Weir SPM EXL Troubleshooting guide

Part Number: 2A33687
Release Date: 8/27/2015
Revision: B
Copyright © 2015, S.P.M. Flow Control, Inc.. All rights reserved. S.P.M. Flow Control, Inc. is the owner of the copyright and all confidential information in
this document, which must not be copied in whole or in part, in any form or by any means, and the information in it must not be used for any purpose
other than the specific purpose for which it has been provided without the prior written consent of the copyright owner. SPM, SAFETY IRON, SAFETY
HAMMER, SUR-DROP, DESTINY, STAMPEDE, DURALAST and GLADIATOR are trademarks and/or registered trademarks of S.P.M. Flow Control,
Inc.. WEIR and WEIR (logo) are trademarks and/or registered trademarks of Weir Engineering Services Limited. Certain features of some of the products
disclosed in this document may be protected worldwide by patents pending and registered in the name of S.P.M. Flow Control, Inc..
SPM
®
Well Service Pumps & Flow Control Products
EXL Back Pressure Relief Valves
Operation Instruction and Service Manual

Part Number: 2A33687
Release Date: 8/27/2015
Revision: B
2
THE FOLLOWING ICONS DENOTE IMPORTANT INFORMATION WITHIN THIS MANUAL.
GENERAL INFORMATION
INSTALLATION AND OPERATION
MAINTENANCE AND REPAIR
SALES AND SUPPORT
NOTE
CAUTION
WARNING/ DANGER

Part Number: 2A33687
Release Date: 8/27/2015
Revision: B
3
IMPORTANT SAFETY INFORMATION ENCLOSED. READ THIS OPERATING AND MAINTENANCE
INSTRUCTIONS MANUAL BEFORE OPERATING PRODUCT.
THIS INFORMATION MUST BE AVAILABLE TO ALL PERSONNEL THAT WILL OPERATE AND
MAINTAIN EQUIPMENT. FAILURE TO READ, UNDERSTAND AND FOLLOW THE OPERATING AND
MAINTENANCE INSTRUCTIONS MANUAL COULD RESULT IN SEVERE PERSONNEL INJURY OR
DEATH!
Most Weir SPM®products generate, control or direct pressurized fluids; therefore, it is critical that those who
work with these products be thoroughly trained in their proper application and safe handling. It is also critical
that these products be used and maintained properly!!
SPM
®
flow products contain elastomeric seals and are not intended to provide proper functionality when
exposed to fire.
MISUSE, SIDE LOADING, IMPROPER MAINTENANCE, OR DISASSEMBLY UNDER PRESSURE CAN
CAUSE SERIOUS INJURY OR DEATH!
The following information is given in good faith and should aid in the safe use of your SPM®products. This
information is not meant to replace existing Company's safety policies or practices.
Personal Responsibilities:
1. When working on Weir SPM®flow control products, safety glasses, approved safety shoes and hard hat
must be worn.
2. Personnel should never hammer on any component when pressure is present. Hammering on any part
or component may also cause foreign material or steel slags to become airborne.
3. It is a personal responsibility to use the proper tools when servicing the valve. It is a personal
responsibility to be knowledgeable and trained in the use and handling of tools for all maintenance of the
valve.
4. Hot surface may be present; it is a person’s own responsibility to protect against burn injury.

Part Number: 2A33687
Release Date: 8/27/2015
Revision: B
4
On Location:
1. Each valve is clearly marked with a maximum pressure rating. This pressure must not be exceeded or
SERIOUS INJURY OR DEATH CAN OCCUR!
2. The valve discharge connections should be properly cleaned and lightly oiled before the downstream
piping is attached. Any worn, damaged or missing seals should be replaced.
3. Welding, brazing or heating any part of the valve is prohibited. If accessories must be attached, consult
Weir Oil & Gas factory prior to installation.
4. A complete visual inspection of the valve must be made prior to each use. Any leaking seals, broken
bolts, leaking hoses or improperly tightened parts must be remedied prior to using.
5. Any repairs or service (even routine maintenance) performed on the valve must be performed by a
trained service technician who is qualified to work on high pressure flow control valves. All such service
and repairs must be supervised by qualified management personnel or returned to Weir Oil & Gas for
service. Only SPM
®
replacement parts should be utilized. Failure to do so may result in loss of
warranty as well as SERIOUS INJURY OR DEATH!
Special Precautions:
1. The modifications to or unauthorized repair of any part of a SPM
®
valve, or use of components not
qualified by SPM
®
, can lead to valve damage or failure and SERIOUS INJURY OR DEATH!
2. All SPM
®
threaded components are right hand threaded unless specifically designated otherwise. Any
turning counterclockwise will unscrew the assembly. Make sure all threaded components are
assembled to the correct torque value.
3. All products should be properly cleaned, greased or oiled after each use and inspected prior to each
use.
4. Each integral union connection is clearly marked with a pressure code (i.e. “1502”, 15,000 psi). This
pressure must not be exceeded. This code should also be used with mating unions. Improper mating
can result in failures. All integral union connections used must match (according to size, pressure
rating, etc.). These connections must also match the service of the designated string they are installed
in.

Part Number: 2A33687
Release Date: 8/27/2015
Revision: B
5
CONTENTS
SECTION I: GENERAL INFORMATION..............................................................................................................................................6
T
HIS SERVICE MANUAL COVERS
:.............................................................................................................................................................6
R
EBUILD
K
ITS
/C
RITICAL
C
OMPONENTS
:................................................................................................................................................6
P
RODUCT
D
ESCRIPTION
:........................................................................................................................................................................7
G
ENERAL
D
ESCRIPTION OF
R
ELIEF
V
ALVE
O
PERATION
:.......................................................................................................................8
E
ND
C
ONNECTION
O
PTIONS
:..................................................................................................................................................................8
SECTION II: INSTALLATION AND OPERATION..............................................................................................................................9
I
NSTALLATION
:.........................................................................................................................................................................................9
M
ETHODS TO OPERATE
R
ELIEF
V
ALVE
.................................................................................................................................................10
EXL
B
ACK
P
RESSURE
R
ELIEF
V
ALVE
C
ONTROL
P
ANEL
S
ETTING
G
UIDE
(O
PTIONAL
)......................................................................15
P
RESSURE
/
T
EMPERATURE
R
ATINGS
:..................................................................................................................................................17
SECTION III: MAINTENANCE AND REPAIR ...................................................................................................................................18
M
AINTENANCE
R
EQUIREMENTS
:...........................................................................................................................................................19
BOM
T
ABLE
:.........................................................................................................................................................................................21
P
REVENTATIVE
M
AINTENANCE AND
D
ISASSEMBLY
:.............................................................................................................................25
P
REVENTATIVE
M
AINTENANCE
:
I
NSPECTING
I
NTERNAL
C
OMPONENTS
...............................................................................................30
P
REVENTATIVE
M
AINTENANCE
:
R
EPLACEMENT AND
A
SSEMBLY OF
M
ETAL
S
EALING
C
OMPONENTS
................................................32
A
NNUAL
M
AINTENANCE
:
D
ISASSEMBLY AND
R
EPAIR OF
C
YLINDER
C
OMPONENTS
............................................................................36
A
NNUAL
M
AINTENANCE
:
I
NSPECTION OF INTERNAL COMPONENTS
.....................................................................................................36
A
SSEMBLY
:............................................................................................................................................................................................38
V
ESSEL
T
EST
P
ROCEDURES
:...............................................................................................................................................................47
S
ETTING AND
A
DJUSTING
P
RESSURE
:.................................................................................................................................................47
ERV
S
TAND
A
SSEMBLY
:.......................................................................................................................................................................48
T
ROUBLESHOOTING
G
UIDE
...................................................................................................................................................................49
SECTION IV: SERVICE AND SUPPORT...........................................................................................................................................50
S
ERVICE
C
ENTER
O
RDER
I
NFORMATION
:............................................................................................................................................50
W
EIR
O
IL
&
G
AS
L
OCATIONS
:...............................................................................................................................................................51

Part Number: 2A33687
Release Date: 8/27/2015
Revision: B
6
SECTION I: General Information
This service manual covers:
2A33687 ASSY/RLF VA/3-1502/FULL BORE/THRD/BP
Rebuild Kits/Critical Components:
2A37213 Full Kit (Metal and Seal kit)
4L28050 Metal Seal Kit (Nozzle Assembly, Valve Gate)
P33637 Cartridge
2P39528 Spider

Part Number: 2A33687
Release Date: 8/27/2015
Revision: B
7
Product Description:
The SPM®EXL Back Pressure Relief Valve provides increased efficiency during service/maintenance;
improved safety mechanism in the event of a blocked discharge port and increased longevity of service by
design.
The following components of the EXL Back Pressure Relief Valve have been re-designed from the Legacy Back
Pressure N2 valve:
Threaded Body/Flange
Overhaul of both Upper/Lower inner components
Removable Packing Assembly & Nut
These modified components to the EXL will benefit in the following ways:
Eliminates the area of danger in the event the valve’s discharge port is blocked
Aids in a quicker re-kitting in the field
Reduces assembly time
The SPM®EXL Back Pressure Relief Valve provides over-pressure protection for reciprocating pumps, treating
lines, pressure vessels, and other equipment operating under high pressure, high flow conditions. Compact
and simple to operate, the valve is direct acting, relying on the system's hydraulic pressure to overcome a
preset nitrogen gas force to relieve. It is externally adjustable from zero pressure to maximum setting.
The SPM
®
valve will reseat once the system pressure reduces. Unlike many “High-Lift” Valves, which require a
substantial drop in pressure before they will reseat, the SPM
®
Relief Valve exhibits little blow down and will
reseat at or near the “cracking pressure.”
Manufactured to Weir Oil & Gas’s stringent Quality Assurance System, all pressure bearing components are
made from high quality material. The forged body features an integral wing union male inlet connection,
suitable for the pressure rating of the component.
The low-pressure outlet is available with an integral wing union connection. Conforming to conditions of design
and performance in API RP520, the SPM
®
EXL Back Pressure Relief Valve is intended for liquid service. It is
not intended for elevated temperatures or as a safety device in case of fire.
Available in 3”, this valve offers pressure ranges from 1,000 – 15,000 psi. The valve is best suited for over
pressure protection in a “slick water” medium.
DO NOT USE FOR H2S SERVICE! Contact your Weir Oil & Gas representative for advice about
sour gas service applications.

Part Number: 2A33687
Release Date: 8/27/2015
Revision: B
8
General Description of Relief Valve Operation:
The SPM
®
EXL Back Pressure Relief Valve’s operation is a simple balance between the nitrogen acting on the
piston and the inlet liquid pressure acting on the rod and wear sleeve. The equation is Pressure times Area
equals Force (PxA=F). The ratio of areas is approximately 25:1 for the 15,000 psi rated valve.
This means that nitrogen pressure of 100 psi can counter an inlet line pressure of 2500 psi for the 15,000 psi
rated Back Pressure Relief Valve. Variations in this ratio in practice are due to friction of seals and will be
discussed in setting and adjusting section on page 11.
End Connection Options:
The SPM
®
3” EXL Back Pressure Relief Valve is available with SPM
®
wing union connections. The nameplate
will indicate the cold working pressure allowable for each assembly.
Wing union connections on the relief valve are interchangeable with other union connections of the same size
and figure (pressure rating). Caution must be taken to avoid mixing different ratings of wing connections.
There are various sizes and figures that are capable of making marginal connections. Failure to observe good
judgment may lead to failure of components and danger to life and limb. Always verify working pressure ratings
of each connection before use.
This device is intended to discharge to atmospheric pressure when it relieves. It must not be subjected to any
significant backpressure; other than that generated by gravity or frictional losses on the discharge line. The
choice of discharge connections is offered as a convenience for the user and does not imply high-pressure
capability.
WARNING: OBSERVE ALL INSTRUCTIONS, CAUTIONS AND WARNINGS AS NOTED IN THIS
MANUAL. FAILURE TO DO SO CAN LEAD TO EQUIPMENT DAMAGE AND PERSONAL INJURY OR
DEATH!

Part Number: 2A33687
Release Date: 8/27/2015
Revision: B
9
SECTION II: Installation and Operation
Installation:
The SPM®
EXL Back Pressure Relief Valve should be installed in a branch on the high-pressure pump line (Fig.
1). It is recommended that the valve be placed downstream away from the high pressure pumps. This
increased distance will reduce the likelihood of the valve seat’s experiencing “chatter”. Any application
requiring localized protection of the high pressure pump is acceptable. However, this will require additional
differential between the fluid pressure and set pressure of the valve to prevent “valve chatter”. Contact
Engineering for additional recommendations.
It is recommended to operate the valve in the upright position. This will reduce the tendency for proppants to
accumulate around the sealing area and potentially affect the sealing performance. However, the valve will
function within 90 degrees declination (Angle from vertical).
The gas regulator and gas back pressure relief valve should be installed as close to the relief valve as possible.
The nitrogen filled high-pressure cylinder must be secured to either a skid or trailer or by staking it to the
ground.
All general Frac Fluids may be discharged through the valve. The valve will tolerate clean liquids better than
others and lighter liquids will flow greater rates than heavier liquids. Particulates, abrasives and contaminants
will not preclude the valve from opening at the appropriate set pressure. However, abrasive materials will
cause some wear between the wear sleeve, nozzle, and main seal. While these components feature wear
resistant surfaces, their life will be reduced as the abrasives increase in the fluid.
WEIR OIL & GAS HIGHLY RECOMMENDS THAT AN ISOLATION VALVE BE PLACED BETWEEN
THE PRESSURE LINE AND THE RELIEF VALVE. THE ISOLATION VALVE MUST BE IN THE OPEN
POSITION DURING NORMAL OPERATION.
With the isolation valve installed, as shown in Figure 1, any time the pressure exceeds the set pressure at the
EXL Back Pressure Relief Valve, the fluid will pass through the valve and out the discharge.
Figure 1

Part Number: 2A33687
Release Date: 8/27/2015
Revision: B
10
Installation (Cont.):
At low flow rates, the valve will discharge fluid at approximately the set pressure (Fig. 2). At higher flow rates,
the valve will discharge fluid at levels above the set pressure. API 520 defines the valve flow capacity as the
rate that can be relieved at an over pressure of 25%. When the fluid pressure falls to the set pressure level or
below, the valve will reseat and reseal.
Figure 2

Part Number: 2A33687
Release Date: 8/27/2015
Revision: B
11
Methods to operate Relief Valve
Weir’s SPM®EXL Relief Valve can be operated in the following ways:
1. Standard Gauges - This method uses the traditional regulators that are used to calibrate an adjacent
Relief Valve.
2. Legacy Control Panel – This method encompasses the standard gauges into a control panel that can be
accessed away from the Relief Valve. Additional information can be found in “ SPM®Back Pressure RV
Control Panel Setting Guide” and accessed via www.WeirInAction.com/downloads
3. Automated Relief Valve Control System (ARC System) – This system allows the operator to input a
POP off and RESET pressure via an electrical control panel that automatically controls the Relief Valve
by monitoring a high pressure transducer that is installed on the main treating iron. Additional
information can be found in “Automated Relief Valve Control (A.R.C.) System ” and accessed via
www.WeirInAction.com/downloads
Standard Gauges - Calibration Guide
This guide is to be used when calibrating the SPM®
EXL Back Pressure Relief Valve. The valve should be set
at a minimum of 1000 PSI above system fluid pressure. If the valve is sequenced prior to each stage, than
valve life decreases due to frequent exposure to abrasive fluids. The more the valve is exposed to abrasives,
the greater likelihood that the valve will not reseat and possible washing may occur. The following information is
to be used as a best practices guide, based on extensive field utilization, to assist the user in more convenient
and accurate operation of the relief valve system. Refer to Figure 3 for N2 tank setting components.
WARNING: BLEED ALL PRESSURE FROM THE SYSTEM! (REFER TO DISASSEMBLY SECTION
PG. 23)

Part Number: 2A33687
Release Date: 8/27/2015
Revision: B
12
Standard Gauges – Calibration Guide Cont.
STEP 1
Turn the Black regulator counter clockwise all the way out as shown. (B)
Open the valve on the nitrogen bottle (A). The inlet gauge should indicate the pressure in the Nitrogen bottle.
Verify it is over 1,000 PSI.
STEP 2
Tighten the BLUE regulator fully by turning clockwise, as shown. Be sure not to over- tighten. (C)
Review chart on page 15 to find the “Line set pressure,” which is the pressure you want the valve to OPEN in
case of an over pressure event. To the right of that is the required Nitrogen pressure for the valve. Field use
has shown, due to variables such as thermal compression and friction, the best practice is the turn the BLACK
(B) regulator knob clockwise until the Nitrogen line pressure reaches over 40 PSI over that desired pressure.
The operator will hone in on that set pressure in later steps.

Part Number: 2A33687
Release Date: 8/27/2015
Revision: B
13
Standard Gauges – Calibration Guide Cont.
STEP 3
Perform a pressure test of pumping system to the desired “Pop-off” pressure (or opening of the valve). Hold at
that pressure. The “Pop-off” setting in case of an over pressure incident must be at a minimum of 1000 PSI over
the system operating pressure to prevent chattering and decreased life of the valve.
As the system is holding pressure, calibration can begin by SLOWLY turning the BLACK (B) regulator now
counter- clockwise, at intervals of 5 PSI. A slight amount of fluid can be seen discharged from the outlet port of
the valve. Iron connected to the discharge port of the valve may need to be disconnected to see an immediate
indication.
NOTE: DUE TO THE SMALL AMOUNT OF DISCHARGE, THE USER WILL LIKELY NOT SEE AN
INDICATION IN THE DATA VAN.
STEP 4
Turn the BLUE regulator (C) counter-clockwise until the gas starts to exhaust. (Tattle-tale opens; reference
Step 4A)
Then, slightly turn the BLUE regulator (C) clockwise until the gas ceases to exhaust. The correct setting should
be verified by manually pushing the Tattle-tale to the closed position. If it remains closed, the setting is correct.
If the tattle-tale opens, then Nitrogen is still venting. This will require an additional clockwise rotation of the
BLUE regulator (C) and closing of the tattle-tale to verify that Nitrogen is not venting.

Part Number: 2A33687
Release Date: 8/27/2015
Revision: B
14
Standard Gauges – Calibration Guide Cont.
STEP 5
The use of the Tattle-tale will allow the user to indicate if there is a Nitrogen leak present during calibration. This
applies to both a stand-alone Nitrogen Relief Valve and the Control Panel option. The Tattle-tale has two
positions, as shown.
To set the backpressure, follow this procedure:
Slowly decrease the back pressure regulator (BLUE dial- C) until the Tattle-tale pops. This is an
indication that the Nitrogen is venting.
Slowly increase the back pressure regulator (BLUE dial –C) until the Tattle-tale is able to be pushed in
and remains closed.

Part Number: 2A33687
Release Date: 8/27/2015
Revision: B
15
EXL Back Pressure Relief Valve Control Panel Setting Guide (Optional)
The Nitrogen Relief Valve can be controlled remotely through the use of the SPM®Remote Control Panel. It
regulates the flow of rig air or nitrogen to the relief valve and allows the operator to change pressure relief
settings with the flow line. The Remote Control Panel is also engraved with a quick reference chart for easy
adjustment. An as option, available upon request is the Tattle Tale feature on the Control Panel. This allows
the user to have a visual indication when the N2 gas is venting during calibration.
Control Panel Components
Setting and calibration is the same as previously described. See page 11.
Additional information can be found in “SPM
®
Back Pressure RV Control Panel
Setting Guide” and accessed via www.WeirInAction.com

Part Number: 2A33687
Release Date: 8/27/2015
Revision: B
16
EXL Back Pressure Relief Valve Calibration Guide (Cont.)
Values in this chart should be considered preliminary and if the predicted gas pressure does not produce the
desired set pressure, you may have to adjust the regulator up or down. Some of the factors affecting
performance include ambient and liquid temperature, and the gas media used.
3” EXL Back Pressure Relief Valve Set Pressure vs. Nitrogen Pressure Performance Data
Line
Set
Pressure
PSI
Required
Nitrogen (or gas)
Pressure
PSI
350 0
500 14
1000 28
1500 41
2000 55
2500 69
3000 83
3500 97
4000 110
4500 124
5000 138
5500 152
6000 166
6500 179
7000 193
7500 207
8000 221
8500 234
9000 248
9500 262
10000 276
10500 290
11000 303
11500 317
12000 331
12500 345
13000 359
13500 372
14000 386
14500 400
15000 414

Part Number: 2A33687
Release Date: 8/27/2015
Revision: B
17
Pressure/ Temperature Ratings:
The SPM
®
3” EXL Back Pressure Relief Valve is available in the following configurations at this time.
Part
Number Description Working Pressure (PSI)
2A33687 3-1502 Relief Valve Assembly EXL Back
Pressure 15,000
Gas Side Specifications:
Low Pressure Working Range: 0 to 800 psi
Recommended Nitrogen Bottle: 2,500 psi, (1,000 min)
Operating Temperature:
-22F to 120F (-30C to 49C)

Part Number: 2A33687
Release Date: 8/27/2015
Revision: B
18
SECTION III: Maintenance and Repair
WARNING: DISASSEMBLY UNDER PRESSURE CAN CAUSE SERIOUS INJURY OR DEATH!
Always Remember:
1. Always wear PPE (personal protective equipment).
2. Only qualified technicians should perform maintenance on SPM
®
products.
3. Always use Weir Oil & Gas supplied new parts kit for reassembly.
4. Clean all components thoroughly prior to reassembly.
5. Check sealing surface area of valve gate and nozzle for pitting, erosion or other flaws. Failure in sealing
can result if these areas are not smooth.
6. Use only SPM
®
Relief Valve parts on SPM
®
Relief Valves.
7. This device is intended to discharge atmospherically when it relieves.
ID REQUIRED TOOLS ID REQUIRED TOOLS
1
SAFETY GLASSES 11 STANDARD ALLEN WRENCH SET
2
PROTECTIVE GLOVES 12 VISE WITH ALUMINUM JAWS
3
2 LB HAMMER 13 BLUE LOCTITE 242 OR EQUIVALENT
4
600 GRIT SAND PAPER 14 FLANGE LIFTING TOOL, 2A41047
5
1/2" ALUMINUM BAR 15 DUMMY SEAT FOR TESTING RELIEF VALVE BODY,
2P41038
6
SCREWDRIVER (FLAT TIP) 16 WRENCH EXTENSION, 2P24505
7
HOIST AND CHAIN - 500 LBS. RATING MIN 17 15/16” SOCKET 1/2" DRIVE
8
LPS LAB #02910 COPPER BASED ANTI-SEIZE OR
EQUIVALENT 18 1/2” IMPACT ALLEN SOCKET
9
ASSEMBLY TORQUE TOOL, 2P39525 19 1/2” TORQUE WRENCH (10 – 100 FT LBS), P24509
10
NEEDLE NOSE PLIERS 20 IMPACT WRENCH

Part Number: 2A33687
Release Date: 8/27/2015
Revision: B
19
Maintenance Requirements:
The SPM®
3” EXL Back Pressure Relief Valve is a well-designed, dependable valve that provides long term
reliable performance. Like any device, however, it requires routine inspection and servicing to maintain its
functionality. Due to the harsh field environment where this relief valve will be used, it is imperative that
maintenance of this valve be HIGH Priority to ensure repeatability.
Weir Oil & Gas recommends that the valve be serviced during the following:
Preventative Maintenance (After 20 Fracturing Stages, or 1 Complete Frac Job)
Any time the valve is sequenced in operation as a result of overpressure (other than routine calibration with
clean water prior to pumping operations), it must undergo a teardown and the primary seal surfaces be
inspected. If no over-pressure event occurs, the valve shall be serviced after every 20 stages or 1 frac job,
whichever comes first. This should be done immediately following the completion of the current job.
Not properly servicing the valve once it has discharged frac media (including frac sand) is a dangerous
practice and increases the risk of leakage during the next operation. Disassembly, repairs, and reassembly
should be done in accordance with service manual instructions.
The valve’s design allows for a quick and easy inspection of its internal components. The components
that require inspecting are listed below and are referenced on the bill of materials on page 24. (Illustrated on
pages 25-27)
The components that must be replaced during a re-kitting are highlighted in yellow below.
Valve Gate
Nozzle Assembly
O-Ring Seal (under Nozzle Assembly)
Spring
Gate
Bushing
Spider
Disassembly/Inspection guidelines are on pages 24 through 32.
The following kits can be ordered separately through Weir Oil & Gas Service centers:
P33637 Cartridge
2P39528 Spider
4L28050 Metal Seal Kit (Nozzle Assembly, Valve Gate)
2A37213 Full Kit
Annual Inspection
An annual inspection is required to ensure that all internal components of the valve are working properly
and are to Weir Oil & Gas Engineering’s specifications. It is imperative that a qualified Weir Oil & Gas
Technician follow the assembly/disassembly/inspection instructions illustrated on pages 33 through 36.

Part Number: 2A33687
Release Date: 8/27/2015
Revision: B
20
Maintenance Requirements (Cont.):
The SPM®EXL Backpressure Relief Valve incorporates both threaded and flanged connections within the
design. These features are intended to provide easy internal access and maintenance-free performance.
However, in the event the valve experiences leaking at either the threaded or bolted external connections, the
valve must be immediately removed from operation and returned to the nearest SPM®Service Center for
inspection and repair. Under no circumstance should the valve be allowed to continue operations with any
visible external leak.
REGULAR MAINTENANCE SPARE PARTS
NOTE: ALWAYS KEEP WEIR OIL & GAS SPARE PARTS ON HAND: (19, 21, 22, 26, 27)
ANNUAL MAINTENANCE SPARE PARTS
NOTE: ALWAYS KEEP WEIR OIL & GAS SPARE PARTS ON HAND: ALL ELASTOMER SEALS
SHOULD BE REPLACED REGARDLESS OF CONDITION. (28, 27, 11, 12, 8, 9, 17)
Expendables: Valve gate (21), Nozzle assembly (26)
Table of contents
Other Weir Control Unit manuals
Popular Control Unit manuals by other brands
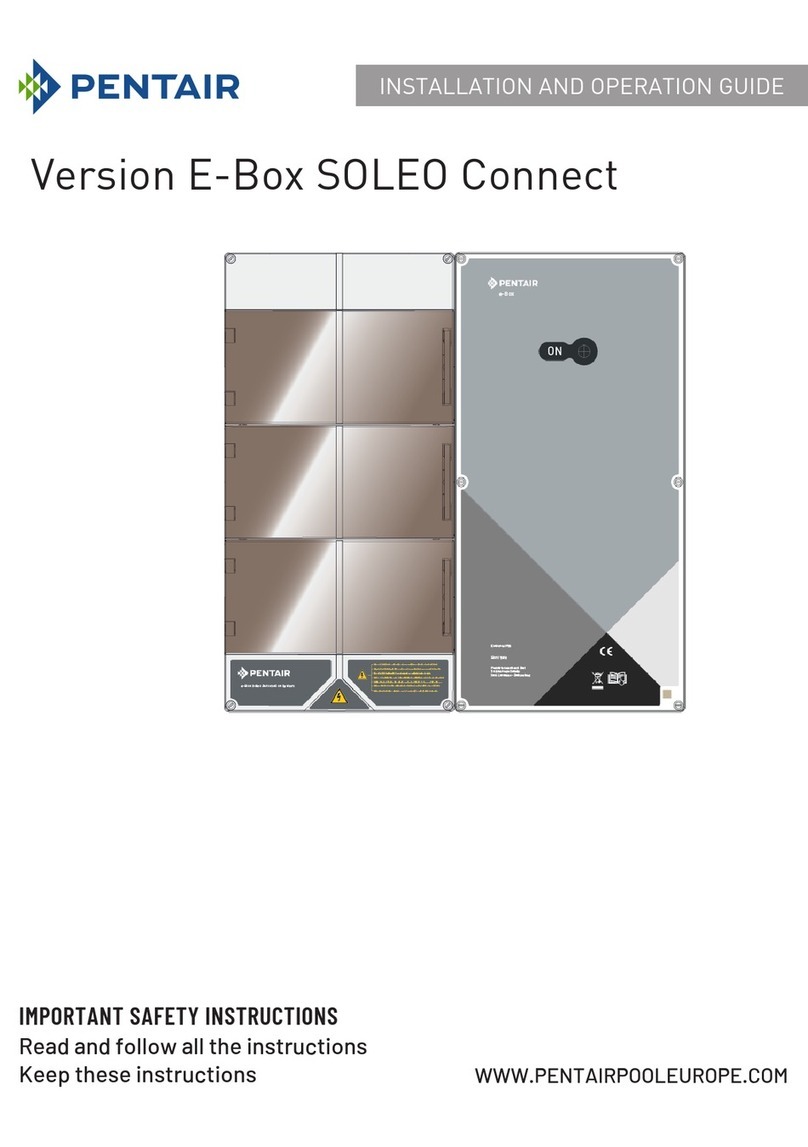
Pentair
Pentair E-Box SOLEO Connect Installation and operation guide
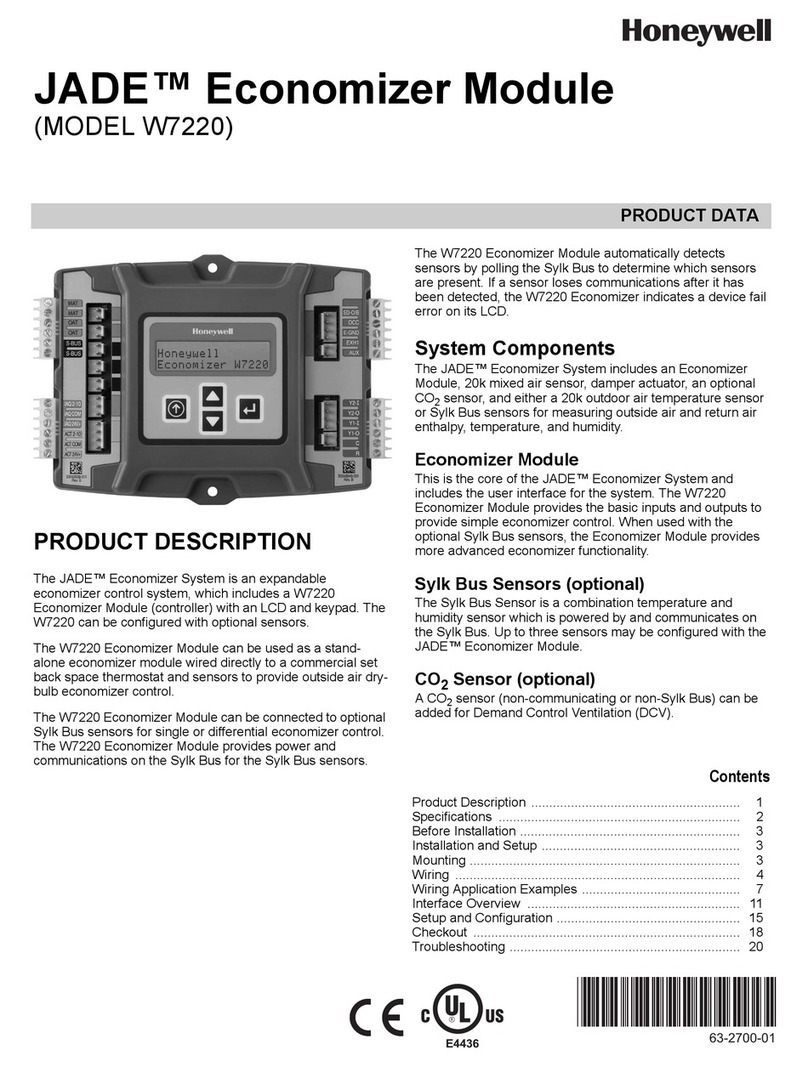
Honeywell
Honeywell JADE W7220 Product data
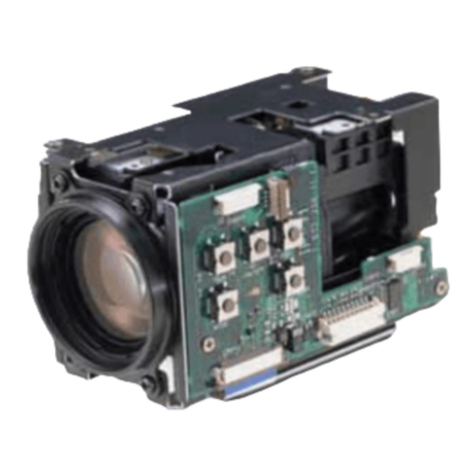
Sony
Sony FCB-IX47 instruction manual
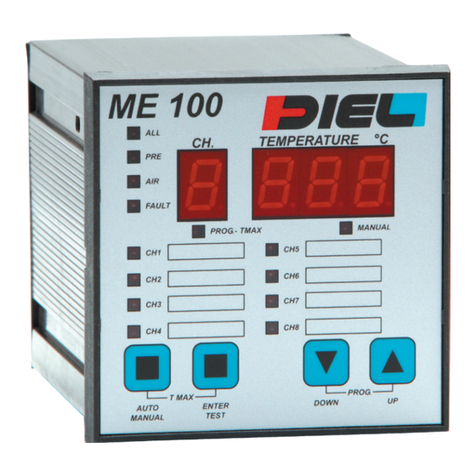
DIEL
DIEL ME 100 V3 Installation and instruction manual
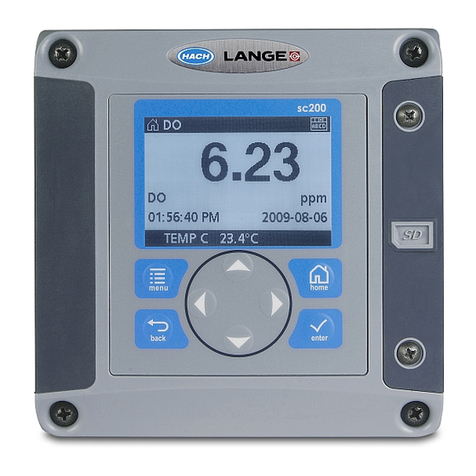
Hach
Hach sc200 user manual
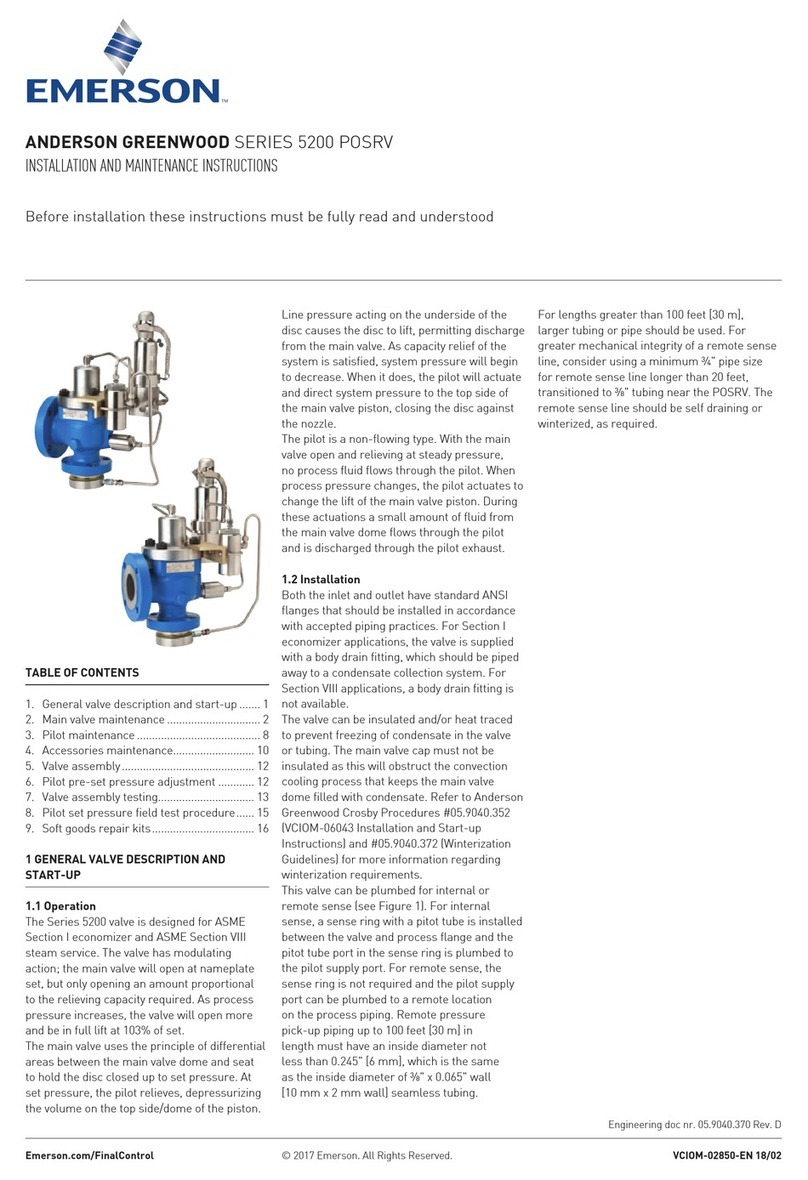
Anderson
Anderson Greenwood Series Installation and maintenance instructions