Access Combustion B Setup guide

Model B Burner
INSTALLATION,OPERATION,AND SERVICE MANUAL
ACCESS
COMBUSTION, LLC
Copyright 2018 © by Access Combustion LLC.
All rights reserved. This document is a proprietary property of Access Combustion, LLC.
The manual is not to be disclosed to others without consent of Access Combustion.
Unauthorized use is expressly forbidden.
For Information, Service, or Repair Please Contact:
Access Combustion, LLC.
www.Access-combustion.com
Phone: 918-576-7100
E-Mail: [email protected]om
WARNING: Only Factory Authorized Burner Service Personnel Should Start, Adjust, or Service This
Equipment

ACCESS COMBUSTION, LLC
WARNING:
Only authorized burner service personnel should start, adjust, or service this equipment!
Rev. 05
Page 2 of 19
TABLE OF CONTENTS
Installation, Operation, and Service Manual .............................................................................................................1
Section I: General Safety and Warnings ........................................................................................................................3
Installation Checklist.....................................................................................................................................................4
Section III: Burner Installation .......................................................................................................................................6
Typical Gas Train........................................................................................................................................................7
Gas Train Pressure Test .............................................................................................................................................8
Electrical Connection .................................................................................................................................................8
Burner Sequence of Operation..................................................................................................................................9
Section IV: Burner Commissioning ..............................................................................................................................10
Pilot Spark Pickup Test.............................................................................................................................................10
Pilot Commissioning ................................................................................................................................................11
Main Flame Commissioning.....................................................................................................................................12
Adjustment of Air Flow Switch ................................................................................................................................13
Adjustment of Filter Switches..................................................................................................................................13
Adjustment of Gas Pressure Regulators ..................................................................................................................13
Adjustment of Gas Pressure Switch.........................................................................................................................14
Section V: Maintenance...............................................................................................................................................15
General Maintenance ..............................................................................................................................................15
Pilot Troubleshooting ..............................................................................................................................................16
Pilot Assembly .........................................................................................................................................................17
Pilot Adjustment, Cleaning. .....................................................................................................................................17
Warranty Policy ...........................................................................................................................................................18

ACCESS COMBUSTION, LLC
WARNING:
Only authorized burner service personnel should start, adjust, or service this equipment!
Rev. 05
Page 3 of 19
SECTION I: GENERAL SAFETY AND WARNINGS
•Do not attempt to operate the burner without first familiarizing yourself with burner operating
instructions!
•This burner must only be serviced by fully trained and qualified personnel.
•Do not operate this equipment until the equipment has passed all safety inspections required by
your area.
•Before performing any service work on the burner, turn OFF ALL manual fuel shut offs valves,
including pilot gas shutoff valve, and turn OFF ALL electrical power to the appliance and any
other equipment that is electrically interlocked with the appliance.
•Do not bypass flame management sequencing and safety interlocks!
•This burner utilizes fuel that is flammable and potentially explosive. If smell of fuel is present
evacuate the area and call gas supplier and/or fire department.
•Do not enter a furnace, boiler or fired vessel.
•Use and storage of gasoline or other flammable liquids and vapors in open containers in the
vicinity of this burner is hazardous and could result in a fire or explosion.
•DO NOT use Teflon tape or components with Teflon as an oil or gas pipe sealant as Teflon can
cause valves to fail, creating a SAFETY HAZARD. All manufacturer warranties are voided and all
liability rests with the INSTALLER when evidence of Teflon is found. ONLY use a pipe sealant
approved by the Underwriters Laboratories for assembly of oil and gas piping.
•Castable refractory dust contains cristabolite and / or crystalline silica and the ceramic fiber
refractory contains fibers, all of which may be carcinogenic. Use proper and approved respiratory
protective equipment, as well as any other necessary personal protective equipment required to
avoid exposure.
•If this appliance is not installed, vented, operated and maintained properly per manufacture
instructions, it could expose you to hazardous substances in the fuel or hazardous fumes from
fuel combustion which can cause death or serious illness and are known by the State of
California to cause cancer, birth defects and reproductive harm.
•This manual has been prepared to assist in installation, operation and maintenance of your
burner. Only appropriately trained and qualified personnel should be permitted to operate this
equipment. The instructions contained herein should be read carefully before operating the
equipment.
•Improper operation of the equipment will result in injury to persons or loss of life and damage to
equipment. Access Combustion shall assume no responsibility for the improper or unsafe
operation of the burner due to failure to adequately address the concerns above.
•The information contained in this manual is to be used as a guide ONLY and may be superseded
by project specific specifications and drawings.

ACCESS COMBUSTION, LLC
WARNING:
Only authorized burner service personnel should start, adjust, or service this equipment!
Rev. 05
Page 4 of 19
Section II: Burner Overview
Fuel Gas Inlet
Pilot Gas Inlet
Combustion Blower
Flame Scanner Port
Observation Port
Burner Front Plate
Access Combustion Model B, Package Forced Draft Burner utilizes stage fuel design and with flue gas
recirculation (FGR) achieves Ultra-Low NOx emissions and near zero CO emissions when corrected to 3% O2.
Fuel is delivered to the burner via the gas inlet pipe and is mixed with air inside the burner housing. Portion of
the fuel is forced into the center of the diffuser. Remaining gas is forced into fuel nozzles where some is
partially premixed with air around the diffuser and/or forced into the combustion chamber tangent to the flame
envelope. The mixture is ignited downstream of the diffuser using internally located gas/electric pilot system.
The pilot is located inside the burner housing. The diffuser is a stainless-steel mixing device. The angle of the
diffuser blades forces the air to exit the diffuser with a spinning motion. The spinning air flow is mixed with gas
and is anchored by the turbulence generated by the diffuser. For Ultra-Low NOx emissions FGR can be added
to the combustion air. FGR dilutes the air with additional N2 and CO2. The additional N2 and CO2 lowers flame
temperature and the corresponding NOx emissions. FGR is delivered via FGR damper and is mixed with
combustion air stream in the combustion blower.
The burner is design to operate in a fire-tube and/or water-tube boiler application, as well as helical coil or
sealed combustion heat exchangers.
Burner housing
Air Inlet Damper
FGR Damper

ACCESS COMBUSTION, LLC
WARNING:
Only authorized burner service personnel should start, adjust, or service this equipment!
Rev. 05
Page 5 of 19
INSTALLATION CHECKLIST
Warning:
Make sure the checklist is reviewed and verified before proceeding to Burner Commissioning section.
Burner Check List
Is the burner securely connected to the heat exchanger?
Is the front plate properly installed and secured inside the heat exchanger?
Was the electrical wiring verified?
Were all motors checked for rotation?
Are all gas train components installed, and have been properly selected, sized and installed per
appropriate installation and wiring drawings and instructions?
For gas trains requiring venting, are the vent lines properly sized and installed?
Are gas train piping and components tested for leaks and are they gas tight?
Have the gas lines been purged?
Is the proper gas pressure available at the inlet to the fuel train?
Are there adequate provisions for the combustion air installed?
Is the burner combustion air inlet free from obstruction?
Heat Exchanger Check list
Is the heat exchanger filed with sufficient heating medium (water, oil, glycol, etc.)?
Are the heat exchanger safety limits verified, (low fluid cut-off, high temperature shutdown, etc.)?
Are any connected load circulation systems properly installed and operation verified?
Is the heat exchanger stack properly installed?
Is the heat exchanger stack unobstructed to allow for safe relief of the hot flue gasses generated by the
burner?
If draft control equipment is required, is it installed, and operation verified?
Are all specified auxiliary equipment installed properly? This may include thermostats, flow switches or
others.
At a minimum, the following interested parties should be notified of the burner startup date.
oEquipment Owner’s Representative
oMechanical Contractor’s Representative
oElectrical Contractor’s Representative
oService Organization’s Representative
oBurner Manufacturer’s Representative

ACCESS COMBUSTION, LLC
WARNING:
Only authorized burner service personnel should start, adjust, or service this equipment!
Rev. 05
Page 6 of 19
SECTION III:BURNER INSTALLATION

ACCESS COMBUSTION, LLC
WARNING:
Only authorized burner service personnel should start, adjust, or service this equipment!
Rev. 05
Page 7 of 19
TYPICAL GAS TRAIN
The gas outlet pressure setpoint adjustment screw is in the center of the
regulator cover. Clockwise rotation of the setpoint adjustment screw increases
the outlet gas pressure. Counterclockwise rotation decreases the outlet gas
pressure. The hexagonal cap must be tightened after the setpoint screw has
been adjusted and may be sealed from tampering by means of a wire and lead
seal.
2
1

ACCESS COMBUSTION, LLC
WARNING:
Only authorized burner service personnel should start, adjust, or service this equipment!
Rev. 05
Page 8 of 19
GAS TRAIN PRESSURE TEST
Warning:
Incoming main gas pressure must be lower than the maximum rated pressure on all gas trains components.
If smell of fuel is present evacuate the area and call gas supplier and/or fire department.
1. Make sure Leak Test Valve (1) is closed.
2. Slowly open incoming gas valve (2) and measure incoming gas pressure.
a. Close the incoming gas valve if main gas pressure exceeds maximum pressure ratings on the gas
train.
b. Contact your local gas supply company for pressure adjustment.
c. Contact Access Combustion Representative.
3. Check for gas leaks between main incoming gas and valve (2) on the gas train by either performing a bubble
test or measuring gas pressure.
a. Refer to your local gas code guidelines for gas leak test and gas test procedure.
4. Main Gas train leak test can only be performed during burner operation.
ELECTRICAL CONNECTION
Warning:
Risk of electric shock!
Only a qualified electrician should perform all electrical connection to the burner and all burner related
components!
1. Make sure Leak Test Valve (1) is closed and remains closed until burner is ready for commissioning.
2. Refer to the Wiring Diagram provided with the burner.
3. Check the wiring connection between fuel valves and burner control panel.
4. Check the wiring connections between the burner and heat exchanger limit switches.
5. Check blower rotation and verify the rotation is in the direction of the rotation indicated on the blower housing.

ACCESS COMBUSTION, LLC
WARNING:
Only authorized burner service personnel should start, adjust, or service this equipment!
Rev. 05
Page 9 of 19
BURNER SEQUENCE OF OPERATION
Refer to a Specific Burner Management System (BMS) Manual provided with the burner for detailed information
and control sequence timing information.
1. Burner is energized when demand is activated by heat exchanger limit switch.
2. Burner motor starts.
3. Air damper valve opens.
4. A pre-ignition air purge sequence begins.
5. Air purge time depends on the control type and is intended to provide 4 to 5 volume air exchanges before
starting the burner.
6. Air damper valve closes.
7. Ignition Transformer is energized.
8. Pilot solenoid valve opens.
9. Pilot flame is detected by the BMS.
10. Ignition Transformer is de-energized.
11. Main Solenoid valve opens.
12. Pilot Solenoid valve is de-energized.
13. Main flame is detected by the BMS.
14. Burner is ready for modulation.
If demand is interrupted
15. Main Solenoid valve are de-energized.
16. Air damper valve opens.
17. A post-ignition air purge sequence begins.
18. Air purge time depends on the control type.
19. Air damper valve closes.
20. Blower is de-energized.
21. Burner remains in standby mode.
22. If a fault occurs during the sequence of operation an error message will be displayed on the BMS.
23. Refer to the specific BMS manual provided with the burner for additional information.

ACCESS COMBUSTION, LLC
WARNING:
Only authorized burner service personnel should start, adjust, or service this equipment!
Rev. 05
Page 10 of 19
SECTION IV: BURNER COMMISSIONING
Warning!
Make sure Burner Installation Check list has been completed!
Make sure all steps were followed in accordance to the manual and local codes before commissioning the
burner.
Make sure proper combustion instruments (emission analyzers) are available and connected during the
duration of the burner commissioning!
PILOT SPARK PICKUP TEST
1. Make sure Leak Test Valve (1) is CLOSED and remains closed thought the duration of this test.
2. Make sure pilot manual valve is CLOSED
3. Open the manual shut-off valve (2)
4. Allow heat exchanger limit switch to close and energize the burner (demand).
5. Burner motor should start.
6. Air damper should drive to open, or fan should speed up.
7. A pre-ignition air purge sequence begins.
8. After pre-ignition purge air damper valve should close, or fan should speed down.
9. Ignition Transformer should energize.
10. Pilot solenoid valve should open.
11. At this point the BMS system should error out and fail on pilot flame failure. The BMS system should report
an error indicating failure to prove pilot flame. Refer to the specific BMS manual for details on how this
error will be reported.
12. Proceed to pilot commissioning test.
Spark Pickup condition is present when the BMS doesn’t show an alarm and allows the main gas valves to open.
Spark Pickup condition is not a safe operating condition and must be corrected before proceeding with
commissioning the burner.
Please contact Access Combustion Service Department for resolution.

ACCESS COMBUSTION, LLC
WARNING:
Only authorized burner service personnel should start, adjust, or service this equipment!
Rev. 05
Page 11 of 19
PILOT COMMISSIONING
Warning!
Make sure Spark Pickup Test was conducted and no Spark Pickup condition is present!
1. Make sure Leak Test Valve (1) is CLOSED and remains closed thought the duration of this test.
2. Make sure pilot manual valve is OPEN
3. Open the manual shut-off valve (2)
4. Allow heat exchanger limit switch to close and energize the burner (demand).
5. Burner motor should start.
6. Air damper should drive to open, or fan should speed up.
7. A pre-ignition air purge sequence begins.
8. After pre-ignition purge air damper valve should close, or fan should speed down.
9. Ignition Transformer should energize.
10. Pilot solenoid valve should open.
11. At this point the BMS system should sense the pilot flame. The BMS system should show a confirmed pilot
flame. Refer to the specific BMS manual for details on how this will be reported.
12. Verify pilot signal strength before proceeding to the next step.
a. Refer to the specific BMS manual for pilot flame signal strength test.
13. Adjust pilot pressure.
a. For more pressure adjust pilot pressure regulator by turning adjusting screw IN (clockwise).
b. For less pressure adjust pilot pressure regulator by turning adjusting screw OUT
(counterclockwise).
c. Pilot gas pressure should be between 6 to 10inch W.C. (15 to 25mbar)
14. If pilot flame signal is weak please refer to pilot troubleshooting section in the manual.
15. Contact Access Combustion Service Department for resolution.

ACCESS COMBUSTION, LLC
WARNING:
Only authorized burner service personnel should start, adjust, or service this equipment!
Rev. 05
Page 12 of 19
MAIN FLAME COMMISSIONING
Caution!
Make sure pilot flame signal is within BMS operation range before proceeding to the main flame test.
The burner is factory adjusted for “dry run” conditions. Adjustments and initial settings MUST BE CHECKED prior
to initial light off and settings MUST BE VERIFIED by combustion tests. All parts should be checked for proper
adjustment before initial light off as parts can shift during shipment.
1. Make sure Leak Test Valve (1) is OPEN.
2. Make sure pilot manual valve is OPEN
3. Open the manual shut-off valve (2)
4. Allow heat exchanger limit switch to close and energize the burner (demand).
5. Burner motor should start.
6. Air damper should drive to open, or fan should speed up.
7. A pre-ignition air purge sequence begins.
8. After pre-ignition purge air damper valve should close, or fan should speed down.
9. Ignition Transformer should energies.
10. Pilot solenoid valve should open.
11. The BMS system should show a confirmed pilot flame. Refer to the specific BMS manual for details on how this
will be reported.
12. Ignition Transformer should de-energize.
13. Main gas valves should open followed by main flame ignition.
At this point the BMS system should sense the main flame. Refer to the specific BMS manual for details on how
this will be reported.
14. Pilot valve should de-energize.
15. Burner should remain lit.
•Verify main flame signal.
•Verify CO and O2 emissions levels before changing burner setting.
•If the flame appears weak, slightly open gas butterfly valve until flame develops. Refer to specific BMS
manual for instructions on how to accomplish this setting change.
•It is normal for flame to appear orange during ignition and low fire setting.
•Check ALL remaining gas connections for gas leaks.
•Allow the heat exchanger and the front plate to slowly heat up before increasing firing rate.
16. Please refer to the BMS manual for further commissioning instructions.

ACCESS COMBUSTION, LLC
WARNING:
Only authorized burner service personnel should start, adjust, or service this equipment!
Rev. 05
Page 13 of 19
ADJUSTMENT OF AIR FLOW SWITCH
Air flow switch is used to prove the flow of combustion air from the blower assembly. It causes a lockout and burner
shutdown upon loss of or inadequate combustion air.
Switch should be set to open when combustion air is below minimum fire set point.
Switch should only energize and close when air flow is present.
ADJUSTMENT OF FILTER SWITCHES
Filter Switches are optional equipment.
For burner equipped with air inlet filter, the burner is supplied with additional air flow switches. The additional
switches are used to prove the performance of the filter and ensure proper flow of combustion air. Depending on
the option selected up to two switches may be provided;
Optional Filter Switch one causes lockout if filters are not providing sufficient air for high fire combustion.
Optional Second Filter Switch, triggers a dirty filter warning.
Filter switches should be adjusted at high fire by temporarily restricting filter inlet. Warning switch should be set to
open when high fire O2 level drops 1% from the normal operating condition. Lockout switch should be set to open
when high fire O2 level drops 2% from the normal operating condition.
ADJUSTMENT OF GAS PRESSURE REGULATORS
Gas burners have two gas pressure regulators, one to regulate and limit the pilot gas pressure and one to regulate
and limit the main gas pressure.
Refer to Pilot Commissioning for instruction on Pilot Regulator settings.
Main gas pressure regulator should be set together with main gas control valve. At high fire, main gas control valve
should be set to fully open position and the regulator set screw should be adjusted to provide sufficient gas flow at
high fire setting.
Turn adjusting screw clockwise to increase pressure or counterclockwise to decrease pressure.

ACCESS COMBUSTION, LLC
WARNING:
Only authorized burner service personnel should start, adjust, or service this equipment!
Rev. 05
Page 14 of 19
ADJUSTMENT OF GAS PRESSURE SWITCH
Gas pressure switches may or may not be supplied with the burner. They are optional and depending on the local
code and regulations, the size of the burner and job specific requirements.
Gas pressure switches are pressure activated switch devices designed for safety shutoff when the gas pressure is
either too high or too low. If the gas pressure sensed by the device reaches the device set point, the switch will open,
causing a shutdown. The system will then recycle or lockout depending on the control system used.
Gas pressure switches are designed to operate over a specific range, therefore they must be selected to be
compatible with the burner operating gas pressure and have the desired features. Gas pressure switch
manufacturer’s instructions should be consulted for detailed adjustment procedures.

ACCESS COMBUSTION, LLC
WARNING:
Only authorized burner service personnel should start, adjust, or service this equipment!
Rev. 05
Page 15 of 19
SECTION V: MAINTENANCE
GENERAL MAINTENANCE
DAILY MAINTENANCE
1. Observe the operation of the burner and operating controls to determine proper burner operation.
2. Visually inspect the condition of the filter assembly.
If the burner is installed on a boiler.
1. Check boiler water level in the sight glass and the steam pressure on the gauge to the steam boilers. Check
temperature reading and water pressure on hot water boilers.
2. Check the low water cutoff operation by opening the blow down valve on the low water cutoff to remove rust and
dirt and determine that the burner cuts out with low water in the sight glass. Immediate corrective action must be
taken if burner does not cut off with low water in the sight glass.
WEEKLY MAINTENANCE
1. Check all burner actuator connections. Tighten if necessary.
2. Check all phases of the operation of the control circuit for proper operation.
3. Operate burner manual shutoff valves to determine that they are working freely and properly. Lubricate if necessary.
4. On burners equipped with air inlet filters, remove and clean the pre-filter assembly.
MONTHLY MAINTENANCE
1. Check pilot assembly.
a. The ignition electrode must be centered in the ignitor body.
b. The ignition electrode and pilot assembly should be inspected and cleaned if necessary.
c. The high-tension wire between the transformer and the ignition electrode should be checked for
deterioration.
d. The flame scanner should be inspected and cleaned if necessary.
2. Check air dampers for smooth operation. Remove accumulation of lint or dirt.
3. Lubricate motors in accordance with motor manufacturer’s instructions.
4. Perform all tests and inspections required under “Weekly Maintenance”.
5. On burners equipped with air inlet filters, remove and clean the pre-filter assembly.
ANNUAL MAINTENANCE
1. Have the burner inspected and checked by a qualified service representative.
2. If the heat exchanger is to be out of service for a long period of time close all manual valves. Turn off burner by control
switch, being sure to leave electrical power on the control panel. Leaving power on the control panel will help prevent
humidity damage to the flame safeguard.
3. On burners equipped with filters, remove and replace filter assembly.

ACCESS COMBUSTION, LLC
WARNING:
Only authorized burner service personnel should start, adjust, or service this equipment!
Rev. 05
Page 16 of 19
PILOT TROUBLESHOOTING
A problem with pilot operation is one of the most common problems to occur in a burner system. Typically, these
problems are due to improper adjustment or maintenance. This list is intended to cover the most common pilot
problems which occur and potential actions to take. This list is not exclusive but should be used as a starting point
when problems are occurring with the pilot.
Problem
Possible Cause
Action
Motor runs but ignition spark does not occur.
Ignition cable or electrode loose or
grounded.
Check to insure ignition cable is securely
plugged into the electrode. Check cable or
replace if necessary.
Remove and check electrode insulator for
cracks.
Using a multimeter set to resistance (Ohms
or Ω), check resistance between the ignition
electrode and the pilot insert. The resistance
should show as infinite (overload). If
resistance is less than infinite the ignition
electrode is grounded. Check entire ignition
electrode for potential grounding locations,
such as foreign materials or obstructions,
cracked insulator or damaged ignition
electrode.
Pilot ignition transformer defective.
Check for 120 volts primary voltage on
ignition panel terminal. Replace transformer
if needed.
Defective flame safeguard.
Check for 120 volts primary voltage on
ignition panel terminal. Replace flame
safeguard if needed.
Motor runs, ignition spark occurs, but gas
does not ignite.
No gas supplied to pilot.
Check the manual pilot gas shutoff valve to
ensure it is open.
Make sure gas line has been purged of air or
other purge gases.
Ensure the pilot orifice and supply line are
free of obstruction. If they are obstructed,
clean.
Gas pilot regulator failed. Check inlet gas
pressure and replace gas pilot regulator if
required.
Pilot gas valve does not open.
Check for 120 volts to coil. Check valve action
by sound and feel. Replace coil or valve body
as needed.
Improper gas flow to pilot.
Increase or decrease gas pressure to pilot.
Motor runs, gas pilot lights, but pilot flame
does not prove, and control locks out of
pilot flame failure.
Improper gas flow to pilot.
Increase or decrease gas pressure to pilot.
Flame sensor dirty.
Clean or replace sensor.
Flame sensor cannot see pilot.
Look through sight tube. If unable to get clear
view of pilot, adjust sight tube.
Improper ground circuit.
Check for voltage on neutral wire to panel
ground. Voltage should not be more than 0.5
Volts.

ACCESS COMBUSTION, LLC
WARNING:
Only authorized burner service personnel should start, adjust, or service this equipment!
Rev. 05
Page 17 of 19
PILOT ASSEMBLY
ITEM
PART DESCRIPTION
ITEM 1
PILOT GAS CONNECTION
ITEM 2
ELECTRODE
ITEM 3
IGNITION TUBE
ITEM 4
SPARK ROD
Pilot fuel adjustments can be made via the pilot fuel regulator. This is typically set during burner commissioning and
should be checked as a part of an annual inspection by qualified service personnel and does not require adjustment
unless conditions change.
PILOT ADJUSTMENT,CLEANING.
1. Disconnect cables, lines and tubes from the pilot assembly and remove from burner assembly.
2. Inspect ignition tip for cleanliness and proper adjustment.
a. Make sure spark rod is clean and free of corrosion and/or soot.
b. Make sure the spark rod location is as shown and the gap between spark rod and ignition tube is
set to 1/8 inch. If not, the spark rod may be gently bent back into the proper position.
3. Check Electrode for cleanliness and/or cracks.
4. Reinstall ignition electrode assembly and check that the spark rod maintains the proper gap and is not
touching igniting tube.
5. Reinstall pilot assembly in the burner, ensuring that all cable, lines and tubes are reattached and tightened.
Set Gap Between Item 4 and Item 3 to 1/8 INCH
Item 2
Item 1
Item 3
Item 4

ACCESS COMBUSTION, LLC
WARNING:
Only authorized burner service personnel should start, adjust, or service this equipment!
Rev. 05
Page 18 of 19
WARRANTY POLICY
Limited Warranty:
Access Combustion warrants that at the time of shipment, the equipment manufactured by Access
Combustion shall be free from defects in material and workmanship. Access Combustion warranty is conditioned
upon the equipment being properly installed, maintained and operated within the equipment’s capacity under
normal load conditions.
Equipment, accessories and other parts and components not manufactured by Access Combustion are warranted
only to the extent of and by the original manufacturer’s warranty to Access Combustion. In no event shall such other
manufacturer’s warranty create any more extensive warranty obligations of Access Combustion to the Buyer than
Access Combustion warranty covering equipment manufactured by Access Combustion.
Exclusions from Warranty:
The foregoing is in lieu of all other warranties, oral or express or implied, including any warranties that
extend beyond the description of the equipment There are no express warranties other than those contained herein
to the extent permitted by the law. There are no implied warranties of fitness for a purpose. The provision as to
duration, warranty adjustment and limitation of liability shall be the same for both implied warranties and expressed
warranties.
Access Combustion warranty is solely as stated above and does not apply or extends to expendable items,
ordinary wear and tear, altered equipment, equipment repaired by persons not expressly approved by Access
Combustion, material not made by Access Combustion, or to equipment damage caused by accident, abuse, misuse,
temporary heat, electrical overload, erosive or corrosive substance or other contaminated elements.
Warranty Adjustment:
Buyer must make claim of any breach of any warranty by written notice to Access Combustion within thirty
(30) days of the discovery of any defects. Access Combustion retains an option to repair or replace, BUT NOT INSTALL,
F.O.B. Access Combustion plant, any parts or parts of the equipment which within twelve (12) months from the date
of initial operation but no more than eighteen (18) months from date of shipment are found to be defective within
the above warranty. Access Combustion retains the right to review and inspect the defective parts or equipment
before any warranty action is taken. Any warranty adjustments made by Access Combustion shall not extend the
initial warranty period set forth above. Expense incurred by the Buyer in replacing or repairing or returning the
equipment or any part or parts will not be reimbursed by Access Combustion.
Spare and Replacement Parts Warranty Adjustment:

ACCESS COMBUSTION, LLC
WARNING:
Only authorized burner service personnel should start, adjust, or service this equipment!
Rev. 05
Page 19 of 19
Access Combustion sells spare and replacement parts. Buyer must make claim of any breach of any spare
or replacement parts by written notice to Access Combustion within thirty (30) days of the discovery of any alleged
defect for all such parts manufactured by Access Combustion. The company agrees to its option to repair or replace,
BUT NOT INSTALL, F.O.B. Access Combustion plant, any parts or parts of the equipment which within twelve (12)
months from the date of initial operation but no more than eighteen (18) months from date of shipment are found
to be defective within the above warranty. Access Combustion retains the right to review and inspect the defective
parts or equipment before any warranty action is taken. Any warranty adjustments made by Access Combustion
shall not extend the initial warranty period set forth above. The warranty and warranty period for spare and
replacement parts not manufactured by Access Combustion (purchased by Access Combustion from third party
suppliers) shall be limited to the warranty and warranty adjustment extended to Access Combustion by the original
manufacturer of such parts. In no event shall such other manufacturer warranty create any more extensive warranty
obligations Access Combustion to the Buyer for such parts then Access Combustion warranty adjustment covering
part manufactured by Access Combustion. Expense incurred by the Buyer in replacing or repairing or returning the
equipment or any part or parts will not be reimbursed by Access Combustion.
Limitation of Liability:
The above warranty adjustment set forth Buyers exclusive remedy and the extend of Access Combustion
liability for breach of implied (if any) and express warranties, representations, instructions or defects from any cause
in connection with the sale or use of the equipment. Access Combustion shall not be liable for any special, indirect
or consequential damages or for loss, damage or expense, directly or indirectly arising from the use of the equipment
or from any other cause whether based on warranty (express or implied) of tort or contract, and regardless of any
advice or recommendations that may have been rendered concerning the purchase, installation, or use of the
equipment.
Table of contents
Popular Burner manuals by other brands
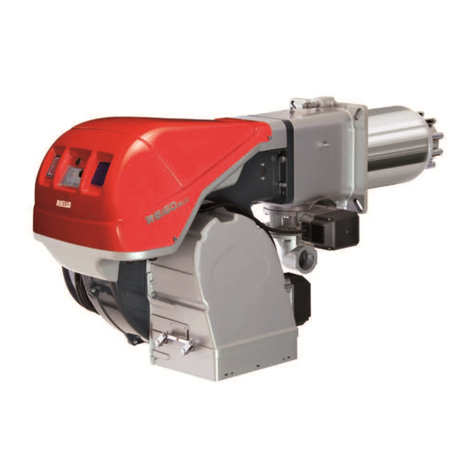
Riello
Riello RRS 68/E O2 BLU Installation, use and maintenance instructions
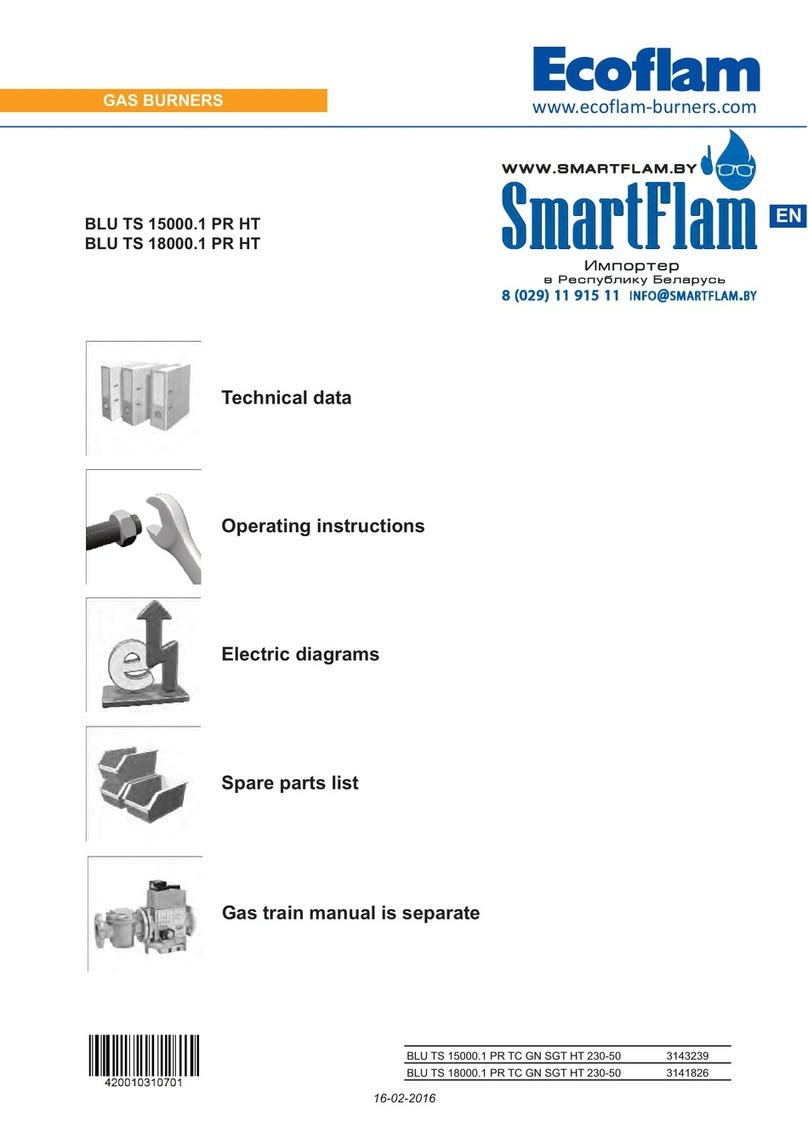
Ecoflam
Ecoflam BLU TS 15000.1 PR HT instruction manual

Riello
Riello GAS 3 Installation, use and maintenance instructions
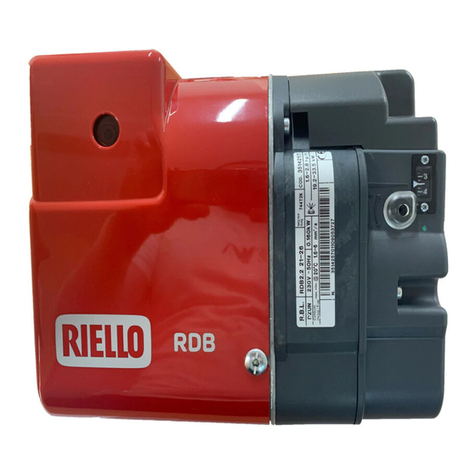
Riello
Riello RDB2.2 FIREBIRD C20 70K DGT Installation, use and maintenance instructions

LAMBORGHINI
LAMBORGHINI ECO 30 Installation and maintenance manual
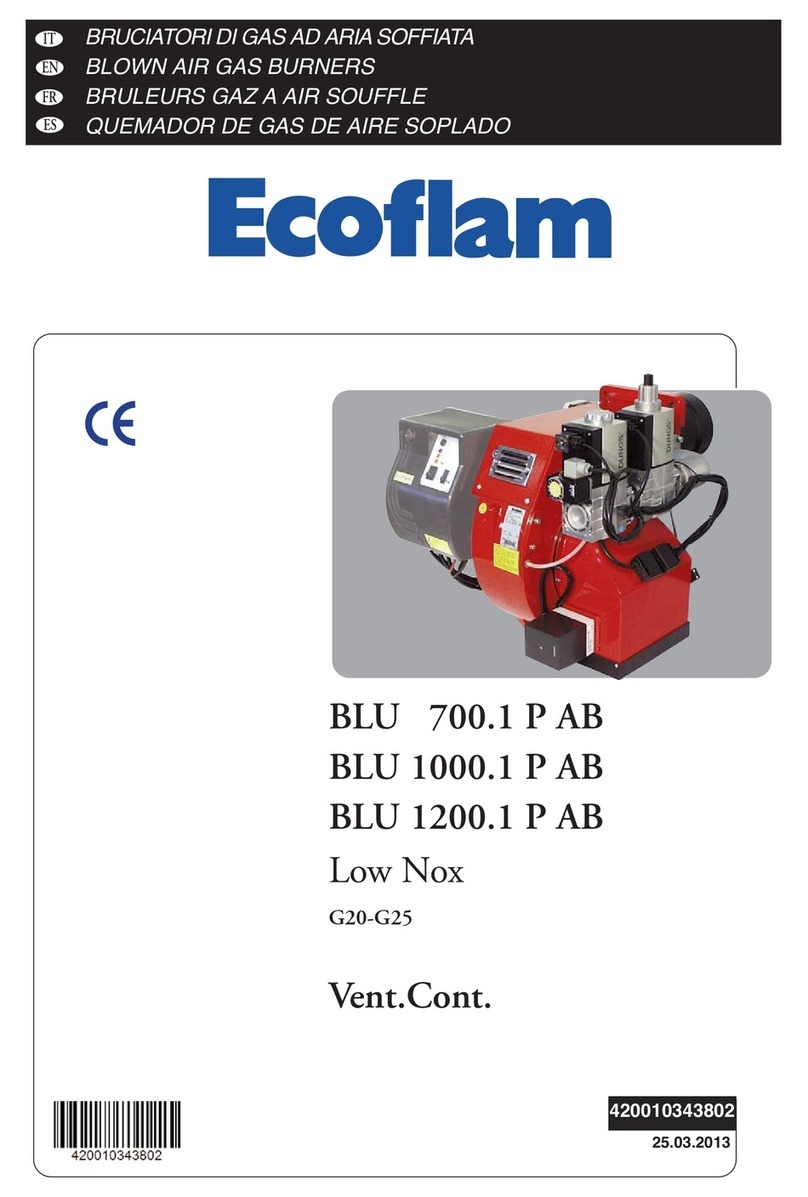
Ecoflam
Ecoflam BLU 700.1 P AB instruction manual
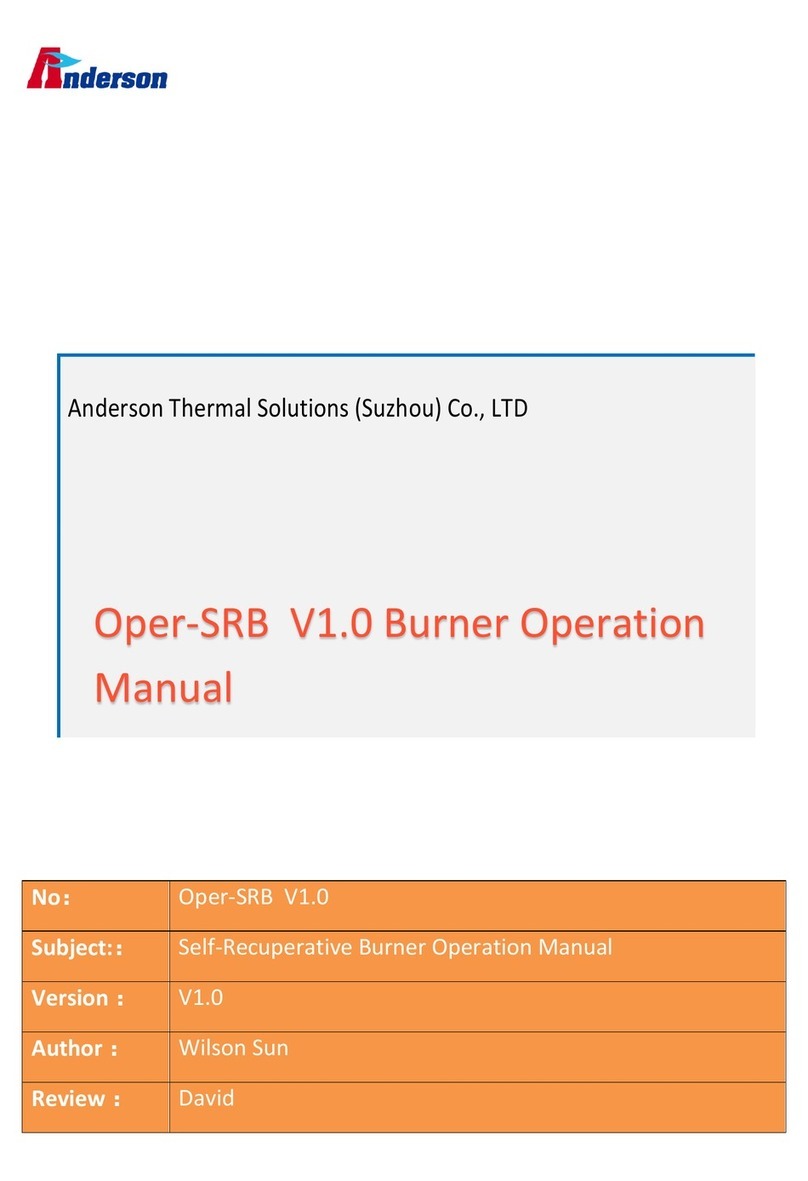
Anderson
Anderson Oper-SRB Operation manual

Riello
Riello 484 LD2X Installation, use and maintenance instructions
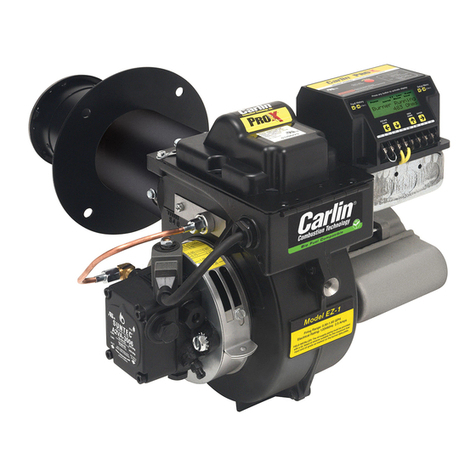
Carlin
Carlin EZ Series instruction manual
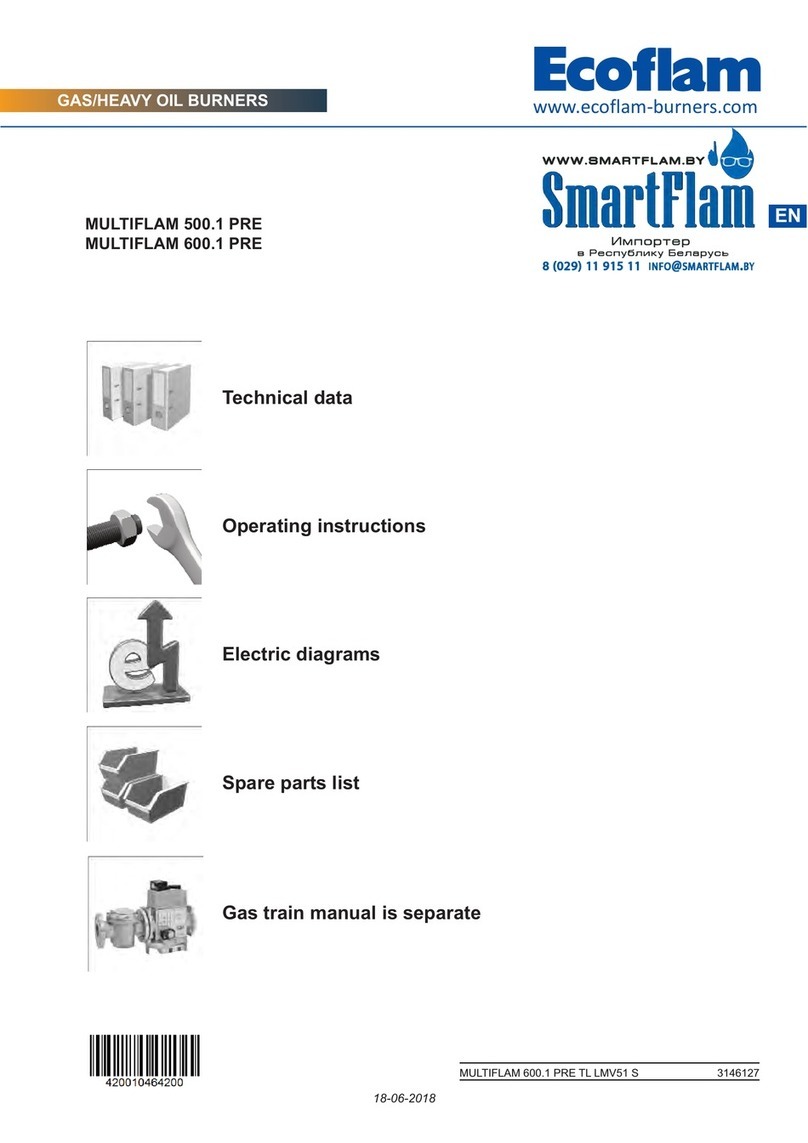
Ecoflam
Ecoflam MULTIFLAM 500.1 PRE manual
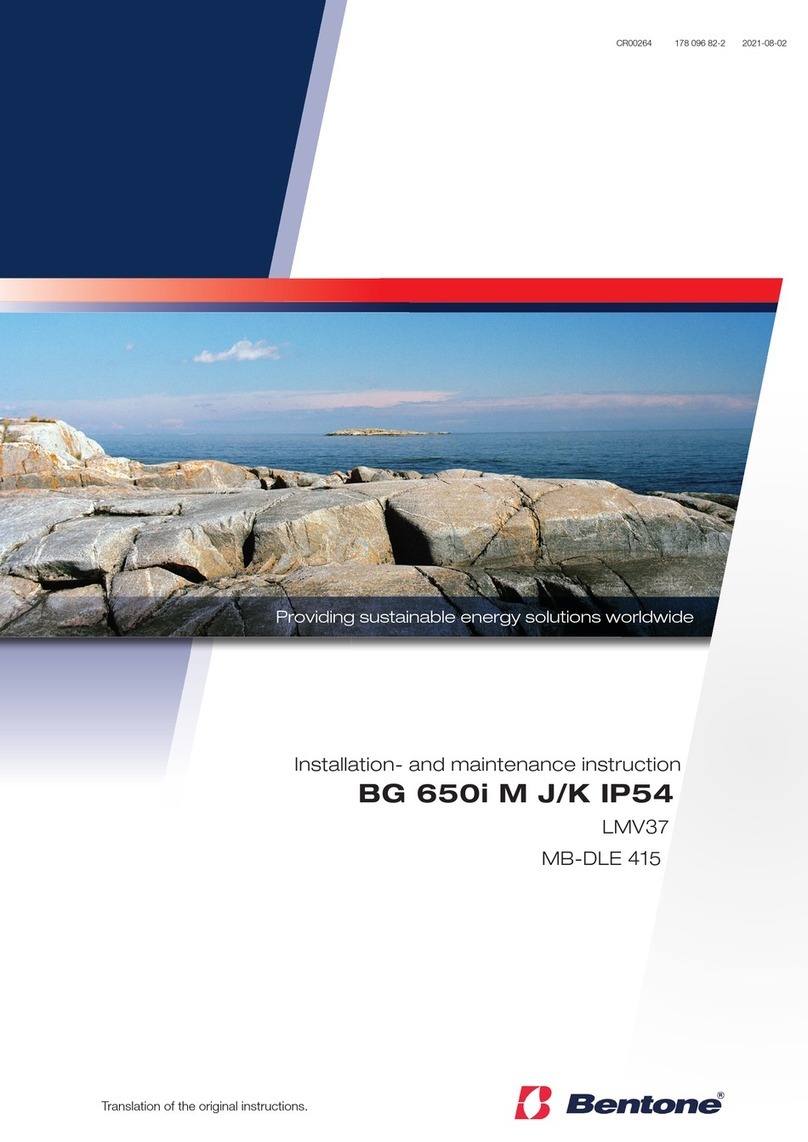
Bentone
Bentone BG 650i M J/K IP54 Installation and maintenance instruction

Integra
Integra FIREBOY eco operating instructions