White International Icon Series User manual

ICON SERIES ISUB
Intelligent Constant Pressure
Water Supply Controller User Manual

PREFACE
Thank you for choosing ICON ISUB, which is designed to enhance the performance of ICON series
submersible bore hole pumps up to 2.2 kW, 240V 3ph.
The ICON ISUB eliminates the requirement for large pressure tanks and pressure switches used for
automatic operation as well as associated pressure cycling.
Professional design based on users’ needs, simplicity of operation and suitable for all kinds of
applications.
According to the water condition to supply constant pressure water without manual operation after
parameters are set correctly.
Stop running automatically when there is no water consumption and Alarm automatically when faults
occur.
Features:
Constant water pressure.
Optimises pump performance.
Soft start, low motor start current.
No large pressure tank required.
Protection:
Dry run protection.
High and low voltage protection.
Input and output short circuit protection.
High and low water pressure protection.
Input and output phase failure protection.
Over temperature protection.
Sensor fault protection.
Conformity:
Verification of EMC compliance certificate no. AC/0410709 to EN 61326-1:2006,
EN 61000-3-2:2005, EN 61000-3-3:1995+A1:2001+A2:2005.
Verification of LVD compliance certificate no. AC/0420709 to EN 61010-1:2001.

List of contents:
A. Pump controller in cabinet with fan and circuit breaker.
B. Stainless steel manifold.
C. Pressure transducer 0 - 1 mPa, 4 –20 mA with 2 metre lead.
D. Pressure gauge 0 –1 mPa.
E. Installation manual.
Supplied separately as part of ISUB Borehole Pump Kit:
F. DAB Borehole Pump, with up to 2.2 kW 3ph 240V motor.
G. GWS 18 litre pressure tank.

SAFETY PRECAUTIONS
ISUB is a new power electronic product, please read the operation manual carefully before using to keep
your safety and make sure proper operation.
In this manual, the safety precautions were sorted to “WARNING” and “CAUTION”.
!WARNING: Incorrect use may result in death or serious personal injury.
!CAUTION: Incorrect use may result in the damage of controller or system.
!WARNING
Do not dismantle or change the product, which may cause electric shock, fire hazard and personal injury.
Do not open the cover during the running of controller. Disconnect power and allow 5 minutes for the
internal capacitors to discharge dangerous internal voltage before working on controller and pump.
Ensure that the controller along with the pump as well as metal in proximity are adequately earthed.
Do not put wire, metal bar, filaments etc. into the controller as to cause a short circuit or get an electric
shock.
Do not splash water or other liquid over the controller.
!CAUTION
The controller and pump should be installed by suitably qualified technical personnel, and failure to
install in compliance with local standards may result in poor performance, equipment damage, fire and
electrical shock.
Do not perform high voltage insulation testing on the controller.
Never connect AC power to output UVW terminals.
The motor, controller and power specifications should be matching, otherwise it could cause abnormal
operation and damage the equipment.
If the controller has serious vibration, noise, heat or peculiar smell in the first operation, please cut off
the power immediately and contact customer service.
Do not install the controller in an environment with direct sunlight, rain, dust, frost or snow.
Warm reminder:
For convenience, the controller has set default with a nonzero AI1 Feedback Lost Detecting Value. If there
hasn’t been a pressure signal feedback into the terminal AI1, the controller will start up with failure and
display “E022”.
◇If the controller is a master, please connect a transducer to the controller and then press the STOP/RST
key;
◇If the controller is an auxiliary, it should be set as AI1 Feedback Lost Detecting Value (b02.08) 0 and then
press the STOP/RST key to reset error warning.


Power Symbol 010: 10HP/7.5KW
Voltage Class 2: 240VAC 4: 415VAC
Series Number of Intelligent Constant Water Supply Controller
B603 series IP21 0.75 –350 kW
B603B series IP54 0.75 –7.5 kW
1. GENERAL
1.1 Technology Features
●Input & Output
◆Input Voltage Range:240/415V±15%
◆Input Frequency Range:47~63Hz
◆Output Voltage Range:0~rated input voltage
◆Output Frequency Range:0~50/60Hz
◆Digital Switch Input:3 input
◆Analogue Signal Input:AI1:0~10V or 0~20mA input; AI2: 0~10V or 0~20mA input
◆Relay Output:A pair of switch Output
●Function Characteristics
◆Multi-Pump Control:Can realize 1 master and Max. 5 auxiliaries to combine work
◆Sleep Function:Sleep down when there is no water consumption, to earn a better energy saving
◆Freeze-Proofing Function:Suitable to low temperature area, prevent pump from freezing
◆Anti-clogging Function:take precaution against pipe clogging and clean the pipe dirt
◆Power On Restart:Running automatically when power on
◆Master Fault Shift Automatically:keep on working when the master is not working
◆Alternate Running:balance every pump’s running time, prolong service life of the whole unit machine
◆Day-Part Function:3 independent day-part control, up to 7 day-part achieved when define separated
◆Two Running Mode:synchronous control mode, master-slave control mode
◆Terminal Control Mode:Terminal Run/Stop、Manual/Auto Control、Electronic Contact Gauge Control
◆Various of water supply Fault Alarm Function: High-Pressure, Low-Pressure, Low-Level, Transducer Error etc.
◆As many as 22 kinds of fault protection function: Over-Current, Over-Voltage, Low-Voltage, Phase-Failure,
Over-Load etc.
1.2 Description of Name Plate

3. ENVIRONMENTAL REQUIREMENT
3.1 Environment temperature range: -10℃~+40℃. Controller will be derated if ambient temperature exceeds
40℃.
3.2 Prevent rain drops, moist environment, oil fog, salt erosion, corrosive gas, etc.
3.3 Prevent direct sunlight, keep away from radiation source.
3.4 Prevent violent vibration or sudden impact.
3.5 Lower than 1000m installation altitude, it will be derated when the altitude is higher than 1000m.
CAUTION
When moving the controller please lift by its base and don’t lift by the panel. Otherwise may
cause the main unit fall off which may result in personal injury.
Install the controller on the fireproofing material (such as metal) to prevent fire.
When power off, should not install the controller until the power indicator light was
extinguished, which can ensure the device has been discharged completely.

4. WIRING
Figure 4-1- 1 wiring diagram
In order to keep safety and prevent electric shock and fire, PE must be grounded with ground resistance.
Ground wire should be big and short, and it is better to use copper wire (>3.5
2
mm
). Furthermore, reliable
grounding is the simplest, most effective and minimum cost solution for EMC problems, so it enjoys priority in
all EMC methods.

5. OPERATION
5.1 Keypad Description
Figure5.1 Keypad schematic diagram
5.2 Operation Procedure
5.2.1Power-on initialization
Firstly the system initializes during the controller power-on, and LED displays “b-603”. After the
initialization is completed, the controller is on stand-by status.
5.2.2 Parameter setting Three levels of menu are:1. Function code group (first-level); 2. Function code
(second-level); 3. Function code setting value (third-level)
▲At the primary interface, press <</SHIFT or >>/SHIFT will switchover display running/stop status
monitoring parameters;
▲At the primary interface, press PRG/ESC will enter the first-level menu then press PRG/ESC will return to
the primary interface;
▲At the first-level menu, press DATA/ENT will enter the second-level menu. In second-level menu can also
press PRG/ESC and DATA/ENT return to first-level menu or enter third-level menu;
▲At third-level menu, press both PRG/ESC and DATA/ENT can return to the second-level menu, difference
is: pressing DATA/ENT will save the parameters into the controller and return to the second-level menu
with shifting to the next function code automatically; while pressing PRG/ESC will directly return to the
second-level menu without saving the parameters, and keep staying at the current function code.
Example 1: Change factory pressure setting 3.0 bar to 2.5 bar Method 1:Enter parameter setting

Operation flow chart:
Figure 5-2-1 Operation Flow Chart
Method 2: Direct setting at the primary interface
Press △or ▽at primary interface, the system will switch over to display setting pressure, press △or ▽
again, the setting pressure increase/decrease, mean while the system trace the setting pressure. After
completing the pressure setting, please press DATA/ENT to save the value.
Example 2: During the running of controller, press <</SHIFT or >>/SHIFT to scroll through the parameters
in left or right order until there are two upper lights on, can check the feedback pressure value.
6. INSTRUCTIONS OF PARAMETERS GROUP
Function
Code
Name
Setting Range
Factory
Setting
Description
Br00 Group Application Function
b00.00
Debugging password
0~65535
65535
Decide by b06.09, default is 65535.
b00.01
Pressure setting value
0.0~100.0
3.0bar
Set according to the actual requirements
of user
b00.02
Motor Rotating
direction
0~1
0
0: forward 1: reverse
b00.03
Freeze- proofing
0~1
0
Used in cold areas 0: invalid 1: valid
b00.04
Anti-clogging
0~1
0
Prevention measures 0: invalid 1: valid

Function
Code
Name
Setting Range
Factory
Setting
Description
b00.05
Anti-clogging Rotating
cycle
1.0~300.0s
20.0
Set the forward/reverse rotating direction
cycle and corresponding output
frequency (should not be higher than the
rated frequency of the pump )
b00.06
Anti-clogging Output
frequency
0.00~600.00 Hz
15.00Hz
Br01 Group Application Function
b01.00
High Water
Pressure/Level Alarm
Value
0.0~100.0 bar
8.0bar
When pressure is higher than this preset
value, the controller halts, alarms and
displays HP.
b01.01
Low Water
Pressure/Level Alarm
Value
0.0~100.0 bar
0.5bar
When pressure is lower than the preset
value for a Low Pressure Running Time,
the controller halts,alarms and displays
LP.
b01.02
Low Pressure/Level
Running Time
0~300s
20s
b01.03
Minimum Freeze-
proofing Frequency
1.00~30.00Hz
5.00Hz
Be valid when b00.03 was set to 1,
whenever sleeps, running with the setting
frequency in case of Freezing.
b01.04
Anti-clogging
FWD./REV. Dead Time
0.0~3600.0s
1.0s
When anti-clogging is valid, b01.04 set
the FWD./REV. transition time
b01.05
Maximum Transducer
Setting Range
0.0~100.0 bar
10.0
E.g. If the rated max. range of transducer
is 10Bar, b01.05 should be set to 10.0
b01.06
AI1 Lower Limit
0.00~10.00V
1.00V
•Lower limit use to Transducer Zero
Setting
•Higher limit use to accordant display and
transducer pressure. •When display
smaller than gauge, increase higher limit;
When display greater than gauge,
decrease higher limit.
•When analog input is interfered, prolong
Filtering time so as to increase the ability
of anti-interference, but decrease the
sensitivity.
•Corresponding relationship of
Transducer Parameter Setting:
Figure6-1-1 Transducer Parameters
b01.06
AI1 Lower Limit
0.00~10.00V
1.00V
b01.07
Corresponding Setting
of AI1 Lower Limit
-100.0~100.0%
0.0%
b01.08
AI1 Higher Limit
0.00~10.00V
5.00V
b01.09
Corresponding Setting
of AI1 Higher Limit
-100.0~100.0%
100.0%
b01.10
AI1 Filtering time
0.00~10.00s
0.10s
b01.11
AI2 Lower Limit
0.00~10.00V
1.00V
b01.12
Corresponding Setting
of AI2 Lower Limit
-100.0~100.0%
0.0%
b01.13
AI2 Higher Limit
0.00~10.00V
5.00V
b01.14
Corresponding Setting
of AI2 Higher Limit
-100.0~100.0%
100.0%
•Lower limit use to Transducer Zero
Setting
•Higher limit use to accordant display
and transducer pressure.
•When display smaller than gauge,
increase higher limit;
*When display greater than gauge,
decrease higher limit.
•When analogue input is interfered,
prolong Filtering time so as to increase
the ability of anti-interference, but
decrease the sensitivity.
•Corresponding relationship of
Transducer Parameter Setting:

Function
Code
Name
Setting Range
Factory
Setting
Description
b01.15
AI2 Filtering time
0.00~10.00s
0.10s
b01.16
Restart After Power-
on
0~1
0
0:invalid 1:valid
b01.17
Control mode
0~1
1
0:synchronous 1:master-slave
Br02 Group Application Function
b02.00
PID Source Selection
0~1
0
0:Keypad 1:Reserved
b02.01
PID Feedback Source
Selection
0~1
0
0:AI1 1:Reserved
b02.02
PID Output
Characteristics
0~1
0
0:Water Supply 1:Pumping
b02.03
Proportional
Gain (Kp)
0.00~100.00
2.50
Determining the strength of PID
regulation, Kp is bigger, regulation is
stronger, but fluctuate easier too.
b02.04
Integral Time (Ti)
0.00~10.00
1.00s
Bias between the Feedback and the
Given, determining the speed of
regulation, a shorter Ti gains a stronger
regulation.
b02.05
Differential
Time (Td)
0.00~10.00
0.00s
Variable Ratio between the Feedback and
the Given, a longer Td gives a stronger
regulation. Be cautious use, for
differential regulation amplifies
interference of system.
b02.06
Sampling
Cycle (T)
0.01~100.00
0.10s
Calculating time of regulator, when
increased, response sluggishly.
b02.07
PID Control Bias Limit
0.0~100.0%
0.0%
Max. Bias of PID output value corresponding to
closed loop given value:
Figure6-2-1 PID control curve
Corresponding System Diagram of Max. Limit and
Output Frequency.
Properly set the value can regulate the accuracy and
stability of PID system.

Function
Code
Name
Setting Range
Factory
Setting
Description
b02.08
AI1 Feedback Lost
Detecting Value
0.0~100.0%
1.0%
Transducer Fault Detecting Setting Value,
corresponding to full range(100%), when
the detecting time exceeds Feedback Lost
time, it is deemed as malfunction by
Transducer, the system will report E022
as Transducer Fault Code
b02.09
AI2 Feedback Lost
Detecting Value
0.0~100.0%
0.0%
b02.10
Feedback Lost
Detecting time
0.0~3600.0s
1.0s
Br03 Group Application Function
b03.00
Communication
Address
0~31
02
00: Master controller
01~05:Auxiliary controller
06~31:Reserved
b03.01
Baud Rate Selection
0~5
3
Data of master and auxiliary comes into
the rate.
0:1200BPS 1:2400BPS
2:4800BPS 3:9600BPS
4:19200BPS 5:38400BPS
b03.02
Data Format
0~5
0
Data Format(Parity Check)
b03.03
Communication Delay
Time
0~200ms
15ms
Interval of Data responding.
b03.04
Communication
Timeout Delay 0.0:
invalid
0.0~100.0s
0.0s
If the interval time exceeds the setting
value, the system will report E018 as
fault.
b03.05
Communication Error
Action
0~1
0
0: Halt and alarm
1:Don’t alarm and continue
b03.06
Communication
Response Action
0~1
0
0: Responding to Write Operation
1: Un-responding to Writer Operation
b03.07
Data Transmission
Time Interval
0.05~2.00
0.10s
Ensure the effects of Data Transmission,
long-time setting will slow down Data
Transmission and short-time setting will
easily make mistakes.

Function
Code
Name
Setting Range
Factory
Setting
Description
b03.08
Auxiliary Quantity
0~5
0
0:none
b03.09
Fault Shift
0~2
2
Fault Master Shift
●Invalid: Factory Setting
●Valid: Master set as 0;
Axiliary1 set as 1.
Remarks: Fault Shift demands the
Axiliary1 to connect a backup transducer.
Br04 Group Application Function
b04.00
Sleeping Function
0~1
1
No consuming auto stop. 0:Invalid 1:Valid
b04.01
Sleeping Waiting time
0.0~300.0s
5.0s
Delay time, seconds unit
b04.02
Sleeping Test
0.0~10.0%
4.0%
Water consuming test frequency rate.
b04.03
Wake-up Pressure
Bias
0.0~20.0bar
0.5bar
During sleeping the wake-up pressure
bias, e.g. the setting value(L)=3.0Bar,
Bias(b04.03)=0.5bar, Practical pressure
(P)<L-0.5=2.5bar, the pump will restart
again.
b04.04
Sleeping Bias
0.0~1.0bar
0.0
The pressure fluctuation which allows
sleeping
Br05 Group Application Function
b05.00
Water Level Control
0~2
2
Water level switch style,
0:invalid 1:NC 2:NO
b05.01
Low Lever restart
Delay Time
0~300min
1min
Delay time of restart after water level
switch recover.
b05.02
Terminal S1S2 Control
0~3
2
0: invalid
1: Electric contact control
S1-COM on: Frequency rise
S2-COM on: Frequency drop
2: Manual/auto control
S2-COM off: auto control
S2-COM on: manual control
3: Terminal run/stop
S1-COM on: Run
S1-COM off: Stop
S2-COM off: auto control
S2-COM on: manual control

Function
Code
Name
Setting Range
Factory
Setting
Description
b05.03
Acceleration Time
0.1~3600.0s
Model Set
The setting time from max. Frequency to
zero.
b05.04
Deceleration Time
0.1~3600.0s
Model Set
The setting time from zero to max.
Frequency
b05.05
Maximum Output
Frequency
10.00~600.00Hz
50.00Hz
Determine the Acc./Dec. rate
b05.06
Up limit of Output
Frequency
b05.07~b05.05
(Maximum
Frequency)
50.00Hz
Maximum running frequency
b05.07
Lower Limit of Output
Frequency
0.00~b05.07Hz
20.00Hz
The minimum running frequency of
pump.
b05.08
Carrier Frequency
1.0~15.0kHz
Model Set
Use to ameliorate the noise of motor and
controller’s interference to the
surroundings.
A high carrier makes a low motor noise,
but leads to a big temperature rise and
interference.
Should not be altered if unnecessary.
b05.09
Low Pressure(LP)
Restart Delay Time
00~60min
10
In case of Low Pressure, BR5.09≠0, the
controller restarts to work according to
the setting time automatically, without
artificial restart. BR5.09=0, restart invalid.
b05.10
Alternating Time
0.00~300.00h
8.00h
In order to balance and prolong the pump
service life to set the parameter, Unit:
hour. When the parameter is set to 0.0, it
means in-execution. Operational time of
master and auxiliary pump switches over
according to the setting Alternating Time.
Br06 Group Application Function
b06.00
Running Status
Display Selection
0~0x1FF
0x01F
bit0: Operational Frequency
bit1: Pressure tested value
bit2: Pressure setting value
bit3: Output Current
bit4:Bus Voltage
bit5:Output Voltage
bit6:Present Time
bit7: Inlet Pump Pressure
bit8: Input Terminal Status
b06.01
Stop Status Display
Selection
0~0x1FF
0x00F
bit0: Pressure setting value
bit1: Pressure tested value
bit2: Giver Frequency
bit3: Bus Voltage
bit4: Input Terminal Status
bit5:Output Terminal Status

Function
Code
Name
Setting Range
Factory
Setting
Description
bit6:AI1 Input Voltage
bit7: Inlet Pump Pressure
bit8: Present Time
b06.02
Keypad Display
Selection
0~3
3
0:External Keypad Prior Enable
1:Both Display Enable, Only External
Keypad Control;
2:Both Display Enable, Only Onboard
Keypad Control;
3:Both Display Enable and Keypad
Control.
b06.03
Relay Output
Selection
0~4
0
0:Error or External Fault
1:Forward Running
2:Frequency Reaching
3:Stop Status
4:Lower Limit of Output Frequency
Reaching
b06.04
Third Latest Fault
Type
Read Only
E000~E022
Refers to chapter 9.
b06.05
Second Latest Fault
Type
b06.06
Latest Fault Type
b06.07
Parameters Storage
Condition
0~2
0
0:Power-off Storage
1:Power-off default storage
2:Invalid
b06.08
Accumulated Running
Time
0~65535h
Read Only
Display Accumulated Running Time
b06.09
Set the Password of
br00.00
0~65535
65535
Password set prevent user from
modifying the parameters randomly,
avoiding running abnormally and
damages.
Br07 Group Application Function
b07.00
Day-part Function
Selection
0~3
0
0:invalid
1:day-part A
2:day-part A and B
3:day-part A, B, C
b07.01
Day-part A Starting
Time
00.00~24.00
0
●Setting Starting Time and Finishing Time
to 0 is invalid.
●Pressure Setting determines the steady
state value of outlet pressure.
b07.02
Day-part A Pressure
Setting
0.0~20.0bar
3.0bar
b07.03
Day-part A Finishing
Time
00.00~24.00
0

Function
Code
Name
Setting Range
Factory
Setting
Description
b07.04
AI2 Lower Limit of
Day-part A
0.0~20bar
2.0bar
b07.05
Day-part B Starting
Time
00.00~24.00
0
●Once actual pressure from inlet pipe
network lower than inlet pressure lower
limit, the pump stops.
●When regardless of the inlet water
pressure, just set the lower limit as 0.
b07.06
Day-part B Pressure
Setting
0.0~20bar
3.0bar
b07.07
Day-part B Finishing
Time
00.00~24.00
0
b07.08
AI2 Lower Limit of
Day-part B
0.0~20.0bar
3.0bar
b07.09
Day-part C Starting
Time
00.00~24.00
0
b07.10
Day-part C Pressure
Setting
0.0~20.0bar
3.0bar
b07.11
Day-part C Finishing
Time
00.00~24.00
0
b07.12
AI2 Lower Limit of
Day-part C
0.0~20.0bar
2.0bar
b07.13
Lower Limit of Inlet
Pressure
0.0~100.0
0.0bar
Valid all day, especially for the use of
taking account of inlet water pressure.
When needn’t, set as 0.
b07.14
Restore Defaults
0~2
0
0:No action
1:Set to default
2:Clear error records
b07.15
Password of Group
br08
0~65535
65535
Br08 Group Application Function
b08.00
G/P Option
0~1
1
0:G model 1:P model
b08.01
Motor Rated Power
0.4~350kw
Model Set
Depend on Model, Setting parameters
according to nameplate of Motor
b08.02
Motor Rated
Frequency
0.00~600.00Hz
50.00Hz
b08.03
Motor Rated Speed
0~36000RPM
Model Set
b08.04
Motor Rated Voltage
0~460V
b08.05
Motor Rated Current
0.0~2000.0A
b08.06
Set the Password of
br07
0~65535
65535
Modify password of BR7.13
b08.07
Password of Factory
Parameters
0~65535
xxxxx
Don’t try to enter or will cause abnormal
operation and damages.
In order to ensure the pumps running safety, please enter rated value correctly from Motor Nameplate.

7. APPLICATION GUIDANCE
The ISUB22 B603 product has various function, the following introduce some typical application cases of
B603 and relevant parameter setting methods. In practical applications, you can reference to set.
7.1 Single Pump Water Supply and Parameter Setting
7.1.1 System Wiring
In Diagram:① B603 Intelligent Controller; ②Pumps Group; ③Pressure Tank; ④None-return Valve; ⑤
Pressure Transducer; ⑥Level Switch (to pool); ⑦Fault Indicator; ⑧Power Supply Indicator; ⑨
Fuse; ⑩Breaker.
Optional items ⑦⑧⑨ shown.
Figure7-1-1 Single Pump Wiring Addition Failure Indication
1)In the figure, we adopted the transducer is two line current type transducer of the company. Others
connect refers to Figure4-1-1;
2)The pool water should be used water level control switch. If the water pump is the pipeline booster
pressure pump, it does not need the water level control switch.
7.1.2 Debugging
Figure7-1-2 Debugging Flow Diagram

7.1.3 Parameter Setting of Single Pump Constant Pressure control Water Supply
Code
Factory
Setting
Recom -
mend
Description
b00.00
65535
65535
Password of entering parameter groups. Factory set is 65535, it can be
modified by b06.09
b08.01~
b08.05
Ensure normal operation, must input parameter according to Nameplate of
Motor
b00.02
0
x
Motor rotating direction, set according to the actual motor wiring of spot.
Make sure the motor is running in forward direction
B01.05
10.0
xx.x
Transducer Range, input the max. range of connected transducer
b01.08
When display smaller than gauge, decrease b01.08;
When display greater than gauge, increase b01.08
Below need to set based on working conditioning and user’s requirement.
b00.01
3.0
x.x
The pressure of water supply
b01.00
8.0
xx.x
High Water Pressure Alarm Value, Prevent system from damage caused by
high water pressure.
b01.01
0.5
x.x
Low Water Pressure Alarm Value, prevent pump from damage caused by
anhydrous idling.
b01.16
0
x
Restart after Power-on, Considering unattended management, set
parameter to 1
b05.00
0
x
Water Level Switch type, according to the using switch type
1:NC valid 2:NO valid
b05.02
2
3
*Notice: Only set this parameter on apply the terminal control , simply set
the master
b00.03
0
1
*Anti-freezing function, valid it when the pump work under a freezing
temperature
b02.03
b02.04
PID Parameter Debugging. Increase voltage stabilization accuracy or proper
regulation when Bias oversize and overwhelmed.
br07 group
Day-part water supply, set when needs the function. Reserved as Additive
Pipe Water Supply Mode, offering Day-part Variable Pressure Water Supply
and prevent insufficient net work pressure from affecting Public Water
Supply. Its’ setting refer to section 7.3.

8. FAULT AND TROUBLE SHOOTING
8.1 System Running Fault and Trouble Shooting
Abnormal Function
Reason
Solution
Can’t Sleep
1、Outlet Pipe Leakage;
2、Check Valve Leakage;
3、Pressure Tank Damage;
4、High Environment EMI;
5、Wrong Parameter
Check Outlet Pipe, or to set b04.04;
Inspect Check Valve;
Change Pressure Tank;
Transducer adopt shielded wires, Shielded
layer connect to PE;
Ensure b04.00=1
Display Pressure Error
1、Detector Error;
2、Wrong Parameters;
3、Transducer Wires is too
long;
Adopt Standard Detector;
Calibration parameter b01.05,b01.08;
Avoid Use too Long Transducer Wires;
Full-Frequency running
1、Lose Pressure Feedback;
2、Wrong Parameter;
3、Pump Under power;
Check Transducer and Wires;
b05.02 should not be set as 1;
S2-Com should be open;
Set b07.14=1, take a factory reset
Pressure vibration,
stabilize slow
1、PID Value unmatched;
2、Acc./Dec. Time too fast;
3、Big delay on pressure
feedback.
Tune PI value b02.03、b02.04
Tune Acc./Dec. time b05.03、b05.04
Avoid Use too Long Transducer Wires
Motor Noise
1、Motor Abnormal;
2、Motor installation is not
stable;
3、Low Carry-Frequency
Check Motor;
Proper turn up Carrier Frequency b05.08
This manual suits for next models
1
Table of contents
Popular Controllers manuals by other brands
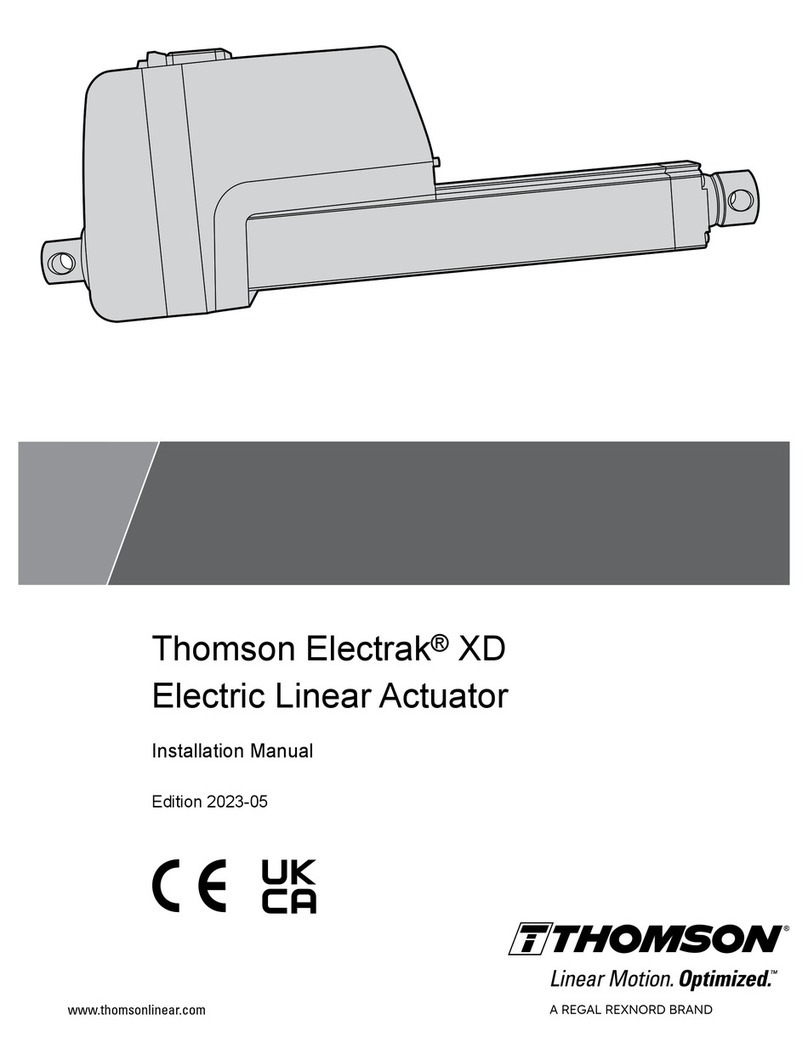
Rexnord
Rexnord Thomson Electrak XD installation manual
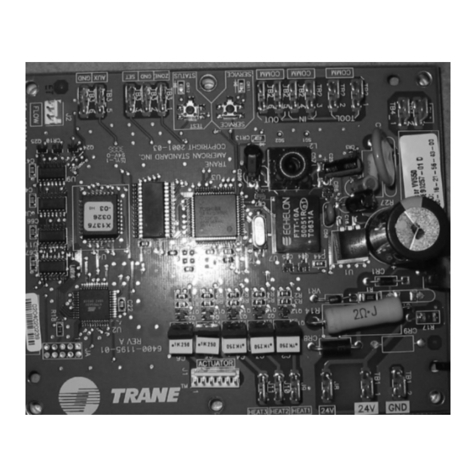
Trane
Trane VAV VV550 LonTalk Installation & operation manual
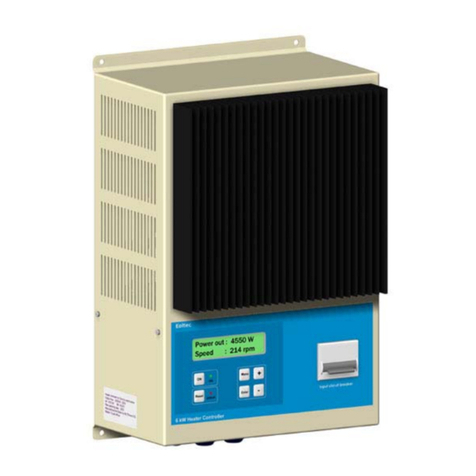
eoltec
eoltec HC-6K-230V-M quick start guide
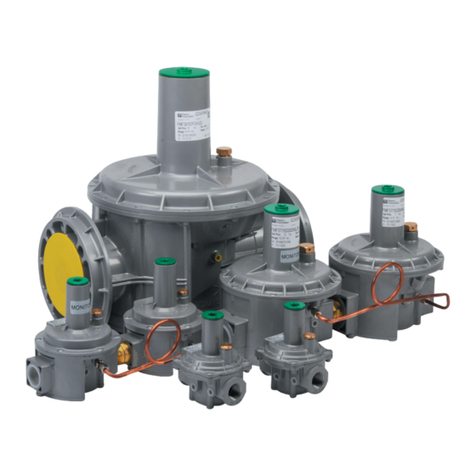
PIETRO FIORENTINI
PIETRO FIORENTINI 30051 Operation and maintenance manual
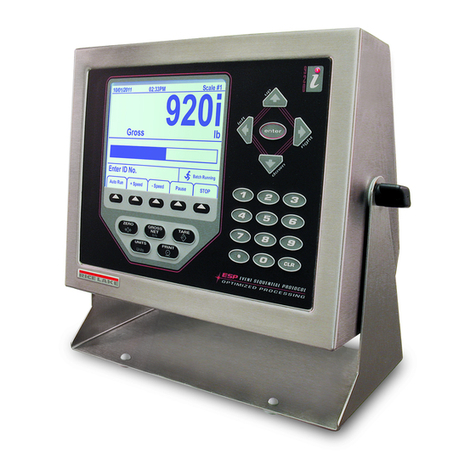
Rice Lake
Rice Lake iRite 920i installation manual
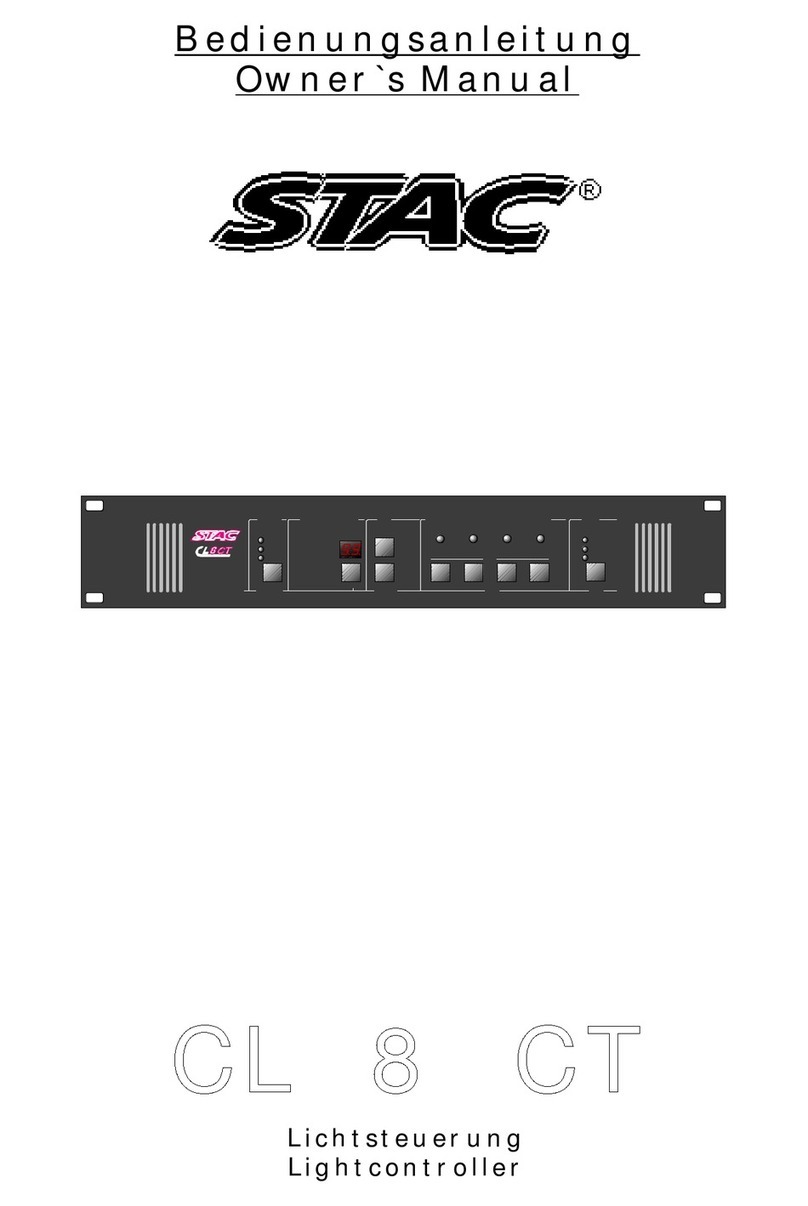
Zeck Audio
Zeck Audio STAC CL8CT owner's manual