Wise RL Series User manual

C-QIM-2731-T24_EN_Rev.2
Cool-down and leak detector
(RL series)
R190 Series

1
C-QIM-2731-T24_EN_Rev.2
Contents
1. General items......................................................................................................................2
1.1 Introduction.........................................................................................................................2
1.2 Application..........................................................................................................................2
1.3 Warranty............................................................................................................................. 2
2. Warning...............................................................................................................................3
3. Main specs..........................................................................................................................4
3.1 Explosion-proof...................................................................................................................4
3.2 Protection grade.................................................................................................................4
3.3 Temperature sensor types .................................................................................................4
3.4 Accuracy and tolerances....................................................................................................4
4. Design.................................................................................................................................5
4.1 Installation components......................................................................................................5
4.2 Basic pre-order design requirements.................................................................................5
4.3 Head...................................................................................................................................6
4.4 Sheathed cable (MI cable) .................................................................................................7
4.5 Types of temperature sensor ............................................................................................. 8
4.5.1 Resistance thermometer detector (RTD) ........................................................................8
4.6 Process connection unit................................................................................................... 10
4.6.1 Basic type......................................................................................................................10
4.7 Additional options.............................................................................................................11
4.7.1 Heat transfer block........................................................................................................11
4.7.2 Compression fitting........................................................................................................11
5. Installation guide ...............................................................................................................12
5.1 Pre-installation checks and precautions...........................................................................12
5.2 Installation requirement.................................................................................................... 13
5.3 Storage............................................................................................................................. 14
5.4 Installation order...............................................................................................................14
6. Wiring ................................................................................................................................17
6.1 Extension wire.................................................................................................................. 17
6.2 Precauation for wiring....................................................................................................... 18
6.3 Terminal block wiring........................................................................................................ 19
6.4 International color code table...........................................................................................20
7. Name plate........................................................................................................................ 21
7.1 Name plate indications.....................................................................................................21
8. Maintenance......................................................................................................................22
9. Defect................................................................................................................................22
10.User's duties......................................................................................................................23
11.Product return....................................................................................................................23

2
C-QIM-2731-T24_EN_Rev.2
1. General items
1.1 Introduction
The Cryogenic leak detecting temperature sensor manufactured by Wise Co., Ltd. is a product
designed with a pressure-resistant explosion-proof structure. An explosion proof structure means that
explosions due to heat or flame inside a vessel do not affect outside gases. This reduces the risk of
explosion due to electrical sparks or arcs in explosive environments under normal and abnormal
circumstances. This product must be tested and stored in appropriate locations, and the requirements
provided in the documentation, test reports and handling manuals, etc., must be adhered to in order to
maintain optimum state during the duration of use.
1.2 Application
They are used for temperature measurement in cold or cryogenic industrial environments, such as
LNG tanks and oxygen temperature monitoring at pharmaceuticals and biotech R&D facilities.
Cryogenic technologies are widely used throughout various state-of-the-art industries such as food
science, agriculture, raw materials, and vaccine development. Most gases which are in a gaseous
state at room temperature liquefy at temperatures of -40℃or higher, by cryogenic gases such as
helium, hydrogen, neon, nitrogen, oxygen, argon and methane can be liquefied at temperatures of -
150℃or lower. Pt100 Ω sensors are commonly used for cryogenic applications, and are capable of
sensing temperatures from -196 to 600℃. K-type and T-type thermocouples can be used, but while
thermocouples are less expensive, they provide a smaller temperature range and the thin cables often
freeze and snap inside chillers. Use of a Pt100 Ω sensor is therefore recommended. They are used for
temperature measurements in various processes, and measured values are used for indication,
recording and control in control panels or process systems. Units can be designed to suit all
applications in accordance with customer requirements.
1.3 Warranty
If one causes damage to the product due to failures to comply with the user manual, or if one
arbitrarily remodels it, changes or repairs the product, the manufacturer will not be responsible for it,
and the product warranty period will expire.

3
C-QIM-2731-T24_EN_Rev.2
2. Warning
Guide on handling for safe use
For the safe and correct use of the product, make sure to read the handling guide carefully before use.
Handling errors can cause device malfunctions, and it can lead to injury, accidents, etc.
Warning !
1) For the safety, only a worker with professional skills in electronics and electrical construction is
allowed to install the product.
2) Make sure to use the product within the rated input/output range set in the specifications.
3) Install the product in the environment of use indicated in the specifications.
4) Install wiring in accordance with the indoor wiring provisions and the Technical Standard for
Electrical Installations.
5) Make sure power has been cut off before performing wiring work.
6) Use wires with a sheath-insulated crimp terminal at the end.
7) Cable glands of the same explosion proof grade or higher.
8) Do not disassemble the product under any circumstances.
9) Use the product in the permissible temperature range.
10) Do not apply excessive loads, vibrations, or impacts.

4
C-QIM-2731-T24_EN_Rev.2
3. Main specs
3.1 Explosion-proof
Model: R190 (RC Series)
Explosion-proof grade: Ex d IIC T6 Gb
Explosion-proof technology criteria: IEC 60079-0, IEC 60079-1
3.2 Protection grade
IP 56, 66
3.3 Temperature sensor types
Resistance thermometer detector (RTD): Pt 100Ω at 0 ℃
3.4 Accuracy and tolerances
Class A, B (IEC/EN 60751)
Tolerance
class
Temperature range of validity (°C)
Tolerance value (℃)
For wire wound resistors
For film resistors
A
-100 to +450
-30 to +300
± ( 0.15 + 0.002 | t | )
B
-196 to +600
-50 to +500
± ( 0.3 + 0.005 | t | )
Operating temperature range by type
Type
Operating temperature range(℃)
RTD
Pt 100 Ω
high-temperature
-200~100
medium
temperature
0~350
high-temperature
0~600

5
C-QIM-2731-T24_EN_Rev.2
4. Design
4.1 Installation components
Head: Structure protecting electrical signals measured by sensor from external risk
(provided with components such as cable glands, earthing terminal and terminals)
Extension cable: Cable (Teflon(260°C)) for electric connection between sheathed cable(MI
cable) and Head
Sensor unit: Sheathed cable comprising thermocouple or RTD
Process connection unit: The connection between the measuring element and the process is
normally supplied as a flange type assembly.
Compression fittings: Select when process environment conditions require appropriate airtight
seals, according to external environment (vulnerable to contact with heat) temperature,
pressure and fluid medium
Additional accessories: Accessories available as an option for installation
(Clips, pads, spacers, stacking spring, heat shield, heat transmission block, pressure valve, etc)
Tailored design for all applications
4.2 Basic pre-order design requirements
High insulation characteristics are required to ensure that the sheath cable (MI cable) material
is protected from process temperatures.
The type of temperature sensor must be selected carefully depending on requirements.
(Check maximum allowable pressure and load, min./max working temperature, process fluid,
vibration)
The sheath cable (MI cable) material must be selected carefully, checking that the material is
appropriate to the material of the tank or pipe and the process environment.
Number and location of measuring points
Insertion length
Materials and process compatibility
Check that the product is compliant with existing control system requirements
A variety of miscellaneous designs specially engineered to customer applications are provided.

6
C-QIM-2731-T24_EN_Rev.2
4.3 Head
Explosion proof head structure protecting against ingress of dust, fine particulate matter and water, etc.
Warning: Certified explosionproof cable glands must be used when installing in hazardous areas.
See the <Table: Head information> below for the types of cables that may be connected
Table : Head information
Head
Head material
Head thread
(Cable entry size)
Conduit adaptor
Conduit adaptor
material
Explosion proof
(Dual entry type)
316SS
PF 1 1/4
PF 1 1/2
NPT 1 1/4
NPT 1 1/2
PT (unavailable)
Brass+Ni.plating
316SS

7
C-QIM-2731-T24_EN_Rev.2
4.4 Sheathed cable (MI cable)
A sheathed cable (MI cable) is an insulated cable for protecting an inner wire. The space between a
protection metal tube and inner wire or nickel wire is filled and sealed with the inorganic insulating
material magnesium oxide (MgO) at high temperature and high pressure.
Sheathed cable(MI cable) structure
1) Protection metal tube: Filled with inorganic insulating material to insulate and protect the inner wire
or nickel wire for metal tube
2) Inorganic Insulator: Highly pure magnesium oxide(MgO) powder to electrically insulate the
protection metal tube and inner wires
3) Internal conductor: The resistance temperature detector (RTD) is a nickel wire used for connecting
the resistor element to the terminal.
4) Insulating tube: Ceramic tube used to insulate and prevent short circuit between the resistor
element and the inner wire connection
5) Resistor element:A resistant platinum element for temperature measurement, fixed in place inside
the protection tube
6) The sheathed cable (MI cable) is flexible and mechanically robust. When installing with a curvature,
the minimum radius of curvature must be 5 times the outer diameter of the sheathed cable (MI
cable). (KS C 1616)
7) The sensor portion of a resistance temperature detector (RTD) contains a resistor element, and the
cable must be kept straight within 100mm from the sensor portion. (Do not bend)
8) Cables, plug-in connectors or connector sockets may be connected.

8
C-QIM-2731-T24_EN_Rev.2
4.5 Types of temperature sensor
4.5.1 Resistance thermometer detector (RTD)
Resistance temperature detectors (RTD) operate according to the principle of thermal resistance. The
electrical resistance of a metal wire increases with temperature. Typical resistance temperature
detectors(RTD) elements made of copper, nickel or platinum have large variations in resistance
according to temperature change, and can more safety and accurately measure temperatures
compared to thermocouples(TC) However, they have limited temperature range and relatively high
cost. They require current to measure temperature, and heat generated by the resistance temperature
detectors (RTD) themselves may impact the accuracy of temperatures measured. Selecting an
resistance temperature detectors (RTD) appropriate for the location of temperature measurement is
most important to ensure accurate temperature measurement.Accordingly, when selecting a
resistance temperature detectors (RTD), sufficient consideration needs to be given to a structure
resistant to surrounding conditions such as heat, corrosion and mechanical impact, installation method,
resistance temperature detectors (RTD) element and protection tubing, etc.
Types of resistance thermometer detector(RTD)
1) Ceramic type (Pt100Ω): Platinum resistance thermometer detector (RTD) elements using ceramics
are used for measuring temperatures in the range of -196 ~ 600℃, and have superior
reproducibility and stability compared to other elements. These are used broadly for industrial
temperature measurements with margins of error ranging from ClassA and B to DIN IEC751, and
used in most standard resistance thermometer detector (RTD).
2) Film type (Pt100Ω): Allows for maximum exposure of the sensor, giving fast response times. Small
length and thickness allows installation in tight spaces, with high impact and vibration resistance.
Used for measuring temperatures in the range of -50 ~ 500℃, and used broadly for industrial
temperature measurements with margins of error ranging from ClassA and B to DIN IEC751, and
used in most standard resistance thermometer detector (RTD).
Ceramic type Film type

9
C-QIM-2731-T24_EN_Rev.2
Inner wires
Nickel wire is typically used for connecting the resistor element to the terminal, and the 3-wire type
connection is standard.
1) 2-wire type: One wire is connected to each of the two terminals of the resistance thermometer
detector (RTD) element. This saves costs, but is subject to the impact of wire resistance and is not
suitable for high accuracy temperature measurements.
2) 3-wire type: Two wires are connected to one terminal of the resistance thermometer detector (RTD)
element, with a single wire connected to the other terminal. This reduces the impact of wire
resistance. Most commonly used for high reliability.
3) 4-wire type: Two wires are connected to each of the resistance thermometer detector (RTD)
terminals to eliminate the impact of wire resistance. Suitable for temperature measurements where
especially high accuracy is required.
4) Typical materials for resistance thermometer detector (RTD) internal wires are pure metals such as
nickel (Ni), copper (Cu), and platinum (Pt),etc

10
C-QIM-2731-T24_EN_Rev.2
4.6 Process connection unit
Basic flange process connection: Designated flange according to international standards
(NPS, pressure, gasket surface and material, etc.)
Tailored design of connections to satisfy process environment conditions
May be provided with eye bolts for lifting the instrument
4.6.1 Basic type
NO.
Description
NO.
Description
1
Head
6
Guide Protector
2
Comp'fitting
7
RTD Sheath
3
Flange
8
RTD Block
4
Nipple
9
Eye-Bolt
5
Lock nut
10
Terminal block

11
C-QIM-2731-T24_EN_Rev.2
4.7 Additional options
The following installation options are available depending on the use environment of the product.
4.7.1 Heat transfer block
Welded to inner wall of reactor for individual
temperature measurement.
Temperature sensors can be removed and replaced individually.
4.7.2 Compression fitting
Compression fitting are fastened or welded within the process.
When attaching compression fittings new tube bandings,confirm that there is sufficient
straight tube section length.
T(Tube OD)
L
inch
mm
inch
mm
1/16
1.6
1/2
12.7
1/8
3.2
23/32
18.3
3/16
4.8
3/4
19.1
1/4
6.4
13/16
20.6
5/16
7.9
7/8
22.2
3/8
9.5
15/16
23.8
1/2
12.7
1 3/16
30.2
5/8
15.9
1 1/4
31.8
3/4
19.1
7/8
22.2
1 5/16
33.3
1
25.4
1 1/2
38.1
1 1/4
31.8
2
50.8
1 1/2
38.1
2 13/32
61.1
2
50.8
3 1/4
82.6

12
C-QIM-2731-T24_EN_Rev.2
5. Installation guide
5.1 Pre-installation checks and precautions
1) Check for any obstacles or obstructions at the installation location before installation. (To prevent
injury and damage to instruments)
2) When installing instruments in explosion proof areas, check the explosion proof or safety equipment.
(To see if the ordered instrument is approved for use in an explosion proof area, consult the technical
information on the name plate on the side of the head.)
3) Use the original packaging to protect the instrument from impact during storage or transport.
Remove the packaging and protective material carefully.
4) When installing, beware of load applied to welds or screw fastenings by the weight of the instrument.
In particular, handle the sheathed cable (MI cable) extending beneath the flange with extra care.
5) Beware not to impact any obstacles nearby the installation location of the instrument.
6) Use the packaging material to wrap and protect the top portion of the flange against rain or moisture
until external wiring to the terminal block has been completed.
7) Protect the sheathed cable (MI cable) from being subjected to the load of the head and
appurtenances during transport or storage.
8) Use a Megger (Megohmmeter) to measure and confirm that insulation resistance is within normal
range prior to installation of the product.
9) When transporting the sensor assembly to the tank and attaching to the nozzle, avoid applying
external physical force (compression, impact, etc.) on the sheathed cable (MI cable).
10) Check that the protection cover and thermocouple are free of scratches, cut marks, oil or other
contaminants. (Even tiny amounts of foreign matter can decrease the accuracy of measurements.)

13
C-QIM-2731-T24_EN_Rev.2
5.2 Installation requirement
1) Installation shall be performed by a qualified worker with the necessary professional expertise, in
compliance with the installation instructions.
2) Do not open the head cover in explosive atmospheres when the circuit is energized.
3) Prior to connecting additional electrical and electronic devices in environments with risk of explosion,
confirm that installation has been carried out in accordance with the indoor wiring provisions and the
electrical technical standards for wiring in intrinsically safe or non-flammable sites.
4) When attaching components, do not pull or push the sheathed cable (MI cable) with excessive force.
5) For products attached to compression fittings, do not loosen screws during operation. Attach the
compression fittings to the temperature sensor prior to installation.
6) For products attached to compression fittings, be careful not to pull or turn the sheathed cable (MI
cable) when attaching or detaching components with the product in an assembled state.
(Can be the cause of leaks)
7) Do not remove the protection tube over the sensor unit of the sheathed cable (MI cable) until the
sheathed cable has been inserted into the heat transmission block and secured in place. The sensor
unit of the sheathed cable (MI cable) contains a ceramic resistor element which can be damaged
even by the slightest impact, and must be handled with particular care.
8) When installing in the field, the sheathed cable (MI cable) itself must not be welded directly. Perform
welding work with caution to avoid weld sparks affecting the sheathed cable.
9) When installing in direct contact with the process, check that the external loads applied to not cause
deformation of the instrumentation and welded parts.
10) The end user must ensure that the instrumental has been appropriately installed so that the allowed
limits are not exceeded.
11) Multi-point temperature sensors must be installed by multiple persons, paying special attention to
safety.
12) This product has been field-tested in accordance with customer requirements, and has been
subjected to all additional safety-related testing in compliance with safety requirements. However,
malfunction or misuse may result in malfunction. When installing, tighten threaded components (bolts
and nuts) using the designated torque and tools. Confirm proper installation using the approved
drawings.

14
C-QIM-2731-T24_EN_Rev.2
5.3 Storage
Carry out the following procedure prior to storage.
1) Place a desiccant inside the sensor head.
2) Tighten the head cover, and plug the conduit entry.
3) Wrap the entire head using packaging material.
Follow the instructions below before selecting a storage location.
1) The product should be stored indoors, avoiding dust and humidity.
2) To prevent damage to the sheathed cable and flange surface, store far away from other machinery
or apparatuses.
3) Do not stack other objects on top of the product.
When keeping in storage for prolonged periods, check the following.
1) Measure insulation resistance at 2 to 3-month intervals.
2) Replace the desiccant annually.
5.4 Installation order
1) Check for obstructions inside the vessel where the instrument will be installed.
(Avoid friction, especially occurrence of sparks while installing the instrument.)
2) Check that the gasket sheet is clean, then place the gasket between the flange nozzle and
instrument flange.
3) Fasten the bolts through the flange bolt holes, and secure using nuts and an appropriate wrench
tool. (Do not fasten completely at this time.) Once all bolts have been fastened, use appropriate
equipment to tighten, alternating diagonally. (Adjust torque according to applicable standard)
4) When installing in a radial pattern, identify the designated installation positions on the supporting
structure (support frame, fixing bar, fixing clip, etc.) installed beforehand inside the reactor in
accordance with installation-related drawings, then secure the units in place.
(Note: The minimum radius of curvature should be at least 5 times the outer diameter of the
sheathed cable(MI cable). The end of the RTD contains a resistor element, the RTD must be kept
straight for at least 100mm from the end.)
5) Weld the heat transmission blocks to the respective sensor locations, according to the Tag No.
indicated on the blocks.

15
C-QIM-2731-T24_EN_Rev.2
6) Secure each sheathed cable(MI cable) to the heat transmission block having the same Tag No.,
using a compression fitting. (Insert all the way into the hole of the heat transmission block, then
secure in place), After installing the sheathed cable(MI cable) remove the tag number stamp if
necessary
7) When tightening the compression fitting, tighten it as much as possible by hand and tighten it to the
specified torque value using a wrench.
8) When installing compression fittings on the nozzle flange, use sealant when tightening to prevent
leakage of internal gases.
9) To wire the system, install the extension or compensation cable through the cable gland of the
head.
10) Connect the cables to the terminal according to the wiring instructions, matching the cable tag
numbers to the terminal tag numbers.
11) When connecting terminals, keep the terminals from rotating to interfere with neighboring terminals.
12) RTD power sources should have a relatively small range of temperature fluctuation. In cases where
AC power is available but DC power (1~12V) is necessary, a rectifier with an integrated transformer
is typically used. In particular, when using a potentiometer, a storage battery, dry cell or stabilized
DC power source should be used.
13) Perform wiring with caution to prevent ingress of rainwater, dust or other foreign matter into the
head.
14) Inspect to confirm wiring has been properly performed. Check for disconnected wires, and measure
insulation resistance.

16
C-QIM-2731-T24_EN_Rev.2
15) After assembling the terminal, manually tighten the head cover clockwise until the O-Ring inside
the head comes into contact and the head cover no longer moves. Use the provided cover tool to
tighten until the head cover cannot be opened without the tool.
16) After installation, confirm that all components are properly connected. In particular, inspect the
sealing state of any screws, and if there are any loose components, tighten to the proper torque.
17) Plug any unused conduit entries to prevent ingress of rainwater into the product.
18) To protect the product from rain or humidity, seal the screw connections by winding with waterproof
tape or applying lubricant.
19) Connect a lock-chain to keep the head cover from coming loose.

17
C-QIM-2731-T24_EN_Rev.2
6. Wiring
6.1 Extension wire
Temperature is measured using the change in resistance (Ω) according to temperature.
Resistance thermometer detector (RTD) cables are selected as 3-wire or 4-wire, and one end of
the shielding wire must be grounded.
Type
Conductor
Insulator
Shielding
Resistance
thermometer detector
(RTD)
Tinned copper wire
Glass braiding
Tinned braided wire
Teflon
Tinned braided wire
Vinyl (PVC)
Vinyl (PVC)
1) Extension wire having specs appropriate for measuring temperature sensor signals must be
selected and used.
2) Voltage flow must be given consideration when deciding cable thickness.
3) The external covering material must be selected appropriately for the installation environment.
4) If there are outdoor wiring sections, do not use glass sheathing. Humidity may reduce insulation
resistance and cause measuring errors.
5) Cables shall be protected from damage such as breakage or cutting by the surrounding
environment.
6) Exercise caution to prevent folding or knitting of cable.

18
C-QIM-2731-T24_EN_Rev.2
6.2 Precauation for wiring
1) Make sure to cut off power before wiring product with an explosion proof grade.
2) Wire resistance temperature detectors (RTD) after disconnecting the A/B/B (3-wire) terminal.
3) Attach the end of the compensation wire and cable to the terminal block using crimp terminals.
Tightly fasten the screws.
4) When wiring to a transmitter, adhere to the wiring instructions given in the user manual for the
transmitter.
5) For equipment with an explosion proof grade, make sure the cover does not open during operation.
Tighten the locking apparatus.
6) Earthing
- Use aluminum earthing terminals to prevent corrosion.
- Use 304SS earthing bolts.
- Use spring washers to prevent loosening of the earthing terminals.
- When using external earthing terminals, check the connectors and use an appropriate earthing
line.
7) After making the connections, inspect to ensure that the power supply and signal cables have been
connected properly.

19
C-QIM-2731-T24_EN_Rev.2
6.3 Terminal block wiring
Typical Wiring for Resistance Thermometer (RTD)
Install wires according to the wiring diagram and polarities indicated on the terminal block. Connect
cables to match the terminal tag numbers.
Single (3-Wire)
Double (6-Wire)
Ex) Max20 Point
This manual suits for next models
1
Table of contents
Other Wise Security Sensor manuals
Popular Security Sensor manuals by other brands
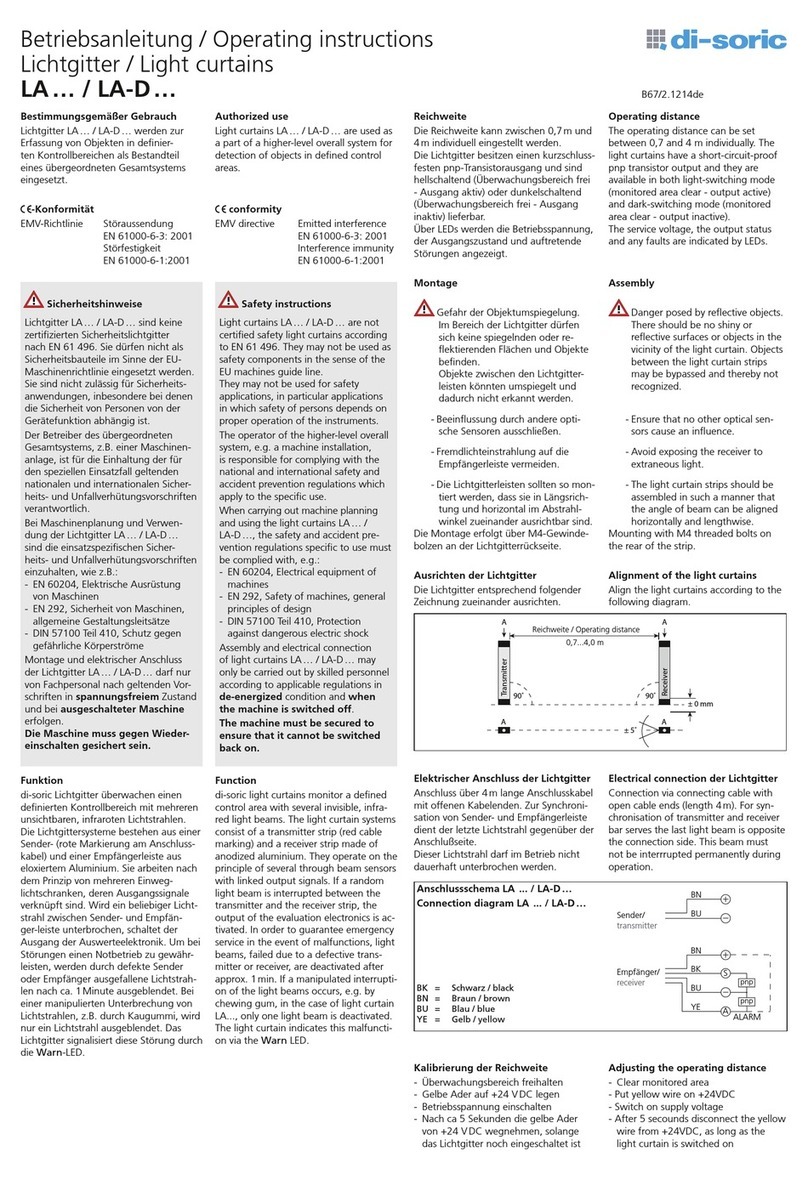
Di-soric
Di-soric LA Series operating instructions
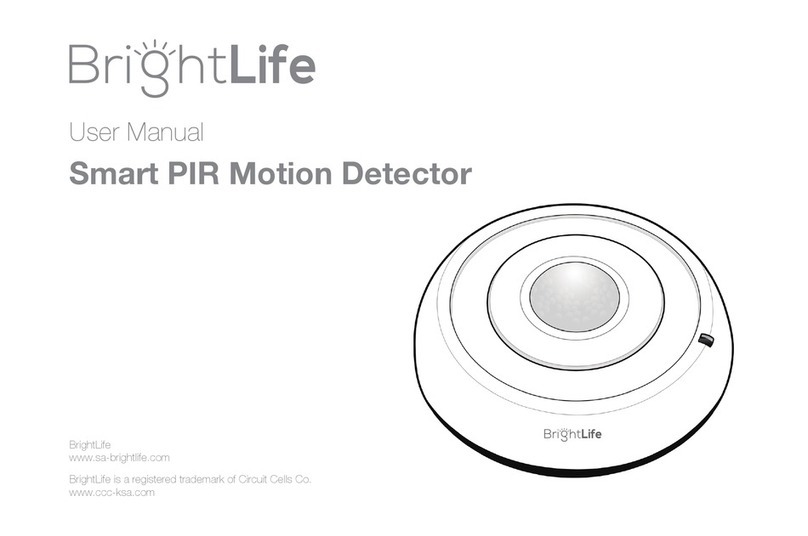
BrightLife
BrightLife Smart PIR Motion Detector user manual

Petzl
Petzl ASAP B71 manual
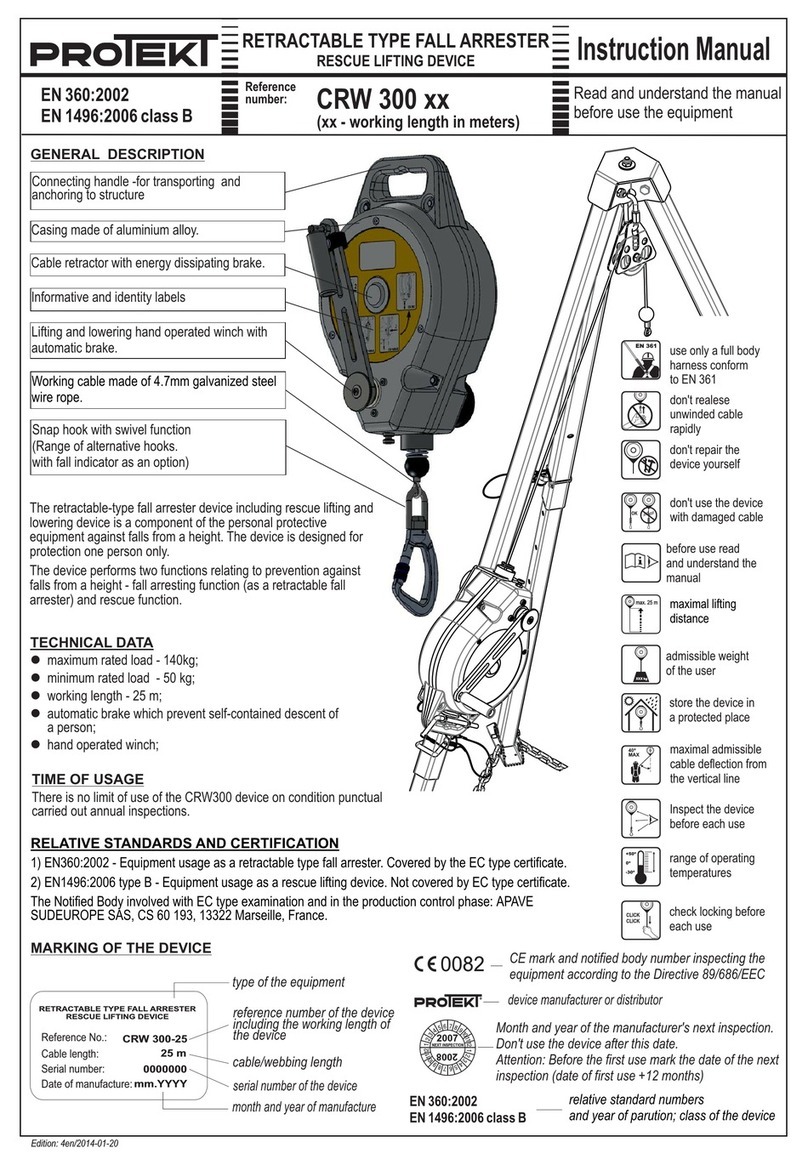
Protekt
Protekt CRW 300 Series instruction manual

PCB Piezotronics
PCB Piezotronics 132B38/010PH Installation and operating manual
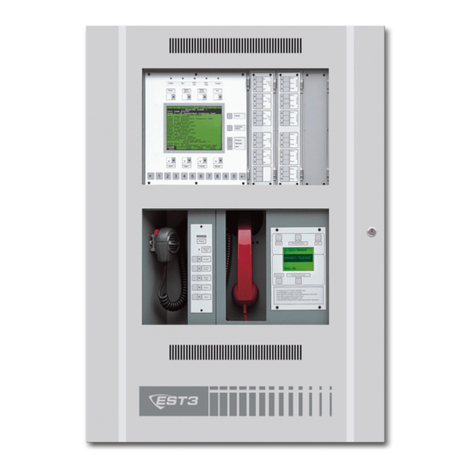
EDWARDS SYSTEMS TECHNOLOGY
EDWARDS SYSTEMS TECHNOLOGY EST3 manual