WellMark 2001NB Series Guide

The Company, L.L.C. Oklahoma City, Oklahoma Tel: (405) 672-6660 Fax: (405) 672-6661
wellmarkco.com
© The WellMark Company • Litho USA • All registered trademarks are the property of their respective owners. • IOM-2001NB 091007
Specifications
Connections
Process 2” MNPT Std. (Others avaialble)
Pilot 1/4” FNPT
Case Exhaust 1/8” FNPT
Output
Throttle (Proportional) 3-15 psig or 6-30 psig
Snap-Acting 0 to Full Supply
General
Repeatability 1.0% of Full Scale
Dead Band 5.0% of Input Scale
Linearity 2.0% of Full Scale
Ambient Temp. Effect 1.0% @ -40°F
3.0% @ +180°F
Specific Gravity 0.4 Minimum
Temp. Limits -40°F to +200°F
(Displacer is limiting factor)
Pressure Rating 6000 psi
Pilot Operating Pressure Normal: 20-35 psi
Overpressure Protection: Gauges are the limiting factor.
Maximum Pressure without Gauges 125 psig
Over-pressure of this control or installation of the
control in applications which may see pressure
levels beyond those for which the control is
designed may result in leakage and/or catastrophic
failure. This failure could result in leaking gas, or
produced liquid, damage to surrounding equipment
and/or environment, personal injury or death.
Suitable pressure-relieving devices, as
recommended by appropriate codes or standards,
should be installed in your system to assure that
maximum rated pressures are not exceeded.
1
WARNING!
2001NB
Series
Application
VesselInstallation
The Series 2001NB Pneumatic Level Control is designed for use in
liquid level and interface liquid control applications. The unit is
available in either Snap-Acting or Throttling configuration and is field
reversible for either Left-hand or Right-hand orientation.
Furthermore, the unit can be set up for Direct or Reversing Acting
operation. This standard displacer is 1-7/8” x 12” PVC in horizontal
configuration. Displacers of other materials and dimensions, as well
as Vertical Displacers are optionally available.
Insure that threaded connections on both the 2001NB and the vessel
are clean, free of debris and undamaged prior to installing. Install the
Displacer (32) onto the Displacer Arm (30) by threading it together
(Note: the Displacer Bushing (31) should already be installed in the
Displacer). If the unit is configured for Vertical Displacer Assemby,
theAdapter (44) will already be attached to the DisplacerArm. In this
case, install the Displacer by threading it onto the Adapter. Snug all
threaded connections firmly.
Install the Control in the vessel. Connect instrument supply line to
SUPPLY port on back. Connect control valve signal line to OUTPUT
port on back. Use a suitable thread sealant to assure leak-tight make
up and to avoid thread galling. Do not overtighten.
CAUTION!
Maximum allowable pressures for this level control are
determined by the rating of the connection. Threaded
connections are rated to 6000 psi @ 100°F. Flanged
connections are subject to the maximum ratings as specified by
ASME B16.5 for specific pressure classes and temperatures.
These pressures should not be exceeded and proper over-
pressure protection should be employed on vessels where
pressures above maximum may occur. Likewise, displacer
material and configuration should be considered when
determining suitability for a particular application.
Prior to installation of the 2001NB Level Control
system must be isolated from pressure. Failure to
do so may result in personal injury, environmental
spill concerns and/or damage to equipment.
WARNING!
Note: This document is to be used in conjunction
with WellMark Catalog Document, Section No.
3.1, “Series 2001NB Pneumatic Level Control”,
pages 1 through 3.
Installation, Operation & Maintenance Instructions
for Series 2001NB Pneumatic Level Control

Operation
The 2001NB Level Control utilizes a balanced method, whereby a
spring acting on a lever balances the weight of the displacer in the
vessel. As liquid rises in the vessel, force is made available via the
Torque Bar (16) and Fulcrum (26), to the pilot proportional to the
weight of the displaced liquid. As the liquid level rises the amount of
force increases to the pilot.
configuration, whereby rising level Pilot
output. When the unit is configured for Direct-Acting operation the
Fulcrum will be located either left or right of the pivot depending upon
whether the unit is Left Hand Mount or Right Hand Mount as
illustrated below.
configuration (rising level Pilot output)
can be accomplished by moving the Fulcrum to the opposite side as
shown below.
refers to the differential between ON and OFF.
This is determined by the position of the Fulcrum along the Torque
Bar.
Direct-Acting
Reverse-Acting
Span or Dump Span
increases
decreases
The Company, L.L.C. Oklahoma City, Oklahoma Tel: (405) 672-6660 Fax: (405) 672-6661
wellmarkco.com
© The WellMark Company • Litho USA • All registered trademarks are the property of their respective owners. • IOM-2001NB 091007
2
2001NB
Series
REVERSE-ACTING
Rising level DECREASES Pilot output
FULCRUM
PIVOT PIVOT
FULCRUM
LEFT HAND MOUNT RIGHT HAND MOUNT
psi psipsi psi
DIRECT-ACTING
Rising level INCREASES Pilot output
FULCRUM PIVOT PIVOT FULCRUM
LEFT HAND MOUNT RIGHT HAND MOUNT
psi psi psipsi
Proportional Band, when referring to a throttling control, is the ratio
of displacer actually used as compared to the overall length of the
displacer. For instance, a 50% proportional band would utilize 6” of a
12”displacer to achieve a 3-to-15 psi output.
FULCRUM
PILOT
FLAPPER
BAR
The Dump Span and Proportional Band are adjusted by moving the
Fulcrum along the Flapper Bar as necessary to achieve the desired
result.
- The Displacer’s weight is held in balance by the
Spring (21). Since the Displacer is buoyant, as the level rises the
apparent weight or of the Displacer decreases. As a result of
Level Adjustment
mass
psipsi
SPRING
ADJUSTMENT ARM
Differential force increases
as Displacer is unweighted
Rotates down, relieving
pressure on Torque Bar
Displacer’s apparent weight
decreases as fluid level rises
FLAPPER BAR
FULCRUM
PILOT
TORQUE
BAR
the rising Displacer the Adjusting Bar rotates, relieving pressure on
the Torque Bar. This results in an increase in differential Spring
force, transmitting that force to the Pilot poppet via the Fulcrum and
Flapper Bar. Increasing tension on the Spring lowers the sensed
level. Conversely, decreasing the spring force raises the sensed
level.
Some systems require control at the interface distinction between the
hydrocarbon and water. This is referred to as . It
is possible to adjust the Spring to a point at which the hydrocarbon
liquid completely envelopes the displacer without transmitting
enough force to engage the pilot and produce any output.
Water has a higher specific gravity than hydrocarbon and naturally
separates lower, with hydrocarbon liquid rising above it. When
properly adjusted, water can rise to a level on the displacer, changing
its apparent weight and causing enough force to engage the pilot,
which will then result in output. The 2001NB unit’s broad range of
control allows liquid interface sensing.
Interface Operation
interface operation

The Company, L.L.C. Oklahoma City, Oklahoma Tel: (405) 672-6660 Fax: (405) 672-6661
wellmarkco.com
© The WellMark Company • Litho USA • All registered trademarks are the property of their respective owners. • IOM-2001NB 091007 3
2001NB
Series
Pilot Operation
IMPORTANT!
Snap-Acting Pilot • No-Bleed On/Off FlowAction
Throttle Pilot • No-Bleed Modulating FlowAction
Although the 2001NB Level Control is appropriately referred to
as , all pneumatic systems require that the
diaphragm operated motor valve exhausts or pressure off
the diaphragm once the valve has completed its actuation cycle.
This vented gas, along with the gas within the lines leading from
the control to the valve will vent back through the control. This
clear distinction, between gas and gas must be
made and understood. As with any or control, the
intent is to stop the unnecessary bleed of gas between valve
actuation cycles. The 2001NB Level Control will accomplish
this task. It will not however, nor will any other or
device stop the required venting of gas from the diaphragm and
lines once the valve has cycled.
The Snap-Acting Pilot is comprised of two inner valves. Valve (1)
admits system supply gas to output. Valve (2) controls system
exhaust from output. Valve (1), as shown in the closed position (Fig.
1), is held closed by force exerted from supply gas. When upward
Flapper Bar forces transferred to Valve (2) is sufficient enough to
overcome supply force, the ball snaps upward, allowing supply
pressure to communicate to output port, which operates the
diaphragm motor valve (not shown). The spherical end of Valve (2)
closes the exhaust port the instant the ball snaps upward and
remains seated against supply pressure until force on the valve
diminishes. As force is removed from Valve (2), causing it to unseat,
a simultaneous action occurs, causing Valve (1) to seat instantly,
closing the supply port to ouput and opening output to exhaust,
thereby allowing the diaphragm motor valve to reverse it’s action.
The Throttle Pilot utilizes a diaphragm, which creates a forced
balance Pilot (Fig. 2). Output pressure acts upon the diaphragm
causing it to push back at the same force being applied to the lower
seat. More force on the seat produces a proportionate increase in
Pilot pressure. When the Flapper Bar of the control exerts upward
force on the lower valve seat, it forces the lower seat closed against
valve body and opens the supply valve. Supply pressure enters the
system, increasing until the control and diaphragm motor valve (not
shown) pressure equals the Flapper Bar force and produces a forced
system balance. The control will stay in this position until a decrease
in the tank level reduces the force allowing exhaust, or an increase in
the level produces an action as described. System supply gas does
not flow while the Pilot is in balance.
“No-Bleed”
vents
“bleed” “vent”
no- low-bleed
no- low-bleed
The 2001NB Level Control has a sealed box which allows the user to pipe vent gas
away from the facility as needed. This is highly recommended if the control is to
be mounted inside an enclosure that might result in a dangerous build up of gas.
Failure to do so may result in damage to equipment, personal injury or death.
!CAUTION!
SUPPLY
OUTPUT

Startup
Assure free-travel of the Displacer and Displacer Arm by rocking the
Torque Bar by hand and observing corresponding movement of
Displacer. The Displacer Arm should be centered in the vessel
nozzle to assure that the vessel nozzle does not inhibit free
operation. Displacer Arm should be parallel to the ground at
installation.
The controller is factory-set for average level and sensitivity.
- Increase the compression of the Spring by
turning theAdjustment Wheel to the
LEVELADJUSTMENT
To DECREASE LEVEL
RIGHT.
SETTING INTERFACE LEVEL
NOTE: The
presence of foam in the interface zone may affect the accuracy
of the control.
The controller is factory-set for average level and sensitivity.
Generally speaking, interface operation is most successful when
there is a substantial differential in specific gravity between the two
liquids. Interface cannot be reliably achieved with a displacer-type
control with specific gravity differentials less than 0.1. Also, the
sensitivity of the interface control is increased by the size of the
displacer. Therefore, it is usually advantageous to use the largest
displacer available, which will fit into the vessel.
The Company, L.L.C. Oklahoma City, Oklahoma Tel: (405) 672-6660 Fax: (405) 672-6661
wellmarkco.com
© The WellMark Company • Litho USA • All registered trademarks are the property of their respective owners. • IOM-2001NB 091007
4
2001NB
Series
psipsi
DECREASE LEVEL
by increasing Spring compression
ADJUSTMENT WHEEL
SPRING
RIGHT
psipsi
ADJUSTMENT WHEEL
SPRING
psipsi
INCREASE LEVEL
by decreasing Spring compression
ADJUSTMENT WHEEL
SPRING
LEFT
To INCREASE LEVEL -
LEFT.
Decrease Spring compression by turning
theAdjusting Wheel to the
ADJUSTING PROPORTIONAL BAND (SPAN)
To DECREASE BAND
(Increase Sensitivity)
Loosen Thumbscrew on Fulcrum and position the Fulcrum along the
Flapper Bar.
Slide Fulcrum along
Flapper Bar toward
Snap Ring.
FULCRUM
PILOT
FLAPPER
BAR
SNAP
RING
FULCRUM
PILOT
FLAPPER
BAR
SNAP
RING
To INCREASE BAND
(decrease Sensitivity)
Slide Fulcrum along
Flapper Bar away from
Snap Ring.
Once desired band/span is achieved re-tighten Thumbscrew.
FULCRUM
PIVOT
PILOT
FLAPPER
BAR
1”
2
1. Set Fulcrum approx. 1/2” from
pivot pin.
Reduce Spring tension slowly by
turning the Adjusting Wheel to the
Allow the upper fluid to rise until
it completely submerges the Displacer.
LEFT.
Next, fine-tune the adjustment by turning the Adjusting Wheel to
the until an output signal is attained.
Finally, turn theAdjusting Wheel back to the until the output
signal returns to
2. Allow the lower liquid to rise until the desired interface level is
attained. Fine tune by slowly turning the Adjusting Wheel to the
until an output signal is obtained. Finally, slowly turn the
Adjusting Wheel to the until the output signal returns to
ZERO.
3. To obtain a shorter dump span, slide the Fulcrum away from the
pivot and repeat the above procedure.
RIGHT
LEFT
ZERO.
RIGHT
LEFT
Maintenance
The 2001NB Level Control is designed to provide years of reliable
service. However, build up of debris, paraffin, etc inside the
controller Body can interfere with proper functioning. A regular
maintenance program should include checking for this condition.
Prior to maintenance of the 2001NB Level Control
system must be isolated from pressure. Failure to
do so may result in personal injury, environmental
spill concerns and/or damage to equipment.
WARNING!

The Company, L.L.C. Oklahoma City, Oklahoma Tel: (405) 672-6660 Fax: (405) 672-6661
wellmarkco.com
© The WellMark Company • Litho USA • All registered trademarks are the property of their respective owners. • IOM-2001NB 091007 5
2001NB
Series
Maintenance- continued
Note: This procedure does not include removal or servicing of the
Pilot. Refer to section elsewhere on this page for information
specific to removal of Pilot. Also, for reference see Sectional
Diagram and Parts List on Page 6.
Relax compression on Spring (21) and remove along with the Upper
Guide (22). Remove the Stud (19) and Adjustment Wheel (20).
Remove Nyloc Nut (28) from Stud (23) and slide the Flapper Bar (24)
off Stud. DO NOT REMOVE THE STUD, as it is press-fit into the
Control Box. Fulcrum (26) and Thumbscrew (27) should remain in
place on the Flapper Bar.
Remove a second Nyloc Nut (28) from the Pivot Shaft (6) and slide
Torque Bar off the Pivot Shaft (6).
Hold the Adjusting Bar (14) while loosening two Capscrews (15).
Once Adjusting Bar is loose, remove it along with the Adjusting
Screw (17) from the Pivot Shaft. The Adjusting Screw need not be
removed from theAdjusting Bar.
Remove two Capscrews (12) holding the Control Box (1) to the Body
(5) and disassemble Control Box from Body.
Mount the Control Box to the Body using the two Capscrews. Screws
should be tightened to 6 ft-lbs.
Install the Spacer on the Pivot Shaft.
If the Adjusting Screw was removed from the Adjusting Bar during
disassembly it should be refitted, threading it into the Adjusting Bar
until an equal amount of threads is showing above and below the
Adjusting Bar.
Slide theAdjusting Bar onto the Pivot Shaft, against the Spacer, such
that the portion through which the Adjustment Screw is installed is on
the opposite side from the Body (see below).
General Disassembly
General Reassembly
Slide the Spacer (11) from the Pivot
Shaft.
Temporarily install the Torque Bar onto the Pivot Shaft. Position the
Level Adjusting Bar and Adjusting Screw such that the Torque Bar is
parallel with the Displacer Arm (30) when the tip of the Adjusting
Screw is touching the bottom of the Torque Bar.
Remove the Torque Bar, being careful not to disturb the position of
the Adjusting Bar, and fully tighten the two Capscrews securing the
Adjusting Bar to the Pivot Shaft. DO NOT OVERTIGHTEN.
Slide the Torque Bar back in place with the hole for the Upper Guide
oriented on bottom and in proper position to accept the Upper Guide
once the Spring is re-installed. Secure the Torque Bar with the Nyloc
Nut, leaving approx. 1/16” clearance between the bottom of the nut
and the Torque Bar.
Slide the Flapper Bar back onto the Stud and secure with the other
Nyloc Nut. IMPORTANT! Do not over-tighten this nut, as the
Flapper Bar must be able to move freely on the Stud.
Re-install the Stud and Adjusting Wheel. Install the Spring and
Upper Guide, engaging the extrusion on the Upper Guide into its
mating hole on the bottom of the Torque Bar.
IMPORTANT! The Torque Bar must be able
to move freely on the Pivot Arm. Tightening the Nyloc Nut too
much will inhibit this free travel.
Pilot Removal/Replacement
The Pilot (4) is held in place by the Pilot Clamp (36) and four
Capscrews (35). Remove the Capscrews, Pilot Clamp and Pilot from
the Control Box. Inspect condition of Gasket (34) and replace if
necessry.
Re-install the Pilot, assuring that the Gasket is seated properly with
port holes aligned with ports in Pilot and Control Box.
Remove the Body from the Control Box as described in the
section.
Remove the two Shaft Retainers (9) utilizing a 1-1/8” wrench.
Remove the Pivot Shaft (6). Remove the Pivot Shaft O-Rings (7),
Back-up Rings (8) and Shaft Retainer O-Rings (10) and discard.
Body Disassembly
General
Disassembly
Prior to removing Pilot system must be isolated from
pressure. Failure to do so may result in personal
injury, environmental spill concerns and/or damage
to equipment.
CAUTION! If the Shaft Retainers (9) are removed, O-Rings (7
and 10) and Back-up Rings (8) MUST BE REPLACED.
Snug, but the two Capscrews that hold the Adjusting
Bar to the Pivot Shaft.
do not tighten
psipsi
BODY
CAPSCREWS
ADJUSTMENT
BAR
on opposite side from BODY
WARNING!

The Company, L.L.C. Oklahoma City, Oklahoma Tel: (405) 672-6660 Fax: (405) 672-6661
wellmarkco.com
© The WellMark Company • Litho USA • All registered trademarks are the property of their respective owners. • IOM-2001NB 091007
6
2001NB
Series
Item Description Qty. Part Number
25 TRU-ARC RING 1 06000-1385
26 FULCRUM, Aluminum 1 05011-4412
27 THUMBSCREW, SS/Plastic 1 06500-5429
28 NYLOC NUT, SS 2 05000-2567
29 ACORN NUT, SS 1 05000-2575
30 DISPLACER ARM - STD., SS 1 06000-1534
30 DISPLACER ARM - VF, SS 1 05011-9296
31 DISPLACER BUSHING, SS 1 06000-5105
32 DISPLACER - STD., PVC 1 05012-3561
33 HINGE PIN, Plated CS 2 06000-7537
34 GASKET, Neoprene 1 06000-4819
35 CAPSCREW, SS 4 05000-5313
36 PILOT CLAMP, SS 1 05012-6325
37 PANEL SCREW, SS 1 06000-1153
38 RETAINER, SS 1 06000-2672
39 SERIAL TAG, Aluminum (not shown) 1 06000-1922
40 THREAD SEAL, Steel/Buna N 1 06000-0395
41 O-RING, Viton® 1 05000-5586
42 BEARING, SS 2 06000-7552
43 TOLERANCE RING, SS 2 06000-7560
44 ADAPTER, VERT. DWN ASSY., SS 1 06500-4350
45 COVER GLASS, Lexan® (not shown) 2 10916
46 COVER GLASS PLATE, SS (not shown) 2 10915
47 COVER GLASS GSKT, Neoprene (not shown) 2 10917
48 SCREW, Plated Steel (not shown) 8 001501P
Item Description Qty. Part Number
1 CONTROL BOX, Die Cast Aluminum 1 05012-4841
2 COVER, Die Cast Aluminum 1 05012-4834
3 BOX SEAL, Neoprene 1 06000-5097
4 SNAP PILOT ASSY., Aluminum & SS 1 06500-5304
4 THROTTLE PILOT ASSY., Aluminum & SS 1 06500-5387
5 BODY, CS 1 05011-4560
6 PIVOT SHAFT, SS 1 05011-4511
7 O-RING, Viton® 2 05000-0769
8 BACK-UP RING, Teflon® 2 06000-1179
9 SHAFT RETAINER, SS 2 05012-9389
10 O-RING, Viton® 2 05000-1155
11 SPACER, SS 1 05011-4495
12 CAPSCREW, SS 2 05000-5578
13 CAPSCREW, SS 1 05000-5453
14 ADJUSTING BAR, Aluminum 1 05011-4438
15 CAPSCREW, SS 2 05000-2526
16 TORQUE BAR, Aluminum 1 05011-4545
17 ADJUSTING SCREW, SS 1 05011-4537
18 JAM NUT, SS 1 05000-2559
19 STUD, SS 1 05011-4552
20 ADJUSTMENT WHEEL, Aluminum 1 05011-4529
21 SPRING, SS 1 06000-4157
22 UPPER GUIDE, Aluminum 1 05011-4479
23 STUD, FLAPPER BAR, SS 2 05012-9371
24 FLAPPER BAR, SS 1 05011-4404
The Bearings (42) and Tolerance Rings (43) need not be removed
from the Shaft Retainers unless they are damaged and must be
replaced.
Parts List
BACK-UP RING (8)
SHAFT RETAINER (9)
O-RING (7)
Body Reassembly
Lightly lubricate new O-Rings and Back-
Up Rings with oil. Install Pivot Shaft
Back-Up Ring into Shaft Retainers first,
with O-Ring next. IMPORTANT! The
Back-Up Ring MUST be outboard of
the O-Ring,as illustrated.
Thread the Shaft Retainer into the Body.
Insert the Pivot Shaft into the Body from the inboard side, seating it
firmly into the Bearing in the Shaft Retainer on the side
Re-install the remaining Shaft Retainer over the Pivot Shaft and
threaded into the side of the Body. Tighten both Shaft
Retainers firmly.
Re-attach the assembled Body to the Control Box as described in the
section.
outboard
outboard
inboard
General Reassembly
SUPPLY OUTPUT
030
255
10 15 20
030
255
10 15 20
35
36
2
23
38
37
16
12
14
18
17
33
40 13 15 29 19 20
21
22
26
23 30 31 32
44
34
41
539 10
8
42
43
9
11 67
3
24
27
25
1
4
28 Vertical Displacer
Assembly
Horizontal Displacer
Assembly
Table of contents
Other WellMark Control Unit manuals
Popular Control Unit manuals by other brands
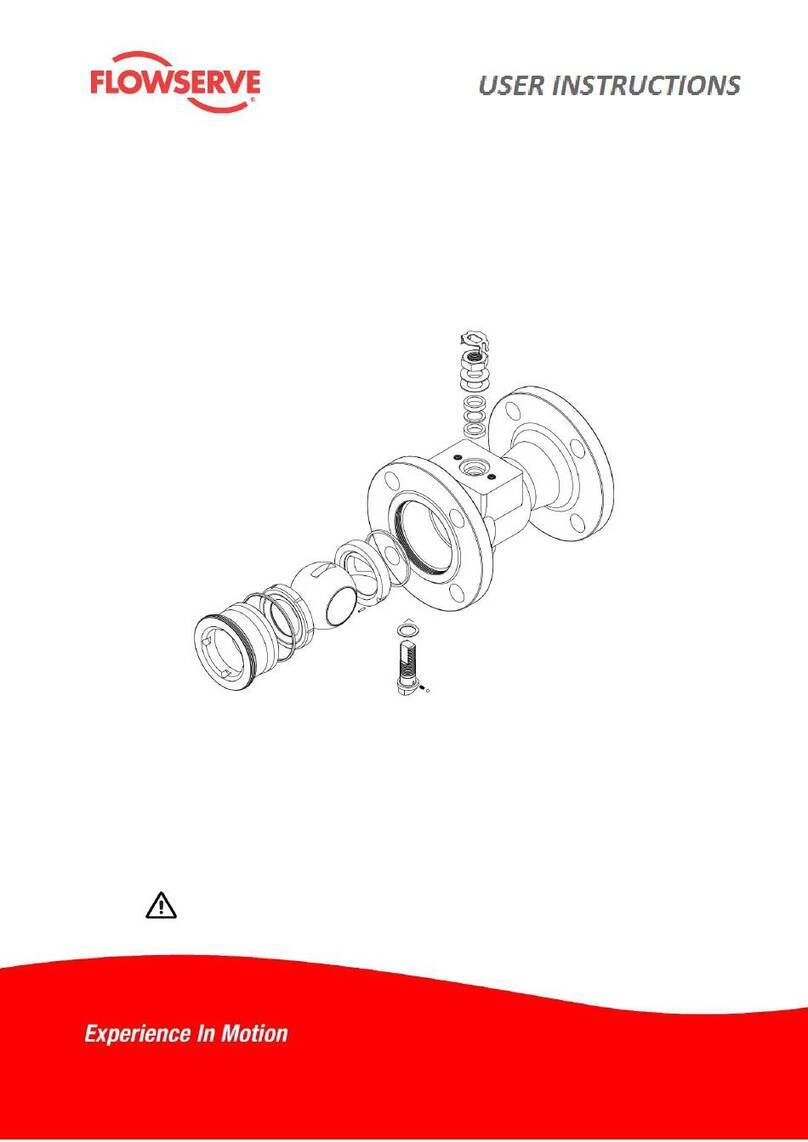
Flowserve
Flowserve Worcester V-Flow 51 Series User instructions
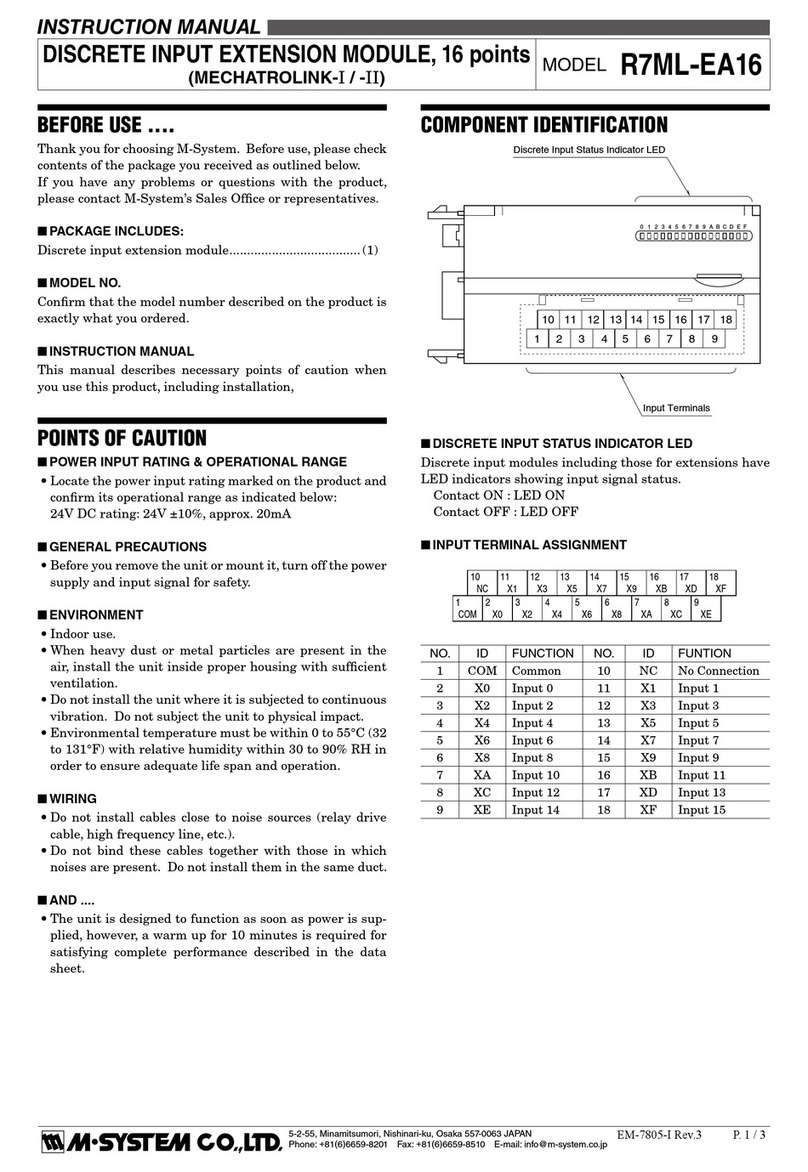
M-system
M-system R7ML-EA16 instruction manual

REMKO
REMKO Smart Control Touch operating manual
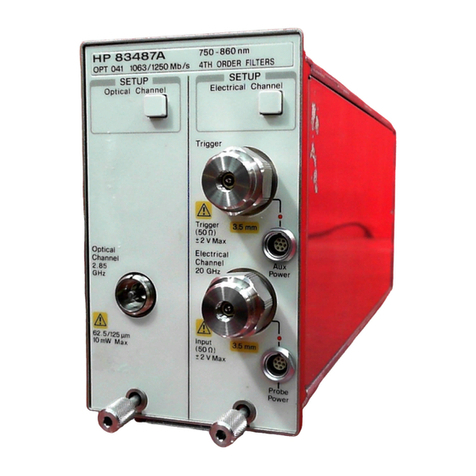
Agilent Technologies
Agilent Technologies 83487A user guide
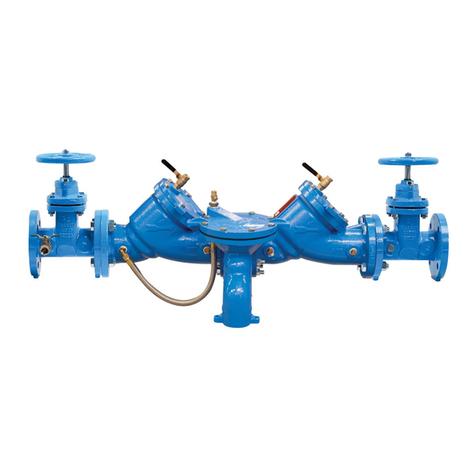
Watts
Watts 909 Series Installation, maintenance & repair
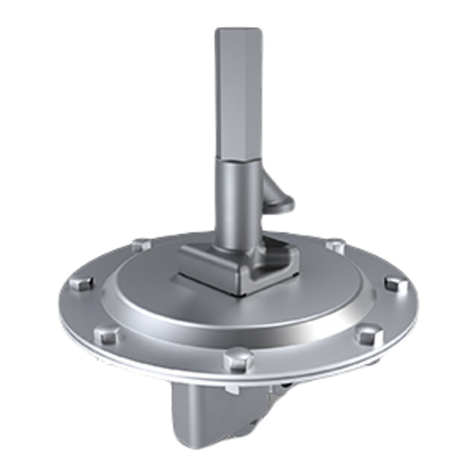
Protectoseal
Protectoseal 30 Series Installation & maintenance guide
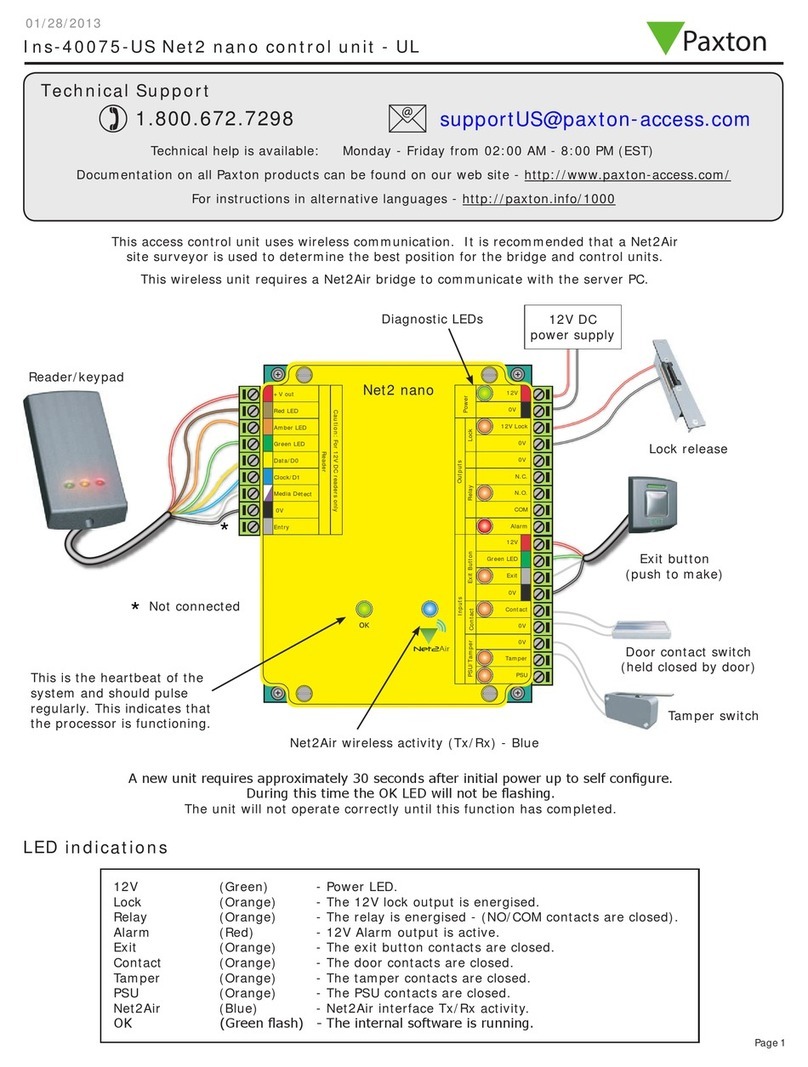
Paxton
Paxton 654-549-US instructions
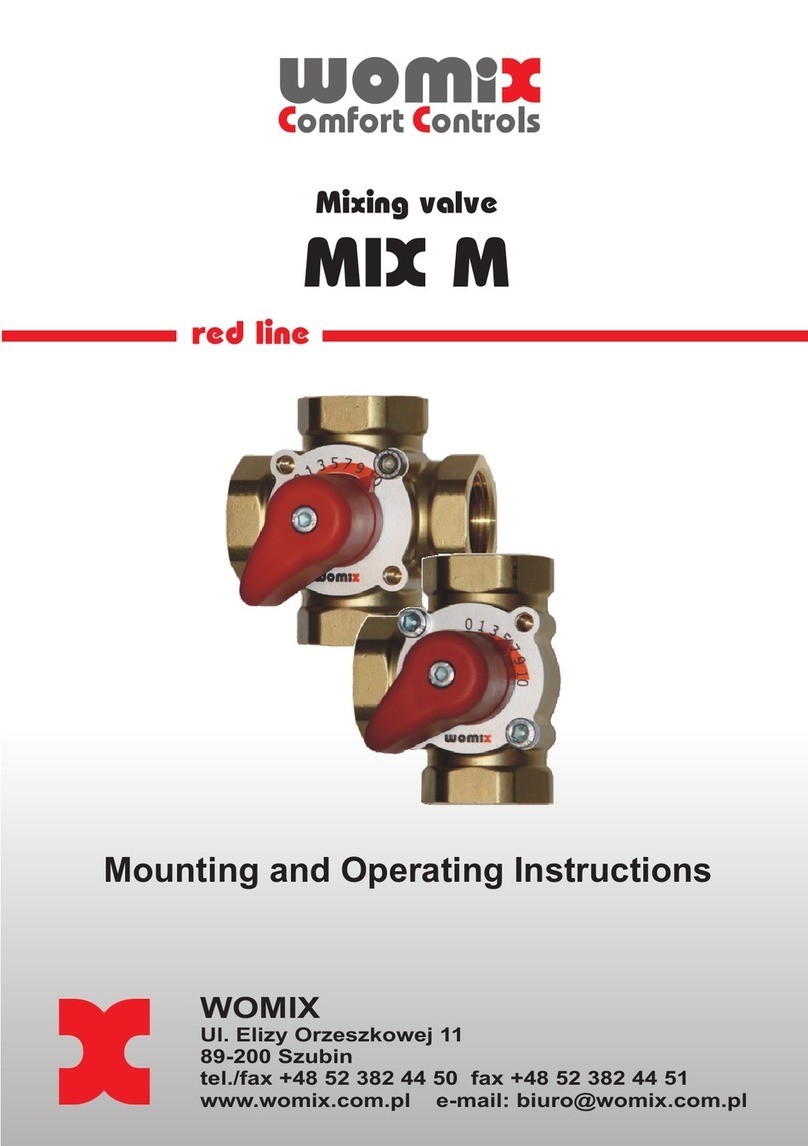
WOMIX
WOMIX MIX M Series Mounting and operating instructions
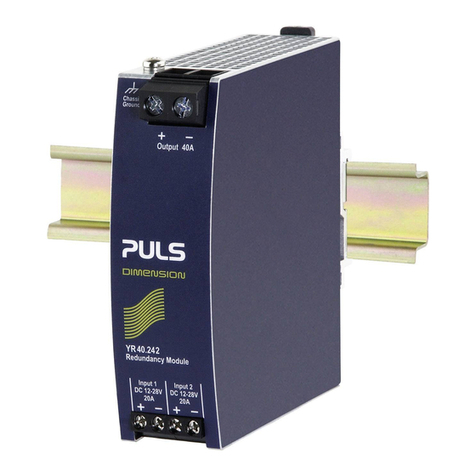
Puls
Puls YR2.DIODE instruction manual
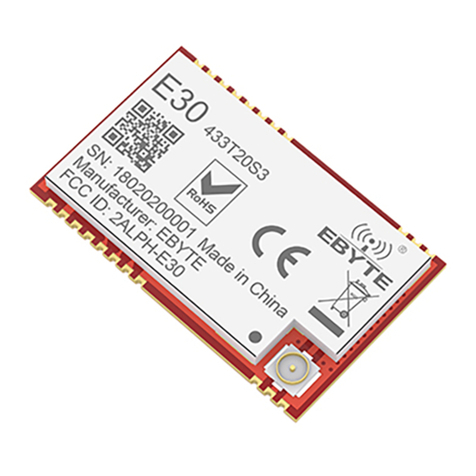
Ebyte
Ebyte E30-433T20S3 user manual

Roger Technology
Roger Technology R70 2AC INSTRUCTIONS AND RECOMMENDATIONS FOR THE INSTALLER
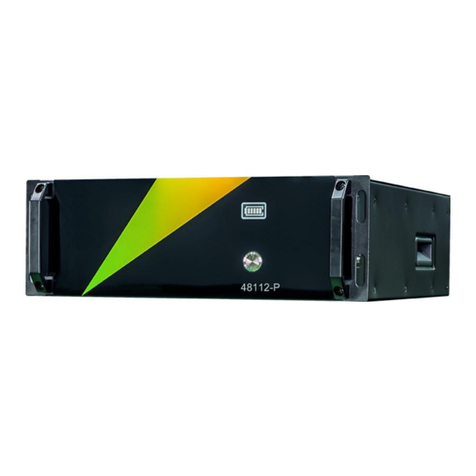
Neosun Energy
Neosun Energy NS48112-P user manual