Zaber Technologies Inc. X-LRQ-DEC Series User manual

X-LRQ-DEC Product
User's Manual
Firmware 5.00 and up
Last Update: November 2 2016
Visit www.zaber.com/wiki for more recent updates.
Zaber Technologies Inc.
#2 - 605 West Kent Ave. N.
Vancouver, British Columbia
Canada, V6P 6T7

Table of Contents
Disclaimer...........................................................................................................................................................1
Precautions.........................................................................................................................................................2
Lubrication of linear guides....................................................................................................................2
Conventions used throughout this document..................................................................................................3
Quick Tutorial....................................................................................................................................................4
Initial Set-up...........................................................................................................................................4
Initialization............................................................................................................................................4
Using the Device.....................................................................................................................................5
Modifying Device Settings...............................................................................................................5
Built-In Help.....................................................................................................................................5
Device Overview.................................................................................................................................................7
Connectors..............................................................................................................................................7
Power................................................................................................................................................7
RS-232 Communications.................................................................................................................7
Indicators.................................................................................................................................................7
Installation..........................................................................................................................................................9
Daisy-Chaining Devices.........................................................................................................................9
Physical Installation.........................................................................................................................................11
Dust Cover Removal and Installation...................................................................................................11
Manual Control................................................................................................................................................14
Velocity Mode......................................................................................................................................14
Displacement Mode..............................................................................................................................14
Summary of knob functionality............................................................................................................14
Trajectory Control and Behaviour.................................................................................................................15
Software Position Limits......................................................................................................................15
Movement Speed..................................................................................................................................15
Quick Command Reference............................................................................................................................16
ASCII Protocol.....................................................................................................................................16
Quick Commands...........................................................................................................................16
Quick Device Settings....................................................................................................................17
Binary Protocol.....................................................................................................................................19
Troubleshooting X-Series Motion Devices.....................................................................................................22
Front Panel Indicators...........................................................................................................................22
Manual Control.....................................................................................................................................23
Unexpected Behaviour..........................................................................................................................23
Communication Errors..........................................................................................................................23
Slipping and Stalling.............................................................................................................................25
i

Table of Contents
Warranty and Repair......................................................................................................................................26
Standard products..................................................................................................................................26
Custom products...................................................................................................................................26
How to return products.........................................................................................................................26
Email Updates..................................................................................................................................................27
Contact Information........................................................................................................................................28
Appendix A - Available Communications Ports...........................................................................................29
Finding Installed Serial Ports................................................................................................................29
Windows.........................................................................................................................................29
Linux..............................................................................................................................................29
Comparison - X-LRQ-DEC Series........................................................................................................32
ii

Disclaimer
Zaber’s devices are not intended for use in any critical medical, aviation, or military applications or situations
where a product's use or failure could cause personal injury, death, or damage to property. Zaber disclaims
any and all liability for injury or other damages resulting from the use of our products.
Disclaimer 1

Precautions
Zaber’s motion control devices are precision instruments and must be handled with care. In particular, moving
parts must be treated with care. Avoid axial loads in excess of the rated thrust load, axial and radial impact,
dust and other contaminants and damage to the drive components. These will reduce the performance of the
device below stated specifications.
Lubrication of linear guides
The X-LRQ-DEC series of linear stages use recirculating ball bearing linear guides to support and guide the
stage top of the device. These linear guides require lubrication in order to achieve the longest possible lifetime
at the highest possible performance. At the rated load of the device, it is recommended to re-lubricate each
bearing block on the linear guide at a 500 km service interval. We recommend using 0.2 cm³ per bearing
block of a NLGI Grade 2, lithium soap based grease. All guides come pre-lubricated and are ready to go out
of the box.
Precautions 2

Conventions used throughout this document
Fixed width type indicates communication to and from a device. The ↵symbol indicates a
carriage return, which can be achieved by pressing enter when using a terminal program.
•
An ASCII command followed by (T:xx) indicates a legacy T-Series Binary Protocol command that
achieves the same result. For example,
move abs 10000 (T:20:10000) shows that a move abs ASCII command can also be
achieved with Binary command number 20.
•
Not all ASCII commands have an equivalent Binary counterpart.
Conventions used throughout this document 3

Quick Tutorial
We recommend using Zaber Console to communicate with the device(s). For other software options, see
Software. Please refer to the ASCII Protocol Manual and/or Binary Protocol Manual for more detailed
information on the available commands.
Initial Set-up
Power up all integrated devices and controllers and daisy chain them together using the RS-232
"Prev" and "Next" connectors (see Daisy-Chaining Devices for more details). Many products share
power through the daisy-chain cables. The power indicator on each should light up.
1.
Turn the knob to move a device. Most devices will only move in one direction until they reach a home
sensor at one limit of travel. Then they will move in both directions over full travel.
2.
Download and install Zaber Console from http://www.zaber.com/wiki/Software. Start Zaber Console
and select the communications port the first controller is connected to. For instructions on how to find
the available communication ports on your system, please refer to: Appendix A - Available
Communications Ports.
3.
From the Console, issue a renumber (T:2) command to all devices (Zaber Console may prompt you to
do this also). The first device in the chain (closest to the computer) will become Device 1, the next
will become Device 2, and so on.
4.
Initialization
Every time the device is powered up or reset, the device should be returned to the home position. This is
achieved by sending the home (T:1) command to the individual unit or all units. Until this is done, most
devices will only allow motion in one direction, towards the sensor.
If it is not possible in your application to home the device after every power-up, see the tools parking (T:65)
Quick Tutorial 4

command. Parking allows the device to be turned off and then used at a later time without first having to
home the axes.
Using the Device
Several commonly used ASCII commands, and their Binary equivalents, are shown below. For a full list of
available commands, please refer to the Command Reference section below.
Command Description
/1 1 get pos↵ (T:60) Query the current position of Device #1 Axis #1.
/1 1 move abs 10000↵ (T:20:10000) Move Device #1, Axis #1 to position 10000 microsteps.
/2 1 move
rel -12800↵ (T:21:-12800) Move Device #2, Axis #1 in the negative direction by 12800 microsteps.
/1 stop↵ (T:23) Decelerate and stop ALL axes on Device 1.
An axis number of 0 or no axis number implies all axes on the device, or
the device itself.
/move vel 153600↵ (T:22:153600)
Move ALL devices and ALL axes in the positive direction at the speed
153600.
A device address of 0 or no device address implies all devices in the
chain.
Modifying Device Settings
Here are some examples if you would like to customize particular device settings. Refer to the ASCII Settings
or Command Reference section for detailed descriptions of each setting.
Command Description
/1 set maxspeed 100000↵ (T:42:100000) Set the speed of all axes on the device.
/1 get maxspeed↵ (T:53:42) Query the axes' speed.
/1 system restore↵ (T:36) Restore all the settings of Device 1 to the default.
Built-In Help
Zaber X-Series devices feature a built-in help guide, providing a quick and easy reference for all Commands
and Settings that the device has. To access the help, send: /1 help↵ (for help with Device 1). The device
number must be specified in the help command. This feature is only available in the ASCII protocol.
The device will respond with a detailed description on how to access specific information about commands
and replies, as shown below:
@01 0 OK IDLE WR 0
#01 0 COMMAND USAGE:
#01 0 '/stop' stop all devices
#01 0 '/1 stop' stop device number 1
#01 0 '/1 2 stop' stop device number 1 axis number 2
#01 0
#01 0 Type '/help commands' for a list of all top-level commands.
#01 0 Type '/help reply' for a quick reference on reply messages.
#01 0 Visit www.zaber.com/support for complete instruction manuals.
To access help for a specific command, for example the move command, send:
Initialization 5

/1 help move↵
@01 0 OK IDLE -- 0
#01 0 move abs {x} Move to absolute position
#01 0 move rel {x} Move by relative position
#01 0 move vel {x} Move at constant velocity
#01 0 move min Move to minimum position
#01 0 move max Move to maximum position}
Built-In Help 6

Device Overview
Connectors
All images are shown looking into the device.
Power
Pin Description
1 24 - 48V
2 GND (Note: Zaber's power supplies ground this pin to AC Earth)
Note: To prevent damage to the device due to static buildup, the device should be properly grounded. The
power supplies Zaber provides for X-Series devices are non-isolated and thus ground the device chassis to
Earth via the negative terminal of the power supply. If for any reason you are using an isolated power supply,
please ensure your device is grounded by connecting the negative terminal of the power connector to AC
Earth.
RS-232 Communications
Pin Previous Next
1 Power Power
2 Ground Ground
3 Receive Transmit
4 Transmit Receive
Default Settings
Baud Rate: 115200• Protocol: Zaber ASCII•
Specifications
Supported Protocols: Zaber ASCII, Zaber Binary• Supported Baudrates: 9600, 19200, 38400, 57600, 115200• Bits: 8• Parity: None• Stop Bits: 1• Flow Control: None•
Indicators
Green - Power
On: Controller is operational.• Blinking at 2Hz: The power supply voltage or device temperature is out of range.• Fading in and out slowly: The device is parked. See the tools parking (T:65) command.•
Device Overview 7

Red - Error
On/blinking: Device has lost its settings, or an error has occurred. Please contact Zaber Technical
Support.
•
Yellow - Communication/Busy
On: Device is moving, or data is being transferred.• Blinking: Device is under manual control via the knob (in Velocity mode). The blinking rate is
proportional to movement speed.
•
Blinking at fixed rate: Packet corruption has occurred for ASCII commands sent with a checksum.•
Blue - Slip/Stall
On: The device is slipping.• 2 short flashes every 1 sec: The stationary device has been forced out of position.• On-Off cycle every 2 sec: The device has stalled and stopped.•
Indicators 8

Installation
The X-LRQ-DEC can be connected to a computer as follows:
Either plug the M8 to D-SUB serial adaptor (X-SDC) into the computer's serial port, or the M8 to
USB adaptor (X-USBDC) into one of your computer's USB ports, then attach the device to the
adaptor. For the USB adaptor, new computers will often be able to install the necessary drivers
automatically when the cable is plugged in for the first time. If the computer reports that the driver
installation was unsuccessful, you can download the drivers for Windows, Mac, or Linux here.
Installation instructions and troubleshooting information are available for each operating system here.
You may need to use a cable extension to reach your computer. There is no need to power-down or
reboot the computer.
1.
Connect the power plug of your power supply to the power connector of the unit. The green LED
should light up indicating the unit has power.
2.
Additional devices can simply be daisy-chained to the first. See Daisy-Chaining Devices below.3. Install software from http://www.zaber.com/wiki/Software. For the initial setup, using Zaber Console
is recommended.
4.
As a simple first test, try entering:
/renumber↵ (T:2)
/1 home↵ (T:1)
/1 move rel 10000↵ (T:21:10000)
The parameter of 10000 in the move command above specifies 10000 microsteps. To see the microstep size
(default resolution) for the device and how it translates to displacement, first go to the product overview page,
find your device, click through to the device's webpage, and click on the "Series Specs" tab. The microstep
size (default resolution) will be shown in the list of product specs either in the "Group Specifications" section
or the "Comparison" section.
Daisy-Chaining Devices
Multiple devices can be connected together in a chain through the Prev and Next connectors. This allows any
number of devices to be controlled from a single connection to a computer, reducing cabling demands. In
addition, X-Series devices carry power through the daisy chain, so in most cases a power supply only needs to
be connected to one device in the chain. Whenever a device is added or removed from a chain, a
renumber (T:2) command should be sent to prevent device-address conflicts.
Installation 9

To daisy-chain X-Series devices with T-Series and A-Series devices:
Ensure all devices are set to the same communication protocol and baud rate before connecting them.
If any T-Series devices will be in the chain, then the communication protocol must be Binary at 9600
baud rate.
•
Connect any X-Series devices at the start of the chain (closest to the computer). This configuration
will reduce the number of adaptor cables required.
•
Connect a T-XDC (or S-XDC for daisy-chaining an A-MCB2) adaptor cable to the Next port of the
last X-Series device in the chain, and to the Prev port of the T-Series or A-Series device.
•
Power supplied to an X-Series device will not be transmitted to any T-Series or A-Series devices in
the chain.
•
Contact Zaber Technical Support for assistance selecting connecting cables when daisy-chaining
multiple series.
•
Daisy-Chaining Devices 10

Physical Installation
The X-LRQ-DEC stage has two sets of mounting features that are acceptable means of fastening the stage to a
structure. The first are the slotted holes in the middle of the stage which use M6 fasteners on a 25 mm x 50
mm grid. The second set of mounting features are the T-slots located on the bottom of the stage which are 84
mm apart. The T-slots will generally accept T-nuts that are used in 20 mm aluminum T-slot extrusions.
Do not mount the stage using the T-slots on the side on the device. The T-slots are designed for use with
accessories such as limit sensors, linear encoders, and cable trays only. This T-slot is designed to accept a
standard M2.5 hex nut. Damage will occur if these T-slots are used to mount the stage.
Dust Cover Removal and Installation
Use caution handling the shim as the edges are extremely sharp. For disassembly, simply remove the four screws securing the stainless steel dust cover shim and slide the shim out.
In most cases, the shim only needs to be lifted slightly to install the mounting screws and does not require full removal. Take care not to kink or bend the shim.
Move the stage at least 50mm away from one end of the LRQ base and feed the LRQ Dust Cover
Shim in from one side. Use a business card as a ramp to help guide the shim over the first rise and
under the second. Be careful not to kink the Dust Cover Shim or cut your fingers on the sharp metal!
•
Carefully feed the Dust Cover Shim through the stage top adapter, making sure that the shim doesn't
rub directly on the aluminum of the Stage Top Adapter. Align the mounting holes at each end such
that the Dust Cover Shim covers all of the magnet slots in the Sheet Metal Sides.
•
Physical Installation 11

Take 2x M3x3 screws and thread them through the Dust Cover Shim and into the Dust Cover Shim
Mount Away. Pull the shim as far as it can go towards the away end, and hand tighten the screws,
ensuring that the Dust Cover Shim does not twist during tightening.
•
Take the remaining 2x M3x3 screws and thread them through the Dust Cover Shim and into the Dust
Cover Shim Mount Home, leaving them loose. Push down on the Dust Cover Shim inside the Stage
Top Adapter, and tighten the M3x3 screws.
•
When properly tensioned, the LRQ Dust Cover Shim should sit below the lid mounting ledge as
indicated and should still have a slight bend. The LRQ Dust Cover Shim should be low enough that it
does not contact the bottom of the LRQ Dust Cover Adapter Lid when installed, but it should not be
so tight that it increases the drag of the stage.
•
Drive the LRQ stage back and forth through its full length a few times, and visually inspect that the
Dust Cover Shim does not bulge anywhere during travel. If the shim bulges, loosen and then re-torque
the M3x3 screw nearest the bulge in order to remove it. If loosening both screws on an end, you may
need to push down on the shim inside the Stage Top Adapter again to add some tension. Repeat this
process until the Dust Cover Shim stays flush with the Sheet Metal Sides through the full length of
travel.
•
Dust Cover Removal and Installation 12

Take the LRQ Dust Cover Adapter Lid and place it in position on the Stage Top Adapter, ensuring
that the countersink holes are on the top. Take the M2x4 screws and hand tighten them into the Stage
Top Adapter.
•
Dust Cover Removal and Installation 13

Manual Control
The X-Series motion control products have an integrated, depressible knob with 20 detents per revolution,
allowing devices to be controlled without the use of a computer. There are two manual movement modes
available: Velocity and Displacement. Switch between these modes by holding down the knob for 1 second or
by configuring the knob.mode (T:109) setting.
On power-up, the device will only travel towards the motor from its start-up position until the home position
is reached. Once the device has been homed, the full range of travel becomes available.
Velocity Mode
Turn the knob clockwise to move the device in the positive direction (extend) or counter-clockwise for
negative direction (retract). Each detent of the knob increases the speed of the carriage.
There are 16 speeds in each direction. The velocity profile and maximum speed can be configured via the
knob.speedprofile (T:112) and knob.maxspeed (T:111) settings. The device stops and resets the knob upon
arriving at the end of travel.
Displacement Mode
Turn the knob clockwise to move the device in the positive direction (extend), counter-clockwise for negative
direction (retract). Each detent of the knob moves the device a fixed number of microsteps, specified by the
knob.distance (T:110) setting. If knob.distance (T:110) is set to 0, each detent of the knob will move to the
next index position, similar to move index (T:78) movements. The device moves at the speed specified by the
maxspeed (T:42) setting, or the slower of maxspeed (T:42) and limit.approach.maxspeed (T:41) if the device
has not been homed. If there are fewer than knob.distance (T:110) microsteps to the end of travel and another
move is requested, the device will move to the end of travel and then stop.
Summary of knob functionality
Turning the knob:
Moves the device in the direction of knob turn.
•
Pressing the knob:
Decelerates and stops the device (identical to a stop (T:23) command).
Instantly stops the device, if the device is already decelerating.
•
Pressing and holding the knob for 1 sec:
Toggles between Velocity Mode and Displacement Mode.
•
Manual Control 14

Trajectory Control and Behaviour
This section describes the behaviour of the device trajectory when a movement command is issued.
Software Position Limits
The travel range of the device is limited by the Minimum Position and Maximum Position settings. The
factory settings for the devices are configured to match the physical travel range. If a customized range is
desired, it can be changed by configuring the limit.min (T:106) and limit.max (T:44) settings to appropriate
values.
Minimum Position
When the Current Position is less than the Minimum Position value, the device cannot move in the
negative direction (towards the motor).
Maximum Position
When the Current Position is greater than the Maximum Position value, the device cannot move in the
positive direction (away from the motor).
Movement Speed
The movement speed of the device depends on device status and various speed settings. If the device has not
been initialized by the home (T:1) command or by moving towards the home end of the device, movement
speed will be constrained to fail-safe values. The home status of the device can be determined by reading the
limit.sensor.triggered (T:53) setting (the binary command additionally requires a value of 103).
Movement speed of the device is specified below:
move vel (T:22)
The device will move at the specified speed regardless of home status.
Knob movement in Velocity Mode
The device will move at the specified speed regardless of home status.
The speed is specified by the knob.speedprofile (T:112) and knob.maxspeed (T:111) settings.
Other movement commands - when the device has not been homed
The device will move at the slower of the maxspeed (T:42) and limit.approach.maxspeed (T:41)
settings.
Other movement commands - when the device has been homed
The device will move at the speed specified by the maxspeed (T:42) setting.
Trajectory Control and Behaviour 15

Quick Command Reference
All X-Series devices ship with the ASCII Protocol enabled by default but the Binary Protocol is also
supported.
ASCII Protocol
The following table offers a quick command and setting reference for the X-LRQ-DEC. Follow the links to
view a detailed description of each instruction or refer to the ASCII Protocol Manual.
Quick Commands
Parameters in square brackets, e.g. [clr], indicate that the parameter is optional.
Parameters in italics, e.g. value, indicate that data, typically a number, needs to be provided.
Parameters separated by a pipe, e.g. abs|rel, indicate that one of the parameters in the set need to be provided.
Command Scope Parameter(s) Returns Firmware
Versions Description
calibration Device Refer to the
documentation 0 6.24+ Configure linear encoder
calibration.
estop Axis 0 6.06+ Instantly stops motorized
movement.
get Device
and Axis setting value 6.06+ Retrieves the current value of
the device or axis setting.
help Device
commands
reply
warnflags
enums
command ...
enum
0 6.06+ Displays the help
information for the system.
home Axis 0 6.06+ Moves the axis to the home
position.
move Axis
abs|rel|vel value
min|max
stored number
index number (6.21+)
sin amplitude period
[count] (6.22+)
sin stop (6.22+)
0 6.06+ Moves the axis to various
positions along its travel.
renumber Device value 0 6.06+ Renumbers all devices in the
chain.
set Device
and Axis setting value 0 6.06+ Sets the device or axis setting
setting to the value.
stop Axis 0 6.06+ Decelerates the axis and
brings it to a halt.
stream Device Refer to the
documentation Refer to the
documentation 6.12+ Performs an action related to
streamed, interpolated
Quick Command Reference 16

multi-axis motion.
system reset Device 0 6.06+ Resets the device, as it would
appear after power up.
system
restore Device 0 6.06+ Restores common device
settings to their default
values.
tools echo Device (message) 0 6.06+ Echoes the provided message
(if any) back to the user.
tools
gotolimit Axis limit dir action update 0 6.06+ Moves the axis to a limit
sensor and performs the
provided actions.
tools
parking Device state|park|unpark 0|1 6.06+
Parking allows the device to
be turned off and used at a
later time without first
having to home.
tools
setcomm Device rs232baud protocol 0 6.06+ Sets RS232 baud rate and
communication protocol for
RS232 and USB.
tools
storepos Axis number
[position|current] 0|position 6.06+ Stores a number of positions
for easy movement.
trigger Device Refer to the
documentation 0 6.06+
Configures actions to be
performed on the device
when a certain condition is
met.
warnings Axis [clear] 0 6.06+ Displays the active device
and axis warnings, optionally
clearing them if applicable.
Quick Device Settings
The settings listed below can be inspected and modified with the get and set commands described above.
Setting Scope Writable Firmware
Versions Description
accel Axis Yes 6.06+ Sets the acceleration used to modify the speed.
calibration.type Axis No 6.24+ The type of calibration saved for the axis.
cloop.counts Axis Yes 6.06+ The number of counts generated by the encoder
for one full revolution.
cloop.displace.tolerance Axis Yes 6.19+ Allowed position deviation before displacement
is reported.
cloop.duration.max Axis Yes 6.17+ Direct reading or linear encoder fine correction
attempt duration.
cloop.mode Axis Yes 6.06+ Sets the closed loop control mode.
cloop.stalltimeout Axis Yes 6.06+ The amount of time to wait after a
stall/displacement condition, in milliseconds.
cloop.steps Axis Yes 6.06+ The number of full steps required for the motor
to complete one revolution.
comm.address Device Yes 6.06+ The device address.
Quick Commands 17
Table of contents
Other Zaber Technologies Inc. Control Unit manuals
Popular Control Unit manuals by other brands
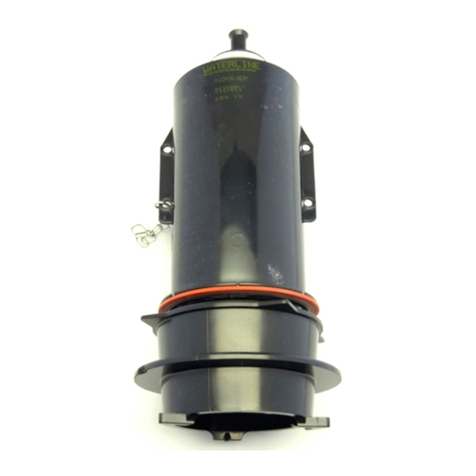
Kohler
Kohler 1216612 Service manual
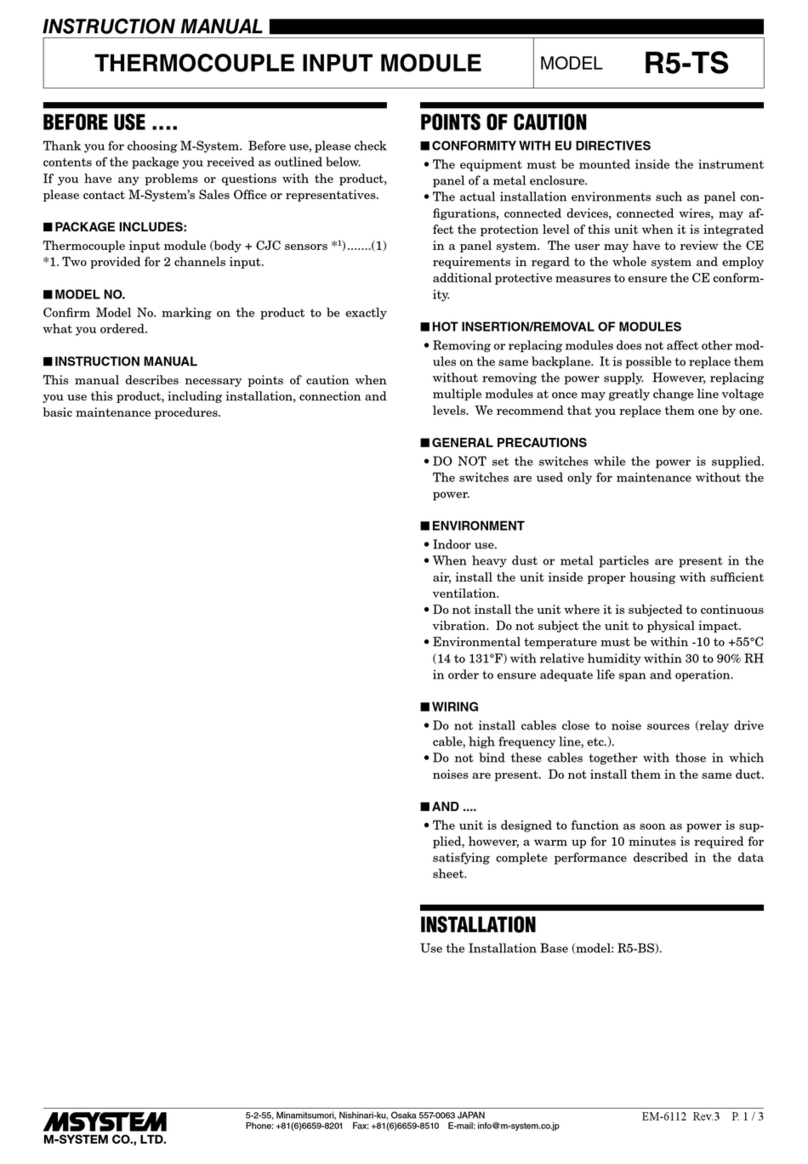
M-system
M-system R5-TS instruction manual

Spectrum Digital
Spectrum Digital TMS320VC5509 Technical reference
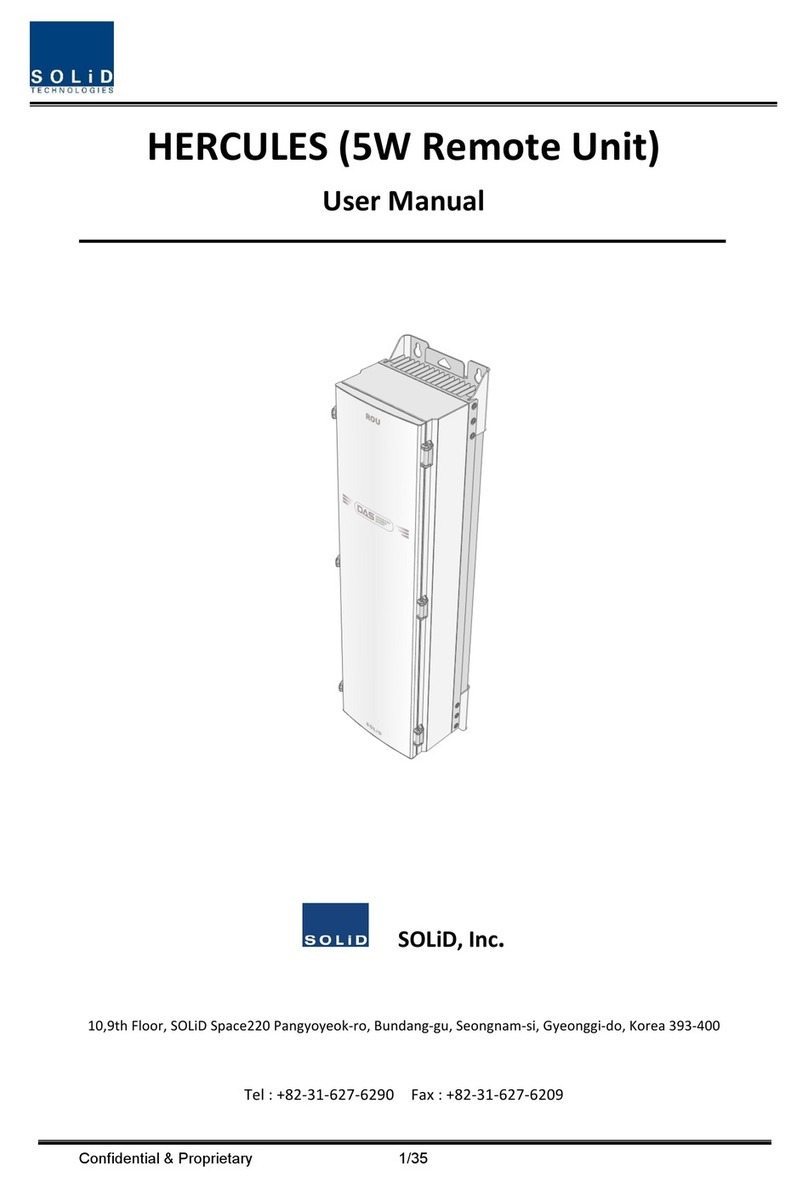
Solid Technologies
Solid Technologies HERCULES user manual
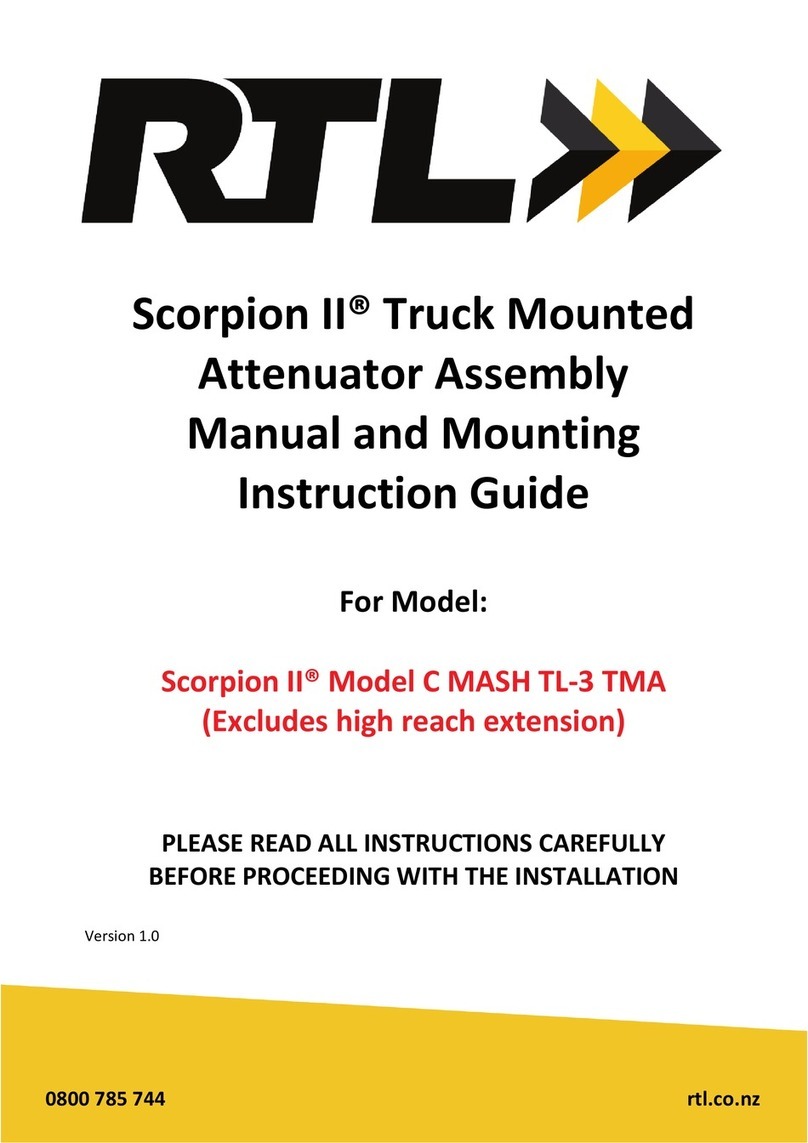
RTL
RTL Scorpion II C MASH TL-3 TMA Assembly Manual and Mounting Instruction Guide
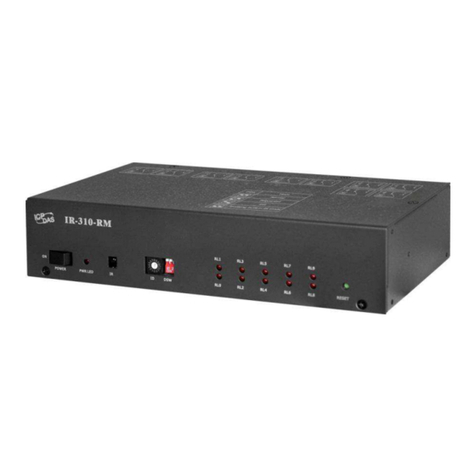
ICP DAS USA
ICP DAS USA IR-310-RM user manual