Protectoseal 30 Series Operating and safety instructions

Installation & Maintenance Guide
PROTECTOSEAL SERIES O. 30
TA K BLA KETI G VALVE
PROTECTOSEAL®
Safety Without Compromise
225 Foster Ave., Bensenville, IL 60106-1690
P630.595.0800 F630.595.8059
[email protected] www.protectoseal.com

PROTECTOSEAL SERIES O. 30
TA K BLA KETI G VALVE
Table of Contents
Installation, Start-up & Shut-Down
Placement . . . . . . . . . . . . . . . . . . . . . . . . . . . . . . . . . . . . . . . . . . . . . . . . . . 1
Start-Up . . . . . . . . . . . . . . . . . . . . . . . . . . . . . . . . . . . . . . . . . . . . . . . . . . . 2
Shut-Down . . . . . . . . . . . . . . . . . . . . . . . . . . . . . . . . . . . . . . . . . . . . . . . . . . 3
Maintenance
Purpose & Frequency. . . . . . . . . . . . . . . . . . . . . . . . . . . . . . . . . . . . . . . . . . 3
Leakage Check . . . . . . . . . . . . . . . . . . . . . . . . . . . . . . . . . . . . . . . . . . . . . . . 3
Disassembly & Inspection . . . . . . . . . . . . . . . . . . . . . . . . . . . . . . . . . . . . . . . 3
Reassembly . . . . . . . . . . . . . . . . . . . . . . . . . . . . . . . . . . . . . . . . . . . . . . . . . 5
Reinstallation & System Check . . . . . . . . . . . . . . . . . . . . . . . . . . . . . . . . . . . 5
Accessories
Filter. . . . . . . . . . . . . . . . . . . . . . . . . . . . . . . . . . . . . . . . . . . . . . . . . . . . . . 11
Pressure auges . . . . . . . . . . . . . . . . . . . . . . . . . . . . . . . . . . . . . . . . . . . . 12
Integral Purge Accessories. . . . . . . . . . . . . . . . . . . . . . . . . . . . . . . . . . . . . 12
Field Test Accessories . . . . . . . . . . . . . . . . . . . . . . . . . . . . . . . . . . . . . . . . 15
Troubleshooting
Problem -
#1 The blanketing valve does not open at all . . . . . . . . . . . . . . . . . . . . . 21
#2 The blanketing valve flows full open without resealing . . . . . . . . . . . . 21
#3 The blanketing valve leaks continuously.. . . . . . . . . . . . . . . . . . . . . . . 22
#4 The blanketing valve opens above or below the set point. . . . . . . . . . 22
#5 The pressure vent or other pressure relief device opens . . . . . . . . . . 22
before the blanketing valve closes
#6 The vacuum vent or other vacuum relief device opens . . . . . . . . . . . . 23
#7 The blanketing valve cycles, repeatedly opening and . . . . . . . . . . . . . 23
closing
Figures
#1 Installation . . . . . . . . . . . . . . . . . . . . . . . . . . . . . . . . . . . . . . . . . . 1
#2 Recommended Minimum Sense Line I.D. Based on Length . . . . . . . . . . 2
#3 Bolt Tightening Pattern. . . . . . . . . . . . . . . . . . . . . . . . . . . . . . . . . . . . . 5
#4 Blanketing Valve. . . . . . . . . . . . . . . . . . . . . . . . . . . . . . . . . . . . . . . . . . 6
#5 Diaphragm Assembly . . . . . . . . . . . . . . . . . . . . . . . . . . . . . . . . . . . . . . 7
#6 Main Valve Assembly. . . . . . . . . . . . . . . . . . . . . . . . . . . . . . . . . . . . . . . 8
#7 Recommended Test Set-Up. . . . . . . . . . . . . . . . . . . . . . . . . . . . . . . . . 10
#8 Pilot Filter. . . . . . . . . . . . . . . . . . . . . . . . . . . . . . . . . . . . . . . . . . . . . . 11
#9 Pressure auges . . . . . . . . . . . . . . . . . . . . . . . . . . . . . . . . . . . . . . . . 12
#10 Integral Purge System . . . . . . . . . . . . . . . . . . . . . . . . . . . . . . . . . . . . 13
#11 Higher Pressure Set Point Field Test Kit . . . . . . . . . . . . . . . . . . . . . . . 19
#12 Low Pressure Set Point Field Test Kit . . . . . . . . . . . . . . . . . . . . . . . . . 20

PROTECTOSEAL SERIES O. 30
TA K BLA KETI G VALVE
Installation & Maintenance Guide
Definition of Terms Some of the terms used in this manual are defined below:
Conservation Vent: A device which is connected to a storage tank and regulates the
pressure therein. Conservation vents may provide pressure relief, vacuum relief, or both.
Pallets move in direct response to tank pressure allowing flow out of or into the tank. Pallet
movement may be controlled by weight-loading, spring-loading, or a pilot valve.
Deadband: The total pressure difference between the blanketing valve opening pressure
(or set point) and resealing pressure.
Diaphragm Chamber: The portion of the valve which contains the sense diaphragm.
Emergency Vent: A conservation vent which provides additional pressure relief to
accommodate extraordinary conditions such as fire exposure to a tank or full-open failure
of a blanketing valve.
Flow Plug: A fitting installed at the valve inlet port to reduce the flow of gas through the
valve.
Inlet Port: The connection to the blanketing valve coming from the gas supply line.
Outlet Port: The connection to the blanketing valve leading to the storage tank.
Poppet: The component in the valve which can move open from a normally seated posi-
tion to allow flow through the valve.
Poppet Spring: The spring which biases the poppet towards the seated position.
Purge: A very low flow of supply gas directed past the sense line and/or the outlet in
order to keep corrosive vapors away from the blanketing valve.
Sense Chamber: The space below the diaphragm chamber to which the pressure from
the sense line is directed. The pressure in the sense chamber controls the opening and
closing of the blanketing valve.
Sense Diaphragm: A thin, non-metallic disc in the diaphragm chamber which flexes in
response to changes in tank pressure acting upon it.
Sense Line: A line running from the storage tank to the sense port of the blanketing
valve. It feeds tank pressure to the underside of the sense diaphragm.
Sense Port: The connection to the blanketing valve coming from the sense line.
Set Point: The tank pressure (positive or negative) at which the blanketing valve opens.
Soft Goods: The elastomeric components of the blanketing valve including the O-rings,
gaskets and diaphragm.
Stop: A bolt connected to the sense diaphragm which contacts the poppet to move it in
response to movement of the sense diaphragm.
Viton® and Kalrez® are registered Trademarks of E.I. DuPont de Nemours & Co., Inc.
Chemraz® is a registered Trademark of reen, Tweed & Co., Inc.

PROTECTOSEAL SERIES O. 30
TA K BLA KETI G VALVE
Installation & Maintenance Guide
Page 1
Placement
I STALLATIO
The blanketing valve should be placed on top of the storage tank with its outlet connect
ed via
a short run of pipe to the top of the tank. A second line runs from the sense port of the
valve to a separate connection on the tank. A line coming from the blanketing gas supply
source connects to the valve inlet. The blanketing valve must be positioned so that the inlet
line is horizontal and the outlet line points downward. Installation requires connecting the
blanketing valve to three lines as shown below in Fig. 1.
Fig. 1
All three lines connecting to the valve should have full bore shut-off valves so that the unit
can be isolated and depressurized for maintenance. The use of pipe unions at each con-
nection will facilitate installation and removal of the blanketing valve. FEP tape should be
applied to all pipe thread connections. However, be careful in applying it so that the tape
cannot get loose inside and potentially clog the blanketing valve. DO NOT USE PIPE DOPE.
Further details regarding the three lines follow:
■ SUPPLY LINE: The piping leading to the blanketing valve inlet should be the same pipe
size as the inlet connection. This line should incorporate a full bore shut-off valve to enable
isolation of the valve from the pressure supply during maintenance. The line should also
include an in-line filter. A 40 micron filter element is recommended. The filter flow capacity
must be higher than the required flow through the blanketing valve.
■ OUTLET LINE: The piping from the valve outlet should be the same size as the outlet
connection. This line should also incorporate a full bore-shut-off valve to enable isolation of
the blanketing valve from the tank during maintenance. A short, straight pipe run from the
valve outlet to the top of the storage tank is recommended. An extended length of pipe
from the blanketing valve to the tank could lead to delayed closing of the valve and thus
overpressurization of the tank.
■ SENSE LINE: The sense line should also include a full bore valve to enable isolation of
the blanketing valve from the tank during maintenance. The horizontal run from the sense
port should be angled slightly down away from the valve to ensure that any

Start-Up
PROTECTOSEAL SERIES O. 30
TA K BLA KETI G VALVE
condensate could not drain into the valve. 1⁄2" O.D. tubing or larger should be used to
ensure that there is not a pressure drop from the tank to the valve. This size line is also
needed so that the high pressure supply gas which leaks into the sense chamber while the
valve is open is able to dissipate into the tank so as not to affect closing of the blanketing
valve.
The sense line connection to the tank should be far enough from the outlet line connection
to ensure that a static pressure is sensed. On the other hand, the line should not be so
long as to lead to a pressure drop in the line. A range of 2 to 10 feet from the outlet line
connection is recommended. If a longer sense line is necessary, then the size of the tubing
or pipe should be increased according to offset pressure drop effects, see Fig. 2.
Installation & Maintenance Guide
Page 2
Sense Line Length * (ft.), For 90° bends add 20 diameters to the length.
Fig. 2
Recommended Minimum Sense Line I.D. Based on Length
The blanketing valve is tested and set to the customer specified set point (as listed on the
label) prior to shipment. Further adjustment in the field should not be required. After instal-
lation is complete, follow the steps below in order to put the blanketing valve into service:
1. Open the shut-off valve in the sense line between the blanketing valve and the tank.
2. Open the shut-off valve in the outlet line between the blanketing valve and the tank.
3. Check the blanketing gas supply line pressure to see that it corresponds to the pres-
sure or pressure range listed on the label of the blanketing valve. If not, the supply
pressure regulator should be adjusted accordingly. The maximum range in which the
valve will operate is 10 to 200 PSI .
4. Slowly open the shut-off valve in the blanketing gas supply line. Pressurizing the blan-
keting valve slowly pre-loads the valve so that it will not initially pop open.
If the tank pressure is above the blanketing valve set point, then the blanketing valve
should seal immediately. Otherwise the valve will open and flow until the tank pressure rises
above the set point. If the blanketing valve does not reseal at all, consult “Troubleshooting”
on page 21.

Shut-Down
Purpose & Frequency
Leakage Check
Disassembly &
Inspection
The blanketing valve must be depressurized when removing it from operation. Follow the
steps below for system shut-down:
1. Close the shut-off valve in the blanketing gas supply line.
2. Close the shut-off valve in the sense line.
3. Pressure between the supply line shut-off and the seals inside the blanketing valve
must be bled off. If the set point pressure is above atmospheric pressure, then the
safest way to do this is to break the seal at the sense port of the blanketing valve.
This will allow the pressure in the sense chamber to drop which will open the blanket-
ing valve and bleed off the internal pressure into the tank. If the blanketing valve has
a setting below atmospheric pressure, then a different method must be used. In addi-
tion to cracking the sense line, a connection between the supply line shut-off valve
and the blanketing valve inlet port must be cracked to allow the high pressure gas to
bleed out. The connection should be cracked slowly so that the high pressure gas
bleeds, not bursts, out.
4. Close the shut-off valve in the outlet line.
5. Remove the supply line to the blanketing valve carefully in case there is still trapped
pressure in the line.
Periodic maintenance checks are recommended to ensure that the blanketing valve is in
good operating condition. Debris in the valve or damaged seals are the most likely caus
es of
operating problems. The frequency of routine maintenance necessary for the blanketing
valve will depend on the severity of the operating conditions. The valve should be checked
within a month of installation and then as determined appropriate after that. At minimum,
the valve should be checked annually.
Before performing any disassembly, it is a good idea to check for external leakage. This can
be done by spraying or brushing soap around mating connections and bolts. If no leakage
is detected around the #12 gasket or the #15 gasket (See Fig. 4), then it should not be
necessary to disassemble the diaphragm case while performing routine maintenance.
The following instructions are for maintenance of the standard components of the blanket-
ing valve. Refer to the section entitled “Accessory Equipment” for instructions regarding
optional accessories. Also, the diagrams in this section show a unit with standard 1⁄2" FNPT
inlet and outlet connections. Except where noted, these instructions apply also to units with
other inlet and outlet connections.
Protectoseal O-rings and gaskets are available from Protectoseal. See Table 6 on page 09
for soft goods kits which can be ordered.
CAUTION: The blanketing valve must be completely depressurized before any disassembly
is performed. See the “shut-down” instructions above.
PROTECTOSEAL SERIES O. 30
TA K BLA KETI G VALVE
Installation/Maintenance Guide
Page 3
MAI TE A CE

PROTECTOSEAL SERIES O. 30
TA K BLA KETI G VALVE
Installation & Maintenance Guide
Page 4
■ DIAPHRA M CASE (See Fig. 4)
Remove the eight (8), #11 bolts, #13 nuts, and #4 lock washers. Carefully pull up the
upper case assembly. Reach under the case to hold the #6 set spring in position while
pulling the case up so that the spring and the #5 upper anchor do not fall over. The #9
diaphragm assembly and the #12 gasket can now be removed and checked. If there is any
corrosion or damage to the gasket, it must be replaced.
Looking at the diaphragm assembly, the two (2), #21 plates should be clamped flat
against the #22 diaphragm, and the diaphragm should be free of cracks, cuts or holes.
See Fig. 5 for disassembly of the diaphragm assembly. Unthread the #24 stop (machined
hex screw) from the #19 lower anchor. Note: This connection may be very tight due to
thread adhesive being applied during assembly. The diaphragm and the #23 gasket should
be free of cracks, cuts or holes. To remove the #14 lower case, remove the four (4), #7
hex screws. This exposes the #15 gasket which can then be inspected for corrosion or
damage.
■ MAIN VALVE (See Fig. 6)
Position the blanketing valve so that the inlet points downward.
Refer to Fig. 6 before removing the #33 lower plug assembly. Identify the marks on the nut
of the lower plug assembly and the bottom of the valve body. These marks, which should be
lined up with each other, identify the proper position of the lower plug. This plug position is
set at the factory for optimal performance of the blanketing valve. If the marks are not easy
to see, then additional marks to identify the position during reassembly (with a felt tip pen
for example) should be made on the nut and the pilot body before unscrewing the lower
plug. Unscrew and remove the #33 lower plug assembly. When the plug is removed, the
#30 poppet and attached parts will come out with it. Be careful not to damage the fine
threads on the lower plug after removal. Set the body aside.
rasping the lower plug assembly in one hand and the poppet in the other, firmly tug on
the poppet to pull it out of the lower plug assembly. Be certain to do this in a slow, con-
trolled manner so that the #31 poppet spring and the #32 spring pin do not fly out and
get lost.
If the #14 lower diaphragm case has been removed, the #26 upper plug can be removed.
The best way to do this is to slowly insert a phillips-head screwdriver into the bottom of the
small hole in the upper plug and tap on it to push the plug out. Be very careful not to dam-
age the inside bottom of the upper plug where the #28 O-ring seats. The O-rings can now
be inspected for corrosion or wear.

PROTECTOSEAL SERIES O. 30
TA K BLA KETI G VALVE
Installation & Maintenance Guide
Page 5
When reassembling the blanketing valve, be sure to replace any worn or damaged O-rings
and gaskets.
■ MAIN VALVE (See Fig. 6)
Before reassembling the main valve, the #28 and #29 O-rings should be lubricated with
an appropriate lubricant. Reinsert all six O-rings in their proper positions. It is recommend-
ed that a conservative amount of anti-seize compound be applied to the fine threads of the
lower plug before it is threaded back into the valve body. Hold the #30 poppet upside
down, insert the #31 poppet spring in the recess in the end of the poppet, and insert the
#32 spring pin into the spring. Slide the #33 lower plug assembly over the spring pin,
spring and poppet and pop it into place. The poppet should move easily up and down
inside the lower plug, being pushed up by the poppet spring. If it has been removed, push
the #26 upper plug back into the #34 valve body. The orientation of the cross holes in the
upper plug is not important. Slowly, being careful not to damage the end of the stem on the
poppet or the seat at the bottom of the upper plug, insert the lower plug/poppet assembly
into the valve body. Thread the lower plug into the body until the nut is seated against the
valve body and the marks on nut and body line up.
Reassembly
■ DIAPHRA M CASE (See Fig. 4)
With the blanketing valve body upright, place the #15 gasket on top of the body. Place the
#14 lower case over the gasket and secure it with four (4), #7 hex screws and #8 lock
washers, tightening to 96 in-lbs. If the #9 diaphragm assembly has been disassembled,
then reassemble it as shown in Fig. 5. Apply thread adhesive to the thread connection and
tighten until lock washer and plates are compressed.
Place the #9 diaphragm assembly on the lower
case. Place the #12 gasket over the diaphragm
and line up the bolt holes. Place the #6 set
spring over the #19 lower anchor of the
diaphragm assembly and insert the #5 upper
anchor in the top of the spring. While holding the
spring upright with one hand, slide the #10
upper case assembly until it rests on top of the
diaphragm. Line up the bolt holes, insert the
eight (8), hex screws, lock washers, and nuts and
tighten to 96 in-lbs. Tighten the hex screws in the
order as shown in Fig. 3. Fig. 3
Reinstallation & System
Check
Follow the installation and start-up instructions on page 2 to reinstall the blanketing valve
after maintenance. After reinstalling the blanketing valve, a soap test should be performed
again. If leakage is detected, then the point of leakage should be noted, and the valve
should be disassembled as appropriate to identify the gasket or O-ring past which the leak
is occurring.
If the blanketing valve flows continuously and does not seal after start-up, then the system
should be shut down so that the problem can be identified. See the section “troubleshoot-
ing” on page 23 for possible problem sources. Any time that a blanketing valve is disas-
sembled and reassembled, its operation should be monitored for a period afterward.

PROTECTOSEAL SERIES O. 30
TA K BLA KETI G VALVE
Installation & Maintenance Guide
Page 6
Fig. 4
Blanketing Valve
#
1
2
3
4
5
6
7
8
9
10
Qty.
1
1
1
9
1
1
8
8
1
1
#
11
12
13
14
15
16
17
18
Qty.
8
1
8
1
1
1
1
1
Part No.
-
20-18C-*
-
-
20-18D-*
-
-
20-18E-*
Description
Cap
Set Screw
Jam Nut, 3⁄8- 24 UNF
Lock Washer, 3⁄8"
Upper Anchor
Set Spring
Hex Screw, 1⁄4- 20 UNC x 1⁄2
Lock Washer, 1⁄4"
Diaphragm Assembly (Fig. 5)
Upper Case Assembly
Description
Hex Screw, 3⁄8- 16 UNC x 3⁄4
asket
Jam Nut, 3⁄8- 16 UNC
Lower Case
asket
Main Valve (Fig. 6)
Flow Plug
asket
* Suffix for the material code, see Table 5 on page 9.

PROTECTOSEAL SERIES O. 30
TA K BLA KETI G VALVE
Installation & Maintenance Guide
Page 7
Fig. 5
Diaphragm Assembly
(Item #9)
#
19
20
21
22
23
24
Qty.
1
1
2
1
1
1
Part No.
-
-
-
-
20-18A-107
20-18B-107
-
Description
Lower Anchor
Lock Washer 1⁄4"
Plate
Diaphragm
asket
Stop

PROTECTOSEAL SERIES O. 30
TA K BLA KETI G VALVE
Installation & Maintenance Guide
Page 8
Fig. 6
Main Valve Assembly
(Item #16)
#
25
26
27
28
29
30
31
32
33
34
35
Qty.
2
1
2
1
1
1
1
1
1
1
1
Part No.
20-R115-*
✢
20-R118-*
20--R109-*
20-R112-*
✢
-
-
✢
✢
-
-
Description
O-Ring
Upper Plug
O-Ring
O-Ring
O-Ring
Poppet
Poppet Spring
Spring Pin
Lower Plug Assembly
Valve Body
Flow Plug
* Suffix for the material code, see Table 5 on page 9.
✢ These parts must be replaced as a set.

Part No.
20-R109-†
20-R112-†
20-R115-†
20-R118-†
Cross Section Dia.
.103
.103
.103
.103
I.D.
.299
.487
.674
.862
PROTECTOSEAL SERIES O. 30
TA K BLA KETI G VALVE
Installation & Maintenance Guide
Page 9
Table 5
O-Ring & Gasket Codes &
Suffixes
Table 6
Soft Goods Kits
Table 7
O-Ring Sizes
Model No. Code*
A
B
C
D
E
F
Material
Buna-N
Neoprene
Viton®
EPDM
Kalrez®**
Chemraz®**
Part No. Suffix (†)
-101
-100
-118
-136
-140
-138
† Suffix for the material code, see Table 5.
† Suffix for the material code, see Table 5.
* Digit #7 of part number.
** On units with Kalrez or Chemraz seals & gaskets, the diaphragm case gasket will be Buna-N.
Note: For all soft goods options, #36 Stem Seal (Fig. 6) will be FEP coated Buna-N.
Kit Part No.
30-S K1-†
30-S K2-†
Contents
All O-rings, askets, & Diaphragms
All O-rings
Table 8
Supply Line Filter
Replacement Elements
Part No.
30-250FE-300
30-252FE-300
For Type
Aluminun/Zinc (40 Micron)
SS 316 (40 Micron)

PROTECTOSEAL SERIES O. 20
TA K BLA KETI G VALVE
PROTECTOSEAL SERIES O. 30
TA K BLA KETI G VALVE
Installation & Maintenance Guide
Page 10
Fig. 7
Recommended Test
Set-Up

PROTECTOSEAL SERIES O. 30
TA K BLA KETI G VALVE
Installation & Maintenance Guide
Page 11
Filter
ACCESSORIES
Fig. 8
Pilot Filter
■ FUNCTION
The optional supply line filter, with a 40 micron element, serves to keep any unwanted par-
ticles out of the blanketing valve flow stream. Particulate matter entering the valve can
result in clogging of the flow passages and/or damage to the valve’s seals. The blanketing
valve should not be mounted in a supply line that does not include an effective filtering
device.
■ MAINTENANCE
The following maintenance guidelines apply to a supply line filter that has been purchased
as an option from The Protectoseal Company. If your system includes some other supply
line filter, please contact the manufacturer of the filter for maintenance recommendations.
Condensate may be drained from the bowl of the filter (See Fig. 8) by turning the drain
cock (serrated knob on the bottom of the bowl). Note: It is possible to drain condensate
from the bowl while the system is pressurized, but care must be taken in that the fluid will
be expelled under a pressure equal to the supply line pressure of the system (typically 10
PSI - 200 PSI ) for the blanketing valve application. CAUTION: DO NOT unscrew the bowl
of the filter while the system is pressurized. After the supply line has been depressurized,
the filter can be cleaned as follows:
1. Make sure that the supply line has been depressurized.
2. Unscrew the bowl of the filter. The bowl may be cleaned with a mild household deter-
gent (do not use solvents or other such industrial cleaning agents).
3. Unscrew the filter element. Check the element for excessive blockage or visible holes.
Damaged elements should be replaced immediately.
4. Reassemble the filter element and bowl. Make sure that the bowl is attached securely
so that any seals are properly compressed. Make sure that the drain cock is com-
pletely closed.

PROTECTOSEAL SERIES O. 30
TA K BLA KETI G VALVE
Installation & Maintenance Guide
Page 12
Pressure Gauges ■ FUNCTION
Optional pressure gauges may be included which enable system pressure monitoring. The
supply line pressure gauge will show the blanketing gas supply pressure at the inlet to and
inside of the blanketing valve. The sense line pressure gauge will show the tank pressure
being sensed by the blanketing valve through the sense line.
■ MAINTENANCE
When the blanketing valve has been completely depressurized, gauges may be removed for
calibration checks. Replacement gauges can be ordered if necessary. The sense line gauge
supplied by Protectoseal has a working pressure of up to 15 psig and so should not be
damaged by fluctuations in tank pressure. Damage to the supply pressure gauge may indi-
cate that the blanketing gas supply system was overpressurized at some point. Excessive
supply pressure can cause blanketing valve failure and should be immediately investigated.
Fig. 9
Pressure auges
Integral Purge
Accessories
■ FUNCTION
The integral purge is used to create a small flow of blanketing gas at the blanketing valve
outlet and/or the sense line connection in order to keep vapors from the material stored in
the tank from corroding the blanketing valve. Due to the blanketing valve’s stainless steel
316 construction, the availability of chemically resistant soft goods, and the high concentra-
tion of blanketing gas present in the blanketing valve, the integral purge should not be nec-
essary except in very severe service conditions. Both the blanketing valve

Fig. 10
Integral Purge System with Outlet & Sense Line Purges
PROTECTOSEAL SERIES O. 30
TA K BLA KETI G VALVE
Installation & Maintenance Guide
Page 13
outlet, and to a much lesser extent, the sense line will be purged with blanketing gas any
time that the blanketing valve opens. The integral purge, however, flows continuously and
also lessens the existence of standing vapors from the stored material when the blanketing
valve is closed.
■ OPERATION
The integral purge system uses the blanketing gas supply to create a trickle of flow at the
outlet port and/or sense port. The purge meter (See Fig. 10) is used to control the flow
going to either of these locations. A recommended flow through the meter is 0.5 SCFH.
Flows higher than about 1.0 SCFH past the sense port are not recommended because they
can create an artificially high pressure at the sense port leading to the valve opening at a
tank pressure lower than the set point. If the purge is only to the outlet line, then

Temp.
(°F)
0
20
40
60
70
80
100
120
Temp.
(°C)
-18
-7
4
16
21
27
38
49
F3
0.932
0.952
0.971
0.991
1.000
1.009
1.028
1.046
higher flows create only the problem of high supply gas usage.
The purge meter has a percent scale. The flow indicated will depend upon the blanketing
gas supply pressure, the molecular weight of the blanketing gas, and (to a lesser degree)
the operating temperature. See the below tables to determine the flows through the purge
meter as follows:
Scale Reading for a Desired Flow:
Scale Reading {%} = (Desired Flow {SCFH} x 125 x F1 x F2 x F3)
Flow Indicated at a Scale Reading:
Flow {SCFH} = (Scale Reading {%} / (125 x F1 x F2 x F3)
PROTECTOSEAL SERIES O. 30
TA K BLA KETI G VALVE
Installation & Maintenance Guide
Page 14
Supply Pressure
(PSI )
20
30
40
50
60
70
80
90
100
110
120
130
140
150
160
170
180
190
200
F1
0.651
0.573
0.518
0.477
0.444
0.417
0.394
0.375
0.358
0.343
0.330
0.319
0.308
0.299
0.290
0.282
0.275
0.268
0.262
as
Air
Carbon Dioxide
Helium
Natural as
Nitrogen
F2
1.00
1.238
0.372
0.775
0.982
Table 10
Molecular Weight Factor (F2)
Table 11
Temperature Factor (F3)
Table 9
Supply Pressure Factor (F1)
■ MAINTENANCE
The integral purge accessories should not normally require maintenance. When the blanket-
ing valve has been removed for maintenance, the purge meter or purge system can be
checked for blockage by hooking up a pressure line to the inlet of the purge meter (the
bottom connection) and checking for flow at the outlet(s).
Since the blanketing gas should be clean, the purge meter should not usually require clean-
ing. However, if it is desired to do so, follow these steps:
1. Squeeze the clear plastic shield to unsnap it from the retainer.
2. Remove the glass tube by pushing it up (against the compression spring) and pulling
it out.

3. Use tweezers to pull the float stop out from the top of the tube and then carefully tilt
the tube to remove the float. Handle the float with care to avoid nicking or scratch
ing it.
4. Clean the tube and float with mild detergent and water or with a suitable solvent. Use
a soft cloth or tube brush to clean the meter tube. Do not expose the tube or float to
extreme temperature changes.
5. The shield may be cleaned with detergent and water or with kerosine. If kerosine is
used, follow up cleaning with detergent and water.
6. Reassemble in the reverse order of disassembly.
Units which have an outlet line purge will include one or more check valves which prevent
back flow from the outlet when the blanketing valve opens. The blanketing valve will not
function without these check valves. If it is desired to inspect these check valves, refer to
the paragraph on check valve maintenance. Be certain to note the direction of the arrows
on the check valves before removing them so that they will be reinstalled properly (the
arrows should point away from the purge meter as shown in Fig. 10.).
PROTECTOSEAL SERIES O. 30
TA K BLA KETI G VALVE
Installation & Maintenance Guide
Page 15
Field Test Accessories ■ FUNCTION
The field test accessories make it possible to check the opening pressure of the valve in
the field. Through a series of valves and a regulator, the blanketing gas supply is regulated
down and directed into the sense chamber of the blanketing valve. A vacuum pump is also
used in the low pressure / vacuum set point version in order to lower the pressure suffi-
ciently. By lowering and raising this regulated pressure, the opening and closing point of
the blanketing valve can be determined. Both the supply pressure gauge and the sense
pressure gauge are included with the field test accessories.
Optional additional accessories are a 3-way valve for the outlet line and/or shut-off valve
for the sense line. The 3-way valve makes it possible to divert outlet flow away from the
tank if the blanketing valve is field tested while connected to the system. The auxiliary outlet
port of the 3-way valve can either be connected to a collector or open directly to atmo-
sphere. The sense line shut-off valve is used to isolate the sense chamber while conducting
a field test. It provides easy accessibility if the valve is field tested while connected to the
tank. It also provides a quick means of sealing off the sense port if the valve is removed
from the tank for testing.
■ SET-UP
If the unit has been removed from the system:
1. Seal off the sense port by closing the sense line shut-off valve or inserting a pipe
plug.
2. Position the outlet of the valve so that the high pressure flow can exhaust safely. The
blanketing valve should be held securely by clamping or other means.
3. Connect a line from a pressure source to the valve inlet. The minimum restriction in
this line should be a 1⁄2" pipe size diameter. The pressure source must be of sufficient
capacity to open the blanketing valve fully, otherwise the valve will not operate consis-
tently. Where possible, the inlet supply pressure should be equivalent to the blanket-
ing gas supply pressure.
If the unit is still connected in the system:
1. Shut-off the blanketing gas supply to the inlet port.
2. Isolate the sense port from the tank by closing the sense line shut-off valve.

PROTECTOSEAL SERIES O. 30
TA K BLA KETI G VALVE
Installation & Maintenance Guide
Page 16
03. If the unit has a 3-way valve, turn the handle on the valve approximately 180° to
close off the path to the tank and open up the blanketing valve outlet to the auxiliary
port.
04. If the unit does not have a 3-way valve, you must leave the outlet line open and
exhaust the blanketing valve into the tank. CAUTION: Exhausting into the tank while
running a field test may cause the tank’s pressure relief vents to open.
NOTES RE ARDIN THE SET POINT AND VALVE OPERATION:
01. The set point of the Protectoseal Series 30 Blanketing Valve is specified as the pres-
sure at which the main valve opens.
02. The opening of the main valve will be audible. Flow through the valve will increase as
the sensed pressure is reduced below the set point.
03. The main valve reseals above the pressure at which it opens.
■ TESTIN - HI HER PRESSURE SET POINT KIT
If the unit has set point range B, C, or D (as indicated by digit 6 of the model number)
(above 3.0 to 69.2 inches W.C.) then this section applies. If the unit has a set point range
of A, then proceed to the next section entitled “Testing - Low Pressure or Vacuum Set
Point”.
Follow these steps to determine the opening and resealing points (See Fig. 11):
01. Connect the test kit as shown at connection #1 and connection #2 (if it is not already
attached). If the blanketing valve includes the integral purge option, the purge meter
should be shut before using the field test unit.
02. Pull up the handle on the regulator to unlock it and turn the handle all the way
counter-clockwise. This minimizes the outlet pressure of the regulator so that the reg-
ulator pressure gauge will not be damaged when inlet pressure is applied.
03. Turn the knobs on the needle valve and the bleed valve clockwise to close them.
04. Open shut-off valve #2 (at the hose end of the test kit).
05. CAUTION: Put on ear protection. The flow out of the valve can be extremely loud.
06. Pressurize the inlet to the blanketing valve.
07. Slowly open shut-off valve #1 (at the inlet of the test kit).
08. Turn the handle on the regulator clockwise to increase the outlet pressure until the
regulator gauge reads approximately 13 PSI .
09. Slowly open the needle valve to pressurize the sense line. Bring the pressure up
above the set point (as indicated by the sense line pressure gauge).
10. Lower the sensed pressure by adjusting the knobs on the bleed valve, the needle
valve and the regulator.
11. Note: If the blanketing valve has been removed from the system, then pressure in the
sense chamber will bleed to atmosphere through the outlet port. Thus, there will not
be a tight system and some gas must be continually bled in through the test kit in
order to maintain the pressure at the sense port.
12. Cycle the sensed pressure up and down to determine the opening pressures. If the
blanketing valve is not opening at the set point, CONSULT THE FACTORY FOR
ASSISTANCE.
13. If other problems are experienced, refer to the troubleshooting guide. Double check
your set-up and test procedures before attempting to fix any other problems.

PROTECTOSEAL SERIES O. 30
TA K BLA KETI G VALVE
Installation & Maintenance Guide
Page 17
■ TESTIN - LOW PRESSURE OR VACUUM SET POINT TEST KIT
If the unit has set point range A (-0.1 to 3.0 inches W.C.), then this section applies. Follow
these steps to determine the blanketing valve’s opening and resealing points (See Fig. 12).
01. Pull up the handle on the regulator to unlock it and turn the handle all the way
counter-clockwise. This minimizes the outlet pressure of the regulator so that the reg-
ulator pressure gauge or the sense line gauge will not be damaged when inlet pres-
sure is applied.
02. Turn the knob on the stem valve clockwise to close it.
03. Open shut-off valve #2 (at the hose end of the test kit).
04. CAUTION: Put on ear protection. The flow out of the valve can be extremely loud.
05. Pressurize the inlet to the blanketing valve.
06. Slowly open shut-off valve #1 (at the inlet of the test kit).
07. Turn the handle on the regulator clockwise to increase the outlet pressure until the
regulator gauge reads 13 to 14 PSI . (NOTE: Do not pressurize above 15 PSI . Doing
so could damage the sense line pressure gauge which is rated at 15 PSI maximum.)
08. Lower the sensed pressure by turning the knob to open the stem valve. NOTE: Due to
the small volume of the field test kit which controls the sense pressure, the blanketing
valve may chatter near the set point. For very low and negative pressure set points
the stem valve is opened to establish a flow pattern through the vacuum venturi tube
and extract air (decrease pressure) in the valve’s sense chamber.
09. Cycle the sensed pressure up and down to determine the opening pressures.
10. If the blanketing valve is not opening at the set point, CONSULT THE FACTORY FOR
ASSISTANCE.
If other problems are experienced, refer to the troubleshooting section. Double check your
set-up and test procedure before attempting to fix any other problems.
■ AFTER TESTIN
To depressurize the blanketing valve and test kit, shut off the inlet supply while the valve is
flowing. Check that the pressure indicated on the sense line gauge is zero. Close shut-off
valve #1 and shut-off valve #2. Disconnect the test kit at connection #1 and connection
#2, if desired.
If the unit has been removed from the system:
01. Open the sense line shut-off valve or remove the pipe plug from the sense port.
02. Disconnect the line from the pressure source.
03. Follow the installation and start-up instructions to reinstall the blanketing valve.
Table of contents
Other Protectoseal Control Unit manuals
Popular Control Unit manuals by other brands
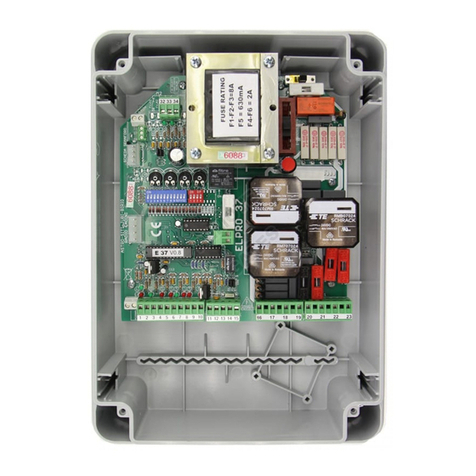
fadini
fadini Elpro 37 manual
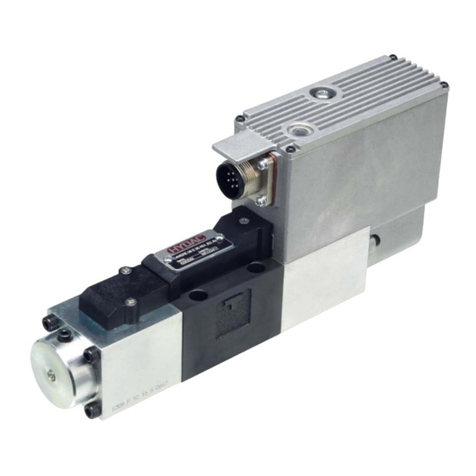
HYDAC International
HYDAC International C4WERE 6 instruction manual

urmet domus
urmet domus ALPHA 1168/50 installation manual
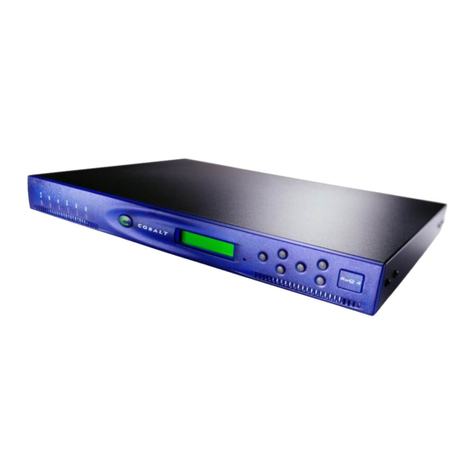
Sun Microsystems
Sun Microsystems Sun Cobalt Control Station Maintaining and Upgrading the Hardware
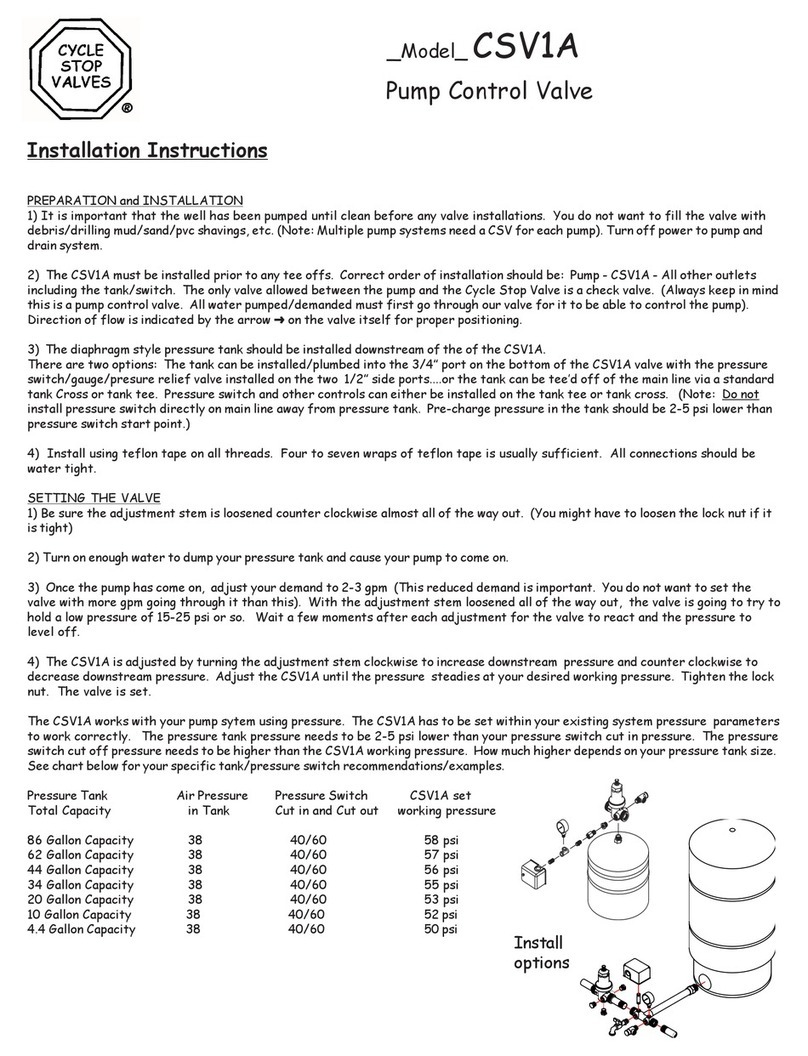
Cycle Stop Valves
Cycle Stop Valves CSV1A installation instructions
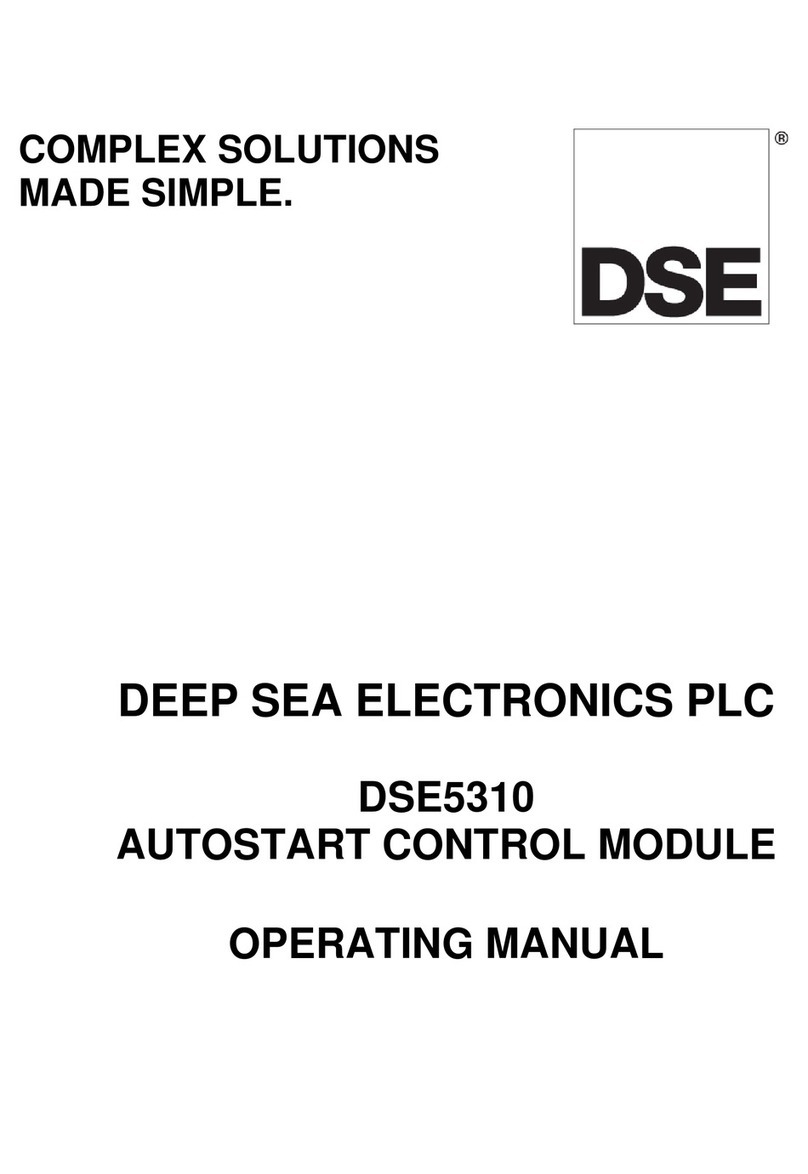
Deep Sea Electronics Plc
Deep Sea Electronics Plc DSE5310 operating manual