Yueming CMA1325C-B-A User manual

I
Product Manual
Applicable Model: CMA1325C-B-A
Version: 1.0

II
Copyright Statement
GD Han’s Yueming Laser Group Co., Ltd.
All rights reserved.
GD Han’s Yueming Laser Group Co., Ltd. (Han’s Yueming Laser hereafter) reserves the right to modify the
products and product specifications described in this manual without advance notice.
Han’s Yueming Laser is not responsible to any direct, indirect, or consequential damage or liability caused by
improper use of this manual or the product.
Han’s Yueming Laser owns the patent, copyright or any other intellectual property right of this product and
the related software. No one shall duplicate, reproduce, process or use this product and its parts, unless
authorized by Han’s Yueming Laser.
All the name referred in this manual only for identification, if belongs to other company’s registered
trademark or copyright, proprietary rights of the name belongs to their respective holder.

III
Disclaimer and Responsibility Statement
Whole using the machine from our company, users are required to ensure integrity and independence of the
product including but not limited to: mechanical, electrical, optical, control software and accessories.
Unauthorized modification is strictly prohibited. It is a must to satisfy operating environment and operating
specifications specified in the owner’s manual.
For the followings:
Machine modified with no authorization (including but not limited to: add, remove, modify,
unauthorized disassembly, replacing parts);
Use the machine in the environment failing to satisfy the operating requirements;
Operate disobeying the specifications of our company;
Unauthorized use the machine parts, accessories and auxiliaries on to other machine or in other places;
Viciously disassemble, destroy, decode hardware and software of the machine from our company
Our company shall not undertake any direct, indirect or joint responsibility. Our company reserves the rights to
ascertain legal responsibility for the serious consequences or economic losses or reputation losses caused by what
mentioned above.

IV
Foreword
Thanks for purchasing the laser engraving machine control system of our company.
Before operating, please read this manual carefully to ensure proper operation.
Please keep the manual properly for reference.
Since the configs are different, certain models do not have the functions listed in this manual. Please refer to
the specific functions for details.
Due to the constantly tech update, the specification for reference only, subject to the real standard.
Tags in this book:
Alarm
Special Attention: User must follow and perform as the manual; otherwise, it could lead to errors or relatively
serious problem.
Note
Note: User should comply with the attention and suggestion in this manual; it could bring much easier operation.
Warning
For a particular case there is no dedicated staff to guide the operation could lead to catastrophic happens

IV
Safety Precautions
Attention
Before using the machine, users are required to carefully read this manual and other operating requirements,
strictly abide by the operating specifications. Professional are required for operating the machine.
Warning
The machine uses class 4 laser (strong laser radiation). The laser radiation may possibly cause the following
accidents:
emblaze the surrounded flammable materials;
generate other radiations and toxic or hazardous gas by processed objects during laser processing;
direct irradiation of laser radiation cause harm to human body. Therefore, firefighting devices are required in the
operating place of the machine. Stacking flammable or explosive objects near the machine is strictly prohibited.
Good ventilation is a must. Only the qualified personnel are authorized to approach the machine.
Note
The processed objects and discharged materials are required to satisfy requirements as per local laws and
regulations.
Warning
Laser processing is with potential risks. Users should carefully make sure if the processed objects are suitable for
laser processing.
There is high voltage and potential risk in the laser machine. Unauthorized disassembly by unqualified personnel is
prohibited.
Reliable earthing is required for the machine and related other machine before power-on.
During operating, removing any cover of the machine is strictly prohibited.
During operating, the operators are required to observe working status of the machine all the time. In case of any
abnormality, it is immediately to disconnect power supply and take active and corresponding measures.
After power-on, special personnel are required for monitoring. Unauthorized leaving is strictly prohibited.
It is a must to disconnect the power supply before leaving.
Warning
It is strictly prohibited to placing any unrelated all-reflective or diffusion reflective objects in the machine to
prevent laser reflecting to human body or flammable materials
Attention
The environment for the machine should be dry, free of interference and influences from pollution, vibration, high
voltage and strong magnet. The operating ambient temperature ranges 5-40 ℃
,and the
-85% (no
dew);
The machine should be far from electric appliances sensitive to electromagnetic interference;
Operating voltage: AC220V, 50Hz. Power-on is strictly prohibited in case of unstable voltage of the power grid or
unspecified voltage.
Attention
Chapter two of this manual is for Safety Rules. Please refer to the chapter more details concerning safe operation
of the machine. Users are required to carefully read and abide by all the requirements of safety.

V
Content
Copyright Statement ............................................................................................................................... II
Disclaimer and Responsibility Statement............................................................................................... III
Foreword ................................................................................................................................................ IV
Safety Precautions...................................................................................................................................... IV
Chapter1. Product Introduction............................................................................................................. 1
1.1 Overview ............................................................................................................................... 1
1.2 Product parameters and requirements ................................................................................ 1
1.3 Using environment................................................................................................................ 1
1.4 Equipment composition........................................................................................................ 2
1.4.1 Auxiliary equipment.............................................................................................................. 2
1.5 Software control system ....................................................................................................... 3
Chapter2. Safety Rules........................................................................................................................... 4
2.1 Refer to safety standards...................................................................................................... 4
2.2 Product safety ....................................................................................................................... 4
2.3 Safe equipment ..................................................................................................................... 4
2.4 Safety awareness .................................................................................................................. 4
2.5 Requirements for personnel ................................................................................................. 5
2.5.1 Definition of terms................................................................................................................ 5
2.5.2 Qualifications ........................................................................................................................ 5
2.5.3 Responsibility ........................................................................................................................ 5
2.5.4 Personal protective devices .................................................................................................. 5
Chapter3. Equipment Installation and Commissioning ......................................................................... 6
3.1 Equipment installation.......................................................................................................... 6
3.1.1 Unpacking steps .................................................................................................................... 6
3.1.2 Out of box audit .................................................................................................................... 7
3.1.3 Preparation for installation................................................................................................... 8

VI
3.1.4 Machine level adjustment .................................................................................................... 8
3.1.5 Installing ventilation tube ..................................................................................................... 9
3.1.6 Installing laser ..................................................................................................................... 10
3.1.7 Installing water cooling system........................................................................................... 11
3.1.8 Installing air pump .............................................................................................................. 12
3.1.9 Installing external power .................................................................................................... 13
3.1.10 Equipment grounding ......................................................................................................... 13
3.1.11 Installing software and device drivers ................................................................................ 14
3.1.12 Installing other accessories................................................................................................. 14
3.2 Instructions of machine button .......................................................................................... 14
3.2.1 Main power switch.............................................................................................................. 14
3.2.2 Emergent stop button......................................................................................................... 15
3.2.3 Motion system power button ............................................................................................. 16
3.2.4 Laser system power button ................................................................................................ 16
3.2.5 USB&LAN interface ............................................................................................................. 16
3.3 Equipment debugging ......................................................................................................... 17
3.3.1Switching sequence............................................................................................................. 17
3.3.2 Movement debugging......................................................................................................... 17
3.3.3 Laser debugging .................................................................................................................. 18
3.3.4 Processing commissioning .................................................................................................. 21
Chapter4. Care and Maintenance........................................................................................................ 23
4.1 Mechanical maintenance.................................................................................................... 23
4.1.1 Guide rail, Lead screw......................................................................................................... 23
4.1.2 Synchronous belt and synchronous pulley ......................................................................... 24
4.1.3 Fasten screws and coupling ................................................................................................ 24
4.2 Electrical inspection ............................................................................................................ 25
4.2.1 Limit switch ......................................................................................................................... 25
4.2.2 Stop button ......................................................................................................................... 25

VII
4.3 Light route and optics parts maintenance .......................................................................... 25
4.4 Auxiliary equipment maintenance...................................................................................... 27
4.4.1 Cleaning the fan .................................................................................................................. 27
4.4.2 Water chiller maintenance ................................................................................................. 28
4.4.3 Worktable maintenance ..................................................................................................... 29
4.5 Maintenance cycle .............................................................................................................. 29
4.6 Runtime maintenance......................................................................................................... 30
4.7 Maintenance of long-term shutdown................................................................................. 30
Chapter5. Troubleshooting .................................................................................................................. 31
Chapter6. Transportation, Shipment and Storage............................................................................... 32
6.1 Packaging ............................................................................................................................ 32
6.2 Transport and shipment method and precautions............................................................. 32
6.3 Storage conditions, period and precautions....................................................................... 32
6.4 Flat Machine Installation Diagram ...................................................................................... 33
Postscript................................................................................................................................................... 34

1
Chapter1. Product Introduction
1.1 Overview
CMA1325C-BA non-metal laser cutting machine is a laser cutting machine designed by Guangdong Han's
Yueming LaserGroup Co., Ltd. for laser cutting of non-metallic materials. Featuring high-speed, high-precision,
high efficiency and cost effective, it is a high-tech product that integrates laser cutting, precision machinery and
motion control technology. It is a high-precision, high performance and highly automated laser cutting machine
and is widely used in advertising, die cutter, crafts and other processing industries.
CMA1325C-B-A laser cutting machine has the following features:
Use CO2glass laser tube;
Use high rigidity thickened welding frame, and carry out vibration aging treatment to ensure that the
machine is stable and reliable;
The beam structure is made of high-strength aluminum alloy, featuring light weight, high rigidity and
smoother running compared with traditional steel beams;
Semi flying optical path design improves the consistency and quality of the beam in the entire work
area;
Japan Shinano stepper motor and Taiwan precision linear guide rail offer high dynamic response for the
machine;
Box exhaust system ensures clean working environment;
Support Bmp, plt, dst, ai and other file formats, easy to operate;
Support thick plate cutting, and maximum acrylic cutting thickness is 30mm.
1.2 Product parameters and requirements
Maximum size of cutting sheet 1300mm×2500mm
Maximum speed 18m/min
Positioning accuracy ±0.2mm/1000mm
Repeat positioning accuracy ±0.1mm/1000mm
Cooling mode Water cooling
Drawing format Bmp, plt, dst, ai
Work environment 5-40℃, RH ≤ 85%, non-condensing
Equipment power <4KW
Power requirement 220V/50Hz
1.3 Using environment
Humidity: 5%~85%, non-condensing;

2
Temperature: 5 ℃-40 ℃;
Power supply: AC220V, 50Hz;
Ground: The resistance to ground should be less than 5Ω;
The environment for the equipment should be dry, smokeless, dust-free, pollution-free, and shouldn’t have
vibration, strong current, strong magnetic field and other interferences.
Air pressure: 86-106kpa.
1.4 Equipment composition
CMA1325C-B-A laser cutting machine adopts modular design and consists of the frame, beams,
cutting head, worktable, console and auxiliary equipment, as shown below:
Fig.1-1 CMA1325C-B-A Laser Cutting Machine (refer to real machine)
1.4.1 Auxiliary equipment
In order to ensure the normal operation, the laser equipment also requires some auxiliary parts, such as fan
and chiller. Different models have different auxiliary parts, and the actual equipment shall prevail.
Air pump
Fan
Water chiller
Fig.1-2 Auxiliary equipment

3
1.5 Software control system
SmartCarve4 software is new PC platform software launched by Han's Yueming Laser Group Co., Ltd. and
supports process control or data generation. The major functions are computer-aided design, computer
intelligent control, graphics and image processing, support for multiple data types, a variety of laser machining
processes, multi-layer setting and multi-language support, as described below:
Computer-aided design capabilities. SmartCarve4 software can achieve simple graphics rendering and
editing, including solid lines, rectangles, polygons, arcs, ellipses, curves, texts, perforation and other
element drawing and editing; supporting element node editing, allowing easy tuning of graphics;
support graphics translation, rotation, mirroring, stretching, shearing, alignment, cloning, arrangement,
filling, slope handling and other advanced editing features;
Support importing a variety of graphics data, including: plt, dxf, dst, dsb, ai, bmp, jpg, gif, out, oux, ymd,
yln, cut, smc, etc.;
Simple graphics and image processing functions, including vector and bitmap translation, rotation,
mirroring, stretching, shearing, arrangement, cloning and other major editing functions; support bitmap
dot graphics processing and inverse color processing;
Support multiple languages: SmartCarve4 software fully supports Unicode, and supports languages of all
countries theoretically. The standard format is internationally accepted Xml files, and the users can
modify the languages. Currently the software is available in Chinese Simplified, Chinese Traditional and
English, and the user can add/delete accordingly;
Support up to 256 processing layers, and the user can set the processing parameters and priority of
different layers as needed.

4
Chapter2. Safety Rules
This chapter mainly introduces safety warnings for protecting personnel and the machine, and makes an
introduction to signs used in the owner’s manual. The machine is already equipped with sufficient safety
guarantee, yet it is still with certain risk. All the operators are required to carefully read through and well
understand the safety rules.
2.1 Refer to safety standards
Laser processing equipment and operations shall be in accordance with both two national standards, which
are GB7247-87 Radiation safety of laser products, equipment classification, requirements and user guide, and
GB10320-88 electrical safety of laser equipment and facilities.
2.2 Product safety
The following conditions are required to be satisfied to ensure safe work:
Abide by operation manual and instruction signs;
Operators and maintenance personnel have received training held by machine manufacture;
In case of operation by couples of person at the same time, division of responsibility should be made
and followed;
No admission to the working area for the unauthorized personnel;
Avoid any working method breaking the safety rules;
Timely eliminate all the failures possibly causing lower safety coefficient;
Abide by maintenance regulations of the machine.
2.3 Safe equipment
Safety machines are used for protecting personnel, and unauthorized disassembly, bridge-group or by-pass
connection are strictly prohibited; in case of failure with the safety machine, professional are required for repair.
If part replacement is needed, the product with same model, specification and from the same manufacture is
required; otherwise, written consent from the manufacturer is required.
2.4 Safety awareness
The machine can be operated only by skilled personnel or under supervision of them. Improper use or
operation may possibly be very dangerous and cause damage to the machine. Therefore, the followings are
strictly prohibited:
Placing heavy objects or stepping on the working table of the machine;
Used for processing the materials unapproved by manufacturer;
Staying of unauthorized personnel in the dangerous area (It is the responsibility of operators to ensure
keeping unauthorized personnel away from the working area.);

5
Block of using emergency stop button (Regular check is required to ensure a good condition for the
emergency stop button.)
2.5 Requirements for personnel
After trail operation, maintenance personnel from the manufacturer may perform training on the operators.
It is the responsibility of machine owner to have operators trained at corresponding level.
We have prepared ready a series of training course for your option. Please make phone call to our Customer
Training Center for details.
2.5.1 Definition of terms
All the personnel using or operating the machine are called User in the manual;
Different requirements are for different users. Users are classified into the followings:
Owner
Owner means the authorized person or representative to sign contract with the manufacturer. With
authorization, the owner has rights to sign the agreement with binding force of law;
Operator
Operator means the personnel trained for operating the machine. Training of the operator includes
participation of training held by the manufacturer.
Maintenance personnel
Maintenance personnel mean the technicians having received formal training for machine and electric
engineering. The maintenance personnel are responsible for daily maintenance of the machine, and repair at low
level if needed. Training on the maintenance personnel contains participation training held by manufacturer.
2.5.2 Qualifications
The operator is required to accept guidance and training of the owner, and the operator is responsible for
the safety of a third party in the working area; the personnel required for further training and guidance are
required work or operate the machine under supervision of the operators.
2.5.3 Responsibility
It is a must to clarify the related responsibilities of each performance (operation, maintenance, parameter
setting), and carry it out. Unclarified responsibilities will cause safety hidden risks.
Owner is required to provide operation manual for the operators and maintenance personnel, and ensure
that they have read and understood the operation manual.
2.5.4 Personal protective devices
When technology or measures fail to absolutely avoid risk of health, the owner is required to provide
personal protective devices for operator and maintenance personnel. For example,
Protective gloves;
Laser-proof goggle;
Light respirator

6
Chapter3. Equipment Installation and Commissioning
3.1 Equipment installation
3.1.1 Unpacking steps
Before installing, disassemble the wooden box packaging the machine in the following steps:
Fig.3-1 Equipment Crate
Open the machine body crate with a crowbar (user supplied), and unpack the crate in sequence: top
cover, side cover, front and rear cover, and foot cup mounting plate (the crate of some parts is
connected with screws, which should be removed before unpacking).
Fig.3-2 Machine Body Crate

7
Fork the machine from the substrate with a forklift and transport to the destination, and unscrew the foot
cup.
Then open the accessory crate, laser tube crate and laser crate.
Accessory Crate
Laser Tube Crate
3.1.2 Out of box audit
After unpacking, examine the equipment and accessories to ensure that the product has no accident during
transport. Check the following items:
1.Equipment model audit
Please confirm if the model is the equipment you ordered.
Equipment appearance
Please check if the equipment appearance has scratches, breakage, deformation, corrosion and other
defects.
2.Equipment interior audit
Open the beam organ cover, and check if the equipment has parts and thread falling off or internal
damage.

8
Spare parts and accessories
Please confirm that the equipment model is the one you ordered, open the auxiliary chassis and laser tube
crate, check if any part is missing or doesn’t match according to the packing list, and check the accessories for
damage and deformation.
Attention
Do not unpack the crate without permission.
To unpack, first obtain permission from customer service or business personnel of Han's Yueming Laser, or else the
company doesn’t assume any responsibility for any accidents.
Attention
If any problem occurs after unpacking, please inform the customer service or business personnel of Han's Yueming
Laser, or directly call Han's Yueming Laser. Do not handle without authorization.
3.1.3 Preparation for installation
Site
The dimensions of CMA1325C-B-A machine body are3480*1900*1150mm; to ensure the normal
use of the machine, ensure that the machine's working space is at least 4000*3000*4000mm;
Laser equipment has requirements on site conditions and working environment; please confirm
that if the site is appropriate in accordance with section 1.3 and the requirements of our company.
Staff
The installation personnel are professional service commissioner of Han's Yueming or operating personnel of
agents trained by Han's Yueming. To install the machine independently, the client must have accepted full
installation training by Han's Yueming Laser and have master the points of installation of laser-related equipment.
Tools
According to the order requirements, related installation tools may be provided. If the user does not have
such requirement, it may be necessary to provide the installation and testing tools, such as hex wrench,
screwdriver, multimeter, and wrench.
Others
The user needs to prepare 0.8MP high-pressure gas source, water, 220V power supply, exhaust channels,
proofing materials and electrical outlets related to the equipment.
Attention
While the service commissioner is installing, the client must accompany throughout. Equipment installation and
commissioning are part of the training, and the user needs to master.
3.1.4 Machine level adjustment
After the machine is moved to the workplace from the crate, please re-adjust the level of the machine as
follows due to differences in the workplace:
First adjust the six foot cups of the machine to make it completely hold up the machine;
Then, remove the screws in the middle of the Y axis organ cover and crossbeam organ cover, and slide
the organ covers to both ends;

9
Then, place the level meter on the rails of the machine, observe the offset direction of bubble in the
level meter; first place the level meter on the rails of the beam; if bubble shifts left, the left side of the
machine is higher than the right side; adjust the machine level by reducing the height of left foot cup of
the machine or increasing the height of the right foot cup; when the bubble is centered in the level
meter, the level of the machine front has been adjusted properly;
Then, adjust the level of the rear, left and right side successively in the same way. After adjusting the
level of the four positions, the machine level has been adjusted properly, and next installation can
proceed.
Attention
The machine level adjustment is required. If the machine level is quite different, it will affect the subsequent use of
the machine.
3.1.5 Installing ventilation tube
Take out theΦ6″exhaust pipe, Φ6″hose clamp from the crate; as shown below, connect the exhaust
pipe and fan securely with Φ6" hose clamp;
Use a cross screwdriver to connect the exhaust pipe to the receiver through φ6 hose clamp as shown
below.
Installation Diagram of Exhaust Pipe and Fan
Installation location
Installation location

10
Installation Diagram of Exhaust Pipe and Receiver
3.1.6 Installing laser
First, move the beam to the rearmost of the machine, and remove the rear shield of the beam;
Then, unscrew the screws from the top cover of the support base with a hex wrench;
Take out the laser tube from the box and place the laser in the support base of the laser tube;
Use a hex wrench to tighten the screws to the top cover of the support base, and fix the laser tube to
the support base;
Adjust the position of the laser tube support base, and target the laser tube outlet at the first reflector;
Install earth wire, HV lines, inlet pipe and outlet pipe of the laser tube in sequence, and fix the lines with
adhesive tape;
Adjust the optical path concentricity of the laser tube and the reflector by adjusting the support base of
the laser tube and the nuts of the support base;
After adjusting the concentricity, fix the screws of the support base, and install the rear shield of the
beam.
Installation location
Installation location
Install ground wire
Water inlet
Water outlet
Install HV wire
(remove the cover
before installing)

11
Laser Installation Diagram
Attention
Be careful when moving and installing the laser. It is prohibited to force installation or knock at the laser; otherwise,
it will affect the stability of the laser power and cause light spot quality declines and even laser damage!
3.1.7 Installing water cooling system
First connect the water outlet of the chiller to the water inlet of the machine with the pipe provided
with the chiller, and connect the water inlet of the chiller to the water outlet of the machine;
Then, fill up the chiller with distilled water (medical deionized distilled water is recommended);
Connect the power and turn on the chiller, set the chiller temperature to room temperature ±5°C, and
adjust in the range 10°C~35°C;
After the chiller is turned on, if the laser is gradually filled with water and the water outlet pipe flows
smoothly, the chiller is working properly.
Remove this
cover before
removing the
laser tube
Adjust the height
of the laser tube
with this nut
This label on
the laser tube
should be
Fix the wire and tube on
the laser with insulating
tape

12
Chiller Fittings Installation Diagram
3.1.8 Installing air pump
The air pipe of the machine is in hard PU structure. For installation, insert the hard PU pipe directly into the
air pump and fast plug of the machine, as shown below:
The high pressure gas is very important in the system. The high pressure gas discharges from the light outlet
of the cutting head through the pipe. On the one hand, it ensures the cleanliness of the focusing lens, and
prevents materials being ignited by laser. Therefore, do not break or damage the air pipe during routine
maintenance, or else abnormal blowing may cause material burning.
Air Pump Interface Installation Diagram
Attention
Ensure that the height of the cooling water inside the tank is in predetermined range.
To ensure normal circulation of laser cooling water, the water outlet pipe is installed with flow switch. For
water-cooled laser tube, the water circulation must be normal, or else it may cause damage to the laser tube.
Therefore, pay attention to purified water and clean water pipes in routine maintenance process to prevent filter
screen clogging, resulting in poor water circulation and causing damage to the laser tube.
Water
inlet
Water
outlet
Gas outlet
Table of contents
Other Yueming Printer manuals
Popular Printer manuals by other brands
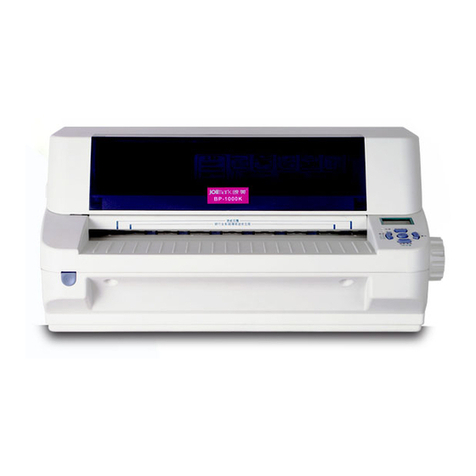
Jolimark
Jolimark BP-1000K (Model B) user manual
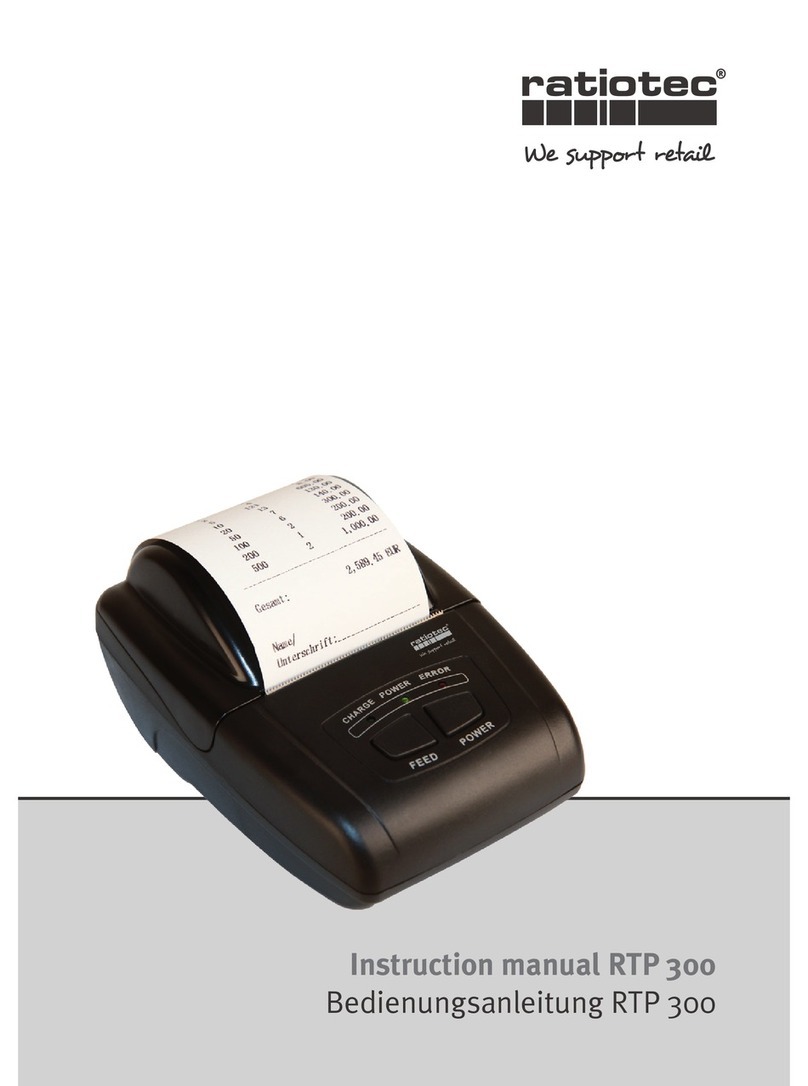
ratiotec
ratiotec RTP 300 instruction manual
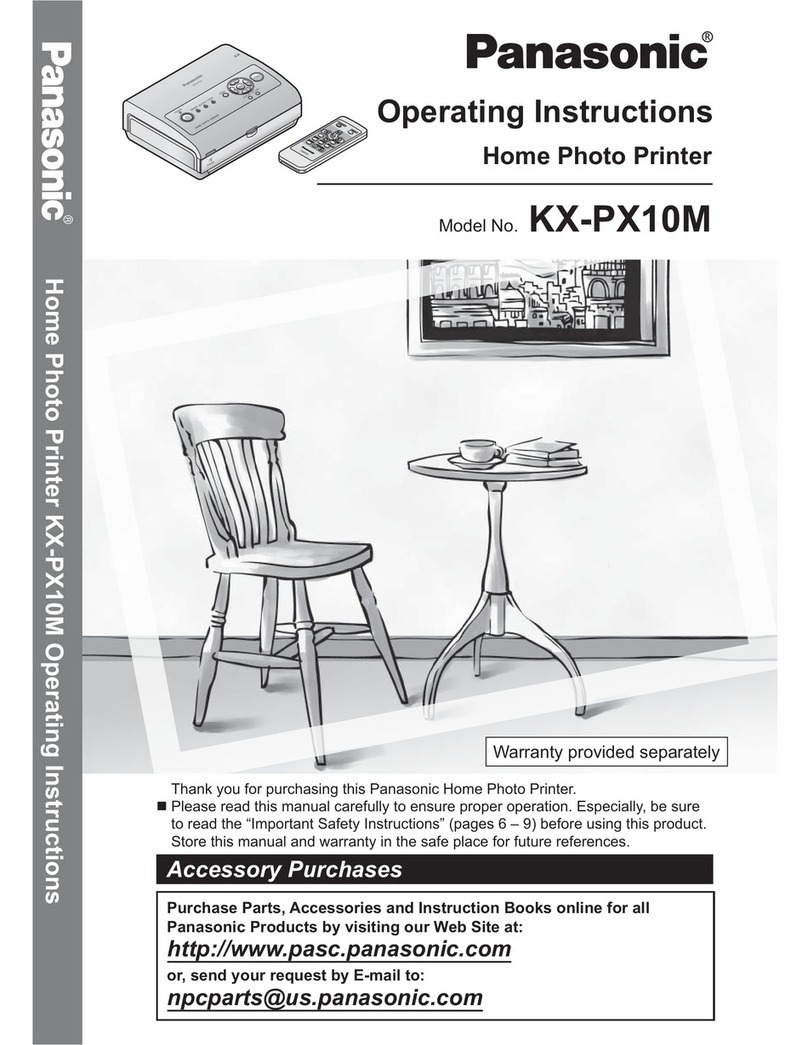
Panasonic
Panasonic KXPX10M - DIGITAL VIDEO PRINTER operating instructions
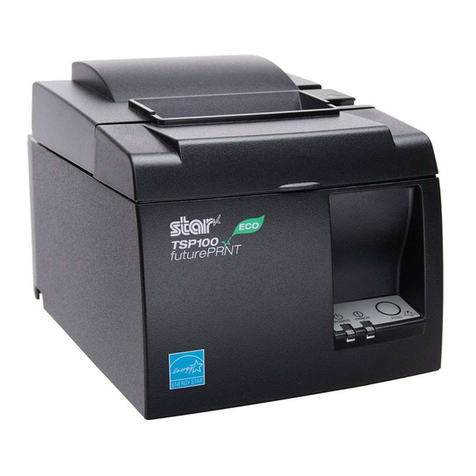
Star Micronics
Star Micronics TSP143IIU Hardware manual

Canon
Canon imageCLASS MP390 Setup guide
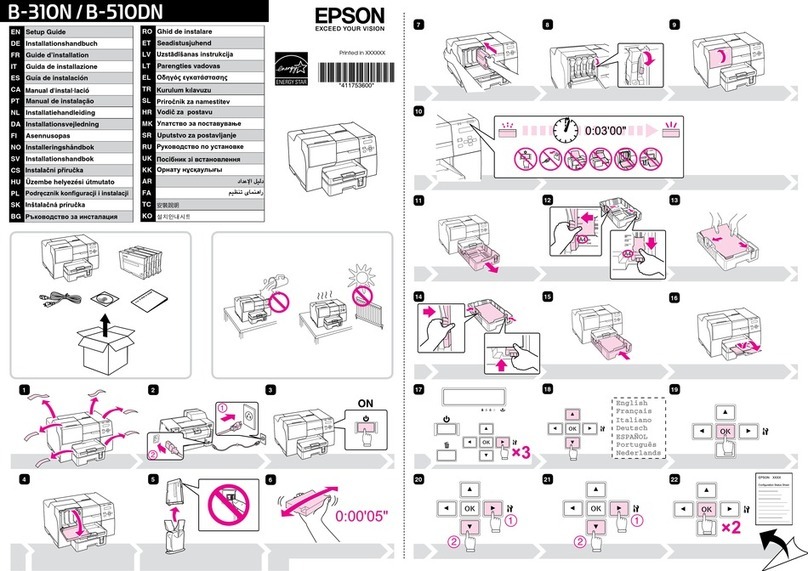
Epson
Epson B-310N - Business Color Ink Jet Printer Setup guide