17
3.7.11. INSPECTIONS AND RECORDS DURING STORAGE............................................................... 17
3.7.12. PREPARATION FOR SERVICE AFTER LONG TERM STORAGE............................................ 17
3.7.12.1 CLEANING.....................................................................................................................17
3.7.12.2 BEARINGS LUBRICATION............................................................................................18
3.7.12.3 INSULATION RESISTANCE VERIFICATION................................................................18
3.7.12.4 OTHER ..........................................................................................................................18
3.7.13. MAINTENANCE PLAN FOR STORAGE..................................................................................... 19
4. HANDLING............................................................................................................................................ 20
HANDLING RIBBED COOLED MOTORS...................................................................................20
4.1.1. HORIZONTAL MOTORS............................................................................................................... 20
4.1.2. VERTICAL MOTORS.................................................................................................................... 20
HANDLING TUBE COOLED MOTORS.......................................................................................21
4.2.1. HORIZONTAL MOTORS............................................................................................................... 21
4.2.2. VERTICAL MOTORS.................................................................................................................... 21
4.2.3. VERTICAL TUBE COOLED MOTORS POSITIONING................................................................. 21
5. INSTALLATION .................................................................................................................................... 23
MECHANICAL ASPECTS............................................................................................................23
5.1.1. MOUNTING................................................................................................................................... 23

6|Flameproof motors
www.weg.net
5.1.2. FOUNDATIONS ............................................................................................................................ 23
5.1.3. TYPES OF BASES........................................................................................................................ 24
5.1.3.1 CONCRETE BASES........................................................................................................24
5.1.3.2 SLIDE RAILS ...................................................................................................................25
5.1.3.3 METALLIC BASES...........................................................................................................25
5.1.4. ALIGNMENT/LEVELLING............................................................................................................. 26
5.1.5. COUPLINGS................................................................................................................................. 26
5.1.5.1 DIRECT COUPLING........................................................................................................27
5.1.5.2 GEARBOX COUPLING....................................................................................................27
5.1.5.3 BELT AND PULLEY COUPLING.....................................................................................27
5.1.5.4 COUPLING ARRANGEMENT FOR SLEEVE BEARING - AXIAL CLEARANCE.............30
5.1.6. COOLING...................................................................................................................................... 31
5.1.7. VIBRATION / BALANCE ............................................................................................................... 31
5.1.8. SHAFT VIBRATION LIMITS.......................................................................................................... 31
5.1.9. AUTOMATIC LUBRICATORS....................................................................................................... 32
ELECTRICAL ASPECTS.............................................................................................................32
5.2.1. POWER SUPPLY.......................................................................................................................... 32
5.2.2. CONNECTIONS............................................................................................................................ 33
5.2.3. ROTATION DIRECTION............................................................................................................... 34
5.2.4. PROTECTIONS ............................................................................................................................ 35
5.2.4.1 WINDINGS PROTECTIONS............................................................................................35
5.2.4.2 BEARINGS PROTECTIONS............................................................................................35
5.2.5. ADJUSTMENT OF MOTOR PROTECTION DEVICES................................................................. 36
5.2.6. ELECTRIC CONNECTION CHECKING........................................................................................ 36
6. MECHANICAL INSTALLATION CHECKING ...................................................................................... 36
SPACE HEATERS.......................................................................................................................36
7. NOISE LEVEL....................................................................................................................................... 37
8. MAINTENANCE.................................................................................................................................... 37
CLEANLINESS.............................................................................................................................37
8.1.1. PARTIAL CLEANING.................................................................................................................... 37
8.1.2. COMPLETE CLEANING ............................................................................................................... 37
LUBRICATION.............................................................................................................................38
8.2.1. GREASE LUBRICATED BEARINGS ............................................................................................ 38
8.2.2. TYPE AND GREASE CHARACTERISTICS.................................................................................. 39
8.2.3. LUBRICATION INTERVALS ......................................................................................................... 39
8.2.4. LUBRICATION INTERVALS FOR HIGH TEMPERATURE........................................................... 41
8.2.5. QUALITY AND QUANTITY OF GREASE...................................................................................... 43
8.2.6. COMPATIBILITY........................................................................................................................... 43
8.2.7. LUBRICATING INSTRUCTIONS .................................................................................................. 44
8.2.8. BEARING LUBRICATION STEPS ................................................................................................ 44
8.2.9. AUTOMATIC LUBRICATION........................................................................................................ 45
8.2.9.1 REFILLING/REPLACING LUBRICATORS ......................................................................45
8.2.9.2 PROLONGED STORAGE................................................................................................45
8.2.10. SLEEVE BEARINGS................................................................................................................... 46
8.2.10.1 GENERAL INSTRUCTIONS..........................................................................................47
8.2.10.2 OIL TYPE AND CHARACTERISTICS............................................................................47
8.2.10.3 DISASSEMBLY OF THE SLEEVE BEARING SYSTEM (TYPE "EF") ...........................47
8.2.10.4 SLEEVE BEARING ASSEMBLY....................................................................................48
8.2.10.5 SETTING OF THERMAL PROTECTIONS (PT100).......................................................49
8.2.10.6 WATER COOLING SYSTEM.........................................................................................49
8.2.10.7 LUBRICATION...............................................................................................................49
8.2.10.8 SHAFT SEALS...............................................................................................................50
8.2.10.9 OPERATION..................................................................................................................50
AIR GAP CHECKING...................................................................................................................50
PARTIAL DISCHARGE MONITORING .......................................................................................50

Flameproof motors | 7
www.weg.net
MOTORS WITH INTERNAL BEARING TEMPERATURE PROBES...........................................52
8.5.1. STANDARD SOLUTION ............................................................................................................... 52
8.5.2. OPTIONAL SOLUTION................................................................................................................. 52
POWER TERMINAL BOX ROTATION PROCEDURE................................................................53
TIGHTENING TORQUE FOR FLAMEPROOF ENCLOSURES BOLTS.....................................55
SPARE PARTS............................................................................................................................55
9. MAINTENANCE PLAN......................................................................................................................... 55
10. MOTOR ABNORMALITIES IN SERVICE............................................................................................. 58
COMMOM DAMAGE TO INDUCTION MOTORS.............................................................58
10.1.1. SHORT CIRCUIT AMONG TURNS............................................................................................. 58
10.1.2. DAMAGE CAUSED TO THE WINDING...................................................................................... 58
10.1.2.1 ONE PHASE OF THE BURNT WINDING......................................................................58
10.1.2.2 TWO PHASES OF THE BURNT WINDING...................................................................58
10.1.2.3 THREE PHASES OF THE BURNT WINDING...............................................................58
10.1.3. DAMAGE TO THE BEARINGS ................................................................................................... 59
10.1.4. SHAFT RUPTURE ...................................................................................................................... 59
10.1.5. DAMAGE DUE TO BADLY ADAPTED TRANSMISSION PARTS OR DEFECTIVE ALIGNMENT
OF THE MOTORS...................................................................................................................................... 59
TROUBLESHOOTING CHART .........................................................................................60
TROUBLESHOOTING CHART ABOUT BEARINGS........................................................62
11. WARRANTY TERMS............................................................................................................................ 63
LIABILITY...........................................................................................................................63

8|Flameproof motors
www.weg.net

Flameproof motors | 9
www.weg.net
1. GENERAL INFORMATION
INTRODUCTION
This Manual is intended to supply and clarify
important topics that must be followed accordingly -
including storage, operation and maintenance of
WEG motors used in explosive atmospheres.
Therefore, we recommend reading it carefully,
together with the Instructions Manual and all
specific documents (data sheet, general
arrangement drawing, connection diagrams,
curves, etc.) delivered with the motor, before
performing any installation service or before
operating the electric motor.
Once these WEG motors have been designed for
explosive atmospheres, all safety information
described in item 1.2 below should be followed
carefully.
SAFETY INFORMATION
ATTENTION
When any motor or equipment is
used out of the industrial area, it is
the enduser´s responsibility to
provide all safety and protection
information while installing the motor
(for example, to avoid that people
come close to the motor and others).
ATTENTION
The motors referenced in this manual
go thorough constant improvement
so the information contained here
may be changed without prior notice.
DANGER
During operation, such equipment
has energized or rotating parts that
may present high temperature.
Opened terminal boxes, unprotected
couplings or incorrect handling may
cause serious accidents to people
and/or material damage.
The people responsible for
installation safety should ascertain
that:
- Only qualified personnel perform
installation and operation services on
the equipment;
- This personnel must carry this
Manual along with other documents
supplied with the motor, and the
works should be performed in
accordance with specific standards
and documentation for this product;
- Unqualified personnel should never
perform any work on electric
equipment;
- If installation and safety instructions
are not followed accordingly,
warranty may be void.
ATTENTION
QUALIFIED PERSONNEL are those
people who based on their
education, experience, knowledge of
standards and service conditions
required are duly authorized to
perform any service on the motor.
Furthermore, these people should
know how to carry out first aid
procedures.
If further doubts exists about this,
especially in reference to specific
product information, WEG is willing
to provide such information via its
network of authorized service agents
and/or representatives.

10 |Flameproof motors
www.weg.net
ATTENTION
We recommend that all services
related to installation plan as well as
all transportation activities, storage,
assembly, installation, start-up,
maintenance and repairs should be
carried out only by qualified
personnel. Special attention should
be paid to:
- Technical data referred to
allowed applications (assembly
conditions, connections and
installation conditions), included in
this Manual, Purchase Order
documentation, operation
instructions, manuals and other
documents;
- Instructions and specific
conditions for installation on site;
- The use of proper tools and
equipment: for handling and
transportation;
- That all protection devices of
each component are removed before
installation.
Additionally, all individual parts must
be stored in vibration-free rooms to
avoid sudden faillure, knocking or
damage to parts and causing injury
to people.
For practical reasons, it is not
possible to include in this Manual
detailed information that covers all
constructive variables, nor covering
all possible assembly, operation or
maintenance alternatives.
For this reason, the present Manual
only includes required information
that allow qualified and trained
personnel to carry out the work.
In order to allow WEG to provide a prompt service
when resquested, within technical standards, the
motor serial number that is available on the
identification nameplate should be supplied.
ATTENTION
If this Installation and Maintenance
Manual gets lost, WEG may provide
an additional sample. WEG is
prepared to solve any further doubt
you may require. In this case, motor
serial number should be also
supplied.
Aiming a satisfactory motor performance, we
suggest to make the installation plan,
commissioning, start up and maintenance in
conjunction with WEG Service Department people.
ATTENTION
To prevent from eventual motor
operating problems, we recommend
that all maintenance and revision
services described in this Storage,
Installation, Operation and
Maintenance Manual be carried out
by duly trained personnel. Changes
of rated operating characteristics,
such as excess demand of energy,
increase in temperature, noise level,
abnormal smell and tripping of
protections are the first signs of any
abnormal occurrence. In this case, to
avoid material damage or injury to
people, maintenance people should
be immediately informed about such
circumstances.
DANGER
In case of doubt, switch off the motor
immediately!
EX ATMOSPHERE INFORMATION
We recommend that all personnel
responsible for the application of
electric motors in hazardous areas
have been duly trained for such
purpose.
ATTENTION
Safety and start up instructions meet
the followind standards:
IEC 60034-1 Electric Rotating
Machines
IEC 60079-0 –General Standard for
Explosion Proof Equipment
IEC 60079-1 –Standard for Ex "d"
Protection
IEC 60079-7 –Standard for Ex "e"
Protection
IEC 60079-31 –Standard for Ex "tb"
Protection
IEC 60079-14 –Electrical
installations design, selection and
erection in explosive atmospheres.
IEC 60079-17 –Electrical
installations inspection and
maintenance in explosive
atmospheres.

Flameproof motors | 11
www.weg.net
NOTE
WEG states that all information
included in this Manual make part of
the contract and motor warranty.
2. GENERAL INSTRUCTIONS
MOTOR APPLICATION
Based on the above mentioned Standards, WEG
motors are intended for industrial applications.
NOTE
It is not allowed to use standard
design motor in explosive
atmospheres if they have not been
specifically certified for such
purpose.
EX ATMOSPHERE INFORMATION
This symbol indicates that the
present paragraph contains
important information about
explosive atmospheres, which must
be strictly followed to avoid damages
and risks.
If a customer makes special requirements, he will
be then responsible to provide safety measures.
The ambient parameters for WEG standard motors
are the following:
- Temperature: -20ºC ≤T ≤+40ºC;
- Altitude: ≤1000 masl;
In environments containing water and dust, motor
installation will only be allowed if such motor is
specifically designed for such purpose with
instructions on its nameplate.
2.1.1. SAFETY WARNINGS IN THE MANUAL
During installation, operation and maintenance, the
following symbols must be considered:
DANGER
Failure to observe the procedures
recommended in this warning may
result in death, serious injuries and
extensive equipment damage.
ATTENTION
Failure to observe the procedures
recommended in this warning may
result in equipment damage.
NOTE
This provides important information
for correct understanding and proper
operation of the product.
EX ATMOSPHERE INFORMATION
This provides important information
for correct understanding and proper
operation of the Ex Certified product.
TRANSPORTATION
WEG motors equipped with cylindrical-roller,
angular contact or sleeve bearings are supplied with
a shaft locking device on DE side (in some cases,
shaft locking device on NDE side can also be
applied, for example in sea transportation).
Corrosion resistant protection is applied on all
machined surfaces as well.
A visible warning is placed on the motor whenever
this is equipped with a shaft locking device on the
NDF side.
Prior to shipment, motors are factory–tested and
dynamically balanced.
ATTENTION
Shaft locking device must be
removed before putting the motor
into operation.
ATTENTION
Whenever motor is transported,
reuse shaft locking device.
ATTENTION
To avoid accidents and damages to
the motor, it should be always lifted
with proper cables and devices.

12 |Flameproof motors
www.weg.net
ATTENTION
Motor should only be lifted by the
eyebolts. These eyebolts have been
designed to hold motor weight only.
So avoid lifting additional loads.
Special care should be taken with the motor
package so as to avoid any damage to it.
Figure 2-1 - Warning stamp for NDE locking device
removal.
RECEIVING INSPECTION
When receiving the motor, check if any damage has
occurred during transportation. Then remove the
shaft locking device and keep it in a safe room once
it needs to be used on future transportation.
If anything has been noticed, notify immediately the
carrier, the insurance company and WEG.
EX ATMOSPHERE INFORMATION
Failure in giving notice to the carrier,
to the insurance company and to
WEG may result in loosing the
warranty.
When lifting the boxes, it is important to observe the
appropriate locals for this purpose as well as to
check the weight of the box and the hoist capacity.
The motors shipped in wooden boxes must be
always lifted by the eyebolts or by forklift machines
and never by the shaft. The box must never be
turned around. Lifting and lowering of such boxes
must be done gently in order to avoid damage to the
bearings.
After being removed from the package, a complete
visual inspection on the motor should be made.
Do not remove the existing protecting grease from
the shaft end, nor the stoppers or plugs that close
the terminal box holes, if any. These protection
items must be kept in place until the final installation
has been concluded.
For motors supplied with roller bearings, shaft
should be rotated manually a few times for a uniform
grease distribution.
ATTENTION
To ensure the degree of protection,
the connection box should be kept
closed. Before energise the motor,
check the cleanliness and moisture
condition inside of the terminal box.
3. STORAGE
INDOOR STORAGE
When motors are not unpacked immediately after
receiving, they should be maintained in places
protected from humidity, vapors, sudden heat
changes and rodents. To avoid bearing damage,
motor should also be storage in places free of
vibrations. Any painting damage and protecting
grease absent areas should be fixed so as to avoid
future rusting.
For maintenance purposes, please refer to Table
3-4.
OUTDOOR STORAGE
A dry storage location, safe from flooding, dust-free
and free from vibrations, should be choosen. Repair
any damage to the packing before putting the
equipment in storage to ensure proper storage
conditions. Position machines, devices and crates
on pallets, wooden beams or foundations that
guarantee protection against ground dampness. It
also prevents the equipment from sinking into the
ground and allows the circulation of air underneath
the equipment.
Covers or tarpaulins used to protect the equipment
against the weather must not make contact with the
surfaces of the equipment. Ensure adequate air
circulation by positioning wooden spacer blocks
between the equipment and such covers.
For maintenance purposes, please refer to Table
3-5.

Flameproof motors | 13
www.weg.net
VERTICAL MOTORS STORAGE
Vertical motors should be stored in the position as
they were initially transported. Usually they can be
stored in vertical or horizontal position but this
needs always to be prior validated with WEG
Service Team.
OTHER CARES DURING
STORAGE
For motors fitted with space heaters, these
accessories must be kept switched-on.
If painting has suffered any damage, this must be
repainted to avoid rusting. The same applies to the
machined surfaces when protecting grease has
been wasted.
INSULATION RESISTANCE
EX ATMOSPHERE INFORMATION
Be sure that no potentially explosive
atmosphere is present before any
measuring of Insulation Resistance.
DANGER
Before measuring insulation
resistance, the machine must be at
standstill and all windings and frame
must be grounded for a time to
remove all residual electrostatic
charge (connect all winding to the
frame and this one to the ground).
Capacitors (if any) must also be
grounded before disconnecting and
separating the terminals to measure
the insulation resistance.
The non observation of these
precautions may result in injury to
personnel.
When a motor is not immediately installed, it should
be then protected against moisture, heat and dirt so
as to avoid deterioration of the insulation. The
winding insulation resistance must be measured
before operating the motor.
If the ambient contains high humidity, a periodical
inspection is recommended during storage. It is
difficult to determine rules for the actual insulation
resistance value of a motor as the resistance varies
according to type, size, rated voltage, condition of
the insulating material used and method of
construction of the motor. A lot of experience is
required to decide when a motor is ready for
operation. Periodical records will help to take such
decision.
DANGER
Disconnect motor from power supply
before making any insulation
measurement.
The insulation resistance should be measured using
a Megohmmeter. The test voltage for the motors
windings should be according the table below in
accordance with the standard IEEE 43.
Table 3-1 –Insulation resistance test voltage
Winding rated voltage
(V)
Insulation resistance test
direct voltage (V)
< 1000
500
1000 –2500
500-1000
2501 –5000
1000 –2500
5001 - 12000
2500 –5000
> 12000
5000 –10000
The test voltage for space heaters, other
accessories and thermal protectors is 500Vcc.
If the test is performed at a different temperature, it
is necessary to correct the resistance reading to
40ºC by using an insulation resistance variation
curve in relation to temperature, given by the motor
itself. If this curve is not available it is possible to use
an approximate correction given by the curve of
Figure 3-1, as per IEEE 43 Standard.
Figure 3-1 –Insulation resistance variation with
temperature

14 |Flameproof motors
www.weg.net
ATTENTION
On motors still in operation higher
values may be obtained compared to
new motors. On new motors lower
values can be obtained, as solvents
are present in the insulating
varnishes which become volatile in a
later stage during normal operation.
This does not necessarily mean that
the motor is not suitable for operation
once the insulation resistance will
increase after a period of operation.
The comparison with values
obtained from previous tests on the
same motor under identical load,
temperature and humidity conditions
will be a better indication of the
insulation conditions in comparison
to the value obtained from a single
test. Any sudden or high reduction of
the value requires careful attention.
Table 3-2 –Recommended minimum insulation
resistance values at 40ºC (all values in MΩ)
Minimum insulation
resistance
(megohms)
Test specimen
/R1min =100
For most ac winding built after
about 1970 (form-wound coils)
/R1min =5
For most machines with random-
wound stator coils and form-
wound coils rated below 1kV
MINIMUM INSULATION RESISTANCE
If the insulation resistance measured is smaller than
100 M(for medium or high voltage motors) and 5
M(for low voltage motors), the winding must be
dried according to the procedure below before
starting the motor:
- Disassemble the motor, removing the rotor and
the bearings;
- Take the frame with stator winding to an oven
and warms it to a temperature of 130°C, keeping
this temperature for at least 8 hours. For bigger
machines (above IEC frame 630), it can be
necessary to stay for at least 12 hours).
Double check the insulation resistance to verify if it
has reached the acceptable values, according to
Table 3-2, otherwise refers to WEG for instructions.
POLARIZATION INDEX
The polarization index (P.I.) is traditionally defined
as a ratio of the 10 min. insulation resistance (IR10)
to the 1 min. insulation resistance (IR1), tested at a
relatively constant temperature.
Through the polarization index, the user can
evaluate the motor insulation conditions, according
to the table bellow:
Table 3-3 - Polarization index
Polarization Index
Insulation Level
1 or smaller
Bad
< 1,5
Dangerous
1,5 to 2,0
Abnormal
2,0 to 3,0
Good
3,0 to 4,0
Very Good
> 4,0
Excellent
EX ATMOSPHERE INFORMATION
To avoid electric discharge risks,
discharge the terminals right after
performing the measurement.
DANGER
In order to avoid injuries to
personnel, the winding must be
grounded immedialtly after
measuring the insulation resistance.
PROLONGED STORAGE
3.7.1. INTRODUCTION
The instructions for long term storage described as
follows are valid for motors to be long term stored
and/or long periods of standstill before the
commissioning.
3.7.2. GENERALITIES
The existing tendency, especially during the
construction of the plant, of storing the motors for
several years before commissioning or to install
immediately some units, results that the motors are
exposed to influences that cannot be evaluated in
advance for this time's period.
It is difficult to evaluate the different forms of stress
(atmospheric, chemical, thermal, and mechanical)
imposed to the motor, which might happen during
storage maneuvers, assembly, initial tests and
storage until the commissioning.
Other essential factor is the transportation, for
example, the general contractor may transport the
motor or the complete unit with motor as joint
transportation to the installation location.
The motor internal gaps (air gap, bearings and
interior of connection box) are exposed to the

Flameproof motors | 15
www.weg.net
atmospheric air and temperature fluctuations. Due
to the air humidity, it is possible the liquid
condensation and, depending on the kind and air
contamination degree, aggressive substances may
penetrate into these spaces.
As a consequence, after long periods the internal
components such as the bearings might get rust, the
insulation resistance can decrease to under the
admissible values and the grease lubricant capacity
in the bearings is adversely affected. This influence
increases the damage risk before commissioning of
the plant.
The flameproof joints of terminal boxes that were
exposed during storage, for example to allow the
measuring of the insulation resistance, before
assembling and bolting, should be properly
protected against corrosion with a thin layer of
grease from one type recommended by WEG in
section 3.7.8.
NOTE
To keep manufacturer's warranty, it
should be insured that the described
preventive measures in this
instructions are followed and
registered: constructive aspects,
preservation, packing, storage and
inspections.
3.7.3. STORAGE PLACE
3.7.3.1 INDOOR STORAGE
In order to ensure the best storage conditions to the
motor during long standstill periods, the storage
location should obey rigorously the criteria
described as follow:
-Closed storage room with roof;
-The location must be protected against
humidity, vapors, aggressive fumes
discharge, fast heat changes, gnawing and
insects;
-It must not present corrosive gases such as
chlorine, sulfur dioxide or acid;
-It must not present continuous or intermittent
vibrations;
-It should have ventilation system with filter;
-It must not present quickly changes of
temperature;
-Ambient temperature (5° C < T < 60 °C);
-Relative air humidity < 50%;
-It should have prevention against dirt and
dust deposits;
-It should have fire detection system;
-Electrical supply for space heater and
illumination must be provided.
If some of these requirements can not be attended
by the storage environment, WEG suggests that
additional protections be incorporated in the motor
packing during the storage period, like follows:
- Closed wooden or similar box with electrical
installation, enable to the space heaters supply;
- Closed wooden box or similar with installation
that allows the space heaters be energized;
- If there is a risk of fungus infestation and
formation, the packing must be protected in the
storage location by spraying or painting it with
appropriated chemical agents;
- Preparation of packing must be done with
greatest care by an experienced person. A
reliable packing company must take over of the
packing.
3.7.3.2 OUTDOOR STORAGE
The outdoor storage of the motor is not
recommended.
If the external storage cannot be avoided, the motor
should be packed in specific packing for this
condition, as described bellow.
-For outdoor storage, besides the packing
recommended above, we recommend to
cover completely this packing with a
protection against dust, humidity and other
strange materials.
-Place the packing in pallets, wooden bunches
or foundations that guarantee the protection
against the soil humidity.
-Prevent the packing sink itself in the soil.
-After covering the machine, a shelter should
be build to protect it against rain, snow and
excessive sun heat.
ATTENTION
It is recommendable to check the
storage local conditions and the
motors condition according to the
maintenance plan for long term
storage, described in this manual.
3.7.4. SPARE PARTS
If parts have been supplied separately (terminal
boxes, endshields, covers, etc...) these ones must
be packed as described above.
The air relative humidity inside the packing should
not exceed 50% until unpacking the machine.
3.7.5. SPACE HEATERS
The space heaters installed in the motor must be
energized during the storage period to avoid the
moisture condensation inside the motor and this

16 |Flameproof motors
www.weg.net
way keeping the winding insulation resistance within
acceptable levels.
ATTENTION
The space heaters of the motor must
be mandatorily energized when the
motor is stored in local with
temperature < 5 °C and relative air
humidity > 50%.
3.7.6. INSULATION RESISTANCE
During the storage period, the winding insulation
resistance of the motor should be measured
according to item 3.5 of this manual and registered
every 3 months and before the motor installation.
Eventual drops in the insulation resistance level
must be investigated.
3.7.7. EXPOSED MACHINED SURFACES
At factory, all exposed surfaces (for example, the
shaft edge and flanges) are protected with a
temporary protective agent (rust inhibiter).
This protective coating should be reapplied every 6
months at least. When this coating is removed
and/or damaged, the same preventive action must
be done.
RECOMMENDED PRODUCTS
- Anticorit BW 366, Manufacturer: FUCHS.
- Dasco Guard 400 TX AZ, Manufacturer:
D.A.Staurt.
- Tarp, Manufacturer: Castrol.
- Tectyl 511-M, Manufacturer: Valvoline.
3.7.8. FLAMEPROOF JOINTS
For motors with protection “d”, all the surfaces of
flameproof joints shall be verified with special care
to assure that all the machined surfaces of
flameproof joints are properly protected with a
corrosion inhibiting grease.
Before the assembly of any part of motor or terminal
box enclosures, the surfaces of flameproof joints
shall be protected against corrosion with protective
grease.
AUTHORIZED PRODUCTS
- Polyrex EM, Manufacturer: MOBIL.
- Molycote 33, Manufacturer: Dow Corning
Corporate.
- Lumomoly PT/4, Manufacturer: Lumobras.
3.7.9. BEARINGS
3.7.9.1 ANTIFRICTION BEARINGS
LUBRICATED BY GREASE
The bearings are lubricated at the factory to perform
the motor tests.
During the storage period, every two months is
necessary to remove the shaft locking device and
turn the shaft manually to conserve the bearing in
good conditions. After perform the shaft rotation,
this one shall be turned at 45º from the original
position.
After 6 months of storage and before starting in
operation, the bearings should be regreased, as
item 8.2.7 of this manual.
If motor is kept in storage for approximately 2 years
or more, the bearings must be inspected and
regreased according to item 8.2 of this manual.
3.7.9.2 SLEEVE BEARINGS
Motors with sleeve bearings are always transported
without oil inside the bearings.
The motor must be stored in its original operation
mounting position and with oil inside the bearings
(see oil quantities in the Table 8-17).
The oil level should be respected, remaining in the
midle of the oil sight glass.
During the storage period, every two months is
necessary to remove the shaft locking device and
rotate at about 30 rpm for the oil circulation and to
conserve the bearing in good conditions.
If it is not possible to rotate the shaft of the motor,
the follow procedure should be used to protect
internally the bearing and the contact surfaces
against corrosion:
- Drain the whole bearing oil;
- Dismantle the bearing, following the procedure
described in the item 8.2.10.3 of this manual;
- Clean the bearing;
- Apply the anti-corrosive (ex.: TECTIL 511 or
equivalent) inside the bearing, bearing line (top
and bottom half) and in the shaft contact surface
of the motor;
- Assemble the bearing, following the procedure
described in the item item 8.2.10.4 of this
manual;
- Close all tapped holes with screw plugs;
- Seal the gaps between the shaft and bearing
seal, and between bearing seal and bearing
housing by using self-adhesive permanent tape;
- Connecting flanges (Ex.: Oil inlet and outlet)
must be covered with blank plates.
- Remove the bearing top sight glass and spray
the corrosion inhibitor on the bearing.
- Put some desiccant (silica gel) inside of the
bearing. The desiccant absorbs the humidity and
prevents the formation of moisture and water
condensation inside the bearing.

Flameproof motors | 17
www.weg.net
- Close the bearing tightly with the top sight glass.
In case the standstill period is longer than 6
months:
- Repeat the procedures described above.
- Replace the desiccant (silica gel) into the
bearing each six months.
In case the standstill period is longer than 2 years:
- Dismantle the bearing;
- Preserve and store the bearing parts.
ATTENTION
By using either a chain block or a
jack, raise the end of the rotor at
which the work is being done
aproximately 0.1 to 0.3mm so as to
remove the weight from the bottom
half of the bearing and not damage
the flameproof labyriths.
3.7.10. CONNECTION BOX
When the winding insulation resistance of the motor
is verified, the main terminal box and the auxilliary
terminal boxes must also be inspected, observing
the following aspects:
- The interior should be dry, cleaned and free of
any dust accumulation.
- The contact elements cannot present corrosion.
- The machined surfaces of explosion proof
terminal boxes with protection “d” which
functions as flamepath joints should be perfectly
clean, without any deformation, damage or
scratches. Before reassembling the covers of
these terminal boxes apply a corrosion inhibiting
grease (ex.: Polyrex EM or Molycote 33 or
Lumomoly PT/4) to avoid the corrosion of the
machined surfaces.
- The motors with protection “de” are equipped
with terminal boxes with protection “e” that
constructively can be the same used for
protection “d”. In this case, machined surfaces
don’t function as flamepath joints but it’s very
important to maintain them in good conditions
applying also a corrosion inhibiting grease (ex.:
Polyrex EM or Molycote 33 or Lumomoly PT/4)
to avoid the corrosion of the machined surfaces.
- The cables inlet should be correctly sealed.
- The cable entrances into the terminal boxes
must be done using certified cables glands with
the same, or higher, protection of the motor (Ex
d IIB, Ex d IIC, Ex e, Ex d I or Ex e I) indicated in
the motor nameplate.
If any of these items are not in proper condition, an
adequate maintenance should be performed and, if
necessary, the damaged parts should be replaced.
EX ATMOSPHERE INFORMATION
The use and assembling of the
appropriate cable glands is
responsibility of the motor installer.
3.7.11. INSPECTIONS AND RECORDS DURING
STORAGE
The stored motor must be inspected periodically
and inspection records must be filled.
The following points must be inspected:
- Physical damages;
- Cleanliness;
- Signs of water condensation;
- Protective coating conditions;
- Paint conditions;
- Signs of aggressive agents;
- Satisfactory operation of space heaters. It is
recommended that a signaling or alarm system
be installed in the location in order to detect
power interruption on the space heaters;
- Record the ambient temperature and relative
humidity around the motor, the winding
temperature (using RTDs), the insulation
resistance and the polarization index;
- Record vibrations, in horizontal, vertical and
axial directions at Drive End and Non Drive End
sides to guarantee that motor is not being
subjected to harmfull values;
- Storage site, so that it complies with the criteria
described in sub-section 3.7.3.
3.7.12. PREPARATION FOR SERVICE AFTER
LONG TERM STORAGE
3.7.12.1 CLEANING
- The machine interior and exterior should be free
of oil, water, dust and dirt.
- Remove the corrosion inhibitor of the exposed
surfaces with a cloth soaked in petroleum based
solvent.
- Be sure that the bearings and cavities used to
lubrication are free of dirt and the plugs on the
holes are correctly sealed and tighten.
Oxidations and marks on the bearings seats and
shaft should be carefully removed.
- Be sure that the flameproof joints that were
exposed during storage are free of any
corrosion, scratches or deformations and are
properly protected against corrosion.

18 |Flameproof motors
www.weg.net
3.7.12.2 BEARINGS LUBRICATION
Use the lubricant specified for bearing lubrication.
This information is indicated on the bearings
nameplate, and the lubrication must be done as
described in chapter 8-MAINTENANCE of this
Manual, always considering the type of bearing.
ATTENTION
Inspection to the rolling bearing must
be performed. If there are corrosion
signals or races marks, the bearing
must be replaced.
NOTE
Sleeve bearings, where was applied
internally the protection product
against corrosion and desiccant,
should be disassembled as the
procedure described in the item
8.2.10.3 of this manual, washed for
remove the anti-corrosive agent and
the desiccants.
Assemble again the bearings, as the procedure
described in the item 8.2.10.4 of this manual and
proceeds the re-lubrication.
3.7.12.3 INSULATION RESISTANCE
VERIFICATION
Before starting in operation the insulation resistance
must be verified, according to the section 3.5 of this
manual.
3.7.12.4 OTHER
Follow the further procedures described in the
chapter 5-INSTALLATION of this manual, before
putting the machine in operation.

Flameproof motors | 19
www.weg.net
3.7.13. MAINTENANCE PLAN FOR STORAGE
During the storage period, the motor maintenance
must be executed and registered according to the
plan described in the table below:
Table 3-4 - Maintenance plan for indoor storage
Inspection / Periodicity
1M
2M
6M
2Y
BS
Storage
Cleanliness
X
X
Humidity and Temperature
X
Check for signs of insect
infestation
X
Vibration Levels
X
Packaging
Physical Damages
X
Relative Humidity inside
Motor
X
Replace Dehumidifier Bag
X
Space Heaters
Check operation
conditions
X
Complete Motor
Perform External Cleaning
X
X
Tubes cooling exchanger
X
Check Painting Conditions
X
Check Oxidation Inhibitor
on Exposed Machined
Parts
X
Replace the Oxidation
Inhibitor
X
Windings
Measure Insulation
Resistance
X
X
Measure Polarization
Index
X
X
Terminal Box and Grounding Terminals
Clean the boxes inner
parts
X
X
Inspect Seals and Sealing
X
X
Bearings
Rotate the Shaft
X
Lubricate the Bearings
X
X
Disassemble / Clean
Bearings
X
Sleeve Bearings
Rotate the Shaft1)
X
Apply Anticorrosive and
Dehumidifier
X
Clean / Lubricate Bearings
X
Disassemble / Store
Bearing Parts
X
1)After rotate, positioning the shaft at 45º from the original
position.
1M All inspections that must be performed and recorded on
a monthly basis;
2M All inspections that must be performed and recorded
every two months;
6M All inspections that must be performed and recorded
every six months;
Table 3-5 - Maintenance plan for outdoor storage
Inspection / Periodicity
1M
2M
6M
2Y
BS
Storage
Cleanliness
X
X
Humidity and Temperature
X
Check for signs of insect
infestation
X
Vibration Levels
X
Packaging
Physical Damages
X
Relative Humidity inside
Motor
X
Replace Dehumidifier Bag
X
Space Heaters
Check operation
conditions
X
Complete Motor
Perform External Cleaning
X
X
Tube cooling exchanger
X
Check Painting Conditions
X
Check Oxidation Inhibitor
on Exposed Machined
Parts
X
Replace the Oxidation
Inhibitor
X
Windings
Measure Insulation
Resistance
X
X
Measure Polarization
Index
X
X
Terminal Box and Grounding Terminals
Clean the boxes inner
parts
X
X
Inspect Seals and Sealing
X
X
Bearings
Rotate the Shaft
X
Lubricate the Bearings
X
X
Disassemble / Clean
Bearings
X
Sleeve Bearings
Rotate the Shaft1)
X
Apply Anticorrosive and
Dehumidifier
X
Clean / Lubricate Bearings
X
Disassemble / Store
Bearing Parts
X
1)After rotate, positioning the shaft at 45º from the original
position..
2Y All inspections that must be performed and recorded
after 2 years;
BS All inspections that must be performed and recorded
before Start-up;

20 |Flameproof motors
www.weg.net
4. HANDLING
Use only the existing eyebolts to lift the motor.
Never lift the motor by the shaft. Check the motor
weight. Lifting and lowering must be done gently in
order to avoid damage to the bearings.
HANDLING RIBBED COOLED
MOTORS
4.1.1. HORIZONTAL MOTORS
The eyebolts attached to endshields, fan cover, etc,
should be used to handle these specific
components only. The complete motor should be
lifted only by the eyebolts in the frame.
Figure 4-1 - W22Xd LINE –horizontal ribbed cooled
motors
Lifting lugs on the frame are designed for
lifting machine only. Do not use for lifting
coupled equipment such as pumps,
compressors, gears or other equipment;
The chains or handles of hoisting must have
on maximum angle of 30º with regard to
vertical line:
Use all of eyebolts fixed in the frame, supplied
together with the motor;
Failure to observe these precautions may
result in damage to the equipment, injury to
personnel or both.
When the risk of motor damage exists by the
lifting chains, special tools must be predicted
by the customer.
4.1.2. VERTICAL MOTORS
Figure 4-2 - W22Xd LINE –vertical ribbed cooled motors
The handling of the vertical ribbed cooled motors
must be done as showed in the Figure 4-2.
Lift the motor using 2 cranes and 4 eyebolts:
2 chains or cables in motor eyebolts (b) and
2 chains or cables in flange eyebolts (a); (see
detail in Figure 4-3)
Lower the crane that is holding the flange
eyebolts (a) and simultaneously lift the crane
holding motor eyebolts (b);
Attach a third chain or cable (c) to the crane
holding motor eyebolts (b);
Continue to lower the crane attached to
flange eyebolts until motor is in vertical
position and remove flange chains and
eyebolts (a).
1
2
3
4
a) b)
a)
b)
a) b)
c) c)
b)
c)
b)b)
a) a)
b)
a)
b)
a)
b)
a)
b)
a)
b)b) c)
30º
Other manuals for W22Xdb C 315
1
This manual suits for next models
1
Table of contents
Other WEG Engine manuals
Popular Engine manuals by other brands
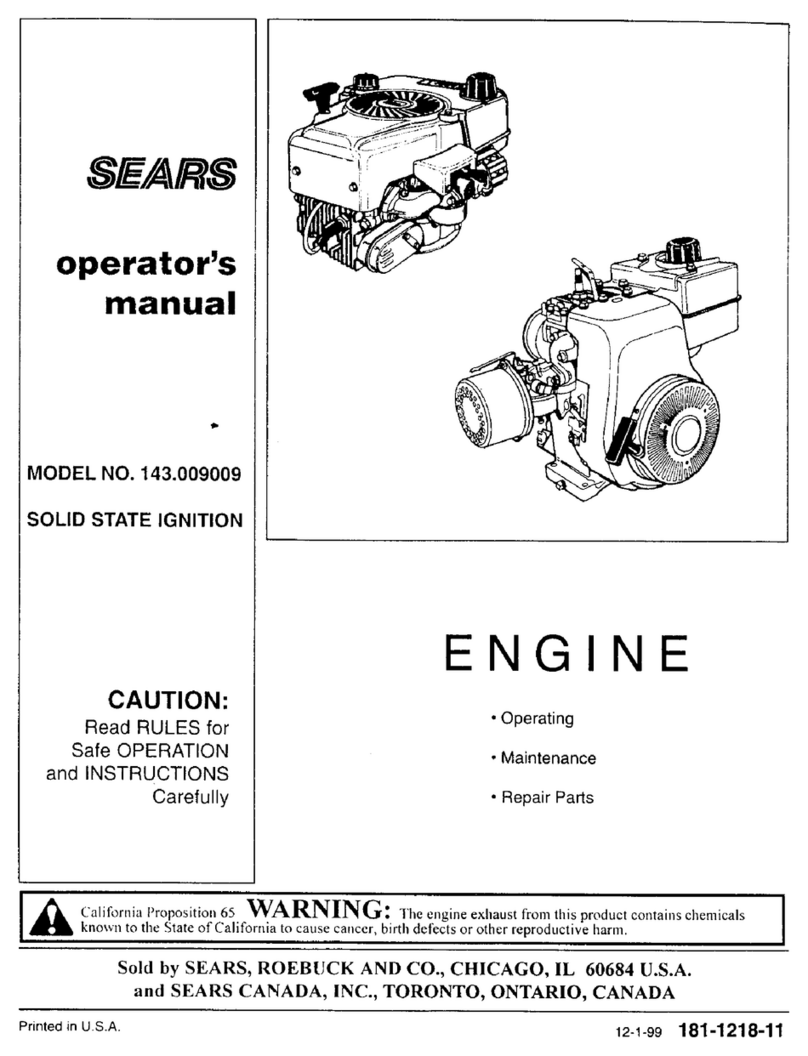
Sears
Sears 143.009009 Operator's manual
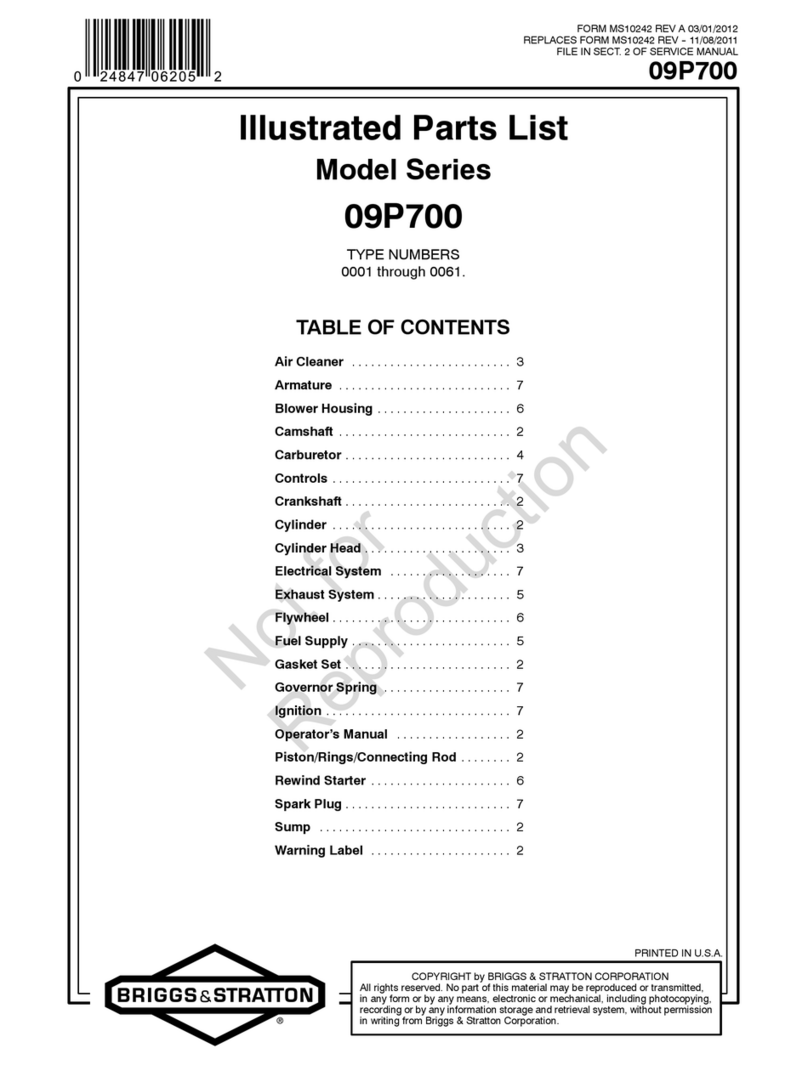
Briggs & Stratton
Briggs & Stratton 09P700 Series Illustrated parts list
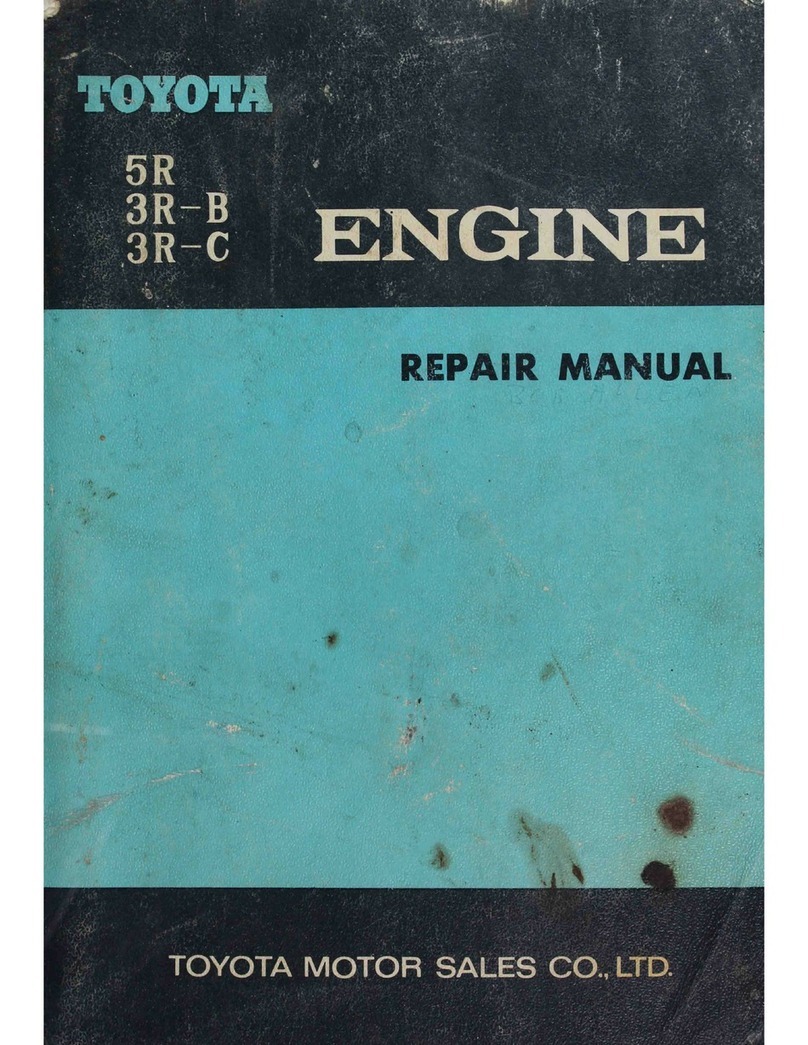
Toyota
Toyota 5R 1969 Repair manual
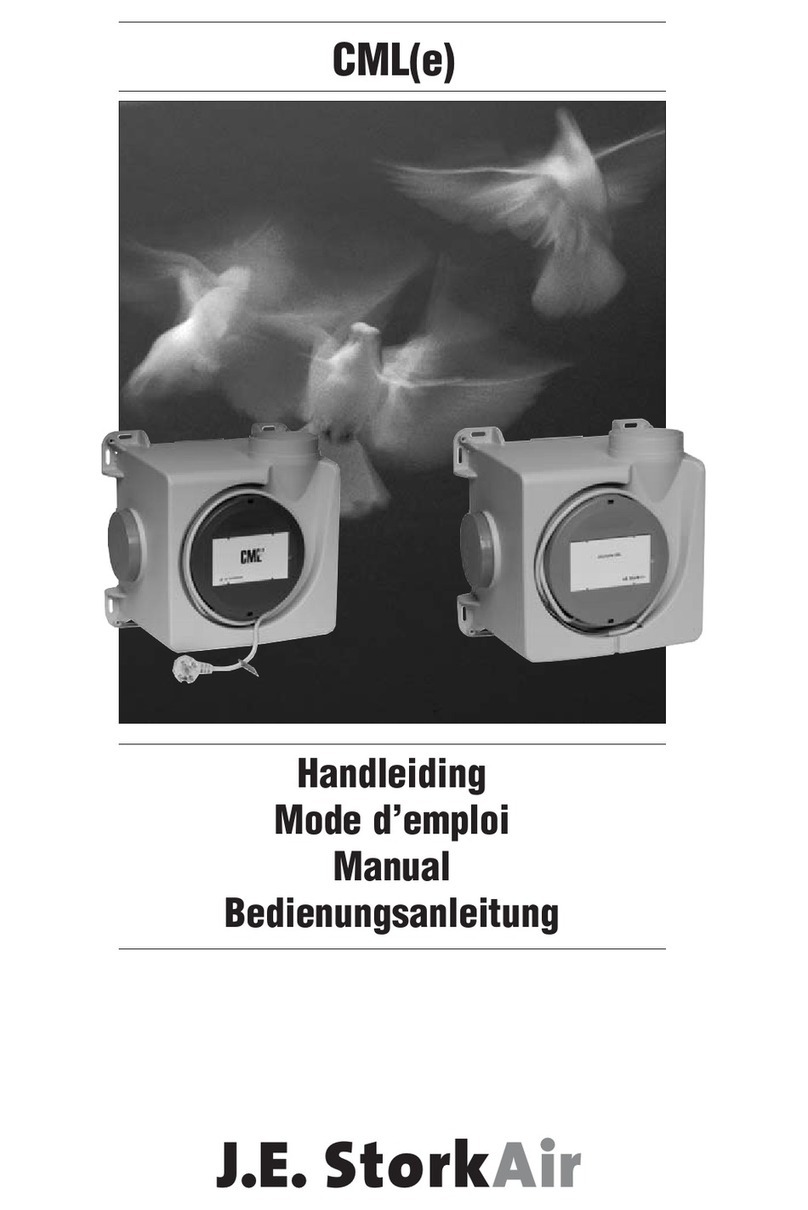
J.E. StorkAir
J.E. StorkAir CML manual
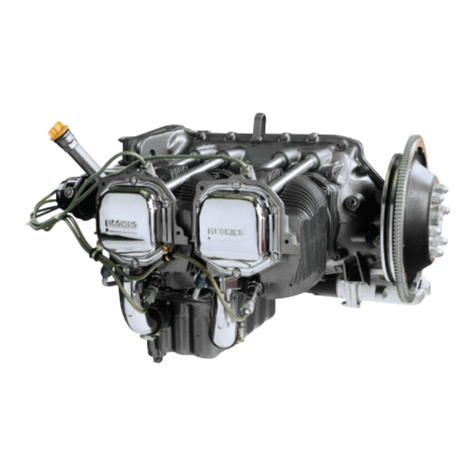
Lycoming
Lycoming IO-360-N1A Installation and operation manual

Vestamatic
Vestamatic VL-ME-230-45 Series Installation and operating instructions