Weldclass FORCE 160MST MK2 User manual

OPERATING INSTRUCTIONS
To qualify for full extended warranty, you must register within 30 days
of purchase. See inside for details.
IMPORTANT!
FORCE 160MST MK2
FORCE 180MST MK2

2
Congratulations & thank you for choosing Weldclass
The Force range from Weldclass provides market leading value, features and
durability. Force machines have been designed with emphasis on robust
construction, with simple and functional operation.
Register Your Warranty Now
Standard warranty without registration is 12 months. To qualify for an
extended full 24 month warranty your purchase you must register within
30 days of purchase.
Please register your warranty now by going to:
www.weldclass.com.au/warrantyregistration
You will need;
a. A copy of your purchase invoice / receipt.
b. Your machine serial number which can be found on the back of the
machine.
Using Gasless MIG Wire?
Weldclass Platinum GL-11 is Australia’s No.1 Gasless wire.
Welders right across Australia & beyond rate Platinum GL-11
as the most user-friendly, smoothest running gasless wire
on the market.
Talk to your Weldclass distributor today, or go to:
www.Weldclass.com.au/GL-11 Platinum GL-11

3
FORCE 160MST & 180MST
............................................................................................... 5
.................................................................................................. 5
............................................................................................................... 6
...................................................................................... 6
...................................................................................................... 9
.................................................................................................................. 9
................................................................................ 10
............................................................................................ 11
................................................................................ 11
.................................................................... 15
............................................................. 17
...................................................................... 23
.................................................................................. 24
...................................................................... 26
................................................................................... 27
.............................................................................................................................. 27
....................................................................................................................... 31
Contents
Know Your Machine
Controls Explained
Power Supply
Operating Environment
Welding Settings
Tips & Tricks
Accessories & Spare Parts
Care & Maintenance
MIG Basic Welding Guide
MIG Welding Troubleshooting
MMA (Stick) Basic Welding Guide
MMA (Stick) Troubleshooting
TIG Basic Welding Guide
TIG Welding Troubleshooting
Knowledge & Resources
Safety
Warranty

4
Specications
Specications 160MST 180MST
Output Power MIG: 40-160A
ARC/TIG: 30-140A
MIG: 40-180A
ARC/TIG: 30-160A
Duty Cycle MIG: 130A @ 60%
ARC/TIG: 120A @ 60%
MIG: 144A @ 60%
ARC/TIG: 128A @ 60%
MIG Wire Size 0.6, 0.8, 0.9mm 0.6, 0.8, 0.9mm
MMA Electrode Size 1.6 – 3.2mm 1.6 – 3.2mm
TIG Tungsten Size 1.6mm 1.6mm
Spool Size 100mm (1kg) & 200mm (5kg) 100mm (1kg) & 200mm (5kg)
Input Power 240V, 10A 240V, 10A

5
FORCE 160MST & 180MST
2
1
34
5
67
8
9
10
18
15
11
16
17
19
20
Know Your Machine
1. MIG Torch Euro Connection
2. LCD current meter - Displays output current
(amps) in real time
3. LCD Voltage meter - Displays output voltage
in real time
4. Welding voltage adjustment knob - Adjusts
welding voltage in MIG mode
5. MIG wire feed speed adjustment knob/
Arc (Stick / TIG) current adjustment knob
6. Overload Indicator Lamp
7. Welding output mode switch. Sets power
source in MIG, MMA or Lift TIG mode
8. Cooling Fan Inlet (obscured)
9. MIG Torch Polarity Connection Lead
10. Negative (-) welding power output
connection socket
11. Positive (+) welding power output
connection socket (obscured)
12. Shielding Gas Inlet Connection
13. 240V AC mains power input lead
14. Mains power switch
15. Wire spool holder
16. Wire drive inlet guide
17. Wire feed tension adjustment
18. Wire feed tension arm
19. Wire drive roller retainer
20. Wire drive roller (obscured)
21. Spool Gun vs Normal MIG Mode Switch
22. Spool Gun Control plug socket
Controls Explained
These indicate voltage and current (amperage) settings, both statically (before welding) and dynamically
(during welding). These are very sensitive, so it is not abnormal to observer some small uctuations on
them when the machine is at rest.
LCD Current & Voltage Display Meters
12
13
14 21
22

6
Adequate ventilation is required to provide proper
cooling. Ensure that the machine is placed on
a stable level surface where clean cool air can
easily ow through the unit. The Force range has
electrical components and control circuit boards
which may be damaged by excessive dust and dirt,
so a clean operating environment is essential.
The MIG voltage control is essentially the power in
the welding arc that sets the heat. The wire speed
feed simply controls the rate at which the welding
wire is fed into the weld pool.
For any voltage position setting, there will be a
specic corresponding ‘sweet spot’ in the wire
feeding speed that will give the smoothest and
most stable welding arc. The correct wire feeding
speed for a given voltage setting is aected by
welding wire type and size, shielding gas, welding
material and joint type.
It is recommended to set the welding voltage as
desired and then slowly adjust the wire speed until
the arc is smooth and stable. When reaching this
point, if the penetration/ heat input is too much/
not enough, adjust the voltage setting and repeat
the process. If the operator is not able to achieve a
smooth and stable arc with the desired heat input
for the weld, it is likely that a change in wire size
and/or shielding gas type is required (assuming all
other factors are correct).
A chart with recommended settings using this
machine for common welding applications is
located on the underside 0f the wire feeder cover
door and further on in this manual.
MIG Welding Mode
The current control knob sets the target welding
output current for either mode selected. The
voltage knob has no eect in MMA or TIG mode.
MMA/ Lift TIG Welding Mode
Lights when duty cycle is exceeded and thermal
protection is activated. When thermal protection is
activated, welding output will be disabled until
machines cools suciently and overload indicator
lamp goes out. Also may activate with inverter
circuit failure issues.
Overload Indicator Lamp
Lift TIG is an arc ignition system for basic TIG
welding that removes the need to ‘scratch’ start or
strike the tungsten on the work piece to start the
arc, which can have a negative eect on the weld
quality due to tungsten contamination. Lift arc
starting works by gently touching the tungsten on
the work piece and then lifting it o. The control
circuit will sense when the tungsten is removed
from the work piece and send a pulse of electricity
through the torch that will cause the TIG arc to
initiate.
Lift TIG Mode
Power Supply
The 160MST & 180MST are designed to operate on
a 10A 240V AC power supply.
Electrical Connection
This machine has a wide input power variation
tolerance (~170-265V), allowing it to operate o
generator power. However, this machine is NOT
designed for frequent generator use and is NOT
protected against poor quality power or voltage
spikes. Any damage caused by generator power
supply is not covered under warranty.
If generator power must be used, generator size
should be not less than 8kva. Avoid using poor, low
quality generators as these have the greatest risk
of power spikes etc. A suitable quality generator
should have a THD (total harmonic distortion)
rating of not more than 6%. Most reputable
generator supplier will be able to specify the THD
ratings on their product.
Generator Use
If an extension cord must be used, it should be
minimum cable core size 2.0mm2for length of
up to 10m, or minimum 2.5mmfor length up to
20m. Using extension leads of over 20m is not
recommended.
Extension Leads
Operating Environment

7
FORCE 160MST & 180MST
1. Fitting Wire Spool
1.1 Open wire feeder compartment door. Fit wire
spool to spool holder post. Ensure that
wire exits from the bottom of the spool.
100mm/1kg Spool Set Up:
Use plastic slotted washed/spacer and
threaded nut as shown here;
1.2 200mm/5kg spools only: Before replacing
spool retaining nut, set spool brake tension
by adjusting the smaller nut inside the spool
hub. Spool should be able to rotate freely,
but not continue to rotate when drive stops.
Tension may need to be adjusted as spool
weight decreases.
WARNING!
Excessive spool brake tension will cause wire
feeding issues and aect welding performance
as well as premature failure/ wear of wire feed
components.
1.3 Feed the wire from the spool through the wire
drive inlet guide (18) into the wire feeder.
2. Loading Wire Feeder
2.1 Release the wire feed tension arm (20) by
pivoting the wire feed tension adjustment
lever (19) towards you from the vertical
‘locked’ position.
2.2 Check the wire drive roller (22) groove
matches the selected MIG wire type and
size. The drive roller will have two dierent
sized grooves; the size of the groove in use
is stamped on the side of the drive roller. For
ux cored ‘soft’ wire, such as that used in
gasless MIG welding, the drive roller groove
has a serrated prole (known as knurled). For
solid core ‘hard’ MIG wire, the drive roller
groove used has a ‘v’ shaped prole. If
necessary, remove and change the drive roller
by rotating anti clockwise and removing the
drive roller retainer (21).
2.3 Once the correct drive roller (22) is selected
and tted and the drive roller retainer (21) is
secured in place, manually feed the wire
through the wire drive inlet guide (18),
through the drive roller groove and into the
outlet wire guide tube. Ensuring that the wire
is correctly seated in the drive roller groove,
replace the wire feed tension arm (20) and
lock it into place by pivoting the wire feed
tension adjustment lever (19) back to the
vertical position.
3. Adjusting Wire Feed Tension
This is accomplished by winding the knob on the
tension adjustment lever (19). Clockwise will
increase tension, anti-clockwise will decrease drive
tension. Ideal tension is as little as possible, while
maintaining a consistent wire feed with no drive
roller slippage. Check all other causes of excess
wire feeding friction causing slippage rst, such as;
incorrect/ worn drive roller, worn/ damaged torch
consumables, blocked/ damaged torch wire guide
liner, before increasing wire feed tension. There is a
number scale on the tension adjustment lever (19)
to indicate the adjustment position. The higher
the number indicated, the higher the tension that
is set.
WARNING!
Before changing the feed roller or wire spool,
ensure that the mains power is switched o.
WARNING!
The use of excessive feed tension will cause
rapid and premature wear of the drive roller, the
support bearing and the drive motor/gearbox.
3.4 Check that the correct matching MIG wire,
drive roller (22) and MIG torch tip are tted.
3.5 Connect the machine to suitable mains power
using the mains input power lead (13). Switch
the mains power switch (14) to ‘on’ to power
up the machine. Set the welding mode switch
(7) to ‘MIG’ position.
3.6 You are now ready to feed the wire through
the torch. With the wire feeder cover open,
pull the trigger of the MIG torch to check that
the wire is feeding smoothly through the
feeder and into the torch.
3.7 Set the wire feeding speed knob (5) to
maximum. With the torch tip removed
from the torch and the torch laid out as
straight as possible, depress MIG torch trigger
until the wire feeds out through the end of
the MIG torch. Replace the tip on the MIG
torch and trim o any excess wire.
MIG Welding Operation

8
4. Gas MIG Welding Operation
NOTE: Gas MIG welding will require a gas cylinder.
4.1 Connect the earth cable quick connector to
the negative welding power output socket
(10). Connect the earth clamp to the work
piece. Contact with the work piece must be
rm, contacting with clean, bare metal, with
no corrosion, paint or scale at the contact
point.
4.2 Connect the MIG power connection lead (9)
to the positive welding power output socket
(11).
NOTE: If this connection is not made, there will be no
electrical connection to the welding torch!
4.3 Connect the gas regulator to a gas cylinder
(not included with machine) and connect
the gas hose from the regulator to the gas
inlet on the rear of the machine (12). Ensure
all hose connections are tight. Open gas
cylinder valve and adjust regulator, ow
should be between 10-25L/min depending
on application. Re-check regulator ow
pressure with torch triggered as static gas
ow setting may drop once gas is owing.
4.4 Set the welding voltage adjustment knob (4)
and wire speed control knob (5).
MIG welding with Aluminium
For tips and tricks on setting up for MIG welding
Aluminium, go to: www.weldclass.com.au/alumig
5. Gasless Welding Operation
5.1 Connect the earth cable quick connector
to the positive welding power output socket
(11). Connect the earth clamp to the work
piece. Contact with the work piece must
be rm contact with clean, bare metal, with
no corrosion, paint or scale at the contact
point.
5.2 Connect the MIG power connection lead (9)
to the negative welding power output socket
(10).
NOTE: If this connection is not made, there will
be no electrical connection to the welding torch!
6. Spool Gun Operation
NOTE: Requires optional spool gun (part no.
WC-06610).
6.1 Connections for torch, earth lead, polarity
cable and gas hose are the same as standard
MIG function.
6.2 Connect control cable on Spool Gun torch to
the spool gun Socket on rear of machine.
Mode switch on front of machine must be
switched to “MIG” and Spool-Gun switch on
rear of machine must be switched to “Spool
Gun”.
6.3 Use control knobs on front of machine to
adjust wire speed and voltage. When in spool
gun mode, the wire speed control will adjust
the speed of wire feed motor inside the spool
gun head
7. ARC/ MMA Welding Operation
7.1 Connect the earth cable quick connector
to the negative welding power output socket
(10) Connect the earth clamp to the work
piece. Contact with the work piece must
be rm contact with clean, bare metal, with
no corrosion, paint or scale at the contact
point.
7.2 Insert an electrode into the electrode holder
and connect the electrode holder and work
lead to the positive welding power output
socket (11).
NOTE: This polarity connection conguration is valid
for most GP (General Purpose) MMA electrodes. There
are variances to this. If in doubt, check the electrode
specications or consult the electrode manufacturer.
7.3 Connect the machine to suitable mains power
using the mains input power lead (13). Switch
the mains power switch (14) to ‘on’ to power
up the machine. Set the welding mode switch
(7) to ‘MMA’.
7.4 Select the required output current using the
current control knob (5). You are now ready to
weld!
8. Lift TIG Operation
NOTE: Lift TIG operation requires an optional valve
control TIG torch, and argon gas cylinder & regulator.

9
FORCE 160MST & 180MST
8.1 Connect the earth cable quick connector
to the positive welding power output socket
(11). Connect the earth clamp to the work
piece. Contact with the work piece must
be rm contact with clean, bare metal, with
no corrosion, paint or scale at the contact
point.
8.2 Insert TIG torch power connection into the
negative welding power output socket (10).
Connect valve TIG torch gas line to the
regulator, ensuring all connections are tight.
8.3 Open gas cylinder valve and adjust regulator,
owshouldbebetween5-10l/mindepending
on application. Re-check regulator ow
pressure with torch valve open as static gas
ow setting may drop once gas is owing.
8.4 Connect the machine to suitable mains power
using the mains input power lead (13) Switch
the mains power switch (14) to ‘on’ to power
up the machine. Set the welding mode switch
(7) to ‘Lift TIG’.
8.5 Select the required output current using the
current control knob (5). You are now ready to
weld!
NOTE: The 160MST / 180MST is a DC (Direct Current)
output welder only, this means that it is unable to TIG
weld reactive metals such as Aluminium alloys and
Brass (which require AC output). DC TIG output is
suitable for steel, stainless steel and copper.
Tips & Tricks
Welding Settings
Welding duty cycle is the percentage of actual
welding time that can occur in a ten minute cycle.
E.g. 20% at 160 amps - this means the welder can
weld at 160 amps for 2 minutes and then the unit
will need to be rested for 8 minutes. All duty cycle
ratings are based on an ambient air temperature of
40°Cwith 50% humidity, which is the international
standard for such a rating. In an environment with
temperature s exceeding 40°C, the duty cycle will
be less than stated. In ambient temperature less
than 40°C, duty cycle performance will be higher.
Duty Cycle Rating
Use chart as guide only, as optimal settings will vary with weld joint type and operator technique.
Cells left blank not recommended combination for effective welding results.
MIG Welding Parameter Material Thickness Material Thickness
Welding
Material Wire Type Polarity Wire Size
Drive
Roller
Type
Torch
Liner
Shielding
Gas
1.0mm 2.0mm 3.0mm 5.0mm 1.6mm 3.0mm 6.0mm 8.0mm
Voltage / Wirespeed Voltage / Wirespeed
Mild
Steel
Gasless Torch (-)
Earth (+)
0.8mm Knurled
Groove Blue
N/A
2/5 4/7 6/9 9/9 2/2 6/6 10/10 -
0.9mm Red 3/4 4/4.5 5/5 7/8 1/2 5/6 7/8 10/10
Solid
Steel
Torch (+)
Earth (-)
0.6mm ‘V’
Groove Blue Mixed
(Argon +
CO2)
3/6 5/9 - - 4/6 - - -
0.8mm 3/5 6/8 6/9 - 3/2 7/7 - -
0.9mm Red 3/4 5/6 7/9 9/9 2/2 6/6 9/10 10/10
160MST 180MST
Wire Jam Troubleshooting
• If wire jam occurs when the torch becomes hot, this is often because the heat causes the wire and the tip
to expand (which shrinks the hole in the tip). Using a slightly oversize tip can prevent this – eg: for 0.9mm
wire, use a 1.0mm tip.
• Do NOT over-tighten the drive roll tension – this will accelerate wear of the drive system, may distort the
wire & will cause further wire feed problems.
• Refer to page 15-16 for more troubleshooting tips.

10
Accessories & Spare Parts:
The MIG Torch supplied with the 180MST is a BZL 25 (Binzel 25 style) model.
To view parts for this torch, go to: www.weldclass.com.au/BZL25
For machine parts, go to www.weldclass.com.au/machines or contact
your Weldclass distributor
The compatible TIG torch for this machine is Weldclass 9/17 torch with valve.
To view this torch, go to: www.weldclass.com.au/TigTorch917v
MIG Torch Spare Parts - 180MST:
Machine Spare Parts:
TIG Torch (Optional Extra):
The MIG Torch supplied with the Weldforce 160MST is a BZL 15 (Binzel 15 style) model.
To view parts for this torch, go to: www.weldclass.com.au/BZL15
MIG Torch Spare Parts - 160MST:

11
FORCE 160MST & 180MST
Care & Maintenance
MIG Basic
Welding Guide
The Force range does not require any special
maintenance, however the user should take care
of the machine as follows:
• Regularly clean the ventilation slots.
• Keep the casing clean.
• Check all cables before use.
• Check electrode holders, work lead/clamps and
welding torches before use.
• Replace worn electrode holders and earth
clamps, which do not provide a good connection.
• Replace worn torch consumable parts in a timely
manner.
• Replace worn wire drive components in a timely
manner.
• Use a soft cloth or brush to clean electrical
components. Do not use liquid cleaning
products, water or especially solvents.
• Do not use compressed air to clean electrical
components as this can force dirt and dust
further into components, causing electrical short
circuits.
• Check for damaged parts.
Two dierent welding processes are covered in
this section (GMAW and FCAW), with the intention
of providing the very basic concepts in MIG
welding, where a welding gun is hand held, and
the electrode (welding wire) is fed into a weld
puddle, and the arc is shielded by a gas (GMAW) or
ux cored wire (FCAW).
Keep your Welding Machine in Top
Condition
MIG Basic Welding Techniques
If damaged, before further use, the welder must be
carefully checked by a qualied person to
determine that it will operate properly. Check for
breakage of parts, mountings and other conditions
that may aect its operation.
Have your welder repaired by an expert. An
authorised service centre should properly repair a
damaged part.
This appliance is manufactured in accordance with
relevant safety standards. Only experts must carry
out repairing of electrical appliances, otherwise
considerable danger for the user may result.
Use only genuine replacement parts. Do not use
modied or non-genuine parts.
When not in use the welder should be stored in the
dry and frost-free environment.
WARNING!
Before performing cleaning/maintenance,
replacing cables / connections , make sure the
welding machine is switched o and
disconnected from the power supply.
Storing the Welder

12
Gas Metal Arc Welding (GMAW)
This process, also known as MIG welding, CO2
welding, Micro Wire Welding, short arc welding,
dip transfer welding, wire welding etc., is an electric
arc welding process which fuses together the parts
to be welded by heating them with an arc between
a solid continuous, consumable electrode and the
work.
Shielding is obtained from an externally supplied
welding grade shielding gas. The process is
normally applied semi automatically; however the
process may be operated automatically and can
be machine operated. The process can be used
to weld thin and fairly thick steels, and some non-
ferrous metals in all positions.
Flux Cored Arc Welding (FCAW)
This is an electric arc welding process which
fuses together the parts to be welded by heating
them with an arc between a continuous ux lled
electrode wire and the work. Shielding is obtained
through decomposition of the ux within the
tubular wire. Additional shielding may or may
not be obtained from an externally supplied gas
or gas mixture. The process is normally applied
semi automatically; however the process may be
applied automatically or by machine.
It is commonly used to weld large diameter
electrodes in the at and horizontal position and
small electrode diameters in all positions. The
process is used to a lesser degree for welding
stainless steel and for overlay work.
GMAW Process
(Fig 1-1) Shielding Gas
Molten Weld Metal
Nozzle
Electrode Arc
Base Metal
Weld Metal
FCAW Process
(Fig 1-2) Nozzle
(Optional)
Flux Cored
Electrode
Arc
Base
Metal
Weld Metal
Slag
Molten
Slag
Molten Metal
Shielding Gas
(Optional)
Push Vertical Drag Pull
Position of MIG Torch
(Fig 1-3)
(Fig 1-4) 5oto 15o
Longitudinal Angle
Direction of Travel
90oTransverse
Angle
(Fig 1-5)
5oto 15o
Longitudinal Angle 30oto 60o
Transverse
Angle
Direction
of Travel
The angle of MIG torch to the weld has an eect on
the width of the weld.
The welding gun should be held at an angle to the
weld joint. (See Secondary Adjustment Variables
below).
Hold the gun so that the welding seam is viewed at
all times. Always wear the welding helmet with
proper lter lenses and use the proper safety
equipment.
CAUTION!!
Do not pull the welding gun back when the arc is
established. This will create excessive wire
extension (stick-out) and make a very poor
weld.
The electrode wire is not energized until the gun
trigger switch is depressed. The wire may therefore
be placed on the seam or joint prior to lowering
the helmet.

13
FORCE 160MST & 180MST
Distance from the MIG Torch Nozzle
to the Work Piece
The electrode wire stick out from the MIG Torch
nozzle should be between 10mm to 20mm. This
distance may vary depending on the type of joint
that is being welded.
Travel Speed
The speed at which the molten pool travels
inuences the width of the weld and penetration
of the welding run.
MIG Welding (GMAW) Variables
Most of the welding done by all processes is on
carbon steel. The items below describe the welding
variables in short-arc welding of 24gauge (0.024”,
0.6mm) to ¼” (6.4mm) mild sheet or plate. The
applied techniques and end results in the GMAW
process are controlled by these variables.
Preselected Variables
Preselected variables depend upon the type
of material being welded, the thickness of the
material, the welding position, the deposition rate
and the mechanical properties.
These variables are:
• Type of electrode wire
• Size of electrode wire
• Type of gas
• Gas ow rate
Primary Adjustable Variables
These control the process after preselected
variables have been found. They control the
penetration, bead width, bead height, arc stability,
deposition rate and weld soundness.
These variables are:
• Arc Voltage
• Welding current (wire feed speed)
• Travel speed
Secondary Adjustable Variables
These variables cause changes in primary
adjustable variables which in turn cause the
desired change in the bead formation. They are:
1. Stick-Out (distance between the end of the
contact tube (tip) and the end of the electrode
wire). Maintain at about 10mm stick-out
2. Wire Feed Speed. Increase in wire feed speed
increases weld current. Decrease in wire feed
speed decreases weld current.
3. Nozzle Angle. This refers to the position of the
welding gun in relation to the joint. The transverse
angle is usually one half the included angle
between plates forming the joint. The longitudinal
angle is the angle between the centre line of the
welding gun and a line perpendicular to the axis
of the weld. The longitudinal angle is generally
called the Nozzle Angle and can be either trailing
(pulling) or leading (pushing).
Vertical Fillet Welds (Fig 1-6)
10o
Longitudinal Angle
Direction of Travel
10oto 20o
Longitudinal Angle
30oto 60o
Transverse
Angle
30oto 60o
Transverse
Angle
Direction of Travel
(Fig 1-7)
5oto15o
Longitudinal
Angle
30oto 60o
Transverse
Angle
Electrode Stick-Out
(Fig 1-8)
Gas Nozzle
Tip to
Work Distance
Contact Tip (Tube)
Electrode Wire
Actual
Stick-Out
Transverse & Longitudinal
Nozzle Axes (Fig 1-9)
Longitudinal Angle
Transverse Angle
Axis of Weld

14
Whether the operator is left handed or right
handed has to be considered to realize the eects
of each angle in relation to the direction of travel.
Nozzle Angle, Right Handed Operator
(Fig 1-10)
Direction of Travel
Leading or “Pushing”
Angle (Forward Pointing)
Trailing or “Pulling”
Angle (Backward Pointing)
90o
Establishing the Arc and Making
Weld Beads
Before attempting to weld on a nished piece of
work, it is recommended that practice welds be
made on a sample metal of the same material as
that of the nished piece.
The easiest welding procedure for the beginner to
experiment with MIG welding is the at position.
The equipment is capable of at, vertical and
overhead positions.
For practicing MIG welding, secure some pieces of
16 or 18 gauge (1.5mm or 2.0mm) mild steel plate
(150 x 150mm). Use (0.8mm) ux cored gasless
wire or a solid wire with shielding gas.
Setting of the Power Source
Power source and Current (Wire Speed) setting
requires some practice by the operator, as the
welding plant has two control settings that have
to balance. These are the Current (Wire Speed)
control and the welding Voltage Control.
The welding current is determined by the Current
(Wire Speed) control, the current will increase with
increased Current (Wire Speed), resulting in a
shorter arc. Less Current (Wire Speed) will reduce
the current and lengthen the arc. Increasing the
welding voltage hardly alters the current level,
but lengthens the arc. By decreasing the voltage,
a shorter arc is obtained with a little change in
current level.
When changing to a dierent electrode wire
diameter, dierent control settings are required.
A thinner electrode wire needs more Current
(Wire Speed) to achieve the same current level.
A satisfactory weld cannot be obtained if the
Current (Wire Speed) and Voltage settings are not
adjusted to suit the electrode wire diameter and
the dimensions of the work piece.
If the Current (Wire Speed) is too high for the
welding voltage, “stubbing” will occur as the wire
dips into the molten pool and does not melt.
Welding in these conditions normally produces a
poor weld due to lack of fusion. If, however, the
welding voltage is too high, large drops will form
on the end of the wire, causing spatter. The correct
setting of voltage and Current (Wire Speed) can be
seen in the shape of the weld deposit and heard by
a smooth regular arc sound.
Electrode Wire Size Selection
The choice of Electrode wire size and shielding gas
used depends on the following:
• Thickness of the metal to be welded
• Type of joint
• Capacity of the wire feed unit and power
source
• The amount of penetration required
• The deposition rate required
• The bead prole desired
• The position of welding
• Cost of the wire

15
FORCE 160MST & 180MST
MIG Welding
Troubleshooting
The general approach to x Gas Metal Arc Welding
(GMAW) problems is to start at the wire spool then
work through to the MIG torch. There are two main
areas where problems occur with GMAW, Porosity
and Inconsistent wire feed.
When there is a gas problem the result is usually
porosity within the weld metal. Porosity always
stems from some contaminant within the molten
weld pool which is in the process of escaping
during solidication of the molten metal.
Contaminants range from no gas around the
welding arc to dirt on the workpiece surface.
Porosity can be reduced by checking the following
points.
WARNING!
Wire feeding problems can be reduced by checking the following points.

16
Other weld problems can be reduced by checking the following points.

17
FORCE 160MST & 180MST
MMA (Stick) Basic
Welding Guide
Flat Position,
Down Hand Butt Weld
(Fig 1-11)
Flat Position,
Gravity Fillet Weld
(Fig 1-12)
Horizontal Position,
Butt Weld
(Fig 1-13)
Horizontal-Vertical
(HV) Position
(Fig 1-14)
Vertical Position,
Butt Weld
(Fig 1-15)
Vertical Position,
Fillet Weld
(Fig 1-16)
Overhead Position,
Butt Weld
(Fig 1-17)
Overhead Position,
Fillet Weld
(Fig 1-18)
Size of Electrodes
The electrode size is determined by the thickness
of metals being joined and can also be governed
by the type of welding machine available. Small
welding machines will only provide current
(amperage) to run smaller sized electrodes.
For thin sections, it is necessary to use smaller
electrodes otherwise the arc may burn holes
through the job. A little practice will soon establish
the most suitable electrode for a given application.
Storage of Electrodes
Always store electrodes in a dry place and in their
original containers.
Electrode Polarity
Electrodesaregenerallyconnectedtotheelectrode
holder with the electrode holder connected
positive polarity.
The work lead is connected to the negative polarity
and is connected to the work piece. If in doubt
consult the electrode data sheet.
Eects of MMA(Stick) Welding
on Various Materials
High Tensile and Alloy Steels
The two most prominent eects of welding these
steels are the formation of a hardened zone in
the weld area, and, if suitable precautions are not
taken, the occurrence in this zone of under-bead
cracks. Hardened zone and underbead cracks in
the weld area may be reduced by using the correct
electrodes, preheating, using higher current
settings, using larger electrodes sizes, short runs
for larger electrode deposits or tempering in a
furnace.
Manganese Steels
The eect on manganese steel of slow cooling from
high temperatures causes embrittlement. For this
reason it is absolutely essential to keep manganese
steel cool during welding by quenching after each
weld or skip welding to distribute the heat.
Cast Iron
Most types of cast iron, except white iron, are
weldable. White iron, because of its extreme

18
Joint Preparations
In many cases, it will be possible to weld steel
sections without any special preparation. For
heavier sections and for repair work on castings,
etc., it will be necessary to cut or grind an angle
brittleness, generally cracks when attempts are
made to weld it. Trouble may also be experienced
when welding white-heart malleable, due to the
porosity caused by gas held in this type of iron.
Copper and Alloys
The most important factor is the high rate of heat
conductivity of copper, making pre-heating of
heavy sections necessary to give proper fusion of
weld and base metal.
Types of Electrodes
Arc Welding electrodes are classied into a number
of groups depending on their applications.
There are a great number of electrodes used for
specialised industrial purposes which are not
of particular interest for everyday general work.
These include some low hydrogen types for high
tensile steel, cellulose types for welding large
diameter pipes, etc. The range of electrodes dealt
with in this publication will cover the vast majority
of applications likely to be encountered; are all
easy to use.
between the pieces being joined to ensure proper
penetration of the weld metal and to produce
sound joints. In general, surfaces being welded
should be clean and free of rust, scale, dirt, grease,
etc. Slag should be removed from oxy-cut surfaces.
Typical joint designs are shown in Figure 1-19.
MILD STEEL :
E6011 - This electrode is used for all-position welding or
for welding on rusty, dirty, less-than- new metal. It has
repair or maintenance work.
E6013 - This all-position electrode is used for welding
clean, new sheet metal. Its soft arc has minimal spatter,
moderate penetration and an easy-to-clean slag.
E7014 - All positional, ease t o use electrode f or u se on
thicker steel than E6013. Especially suitable for sheet metal
E7018 - A low-hydrogen, all-position electrode used when
quality is an issue or for hard-to-weld metals. It has the ca-
pability of producing more uniform weld metal, which has
better impact properties at low temperatures.
CAST IRON:
ENI-CL - Suitable for joining all cast irons except white
cast iron.
STAINLESS STEEL:
E318L-16 - High corrosion resistances. Ideal for dairy
work etc.
Open Square Butt Joint
(Fig 1-19a)
Gap varies from1.6mm (1/16”)
to 4.8mm (3/16”) depending on plate thickness
Single Vee Butt Joint
(Fig 1-19b) Not less than 45˚
Single Vee Butt Joint
(Fig 1-19c) Not less than 70˚
1.6mm (1/16”) max.
1.6mm (1/16”)
Double Vee Butt Joint
(Fig 1-19d) Not less than 70˚
1.6mm (1/16”) max.
1.6mm (1/16”)
Lap Joint (Fig 1-19e)
Fillet Joint (Fig 1-19f)

19
FORCE 160MST & 180MST
MMA Welding Techniques
- A Word for Beginners
For those who have not yet done any welding, the
simplest way to commence is to run beads on a
piece of scrap plate. Use mild steel plate about
6.0mm thick and a 3.2mm electrode.
Clean any paint, loose scale or grease o the plate
and set it rmly on the work bench so that welding
can be carried out in the down hand position. Make
sure that the Work Lead/Clamp is making good
electrical contact with the work, either directly or
through the work table. For light gauge material,
always clamp the work lead directly to the job,
otherwise a poor circuit will probably result.
The Welder
Place yourself in a comfortable position before
beginning to weld. Get a seat of suitable height
and do as much work as possible sitting down.
Don’t hold your body tense. A taut attitude of
mind and a tensed body will soon make you feel
tired. Relax and you will nd that the job becomes
much easier. You can add much to your peace of
mind by wearing a leather apron and gauntlets.
You won’t be worrying then about being burnt or
sparks setting alight to your clothes.
Place the work so that the direction of welding
is across, rather than to or from, your body. The
electrode holder lead should be clear of any
obstruction so that you can move your arm freely
along as the electrode burns down. If the lead is
slung over your shoulder, it allows greater freedom
of movement and takes a lot of weight o your
hand. Be sure the insulation on your cable and
electrode holder is not faulty; otherwise you are
risking an electric shock.
Striking the Arc
Practice this on a piece of scrap plate before going
on to more exacting work. You may at rst
experience diculty due to the tip of the electrode
“sticking” to the work piece. This is caused by
making too heavy a contact with the work and
failing to withdraw the electrode quickly enough.
A low amperage will accentuate it. This freezing-
on of the tip may be overcome by scratching the
electrode along the plate surface in the same way
asamatchisstruck.As soon as the arc isestablished,
maintain a 1.6mm to 3.2mm gap between the
burning electrode end and the parent metal. Draw
Corner Weld
(Fig 1-19g)
Tee Joints
(Fig 1-19h)
Edge Joint
(Fig 1-19i)
Plug Welds
(Fig 1-19j)

20
Arc Length
The securing of an arc length necessary to produce
a neat weld soon becomes almost automatic. You
will nd that a long arc produces more heat.
A very long arc produces a crackling or spluttering
noise and the weld metal comes across in large,
irregular blobs. The weld bead is attened and
spatter increases. A short arc is essential if a high
quality weld is to be obtained although if it is too
short there is the danger of it being blanketed by
slag and the electrode tip being solidied in. If this
should happen, give the electrode a quick twist
back over the weld to detach it. Contact or “touch-
weld” electrodes such as E7014 Stick electrodes
do not stick in this way, and make welding much
easier.
Rate of Travel
After the arc is struck, your next concern is to
maintain it, and this requires moving the electrode
tip towards the molten pool at the same rate as it is
melting away. At the same time, the electrode has
to move along the plate to form a bead.
The electrode is directed at the weld pool at about
20º from the vertical. The rate of travel has to be
adjusted so that a well-formed bead is produced.
If the travel is too fast, the bead will be narrow and
strung out and may even be broken up into
individual globules. If the travel is too slow, the
weld metal piles up and the bead will be too large.
Making Welded Joints
Having attained some skill in the handling of an
electrode, you will be ready to go on to make up
welded joints.
A. Butt Welds
Set up two plates with their edges parallel, as
shown in Figure 1-21, allowing 1.6mm to 2.4mm
gap between them and tack weld at both ends. This
is to prevent contraction stresses from the cooling
weld metal pulling the plates out of alignment.
Platesthicker than 6.0mm should havetheir mating
edges beveled to form a 70º to 90º included angle.
This allows full penetration of the weld metal to
the root. Using a 3.2mm E7014 Stick electrode
at 100 amps, deposit a run of weld metal on the
bottom of the joint.
Do not weave the electrode, but maintain a steady
rate of travel along the joint sucient to produce a
well-formed bead. At rst you may notice a
tendency for undercut to form, but keeping the arc
length short, the angle of the electrode at about
20º from vertical, and the rate of travel not too fast,
will help eliminate this.
The electrode needs to be moved along fast
enough to prevent the slag pool from getting
ahead of the arc. To complete the joint in thin
plate, turn the job over, clean the slag out of the
back and deposit a similar weld.
the electrode slowly along as it melts down.
Another diculty you may meet is the tendency,
after the arc is struck, to withdraw the electrode so
far that the arc is broken again. A little practice will
soon remedy both of these faults.
20o
1.6mm (1/16”)
Striking an Arc
(Fig 1-20)
Tack Weld
Butt Weld
(Fig 1-21)
Electrode
20o- 30o
Tack Weld
Weld Build Up Sequence
(Fig 1-22)
This manual suits for next models
1
Table of contents
Other Weldclass Welding System manuals

Weldclass
Weldclass CutForce 43P User manual
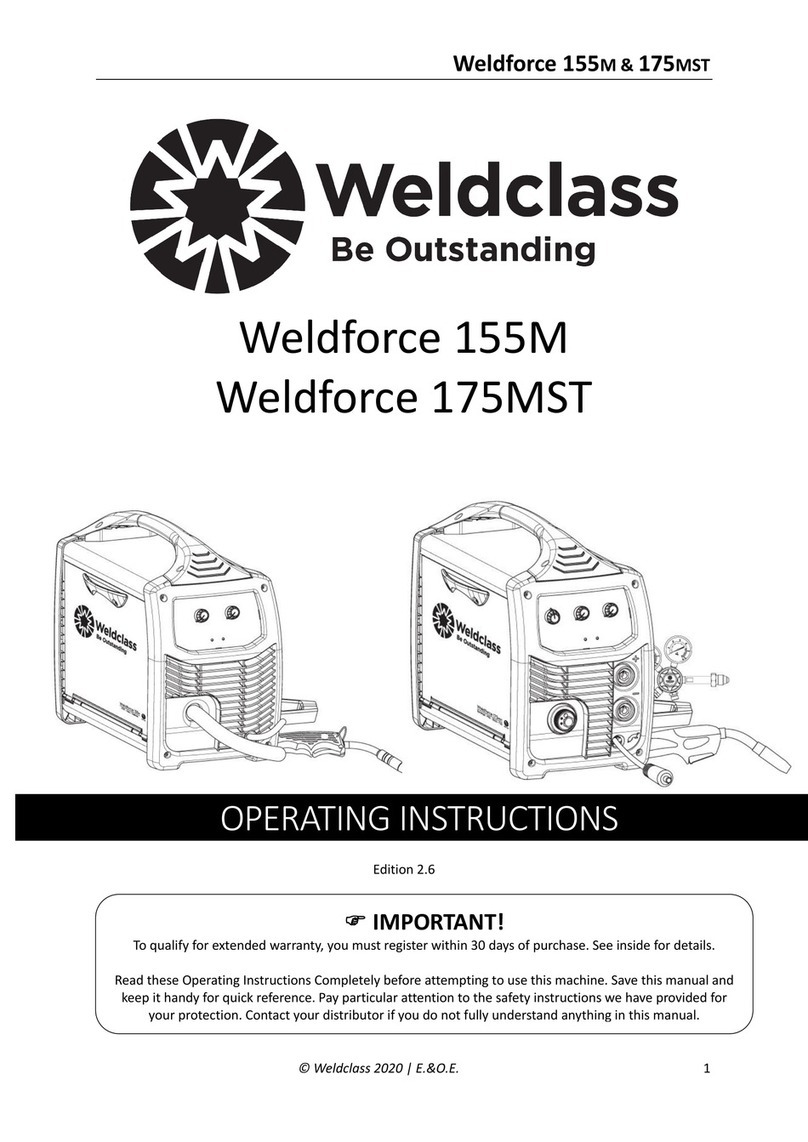
Weldclass
Weldclass Weldforce 155M User manual
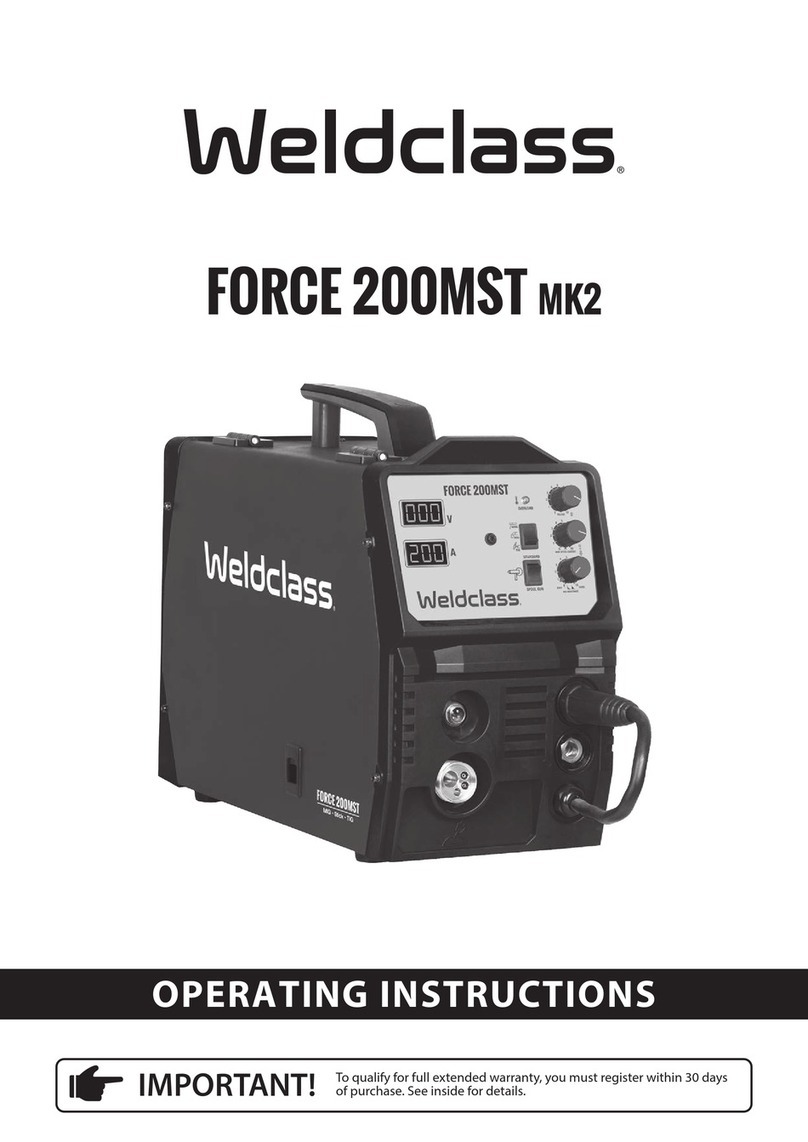
Weldclass
Weldclass FORCE 200MST MK2 User manual
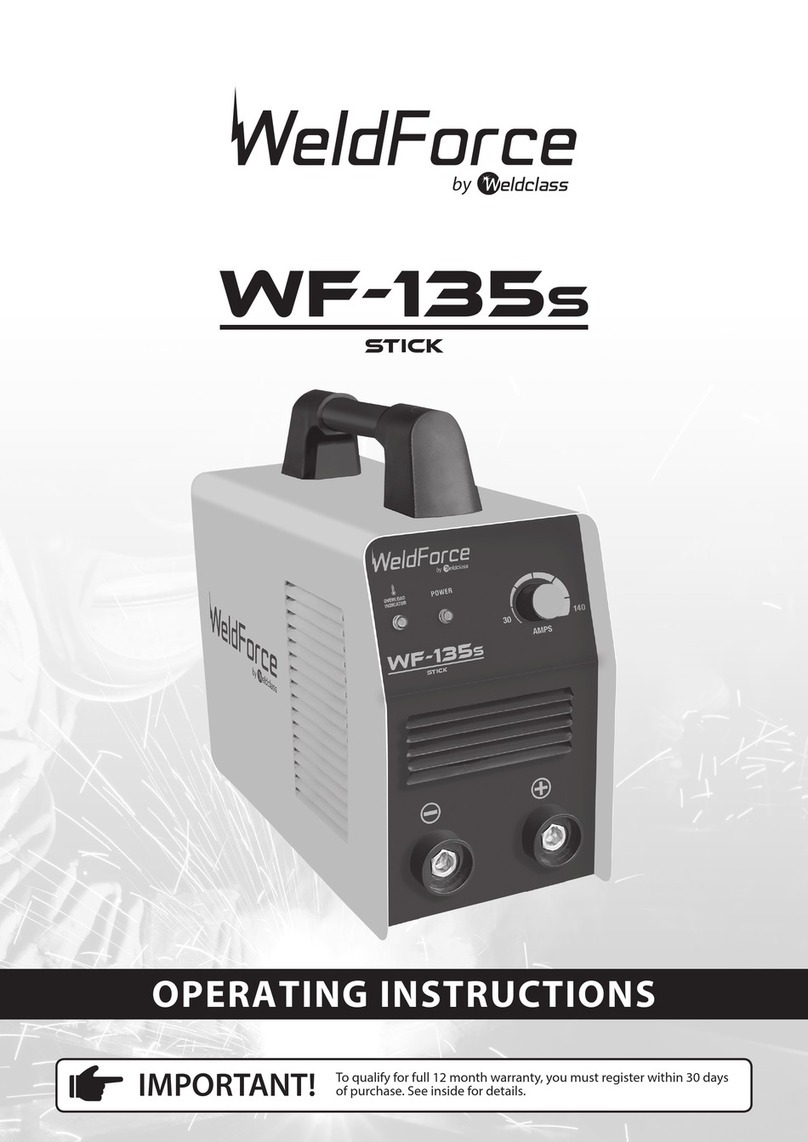
Weldclass
Weldclass WeldForce WF-135s stick User manual
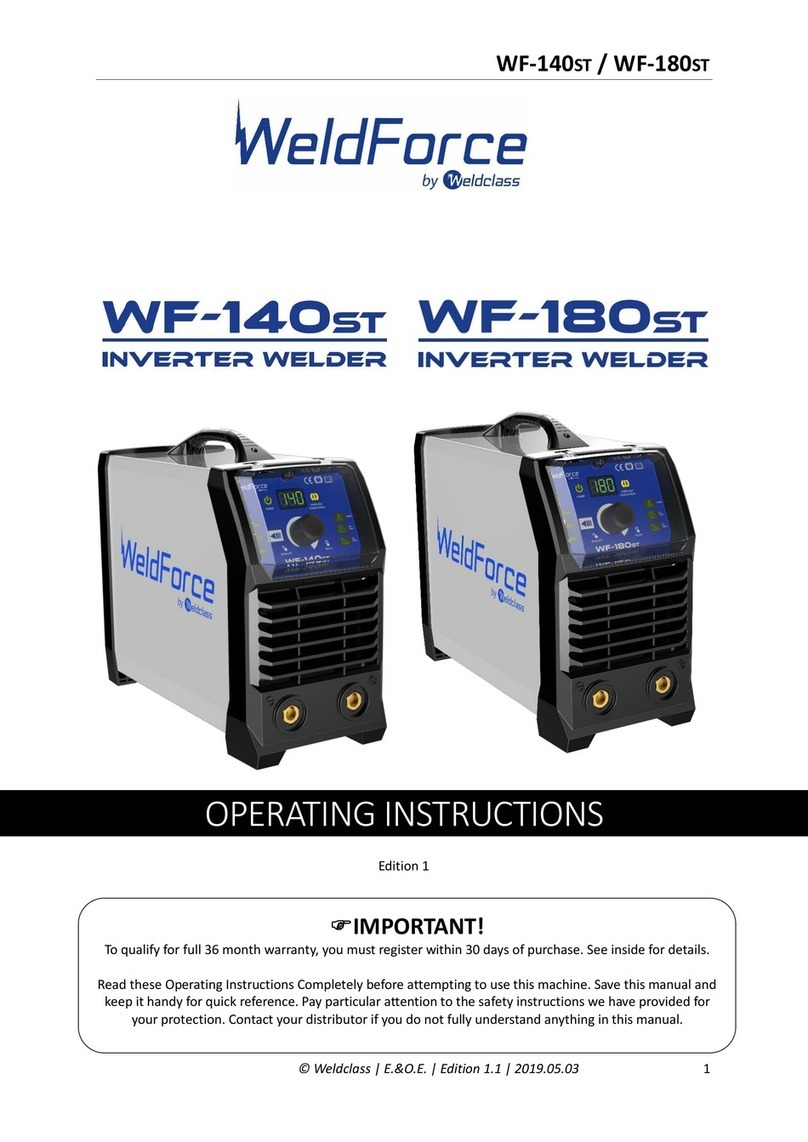
Weldclass
Weldclass WeldForce WF-140ST User manual
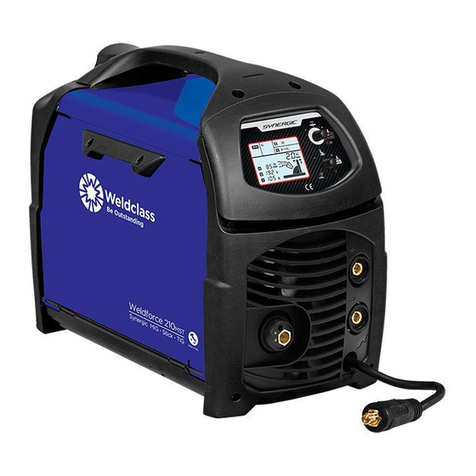
Weldclass
Weldclass Weldforce 210MST User manual
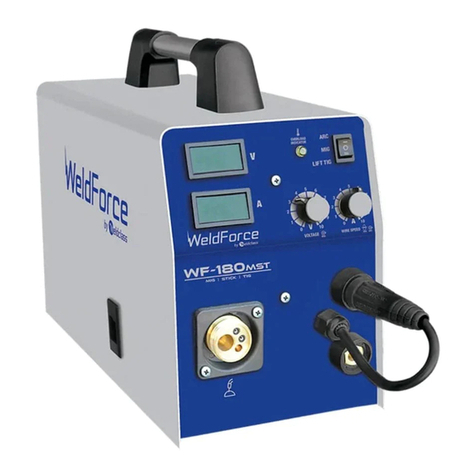
Weldclass
Weldclass WeldForce WF-180MST User manual

Weldclass
Weldclass CutForce CF-40p User manual
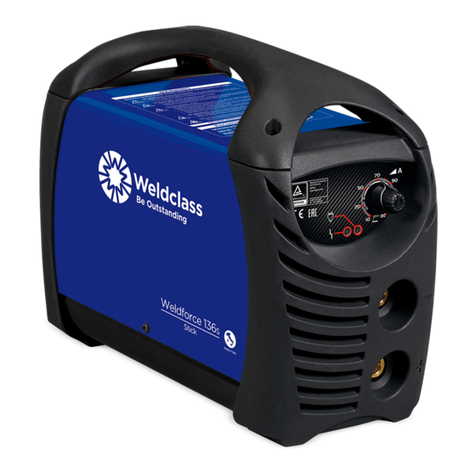
Weldclass
Weldclass Weldforce 136S User manual
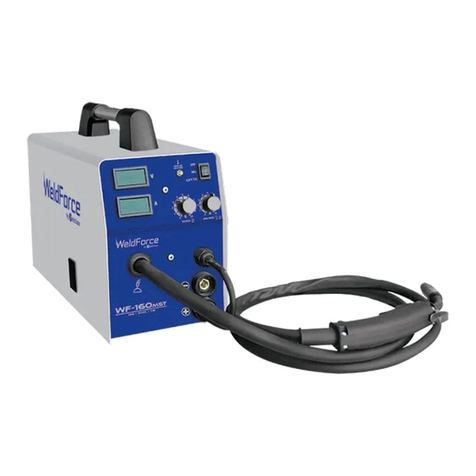
Weldclass
Weldclass WeldForce WF-160MST User manual