Xinje DP3F Series User manual

1
DP3Fseries closed loop stepping driver
User manual
Wuxi Xinje Electric Co., Ltd.
Data No. D3C05 202001215 1.0

2
Basic description
Thank you for purchasing Xinje DP3F series stepping driver. Please read this product manual carefully
before operating.
The manual mainly provides the user with relevant guidance and instructions for the correct use and
maintenance of the step driver. The manual involves the function, use method, installation and maintenance
of the step driver.
The contents described in the manual are only applicable to Xinje's DP3F series stepping driver products.
Notice to user
This manual is applicable to the following personnel:
The installation personnel of stepper driver
Engineering and technical personnel (electrical engineers, electrical operators, etc.)
The designer
Before operating or debugging the stepper driver, the above personnel should carefully read the safety precautions
section of this manual.
Statement of responsibility
Although the contents of the manual have been carefully checked, errors are inevitable and we can not
guarantee that they are completely consistent.
We will always check the contents of the manual and make corrections in subsequent versions. We welcome
your comments.
The contents described in the manual are subject to change without prior notice.
Contact us
If you have any questions about the use of this product, please contact the agent and office that purchased the
product, or contact Xinje company directly.
Tel: 400-885-0136
Fax: 0510-85111290
Address: 4th Floor, building 7, creative industry park, No. 100 Dicui Road, Wuxi City
Postcode: 214072
Website: www.xinje.com
WUXI XINJE ELECTRIC CO., LTD. Copyright
Without explicit written permission, this information and its contents shall not be copied, transmitted or
used. Violators shall be liable for the losses caused.All rights provided in patent license and registration
including utility module or design are reserved.
December 2020

3
Catalog
1. PRODUCT INTRODUCTION............................................................................................................................4
1-1. MODEL NAMING RULE ......................................................................................................................................4
1-2. PERFORMANCE.................................................................................................................................................4
1-3.APPLICATION FIELD ..........................................................................................................................................4
1-4. ELECTRIC FEATURES.........................................................................................................................................4
1-5. SAFETY PRECAUTIONS......................................................................................................................................5
2. INSTALLATION AND WIRING........................................................................................................................6
2-1. INSTALLATION ..................................................................................................................................................6
2-1-1. Outline dimension....................................................................................................................................6
2-1-2. Installation environment ..........................................................................................................................7
2-2. WIRING ............................................................................................................................................................7
2-2-1. Typical wiring diagram............................................................................................................................7
2-2-2. Wiring notice............................................................................................................................................7
3. DRIVER INTERFACE ........................................................................................................................................8
3-1. STATUS INDICATOR AND TROUBLESHOOTING ....................................................................................................8
3-2. UPPER COMPUTER COMMUNICATION INTERFACE ..............................................................................................8
3-3. CONTROL SIGNAL INTERFACE ...........................................................................................................................9
3-3-1. Function...................................................................................................................................................9
3-3-2. Control signal circuit.............................................................................................................................10
3-4. ENCODER SIGNAL INPUT TERMINAL................................................................................................................ 11
3-5. MOTOR AND POWER SUPPLY INTERFACE ......................................................................................................... 11
3-5-1. Strong current interface function........................................................................................................... 11
3-5-2. Power supply requirements....................................................................................................................12
4. DIP SWITCH ......................................................................................................................................................13
4-1. DIPSWITCH FUNCTIONS .................................................................................................................................13
4-2. 5V/24V SWITCH .............................................................................................................................................14
5. DRIVER PARAMETERS..................................................................................................................................15
6. COMMON TROUBLESHOOTING.................................................................................................................20

4
1. Product introduction
1-1. Model naming rule
Take DP3F-705 as an example:
DP3F - 70 5
① ② ③
①: DP3F series closed loop stepping driver
②: Driver output maximum peak current 7A
③: The maximum supply voltage of the driver is 50VDC
1-2. Performance
⚫The encoder is used as position feedback, which can compensate the position deviation in real time, and
solve the problem of losing step of traditional stepping motor
⚫The current can be adjusted in real time according to the load and speed, so that the operation is more
stable and the motor heating is lower
⚫Compared with the open-loop stepping, the high-speed performance of the motor is significantly
improved
⚫The pulse and direction input voltage supports 5V and 24V, which can be set by sliding switch
⚫4-bit DIP switch, 16 levels subdivision can be set to meet the needs of most customers
⚫The rotation direction of the motor can be changed by switch
⚫It has power on auto-tuning function, can be set by switch
⚫It supports single and double pulse mode, can be set by switch
⚫Support smoothing time, can be set by switch and convenient for debugging and improves the stability
of motor operation
⚫Two digital input signals: enable signal input and alarm clear signal input
⚫Three digital output signals: alarm signal output, in place /Z signal output, brake signal output
⚫It has over-current, over-voltage, rotation blocking detection, out of step compensation and other
protection functions
1-3. Application field
It is suitable for all kinds of small and medium-sized automation equipment and instruments, such as engraving
machine, stripping machine, marking machine, cutting machine, laser machine, plotter, medical equipment, CNC
machine tool, automatic assembly equipment, electronic processing equipment, etc.
1-4. Electric features
Model
DP3F-305
DP3F-705
DP3F-808
Input power supply (VDC)
20~50
20~50
20~80
Output peak current (A)
1~3
1~7
1~8.4
Matched motor (base)
42
57/86
86
Step pulse frequency (KHz)
24V signal 200K, 5V differential signal 500K
Control signal input voltage (VDC)
5/24 (Sliding switch setting)

5
Model
DP3F-305
DP3F-705
DP3F-808
Using
environment
Using location
Try to avoid dust, oil mist and corrosive gas
Ambient temperature
0℃~50℃
Max working temperature
60℃
Humidity
40%~90%RH (No condensation or water droplets)
Vibration
5.9m/s2 Max
Storage temperature
-20℃~65℃
1-5. Safety precautions
(1) The drive must be installed and operated by professional technicians!
(2) The input voltage of the driver must meet the technical requirements!
(3) It is strictly forbidden to plug the strong current terminal of the driver when the power is on. When the motor
stops, there is still a large current flowing through the coil. Plug the strong current terminal will produce a huge
instantaneous induced electromotive force, which will burn the driver!
(4) Before power on, please ensure the correctness and firmness of power cable, motor cable and signal cable
connection!
(5) Avoid electromagnetic interference!

6
2. Installation and wiring
2-1. Installation
2-1-1. Outline dimension
⚫DP3F-305, DP3F-705 Unit: mm
31 77
110
102.6 4
21.8 5.2
∅4.3
∅4.3
⚫DP3F-808 Unit: mm
35.5 86.7
135
127.9
25.3
∅4.3
∅4.3
3.8
5.2

7
2-1-2. Installation environment
The reliable working temperature of the driver is usually within 60℃and that of the motor is within 80℃. To
ensure that the driver works within the reliable working temperature range, the driver should be installed in the
electric cabinet with good ventilation and proper protection. If necessary, a fan should be installed near the driver
for forced heat dissipation.Avoid being used in dust, oil mist, corrosive gas, high humidity and strong vibration.
2-2. Wiring
2-2-1. Typical wiring diagram
2-2-2. Wiring notice
(1) The pulse and direction signal cables and motor cables are not allowed to be bound side by side, and it is better
to separate them at least 10cm, otherwise it is easy to interfere with the pulse direction signal, resulting in
inaccurate motor positioning, system instability and other problems.
(2) If a power supply supplies multiple drives, parallel connection should be adopted at the power supply, and
chain connection from one to another is not allowed.
(3) It is strictly forbidden to connect the wire head to the terminal after adding tin, otherwise the terminal may be
damaged due to overheating due to increased contact resistance.
(4) The wiring head should not be exposed outside the terminal to prevent accidental short circuit from damaging
the driver.

8
3. Driver interface
3-1. Status indicator and troubleshooting
The green LED is the power indicator. When the driver is powered on, the LED is always on; When the drive is
powered off, the LED goes out.
The red LED is the fault indicator. When there is a fault, the indicator will flash continuously, then stop for one
second, and then flash continuously. When the fault is cleared by the user, the red LED is always off.
The continuous flashing times of red LED represent different fault information, and the specific relationship is
shown in the table below. The alarm output terminal outputs high level.
Flashing times
Fault
Solution
1
Over current or short
circuit
Check the power cable for short circuit
2
Over voltage
Check whether the power supply voltage is too high
3
Under voltage
Check whether the power supply voltage is too low
4
Motor open circuit or
poor contact
Check whether the power cable is well installed or
broken
5
Position over limit
Check whether the encoder cable is broken, check
whether the motor is blocked, and increase the
acceleration time appropriately
Note: since the driver does not have the function of reverse connection protection of positive and negative poles of
power supply, please confirm that the wiring of positive and negative poles of power supply is correct again
before power on. The reverse connection of positive and negative poles will burn out the safety tube in the driver.
3-2. Upper computer communication interface
The definition of RS232 interface pin arrangement is as follows:
Pin
Function
Note
1
VCC
Power supply +
2
WT
Data write
3
WR
Data read

9
4
ID
Vacant
5
GND
Power supply ground
Note: the upper computer can set the subdivision and other functions. When SW1-SW4 are all on, the upper
computer can set the subdivision, please power on again after setting. Other switch status is subject to dialing
setting.
3-3. Control signal interface
3-3-1. Function
Signal
Function
Explanation
PUL+
Pulse control signal
The 5/24 VDC pulse input signal can be selected by dialing code, and the
pulse edge can be changed through the upper computer according to the
demand. The rising edge is valid by default.
(!!! Note: the input of 24V signal will damage the input terminal when
5 V is selected.)
PUL-
DIR+
Direction control
signal
DIR-
ENA-
Enable input signal
Two channels of input signal, support 24V signal
RST-
Alarm clearing input
signal
COM+
Input signal common
terminal
ALM+
Alarm output signal
Three output signals, maximum saturation output 50 mA, maximum 24
VDC. Pend+/Z terminal default is in place signal, the customer can
modify the in place signal to Z signal through the upper computer
according to the demand.
Pend+/Z
In place/Z signal
output
BRK+
Brake output signal
COM-
Output signal
common terminal

10
3-3-2. Control signal circuit
Control signal input and output circuit diagram, as shown in the figure below:
Differential mode input
Input single ended common anode connection method
Input single ended common cathode connection

11
3-4. Encoder signal input terminal
Pin
Name
NC
Reserved
NC
Reserved
NC
Reserved
NC
Reserved
VCC
5V power output, provided by driver, only used for encoder power
supply
GND
EZ+
Encoder Z phase signal +
EZ-
Encoder Z phase signal -
EB+
Encoder B phase signal +
EB-
Encoder B phase signal -
EA+
Encoder A phase signal +
EA-
Encoder A phase signal -
3-5. Motor and power supply interface
3-5-1. Strong current interface function
Interface
Function
Explanation
A+, A-
Motor phase A coil
Cannot change direction by exchanging A+, A-
B+, B-
Motor phase B coil
Cannot change direction by exchanging B+, B-
GND
DC power supply
ground
DC power supply ground
+V
DC power supply
positive pole
Select the voltage according to the demand
Note:
DP3F-305 range is 20~50VDC: recommended value is 24~36VDC.
DP3F-705 range is 20~50VDC: recommended value of 57 motor is 24 ~ 36VDC, recommended value of 86

12
motor and high-speed application is 48V.
DP3F-808 range is 20~80VDC: recommended value is above 48V.
3-5-2. Power supply requirements
The power supply voltage can work normally within the calibration range. The driver should preferably use
non-regulated DC power supply, or use transformer + bridge rectifier + capacitor filter. It is recommended that
users use 24V-48VDC power supply to avoid grid fluctuation exceeding the working range of driver voltage. If
the regulated switching power supply is used, the switching power supply output current range should be set to the
maximum.
Note:
(1) Do not reverse the power supply voltage!
(2) Do not exceed the working range of the power supply to ensure the normal operation of the driver.
(3) The power supply should be non-regulated DC power supply, and the output capacity of the power supply
should be greater than 60% of the set current of the driver.
(4) If the stabilized voltage switching power supply is used for power supply, the output current range of the
power supply should be greater than the working current of the motor.
(5) In order to save space, two or three drives can share one power supply, but the power supply should be large
enough.

13
4. DIP switch
DP3F series drivers adopt 10 digit DIP switch to set subdivision precision and driver related function settings.
Detailed description is as follows:
SW1SW2SW3SW4SW5SW6SW7SW8SW9SW10
Subdivision Smooth filter
Closed/open loop
Auto-tuning
Motor initial operation
direction Single/double pulse
4-1. DIP switch functions
SW1-SW4 is used for subdivision setting, as shown in the following table:
Step
SW1
SW2
SW3
SW4
Default, set by upper computer
(4000)
On
On
On
On
800
Off
On
On
On
1600
On
Off
On
On
3200
Off
Off
On
On
6400
On
On
Off
On
12800
Off
On
Off
On
25600
On
Off
Off
On
51200
Off
Off
Off
On
1000
On
On
On
Off
2000
Off
On
On
Off
4000
On
Off
On
Off
5000
Off
Off
On
Off
8000
On
On
Off
Off
10000
Off
On
Off
Off
20000
On
Off
Off
Off
40000
Off
Off
Off
Off
The specific functions of SW5-SW10 are as follows:
Switch
Function
ON
OFF
SW5
Initial direction selection
of motor
CW (face the shaft end)
CCW (face the shaft end)
SW6
Power on auto-tuning
The driver parameters are not
automatically set when the power
is on
When the power is on, the driver
parameters are automatically set

14
Switch
Function
ON
OFF
SW7
Control signal pulse mode
Double pulse (CW/CCW)
Pulse+ direction
SW8
Open/closed loop
Open loop
Closed loop
SW9
SW10
Smooth filter
1.5ms, 3ms, 12ms instruction filtering time can be set in combination
Smooth time
SW9
SW10
Set by the upper computer
(default 1.5ms)
ON
ON
3ms
ON
OFF
12ms
OFF
ON
Shut down the filter
OFF
OFF
4-2. 5V/24V switch
DP3F can select the 5V/24V pulse and the direction input level through this switch. The default is 24V.
Function
Description
5V
The input level of pulse direction is 5V
24V
The input level of pulse direction is 24V
Note: according to the actual needs, the state of the slide switch should be set correctly to avoid the damage of the
port.

15
5. Driver parameters
DP3F series driver parameters can be set by PC. The driver has a set of best default configuration parameters
corresponding to the motor, which does not need to be adjusted normally. Refer to the table below for specific
parameters and functions.
Group P0: basic function
Parameter
Address
Function
Range
Default
Note
P0-01
0x0001
Subdivision
200~51200
4000
Subdivision switch takes effect when
all on, and the rest of the switch status
is subdivision setting
P0-02
0x0002
Pulse filter
1~240
30
Filter switch takes effect when all on,
and the rest of the switch status is
filter setting
P0-03
0x0003
Closed loop
current
percentage
1~100
100
Maximum current percentage in
closed loop mode
Maximum current in closed loop
mode=
Percentage of closed loop current % ×
peak current
P0-04
0x0004
Internal pulse
0~1
0
Internal pulse operation mode:
0: external pulse; 1: internal pulse
P0-05
0x0005
Open loop
current
percentage
1~100
50
Operating current in open loop mode
=
Percentage of open loop current % ×
peak current
P0-06
0x0006
Open/closed loop
mode
0~1
1
0: open loop mode; 1: closed loop
mode
P0-07
0x0007
Pulse edge
0~1
0
0: rising edge; 1: falling edge
P0-08
0x0008
Pulse mode
0~1
1
0: double pulse; 1: pulse + direction
P0-09
0x0009
Closed loop
holding current
percentage
1~100
50
Percentage of holding current in
closed loop mode
Closed loop holding current =
Percentage of closed loop holding
current % × Maximum current in
closed loop mode
Group P1: gain control parameters
Parameter
Address
Function
Range
Default
Note
P1-00
0x0100
Auto-tuning
0~1
1
0: off; 1: on
P1-01
0x0101
Current Kp
1~65535
1500
P1-02
0x0102
Current Ki
1~65535
400
P1-03
0x0103
Current kd
0~65535
0
P1-04
0x0104
Current Kc
0~65535
0
P1-05
0x0105
Speed Kp
1~65535
60
P1-06
0x0106
Speed Ki
0~65535
0
P1-07
0x0107
Position Kp
1~65535
2200

16
P1-08
0x0108
Position Ki
0~65535
500
P1-09
0x0109
Back EMF
1~300
50
P1-10
0x010A
Weak magnetic
coefficient
1~100
20
P1-11
0x010B
Inductance
1~10000
1000
P1-12
0x010C
Startup delay
1~10
1
P1-13
0x010D
In place delay
0~100
3
P1-14
0x010E
In place error
0~100
4
Group P2: IO configuration parameters
Parameter
Address
Function
Range
Default
Note
P2-00
0x0200
Motor enable
0~1
0
0: not enable 1: enable
P2-01
0x0201
Z phase output
0~1
0
0: high level 1: low level
P2-02
0x0202
Alarm output
0~1
0
0: high level 1: low level
P2-03
0x0203
Brake output
0~1
0
0: high level 1: low level
P2-04
0x0204
In place output
0~1
0
0: high level 1: low level
P2-05
0x0205
Alarm clear
0~1
0
0: high level 1: low level
Group P3: protection function parameters
Parameter
Address
Function
Range
Default
Note
P3-00
0x0300
Tracking error limit
1~65535
4000 (1 turn)
P3-01
0x0301
Fault detection
selection
0~65535
255
P3-02
0x0302
Under voltage alarm
threshold
0~20
0
When the default value is 0,
the alarm is shielded
Group P4: motor parameters
Parameter
Address
Function
Range
Default
Note
P4-00
0x0400
peak current
305: 1~30
705: 1~70
808: 1~84
305: 25
705: 60
808: 74
0.1A
P4-01
0x0401
Encoder
resolution
200~20000
4000
Quadruple frequency,
modification not supported
P4-02
0x0402
Operation
direction
0~1
0
0: counter clockwise; 1: clockwise
Group P5: self-operation parameters
Parameter
Address
Function
Range
Default
Note
P5-00
0x0500
Self-operation
mode
0~1
0
0: infinite pulse 1: set pulse
P5-01
0x0501
Pulse high
byte
0~65535
0
P5-02
0x0502
Pulse low
byte
0~65535
4000
Pulse number = pulse high byte×65535+pulse
low byte
P5-03
0x0503
Speed
0~2000
200
rpm
P5-04
0x0504
Acceleration
1~2000
200
rpm/s

17
speed
P5-05
0x0505
Direction
0~1
0
0: counter clockwise; 1: clockwise
P5-06
0x0506
shuttle run
0~1
0
0: single direction 1: double direction
P5-07
0x0507
Repeat
0~2
0
0: not repeat 1: repeat times 2: always repeat
P5-08
0x0508
Repeat times
0~65535
0
P5-09
0x0509
Repetition
interval
0~65535
1000
ms
P5-10
0x050A
Startup speed
0~2000
200
rpm
P5-11
0x050B
Stop speed
0~2000
200
rpm
P5-12
0x050C
Operation
status
0~3
0
0: idle 1: run 2: deceleration stop 3: emergency
stop
Group P7: communication parameters
Parameter
Address
Function
Range
Default
Note
P7-00
0x0700
Driver station
no.
1~100
1
P7-01.0
0x0701.0~1
Baud rate
03:2400
04:4800
05:9600
06:19200
07:38400
08:57600
09:115200
0A:192000
0B:256000
0C:288000
06
Default 19200bps, 1 stop bit, even
parity
P7-01.2
0x0701.2
Stop bit
0: 2 bits
2: 1 bit
2
P7-01.3
0x0701.3
Parity bit
0: no parity
1: odd
parity
2: even
parity
2
P7-02
0x0702
Communication
protocol
0~1
1
1: Modbus, 0: others
P7-03
0x0703
Reserved
1~65535
1
P7-04
0x0704
Reserved
1~65535
1
Group U0
Parameter
Address
Content
Note
U0-00
0x1000
Set speed
rpm
U0-01
0x1001
Feedback speed
rpm
U0-02
0x1002
Encoder quantity
0~15 bits
Encoder pulse
U0-03
0x1003
16~31 bits
U0-04
0x1004
32~47 bits
U0-05
0x1005
48~62 bits, 63: direction bit
U0-06
0x1006
Feedback pulse numbers
0~15 bits
Command pulse

18
Parameter
Address
Content
Note
U0-07
0x1007
16~31 bits
U0-08
0x1008
32~47 bits
U0-09
0x1009
48~62 bits, 63: direction bit
U0-10
0x100A
Pulse numbers
0~15 bits
Command pulse
U0-11
0x100B
16~31 bits
U0-12
0x100C
32~47 bits
U0-13
0x100D
48~62 bits, 63: direction bit
U0-14
0x100E
Position offset
0~15 bits
Command pulse
U0-15
0x100F
16~31 bits
U0-16
0x1010
Single turn encoder
counting value
0~15 bits
Encoder pulse
U0-17
0x1011
16~31 bits
U0-18
0x1012
Single turn pulse
counting value
0~15 bits
Command pulse
U0-19
0x1013
16~31 bits
U0-20
0x1014
Pulse turns
0~15 bits
U0-21
0x1015
16~31 bits
U0-22
0x1016
Encoder turns
0~15 bits
U0-23
0x1017
16~31 bits
U0-24
0x1018
Feedback electric angle
U0-25
0x1019
Set electric angle
U0-26
0x101A
A phase feedback current
mA
U0-27
0x101B
B phase feedback current
mA
U0-28
0x101C
Reference feedback current
mA
U0-29
0x101D
A phase set current
mA
U0-30
0x101E
B phase set current
mA
U0-31
0x101F
Reference set current
mA
U0-32
0x1020
Bus voltage
V
Group U1 monitor parameters
Parameter
Address
Content
Note
U1-00
0x1100
Present alarm code
U1-01
0x1101
Phase A current when alarm occurs
U1-02
0x1102
Phase B current when alarm occurs
U1-03
0x1103
Reference current when alarm occurs
U1-04
0x1104
Bus voltage when alarm occurs
U1-05
0x1105
Position offset when alarm occurs
U1-06
0x1106
Speed when alarm occurs
U1-07
0x1107
The time when alarm occurs
0~15 bits
U1-08
0x1108
The time when alarm occurs
16~31 bits
U1-09
0x1109
Error numbers for this time operation
U1-10
0x110A
Latest 2nd alarm code
U1-11
0x110B
Latest 3rd alarm code
U1-12
0x110C
Latest 4th alarm code
U1-13
0x110D
Latest 5th alarm code
U1-14
0x110E
Latest 6th alarm code

19
Group U2 monitor parameters
Parameter
Address
Content
Note
U2-00
0x1200
Power on times
U2-01
0x1201
Machine type
U2-02
0x1202
Series
U2-03
0x1203
Model
U2-04
0x1204
Firmware generation date
Year
U2-05
0x1205
Firmware generation date
Month
U2-06
0x1206
Firmware generation date
Day
U2-07
0x1207
Software version
U2-08
0x1208
Hardware version
U2-09
0x1209
Power on operation time
Hour
U2-10
0x120A
Power on operation time
Minute
U2-11
0x120B
Power on operation time
Second
U2-12
0x120C
Device serial number
0~15 bits
U2-13
0x120D
Device serial number
16~31 bits
U2-14
0x120E
Firmware generation date
Year
U2-15
0x120F
Firmware generation date
Month /day
U2-16
0x1210
Firmware generation date
Hour /minute

20
6. Common troubleshooting
Fault
Reason
Solution
The power light doesn't
work
Power supply system error
Check the power supply
circuit
Low supply voltage
Increase the power supply
voltage
The motor doesn't work
The current setting is too small
Set suitable current
The subdivision is too large
Set suitable subdivision
Protection circuit action
Power on again
Release signal is low
Do not connect this signal
Not power on
Power on again
Motor wiring error
Check the wiring
No pulse signal input
Check the pulse cable and
signal voltage
Motor direction is error
Line failure
Check the circuit
Alarm light is on
Motor cable connection error
Wiring again
Voltage too high or too low
Adjust the power supply
voltage
Motor or driver damaged
Check the motor and driver
Motor torque is small
Acceleration is too fast
Decrease the acceleration
value
The model selection is not suitable
Select the model again
This manual suits for next models
3
Table of contents
Other Xinje DC Drive manuals
Popular DC Drive manuals by other brands

Inovance
Inovance MD330H user manual

Aerotech
Aerotech Soloist HPe 10 Hardware manual

American Control Electronics
American Control Electronics LGC400 quick start guide
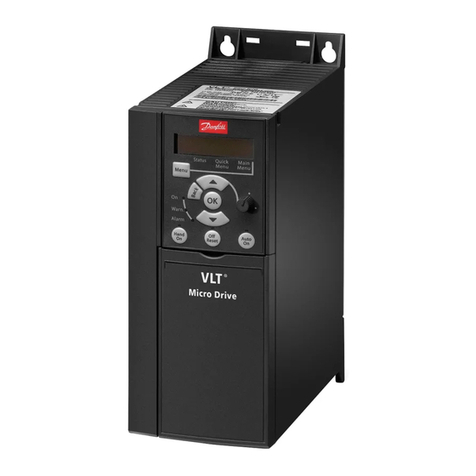
Danfoss
Danfoss VLT Micro Drive FC 51 Series operating guide
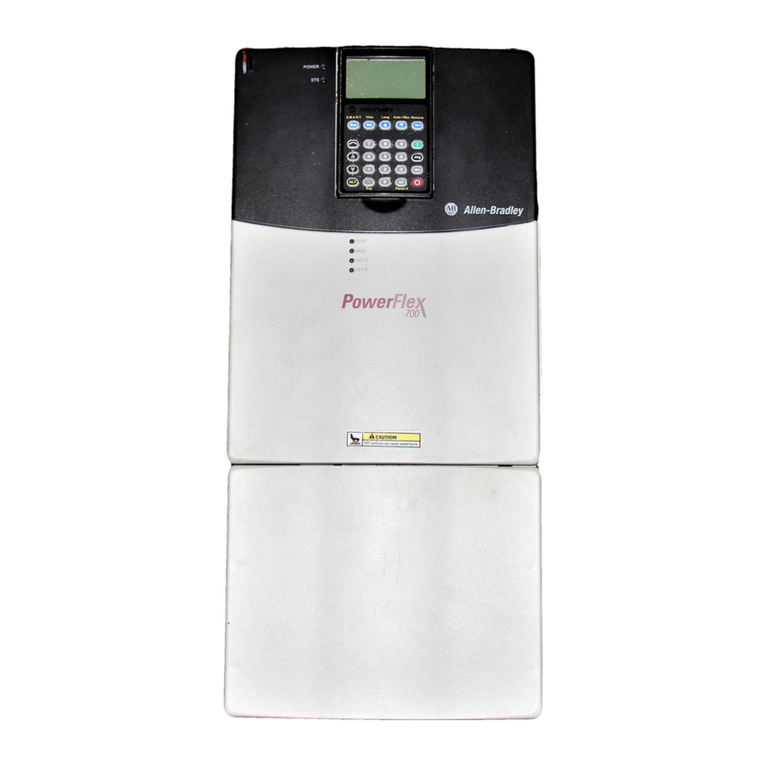
Allen-Bradley
Allen-Bradley powerflex 700 quick start guide
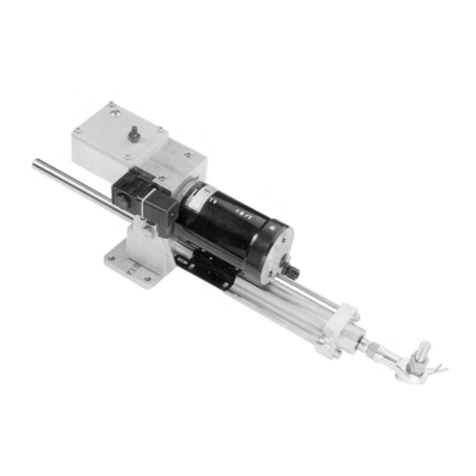
Kongsberg
Kongsberg Simrad HLD350 MK2 instruction manual