Xsensor CLMI X-232 User manual

Manuel_X_232_EN 1 / 13 27.01.2016
X-Sensors AG
Landenbergerstrasse 13
CH-8253 Diessenhofen
T: Intl. (0)52 657 38 77
F: Intl. (0)52 741 47 66
Configurable Load Measuring Interface CLMI X-232
Operation Manual Rel.: Jan. 2016
Table of content
General technical informations...................................................... 2
Content of delivery................................................................ 2
Introduction & usage............................................................. 2
Mecanical dimensions........................................................... 3
Configurations....................................................................... 3
Degree of protection, mounting ............................................ 3
Installation........................................................................................ 4
Some reflections to the minimum load measurement .......... 4
Background information about the floor detection................ 4
Truth table of the external sensor......................................... 5
Electrical installation ............................................................. 5
Typical installation, minimum configuration.......................... 6
Advances installation............................................................ 6
Commissioning................................................................................ 7
Commissioning, easy installation.......................................... 7
Commissioning, advanced installation.................................. 7
Description of in- and outputs............................................... 8
Position and orientation of the terminals............................... 8
Programmable functions....................................................... 9
Setup menu........................................................................... 9
Menu-structure.................................................................... 10
Technical data..................................................................... 11
Troubleshooting, diagnostic ........................................................ 11
Frequently asked questions (FAQ)..................................... 11
Installation, general rules.................................................... 12
Maintenane, repairing......................................................... 12

Manuel_X_232_EN 2 / 13 27.01.2016
1. General technical informations
Content of delivery
Introduction & Usage
Ident-Number 5926 1534
Ident-Nummer 5926 1535
X-232-AC
Configurable load measuring interface for mains operation
115VAC/230VAC switchable
- incl. attaching plug
- incl. 2m access line mains, free end
- incl. 2m access line control, free end
Device is connected to the power line by user. CLMI is supplied with all
necessary material.
X-232-DC
Configurable load measuring interface for 24VDC operation
- incl. attaching plug
- incl. 2m access line control, free end
Device is connected to the power line by user. CLMI is supplied with all
necessary material.
The CLMI (Configurable Load-Measuring Interface) connects the load measuring sensor to the control unit. The
CLMI continuously compares the measured load to the programmed limits and if necessary activates the
analogous switching output. The switching outputs are connected to the control unit and they send the signal of
the load to the control unit. The relay contacts are provided for:
- Car Empty
- full load (90% group travelling, reduces intermediate stops)
- overload
These values are easily programmable without any means such as the CLMI can be individually adjusted to the
task.
Attention: Depending on execution, the plugs maybe live. Do never handle the CLMI with metal tools and if
necessary disconnect the device from the mains before you start to work with.
Devices constantly connected to the electric circuit must be connected to a circuit breaker (fuse, etc.). It must be
marked as safeguard.
Check the supply voltage before connecting the device. Make sure, that you operate this device only if
you aren’t electrostatic charged and if the device is correctly grounded.
The supply cable must be separate from the signal cable and must not be installed in the same wire. The signal
cable must be shielded and the cable shield must be connected to the grounding clip.
Important advice:
Before commissioning acquaint yourself with the
programming and functionality of this device and
read this manual carefully.

Manuel_X_232_EN 3 / 13 27.01.2016
Mechanical Dimensions
Configurations, depending on Application
The CLMI X-232 is not bound to a special sensor. Following sensors and installations are contemplable:
Installation
Sensor
Equipment
Accuracy (*)
Empty Car
Yoke
X-109-S02-300
Ident: 59343199
Extension cable
35kg
Yes –with
restrictions
Yoke
2x
X-109-S02-300
Ident: 59343199
Extension cable
20kg
Yes –with
restrictions
Fixed point
X-130-Sxx
4kN 56014397
8kN 56014398
12kN 56015256
Extension cable
40kg
Yes –with
restrictions
Below the car
X-133-Sxx
Extension cable
Junction Boxes for
two sensors
5kg
Yes –without
restrictions
Below the ground
X-133-Sxx
Extension cable
Junction Boxes for
two sensors
2kg
Yes –without
restrictions
(*) heavily depends on the installation
If more than two sensors are connected to the CLMI, a junction box of the series X-914 will be required.
The CLMI sends a digital 0V/24V breaker signal and a relay contact as output signal.
Drill Layout
Degree of Protection, Mounting
The CLMI has the access openings only at the lower side. During the mounting make sure the device is vertically
installed with the access openings and the cable passage at the lower side.
In this way the degree of protection IP22 can be reliably achieved.
Vertical mounting, in this case well protected
by the journal of the yoke

Manuel_X_232_EN 4 / 13 27.01.2016
2. Installation
Some Reflections to the Minimum Load Measurement
Background Information about the Floor Detection
The paragraph “Configurations“has explained that the CLMI is potentially able to perform a minimum load measurement. For this
purpose following provisions has been made:
- The possibility to compensate the error factor of the travelling cable (floor detection). The floor detection should be
activated if the maximum weight of the travelling cable amounts 25% of the minimum load.
Example: A minimum load measurement of 40 kg is required. The height of the elevator shaft amounts 12m and the
weight of the travelling cable is 1,5kg/m. According to this, the travelling cable (6m) itself affects the zero point for 9kg
what corresponds 23%. The floor detection must be activated.
- Prevention of the slow drift of the zero point (e.g. at outdoor elevator shafts and variation of temperature). This function
is always on.
The chosen strategy is important to the achievable accuracy. A schedular rating:
Rank
Installation
Sensor
Equipment
Accuracy
Zero Load
1
Below the ground
X-133-Sxx
Extension cable
Junction Boxes for 4
sensors
2kg
Yes –without
restrictions
2
Below the car
X-133-Sxx
Extension cable
Junction Boxes for 4
sensors (X-914)
5kg
Yes –without
restrictions
3
Yoke
2x
X-109-S02-300
Extension cable
(only if needed)
The CLMI is already
prepared for
connecting two
sensors.
20kg
Yes –with
restrictions
4
Yoke
X-109-S02-300
Extension cable
(only if needed)
35kg
Yes –with
restrictions
5
Fixed point
X-130-Sxx
Extension cable
(only if needed)
40kg
Yes –with
restrictions
Rank 1 and 2: Achievable accuracy does not depend on the suspension of the car, slide guide, etc..
Universal, very accurate measuring strategy but often an inconvenient execution.
Rank 3: Best choice for yoke measurement. By installing a sensor on each journal, torsion forces and
asymmetric bend phenomenon are effectively compensated.
Rank 4: Easy, robust measuring method, can be used everywhere. Widespread at modernizations.
Friction, hysteresis (etc.) at the slide guidance affect the measurement result.
An optimal choice of the measuring position (point at joke with the biggest elongation) can
reduce the error. If possible use a very elastic yoke.
Rank 5: Another easy and robust method. This solution suits in every case where no suitable yoke is available.
Beside the already mentioned errors of the slide guidance caused by friction, the errors of the unequal load distribution
in the cable additionally affect the measurement.
In this case a measurement with two force sensors significantly improves the accuracy, by simultaneously measuring
all cable loads 100% with two sensors.
The CLMI calculates with the floor information the weight of the travelling cable and automatically subtracts
this weight from the measured value. So the zero point remains constant on each floor.
For this process, the CLMI needs information about the car’s floor position. The CLMI can receive this
information through a parallel 6Bit wide interface. The information can be transmitted in Gray code or in
binary code. The signalling lines must be positive switching but the code can be also processed in inversed
logic. (See “Technical Data”and “Setup Menu”)
Control the function of the floor detection by reading the code in the test menu of the CLMI. (See paragraph
“Advices about Commands”and “FAQ“)
The signal “Synch“shows the validity of the code from Bit0 to Bit5. A logic “1” (active) signifies the validity of
the code, and the CLMI evaluates the floor information and load information.
If the signal “Synch“is a logic “0“, the measurement, the current status of the readout and switching status will
be frozen. There won’t be an evaluation of the load information. The polarity of this logic can be inverted by
changing the parameter “L”, refer to the truth table below.
When the floor detection is online, the signal “Synch“ can even be used by putting the signal “Door Open” on
the signal “Synch”. The load is only measured as long as the door is open. So, unwanted signals will be
disabled during the ride.
Please note that the signals are galvanically separated and a separate reference potential is needed!
Parameter in the setup menu: E=x, F=x, C=x, L=?, S=x, P=x, I=x, A=x, H=x (x= 0 or 1)
Programmed parameter
L=
Input level “Synch“
Comment/Result
0 = (0-active)
0V/ not connected
Measurement is active mode
0 = (0-active
1
current readout and switching
status is frozen
1 = (1-active)
1
Measurement is active mode
1 = (1-active)
0/ not connected
current readout and switching
status is frozen

Manuel_X_232_EN 5 / 13 27.01.2016
“Truth table” of the external Sensor
External Sensor, Motion Detector
Parameter in the Setup Menu: E=1, F=x, C=x, L=x, S=1, P=x, I=x, A=x, H=x (x= 0 or 1)
Measured
Load
Programmed
Value in PE
Breaker Signal
Motion Detector
Switching Output
Minimum Load
(KL3)
Comment
17kg
40kg
High/open
Activated
Load measurement detects minimum
load, motion detector detects no motion
25kg
40kg
Low (0V)
Not activated
Load measurement detects minimum
load, but motion detector detects motion
(person inside the car)
80kg
40kg
High/open
Not activated
Load measurement detects no minimum
load, motion detector detects no motion
(e.g. packet or palett is inside the car)
80kg
40kg
Low (0V)
Not activated
Load measurement detects no minimum
load, motion detector detects motion
(person inside the car)
The CLMI can connect the breaker signal of an external motion detector to the measured load. If the
parameter “S” is set to 1, the input (X5, Pin1) of the external sensor will be activated. The switching output
which shows the status “Minimum Load” will only be activated if a logical 1 is present at this input.
Electrical installation
Advices:
Before the commissioning, control if the
mains voltages are correctly chosen.
Please note the relevant ground and
isolation instructions.
Switch electric loads over 20mA with the
relay contacts, not with the control outputs.
If the CLMI is operated with mains voltage,
the 24V terminal (X1, Pin 1) as supply
output may be loaded with maximal 70 mA.
The terminal might serve to supply an
external overload indicator with 24V.

Manuel_X_232_EN 6 / 13 27.01.2016

Manuel_X_232_EN 7 / 13 27.01.2016
Typical Installation, minimum configuration
Advanced Installation
In the easiest variant, a yoke sensor is connected to the CLMI. The relay contact “overload”is then wired to the appropriate input of the
control unit. After commissioning, the CLMI with the relay contact reports the overload to the control unit.
Beside the basic functions the CLMI X-232 offers some expansions:
- Compensation of the weights of the travelling cables
- Input for external motion detector
- Advanced software functions
In this case the +24V wire (Pin 1 at X1) is the output, i.e. it supplies the external overload indicator.

Manuel_X_232_EN 8 / 13 27.01.2016
3. Commissioning
Commissioning, easy Installation
(Full- and overload measurement)
Commissioning, Advanced Installation
(Measurement with minimum load and floor detection)
Wire the supply, sensors and alarm output according to the electrical installation.
Turn on the supply –the display shows a random number, now.
Preparation
Acquaint yourself with functions in the setup menu and set these functions relative to your installation and desires.
A) Programming of the Options in the Setup Menu
1. Press UP at least 10 seconds until E_x appears.
2. You are in the setup menu, now.
3. Set E, F, C, L, S, P and I to 0 provided these parameters aren’t already set 0.
4. Set A to 10 (on-delay = 1 second)
5. Set H to 12 (switch hysteresis 12kg)
6. Wait 10 seconds, the setup menu will be automatically quitted.
Please note: Point A may be shortened, by executing a general reset. (See paragraph “Advices to Commands”)
B) Parameterization of the Load Measurement
7. Make sure the car is empty.
8. Press RIGHT –P0 appears.
9. By pressing UP/DOWN the readout is changed to the desired value when the car is empty. (*)
10. Press RIGHT –P1 appears.
11. Set P1 to 0 by using UP/DOWN.
12. Press RIGHT –P2 (full load) appears.
13. By pressing UP/DOWN set P2 for the maximal allowed car load.
14. Press RIGHT –P3 (overload) appears.
15. By pressing UP/DOWN set P3 to 110% of the maximal allowed car load (therefore consult the information of the car/elevator
manufacturer and the relevant norms)
16. Load the car with the maximal allowed car load.
17. Execute 3 to 6 rides with the elevator.
18. Press RIGHT until P4 appears (teach-in nominal load).
19. By pressing UP/DOWN set P4 to the maximal allowed car load. If necessary add your body weight.
20. Press 1x RIGHT or wait 10 seconds.
21. The device returns to the display mode and it is ready, now.
C) Control the Commissioning
22. During the following unloading, control if the readout proportionally drops to the load reduction.
23. If the display doesn’t exactly drop to 0 afterwards, you can teach-in the zero point in P0 again.
24. Load the car again with 50%...80% of the nominal load and observe the changes on the display
25. If there are large aberrations, teach-in P4 again. Control the installation of the sensors and the behaviour of the car in its
guidance (friction!).
26. Complete the final tests according to the instructions of the elevator manufacturer.
(*) Variant 1
Usually the readout is set 0(kg) when the car is empty. But if the installer is on the top side of the car and his weight affects the
measurement, he must program his own body weight (not 0kg). After leaving the top side, the readout drops to 0.
(*) Variant 2
The readout is set 0 kg, although the installer is on the top of the car. After the last key pressing (UP or DOWN), the installer MUST
NOT press RIGHT but leave the top side of the car. After 10 seconds the CLMI automatically learns the new measured value and
reprograms the zero point relative to the new value (without persons on the top side of the car).
This is the elegant method to program the readout to 0 kg, although the installer is on the top side of the car during the installation.
Wire the supply, sensors, floor detection, motion detector and alarm output according to electrical installation.
Turn on the supply –the display shows a random number, now.
Preparation
Acquaint yourself with functions in the setup menu and set these functions relative to your installation and desires.
A) Programming of the Options in the Setup Menu
1. Press UP at least 10 seconds until E_x appears.
2. You are in the setup menu, now.
3. Set E, F, C, L, S, P, I relative to your installation and your desires.
4. Set A to your installation and your desires.
5. Set H to your installation and your desires.
6. Wait 10 seconds, the setup menu will be automatically quitted.
Please note: Point A may be shortened, by executing a general reset. (See paragraph “Advices to Commands”)
B) Parameterization of the Load Measurement
7. Make sure the car is empty.
8. Press RIGHT –P0_ (teach-in zero point lowest floor) appears
9. By pressing UP/DOWN the readout is changed to the desired value when the car is empty. (*)
10. Press RIGHT –P0¯(teach-in zero point highest floor) appears.
11. By pressing UP/DOWN the readout is changed to the desired value when the car is empty,
(Please note: The CLMI „knows“how to compensate the travelling cable, etc., now.)
12. Press RIGHT –PE (Car Empty) appears
13. By pressing UP/DOWN set PE to the limit value of the signal “Car Empty”. When a measured value is below your
entered limit, the signal “Car Empty” will be activated. (e.g. 40kg)
14. Press RIGHT –P1 appears.
15. By pressing UP/DOWN set P1 to 0.
16. Press RIGHT –P2 (full load) appears
17. By pressing UP/DOWN set P2 to its maximal allowed car load.
18. Press RIGHT –P3 (overload) appears
19. By pressing UP/DOWN set P3 to 115% of the maximal allowed car load (therefore consult the information of the
car/elevator manufacturer and the relevant norms).
20. Load the car with the maximal allowed car load.
21. Execute 3 to 6 rides with the elevator.
22. Press RIGHT until P4 appears (teach-in nominal load).
23. By pressing UP/DOWN set P4 to the maximal allowed car load, respective the real loaded weight.
24. Press 1x RIGHT or wait 10 seconds.
25. The device returns to the display mode and it is ready, now.
C) Control the Commissioning
26. During the following unloading, control if the display proportionally drops to the load reduction.
27. If the display doesn’t exactly drop to 0 afterwards, you can teach-in the zero point in P0 again.
28. Load the car again with 50%...80% of the nominal load and observe the changes on the display.
29 If there are large aberrations, teach-in P4 again. Control the installation of the sensors and the behaviour of the car in
its guidance (friction!).
30. Complete the final tests according to the instructions of the elevator manufacturer.
(*) Variant 1
Usually the readout is set 0(kg) when the car is empty. But if the installer is on the top side of the car and his weight affects
the measurement, he must program his own body weight (not 0kg). After leaving the top side, the readout drops to 0.
(*) Variant 2
The readout is set 0 kg, although the installer is on the top of the car. After the last key pressing (UP or DOWN), the installer
MUST NOT press RIGHT but leave the top side of the car. After 10 seconds the CLMI automatically learns the new
measured value and reprograms the zero point relative to the new value (without persons on the top side of the car).
This is the elegant method to program the readout to 0 kg, although the installer is on the top side of the car during the
installation.

Manuel_X_232_EN 9 / 13 27.01.2016
Description of Inputs and Outputs (I/O)
Position and Orientation of the Terminals
Terminal
Function
Comment
X6
Type: Input
Cable: At least 3x 0.25²,
approved for mains
voltage
Mains supply
115VAC/230VAC
Before connecting, preselect voltage correctly
Pin 1: P (Phase)
Pin 2: N (0)
Pin 3: E (Ground, mandatory)
X1
Type: In / output
Cable: At least 5x0.25²
Digital breaker signal &
24V supply
X-232-DC: Supply 24V
X-232-AC: Do not connect (→s. “Electrical Installation”)
Pin 1: Supply, +24V (only X-230-DC)
Pin 2: Breaker signal full load
Pin 3: Breaker signal overload
Pin 4: Breaker signal minimum load
Pin 5: Supply 0V, breaker signal 0V
Pin 6: Ground (only X-230-DC)
X2
Type: Input
Cable: At least 5x0.14²,
shielded
Sensor input
Metallic circular connector at case
Pin 1: Sensor supply + (Exc+)
Pin 2: Signal +
Pin 3: Signal -
Pin 4: Sensor supply –(Exc-)
X3
Type: Output
Cable: At least 6x0.25²,
The insulation class
must correspond to the
switching voltage!
Relay contacts
3 relay contacts (normally open, NO)
Galvanically separated
Pin 1: C, KL1 Full load
Pin 2: NO, KL1 Full load
Pin 3: C, KL2 Overload
Pin 4: NO, KL2 Overload
Pin 5: C, KL3 Minimum load
Pin 6: NO, KL3 Minimum load
X4
Type: Input
Cable: At least 8x0.25²
Floor detection
(see separate paragraph
“Background Information
about Floor Detection“)
Digital input, galvanically separated
(6bit + synchronization)
Pin 1: Bit 0 (LSB) Floor detection
Pin 2: Bit 1
Pin 3: Bit 2
Pin 4: Bit 3
Pin 5: Bit 4
Pin 6: Bit 5 (MSB) Floor detection
Pin 7: Synchronization, Measuring Stop
(if unused, leave unconnected,
Parameter L=0)
Pin 8: 0V, reference potential
X5
Type: Input
Cable: At least 4x0.25²
External motion detector
Breaker signal and supply of an external motion detector
(PIR, Radar, Opto)
Pin 1: Breaker signal input (internal Pull-Up)
Pin 2: Not used
Pin 3: 0V
Pin 4: +24V/20mA supply for external sensor
Pin 5: 0V
The two sensor inputs are paralleled. If only one sensor is connected, it doesn’t matter if it is connected at the left or right
female input connector.

Manuel_X_232_EN 10 / 13 27.01.2016
Programmable Functions
Setup Menu
Basic Menu
Function
Command
Range of Values, Comment
P0
(Parameter 0)
Teach-in zero point.
Assigning a currently
measured load to a
certain zero point.
Only executing when the car is empty.
Allowed range: -99 to 999
Suggestive range: -10 to 100
(→s. paragraph “Setup Menu”, “Floor Detection”)
(*) P0_
(Parameter 0 bottom)
Teach-in zero point at
lowest floor.
Assigning a currently
measured load to a
certain zero point.
Only executing when the car is empty.
Allowed range: -99 to 999
Suggestive range: -10 to 100
(→s. paragraph “Setup Menu”, “Floor Detection”)
(*) P0‾
(Parameter 0 top)
Teach-in zero point at
highest floor.
Assigning a current
measured load to a
certain zero point.
Only executing when the car is empty.
Allowed range: -99 to 999
Suggestive range: -10 to 100
(→s. paragraph “Setup Menu”, “Floor Detection”)
(*) PE
Operating threshold for
relay contact KL3
(Car Empty)
Allowed range: -99 to 999
Suggestive range: 5..25% of nominal load
(→s. paragraph “Setup Menu”, “Floor Detection”)
P1
(Parameter 1)
Not used
Allowed range: -99 to 999
Suggestive range: 0 (not used)
P2
(Parameter 2)
Operating threshold for
relay contact KL1
(full load)
Allowed range: -99 to 999
Suggestive range: 100% of nominal load
P3
(Parameter 3)
Operating threshold for
relay contact KL2
(overload)
Allowed range: -99 to 999
Suggestive range: 120% of nominal load
P4
(Parameter 4)
Teach-in nominal load.
Assigning the currently
measured load to a
certain displayed value.
Only executing when the car is full.
Allowed range: -99 to 999
Suggestive range: Nominal load, i.e. real weight of
the load in kg inside the car.
(*) Optional Parameter must be activated in the setup menu.
The switching polarity of KL3 is always inverted to the switching polarity of KL1 and KL2.
Function
Command
Range of Values, Comment
E
(Minimum load
measuring)
Activates the Parameter
PE
0= Relay contact inactive, PE not programmable
1 = Relay contact active, PE programmable.
F
(Floor detection)
Activates the floor
detection and the
travelling cable
compensation
0= Floor detection inactive
1 = Floor detection active, P0 must be taught-in twice
Once at lowest floor, once at highest floor.
C
(Coding)
Floor information is read
in binary or Gray code
0= Binary coded
1 = Gray coded
L
(Logic Polarity of
coding)
Floor information and
Synch is low or high
active
0= 5..24V corresponds logic 1 (1 active)
1 = 0V corresponds logic 1 (0 active)
S
(External sensor for “Car
Empty”)
Activates sensor at X5
(→s. paragraph “Input
and Output“)
0= Breaker signal is not processed
1 = Breaker signal is processed
(→s. paragraph “External Sensor”)
P
(Polarity of the switching
output X1 and relay at
X3)
Inverts the polarity of the
digital switching outputs
X1 and the relay at X3
0= normal polarity, achieved operating threshold
sets output to plus, relay energizes.
1 = inverted polarity, achieved operating threshold
sets output to 0V, relay de-energizes.
I
(Polarity load measuring
sensor at X2)
Inverts the polarity of the
signals of the load
measuring sensor at X2
0= normal polarity, sensor signal becomes more
positive during loading of the car
1= inverted polarity, sensor signal becomes more
negative during loading of the car
A
(Response delay of
KL 2)
Delays the operating of
KL2 (overload) during
programmed time
Adjustable from 99 Digits, relative 0 to 9.9 seconds.
Recommended value: 1 second (10 Digits)
H
(Switching hysteresis for
all outputs)
Switching hysteresis in
kg for all outputs.
Adjustable from 0..99kg.
Recommended value: 10..15kg.
Prevents the “oscillating“of the relay contacts.
(→consult the paragraph "Troubleshooting“)
Please note!
If the functions (E, F, P, I) are modified in the setup menu, so P0 und P4 must be compulsory taught-in again.
This signifies the car must be load with the nominal load again.
The blinking of the left zero point warns you that a new teach-in is required.
If the change is manually undone in the setup menu, so another teach-in won’t be required.
But this isn’t possible anymore when you have left the setup menu before without undoing the change.
Default settings of the setup menu are marked bold in the list above.

Manuel_X_232_EN 11 / 13 27.01.2016
Menu-Structure
Advices about Commands
Main Menu / Parameterization
By pressing UP/DOWN you can change the values of the parameters.
When the left decimal point is rapidly blinking, so a change has been made. The change will be automatically saved when
you leave the process of parameterization.
Important: During the parameterization you can restore the last saved value by pressing UP and DOWN at the same time.
(→s. paragraph “FAQ“)
60 seconds after the last key pressing, the device returns to the display mode. Any taken change will be saved.
Setup Menu
By pressing UP/DOWN you can change the values of the parameters.
10 seconds after the last key pressing, the device returns to the display mode. Any taken change will be saved.
Special Commands:
General Reset (deletes ALL preferences)
By simultaneously pressing UP and DOWN for 10 seconds.
Test Menu (see “FAQ”)
By pressing DOWN for 10 seconds.

Manuel_X_232_EN 12 / 13 27.01.2016
4. Troubleshooting, Diagnostic
Technical Data
FAQ
General
Supply X-232-AC 115VAC switchable 230VAC / 8VA
Fuse self resetting, 50mA
Supply X-232-DC 18..28VDC, <350mA
Fuse self resetting, 400mA
Temperature range -10...+60°C
Display red, three-digit, 7-segment
Display range 0...999 Digits
Resolution 1 Digit
Measuring velocity 3 Measurements/s
Measuring aberration max. 6kg (within the specific operation range)
Refresh rate 200ms
Dimension 160 x 120 x 80mm³ (L x B x H)
Mounting 4x M4 (88x148mm²)
Case material Polycarbonate
Weight 0,65kg
Degree of protection IP22 (vertical mounting)
Sensor supply max. 5V, safe against short-circuit
Nom. 4,3V @ 350Ω
Nom. 3,8V @ 175Ω
Zero point range (P0) -1,0 ... +4,0 mV/V
Span sensor (P4) 0,15mV/V...2mV/V
Input measuring range, absolute ±7,5mV/V
Bridge resistance Sensor 300…5’000Ω
Switching capacity, digital outputs High-threshold: Vcc-3V
Low-threshold: <1.5V
Sourcing capacity, with reference to 0V: max. 30mA
Switching capacity, relay contacts Max. switching voltage: 250VAC, 125VDC
Max. switching capacity: 500VA(AC), 200W(DC)
Maximal switching current: 2A (DC or AC)
Product life, relay contacts 10 x 106
Sensor Car Empty (X5)
Supply from CLMI, i.e. 18..28VDC
Current consumption max. 50mA
Output Switching output, Minus-switching
Motion detected: Switching contact inactive
No motion: Switches to 0V.
Galvanic separation No
Floor detection (X4)
Input Threshold, digital inputs 0…1V = Logic 0, 5...30V= Logic 1
Input resistance 4 kΩ against reference potential
Galvanic separation 50V (AC or DC)
Parallel interface 6bit, binary coded (optional Gray code)
Synchronization 7. Bit shows validity of the code on B0..B5.
(→ s. Function: Measuring Stop)
(Q&A)
Q: Can I use KL1 and KL2 in a different way as proposed?
A: Yes, the thresholds are freely programmable. E.g. I can program half load instead of full load.
Take note: The response delay works with KL2 (overload) ONLY, and KL3 (Car Empty) must be activated in
the setup menu before.
Q: After having changed the configuration in the menu “Configuration”, do I always have to calibrate
before commissioning?
A: No, but it is assumed that if the Empty-Car detection and the floor detection Floor (F) are changed, a
general change of the configuration has been done. So before the commissioning another calibration is
required.
The external motion detector (S) can be turned on and off without requiring a calibration again.
(→s. paragraph “Setup Menu“)
Q: How do I have to set the zero point if I have to be on the car while I operate?
A: Consult the paragraph “Commissioning“, Variant 1 and Variant 2.
Q: How can I undo values (after a faulty operation)?
A: By shortly pressing “UP“ and “DOWN“ at the same time the original value will be restored. This is only
possible as long as you are in the relevant menu. If you have left the menu, changes can’t be undone in this
way.
Q: Why is the decimal point to the left rapidly blinking?
A: This blinking shows you that a value has been modified and the device saves the new value.
Q: Do I always have to load the car with the full payload while I am calibrating the car?
A: No, depending on the sensitivity of the sensor 50..75% of the payload suffices. Please note: The
measurement will probably be very inaccurate if you calibrate a large measuring range with a small
reference weight. We recommend no to go below 70% of the payload.
Q: How can I completely reset the CLMI (General-Reset)?
A: Press the keys “UP”and “DOWN”for 10 seconds. All values including the calibration values are deleted,
now.
Q: How can I expand the measuring range over 999kg?
A: Take a tenth of the absolute values of P1 to P4. I.e. when you have a 1500 kg payload, you set P4 to
150. Proceed with the thresholds analogously.
Q: How do I have to interpret the blinking numerical code which is displayed in the test menu?
A: The two digits to the right and in the middle show the reported number of floor in plaintext. The digit to the
left shows the switching state of “Measuring Stop“ and “Empty Car” in the coded form.
Significations:
2xx Ext. motion detector reports “Empty Car“
1xx “Measuring Stop“not active, i.e. measuring is running
3xx “Empty Car”and measuring is running
xx Number of floor in plaintext
After a minute, the CLMI returns itself to the normal operation mode.
Q: Is the CLMI limited to a certain sensor?
A: No, the CLMI processes a mV/V signal which a strain gauge full bridge generates depending on the force
effect. The CLMI can measure at the yoke, fixed point, rope tension, car ground, car frame or at the motors
bed frame. Ask X-Sensors, there are suitable sensors for any imaginable measuring strategy.
Q: How can I request the software version?
A: Return to the normal mode of the CLMI, it shows the load in kg, now. Press consecutively “DOWN “ and
“LEFT“and keep pressing both keys. The display shows a three-digit number. This number represents the
software version. →consult the paragraph “FAQ“

Manuel_X_232_EN 13 / 13 27.01.2016
Troubleshooting
Warnings
Q: I try to set P4 by pressing UP/DOWN but it always appears “Err“.
A: You have tried to calibrate with a too low load or with an unavailable span. Load the car with the payload or control the sensor.
You can increase the sensor signal by loading the cabin with 120% of payload. It is understood that also P4 has to be increased to
120%.
You have tried to teach-in P4 although Bit6 at X4(synchronization) is set to “High“. This means “Measuring Stop“ and no
measurement will be executed.
You tried to calibrate P4 with a negative signal span. Check polarity settings of sensor and/or X-232.
Q: The alarm contacts are switching during the ride.
A: Short fluctuations of the measured values can be disabled by increasing the response delay by a few seconds and by adding some
kilograms to the hysteresis value. (→s. paragraph “Setup Menu“)
Alternative: Connect the output "Measuring Stop" to your control unit. In this way, you can synchronize the CLMI to the elevator. E.g.
You can only accept measurements as long as the door is open.
Q: The minimum contact doesn’t switch reliably
A: If the switching hysteresis (→Setup Menu) is set too large, it may occur that the hysteresis is as large as the set limits for the
minimum load measuring. The CLMI cannot clearly determine the status. Reduce the hysteresis by maximal 50% of the value which
was programmed in “PE“.
Q: The minimum contact doesn’t switch.
A: If the parameter “S“ (external sensor) is set to 1, you must pull down Pin 1 at X5 to 0V, thereby KL3 will be activated. If there is a
cable break or defect motion detector, KL3 won’t be activated.
As a general rule, the contacts do only switch, if ALL parameters have been programmed.
Q: The zero point is fluctuating.
A: Depending on the chosen strategy of load measuring, the measuring is more or less immune to any kind of fault. Load measuring
at the yoke or fixed point requires an almost frictionless guidance of the car to generate a repeatable zero point. If you can realize a
load measuring below the ground, the effect of the friction can be completely eliminated.
At the yoke, you can reduce the hysteresis by mounting a second sensor at another yoke profile.
The correct mounting of the sensor is the general condition (no color at the bearing areas, screws well tied up)
Q: After a certain time my display shows nothing except a blinking decimal point.
A: After 30 minutes idle time the display changes to the standby-mode. If you press any key, the display will show plaintext again.
Q: During the installation, I have sometimes realized aberrations of the zero point which slowly disappear.
A: The CLMI has an approximation process of the zero point. Is the measured load closer to 40kg than to zero and when this
measured load doesn’t change for two hours, so the CLMI will slowly adopt the 40kg as new zero point. This process would last a few
days, so the CLMI evaluates an optimal zero point. Long-term errors due to drift or continually mechanical abrasion can be
compensated.
Q: I have two sensor inputs at the CLMI. How does the CLMI interpret the signal from these two sensors?
A: The signal of these two sensors is averaged. Therefore all errors, working in the opposite direction are compensated.
It is understood, that the setup, configuration and operation may only be done by qualified personnel.
The series X-232 load indicators must not be used in life-supporting applications. The series X-232 load indicators
must not be used in safety-critical applications.
If you do not pay attention to this security hints, serious damages can be provoked.
General rules for installation
Maintenance, Repairing
Pay attention all the time and mainly during your installation process to all legal rules and security-hints to prevent any accident. Do
always separate the signal lines from power lines (drives, converters) and do never interrupt the signal lines unless you use
designated junction boxes. (X-914)
Tie cable shield (braid) at both ends to a proper ground. Tie all machine parts to one well defined potential by using massive copper
wires. Prevent at any case that a ground current flows over the cable shield. Prevent different potentials in your machine, they will
create currents which can be hardly controlled.
The devices of the serie X-232 do not contain any serviceable parts. Any repairing is done exclusively by the
manufacturer
Table of contents
Popular Measuring Instrument manuals by other brands
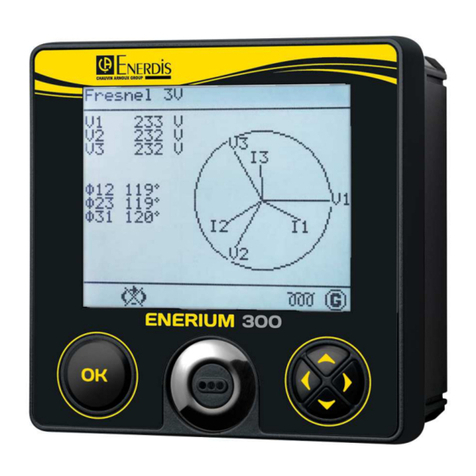
Enerdis
Enerdis Enerium 100 user manual

Pittsburgh
Pittsburgh 63730 Owner's manual & safety instructions
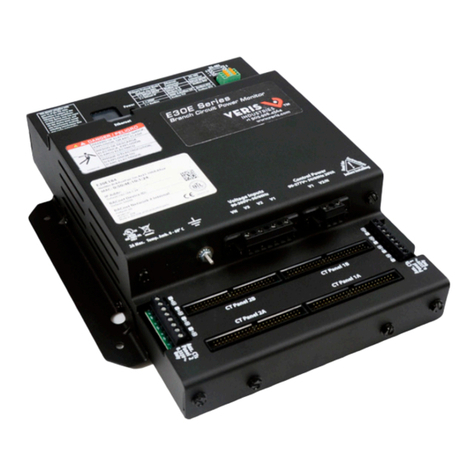
Veris Industries
Veris Industries E31E Series installation guide

HD Electric
HD Electric CDM-50 Operating and instruction manual

Alia
Alia AUF750 Series Operation manual
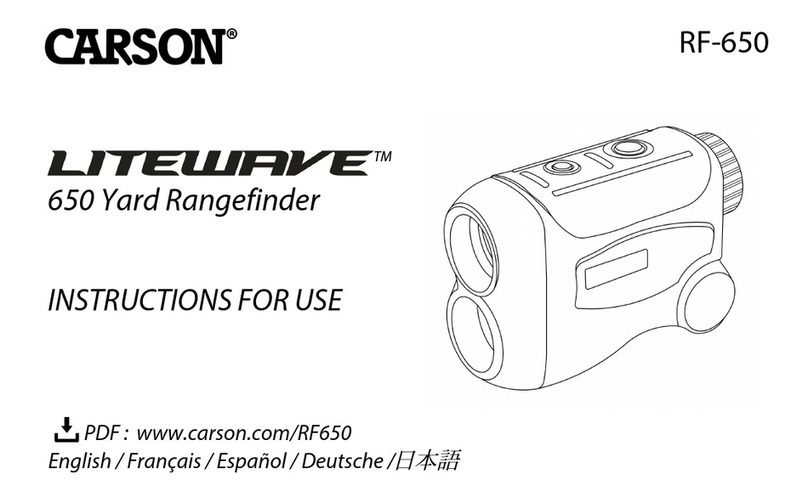
Carson
Carson Litewave RF-650 Instructions for use