2Flow MAG-11 Series User manual

Electromagnetic Heat Meter
MAG-11 Series
Instruction Manual
Please read this manual carefully and use the product correctly on the basis of full understanding.

CONTENTS
1. Preface ................................................................................................................................. 1
1.2 Disclaimers .................................................................................................................... 2
2. Acceptance, storage and transportation ......................................................................... 2
2.1 Unpacking inspection .................................................................................................. 2
2.2 Storage .......................................................................................................................... 2
2.3 Carry .............................................................................................................................. 2
3. Product overview ................................................................................................................ 3
3.1summary ......................................................................................................................... 3
3.2 Product features ........................................................................................................... 3
3.3 Working principle of heat metering ............................................................................ 4
4. Technical parameter .......................................................................................................... 5
4.1 Basic parameters ......................................................................................................... 5
4.2 Converter ....................................................................................................................... 5
4.3 Sensor ........................................................................................................................... 6
4.4 Temperature sensor .................................................................................................... 8
5. Installation ........................................................................................................................... 8
5.1 Installation position ...................................................................................................... 8
5.2 Pipe section meeting the working conditions of flow sensor ................................. 9
5.4 Installation instructions .............................................................................................. 12
6. Grounding .......................................................................................................................... 14
6.1 Metal pipe .................................................................................................................... 14
6.2 Non metallic pipe ........................................................................................................ 15
7. Connection ........................................................................................................................ 15
7.1 Cable selection ........................................................................................................... 15
7.2 Cable laying ................................................................................................................ 17
7.3 Connection .................................................................................................................. 18
8. Panel operation and display ........................................................................................... 24
8.1 Panel and key description ......................................................................................... 24
8.2 Real time data display interface ............................................................................... 25
8.3 Menu list ...................................................................................................................... 27

8.4 Operation examples ................................................................................................... 27
8.4.1 Example of password setting ................................................................................ 28
8.4.2 Enumeration type parameter setting example .................................................... 29
8.4.3 Example of parameter setting with fixed or no decimal point ........................... 31
8.4.4 Example of parameter setting with non fixed decimal point ............................. 32
8.4.5 Example of mixed alpha numeric parameter setting ......................................... 35
9. Major function ................................................................................................................... 36
9.1 Zero check and zero adjustment ............................................................................. 36
9.2 Clearing accumulation and report clearing ............................................................. 38
9.3 Report query ............................................................................................................... 39
10. Parameter list .................................................................................................................. 48

1
1. Preface
In order to ensure the normal use of the instrument, please read this manual carefully and
fully understand how to use the instrument before operation.
About this user manual
● The instructions must be provided to the end user.
● Please read this manual carefully before use.
● The contents of this manual can be changed without prior notice.
● All rights reserved. Without the written consent of 2 flow AB, no part of the manual can
be copied in any form.
● 2Flow AB makes no guarantee in any form for this manual, including but not limited to
the sale of this manual and its use for other special purposes.
● The company makes every effort to ensure the correctness of the contents of the
instructions. If there are any errors or omissions, please inform 2Flow AB.
● Besides the contents mentioned in the statement, 2Flow AB will not bear any other
responsibilities for this product.
● If the change of product specification, structure or operating parts does not affect the
operation and performance, the user manual will not be revised accordingly.
1.1 Safety tips
●The installation and wiring of flow sensor and temperature sensor must be completed by
professional technicians;
● all wiring terminals and connecting wires of the instrument must be plugged in and out
after power failure;
● when measuring high-temperature fluid, the sensor housing will become very hot to
prevent personnel from scalding.
The provisions of this manual must be observed at all stages of product operation and
maintenance, especially the contents with the following marks.
A warning indicates a danger that may result in injury or death.
Attention indicates that there is a danger, which may cause partial or overall
damage to the instrument.
It is forbidden to indicate that the instrument will not work normally or be damaged.
It is important to draw the attention of operators to avoid instrument damage.
Notes indicate information that must be known about the operation and
characteristics of the instrument.

2
1.2 Disclaimers
The following situations do not belong to product liability:
(1) Damage caused by customers' negligence or lack of maintenance of products.
(2) Problems or damage caused by violation of relevant regulations during operation,
operation and storage.
(3) Problems or damage caused by natural disasters and other external factors.
(4) Problems or damage caused by repair or modification by personnel not authorized by
the company.
(5) If the customer or a third party is injured when using the product, and these injuries are
caused by unpredictable defects of the product, the company will not bear any
Responsibility, nor will it be responsible for indirect injuries.
2. Acceptance, storage and transportation
2.1 Unpacking inspection
When unpacking the product, please check the following contents in time:
(1) Appearance
This instrument has been carefully checked before leaving the factory. If damage is
caused during transportation (please pay special attention to the lining and shell), please
contact our company.
(2) Nameplate
Check whether the product conforms to the ordering requirements according to the
nameplate contents, see the instructions in 4.5. Fel! Hittar inte referenskälla.
(3) Attachment
Check whether the accessories in the packing box are complete according to the
packing list.
2.2 Storage
If the instrument needs to be stored for a long time after delivery, please pay attention
to the following points:
● the instrument must be stored in the original packaging box.
● the storage place must be dry, vibration free and the ambient temperature suitable.
2.3 Carry
Handle all parts carefully to prevent damage. Please use the original packing box to
transport the instrument to the installation place.
important
● the damaged lining will cause the flow sensor to be scrapped.
● if the cable is not selected reasonably (see the instructions in 7.1) and the cable sealing
plug or instrument cover is not tightened, the product may be scrapped due to water ingress
or moisture on the instrument shell. 0

3
3. Product overview
3.1summary
MAG-11 electromagnetic heat meter (hereinafter referred to as "heat meter") is a
product integrating the measurement of air conditioning water flow, heat and temperature
difference, which is suitable for cold / hot water air conditioning billing system.
The converter, electromagnetic flow sensor and supply / return water temperature
sensor form a heat meter. The converter can be installed independently or assembled
on the electromagnetic flow sensor.
Figure 3
-
1 system diagram31
Users can operate by pressing keys and remote control by Bluetooth(Set the heat
meter to different working modes for heat metering by using the mobile phone with
Bluetooth chip and corresponding APP) or the upper computer (modbus\ bacnet
protocol).
Figure 3
-
2 system function block diagram32
3.2 Product features
Unimpeded detection: the pipeline is unobstructed, will not block the flow, will not
cause pressure loss, save the power consumption of the water pump, and does not need
a filter.
High precision measurement: high precision A/D conversion circuit is adopted, and the
flow measurement error can be within ± 0.5% of the actual flow.

4
Screen display: dot matrix LCD is used, and the panel information is complete. Under
different panels, positive and negative flow, cold and heat, alarm information,
temperature sensor status and other contents can be displayed, and a variety of
parameter settings can be carried out. The screen supports 90゜, 180゜, 270゜.
Safety protection: the standard protection grades of sensors and calculators are IP65,
IP67 and IP68.
Applicable to a variety of fluids: different linings can be used to measure the flow and
temperature of a variety of fluids with different temperatures, physical and chemical
properties, such as central air-conditioning water, primary and secondary network hot
water in heat exchange stations, industrial refrigerant, etc.
Power off holding parameters: EEPROM is used to store configuration parameters
and cumulative data, which can be memorized in case of power failure.
Remote communication: support MODBUS or BACNET communication protocol
based on RS485 or MOSBUS communication protocol based on Bluetooth
communication.
Automatic switching of cold and heat: it has heat mode, cooling capacity mode and
automatic switching mode of cold and heat, and the display and accumulation of cooling
capacity and heat can be switched automatically.
Good lightning protection function and anti-static interference: the surge protection of
power line meets class A at 2KV; Electrostatic interference meets class a requirements
when contacting 6kV and gap 8Kv.
Complete reporting functions: support 1200 hours of time reports, 365 days of daily
reports, 36 months of monthly reports, 15 years of annual reports, 100 power on and
power off records and 100 error report records.
3.3 Working principle of heat metering
This heat meter includes the functions of temperature, temperature difference and
power measurement. Generally, the measuring medium is water. When the medium is
water, the pipe pressure needs to be set, and when using other media, the medium
density and enthalpy need to be set.
The setting parameter positions are as follows:
Media: detail - > power set - > medium
Pressure option: power->pressure opt
Media density: detail - > power set - > density (g/cm³)
Enthalpy: detail - > power set->heat C
The specific calculation method is as follows:
When the medium is water:
Power calculation p=q×ρTS×(HTs-HTr)
Q is the measured flow;
ρTS is the medium density at the water supply end, which is obtained by looking
up the table according to the water supply temperature ts and pressure options;
HTS is the enthalpy value of the medium at the water supply end, which is
obtained by looking up the table according to the water supply temperature ts;
HTR is the enthalpy of the medium at the return water end, which is obtained by
looking up the table according to the return water temperature tr.

5
When the media is other:
Power calculation p=q×ρ×∆T×H
Q is the measured flow;
Ρ is the set medium density;
H is the set enthalpy of medium;
∆T=|Ts-Tr|.
The power measurement mode is divided into heating mode (heat), cooling mode
(cold) and automatic judgment mode (auto), which are calculated according to the rules
in the following table:
Tabl e 3
-
1 Calculation rules of heat and cooling capacity31
Power
option
settings
Flow
Temp .
Power
measure
mode
Abnormal conditions
Heating
Forward
Ts>Tr
Heating
Reverse
Not calculate heat
Cooling
Forward
Ts<Tr
Reverse
Not calculate heat
Auto.
Forward
Ts>Tr
Heating
Not calculate heat when
Ts<3 0 ℃
Ts<Tr
Cooling
Not calculate cooling when
Ts>1 8 ℃
reverse
Ts>Tr
Cooling
Not calculate cooling when
Tr>18℃
Ts<Tr
Heating
Not calculate heat when
Tr<30℃
4. Technical parameter
4.1 Basic parameters
(1) Measuring medium: central air conditioning water, primary and secondary network
hot water of heat exchange station, industrial refrigerant, etc.
(2) Measurable flow rate range: 0 ~ 12m / S
(3) The accuracy of flow measurement is level 0.5
4.2 Converter
4.2.1 Input / output signal parameters
4.2.1.1 Current output interface
Through parameter setting, it can be set to
4 ~ 20 mA corresponding instantaneous flow output (load resistance ≤ 500 Ω)
4 ~ 20 mA corresponding power output (load resistance ≤ 500 Ω)
4.2.1.2 Pulse output interface
The pulse output is a passive pulse.
Transistor contact capacity: 30VDC, 200mA
Output frequency: 0.0001~5000Hz.
Scaled pulses can be output through the setting of pulse equivalent.
Pulse width: 50% duty cycle or fixed value (≤ 200ms).
4.2.1.3 RS485 output

6
Through parameter setting, it can be set to
For Modbus protocol, see 9.5rs485 communication function (MODBUS-RTU) for detailsFel!
Hittar inte referenskälla.Fel! Hittar inte referenskälla.
For BACnet protocol, see 9.6rs485 communication function (BACnet ms/tp) for detailsFel!
Hittar inte referenskälla.Fel! Hittar inte referenskälla.
4.2.1.4 Bluetooth communication
Support Bluetooth 4.0 communication of Android 6.0 and above systems,and use
MODBUS-RTU protocol.
4.2.1.5 Temperature interface
Pt-1000 input.
Default two-wire system, optional four wire system.
Measuring range: When the medium is water, the range is (0 ~ 130)
℃
When the medium is other, the range is (-30 ~ 175)
℃
Temperature diff e r e n c e r a n ge: (3 ~ 70) K.
4.2.2 Display
(1) 128 x 64 full dot matrix LCD display
(2) Language English
(3) Display units: "instantaneous flow", "cumulative flow", "power", "cumulative heat"
4.2.3 Power supply DC 18 ~ 36V
AC 100 ~ 240V, 48 ~ 62Hz
4.2.4 Ambient temperature -10
℃
~ +60
℃
(when AC power supply)
-10
℃
~ +50
℃
(DC power supply)
4.2.5 Protection grade IP65
4.2.6 Cable access hole m20x15 internal thread
4.2.7 Terminal plug-in connector (wiring diameter 0.3 ~ 1.5mm2)
4.2.8 The shell is made of cast aluminum alloy, and the surface is coated with pure
polyester plastic powder.
4.3 Sensor
Threaded sensor
4.3.1.1 Normal diameter
DN10~40
4.3.1.2 Appearance dimension

7
Figure 4
-
3 Schematic diagram of external dimensions of threaded calorimeter41
Tabl e 4
-
5 dimension table of threaded sensor41
Normal
diameter
Measuring tube
length L
Total length
L1
G
R
H1
H
DN10
100
194
G 3/4
R 1/2
147
284
DN15
100
194
147
284
DN20
100
208
G 1
R 3/4
147
284
DN25
100
226
G 1 1/4
R 1
147
284
DN32
100
227
G 1 1/2
R 1 1/4
152
289
DN40
100
227
G 2
R 1 1/2
162
299
4.3.1.3 Electrode material
Stainless steel 316L.
4.3.1.4 Lining material
PU, FEP.
4.3.1.5 Medium temperature
It is related to the temperature resistance of lining materials. See Appendix
B lining material performance table. Fel! Hittar inte referenskälla.
4.3.1.6 Withstand voltage level
1.6MPa.
4.3.2 Degree of protection
IP65,IP67,IP68
4.3.3 Junction box
Cable access hole M20 x 1.5 female
The shell is made of cast aluminum alloy, and the surface is coated with pure
polyester plastic powder.

8
4.4 Temperature sensor
El= insertion depth, AI= cable length, M= mounting accessories, D= sheath outer
diameter
Product standard DIN EN 60751 (according to IEC 751)
Sensor PT1000
Measurement accuracy Two-wire system ± 0.15
℃
Four wire system ± 0.1
℃
Measuring range: 0 ~ 105
℃
Humidity condition <95% relative humidity (non condensing)
Withstand voltage grade PN25
Protection grade IP67
Sheath material 316L stainless steel
Outer diameter of sheath: 5 ~ 12 mm
The insertion depth is 50mm for DN15 ~ DN50
The connection mode is two-wire or four wire system for optional
Cable length 3m, 5m, 10m for optional (customized)
5. Installation
important
1. Sufficient operating space shall be reserved at the installation position of the instrument
to facilitate overhaul and maintenance;
2. Avoid places that are prone to lightning strikes or may be flooded and sprayed by
rainwater:
3. Avoid being installed in an environment that is overheated, exposed to direct sunlight
and prone to corrosion; For the flow sensor, if the pipeline temperature is high,
measures should be taken to ensure that the working environment temperature of the
converter meets the requirements of 4.2.4. 0
4. Choose a place where the pipeline has no vibration or less vibration.
5.1 Installation position
The flow sensor shall be installed at the water supply end.

9
5.2 Pipe section meeting the working conditions of flow sensor
5.2.1 The upstream and downstream straight pipe sections shall be of sufficient length
5.2.1.1 The minimum allowable length of the upstream straight pipe section of the sensor
is 5dn and the downstream is 2DN (DN is the pipe diameter)
Single elbow full open gate valve or ball valve
5.2.1.2 When there are spoiler components (half open valve, regulating valve, stop valve,
etc.) upstream, the length of the straight pipe should be extended
5.2.1.3 When the reducer with a taper of less than 15 ° is installed on the upstream and
downstream sides of the measurement, it can be regarded as a straight pipe
5.2.2 The sensor shall be installed in the pipe section filled with medium
When the pipe is not full, the flow sensor will have serious measurement error or

10
cannot display the measured value normally.
Raise the outlet end of the downstream pipe section to ensure full pipe.
The flow direction is from bottom to top, which can ensure the full pipe.
5.2.3 It should be ensured that the installation position of the measuring pipe will not
produce or accumulate bubbles
If bubbles enter the sensor measuring tube, the flow display will be affected and
measurement errors will occur.
Bubbles are easily generated downstream of the regulating valve.
The pipe with the outlet facing downward is easy to accumulate bubbles at the
highest point.
In the downward pipeline longer than 5 meters, cavitation occurs due to the
pressure drop of the system, so it is necessary to install a siphon or relief valve
downstream of the sensor.
Det gick inte
att hitta
bilddelen med
relations-ID
rId24 i filen.

11
5.2.4 In the pipe section where the measuring pipe is located, the fluid conductivity
should remain stable
important
In the case of upstream chemical injection, the fluid conductivity may fluctuate violently,
thus affecting the normal operation of the flow sensor. To avoid this situation, it is
recommended to change the injection port of chemical substances to the downstream side
of the flow sensor. If it is necessary to inject from the upstream side, a sufficient distance
(more than 50D) should be ensured to ensure that the fluid and the injected material are
fully mixed.
5.2.5 The pipe section near the upstream side of the sensor is not allowed to have
projections
5.2.6 The flow sensor is not allowed to be installed in the negative pressure pipeline such
as the suction side of the pump
5.3 Installation of temperature sensor
To e n s u r e t h a t the insertion d e p t h o f the temperature sensor i s g r e a t e r than half o f the
pipe diameter, refer to below pictures for details. 0

12
5.4 Installation instructions
5.4.1 welding
The pipe flange for installing the flow sensor should be welded before the instrument is in
place. Electric welding is prohibited after the instrument is in place; After the instrument is
installed, when welding is required at other positions of the pipeline, the power supply of
the instrument must be disconnected first.
5.4.2 Pipe cleaning
The newly installed pipeline usually has foreign matters such as welding slag, which should
be washed away before the sensor is in place. To prevent damage to the lining.
Attention
Pipes that are not centered or inclined will cause leakage or damage to the lining.
5.4.3 flow direction
The arrow direction of the instrument flow direction sign should be consistent with
the medium flow direction.
notes
For instrument operation or data observation, the direction of the converter can be changed:
Remove the four fastening screws at the bottom of the converter housing. The converter
can be rotated ± 90 ° or 180 °, and then reinstall the screws. Pay attention to the correct
position of the sealing gasket at the bottom of the shell during the tightening of the screws.
5.4.4 Horizontal installation
After the sensor is installed in the pipeline, the connecting line XX between the two
electrodes should be kept as horizontal as possible.

13
important
The electrode shown in the above figure on the right is located at the top of the
measuring tube, and the bubbles released from the medium will cause the electrode
to be insulated from the medium for a short time, thus making the measurement result
wrong.
5.5 Converter (split) installation
The installation position of the converter should be as far away from the high-power
motor or frequency converter as possible;

14
important
Sufficient operating space shall be reserved at the installation position of the converter
to facilitate wiring and connecting conduit.
When wall hanging is installed, enough length of cable shall be reserved.
6. Grounding
The instrument housing and the medium must be grounded together.
Figure 6
-
1 Schematic diagram of instrument grounding61
6.1 Metal pipe
Connect the grounding of the instrument shell with the pipe flange by wire.
Figure 6
-
2 Schematic diagram of metal pipeline instrument grounding62

15
6.2 Non metallic pipe
Grounding ring or grounding electrode must be used.
Grounding connection of flow meter with grounding ring on nonmetallic pipe.
Figure 6
-
5 Schematic diagram of non-metallic pipeline instrument grounding63
notes
The grounding mode of the three electrode sensor is shown in Figure 6
-
1.
7. Connection
The wiring of electromagnetic calorimeter includes the following three aspects:
1. Select the appropriate cable;
2. Cable laying;
3. Wiring.
7.1 Cable selection
important
It is forbidden to use hard copper wire for the power supply and output signal of the
heat meter.
7.1.1Power cable
In order to ensure the sealing of the instrument access hole, a circular three core multi
strand sheathed cable with an outer diameter of 6 ~ 10mm shall be selected, and the cross-
sectional area of each core shall be 1.0 ~ 1.5mm2.
Cables with a rated temperature of 80
℃
should be used in ambient temperatures above
60
℃
. If the ambient temperature exceeds 80
℃
, cables with a rated temperature of 110
℃
should be used.
important
When using 24V DC power supply, the voltage delivered to the converter end will drop
due to the cable resistance. The relationship between the power supply voltage and the
allowable cable length is shown in the table below.

16
7.1.2 Input / output signal cable
In order to ensure the sealing performance of the instrument access hole, the
single hole sealed cable should be a round multi strand sheathed cable with an outer
diameter of 6 ~ 10mm, and the double hole sealed cable should be a round multi
strand sheathed cable with an outer diameter of 3 ~ 5mm, with a copper core cross-
sectional area of 0.5 ~ 1.5mm2.
If ambient noise and crosstalk will adversely affect the signal, please use RVVP
shielded cable.
7.1.3 Temperature sensor signal cable
The signal cable of temperature sensor shall be a round multi strand sheathed
cable with an outer diameter of 3 ~ 5mm, and the cross-sectional area of copper core
is 0.2 ~ 0.3mm2.
7.1.4 Special signal cable for split flow sensor
five×0.5mm2rvvp special shielded cable, with an outer diameter of 8-10mm.
important

17
If the signal cable provided with the product is found to be too short, please contact
our company for replacement. It is forbidden to lengthen it at will.
If the signal cable is too long in practical application, please do not wind it up; If you
need to cut it short, please handle the thread end as shown in the above figure.
7.2 Cable laying
7.2.1 Cable access hole sealing
Put the parts of the sealing plug into the cable as shown in the figure below, and then screw
them into the cable access hole of the instrument in turn.
When connecting the conduit with the sealing plug, pay attention not to damage the sealing
performance of the cable, and do not over compress the cable.
Figure 7
-
1 Schematic diagram of double hole sealed cable threading (applicable wire
diameter 3-5mm)71
Figure 7
-
2 Schematic diagram of single hole sealed cable threading (applicable wire diameter
6-10mm)72
7.2.2 Use conduit correctly
In order to protect cables and prevent electrical noise interference, it is
recommended to use conduit to lay cables and construct according to the following
requirements:
(1) Power cables and output signal cables are not allowed to share conduit, nor are
they allowed to share conduit with excitation cables and signal cables, and power
cables cannot be laid in the same cable tray with the above other cables or at
least kept isolated.
(2) Excitation cables and signal cables are allowed to share conduit, but excitation
cables and signal cables of different heat meters are not allowed to share conduit
or bundle together.
(3) The instrument shall be connected with the conduit with a waterproof sealing plug
with conduit connector, and the position of conduit A (see the figure below) shall
be lower than the instrument cable access port. Install a drain valve at the end
of the standpipe to regularly drain the accumulated water in the conduit.
Other 2Flow Measuring Instrument manuals
Popular Measuring Instrument manuals by other brands
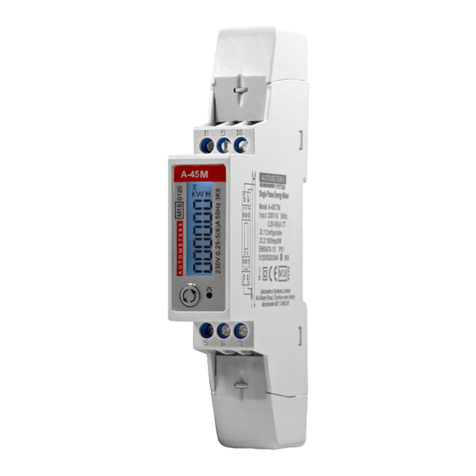
Autometers Systems
Autometers Systems A-45 Series quick start guide
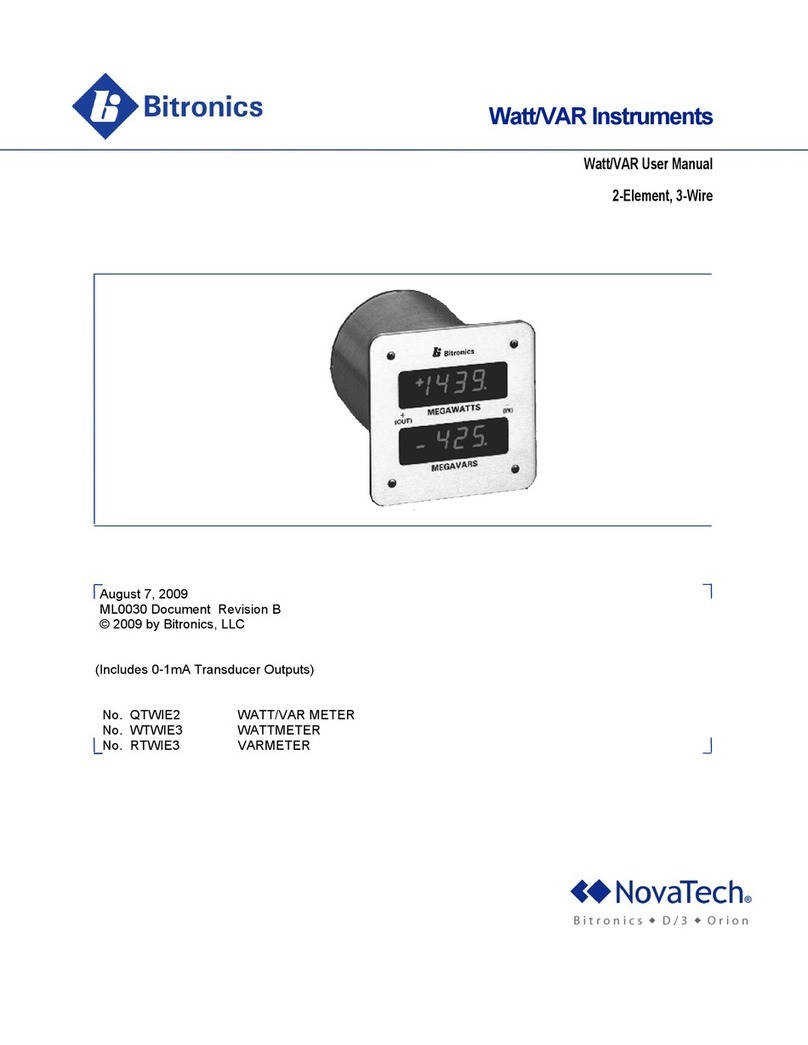
Bitronics
Bitronics QTWIE2 user manual
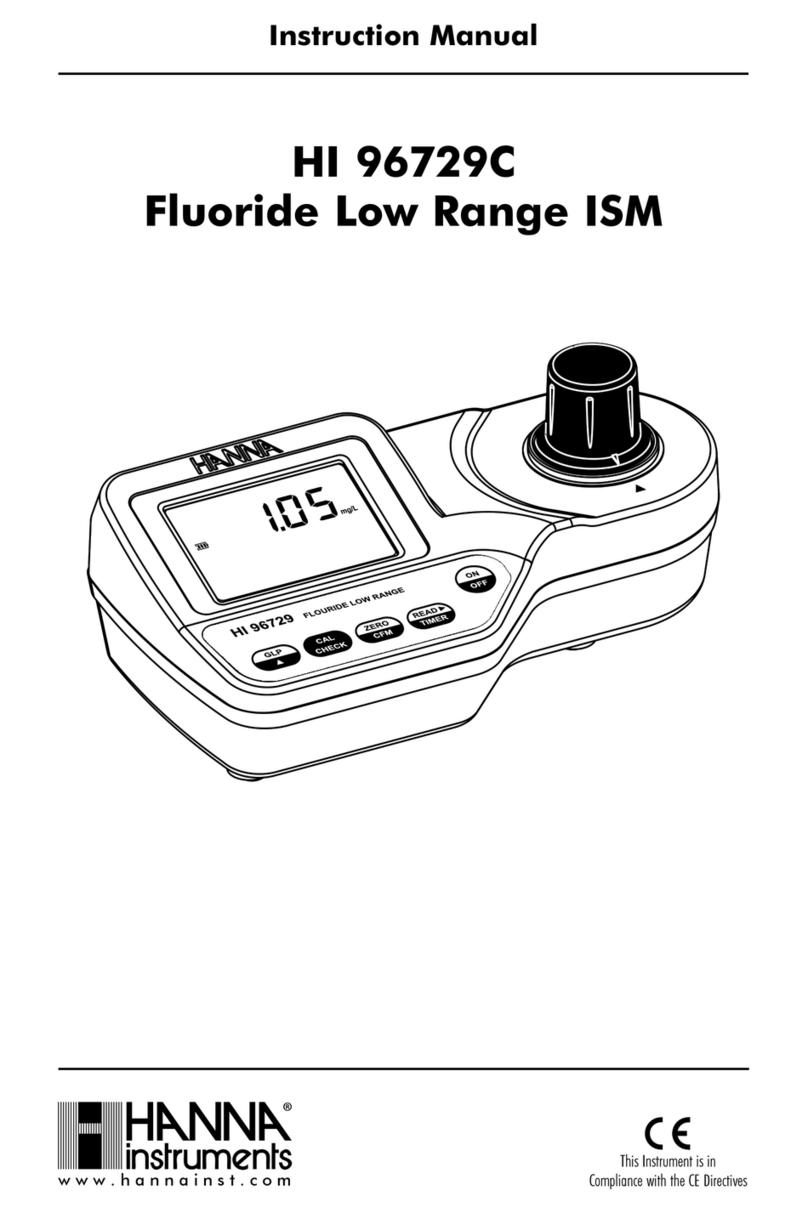
Hanna Instruments
Hanna Instruments HI 96729C instruction manual
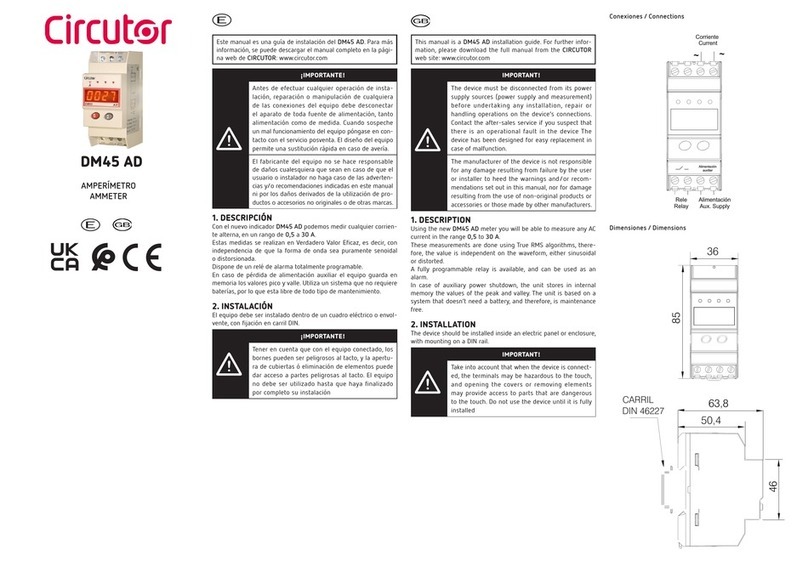
Circutor
Circutor DM45 AD manual
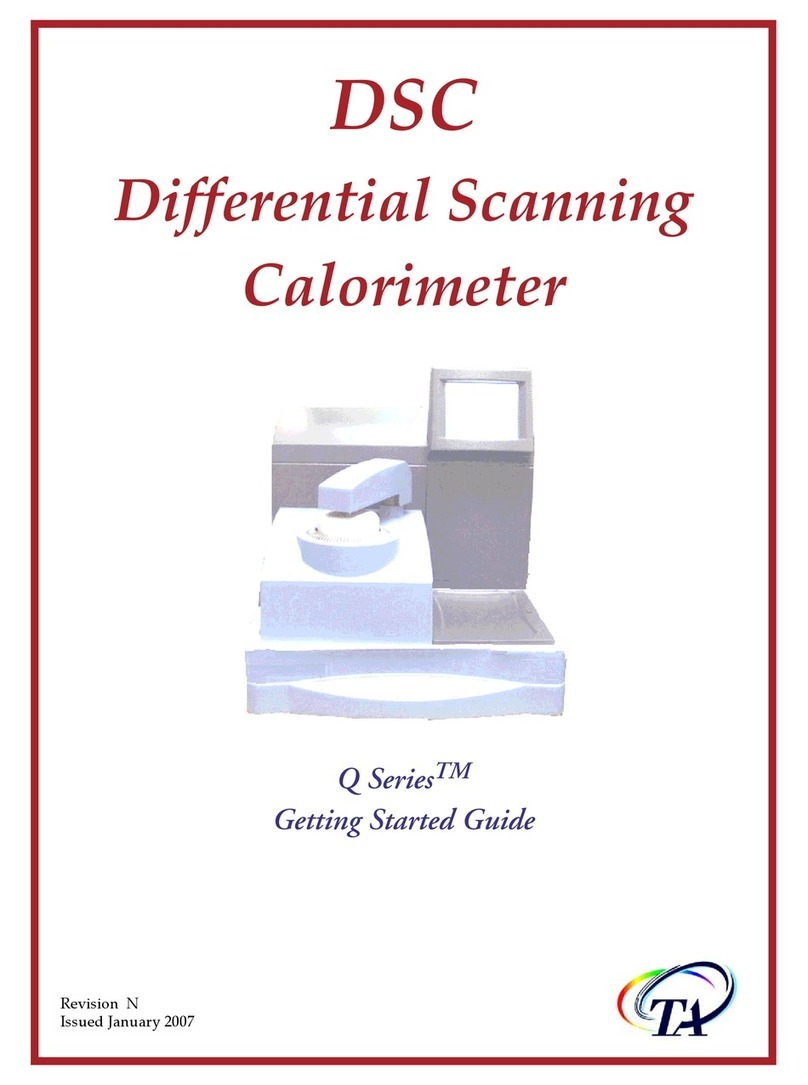
TA Instruments
TA Instruments DSC Q Series Getting started guide
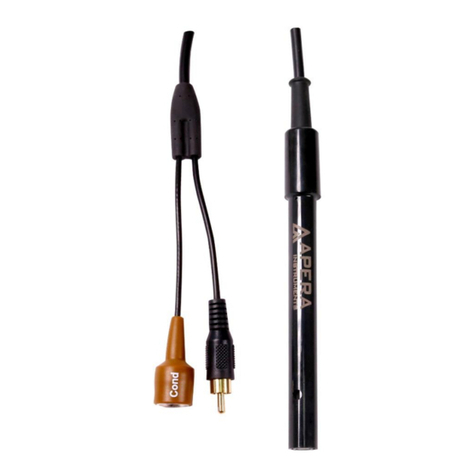
Apera Instruments
Apera Instruments 2310T-F user manual
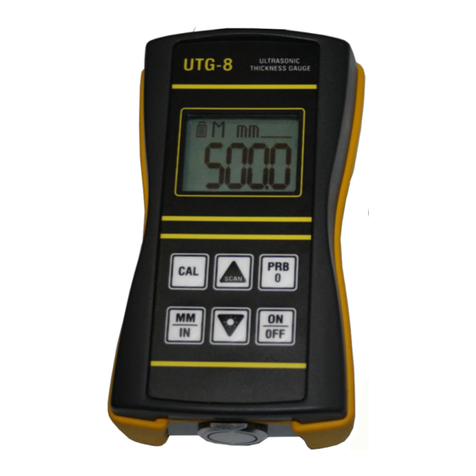
OKOndt GROUP
OKOndt GROUP UTG-8 quick start guide
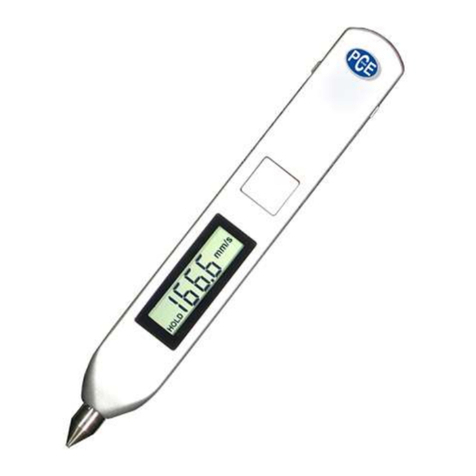
PCE Instruments
PCE Instruments PCE-VT 1000 manual
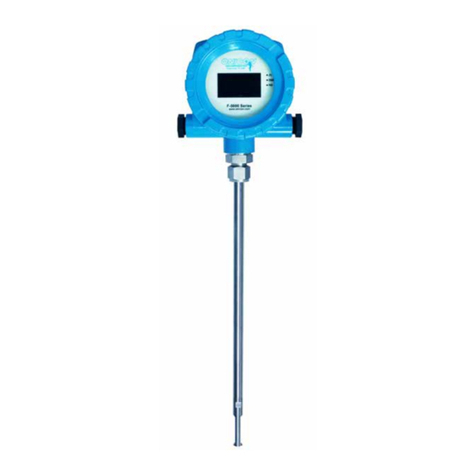
Onicon
Onicon F-5100 Inline Installation and operation guide
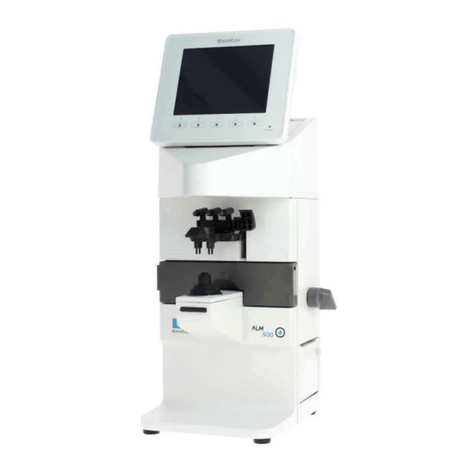
Essilor Instruments
Essilor Instruments ALM 500 user guide
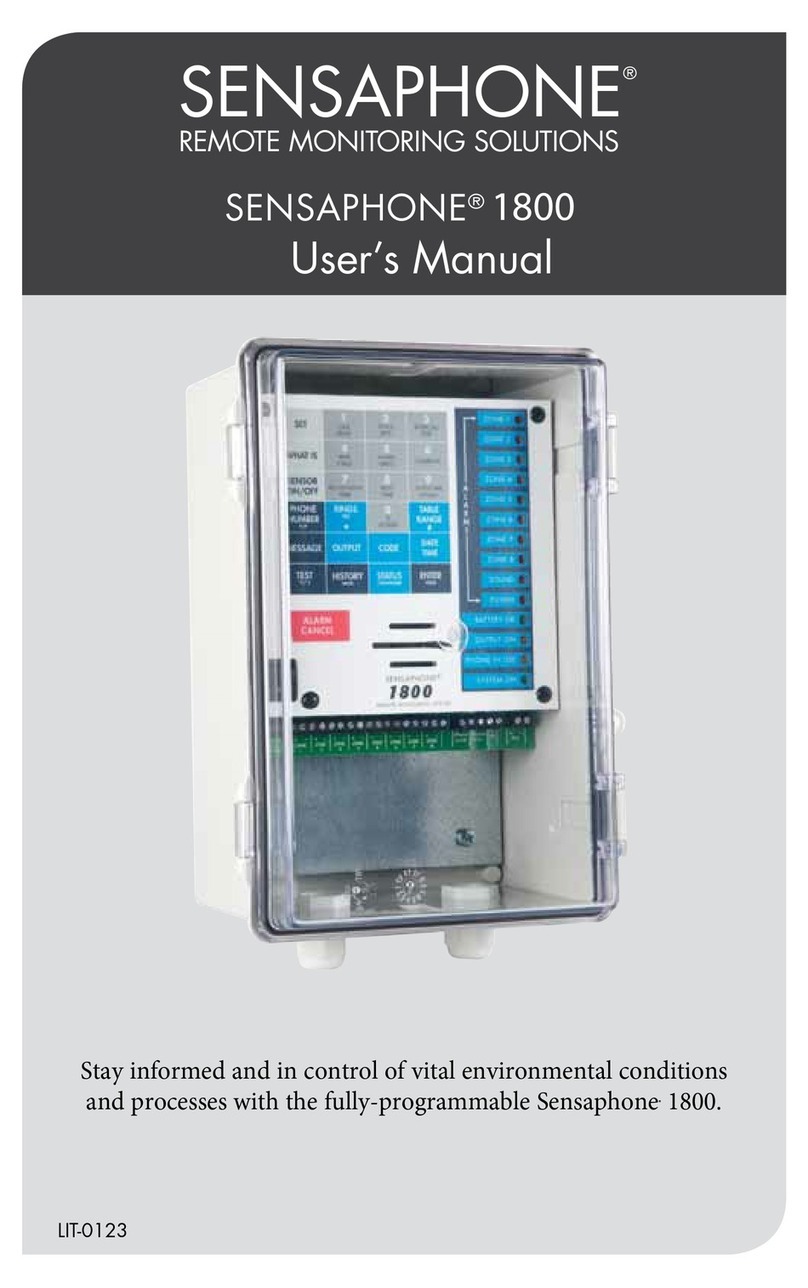
Sensaphone
Sensaphone 1800 user manual
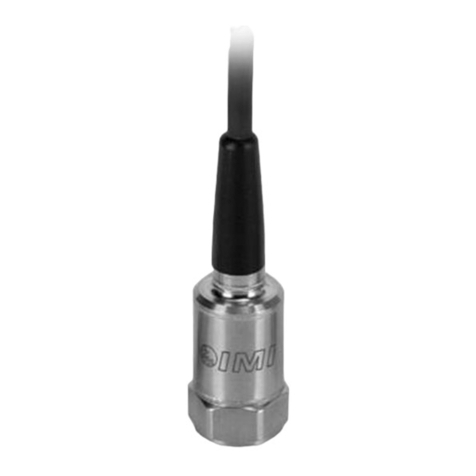
PCB Piezotronics
PCB Piezotronics IMI SENSORS M601A11 Installation and operating manual