Zenith ZPP 416 User manual


ZPP 416 - Engine DOHC
GENERAL
TIMING SYSTEM
TIMING BELT
CYLINDER HEAD ASSEMBLY
CYLINDER HEAD
MAIN MOVING SYSTEM
CAM SHAFT
CRANK SHAFT
FLY WHEEL
PISTON
COOLING SYSTEM
ENGINE COOLANT HOSE/PIPES
ENGINE COOLANT PUMP
RADIATOR
RADIATOR CAP
THERMOSTAT
LUBRICATION SYSTEM
OIL PUMP
ENGINE BLOCK
ENGINE BLOCK
INTAKE AND EXHAUST SYSTEM
EXHAUST MANIFOLD
INTAKE MANIFOLD

EM -2 ENGINE DOHC
GENERAL
SPECIFICATION E5EC07D6
Description Specification Limit
General
Type
Number of cylinders
Bore
Stroke
Total displacement
Compression ratio
Firing order
In-line, Double Over Head Camshaft
4
76.5mm (3.0118 in)
87mm (3.4252 in)
1599 cc (97.54 cu.in)
10
1-3-4-2
Valve timing
Intake valve
Opens (BTDC)
Closes (ABDC)
Exhaust valve
Opens (BBDC)
Closes (ATDC)
Valve overlap
5
35
43
5
10
Cylinder head
Flatness of cylinder head surface
Flatness of mainfold mounting surface
Oversize rework dimension of valve seat hole
Intake
0.3mm (0.012 in.) O.S.
0.6mm (0.024 in.) O.S.
Exhaust
0.3mm (0.012 in.) O.S.
0.6mm (0.024 in.) O.S
Max. 0.03mm (0.0012 in.)
0.15mm (0.0059 in.)
30.7 ~ 30.721 mm (1.2087 ~ 1.2095 in.)
31.0 ~ 31.021 mm (1.2205 ~ 1.2213 in.)
27.3 ~ 27.321mm (1.0748 ~ 1.0756 in.)
27.6 ~ 27.621mm (1.0866 ~ 1.0874 in.)
0.1 mm (0.0039in.)
0.2mm (0.008in.)
Oversize rework dimensions of valve
Guide hole
0.05mm (0.002 in.) O.S.
0.25mm (0.010 in.) O.S.
0.50mm (0.020 in.) O.S.
11.05 ~ 11.068mm (0.435 ~ 0.4357 in.)
11.25 ~ 11.268mm (0.443 ~ 0.4436 in.)
11.50 ~ 11.518mm (0.453 ~ 0.4535 in.)
Camshaft
Cam lobe height
Intake
Exhaust
Joumal O.D
Bearing oil clearance
End play
43.4484mm (1.7106 in.)
43.8489mm (1.7263 in.)
ø27mm (1.0630 in.)
0.035 ~ 0.072mm (0.0014 ~ 0.0028 in.)
0.1 ~ 0.2mm (0.004 ~ 0.008 in.)
42.9484mm
(1.6909in.)
43.3489mm
(1.7.66in.)
ZENITH POWER PRODUCTS - 416

GENERAL EM -3
Description Specification Limit
Valve
Valve length
Intake
Exhaust
Stem O.D.
Intake
Exhaust
Face angle thickness of valve head (Margin)
Intake
Exhaust
Valve stem to valve guide clearance
Intake
Exhaust
91.7mm (3.6102 in.)
92.3mm (3.6339 in.)
5.955 ~ 5.97mm (0.2344 ~ 0.2350 in.)
5.935 ~ 5.95mm (0.2337 ~ 0.2343 in.)
1.1mm (0.0433 in.)
1.3mm (0.0512 in.)
0.03 ~ 0.06mm (0.0012 ~ 0.0024 in.)
0.05 ~ 0.08mm (0.0020 ~ 0.0031 in.)
0.8mm (0.031in.)
1.0mm (0.039in.)
0.10mm (0.0039in.)
0.15mm (0.0059in.)
Valve guide
Installed dimension O.D.
Intake
Exhaust
Service size
12.8mm (0.504 in.)
12.8mm (0.504 in.)
0.05, 0.25, 0.50mm
(0.002, 0.010, 0.020 in.) oversize
Valve seat
Width of seat contact
Intake
Exhaust
Seat angle
Oversize
0.8 ~ 1.2mm (0.031 ~ 0.047 in.)
1.3 ~ 1.7mm (0.051 ~ 0.066 in.)
45
0.3, 0.6mm (0.012, 0.024 in.) oversize
Valve spring
Free length
Load
Squareness
44.00mm (1.7323 in.)
21.6kg/ 35mm (47.6lb/1.3780 in.)
45.1kg/ 27.2mm (99.4lb/1.071 in.)
1.5 or less
Cylinder block
Cylinder bore
Out- of- round and taper of cylinder bore
Clearance with piston
76.50 ~ 76.53mm (3.0118 ~ 3.0130 in.)
Less than 0.01mm (0.0004 in.)
0.025 ~ 0.045mm (0.0009 ~ 0.0017 in.)
Piston
O.D.
Service size 76.465 ~ 76.495mm (3.0104 ~ 3.0116 in.)
0.25 mm (0.010 in.) oversize
Piston ring
Side clearance
No. 1
No. 2
Endgap
No. 1
No. 2
Oil ring side rail
Service size
0.04 ~ 0.085 mm (0.0015 ~ 0.0033 in.)
0.04 ~ 0.085 mm (0.0015 ~ 0.0033 in.)
0.15 ~ 0.30 mm (0.0059 ~ 0.012 in.)
0.30 ~ 0.45 mm (0.012 ~ 0.0177 in.)
0.2 ~ 0.7 mm (0.0078 ~ 0.0275 in.)
0.25 mm (0.010 in.) oversize
0.1 mm (0.004 in.)
0.1 mm (0.004 in.)
1.0 mm (0.039 in.)
1.0 mm (0.039 in.)
1.0 mm (0.039 in.)
ZENITH POWER PRODUCTS - 416

EM -4 ENGINE DOHC
Description Specification Limit
Connecting rod
Bend
Twist
Connecting rod big end to crankshaft
side clearance
Connecting rod bearing oil clearance
Undersize
0.05mm (0.0020 in.) or less
0.1mm (0.0039 in.) or less
0.100-0.250mm (0.0039-0.0098 in.)
0.018-0.036mm (0.0007-0.0014 in.)
0.25, 0.50, 0.75mm
(0.010, 0.020, 0.030 in.)
0.4mm (0.0157in.)
Crankshaft
Pin O.D.
Journal O.D.
Bend
Out- of- round, taper of journal and pin
End play
45 mm (1.77 in.)
50 mm (1.97 in.)
0.03 mm (0.0012 in.) or less
0.005 mm (0.0002 in.) or less
0.05- 0.175 mm (0.0019- 0.0068 in.)
Undersize rework dimension of pin
0.25mm (0.010 in.)
0.50mm (0.020 in.)
0.75mm (0.030 in.)
44.725 ~ 44.74mm (1.7608 ~ 1.7614 in.)
44.475 ~ 44.49mm (1.7509 ~ 1.7516 in.)
44.225 ~ 44.24mm (1.7411 ~ 1.7417 in.)
Undersize rework dimension of journal
0.25mm (0.010 in.)
0.50mm (0.020 in.)
0.75mm (0.030 in.)
49.727 ~ 49.742mm (1.9577 ~ 1.9583 in.)
49.477 ~ 49.492mm (1.9479 ~ 1.9485 in.)
49.227 ~ 49.242mm (1.9380 ~ 1.9386 in.)
Flywheel
Runout 0.1mm (0.0039 in.) 0.13mm (0.0051in.)
Oil pump
Clearance between outer circumference
and front case (body clearance)
Front case tip clearance
Side clearance
Inner gear
Outer gear
0.12 ~ 0.18mm (0.0047 ~ 0.0070 in.)
0.025 ~ 0.069mm (0.001 ~ 0.0027 in.)
0.04 ~ 0.085mm (0.0016 ~ 0.0033 in.)
0.04 ~ 0.09mm (0.0016 ~ 0.0035 in.)
Engine oil pressure
Engine at idle [Oil temperature is 90 to
100 C(194to215F)] 147KPa (1.5 kg/ cm², 21.33psi)
Relief spring
Free height
Load 46.6mm (1.8346 in.)
6.1kg at 40.1mm (13.42lb/ 1.578 in.)
Cooling method Water-cooled, pressurized, forced circulation
with electrical fan
Coolant
Quantity
Radiator
Type
6.5 liter
Pressurized corrugated fin type
Radiator cap
Main valve opening pressure
Vacuum valve opening pressure
81.4 ~ 108 kpa (11.8 ~ 15.6 psi.,0.83
~1.1kg/cm²)
-6.86 kpa (-1.00 psi, -0.07 kg/cm² or less
Coolant pump Centrifugal type impeller
ZENITH POWER PRODUCTS - 416

GENERAL EM -5
Description Specification Limit
Thermostat
Type
Valve opening temperature
Full-opening temperature
Waxpellettypewithjigglevalve
82 C (180 F)
95 C (203 F)
Engine coolant temperature sensor
Type
Resistance Heat-sensitive thermistor type
2.31 ~ 2.59k at 20 C(68 F)
146.9 ~ 147.3 at 110 C(230 F)
Air cleaner
Type
Element Dry type
Un woven cloth type
Exhaust pipe
Muffler
Suspension system Expansion resonance type
Rubber hangers
NOTE
O.D. = Outer Diameter
I.D. = Inner Diameter
O.S. = Oversize Diameter
U.S. = Undersize Diameter
ZENITH POWER PRODUCTS - 416

EM -6 ENGINE DOHC
TIGHTENING TORQUE
Item Nm Kg.cm Ib.ft
Cylinder Block
Front engine support bracket bolt and nut
Engine suppot bracket stay bolt
Oil pressure switch
45 ~ 55
45 ~ 55
13 ~ 15
450 ~ 550
450 ~ 550
130 ~ 150
33 ~ 41
33 ~ 41
10 ~ 11
Cylinder head
Cylinder head bolt
Intake manifold bolts or nuts
Exhaust manifold nut
Cylinder head cover bolt
Camshaft bearing cap bolt
Rear plate bolt
30+(90 )+Release
all bolts+30+(90 )
15 ~ 20
25 ~ 30
8~10
12 ~ 14
32 ~ 35
300+(90 )+Release all
bolts+300+(90 )
150 ~ 200
250 ~ 300
80 ~ 100
120 ~ 140
320 ~ 350
22+(90 )+Release
all bolts+22+(90 )
11 ~ 15
18 ~ 22
6~7
9~10
24 ~ 26
Main Moving system
Connecting rod cap nut
Crankshaft bearing cap bolt
Fly wheel M/T bolt
Drive plate A/T bolt
32 ~ 35
55 ~ 60
120 ~ 130
120 ~ 130
320 ~ 350
550 ~ 600
1200 ~ 1300
1200 ~ 1300
24 ~ 26
41 ~ 44
89 ~ 96
89 ~ 96
Timing system
Crankshaft pulley bolt
Camshaft sprocket bolt
Timing belt tensioner bolt
Timing belt idle bolt
Timing belt cover bolt
Front case bolt
140 ~ 150
80 ~ 100
20 ~ 27
43 ~ 55
8~10
20 ~ 27
1400 ~ 1500
800 ~ 1000
200 ~ 270
430 ~ 550
80 ~ 100
200 ~ 270
103 ~ 111
59 ~ 74
15 ~ 20
32 ~ 41
6~7
15 ~ 20
Engine Mounting
Right mounting insulator (large) bolt
Right mounting insulator (small) nut
Transmission mount insulator bolt
Transmission insulator bracket to side
member bolts
Front roll stopper insulator bolt
Front roll stopper bracket to sub frame bolt
Rear roll stopper insulator bolt
Rear roll stopper bracket to sub frame bolt
90 ~ 110
50 ~ 65
90 ~ 110
30 ~ 40
45 ~ 60
30 ~ 40
45 ~ 60
30 ~ 40
900 ~ 1100
500 ~ 650
900 ~ 1100
300 ~ 400
450 ~ 600
300 ~ 400
450 ~ 600
300 ~ 400
66 ~ 81
37 ~ 48
66 ~ 81
22 ~ 30
33 ~ 44
22 ~ 30
33 ~ 44
22 ~ 30
Oil filter
Oil pan bolts
Oil pan drain plug
Oil screen bolts
12 ~ 16
10 ~ 12
40 ~ 45
15 ~ 22
120 ~ 160
100 ~ 120
400 ~ 450
150 ~ 220
9~12
7~9
30 ~ 33
11 ~ 16
ZENITH POWER PRODUCTS - 416

GENERAL EM -7
Item Nm Kg.cm Ib.ft
Alternator support bolt and nut
Alternator lock bolt
Alternator brace mounting bolt
Coolant pump pulley
Coolant pump bolt
Coolant temperature sensor
Coolant inlet fitting bolt
Thermostat housing bolt
20 ~ 25
12 ~ 15
20 ~ 27
8~10
12 ~ 15
25 ~ 30
17 ~ 20
15 ~ 20
200 ~ 250
120 ~ 150
200 ~ 270
80 ~ 100
120 ~ 150
250 ~ 300
170 ~ 200
150 ~ 200
15 ~ 18
9~11
15 ~ 20
6~7
9~11
18 ~ 22
13 ~ 14
11 ~ 14
Air cleaner body mounting bolts
Resonator mounting bolts
Intake manifold to cylinder head nuts and bolts
Surge tank stay to cylinder block bolts
Throttle body to surge tank bolts
Exhaust manifold to cylinder head nuts
Exhaust manifold cover to exhaust
manifold bolts
Oxygen sensor to exhaust manifold
Front exhaust pipe to exhaust manifold nuts
Front exhaust pipe bracket bolts
Front exhaust pipe to catalytic converter bolts
8~10
4~6
15 ~ 20
18 ~ 25
15 ~ 20
25 ~ 30
15 ~ 20
50 ~ 60
30 ~ 40
30 ~ 40
40 ~ 60
[80 ~ 100
40 ~ 60
150 ~ 200
180 ~ 250
150 ~ 200
250 ~ 300
150 ~ 200
500 ~ 600
300 ~ 400
300 ~ 400
400 ~ 600
6~7
3~4
11 ~ 14
13 ~ 18
11 ~ 14
18 ~ 22
11 ~ 14
37 ~ 44
22 ~ 30
22 ~ 30
30 ~ 44
SERVICE STANDARD
Standard value
Antifreeze Mixture ratio of anti-freeze in coolant
ETHYLENE GLYCOL BASE FOR ALUMINUM 50%
ZENITH POWER PRODUCTS - 416

EM -8 ENGINE DOHC
MAINTENANCE
CHECKING ENGINE OIL
1. Position the vehicle on a level surface.
2. Warm up the engine.
NOTE
If a vehicle has been out of service for a prolonged
period of time, warm up the engine for approximately
20 minutes.
3. Turn off the engine, and wait 2 or 3 minutes, then
check the oil level.
4. Check that the engine oil level is within the level range
indicated on the oil dipstick If the oil level is found to
have fallen to the lower limit (the L mark), refill to the
"F" mark.
LF
Lower limit Upper limit
ECDA001A
NOTE
When refilling, use the same type of engine oil.
5. Check that the oil is not dirty or contaminated with
coolant or gasoline, and that it has the proper viscos-
ity.
CHANGING ENGINE OIL
CAUTION
Be careful not to burn yourself, as the engine oil
is hot.
1. Run the engine until it reaches normal operating tem-
perature.
2. Turn off the engine
3. Remove the oil filler cap and the drain plug (on the oil
pan). Drain the engine oil.
KCPC001B
4. Install and tighten the drain plug to the specified
torque.
Tightening torque
Drain plug : 40 ~ 45 Nm (400 ~ 450 kg.cm, 30 ~ 33 lb.ft)
5. Fill the crankcase with fresh engine oil through the oil
filler cap opening.
Drain and Refill Without oil filter :
3.0 liter (3.17 U.S.qts, 2.64 lmp.quts)
Draing and Refill With oil filter :
3.3 liter (3.48 U.S.qts, 2.64 lmp.quts)
6. Install the oil filler cap.
7. Start and run the engine.
8. Turn off the engine and then check the oil level. Add
oil if necessary.
ZENITH POWER PRODUCTS - 416

GENERAL EM -9
FILTER SELECTION
All Hyundai engines are equipped with a high quality, dis-
posable oil filter. This filter is recommended as a replace-
ment filter on all vehicles. The quality of replacement fil-
ters varies considerably. Only high quality filters should
be used to assure the most efficient service. Make sure
that the rubber gasket from the old oil filter is completely
removed from the contact surface on the engine block be-
fore installing the new filter.
Part number
EDDA063A
PROCEDURE FOR REPLACING THE OIL FILTER
CAUTION
Be careful not to burn yourself, as the engine and
engine oil are hot.
1. Use a filter wrench to remove the oil filter.
2. Before installing the new oil filter on the engine, apply
clean engine oil to the surface of the rubber gasket.
Apply engine oil
to the surface
EDDA063B
3. Tighten the oil filter to the specified torque.
KCPC001C
Tightening torque
Oil filter : 12 ~ 16 Nm (120 ~ 160 kg.cm, 9 ~ 12 lb.ft)
4. Run the engine to check for engine oil leaks.
5. After turning off the engine, check the oil level and add
oil as necessary.
ZENITH POWER PRODUCTS - 416

EM -10 ENGINE DOHC
SELECTION OF ENGINE OIL
Recommended API classification : SH OR ABOVE
Recommended SAE viscosity grades :
Recommended SAE viscosity number
Temperature range
anticipated before
next oil change
*1 Restricted by driving condition and environment.
*2 Not recommended for sustained high speed vehicle operation
20
10
-10
-15
-25 -13
5
14
50
68
˚C
40 ˚F
104 15W
-50
-40
10W
-50
-40
20W
-50
-40
10W
-30
5W
-20
5W
-30 *1
*2
*1
5W
-40*1
EDA9990B
NOTE
For best performance and maximum protection of all
types of operation, select only those lubricants which:
1. Satisfy the requirements of the API classification.
2. Have properSAE gradenumberforexpectedam-
bient temperature range.
Lubricant that does not have both an SAE grade number
and an API service classification on the container should
not be used.
ZENITH POWER PRODUCTS - 416

GENERAL EM -11
CHECKING COOLANT LEAK
1. Wait until the engine is cool, then carefully remove the
radiator cap.
2. Confirm that the coolant level is up to the filler neck.
3. Install a radiator cap tester to the radiator filler neck
and apply 140 KPa (1.4 kg/cm², 20psi ) pressure.
Hold it for two minutes in that condition, while check-
ing for leakage from the radiator, hoses or connec-
tions.
NOTE
1. Radiator coolant may be extremely hot. Do not
open the system because hot, or scalding water
could gush out causing personal injury. Allow the
vehicle to cool before servicing this system.
2. Be sure to clean away any moisture from the
places checked completely.
3. When the tester is removed, be carefulnot to spill
any coolant from it.
4. Be careful, when installing and removing the
tester and when testing, not to deform the filler
neck of the radiator.
4. If there is leakage, repair or replace with the apropri-
ate part.
KDPC001F
RADIATOR CAP PRESSURE TEST
1. Remove the radiator cap, wet its seal with engine
coolant, then install it on the tester.
2. Increase the pressure until the gauge stops moving.
Main valve opening pressure :
83 ~ 110 kPa (0.83 ~ 1.1 kg/cm², 12 ~ 16 psi)
Vacuum valve opening pressure :
-7 kPa (-0.07 kg/cm², -1.0 psi)
3. Check that the pressure level is maintained at or
above the limit.
4. Replace the radiator cap if the reading does not re-
main at or above the limit.
NOTE
Be sure that the cap is clean before testing, since rust
or other foreign material on the cap seal will cause an
incorrect reading.
Adapter
ECA9090A
ZENITH POWER PRODUCTS - 416

EM -12 ENGINE DOHC
SPECIFIC GRAVITY TEST
1. Measure the specific gravity of the coolant with a hy-
drometer.
2. Measure the coolant temperature and calculate the
concentration from the relation between the specific
gravity and temperature, using the following table for
reference.
KDPC001E
RELATION BETWEEN COOLANT CONCENTRATION AND SPECIFIC GRAVITY
Coolant temperatur C(F) and specific gravity
10 (50) 20 (68) 30 (86) 40 (104) 50 (122)
Freezing
temperature
C(F)
Safe operating
temperature
C(F)
Coolant
concentration
(Specific
volume)
1.054 1.050 1.046 1.042 1.036 -16 (3.2) -11 (12.2) 30%
1.063 1.058 1.054 1.049 1.044 -20 (-4) -15 (5) 35%
1.071 1.067 1.062 1.057 1.052 -25 (-13) -20 (-4) 40%
1.079 1.074 1.069 1.064 1.058 -30 (-22) -25(-13) 45%
1.087 1.082 1.076 1.070 1.064 -36 (-32.8) -31 (-23.8) 50%
1.095 1.090 1.084 1.077 1.070 -42 (-44) -37 (-35) 55%
1.103 1.098 1.092 1.084 1.076 -50 (-58) -45 (-49) 60%
Example
The safe operating temperature is -15 C(5F) when the
measured specific gravity is 1.058 at coolant temperature
of 20 C(68F)
CAUTION
•If the concentration of the coolant is below
30%, its anti-corrosion properties will be ad-
versely affected.
•If the concentration is above 60%, both the
anti-freeze and engine cooling property will
decrease, affecting the engine adversely. For
these reasons, be sure to maintain the con-
centration level within the specified ragne.
•Do not use together with another brank’s
product.
RECOMMENDED COOLANT
Antifreeze Mixture ratio of anti freeze in coolant
ETHYLENE GLYCOL BASE FOR ALUMINUM 50% [Except tropical areas]
40% [Tropical areas]
ZENITH POWER PRODUCTS - 416

GENERAL EM -13
CHANGING ENGINE COOLANT
CAUTION
When pouring engine coolant, be sure to shut the
relay box lid and not to let coolant spill on electri-
cal parts or the paint. If any coolant spills, rinse it
off immediately.
1. Slide the heater temperature control lever to maxi-
mum heat. Make sure the engine and radiator are
cool to the touch.
2. Remove the radiator cap.
3. Loosen the drain plug, and drain the coolant.
KDDC008B
4. Tighten the radiator drain plug securely.
5. Remove, drain and reinstall the reservior.
Fill the tank halfway to the MAX mark with water, then
up to the MAX mark with antifreeze.
6. Pour coolant into the radiator up to the base of the
filler neck, and install the radiator cap loosely.
7. Start the engine and let it run until it warms up (the
radiator fan comes on at least twice).
8. Turn off the engine.
Check the level in the radiator, add coolant if needed.
9. Put the radiator cap on tightly, then run the engine
again and check for leaks.
CHECKING COMPRESSION PRESSURE
1. Before checking engine compression, check the en-
gine oil level. Also check that the starter motor and
battery are all in normal operating condition.
2. Check the DTC and note it. Use the scan tool to clear
the ECM’S memory.
3. Start the engine and wait until engine coolant temper-
ature reaches 80 ~ 95 C (176 ~ 205 F).
4. Disconnect the fule pump connector.
5. Turn off engine and disconnect the spark plug cables.
KCDC002B
6. Remove the spark plugs.
7. Disonnect the I.G. connector.
8. Crank the engine to remove any foreign material in
the cylinders.
9. Insert the compression gauge into the spark plug
hole.
KDPC001B
10. Depress the accelerator pedal to open the throttle
fully.
ZENITH POWER PRODUCTS - 416

EM -14 ENGINE DOHC
11. Crank the engine and read the gauge.
Standard value : 1500kpa (15Kg/cm², 218 psi)
Limit : 1400kpa (14Kg/cm², 203 psi)
12. Repeat steps 9 to 11 over all cylinders, ensuring that
the pressure differential for each of the cylinders is
within the specified limit.
Limit
Max 100 kpa (1.0 kg/cm², 14 psi) between cylinders
13. If a cylinder’s compression or pressure differential is
outside the specification, add a small amount of oil
through the spark plug hole, and repeat steps 9 to 12.
1) If the addition of oil makes the compression to
rise, it is likely that there may be wear between
the piston ring and cylinder wall.
2) If compression remains the same, valve seizure,
poor valve seating or a compression leak from
the cylinder head gasket are all possible causes.
Tightening torque
Spark plug : 20 ~ 30 Nm (200 ~ 300 kg.cm, 14 ~ 22 lb.ft)
ADJUSTING TIMING BELT TENSION
1. Rotate the steering wheel counter-clockwise
throughly.
NOTE
Do watch not to over load.
2. Lift the vehicle by using of jack.
KCDA125K
3. Remove the engine support bracket. (14mm bolt and
2nuts, 17mm bolt)
KDDC003B
4. Remove the drive belts and the water pump pulley.
(10 mm 4 bolts)
KDDC004B
5. Remove the timing belt upper cover. (10 mm 4 bolts)
KCDC002C
ZENITH POWER PRODUCTS - 416

GENERAL EM -15
6. Remove the crankshaft pulley.
KDDC007B
7. Remove the timing belt lower cover.
8. Place the pistion of No. 1 cylinder to TDC of the com-
pression stroke by rotating the crankshaft clockwise.
NOTE
Crankshaft is to be rotated clockwise otherwise, the
tension is inadequately adjusted.
Tensioner
pulley
Idler pulley
EDDB091A
9. Loosen the tensioner bolt of pivot side and slotside.
EDDA092A
10. Rotate the crankshaft clockwise as many as 2 teeth
of camshaft sprocket.
11. Check that the teeth of the sprocket and belt coincide
with each other.
12. Tighten the slot side bolt first and then tighten the bolt
of pivot side.
13. Check the tension of the timing belt.
When the tensioner and the tension side of the timing
belt are pushed in horizontally with a moderate force
[approx. 49N (11 lb)], the the timing belt log end is ap-
prox. half of the tensioner mounting bolt head radius
(cross flats) away from the bolt head center.
EDKE108A
14. Rotate the crankshaft pulley two turns clockwise so
that the timing belt positions on the pulleys.
15. Install the timing belt lower cover.
16. Install the crankshaft pulley.
17. Install the timing belt upper cover.
18. Install the water pump pulley and engine support
bracket.
ZENITH POWER PRODUCTS - 416

EM -16 ENGINE DOHC
ADJUSTING DRIVE BELT TENSION
1. Check that the belts are not damaged and are prop-
erly fit for the pulley grooves.
2. Apply 100 N (22 lbs.) force to the back and midway
portion of the belt between the pulleys as shown in
the illustration, measure the amount of deflection with
atens
ion gauge.
CAUTION
1. When installing the V-ribbed belt, check that
the V-ribs are properly aligned.
2. If noise or slippage is detected, check the belt
for wear, damage, or breakage on the pul-
ley contact surface, and check the pulley for
scoring. Also check the amount that the belt
is deflected.
Pulley
V-ribbed belt
Wrong Wrong
Right
ECA9980A
STANDARD VALUE:
Adjustment
Itmes Inspection New Used
Deflection mm (in.) 5.1~6.0(0.200~0.236) 4.0~4.4(0.157~0.173) 5.0~5.7(0.200~0.224)
For alternator Tension N (lb) 350~500(79~112 650~750(143~165) 400~500(88~110)
Deflection mm (in.) 8(0.31) 5.0~5.5(0.20~0.22) 6.0~7.0(0.24~0.28)
For air conditioner Tension N (lb) 250~500(56~112) 470~570(106~128) 320~400(72~90)
For power steering Deflection mm (in.) 6.0~9.0(0.24~0.35) - -
ZENITH POWER PRODUCTS - 416

GENERAL EM -17
NOTE
1. The belt tension must be measured half - way
between the specified pulleys.
2. Whena new belt is installed, adjustthetension to
the central value of the standard range indicated
under "New" in the above table. Let the engine
idle for 5 minutes or more, and check the stan-
dard value indicated under "Inspection."
3. When adjusting a belt which has been used,or
newly installed, after 5 minutes or more of oper-
ation, refer to the standard value indicated under
"Used" in the above table.
4. Refer to the standard value indicated under "In-
spection" for periodic inspections.
Power steering oil
pump pulley
Coolant pump pulley
Alternator
Crankshaft pulley
Air conditioning compressor pulley
Tensioner pulley
ECPD001B
TYPEATENSIONGAUGE
Do not let the dial section of the tension gauge contact
other objects during measurement.
Typ A Indicated value
Dial
Spindle
V-ribbed belt
Hook
Spindle Hook
ECA9980C
TYPE B TENSION GAUGE
1. When measuring, turn the reset button in the direction
of the arrow and set the gauge needle to the RESET
position.
2.If the tension gauge is removed from the belt, the nee-
dle will still indicate the tension. Read the tension
value after removing the gauge.
Typ B
Spindle
V-ribbed belt Hook
RESET button
RESET position
ECA9980D
ADJUSTING THE ALTERNATOR BELT
CAUTION
If the belt is too loose, it will cause noise or sud-
den wear.
If the belt is too tight, the engine coolant pump
bearing or the alternator can get damaged.
1. Loosen the alternator nut "A" and the tension adjuster
lock bolt "B".
2. Using the tension adjuster bolt, adjust the belt tension
to the specification.
3. Tighten the adjuster lock bolt "B".
4. Tighten the alternator nut "A".
5. Check the tension or the deflection of belt, readjust if
necessary.
Tightening torque
Alternator support bolt and nut :
20 ~ 25 Nm (200 ~ 250 kg.cm, 14 ~ 18 lb.ft)
Alternator lock bolt B :
12 ~ 15 Nm (120 ~ 150 kg.cm, 9 ~ 11 lb.ft)
Alternator brace mounting bolt :
20 ~ 27 Nm (200 ~ 270 kg.cm, 15 ~ 20 lb.ft)
A
B
1
Alternator brace
Coolant pump
pulley
Crankshaft
pulley
ECKA010H
ZENITH POWER PRODUCTS - 416

EM -18 ENGINE DOHC
SPECIAL TOOLS E0845550
Tool (Number and name) Illustration Use
Crankshaft front oil seal installer
(09231 - 22000)
ECKA010C
Installation of the front oil seal
Crankshaft front oil seal guide
(09231 - 22100)
ECKA010D
Guide of oil seal
Camshaft oil seal installer
(09221 - 21000)
EDDA005B
Installation of the camshaft oil seal
Valve guide installer
(09221 - 3F100 A/B)
ECKA010B
Removal and installation of valve guides
Valve stem oil seal installer
(09222 - 22001)
ECKA010A
Installation of valve stem oil seals
ZENITH POWER PRODUCTS - 416

GENERAL EM -19
Tool (Number and name) Illustration Use
Valve spring compressor
(09222 - 28000)
Valve spring compressor holder
(09222 - 28100)
EDDA005C
Removal and installation of intake
and exhaust valves
Water temperature sensor socket
wrench
(09221 - 25100)
EDKD101B
Removal and installation of the water
temperature sensor
Crankshaft rear oil seal installer
(09231 - 21000)
EDDA005F
Installation of engine real oil seal
and crankshaft rear oil seal
ZENITH POWER PRODUCTS - 416
Table of contents
Other Zenith Engine manuals
Popular Engine manuals by other brands

bpr
bpr Rotax 912 i Series Maintenance manual
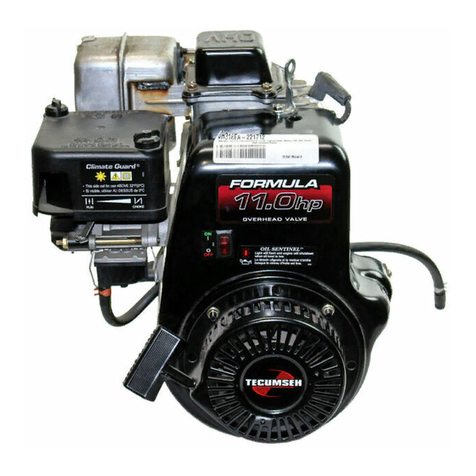
Tecumseh
Tecumseh OH318 Operator's manual
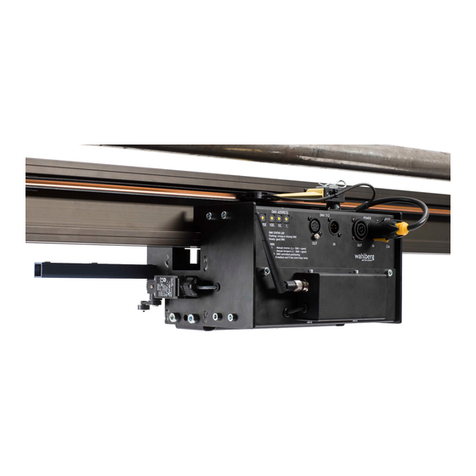
Wahlberg
Wahlberg Track Runner Series user manual

Briggs & Stratton
Briggs & Stratton 210000 Series Operator's manual
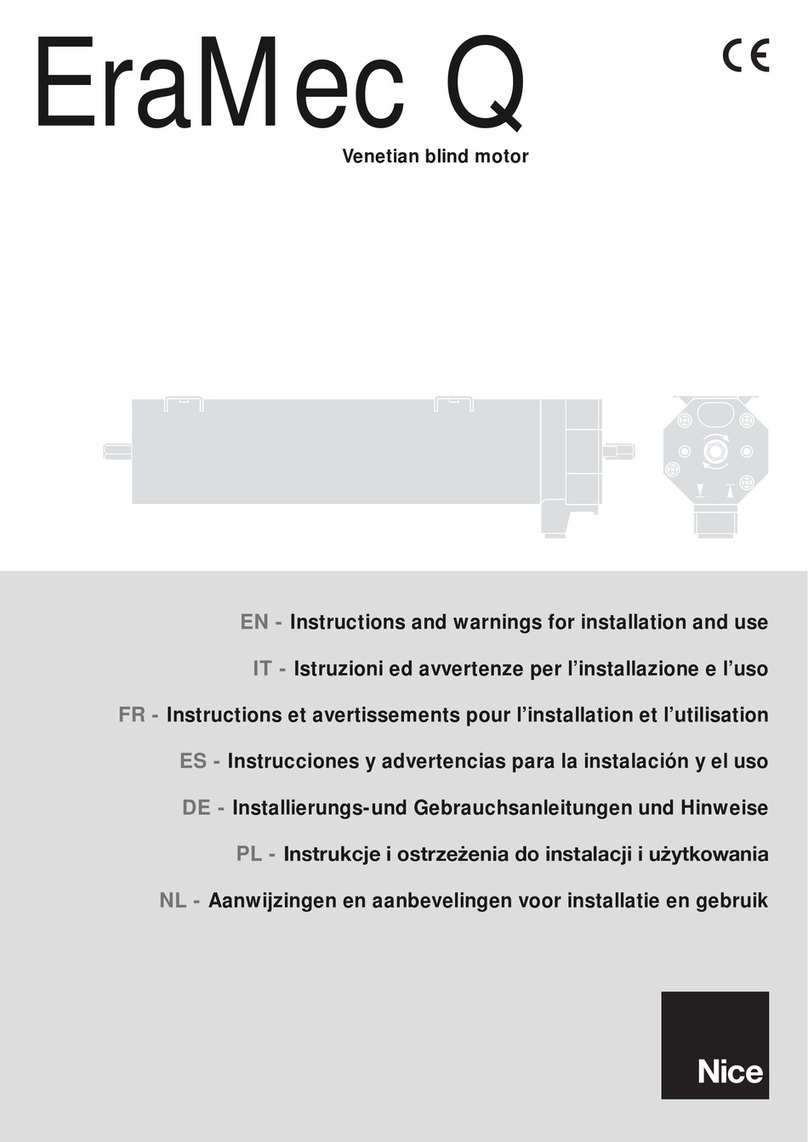
Nice
Nice EraMec Q Instructions and warnings for installation and use

Scania
Scania DC13 070A Operator's manual