Weidmüller maxGUARD User manual

Load monitoring with integrated potential distribution
maxGUARD
Manual
Letʼs connect.

Content
2Manual maxGUARD2526740000/02/03.2018
1 About this documentation 3
1.1 Symbols and notes 3
1.2 Complete documentation 3
2 Safety 4
2.1 General safety notes 4
2.2 Intended use 4
2.3 Use in explosive risk zones 5
2.4 Legal notice 5
3 System overview 6
3.1 Mode of operation and connection concept 7
3.2 Functions 8
3.3 Type plate 8
3.4 Markers 9
3.5 Internal fuse 10
3.6 Product overview 11
3.7 General technical data 14
3.8 Tripping characteristics 16
3.9 Conformity and approvals 19
4 Conguration 21
4.1 Conguration in the Weidmüller Congurator 21
4.2 Arrangement and combination of the modules 21
4.3 Installation position and mounting distances 22
4.4 Conguring cross-connections 22
4.5 Earthed and non-earthed control voltage distributors 23
4.6 Connection to the control unit 24
4.7 Segmentation of control voltage distributors 25
4.8 Extending control voltage distributors 26
4.9 Example congurations 27
5 Feed-in modules, control modules, alarm modules 30
5.1 Passive feed-in modules AMG FIM-0... 30
5.2 Active feed-in modules AMG FIM-C... 31
5.3 Control modules AMG CM... 32
5.4 Alarm modules AMG AM... 33
6 Electronic load monitors 34
6.1 AMG ELM-x... 34
6.2 AMGELM-xF... 36
6.3 AMGELM-xF CL2 38
6.4 AMGELM-Qxxxx 40
6.5 AMG ELM-xD C0 42
7 Potential distribution terminals 44
7.1 AMG PD... potential distribution terminal 44
7.2 AMG OD... potential distribution terminal 44
7.3 AMG MD... potential distribution terminal 45
7.4 AMG XMD... potential distribution terminal 45
7.5 AMG DIS... potential distribution terminal 46
8 Installation and wiring 47
8.1 Preparations for installation 47
8.2 Installing the maxGUARD station 48
8.3 Attaching markers 50
8.4 Installing cross-connectors 50
8.5 Wiring 51
8.6 Insulation tests 52
9 Operation 53
9.1 Commissioning 53
9.2 Switching load monitors on/off 53
9.3 Resetting load monitors 54
9.4 Setting a new characteristic 54
10 Disassembly and disposal 55
10.1 Required tools 55
10.2 Disassembling a module 55
10.3 Disassembling a maxGUARD station 55
10.4 Disposing of a maxGUARD station 56
11 LED indicators and troubleshooting 57
ANNEX A-1
Normal tripping characteristic 1AN A-2
Normal tripping characteristic 2AN A-3
Normal tripping characteristic 3AN A-4
Normal tripping characteristic 4AN A-5
Normal tripping characteristic 6AN A-6
Normal tripping characteristic 8AN A-7
Normal tripping characteristic 10AN A-8
Normal tripping characteristic 12AN A-9
Normal tripping characteristic 1ACL2 A-10
Normal tripping characteristic 2ACL2 A-11
Normal tripping characteristic 4ACL2 A-12
Lagged tripping characteristic 1AT A-13
Lagged tripping characteristic 2AT A-14
Lagged tripping characteristic 3AT A-15
Lagged tripping characteristic 4AT A-16
Lagged tripping characteristic 6AT A-17
Lagged tripping characteristic 8AT A-18
Lagged tripping characteristic 10AT A-19
Lagged tripping characteristic 12AT A-20
Manufacturer
Weidmüller Interface GmbH & Co. KG
Klingenbergstraße 16
D-32758 Detmold
T +49 5231 14-0
F +49 5231 14-292083
www.weidmueller.com
Document No. 2526740000
Revision 02/March 2018

3Manual maxGUARD2526740000/02/03.2018
1 Aboutthisdocumentation | Symbols and notes
1 About this documentation
1.1 Symbols and notes
The safety notices in this documentation are designed ac-
cording to the severity of the danger.
DANGER
Imminent danger to life!
Notes with the signal word “Danger” warn
you of situations that will result in serious
injury or death if you do not follow the
instructions given in this manual.
WARNING
Possible danger to life!
Notes with the signal word “Warning” warn
you of situations that may result in serious
injury or death if you do not follow the
instructions given in this manual.
CAUTION
Risk of injury!
Notes with the signal word “Caution” warn
you of situations that may result in injury if
you do not follow the instructions given in
this manual.
ATTENTION
Material damage!
Notes with the signal word “Attention” warn you of hazards
that may result in material damage.
Text next to this arrow are notes that are not rel-
evant to safety, but provide important information
about proper and effective work procedures.
The situation-dependent safety notices may contain the fol-
lowing warning symbols:
Symbol Bedeutung
Warning against hazardous electrical
voltage
Warning against explosive atmospheres
Warning against electrostatically charged
components
Instruction: Observe the documentation
▶All instructions can be identified by the black triangles
next to the text.
–Lists are marked with a tick.
1.2 Complete documentation
Observe the documentation delivered with the
maxGUARD products.
All documents are available to download from the
Weidmüller website.

4Manual maxGUARD2526740000/02/03.2018
2 Safety | General safety notes
2 Safety
This section includes general safety notes on handling prod-
ucts belonging to the maxGUARD family. Specic warnings
for specic tasks and situations are given at the appropriate
places in the documentation. Failure to observe the safety
notes and warnings may lead to personal injury and damage
to property.
All work may only be carried out by trained
electricians who are familiar with the safety
standards that apply to electrical engineering.
2.1 General safety notes
Work on the maxGUARD products may only be performed
by qualied electricians with the support of trained persons.
As a result of their professional training and experience, an
electrician is qualied to perform the necessary work and
identify any potential risks.
Before any work is carried out on the products (installa-
tion, maintenance, retrotting) the power supply must be
switched off and secured against being switched on again.
maxGUARD products do not contain any modules or compo-
nents that can be serviced by the user. If faults connected to
a maxGUARD product cannot be rectied using the recom-
mended measures (see chapter 11), the product in question
must be sent to Weidmüller. Weidmüller assumes no liability
if the product is tampered with!
Electrostatic discharge
maxGUARD products can be damaged or destroyed by elec-
trostatic discharge. When handling the products, the neces-
sary safety measures against electrostatic discharge (ESD)
according to IEC61340-5-1 and IEC61340-5-2 must be
observed. The packing and unpacking as well as the assem-
bly and disassembly of a device may only be carried out by
qualied personnel.
Open equipment
maxGUARD products are open equipment that may only be
installed and operated in lockable housings, cabinets or elec-
trical operations rooms. Only trained and authorised person-
nel may access the equipment.
The standards and guidelines applicable for the assembly
of control cabinets and the arrangement of data and supply
lines must be complied with.
Fusing
The operator must set up the equipment so that it is protect-
ed against overloading. The upstream fuse must be designed
such that it does not exceed the maximum load current.
The maximum permissible load current of the maxGUARD
products can be found in the technical data. The operator
must decide whether additional surge protection is required
according to IEC 62305. Voltages that exceed +/-30V may
cause the destruction of the modules.
Earthing
Products belonging to the maxGUARD family may be used
for earthed and non-earthed control voltage distributors.
Products belonging to the maxGUARD family do not have
a designated earth connection. Further information can be
found in section 4.5.
2.2 Intended use
maxGUARD is an electronic load monitoring system with
integrated potential distribution. It is used for the selective
overload and short-circuit monitoring of 24VDC control
circuits in the eld of programmable controllers or similar
control systems. Electronic load monitoring devices are used
for line protection. In case of a fault, the affected circuit is
switched off. The wire cross-section has to be dimensioned
according to the internal fuse (see section3.5).
The system must be operated with 24VDC safety extra-low
voltage (SELV, 18–30VDC) or protective extra-low voltage
(PELV).
An AMG ELM electronic load monitoring device can only
be operated in conjunction with a power-feed unit (AMG
FIM-0..., AMGFIM-C...). The potential distributors of the
maxGUARD family can be used for contact replication of the
load monitor output. Only Weidmüller ZQV4N cross-connec-
tors may be used for connections within a station.
All products belonging to the maxGUARD family are intend-
ed for use in equipment or machinery installed in enclosed
areas.
Installation in a suitable enclosure provides adequate pro-
tection against contact with live parts and also against the
ingress of dust and water (e.g. control cabinet, panel, con-
sole or similar). Mounting is only permissible on a prole
rail made of steel or galvanised steel in accordance with EN
60715 (TH35-7.5, e.g. Weidmüller TS35X7.5).
The products described in this manual may only be used for
the intended applications. If used for any other purpose, the
protective measures of the product may be rendered ineffec-
tive.
Any intervention in the products’ hardware or software other
than described in this manual may only be performed by
Weidmüller.
Observance of the documentation is also part of the intend-
ed use.

5Manual maxGUARD2526740000/02/03.2018
2 Safety | Use in explosive risk zones
2.3 Use in explosive risk zones
A list of all maxGUARD products that may be used in explo-
sive atmospheres, zone 2, can be found in section 3.9. If
maxGUARD products are used in explosive risk zones, the fol-
lowing additional notes apply:
–Staff involved in assembly, installation and operation must
be qualified to perform safe work on electrical systems
protected against potentially expolsive atmospheres.
–The provisions of IEC60079-14 must be observed.
–The products must be installed in a tool-secured enclo-
sure with a degree of protection of at least IP54 accord-
ing to IEC 60079-7.
–The housing enclosing the products must meet the
requirements of explosion protection type Ex na, Ex eb or
Ex ec.
–Prior to starting installation, ensure that no potentially
explosive atmosphere exists.
–If cut cross-connectors are used, AMG PP separation
plates must be inserted wherever there are bare cut
edges next to one another.
–If the temperature of a conductor or conductor entry
exceeds 70°C during rated operation, or 80°C at the
contact point, a conductor must be used that complies
with the temperature specifications as per the actually
measured temperature values.
–The products may only be operated in an environment
with pollution severity level 2 or lower in accordance with
IEC60664-1.
–A stabilised power supply (24VDC) with double or rein-
forced isolation must be used (SELV/PELV).
–A visual inspection of the maxGUARD station is to be per-
formed once per year.
–If a potentially explosive atmosphere exists, the following
applies:
–Live electrical connections may not be disconnected.
–DIP switches, binary switches and potentiometers may
not be operated.
2.4 Legal notice
The products belonging to the maxGUARD family are CE-
compliant according to EU Directive 2014/30/EU (EMC
Directive).
Selected products belonging to the maxGUARD family meet
the requirements of the ATEX Directive 2014/34/EU.

6Manual maxGUARD2526740000/02/03.2018
3 Systemoverview
3 System overview
1 2 3 4 5 6
7
9
8
Example arrangement of a maxGUARD station
1 (Active) feed-in module
2 Electronic load monitor
3 Potential distribution terminal
4 Separation plate
5 Control module
6 Alarm module
7 Cross-connector
8 End plate
9 End bracket
maxGUARD is a modular system for building customised
24Vcontrol voltage distributors. It consists of electronic
load monitors, potential distribution terminals, and feed-in,
control and alarm modules.
The electronic load monitors selectively protect individual
load circuits against overload and short circuit. They are
available as xed-value variants or with an adjustable trip-
ping characteristic, as well as with a 2-pole output relay.
Active feed-in modules, control modules and alarm modules
are used to control and monitor the electronic load monitors.
Multiple control modules can be used to segment the control
voltage distributor into separate load groups. Alarm modules
can be used to transmit signals potential-free to external con-
trol boards.
All connections between the modules of a maxGUARD sta-
tion are established using cross-connectors. All connection
terminals are PUSH IN connections, are colour-coded and
have an additional 2 mm test socket.
A large number of the modules are available in two perfor-
mance classes:
–standard version with uncoated PCBs
–enhanced version with coated PCBs and enhanced certifi-
cation for maritime applications and applications in explo-
sive risk zones.

7Manual maxGUARD2526740000/02/03.2018
3 Systemoverview | Mode of operation and connection concept
3.1 Mode of operation and connection concept
AMG FIM-0 AMG CM AMG ELM AMG OD AMG FIM-0 AMG CM AMG ELM AMG OD
Left:Mainstrandsandloadoutputs(red:+24V,blue:0V)
Right:Communicationviatheinternalsignalline(orange)
A maxGUARD station has three main internal connection
channels:
–+24V main strand for +24 V potential
–GND main strand for 0 V potential
–Internal signal line for communication
The two main strands are connected to the power supply via
a feed-in module and distribute the respective potentials for
the entire maxGUARD station.
The electronic load monitors form parallel junctions originat-
ing from the main strands.
Potential distribution terminals may be used to replicate the
outputs of the load monitors as required.
The internal signal line enables communication within the
maxGUARD station. Active feed-in modules, control modules
and alarm modules connect the internal signal line to an ex-
ternal control board.
All connections between the modules of a maxGUARD sta-
tion are established using cross-connectors.
The main connection channels are designed as double
channels. For high currents, the main strands must each be
equipped with two cross-connectors (see section4.4). If nec-
essary, the maxGUARD station can be extended by interleav-
ing the placement of the cross-connectors.
If a module cannot be connected to a specic main connec-
tion channel, the corresponding cross-connection contacts
will not be available. Installed cross-connectors will subse-
quently not be connected to the module and the individual
contact elements of the cross-connectors do not have to be
removed. White markings on the plastic tabs of the modules
indicate the active cross-connection sockets.

8Manual maxGUARD2526740000/02/03.2018
3 Systemoverview | Functions
Internal signal line
The individual modules communicate via a shared signal
line. The signals are processed according to priority (1= high,
5= low).
Signal Priority Encoder
Reset 1 AMG FIM-C, AMG CM
ON/OFF 2AMG CM
Alarm 3AMG ELM
Overload advance warning (I>90%) 4AMG ELM
IDLE 5AMG FIM-C, AMG CM
3.2 Functions
Overload advance warning
The adjustable load monitors are equipped with an overload
advance warning function.
If the output current of an adjustable load monitor exceeds
90% of the designated tripping current, this load monitor
couples an overload advance warning into the internal signal
line. The load monitor LED will ash green.
The overload advance warning can be transmitted to a con-
trol board via control modules or potential-free via alarm
modules.
Low voltage detection
Active feed-in modules, control and alarm modules as well
as all load monitors are equipped with low voltage detection.
If the input voltage of a load monitor falls below 18V, the
module LED will quickly ash red.
If the input voltage of a load monitor falls below 18V, the
load monitor will also disconnect the output.
If the input voltage falls below 15V, the module will power
down completely. The module LED will be off.
After power is restored, the module will automatically switch
to its last operational state prior to the undervoltage.
Surge detection
Active feed-in modules, control and alarm modules as well
as all load monitors are equipped with surge detection.
If the input voltage of these modules exceeds 31.2V, the
module LED will quickly ash red.
Overtemperature detection
The adjustable load monitors and the 4-channel load moni-
tors are equipped with overtemperature detection.
If an overtemperature is detected on a channel, the load
monitor will disconnect the output and couple an alarm
signal into the internal signal line. The load monitor LED will
illuminate orange (red and green simultaneously).
3.3 Type plate
Each module features a type plate, which includes identica-
tion information, the key technical specications and a block
diagram.
2
1
4
6
5
3
Typeplate(example)
1 Product identification
2 Block diagram
3 Certification
4 Manufacturer
5 Serial number
6 Technical data

9Manual maxGUARD2526740000/02/03.2018
3 Systemoverview | Markers
3.4 Markers
A wide range of markers are available as accessories for label-
ling equipment.
Module markers
The individual modules can be tted with WS-series terminal
markers (pitch dimension of 6mm).
ModuleswithWS10/6terminalmarkers
The following markers are available for the labelling:
–Markers for printing with Weidmüller PrintJet ADVANCED
(Order No.1324380000)
–Order No. 1818400000, WS10/6, white, PA66
–Markers for printing with Weidmüller THM MMP
(Order No. 2430820000)
–Order No. 2007160000, WS8/6MM, white, PC-ABS/
TPU
WAD group marker
The AMGPP separation plate can be tted with the WAD5
group marker.
The WEW35/2 end bracket and the AMGEP end bracket
can be tted with the WAD8 group marker.
SeparationplatewithWAD5groupmarker
The following markers are available for the labelling:
–Markers for printing with Weidmüller
PrintJet ADVANCED (Order No.1324380000)
–Order No. 1112910000, WAD5, white, PA66
–Order No. 1112920000, WAD5, yellow, PA66
–Order No. 1112940000, WAD8, white, PA66
–Order No. 1112950000, WAD8, yellow, PA66

10Manual maxGUARD2526740000/02/03.2018
3 Systemoverview | Internal fuse
EM8/30endbracketmarker
The WEW35/2 end bracket and AMGEP end bracket can
be tted with the EM8/30 end bracket marker (Order No.
1806120000).
EndbracketwithEM8/30endbracketmarker
The following markers are available for the labelling:
–Markers for printing with Weidmüller
PrintJet ADVANCED (Order No.1324380000)
–Order No. 1045570000, ELS6/30, white, PA66
–Order No. 1045580000, ELS6/30, yellow, PA66
–Markers for printing with Weidmüller
THM MMP (Order No. 2430820000)
–Order No. 2009980000, ELS6/30MM, white,
polyester
–Order No. 2010620000, ELS6/30MM, yellow,
polyester
–Labels for printing with office laser printers
–Order No. 1607720000, ESO 7 white, paper
–Order No. 1634780000, ESO 7 yellow, paper
–Order No. 1670390000, ESO 7 P white, polyester
–Order No. 1670400000, ESO 7 P yellow, polyester
3.5 Internal fuse
All load monitors are equipped with an internal fuse on the
PCB. If the electronic switch-off fails, the fuse will protect the
electronics and the external conductors against overload.
If the electronics are intact, the electronic switch-off will al-
ways be tripped rst.
The wire cross-sections must be measured ac-
cording to the internal fuse value, not the tripping
current of the electronic load monitor.
The wire cross-sections are to be measured according to
DINVDE0298-4. National regulations must be observed.
Load monitor Internal fuse
AMG ELM 6... 2x6.3A
AMG ELM 12... 2x10A
AMG ELM-6D CO 2x6.3A
AMG ELM-10D CO 2x8A
AMG ELM-1F... 2x6.3A
AMG ELM-2F... 2x6.3A
AMG ELM-4F... 2x6.3A
AMG ELM-6F... 2x6.3A
AMG ELM-8F... 2x8A
AMG ELM-10F... 2x8A
AMG ELM-1F CL2 1x 6,3A
AMG ELM-2F CL2 1x 6,3A
AMG ELM-4F CL2 1x 6,3A
AMG ELM Q2222 4x(2x6.3A)
AMG ELM Q4444 4x(2x6.3A)
AMG ELM Q6666 4x(2x6.3A)
AMG ELM Q2244 4x(2x6.3A)
AMG ELM Q2266 4x(2x6.3A)

11Manual maxGUARD2526740000/02/03.2018
3 Systemoverview | Product overview
3.6 Product overview
maxGUARDcomponents–standardversion
The following maxGUARD products have uncoated PCBs and
standard certication (see section 3.9).
Product designation Function Order No.
Feed-in modules, control module, alarm module
AMG FIM-0 Feed-in module, passive 2081870000
AMG FIM-C Feed-in module, active (reset, alarm) 2081880000
AMG CM Control module (reset, alarm, overload advance warning, ON/OFF) 2081900000
AMG AM Alarm module (alarm, overload advance warning), potential-free output contacts 2081890000
Electronic load monitors
AMG ELM-6 1-channel, adjustable: 1–6A 2080360000
AMG ELM-12 1-channel, adjustable: 4–12A 2080410000
AMG ELM-1F 1-channel, xed-value: 1A 2080420000
AMG ELM-2F 1-channel, xed-value: 2A 2080480000
AMG ELM-4F 1-channel, xed-value: 4A 2080490000
AMG ELM-6F 1-channel, xed-value: 6A 2080500000
AMG ELM-8F 1-channel, xed-value: 8A 2080600000
AMG ELM-10F 1-channel, xed-value: 10A 2080650000
AMG ELM-1F CL2 1-channel, xed-value: 1A, Class2 (UL1310) 2491270000
AMG ELM-2F CL2 1-channel, xed-value: 2A, Class2 (UL1310) 2491280000
AMG ELM-4F CL2 1-channel, xed-value: 4A, Class2 (UL1310) 2491290000
AMG ELM-Q2222 4-channel, xed-value: 2-2-2-2A 2080750000
AMG ELM-Q4444 4-channel, xed-value: 4-4-4-4A 2080880000
AMG ELM-Q6666 4-channel, xed-value: 6-6-6-6A 2080920000
AMG ELM-Q2244 4-channel, xed-value: 2-2-4-4A 2081650000
AMG ELM-Q2266 4-channel, xed-value: 2-2-6-6A 2081820000
Potential distribution terminals
AMG PD 4xplus (grouped) 2122920000
AMG OD 2xplus, 2xminus (alternating) 2122910000
AMG MD 4xminus (grouped) 2122930000
AMG XMD 4xminus, electrical connection to GND main strand 2122940000
AMG DIS Disconnecting lever for all-pole load separation 2123050000

12Manual maxGUARD2526740000/02/03.2018
3 Systemoverview | Product overview
maxGUARDcomponents–enhancedversion
The following maxGUARD products have coated PCBs and
enhanced certication (see section 3.9).
Product designation Function Order No.
Feed-in modules, control module, alarm module
AMG FIM-0 EX Feed-in module, passive 2082530000
AMG FIM-C EX Feed-in module, active (reset, alarm) 2082540000
AMG CM EX Control module (reset, alarm, overload advance warning, ON/OFF) 2083360000
AMG AM EX Alarm module (alarm, overload advance warning), potential-free output contacts 2082770000
Electronic load monitors
AMG ELM-6 EX 1-channel, adjustable: 1–6A 2082000000
AMG ELM-12 EX 1-channel, adjustable: 4–12A 2082010000
AMG ELM-6D CO 1-channel, adjustable: 1–6A, 2-pole output relay 2082440000
AMG ELM-10D CO 1-channel, adjustable: 4–10A, 2-pole output relay 2082470000
AMG ELM-1F EX 1-channel, xed-value: 1A 2082040000
AMG ELM-2F EX 1-channel, xed-value: 2A 2082050000
AMG ELM-4F EX 1-channel, xed-value: 4A 2082060000
AMG ELM-6F EX 1-channel, xed-value: 6A 2082310000
AMG ELM-8F EX 1-channel, xed-value: 8A 2082320000
AMG ELM-10F EX 1-channel, xed-value: 10A 2082430000
Potential distribution terminals
AMG PD EX 4xplus (grouped) 2495070000
AMG OD EX 2xplus, 2xminus (alternating) 2495090000
AMG MD EX 4xminus (grouped) 2495040000
AMG XMD EX 4xminus, electrical connection to GND main strand 2495080000
AMG DIS EX Disconnecting lever for all-pole load separation 2495100000

13Manual maxGUARD2526740000/02/03.2018
3 Systemoverview | Product overview
Fixing and disconnection elements
Product designation Function Order No.
Fixing and disconnection elements
AMG PP Separation plate 2123000000
AMG EP KIT Termination kit (2x AMG EP end plates, 2x WEW35/2V0 GF SW end brackets) 2500760000
AMG EP End plate, single 2495380000
WEW 35/2 SW End bracket, ammability rating HB (UL94), single 1061210000
WEW 35/2 V0 GF SW End bracket, ammability rating V-0 (UL94), single 1479000000
Cross-connectors
Orange cross-connectors Blue cross-connectors Red cross-connectors
Number of poles Type Order No. Type Order No. Type Order No.
2-pole ZQV4N/2 1527930000 ZQV4N/2BL 1528040000 ZQV4N/2RD 2460450000
3-pole ZQV4N/3 1527940000 ZQV4N/3BL 1528080000 ZQV4N/3RD 2460810000
4-pole ZQV4N/4 1527970000 ZQV4N/4BL 1528120000 ZQV4N/4RD 2460800000
5-pole ZQV4N/5 1527980000 ZQV4N/5BL 1528140000 ZQV4N/5RD 2460790000
6-pole ZQV4N/6 1527990000 ZQV4N/6BL 1528170000 ZQV4N/6RD 2460780000
7-pole ZQV4N/7 1528020000 ZQV4N/7BL 1528180000 ZQV4N/7RD 2460770000
8-pole ZQV4N/8 1528030000 ZQV4N/8BL 1528190000 ZQV4N/8RD 2460760000
9-pole ZQV4N/9 1528070000 ZQV4N/9BL 1528220000 ZQV4N/9RD 2460750000
10-pole ZQV4N/10 1528090000 ZQV4N/10BL 1528230000 ZQV4N/10RD 2460740000
50-pole ZQV4N/50 1528130000 ZQV4N/50BL 1528240000 ZQV4N/50RD 2460730000

14Manual maxGUARD2526740000/02/03.2018
3 Systemoverview | General technical data
3.7 General technical data
General
Total length of a maxGUARD station max. 300mm (with 50-pole cross-connector), max. 900mm (with extension)
Dimensions Height: 125mm
Width: 6.1/12.2/18.3/24.4mm
Depth 96.5mm
Number of bus participants max. 25 (incl. control or active feed-in module)
Cross-connectors(type) ZQV4N, max. 50-pole (see section 3.6)
Installation position any
maxGUARD station mounting distance 20mm all round
Type of protection IP20 (if end plates are used)
Electrical values
Rated input voltage 24VDC
Input voltage range 18–30V
Operating voltage of potential distribution terminals max. 50V
Voltagerippleofinputvoltage max. 8.5 VPP (peak-to-peak)
Rated current of feed-in module 40A
Current-carrying capacity of main strands max.40A (if equipped with twin cross-connectors)
Pollution severity 2
Overvoltage category III
Rated current of cross-connectors 32A (2 contacts for 40 A feed-in required)
Current-carrying capacity of load connections max. 12Atotal current (load monitors, potential distribution terminals)
Connections
Connectiontype(alllineconnections) PUSH IN
16mm²connections(feed-inmodule) Clamping range rigid: 0.75–10mm2
exible with or without wire-end ferrule: 0.75–16mm2
AWG18–AWG6
Stripping length 18mm1)
Contact surface length Contact surface length: 18mm
1.5 mm2 connections Clamping range rigid: 0.14–1.5mm2
exible with or without wire-end ferrule: 0.14–1.5mm2
exible with twin wire-end ferrule: 0.5–1mm2
AWG26–AWG14
Stripping length 10mm1)
Contact surface length 10mm (for twin wire-end ferrule: 12mm from 0.75mm2 and 14mm for 1mm2)
2.5 mm2connections Clamping range rigid: 0.14–2.5mm2
exible with or without wire-end ferrule: 0.14–2.5mm2
exible with twin wire-end ferrule: 0.5–1.5mm2
AWG26–AWG13
Stripping length 10mm1)
Contact surface length 10 mm (for twin wire-end ferrule: 12mm from 0.75mm2 )
Test sockets 2 mm test adapter
1) If wire-end ferrules with plastic collars are used, the connector must be stripped 2mm further than the contact surface length of the wire-end ferrule used (min. 3mm longer for twin
wire-end ferrules). Observe the information on the wire-end ferrule’s data sheet.

15Manual maxGUARD2526740000/02/03.2018
3 Systemoverview | General technical data
Environment
Ambient temperature Operation -25°C–+55°C (no derating)
Storage, transport -40°C –+85°C
Permissible humidity 5%–95% RH
EMC, shock, vibration
Emitted interference according to EN 61000-6-3, EN
61000-6-4
EN 55022 Class B
Interference resistance according to EN 61000-6-2 Burst
EN61000-4-4
DCinput/output: ±2kV
Signal connection: ±1kV
Surge
EN61000-4-5
DCinput/output: ±0.5kV cable-to-cable
±0.5kV cable-to-earth
Signal connection: ±1kV cable-to-earth
ESD
EN61000-4-2
Contact discharge: ±6kV
Air discharge: ±8kV
HF voltage (CDN)
EN61000-4-6
DCinput/output: 10V; 0.15–80MHz; 80%AM
Signal connection: 10V; 0.15–80MHz; 80%AM
Functional earth: 10V; 0.15–80MHz; 80%AM
HF eld
EN61000-4-3
Enclosure: 10V/m; 80–1000MHz
3 V/m; 1.4GHz–2GHz
1V/m; 2GHz–2.7GHz
ShockresistanceaccordingtoEN60068-2-27Test
Ea
15g/11ms
VibrationresistanceaccordingtoEN50178,
EN60068-2-6
1g/0.075mm (10Hz–150Hz)
Standards applied DIN EN50178, EN55022, EN60529, EN60950-1, EN61000-6-2, EN61000-6-3, EN61000-6-4
IEC60068-2-1, IEC60068-2-2, IEC60068-2-6, IEC60068-2-30,
IEC61000-4-2, IEC61000-4-3, IEC61000-4-4, IEC61000-4-5, IEC61000-4-6
1) If wire-end ferrules with plastic collars are used, the connector must be stripped 2mm further than the contact surface length of the wire-end ferrule used (min. 3mm longer for twin
wire-end ferrules). Observe the information on the wire-end ferrule’s data sheet.
All product-specic technical data can be found in the corresponding product description in chapters 5 to 7.

16Manual maxGUARD2526740000/02/03.2018
3 Systemoverview | Tripping characteristics
3.8 Tripping characteristics
Enlarged representations and numerical values
for the individual characteristics can be found in
the annex
PV
PV
PV
V
V
$ $ $
$1$1$1$1
Tripping characteristics, normal: 1AN–4AN
$1$1$1$1
PV
PV
PV
V
V
$ $$
Tripping characteristics, normal: 6AN–12AN
PV
PV
PV
V
V
$ $ $
$&/ $&/ $&/
Trippingcharacteristics,normal,Class2:1ACL2–4ACL2
$7$7$7$7
PV
PV
PV
V
V
$ $$
Tripping characteristics, lag: 1AT–4AT

17Manual maxGUARD2526740000/02/03.2018
3 Systemoverview | Tripping characteristics
$7$7$7$7
PV
PV
PV
V
V
$ $$
Tripping characteristics, lag: 6AT–12AT

18Manual maxGUARD2526740000/02/03.2018
3 Systemoverview | Tripping characteristics
The lled cells in the following table show which tripping
characteristics are available for the individual electronic load
monitors.
Electronic load monitor Normal tripping characteristic Lagged tripping characteristic
Designation Order No. 1AN2AN3AN4AN6AN8AN10AN12AN1ACL2 2ACL2 4ACL2 1AT2AT3AT4AT6AT8AT10AT12AT
AMG ELM-6 2080360000
AMG ELM-12 2080410000
AMG ELM-1F 2080420000
AMG ELM-1F CL2 2491270000
AMG ELM-2F 2080480000
AMG ELM-2F CL2 2491280000
AMG ELM-4F 2080490000
AMG ELM-4F CL2 2491290000
AMG ELM-6F 2080500000
AMG ELM-8F 2080600000
AMG ELM-10F 2080650000
AMG ELM-Q2222 2080750000
AMG ELM-Q4444 2080880000
AMG ELM-Q6666 2080920000
AMG ELM-Q2244 2081650000
AMG ELM-Q2266 2081820000
AMG ELM-6 EX 2082000000
AMG ELM-12 EX 2082010000
AMG ELM-6D CO 2082440000
AMG ELM-10D CO 2082470000
AMG ELM-1F EX 2082040000
AMG ELM-2F EX 2082050000
AMG ELM-4F EX 2082060000
AMG ELM-6F EX 2082310000
AMG ELM-8F EX 2082320000
AMG ELM-10F EX 2082430000

19Manual maxGUARD2526740000/02/03.2018
3 Systemoverview | Conformity and approvals
3.9 Conformity and approvals
The lled cells in the following tables show the scope of ap-
provals for the individual maxGUARD products.
Standard version
Conformity and approvals
Designation Order No. CE TÜVSüd CULUS CURUS Class 2
AMG FIM-0 2082530000
AMG FIM-C 2082540000
AMG CM 2083360000
AMG AM 2082770000
AMG ELM-6 2080360000
AMG ELM-12 2080410000
AMG ELM-1F 2080420000
AMG ELM-1F CL2 2491270000
AMG ELM-2F 2080480000
AMG ELM-2F CL2 2491280000
AMG ELM-4F 2080490000
AMG ELM-4F CL2 2491290000
AMG ELM-6F 2080500000
AMG ELM-8F 2080600000
AMG ELM-10F 2080650000
AMG ELM-Q2222 2080750000
AMG ELM-Q4444 2080880000
AMG ELM-Q6666 2080920000
AMG ELM-Q2244 2081650000
AMG ELM-Q2266 2081820000
AMG PD 2122920000
AMG OD 2122910000
AMG MD 2122930000
AMG XMD 2122940000
AMG DIS 2123050000
IND. CONT. EQ
E258476
Poll. Deg. 2, Ta: 55°C
E258476
Poll. Deg. 2
Ta: 55°C
Class 2
UL1310/NEC 725
CE TÜVSüd CULUS CURUS Class 2

20Manual maxGUARD2526740000/02/03.2018
3 Systemoverview | Conformity and approvals
Enhanced version
Conformity and approvals
Designation Order No. CE TÜVSüd ATEX IECEx CULUS Cl. 1, Div. 2 DNV-GL BV RINA LR ABS
AMG FIM-0 EX 2082530000
AMG FIM-C EX 2082540000
AMG CM EX 2083360000
AMG AM CO 2082770000
AMG ELM-6 EX 2082000000
AMG ELM-12 EX 2082010000
AMG ELM-6D CO 2082440000
AMG ELM-10D CO 2082470000
AMG ELM-1F EX 2082040000
AMG ELM-2F EX 2082050000
AMG ELM-4F EX 2082060000
AMG ELM-6F EX 2082310000
AMG ELM-8F EX 2082320000
AMG ELM-10F EX 2082430000
AMG PD EX 2495070000
AMG OD EX 2495090000
AMG MD EX 2495040000
AMG XMD EX 2495080000
AMG DIS EX 2495100000
IND. CONT. EQ
E258476
Poll. Deg. 2, Ta: 55°C
IND. CONT. EQ for use in Haz. Loc.
also LISTED IND. CONT. EQ E470829
Cl. I, Div. 2, Groups ABCD
Poll. Deg. 2, Ta: 55°C, T4
CE TÜVSüd ATEX IECEx CULUS Cl. 1, Div. 2
DNVGL.COM/AF
T
Y
P
E
A
P
P
R
O
V
E
D
P
R
O
D
U
C
T
D
E
S
I
G
N
A
S
S
E
S
S
E
D
DNV-GL BV RINA LR ABS
ATEX Certicate number:
DEMKO 17 ATEX 1870X
Markings:
II 3G Ex ec IIB T4 Gc
Standards:
EN 60079-0:2012 + A11 2013, EN 60079-7:2015
IECEx Certicate number:
IECEx ULD 17.0018X
Markings:
Ex ec IIB T4 Gc
Standards:
IEC 60079-0 (Ed. 6) and IEC 60079-7 (Ed. 5)
Table of contents
Other Weidmüller Power Distribution Unit manuals
Popular Power Distribution Unit manuals by other brands
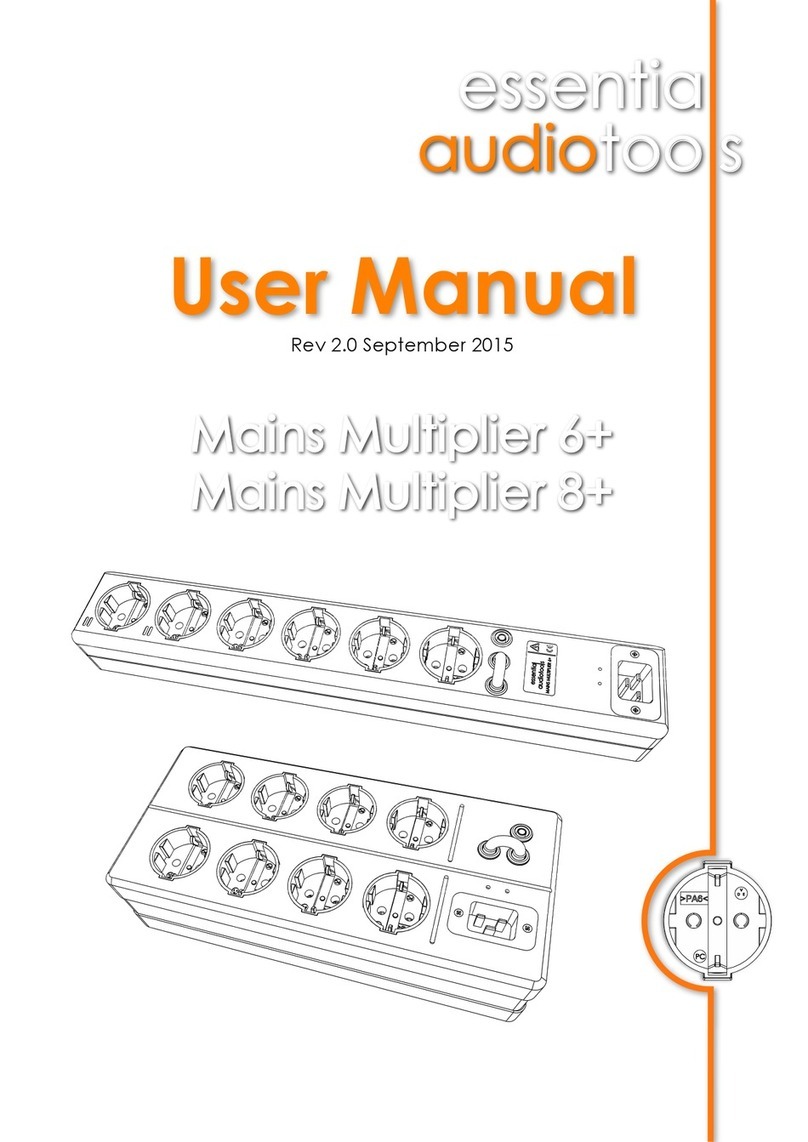
Essential Audio Tools
Essential Audio Tools Mains Multiplier 6+ user manual
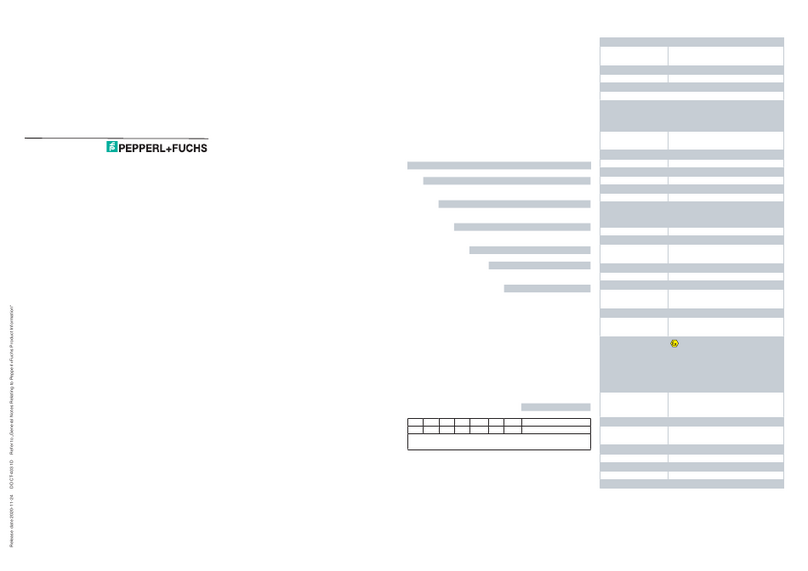
Pepperl+Fuchs
Pepperl+Fuchs GUB Series Brief instructions
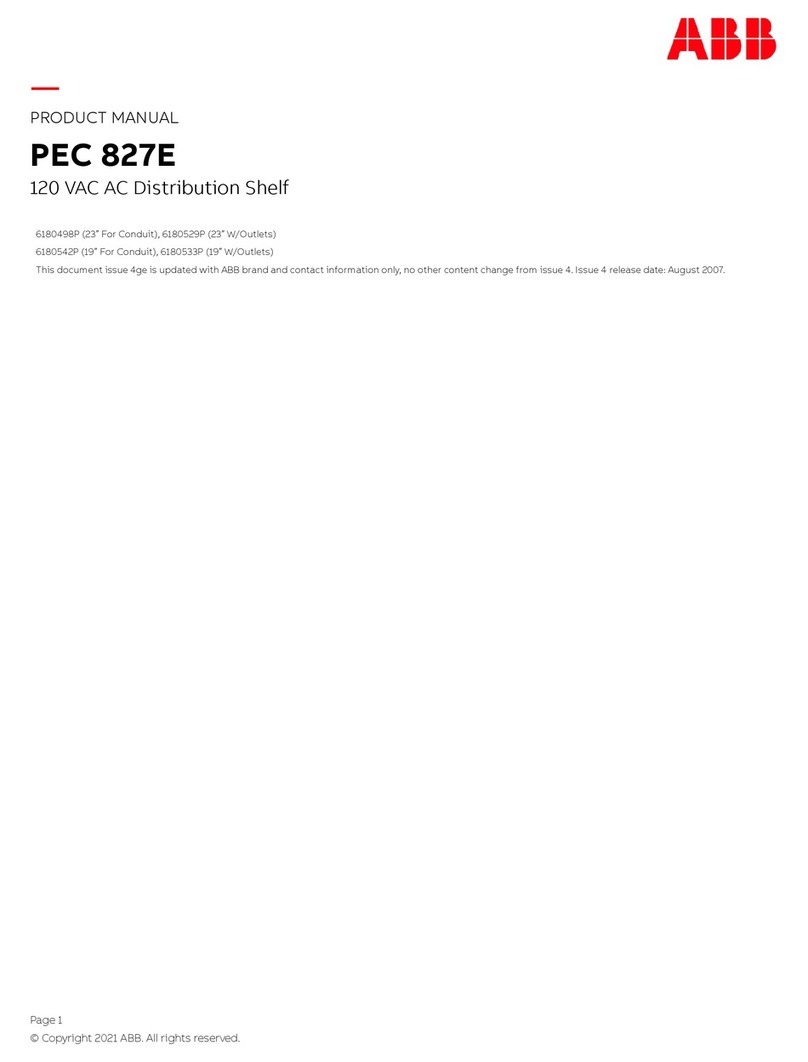
ABB
ABB PEC 827E product manual
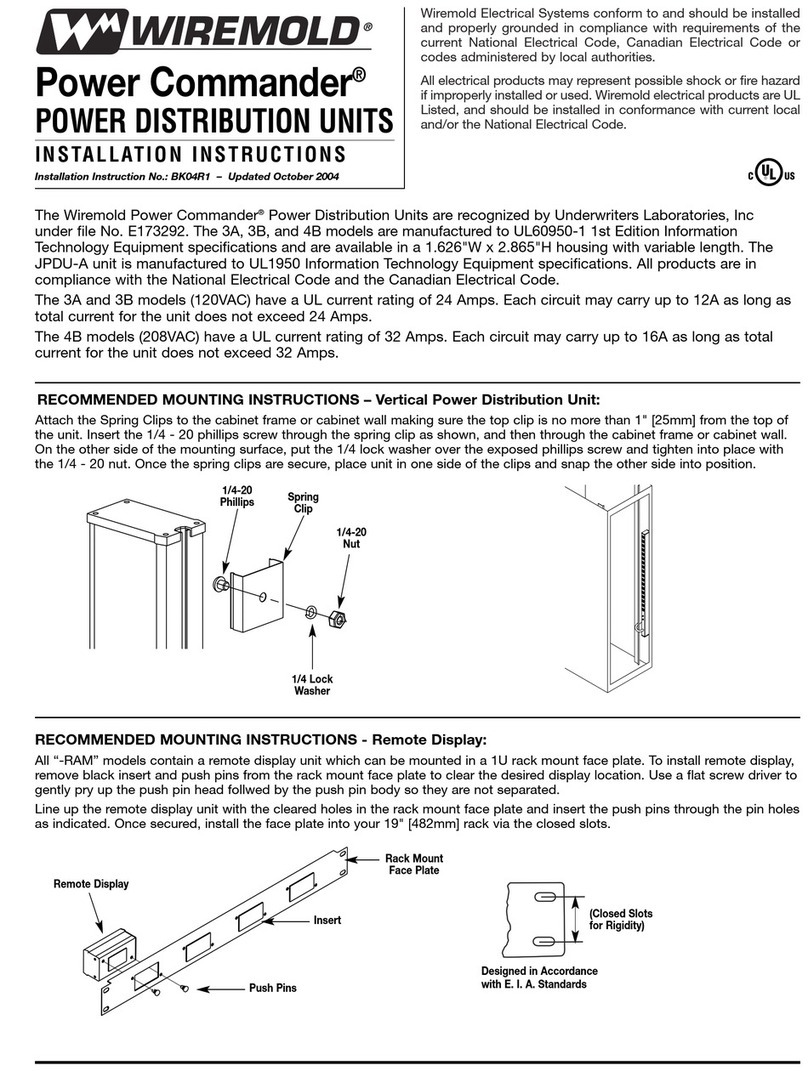
Wiremold
Wiremold Power Commander installation instructions
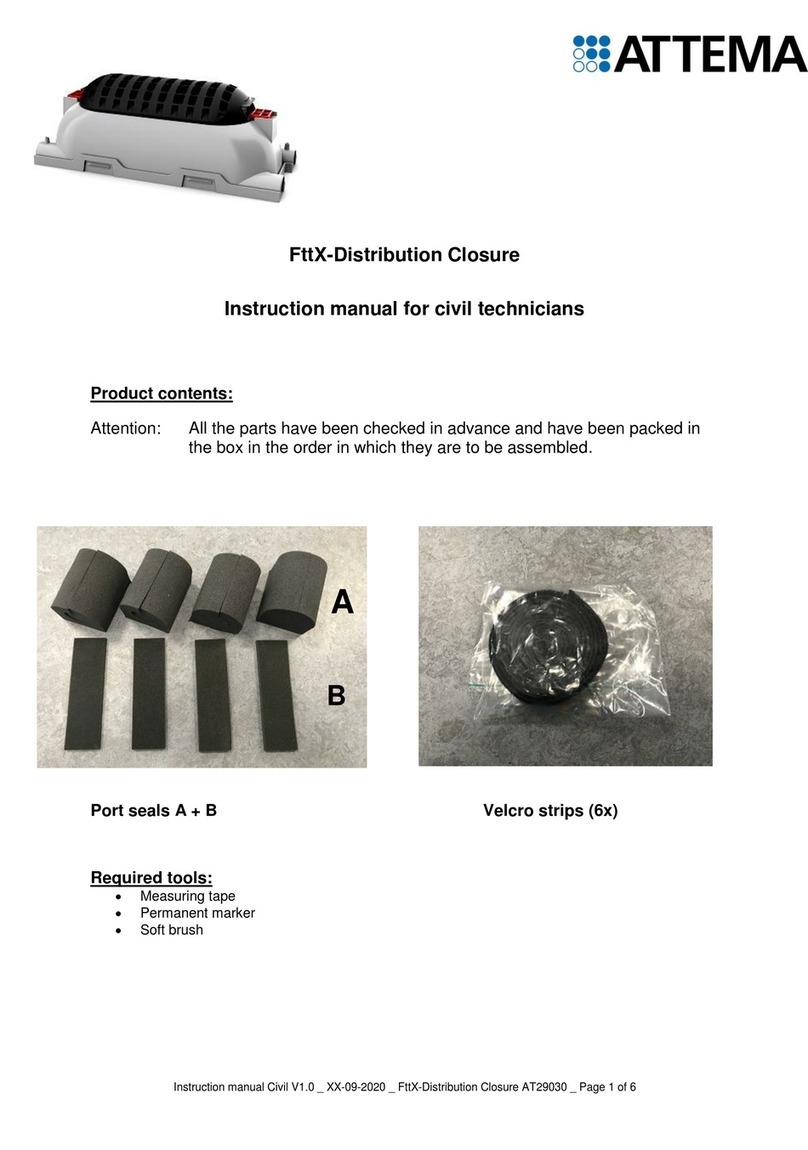
ATTEMA
ATTEMA FTTX instruction manual
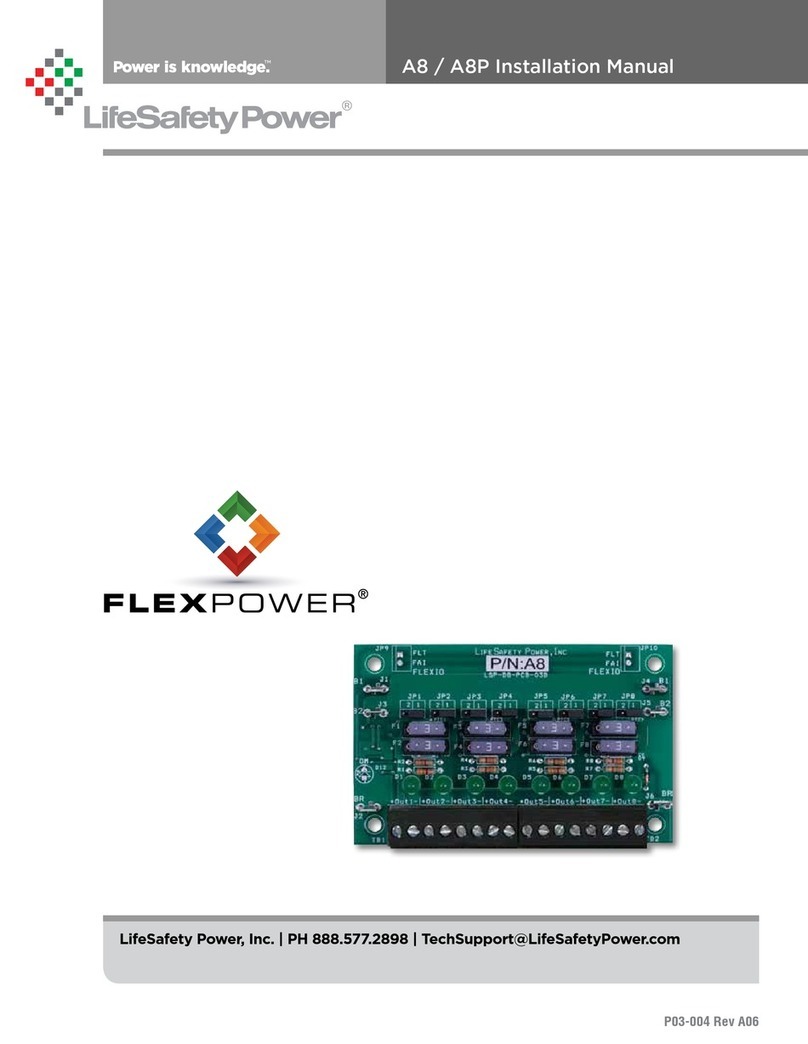
LifeSafety Power
LifeSafety Power FlexPower A8 installation manual