Adisa ADITRAT User manual

ADITRAT
REFILLING WATERS TREATMENT
TECHNICAL MANUAL OF INSTALLATION,
USE AND MAINTENANCE
3/2011bis

INDEX
1. ADITRAT 1
1.1. Introduction 1
1.2. Construction – Installation – Operation 1
1.3. System 2
2. WATER SOFTENER 3
2.1. Generalities 3
2.2. Operation 3
2.3. General characteristics of the programmer valve 4
2.3.1. General notes for the valve installation 5
2.3.2. Installation of the softener 5
2.3.3. Hydraulic operation 6
2.3.4. Regulation of the regeneration phases 6
2.3.5. Start up 7
2.3.6. Change of the injector 7
2.4. Maintenance guide 8
3. DISPENSER 11
3.1. Working conditions 11
3.2. Start up 11
3.3. How to regulate the dosage 11
3.4. Maintenance 11
3.5. Recommendations 12
4. DESCALING PRODUCT 12
4.1. Characteristics 12
4.2. Chemical properties 12
4.3. Treatment doses 12
Data indicated in the present manual are liable to changes.
ADISA CALEFACCIÓN (ARTICULOS DOMESTICO-INDUSTRIALES CALEFACCIÓN S.L.) has the right to
make modifications without notice of any product of its range.
No company, person or entity external to ADISA CALEFACCION (ARTICULOS DOMESTICO-
INDUSTRIALES CALEFACCIÓN S.L.) can modify this document.

Technical manual ADITRAT
1
1. ADITRAT
1.1. Introduction:
In a closed heating or cooling circuit, if periodical water refillings are not realized, the initial water can
eventually lose its content of cal and salts, which will settle down in a negligible quantity without
affecting the installation. Air, oxygen and dissolved gases are evacuated by the air/gas venting
purgers installed, so the processes of corrosion and oxidation are minimal.
However, if periodical refillings with non-treated water are continually realized in these circuits, new
inputs of cal, salts, oxygen, etc. are also introduced, which means:
- Cal and salts will start to settle down more and more, contributing to cause scaling in
the installation, especially in the boilers, and the scale thickness will increase every time the
installation is refilled, decreasing its transfer capacity.
- Oxygen, air and dissolved gases can give rise to oxidation and corrosion processes in the
circuit, producing oxides and sludge. These oxides and sludge will start to settle down in the
installation preventing the equipments to correctly operate, the radiators to work at 100% of
their capacity, and the same will happen to the heating and cooling generators.
This process will cause deterioration of the installation and of the equipments installed. So it would be
important to avoid realizing refillings with non-treated water and, if this is not possible, at least add a
chemical treatment in the refilling water.
In order to avoid this deterioration, ADISA introduces its system for treating the refilling water:
ADITRAT.
1.2. Construction - Installation - Operation
The equipment ADITRAT is a compact unit, hydraulically connected and fixed on a base, composed
of: 1. Gas pressure governor.
2. Descaling product.
3. Dispenser of chemical product inhibiting corrosion and scaling.
4. Tank for an easy and quick refilling of the inhibiting product.
5. Water meter.
6. Non-return valve.
7. Cut-off valves.
Operation parameters :
* Connections of 3/4".
* Minimum pressure: 2 bar
* Maximum pressure: 4 bar
* Minimum flow: 20 l/h
* Maximum flow: 1.500 l/h
* Temperature: 45º C
* Electric supply: 220 V, 50 Hz, single phase
You just need to connect it to the water inlet of the circuit.

Technical manual ADITRAT
2
1.3. System:
1. GAS PRESSURE GOVERNOR
2. SOFTENER
3. DISPENSER
4. TANK FOR QUICK REFILLING
5. WATER METER
6. NON-RETURN VALVE
7. CUT-OFF VALVES
E. COLD WATER INLET
C. CONNECTION TO THE
INSTALLATION
L. QUICK REFILLING OF THE PRODUCT
V. DRAINING
DIMENSIONS OF THE BASE: 800 x 680 mm.
HEIGHT: 1050 mm.
2
E
1
C
6
5
3
L

Technical manual ADITRAT
3
2. WATER SOFTENER
2.1. GENERALITIES:
The water, while crossing the earth strata, becomes rich of mineral salts that represent its total
salinity. The presence of some of these salts, such as calcium and magnesium, determines its
hardness, which is the main cause of scale and damages to the water installations (control valves,
security valves, purgers, boilers, heaters…).
It is convenient to install a SOFTENER that, by means of synthetic resins, can absorb the calcium and
magnesium salts and eliminate the excessive hardness.
SCALE:
Scale is another serious problem caused by the water hardness. Pipes, through which the hard water,
cold or hot, is circulating, can get obstructed. Scale is not necessarily produced when the water
temperature is high, any variation on the original water temperature is sufficient to generate it.
With the progressive increase of scale in a water heater, or boiler, it happens that the boiler can need
more and more energy to transfer the same heat, coming to consume by 30% more than if it would
work with soft waters. Furthermore, this can cause overheating of the materials with the consequent
break of the equipments. All these problems disappear with the use of soft or decalcified water.
THE SOFTENER:
There are various effective methods to reduce the water hardness, the most appropriate are:
deionization, distillation, reverse osmosis and the ionic interchange (decalcification).
The softener is composed of a tank for resins and another one for salt (salt is necessary for the
periodical regeneration of the resins). The unit is completed by a programmer valve regulating the
washing cycles necessary to the equipment’s efficiency.
2.2. OPERATION
The water decalcification is due to an interchange of ions (calcium-magnesium for sodium) at the
moment the water passes through a bed of special resin. Once the resin gets saturated, it must be
washed or regenerated with salt.
In order to preserve the life of the resin, its regeneration must be realized according to the following
guidelines:
First of all, a good cleaning in order to eliminate all the impurities that may have settled down on the
resins.
Secondly, proceed to wash the resins with brine (salt dissolved in water).
Finally, a good rinsing to eliminate the exceeding salt.

Technical manual ADITRAT
4
In order to facilitate these operations of regeneration, we have incorporated a programmer valve (type
chronometric) in our equipments, which realizes automatically all these different operations.
BODY
Diameter
Nr. Cycles
DESCRIPTION AND APPLICATIONS
NORIL
3/4"
3
AUTOMÁTIC-CHRONOMÉTRIC
Automatic regeneration programmable per days.
Cycles: service-salt suction and slow washing.
A. Programmer valve
B. Resin column
C. Feed central pipe
D. Resin
E. External casing
F. Assembly of brine
2.3. GENERAL CHARACTERISTICS OF THE PROGRAMMER VALVE:
* Body in NORYL, just one piece, no risk of leaks.
* No possibility of corrosion due to the NORYL characteristics.
* Possibility of regulating the draining water.
* Flow guaranteed from 20 to 50 litres/minute, with a pressure drop of 1 kg/cm
2
.
* Hydraulic characteristics : Kv. SERVICE = 68,54
Kv. COUNTER-WASHING = 11,995
* MAINS CONNECTIONS AND CONSUMPTION OF 3/4" Gas.
* The programmer is made in NORYL.

Technical manual ADITRAT
5
2.3.1. GENERAL NOTES FOR THE VALVE INSTALLATION:
1.- The softener must be installed very close to a draining point in order to discharge in it the
water coming from the regeneration processes.
2.- The drain pipe should be as shortest as possible, with a pass of ½” at least. It should not be
installed in a higher point than the draining connection of the softener in order not to limit the
suction process of the brine.
3.- The drain outlet leading to the drain should be free fall, without any obstacles interrupting or
reducing the connection diameter.
4.- Be sure that the softener and the salt tank are well levelled. Place them on a clean and plate
surface.
5.- Before realizing the electric connections, check that the voltage and the frequency from the
mains correspond to the ones of the valve (220V, 50Hz).
6.- The valve power point should be provided with a good earth connection.
2.3.2. INSTALLATION OF THE SOFTENER
1.- Connection of the drain pipe.
- The connection must be realized in the point marked in the valve with the word DRAIN,
which is situated on a side of the programmer head.
2.- Assembly brine injector.
- This series of valves are equipped in our factory with the injector nr. 3. The function of the
injector disk is to create the necessary vacuum to extract the brine from the salt tank and
inject it into the softener.
3.- Correspondence pressure-injector disk.
4.- Salt tank.
- This is the procedure to measure the height of the brine valve floater:
a) Pour into the tank as many litres of water as the litres of resin contained in the softener. It
is recommended to add a 20% more of water as a safety margin.
b) Fill the tank with salt up to the level of the chimney.
c) Wait a few minutes until the salt settles down.
d) Put the valve floater at the same height as the level the water has reached inside the
chimney.
- It is necessary to maintain the level of the salt ALWAYS above the level of the floater after
the first regeneration.

Technical manual ADITRAT
6
2.3.3. HYDRAULIC OPERATION.
Cycles of five or three phases:
** PHASE 1 - SERVICE.
Decalcification of the water in a downward circulation.
** PHASE 2 – BRINE SUCTION.
In a downward mode, the injector will suck the brine from the salt tank and bring it to the resin.
The drain outlet is open.
** PHASE 3 - SLOW WASHING.
Once the phase of the brine suction is over, the valve will realize a slow rinsing of the resin,
sweeping away the salts that have gathered in the bed. It is a downward circulation.
- It is necessary to calculate the required time for these two phases, so that the time fixed for
the first phase should correspond to 1/3 of the total time required for both.
2.3.4. REGULATION OF THE REGENERATION PHASES.
1.- Duration of the regeneration.
Be sure that all clips of the wheel (H) are stretched
(outwards) in order to avoid a spontaneous regeneration
when you use the controls.
- Loosen the screw (A) and move the cams so that the
signal (B) coincides with the required total
regeneration time.
EXEMPLE:
In the drawing, the signal (B) coincides with a time of
70 minutes, tighten again the screw (A) once you have
fixed the regeneration time.
2.- Set the regeneration hour.
- Turn the disk (J) until the required hour for the regeneration can be read in the hole (L). Make
sure that the programmed hour corresponds to Day or Night.
+ AM = from midnight to noon.
+ PM = from noon to midnight.
3.- Set the hour.
- Turn the milling wheel (C) until the signal (D) coincides with the actual hour, marked on the
disk (J). The concept of “actual hour” corresponds to the hour at the moment of realizing this
operation.

Technical manual ADITRAT
7
4.- Frequency of regenerations.
Being all the clips stretched (according to operation 1):
- Press as many clips as many days you want to realize the regeneration, consecutive or
alternate.
EXAMPLE: - Daily regeneration:
Press all clips.
- Alternate regeneration, every 3 days:
Press the first clip, leave the following two clips on the left stretched,
then press the next clip, and so on, until the clips are over.
- Once you have fixed all the clips, make coincide one of the ones you have pressed with the
signal (E) DAY, and you will activate a process of regeneration for that same day.
5.- Manual immediate regeneration:
- Make coincide one of the pressed clips of the wheel (H) with the signal (E) DAY.
- Turn the control (C) anticlockwise until the wheel (F) gets in contact with and presses the
drain valve stem (G), and you will immediately activate a process of regeneration.
- Do not forget to reset the hour of the programmer after manipulating it.
2.3.5. START UP.
As previously mentioned, the working pressure of the softener must be between 2 kg/cm
2
and 4
kg/cm
2
. * Check it.
A pressure lower than 2 kg/cm
2
does not allow obtaining correct brine suction, and an excessive
pressure risks to damage the valve or the salt suction system.
In case the pressure from the mains is higher than the maximum pressure recommended, it is
important to install a reducing pressure valve before the softener.
* Check the prefixed times in the programmer.
* Activate the phase of counter-washing to wash the resin in order to eliminate the dust and the
dirtiness that can be present in it. This operation can be realized by disconnecting the brine
suction pipe from the salt tank and then by activating the phase of slow washing during 20
minutes.
* Put the softener in the phase SERVICE.
* Then, check the operation of the other phases in the fixed times.
* At the end, once a complete regeneration has ended, check that the softener supplies water
with a hardness = 0ºF (the recommended hardness is 5ºF).
2.3.6. CHANGE OF INJECTOR.
In case the inlet pressure is not high enough to suck brine or, on the contrary, is too high for the
valve injector, it is recommended to change the latter. In order to regulate and make the suction
times more precise, act on the drain regulation valve.

Technical manual ADITRAT
8
2.4. MAINTENANCE GUIDE.
- The filter installed inside the injector must be periodically cleaned and checked.
- It is recommended to put a filter for impurities in the installation, before the softener.
PROBLEM: AFTER REALIZING A COMPLETE REGENERATION, THE HARDNESS IS > 5º F
POSSIBLE ORIGIN CORRECTION
Increase of the planned water quantity.
Check the consumption.
Adjust again the programmer in case you
need more than one regeneration.
Not sufficient brine quantity.
Raise the position of the floater in the
brine valve.
Excessively fast brine suction.
Change the injector disk for one of greater
number.
Check the height of the floater.
Low concentration of brine due to a reduction of
the diameter or to a constriction in the suction
pipe.
Eliminate the constriction.
Change the suction pipe.
Low concentration of brine due to dirtiness in the
injector passage grooves.
Clean the injector disk.
Clean the injector filter.
Short times of counter-washing and total times
of suction.
Increase.
Change of water quality
(Content of Ca, Mg in bicarbonates)
Analyze the water from the mains.

Technical manual ADITRAT
9
PROBLEM: THE SOFTENER DOES NOT SUCK THE BRINE
Disconnect the brine suction pipe from the floater valve.
Check if during the induction cycle, there is suction through this
pipe. If it is so, the origin of the problem is in the brine tank.
POSSIBLE CAUSE
CORRECTION
Lack of salt in the tank
Add salt
Obstruction in the floater valve
Clean and eliminate the obstruction
Faulty brine valve
Change the salt valve
Disconnect the brine suction pipe from the floater valve. During the
salt induction cycle, there is no suction through this pipe. The origin
of the problem is in the valve (apart from a possible fault in the tank
too).
Obstruction in the brine suction pipe.
Eliminate the obstruction
Valve H.1020, or, PNV-7 is obstructed.
Unblock or change it.
Injector’s filter is obstructed (full of dirtiness)
Eliminate dirtiness or change it.
Obstructed injector. (Grooves covered with
dirtiness).
Clean the injector disk grooves. Change.
Insufficient inlet pressure.
Watch that the minimum pressure is
higher than 2 kg/cm
2
.
Disconnect the brine suction pipe from the floater valve. During the
induction cycle no suction is detected, on the contrary water is
expulsed towards the salt tank. The origin of the problem is in the
valve or in the mains.
Insufficient suction power of the injector.
Change the injector disk for another one
of a lower number.
Drain regulation valve closed. It is placed in the
front higher part, immediately behind the timer.
Open it.
With the valve in front, you can see the
two flat faces on both sides.
Injector gasket is not well placed. (It does not
coincide with the disk grooves).
Place the gasket in the right position.
Insufficient inlet pressure.
Watch that it must be minimum 2 kg/cm
2
.

Technical manual ADITRAT
10
PROBLEM: THE SOFTENER DOES NOT REGENERATE ALTHOUGH IT SUCKS BRINE.
(Salted water comes out of the drain just after sucking brine).
The lower feed pipe is short or split.
The water with brine goes directly to the drain
without passing through the tank (which means
without passing through the resin).
Change the feed pipe.
Check that this pipe connection is not
loose or broken.
Change the lower connection. Change
connection pipe.
High content of chlorides, nitrates or iron
compounds in the water from the mains.
Analyze again the water and rectify
according to the result of the new
analysis.
PROBLEM: PRESENCE OF SALT IN THE CONSUMPTION LINE
The time of slow washing is too short.
Increase it.
The injector is small (it needs too much time for
sucking brine.)
Change the injector for another one of
greater size.
Suction of excessive quantity of brine.
Check the floater height in the salt valve.
Lower it.
PROBLEM: WATER KEEPS ON COMING OUT FROM THE DRAIN AFTER THE
REGENERATION HAS ENDED.
Damaged drain valve.
It does not adjust correctly, or lack of a O-ring
gasket.
Change the valve.
Clean the drain valve. Put a O-ring
gasket.
Programme cams are loose.
Tighten the fixing screw.
The control pinion for regeneration is jammed or
the cogs worn down.
Change the control pinion.
** OBSERVATIONS.
- It is recommended that the power point of the supply system (from the mains) is provided
with a good earth connection, no higher than 16 Ω.
- In case you have to tighten or loosen the tank valve, it is recommended to do it with the
maximum precaution, without levering up one of the connections, in order not to break its
base. Consider that, even if NORYL is a resistant material, it has a low limit of flexibility.

Technical manual ADITRAT
11
3.
DISPENSER
3.1. WORKING CONDITIONS
* Minimum pressure: 2 bar
* Maximum pressure: 4 bar
* Minimum flow: 20 l/h
* Maximum flow: 1.500 l/h
* Minimum temperature: 45º C
3.2. START-UP
Progressively open the water and let the suction pipe fill with
the product to be dispensed. Once the suction pipe is full, the
dispenser will be ready to operate.
3.3. HOW TO REGULATE THE DOSAGE
Unscrew the dispenser’s body P004.
Pull down the spring.
Take out the pin and place it where you prefer.
Dosage: . Not use
. 0'5 %
. 0'8 %
. 1 %
Release the spring so that it can go back to its initial position.
Screw the dispenser’s body P004.
3.4. MAINTENANCE
Respect the flow and pressure values indicated in paragraph 4.
Use the dispenser with cold or tepid water and if the products to be dispensed are solid
take care that they are well dissolved.
Install the dispenser by avoiding sources of heat and frost.
Clean the dispenser every time after using it: make it work and suck clean water at the
same time during 15 minutes.

Technical manual ADITRAT
12
3.5. RECOMMENDATIONS
Dispense just soluble products and take care that they do not crystallize.
Do not use very dense or thick products.
Consult before using acid products (chloride, acetic acid…), alkaline (detergents, chlorine...)
or solvents.
In case you use some tools to manipulate the equipment, it is recommended not to force on
the pieces because most of them are closed by means of O-ring gaskets.
4. DESCALING PRODUCT
It is a liquid descaling product against corrosion and incrustation for closed circuits.
It is principally made of: molybdates, polyacrylates, organic polymers and corrosion inhibitors.
4.1. CHARACTERISTICS
Colour: light yellow liquid.
Smell: slightly ammoniac.
Density: 1,2 gr./c.c.
ph pure product: 10'7
ph in dissolution at 1%: 9'5
It is compatible with glycolic antifreeze.
4.2. CHEMICAL PROPERTIES
This product should be employed in closed circuits, cold or hot water, or in those cases requiring
the maximum effectiveness that no other products can achieve.
Thanks to its chemical stability and its dispersing action, it has an excellent inhibiting effect of
large duration in all metals (steel, copper, aluminium, brass, zinc, etc…).
4.3. TREATMENT DOSES
They will depend on the water quality and on the system work conditions.
The recommended doses are:
- 2-3 gr/litre in water of very low hardness or in circuits where the treatment is applied for the first
time.
- 1 gr/litre in hard waters or in doses for maintenance.
No more quantity of product should be added if there is no water refilling in the circuit.

13
Table of contents
Popular Water System manuals by other brands
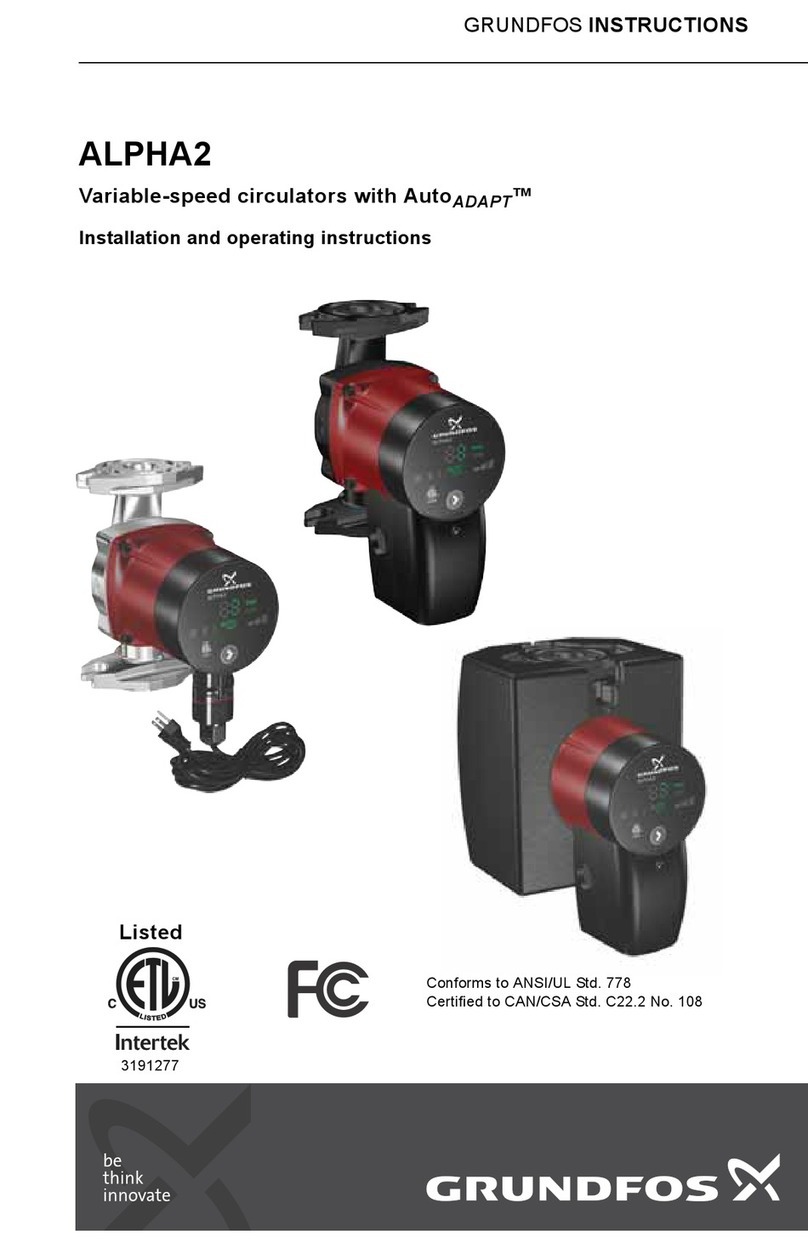
Grundfos
Grundfos alpha2 l Installation and operating instructions

Watts Premier
Watts Premier RO-PURE Installation, operation and maintenance manual

Rotek
Rotek KSRO Series installation manual
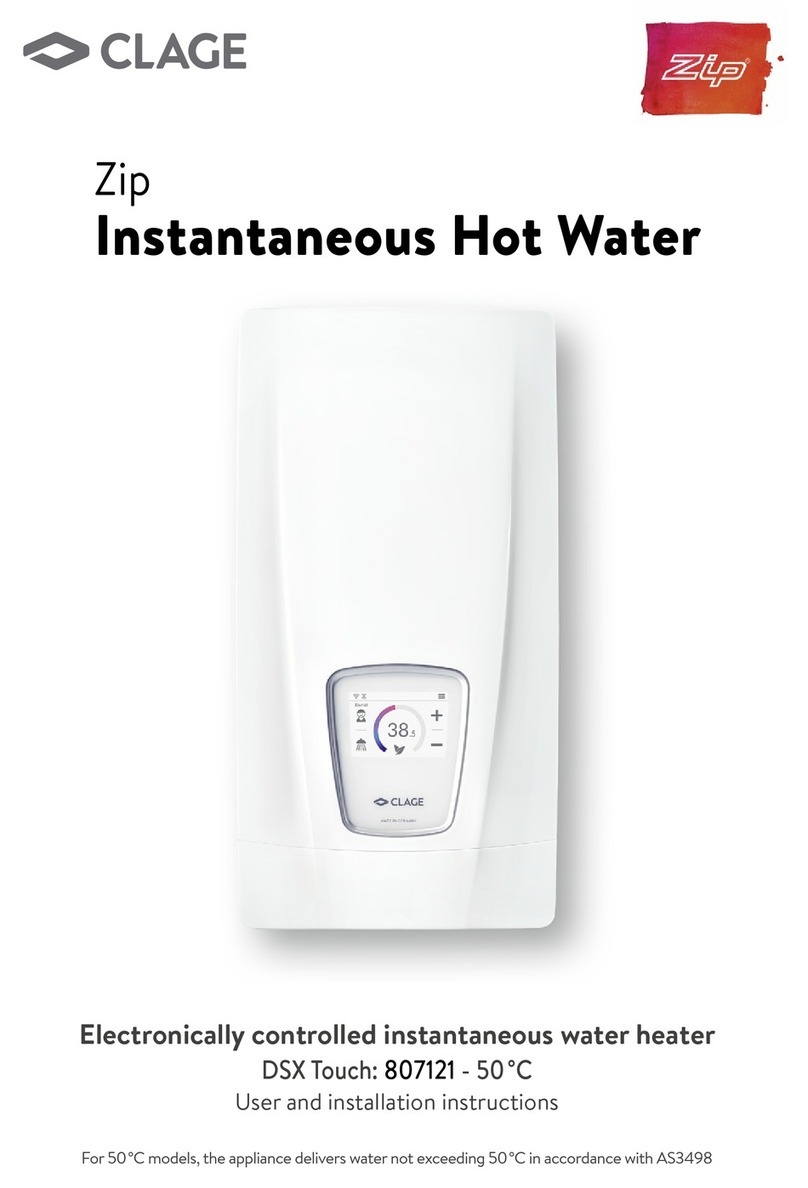
clage
clage Zip 807121 User and installation instructions
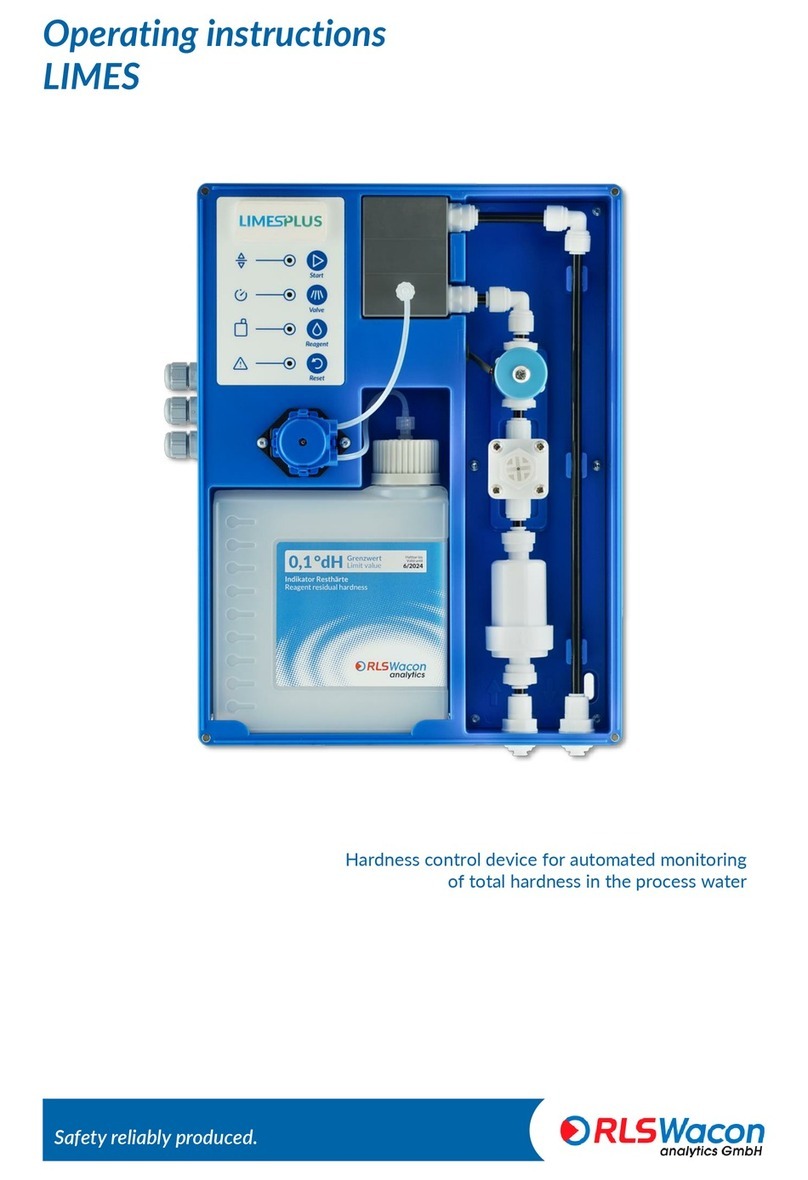
RLS Wacon
RLS Wacon LIMES PLUS operating instructions
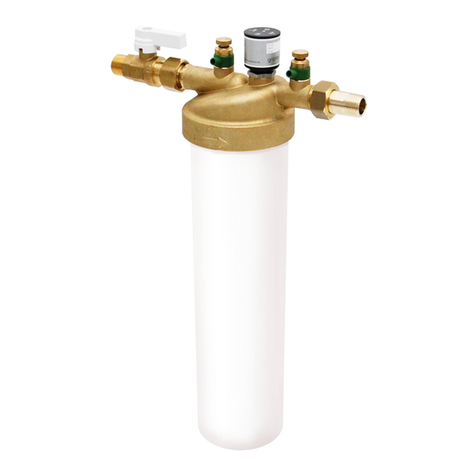
Grunbeck
Grunbeck thermaliQ:HB2 Operation manual
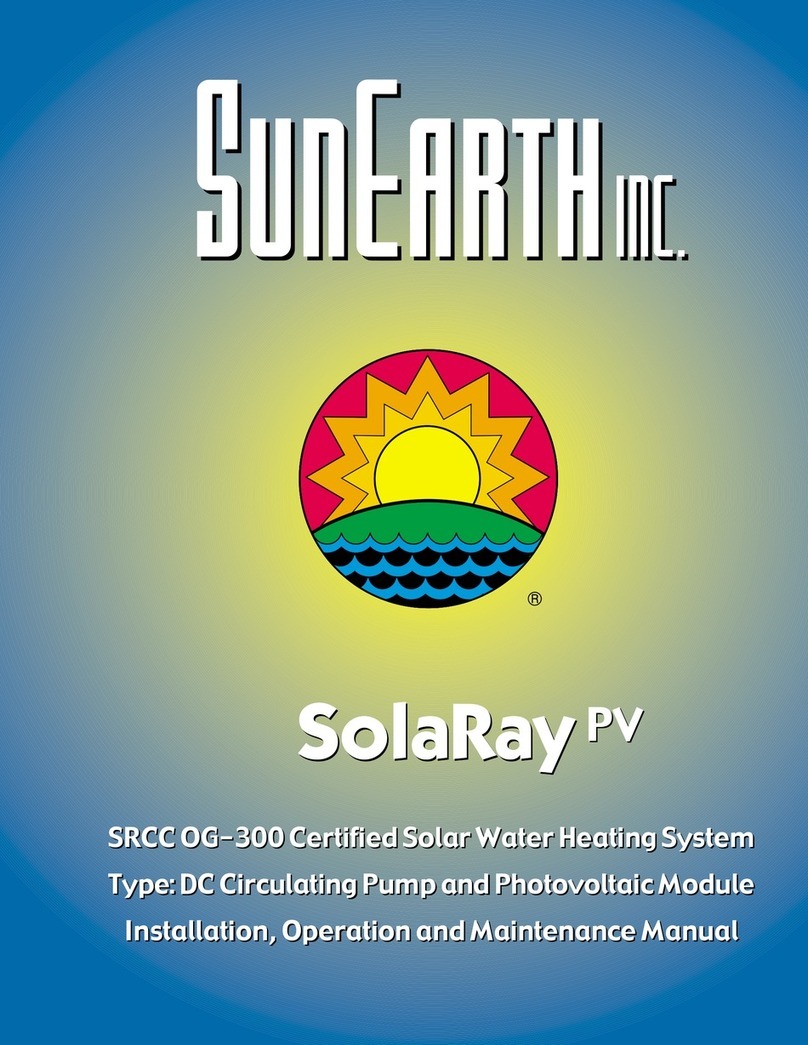
SunEarth
SunEarth SolaRay PV Installation, operation and maintenance manual
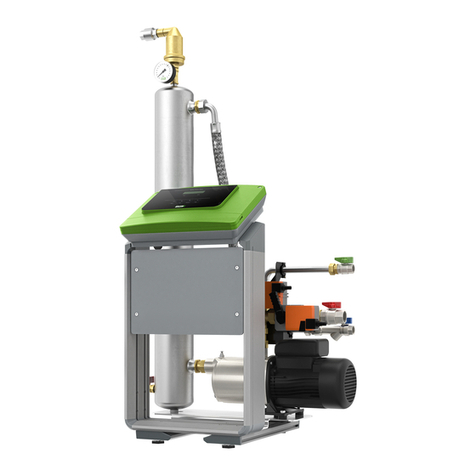
Reflex
Reflex Servitec 35 Original operating manual
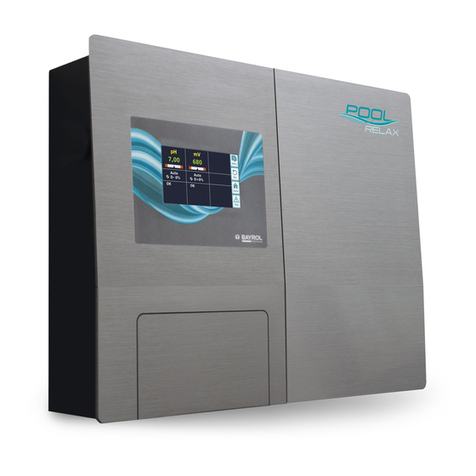
Bayrol
Bayrol Pool Relax Chlorine instruction manual
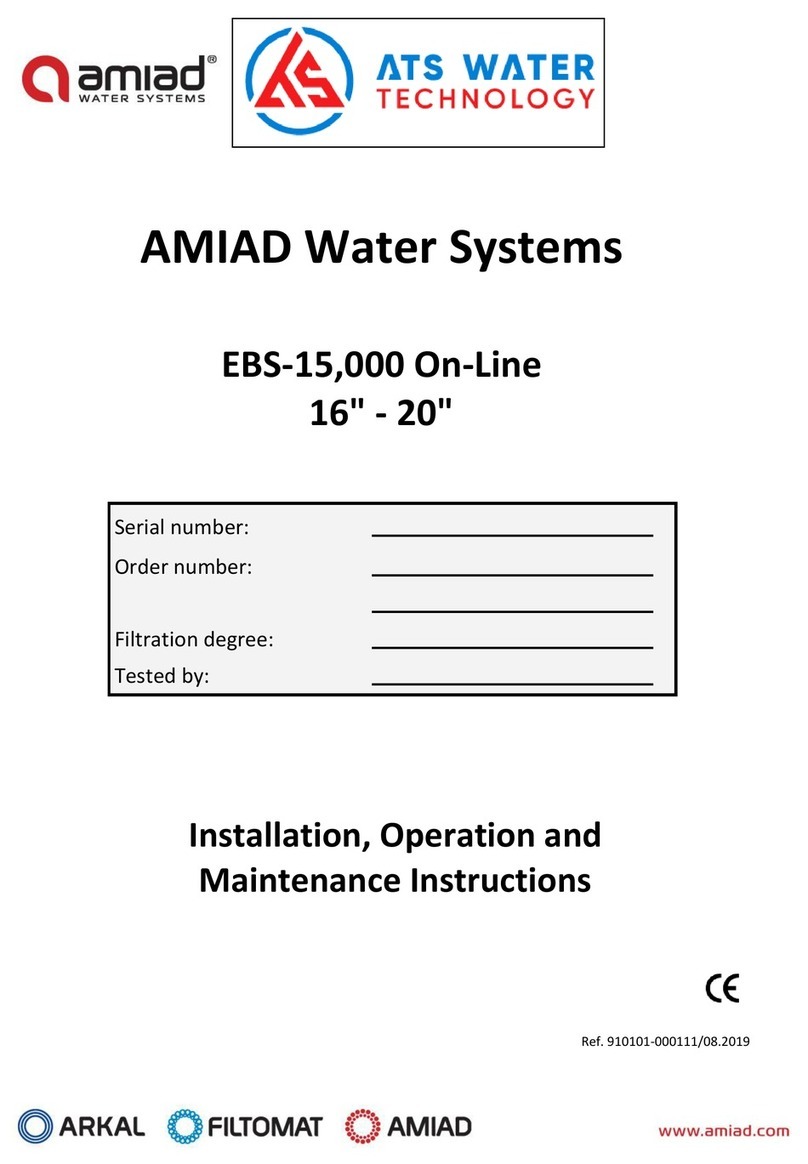
amiad
amiad EBS-15000 On-Line Installation, operation and maintenance instructions
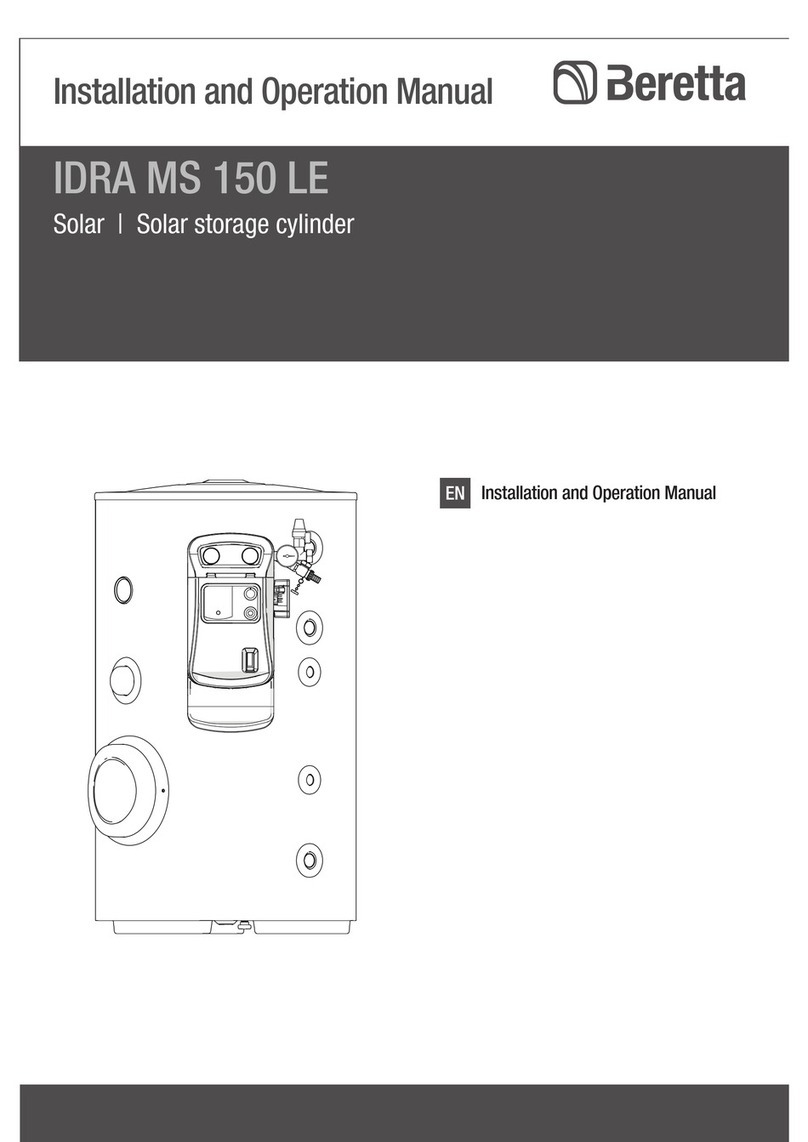
Beretta
Beretta IDRA MS 150 LE Installation and operation manual
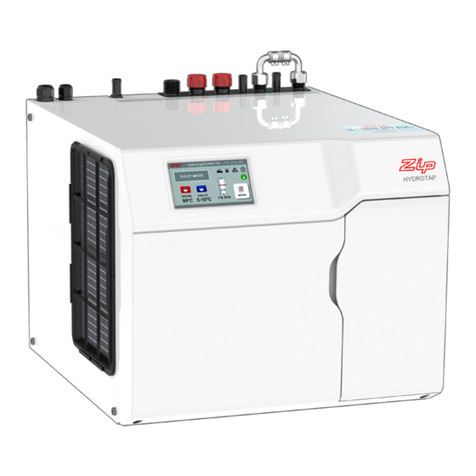
Zip
Zip 5253UK installation instructions