Woodward DSS-2 User manual

User Manual
DSS-2
Two-Channel
Digital Speed Switch
Manual 36598

WARNING
Read this entire manual and all other publications pertaining to the work to be
performed before installing, operating, or servicing this equipment. Practice all
plant and safety instructions and precautions. Failure to follow instructions can
cause personal injury and/or property damage.
The engine, turbine, or other type of prime mover should be equipped with an
overspeed shutdown device to protect against runaway or damage to the prime
mover with possible personal injury, loss of life, or property damage.
The overspeed shutdown device must be totally independent of the prime mover
control system. An overtemperature or overpressure shutdown device may also be
needed for safety, as appropriate.
CAUTION
To prevent damage to a control system that uses an alternator or battery-charging
device, make sure the charging device is turned off before disconnecting the battery
from the system.
In systems where large inductive loads are switched on the DC power buss, surge
impulse energy will be present due to the switching. To address surge energy
affects on the control, appropriate suppression devices must be installed in the DC
power buss prior to the control’s power connection.
Electronic controls contain static-sensitive parts. Observe the following precautions
to prevent damage to these parts.
• Discharge body static before handling the control (with power to the control
turned off, contact a grounded surface and maintain contact while handling the
control).
• Avoid all plastic, vinyl, and Styrofoam (except antistatic versions) around
printed circuit boards.
• Do not touch the components or conductors on a printed circuit board with
your hands or with conductive devices.
IMPORTANT DEFINITIONS
WARNING—indicates a potentially hazardous situation which, if not avoided, could
result in death or serious injury.
CAUTION—indicates a potentially hazardous situation which, if not avoided, could
result in damage to equipment.
NOTE—provides other helpful information that does not fall under the warning or
caution categories.
Revisions—Text changes are indicated by a black line alongside the text.
Woodward Governor Company reserves the right to update any portion of this publication at any time. Information
provided by Woodward Governor Company is believed to be correct and reliable. However, no responsibility is
assumed by Woodward Governor Company unless otherwise expressly undertaken.
© Woodward 2005
All Rights Reserved

Manual 36598 DSS-2 Two-Channel Digital Speed Switch
Woodward i
Contents
R
EGULATORY
C
OMPLIANCE
......................................................................
III
E
LECTROSTATIC
D
ISCHARGE
A
WARENESS
.................................................
IV
C
HAPTER
1. G
ENERAL
I
NFORMATION
..........................................................1
Introduction.............................................................................................................1
How Speed Switches Work ....................................................................................2
Set vs. Reset...................................................................................................2
Normal vs. Reverse Relay Logic.....................................................................2
Autocrank........................................................................................................3
Glow Plug Preheat..........................................................................................3
System Components ..............................................................................................3
DSS-2 Controller.............................................................................................3
All-purpose Calibration Tool (ACT).................................................................5
C
HAPTER
2. S
PECIFICATIONS
.....................................................................6
Electrical .................................................................................................................6
Mechanical..............................................................................................................6
C
HAPTER
3. I
NSTALLATION
........................................................................7
DSS-2 Mounting .....................................................................................................7
DSS-2 Wiring..........................................................................................................7
Controller Pinout ...........................................................................................10
Speed Sensor Installation.....................................................................................11
C
HAPTER
4. C
ALIBRATION
.......................................................................12
Calibration Guide..................................................................................................12
Manual Calibration........................................................................................12
Calibration with ACT .....................................................................................12
Speed Switch Configuration..........................................................................14
Figure 4. Typical Speed Switch InstallationManual Calibration ....................14
Manual Calibration........................................................................................15
Speed Switch Calibration Using ACT ...........................................................15
Normal Operation vs. Reverse Operation.....................................................16
Reset Mode: Auto/Manual/Latch...................................................................16
Speed Switch Options...................................................................................16
Speed Switch Options...................................................................................17
Autocrank Configuration .......................................................................................18
Manual Calibration........................................................................................19
Autocrank Calibration Using ACT.................................................................20
Enabling Autocrank.......................................................................................20
Autocrank Options ........................................................................................21
Glow Plug Controller Configuration ......................................................................21
Manual Calibration........................................................................................22
Glow Plug Controller Adjustment Using ACT ...............................................23
Enabling Glow Plug Control..........................................................................23
Pre-Heat Time ..............................................................................................24
Engine Protection Switch Configuration ...............................................................24
Completing Wizard Configuration.........................................................................25

DSS-2 Two-Channel Digital Speed Switch Manual 36598
ii Woodward
Contents
(cont'd.)
C
HAPTER
5. ACT O
PERATION
..................................................................26
ACT Installation ....................................................................................................26
ACT Kit Contents ..........................................................................................26
Set-up Requirements....................................................................................26
Hardware Set-up...........................................................................................26
Software Set-Up............................................................................................27
Basic ACT Operation............................................................................................28
Running the ACT Software ...........................................................................28
Progress Display Screen ..............................................................................28
Moving Around the Software.........................................................................29
ACT Menus & Options..........................................................................................29
ACT Menu Structure .....................................................................................29
File Menu ..............................................................................................................30
Purpose.........................................................................................................30
Save DSS-2 Cal to File.................................................................................30
View Cal File Comments...............................................................................31
View Text File ...............................................................................................32
Convert Commands......................................................................................32
Convert DSS-2 Cal to Text ...........................................................................32
Convert Cal File to Text ................................................................................33
Convert Cal File to Strategy..........................................................................33
Calibrate Menu......................................................................................................33
Change DSS-2 Calibration............................................................................33
Calibration Categories ..................................................................................35
List of Parameters.........................................................................................36
Download Cal File to DSS-2 .........................................................................39
Compare DSS-2 Cal to File Cal....................................................................40
Change DSS-2 Password.............................................................................41
DSS-2 Calibration Wizard.............................................................................43
Monitor Menu........................................................................................................44
Parameter View ............................................................................................44
Parameter Plot..............................................................................................45
Display Faults................................................................................................46
Control Strategy ............................................................................................47
Configure Menu ....................................................................................................48
Configure Serial Port.....................................................................................48
Help Menu.............................................................................................................49
Help Topics...................................................................................................49
About ACT ....................................................................................................49
User Manuals................................................................................................49
C
HAPTER
6. T
ROUBLESHOOTING
..............................................................50
General Checklist .................................................................................................50
Fault Codes ..........................................................................................................50
Glossary of Technical Terms................................................................................52
C
HAPTER
7. S
ERVICE
O
PTIONS
................................................................53
Product Service Options .......................................................................................53
Returning Equipment for Repair ...........................................................................54
Replacement Parts ...............................................................................................55
How to Contact Woodward...................................................................................55
Engineering Services............................................................................................56
Technical Assistance............................................................................................57

Manual 36598 DSS-2 Two-Channel Digital Speed Switch
Woodward iii
Regulatory Compliance
European Compliance for CE Marking
EMC Directive
Declared to 89/336/EEC COUNCIL DIRECTIVE of 03 May 1989 on the
approximation of the laws of the Member States relating to electromagnetic
compatibility.
Electromagnetic Compatibility
Testing was performed to ISO/EN 14982:1998 and EN 13309:2000 standards.
Evaluations, other than specific testing, were performed to cover:
• EN 12895:2000
• EN 61000-6-2:2001
• EN 61000-6-4:2001
Testing to EN 14982:1998 and application specific installation requirements cover
evaluations. (See Chapter 1 of this manual for intended usage of this unit.)
EMC Limitations
All cabling for these controllers is limited to less than 3m (9.84’).
Power cabling is limited to less than 10m (32.8’) in total length.
See wiring diagrams for specific cable types required.
Declaration of Conformity
The official Declaration of Conformity is available upon request. Please see the
“How to Contact Woodward” section in Chapter 7 to request a copy.

DSS-2 Two-Channel Digital Speed Switch Manual 36598
iv Woodward
Electrostatic Discharge Awareness
All electronic equipment is static-sensitive, some components more than others.
To protect these components from static damage, you must take special
precautions to minimize or eliminate electrostatic discharges.
Follow these precautions when working with or near the control.
1. Before doing maintenance on the electronic control, discharge the static
electricity on your body to ground by touching and holding a grounded metal
object (pipes, cabinets, equipment, etc.).
2. Avoid the build-up of static electricity on your body by not wearing clothing
made of synthetic materials. Wear cotton or cotton-blend materials as much
as possible because these do not store static electric charges as much as
synthetics.
3. Keep plastic, vinyl, and Styrofoam materials (such as plastic or Styrofoam
cups, cup holders, cigarette packages, cellophane wrappers, vinyl books or
folders, plastic bottles, and plastic ash trays) away from the control, the
modules, and the work area as much as possible.
4. Do not remove the printed circuit board (PCB) from the control cabinet
unless absolutely necessary. If you must remove the PCB from the control
cabinet, follow these precautions:
•Do not touch any part of the PCB except the edges.
•Do not touch the electrical conductors, the connectors, or the
components with conductive devices or with your hands.
•When replacing a PCB, keep the new PCB in the plastic antistatic
protective bag it comes in until you are ready to install it. Immediately
after removing the old PCB from the control cabinet, place it in the
antistatic protective bag.
CAUTION
To prevent damage to electronic components caused by improper
handling, read and observe the precautions in Woodward manual
82715, Guide for Handling and Protection of Electronic Controls,
Printed Circuit Boards, and Modules.

Manual 36598 DSS-2 Two-Channel Digital Speed Switch
Woodward 1
Chapter 1.
General Information
Introduction
DSS-2 (Digital Speed Switch, 2-Channel) is a two-
channel electronic speed switch that combines the
convenience of manual adjustments with the flexibility
of a computer-based calibration tool. DSS-2 was
designed for use on engine applications where it can
perform a variety of speed related functions such as
starter motor disable and engine overspeed protection.
DSS-2 monitors engine rpm via a magnetic pickup
(MPU) input and controls two independent relays.
Once engine speed exceeds the user selected speed
setpoint, the relay will go to the designated set
condition. DSS-2 can also be re-configured with the
ACT (All-purpose Calibration Tool) to function as an
engine autocrank controller or glow plug controller.
DSS-2 has two multi-turn potentiometers for manual speed setpoint adjustment. A
computer interface is provided for additional adjustments with the All-purpose
Calibration Tool (ACT). Electrical connections consist of thirteen wires and utilize a
Euro-style terminal strip. For most applications, DSS-2 can be connected and
adjusted with simple hand tools. For more advanced features, the calibration tool
provides user-friendly access. Three indicator lamps permit system monitoring and
diagnosis without use of additional tools.
As shipped from the factory, DSS-2 can be manually adjusted on most applications
that supply a MPU frequency of 2500 to 5000 Hz. Optionally, the user may attach
the calibration tool (ACT) to gain access to a number of user-adjustable features
including:
• Frequency range (200-15,000 Hz)
• Normal and reverse mode operation
• Automatic, Manual or Latched reset
• Set condition on Engine Protection (EP) switch on
• Set condition on loss of speed signal
• Set condition on Start Switch (VER) off
• Autocrank: Configure crank disconnect speed range, crank time, rest time
and number of crank attempts
•
Glow plug preheat
Intended Usage
The DSS-2 is intended as a sub-system for integration into construction/commercial
and industrial engine systems by original equipment manufacturers and industrial
plants. It is not intended for consumer or on-highway vehicles or for use by the
general consumer/public. Typical applications include generator sets, compressors,
construction machinery and farm vehicles.

DSS-2 Two-Channel Digital Speed Switch Manual 36598
2 Woodward
Figure 1. DSS-2 Engine Control System
How Speed Switches Work
The purpose of a speed switch is to monitor the speed of a rotating device, such as
an internal combustion engine, and close or open a set of switch contacts when
speed exceeds a threshold. Speed switches are most often used to disengage
starter motors when the engine starts, and to shut down the engine should an
overspeed occur. With the addition of some logic, speed switches may be applied to
a number of applications. Electrical loads controlled with a speed switch include
starter relays, ignition system power, indicator lamps, glow plug relays, solenoids
and electro-hydraulic valves.
Set vs. Reset
Speed switches make frequent use of the terms “Set” and “Reset.” The “Reset”
condition or state is that which exists when the unit is first powered up and when
engine speed is below the speed threshold. Once speed rises above the threshold
(set speed), the speed switch output (relay) transitions to the “Set” condition. In
some cases, depending on configuration, the speed switch can return to the “Reset”
condition when engine speed drops below a lower threshold (reset point), or when a
manual reset switch is actuated. The speed switch may also be configured to latch a
Set condition until battery power is cycled.
Normal vs. Reverse Relay Logic
A normally configured speed switch channel has the relay de-energized in the Reset
condition and energized in the Set condition. It is possible to configure each channel
in Reverse mode such that the relay is energized in the Reset condition and de-
energized in the Set condition. This is helpful in applications such as engine crank
disable where a loss of power to the DSS-2 should produce the same response as

Manual 36598 DSS-2 Two-Channel Digital Speed Switch
Woodward 3
exceeding the set engine speed. Configuring a channel in normal mode for a crank
disable feature could cause overcranking if power were interrupted to the DSS-2.
Autocrank
The DSS-2 speed switch channels can be easily configured to provide an autocrank
feature using the ACT. In this mode, applying battery voltage to the VER input will
initiate the starting sequence. When this happens, the relay will be energized until
either the engine starts, or a maximum crank time is exceeded. If the latter occurs,
the logic will wait for a rest period before attempting to crank again. Crank Time,
Rest Time and Maximum number of crank attempts are user selectable using the
ACT. The rpm at which the DSS-2 assumes the engine has started, referred to as
the crank disable speed, is adjustable using the multi-turn potentiometer for that
channel.
Glow Plug Preheat
When one channel of the DSS-2 has been configured for autocrank, the user may
configure the other channel as a glow plug controller. In this mode, the DSS-2 will
energize the glow plug relay for a fixed period of time before engine cranking begins.
The relay will remain on until the end of the crank period, or until the engine starts –
whichever comes first. The glow plug relay will remain on during the rest period
provided that the glow plug preheat time is longer than the rest time, if not, the glow
plug relay will be turned off until the appropriate preheat delay prior to the next crank
attempt. The maximum glow plug preheat time is user selectable using the ACT.
The actual preheat time is adjustable between zero and the maximum using the
multi-turn potentiometer for that channel.
System Components
The two components required to install a DSS-2 on an engine are the DSS-2 controller
and magnetic pickup (MPU) speed sensor. Both components contribute to the overall
performance of the system and shortcomings in either will detract from total system
performance. Optionally, the All-purpose Calibration Tool (ACT) may be used to
customize operation.
DSS-2 Controller
DSS-2 contains a powerful microcontroller that processes
the signal received from the MPU sensor and compares it
to the speed setpoints. Output control is accomplished by
means of two independently controlled form-C relays with
Common (C), Normally Closed (NC) and Normally Open
(NO) contacts.
The DSS-2 controller has two multi-turn potentiometers
for speed setpoint adjustment. A computer serial
interface is provided for additional adjustments with the ACT.
The controller has thirteen Euro-style screw terminals for:
• Battery Positive and Negative (9-30 Vdc). Reverse voltage protected
• Two form-C relays (10A continuous). Independent Common (C), Normally
Closed (NC) and Normally Open (NO) contacts are provided. DSS-2 is
factory programmed for standard relay logic (relay de-energized below set
speed), but may be modified with the ACT for reverse relay logic (relay
energized below set speed). External diodes should be added for transient
suppression with inductive loads

DSS-2 Two-Channel Digital Speed Switch Manual 36598
4 Woodward
• Magnetic Pickup (MPU) Positive and Negative (2 VAC minimum at 1000
Hz). The controller is factory programmed for 2500 to 5000 Hz. This range
may be modified with the ACT to cover 200-15,000 Hz or operate in units of
rpm.
• Reset Switch Input (RST): A switch to battery positive switch input is
provided for manual reset functions. DSS-2 is factory programmed for
automatic reset at 80% of set speed, but may be modified with the ACT for
manual or latched reset.
• Engine Protection Switch Input (EP): A switch to battery positive switch
input is provided for connection to external engine protection devices.
• Verify Switch Input (VER): A switch to battery positive switch input is
provided for a verify function. Activating this switch will reduce both
channel set frequencies to 70% of their normal values. The VER input
also functions as a Start/Stop switch input in certain modes of operation.
When a channel is configured as an autocrank controller, the Verify switch
is used to initiate the start sequence. If a channel uses the Verify switch
as a Start Switch, removing the switch input will force the channel to a set
status.
Use insulated, automotive grade wiring (minimum 18 AWG or 1 mm
2
) for all connections.
Shielded wiring is recommended for the MPU.
The DSS-2 is equipped with three LEDs: one green and two red. All LEDs will be turned on
for one second following power up as a lamp test and as an indication of normal operation.
Green LED:
The green LED is an engine status indicator and functions as follows:
OFF: No engine speed
ON: Engine speed sensed
Flashing: Fault present
Red LEDs:
The red LEDs are each assigned to a speed switch channel.
• When a channel is configured as a speed switch, its LED will be illuminated
when the channel relay is in the Set condition.
• When a channel is configured as a glow plug controller, its LED will be
illuminated when the relay is energized (glow plug ON).
• When a channel is configured as an autocrank controller, its LED will be
illuminated when the relay is energized. The LED will flash rapidly during the
starter rest period (relay de-energized).

Manual 36598 DSS-2 Two-Channel Digital Speed Switch
Woodward 5
Speed Sensor
DSS-2 monitors engine speed continuously using
a magnetic pickup (MPU), which detects the
passing of teeth on an engine driven gear (e.g.,
flywheel). The frequency of the voltage generated
by the MPU is proportional to engine rpm.
A variety of MPU sensors are available from
Woodward.
All-purpose Calibration Tool (ACT)
ACT is a PC (personal computer) based software calibration and
monitoring tool. ACT is designed specifically for use with engines
equipped with the DSS-2 controller. The tool can be run on any
IBM compatible computer that meets the requirements listed
ACT Installation” in Chapter 5.
Once the DSS-2 controller has been programmed, ACT may be
disconnected. The DSS-2 unit will continue to operate normally
with ACT either connected or disconnected.
Woodward P/N SA-5206
CAUTION
An unsafe condition could occur with improper use of these software
tools. Only trained personnel should have access to these tools.

DSS-2 Two-Channel Digital Speed Switch Manual 36598
6 Woodward
Chapter 2.
Specifications
Woodward P/N: 8800-1001
Electrical
Power Input
9-30 Vdc, Reverse polarity protected
Electromagnetic Compatibility
See Regulatory Compliance on page iii.
Operating Current:
Both Channels On:
Both Channels Off:
12 V: 100 mA / 24 V: 100 mA
12 V: 50 mA / 24 V: 50 mA
Relay Contact Ratings @ 28 Vdc
Resistive Load: 1 to 10A
Inductive Load: 1 to 8A
Mechanical
Operating Temperature
-40°F to +185°F (-40°C to 85°C)
Vibration
4 G’s from 40 to 2000 Hz
Shock
10 G’s @ 45 Hz
Housing
UV, chemical resistant. UL 94 V-O
flame retardant. Encapsulated for
reliability in harsh environments
Terminations
Euro-style terminal block
Calibration
Manual or with PC-based All-purpose
Calibration Tool / ACT [SA-5206]
Weight:
0.38 lbs (0.17 kg)
NOTE
The scope of this manual does not include selection of speed
sensors or other components that Woodward offers for use with
the DSS-2 system. Information is available on our website at
www.woodward.com.
NOTE
The need for sub-components such as switches is application
dependent. Please contact Woodward for information specific to
your application.

Manual 36598 DSS-2 Two-Channel Digital Speed Switch
Woodward 7
Chapter 3.
Installation
CAUTION
Take adequate protection to ensure personal and equipment safety
and follow the suggested installation sequence given below.
Refer to Figures 2 & 3 and Table 1 to install the system and subcomponents.
DSS-2 Mounting
Mount the unit in a location where the effects of vibration and temperature are within
the specified range. Operating temperature: -40°F to +185°F (-40°C to +85°C);
vibration: 6 G’s from 40 to 2000 Hz. (See Figure 2 for controller dimensions.)
DSS-2 Wiring
DSS-2 has thirteen Euro-style terminals for external connections. To use:
1. Loosen the terminals with a small blade screwdriver.
2. Strip wire.
3. Insert wire into terminal hole.
4. Tighten terminal with a small blade screwdriver.
Refer to Figure 3. Use proper wire gauges (18 AWG/ 1 mm
2
minimum). All wire
insulation should be appropriate for engine applications. Terminations must be
impervious to moisture to prevent shorts and corrosion.
Use of convoluted tubing, conduit, or other wire shielding is recommended to
minimize the likelihood of mechanical damage to wires. Avoid routing wires near
sharp edges or near locations that can cause the wires to be pinched or damaged.
Power Leads: Power leads are to be connected directly to a switched power
source (i.e., battery). With both channels on, DSS-2 draws a maximum of 100 mA.
Use of a slow-blow fuse is recommended in the battery (positive) wire. Electrical
loads attached to the two relays should be separately fused.
MPU Wiring: Use shielded cable for MPU signal. The shield should be connected
to the battery ground wire at one end only.
Output Loads: Channel 1 and Channel 2 output relays may be connected to a
variety of electrical loads including starter relays, engine ignition systems, fuel
shutdown solenoids, indicator lamps, hydraulic solenoid valves, etc. The current
requirements of the load must be matched to the contact capability of the output
relays (10A resistive load). When the output relays are connected to inductive loads
(e.g. solenoids) external diodes should be added to increase contact life and for
transient suppression. Electrical loads attached to the two relays should be
separately fused.
Excessive resistance in the wiring will result in reduced current to the electrical load.
Such increased resistance can result from too much wire length, inadequate wire
gauge, or poor connections. Total wiring length–between battery power and the
DSS-2 as well as between the DSS-2 and the load–must be considered.

DSS-2 Two-Channel Digital Speed Switch Manual 36598
8 Woodward
It is important to use good quality terminations and proper crimping technique.
Switch Inputs: The switch inputs (VER, RST, EP) draw very little current (less than
1 mA each). The external switches should be selected for prolonged use at these
low currents. One side of the switch should be connected to battery voltage and the
other side connected to the DSS-2 switch input.
Figure 2. DSS-2 Dimensions

Manual 36598 DSS-2 Two-Channel Digital Speed Switch
Woodward 9
Table 1. Controller Wiring
FUNCTION PIN INFORMATION
Battery BAT(+), GND(-)
MPU Speed Signal Input RPM(+), RPM(-)
Channel 1 C-1, NC-1, NO-1
Channel 2 C-2, NC-2, NO-2
Verify/Start Switch VER
Reset Switch RST
Engine Protection Switch EP
ACT Connector RCV (Pin 4), TXD (Pin 3), GND2 (Pin 1)
CAUTION
To prevent damage to the controller, make sure that it is wired in
accordance with the wiring instructions and diagrams in this
manual.

DSS-2 Two-Channel Digital Speed Switch Manual 36598
10 Woodward
Controller Pinout
Use the diagram below to connect your DSS-2 controller to battery power, the mag pickup, loads,
switches and ACT.
NOTE
All cabling for the DSS-2 controller is limited to less than 3m (9.84’).
Power cabling is limited to less than 10m (32.8’) in total length. The
wiring diagram below shows specific cable types required.
Figure 3. DSS-2 Wiring Diagram

Manual 36598 DSS-2 Two-Channel Digital Speed Switch
Woodward 11
Speed Sensor Installation
Installed opposite an engine driven gear such as the
flywheel, the mag pickup (MPU) transmits a signal
each time the magnetic flux path across the pole is
interrupted by a gear tooth. The frequency of the AC
signal generated by the MPU is proportional to the
engine speed.
The mounting of the sensor unit must be rigid; excessive vibration can cause
erroneous signals and unreliable performance.
MPU output voltage is affected by tooth speed and gap size between the sensor
and the gear tooth. The higher the tooth speed, the higher the output voltage.
Conversely, the larger the sensor gap, the lower the output voltage. In general,
gap of 0.015 to 0.018” (0.38 to 046mm) is adequate for most engines and
operating speeds. If the gap cannot be measured, it may be adequate to do the
following:
1. Align a gear tooth in the center of the hole.
2. Install the MPU until the tip touches the tooth. This assumes that the
hole is tapped to the full depth and no burrs exist which preclude
moving the sensor all the way up to the tooth.
3. Unscrew the MPU approximately one-quarter to one-half turn.
4. While holding MPU position fixed, tighten lock nut.
5. Hand turn the engine one complete revolution to confirm that none of
the gear teeth contact the MPU.
Connect the speed sensor to the two rpm inputs on the controller. Most sensors
do not have a positive or negative side and can be connected either way. Use
twisted pair shielded wire for all speed sensor wiring. The shield should be
grounded at the controller only. DSS-2 requires a minimum output voltage of
2 Vac. It is recommended that the MPU output not be shared with other devices
(tachometers, etc.).
Figure 4. Speed Sensor Wiring
The frequency of the signal coming out of the MPU is related to the engine rpm as
follows:
Frequency (Hz) = RPM X nteeth/60
Where nteeth is the number of teeth on the gear adjacent to
The MPU (usually the flywheel).
Conversely:
RPM = frequency X 60/nteeth
Many hand held digital multi-meters can measure signal frequency (Hz).

DSS-2 Two-Channel Digital Speed Switch Manual 36598
12 Woodward
Chapter 4.
Calibration
Calibration Guide
This section explains the procedures for calibrating (configuring and adjusting) the
various DSS-2 features to work with your application.
Each of the two DSS-2 channels can be independently configured as:
• Speed Switch (either normal or reverse acting)
• Autocrank Controller
• Glow Plug Controller
Each of these will be addressed separately.
Before proceeding, make sure you have completed the installation of all the required
hardware for your system as discussed in Chapter 2.
Manual Calibration
DSS-2 is equipped with two operator-adjustable potentiometers, one for each
channel. These are multi-turn potentiometers that require 20-30 turns to cover the
full range of setspeeds. The potentiometers have an internal clutch to prevent
damage from overturning. The function of the potentiometer will vary depending on
how the DSS-2 is configured.
Calibration with ACT
ACT (All-purpose Calibration Tool) can be used to provide a wide variety of custom
features to the DSS-2. Refer to Chapter 5 for general information regarding
installation, connection and operation of ACT. The Calibration Wizard is the
preferred approach to ACT calibration, but similar results can be obtained using the
Calibrate/Change DSS-2 Calibration Menu item (see Chapter 5 for details). ACT is
not required as long as the channels have been previously configured as desired by
the user.
To launch the Calibration Wizard:
1. Select “Calibrate”, then
Calibration Wizard.

Manual 36598 DSS-2 Two-Channel Digital Speed Switch
Woodward 13
2. Select default values or
current values as a starting
point in the calibration. When
adjusting a DSS-2 that, for
the most part, has the
desired calibration, it is best
to use “current values”.
3. Enter the number of teeth on
the flywheel. If you wish to
work in Hz, enter a value of
60. If you wish to work in rpm,
enter the correct number of
flywheel teeth.
4. Information in the following
sections will detail how ACT
can be used to configure both
channels and the Engine
Protection (EP) input.
CAUTION
The DSS-2 is a user-configurable engine control device and will follow
your settings and commands immediately. Please be aware of this when
calibrating and entering values in the unit.
It is possible to enter values in the DSS-2 unit that are in excess of what
the engine is capable of performing and outside of safe operating range.
It is the user’s responsibility to be accurate when entering data into the
DSS-2 or the ACT. Entering values outside of safe operating range can
result in serious physical injury and/or damage to the equipment or
application.

DSS-2 Two-Channel Digital Speed Switch Manual 36598
14 Woodward
Speed Switch Configuration
As shipped from the factory, DSS-2 is configured as follows:
• Two-channel speed switch
• Normal operation
• Automatic reset at 80% of setspeed
• Range of pot adjustable set speed: 2500 to 5000 Hz
• Go to set condition on EP switch input
• Set speed reduced to 70% on VER switch input
The speed setpoints can be calibrated manually by adjusting the two potentiometers
on the front of the DSS-2 controller.
A typical speed switch installation is shown below.
In this example, Channel 1 is configured as a crank disable switch that disconnects
power to the starter motor when engine speed rises above the set speed. Channel 2
is configured as an overspeed shutdown switch that will interrupt power to the
ignition coil when an overspeed threshold is exceeded.
Figure 4. Typical Speed Switch Installation
Other manuals for DSS-2
1
Table of contents
Other Woodward Switch manuals
Popular Switch manuals by other brands

Raritan
Raritan dominion kx III user guide
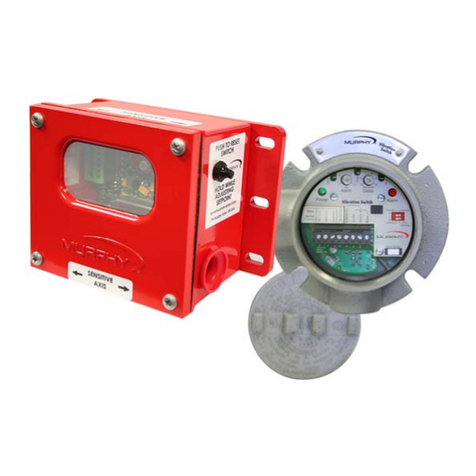
Murphy
Murphy EVS-A Specification sheet
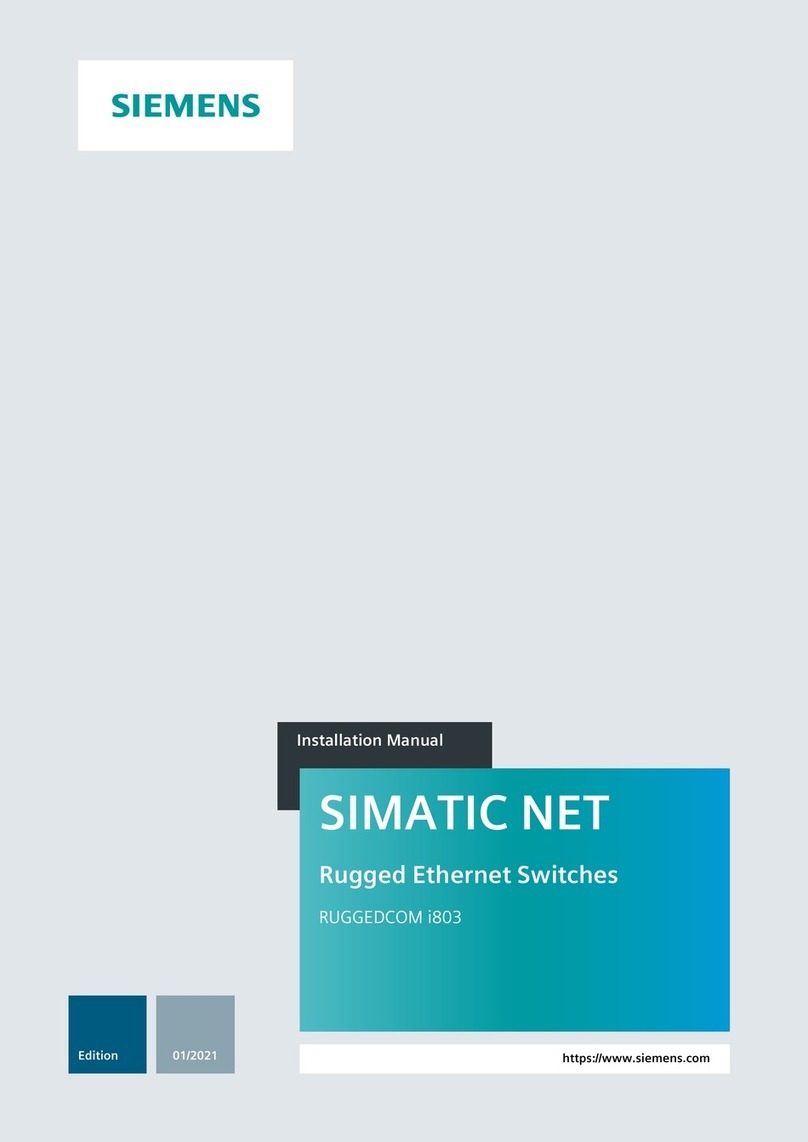
Siemens
Siemens SIMATIC NET RUGGEDCOM i803 installation manual
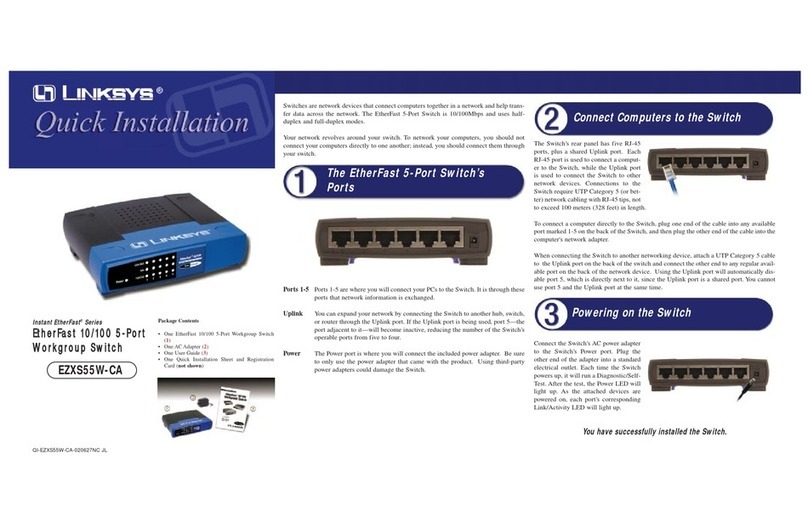
Linksys
Linksys EZXS55W - EtherFast 10/100 Workgroup Switch Quick installation
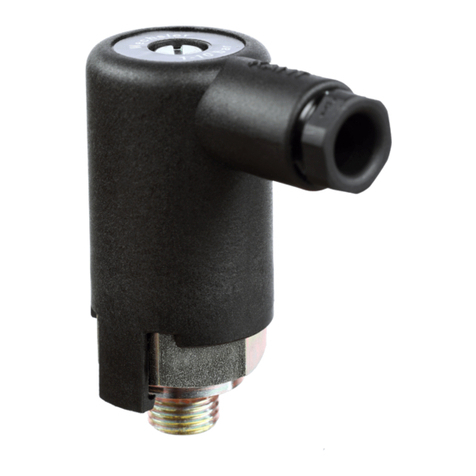
KANT Druckschalter
KANT Druckschalter 602 instruction manual

TRENDnet
TRENDnet TEG-S40SX user guide